V-CUT削铜计算公式
工序质量检验规范--V-CUT

责任单位
详细说明
制造部
生产部安装 MI 资料进行生产 作业,制作首件 部品,制作完成 后进行首件部 品自检,自检 OK 后交于生产 组长进行检查
品管部
生产部自检合格 的首件部品交于 品质 QA 进行检
查
制造部
品质部确认 OK 后生产部根据 首件确认样品 进行批量生产
品管部
品质部 QA 不定 时的进行巡检, 检验发现有异常 部件,作出判定, 在通过返工修理 后的板进行全检
√
√
HX-WI-018 HX-QR-048 HX-QR-120
东莞洪兴电子有限公司
CHANGAN JINXIA HUNGHING ELECTRONICS FACTORY
作业指导书
文件编号﹕WI-QA(IPQC)-08 制订日期﹕ 2016-10-20 版 本﹕A/1 页 码﹕第 7 页 共 6 页
文件 名称
工序质量检验规范—V-CUT
OK 方可转出
东莞洪兴电子有限公司
CHANGAN JINXIA HUNGHING ELECTRONICS FACTORY
作业指导书
文件编号﹕WI-QA(IPQC)-08 制订日期﹕ 2016-10-20 版 本﹕A/1 页 码﹕第 5 页 共 6 页
文件 名称
工序质量检验规范—V-CUT
6.0 检验标准
3.1 工程部:负责提供公司产品的相关技术资料。 3.2 制造部:负责完成产品的制造及产品品质符合要求。 3.3 品保部:负责依据工程资料及客户品质要求对产品进行检验与判定。 3.4 计划部:负责生产板的排程与进度的跟踪。
4.0 作业流程:
4.1 首件确认时机: 4.1.1 凡交接班生产之料号均须进行首件确认。 4.1.2 新料号第一次量产时须进行首件确认。 4.1.3 调整或修复机器生产时须进行首件确认。 4.1.4 机台转换料号生产时须进行首件确认。 4.1.5 工程资料变更后须进行首件确认。 4.1.6 首件判退改善后须重新进行首件确认。
V-CUT计算公式

公制尺寸 0.25 45
0.207
邊銅箔/線路距 V-CUT 中心線之最小安全距離
0.23
mm
V-CUT槽宽及角度之计算
V-CUT要求:
b
Θ
1、V-VCU-CT U示T意深圖度:以客户要求V为型准槽,如客户无要求时,则依以下标准:
bc
a、板厚≥0.9mm时,则V-CUT保留厚度为:板厚的1/3±0.1mm;但若工
局部放
作边在<1以0m下m紅,则底其黃工字作的边儲保存留厚格度內:输0.入3±已0.知1m數m.據,即可自动算出所需答案 (
B. 板 厚 <0. 9mm , 保 留 厚 度 为: 0.3 ± 0.1 mm
计算
b Θ
a
局部放大图
自动算出所需答案 (綠底黃字)
項目
單位 公制尺寸
V-CUT 深
mm
0.65
理論角度(θ)
度
14
V-CUT槽宽 (b)
mm
0.161
項目
V-CUT 深 角度 (θ) 理論槽宽 (b)
單位 mm 度 mm
mil
11.81 30
6.329
板邊銅箔/線路距 V-CUT 中心線之最小安全距離
8.16
mil
項目
單
V-CUT 深
角度 (θ)
理論槽宽 (b)
板邊銅箔/線路距 V-CUT
0.23
VCUT 深 度 以 客 户 要 求 为 准, 如 无 要 求 时, 则 依 以 下 标 准:
A. 板 厚 >=0 .9m m 时, 保 留 厚 度 为: 板 厚 的 1/3 ± 0.1 mm, 但 工 作 边 <10 mm
V-CUT余厚

客户无指定余厚时,V 槽余厚标准(单位:mm)
1) 如L<0.6的板必须进行V 槽加工时,应在MI中注明允许局部单面V槽。
2) 阴影处为跳线余厚,如遇V槽切割处镂空较多、板易折断或外形不规则等情况时应选择跳线加工,因跳线产能较低故正常情况下不推荐使用。
