炼钢应运计算
炼钢工艺流程简介
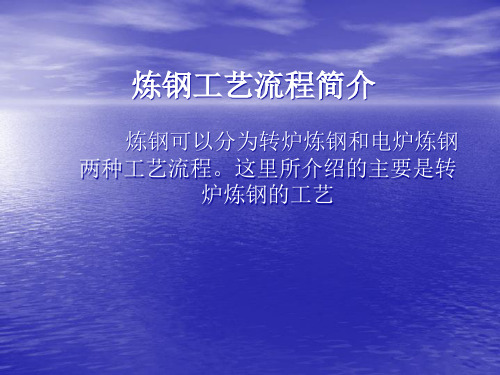
这是火焰切割的场景。
★铸坯的输送
经切割的铸坯利用辊道输送至冷床。这是铸坯 在运输辊道上的场景。
★铸坯的收集(冷床,推钢)
连铸坯通过步进式翻转冷床冷却,然后由推钢 机收集。这就是步进式冷床场景。
★铸坯堆垛
用夹钳将铸坯从冷床上吊至指定的堆放 场地码放成垛,等待外运。
这就是成品铸坯垛场景。
★铸坯外运
★测温取样
每炉钢出钢前必须符合工艺规定的温 度和化学成分的要求,因此冶炼到一定阶 段需要倒炉进行测温取样。温度在现场大 屏幕和主控室计算机上均有显示,试样则 需送到炉前化验室经直读光谱仪分析再报 出结果。
这就是炉前工正在测温取样的场景。
★转炉出钢
出钢过程中要实现的目标是脱氧、脱碳、 脱硫、合金化,为此要向钢包中加入铁合 金、脱氧剂、脱硫剂、覆盖剂等。为了实 现无渣或少渣出钢还得投抛挡渣球。
★向混铁炉兑入铁水
混铁炉是一种贮存铁水的容器,通过 多包铁水混兑可以均匀铁水温度和成分, 为转炉冶炼创造更好的原料条件。此外由 于混铁炉容量较大,它还是调节高炉和转 炉生产节奏的缓冲器。
这就是向混铁炉兑入铁水的场景。
★混铁炉出铁
根据转炉生ห้องสมุดไป่ตู้的需要,混铁炉随时可提供一定量的铁 水。这是混铁炉出铁的场景。出铁量通过铁水车上的电子 秤称量并在大屏幕上显示。
电弧炉炼钢是除转炉炼钢以外最主要的炼钢 方法,与转炉炼钢相比主要区别在于使用的原料 不一样:转炉主原料是铁水,有足够的热源,故 只要吹氧就可以了;而电炉则不同,其主要原料 是废钢,必须输入足够的能量才能将其熔化,而 电弧加热是很成熟的工业化大生产加热方法,故 电弧炉就自然成为以废钢为主原料的炼钢工艺所 选择的炉型了。除此而外现代化超高功率电炉炼 钢与转炉炼钢有许多相似之处,如吹氧氧化、挡 渣出钢、炉外精炼、连铸等二者无大差别。另外, 很多有电炉的厂也建高炉,采取向电炉加入一定 量铁水(一般为30%左右)代替废钢,这就是电 炉工艺与转炉更拉近一步。
转炉炼钢岗位作业规程

转炉炼钢岗位作业规程转炉炼钢岗位作业规程转炉炼钢岗位作业规程:1使用设备1.1公称80t转炉1.2氧枪系统1.3喷补机1.4测温仪表1.5挡渣小车1.6合金旋转溜槽1.7叉子车1.8拆炉机2设备功能2.1转炉:冶炼。
2.2氧枪系统:供氧吹炼、移换氧枪。
2.3喷补机:喷补炉衬。
2.4测温仪表:测定温度。
2.5挡渣小车:加挡渣锥减少出钢下渣。
2.6合金旋转溜槽:加合金2.7叉子车:运送合金。
2.8拆炉机:清理炉头及更换出钢口。
3技术标准3.1产品标准按照转炉炼钢工艺技术规程的标准执行,品种钢按质量计划执行。
3.2温度控制执行附录B《温度控制标准》。
4操作内容4.1生产准备4.1.1炉长必须明确并传达本班生产作业计划。
4.1.2炉长必须向上班询问生产和操作情况。
4.1.3炉长接班后必须检查炉况、出钢口,并指挥炉前工测量炉底和枪位。
4.1.4摇炉工接班后必须检查炉体倾动机构,操枪工检查氧枪升降机构、加料工检查散装料系统,合金工检查挡渣小车及合金旋转溜槽。
4.1.5合金工必须准备好样勺两把,备好脱氧剂,明确合金料成分。
4.1.6炉前工必须检查测温仪表,领取测温头,取样器,准备好挡渣帽、挡渣球、碳粉、覆盖剂、补炉料,冶炼高碳钢时还必须准备好定碳仪、定碳杯等工具。
4.1.7兑铁水工必须明确铁水包号、包皮及相应容重。
4.1.8废钢工必须检查吊具,明确交班废钢重量。
4.2平时操作4.2.1兑铁水4.2.1.1补炉后第一炉兑铁水时,应先缓慢倒入5-8吨铁水烫炉5分钟,然后将余下铁水缓慢倒入炉内。
4.2.1.2兑入回炉钢水必须称量,并在兑加前通知炉长。
4.2.1.3兑加铁水时铁水工应站在天车工和摇炉工均能看见的位置,手势明确,哨音响亮,严禁将铁水泼在炉头上和倒入炉坑内。
4.2.1.4认真做好《转炉炼钢吹炼操作记录表》的原始记录。
4.2.2加废钢4.2.2.1废钢块度及单重按执行《公司废钢标准》。
4.2.2.2废钢加入量必须严格按工艺技术规程要求装入,班中必须做到及时称量、挂钩,不影响转炉生产。
炼钢全流程协同优化控制模型的开发与应用

