RS24ADPIO-2使用说明书
PCI-DIO24系列产品说明书

Software SupportThe PCI-DIO24 series issupplied with InstaCal software for configuration and testing. In addition, it is also supported by the optional Universal Library. The Universal Library is a set of I/O libraries and drivers for users creating their own custom programs.The Universal Library is compatible with most Windows (32-bit) based languages and supports the PCI-DIO, PCI-DAS and CIO families of boards.The Library includes an extensive set of programming examples written in Visual Basic,C and Pascal for Windows 95 and Windows NT. An optional driver for LabVIEW is also available.The boards are also supported by the same wide variety of external relay and solid state I/O module racks as are the CIO-DIO24 boards.The PCI-DIO24 is completely plug-and-play. There are no switches or jumpers on the board. All board addresses, interrupt channels, etc.,are set by your computer’s plug-and-play software.Connectors and CablesAll I/O signals are brought through a 37-pin male “D” connector. The (optional) C37FF-XX series cable brings all of the pins out and is suitable for use with all compatible screw terminal and signalconditioning accessory boards. The PCI-DIO24 and PCI-DIO24H connector pin-out is identical to the standard ISA bus CIO-DIO24boards and is fully compatible with the same wide assortment of signal conditioning accessory boards.D3-3PCI-DIO24 and PCI-DIO24H24-Bit Digital I/O Board for PCI Bus$109Basic Unitߜ24 Digital I/O Bits ߜHigh Current Output for PCI-DIO24HߜConnector and Software Compatible with CIO-DIO24ߜFully Plug-and-PlayThe PCI-DIO24 and PCI-DIO24H are low cost, 24-bit, logic level digital I/O boards for the PCI bus for IBM or compatible PC’s. The PCI-DIO24 is based on the industry standard 82C55 chip, and the82C55 I/O pins are brought directly to the board’s I/O connector. The 82C55 is a powerful 24-bit chip which functions as two 8-bit ports (Ports A and B) and a third 8-bit port (Port C) that may be further divided into two 4-bit ports (Ports C-HI and C-LO). The CMOSoutputs of the 82C55 are suitable for driving a wide array of logic devices, although the chip’s ±2.5 mA drive capability may not be enough for some applications.The PCI-DIO24H board provides a discrete logic emulation of the 82C55 mode 0, but offerssignificantly higher output drive capability (64 mA sink, 15 mA source). This mode 0 emulation is fully compatible with the 82C55,and all codes written for 82C55-mode based boards will function perfectly on the PCI-DIO24H.The PCI-DIO24 series boards are connector and software compatible with OMEGA’s highly popular ISA based CIO-DIO24 board, as well as with a host of 82C55-based boards from other vendors.PCI-DIO24H, $179,shown smalller thanactual sizePCI-DIO24, $109, shown smalller than actual sizeD3DIGITAL I/O AND COUNTER/TIMER CARDSThe optional CIO-ERB24, $249, relay rack, shown smaller then acutal size, (see Section H for details)SpecificationsPCI-DIO24Number of Channels: 24 I/O Configuration:2 banks of 8, 2banks of 4, programmable by bank as input or outputI/O Device Type:82C55Output High:******************Output Low:*****************Input High:2.2 volts min, VCC +0.3 volts absolute max Input Low:0.8 volts max, -0.3 volts absolute min Power-Up/Reset State:Input mode (high impedance)Interrupts:INTA# - mapped to IRQn via PCI BIOS at boot-time Interrupt Enable:External (IRENABLE, active low, programmable through PCI9050-1; 0 = disabled, 1 = enabled (default)Interrupt Sources:External source (IR INPUT), polarity programmable through PCI9050-1; 1 = active high, 0 = active low (default)Power Consumption:+5 V Operating:240mA typical,350mA max+12, -12:not used, but supplied to I/O connectorENVIRONMENTALOperating Temperature:0 to 50°C (32 to 122°F)Storage Temperature:-20 to 70°C (-4 to 158°F)Humidity:0 to 90% non-condensing PCI-DIO24HNumber of Channels:24 I/O Configuration:2 banks of 8, 2banks of 4, programmable by bank as input or outputI/O Device Type : TTL based 82C55 mode 0 emulation Output:74S244 Input:74LS373D3-4The PCI-DIO24series comes with InstaCal testing software and complete operator’s manual.Note:The SSR-RACK24solid state switch I/O card, CIO-ERB08or any compatible relay accessory card can be used instead of the CIO-ERB24.OMEGACARE SM extended warranty is available for models shown on this page. Ask your sales representative for full details when placing order.Ordering example: PCI-DIO24H digital I/O card, C37FF-2 cable, CIO-MINI37terminal panel, ENC-MINI37enclosure, OMEGACARE SM 1-year extended warranty for PCI-DIO24H (adds 1 year to 3-year standard warranty) and UNIV-DRVR Universal Software Library, $179 + 25 + 69 + 29 + 25 + 49=$376.Output High:2.4 volts min @ -15 mAOutput Low:0.5 volts max @ 64 mAInput High:2.0 volts min, 7 volts absolute maxInput Low:0.8 volts max, -0.5 volts absolute minPower-Up/Reset State:Input mode (high impedance)Interrupts:INTA# - mapped to IRQn via PCI BIOS at boot-time Interrupt Enable:External (IR ENABLE, active low,programmable through PCI9050-1;0 = disabled,1 = enabled (default)Interrupt Sources:External source (IR INPUT), polarityprogrammable through PCI9050-1;1 = active high, 0 = active low (default)POWER CONSUMPTION+5 V Operating:625 mA typical, 960 mA max+12, -12:not used, but supplied to I/O connectorENVIRONMENTALOperating Temperature:0 to 50°C (32 to 122°F)Storage Temperature:-20 to 70°C (-4 to 158°F)Humidity:0 to 90% non-condensingAVAILABLE FOR FAST DELIVERY!CANADA www.omega.ca Laval(Quebec) 1-800-TC-OMEGA UNITED KINGDOM www. Manchester, England0800-488-488GERMANY www.omega.deDeckenpfronn, Germany************FRANCE www.omega.frGuyancourt, France088-466-342BENELUX www.omega.nl Amstelveen, NL 0800-099-33-44UNITED STATES 1-800-TC-OMEGA Stamford, CT.CZECH REPUBLIC www.omegaeng.cz Karviná, Czech Republic596-311-899TemperatureCalibrators, Connectors, General Test and MeasurementInstruments, Glass Bulb Thermometers, Handheld Instruments for Temperature Measurement, Ice Point References,Indicating Labels, Crayons, Cements and Lacquers, Infrared Temperature Measurement Instruments, Recorders Relative Humidity Measurement Instruments, RTD Probes, Elements and Assemblies, Temperature & Process Meters, Timers and Counters, Temperature and Process Controllers and Power Switching Devices, Thermistor Elements, Probes andAssemblies,Thermocouples Thermowells and Head and Well Assemblies, Transmitters, WirePressure, Strain and ForceDisplacement Transducers, Dynamic Measurement Force Sensors, Instrumentation for Pressure and Strain Measurements, Load Cells, Pressure Gauges, PressureReference Section, Pressure Switches, Pressure Transducers, Proximity Transducers, Regulators,Strain Gages, Torque Transducers, ValvespH and ConductivityConductivity Instrumentation, Dissolved OxygenInstrumentation, Environmental Instrumentation, pH Electrodes and Instruments, Water and Soil Analysis InstrumentationHeatersBand Heaters, Cartridge Heaters, Circulation Heaters, Comfort Heaters, Controllers, Meters and SwitchingDevices, Flexible Heaters, General Test and Measurement Instruments, Heater Hook-up Wire, Heating Cable Systems, Immersion Heaters, Process Air and Duct, Heaters, Radiant Heaters, Strip Heaters, Tubular HeatersFlow and LevelAir Velocity Indicators, Doppler Flowmeters, LevelMeasurement, Magnetic Flowmeters, Mass Flowmeters,Pitot Tubes, Pumps, Rotameters, Turbine and Paddle Wheel Flowmeters, Ultrasonic Flowmeters, Valves, Variable Area Flowmeters, Vortex Shedding FlowmetersData AcquisitionAuto-Dialers and Alarm Monitoring Systems, Communication Products and Converters, Data Acquisition and Analysis Software, Data LoggersPlug-in Cards, Signal Conditioners, USB, RS232, RS485 and Parallel Port Data Acquisition Systems, Wireless Transmitters and Receivers。
RS2快速入门手册
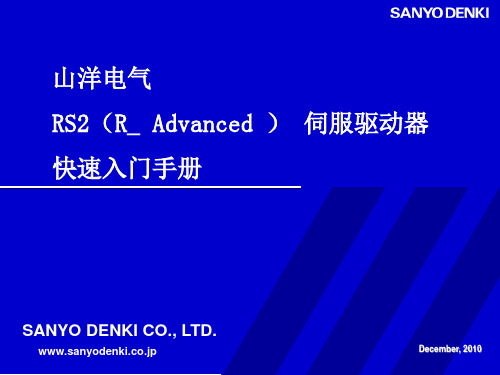
如何改参数- 4
多个参数可以通过点击 一次 “Write to amplifier” 图标保存
电机参数设定
电机参数区
1.点击“Select from the list”(M) 按钮
2. 从这个列表中选择 旋转/直线电机, 输入电压 值, 驱动器容量以及电机部分型号
3. 点击 OK 4. 点击 “Write to amplifier” 图标 (与其他参数设置一样)
1000
2000 [pulse]
3. I/O 接线(驱动器 CN1)
• 通用输入(伺服ON,报警清除,极限) • 脉冲指令输入(位置指令) • 模拟指令输入(速度,扭矩指令)
通用输入接线: CONT1-6 - 1
控制器单元 伺服驱动器
CONT-COM
50 CONT1 37 36 2.2kohm 4.7kohm
AL.A2.0
报警发生时驱动器的状态
0: 控制电源ON 2: 主电源ON
4: 准备伺服使能
8: Servo-ON(伺服使能)
报警代码
报警代码表在操作说明书第8章
“AL” 指它显示报警代码
常见报警代码: 85
检查编码器接线 •电缆连接器在放大器端
•如果使用编码器延长线、延长线上所有端子和其他侧面接口
“P“ ->
05 06
串行编码器分辨率 备用电池式绝对编码器功 能选择 控制模式选择
选择编码器分辨率. 06:131072_FMT (大部分编码器是 131072 脉冲/转.) 选择是否连接编码器的备用电池. 电池安装在山洋电气标准选配电缆之上. 连接电池-> 00:Absolute system 不连接电池 -> 01:Incremental system 选择控制器的命令类型. 00:Torque (模拟电压) 01:Velocity (模拟电压) 02:Position (脉冲指令)
RS欧时电子自动化控制产品说明