3) 上述标注仅作为参考标注,按以上要求余厚制作样板,客户反馈样板信息后,如对V槽余厚认可,则可批量生产;如对V槽余厚不满意,由样板室通知ME进行调整后交客户确认。
4) 客户对余厚有规定的,按客户规定执行。
FR-4板料: 客户无要求时,当完成厚度≤1.0MM时,余厚一般按1/3板厚制作,为方便生产操作,余厚最小需保持0.25+/-0.05MM,若1/3板厚小于0.25MM,则仍按0.25+/-0.05MM控制;
当完成厚度>1.0MM时, 余厚一般按1/4板厚制作, 为方便客户掰开,余厚最大0.6+/-0.05MM,若1/3板厚大于0.60MM,则仍按0.60+/-0.05MM控制;客户有要求时按客户要求制作。
CEM板料V-CUT 余厚一般为1/2板厚金属基板:客户无要求按“0.3±0.05mm”余厚要求控制;客户有要求时按照客户要求制作!。
切削加工常用计算公式
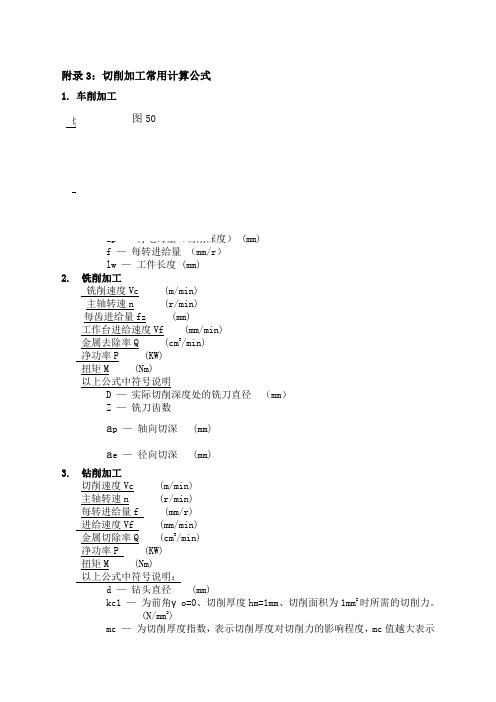
附录3:切削加工常用计算公式
(mm)
f —每转进给量(mm/r)
lw —工件长度 (mm)
2. 铣削加工
铣削速度Vc (m/min)
主轴转速n (r/min)
每齿进给量fz (mm)
工作台进给速度Vf (mm/min)
金属去除率Q (cm3/min)
净功率P (KW)
扭矩M (Nm)
以上公式中符号说明
D —实际切削深度处的铣刀直径(mm)
Z —铣刀齿数
a p —轴向切深 (mm)
a e —径向切深 (mm)
3. 钻削加工
切削速度Vc (m/min)
主轴转速n (r/min)
每转进给量f (mm/r)
进给速度Vf (mm/min)
金属切除率Q (cm3/min)
净功率P (KW)
扭矩M (Nm)
以上公式中符号说明:
d —钻头直径 (mm)
kc1 —为前角γo=0、切削厚度hm=1mm、切削面积为1mm2时所需的切削力。
(N/mm2)
mc —为切削厚度指数,表示切削厚度对切削力的影响程度,mc值越大表示
切削厚度的变化对切削力的影响越大,反之,则越小—前角(度)
γ
o。
PCB加工V-CUT说明
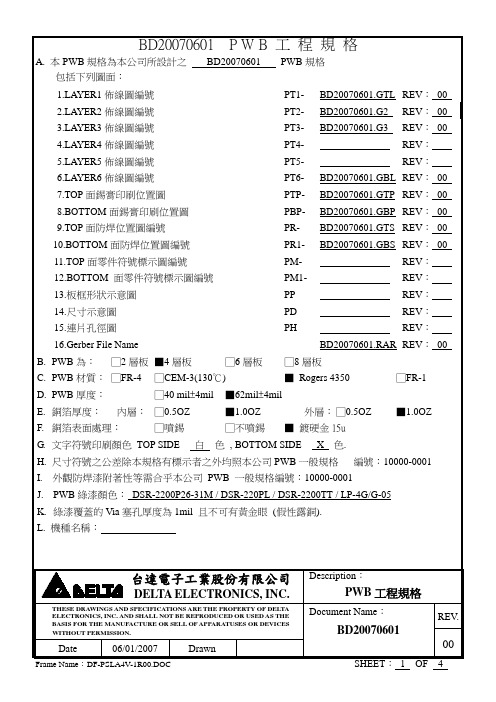
K. 綠漆覆蓋的 Via 塞孔厚度為 1mil 且不可有黃金眼 (假性露銅).
L. 機種名稱:
台達電子工業股份有限公司
DELTA ELECTRONICS, INC.
THESE DRAWINGS AND SPECIFICATIONS ARE THE PROPERTY OF DELTA ELECTRONICS, INC. AND SHALL NOT BE REPRODUCED OR USED AS THE BASIS FOR THE MANUFACTURE OR SELL OF APPARATUSES OR DEVICES
MODEL: □:RE-LAYOUT □:MINOR CHANGE □:PD □:PM □:PM-1 □:PH
□:PP
REV:00 □:PT □:PR
CODE:00 □:PR-1
ITEM
COMPONENTS
HOLES PITCHS
1
2
3
4
5
6
7
8
10
ITEM 1 2 3 4 5
OTHERS
台達電子工業股份有限公司
7. ■ CAM 加上日期
8. ■ CAM 加上防火等級
9. ■ CAM 加上廠商安規等級
10. □ CAM 於四角加上蝕刻監測 Track;L:400mil、W:10mil
11. ■ 蝕刻後走線寬度誤差不得超過 20%
12. ■ PWB 鑽孔偏移量加板層對位偏移量不得超過 5mil
13. □ Each Layout Offset 不得超過 3mil
WITHOUT PERMISSION.