炼钢全流程协同优化控制模型的开发与应用1. 引言1.1 概述在现代工业领域中,炼钢是一个非常重要的过程。
然而,在传统的炼钢生产中,存在着许多问题,如过程不稳定、生产周期长、能耗高等。
这些问题给企业带来了巨大的经济损失和环境负担。
因此,如何提高炼钢过程的效率和控制精度成为了一个迫切需要解决的问题。
1.2 背景介绍近年来,随着信息技术的飞速发展,协同优化控制技术逐渐引起了人们的关注并得到广泛应用。
该技术通过建立全流程控制模型,并运用最先进的优化算法对炼钢过程进行优化调整。
这种技术可以实现各个环节之间的协同工作,实现整个炼钢过程的高效运行。
1.3 研究意义本文旨在开发和应用一种全新的炼钢全流程协同优化控制模型,以期提高炼钢过程的效率和质量,并降低生产成本和能源消耗。
通过将先进的协同优化技术与炼钢过程相结合,本研究将为炼钢行业的发展提供新思路和方法。
通过本文的研究,我们将探索以下问题:- 炼钢全流程控制模型的构建原理和方法;- 协同优化技术在炼钢中的应用实践;- 模型开发与验证过程中的关键环节及其效果评估。
本研究成果对于提高我国炼钢工业的技术水平、降低生产成本、促进可持续发展具有重要意义。
同时,也能为其他行业以及整个国民经济的增长做出一定贡献。
尽管存在一些挑战和难题,但我们有足够的信心通过本次研究取得令人满意的成果。
2. 炼钢全流程控制模型2.1 炼钢过程概述炼钢是将生铁通过高温熔化、精炼、调质等一系列物理和化学变化得到合格钢材的过程。
该过程通常包括原料准备、融化炉冶炼、精炼处理以及连铸等阶段。
每个阶段都必须进行有效的控制,以确保产品质量、提高生产效率和降低能耗。
2.2 控制模型基础原理控制模型是指基于系统动力学理论构建的描述炼钢过程中各环节相互关系的数学模型。
其基本原理是利用质量守恒定律、能量守恒定律和动量守恒定律来描述不同环节之间的物料传递、能量转移和动力平衡关系。
通过对这些关系进行建模和分析,可以更好地理解整个流程,并为优化控制提供依据。
炼钢厂原材料和废钢安全规定

炼钢厂原材料和废钢安全规定炼钢厂是一个重要的工业生产环节,涉及到大量的原材料和废钢处理。
为了确保炼钢过程的安全和可持续性发展,必须有一系列的安全规定来指导和管理原材料和废钢的使用、储存和处理。
以下是炼钢厂原材料和废钢的安全规定的主要内容。
一、原材料的安全规定:炼钢厂的原材料主要包括铁矿石、焦炭、石灰石等。
为了确保原材料的安全使用,需要采取以下措施:1. 原材料的储存:原材料的储存需要选择合适的场所,并确保其干燥、通风和防火安全。
储存场所应远离火源和易燃物,并保持储存区域的通道畅通,以便紧急情况下的疏散和救援。
2. 原材料的运输:原材料的运输过程中需要严格遵守安全操作规程,确保货物牢固安全地固定在运输工具上,并遵守道路交通规则。
3. 原材料的装卸:原材料的装卸需要使用适当的设备和工具,并严格遵守相关的操作规程。
装卸操作人员需要经过专业培训,熟悉装卸过程中的安全要求和操作流程。
4. 原材料的使用:原材料在炼钢过程中的使用需要符合相关的工艺要求,并确保操作人员的安全意识和防护措施。
二、废钢的安全规定:废钢是炼钢厂的重要原料之一,也是一种危险废物。
为了安全处理和利用废钢,需要采取以下安全规定:1. 废钢的储存和分类:废钢需要分类储存,确保不同类型的废钢不会混合在一起。
储存场所应具备防火、防尘和防雨等安全设施,废钢的堆放需要满足安全和稳定要求,并保持通道畅通,以便紧急情况下的疏散和救援。
2. 废钢的运输和装卸:废钢的运输需要严格遵守相关的运输规定和安全操作流程,确保货物的安全固定和运输工具的稳定。
废钢的装卸过程中,需要使用适当的设备和工具,并严格遵守相关的操作规程。
3. 废钢的处理和利用:废钢的处理和利用需要严格按照环境保护和安全规定进行。
废钢的处理过程中需要合理使用防尘设施和防火设施,确保废钢的处理和利用过程中的安全和环保。
对于不能再利用的废钢,需要按照相关的废物处理规定进行妥善处置。
4. 废钢的回收利用:炼钢厂的废钢回收利用是实现资源循环利用的重要环节。
炼钢工艺流程简介

炼钢工艺流程简介炼钢厂目前共有大小转炉11座,其中炼钢一厂8座,分别为40吨转炉4座,80吨转炉1座,100吨转炉3座;炼钢二厂150 吨转炉3座。
炼钢系统的主要工艺流程为:转炉兑铁——冶炼——出钢——钢包吹氩——LF精炼炉——方坯连铸工艺。
•铁水供应转炉炼钢所需铁水用钢包或鱼雷罐由炼铁厂运往炼钢厂。
高炉运来的铁水除一部分兑入混铁炉贮存外,其余铁水经倒包调整和称量作业,保证入炉铁水控制在所需的范围。
需要进行脱硫处理的铁水,由天车运往脱硫站进行脱硫处理,不需处理的铁水,直接兑入转炉。
转炉兑铁铁水是转炉炼钢最主要的金属料,一般占转炉金属料70%以上。
铁水的成分、温度是否适当和稳定,对简化、稳定转炉操作,保证冶炼顺行以及获得良好的技术经济指标都十分重要。
•废钢供应在炼钢厂设有废钢库,外来的废钢由汽车运到废钢库存放。
废钢铁通过磁盘吊车按不同配比和装料顺序装入废钢料槽,由天车加入转炉。
转炉加冷料转炉炼钢时,由于热量富裕,可以加入多达30%的废钢,作为调整吹炼温度的冷却剂。
采用废钢冷却,可以降低铁水量、造渣材料和氧气的消耗,而且比用铁矿石冷却的效果稳定,喷溅少。
•散状原料供应(石灰、铁皮球、镁球等)1、100吨转炉炼钢散状原料上料系统选用皮带上料工艺。
散状原料通过汽车运到地下受料仓,由垂直皮带运送到42m平台,再由水平皮带运输机和布料小车装入相应的料仓。
转炉加料画面2、加料系统布置在转炉的上方,每座转炉有一套炉顶料仓,每套有10个炉顶料仓,分别为调渣剂、脱硫剂、石灰、铁皮球、镁球、萤石、包渣料仓等。
料仓中的散状料分别通过振动给料器→称量斗→汇总斗→下料溜管,加入转炉。
•铁合金供应100吨转炉设有一组铁合金料仓,由10个铁合金料仓组成.,为3座转炉供应合金料。
铁合金是脱氧及合金化材料。
用于钢液脱氧的铁合金叫做脱氧剂;用于调整钢液成分的铁合金叫做合金剂。
炼钢常用的铁合金有:硅铁、锰铁、钒铁、钼铁、硅钙合金等。
•转炉冶炼炼钢是通过氧化反应脱碳、升温、合金化的过程。
智能化炼钢厂制造执行系统的研究与应用

