半导体制造前道工艺 PPT
合集下载
半导体前道制造工艺流程.完美版PPT

SiO2
P+ N-epi P+ N-epi P+
N+-BL
N+-BL
P-SUB
涂胶—烘烤---掩膜(曝光)---显影---坚膜—蚀刻—清洗 —去膜--清洗—P+扩散(B)
第三次光刻—P型基区扩散孔
决定NPN管的基区扩散位置范围 SiO2
三、IC构装制程
• IC構裝製程(Packaging):利用塑膠 或陶瓷包裝晶粒與配線以成積體電路
• 目的:是為了製造出所生產的電路的保 護層,避免電路受到機械性刮傷或是高 溫破壞。
半导体制造工艺分类
MOS型
双极型
PMOS型 NMOS型 CMOS型 饱和型
非饱和型
BiMOS TTL I2L ECL/CML
衬底制备 一次氧化 隐埋层光刻 隐埋层扩散
外延淀积
基区光刻
再氧化
隔离扩散
隔离光刻
基区扩散 再分布及氧化 发射区光刻 背面掺金
热氧化 发射区扩散
铝合金
反刻铝
铝淀积
接触孔光刻 再分布及氧化
淀积钝化层 压焊块光刻
中测
横向晶体管刨面图
B
C E
P+
P N
P
P+
P
PNP
纵向晶体管刨面图
CBE P
N
N+ C
B
二、晶圆针测制程
• 经过Wafer Fab之制程後,晶圆上即形成 一格格的小格 ,我们称之为晶方或是晶粒 (Die),在一般情形下,同一片晶圆上 皆制作相同的晶片,但是也有可能在同一 片晶圆 上制作不同规格的产品;这些晶圆 必须通过晶片允收测试,晶粒将会一一经 过针测(Probe)仪器以测试其电气特性, 而不合格的的晶粒将会被标上记号(Ink Dot),此程序即 称之为晶圆针测制程 (Wafer Probe)。然後晶圆将依晶粒 为单位分割成一粒粒独立的晶粒
P+ N-epi P+ N-epi P+
N+-BL
N+-BL
P-SUB
涂胶—烘烤---掩膜(曝光)---显影---坚膜—蚀刻—清洗 —去膜--清洗—P+扩散(B)
第三次光刻—P型基区扩散孔
决定NPN管的基区扩散位置范围 SiO2
三、IC构装制程
• IC構裝製程(Packaging):利用塑膠 或陶瓷包裝晶粒與配線以成積體電路
• 目的:是為了製造出所生產的電路的保 護層,避免電路受到機械性刮傷或是高 溫破壞。
半导体制造工艺分类
MOS型
双极型
PMOS型 NMOS型 CMOS型 饱和型
非饱和型
BiMOS TTL I2L ECL/CML
衬底制备 一次氧化 隐埋层光刻 隐埋层扩散
外延淀积
基区光刻
再氧化
隔离扩散
隔离光刻
基区扩散 再分布及氧化 发射区光刻 背面掺金
热氧化 发射区扩散
铝合金
反刻铝
铝淀积
接触孔光刻 再分布及氧化
淀积钝化层 压焊块光刻
中测
横向晶体管刨面图
B
C E
P+
P N
P
P+
P
PNP
纵向晶体管刨面图
CBE P
N
N+ C
B
二、晶圆针测制程
• 经过Wafer Fab之制程後,晶圆上即形成 一格格的小格 ,我们称之为晶方或是晶粒 (Die),在一般情形下,同一片晶圆上 皆制作相同的晶片,但是也有可能在同一 片晶圆 上制作不同规格的产品;这些晶圆 必须通过晶片允收测试,晶粒将会一一经 过针测(Probe)仪器以测试其电气特性, 而不合格的的晶粒将会被标上记号(Ink Dot),此程序即 称之为晶圆针测制程 (Wafer Probe)。然後晶圆将依晶粒 为单位分割成一粒粒独立的晶粒
第三章半导体制造工艺简介ppt课件
