石油炼制中废气来源及处理
石油炼制废气净化改造及脱硫脱硝工程技术方案

石油炼制废气净化改造及脱硫脱硝工程技术方案介绍本文档旨在提供一种对石油炼制废气进行净化改造以及脱硫脱硝的工程技术方案。
通过采用简单且无法引起法律风险的策略,我们将重点解决废气处理中的主要问题,并提出相应的解决方案。
废气净化改造方案废气净化改造是为了减少石油炼制过程中产生的有害气体排放。
我们建议采用以下几个步骤来实施废气净化改造:1. 废气监测与分析:首先,对石油炼制过程中产生的废气进行监测和分析,以确定主要的污染物和排放浓度。
废气监测与分析:首先,对石油炼制过程中产生的废气进行监测和分析,以确定主要的污染物和排放浓度。
2. 废气收集与处理:将废气有效地收集起来,并通过适当的处理设备进行处理,如采用活性炭吸附、湿式洗涤等方法来去除有害物质。
废气收集与处理:将废气有效地收集起来,并通过适当的处理设备进行处理,如采用活性炭吸附、湿式洗涤等方法来去除有害物质。
3. 废气排放监控:在废气净化改造后,建立废气排放监控系统,以确保排放符合相关的环境标准和法规要求。
废气排放监控:在废气净化改造后,建立废气排放监控系统,以确保排放符合相关的环境标准和法规要求。
脱硫脱硝工程技术方案脱硫和脱硝是减少石油炼制废气中二氧化硫和氮氧化物排放的重要措施。
以下是我们的工程技术方案:1. 脱硫工艺选择:根据炼厂的具体情况,选择适合的脱硫工艺,如湿法脱硫或干法脱硫,并确保该工艺符合环境标准。
脱硫工艺选择:根据炼厂的具体情况,选择适合的脱硫工艺,如湿法脱硫或干法脱硫,并确保该工艺符合环境标准。
2. 脱硝工艺选择:针对石油炼制废气中的氮氧化物排放,选择适当的脱硝工艺,如选择选择选择选择选择选择,以降低氮氧化物的排放浓度。
脱硝工艺选择:针对石油炼制废气中的氮氧化物排放,选择适当的脱硝工艺,如选择选择选择选择选择选择,以降低氮氧化物的排放浓度。
3. 脱硫脱硝设备安装与调试:安装并调试脱硫脱硝设备,确保其正常运行并达到预期的脱硫脱硝效果。
脱硫脱硝设备安装与调试:安装并调试脱硫脱硝设备,确保其正常运行并达到预期的脱硫脱硝效果。
石油化工废气治理方案-有机废气处理

石油化学工企业排放包括:烃类、醇类、醛类、酸类、酮类和胺类、丁二烯、二氯甲烷等有机物废气。
选择治理方案的几个基本要素:根据废气成分(是否含有水分、固态物、油状物,及处理难易程度)、浓度(高、低)、排放形式(连续或间歇排放)选择处理方案。
以下情况适合选择等高温离子焚烧处理方案:有机物含量较高、成分复杂、易燃易爆(丁二烯等)、较难分解物质如二硫化碳,含有颗粒物、油状物、连续大剂量排放的工业废气。
如凹版印刷、胶板印刷、涂装、化学合成、石油化工、香精、香料等行业。
以下情况需要增加旋风除尘装置:含有颗粒物的工业废气,如涂装行业废气。
以下情况需要增加冷凝器:废气温度超过70℃且含有大量水分,需要加装冷凝器。
以下情况需要增加气、液(油)分离装置:1、含有油状物的工业废气,如垃圾焚烧装置排放尾气。
2、含有大量水分。
以下情况需要加装防爆阻火器(天然气防爆阻火器)、防爆井及爆破片废气中含易燃易爆成分,工作场所有防爆要求。
高温等离子焚烧技术:高温等离子焚烧技术是高频(30KHz)高压(100KV)大功率电源在特定条件下的聚能放电,产生3千℃等离子态高温气流。
待处理气体在反应器中经过压缩、高压聚能放电成为高温等离子体。
处理过程中气体由常温急剧上升至3千度高温,反应器压力增高,气体体积也因此急剧膨胀,在极短的时间里完成物质的裂解过程。
经高温等离子焚烧处理,废气中长分子链有机物裂解成单质原子。
处理设备排出气体主要成分为二氧化碳、水蒸气。
高温等离子焚烧技术能够处理高浓度、成分复杂、易燃易爆、含有固态、油状物的工业废气。
天然气防爆阻火器(定制):该产品适用输送可燃性气体、加热炉燃料气、石油液化气、煤矿瓦斯及民用煤气管道管网,防止在非正常情况下火焰于管道中的逆向传播,防止外部火焰窜入存有易燃易爆气体的设备,阻止火焰在设备管道间蔓延,避免灾难性事故的发生。