智能化炼钢厂制造执行系统的研究与应用摘要:随着工业4.0时代的到来,智能制造已成为制造业发展的重要方向。
作为湘潭钢铁集团的一名工程师,本文将对智能化炼钢厂制造执行系统(MES)的研究与应用进行深入探讨,着重分析MES在炼钢生产过程中的优化、监控和调度作用,以期推动炼钢行业的智能化和可持续发展。
一、引言炼钢生产作为钢铁行业的核心环节,其生产效率和质量直接影响到整个钢铁产业链的竞争力。
随着制造业数字化、网络化和智能化的快速发展,炼钢企业需要利用先进技术手段实现制造过程的自动化、智能化和柔性化。
本文首先概述了制造执行系统的基本概念和功能,然后分析了智能化炼钢厂MES的研究与应用现状,并重点探讨了MES在炼钢生产过程中的优化、监控和调度作用。
二、制造执行系统(MES)概述制造执行系统(MES)是一种生产管理信息系统,位于企业资源计划(ERP)系统和现场自动化控制系统之间,其主要功能包括生产调度、数据采集与分析、质量管理和维护管理等。
MES能够实现生产过程的实时监控和控制,提高生产效率、降低生产成本,确保产品质量,为企业决策提供数据支持。
三、智能化炼钢厂MES的研究与应用现状智能化炼钢厂MES的研究与应用现状在以下几个方面取得了显著的进展:3.1基于大数据技术的生产数据分析:炼钢厂产生了大量的生产数据,包括原料、能源、工艺参数、设备状态、产品质量等。
利用大数据技术对这些数据进行挖掘和分析,可以发现生产过程中存在的问题,为生产调度和优化提供支持。
通过对历史数据的分析,可以预测生产过程中可能出现的异常情况,从而提前采取措施避免生产事故的发生。
炼钢生产过程中,产品质量受到众多因素的影响。
利用人工智能技术,如机器学习和深度学习,可以根据历史数据建立质量预测模型,实现对炼钢过程中产品质量的实时预测和监控。
此外,人工智能技术还可以用于优化生产参数,实现质量控制的自动化和智能化。
物联网技术可以实现设备的实时监控和远程控制,有效提高设备利用率和维护效率。
钢板承重计算

钢板承重计算
钢板承载力的计算公式是σ=Fb/So。
钢板在拉伸过程中,经过屈服阶段后进入强化阶段后随着横向截面尺寸明显缩小在拉断时所承受的最大力(Fb),除以试样原横截面积(So)所得的应力(σ),称为抗拉强度或者强度极限(σb),单位为N/(MPa)。
它表示金属材料在拉力作用下抵抗破坏的最大能力。
计算公式为:σ=Fb/S o。
扩展资料:
当钢材屈服到一定程度后,由于内部晶粒重新排列,其抵抗变形能力又重新提高,此时变形虽然发展很快,但却只能随着应力的提高而提高。
之后钢材抵抗变形的能力明显降低,并在最薄弱处发生较大的塑性变形,此处截面迅速缩小,出现颈缩现象,直至断裂破坏。
单位:N/mm^2(单位面积承受的公斤力)
国内测量抗拉强度比较普遍的方法是采用万能材料试验机等来进行材料抗拉/压强度的测定。
对于脆性材料和不成形颈缩的塑性材料,其拉伸最高载荷就是断裂载荷,因此,其抗拉强度也代表断裂抗力。
对于形成颈缩的塑性材料,其抗拉强度代表产生最大均匀变形的抗力,也表示材料在静拉伸条件下的极限承载能力。
对于钢丝绳等零件来说,抗拉强度是一个比较有意义的性能指标。
抗拉强度很容易测定,而且重现性好,与其他力学性能指标如疲劳极限和硬度等存在
一定关系,因此,也作为材料的常规力学性能指标之一用于评价产品质量和工艺规范等。
Q195炼钢要求

Q195钢工艺操作默认分类2010-09-20 20:54:12 阅读58 评论0 字号:大中小订阅一、工艺流程:转炉→LF精炼→矩坯连铸→切割检验→发运装车二、原料:技术要求1、兑铁前必须取铁样分析,铁水[S]≤0.050%。
2、铁水温度>1250℃。
3、准备Fe-Si、Mn-Si、Ba-Al-Si合金.要求合金干净、干燥,阴雨天送合金时必须用栅布遮盖.4、炼钢前一天,合金上料工提供准确的合金成份,并登记在炉前黑板上。
三、转炉操作:(一)、化学成份(%)钢种液相温度:T=1523℃。
(二)、冶炼控制:1、开新炉前10炉、大补炉后第一炉不得冶炼此钢种。
2、造渣制度:造渣采用单渣操作,要保证早化渣、化好渣、中期不返干,终渣碱度按2.8—3.2控制。
3、终点控制:1)提倡一次倒炉,必要是可以补吹,但补吹次数≯1次,确保C-T协调出钢。
2)终点目标:C=0.06—0.08%; P≤0.025%出钢温度第一炉1685--1705℃第二、三炉 1675--1695℃; 连拉炉1665--1685℃4、脱氧合金化、出钢1)采用硅锰铁、硅铁和硅铝钡脱氧合金化。
锰的回收率按85—90%、硅的回收率按80—85%。
Mn/Si>2.2参考加入量:硅锰按6.5Kg/t.s、硅铁按0.9Kg/t.s、硅铝钡按1.0—1.5Kg/t.s配加2)出钢:(1)钢包采用干净的红热周转包,严禁使用新包。
(2)出钢前堵挡渣帽,出钢3/4-4/5时加挡渣球,要求钢包渣层厚度小于80mm。
(3)脱氧合金化次序: 当钢水出至1/4后,顺序加入硅锰→硅铁→硅铝钡(4)出钢口要维护好,保证钢流圆整,出钢时间不小于3分钟。
(5)出钢过程中钢包要底吹氩操作。
四、精炼操作要点1、进站温度要求第一炉1610--1630℃第二、三炉1605--1625℃连拉炉1595--1615℃2、钢水进站后要测温、取样,根据温度、上钢时间决定是否加热;根据钢包样决定是否调整成分,即Mn/Si<2或[Mn]≤0.40%,加锰铁调成分。
炼钢安全规程(适用于炼钢厂的设计、设备制造、施工安装、生产和设备检修)