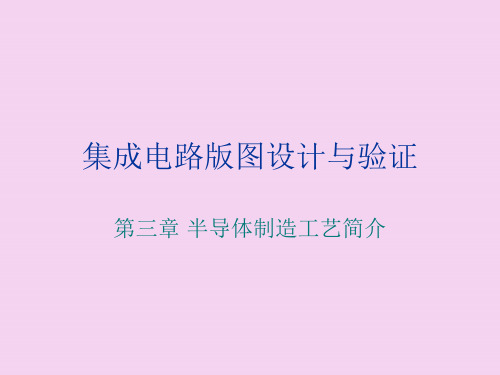
8 常用工艺之五:薄膜制备
❖ 四种薄膜:氧化膜;电介质膜;多晶硅膜; 金属膜
8 常用工艺之五:薄膜制备
❖ (1〕氧化 ❖ SiO2的作用 ❖ 屏蔽杂质、栅氧化层、介质隔离、器件保护和表面
钝化 ❖ SiO2的制备 ❖ 需要高纯度,目前最常用的方法是热氧化法。主要
分为干氧氧化、水汽氧化和湿氧氧化三种。 ❖ 氮化硅的制备 ❖ 主要用作:金属上下层的绝缘层、场氧的屏蔽层、
主要内容
❖ 3.1半导体基础知识 ❖ 3.2 工艺流程 ❖ 3.3 工艺集成
3.2 工艺流程
❖ 1 制造工艺简介 ❖ 2 材料的作用 ❖ 3 工艺流程 ❖ 4 常用工艺之一:外延生长 ❖ 5 常用工艺之二:光刻 ❖ 6 常用工艺之三:刻蚀 ❖ 7 常用工艺之四:掺杂 ❖ 8 常用工艺之五:薄膜制备
扩散和离子注入的对比
离子注入
注入损伤
❖ 注入损伤:带有能量的离子进入半导体衬底, 经过碰撞和损失能量,最后停留下来。
❖ 电子碰撞:电子激发或新的电子空穴对产生 ❖ 原子核碰撞:使原子碰撞,离开晶格,形成
损伤,也称晶格无序
晶格无序
退火
❖ 由于离子注入所造成的损伤区及无序团,使 迁移率和寿命等半导体参数受到严重影响。
❖ 每层版图都有相对应的掩膜版,并对应于不 同的工艺。
4 常用工艺之一:外延生长
❖ 半导体器件通常不是直接做在衬底上的, 而是先在沉底上生长一层外延层,然后将 器件做在外延层上。外延层可以与沉底同 一种材料,也可以不同。
❖ 在双极型集成电路中:可以解决原件间的 隔离;减小集电极串联电阻。
❖ 在CMOS集成电路中:可以有效避免闩锁 效应。
度取决于温度。
3.1半导体基础知识
❖ 关于扩散电阻: ❖ 集成电路中经常见到的扩散电阻其实就是利
半导体前道制造工艺流程ppt

薄膜厚度的测量
总结词
薄膜厚度的测量是半导体前道制造工艺中非常重要的环节,对于产品的质量和稳 定性具有重要影响。
详细描述
薄膜厚度的测量一般采用光学测量方法,如椭圆偏振仪、干涉仪等。这些仪器利 用光的干涉原理来测量薄膜厚度,精度可达到纳米级别。在测量过程中,需要注 意薄膜的均匀性和稳定性,以避免对测量结果造成误差。
掺杂浓度的测量
总结词
掺杂浓度的测量是半导体前道制造工艺中的重要环节 ,对于产品的电学性能和质量具有重要影响。
详细描述
掺杂浓度的测量一般采用离子束分析(IBA)或二次离 子质谱(SIMS)等精密仪器。这些仪器通过分析薄膜 中的离子束或二次离子的数量和能量,来确定掺杂浓 度和分布情况。在测量过程中,需要注意仪器的精度 和稳定性,以避免对测量结果造成误差。
半导体前道制造工艺流程ppt
xx年xx月xx日
目 录
• 半导体前道制造工艺概述 • 半导体前道制造工艺流程 • 半导体前道制造工艺的设备 • 半导体前道制造工艺的检测与测量 • 半导体前道制造工艺的优化与发展趋势
01
半导体前道制造工艺概述
半导体前道制造工艺的定义
半导体前道制造工艺是指利用半导体材料和制程技术,将半 导体器件制作成集成电路的过程。
随着工艺节点缩小,技术难度和成本急剧 增加。
材料短缺
部分新型材料依赖进口,存在供应风险。
制造成本
工艺复杂度高,制造成本高。
良品率
工艺不稳定导致良品率低。
半导体前道制造工艺的未来发展
新工艺技术
研究和发展新的工艺技术,如新材 料、新结构、新器件等。
跨领域合作
