电动平车安装焊接夹渣焊接缺陷原因分析
常见焊接缺陷产生原因及防止措施
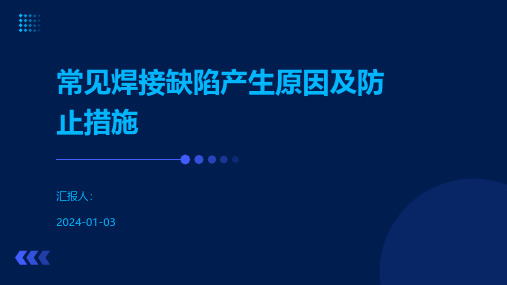
常见焊接缺陷产生原因及防止措施汇报人:2024-01-03•焊接缺陷概述•常见焊接缺陷及其产生原因•焊接缺陷的检测方法目录•提高焊接质量的措施与建议01焊接缺陷概述在焊接过程中,由于各种原因导致焊缝中出现的缺陷,如气孔、夹渣、未熔合等。
根据缺陷的性质和形态,焊接缺陷可分为表面缺陷和内部缺陷两类。
表面缺陷包括咬边、焊瘤等,内部缺陷包括气孔、夹渣、未熔合等。
焊接缺陷的定义与分类焊接缺陷分类焊接缺陷定义焊接缺陷会降低焊接接头的承载能力,导致结构强度下降,可能引发安全事故。
影响结构强度引起应力集中泄露风险焊接缺陷会导致焊缝处的应力集中,使结构在承受载荷时容易发生疲劳断裂。
对于压力容器、管道等焊接结构,焊接缺陷可能导致介质泄露,引发环境污染或安全事故。
030201焊接缺陷对产品质量的影响02常见焊接缺陷及其产生原因0102气孔的产生原因可能是由于焊接过程中熔池过快冷却,气体来不及逸出,或是焊接材料中含有易蒸发的元素,如氢、氮等。
气孔是由于焊接过程中熔池中的气体在凝固之前未能完全逸出,在焊缝中形成的气孔。
夹渣的产生原因可能是由于焊接过程中熔池搅拌不充分,熔渣未能及时浮出,或是焊接速度过快,熔渣来不及浮出。
未熔合是由于焊接过程中母材与填充金属未能完全熔合在一起,在焊缝中形成的未熔合。
未熔合的产生原因可能是由于焊接过程中热输入不足,母材与填充金属未能充分熔化,或是焊接操作不当,填充金属未能充分覆盖母材。
未焊透是由于焊接过程中接头根部未完全熔透,在焊缝中形成的未焊透。
未焊透的产生原因可能是由于焊接过程中热输入不足,接头根部未能充分熔化,或是焊接操作不当,接头根部存在间隙或氧化物等杂质。
03焊接缺陷的检测方法利用高频声波检测焊缝内部和表面缺陷,具有无损、快速、准确的特点。
超声检测通过X射线或γ射线穿透焊缝,检测内部缺陷,具有较高的检测精度。
射线检测适用于铁磁性材料,通过磁粉显示焊缝表面和近表面缺陷。
磁粉检测利用电磁感应原理检测导电材料焊缝中的缺陷,具有快速、简便的优点。
浅论部分焊接缺陷产生的原因及防治措施

充金属覆盖;坡口及层间清理不干净;单面焊双面成形焊接时第一层的电弧燃烧时间短等。 防治措施 焊条、焊丝和焊炬的角度要合适,运条摆动应适当,要注意观察坡口两侧熔化情况;选用稍大的焊接电流和火焰能率,焊速不宜过
快,使热量增加足以熔化母材或前一层焊缝金属;发生电弧偏吹应及时调整角度,使电弧对准熔池;加强坡口及层间清理。 五、焊瘤 焊瘤是焊接过程中,熔化金属流淌到焊缝之外未熔化的母材上所形成的金属瘤。焊瘤不仅影响了焊缝的成形,而且在焊瘤的部位往往
焊接时,熔池中的气泡在凝固时未能及时逸出而残留下来所形成的空穴叫做气孔。产生气孔的气体主要有氢气、氮气和一氧化碳。气 孔有球形、条虫状和针状等多种形状。气孔有时是单个分布的,有时是密集分布的,也有连续分布的。气孔有时在焊缝内部,有时暴露在 焊缝外部。气孔的存在会削弱焊缝的有效断面,造成应力集中,降低焊缝金属的强度和塑性,尤其是冲击韧度和疲劳强度降低得更为显 著。
浅论部分焊接缺陷产生的原因及防治措施
发表时间:2018-01-03T11:00:38.550Z 来源:《知识-力量》2017年9月下 作者: 张爱军
[导读] 本文主要论述了气孔、夹产生的原因、以及防治措施。
张爱军 首钢长钢技工学校 046031 摘要:本文主要论述了气孔、夹渣、未焊透、未熔合、焊瘤、凹坑与弧坑六项焊接缺陷的特征、产生的原因、以及防治措施。 关键词:气孔、夹渣、未焊透、未熔合、焊瘤、凹坑与弧坑、焊接缺陷 在焊接接头中产生的金属不连续、不致密或连接不良的现象称为焊接缺陷。焊接缺陷的存在,将直接影响焊接结构的安全使用。常见的焊 接缺陷有:焊缝尺寸不符合要求、咬边、焊瘤、未焊透、未熔合、下塌与烧穿、气孔、冷缩孔、夹渣、凹坑与弧坑、裂纹、夹钨。现就其 中气孔、夹渣、未焊透、未熔合、焊瘤、凹坑与弧坑六项缺陷进行论述。 一、气孔
常见焊接缺陷的产生原因和防止措施

1.启动焊机前,检查焊把,禁止与工件短路,遵守安全规程;
2.包裹绝缘带;
3.在坡口内引弧,加强规程教育,严肃工艺纪律
飞溅
1.焊接电流过大;
2.未采取防护措施;
3.CO2气体保护焊焊接回路电感量不合适
1.选用合适的规范参数;
2.采用涂白垩粉等措施;
3.调整CO2气体保护焊焊接回路的电感
2.选择合理的焊接规范和工艺措施,如焊前预热、控制层间温度、焊后缓冷、进行焊后热处理等。避免产生淬硬组织;
3.采取降低焊接应力的工艺措施
再热裂纹
1.过饱和固溶的碳化物在再次加热时析出,造成晶内强化;
2.焊接残余应力
1.减少焊接应力和应力集中程度,如焊前预热、焊后缓冷等以及使焊缝与母材平滑过渡;
2.在满足性能要求的前提下,选用强度等级稍低于母材的焊接材料;
4.操作不熟练;
5.坡口设计不合理,焊层形状不良
1.彻底清理层间焊道;
2.选用合理的焊接规范;
3.提高操作技术;
4.合理选用坡口,改善焊层成形
金属夹杂
1.氩弧焊采用接触引弧,操作不熟练;
2.钨极与熔池或焊丝短路;
3.焊接电流过大,钨棒严重烧损
1.氩弧焊时尽量采用高频引弧;
2.熟练操作技术;
3.选用合适的焊接规范
6.气焊火焰调整不合适、焊炬摆动幅度大,焊丝搅拌熔池不充分,对熔池保护差;
7.操作不熟练;
8.焊接环境湿度大
1.不使用药皮剥落、开裂、变质、偏心和焊芯锈蚀的焊条。焊条和焊剂按规程要求烘烤;
2.按规程要求做好焊前清理工作;
3.选用合适的焊接规范,控制焊接电流和电弧长度;
常见焊接缺陷的成因分析及对策
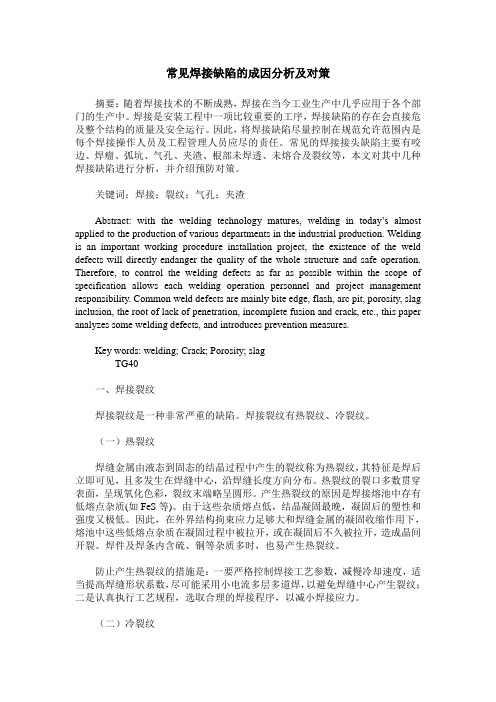
常见焊接缺陷的成因分析及对策摘要:随着焊接技术的不断成熟,焊接在当今工业生产中几乎应用于各个部门的生产中。
焊接是安装工程中一项比较重要的工序,焊接缺陷的存在会直接危及整个结构的质量及安全运行。
因此,将焊接缺陷尽量控制在规范允许范围内是每个焊接操作人员及工程管理人员应尽的责任。
常见的焊接接头缺陷主要有咬边、焊瘤、弧坑、气孔、夹渣、根部未焊透、未熔合及裂纹等,本文对其中几种焊接缺陷进行分析,并介绍预防对策。
关键词:焊接;裂纹;气孔;夹渣Abstract: with the welding techno logy matures, welding in today’s almost applied to the production of various departments in the industrial production. Welding is an important working procedure installation project, the existence of the weld defects will directly endanger the quality of the whole structure and safe operation. Therefore, to control the welding defects as far as possible within the scope of specification allows each welding operation personnel and project management responsibility. Common weld defects are mainly bite edge, flash, arc pit, porosity, slag inclusion, the root of lack of penetration, incomplete fusion and crack, etc., this paper analyzes some welding defects, and introduces prevention measures.Key words: welding; Crack; Porosity; slagTG40一、焊接裂纹焊接裂纹是一种非常严重的缺陷。