炼钢安全规程1 范围本标准规定了炼钢安全生产的技术要求。
本标准适用于炼钢厂的设计、设备制造、施工安装、生产和设备检修。
2 规范性引用文件下列文件对于本文件的应用是必不可少的。
凡是注日期的引用文件,仅注日期的版本适用于本文件。
凡是不注日期的引用文件,其最新版本(包括所有的修改单)适用于本文件。
GB2894安全标志及其使用导则GB4053.1 固定式平台及钢梯安全要求第1部分:钢直梯GB4053.2 固定式平台及钢梯安全要求第2部分:钢斜梯GB4053.3 固定式平台及钢梯安全要求第3部分:工业防护栏杆及钢平台GB4387 工业企业厂内铁路、道路运输安全规程GB/T5082起重吊运指挥信号GB5768.2 道路交通标志和标线第2部分:道路交通标志GB5768.3 道路交通标志和标线第3部分:道路交通标线GB/T5972 起重机钢丝绳保养、维护、安装、检验和报废GB/T6067.1起重机械安全规程第1部分:总则GB6222 工业企业煤气安全规程GB6722 爆破安全规程GB7231 工业管道的基本识别色、识别符号和安全标识GB14784 带式输送机安全规范GB16912 深度冷冻法生产氧气及相关气体安全技术规程GB/T 20801.6 压力管道规范工业管道第6部分:安全防护GB28664炼钢工业大气污染物排放标准GB/T29639 生产经营单位生产安全事故应急预案编制导则GB/T33000企业安全生产标准化基本规范GB50016 建筑设计防火规范GB50030 氧气站设计规范GB50034 建筑照明设计标准GB50057建筑物防雷设计规范GB50058爆炸危险环境电力装置设计规范GB50140 建筑灭火器配置设计规范GB50184 工业金属管道工程施工质量验收规范GB50235 工业金属管道工程施工规范GB50236 现场设备、工业管道焊接工程施工规范GB50316 工业金属管道设计规范GB50683 现场设备、工业管道焊接工程施工规范GB50414 钢铁冶金企业设计防火规范GB50439炼钢工程设计规范GB50603钢铁企业总图运输设计规范GBJ22 厂矿道路设计规范GBZ/T205密闭空间作业职业危害防护规范DL408电业安全工作规程TSG D0001 压力管道安全技术监察规程-工业管道3 术语和定义下列术语和定义适用于本文件。
炼钢—连铸生产计划与调度的优化方法研究及应用

2023-11-02CATALOGUE 目录•引言•炼钢—连铸生产计划优化方法•炼钢—连铸生产调度优化方法•炼钢—连铸生产计划与调度优化的应用与实践•结论与展望01引言研究背景与意义炼钢-连铸是钢铁生产的核心环节,优化生产计划与调度对于提高生产效率、降低成本具有重要意义。
当前炼钢-连铸生产计划与调度存在一些问题,如计划制定不准确、调度调整不及时等,需要进行深入研究。
本研究旨在探索炼钢-连铸生产计划与调度的优化方法,提高生产计划的准确性和调度的及时性,为钢铁企业的生产管理提供理论支持和实践指导。
本研究以炼钢-连铸生产计划与调度为研究对象,针对现有问题,研究优化方法。
具体研究内容包括:生产计划的制定、调整和执行,生产进度的监控和调整,生产过程的仿真和优化等。
研究方法本研究采用理论研究和实证研究相结合的方法。
首先,通过文献综述和市场调研,了解炼钢-连铸生产的现状和问题;其次,运用系统分析方法,对炼钢-连铸生产计划与调度进行深入分析;最后,通过实验验证和实际应用,评估优化方法的可行性和效果。
研究内容研究内容与方法VS02炼钢—连铸生产计划优化方法基于遗传算法的炼钢—连铸生产计划优化炼钢—连铸生产特点炼钢—连铸生产具有多目标、多约束、大规模的特点,适用于遗传算法进行优化。
算法设计与实现设计适应度函数、选择算子、交叉算子和变异算子,实现基于遗传算法的炼钢—连铸生产计划优化。
遗传算法概述遗传算法是一种基于生物进化原理的优化算法,适用于解决大规模、复杂的优化问题。
03算法设计与实现设计初始解、邻域结构、状态转移规则和终止条件,实现基于模拟退火算法的炼钢—连铸生产计划优化。
基于模拟退火算法的炼钢—连铸生产计划优化01模拟退火算法概述模拟退火算法是一种概率型优化算法,通过模拟金属退火过程来寻找问题的最优解。
02炼钢—连铸生产优化问题建模建立炼钢—连铸生产优化问题的数学模型,包括目标函数、约束条件和变量。
1基于粒子群算法的炼钢—连铸生产计划优化23粒子群算法是一种基于群体行为的优化算法,通过模拟鸟群飞行觅食行为来寻找问题的最优解。
炼钢工序时间节点安排