加强与科研机构、高校的合作,推 动产学研一体化。
曝光设备
半导体制造工艺课件(PPT 98页)

激活杂质:使不在晶格位置上的离子运动到晶格 位置,以便具有电活性,产生自由载流子,起到 杂质的作用
消除损伤
退火方式:
炉退火
快速退火:脉冲激光法、扫描电子束、连续波激 光、非相干宽带频光源(如卤光灯、电弧灯、石墨 加热器、红外设备等)
氧化工艺
氧化:制备SiO2层 SiO2的性质及其作用 SiO2是一种十分理想的电绝缘材料,
去掉氮化硅层
P阱离子注入,注硼
推阱
去掉N阱区的氧化层 退火驱入
形成场隔离区
生长一层薄氧化层 淀积一层氮化硅
光刻场隔离区,非隔离区被 光刻胶保护起来
反应离子刻蚀氮化硅 场区离子注入 热生长厚的场氧化层 去掉氮化硅层
形成多晶硅栅
生长栅氧化层 淀积多晶硅 光刻多晶硅栅 刻蚀多晶硅栅
掺杂的均匀性好 温度低:小于600℃ 可以精确控制杂质分布 可以注入各种各样的元素 横向扩展比扩散要小得多。 可以对化合物半导体进行掺杂
离子注入系统的原理示意图
离子注入到无定形靶中的高斯分布情况
退火
退火:也叫热处理,集成电路工艺中所有的 在氮气等不活泼气氛中进行的热处理过程都 可以称为退火
Salicide工艺
淀积多晶硅、刻蚀 并形成侧壁氧化层;
淀积Ti或Co等难熔 金属
RTP并选择腐蚀侧 壁氧化层上的金属;
最后形成Salicide 结构
形成硅化物
淀积氧化层 反应离子刻蚀氧化层,形成侧壁氧化层 淀积难熔金属Ti或Co等 低温退火,形成C-47相的TiSi2或CoSi 去掉氧化层上的没有发生化学反应的Ti或Co 高温退火,形成低阻稳定的TiSi2或CoSi2
氧化层刻蚀掉,并去掉光刻胶 进行大剂量As+注入并退火,形成n+埋层
消除损伤
退火方式:
炉退火
快速退火:脉冲激光法、扫描电子束、连续波激 光、非相干宽带频光源(如卤光灯、电弧灯、石墨 加热器、红外设备等)
氧化工艺
氧化:制备SiO2层 SiO2的性质及其作用 SiO2是一种十分理想的电绝缘材料,
去掉氮化硅层
P阱离子注入,注硼
推阱
去掉N阱区的氧化层 退火驱入
形成场隔离区
生长一层薄氧化层 淀积一层氮化硅
光刻场隔离区,非隔离区被 光刻胶保护起来
反应离子刻蚀氮化硅 场区离子注入 热生长厚的场氧化层 去掉氮化硅层
形成多晶硅栅
生长栅氧化层 淀积多晶硅 光刻多晶硅栅 刻蚀多晶硅栅
掺杂的均匀性好 温度低:小于600℃ 可以精确控制杂质分布 可以注入各种各样的元素 横向扩展比扩散要小得多。 可以对化合物半导体进行掺杂
离子注入系统的原理示意图
离子注入到无定形靶中的高斯分布情况
退火
退火:也叫热处理,集成电路工艺中所有的 在氮气等不活泼气氛中进行的热处理过程都 可以称为退火
Salicide工艺
淀积多晶硅、刻蚀 并形成侧壁氧化层;
淀积Ti或Co等难熔 金属
RTP并选择腐蚀侧 壁氧化层上的金属;
最后形成Salicide 结构
形成硅化物
淀积氧化层 反应离子刻蚀氧化层,形成侧壁氧化层 淀积难熔金属Ti或Co等 低温退火,形成C-47相的TiSi2或CoSi 去掉氧化层上的没有发生化学反应的Ti或Co 高温退火,形成低阻稳定的TiSi2或CoSi2
氧化层刻蚀掉,并去掉光刻胶 进行大剂量As+注入并退火,形成n+埋层
半导体前道制造工艺流程

SiO2
P+ N-epi P+ N-epi P+
N+-BL
N+-BL
P-SUB