焊接缺陷产生原因及防止措施

焊接缺陷产生原因及防止措施焊接接头的不完整性称为焊接缺陷,主要有焊接裂纹、未焊透、夹渣、气孔和焊缝外观缺陷等。
这些缺陷减少焊缝截面积,降低承载能力,产生应力集中,引起裂纹;降低疲劳强度,易引起焊件破裂导致脆断。
一缺陷名称:气孔(blowhole)(1)焊条不当或干燥.(2)焊件存有水分、油污或锈.(3)冲压速度太快.(4)电流太弱.(5)电弧长度不适宜.(1)选用适当的焊条并注意烘干.(2)焊接前清洁被焊部份.(3)减少冲压速度,并使内部气体难逸(4)使用厂商建议适当电流.(6)施行适当的预热工作.(6)焊件厚度小,金属加热过速.(5)调整适度电弧长度.(1)母材不洁.(2)焊丝存有锈或焊药干燥.(3)点焊不当,焊丝挑选不当.(1)焊接前注意清洁被焊部位.(2)选用适当的焊丝并注意保持干燥.(3)点焊焊道不得有缺陷,同时要清洁(4)减小干伸长度,调整适当气体流(4)干伸长度太短,co2气体保与整洁,且采用焊丝尺寸必须适度.co2气体(5)风速较大,无挡风装置.(5)安装挡风设备.(7)注意清除喷嘴处焊渣,并涂以飞溅(8)co2纯度为99.98%以上,水分为0.005%以下.维护焊接(6)冲压速度太快,加热快速.体乱流.别含水分).(7)火花溅黏在燃烧室,导致气(6)减少速度并使内部气体逸出.(8)气体纯度不当,不含杂物多(特粘附避免剂,以缩短燃烧室寿命.(1)焊缝有锈、氧化膜、油脂等(1)焊缝需研磨或以火焰烧除,再以钢有机物的杂质.(2)焊剂潮湿.(3)焊剂受污染.(4)焊接速度过快.(5)焊剂高度不足.(2)约须要300℃潮湿(3)注意焊剂的储存及焊接部位附近地区的洁净,以免杂物混进.(4)降低焊接速度.(6)焊剂高度过小,并使气体难于(5)焊剂出口橡皮管口必须调整低些.逸出(特别在焊剂粒度细的情(6)焊剂出口橡皮管要调整低些,在自形).(7)焊丝锈蚀或沾满油污.动焊接情形适当高度30-40mm.(7)换用洁净焊丝.c+).(8)极性不适当(特别在对接时(8)将直流正接(dc-)改为直流反接(d受到污染可以产生气孔).(1)减压表冷却,气体无法流出.(1)气体调节器无附电热器时,要加装(2)喷嘴被火花飞溅物堵塞.电热器,同时检查表之流量.(2)经常清除喷嘴飞溅物.并且涂以飞(3)焊丝有油、锈.溅附着防止剂.(3)焊丝储藏或加装焊丝时不容跌破(1)电压过高.(2)焊丝注重长度过短.(1)降低电压.(2)依各种焊丝表明采用.(4)增加拖拽角至约0-20°.(5)调整适度.自保护药(3)钢板表面有锈蚀、油漆、水(3)焊前清除干净.芯焊丝分.(4)焊枪拖拽角弯曲太多.(5)卢瓦龙县速度太快,尤其斜焊接.二缺陷名称咬边(undercut)(1)电流太弱.(2)焊条不适宜.(3)电弧过长.(4)操作方法不当.(5)母材污秽.(6)母材失灵.(1)使用较低电流.(2)采用适度种类及大小之焊条.(3)维持适度的弧长.(4)采用正确的角度,较慢的速度,较短的电弧及狭窄的运转法.(5)清除母材油渍或锈.(6)使用直径较小之焊条.(1)电弧过长,冲压速度太快.(1)降低电弧长度及速度.(2)角焊时,焊条对准部位不正(2)在水平角焊接时,焊丝边线应离交点道二边填补不足产生咬边.(3)立焊转动或操作方式不当,并使焊接(3)废止操作方法.三缺陷名称:夹渣(slaginclusion)冲压方式出现原因(1)前层焊渣未完全清除.(1)彻底清除前层焊渣.(2)使用较低电流.(3)提升冲压速度.(4)增加焊条转动宽度.(5)废止适度坡口角度及间隙.(1)尽可能将焊接件置放水平边线.(2)特别注意每道焊道之洁净.(4)提升冲压速度(2)焊接电流太低.(3)焊接速度太慢.(4)焊条摆动过宽.(5)焊缝组合及设计不良.(1)母材倾斜(下坡)使焊渣超co2气体整洁.(2)前一道焊接后,焊渣未清洁(3)增加电流和焊速,使焊渣容易浮起.电弧焊(3)电流过大,速度慢,焊着量(4)用前进法焊接,开槽内焊渣(1)冲压方向朝母材弯曲方向,(1)冲压移向恰好相反方向冲压,或将母材因此焊渣流动超前.尽可能改成水平方向焊接.(2)多层冲压时,凹槽下受焊丝(2)凹槽侧面和焊丝之间距离,最少必须溶入,焊丝过于靠近开槽的侧大于焊丝直径以上.边.(3)在冲压起点存有导板处易产(3)导板厚度及开槽形状,需与母材相(4)提升冲压电流,并使残余焊渣难熔(4)电流过小,第二层间有焊渣化.存留,在冲压薄板时难产生(5)减少冲压电流及冲压速度.裂纹.(6)最后完成层电弧电压过高,(6)增大电压或提升焊速,必要时盖面(5)焊接速度过低,使焊渣超前.层由单道焊改为多道焊接.使游离焊渣在焊道端头产生弄卷.(1)电弧电压过低.(2)焊丝摆弧不当.(3)焊丝伸出过长.(4)电流过高,冲压速度过慢.(5)第一道焊渣,未充份去除.(6)第一道融合不当.(7)坡口太窄小.(1)调整适当.(2)加多练习.(3)依各种焊丝采用表明.(4)调整冲压参数.(5)全然去除(6)使用适当电压,注意摆弧.(7)改正适当坡口角度及间隙.自维护药芯焊丝焊接方式发生原因(1)前层焊渣未全然去除.(1)彻底清除前层焊渣.(2)采用较高电流.(3)提高焊接速度.(4)减少焊条摆动宽度.(5)改正适当坡口角度及间隙.(1)尽可能将焊件放置水平位置.(2)注意每道焊道之清洁.(4)提高焊接速度(2)冲压电流太低.(3)冲压速度很慢.(4)焊条转动过阔.(5)焊缝女团及设计不当.(1)母材弯曲(下坡)并使焊渣逊于co2气体干净.(2)前一道冲压后,焊渣未洁净(3)减少电流和焊速,并使焊渣难浮.电弧焊(3)电流过小,速度慢,焊着量(4)用行进法冲压,凹槽内焊渣(1)焊接方向朝母材倾斜方向,(1)焊接改向相反方向焊接,或将母材因此焊渣流动全面性.尽可能换成水平方向冲压.(2)多层焊接时,开槽面受焊丝(2)开槽侧面和焊丝之间距离,最少要渗入,焊丝过分紧邻凹槽的侧大于焊丝直径以上.边.(3)在焊接起点有导板处易产(3)导板厚度及凹槽形状,而因母材二者(4)提高焊接电流,使残留焊渣容易熔(4)电流过大,第二层间有焊渣化.留存,在焊接薄板时容易产生(5)增加焊接电流及焊接速度.裂纹.(6)最后顺利完成层电弧电压过低,(6)减小电压或提高焊速,必要时盖面(5)冲压速度过高,并使焊渣全面性.层由单道焊接改成多道冲压.使得游离焊渣在焊道端头产生搅卷.(1)电弧电压过高.(2)焊丝挂弧不当.(3)焊丝张开过长.(4)电流过低,焊接速度过慢.(5)第一道焊渣,未充分清除.(6)第一道结合不良.(7)坡口太狭窄.(1)调整适度.(2)加多练.(3)依各种焊丝使用说明.(4)调整焊接参数.(5)完全清除(6)采用适度电压,特别注意挂弧.(7)废止适度坡口角度及间隙.自保护药芯焊丝(1)焊条采用不当.(2)电流太低.(1)选用较具渗透力的焊条.(2)使用适当电流.(3)改用适当焊接速度.手工(3)冲压速度太快温度下降不电弧焊够,又进行速度太慢电弧冲力(4)增加开槽度数,增加间隙,并减少根被焊渣所抵挡,无法给与母材.深.(4)焊缝设计及组合不正确.(1)电弧过大,冲压速度过高.(2)电弧过长.(3)凹槽设计不当.(1)增加焊接电流和速度.