Date
06/01/2007
Drawn
Frame Name:DF-PSLA4V-1R00.DOC
常用的车削、铣削、钻削加工计算公式全在这里了,随用随查

常用的车削、铣削、钻削加工计算公式全在这里了,随用随查01常用车削加工计算公式●切削线速度Vc(m/min)D m:加工直径,单位(mm)n:主轴转速,单位(rpm)●主轴转速 n (rpm)Vc:切削线速度,单位(m/min)D m:加工直径,单位(mm)●金属去除率 Q (cm3/min)Vc:切削线速度,单位(m/min)a p:切深(吃刀量),单位(mm)f n:每转进给量,单位(mm/r)●净功率 Pc (kW)Vc:切削线速度,单位(m/min)a p:切深(吃刀量),单位(mm)f n:每转进给量,单位(mm/r)●加工时间 Tc (min)I m:加工长度,单位(mm)f n:每转进给量,单位(mm/r)n:主轴转速,单位(rpm)●特定切削力 Kc(N/mm2)k c1:特定切削力,适用于h m= 1 mmh m:平均切屑厚度,单位(mm)m c:实际校正系数h mγ0:切屑前角02常用铣削加工计算公式03常用孔加工计算公式其它一些加工计算公式,也许对你有用。
一、挤牙丝攻内孔径计算公式:公式:牙外径-1/2×牙距例1:公式:M3×0.5=3-(1/2×0.5)=2.75mm M6×1.0=6-(1/2×1.0)=5.5mm例2:公式:M3×0.5=3-(0.5÷2)=2.75mm M6×1.0=6-(1.0÷2)=5.5mm二、一般英制丝攻之换算公式:1英寸=25.4mm(代码)例1:(1/4-30)1/4×25.4=6.35(牙径)25.4÷30=0.846(牙距)则1/4-30换算成公制牙应为:M6.35×0.846例2:(3/16-32)3/16×25.4=4.76(牙径)25.4÷32=0.79(牙距)则3/16-32换算成公制牙应为:M4.76×0.79三、一般英制牙换算成公制牙的公式:分子÷分母×25.4=牙外径(同上)例1:(3/8-24)3÷8×25.4=9.525(牙外径)25.4÷24=1.058(公制牙距)则3/8-24换算成公制牙应为:M9.525×1.058四、美制牙换算公制牙公式:例:6-326-32 (0.06+0.013)/代码×6=0.1380.138×25.4=3.505(牙外径)25.4÷32=0.635(牙距)那么6-32换算成公制牙应为:M3.505×0.6351、孔内径计算公式:牙外径-1/2×牙距则应为:M3.505-1/2×0.635=3.19那么6-32他内孔径应为3.192、挤压丝攻内孔算法:下孔径简易计算公式1:牙外径-(牙距×0.4250.475)/代码=下孔径例1:M6×1.0M6-(1.0×0.425)=5.575(最大下孔径)M6-(1.0×0.475)=5.525(最小)例2:切削丝攻下孔内径简易计算公式:M6-(1.0×0.85)=5.15(最大)M6-(1.0×0.95)=5.05(最小)M6-(牙距×0.860.96)/代码=下孔径例3:M6×1.0=6-1.0=5.0+0.05=5.05五、压牙外径计算简易公式:1.直径-0.01×0.645×牙距(需通规通止规止)例1:M3×0.5=3-0.01×0.645×0.5=2.58(外径) 例2:M6×1.0=6-0.1×0.645×1.0=5.25(外径) 六、公制牙滚造径计算公式:(饱牙计算)例1:M3×0.5=3-0.6495×0.5=2.68(车削前外径) 例2:M6×1.0=6-0.6495×1.0=5.35(车削前外径)七、压花外径深度(外径)外径÷25.4×花齿距=压花前外径例:4.1÷25.4×0.8(花距)=0.13 压花深度应为0.13八、多边形材料之对角换算公式:1.四角形:对边径×1.414=对角径2.五角形:对边径×1.2361=对角径3.六角形:对边直径×1.1547=对角直径公式2:1.四角:对边径÷0.71=对角径2.六角:对边径÷0.866=对角径九、刀具厚度(切刀):材料外径÷10+0.7参考值十、锥度的计算公式:公式1:(大头直径-小头直径)÷(2×锥度的总长)=度数等于查三角函数值公式2:简易(大头直径-小头直径)÷28.7÷总长=度数-End-。
切削参数和计算公式
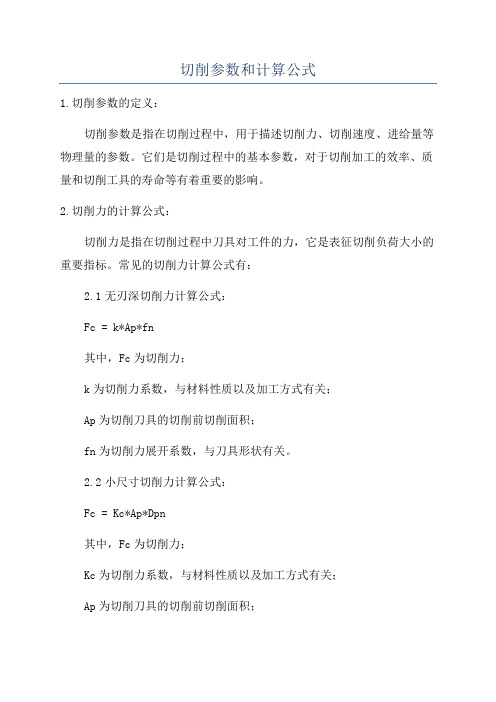
切削参数和计算公式1.切削参数的定义:切削参数是指在切削过程中,用于描述切削力、切削速度、进给量等物理量的参数。
它们是切削过程中的基本参数,对于切削加工的效率、质量和切削工具的寿命等有着重要的影响。
2.切削力的计算公式:切削力是指在切削过程中刀具对工件的力,它是表征切削负荷大小的重要指标。
常见的切削力计算公式有:2.1无刃深切削力计算公式:Fc = k*Ap*fn其中,Fc为切削力;k为切削力系数,与材料性质以及加工方式有关;Ap为切削刀具的切削前切削面积;fn为切削力展开系数,与刀具形状有关。
2.2小尺寸切削力计算公式:Fc = Kc*Ap*Dpn其中,Fc为切削力;Kc为切削力系数,与材料性质以及加工方式有关;Ap为切削刀具的切削前切削面积;Dpn为主切削刃数。
2.3端面切削力计算公式:Fc=Kc*Ap其中,Fc为切削力;Kc为切削力系数,与材料性质以及加工方式有关;Ap为切削刀具的切削前切削面积。