该产品基于金属波纹板之间狭缝间隙对管道中传播的亚音速或超音速火焰具有淬熄作用的原理设计制造。
技术:炼油企业恶臭废气治理技术

技术 | 炼油企业恶臭废气治理技术恶臭作为一种环境公害,在世界范围内受到越来越多的关注。
在日本,恶臭投诉仅次于噪声,占环保投诉案件量的第二位。
石油炼制是一个恶臭污染较重的行业,近年来,我国炼油企业恶臭扰民案件迅速上升,有的恶臭污染甚至酿成公害事件,受到国家环保局查处。
因此,开展炼油企业恶臭污染控制治理十分必要。
1、炼油厂恶臭污染物及其控制标准恶臭是刺激人的嗅觉器官、引起不愉快或厌恶、损害人体健康的气味。
抚顺石油化工研究院(简称FRIPP)在对多家炼油企业的恶臭污染调查中,曾测定、检出过硫化氢、甲硫醇、乙硫醇、甲硫醚、乙硫醚、二硫化碳、二甲二硫、氨、甲胺、二甲胺、三甲胺、苯、甲苯、二甲苯、苯乙烯、苯酚、甲酚、总硫、总烃、C1~C8。
烃等物质和项目,可以将这些恶臭污染物归类为硫化物、烃类、氨、有机胺等。
我国炼油企业要控制上述恶臭污染物,应同时执行《恶臭污染物排放标准》(GBl4554-93)和《大气污染物综合排放标准》(GBl6297-1996)。
2、炼油厂恶臭污染源及其综合治理技术炼油工业的恶臭污染源有10多种,其污染类型及治理技术有:2.1碱渣湿式氧化脱臭催化汽油碱渣、液态烃碱渣含有高浓度Na2S和有机硫化物(盐),pH>12,传统的处理方法是加酸调节pH到中性,进污水处理场处理。
在碱渣加酸调pH过程中,产生高浓度H2S气体,极易造成恶臭污染和中毒事件。
2000年,FRIPP开发的碱渣湿式氧化处理技术通过了中石化组织的技术鉴定。
这项技术能够在150~200℃,0.9~3.2MPa,用空气中的氧将碱渣中的硫化钠和有机硫化物氧化为硫酸钠,将部分有机物氧化为H2O和C02,脱除COD,防止碱渣中和处理时产生H2S恶臭气体。
目前,这项技术已在国内近20家企业应用。
2.2焦化冷焦水密闭冷却循环使用从焦化塔排出的冷焦水温度可达85℃以上,含有挥发烃、重油和焦粉等,按传统处理方法,冷焦水经过隔油池、敞开式空气凉水塔冷却到约50℃,返回焦化塔循环使用。
石油化学工业废气污染简介

石油化学工业废气污染简介石油化学工业中的炼油厂和石化厂的加热炉和锅炉燃烧排放燃烧废气;生产装置产生不凝气、弛放气和反映中产生的副产品等过剩气体;轻质油品、挥发性化学药品和溶剂在贮运过程中的挥发、泄漏;废水和废弃物的处理和运输过程中散发的恶臭和有毒气体;以及石化工厂再生产原料和产品运输过程中的挥发和泄漏散发出的废气是石化工业废气的主要来源石油化工废气按生产行业可分为石油炼制废气、石油化工废气、合成纤维废气和石油化肥废气。
四大生产行业排放的废气按排放方式可分为:燃烧烟气、生产工艺废气、火炬废气和无组织排放废气。
1、燃烧烟气污染石化装置燃烧烟气排放量约占废气排放总量的60%。
石化的加热炉多以减压渣油为燃料,渣油含硫约0.2—3%,燃烧产生废气中含二氧化硫、氮氧化物和尘,经除尘后排放,其中的二氧化硫、氮氧化物多未处理,一般采用高空排放。
2、工艺废气污染石化企业生产装置规模较大,因此工艺废气排放量较大。
污染物扩散范围较大,虽经高空排放,环境污染仍较严重。
3、火炬废气污染火炬是石化生产必备的安全环保设施。
石化生产装置在开、停工及非正常操作(如放气减压)情况下将可燃性气体泄到火炬燃烧后排放。
火炬排污量相对加热炉要大,对环境影响也较大。
4、尾气污染石化生产的工艺废气经工业装置回收及处理后成为尾气排入环境。
5、无组织排放的废气污染石化企业的无组织排放主要包括两部分:一是生产过程中管线、机泵、设备等的泄漏、级地沟内的挥发排入环境的有害气体;二是轻质石油化工产品在储运过程中的石油产品蒸气挥发进入环境污染空气。