(2)降低电弧长度.(3)减少凹槽度数.减少间隙增加根深.五缺陷名称:裂纹(crack)(1)焊件所含过低的碳、锰等再分(1)采用高氢系焊条.(2)焊条品质不良或潮湿.(3)焊缝拘束应力过大.(4)母条材质含硫过高不适于(2)采用适合焊条,并特别注意潮湿.(3)改进结构设计,特别注意冲压顺序,焊接接后进行热处理.(4)防止采用不当钢材.(5)冲压时需考量预演或后热.(6)预演母材,焊接后缓冷.(7)采用适度电流.(8)首道焊接之焊着金属须充分抵抗(5)施工准备工作严重不足.(6)母材厚度较大,冷却过速.(7)电流太强.(8)首道焊道严重不足抵抗膨胀应当(1)开槽角度过小,在大电流焊(1)注意适当开槽角度与电流的配合,直奔时,产生梨形和焊道裂纹.(2)母材含碳量和其它合金量必要时必须加强凹槽角度.(2)采用含碳量低的焊条.(3)第一道焊着金属须充份能够抵抗交(4)改进结构设计,特别注意冲压顺序,焊接(5)特别注意焊丝留存.(6)特别注意焊件女团之精度.过高(焊道及热影区).小.过强.(5)焊丝干燥,氢气入侵焊道.(3)多层焊接时,第一层焊道过缩应力.(4)冲压顺序不当,产生拘束力后展开热处理.(6)套板密接不良,形成高低不(7)注意正确的电流及焊接速度.平,并致应力集中.(7)因第一层焊接量过多,冷却缓慢(不锈钢,铝合金等).(1)对焊缝母材所用的焊丝和(1)采用含锰量较低的焊丝,在母材含(2)冲压电流及电压须要减少,冲压速度焊剂之配合不适当(母材含碳碳量多时,要有预热之措施.量过大,焊丝金属含锰量太少).(3)焊丝含碳、硫量过大.(4)在多层冲压之第一层所生降低,母材需加热措施.(4)第一层焊道之焊着金属须充份抵(2)焊道急速冷却,使热影响区(3)更换焊丝.(5)将冲压电流及冲压速度降低,发生改变焊道力,不足抵抗收缩应力.(5)在角焊时过浅的扩散或偏(6)注意规定的施工方法,并予焊接操析.作施工指导.(6)焊接施工顺序不正确,母材(7)焊道宽度与深度的比例约为1:1:六瑕疵名称:变形(distortion)焊接方式发生原因手焊、co(1)冲压层数太多.(2)冲压顺序不当.(3)施工准备工作严重不足.(4)母材加热过速.(5)母材失灵.(薄板)(6)焊缝设计不当.(7)焊着金属过多.(8)束缚方式不的确.(1)使用直径较大之焊条及较高电流.(3)冲压前,采用夹具将焊接件紧固以免护焊、自保护药芯焊丝焊接、自动埋弧焊接.(4)防止加热过速或预演母材.(5)采用穿透力高之焊材.(6)增加焊缝间隙,增加凹槽度数.(7)特别注意冲压尺寸,不并使焊道过小.(8)特别注意避免变形的紧固措施.(2)操作方法不适.(2)使用光滑适度之速度及冲压顺序.(4)减少电流.(5)多加练习.(6)更改导电嘴.(7)维持的定短、娴熟.焊道外观形(3)焊接电流过高,焊条直径过(3)选用适当电流及适当直径的焊接.状不良(bad粗.appearanc(4)焊件失灵.(5)焊道内,熔填方法不良.(6)导电嘴磨耗.(7)焊丝伸出长度不变.(1)使用焊条不当.(2)焊条潮湿.(3)母材冷却过速.(1)采用适度焊条,例如无法消解时用高(2)使用干燥过的焊条.(3)降低冲压速度,防止急冷,最出色施予凹痕(pit)(4)焊条不洁及焊件的偏析.(5)焊件含碳、锰成分过低.(4)使用良好低氢型焊条.(5)使用盐基度较高焊条.(1)在直流电焊接时,焊件所生磁(1)·电弧偏向一方复置一地线.场不均,使电弧偏向.(2)接地线边线不尽如人意.(3)焊枪拖拽角太大.(4)焊丝张开长度太短.(5)电压太高,电弧太长.(6)电流太大.(7)冲压速度太快.·正对偏向一方焊接.·采用短电弧.·改正磁场使趋均一.·改用交流电焊(2)调整接地线位置.(3)减小焊枪拖曳角.(4)增长焊丝伸出长度.(5)降低电压及电弧.(6)调整使用适当电流.(7)焊接速度变慢.偏弧(arcbl(1)在有开槽焊接时,电流过大.(1)降低电流.(2)因开槽不良焊缝间隙太大.(2)减少焊缝间隙.(1)导电嘴磨损,焊丝输出产生(1)将焊接导电嘴换新使用.焊道不光滑左右摇摆.(2)焊枪操作不熟练.(1)电流过大,焊接速度太慢.(2)多提操作方式练.(1)选用正确电流及焊接速度.(2)提高电弧长度.(3)焊丝不可离交点太远.(2)电弧太短,焊道低.(3)焊丝对准边线不适度.(角(2)电弧太长.(3)电流太高或太低.(2)采用较短之电弧.(3)采用适度之电流.(4)调整适度.(5)依各种焊丝使用说明.(7)注意仓库保管条件.(8)修理,平日注意保养.(1)使用适度的长度,比如实心焊丝在火花飞溅过(4)电弧电压太高或太低.(5)焊丝注重过长.(7)焊丝过度经久耐用.(8)焊机情况不当.(1)焊丝张开过长.(6)焊枪倾斜过度,拖曳角太大.(6)尽可能保持垂直,避免过度倾斜.(2)焊丝歪曲.(3)直线操作方式不当.大电流时伸出长20-25mm.在自保护焊接时伸出长度约为40-50mm.(2)更改崭新焊丝或将歪曲不予校正.(3)在直线操作方式时,焊枪必须维持横向.(1)焊枪前端之导电嘴比焊丝(1)焊丝心径必须与导电嘴配合.(2)更换导电嘴.(3)将焊丝卷曲拉直.(4)将输送机轴助威,并使调头杀菌.(5)更改运送轮.(6)压力要适当,太松送线不良,太紧焊(2)导电嘴出现磨损.(3)焊丝出现卷曲.(4)焊丝输送机调头不顺遂.(5)焊丝运送轮子沟槽磨损.(6)冷却轮子压入不当.(7)导管接点阻力太大.(7)导管弯曲过大,调整减少弯曲量.燃烧室与母材(1)燃烧室,导管或导电嘴间出现(1)火花溅物粘及燃烧室过多须除去,间出现电弧短路.(1)冷却水不能充分流出.或是采用焊枪存有绝缘维护之陶瓷管.(1)冷却水管不通,如冷却水管阻塞,必焊枪燃烧室过(2)电流过小.须清除使水压提升流量正常.(2)焊枪采用在允许电流范围及采用(1)导电嘴与母材间的距离过(1)采用适度距离或稍为短些去起至弧,焊丝粘住导短.(2)导管阻力过小,送来线不当.(3)电流太小,电压太大.然后调整到适当距离.(2)去除导管内部,CX600X稳定运送.(3)调整适度电流,电压值.典型缺陷照片-焊穿-。
常见的焊接缺陷及成因
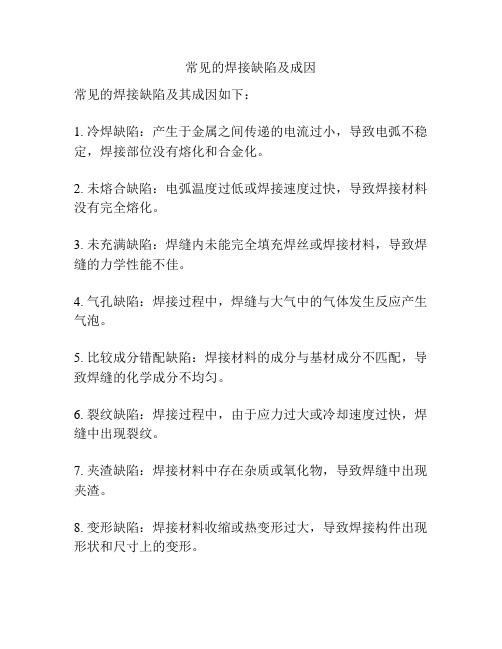
常见的焊接缺陷及成因
常见的焊接缺陷及其成因如下:
1. 冷焊缺陷:产生于金属之间传递的电流过小,导致电弧不稳定,焊接部位没有熔化和合金化。
2. 未熔合缺陷:电弧温度过低或焊接速度过快,导致焊接材料没有完全熔化。
3. 未充满缺陷:焊缝内未能完全填充焊丝或焊接材料,导致焊缝的力学性能不佳。
4. 气孔缺陷:焊接过程中,焊缝与大气中的气体发生反应产生气泡。
5. 比较成分错配缺陷:焊接材料的成分与基材成分不匹配,导致焊缝的化学成分不均匀。
6. 裂纹缺陷:焊接过程中,由于应力过大或冷却速度过快,焊缝中出现裂纹。
7. 夹渣缺陷:焊接材料中存在杂质或氧化物,导致焊缝中出现夹渣。
8. 变形缺陷:焊接材料收缩或热变形过大,导致焊接构件出现形状和尺寸上的变形。
这些焊接缺陷的成因主要包括焊接工艺参数不当、焊接材料质量不过关、焊接操作不规范等原因。
对这些缺陷的预防和修复可以通过合理的焊接工艺设计、选择质量良好的焊接材料、进行焊前和焊后的检测等方式来实现。
最常见焊接缺陷并分析原因
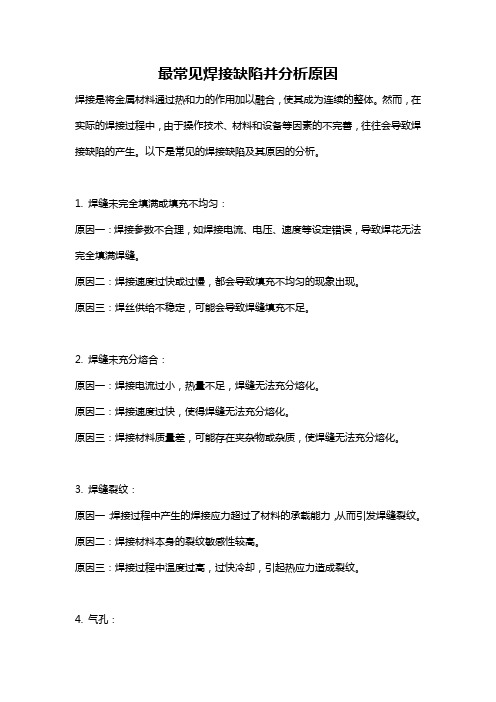
最常见焊接缺陷并分析原因焊接是将金属材料通过热和力的作用加以融合,使其成为连续的整体。
然而,在实际的焊接过程中,由于操作技术、材料和设备等因素的不完善,往往会导致焊接缺陷的产生。
以下是常见的焊接缺陷及其原因的分析。