3.切削速度的计算公式:切削速度是指刀具与工件相对运动的速度,它是切削过程中非常重要的参数,对于切削效果和工件表面质量有显著影响。
通常使用单位时间内刀具工作长度与刀具进给速率之比来表示切削速度。
常见的切削速度计算公式有:3.1转速计算公式:n=1000*v/(π*d)其中,n为转速;v为切削速度;d为刀具直径。
3.2切削速度计算公式:v=n*(π*d)/1000其中,v为切削速度;n为转速;d为刀具直径。
4.进给量的计算公式:进给量是指切削刀具每转一周与工件的相对位移距离,它是切削过程中控制材料去除率和工件表面质量的关键参数。
4.1转速计算公式:S=n*f其中,S为进给量;n为转速;f为进给速率。
4.2进给速率计算公式:f=S/n其中,f为进给速率;S为进给量;n为转速。
总结:切削参数是切削过程中描述切削力、切削速度、进给量等物理量的参数,对切削加工的效率、质量和切削工具的寿命有重要影响。
常见的切削参数计算公式包括切削力公式、切削速度公式和进给量公式等。
切削速度计算公式

切削速度计算公式切削速度是切削加工中一个十分重要的参数,它表示刀具在切削过程中每分钟切削的长度。
切削速度的计算公式可以通过根据工件材料、切削刀具和刀具直径来确定。
以下是常见的切削速度计算公式。
1.单刃铣刀的切削速度计算公式:Vc=π*Dc*n其中,Vc表示切削速度(单位:m/min),Dc表示刀具直径(单位:mm),n表示主轴转速(单位:rpm)。
2.钢材的切削速度计算公式:Vc=(π*Dc*n)/1000其中,Vc表示切削速度(单位:m/min),Dc表示刀具直径(单位:mm),n表示主轴转速(单位:rpm)。
3.车削加工中的切削速度计算公式:Vc=(π*Dc*n)/1000其中,Vc表示切削速度(单位:m/min),Dc表示刀具直径(单位:mm),n表示主轴转速(单位:rpm)。
4.钻削加工中的切削速度计算公式:Vc=(π*Dc*n)/1000其中,Vc表示切削速度(单位:m/min),Dc表示刀具直径(单位:mm),n表示主轴转速(单位:rpm)。
5.铣削加工中的切削速度计算公式:Vc = nc * fz * z其中,Vc表示切削速度(单位:mm/min),nc表示铣削系数(单位:mm/z),fz表示进给速度(单位:mm/min),z表示齿数。
需要注意的是,以上计算公式中的单位可能有所不同,具体应根据实际情况进行转换。
切削速度的选择直接影响到加工效率和工件表面质量,因此在具体应用中需要综合考虑工件材料特性、刀具耐磨性和工艺要求等因素,选择合适的切削速度。
同时,切削过程中应注意刀具的冷却润滑,以减少切削热量对刀具和工件的损伤。
v-cut作业指导书
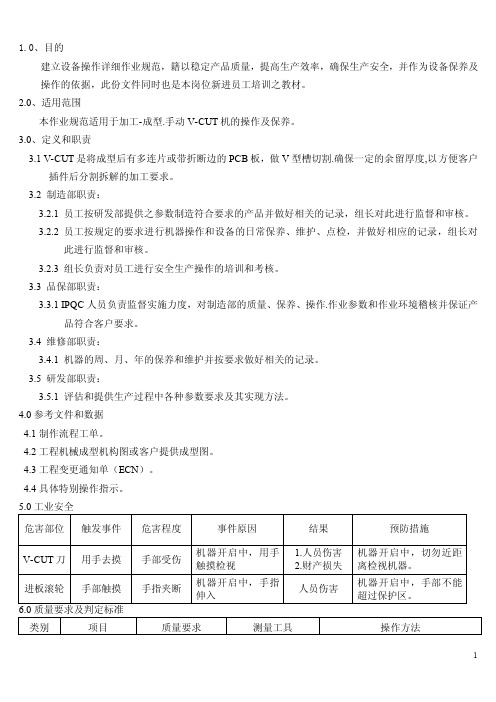
1.0、目的建立设备操作详细作业规范,籍以稳定产品质量,提高生产效率,确保生产安全,并作为设备保养及操作的依据,此份文件同时也是本岗位新进员工培训之教材。
2.0、适用范围本作业规范适用于加工-成型.手动V-CUT机的操作及保养。
3.0、定义和职责3.1 V-CUT是将成型后有多连片或带折断边的PCB板,做V型槽切割.确保一定的余留厚度,以方便客户插件后分割拆解的加工要求。
3.2 制造部职责:3.2.1 员工按研发部提供之参数制造符合要求的产品并做好相关的记录,组长对此进行监督和审核。
3.2.2 员工按规定的要求进行机器操作和设备的日常保养、维护、点检,并做好相应的记录,组长对此进行监督和审核。
3.2.3 组长负责对员工进行安全生产操作的培训和考核。
3.3 品保部职责:3.3.1 IPQC人员负责监督实施力度,对制造部的质量、保养、操作.作业参数和作业环境稽核并保证产品符合客户要求。
3.4 维修部职责:3.4.1 机器的周、月、年的保养和维护并按要求做好相关的记录。
3.5 研发部职责:3.5.1 评估和提供生产过程中各种参数要求及其实现方法。
4.0参考文件和数据4.1制作流程工单。
4.2工程机械成型机构图或客户提供成型图。
4.3工程变更通知单(ECN)。
4.4具体特别操作指示。
7.1操作示意图7.2 V-CUT 机开机操作流程8.0 工艺操作过程及操作要求:N/A 9.0 操作要求9.1 V-CUT 机操作要求流程 操作要求9.2 异常现象原因分析及改善措施9.2.1 露铜、露线、偏位原因:在生产过程中此类异常是较为常见的,造成此异常的主要原因是V-CUT机前后挡板松动及锣板在生产过程中有板大小不一造成。
改善措施:操作员在生产操作过程中要做到定时自检,定时查看V-CUT机文挡板是否有松动,在生产锣板的尺寸有不一致的须将尺寸不一的板挑出分开V-CUT并做到3-5SET自检一次。
9.2.2 跳刀原因:造成板在V-CUT过程中跳刀主要是因为刀具上有缺口和压板胶轮不转造成改善措施:操作员在调刀前必须有对胶轮进行检查,对废弃和有缺口的刀具应分开放置或打报废,胶轮须经常保养使其润滑表面无锈。
切削速度的公式
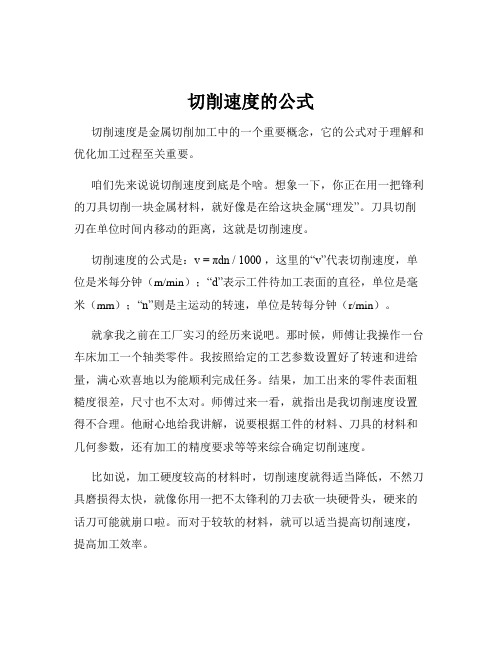
切削速度的公式切削速度是金属切削加工中的一个重要概念,它的公式对于理解和优化加工过程至关重要。
咱们先来说说切削速度到底是个啥。
想象一下,你正在用一把锋利的刀具切削一块金属材料,就好像是在给这块金属“理发”。