涂胶—烘烤---掩膜(曝光)---显影---坚膜—蚀刻—清洗 —去膜--清洗—P+扩散(B)
第三次光刻—P型基区扩散孔
决定NPN管的基区扩散位置范围 SiO2
P
P
P+
P+ N-epi P+
N+-BL
N+-BL
P-SUB
去SiO2—氧化--涂胶—烘烤---掩膜(曝光)---显影---坚膜 —蚀刻—清洗—去膜—清洗—基区扩散(B)
• 5。光III---N管场区光刻,N管场区注入, 以提高场开启,减少闩锁效应及改善阱 的接触。
B+
光刻胶
P-
N-Si
CMOS集成电路工艺 --以P阱硅栅CMOS为例
• 6。光III---N管场区光刻,刻出N管场区 注入孔; N管场区注入。
P-
N-Si
CMOS集成电路工艺 --以P阱硅栅CMOS为例
第四次光刻—N+发射区扩散孔
• 集电极和N型电阻的接触孔,以及外延层的反偏孔。 • Al—N-Si 欧姆接触:ND≥1019cm-3,
P P+
N+-BL
N+
P+ NP-epi
P+
N+-BL
P-SUB
SiO2
去SiO2—氧化--涂胶—烘烤---掩膜(曝光)---显影---坚膜 —蚀刻—清洗—去膜—清洗—扩散
二、晶圆针测制程
• 经过Wafer Fab之制程後,晶圆上即形成 一格格的小格 ,我们称之为晶方或是晶粒 (Die),在一般情形下,同一片晶圆上 皆制作相同的晶片,但是也有可能在同一 片晶圆 上制作不同规格的产品;这些晶圆 必须通过晶片允收测试,晶粒将会一一经 过针测(Probe)仪器以测试其电气特性, 而不合格的的晶粒将会被标上记号(Ink Dot),此程序即 称之为晶圆针测制程 (Wafer Probe)。然後晶圆将依晶粒 为单位分割成一粒粒独立的晶粒
P+ N-epi P+ N-epi P+
N+-BL
N+-BL
P-SUB
涂胶—烘烤---掩膜(曝光)---显影---坚膜—蚀刻—清洗 —去膜--清洗—P+扩散(B)
第三次光刻—P型基区扩散孔
决定NPN管的基区扩散位置范围 SiO2
P
P
P+
P+ N-epi P+
N+-BL
N+-BL
P-SUB
去SiO2—氧化--涂胶—烘烤---掩膜(曝光)---显影---坚膜 —蚀刻—清洗—去膜—清洗—基区扩散(B)
• 5。光III---N管场区光刻,N管场区注入, 以提高场开启,减少闩锁效应及改善阱 的接触。
B+
光刻胶
P-
N-Si
CMOS集成电路工艺 --以P阱硅栅CMOS为例
• 6。光III---N管场区光刻,刻出N管场区 注入孔; N管场区注入。
P-
N-Si
CMOS集成电路工艺 --以P阱硅栅CMOS为例
第四次光刻—N+发射区扩散孔
• 集电极和N型电阻的接触孔,以及外延层的反偏孔。 • Al—N-Si 欧姆接触:ND≥1019cm-3,
P P+
N+-BL
N+
P+ NP-epi
P+
N+-BL
P-SUB
SiO2
去SiO2—氧化--涂胶—烘烤---掩膜(曝光)---显影---坚膜 —蚀刻—清洗—去膜—清洗—扩散
二、晶圆针测制程
• 经过Wafer Fab之制程後,晶圆上即形成 一格格的小格 ,我们称之为晶方或是晶粒 (Die),在一般情形下,同一片晶圆上 皆制作相同的晶片,但是也有可能在同一 片晶圆 上制作不同规格的产品;这些晶圆 必须通过晶片允收测试,晶粒将会一一经 过针测(Probe)仪器以测试其电气特性, 而不合格的的晶粒将会被标上记号(Ink Dot),此程序即 称之为晶圆针测制程 (Wafer Probe)。然後晶圆将依晶粒 为单位分割成一粒粒独立的晶粒