1. 焊缝未完全填满或填充不均匀:原因一:焊接参数不合理,如焊接电流、电压、速度等设定错误,导致焊花无法完全填满焊缝。
原因二:焊接速度过快或过慢,都会导致填充不均匀的现象出现。
原因三:焊丝供给不稳定,可能会导致焊缝填充不足。
2. 焊缝未充分熔合:原因一:焊接电流过小,热量不足,焊缝无法充分熔化。
原因二:焊接速度过快,使得焊缝无法充分熔化。
原因三:焊接材料质量差,可能存在夹杂物或杂质,使焊缝无法充分熔化。
3. 焊缝裂纹:原因一:焊接过程中产生的焊接应力超过了材料的承载能力,从而引发焊缝裂纹。
原因二:焊接材料本身的裂纹敏感性较高。
原因三:焊接过程中温度过高,过快冷却,引起热应力造成裂纹。
4. 气孔:原因一:焊工操作不当,引入大量空气进入焊接区域。
原因二:焊接环境湿度过高,焊材含水量较高,蒸汽在焊接时形成气孔。
原因三:焊接电流过大,使得电解液膨胀并形成气孔。
5. 偏心焊缝:原因一:焊工操作不准确,在焊接过程中无法保持合适的焊接位置,导致焊缝偏移。
原因二:焊接设备的不准确性或不稳定性,可能导致焊缝位置不正确。
6. 焊接变形:原因一:在多道焊接中,没有采取适当的换向焊接方法,导致焊接变形。
原因二:焊接时温度过高,快速冷却会导致焊接变形。
原因三:焊接残余应力超过了材料的承载能力,导致焊接变形。
以上是焊接过程中常见的缺陷及其原因的分析,通过了解这些缺陷和原因,焊工可以采取相应的措施来减少和避免焊接缺陷的发生,从而提高焊接质量。
简述焊接缺陷及原因
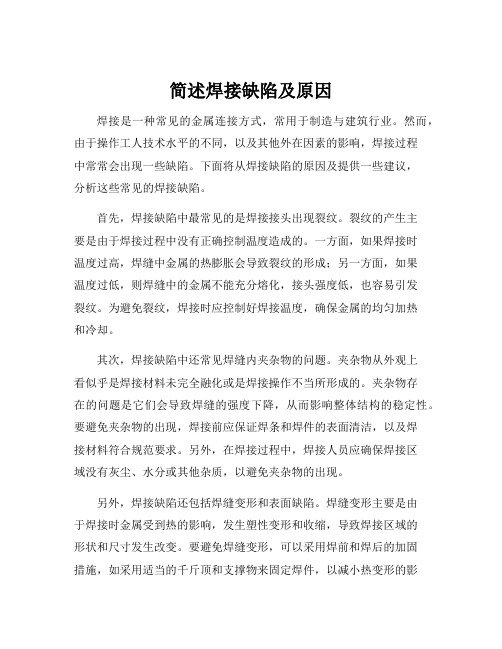
简述焊接缺陷及原因焊接是一种常见的金属连接方式,常用于制造与建筑行业。
然而,由于操作工人技术水平的不同,以及其他外在因素的影响,焊接过程中常常会出现一些缺陷。
下面将从焊接缺陷的原因及提供一些建议,分析这些常见的焊接缺陷。
首先,焊接缺陷中最常见的是焊接接头出现裂纹。
裂纹的产生主要是由于焊接过程中没有正确控制温度造成的。
一方面,如果焊接时温度过高,焊缝中金属的热膨胀会导致裂纹的形成;另一方面,如果温度过低,则焊缝中的金属不能充分熔化,接头强度低,也容易引发裂纹。
为避免裂纹,焊接时应控制好焊接温度,确保金属的均匀加热和冷却。
其次,焊接缺陷中还常见焊缝内夹杂物的问题。
夹杂物从外观上看似乎是焊接材料未完全融化或是焊接操作不当所形成的。
夹杂物存在的问题是它们会导致焊缝的强度下降,从而影响整体结构的稳定性。
要避免夹杂物的出现,焊接前应保证焊条和焊件的表面清洁,以及焊接材料符合规范要求。
另外,在焊接过程中,焊接人员应确保焊接区域没有灰尘、水分或其他杂质,以避免夹杂物的出现。
另外,焊接缺陷还包括焊缝变形和表面缺陷。
焊缝变形主要是由于焊接时金属受到热的影响,发生塑性变形和收缩,导致焊接区域的形状和尺寸发生改变。
要避免焊缝变形,可以采用焊前和焊后的加固措施,如采用适当的千斤顶和支撑物来固定焊件,以减小热变形的影响。
而表面缺陷则可能是焊接过程中气孔、烧穿、未熔合或未填充等问题所导致的。
要避免表面缺陷,焊接操作员应控制好焊接电流和电压,并使用合适的焊接速度,以确保焊接材料充分熔化和填充。
总之,焊接缺陷的产生是由于焊接过程中技术操作不当或外部因素的影响。
为避免焊接缺陷,操作人员应严格按照操作规程要求进行焊接,控制好焊接温度、清洁焊接材料和焊接区域,并使用合适的焊接设备和工具。
只有这样,才能确保焊接接头的质量,保证焊接结构的安全性和稳定性。
史上最全的焊接缺陷产生原因及处理办法

史上最全的焊接缺陷产生原因及处理办法焊接缺陷是指焊接过程中出现的质量问题,包括焊接接头的裂纹、孔隙、夹杂物等缺陷。
这些缺陷会影响焊接接头的强度、密封性和耐腐蚀性,因此及时发现并处理焊接缺陷至关重要。
本文将介绍一些常见的焊接缺陷产生原因及相应的处理办法。
1.焊接接头裂纹:原因:(1)热裂纹:焊接过程中,金属在快速冷却过程中产生应力,导致裂纹产生。
(2)冷裂纹:焊接接头长时间在低温环境下使用,受到外部冻结和膨胀引起。
处理办法:(1)控制焊接温度和预热焊件,以减少热应力。
(2)使用低氢焊条或预热焊件,以减少氢原子的进入。
(3)进行适当的回火处理,以减少残余应力。
2.焊接接头孔隙:原因:(1)焊接材料含有气体,如铁锈或涂层。
(2)焊接过程中保护性气体不足。
(3)焊接参数设置不正确,如焊接电流过低或焊接速度过快。
(4)焊接材料含有水分。
处理办法:(1)使用清洁的焊接材料,并确保焊接表面干净。
(2)提供足够的保护气体,以减少氧气和水蒸气的进入。
(3)调整焊接参数,使其适合焊接材料。
(4)在焊接前进行预热,以减少水分含量。
3.焊接接头夹杂物:原因:(1)焊接材料中包含的杂质。
(2)焊接材料与辅助材料的不匹配。
(3)焊接材料的氧化物。
处理办法:(1)使用高纯度的焊接材料,以减少杂质含量。
(2)选用合适的焊接材料和辅助材料,确保它们的化学成分相似。
(3)确保焊接材料没有明显的氧化。
4.焊接接头下沉:原因:(1)焊接时材料太薄,导致热传导速度过快。
(2)焊接过程中温度不均匀分布。
(3)焊接电流过高,引起材料融化。
处理办法:(1)加大焊接电流,以增加热量传输。
(2)调整焊接速度和焊接参数,使其适合焊接材料。
(3)使用合适的焊接材料和辅助材料,以增加熔池的稳定性。
5.焊接接头变形:原因:(1)焊接过程中产生的应力导致材料变形。
(2)焊接过程中热膨胀引起的变形。
处理办法:(1)使用适当的夹具和支撑装置,以减少焊接过程中的应力。
电渣焊常见缺陷产生原因分析及防止方法

电渣焊常见缺陷产生原因分析及防止方法一. 概述电渣焊是一种以电流通过液体溶渣所产生的电阻热作为热源的熔化焊接方法。
对于中厚板的焊接可以不开坡口而一次焊成,所以焊接生产效率比较高;同时也可以用于一些构件用常规焊接方法无法完成的焊接;例如箱形柱的隔板于翼板的焊接。
我公司为某工程制作的箱形柱,其隔板与两侧腹板采用气保焊焊后,再与上下翼板相焊。
由于隔板与两侧的间距较小,隔板的开孔也较小,焊工无法进入施焊,而且该焊缝需要焊透;质量要求较高;焊后须经超声波探伤达到Ⅱ级要求,所以只有采用电渣焊来解决。
二. 基本条件1. 箱形柱的结构形式见图一图一2. 母材型号及规格型号:Q345B 翼板厚40mm 。
隔板和腹板厚36mm3. 焊接设备⑴焊接电源:采用松下产平特性的KH Ⅱ600⑵送丝机:松下产单驱动送丝机⑶冷却水箱:型号YX-09KGC1HGE 松下产⑷控制箱、焊枪、焊枪提升机构、焊枪摆动机构:杭州欣诚祥机电技术有限公司制造。
控制箱为双极非熔咀式电渣焊控制箱。
⑸焊接操作机架为自制。
三.焊接规范由于焊接工件的厚度比较小,故而采用单丝丝极电渣焊比较合适。
因为丝极电渣焊设备较简单、操作容易、成本较低,适合于中小厚度工件的焊接,而且焊枪不用摆动即能满足要求。
1.焊接接头装配形式见图二图二2.焊接材料的选用:⑴焊丝选用强度与母材匹配的型号为ER50-6规格为ф1.6。
⑵焊剂的选用:焊剂的选用原则:a).造渣容易,电渣过程稳定;b).稳弧性能较低,当熔化成渣后,具有较合适的粘度和导电度,使电弧放电现象不致发生,才能有效避免电渣过程产生电渣-电弧夹杂过程,否则会破坏电渣焊的正常进行,甚至可使焊接中断,产生未焊透夹渣等缺陷。
基于上述原则国产焊剂可采用HJ431粒度为40-60目,进口焊剂有日铁产YF15Ⅰ。
这是一种电渣焊专用焊剂,其性能比HJ431优越。
所以电渣焊焊剂选用日铁YF15Ⅰ。
3.焊接规范焊接规范的正确与否直接影响电渣过程的稳定性和焊接质量。
焊接缺陷产生原因及防止措施
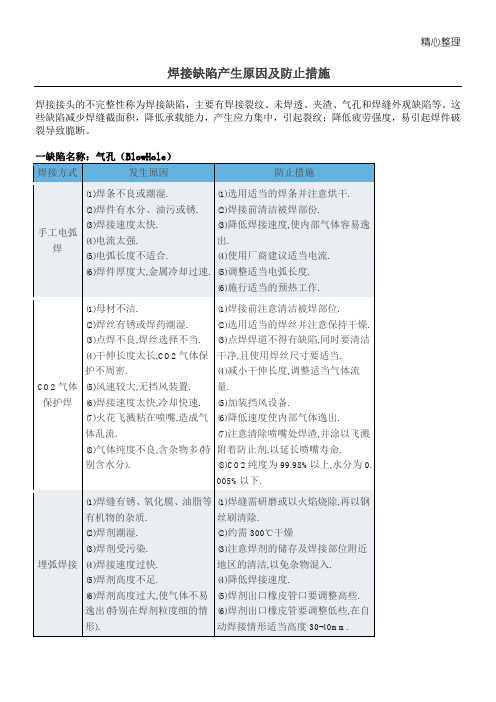
(3)焊剂受污染.