刀具切削刃在单位时间内移动的距离,这就是切削速度。
切削速度的公式是:v = πdn / 1000 ,这里的“v”代表切削速度,单位是米每分钟(m/min);“d”表示工件待加工表面的直径,单位是毫米(mm);“n”则是主运动的转速,单位是转每分钟(r/min)。
就拿我之前在工厂实习的经历来说吧。
那时候,师傅让我操作一台车床加工一个轴类零件。
我按照给定的工艺参数设置好了转速和进给量,满心欢喜地以为能顺利完成任务。
结果,加工出来的零件表面粗糙度很差,尺寸也不太对。
师傅过来一看,就指出是我切削速度设置得不合理。
他耐心地给我讲解,说要根据工件的材料、刀具的材料和几何参数,还有加工的精度要求等等来综合确定切削速度。
比如说,加工硬度较高的材料时,切削速度就得适当降低,不然刀具磨损得太快,就像你用一把不太锋利的刀去砍一块硬骨头,硬来的话刀可能就崩口啦。
而对于较软的材料,就可以适当提高切削速度,提高加工效率。
还有啊,如果刀具的耐磨性好,也能承受更高的切削速度。
就好比一个强壮的运动员能跑得更快更久一样。
在实际的加工过程中,还得考虑机床的性能。
有的老旧机床,它的主轴转速范围有限,可能就没法达到理想的切削速度。
这时候,就得想办法调整其他参数来弥补。
另外,切削速度还会影响切削温度。
速度太快,产生的热量多,刀具和工件都容易过热,影响加工质量和刀具寿命。
速度太慢呢,又会降低生产效率。
所以,找到那个最合适的切削速度,就像是在走钢丝,得小心翼翼地保持平衡。
总之,切削速度这个公式虽然看起来简单,但是要真正用好它,可得综合考虑好多因素。
只有这样,才能加工出高质量的零件,提高生产效率,降低成本。
希望大家在实际操作中都能熟练掌握这个公式,让金属切削加工变得更加得心应手!。
金属条切割计算公式

金属条切割计算公式金属条切割是制造业中常见的加工工艺之一,它通常涉及到金属材料的切割、成型和加工。
在进行金属条切割时,需要考虑到切割的精度、速度、切割力、切割角度等因素,以确保切割的质量和效率。
在实际的生产中,通过合理的计算公式可以帮助工程师和操作人员更准确地进行金属条切割,提高生产效率和降低成本。
金属条切割的计算公式主要涉及到切割力、切割速度和切割角度等方面。
下面将分别介绍这些计算公式的应用和原理。
1. 切割力的计算公式。
金属条切割时,需要克服金属材料的抗拉强度才能进行切割。
切割力的大小直接影响到切割的效率和质量。
切割力的计算公式通常可以通过以下公式来计算:F = S × L × K。
其中,F表示切割力,单位为牛顿(N);S表示金属材料的截面积,单位为平方米(m²);L表示金属材料的长度,单位为米(m);K表示金属材料的抗拉强度,单位为牛顿/平方米(N/m²)。
通过这个公式,可以根据金属材料的性能参数来计算出切割时所需的力量,从而选择合适的切割设备和工艺参数,确保切割的顺利进行。
2. 切割速度的计算公式。
切割速度是指切割刀具在单位时间内切割金属材料的长度,通常用米/分钟(m/min)来表示。
切割速度的大小直接影响到切割的效率和切割刀具的寿命。
切割速度的计算公式通常可以通过以下公式来计算:V = N ×π× D。
其中,V表示切割速度,单位为米/分钟(m/min);N表示主轴转速,单位为转/分钟(r/min);π表示圆周率,取3.14;D表示刀具直径,单位为米(m)。
通过这个公式,可以根据切割设备的主轴转速和刀具的直径来计算出切割速度,从而控制切割的速度和质量,确保切割刀具的寿命和切割效率。
3. 切割角度的计算公式。
切割角度是指切割刀具与金属材料表面的夹角,通常用度(°)来表示。
切割角度的大小直接影响到切割的质量和切割刀具的磨损。
切削参数和计算公式
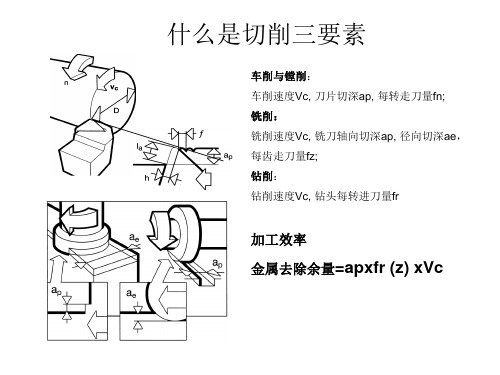
车削功率和扭矩计算
Vc= 3.14 xD xRPM 1000 V=Vc xap xfr(mm3/min) L
举例:车削奥氏体不锈钢外圆,工件硬度HB200, 工 件直径75mm,切深3mm,走刀量0.2mm/r, 切削速度 230m/min, 材料单位切削力为2900N/mm2,加工长度 为100mm RPM=(230X1000)/(3.14X75)=976转每分钟 金属去除率V=230x2x0.2=92 立方厘米每分钟 每加工一个零件的时间=100/(0.2x976)=0.51分钟 车削功率P=(230x3x0.2x2900)/60037.2=6.7千瓦 车削力=2900 x0.2 x3=1740牛顿=177.5公斤 车削扭矩T=1740 x37.5=65牛顿米
P=
Vc xap xfr=46 立方厘米每分钟 每加工一个零件的时间=100/(0.2x488)=1.02分 钟 镗削功率P=(115x3x0.2x2900)/60037.2=3.35千 瓦 镗削力=2900 x0.2 x3=1740牛顿=177.5公斤 镗削扭矩T=1740 x37.5=34牛顿米
N铝=2388rpm vf铝=2865mm/r p铝=9.16kw N不锈钢=597rpm vf不锈钢=716mm/r p不锈钢=6.87kw
T铝=36Nm
T不锈钢=109Nm
U钻钻削功率和扭矩的计算 Power consuming and Torque force