半导体制造工艺流程简介ppt课件

元件最小尺寸达到0.5微米
集成电路技术的分类
集成电路技术总的可以分为“设计”和“制造”两大部分 设计是指半导体芯片的设计技术,以开发新的功能或使最终产品获得优良的
性能价格比,现在一般采用计算机辅助设计
制造:这是我们要重点介绍的)
半导体工艺--- “三超”技术:
(一)超净技术
即要求严格控制工作环境中的尘埃,做到无污染生 产。目前的尘埃颗粒直径已能控制在0.1微米
被郁闷了这么久,也该看看是怎样加工的了 半导体的制造工艺
流程
---- 芯片的加工
总结:
1.半导体材料及分类。 2.集成电路技术。 3. 半导体的使用历史 4. 半导体的加工工艺。
感谢下 载
半导体的使用
集成电路简介
所谓集成电路,是指把某一单元电路用集成工艺制作在同一基片上,使之具有 和单个分开的元器件所制作的电子线路同等或更好的功能 。
现有的集成电路,主要是将电阻、电容、二极管、三极管等元器件及其互连
芯片 线集成制作在单个半导体硅片上的半导体集成电路,又称为
芯片内部之间的线很细,芯片很薄,很容易被损坏。 芯片不能“REWORK”
三是超微细加工技术
通常把最小线宽为微米级或亚微米级的加工技术统称为微细加工技术,主要 包括晶体生长和薄层生成技术、微细图形加工技术、精密控制掺杂技术等。 决定集成电路集成度的主要因素是这些技术水平所决定的基片材料拉制的直 径大小和每个元件具有的微小尺寸。
半导体材料的使用
在几百万年前,我们的祖先是用鹅卵石。 十万年前,他们开始使用自制工具。 五千年前,他们开始使用金属工具。 五百年前,他们开始使用会爆炸的工具。 如今,我们使用半导体工具,比如我们常用的电脑,电视,手机,甚至汽车
都跟半导体有关。
集成电路技术的分类
集成电路技术总的可以分为“设计”和“制造”两大部分 设计是指半导体芯片的设计技术,以开发新的功能或使最终产品获得优良的
性能价格比,现在一般采用计算机辅助设计
制造:这是我们要重点介绍的)
半导体工艺--- “三超”技术:
(一)超净技术
即要求严格控制工作环境中的尘埃,做到无污染生 产。目前的尘埃颗粒直径已能控制在0.1微米
被郁闷了这么久,也该看看是怎样加工的了 半导体的制造工艺
流程
---- 芯片的加工
总结:
1.半导体材料及分类。 2.集成电路技术。 3. 半导体的使用历史 4. 半导体的加工工艺。
感谢下 载
半导体的使用
集成电路简介
所谓集成电路,是指把某一单元电路用集成工艺制作在同一基片上,使之具有 和单个分开的元器件所制作的电子线路同等或更好的功能 。
现有的集成电路,主要是将电阻、电容、二极管、三极管等元器件及其互连
芯片 线集成制作在单个半导体硅片上的半导体集成电路,又称为
芯片内部之间的线很细,芯片很薄,很容易被损坏。 芯片不能“REWORK”
三是超微细加工技术
通常把最小线宽为微米级或亚微米级的加工技术统称为微细加工技术,主要 包括晶体生长和薄层生成技术、微细图形加工技术、精密控制掺杂技术等。 决定集成电路集成度的主要因素是这些技术水平所决定的基片材料拉制的直 径大小和每个元件具有的微小尺寸。
半导体材料的使用
在几百万年前,我们的祖先是用鹅卵石。 十万年前,他们开始使用自制工具。 五千年前,他们开始使用金属工具。 五百年前,他们开始使用会爆炸的工具。 如今,我们使用半导体工具,比如我们常用的电脑,电视,手机,甚至汽车