_002我们知道保证您的流程顺利运行所需的条件,也了解您每天面临的挑战。
因此,我们备有 25,000 多种自动化和控制产品,在线订购后可享受免费送达。
支持您的自动化和控制需求…助您在行业中大展宏图。
提供品种齐全的产品,涵盖来自各大领先品牌的关键技术。
欢迎 内容4电动机和控制器 5流体控制和工业开关 6机器防护和安全 7P LC、HMI 和数据采集 8传感器和转换器 11面板仪表、螺线管和发声器 12发声器和信号灯 13 温度控制、计数器和计时器 14 电缆扎带 15热缩套管 16电缆和电线 18线缆附件和扎带附件 19 工业机箱和附件 20 气动装置 21动力传动 22 D IN 导轨电源23继电器扫描关注欧时电子RS长按二维码关注欧时电子RSRS WeChat无微不至 有信必达8621-53854381欧时电子RS 欧时电子RS产品询价:热线:4006107966邮箱:CNquote@流体控制和工业开关电动机和控制器RS Stock No.Description MPN 917-642824 V dc,最大 7 mALTMEV40BDTESYS 扩展模块•专业系列 Schneider 电动机控制器附件。
附件包括扩展模块、连接电缆和跳线。
RS Stock No.DescriptionMPN258-834424 V dc,300 mNm,30 rpm0380-012533MM 12/24VDC 齿轮传动电动机:IG33•其设计适用于自动售货机、磁卡读卡器、打印机、执行器和所有类型的投币控制系统等应用领域 •使用全金属齿轮头安装,烧结铁齿轮在硬质钢轴上转动。
输出轴在烧结铜轴承上转动。
•五极电枢,带 VDR 抑制RS Stock No.DescriptionMPN718-9753.8 W,12 V dc,7.3 mNm,5900 rpm,2mm22N28-210E.20422MM 精密直流伺服系统有刷电动机 22N28•电动机可连接至我们的卵形、直齿或行星齿轮箱,以提高输出扭矩并降低转速 •低机械惯性 •低电器和铁损耗 •极低的镶齿效应•没有任何首选电枢位置 •贵金属合金刷RS Stock No.Description MPN398-991212 V 直流, 147 mNm, 35 rpm DG16L-12-0242直流齿轮传动电动机•输出速度: 35 rpm •电源电压: 12 V 直流 •最大输出扭距: 147 mNm •轴直径: 4mm •齿轮头类型: 行星RS Stock No.DescriptionMPN111-0838Lexium 28VW3M8D2AR30编码器屏蔽电缆 3M,用于BCH2.H/.M/.R、CN2 插头的 MIL 连接器•一系列的附件,适用于 Lexium 28 系列伺服传动装置和电动机。
道尔斯特电气产品说明书

南京道尔斯特电气有限公司地址:南京市秦淮区中山东路448号普华大厦4层QQ :2148984411 网址:回 传我希望了解道尔斯特电气的以下产品我希望了解更多的信息关于:姓名:公司:部门:地址/邮政编码:电话号码/传真:电子邮件:样本工业防雷PDU系列样本数显表/液晶表系列样本温湿度控制系列样本智能隔离器/安全栅系列工业交换机选型手册Product Catalog2022.1版精益求精KEEP IMPROVING样本工业交换机系列样本超级电容缓冲装置系列百兆工业级光电转换器支持2个百兆电口、1个百兆光口光口SC/ST/FC 可选,距离可选可选24V/220V 电源输入工业IP40防护等级支持导轨式/壁挂式安装● ●●●●产品简介DST-MC-3系列工业级百兆光电转换器,支持百兆电口到百兆光口的转换。
冗余电源设计,宽电压范围输入,并提供过载和反接保护。
强抗电磁干扰能力,完全满足苛刻的工业应用环境。
交换机参数IEEE 标准IEEE 802.310BaseT EthernetIEEE 802.3u 100BaseT(X) and 100BaseFX Fast Ethernet IEEE 802.3x Flow Control(流量控制)交换特性MAC 地址表2K 数据包缓存1Mbit 处理方式存储转发接口RJ45端口数2个百兆电口百兆光口1个百兆光口,单模/多模可选,SC/ST/FC 可选,单纤/双纤可选百兆光口传输距离多模2km,单模20km/40km/60km/120km 可选LED 指示灯电源、电口、光口电源24V 输入4针端子,双电源;24VDC 电源支持范围为12~36VDC 220V 输入4针端子,单电源;220V 电源支持范围为85~264VAC/77~300VDC 电源功耗最大3瓦电源保护反接保护、过载保护环境属性工作温度-40~75°C 储存温度-40~85°C相对湿度5~95% (无凝霜)物理特性外壳IP40金属外壳安装方式默认导轨安装,可选壁挂安装尺寸30(W) x 125(H) x 88(D) mm认证EMIFCC Part 15. CISPR(EN55022) class A EMSEN 61000-4-2(ESD)Level 3EN 61000-4-3(RS)Level 3EN 61000-4-4(EFT)Level 3EN 61000-4-5(Surge)Level 3EN 61000-4-6(CS)Level 3EN 61000-4-8机械IEC60068-2-6(震动) IEC60068-2-27(冲击) IEC60068-2-32(自由跌落)质保期MTBF 380000h 保修期5年0102配置型号产品描述DST-MC-2TX/1MC 百兆工业级光电转换器,2个百兆电口,1个百兆SC 光口,多模双纤2公里,24V 双电源DST-MC-2TX/1SC百兆工业级光电转换器,2个百兆电口,1个百兆SC 光口,单模双纤20公里,24V 双电源配置型号产品描述机架插卡式光电转换器每个机箱支持16个卡槽,板卡支持1个电口、1个光口百兆板卡或者千兆板卡可混插机箱双电源供电● 产品简介DST-MC-16系列机架插卡式光电转换器,标准2U 机箱,共支持16个插槽。
DPO2012示波器简易说明书

DPO2012示波器简易说明书使用菜单系统,请执行下列操作:1. 按某个前面板菜单按钮以显示要使用的菜单。
2. 按下方bezel 按钮选择菜单项。
如果出现弹出式菜单,旋转通用旋钮 a 选择所需的选项。
如果出现弹出式菜单,请再次按下按钮选择所需的选项。
3. 按某个侧面bezel 按钮选择侧面bezel 菜单项。
如果菜单项包含多个选项,可重复按下侧面bezel 按钮可看到全部选项。
如果出现弹出式菜单,旋转通用旋钮 a 选择所需的选项。
4. 要清除侧面bezel 菜单,请再按下方bezel 按钮或按Menu Off。
5. 某些菜单选项需要设置数字值才能完成设置。
使用上方或下方通用旋钮a 和 b 来调整数值。
6. 按下“精细”以关闭或打开进行细微调整的功能。
使用菜单按钮使用菜单按钮执行示波器中的许多功能。
1. 测量。
按该按钮对波形执行自动测量或配置光标。
2. 搜索。
按该按钮在捕获数据中搜索用户定义的事件/标准。
3. 测试。
按此按钮可以激活高级的或专门应用的测试功能。
4. 采集。
按此按钮可以设置采集模式并调整记录长度。
5. 自动设置。
按此按钮可以对示波器设置执行自动设置。
6. “触发”菜单。
按此按钮可以指定触发设置。
7. Utility。
按此按钮可以激活系统辅助功能,如选择语言或设置日期/时间。
8. Save/Recall(保存/调出)菜单。
按下可保存和调出内部存储器或USB 闪存驱动器内的设置、波形和屏幕图像。
9. 通道1、2、3 或4菜单。
按下即可以设置输入波形的垂直参数,并在显示器上显示或删除相应的波形。
10.B1 或B2。
如果有对应的模块应用密钥,则按下即可定义和显示串行总线。
DPO2AUTO 模块支持CAN和LIN 总线。
DPO2EMBD 模块支持I2C 和SPI 总线。
DPO2COMP 模块支持RS-232、RS-422、RS-485 和UART 总线。
在MSO2000 产品上提供并行总线支持。
RS-485双相24AWG铜电缆产品说明书

UK Regulation Compliance:
UKCA Mark
APAC Compliance:
China RoHS II (GB/T 26572-2011)
Non-Plenum Number: 9842
History
Update and Revision:
Revision Number: 0.539 Revision Date: 11-27-2023
0.6 dB/100ft
Nom. Velocity of Prop.
76%
Max. Current
3.2 Amps per Conductor at 25ºC
Voltage UL Voltage Rating 300 V (CMP)
Mechanical Characteristics
Temperature
PVC - Polyvinyl Chloride 0.015 in (0.38 mm) 0.273 in (6.93 mm)
Overall Cable Diameter (Nominal):
0.273 in (6.93 mm)
Electrical Characteristics
Electricals
Outer Shield
Shield Type
Material
Coverage Drainwire Type
Tape
Bi-Laminate (Alum+Poly) 100%
24 AWG (7x32) TC
Braid
Tinned Copper (TC)
90%
Outer Jacket
Material
Nom. Thickness Nom. Diameter
AT24C02使用手册

7 1 2 3
AT24 C0 2
A)
图9-1 AT24C02引脚及应用电路
B) A)芯片引脚 B)应用电路
4
(1)引脚功能 图9-1 A) 为AT24C02芯片DIP封装引脚图,其中:
SAD、SCL:IC总接口;A2~A0:地址引脚; TEST:测试端,高电平有 效;VDD、VSS:电源端和接地端。 (2)电路设计 图9-1 B)为AT24C02应用电路,AT24C02的SDA和SCL 端分别接 AT89S52虚拟IC总线接口VSDA和VSCL端, TEST端接地,A2、A1、A0 可作为多片AT24C02寻地位,若只用一片AT24C02,A2、A1、A0接地 。
第13章 24c02应用
特性
CAT24WC01 /02/04/08/1 6 1 K/2K/4K/8K/ 6K 位串行E PROM
特性 与 400KHz I 2 C总线兼容 工作电压范围1.8-- 6.0伏
低功耗 CMOS技术 写保护功能 当 WP为高电平时进入写 保护状态 页写缓冲器 自定时擦写周期 1,000,000 /编程 擦除周期 可保存数据 100年 8脚 DIP或 SOIC TSSOP封装 温度范围 -55 +125 商业级 工业级和汽车级
概述
3
4
IC总线EPROM芯片AT24C02
5V
5 .1 k
5 .1 k
P1.1
VSDA 1 2 3 4 A0 A1 A2 VSS VDD TEST SCL SDA 8 7 6 5 VSCL
SDA
V SS V D D
5
8
P1.0
AT89 A0 A1 A2 AT24 C0 2
B) A)芯片引脚 B)应用电路
RS-VPL- -LORA-2 LORA 阀门控制器用户手册说明书

RS-VPL-*-LORA-2 LORA阀门控制器用户手册文档版本:V2.2目录1.产品简介 (3)2.产品选型 (3)3.功能特点 (3)4.技术参数说明 (3)5.外形尺寸说明 (4)6.设备安装 (4)7.使用方法 (5)7.1供电方式 (5)7.2设备配置 (6)7.3设备字典及实时数据选项说明 (8)7.4设备接入平台说明 (8)8.联系方式 (10)9.文档历史 (10)1.产品简介RS-VPL-*-LORA-2是一款低功耗的脉冲阀门控制器。
产品使用LoRa扩频通信技术,传输距离远,穿透性强。
搭配我公司独有的LoRa通信协议,避免了信号传输过程终端节点之间的相互干扰的问题。
供电方式电源、电池二选一,电源供电采用直流宽压供电。
电池供电的采用3.6V对插锂亚电池,可自行拆卸外壳更换电池,每天控制3-4次,可使用3-4年。
外壳防护等级IP65,可满足室外场合使用。
与我公司网络型LORA网关搭配可实现基于平台的手动、自动、定时等操作。
实现智慧联动,精准灌溉。
在工程实施中避免了大工作量的通讯线缆、管线、供电线路的铺设,我公司提供壁挂、立杆、贴片等安装方式,用户也可根据现场实际使用情况,采用不同的安装方式。
2.产品选型RS-公司代号VPL-脉冲输出,电池供电VPL-DY-脉冲输出,电源供电LORA-LORA扩频通信技术2壁挂王字壳3.功能特点⏹与我公司网关搭配可实现2s内控制响应。
⏹采用基于扩频技术的远距离无线传输技术(LoRa),现场施工免布线。
⏹通信距离可达视距3000米。
⏹电池可更换,使用19000mAh对插锂亚电池每天控制3-4次,可使用3-4年。
⏹搭配网关可实现基于我公司平台的远程手动开关,自动,定时等模式的设定。
⏹对自身的电量,信号,及实时数据通过LoRa无线通信方式上传。
⏹可通过手机配置软件“碰一碰NFC配置”进行配置、读取控制器实时数据,阀门开关测试等,方便快捷。
⏹IP65防护等级,可于室外使用。
ACCES ROB-24H 用户手册说明书

MODEL ROB-24(H) USER MANUAL
FILE: MROB24HC3b
Notice
Terms and Conditions
If a unit is suspected of failure, contact ACCES' Customer Service department. Be prepared to give the unit model number, serial number, and a description of the failure symptom(s). We may suggest some simple tests to confirm the failure. We will assign a Return Material Authorization (RMA) number which must appear on the outer label of the return package. All units/components should be properly packed for handling and returned with freight prepaid to the ACCES designated Service Center, and will be returned to the customer's/user's site freight prepaid and invoiced.
Pageiii
阿尔卡特中文说明书