例:工件材料为高合金钢,硬度HRC50,钻削直径20mm,Vc= 40m/min,f=0.07mm/r,Kc=4500N/mm2, =0.9,计算钻削功率和扭矩。
60037.2
T= F力 x(D/2) =P x9549/RPM
切削条件计算公式
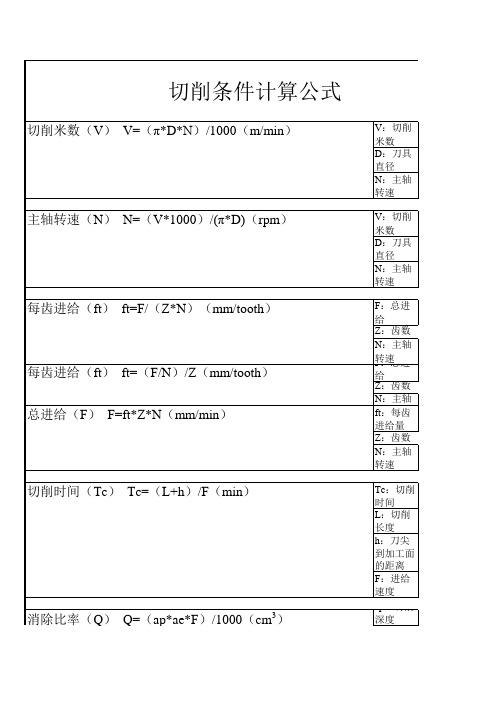
表面粗糙度(h) h=ft2/(40*D)
切削马力(HP) HP=(ap*ae*F*kc)/(60*106*η)(KW)
砂轮线速度的转换公式
Vc:切削米数
切削米数(Vc): Vc=(π*D*n)/1000*60(m/s) 转速(n): n=(Vc*1000*60)/π*D(RPM)
D:砂轮直径 n:主轴转速 Vc:切削米数 D:砂轮直径 n:主轴转速
主轴转速(N) N=(V*1000)/(π*D)(rpm)
每齿进给(ft) ft=F/(Z*N)(mm/tooth) 每齿进给(ft) ft=(F/N)/Z(mm/tooth) 总进给(F) F=ft*Z*N(mm/min)
切削时间(Tc) Tc=(L+h)/F(min)
消除比率(Q) Q=(ap*ae*F)/1000(cm3)
切削米数正常为1~3mm/MIN
V:切削米数 D:刀具直径 N:主轴转速 V:切削米数 D:刀具直径 N:主轴转速 F:总进给
主轴转速(N) N=(V*1000)/(π*D)(rpm) 每转进给(ft) ft=转速*螺距
每转进给(ft) ft=转速*螺距
N:主轴转速
导程的转换公式
导程(L) L=(π*D)/(Tanα)
钻头速度的转换公式
切削米数(V) V=(π*D*N)/1000(m/min)
V:切削米数 D:刀具直径 N:主轴转速 V:切削米数 D:刀具直径 N:主轴转速 F:总进给 N:主轴转速
主轴转速(N) N=(V*1000)/(π*D)(rpm) 每转进给(ft) ft=F/N(mm/tooth)
丝锥速度的转换公式
切削条件计算公式砂轮线速度的转换公式钻头速度的转换公式丝锥速度的转换公式切削米数vvdn1000mminv
常用切削速度计算公式
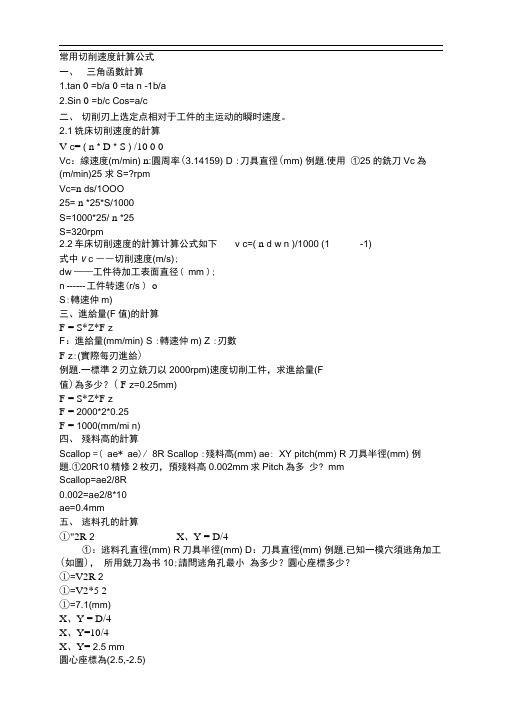
常用切削速度計算公式一、三角函數計算1.tan 0 =b/a 0 =ta n -1b/a2.Sin 0 =b/c Cos=a/c二、切削刃上选定点相对于工件的主运动的瞬时速度。
2.1铣床切削速度的計算V c= ( n * D * S ) /10 0 0Vc:線速度(m/min) n:圓周率(3.14159) D :刀具直徑(mm) 例題.使用①25的銑刀Vc為(m/min)25 求S=?rpmVc=n ds/1OOO25= n *25*S/1000S=1000*25/ n *25S=320rpm2.2车床切削速度的計算计算公式如下v c=( n d w n )/1000 (1 -1)式中v c ――切削速度(m/s);dw ——工件待加工表面直径( mm );n ------ 工件转速(r/s ) oS:轉速仲m)三、進給量(F值)的計算F = S*Z*F zF:進給量(mm/min) S :轉速仲m) Z :刃數F z:(實際每刃進給)例題.一標準2刃立銑刀以2000rpm)速度切削工件,求進給量(F值)為多少?(F z=0.25mm)F = S*Z*F zF = 2000*2*0.25F = 1000(mm/mi n)四、殘料高的計算Scallop =( ae* ae)/ 8R Scallop :殘料高(mm) ae: XY pitch(mm) R 刀具半徑(mm) 例題.①20R10精修2枚刃,預殘料高0.002mm求Pitch為多少? mmScallop=ae2/8R0.002=ae2/8*10ae=0.4mm五、逃料孔的計算①"2R 2 X、Y = D/4①:逃料孔直徑(mm) R刀具半徑(mm) D:刀具直徑(mm) 例題.已知一模穴須逃角加工(如圖),所用銑刀為书10;請問逃角孔最小為多少?圓心座標多少?①=V2R 2①=V2*5 2①=7.1(mm)X、Y = D/4X、Y=10/4X、Y= 2.5 mm圓心座標為(2.5,-2.5)六、取料量的計算Q=( ae* ap*F)/10 0 0Q: 取料量(cm3/min) ae:XY pitch(mm) ap : Z pitch(mm)例題.已知一模仁須cavity等高加工,①35R5的刀XY pitch是刀具的60%每層切1.5mm進給量為2000mm/min求此刀具的取料量為多少?Q=( ae* ap*F)/1000Q= 35*0.6*1.5*2000 /1000Q = 63 cm3/min七、每刃進給量的計算F z =h m * V ( D/ ap )F z:實施每刃進給量h m 理論每刃進給量ap : Z pitch(mm)D:刀片直徑(mm)例題(前提depo XY pitch 是刀具的60%)depo①35R5的刀,切削NAK80材料h m為0.15mm Z軸切深1.5mm 求每刃進給量為多少?F z =h m * V ( D/ ap )F z = 0.2* V 10/1.5F z= 0.5mm沖模刀口加工方法刀口加工深度=板厚—刀口高+鉆尖(0.3D)D表示刀徑鑽頭鑽孔時間公式T(min)=L(min)/N(rpm)*f(mm/rev) =nDL/1000vfL:鑽孔全長N:回轉數f:進刀量系數D:鑽頭直徑v:切削速度如圖孔深1 