炼钢区域各工序时间节点安排一、进LF炉的SPHC类钢种总体时间控制原则,单开前两炉钢水转炉开始—连铸开浇时间≤180min,连浇炉次钢水转炉开始—连铸开浇时间≤150min。
各工序时间节点具体安排如下:1、转炉兑铁—出钢结束按38min(±2min)控制;2、出钢结束—吹氩站出站按6min(±1min)控制;3、吹氩站至LF炉进加热位过程时间(含翻渣)<25min;4、LF炉处理单开前两炉按≥70min;其它连浇炉次按≥60min5、LF炉出站至连铸台时间按8min、钢水上台镇静时间≥10min;6、连铸浇铸时间(先进拉速设计,单开炉次加2min):1)1018mm断面按照50min/炉;2)1100—1200mm断面按照46min/炉;3)1200—1300mm断面按照42min/炉;4)1518mm断面按照39min/炉。
7、连铸浇铸时间由于钢水量、温度、拉速等原因与设定先进水平有所差异,因此需要转炉、LF炉的节点根据连铸开浇时间和拉速做动态调整;8、转炉具体的生产原则是:前两炉按照顺序生产,第3炉在LF炉单开出站时出完钢,第4炉以满足LF炉翻渣节点倒推时间(大包浇铸至50—60吨为参考),以此类推;9、前道工序节点出现延误时,需要及时协调吹氩站、吊运等环节的做好相应的补位工作;10、1500mm的Q235B的生产节点参照≥1268mm先进拉速水平的节点控制。
二、电工钢进LF炉的SPHC类钢种总体时间控制原则,单开钢水(MGW1300、800)转炉开始—连铸开浇时间≤150min(MGW600≤140min),连浇炉次钢水(MGW1300、800)转炉开始—连铸开浇时间≤130min(MGW600≤140min)。
各工序时间节点具体安排如下:1、转炉兑铁—出钢结束按36min(±2min)控制2、出钢结束—吹氩站出站按10min(±1min)控制;3、吹氩站至RH炉进处理位过程时间<20min;4、RH炉处理单开按55min,连浇炉次按50min5、RH炉出站至连铸台时间按15min、钢水上台镇静时间≥10min;6、连铸浇铸时间(先进拉速):1)MGW1300按照53min/炉;2)MGW800(1230mm以上断面)按照55min/炉,窄端面时间相应延长;3)MGW600及以上牌号按照65min/炉2.连铸浇铸时间由于钢水量、温度、拉速等原因与设定先进水平有所差异,因此需要转炉、RH炉的节点根据连铸开浇时间和拉速做动态调整;3.转炉具体的生产原则是:第2炉在单开出吹氩站开始兑铁,第3炉在RH炉单开出站时兑铁,第4炉根据连铸拉速、断面、坯厚决定转炉兑铁时间(低牌号钢水出RH炉时、中高牌号钢水进RH炉工位后),以此类推;4.前道工序节点出现延误时,需要及时协调吹氩站、吊运等环节的做好相应的补位工作;。
转炉炼钢工序低成本运行探讨

工作研究转炉炼钢工序低成本运行探讨徐 韬(宝武钢铁集团八钢公司炼钢厂,新疆 乌鲁木齐 830022)摘 要:转炉炼钢成本主要是钢材消耗,钢铁原料中的一些铁被消耗掉,只有一部分被转移到钢坯或其他半成品中,但一些消耗的铁可以被回收利用,如钢包、钢包和中间包中的残渣。
这种可回收的原料在钢铁工业中是可以回收的,不可回收的消耗品是转炉渣。
据有关资料显示,在我国转炉炼钢中,炉渣量可达90kg/T左右,这种炉渣可用于制球团矿。
目前主要用于道路施工或其他层面。
钢铁是发展钢铁经济和工业生产绿色经济的重要组成部分。
在转炉冶炼过程中,铁占不可弥补损失的90%以上。
不可回收的消耗相对较低,可通过降低渣中总铁含量,即减少渣量,加大对可回收金属及钢渣的利用,提高转炉工序的能源回收,才能达到低成本运行和绿色经济的目的。
关键词:转炉炼钢;工序;低成本;运行1精料方案的实行减少钢渣量对于钢铁行业炼钢环节来说是降低成本的一个主要方向。
每吨钢中约有80-200公斤的炉渣。
根据垃圾的结构和浓度,可以减少炉渣。
精矿和稳定成分是转炉原辅材料的重要标准。
在转炉炼钢中,精矿是影响渣量的关键因素,产品的成本和质量对渣量也有很大的影响。
炼钢的另一个标准是整体稳定性,这是转炉炼钢自动化技术所不可缺少的。
采用高温铁水可以大大降低炼钢成本,这主要取决于铁水本身的性能。
对于高温铁水,其内部物理热优于自身的有机化学热。
在炼钢过程中,冶炼过程的有机化学热过高,会导致炼钢过程中氧气及渣料消耗过多。
同时,有机化学热量过高的热量也会增加炼钢过程中石灰的消耗,造成成本的增加。
采用提高铁水温度的方法,可以大大降低铁水中的有机化学热。
铁水中的物理热量高,可以降低铁水加入的比例,增大废钢加入比例,平衡炉内热力学条件,提高氧气的利用率,从而从本质上降低生产过程的成本。
高炉应避免炉渣过多。
高炉渣中含有多种化学元素。
一般来说,高炉渣中的硫含量是铁水本身硫含量的30~40倍。
高炉渣本身呈碱性,转炉渣本身呈强酸性。
钢材许用量计算公式

钢材许用量计算公式钢材在建筑、制造和其他领域中起着至关重要的作用。
在设计和使用钢材时,需要考虑其许用量,以确保结构的安全性和可靠性。
钢材许用量是指在特定条件下,钢材可以承受的最大应力或变形量。
为了计算钢材的许用量,需要使用相应的计算公式。
本文将介绍钢材许用量的计算公式及其应用。
钢材许用量的计算公式通常包括两个方面,拉伸许用应力和压缩许用应力。
拉伸许用应力是指材料在拉伸状态下可以承受的最大应力,而压缩许用应力是指材料在压缩状态下可以承受的最大应力。
下面将分别介绍拉伸许用应力和压缩许用应力的计算公式。
拉伸许用应力的计算公式如下:\[ \sigma = \frac{F}{A} \]其中,σ表示拉伸应力,单位为N/m²或Pa;F表示受力,单位为N;A表示横截面积,单位为m²。
压缩许用应力的计算公式如下:\[ \sigma = \frac{F}{A} \]其中,σ表示压缩应力,单位为N/m²或Pa;F表示受力,单位为N;A表示横截面积,单位为m²。
在使用这些公式时,需要注意以下几点:1. 计算时需要准确测量材料的横截面积,以确保计算结果的准确性。
2. 在计算拉伸和压缩应力时,需要考虑材料的弹性模量。
弹性模量是材料在弹性变形范围内的应力和应变之比,通常用E表示。
拉伸和压缩应力的计算公式中的A都是指材料的有效横截面积,即在考虑弹性模量的情况下的横截面积。
3. 在实际工程中,还需要考虑材料的屈服强度和断裂强度。
屈服强度是指材料开始产生塑性变形的应力值,通常用σy表示;断裂强度是指材料发生断裂的应力值,通常用σf表示。
在计算许用量时,需要确保拉伸或压缩应力不超过材料的屈服强度和断裂强度。
除了拉伸和压缩应力的计算公式外,还有一些特殊情况需要考虑。
例如在受到横向力作用时,材料会产生剪切应力。
剪切应力的计算公式如下:\[ \tau = \frac{F}{A} \]其中,τ表示剪切应力,单位为N/m²或Pa;F表示受力,单位为N;A表示受力面积,单位为m²。
中铁钢材组织供应、运输、售后服务方案