按生产行业不同排放的废气中所含主要污染物情况如下:石化工业废气主要污染物分类表制总烃油品储罐、污水处理隔油池、工艺装置加热炉、装卸油设施、烷基化尾气、轻油和烃类气提出运设施及管线、阀门及泵等的泄漏氧化沥青尾气苯并( a)芘沥青装置催化再生废气SO 2 、CO、CO 2 、尘催化裂化装置燃烧烟气SO 2 、NO X 、CO、CO 2 、尘加热炉、锅炉、焚烧炉、火炬含硫废气SO 2 、H 2 S、氨含硫污水的汽提、加氢精制、气体脱硫、含硫尾气的回收处理臭气SO 2 、硫醇、酚油品精制、硫磺回收、脱硫、污水处理、污泥处理工燃烧烟气SO 2 、NO X 、CO、CO 2 、尘裂解炉、加热炉、锅炉、焚烧炉、火炬气烷烃、烯烃、环烷烃、醇、芳香烃、醚酮、醛、酚、酯、卤代烃、氰化物SO 2 、NO X 、卤化物、CO 甲醇、乙醛、醋酸、环氧丙烷、苯、甲苯装置,乙基苯、聚乙烯、聚丙烯、氯乙烯、苯乙烯、对本二甲酸装置,顺丁橡胶、丁苯橡胶、丙烯腈、环氧氯丙烷装置维含烃废气总烃催化重整、芳烃抽提、对二甲苯、常减压装置、轻油储罐燃烧烟气SO 2 、NO X 、CO、CO 2 、尘加热炉、锅炉、焚烧炉、火炬刺激性废气甲醇、甲醛、乙醛、除酸、环氧乙烷、己二腈、己二胺、丙烯腈、对本二甲酸、二甲脂对本二甲酸、对本二甲酸二甲脂、己二胺、丙烯腈、聚丙烯腈、腈维装置,硫氰酸钠溶剂回收装置肥燃烧烟气SO 2 、NO X 、CO、CO 2 、尘加热炉、锅炉、焚烧炉、火炬工艺废气CH 4 、H 2 S、氨、尿素、尘、SO 2 、NO X 、CO、CO 2 合成氨、硫磺回收尾气、合成氨弛放气、氨冷冻罐排气、尿素造粒塔排放口、硝酸装置尾气、氨中和器排放口等为了减少石化工业废气污染,除了采取必要的环境治理措施,有效管理污染物的排放和治理外,根本的措施是采用无污染或少污染的先进生产工艺;改进设备,提高机泵设备和管道设备的密闭性;积极开展废气的回收和综合利用。
石化行业VOCs污染源及对应治理措施
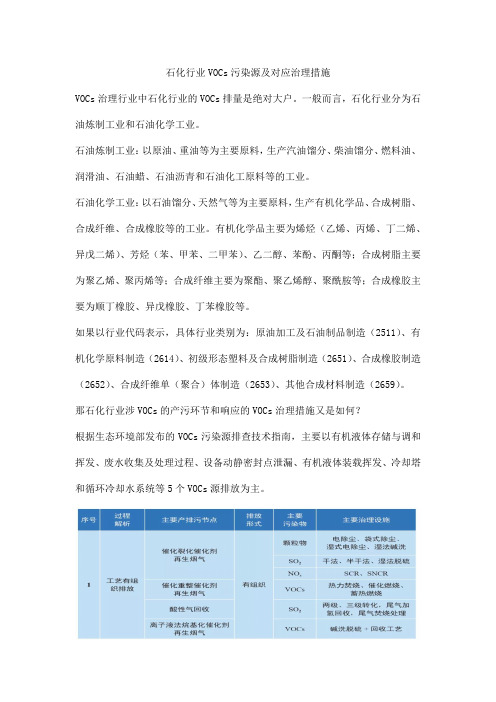
石化行业VOCs污染源及对应治理措施
VOCs治理行业中石化行业的VOCs排量是绝对大户。
一般而言,石化行业分为石油炼制工业和石油化学工业。
石油炼制工业:以原油、重油等为主要原料,生产汽油馏分、柴油馏分、燃料油、润滑油、石油蜡、石油沥青和石油化工原料等的工业。
石油化学工业:以石油馏分、天然气等为主要原料,生产有机化学品、合成树脂、合成纤维、合成橡胶等的工业。
有机化学品主要为烯烃(乙烯、丙烯、丁二烯、异戊二烯)、芳烃(苯、甲苯、二甲苯)、乙二醇、苯酚、丙酮等;合成树脂主要为聚乙烯、聚丙烯等;合成纤维主要为聚酯、聚乙烯醇、聚酰胺等;合成橡胶主要为顺丁橡胶、异戊橡胶、丁苯橡胶等。
如果以行业代码表示,具体行业类别为:原油加工及石油制品制造(2511)、有机化学原料制造(2614)、初级形态塑料及合成树脂制造(2651)、合成橡胶制造(2652)、合成纤维单(聚合)体制造(2653)、其他合成材料制造(2659)。
那石化行业涉VOCs的产污环节和响应的VOCs治理措施又是如何?
根据生态环境部发布的VOCs污染源排查技术指南,主要以有机液体存储与调和挥发、废水收集及处理过程、设备动静密封点泄漏、有机液体装载挥发、冷却塔和循环冷却水系统等5个VOCs源排放为主。
炼油厂废气的排放与防治

直接 或 间接排放 的废气 提 出防治 或治 理措施 。
吸造 成 的蒸
2 废气 来源
损耗 、油 品加 工 过 程 中 的损 耗 以 及 设 备 检 修 、油 罐
某石 化企业 原油 加工 规模 800 ̄10 t/a,采用 常 清洗 、油 品化 验 及 装 置 吹 扫造 成 的 油 品损 耗 等 ,主
值 。本 文 以某石 化企 业 为 例 ,对 炼油 厂 生 产 过程 中 油 品在储存 、运 输 及 加 丁等 过 程 中 ,不 可 避 免地 产
产生 的工 艺废 气 、燃 烧 烟 气 等 进 行 统 计 分 析 ,针 对 生跑 、冒、滴 、漏 ,主要 包 括 油 品 在 储 存 时 的大 小 呼
· 26 ·
气 体 净 化
2018年第 18卷第 5期
炼 油 厂 废 气 的 排 放 与 防 治
曹原 原
(中 国石 化 洛 阳分 公 司 ,河 南 洛 阳 471012)