(4)焊接速度过快.
(5)焊剂高度不足.
(6)焊剂高度过大,使气体不易逸出(特别在焊剂粒度细的情形).
(7)焊丝生锈或沾有油污.
(8)极性不适当(特别在对接时受污染会产生气孔).
(1)焊缝需研磨或以火焰烧除,再以钢丝刷清除.
(2)约需300℃干燥
(3)注意焊剂的储存及焊接部位附近地区的清洁,以免杂物混入.
自保护药芯焊丝焊接、自动埋弧焊接.
(1)焊接层数太多.
(2)焊接顺序不当.
(3)施工准备不足.
(4)母材冷却过速.
(5)母材过热.(薄板)
(6)焊缝设计不当.
(7)焊着金属过多.
(8)拘束方式不确实.
(1)使用直径较大之焊条及较高电流.
(2)改正焊接顺序
(3)焊接前,使用夹具将焊件固定以免发生翘曲.
焊接缺陷产生原因及防止措施
焊接接头的不完整性称为焊接缺陷,主要有焊接裂纹、未焊透、夹渣、气孔和焊缝外观缺陷等。这些缺陷减少焊缝截面积,降低承载能力,产生应力集中,引起裂纹;降低疲劳强度,易引起焊件破裂导致脆断。
一缺陷名称:气孔(BlowHole)
焊接方式
发生原因
防止措施
手工电弧焊
(1)焊条不良或潮湿.
(1)母材不洁.
(2)焊丝有锈或焊药潮湿.
(3)点焊不良,焊丝选择不当.
(4)干伸长度太长,CO2气体保护不周密.
(5)风速较大,无挡风装置.
(6)焊接速度太快,冷却快速.
(7)火花飞溅粘在喷嘴,造成气体乱流.
(8)气体纯度不良,含杂物多(特别含水分).
(1)焊接前注意清洁被焊部位.
(2)选用适当的焊丝并注意保持干燥.
常见焊接缺陷的成因分析及对策
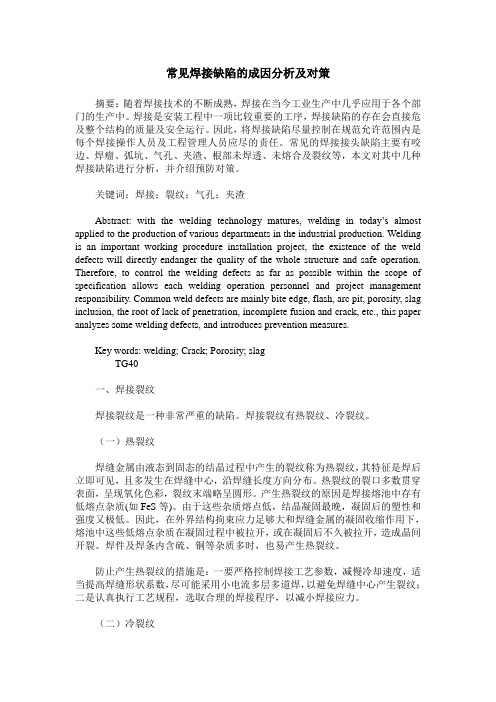
常见焊接缺陷的成因分析及对策摘要:随着焊接技术的不断成熟,焊接在当今工业生产中几乎应用于各个部门的生产中。
焊接是安装工程中一项比较重要的工序,焊接缺陷的存在会直接危及整个结构的质量及安全运行。
因此,将焊接缺陷尽量控制在规范允许范围内是每个焊接操作人员及工程管理人员应尽的责任。
常见的焊接接头缺陷主要有咬边、焊瘤、弧坑、气孔、夹渣、根部未焊透、未熔合及裂纹等,本文对其中几种焊接缺陷进行分析,并介绍预防对策。
关键词:焊接;裂纹;气孔;夹渣Abstract: with the welding techno logy matures, welding in today’s almost applied to the production of various departments in the industrial production. Welding is an important working procedure installation project, the existence of the weld defects will directly endanger the quality of the whole structure and safe operation. Therefore, to control the welding defects as far as possible within the scope of specification allows each welding operation personnel and project management responsibility. Common weld defects are mainly bite edge, flash, arc pit, porosity, slag inclusion, the root of lack of penetration, incomplete fusion and crack, etc., this paper analyzes some welding defects, and introduces prevention measures.Key words: welding; Crack; Porosity; slagTG40一、焊接裂纹焊接裂纹是一种非常严重的缺陷。
焊接缺陷分析及对策

产生原因: 焊件的间隙或边缘未被电弧熔化而留下的空隙称为 焊接电流过小,焊接速度过快,坡口小,钝边大,根部间隙 未焊透。根据未焊透的部位不同,可分为根部未焊透、 小,焊条角度不当,焊件有厚的锈蚀,埋弧焊时焊偏。 在未焊透中,还有一种叫 “未熔合”。 这是由于焊件边缘 边缘未焊透、层间未焊透等几种。 加热不充分,熔化金属都已覆盖在上面;这样,焊件边缘和焊缝 产生未焊透的部位往往也存在夹渣,连续性的未焊 金属未能熔合在一起造成了未熔合。产生原因主要是使用过大的 电流,焊条发红,以致造成熔化太快。当焊件尚未熔化,焊条的 透是极危险的缺陷。因此,在大部分结构中是不允许存 熔化金属就覆盖上去了。另外,造成未熔合的原因还有间隙太小、 焊速太快、弧长过长等。 在的。未焊透不仅使力学性能降低,而且未焊透处的缺 根部未焊透 边缘未焊透 层间未焊透 避免未焊透、未熔合的方法: 口和端部形成应力集中点,承载后往往会引起裂纹。 正确选用和加工坡口尺寸,保证必须的装配间隙,正确选用焊接 电流和焊接速度,认真操作,防止焊偏。
缝的成形系数,即形成宽而浅的焊缝,此时杂质被排至熔池
上方,在同样的拉应力作用下,却具有较高的抗热裂能力。
质量管理部
冷裂纹产生的原因
1、焊接及热影响区收缩产生大的应力。 2、淬硬的显微组织。 3、焊缝中有相当高的氢浓度。
防止冷裂纹的措施
1、选用能降低焊缝金属扩散氢的低氢焊条。
2、焊条、焊剂严格按要求进行烘干。 3、根据材质需要,焊前进行适当预热。 4、焊后立即进行后热或保温。 5、使用碳当量低的钢材。 6、适当增加焊接电流,减慢焊接速度,可降低冷却速度。
危险的缺欠。
质量管理部
按产生的部位不同可分为纵向裂纹、横向裂纹、根部裂纹、 弧坑裂纹、熔合区裂纹以及热影响区裂纹等。
焊接质量缺陷原因分析及预防、治理措施
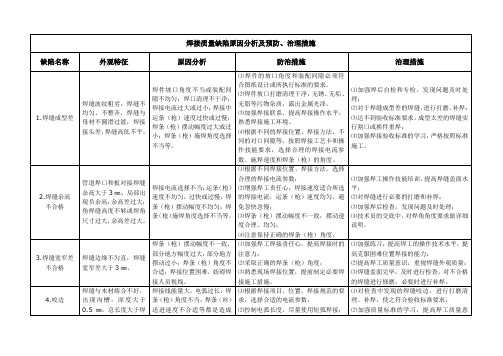
⑴延长收弧时间; ⑵采取正确的收弧方法。
8.表面气孔
焊接过程中,熔池中的 气体未完全溢出熔池 (一部分溢出) , 而熔池 已经凝固,在焊缝表面 形成孔洞。
⑴母材、焊丝按照要求清理干净。 ⑵焊条按照要求烘培。 ⑶防风措施严格,无穿堂风等。 ⑷选用合适的焊接线能量参数,焊接速 度不能过快,电弧不能过长,正确掌握 起弧、运条、息弧等操作要领。 ⑸氩弧焊时保护气流流量合适,氩气纯 度符合要求。
5.错口
表现为焊缝两侧外壁母 材不在同一平面上,错 口量大于 10 %母材厚 度或超过 4 ㎜。
焊件对口不符合要求, 焊工在 对口不合适的情况下点固和 焊接。
6.弯折
由于焊缝的横向收缩或 安装对口偏差而造成的 垂直于焊缝的两侧母材 不在同一平面上,形成 一定的夹角。
⑴安装对口不合适, 本身形成 一定夹角; ⑵焊缝熔敷金属在凝固过程 中本身横向收缩; ⑶焊接过程不对称施焊。
⑴对口间隙、坡口制备、钝边厚度符合标准 要求; ⑵加强打底练习, 熟练掌握操作手法以及对 应的焊接线能量及焊接速度等。
这些缺陷一般出现在吊 18.管道焊口根 焊或斜焊焊口根部,在 部焊瘤、凸出、 平焊及斜平焊位置出现 凹陷 根部焊缝凸出或焊瘤,
9 表面夹渣
在焊接过程中,主要是 在层与层间出现外部看 到的药皮夹渣。
10.表面裂纹
在焊接接头的焊缝、熔 合线、热影响区出现的 表面开裂缺陷。
⑴严格按照规程和作业指导书的要求 准备各种焊接条件; ⑵提高焊接操作技能,熟练掌握使用的 焊接方法; ⑶采取合理的焊接顺序等措施,减少焊 接应力等。
⑴针对每种产生裂纹的具体原因采取相应 的对策; ⑵对已经产生裂纹的焊接接头, 采取挖补措 施处理。
12.支吊架等 T 型焊接接头焊 缝不包角
焊接缺陷产生原因分析及防治措施

焊接缺陷产生原因分析及防治措施随着现代工业和制造业的发展,焊接技术的应用越来越广泛。
然而,在不断增加的焊接工程中,焊接缺陷问题也日益凸显。
焊接缺陷对焊接接头的质量和性能有着不可忽视的影响。
为了提高焊接接头的质量,需要深入了解焊接缺陷的产生原因,采取有效的防治措施。