ADP/ADS 系列2干泵使用说明书阿尔卡特高真空技术有限公司作为阿尔卡特集团的一部分,多年来一直为全球客户提供真空泵,检漏仪,真空计以及微加工系统等。
由于产品非常齐全,阿尔卡特高真空技术有限公司在各个行业都成为了非常重要的供应商,这些行业包括:仪器仪表,研发,一般工业和半导体等。
阿尔卡特高真空技术使用Adixen这个新品牌作为公司形象,在真空行业中占据其国际性重要地位。
我们法国公司分别通过了ISO 9001和ISO 14001认证,提供专业的服务和支持,同时Adixen产品具备最高的质量并符合环境标准。
阿尔卡特高真空技术有限公司拥有超过40年的经验,如今已成为一家全球性公司,在全球都拥有他的网络,包括在各地都有非常有经验的全职子公司,经销商以及代理等。
阿尔卡特高真空技术有限公司首先是在30年前在美国的Hingham-MA也建立了阿尔卡特产品中心,如今已经在美国的Fremont (CA)和Tempe (AZ)更增加了2个子公司。
在欧洲,阿尔卡特(法国)总部以及3个子公司,阿尔卡特(德国),阿尔卡特技术(英国)(位于苏格兰)再加上阿尔卡特系统(意大利)共同构成了整个欧洲网络。
在亚洲,我们在1993年成立了阿尔卡特真空技术(日本)并在1995年设立了阿尔卡特真空技术(韩国)。
随后,在2001年成立了阿尔卡特真空技术(台湾),阿尔卡特真空技术(新加坡),并于2004年成立了阿尔卡特高真空技术(上海)- 中国公司。
如今,阿尔卡特在全球各个地区共有超过40个代表处。
因此,无论发生什么情况,阿尔卡特的用户总是能够得到我们的真空技术专家提供的最快捷的支持!尊敬的客户:非常感谢您购买了阿尔卡特的干泵,我们非常荣幸您能够成为我们众多客户中的一员。
该产品得益于阿尔卡特多年以来在“半导体”工艺以及在干泵上的经验。
为了能够确保您使用的干泵拥有最优的性能并使您满意,我们建议您能够在使用该泵之前详细阅读该使用说明书,尤其是关于安装和开机的章节。
欧美电子24路继电器输出板产品说明书

24-Channel Relay Output BoardSpecificationsRelay Type: 24 form C SPDT Nominal Load:0.5 A @120 Vac, 1A @ 24 Vdc Maximum Switching Power: 60 VA, 24 W Maximum Switching Voltage: 120 Vac, 60 Vdc Maximum Switching Current: 1A Life Expectancy: mechanical (2 x 107), electrical (2 x 105)Time Value: operate (6 ms) Ordering Example: OME-DB-24R 16-channel isolated digital input board and OCW-1, OMEGACARE SM extends standard 1-year warranty to a total of 2 years.OME-DB-24R/ OME-DB-24RDOMEGACARE SM extended warranty program is available for models shown on this page. Ask your sales representative for full details when placing an order. OMEGACARE SM covers parts, labor and equivalent loaners.U 24 Form C SPDT RelaysU OPTO-22 Compatible ConnectorU Connects Directly to OME-DIO-24, OME-DIO-48, OME-DIO-144 or Other OPTO-22 Compatible Digital Output BoardU Switch up to 0.5A at 120 Vac; Switch up to 1A at 24 VdcU On Board Relay Driver CircuitsU LED's Indicate Relay StatusU Screw Terminals for easy Field WiringThe OME-DB-24R consists of 24 form C, electromechanical relays for efficient switching of load by programmed control. The contact of each relay can control a 0.5 A /110 V load or 1 A/24 Vdc. The relay is energized by applying a 5 V signal to the appropriate relay channel on the 50-pin OPTO-22 compatible connector or 37-pin D-Sub connector. Twenty-four enunciator LED's, one for each relay, light when their associated relay is activated. To avoid overloading your PC's power supply, this board needs a +12 Vdc or +24 Vdc external power supply.Control Logic: input TTL high (+5 V) current, relay on Power Consumption: +12 V @ 528 mA max; +5 V @ 150 mA max Dimensions: 132 H x 225 mm W (8.1 x 4.5")Operating Temperature: 0 to 60°C (32 to 140°F)Storage Temperature: -20 to 70°C (-4 to 158°F)Humidity: 5 to 90% RH non-condensing Connector: OME-DB-24, one 50-pin header; OME-DB-24RD, one 50-pin header and one 37-pin D-sub connector。
RB-24模式说明书
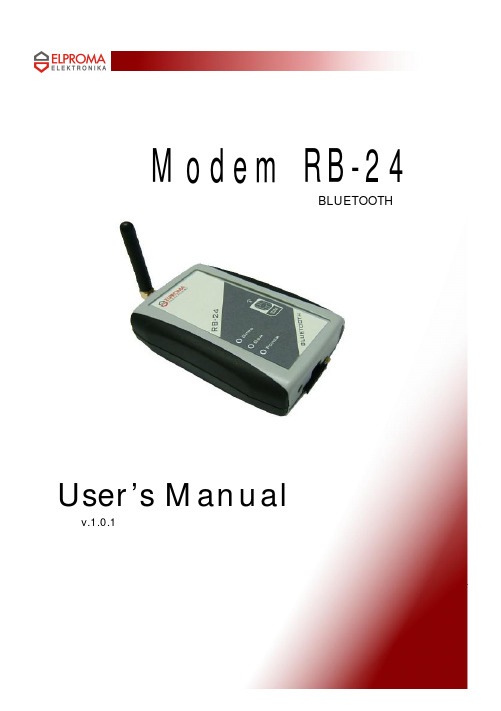
Modem RB-24BLUETOOTH User’s Manualv.1.0.1SWITCH ON SAFELY Do not switch the modem on when wireless devices useis prohibited, or when it may cause interference or danger.ATTENTIONINTERFERENCEAll wireless modems may be susceptible to interference,which could affect performance.SWITCH OFF IN HOSPITALS Follow any restrictions. Switch the modem off nearmedical equipment.QUALIFIED SERVICEOnly qualified personnel may install or repair this product.WATER-RESISTANCEYour modem is not water-resistant. Keep it dry.USE SENSIBLY Use only in the normal position as explained in the product documentation. Don't touch the antenna unnecessarily.WELCOMEThis document will provide you with the instructions how to install and use modem “RB 24” and its software.RB24terminal is powered by Motorola’s G24.It features multiple configurations, including USB, Bluetooth and RS232. RB24 RS232 is a small terminal-modem powered by Motorola G24 embedded engine. RS232 version is a EDGE/GPRS/GSM dedicated for users seeking for easy and mobile internet access. It enables users to use all services provided by GSM operators. Internet/APN Access (EDGE/GPRS), CSD, SMS or FAX just to mention basic capabilities.Additionally it can be used as a mobile phone for voice communication. Perfect when traveling, no need for any external power supply or batteries. Ready PC software for WindowsXP and Linux OS. RS232 version is typical terminal/driver. Small sized easy to install is a perfect solution for any GSM/GPRS telemetry system.1. PACKAGE CONTENTSModem RB-24 is supplied to clients in carton with all1 contents, which are needed for connection to PC and normalwork:1) carton;2) modem RB24 BLUETOOTH;3) “USB A mini USB B” connecting cable;4) external GSM antenna;5) headset6) AC power supply with mini-USB plug output7) CD with User’s Guide and drivers.If any of the components is missing please contact your local distributor.2. T echnical information2.1. Modem features.GSM / GPRS / EDGE / CSD / SMS / FAX modemGSM 850 / 900 / 1800 / 1900 / E-GSMFunctions:EDGE (Mult-slot class 10, max BR downlink 236,8 Kb/s)GPRS (Multi-slot class 10, max BR downlink 85,6 Kb/s) 2FAX (3 group 1 class) 9600bit/sSMS (AT commands ETSI 07.05 & 07.07, PDU & Text)CSD (Max BR 14,4 Kb/s)Bluetooth® 2.0+EDR (up to 3Mbit/s)public device name: RB24default PIN code: 0000class of device (CoD): phone (0x520204)supported profiles:Serial Port Protocol (SPP)Dial-Up Networking (DUN)radio class 2 (range up to 10m)2.2. Electrical and operating specifications.Power supply: 5V DCPower consumption: max 950mASIM Card: 3V DC2.3. Weight and dimensions.Weight100gLength95mmWidth65mmDepth30mm22.4. Panels.A) front panel: headset and mini-USB connectors, SIM-holderB) top panel: 3 LEDs state indicator: POWER ,GSM (data),GPRSC) back panel: antenna SMA connector23. Hardware setupunpack and prepare components from the device boxprepare a SIM cardpress a yellow button of the SIM-holder on the front panelextract the trayput the SIM cardinsert the set3screw the antenna to the SMA connectoron the backpanellif it is necessary plug-in the USB connectorto your computer (a host)plug-in the mini-USB connector ofUSB cable or AC adaptor to thesocket 34. Bluetooth instalationThe device has to own Bluetooth radioBluetooth stack which supports SPP and/orDUN Bluetooth profilesproper distance between the devices (range upto about 10 meters, it depends on environment parameters for radio frequencies, the devices class of power and sensitivity)To connect with the RB24 BLUETOOTH your device (PC / laptop, palmtop, etc.) you need the following things:1. Windows-like OS • native Microsoft ® Windows XP ®SP2 (Service Pack 2)– Generic Bluetooth Radio driver • native Microsoft ® Windows Vista®• IVT BlueSoleil ®()• Widcomm ®(by Broadcom, )2. Unix-like OS (Linux)• BlueZ ()• Affix (developed by Nokia ®, )• OpenBT (/projects/openbt)As Bluetooth radio for computer you can use a cheap USB Bluetooth Dongle. Most of them is based on CSR ® BlueCore ®chip with HCI (Host Command Interface) support . The stack and drivers should be attached to the dongle.If you have not got a Bluetooth stack it is even possible usageone of native stacks for Operating Systems like Microsoft ®Windows or Linux / BSD . Below it is listed several well knownBluetooth stacks for PC: .4General steps you have to do in order to make the firstconnection with the RB24:• call inquiry – scan Bluetooth enabled devices around• select a device named RB24 (phone class)• pair with RB24 for keys exchange, necessary to enter the PIN code (0000)• for some stacks check supported services (SDP) and select SPP or DUN profile• the stack should make a virtual serial port for SPP(UUID: 0x1101, RFCOMM, channel 1)• for DUN (UUID: 0x1103, RFCOMM) a stack can displayInternet connection dialog (Dial-Up)• now you can open the virtual serial port (eg. COM37,/dev/rfcomm1) in a terminal (HyperTerminal, minicom,tip, etc.) or other software for the modemGeneral steps you have to do every next time:4• for some stacks define RFCOMM channel (eg. BlueZ)• open the virtual serial port...5. LimitationsNOTEOnly the first client (SPP or DUN) will able to transfer data from/to modem. If you want to change the active profile you need to disconnect the previous connection .IMPORTANTThe RB24 Bluetooth version requires not to use AT+IPR=... command. If you change the serial port baud rate a Bluetooth connection may result in data fault. In order to undo a mistake you have to plug the device to computer by the USB cable. Afterwardsyou should open a serial port terminal (USB modem represented bya virtual COM port) and send “AT+IPR=230400” command. The230 400 baud rate is an internal speed of data transfer betweenthe GSM modem and the Bluetooth part .Another possibility is to run the GPRS Control software forRB24 connected to the USB, close the connection, un-plug andplug-in the modem to mini-USB again .56. Bluetooth connection guideWindows XP SP2Click double on the Bluetooth iconPress the “Add” button6Select the RB24 and press the “Next” buttonTick the checkbox and press the “Next” button6You should get COM ports number, interesting foryou is the outgoing port COM, press the Finish buttonSelect “Use access code from documentation “,enter PIN code and press the “Next”button6The final effect: paired the devicesNow you can open eg. HyperTerminal with virtual serial port COM228 (the outgoing port) – next time youwill need only this stepou should get COM ports6 number, interesting for you is the outgoing port COM,press the Finish button.Windows XP, WIDCOMM stackClick double on the WIDCOMM Bluetooth iconnalSelect “View devices in range”6Wait until inquiry finishes and click double on “RB246Wait until inquiry finishes and click double on “RB24You should notice something like belowWait until inquiry finishes and click double on “RB246Now you can use the virtual port (eg. COM11) where you need(eg.the HyperTerminal).The final result for the SPP connection6If you want to connect to Internet via PPP(Point-to-Point Protocol) click double.on “Dial-Up Networking” serviceYou should notice something like below6The standard dialog for the connection will be displayed. For GPRS/EDGE connection enter one of the following numbers: . *99# (default APN) . *99***1# (APN1) . *99***2# (APN2) . *99***3# (APN3) .Enter the PIN code for the devices pairing if it isnecessary6Windows XP, IVT BlueSoleil stack Click double on the BlueSoleil Bluetooth iconnClick on a star like the Sun in the center of theBlueSoleil windows.6Please wait for the inquiryClick double on the new mobile phone device (RB24)6Now the RB24 is paired with the BlueSoleil stackand its services are discovered.Enter the PIN code and press the “OK” button 6If you want to connect to Internet via PPP(Point-to-Point Protocol) click double.on “Dial-Up Networking” serviceThe result: is the virtual serial port and modem(eg. COM251), click the “Yes” button6The standard dialog for the connection will be displayed. For GPRS/EDGE connection enter one ofthe following numbers:.*99# (default APN).*99***1# (APN1) .*99***2# (APN2) .*99***3# (APN3) .6The result: is the virtual serial port (eg. COM444),click the “Yes” buttonIf you want to create a virtual COM port click on“Serial Port”service 6On the successful finish you should see somethingbelowlike6• Ciheck your HCI Bluetooth Dongle$hcitool dev Devices:hci0 00:13:EF:F0:C3:54• Find the RB24$hcitool scan name Scanning ...00:A0:96:07:41:2A Bluetooth Display00:07:80:82:F5:75 RB24• Discover services$sdptool search 0x1002Class 0x1002Inquiring ...Searching for 0x1002 on 00:07:80:82:F5:75 ...Service Name: Bluetooth Serial Port Service RecHandle: 0x10000Service Class ID List:"Error: This is UUID-128" (0x00001101-0000-1000-8000-00805f9b34fb)Protocol Descriptor List:"L2CAP" (0x0100)"RFCOMM" (0x0003)Channel: 1Language Base Attr List:code_ISO639: 0x656eencoding: 0x6abase_offset: 0x100Service Name: Dial-Up NetworkingService RecHandle: 0x10001Service Class ID List:"Error: This is UUID-128" (0x00001103-0000-1000-8000-00805f9b34fb)Protocol Descriptor List:"L2CAP" (0x0100)"RFCOMM" (0x0003)Channel: 2Language Base Attr List:code_ISO639: 0x656eencoding: 0x6abase_offset: 0x100Searching for 0x1002 on 00:A0:96:07:41:2A ...• Pair the devices: PIN checking and keys exchanging (needed only the first time)$sudo hcitool cc 00:07:80:82:F5:75$hcitool con Linux, BlueZ stack6Connections:< ACL 00:07:80:82:F5:75 handle 42 state 1 lm MASTER• SPP connection$rfcomm connect /dev/rfcomm0 00:07:80:82:F5:75 1Connected /dev/rfcomm0 to 00:07:80:82:F5:75 on channel 1Press CTRL-C for hangup• open your terminal, for example$gtkterm -p /dev/rfcomm0• DUN connection (you can also use SPP instead of DUN, the result will be the same)$rfcomm connect /dev/rfcomm1 00:07:80:82:F5:75 2Connected /dev/rfcomm1 to 00:07:80:82:F5:75 on channel 2Press CTRL-C for hangup6。
NAMUR隔离放大器24V DC 1-或2-通道应用说明书