都跟半导体有关。
半导体制造流程PPT课件
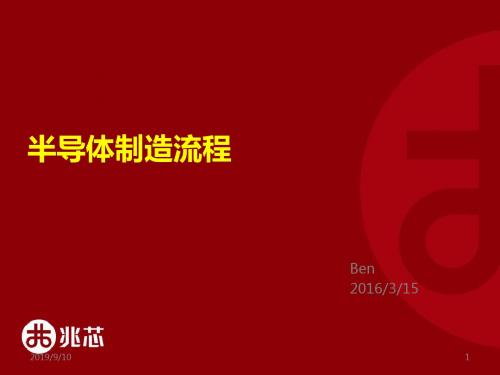
2019/9/10
3
晶圆处理制程
融化(MeltDown)
颈部成长(Neck Growth)
晶柱成长制程
晶冠成长(Crown Growth)
晶体成长(Body Growth)
尾部成长(Tail Growth)
2019/9/10
4
晶圆处理制程
切片 (Slicing)
圆边 (Edge Polishin
2019/9/10
16
晶圆处理制程
• 离子注入是另一种掺杂技术,离子注入掺杂也分为两 个步骤:离子注入和退火再分布。离子注入是通过高 能离子束轰击硅片表面,在掺杂窗口处,杂质离子被 注入硅本体,在其他部位,杂质离子被硅表面的保护 层屏蔽,完成选择掺杂的过程。进入硅中的杂质离子 在一定的位置形成一定的分布。通常,离子注入的深 度(平均射程)较浅且浓度较大,必须重新使它们再分 布。掺杂深度由注入杂质离子的能量和质量决定,掺 杂浓度由注入杂质离子的数目(剂量)决定。
• 一个现代的IC含有百万个以上的独立组件,而其尺寸通 常在数微米,在此种尺寸上,并无一合适的机械加工机 器可以使用,取而代之的是微电子中使用紫外光的图案 转换(Patterning),这个过程是使用光学的图案以及光感 应膜來将图案转上基板,此种过程称为光刻微影 (photolithography)
2019/9/10
11
晶圆处理制程
曝光(exposure) • 在光刻微影过程,首先为光阻涂布,先将适量光阻滴上基
板中心,而基板是置于光阻涂 布机 的真空吸盘上,转盘 以每分钟數千转之转速,旋转30-60秒,使光阻均匀涂布 在 基板上,转速与旋转时间,依所需光阻厚度而定。 • 曝照于紫外光中,会使得光阻的溶解率改变。紫外光通过 光罩照射于光阻上,而在光照及阴影处产生相对应的图形 ,而受光照射的地方,光阻的溶解率产生变化,称之 为光 化学反应, 而阴影处的率没有变化,这整个过称之为曝光 (exposure)。
半导体制造工艺技术PPT(共68页)
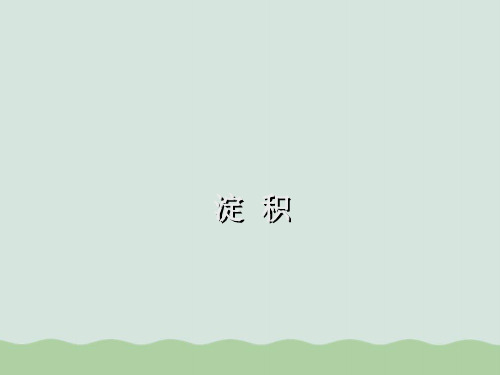
Si2H6(气态) (反应半
3) Si2H6(气态) 品形成)
2Si (固态) + 3H2(气态) (最终产
以上实例是硅气相外延的一个反应过程
• 速度限制阶段
在实际大批量生产中,CVD反应的时间长 短很重要。温度升高会促使表面反应速度增加 。基于CVD反应的有序性,最慢的反应阶段会 成为整个工艺的瓶颈。换言之,反应速度最慢 的阶段将决定整个淀积过程的速度。
种新的化合物。
以上5中基本反应中,有一些特定的 化学气相淀积反应用来在硅片衬底上淀 积膜。对于某种特定反应的选择通常要 考虑淀积温度、膜的特性以及加工中的 问题等因素。
例如,用硅烷和氧气通过氧化反应 淀积SiO2膜。反应生成物SiO2淀积在硅 片表面,副产物事是氢。
SiH4 + O2
SiO2 + 2H2
• CVD 过程中的掺杂
CVD淀积过程中,在SiO2中掺入杂质对硅 片加工来说也是很重要。例如,在淀积SiO2的 过程中,反应气体中加入PH3后,会形成磷硅 玻璃。化学反应方程如下:
SiH4(气)+2PH3(气)+O2(气) SiO2(固)+2P(固)+5H2(气)