中铁钢材组织供应、运输、售后服务⽅案中铁钢材组织供应、运输、售后服务⽅案⼀、组织供应1、运营能⼒(1)⼈⼒资源:本公司⼈⼒资源充⾜,有着良好的信誉,采购⼈员可以随时调配,在采购上不存在问题。
(2)运输调度:我公司所在地与交货地点(xx项⽬经理部)距离较近、交通便利,在运输⽅⾯基本可以做到随时到货。
(3)相关管理措施:我公司采⽤⾦字塔式管理,有专门的配送⼈员、技术⼈员以及采购⼈员,可以根据招标⽅要求配送合适产品,并到⼯地⾛访和了解产品的适⽤情况。
2、财务能⼒本项⽬所需资⾦全部来⾃本公司银⾏存款、现⾦及票据,本公司资⾦充⾜,完全有能⼒承担本项⽬所需资⾦周转。
3、应急保障能⼒为保证为贵项⽬⼯程及时供货,特制定以下保障措施:(1)组建产品供应项⽬部针对本⼯程,我公司抽调经验丰富、责任⼼强的业务⾻⼲组建产品项⽬供应部。
负责本⼯程的产品供应。
(2)供应计划:根据⼯程施⼯进度和招标⽂件要求,制定详细的材料质量控制计划和供应管理办法,并做到有效实施。
(3)运输的基础配备及应急预案①车辆:投⼊应急运输车辆使⽤年限不超过5年,并经检测合格的在⽤车。
②⼈员:参运⼈员年龄在20⾄50岁之间,符合道路运输经营条件的驾驶⼈员,且技术过硬、作风正派、⾝体健康。
③接受应急运输任务后,运输车辆、⼈员必须整合待命,在规定时间内到达指定地点集合。
④执⾏应急运输任务时,运输车辆及参运驾驶⼈员要遵守应急预案的有关规定,服从统⼀调度、指挥,遇事主动请⽰、汇报,协调解决好各项⼯作事务。
⑤根据应急运输保障⼯作的需要,做好相关应急物资的调配,完成运输任务。
⼆、产品运输1、我公司提供的全部物资均按技术规格书规定进⾏包装,包装适应运输、装卸、防潮、防⾬、防震、防锈等需要,确保物资安全⽆损运抵合同约定地点。
2、物资的包装、标记和证件,符合《产品质量法》及技术规格书规定的内容,严格遵守国家有关规定和买⽅的合理要求。
3、我公司负责办理物资在运抵⽬的地途中的运输和保险,将物资完好⽆损地运送到合同约定地点。
DRI ( 直接还原铁)和HBI (热压铁块)的贸易和运输
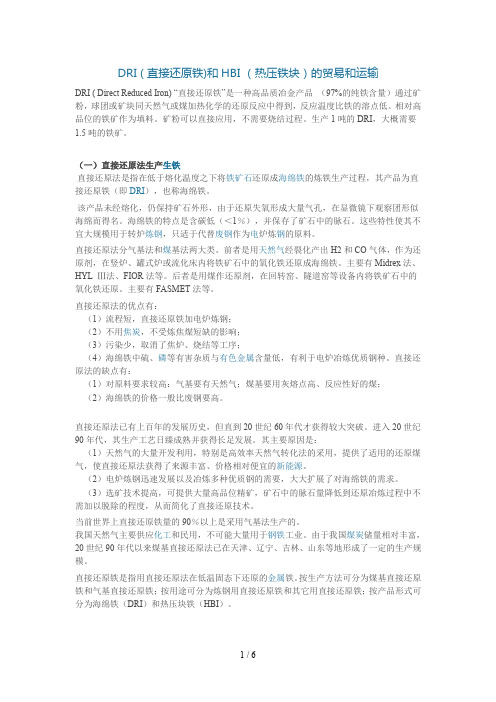
DRI ( 直接还原铁)和HBI (热压铁块)的贸易和运输DRI ( Direct Reduced Iron) “直接还原铁”是一种高品质冶金产品(97%的纯铁含量)通过矿粉,球团或矿块同天然气或煤加热化学的还原反应中得到,反应温度比铁的溶点低。
相对高品位的铁矿作为填料。
矿粉可以直接应用,不需要烧结过程。
生产1吨的DRI,大概需要1.5吨的铁矿。
(一)直接还原法生产生铁直接还原法是指在低于熔化温度之下将铁矿石还原成海绵铁的炼铁生产过程,其产品为直接还原铁(即DRI),也称海绵铁。
该产品未经熔化,仍保持矿石外形,由于还原失氧形成大量气孔,在显微镜下观察团形似海绵而得名。
海绵铁的特点是含碳低(<1%),并保存了矿石中的脉石。
这些特性使其不宜大规模用于转炉炼钢,只适于代替废钢作为电炉炼钢的原料。
直接还原法分气基法和煤基法两大类。
前者是用天然气经裂化产出H2和CO气体,作为还原剂,在竖炉、罐式炉或流化床内将铁矿石中的氧化铁还原成海绵铁。
主要有Midrex法、HYL Ⅲ法、FIOR法等。
后者是用煤作还原剂,在回转窑、隧道窑等设备内将铁矿石中的氧化铁还原。
主要有FASMET法等。
直接还原法的优点有:(1)流程短,直接还原铁加电炉炼钢;(2)不用焦炭,不受炼焦煤短缺的影响;(3)污染少,取消了焦炉、烧结等工序;(4)海绵铁中硫、磷等有害杂质与有色金属含量低,有利于电炉冶炼优质钢种。
直接还原法的缺点有:(1)对原料要求较高:气基要有天然气;煤基要用灰熔点高、反应性好的煤;(2)海绵铁的价格一般比废钢要高。
直接还原法已有上百年的发展历史,但直到20世纪60年代才获得较大突破。
进入20世纪90年代,其生产工艺日臻成熟并获得长足发展。
其主要原因是:(1)天然气的大量开发利用,特别是高效率天然气转化法的采用,提供了适用的还原煤气,使直接还原法获得了来源丰富、价格相对便宜的新能源。
(2)电炉炼钢迅速发展以及冶炼多种优质钢的需要,大大扩展了对海绵铁的需求。
炼钢_文言文翻译