1- or 2-channel NAMUR isolating amplifier 24 V DC with relay signal outputApplication•Isolating amplifier for the transmission of binary switch signals•Input for proximity sensors according to NAMUR (EN60947-5-6) and open contacts or contacts with resistive coupling elements •Galvanic 3-way isolationSuitable for safety-oriented applications up to SIL 2 in accordance with IEC61508•Optionally with resistive coupling element for line monitoring of mechanical switching contacts•Monitoring of input circuits for line faults such as breakage and short-circuit (LFD), disengageableGroup error message via DIN rail bus connector at power and error message module•Output-side relay contacts as signal output, direction of action (operating or quiescent current behavior) can be selected via DIP switches •For ambient temperatures –40 to 60 °C (–40 to 140 °F)Your benefits•Compact housing width: 12.5 mm (0.49 in)•Installation in Ex zone 2 permitted in the option with Ex approval•Simple and quick wiring with plug-in terminals, optional power supply and error message via DIN rail bus connectorProducts Solutions ServicesTechnical Information RLN22NAMUR isolating amplifierTI01560K/09/EN/02.21715457402021-10-19RLN222Endress+HauserTable of contentsFunction and system design (3)Product description ............................3Dependability .. (3)Input (3)Version ....................................3Input data . (3)Output (3)Relay output data .............................3Signal on alarm ...............................4Ex connection data ............................4Galvanic isolation .............................4Power supply (4)Terminal assignment ...........................4Connecting the supply voltage .....................4Performance characteristics ......................4Terminals ..................................5Performance characteristics (5)Response time ...............................5Mounting (5)Mounting location .............................5Installing a DIN rail device .. (5)Environment (5)Important ambient conditions .....................5Shock and vibration resistance .....................5Electromagnetic compatibility (EMC). (5)Mechanical construction (6)Design, dimensions ............................6Weight ....................................6Color ......................................6Materials ...................................6Display and operating elements (7)Local operation ...............................7Truth table, 1-channel ..........................8Truth table, 2-channel .. (8)Ordering information ........................8Accessories .. (9)Device-specific accessories .......................9Service-specific accessories .. (9)Certificates and approvals ....................9CE mark ...................................9Functional safety .. (10)Documentation (10)Brief Operating Instructions (KA)..................10Operating Instructions (BA).....................10Safety Instructions (XA)........................10Supplementary device-dependent documentation . (10)RLN22Endress+Hauser 3Function and system designProduct descriptionProduct designNAMUR isolating amplifier 1-channel•With the "1-channel changeover" option, the 1-channel NAMUR isolating amplifier is designed for the operation of proximity switches (as per EN 60947-5-6 (NAMUR)) and open and mechanical contacts with resistive coupling elements. A relay (changeover) is available as the signal output.•The device is optionally available with Ex approvals for the intrinsically safe operation of proximity switches installed in the hazardous area. Separate Ex documentation (XA) is supplied with these devices. Compliance with the installation instructions and connection data in this documentation is mandatory!•A resistive coupling element (1 kΩ / 10 kΩ) is available as an optional accessory and can be used to monitor line faults of sensors with mechanical contacts. The resistive coupling element isinstalled onsite directly at the contact to be monitored or in the sensor connection compartment.NAMUR isolating amplifier 2-channelWith the "2-channel, NO contact" option, the device has a second channel, which is galvanically isolated from channel 1, while maintaining the same width. A relay (NO contact) is available as the signal output. Otherwise, the function corresponds to the 1-channel device.DependabilityWe only provide a warranty if the device is installed and used as described in the Operating Instructions.InputVersionThe following versions are available:•1-channel •2-channelInput data(floating switch contacts with resistive coupling elements to connect NAMUR proximity switches (IEC/EN 60947-5-6))Switch pointsBlocking: < 1.2 mA Conducting: > 2.1 mALine fault detection (response range)Open circuit:0.05 mA < I IN < 0.35 mA Short-circuit:100 Ω < R sensor < 360 ΩShort-circuit current ~ 8 mA Open-circuit voltage~ 8 V DCSwitching hysteresis< 0.2 mAOutputRelay output dataRelay output dataContact design1-channel: 1 changeover 2-channel: 1 NO contact per channelMechanical operating life107 switching cyclesSwitching voltage,maximum switching current250 V DC (2 A) / 120 V DC (0.2 A) / 30 V DC (2 A)Recommended minimum load5 V / 10 mAMaximum switching capacity 500 VASwitching frequency (no load)≤ 20 HzContact materialAgSnO2, hard gold platedDirection of actionOperating current or closed circuit currentRLN224Endress+HauserSignal on alarmOutput behavior in an alarm conditionIf line fault detection is switched on and the line to the sensor is disconnected or short-circuits, the relay de-energizes in such a way that the output is set to the safe, non-conducting state.Line break in input (response range)0.05 mA < I IN < 0.35 mA Monitored range for line breakI IN < 0.05 mALine short circuit in input (response range)100 Ω < R sensor < 360 ΩMonitored range for short circuitR < 100 ΩEx connection data See associated XA Safety InstructionsGalvanic isolationInput / outputPeak value as per EN 60079-11375 VInput / power supply, DIN rail bus connectorPeak value as per EN 60079-11375 VPower supplyTerminal assignmentQuick wiring guide1Terminal assignment of RLN22: 1-channel version (left), 2-channel version (right)Connecting the supply voltagePower can be supplied via terminals 1.1 and 1.2 or via the DIN rail bus connector.Performance characteristicsPower supplySupply voltage range 19.2 to 30 V DC(24 V DC (-20% / +25%))Current consumption at 24 V DC1-channel: ≤ 21 mA 2-channel: ≤ 35 mA Supply current to the DIN rail bus connectorMax. 400 mAPower consumption at 24 V DC1-channel: < 0.65 W 2-channel: < 0.8 W Power loss at 24 V DC1-channel: < 0.65 W 2-channel: < 1 WRLN22Endress+Hauser 5Performance characteristicsResponse timeFollowing a change of state at the input, the output adopts the safe state in ≤ 40 ms.MountingMounting locationThe device is designed for installation on 35 mm (1.38 in) DIN rails in accordance with IEC 60715(TH35).The device's housing provides basic insulation from neighboring devices for 300 Veff. If several devices are installed side by side, this must be taken into consideration and additional insulation must be provided if necessary. If the adjacent device also offers basic insulation, no additional insulation is required.NOTICE‣When using in hazardous areas, the limit values of the certificates and approvals must beobserved.Installing a DIN rail deviceThe device can be installed in any position (horizontal or vertical) on the DIN rail without lateral clearance from neighboring devices. No tools are required for installation. The use of end brackets (type "WEW 35/1" or equivalent) on the DIN rail is recommended to fix the device.EnvironmentImportant ambient conditionsAmbient temperature range–40 to 60 °C (–40 to 140 °F)Storage temperature –40 to 80 °C (–40 to 176 °F)Degree of protection IP 20Overvoltage category IIPollution degree 2Humidity10 to 95 % No condensationAltitude≤ 2 000 m (6 562 ft)Shock and vibration resistance Vibration resistance as per DNVGL-CG-0339 : 2015 and DIN EN 60068-2-27DIN rail device: 2 to 100 Hz at 0.7g (general vibration stress)Shock resistance as per KTA 3505 (section 5.8.4 Shock test)Electromagnetic compatibility (EMC)Interference immunity as per EN 61000-6-2Interference emission as per EN 61000-6-4RLN22Mechanical constructionDesign, dimensions Dimensions in mm (in)Terminal housing for mounting on DIN railWeight Device with terminals (values rounded up):1-channel: approx. 110 g (3.88 oz); 2-channel: approx. 120 g (4.23 oz)Color Light grayMaterials All the materials used are RoHS-compliant.Housing: polycarbonate (PC); flammability rating according to UL94: V-06Endress+HauserRLN22Endress+Hauser 7Display and operating elements2Display and operating elements1Plug-in screw or push-in terminal 2Green LED "On", power supply3Red LED "LF1", line fault of sensor cable 14Red LED "LF2", line fault of sensor cable 2 (option)5Yellow LED "OUT1", status relay 16Yellow LED "OUT2", status relay 2 (option)7DIP switches 1 to 48DIN rail clip for DIN rail mounting 9DIN rail bus connector (optional)Local operation Hardware settings / configurationAny device settings using the DIP switch must be made when the device is de-energized.Direction of actionAt the device, the direction of action (operating or closed circuit current behavior) can be selected and line fault detection can be enabled or disabled via DIP switches.DIP switch 1 = channel 1; DIP switch 3 = channel 2 (optional)All DIP switches are set to the "I" position when the device is delivered from the factory:•I = normal phase (operating current behavior)•II = inverse phase (closed circuit current behavior)Line fault detectionDIP switch 2 = channel 1; DIP switch 4 = channel 2 (optional)I = line fault detection switched off - not permitted for safety-oriented applications!II = line fault detection switched onIf a line fault occurs, the relay is de-energized and the red LED "LF" flashes (NE 44).An error message is transmitted to the power and error message module RNF22 via the DIN rail bus connector and forwarded as a group error message.NOTICEError detection malfunctions‣the "Quick wiring guide" and "Accessories" sections of the Operating Instructions)RLN228Endress+HauserTruth table, 1-channelTruth table, 2-channelOrdering informationDetailed ordering information is available from the nearest sales organization or in the Product Configurator under :1.Select the product using the filters and search field.2.Open the product page.RLN22Endress+Hauser 9The Configurationbutton opens the Product Configurator.Product Configurator - the tool for individual product configuration •Up-to-the-minute configuration data•Depending on the device: Direct input of measuring point-specific information such as measuring range or operating language •Automatic verification of exclusion criteria•Automatic creation of the order code and its breakdown in PDF or Excel output format •Ability to order directly in the Endress+Hauser Online ShopAccessoriesVarious accessories, which can be ordered with the device or subsequently from Endress+Hauser, are available for the device. Detailed information on the order code in question is available from your local Endress+Hauser sales center or on the product page of the Endress+Hauser website: .Device-specific accessoriesService-specific accessoriesCertificates and approvalsFor the approvals available, see the Configurator on the specific product page: → (search for device name)CE markThe product meets the requirements of the harmonized European standards. As such, it complies with the legal specifications of the EC directives. The manufacturer confirms successful testing of the product by affixing to it the CE-mark.RLN2210Endress+HauserFunctional safetyA SIL version of the device is optionally available. It can be used in safety equipment in accordancewith IEC 61508 up to SIL 2 .Please refer to Safety Manual FY01035K for the use of the device in safety instrumentedsystems according to IEC 61508.Protection against modifications:As it is not possible to disengage the operating elements (DIP switches), a lockable control cabinet is required for use in SIL applications. The cabinet must be locked by key. A normal electrical cabinet key does not suffice for this purpose.DocumentationThe following document types are available in the Downloads section of the Endress+Hauser website (/downloads):For an overview of the scope of the associated Technical Documentation, refer to the following:•W@M Device Viewer (/deviceviewer ): Enter the serial number from the nameplate•Endress+Hauser Operations App : Enter the serial number from the nameplate or scan the matrix code on the nameplateBrief Operating Instructions (KA)Guide that takes you quickly to the 1st measured valueThe Brief Operating Instructions contain all the essential information from incoming acceptance to initial commissioning.Operating Instructions (BA)Your reference guideThese Operating Instructions contain all the information that is required in various phases of the life cycle of the device: from product identification, incoming acceptance and storage, to mounting,connection, operation and commissioning through to troubleshooting, maintenance and disposal.Safety Instructions (XA)Depending on the approval, the following Safety Instructions (XA) are supplied with the device. Theyare an integral part of the Operating Instructions.The nameplate indicates the Safety Instructions (XA) that are relevant to the device.Supplementary device-dependent documentationAdditional documents are supplied depending on the device version ordered: Always comply strictly with the instructions in the supplementary documentation. The supplementary documentation is an integral part of the device documentation.*71545740*71545740。
RS24ADPIO-2使用说明.