摘要 :炼油厂生产过程中会产生大量废 气 ,如不加 以治理 ,会给 环境 带来严重 危害。以某石化企业 为例 ,对炼油厂生产过程 中产生 的工艺废气 、燃烧烟气等进行统计分析 。炼油厂的废气 来源通常包括 有 组 织 排 放 源 、无 组 织 排 放 源 和 火 炬 排 放 烟 气 等 。为 使 废 气 污 染 物 达标 排放 ,治 理 措施 主要 有 :燃 料 气 脱 硫 、催化 烟气旋风分离 、重整装 置再 生尾气处理 、硫磺回收装 置 、减少烃类排放 、减少恶臭气 体排放 、锅炉 废气治理设施等 。其中 ,减少烃类排放主要包括原油及轻 油采用 浮顶罐储存 、设 置气柜 回收燃料气 、常 减压装置 “三顶 ”气 回收 、油气 回收装置等 ;减少恶臭气体排放 主要 包括含硫污水密闭输送 、储罐恶臭 气体处理等 。炼油厂除 了对传统的 SO:、NO 、烟尘等常规污染物排放源进 行监 测外 ,还要加 强对 非 甲烷 总烃 、VOCs、TSP等排放源进行监测 ,并对特征污染物 的无组织排放进行监控 。
石油化工行业VOCs废气处理工艺简介
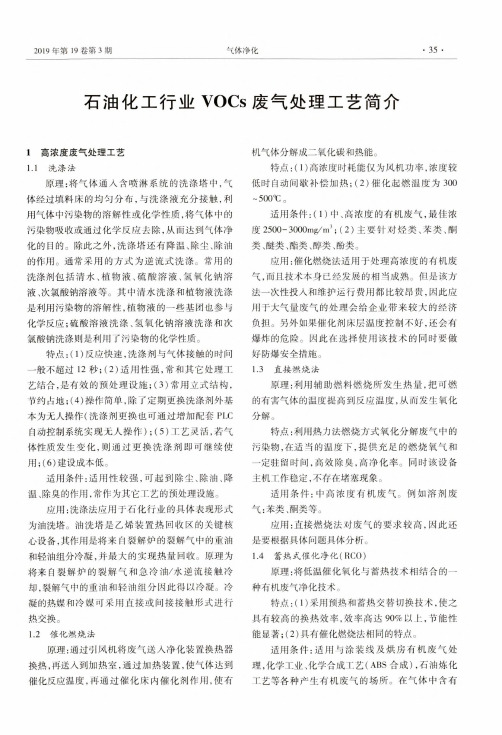
石油化工行业VOCs废气处理工艺简介1高浓度废气处理工艺1.1洗涤法原理:将气体通入含喷淋系统的洗涤塔中,气体经过填料床的均匀分布,与洗涤液充分接触,利用气体中污染物的溶解性或化学性质,将气体中的污染物吸收或通过化学反应去除,从而达到气体净化的目的。
除此之外,洗涤塔还有降温、除尘、除油的作用。
通常采用的方式为逆流式洗涤。
常用的洗涤剂包括清水、植物液、硫酸溶液、氢氧化钠溶液、次氯酸钠溶液等。
其中清水洗涤和植物液洗涤是利用污染物的溶解性,植物液的一些基团也参与化学反应;硫酸溶液洗涤、氢氧化钠溶液洗涤和次氯酸钠洗涤则是利用了污染物的化学性质。
特点:(i)反应快速,洗涤剂与气体接触的时间一般不超过12秒;(2)适用性强,常和其它处理工艺结合,是有效的预处理设施;(3)常用立式结构,节约占地;(4)操作简单,除了定期更换洗涤剂外基本为无人操作(洗涤剂更换也可通过增加配套PLC 自动控制系统实现无人操作);(5)工艺灵活,若气体性质发生变化,则通过更换洗涤剂即可继续使用;(6)建设成本低。
适用条件:适用性较强,可起到除尘、除油、降温、除臭的作用,常作为其它工艺的预处理设施。
应用:洗涤法应用于石化行业的具体表现形式为油洗塔。
油洗塔是乙烯装置热回收区的关键核心设备,其作用是将来自裂解炉的裂解气中的重油和轻油组分冷凝,并最大的实现热量回收。
原理为将来自裂解炉的裂解气和急冷油/水逆流接触冷却,裂解气中的重油和轻油组分因此得以冷凝。
冷凝的热媒和冷媒可采用直接或间接接触形式进行热交换。
1.2催化燃烧法原理:通过引风机将废气送入净化装置换热器换热,再送入到加热室,通过加热装置,使气体达到催化反应温度,再通过催化床内催化剂作用,使有机气体分解成二氧化碳和热能。
特点:(1)高浓度时耗能仅为风机功率,浓度较低时自动间歇补偿加热;(2)催化起燃温度为300 -500%:o适用条件:(1)中、高浓度的有机废气,最佳浓度2500-3000mg/m3;(2)主要针对怪类、苯类、酮类、醛类、酯类、醇类、酚类。
石油炼制过程中的废气处理技术研究
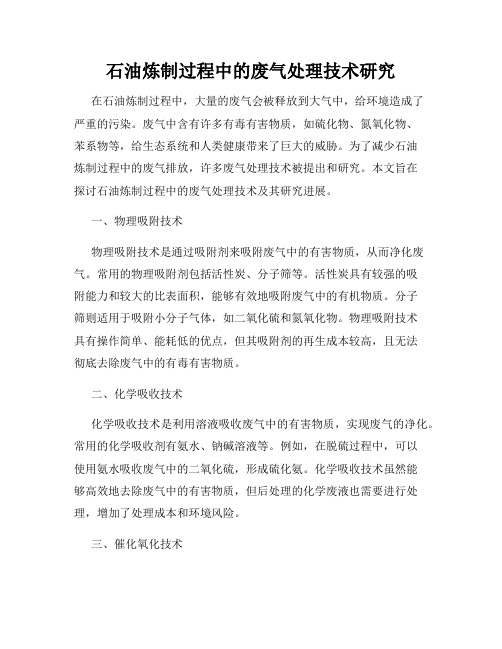
石油炼制过程中的废气处理技术研究在石油炼制过程中,大量的废气会被释放到大气中,给环境造成了严重的污染。
废气中含有许多有毒有害物质,如硫化物、氮氧化物、苯系物等,给生态系统和人类健康带来了巨大的威胁。
为了减少石油炼制过程中的废气排放,许多废气处理技术被提出和研究。
本文旨在探讨石油炼制过程中的废气处理技术及其研究进展。
一、物理吸附技术物理吸附技术是通过吸附剂来吸附废气中的有害物质,从而净化废气。
常用的物理吸附剂包括活性炭、分子筛等。
活性炭具有较强的吸附能力和较大的比表面积,能够有效地吸附废气中的有机物质。
分子筛则适用于吸附小分子气体,如二氧化硫和氮氧化物。