一、焊接缺陷的分类1.焊接孔洞:是最严重的缺陷之一。
它们出现的原因可能是由于焊接区域的污染、松散物质、气孔或有效焊接熔池成分的合金不足导致。
2.焊接裂纹:由焊接过程引起的应力、过热或过冷引起的应力,不良的焊接施工或材料导致的应力等因素造成的裂纹。
3.焊接夹渣:焊接时,渣和气泡也可能在焊接接头中被引入。
这些夹杂物的存在会导致焊接接头的强度下降。
4.焊接凸起:易于出现在对焊、拖焊和坡口焊焊接的开端,并且很难消除。
二、焊接缺陷产生的原因1.焊接材料的质量问题。
如果使用的焊丝或焊条受到了污染或材料不合格等问题,焊接接头质量就可能受到影响。
2.操作不当。
如果焊接时没有遵循标准的焊接工艺,如焊接电流、电压和气体流量等设置不当,也会导致焊接缺陷。
3.人为原因。
焊接操作者经验和技术的欠缺,不正确的操作和操作步骤,从而引起焊接缺陷。
4.材料选择不当。
对于不同的焊接材料,需要选用不同的焊接工艺和方法,如果选用不当,也会导致焊接缺陷的产生。
三、防治焊接缺陷的措施1.提高焊接材料的质量。
在焊接材料的选择过程中,应尽量选用高品质的焊接材料,并确保其焊接性能符合要求。
2.正确选用焊接工艺。
焊接工艺应合理,具有合适的焊接参数、清洁度和气体保护等等。
3.加强焊接培训。
工人必须受到焊接培训并掌握合适的焊接技术、方法和技巧。
4.加强质量管理。
通过加强质量管理,避免质量问题和无序操作,杜绝相关缺陷的出现。
5.实施检测和验证。
利用非毁性检测等试验方法,确保焊接质量,消除潜在缺陷。
综上所述,理解焊接缺陷产生的原因是关键,如何采取有效的防治措施,对保证焊接接头的安全和质量至关重要。
电渣焊常见缺陷产生原因分析及防止方法【VIP专享】

电渣焊常见缺陷产生原因分析及防止方法一.概述电渣焊是一种以电流通过液体溶渣所产生的电阻热作为热源的熔化焊接方法。
对于中厚板的焊接可以不开坡口而一次焊成,所以焊接生产效率比较高;同时也可以用于一些构件用常规焊接方法无法完成的焊接;例如箱形柱的隔板于翼板的焊接。
我公司为某工程制作的箱形柱,其隔板与两侧腹板采用气保焊焊后,再与上下翼板相焊。
由于隔板与两侧的间距较小,隔板的开孔也较小,焊工无法进入施焊,而且该焊缝需要焊透;质量要求较高;焊后须经超声波探伤达到Ⅱ级要求,所以只有采用电渣焊来解决。
二.基本条件1.箱形柱的结构形式见图一图一2.母材型号及规格型号:Q345B 翼板厚40mm 。
隔板和腹板厚36mm 3.焊接设备⑴焊接电源:采用松下产平特性的KH Ⅱ600⑵送丝机:松下产单驱动送丝机⑶冷却水箱:型号YX-09KGC1HGE 松下产⑷控制箱、焊枪、焊枪提升机构、焊枪摆动机构:杭州欣诚祥机电技术有限公司制造。
控制箱为双极非熔咀式电渣焊控制箱。
⑸焊接操作机架为自制。
三.焊接规范由于焊接工件的厚度比较小,故而采用单丝丝极电渣焊比较合适。
因为丝极电渣焊设备较简单、操作容易、成本较低,适合于中小厚度工件的焊接,而且焊枪不用摆动即能满足要求。
1.焊接接头装配形式见图二图二2.焊接材料的选用:⑴焊丝选用强度与母材匹配的型号为ER50-6规格为ф1.6。
⑵焊剂的选用:焊剂的选用原则:a).造渣容易,电渣过程稳定;b).稳弧性能较低,当熔化成渣后,具有较合适的粘度和导电度,使电弧放电现象不致发生,才能有效避免电渣过程产生电渣-电弧夹杂过程,否则会破坏电渣焊的正常进行,甚至可使焊接中断,产生未焊透夹渣等缺陷。
基于上述原则国产焊剂可采用HJ431粒度为40-60目,进口焊剂有日铁产YF15Ⅰ。
这是一种电渣焊专用焊剂,其性能比HJ431优越。
所以电渣焊焊剂选用日铁YF15Ⅰ。
3.焊接规范焊接规范的正确与否直接影响电渣过程的稳定性和焊接质量。
焊接夹渣产生的原因

焊接夹渣产生的原因1. 哎呀,焊接夹渣产生的原因之一可能是焊接速度太快啦!就好比你跑步太快,是不是就容易摔跤呀,焊接也是这样,速度一快,就容易出问题,夹渣就出现啦!比如那次我焊接的时候,就因为太着急了,结果就有夹渣了。
2. 焊接电流太小也会导致夹渣哦!这就好像你吃饭吃得太少,就没力气干活呀。
你想想,电流小了,那焊接能牢固吗?肯定容易有夹渣呀!上次看到别人焊接,电流调得不合适,夹渣可明显了。
3. 焊条角度不对也不行呀!这就像你走路姿势不对,是不是就走不稳呀。
焊接的时候焊条角度不对,那夹渣不就跟着来了嘛!我有次就是焊条角度没弄好,夹渣问题就来了。
4. 焊缝清理不干净,这可是个大问题呢!就像你脸上有脏东西没洗掉,多难看呀。
焊接也是一样,如果焊缝不干净,夹渣肯定就容易产生啦!记得有回焊接前没清理好,夹渣可把我愁坏了。
5. 焊条质量不好也会惹祸呀!这好比你买了双质量差的鞋子,穿不了多久就坏了。
焊条质量不行,焊接时能不出夹渣吗?有次用了质量不太好的焊条,夹渣就找上门了。
6. 焊接工艺不合适也会导致夹渣呀!这就像你选择了不适合自己的发型,怎么看都别扭。
如果焊接工艺不对,夹渣就容易出现啦!那次就是工艺没选对,夹渣问题让我头疼了好久。
7. 母材表面有杂质,这可太容易产生夹渣了!就好像你要画画,纸是脏的,那画能好看吗?焊接的时候母材有杂质,夹渣肯定少不了。
有次看到母材没处理好就焊接,夹渣多得吓人。
8. 焊接时的环境不好也会影响哦!你想想,在一个乱糟糟的环境里做事,能做好吗?焊接时环境不好,夹渣就可能趁机出现啦!有回在很糟糕的环境下焊接,夹渣问题就很严重。
9. 焊工技术不过关,那夹渣可就容易来啦!就像你学骑自行车,技术不好就会摔倒呀。
焊工技术不行,夹渣就容易出现呀!看到过一些新手焊接,夹渣问题比较多。
10. 焊接时的温度不合适也不行呀!这就好像洗澡水温度不合适,要么太冷要么太热。
焊接温度不合适,夹渣肯定容易产生呀!记得有次温度没控制好,夹渣就出现了。
焊接缺陷产生原因及防止措施

焊接缺陷产生原因及防止措施焊接接头的不完整性称为焊接缺陷,主要有焊接裂纹、未焊透、夹渣、气孔和焊缝外观缺陷等。
这些缺陷减少焊缝截面积,降低承载能力,产生应力集中,引起裂纹;降低疲劳强度,易引起焊件破裂导致脆断。
一缺陷名称:气孔(Blow Hole)焊接方式发生原因防止措施手工电弧焊(1)焊条不良或潮湿. (2)焊件有水分、油污或锈. (3)焊接速度太快. (4)电流太强.(5)电弧长度不适合. (6)焊件厚度大,金属冷却过速.(1)选用适当的焊条并注意烘干.(2)焊接前清洁被焊部份. (3)降低焊接速度,使内部气体容易逸出.(4)使用厂商建议适当电流. (5)调整适当电弧长度. (6)施行适当的预热工作.CO2气体保护焊(1)母材不洁. (2)焊丝有锈或焊药潮湿. (3)点焊不良,焊丝选择不当. (4)干伸长度太长,CO2气体保护不周密.(5)风速较大,无挡风装置.(6)焊接速度太快,冷却快速.(7)火花飞溅粘在喷嘴,造成气体乱流. (8)气体纯度不良,含杂物多(特别含水分).(1)焊接前注意清洁被焊部位. (2)选用适当的焊丝并注意保持干燥.(3)点焊焊道不得有缺陷,同时要清洁干净,且使用焊丝尺寸要适当.(4)减小干伸长度,调整适当气体流量. (5)加装挡风设备. (6)降低速度使内部气体逸出. (7)注意清除喷嘴处焊渣,并涂以飞溅附着防止剂,以延长喷嘴寿命. (8)CO2纯度为%以上,水分为%以下.埋弧焊接(1)焊缝有锈、氧化膜、油脂等有机物的杂质. (2)焊剂潮湿. (3)焊剂受污染. (4)焊接速度过快. (5)焊剂高度不足. (6)焊剂高度过大,使气体不易逸出(特别在焊剂粒度细的情形). (7)焊丝生锈或沾有油污. (8)极性不适当(特别在对接时受污染会产生气孔).(1)焊缝需研磨或以火焰烧除,再以钢丝刷清除. (2)约需300℃干燥(3)注意焊剂的储存及焊接部位附近地区的清洁,以免杂物混入. (4)降低焊接速度. (5)焊剂出口橡皮管口要调整高些. (6)焊剂出口橡皮管要调整低些,在自动焊接情形适当高度30-40mm. (7)换用清洁焊丝. (8)将直流正接(DC-)改为直流反接(DC+).设备不良(1)减压表冷却,气体无法流出. (2)喷嘴被火花飞溅物堵塞. (3)焊丝有油、锈.(1)气体调节器无附电热器时,要加装电热器,同时检查表之流量. (2)经常清除喷嘴飞溅物.