RS24ADPIO-2使用说明目录一、安装尺寸二、单片机接口J3线的定义三、EPP操作时序四、口地址定义五、数据的读入六、数据格式七、信号及电源J1定义八、标定九、效果十、编程注意十一、DEMO软件的使用一、 安装尺寸二、单片机接口J3线的定义Pin号名字I/O 并口Pin号功能I 1 读写标识,“1”读;“0“写,1 nWriteIO 2 双向数据线D0位2 PCD03 PCD1IO 3 双向数据线D1位4 PCD2IO 4 双向数据线D2位5 PCD3IO 5 双向数据线D3位IO 6 双向数据线D4位6 PCD47 PCD5IO 7 双向数据线D5位IO 8 双向数据线D6位8 PCD6IO 9 双向数据线D7位9 PCD710 TRIP I 总外触发输入,上升沿触发11 TRIPsI 单片机外触发输入,上升沿触发12 GND12 GND GNDi 备用13 NULL214 nDstrbI 14 数据操作线,低有效15 VCC VCC 5.0V16 nwait O 11 (MCU不要联接)(EPP调试的输出)17 nAstrbI 17 地址操作线,低有效18 NULL1i备用19 vcc vcc 5.0V18TO25 GND20 GND GND三、 EPP操作时序写地址:读地址和写数据读数据四、口地址定义地址值数据值读或写功能0x00 0 写停止数据采集0x00 1 写等待触发条件,触发条件满足后,开始数据采集,0x01 123 写用外触发条件做触发源TRIP1(屏蔽外部触发源TRIP)用外触发条件做触发源TRIP(屏蔽外部触发源TRIP1)用两个外触发条件"或"做触发源(三个都是上升沿触发)0x01 4 写使能软件强行触发(屏蔽外部触发源)0x01 8+4 写强制软件触发操作0x02 0 写关闭高通滤波,可以通过直流。
0x02 1 写使能高通滤波,1HZ信号衰减30dB。
步进电机驱动器(24VDC伺服)说明书
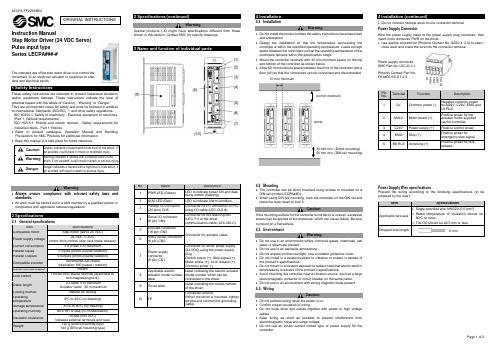
Instruction ManualStep Motor Driver (24 VDC Servo) Pulse input type Series LECPA###-#The intended use of the step motor driver is to control the movement of an electrical actuator in response to step data and electrical inputs.These safety instructions are intended to prevent hazardous situations and/or equipment damage. These instructions indicate the level of potential hazard with the labels of “Caution,” “Warning” or “Danger.”They are all important notes for safety and must be followed in addition to International Standards (ISO/IEC) *1), and other safety regulations.IEC 60204-1: Safety of machinery - Electrical equipment of machines. (Part 1: General requirements)ISO 10218-1: Robots and robotic devices - Safety requirements for industrial robots - Part 1: Robots.• Refer to product catalogue, Operation Manual and Handling Precautions for SMC Products for additional information. • Keep this manual in a safe place for future reference.CautionCaution indicates a hazard with a low level of risk which, if not avoided, could result in minor or moderate injury.WarningWarning indicates a hazard with a medium level of riskwhich, if not avoided, could result in death or serious injury.DangerDanger indicates a hazard with a high level of risk which, ifnot avoided, will result in death or serious injury.Warning• Always ensure compliance with relevant safety laws and standards.• All work must be carried out in a safe manner by a qualified person in compliance with applicable national regulations.2.1General specificationsItemSpecificationsCompatible motorStep motor (servo 24 VDC)Power supply voltage24 VDC +/-10%(motor drive control, stop, lock brake release).Current consumption 3 A (Peak 5 A) maximum Parallel Inputs 5 inputs (photo-coupler isolation) Parallel Outputs 9 outputs (photo-coupler isolation)Compatible encoderIncremental A/B phase(resolution: 800 pulses / rotation)Serial communication RS485Lock controlForced lock release terminal (applicable tonon-magnetizing lock). Cable lengthIO cable: 5 m maximumActuator cable: 20 m maximumCooling method Natural air-cooling Operatingtemperature0o C to 40o C (no freezing)Storage temperature -10o C to 60o C (no freezing) Operating humidity 90% RH or less (no condensation)Insulation resistance50 MΩ (500 VDC)between external terminals and caseWeight120 g (Direct mounting type)140 g (DIN rail mounting type)WarningSpecial products (-X) might have specifications different from those shown in this section. Contact SMC for specific drawings.4 Installation4.1 InstallationWarning• Do not install the product unless the safety instructions have been read and understood.• Design the installation so that the temperature surrounding the controller is within the specified operating temperature. Leave enough space between the controllers so that the operating temperature of the controllers remains within the specification range.• Mount the controller vertically with 30 mm minimum space on the top and bottom of the controller as shown below.• Allow 60 mm minimum space between the front of the controller and a door (lid) so that the connectors can be connected and disconnected.4.2 Mounting• The controller can be direct mounted using screws or mounted on a DIN rail (model LECPA##D).• When using DIN rail mounting, hook the controller on the DIN rail and press the lever down to lock it.CautionIf the mounting surface for the controller is not flat or is uneven, excessive stress may be applied to the enclosure, which can cause failure. Be sure to mount on a flat surface. 4.3 EnvironmentWarning• Do not use in an environment where corrosive gases, chemicals, salt water or steam are present.• Do not use in an explosive atmosphere.• Do not expose to direct sunlight. Use a suitable protective cover.• Do not install in a location subject to vibration or impact in excess of the product’s specifications.• Do not mount in a location exposed to radiant heat that would result in temperatures in excess of the product’s specifications.• Avoid mounting the controller near a vibration source, such as a large electromagnetic contactor or circuit breaker on the same panel. • Do not use in an environment with strong magnetic fields present. 4.4 WiringCaution• Do not perform wiring while the power is on. • Confirm proper insulation of wiring.• Do not route wires and cables together with power or high voltage cables.• Keep wiring as short as possible to prevent interference from electromagnetic noise and surge voltage.• Do not use an inrush current limited type of power supply for the controller.• Do not connect multiple wires to one connector terminal.Power Supply ConnectorWire the power supply cable to the power supply plug connector, then insert it into connector PWR on the driver.• Use special screwdriver (Phoenix Contact No. SZS0.4×2.0) to open / close lever and insert the wire into the connector terminal.Power Supply Wire specificationsPrepare the wiring according to the following specifications (to be prepared by the user).ORIGINAL INSTRUCTIONSPower supply connector. SMC Part No. LEC-D-1-1. Phoenix Contact Part No: FK-MC0.5/5-ST-2.510 mm minimum Driver30 mm min. (Direct mounting) 50 mm min. (DIN rail mounting)30 mm minimumParallel I/O Connector• When connecting the parallel I/O connector to a PLC use an SMC parallel I/O cable (LEC-CL5-#).• There are 2 types of parallel I/O with this controller: NPN type and PNP type. Check the polarity required before use.The parallel I/O wiring should be prepared according to the polarity.For further details of the Parallel I/O wiring refer to the Operation Manual on the SMC website (URL: https:// ).4.5 Ground connection• Place a ground cable with crimped terminal under one of the M4 mounting screws with a shakeproof washer and tighten the screw.CautionThe M4 screw, cable with crimped terminal and shakeproof washer must be prepared by the user.The controller must be connected to Ground to reduce noise. If higher noise resistance is required, ground the 0 V (signal ground). When grounding the 0 V, avoid flowing noise from ground to 0 V.• A dedicated Ground connection must be used. Grounding should be to a D-class ground (ground resistance of 100 Ω maximum).• The cross-sectional area of the ground cable shall be 2 mm 2 minimum. • The Grounding point should be as near as possible to the controller. Keep the grounding cable as short as possible.In order to move the electric actuator to a specific position, it is necessary to set up the patterns of operation with a PC using the controller setting software or by using a teaching box. This set up data will be recorded in the memory of the controller.Step data describes the data that sets items of operation (such as positioning width) excluding speed, position, acceleration, and deceleration, which are determined by the pulse-signal input. Step data will become effective as soon as it is recorded into the driver.Refer to the Operation Manual on the SMC website (URL: https:// ) for further setting details.Refer to the table below for details of the LED status.LEDDescriptionPWROFFPower is not supplied Green LED is ON Power is suppliedGreen LED is flashingEEPROM memory writing ALM OFFNormal operationRed LED is ONController Alarm generated7 How to OrderRefer to the catalogue on the SMC website (URL: https:// ) for the How to Order information.8 Outline Dimensions (mm)Refer to the drawings / operation manual on the SMC website (URL: https:// ) for outline dimensions.9 Maintenance9.1 General MaintenanceCaution• Not following proper maintenance procedures could cause the product to malfunction and lead to equipment damage.• Before performing maintenance, turn off the power supply. Check the voltage with a tester 5 minutes after the power supply is turned OFF. • If any electrical connections are disturbed during maintenance, ensure they are reconnected correctly and safety checks are carried out as required to ensure continued compliance with applicable national regulations.• Do not make any modification to the product.• Do not disassemble the product, unless required by installation or maintenance instructions.Caution• Maintenance should be performed according to the procedure indicated in the Operation Manual.• When equipment is serviced, first confirm that measures are in place to prevent dropping of work pieces and run-away of equipment, etc, then cut the power supply to the system. When machinery is restarted, check that operation is normal with actuators in the correct position.Warning• Perform maintenance checks periodically.• Confirm wiring and screws are not loose. Loose screws or wires may cause unexpected malfunction.• Conduct an appropriate functional inspection and test after completing maintenance. In case of any abnormalities (if the actuator does not move, etc.), stop the operation of the system. Otherwise, an unexpected malfunction may occur and it will become impossible to ensure safety. Operate an emergency stop instruction to confirm safety. • Do not put anything conductive or flammable inside of the controller. • Ensure sufficient space around the controller for maintenance.10 Limitations of Use10.1 Limited warranty and Disclaimer/Compliance Requirements Refer to Handling Precautions for SMC Products.11 Product disposalThis product shall not be disposed of as municipal waste. Check your local regulations and guidelines to dispose of this product correctly, in order to reduce the impact on human health and the environment.12 ContactsRefer to or www.smc.eu for your local distributor / importer.URL: https:// (Global) https://www.smc.eu (Europe) SMC Corporation, 4-14-1, Sotokanda, Chiyoda-ku, Tokyo 101-0021, Japan Specifications are subject to change without prior notice from the manufacturer. © 2021 SMC Corporation All Rights Reserved. Template DKP50047-F-085MPin No. Insulation Colour Dot mark Dot colour Category Signal 1 Light brown ● Black 24 V COM+ 2 Light brown ● Red 0 V COM- 3 Yellow ● Black Pulse signal NP+ 4 Yellow ● Red Pulse signal NP- 5 Light green ● Black Pulse signal PP+ 6 Light green ● Red Pulse signal PP- 7 Grey ● Black Input SETUP 8 Grey ● Red Input RESET 9 White ● Black Input SVON 10 White ● Red Input CLR 11 Light brown ●● Black Input TL 12 Light brown ●● Red Output TLOUT 13 Yellow ●● Black Output WAREA 14 Yellow ●● Red Output BUSY 15 Light green ●● Black Output SETON 16 Light green ●● Red Output INP 17 Grey ●● Black Output SVRE 18 Grey ●● Red Output ESTOP19White ●● Black Output ALARM 20White ●● Red Output AREA。
ProSafe 24 端口 ги格兹比交换机安装指南说明书
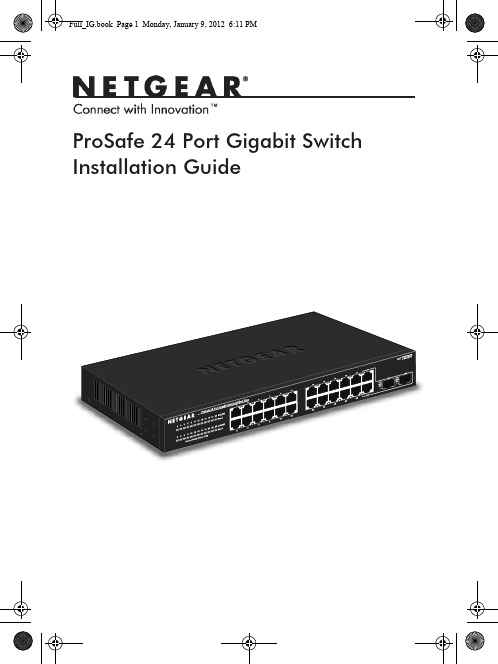
ProSafe 24 Port Gigabit Switch Installation Guide2© 2011 NETGEAR, Inc. All rights reserved.No part of this publication may be reproduced, transmitted, transcribed, stored in a retrieval system, or translated into any language in any form or by any means without the written permission of NETGEAR, Inc.Technical SupportThank you for choosing NETGEAR. To register your product, get the latest product updates, or get support online, visit us at . Phone (US only): 1-888-NETGEARPhone (Other Countries):Check the list of phone numbers at:/app/answers/detail/a_id/984TrademarksNETGEAR, the NETGEAR logo, ReadyNAS, ProSafe, Smart Wizard, Auto NETGEAR, the NETGEAR logo, and Connect with Innovation are trademarks and/or registered trademarks of NETGEAR, Inc. and/or its subsidiaries in the United States and/or other countries. Information is subject to change without notice. Other brand and product names are registered trademarks or trademarks of their respective holders. © 2011 NETGEAR, Inc. All rights reserved.Statement of ConditionsIn the interest of improving internal design, operational function, and/or reliability, NETGEAR reserves the right to make changes to the products described in this document without notice. NETGEAR does not assume any liability that may occur due to the use or application of the product(s) or circuit layout(s) described herein.3Package ContentsVerify that all items are in the box. The package includes:•ProSafe 24-port Gigabit Switch with 2 Gigabit SFP Combo Ports JGS524F V1•Power cord with localized plug •Adhesive feet •Rack-mount brackets and hardware •Installation Guide (this document)Front Viewcombo portsThe switch supports 10 Mbps, 100 Mbps, and 1000 Mbpsconnections. Using Gigabit Ethernet (1000 Mbps), the switch sends files across the network at speeds up of to 2000 Mbps due to the full-duplex nature of Gigabit Ethernet connections. You can eitherconnect 24 Ethernet copper cables or 22 copper cables with 2 optical fibers. The switch supports straight-through or crossover Ethernet cables on 24 ports. Each of these ports configures itself based on the cable that you plug into it. You can use the switch to connect Ethernet devicessuch as computers, file servers, printers, routers, switches, or hubs.4Select a LocationDecide where you want to place the switch. Find a flat horizontal surface or a 19-inch rack.Make sure that the location is:•Not in direct sunlight or near a heater or heating vent.•Not cluttered or crowded. There should be at least 2 inches (5 cm) of clear space on all sides of the switch.•Well ventilated, especially if it is in a closet.Install the Switch1. For each device that you want to connect to the switch, provide an enhanced Category 5 (Cat 5e) Ethernet cable with RJ-45 connections. Each Ethernet cable has to be less than 328 feet (100 meters) long.2. Install the switch on a flat surface or in a standard 19-inch rack.•Flat surface . The switch comes with four self-adhesivefootpads. Stick one footpad on each of the four concavespaces on the bottom of the switch. The footpads cushion the switch against shock and vibrations.•Rack mounting . Follow the instructions in the 19-Inch RackMounting section.Verify Cable ConnectionsBefore you apply power, perform the following checks:1. Inspect the equipment thoroughly.2. Verify that all cables are installed correctly.3. Check cable routing to ensure that cables are not damaged and will not create a safety hazard.4. Be sure that all equipment is mounted securely.519-Inch Rack MountingUse the rack-mount kit supplied with your switch.1. Use the Phillips head screws to fasten the mounting brackets to the sides of the switch. Tighten the screws with a No. 1 Phillips screwdriver.2. Align the bracket and rack holes. Use two pan-head screws with nylon washers to fasten each bracket to the rack. Tighten the screws with a No. 2 Phillips screwdriver to secure the switch in the rack.6Optical Modules (Sold Separately)You can use compatible optical modules such as the NETGEAR ProSafe GBIC SFP Modules AGM731F and AGM732F with your switch. These modules provide full-duplex 1000 Mbps Ethernetoperation in each direction for NETGEAR switches.The switch automatically detects the module, so you can simply plug it into an available module slot. Plugging in an SFP module disables the associated RJ-45 port. The modules can be inserted or removedwhile the switch is operational.Class 1 laser product.Class 1 LED product.Because invisible laser radiation may be emitted from theaperture of the port when no fiber cable is connected, avoidexposure to laser radiation, and do not stare into openapertures..7Install an Optical ModuleInsert the module firmly into the slot that supports the SFP interface.Remove an Optical ModuleRelease the module latch by pulling down the handle bar across the8TroubleshootingYou can use the LEDs to troubleshoot hardware problems.Power LED Is OffThe switch has no power.•Make sure that the power cord is securely connected to the switch.•Make sure that the power cord is connected to a functioningpower outlet. If it is connected to a power strip, make sure that the power strip is turned on. If the socket is controlled by a light switch, make sure the switch is in the on position.Port LEDsIf a port LED is off for a connected device or the LED stays on continuousl,y there is a hardware connection problem.•Make sure that the cable connectors are securely plugged in to the switch and the device.•Make sure that the connected device is turned on.•If the Ethernet cable is connected to a network interface card orother Ethernet adapter, make sure that the card or adapter is installed correctly and is working.•Make sure that the cable is less than 328 feet (100 meters) long .91011Technical SupportThank you for selecting NETGEAR products.After installing your device, locate the serial number on the label of your product and use it to register your product at/register . Registration is required before you can use the telephone support service. Registration through the NETGEAR website is strongly recommended.Go to for product updates and web support.For complete DoC go to the NETGEAR EU Declarations of Conformity website at/app/answers/detail/a_id/11621/.For GNU General Public License (GPL) related information, go to /app/answers/detail/a_id/2649.WARNING: Do not stack equipment, or place equipment in tight spaces, in drawers, or on carpets. Make sure your equipment is surrounded by at least 2 inches of air space.ComplianceThis symbol is placed in accordance with the European Union Directive 2002/96 on the Waste Electrical and Electronic Equipment (the WEEE Directive). If disposed of within the European Union, this product should be treated and recycled in accordance with the laws of your jurisdiction implementing the WEEE Directive.NETGEAR, Inc.350 East Plumeria Drive San Jose, CA 95134, USADecember 2011。
Belimo NRF24A-S2-O 电子旋转阀控制器说明书