物理吸附技术具有操作简单、能耗低的优点,但其吸附剂的再生成本较高,且无法彻底去除废气中的有毒有害物质。
二、化学吸收技术化学吸收技术是利用溶液吸收废气中的有害物质,实现废气的净化。
常用的化学吸收剂有氨水、钠碱溶液等。
例如,在脱硫过程中,可以使用氨水吸收废气中的二氧化硫,形成硫化氨。
化学吸收技术虽然能够高效地去除废气中的有害物质,但后处理的化学废液也需要进行处理,增加了处理成本和环境风险。
三、催化氧化技术催化氧化技术是通过催化剂催化废气中的有害物质进行氧化反应,将其转化为无害物质。
常用的催化剂有金属氧化物、金属活性剂等。
例如,在氮氧化物的处理中,可以使用金属催化剂将氮氧化物催化为氮和水。
催化氧化技术适用于废气中含有可氧化的有害物质的情况,能够彻底降解有机物质和气体污染物。
四、吸附催化技术吸附催化技术是将物理吸附和催化氧化相结合,通过吸附剂上的催化剂将废气中的有害物质吸附并催化氧化,将其转化为无害物质。
该技术的优点在于同时具备物理吸附和催化氧化的特性,能够高效地去除废气中的有害物质。
常用的吸附催化剂有活性炭、过渡金属氧化物复合材料等。
总结石油炼制过程中的废气处理技术涵盖物理吸附技术、化学吸收技术、催化氧化技术和吸附催化技术等多种方法。
不同的处理技术适用于不同类型的废气,选择合适的处理技术对于高效降低废气排放和保护环境具有重要意义。
石油加工中的废气处理技术
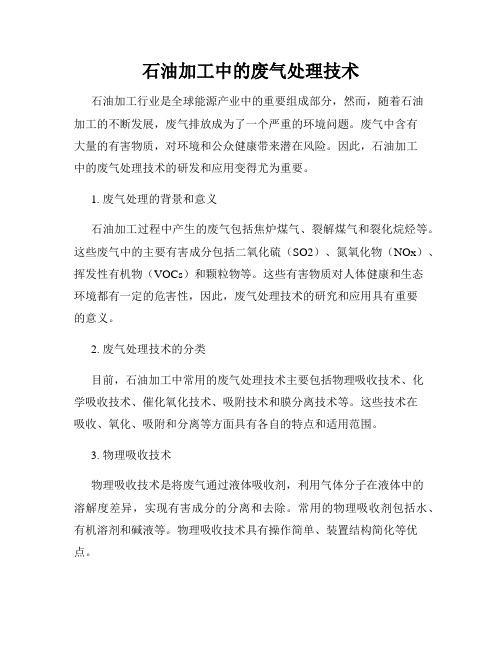
石油加工中的废气处理技术石油加工行业是全球能源产业中的重要组成部分,然而,随着石油加工的不断发展,废气排放成为了一个严重的环境问题。
废气中含有大量的有害物质,对环境和公众健康带来潜在风险。
因此,石油加工中的废气处理技术的研发和应用变得尤为重要。
1. 废气处理的背景和意义石油加工过程中产生的废气包括焦炉煤气、裂解煤气和裂化烷烃等。
这些废气中的主要有害成分包括二氧化硫(SO2)、氮氧化物(NOx)、挥发性有机物(VOCs)和颗粒物等。
这些有害物质对人体健康和生态环境都有一定的危害性,因此,废气处理技术的研究和应用具有重要的意义。
2. 废气处理技术的分类目前,石油加工中常用的废气处理技术主要包括物理吸收技术、化学吸收技术、催化氧化技术、吸附技术和膜分离技术等。
这些技术在吸收、氧化、吸附和分离等方面具有各自的特点和适用范围。
3. 物理吸收技术物理吸收技术是将废气通过液体吸收剂,利用气体分子在液体中的溶解度差异,实现有害成分的分离和去除。
常用的物理吸收剂包括水、有机溶剂和碱液等。
物理吸收技术具有操作简单、装置结构简化等优点。
4. 化学吸收技术化学吸收技术是通过将废气通过特定的化学吸收剂,使有害成分通过化学反应与吸收剂发生反应,从而实现有害成分的去除。
常用的化学吸收剂包括氨水、碱液和酸液等。
化学吸收技术可以根据废气的成分进行选择,具有针对性强、去除效果好等优势。
5. 催化氧化技术催化氧化技术是利用催化剂催化氧化废气中的有害成分,使其转化为无害的物质。
常用的催化剂包括贵金属催化剂、金属氧化物催化剂和氧化钒催化剂等。
催化氧化技术具有高效转化率、催化反应瞬时等特点。
6. 吸附技术吸附技术是利用吸附剂对废气中的有害成分进行吸附、富集和分离的技术。
常用的吸附剂包括活性炭、分子筛和纳米材料等。
吸附技术具有选择性强、再生能力好等特点。
7. 膜分离技术膜分离技术是利用半透膜对废气中的有害成分进行选择性分离和去除的技术。
常用的膜材料包括聚合物膜、陶瓷膜和复合膜等。
石油工业排放废气治理与减排研究
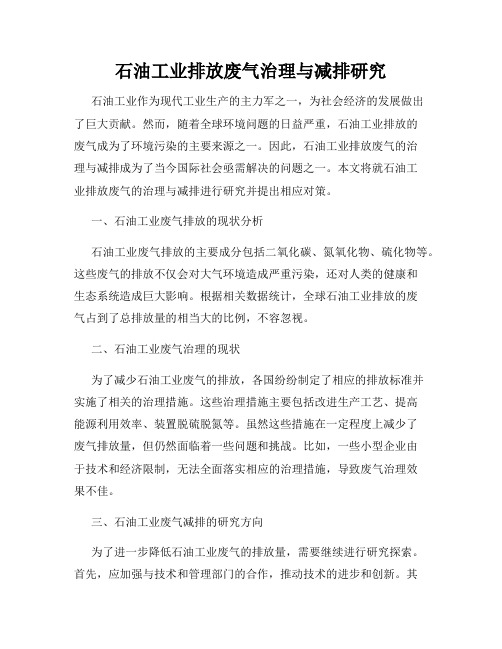
石油工业排放废气治理与减排研究石油工业作为现代工业生产的主力军之一,为社会经济的发展做出了巨大贡献。
然而,随着全球环境问题的日益严重,石油工业排放的废气成为了环境污染的主要来源之一。
因此,石油工业排放废气的治理与减排成为了当今国际社会亟需解决的问题之一。
本文将就石油工业排放废气的治理与减排进行研究并提出相应对策。