炼钢之始,取铁石于地,磨之炼之,得铁精。
铁精者,铁之精华也,质坚而韧,可铸可为器。
然铁石之中,杂质颇多,非炼不可。
夫炼钢之术,首在去杂。
取铁精,置炉中,以木炭为薪,烈火炎炎,煮之炼之。
炉火熊熊,烟尘滚滚,铁精受火,杂质始去。
炼者需心细如发,火候适度,不可急躁,亦不可懈怠。
次则调火。
火候者,炼钢之关键也。
火候得宜,钢质方佳。
若火候过猛,则钢质过硬,易折断;若火候不足,则钢质过软,易变形。
故炼者需掌握火候,视炉火之变化,调整之,使之恰到好处。
再则,锤炼。
锤炼者,使钢质均匀,无裂痕,无气泡之术也。
炼者手持钢锤,于炉旁反复锤击,使钢汁流动,杂质沉淀。
锤炼之工,非一日之功,需耐心锤炼,方能炼成上品。
炼钢之工,又有数法。
其一,生铁炼钢法。
取生铁,经高温熔炼,去杂炼纯,得钢汁。
此法炼钢,质硬而脆,需再加锤炼,方能使用。
其二,熟铁炼钢法。
取熟铁,经反复锤炼,去杂炼纯,得钢汁。
此法炼钢,质韧而软,易变形,需再加锤炼,方能使用。
其三,灌钢法。
取生铁,炼成钢汁,注入熟铁之中,使二者融合,炼成新钢。
此法炼钢,质优而强,为上乘之选。
炼钢之工,非一日之功,需匠心独运,技艺精湛。
炼者需通晓炉火之变化,掌握锤炼之技巧,方能炼出上品。
炼钢之术,既可铸剑,亦能造枪。
剑者,国之利器,枪者,战争之利器。
炼钢之工,肩负重任,为国家强盛,民族繁荣,贡献力量。
今夫炼钢之术,已传遍天下。
然炼钢之工,仍需不断探索,创新技艺,以适应时代之需求。
炼钢之术,实为我国古代科技之瑰宝,传承千年,光耀后世。
炼钢之妙,在于去杂炼纯,锤炼均匀。
炼者需技艺精湛,匠心独运,方能炼出上品。
炼钢之工,实为我国工匠精神之体现,值得我们传承与发扬。
炼钢之术,非一日之功,需炼者不懈努力,方能炼出国之利器。
炼者之心,犹如炼钢之火,熊熊燃烧,永不熄灭。
炼钢之术,永载史册,光照千秋。
高温作业温度指数计算公式为

高温作业温度指数计算公式为高温作业温度指数计算公式为什么重要?在工业生产中,存在许多高温作业环境,如炼钢、玻璃制造、铸造等行业。
在这些高温环境下工作的人们会面临很多健康和安全的风险,包括中暑、热衰竭、热休克等。
因此,为了确保员工的安全和健康,减少事故的发生,必须对高温作业环境进行科学的评估和管理。
高温作业温度指数计算公式就是在此背景下应运而生的。
高温作业温度指数计算公式是通过考虑并综合计算人体在高温环境下的暴露时间、湿度、风速等因素,来判定工作环境的安全程度和对员工的健康影响的一种方法。
它可以帮助工作现场的管理者合理安排工人的工作时间和工作强度,为员工提供一个安全和健康的工作环境。
这个计算公式的核心参数包括温度、湿度、辐射温度和风速。
温度是高温作业环境中非常重要的一个因素,高温会加快人体的代谢,增加水分的蒸发速度,导致脱水和热衰竭。
湿度和辐射温度也会影响人体的热交换和感觉温度。
湿度过高会减缓蒸发速度,导致身体难以散热,引起中暑。
辐射温度是指在高温环境中,通过近距离的辐射热量对人体的影响。
风速会加速蒸发和人体热量的散发,从而改变人体的感觉温度。
高温作业温度指数计算公式的具体内容如下:HI = c1 + c2T + c3R + c4V + c5T × R + c6T × V + c7R × V + c8T × R × V其中,HI表示高温指数,T表示室外温度,R表示相对湿度,V表示风速,c1-c8表示与不同因素相关的系数。
通过这个公式,可以综合考虑多个参数的影响,并对高温工作环境进行评估,判断是否安全。
根据高温指数HI的数值范围,可将高温环境分为不同等级。
通常,指数HI小于80表示安全可接受,80-90表示有些许不适但可继续工作,大于90表示工作环境非常危险,需要采取紧急的措施,如停工、增加休息时间等。
高温作业温度指数计算公式的应用有助于提高工作环境的安全性和员工的生产效率。
炼钢用电特点范文