鑽頭孔全長L 則L=l+D/3T=L/Nf=nDL/1000vf系數表f 直徑mm 進刀mm/rev1.6~3.2 0.025~0.0753.2~6.4 0.05~0.156.4~12.8 0.10~0.2512.8~25 0.175~0.37525 以上0.376~0.6251英寸=25.4mm=8分25.4/牙數二牙距管牙計算公式例如25.4/18 = 1.414 牙距為5/16絲攻馬力(槍鑽)W=Md*N/97.410W:所要動力(KW)Md:扭矩(kg — cm)N:回轉數(r . p . m)扭矩計算公式如下:Md=1/20*f*ps*f為進給量mm/rev系數r為鑽頭半徑賽(mm)a:切削抵抗比值ps.在小進給時,一般鋼為5 0 0 kg/mtf; 一般鑄鐵為300kg/mtf; B1-400K立式升降台铣床主要参数介绍项目单位XA5032 B1-400K 工作面积宽*长mm 320*1250 400*1600工作台承载重量kg 500 800 T型槽数目个 3 3T型槽宽度mm 18 18T型槽间距mm 70 90X向(工作台纵向)手动/机动mm 700/680 900/880行程Y向(滑座横向)手动/机动mm 255/240 315/300 Z向(升降台垂向)手动/机动mm 370/350 385/365 最大回转角度deg ±45 ±45转速r/min 30-1500 300-1500转速级数Step 18 18锥孔ISO7 : 24 NO.50 ISO7 : 24 NO.50 主轴轴向移动距离mm 85 85 主轴端面至工作台距离最小/最大mm 45/415 30/500 主轴中心线至床身垂直导轨面距离mm 350 450切削进给速度mm/minX , Y : 23.5-1180, Z:8-394 X : 19-950 Y : 12.6-634 Z:6.3-317进给快速移动进给速度mm/min X, Y: 2300, Z: 770 X, Y: 2300, Z: 770 进给级数Step 18 18电动主轴电机功率KW 7.5 11机进给电机功率KW 1.5 3其他机床外形尺寸(长*宽*高)mm 2272*1770*2094 2556*2159*2298 机床净重(约)kg 2800 4250。
切削加工常用计算公式
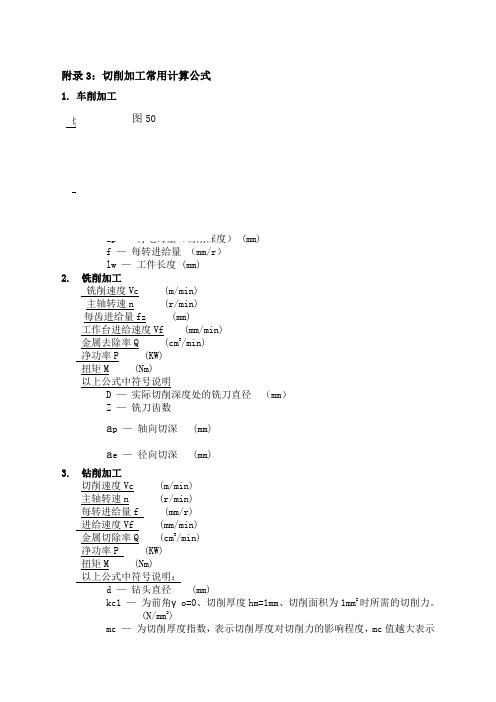
附录3:切削加工常用计算公式
(mm)
f —每转进给量(mm/r)
lw —工件长度 (mm)
2. 铣削加工
铣削速度Vc (m/min)
主轴转速n (r/min)
每齿进给量fz (mm)
工作台进给速度Vf (mm/min)
金属去除率Q (cm3/min)
净功率P (KW)
扭矩M (Nm)
以上公式中符号说明
D —实际切削深度处的铣刀直径(mm)
Z —铣刀齿数
a p —轴向切深 (mm)
a e —径向切深 (mm)
3. 钻削加工
切削速度Vc (m/min)
主轴转速n (r/min)
每转进给量f (mm/r)
进给速度Vf (mm/min)
金属切除率Q (cm3/min)
净功率P (KW)
扭矩M (Nm)
以上公式中符号说明:
d —钻头直径 (mm)
kc1 —为前角γo=0、切削厚度hm=1mm、切削面积为1mm2时所需的切削力。
(N/mm2)
mc —为切削厚度指数,表示切削厚度对切削力的影响程度,mc值越大表示
切削厚度的变化对切削力的影响越大,反之,则越小—前角(度)
γ
o。
刀具参数计算公式

H 2General technical informationTurning calculation formulaen Speed rpm D c Cutter diameter mm v c Cutting speed m/min v f Feed rate mm/minf Feed per revolution mm Q Metal removal ratecm 3/min a p Depth of cut mm A Chip cross sectionmm 2h Chip thickness mm b Chip width mmκ Approach angle °F c Main cutting power N k c1.1* Specific cutting force N/mm 2 for 1 mm² chip cross-section m c * Increase in the k c curveP mot D rive power kWt h Cutting time min l m Length of cut mmR max Roughness profile depth μm r Corner radius of the insert mm η Efficiency of machine (0.75 – 0.9)*m c and k c 1.1 see table on page H 7车削计算公式转速刀具直径切削速度进给速度每转进给量金属去除率切深切屑截面积切屑厚度切屑宽度主偏角主切削力每1mm ²切屑截面积上的单位切削力Kc曲线坡度所需功率切削时间加工长度粗糙度表面微观结构的最大深度刀片半径机床效率系数H 