一、石油工业废气排放的现状分析石油工业废气排放的主要成分包括二氧化碳、氮氧化物、硫化物等。
这些废气的排放不仅会对大气环境造成严重污染,还对人类的健康和生态系统造成巨大影响。
根据相关数据统计,全球石油工业排放的废气占到了总排放量的相当大的比例,不容忽视。
二、石油工业废气治理的现状为了减少石油工业废气的排放,各国纷纷制定了相应的排放标准并实施了相关的治理措施。
这些治理措施主要包括改进生产工艺、提高能源利用效率、装置脱硫脱氮等。
虽然这些措施在一定程度上减少了废气排放量,但仍然面临着一些问题和挑战。
比如,一些小型企业由于技术和经济限制,无法全面落实相应的治理措施,导致废气治理效果不佳。
三、石油工业废气减排的研究方向为了进一步降低石油工业废气的排放量,需要继续进行研究探索。
首先,应加强与技术和管理部门的合作,推动技术的进步和创新。
其次,应加强对废气治理技术的研究,开发出更加高效和环保的治理技术。
此外,还需要完善排放标准,加大对石油工业废气排放的监管力度。
四、石油工业废气治理与减排的对策建议针对石油工业废气治理与减排问题,本文提出以下对策建议。
首先,加强政府的引导作用,制定更加严格的排放标准,加大对废气排放的监管力度。
其次,提供技术和经济支持,鼓励企业采用先进的治理技术和设备。
此外,加强科研力量的建设,培养专业人才,推动废气治理技术的创新和应用。
总结:石油工业排放废气治理与减排是当前急需解决的环境问题之一。
通过加强技术研究、完善管理制度和加大监管力度,我们可以有效降低石油工业废气的排放量,保护环境,促进可持续发展。
第六章 石油炼制中废气来源及处理

石油炼制的基本流程
石油一次加工 石油二次加工 石油产品精制
石油炼制产品
石油炼制中的污染物来源
原油二级电化学脱盐工艺流程图
石油炼制中的污染物来源
石油炼制中的污染物来源
370℃
520℃
原油常、减压蒸馏工艺流程图 催化裂化工艺流程图
石油炼制中的污染物来源
石油炼制中的污染物来源
炼厂气处理单元
炼油过程中各类装置(催化裂化、加氢裂化、加氢精制和延 迟焦化等)所产生的气体 含有氢、甲烷、乙烷和乙烯、丙烷和丙烯、丁烷和丁烯、H2S、 COS、CO2等 炼厂气脱硫 Claus法回收硫磺
① H2S选择性催化氧化为元素硫,反应不可逆 ② H2S催化氧化为S及SO2,然后去Claus催化反应段(Selectox工艺)
Selectox工艺有一次通过法和循环法
• H2S含量<5%时可采用一次通过法 • H2S含量>5%时将过程气进行循环(控制过程气出口温度<371℃)
石油炼制中的废气处理-酸性气回收
反应炉、余热锅炉、转化器、硫冷凝器、再热器等 反应炉(又称燃烧炉) 正常炉温 980~1370℃ 主要作用 ① 使原料气中1/3体积的H2S氧化为SO2; ② 使原料气中烃类、硫醇氧化为CO2等惰性组分 反应炉形式 ① 外置式(与余热锅炉分开设置),硫磺回收规模超过30t/d比较适用 ② 内置式(与余热锅炉组合为一体) 反应物在炉内的停留时间一般至少为0.5s
克劳斯法工艺—Selectox循环直接氧化法
石油炼制中的废气处理-酸性气回收
酸气中 >55% H2S含量 适用 工艺 30-55% 15-30% 10-15% 预热酸气 和空气的 分流法 5-10% < 5% 硫循 环法 直接氧 化法
石油炼制储运废气污染治理与控制

石油炼制储运废气污染治理与控制摘要:针对石油炼制企业储运过程排放挥发性有机物(VOCs)带来严重的环)和臭境问题和油品损耗问题,深入打好污染防治攻坚战,强化细颗粒物(PM2.5)协同控制,石油炼制企业储运过程废气污染治理与控制十分重要。
氧(O3关键词:石油炼制;储运;挥发性有机物;废气治理1背景具有光化学活性的挥发性有机物(Volatile Organic Compounds,VOCs)排放到大气中可以通过各种复杂反应,促进细颗粒物和臭氧形成。