并且涂以飞溅附着防止剂. (3)焊丝贮存或安装焊丝时不可触及油类.自保护药芯焊丝(1)电压过高. (2)焊丝突出长度过短. (3)钢板表面有锈蚀、油漆、水分. (4)焊枪拖曳角倾斜太多. (5)移行速度太快,尤其横焊.(1)降低电压. (2)依各种焊丝说明使用. (3)焊前清除干净. (4)减少拖曳角至约0-20°.(5)调整适当.典型缺陷照片二缺陷名称咬边(Undercut)焊接方式发生原因防止措施手工电弧焊(1)电流太强. (2)焊条不适合. (3)电弧过长. (4)操作方法不当. (5)母材不洁. (6)母材过热.(1)使用较低电流. (2)选用适当种类及大小之焊条. (3)保持适当的弧长. (4)采用正确的角度,较慢的速度,较短的电弧及较窄的运行法.(5)清除母材油渍或锈. (6)使用直径较小之焊条.CO2气体保护焊(1)电弧过长,焊接速度太快.(2)角焊时,焊条对准部位不正确. (3)立焊摆动或操作不良,使焊道二边填补不足产生咬边.(1)降低电弧长度及速度. (2)在水平角焊时,焊丝位置应离交点1-2mm. (3)改正操作方法.典型缺陷照片三缺陷名称:夹渣(Slag Inclusion)焊接方式发生原因防止措施手工电弧焊(1)前层焊渣未完全清除.(2)焊接电流太低. (3)焊接速度太慢. (4)焊条摆动过宽. (5)焊缝组合及设计不良.(1)彻底清除前层焊渣. (2)采用较高电流. (3)提高焊接速度. (4)减少焊条摆动宽度. (5)改正适当坡口角度及间隙.CO2气体电弧焊(1)母材倾斜(下坡)使焊渣超前. (2)前一道焊接后,焊渣未清洁干净. (3)电流过小,速度慢,焊着量多. (4)用前进法焊接,开槽内焊渣超前甚(1)尽可能将焊件放置水平位置.(2)注意每道焊道之清洁. (3)增加电流和焊速,使焊渣容易浮起. (4)提高焊接速度多.埋弧焊接(1)焊接方向朝母材倾斜方向,因此焊渣流动超前. (2)多层焊接时,开槽面受焊丝溶入,焊丝过于靠近开槽的侧边. (3)在焊接起点有导板处易产生夹渣. (4)电流过小,第二层间有焊渣留存,在焊接薄板时容易产生裂纹. (5)焊接速度过低,使焊渣超前.(6)最后完成层电弧电压过高,使得游离焊渣在焊道端头产生搅卷.(1)焊接改向相反方向焊接,或将母材尽可能改成水平方向焊接. (2)开槽侧面和焊丝之间距离,最少要大于焊丝直径以上. (3)导板厚度及开槽形状,需与母材相同. (4)提高焊接电流,使残留焊渣容易熔化. (5)增加焊接电流及焊接速度. (6)减小电压或提高焊速,必要时盖面层由单道焊改为多道焊接.自保护药芯焊丝(1)电弧电压过低. (2)焊丝摆弧不当. (3)焊丝伸出过长. (4)电流过低,焊接速度过慢. (5)第一道焊渣,未充分清除. (6)第一道结合不良. (7)坡口太狭窄. (8)焊缝向下倾斜.(1)调整适当. (2)加多练习. (3)依各种焊丝使用说明. (4)调整焊接参数. (5)完全清除(6)使用适当电压,注意摆弧. (7)改正适当坡口角度及间隙. (8)放平,或移行速度加快.典型缺陷照片四缺陷名称:未焊透(Incomplete Penetration)焊接方式发生原因防止措施手工电弧焊(1)焊条选用不当. (2)电流太低. (3)焊接速度太快温度上升不够,又进行速度太慢电弧冲力被焊渣所阻挡,不能给予母材. (4)焊缝设计及组合不正确.(1)选用较具渗透力的焊条. (2)使用适当电流. (3)改用适当焊接速度. (4)增加开槽度数,增加间隙,并减少根深.CO2气体保护焊(1)电弧过小,焊接速度过低.(2)电弧过长. (3)开槽设计不良.(1)增加焊接电流和速度. (2)降低电弧长度. (3)增加开槽度数.增加间隙减少根深.自保护药芯焊丝(1)电流太低. (2)焊接速度太慢. (3)电压太高. (4)摆弧不当. (5)坡口角度不当.(1)提高电流. (2)提高焊接速度.(3)降低电压. (4)多加练习. (5)采用开槽角度大一点.典型缺陷照片五缺陷名称:裂纹(Crack)焊接方式发生原因防止措施手工电弧焊(1)焊件含有过高的碳、锰等合金元素. (2)焊条品质不良或潮湿. (3)焊缝拘束应力过大. (4)母条材质含硫过高不适于焊接. (5)施工准备不足. (6)母材厚度较大,冷却过速. (7)电流太强. (8)首道焊道不足抵抗收缩应力.(1)使用低氢系焊条. (2)使用适宜焊条,并注意干燥. (3)改良结构设计,注意焊接顺序,焊接后进行热处理. (4)避免使用不良钢材. (5)焊接时需考虑预热或后热. (6)预热母材,焊后缓冷. (7)使用适当电流.(8)首道焊接之焊着金属须充分抵抗收缩应力.CO2气体保护焊(1)开槽角度过小,在大电流焊接时,产生梨形和焊道裂纹. (2)母材含碳量和其它合金量过高(焊道及热影区).(3)多层焊接时,第一层焊道过小. (4)焊接顺序不当,产生拘束力过强. (5)焊丝潮湿,氢气侵入焊道. (6)套板密接不良,形成高低不平,致应力集中. (7)因第一层焊接量过多,冷却缓慢(不锈钢,铝合金等).(1)注意适当开槽角度与电流的配合,必要时要加大开槽角度. (2)采用含碳量低的焊条. (3)第一道焊着金属须充分能抵抗收缩应力. (4)改良结构设计,注意焊接顺序,焊后进行热处理. (5)注意焊丝保存. (6)注意焊件组合之精度. (7)注意正确的电流及焊接速度.埋弧焊接(1)对焊缝母材所用的焊丝和焊剂之配合不适当(母材含碳量过大,焊丝金属含锰量太少). (2)焊道急速冷却,使热影响区发生硬化. (3)焊丝含碳、硫量过大. (4)在多层焊接之第一层所生焊道力,不足抵抗收缩应力. (5)在角焊时过深的渗透或偏析. (6)焊接施工顺序不正确,母材拘束力大. (7)焊道形状不适当,焊道宽度与焊道深度比例过大或过小.(1)使用含锰量较高的焊丝,在母材含碳量多时,要有预热之措施. (2)焊接电流及电压需增加,焊接速度降低,母材需加热措施. (3)更换焊丝.(4)第一层焊道之焊着金属须充分抵抗收缩应力. (5)将焊接电流及焊接速度减低,改变极性. (6)注意规定的施工方法,并予焊接操作施工指导. (7)焊道宽度与深度的比例约为1:1:25,电流降低,电压加大.典型缺陷照片六缺陷名称:变形(Distortion)焊接方式发生原因防止措施手焊、CO 2气体保护焊、自保护药芯焊丝焊接、自动埋弧焊接.(1)焊接层数太多. (2)焊接顺序不当. (3)施工准备不足. (4)母材冷却过速. (5)母材过热.(薄板) (6)焊缝设计不当. (7)焊着金属过多.(8)拘束方式不确实.(1)使用直径较大之焊条及较高电流. (2)改正焊接顺序(3)焊接前,使用夹具将焊件固定以免发生翘曲. (4)避免冷却过速或预热母材.(5)选用穿透力低之焊材. (6)减少焊缝间隙,减少开槽度数. (7)注意焊接尺寸,不使焊道过大. (8)注意防止变形的固定措施.七其他缺陷缺陷名称发生原因防止措施搭叠(Overlap)(1)电流太低. (2)焊接速度太慢.(1)使用适当的电流. (2)使用适合的速度.焊道外观形状不良(Bad Appearance)(1)焊条不良. (2)操作方法不适. (3)焊接电流过高,焊条直径过粗. (4)焊件过热.(5)焊道内,熔填方法不良.(6)导电嘴磨耗. (7)焊丝伸出长度不变.(1)选用适当大小良好的干燥焊条.(2)采用均匀适当之速度及焊接顺序. (3)选用适当电流及适当直径的焊接. (4)降低电流. (5)多加练习.(6)更换导电嘴. (7)保持定长、熟练.凹痕(Pit)(1)使用焊条不当. (2)焊条潮湿. (3)母材冷却过速. (4)焊条不洁及焊件的偏析. (5)焊件含碳、锰成分过高.(1)使用适当焊条,如无法消除时用低氢型焊条. (2)使用干燥过的焊条. (3)减低焊接速度,避免急冷,最好施以预热或后热. (4)使用良好低氢型焊条. (5)使用盐基度较高焊条.偏弧(Arc Blow)(1)在直流电焊时,焊件所生磁场不均,使电弧偏向. (2)接地线位置不佳. (3)焊枪拖曳角太大. (4)焊丝伸出长度太短. (5)电压太高,电弧太长. (6)电流太大. (7)焊接速度太快.