3General technical informationDrilling calculation formulaen Speed rpm D c Cutter diametermm z Number of teethv c Cutting speed m/min v f Feed rate mm/min f z Feed per tooth mm f Feed per revolution mm A Chip cross section mm 2Q Metal removal ratecm 3/min P mot D rive power kWM c Torque Nm F f Axial force Nh Chip thickness mm k c Specific cutting forceN/mm 2η Efficiency of machine (0.7–0.95)κ Approach angle °k c1.1* Specific cutting force N/mm 2 for 1 mm² Chip cross section with h = 1 mm m c * Increase in the k c curve *m c and k c 1.1 see table on page H 7孔加工计算公式转速刀具直径进给速度切削速度每齿进给量金属去除率齿数每转进给量切屑截面积切屑厚度主偏角进给力每1mm ²切屑截面积上的单位切削力Kc曲线坡度所需功率机床效率系数扭矩单位切削力c /2H 4General technical informationn Speed rpmD c Cutter diameter mm a p Depth of cut mm a eWidth of cut mm z Number of teethv c Cutting speed m/min v f Feed rate mm/min f z Feed per tooth mm Q Metal removal rate cm 3/minP motD rive power kW h m Medium chip thickness mm k cSpecific cutting force N/mm 2η Efficiency of machine (0.7–0.95)κ Approach angle °φs Engagement angle °φ1 Up-cut milling area °φ2 Synchronous milling area °k cSpecific cutting force N/mm 2k c1.1* Specific cutting force N/mm 2for 1 mm 2chip cross section m c *Increase in the k c curve y Reverse engagement mm*m c and k c1.1 see table on page H 7Milling calculation formulaeSpeed铣削计算公式转速转速刀具直径切深切宽齿数切削速度进给速度每齿进给金属去除率所需功率平均切屑厚度单位切削力机床效率系数主偏角每1mm ²切屑截面积上的单位切削力Kc曲线坡度逆向切削单位切削力压力角逆铣范围顺铣范围D vH 5General technical informationEngagement ratio for external circular interpolationEngagement ratio for internal circular interpolationExternal profile feed rateExternal contour v fa Feed rate of tool axis [mm/min]D a Cutter outer diameter [mm]D m Mid-point path diameter [mm]D v Workpiece raw diameter[mm]D w Workpiece machined diameter [mm]a e Material removal [mm]n Speed [rpm]f z Feed per tooth [mm]zNumber of teethInternal contour v fi Feed rate of tool axis [mm/min]D a Cutter diameter [mm]D v Workpiece raw diameter [mm]D w Workpiece machined diameter [mm]n Speed [rpm]Internal profile feed rate外圆插补铣切削比例外部轮廓进给速度外部轮廓外部轮廓进给速度铣刀外径中心轨迹直径工件毛坯直径工件成品直径切削宽度转速每齿进给齿数内部轮廓进给速度转速工件成品直径工件毛坯直径铣刀直径内部轮廓进给速度内部轮廓H 6General technical informationThread machining calculation formulaeSpeedThread milling calculation formulae转速螺纹加工计算公式螺纹铣削计算公式。