NRF24A-S2-O ArrayRotary actuator with fail-safe for ball valves• Torque motor 10 Nm• Nominal voltage AC/DC 24 V• Control Open/close• Deenergised open (NO)• with 2 integrated auxiliary switchesTechnical dataElectrical data Nominal voltage AC/DC 24 VNominal voltage frequency50/60 HzNominal voltage range AC 19.2...28.8 V / DC 21.6...28.8 VPower consumption in operation 6 WPower consumption in rest position 2.5 WPower consumption for wire sizing8.5 VAAuxiliary switch 2 x SPDT, 1 x 10% / 1 x 11...100%Switching capacity auxiliary switch 1 mA...3 A (0.5 A inductive), DC 5 V...AC 250 VConnection supply / control Cable 1 m, 2 x 0.75 mm²Connection auxiliary switch Cable 1 m, 6 x 0.75 mm²Parallel operation Yes (note the performance data)Functional data Torque motor10 NmTorque fail-safe10 NmDirection of motion fail-safe Deenergised NO, valve open (A – AB = 100%)Manual override by means of hand crank and locking switchRunning time motor75 s / 90°Running time fail-safe<20 s @ -20...50°C / <60 s @ -30°CSound power level, motor45 dB(A)Position indication MechanicalService life Min. 60'000 fail-safe positionsSafety data Protection class IEC/EN III, Safety Extra-Low Voltage (SELV)Power source UL Class 2 SupplyProtection class auxiliary switch IEC/EN II, reinforced insulationDegree of protection IEC/EN IP54Degree of protection NEMA/UL NEMA 2Enclosure UL Enclosure Type 2EMC CE according to 2014/30/EULow voltage directive CE according to 2014/35/EUCertification IEC/EN IEC/EN 60730-1 and IEC/EN 60730-2-14UL Approval cULus according to UL60730-1A, UL60730-2-14and CAN/CSA E60730-1The UL marking on the actuator depends onthe production site, the device is UL-compliantin any caseType of action Type 1.AA.BRated impulse voltage supply / control0.8 kVRated impulse voltage auxiliary switch 2.5 kVPollution degree3Ambient humidity Max. 95% RH, non-condensingAmbient temperature-30...50°C [-22...122°F]NRF24A-S2-O•••••••Mode of operationSimple direct mountingManual overrideAdjustable angle of rotation High functional reliabilityFlexible signallingWire colours:1 = black 2 = red S1 = violet S2 = red S3 = white S4 = orange S5 = pink S6 = greySafety dataStorage temperature -40...80°C [-40...176°F]Servicingmaintenance-free WeightWeight 2.1 kgSafety notesThis device has been designed for use in stationary heating, ventilation and air-conditioning systems and must not be used outside the specified field of application, especially in aircraft or in any other airborne means of transport.Outdoor application: only possible in case that no (sea) water, snow, ice, insolation or aggressive gases interfere directly with the device and that it is ensured that the ambient conditions remain within the thresholds according to the data sheet at any time.Only authorised specialists may carry out installation. All applicable legal or institutional installation regulations must be complied during installation.The device may only be opened at the manufacturer's site. It does not contain any parts that can be replaced or repaired by the user.Cables must not be removed from the device.The device contains electrical and electronic components and must not be disposed of as household refuse. All locally valid regulations and requirements must be observed.The two switches integrated in the actuator are to be operated either on power supply voltage or at safety extra-low voltage. The combination power supply voltage/safety extra-low voltage is not permitted.Product featuresThe actuator moves the valve to the operating position at the same time as tensioning thereturn spring. The valve is turned back to the fail-safe position by spring force when the supply voltage is interrupted.Simple direct mounting on the ball valve with only one screw. The mounting orientation in relation to the ball valve can be selected in 90° steps.By using the hand crank the valve can be operated manually and engaged with the locking switch at any position. Unlocking is carried out manually or automatically by applying the operating voltage.Adjustable angle of rotation with mechanical end stops.The actuator is overload protected, requires no limit switches and automatically stops when the end stop is reached.The actuator has one auxiliary switch with a fixed setting and one adjustable auxiliary switch. They permit a 10% or 11...100% angle of rotation to be signaled.Electrical installationSupply from isolating transformer.Parallel connection of other actuators possible. Observe the performance data.NRF24A-S2-OWiring diagramsAC/DC 24 V, open/closeAuxiliary switchOperating controls and indicatorsAuxiliary switch settingsNote: Perform settings on the actuator only in deenergised state.For the auxiliary switch position settings, carry out points to successively.17Manual overrideTurn the hand crank until the desired switching position is set.Shaft clampEdge line displays the desired switching position of the actuator on the scale.Fasten the locking deviceTurn the locking switch to the …Locked padlock“ symbol.Auxiliary switchTurn rotary knob until the notch points to the arrow symbol.Unlock the locking deviceTurn the locking switch to the …Unlocked padlock“ symbol or unlock with the hand crank.CableConnect continuity tester to S4 + S5 or to S4 + S6.Manual overrideTurn the hand crank until the desired switching position is set and check whether the continuity tester shows the switching point.12A 34567NRF24A-S2-O DimensionsFurther documentation• The complete product range for water applications• Data sheets for ball valves• Installation instructions for actuators and/or ball valves• General notes for project planning。
Ether I O 24测试应用程序手册说明书