炼钢用电特点范文炼钢是指将生铁或铁合金通过熔炼、净化、脱碳、合金化等工艺操作,制备成不同性能和用途的钢材的过程。
在炼钢过程中,电力是不可或缺的能源之一、下面将详细介绍炼钢用电的特点。
1.大量用电量:炼钢是一个高能耗产业,用电量较大。
炼钢过程中对电力的需求量很高,必须保证足够的电力供应,以满足钢铁生产的需要。
一个典型的大型炼钢厂每天的用电量可以达到上百兆瓦时的级别,相当于成千上万户家庭的用电量之和。
2.连续供电:炼钢过程对电力的稳定供应要求很高,不能有停电或电力波动。
一旦电力供应中断,将给整个生产系统带来巨大损失。
因此,为了确保电力的连续供应,炼钢企业通常会与供电部门签订稳定供电的协议,以得到持续稳定的电力供应。
3.高负荷运行:炼钢过程中,涉及到多台大功率设备的运行,包括电弧炉、连铸机、轧机等。
这些设备的运行需要大量的电力支持,通常会达到极限负荷的运行状态。
因此,电力系统在设计和建设时,需要具备足够的负荷承受能力,以确保设备的正常运行。
4.高稳定性要求:炼钢过程中,设备上的电力负载会不断变化,电力系统需要具备高度的调节能力和稳定性,以适应负荷变化。
对于电网来说,需要通过合理的电力调度和控制措施,确保电力供应的稳定性和可靠性。
5.高品质电力需求:炼钢过程对电力质量的要求很高。
电弧炉等设备需要稳定的电压和频率,以确保炼钢过程中的电弧稳定和电炉操作的正常进行。
同时,为了保证产品的质量和高效能的炼钢操作,炼钢企业也需要提供质量优良的电力供应。
6.高效节能要求:炼钢企业在进行炼钢过程时,需要充分考虑电力的高效使用和节能减排。
采用高效的电力设备和技术,如高温炉料预热技术、炉灰余热回收技术等,可以将能耗降至最低。
因此,炼钢用电的特点之一是强调节能减排和绿色环保。
总之,炼钢用电是一个高能耗、需要连续供电、负荷变化大、对电力质量要求高的过程。
在炼钢过程中,电力是一项重要的能源,保证电力供应的可靠性和稳定性对于炼钢企业的生产效益和质量有着重要的影响。
- 1、下载文档前请自行甄别文档内容的完整性,平台不提供额外的编辑、内容补充、找答案等附加服务。
- 2、"仅部分预览"的文档,不可在线预览部分如存在完整性等问题,可反馈申请退款(可完整预览的文档不适用该条件!)。
- 3、如文档侵犯您的权益,请联系客服反馈,我们会尽快为您处理(人工客服工作时间:9:00-18:30)。
转炉吹炼20#钢,铁水含硅0.7%,含磷0.62%,终渣碱度要求3.2,石灰的有效碱度为82%,试求1000Kg 铁水需要加石灰多少千克?
答案:转炉吹炼中高磷铁水时应该用W(CaO)/{W(SiO2)+W(P2O5)}表示熔渣的碱度,此时石灰加入量的计算公式为:
石灰加入量
答:冶炼该种铁水石灰加入量应为110Kg/吨
10.设渣量为装入量的10%,炉衬侵蚀量为装入量的1%,炉衬MgO 量为40%;铁水成分Si =0.6%、P =0.09%、S=0.04%;
石灰成分:CaO=88%、MgO=1.7%、SiO2=0.4%;
白云石成分:CaO =40%、MgO =35%、SiO2=3%;
终渣要求(MgO)=10%,碱度为4.0。
求需要加入的石灰与白云石量。
答案:1)白云石应加入量:
W 白=10%×10%×1000/35%=28.6kg/t
2)炉衬侵蚀进入渣中MgO 折算白云石量:
W 衬=1%×40%×1000/35%=11.4kg/t
3)石灰带入MgO 折算白云石量:
W 石=2.14×0.6%×3.5×1000×1.7%/[35%×(88%-4×0.4%)]=2.5kg/t
4)实际白云石加入量:
W 白’=28.6-11.4-2.5=14.7kg/t
5)白云石带入渣中CaO 折算石灰量:
14.7×(40%-4×3%)/(88%-4×0.4%)=4.8kg/t
6)实际应加石灰量:
W 石’=2.14×0.6%×4×1000/(88%-4×0.4%)-4.8=54.6kg/t
答:实际加入的白云石量为14.7kg/t 、石灰量54.6kg/t 。
17.计算1吨废钢从25℃加热到1650℃需要吸收多少热量?
已知:废钢熔化温度为1510℃
废钢熔化潜热为271.7千焦/千克
固体废钢的平均热容量为0.7千焦/度·千克
钢液的平均热容量为0.84千焦/度·千克
答案:Q 吸=1000×{(1510-25)}×0.7+271.7+(1650-1510)×0.84} =1428800kj
答:需吸收热量1428800kj 。
39.某厂终渣MgO 含量为5%,溅渣后需将渣中MgO 含量提高到9%,已知轻烧镁球中的含量为75%,计算吨钢需加多少公斤镁球?(吨钢渣量按100公斤,加入镁球后增加的渣量不计)
答案:100×(9%-5%)÷75%=5.3kg
40.已知某转炉渣量为10t ,要求炉渣中氧化镁含量为10%,炉衬侵蚀使炉渣中含氧化镁3%,白云石含氧化镁20%,计算每炉白云石的加入量。
答案:白云石加入量=%20%
3%10 ×10×1000=3500kg
258.计算液相线温度。
已知在钢液中,元素百分含量(R):碳0.11%,硅0.21%,锰0.42%,磷0.02%,硫0.03%,铜0.06%,其余成分不计。
各元素含1%对钢液凝固影响值(P)为:碳90,硅6.2,锰1.7,磷28,硫40,铜2.6;纯铁凝固点为1539℃。
(保留整数位)
答案:△T=1539-∑(R×P)
=1539-0.11×90-0.21×6.2-0.42×1.7-0.02×28-0.03×40-0.06×2.6=1525(℃)
答:液相线温度为1525℃。
265.计算生白云石加入量:
已知条件:铁水成分ω[Si]=0.50%;ω[P]=0.04%;
石灰成分ωCaO石灰=86%,ωSiO2石灰=2.5%,ωMgO石灰=4.09%;
生白云石成分ωCaO白=28%,ωSiO2白=2.0%,ωMgO白=25%;
炉衬成分ωMgO衬=85%;
终点渣成分R=3.5,ωMgO渣=9.66%;
渣量为金属装入量的7.777%,炉衬侵蚀量是装入量的0.07%。
答案:1)不加白云石时石灰加入量=2.14×ω[Si]×R×1000/(ωCaO石灰-R×ωSiO2石灰)
=2.14×0.5×3.5×1000/(86%-3.5×2.5%)
=48.48(Kg/t)
2)按装入量计算生白云石加入量
生白云石加入量=1000×7.777%×9.66%/25%=30.05Kg/t;
3)计算生白云石需石灰补加量=30.05×ω[Si]×R/(ωCaO石灰-R×ωSiO2石灰)
=30.05×2%×3.5/(86%-3.5×2.5%)
=2.72(Kg/t)
4)计算生白云石相当的石灰量:
生白云石相当的石灰量=30.05×28%/(86%-3.5×2.5%)=40.89Kg/t。
5)石灰加入总量为:(48.48+2.72-10.89)=40.31Kg/t。
6)石灰带入的MgO,折合成生白云石的数量:
40.31×4.09%/25%=6.59Kg/t。
由炉衬进入炉渣的MgO,折合为生白云石数量:
1000×0.07%×85%/25%=2.38Kg/t。
7)生白云石的实际加入量
30.05-6.59-2.38=21.08Kg/t
答:如果保持终点渣MgO含量为9.66%时,每吨铁水需要加入生白云石21.08Kg/t 已知:铁水270t、含锰0.40%(散状料带入锰忽略不计),废钢55t、含锰0.50%,钢水量300t、残锰0.12%,终点炉渣中含氧化锰(MnO)4.5%。
计算转炉渣量。
(小数点后保留一位数,Mn原子量55,O原子量16)
答案:终点渣中锰含量=4.5%×[55/(55+16)]=3.49%
锰的投入=铁水带锰+废钢带锰
=270×1000×0.40%+55×1000×0.50%
=1355(kg)
锰的产出=钢水带锰+炉渣带锰
=300×1000×0.12%+渣量(X)×1000×3.49% 根据公式:投入=产出
则:1355=360+34.9X
X=28.5(t)
答:转炉的渣量为28.5t。