根据《中共中央国务院关于深入打好污染防治攻坚战的意见》(2021年11月2日),以石化、油品储运销等行业领域为重点,安全高效推进挥发性有机物综合治理,到2025年,挥发性有机物、氮氧化物排放总量比2020年分别下降10%以上,臭氧浓度增长趋势得到有效遏制,实现细颗粒物和臭氧协同控制。
石油炼制企业储运过程是石化企业重要的VOCs污染源,本文针对挥发性有机液体储罐、装卸、泄漏检测与修复(LDAR)、废气治理设施等关键环节,分析石油炼制储运废气污染治理与控制措施。
2储罐2.1.1油品储罐形式石油炼制常见油品主要包括原油、汽油、柴油、石脑油、航煤、苯、甲苯、二甲苯、液化气等,这些均属于挥发性有机液体(20℃时真实蒸气压大于0.3kPa)。
根据《石油炼制工业排放标准》(GB35170),储罐形式控制要求如下:储存真实蒸气压≥76.6kPa的挥发性有机液体应采用压力储罐。
储存真实蒸气压≥5.2kPa但<76.6kPa的挥发性有机液体储罐应符合下列规定之一:a)采用内浮顶罐;内浮顶罐的浮盘与罐壁之间应采用液体镶嵌式、机械式鞋形、双封式等高效密封方式。
b)采用外浮顶罐;外浮顶罐的浮盘与罐壁之间应采用双封式密封,且初级密封采用液体镶嵌式、机械式鞋形等高效密封方式。
c)采用固定顶罐,应安装密闭排气系统至有机废气回收或处理装置,其大气污染物排放应符合GB 35170表3、表4的规定。
石油废气处理方法

石油废气处理方法
石油废气处理方法有多种,以下是其中几种常见的方法:
1.吸附法:利用活性炭等吸附剂对石油废气中的有机化合物进行
吸附,然后再进行脱附和回收。
这种方法能够有效去除废气中的有机物,达到净化和回收的目的。
2.生物法:利用微生物在适宜的环境下对石油废气中的有机物进
行降解和转化,将其转化为无害或低害的物质。
这种方法具有处理效率高、无二次污染等优点。
3.催化燃烧法:将石油废气中的有机物在催化剂的作用下进行燃
烧,将其转化为无害的二氧化碳和水。
这种方法具有处理效率高、设备简单等优点,但是需要高温燃烧,会消耗大量的能源。
4.冷凝法:将石油废气通过冷凝器进行冷却,使其中的有机物冷
凝成液体状态,然后进行分离和回收。
这种方法具有处理效率高、无二次污染等优点,但是需要消耗大量的能量。
5.膜分离法:利用膜分离技术对石油废气中的有机物进行分离和
回收。
这种方法具有处理效率高、操作简单等优点,但是需要高精度的膜材料和设备。
石油炼化尾气处理方案

石油炼化尾气处理方案石油炼化过程中产生的尾气包含了大量的有害物质,对环境和人体健康都会造成严重影响。
因此,尾气处理方案成为石油炼化企业必须面对的重要课题。
首先,尾气处理方案可以采用物理方法进行处理。
物理方法主要包括分离和吸附。
分离是将尾气中的固体颗粒、液滴和液体物质分离出来,可以利用重力沉淀、离心分离等方法进行。
吸附是利用吸附剂吸附尾气中的有害物质,然后进行再生或处理。
这种方法可以有效去除尾气中的颗粒物、挥发性有机物等。
其次,化学方法也是一种有效的尾气处理方案。
化学方法主要通过化学反应将尾气中的有害物质转化为无害物质。
例如,可以使用催化剂将尾气中的一氧化碳、二氧化氮等气体转化为无害的二氧化碳和氮气。
此外,还可以使用化学药剂将尾气中的有机物进行氧化或还原反应,从而降低有机物的浓度。
另外,生物处理也是一种有效的尾气处理方案。
生物处理利用微生物对尾气中的有害物质进行降解分解,将其转化为无害物质。
生物处理可以使用活性污泥法、固定化法等方法进行。
通过优化微生物种类和环境条件,可以实现高效降解尾气中的有害物质。
最后,综合利用也是一种重要的尾气处理方案。
综合利用指的是将尾气中的有害物质转化为有价值的化学品或能源。
例如,可以利用尾气中的有机物生产生物燃料或化工原料。
此外,还可以通过从尾气中回收有价值的物质,如石油中的硫、氮等元素,从而实现资源循环利用。
总之,针对石油炼化尾气的处理,可以采取物理、化学、生物和综合利用等多种方法进行。
不同的尾气特点和处理要求可能需要采用不同的方案。
因此,石油炼化企业需要根据实际情况选择合适的尾气处理方案,以保护环境,并确保生产过程的可持续发展。
石油炼制与化工行业烟气综述