Ether I/O 24 Test and Programming UtilityThe following manual gives a brief outline of the Ether I/O 24 Test and Programming Utility. Shown in diagram 1 below is a screen shot of the Ether I/O 24 Test Utility.Diagram 1The Ether I/O 24 Test utility can be divided into two sections as shown in diagram 2.12Diagram 2These sections are:1. Drop down menus and Toolbar2. Selection Tabs and ControlsEach of the sections will be briefly discussed below and the individual controls within each section will be discussed further on in the manual.1. Drop Down Menus and ToolbarThe commands provided in the drop down menus are linked directly to the short cut icons found on the toolbar. The corresponding drop down menu command and icon perform identical functions so either one can be pressed to perform the command. Most users will find it much easier to use the shortcut icons in the toolbar instead of using the dropdown menus.Drop Down MenuToolbarThere are three Drop down menus located on the Ether I/O Test and Programming Utility. These include•File•Module•HelpEach Drop down menu will be outlined in the following pages. Shortcut icons have been added to the toolbar for ease of use.FileThe File drop down menu contains three options as shown in diagram 3:Diagram 31.Open Config File – this function opens a previously saved configuration file. Thisfunction is also represented on the toolbar as the following icon.2.Save Config File – this function saves the current settings of the Ether I/O moduleto a configuration file. This function is also represented on the toolbar as thefollowing icon.3.Exit – Exits and closes the Ether I/O Test Application Represented byModuleThe Module drop down menu contains four options as shown in diagram 4Diagram 41.Scan for Modules – this function searches the network for all Ether I/O’s. Thisfunction is also represented on the toolbar as the following icon.The Ether I/O’s which respond to the Test Utility will be displayed in the dropdown menu box next to the toolbar search button. . The information in this dropdown box contains the IP address of the unit followed by the MAC address of the unit followed by the firmware version number. An example drop down box isshown below.2.Write Settings to Module – This function writes any setting changes to theEEPROM memory of the unit providing the EEPROM protect jumper (J2) isOFF. This function is also represented on the toolbar as the following icon.Note: When changing settings on the Ether I/O 24, a reboot of the module may be required before the settings become active.3.Read Settings from Module – This function will read the settings in the EEPROMmemory. This function is also represented on the toolbar as the following icon.4.Reboot Module – This function is used to reboot the module and cause it to loadand activate any new settings.2. Selection Tabs & ControlsThere are a number of Selection Tabs and controls as shown below in diagram 5Diagram 5These selection tabs and controls allow the user to set up the Ether I/O 24 to perform various functions. Each of these tabs/controls will be outlined in the following pages. Test ControlsThe test controls are shown below in diagram 6.Each of the selection tabs located under the test control tab will be outlined in the following paragraphs.Diagram 6ValueThe port value is written to or read from the entire port with each of the value bits affecting the corresponding I/O line. The Auto read values check box when checked will constantly read Port A,B,C (poll) on the device to see if the pin has changed.DirectionThe Direction value of the port can be set as either input or output. When set as output, the I/O line will be driven to the last value written to the port. This value can be pre set by writing to the port before writing to the direction register.Pull UpThe Pull Up configuration applies to those lines that are set as inputs, writing a 0 to the corresponding bit applies a pull up resistor to the line so that if it is not driven low it will be pulled to a known high state, this is very useful if sensing contact closures or open collector outputsThresholdThe threshold function sets the threshold at which a line reads as high or low. When the corresponding bit is set as 1 then the threshold is set at 1.4V and any voltage above this reads as a high level. When the corresponding threshold bit is set to 0 the threshold is set at 2.5V and any voltage above this reads as a high level.SchmittSchmitt trigger inputs means that the input line is compared to 2 voltages, 0.75V and 4.25V. When the line’s voltage drops below 0.75V it will read as a low until the line’s voltage rises above 4.25V at which time the line will read as a high. When the line’s voltage is in between 0.75V and 4.25V, the value will remain stable at its previous level. To enable the Schmitt trigger on any input a 0 must be written to the corresponding bit Programming OptionsThe Programming Options are shown below in diagram 7.Diagram 7Each of the selection tabs located under the Programming Options tab will be outlined in the following paragraphs.Fixed IPFixed IP addressing allows each module to be given a specific address that remains constant throughout the life of the machine thereby simplifying machine software design and allowing easy diagnosis of machine wiring faults.Note: When the Fixed IP address is enabled. Write the settings to the EEPROM and then reboot the unit. Perform a search and the Ether I/O 24 will appear with the new IP address.Programmable Power-Up State.The module can be programmed to power up with all its ports to a programmed state, thus if a machine needs to have certain devices enabled at power up or if the machine designer desires all lamps to light in a lamp test, it is possible for the module to accomplish this before the main control system is active. Listed below are the various settings that can be programmed for power up. Descriptions for these settings have been outlined in previous paragraphs of the manual.•Power Up Value•Power Up Direction•Power Up Pull Up•Power Up Threshold•Power Up SchmittAutoScan SetupThe AutoScan Setup is shown below in diagram 8Diagram 8The AutoScan mode will allow the module to originate communication with a remote device or another Ether I/O 24 module. This mode is very useful as it allows your software the freedom not to have to poll the module to check the state of the inputsBit Test EnablesMask bits are used to allow some of the input pins of the module to toggle without generating messages from the module. Any input whose corresponding mask bit is low, is ignored by the AutoScan function.Scan Rate and FilteringThe Scan Rate is a 16-bit value which is used to divide the scan rate of the AutoScan mode from it’s base rate of 1,000 scans per second down to a user programmed rate from 500 scans per second to one scan per 65.5 seconds. When set at 1 the scan rate is 1,000 scans per second, it is 500 scans per second when the value is 2 and so on. You simply divide the 1,000 per second rate by your desired scan rate to find the value for address 18. The filter value which is in the MSB of Address 17 is used to count the number of identical reads that are required before a port value is considered valid and sent to the target device. When set at 0 the filter is turned off, when set at 1 the port must read the same for two scans to be considered valid and sent to the target. Higher numbers simply increase the number of identical reads required before the value is considered valid.Care should be taken when using high filter values with slow scan rates, as the reporting time for a change under these conditions can be over 4 hours.Target IP Address and Port NumberA Target IP Address and Port Number are provided to tell the Ether I/O what destination address the Autoscan data has to be sent too.To allow the module to communicate through a router without having to set up Gateway addresses and Subnet masks, the module stores the Ethernet address of the target device as well as the IP address and Port number. If your target device is outside your local network then this address will be that of the gateway or router whereas if your target device is on your local area network then this address will be that of the device itself. Combined with the IP address of the target device and the port number there are 12 bytes of the EEPROM that relate to the target device’s address and these occupy the addresses from 19 to 24 in the EEPROM. Words 16, 17 and 18 are used to store the Mask bits, Filter Count and Scan rate settings for AutoScan mode.EEPROM ValuesThe EEPROM values are shown below in diagram 9Diagram 9Read EEPROMThe module will read the EEPROM memory and display the contents of the EEPROM in the EEPROM values display.Write EEPROMThe module will write any setting changes to the EEPROM memory.Running the Ether I/O 24 Test utility.When the program is first run it will automatically search for any Ether I/O 24s that are located on the network. If no modules are found then make sure that you have the correct network settings and check the jumpers on the Ether I/O 24 as detailed in the User Manual.Technical Support and Further InformationFor any questions relating to the Ether I/O 24 please contact us by Email.Email: ******************Document Revision HistoryEther I/O 24 Test Application Manual V1.0– Initial document created 6th April 2005。
RA24ZC 零距离框架套件与 RF24 电源炉说明书