在磷硅玻璃中,磷以P2O5的形式存在,磷 硅玻璃由P2O5和SiO2的混合物共同组成;对于 要永久黏附在硅片表面的磷硅玻璃来说, P2O5 含量(重量比)不超过4%,这是因为磷硅玻 璃(PSG)有吸潮作用。
CVD 反应
• CVD 反应步骤
基本的化学气相淀积反应包含8个主要步骤, 以解释反应的机制。 1)气体传输至淀积区域; 2)膜先驱物的形成; 3)膜先驱物附着在硅片表面; 4)膜先驱物黏附; 5)膜先驱物扩散; 6)表面反应; 7)副产物从表面移除; 8)副产物从反应腔移除。
半导体前道制造工艺流程
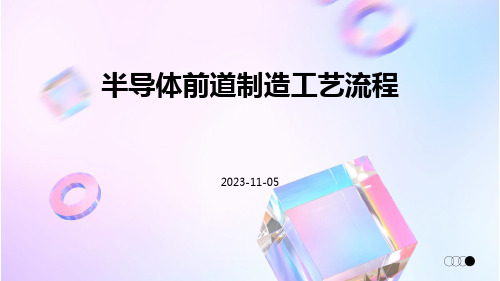
详细描述:半导体前道制造工艺流程中,各种原材料的 质量和稳定性对产品性能有着重要影响。材料问题可能 导致产品性能下降、良品率降低等问题。
1. 严格把控原材料质量:建立严格的原材料质量标准 和检验程序,确保进厂原材料符合要求。
3. 与可靠的供应商合作:选择具有良好信誉和稳定质 量的供应商,确保原材料的稳定供应和质量保障。
02
半导体前道制造主要工艺 流程
氧化过程
设备
氧化炉、尾气处理装置等。
方法
干法氧化、湿法氧化。
目的
提高硅片表面的氧化层,增加薄膜的附着 力和稳定性,同时减少杂质离子影响。
影响因素
温度、湿度、氧气流量等。
光刻过程
设备
光刻机、涂胶/显影机等。
方法
涂胶、曝光、显影。
目的
将设计好的电路图案转移到硅片表 面,以实现电路结构的精确刻画。
03
解决方法:为解决工艺偏差问题,可以采取以下措施
工艺偏差及解决方法
1. 强化工艺控制
通过实时监控关键工艺参数,确保工艺过程的一致性和稳定性。
2. 引入自动化和智能化设备
利用先进的设备和技术,提高工艺控制精度和效率。
3. 定期进行工艺验证和审计
通过验证和审计,发现并纠正工艺偏差,确保工艺过程的可靠性 。
设备故障及解决方法
总结词:设备故障
详细描述:半导体前道制造工艺流程中,各种高精度的设备在长时间运行过程中可能会出现故障,如机械部件磨损、电路故障 等。这些故障可能导致生产停滞、影响产品质量等问题。
设备故障及解决方法
解决方法
为解决设备故障问题,可以采取以下措施
2. 安装监控系统
通过安装传感器和监控系统,实时监测设 备的运行状态,及时发现并处理故障。
相关主题
- 1、下载文档前请自行甄别文档内容的完整性,平台不提供额外的编辑、内容补充、找答案等附加服务。
- 2、"仅部分预览"的文档,不可在线预览部分如存在完整性等问题,可反馈申请退款(可完整预览的文档不适用该条件!)。
- 3、如文档侵犯您的权益,请联系客服反馈,我们会尽快为您处理(人工客服工作时间:9:00-18:30)。
• 涂底 • 旋转涂胶*(利用离心力) • 软烘(去除圆片表面的潮气,增加粘附性) • 边缘光刻胶的去除 • 对准* • 曝光*(接触、接近、投影、步进) • 后烘(平衡驻波效应,提高分辨率。) • 显影* • 硬烘(提高刻蚀和注入的抵抗力,提高粘附性)
大家学习辛苦了,还是要坚持
继续保持安静
清洗
半导体制造前道工艺
Attention
• 在参考资料的时候,有的步骤 或是工艺在不同资料里面的说 法有点出入,所以本PPT可能 有很多不对的地方,希望大家 多多指正。
晶圆