(1)·电弧偏向一方置一地线.·正对偏向一方焊接.·采用短电弧.·改正磁场使趋均一.·改用交流电焊(2)调整接地线位置. (3)减小焊枪拖曳角. (4)增长焊丝伸出长度. (5)降低电压及电弧. (6)调整使用适当电流. (7)焊接速度变慢.烧穿(1)在有开槽焊接时,电流过大. (2)因开槽不良焊缝间隙太大.(1)降低电流. (2)减少焊缝间隙.焊道不均匀(1)导电嘴磨损,焊丝输出产生摇摆. (2)焊枪操作不熟练.(1)将焊接导电嘴换新使用. (2)多加操作练习.焊泪(1)电流过大,焊接速度太慢.(2)电弧太短,焊道高. (3)焊丝对准位置不适当.(角焊时)(1)选用正确电流及焊接速度. (2)提高电弧长度. (3)焊丝不可离交点太远.火花飞溅过多(1)焊条不良. (2)电弧太长.(3)电流太高或太低. (4)电弧电压太高或太低. (5)焊丝突出过长 . (6)焊枪倾斜过度,拖曳角太大. (7)焊丝过度吸湿. (8)焊机情况不良.(1)采用干燥合适之焊条. (2)使用较短之电弧. (3)使用适当之电流.(4)调整适当. (5)依各种焊丝使用说明. (6)尽可能保持垂直,避免过度倾斜. (7)注意仓库保管条件. (8)修理,平日注意保养.焊道成蛇行状(1)焊丝伸出过长. (2)焊丝扭曲. (3)直线操作不良.(1)采用适当的长度,例如实心焊丝在大电流时伸出长20-25mm.在自保护焊接时伸出长度约为40-50mm.(2)更换新焊丝或将扭曲予以校正.(3)在直线操作时,焊枪要保持垂直.电弧不稳定(1)焊枪前端之导电嘴比焊丝心径大太多. (2)导电嘴发生磨损. (3)焊丝发生卷曲. (4)焊丝输送机回转不顺. (5)焊丝输送轮子沟槽磨损. (6)加压轮子压紧不良. (7)导管接头阻力太大.(1)焊丝心径必须与导电嘴配合.(2)更换导电嘴. (3)将焊丝卷曲拉直. (4)将输送机轴加油,使回转润滑. (5)更换输送轮. (6)压力要适当,太松送线不良,太紧焊丝损坏.(7)导管弯曲过大,调整减少弯曲量.喷嘴与母材间发生电弧(1)喷嘴,导管或导电嘴间发生短路.(1)火花飞溅物粘及喷嘴过多须除去,或是使用焊枪有绝缘保护之陶瓷管.焊枪喷嘴过热(1)冷却水不能充分流出.(2)电流过大.(1)冷却水管不通,如冷却水管阻塞,必须清除使水压提升流量正常. (2)焊枪使用在容许电流范围及使用率之内.焊丝粘住导电嘴(1)导电嘴与母材间的距离过短. (2)导管阻力过大,送线不良. (3)电流太小,电压太大.(1)使用适当距离或稍为长些来起弧,然后调整到适当距离. (2)清除导管内部,使能平稳输送. (3)调整适当电流,电压值.典型缺陷照片-焊穿--搭叠--焊道蛇形-。
焊接缺陷及产生原因

焊接缺陷及产生原因焊接缺陷产生原因及防止措施一、焊接缺陷定义焊接接头的不完整性称为焊接缺陷,主要有焊接裂纹、未焊透、夹渣、气孔和焊缝外观缺陷等。
这些缺陷减少焊缝截面积,降低承载能力,产生应力集中,引起裂纹;降低疲劳强度,易引起焊件破裂导致脆断。
其中危害最大的是焊接裂纹和气孔。
二、焊接缺陷的分类焊接生产中产生焊接缺陷的种类是多种多样的,按其在焊接接头中所处的位置和表现形式的不同,可以把焊接缺陷大致分为两类:一类是外部缺陷;另一类是内部缺陷。
焊接缺陷的详细分类如图1所示。
图1 焊接缺陷分类图焊接缺陷示意图如图2所示:(a)裂纹(b)焊瘤(c)焊穿(d)弧坑(e)气孔(f)夹渣(g )咬边 (h )未融合 (i )未焊透图2 焊接缺陷示意图三、影响焊接缺陷的因素1. 材料因素所谓材料因素是指被焊的母材和所使用的焊接材料,如焊丝、焊条、焊剂及保护气体等。
这些材料在焊接时都直接参与熔池或熔合区的物理化学反应,其中,母材本身的材质对热影响区的性能起着决定性的作用,当然,所采用的焊接材料对焊缝金属的成分和性能也是关键因素。
如果焊材与母材匹配不当,不仅可能引起焊接区内的裂纹、气孔等各种缺陷,也可能引起脆化、软化等性能变化。
所以,为了保证得到良好的焊接接头,必须对材料因素予以重视。
2.工艺因素同一种母材,在采用不同的焊接方法和工艺措施的条件下,其焊接质量会表现出很大的差别。
焊接方法对焊接质量的影响主要在两个方面:首先是焊接热源的特点,其可以直接改变焊接热循环的各项参数,如线能量、高温停留时间、冷却速度等;其次是对熔池和接头附近区域的保护方式,如渣保护、气保护等。
焊接热过程和冶金过程必然对接头的质量和性能会有决定性的影响。
3.结构因素焊接接头的结构设计影响其受力状态,其既可能影响焊接时是否发生缺陷,又可能影响焊后接头的力学性能。
设计焊接结构时,应尽量使接头处于拘束度较小、能自由伸缩的状态,这样有利于防止焊接裂纹的产生。
- 1、下载文档前请自行甄别文档内容的完整性,平台不提供额外的编辑、内容补充、找答案等附加服务。
- 2、"仅部分预览"的文档,不可在线预览部分如存在完整性等问题,可反馈申请退款(可完整预览的文档不适用该条件!)。
- 3、如文档侵犯您的权益,请联系客服反馈,我们会尽快为您处理(人工客服工作时间:9:00-18:30)。
注意请除前道焊渣,正确运条,以利于熔渣浮出。
KPX 蓄电池、KPD 36V 轨道供电及 KPJ 卷筒供电电动平车比较:
型号/吨位 KPX 蓄电池电动平车 KPD(S)36V 轨道供电平车
KPJ 卷筒供电平车
电源
DG 牵引蓄电池
AC380 降压至 36V 到轨道再升 压至 AC380 V
AC380V
轨道要求
电动平车安装焊接夹渣焊接缺陷原因分析
新乡市百分百机电有限公司
夹渣是指残留在焊缝金属中的溶渣,即由于焊接冶金过程中熔池中的一些非金 属夹杂物在结晶过程中来不及浮出而残存在焊缝内部。药芯焊丝和埋弧焊容易产 生夹渣。夹渣的产生与焊接方法、焊材(焊丝、焊剂)及被焊母材的成份纯度有 关。夹渣主要分为根部夹渣、焊层及晶界夹渣、缝焊内夹渣。
容易
设备投资
高
轨道基础投资
低
保养
中
可靠性
高
无线遥控
可选
连续工作 需调换备用蓄电池组
容易 略高
高 难 中 不推荐 Yes
容易 最低
低 易 高 可选 Yes
环境要求
不推荐室外使用,雨雪、潮湿易 不适用于轨道区道路有
加速轨道绝缘老化。
汽车通行的场合。
经济方面:与目前社会上普遍使用的铅酸电池相比,锂电池是其价格的 3 倍左右,对中国普通老百姓来说,这存在着很大的经济负担,所以锂电池电动 平板车现在销售份额非常低。相对来说,铅酸电池的性价比更高。今年,3 月 29 日国务院办公会议批准全国 10 个省“电动车下乡”后,充分表明国家对铅酸电 动车的产业支持。因为经济上的补贴,将直接刺激农民选购电动车作为其代步及 致富工具的热情。而锂电池电动车则因为价格昂贵,农村市场的经济承载能力有 限,因此,‘电动车下乡’可以说是铅酸电池电动车下乡而非锂电池电动车下乡。 新日预计,电动车下乡将拉动 18 亿电动车的消费
环保方面,锂电池由于技术上存在缺陷,所以在全世界现在锂电池都没 回收价值,一般都是粉碎深埋处理,对环境具有一定的污染,这一点大家对于使 用手机电池就有深刻体会。而铅的用途更广且技术成熟,目前,在我国铅酸电池 由于具有很高的回收经济价值,大部分都被合理回收,所以在中国的垃圾筒中找 不到旧的铅酸电池。所以,在可预见的未来,铅酸电池更符合电动车节能环保的 特性以及目前‘低碳经济’的要求,在很长时间内仍将是电动平板车,复杂,轨道之间要求绝缘,并加 铜补偿线
简单
安全耐侯性
最高 时间长
潮湿、金属件跌落、几年后绝缘 电缆拉断,被金属件压断
老化等易导致跳闸,影响工作。
等导致停机。
机动性
高 允许道岔,转弯,任
意长轨道
中 允许道岔,转弯,轨道长度受变
压器送电距离限制
低 只能直线轨道,运行距离
一般小于 200 米
维修/操作
1、危害:不仅降低力学性能,而且增加了产生热裂纹的倾向,诱发厚板的层 状撕裂。
2、产生原因:1、焊接电流太小,液态金属和熔渣分不开。
2、焊接速度过快,熔渣来不及浮出来。
3、多层焊对工件边缘和焊缝清理不干净。
4、运条角度不正确。
3、电动平车防止措施:应正确选择焊接材料(焊丝纯度、焊剂),控制母材硫
磷的含量,工艺上应选择适当的焊接参数,使熔池存在时间不要太短。多层焊时,