Model RA24ZCZERO CLEARANCE KIT for RF24BN/BP INSERTManufactured byMILES INDUSTRIES LTD.British Columbia, CanadaVous pouvez vous procurer un exemplaire français de cette brochure chez votre marchand.4000876/03Patents PendingPlease read this manual in conjunction with the RF24 HeaterInstallation Manual OverviewGeneral ApplicationThe RA24ZC Zero Clearance Kit with RF24 heater may beinstalled in new wood frame construction with type “B”venting.The zero clearance box may be roughed-in on its own and the RF24 heater inserted later.The Zero Clearance Kit is also intended for applications where an existing gas or wood burning fireplace is being removed in whole or in part, without disturbing the surrounding wall finish.The minimum cavity for installing the Zero Clearance Kit isshown in the Framing Dimensions diagram next page. Existing type “B” gas venting may be utilized provided the integrity is intact. Existing mantle clearances must conform to the chart.For visual reasons, the zero clearance box is painted black on the inside; it is recommended to paint the vent liner and gas line with high heat paint after installing.Kit Contents743 Double Door (hinged)Supplied with fret 744 Single Door (hinged)Supplied with fret RA24DS (draw screen)Fret supplied separately RA24FS (fixed screen)Fret supplied separatelyMantle ClearancesInner Front Trim Choices (one must be selected)(same perimeter size for all)Framing DimensionsNote - 29” x 33” min. opening in combustible wallOuter Trim Options (Note - Must Cover 29” x 33” min. opening in combustible wall)Custom trims may be used to replace or extend these options.746/747, 3-sided Shown w/750OCP748/749, 4-sided 715 Cast MantlePrepare Z.C. Box1. Remove stand-offs from top of Z.C. box; fold and reattach to top of box. See Fig. 1.2. Position zero clearance box in cavity and connect to vent system.3. Rough-in gas line to left hand side.4. Install the short length of 3” dia. flex liner supplied with the kit to the collar on the underside of the Z.C. box using the gear clamp provided. Secure the vent plate removed from the insert to the other end of the liner using a gear clamp. See Fig. 2.5. Compress/stretch the liner so the vent plate is approximately 19“ above the floor. See Fig. 3.6. Paint liner and gear clamps using black high heat paint (not supplied).Install Insert Into Z.C. BoxIf a fan is to be installed, it should beinstalled to the heater before the heater is inserted into the Z.C. box. See separate installation instructions with the fan kit.1. Slide the insert into the zero clearance box while guiding the vent plate into the cleats on top of the insert. Mount the fret retainers to the insert prior to installing for RA24DS/FS Inner Fronts (other fronts have the retainers built in). Secure the vent plate using 2 screws. See Fig. 4.2. Connect the gas line to the unit.Fig. 2Fig. 1Fig. 3Fig. 41. Place heat shield into Z.C. boxthrough the notched cut-outs on each side at the top of box. See Fig. 5.Install Heat Shield and Convection BaffleFig. 5Fig. 6Fig. 72. Place the tabs at the rear edge of the heat shield into the slots. Secure the heat shield using 2 screws on each side. Screw from within the Z.C. box.See Fig. 6.3. Slide the convection baffle supplied with the heater into the slots at the top and tighten the wingnuts. See Fig. 7.4. Finish the installation of bricks, logs,remote control, glass etc. as per instructions packed with the RF24heater.Install TrimsNote: Outer trims may require extending or custom trims may be required to cover openings.The trim packs may contain redundant parts not required for these applications as trims are common to other modelheaters. Discard unused parts.1. Fasten the mounting brackets supplied with the zero clearance kit to the back of the outer trim using screws provided. See Fig. 8.Note: It may be necessary to extend the outer trim to cover the combustible wall opening. Custom non-combustible sheet metal pieces may be added to the extruded aluminum trims and fastened using the screw channel on the back of the trim.2. Fasten the outer trim with the mounting brackets attached to the side flanges of zero clearance box using 2 screws each side. See Fig. 9.3. Hook the cast iron fret onto theretainers mounted to the heater if using the RA24DS or FS Inner Trims.Note: Other inner trims include the retainers. See Fig. 10.4. Hook the inner front trim to the mounting brackets on the zeroclearance box. See Fig. 11. It may be desirable for visual reasons to adjust the front to back position of the insert depending on which inner front trim is used and where the cast iron fret positions.Fig. 8Fig. 9Fig. 10Fig. 11Parts。
- 1、下载文档前请自行甄别文档内容的完整性,平台不提供额外的编辑、内容补充、找答案等附加服务。
- 2、"仅部分预览"的文档,不可在线预览部分如存在完整性等问题,可反馈申请退款(可完整预览的文档不适用该条件!)。
- 3、如文档侵犯您的权益,请联系客服反馈,我们会尽快为您处理(人工客服工作时间:9:00-18:30)。
RS24ADPIO-2使用说明
目录
一、安装尺寸
二、单片机接口J3线的定义
三、EPP操作时序
四、口地址定义
五、数据的读入
六、数据格式
七、信号及电源J1定义
八、标定
九、效果
十、编程注意
十一、DEMO软件的使用
一、 安装尺寸
二、单片机接口J3线的定义
Pin号名字I/O 并口Pin号功能
I 1 读写标识,“1”读;“0“写,
1 nWrite
IO 2 双向数据线D0位
2 PCD0
3 PCD1
IO 3 双向数据线D1位
4 PCD2
IO 4 双向数据线D2位
5 PCD3
IO 5 双向数据线D3位
IO 6 双向数据线D4位
6 PCD4
7 PCD5
IO 7 双向数据线D5位
IO 8 双向数据线D6位
8 PCD6
IO 9 双向数据线D7位
9 PCD7
10 TRIP I 总外触发输入,上升沿触发
11 TRIPs
I 单片机外触发输入,上升沿触发
12 GND
12 GND GND
i 备用
13 NULL2
14 nDstrb
I 14 数据操作线,低有效
15 VCC VCC 5.0V
16 nwait O 11 (MCU不要联接)(EPP调试的输出)
17 nAstrb
I 17 地址操作线,低有效
18 NULL1
i备用
19 vcc vcc 5.0V
18TO25 GND
20 GND GND
三、 EPP操作时序
写地址:
读地址和写数据
读数据
四、口地址定义
地址值数据值读或写功能
0x00 0 写停止数据采集
0x00 1 写等待触发条件,触发条件满足后,开始数据采集,
0x01 1
2
3 写用外触发条件做触发源TRIP1(屏蔽外部触发源TRIP)用外触发条件做触发源TRIP(屏蔽外部触发源TRIP1)
用两个外触发条件"或"做触发源(三个都是上升沿触
发)
0x01 4 写使能软件强行触发(屏蔽外部触发源)
0x01 8+4 写强制软件触发操作
0x02 0 写关闭高通滤波,可以通过直流。
0x02 1 写使能高通滤波,1HZ信号衰减30dB。
0x03 0 写关闭硬件自适应滤波,记录长度可达到10K。
0x03 1 写使能硬件自适应滤波,记录长度可达到4K。
0x04 PCD[2..0 写 PCD0=’1’,
使能第一通道值触发,PCD1=’1’, 使能第
二通道值触发,PCD2=’1’, 使能外触发,反之就关闭
了。
0x0a PCD[7..0] 写记录长度设定值低8位0x0b PCD[6..0] 写记录长度设定值高6位0x0c 0xaa 写允许从地址线读数据。
0x0d PCD[3..0] 读数据
线PCD0第一通道触发标识,‘1’已触发。
PCD1第二通道触发标识,‘1’已触发。
PCD2外触发标识,‘1’已触发。
PCD3=‘1’完成了设定记录长度的采集。
0x0e PCD[0] 写 PCD0=0第一通道读标识,读第一通道。
PCD0=1第二通道读标识,读第二通道。
0x0f PCD[6..0] 写采样频率设置。
1K 0X3F
2K 0X1F
4K 0XF
8K 0X7
16K 0X3
32K 0X1
64K 0X0
128k 0X80
0x10 PCD[2..0] 写第一通道 PGA
0 是0.5倍;1 是1倍;2 是2倍;3是4倍;4 是8倍;5
是16倍;6 是32倍;7 是64倍
0x11 PCD[2..0] 写第二通道 PGA
0 是0.5倍;1 是1倍;2 是2倍;3是4倍;4 是8倍;5
是16倍;6 是32倍;7 是64倍
采集时间T= (记录长度/采样频率)
50HZ个数=CEIL(采集时间T/20mS)
需要移的时间=50HZ个数*20mS
需要移的样点数=需要移的时间*采样频率
五、数据的读入
1写地址为0x0c
2写数据为0xaa
3, 读数据软件。
写地址为0x0e,
写数据为0x0;//只读单一通道后面就不写了,这里可以写0或1;
for(I=0;I<记录长度;I++)
{
写数据为0x0;//如果只读第二通道数据就不写她
读地址口。
第一通道数据低8位;d7-d0。
读地址口。
第一通道数据中8位;d15-d8。
读地址口。
第一通道数据高8位;d23-d16。
写数据为0x1;//如果只读第一通道数据就不写她
读地址口。
第二通道数据低8位;d7-d0。
读地址口。
第二通道数据中8位;d15-d8。
读地址口。
第二通道数据高8位;d23-d16。
}
//注意:数据前后交换了.
六、数据格式
以采样长度为N说明
最先读入的数据是最后第N点的数据。
读入次数 样点序号 通道1 通道2
1 N 通道1第N样点 通道2第N样点
2 N-1 通道1第N-1样点 通道2第N-1样点
3 N-2 通道1第N-2样点 通道2第N-2样点
…………通道1第。
样点通道2第。
样点
N-1 2 通道1第2样点 通道2第2样点
N 1 通道1第1样点 通道2第1样点
三个字节一个数,顺序是数据低8位;数据中8位;数据高8位;最高位是符号位,负数以补码表示。
24位数与32位数的转换
PC及单片机在24位AD采集中用32位数(LONG INTEGER)来表示采集值。
就需要将我们得到的24位数转换32位数,为PC及单片机使用。
24位数的组织,每通道三字节,先读低八位,后读中八位,再读最高八位。
第三字节的最高位是符号位。
0到2。
5V对应数值,0到8388607(0到0X7FFFFF);
0到-2。
5V对应数值,0到-8388607(0XFFFFFF到0X800000);
在24位数转换32位数的过程中,正数直接赋过去,当判短到24位数的最高位为高了,就代表是负数,赋给32位变量必需进行处理。
如下程序
if (data[j][i] >= 0x800000l)
{
n=
data[j][i];
n=(n&0x7fffff)*(-1);
data[j][i] = n;
}
七、信号及电源J1定义
1、 信号定义
J1信号定义
PIN 1 AGND 模拟电源地
PIN 2 9VA 模拟电源
PIN 3 AGND 模拟电源地
PIN 4 9VA 模拟电源
PIN 5 AGND 模拟电源地
PIN 6 S1- 第一路输入信号负(-5 TO 5V)diff PIN 7 AGND 模拟电源地
PIN 8 S1+ 第一路输入信号正(-5 TO 5V)diff PIN 9 AGND 模拟电源
PIN 10 S2- 第二路输入信号负(-5 TO 5V)diff PIN 11 DGND 数字电源地
PIN 12 S2+第二路输入信号正(-5 TO 5V)diff PIN 13 9VD 数字电源
PIN 14 9VD
八、标定
标定举例
下列标定系数举例
通道零点比例
1 +696
1.025
1.028
2 +872
软件实例:
for(i=0;i<RecordLength;i++)
{
data[1][i] = data[1][i]-872;
data[1][i] = (data[1][i]*1.0)*1.028;
data[0][i] = data[0][i]-696;
data[0][i] = (data[0][i]*1.0)*1.025;
fprintf(fp1,"%ld,%ld\n",data[0][i],data[1][i]);
}
九、效果
交流偶合,4uV的效果。
直流偶合,4uV的效果
手感应50HZ输入
50HZ,硬件去工频效果,7uV是有其它频普感应进去了
十、编程注意
1、先要根据口地址涵义设置系统的工作状态
2、写开始采集
3、读回系统状态,叛断触发没有?采集完成没有
4、采集完成后,读回一个记录长度的数据。
十一、DEMO软件的使用
1、将PC的BIOS中的并口设为EPP模式。
2、运行CD中目录:并口读安装软件的SETUP。
EXE
3、在桌面点击READDATA图标。
4、再下列界面中先点S,再点ST,再点RD。