晶圆是指硅半导体集成电路制作所 用的硅晶片,由于其形状为圆形, 故称为晶圆;在硅晶片上可加工制 作成各种电路元件结构,而成为有 特定电性功能之IC产品。晶圆的原 始材料是硅,而地壳表面有用之不 竭的二氧化硅。二氧化硅矿石经由 电弧炉提炼,盐酸氯化,并经蒸馏 后,制成了高纯度的多晶硅,其纯 度高达99.999999999%。
预烘和底膜涂覆
蚀刻
• 通常所指蚀刻也称光化学蚀刻,指通过曝 光制版、显影后,将要蚀刻区域的保护膜 去除,在蚀刻时接触化学溶液,达到溶解 腐蚀的作用,形成凹凸或者镂空成型的效 果。(选择性刻蚀转移光刻胶上的IC设计 图形到晶圆表面)
• 干法蚀刻 • 湿法蚀刻( HNO3去撞击固态物体。固态物 体会对离子束的运动产生阻碍,使 其最终留在固体中,这一现象就是 离子注入。(掺杂、真空、低温、加 速)
晶圆处理工序
• 本工序主要是通过清洗、氧化、 化学气相沉积、涂膜、曝光、显 影、蚀刻、离子植入、金属溅镀 等反复步骤在晶圆上制作电路及 电子元件,最终在晶圆上完成数 层电路及元件加工与制作。
• 清洗:用特殊的清洗机和不同的清 洗剂进行多道清洗。用于减少污染 物。
• 氧化:使硅片表面形成氧化膜。主 要方法有热氧化法及气相成长法。 (绝缘、保护等作用)
• 化学气相沉积:反应物质在气态条 件下发生化学反应,生成固态物质 沉积在加热的固态基体表面,进而 制得固体材料的工艺技术。
光刻加工
• 光刻是一种利用类似于照片洗印的原 理通过曝光和选择性化学腐蚀将掩膜 版上的集成电路印制到硅片上的精密 表面加工技术。
• 硅片清洗烘干(用于减少污染物,减少缺陷,使光刻 胶更容易粘附。)
大家学习辛苦了,还是要坚持
继续保持安静
清洗
半导体制造前道工艺
Attention
• 在参考资料的时候,有的步骤 或是工艺在不同资料里面的说 法有点出入,所以本PPT可能 有很多不对的地方,希望大家 多多指正。
晶圆
晶圆是指硅半导体集成电路制作所 用的硅晶片,由于其形状为圆形, 故称为晶圆;在硅晶片上可加工制 作成各种电路元件结构,而成为有 特定电性功能之IC产品。晶圆的原 始材料是硅,而地壳表面有用之不 竭的二氧化硅。二氧化硅矿石经由 电弧炉提炼,盐酸氯化,并经蒸馏 后,制成了高纯度的多晶硅,其纯 度高达99.999999999%。
预烘和底膜涂覆
蚀刻
• 通常所指蚀刻也称光化学蚀刻,指通过曝 光制版、显影后,将要蚀刻区域的保护膜 去除,在蚀刻时接触化学溶液,达到溶解 腐蚀的作用,形成凹凸或者镂空成型的效 果。(选择性刻蚀转移光刻胶上的IC设计 图形到晶圆表面)
• 干法蚀刻 • 湿法蚀刻( HNO3去撞击固态物体。固态物 体会对离子束的运动产生阻碍,使 其最终留在固体中,这一现象就是 离子注入。(掺杂、真空、低温、加 速)
晶圆处理工序
• 本工序主要是通过清洗、氧化、 化学气相沉积、涂膜、曝光、显 影、蚀刻、离子植入、金属溅镀 等反复步骤在晶圆上制作电路及 电子元件,最终在晶圆上完成数 层电路及元件加工与制作。
• 清洗:用特殊的清洗机和不同的清 洗剂进行多道清洗。用于减少污染 物。
• 氧化:使硅片表面形成氧化膜。主 要方法有热氧化法及气相成长法。 (绝缘、保护等作用)
• 化学气相沉积:反应物质在气态条 件下发生化学反应,生成固态物质 沉积在加热的固态基体表面,进而 制得固体材料的工艺技术。
光刻加工
• 光刻是一种利用类似于照片洗印的原 理通过曝光和选择性化学腐蚀将掩膜 版上的集成电路印制到硅片上的精密 表面加工技术。
• 硅片清洗烘干(用于减少污染物,减少缺陷,使光刻 胶更容易粘附。)