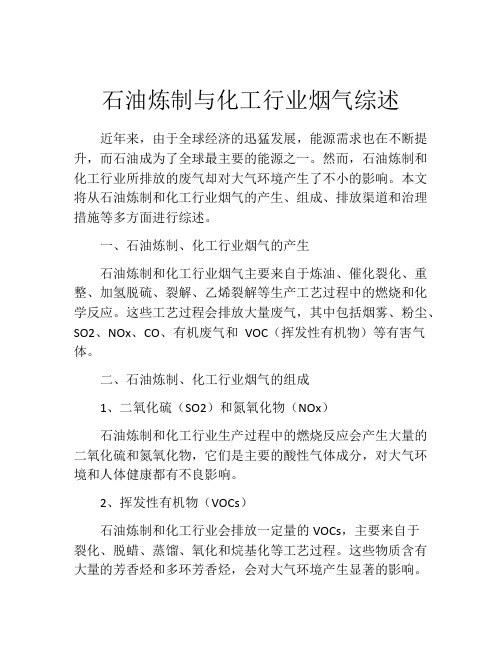
石油炼制与化工行业烟气综述近年来,由于全球经济的迅猛发展,能源需求也在不断提升,而石油成为了全球最主要的能源之一。
然而,石油炼制和化工行业所排放的废气却对大气环境产生了不小的影响。
本文将从石油炼制和化工行业烟气的产生、组成、排放渠道和治理措施等多方面进行综述。
一、石油炼制、化工行业烟气的产生石油炼制和化工行业烟气主要来自于炼油、催化裂化、重整、加氢脱硫、裂解、乙烯裂解等生产工艺过程中的燃烧和化学反应。
这些工艺过程会排放大量废气,其中包括烟雾、粉尘、SO2、NOx、CO、有机废气和VOC(挥发性有机物)等有害气体。
二、石油炼制、化工行业烟气的组成1、二氧化硫(SO2)和氮氧化物(NOx)石油炼制和化工行业生产过程中的燃烧反应会产生大量的二氧化硫和氮氧化物,它们是主要的酸性气体成分,对大气环境和人体健康都有不良影响。
2、挥发性有机物(VOCs)石油炼制和化工行业会排放一定量的VOCs,主要来自于裂化、脱蜡、蒸馏、氧化和烷基化等工艺过程。
这些物质含有大量的芳香烃和多环芳香烃,会对大气环境产生显著的影响。
3、颗粒物(TSP和PM2.5)颗粒物是产生在石油炼制和化工生产过程中的一种常见污染物,主要来自于生产过程中的机械撞击、石油搅拌、粉碎等工艺操作。
颗粒物的存在会对呼吸系统造成不良影响,同时,也会对机械设备和环境造成危害。
三、石油炼制、化工行业烟气的排放渠道石油炼制和化工行业烟气的排放主要分为两种方式:1、直接排放石油炼制和化工生产过程中,具有众多的烟气排放口。
当烟气排放口与大气相连通时,大气的风向、风速等气象因素对烟气的扩散和规划明显影响。
2、间接排放间接排放是指石油炼制和化工行业在生产过程中排放到水、土壤和固体废弃物中的有害气体。
这种排放方式会对水源产生污染,并潜在地威胁到生态系统和农作物的安全。
四、石油炼制、化工行业烟气的治理措施为了缓解石油炼制和化工行业烟气的排放问题,不断提高废气治理技术和设备的技术水平显得尤为重要。
- 1、下载文档前请自行甄别文档内容的完整性,平台不提供额外的编辑、内容补充、找答案等附加服务。
- 2、"仅部分预览"的文档,不可在线预览部分如存在完整性等问题,可反馈申请退款(可完整预览的文档不适用该条件!)。
- 3、如文档侵犯您的权益,请联系客服反馈,我们会尽快为您处理(人工客服工作时间:9:00-18:30)。
过程气进入转化器的温度可按下述要求确定: ① 比预计的出口硫露点高14~17℃ ② 一级转化器的温度应足以使COS和CS2充分水解成H2S和CO2 ③ 获得令人满意的反应速度下,温度尽可能低,以提高H2S转化率
石油炼制中的废气处理-酸性气回收
石油炼制中的废气处理-酸性气回收
余热锅炉(又称废热锅炉) ① 回收热量以产生高压蒸汽(蒸汽压力通常为1.0~3.5MPa) ② 降低过程气温度,满足下游要求
转化器 ① H2S与SO2在催化剂床层上继续反应生成元素硫; ② COS和CS2等有机化合物水解为H2S与CO2
石油炼制中的废气处理-酸性气回收
• 荷兰Comprimo 公司改进SCOT工艺中的吸收-再生部分 • 二段再生塔:一段再生产生半贫液部分半贫液返回吸收塔中
部,另一部分半贫液进入二段再生塔进行深度气提,得到的超 贫液再送到吸收塔的顶部 • 降低超贫液的温度 • 效果:超贫液的低温和超低H2S 分压均有利于H2S在吸收塔内 醇胺溶液中的溶解,降低排入尾气中H2S 的浓度至10-50 ppmv;再生的蒸汽消耗量节省30%
定,常规分流法则炉温过高) ② 进入反应炉的原料气量提高至1/3以上
两种分流法的问题:部分原料气直接进入催化反应段,当原料气 中含有重烃尤其是芳香烃时,会在催化剂上结焦,影响催化剂的 活性和寿命,同时影响硫磺颜色
石油炼制中的废气处理-酸性气回收
克劳斯法工艺—硫循环法(很少采用) H2S含量为5~10%时,将部分硫产品喷入反应炉燃烧 → 维持炉温
直流法三级硫磺回收工艺
石油炼制中的废气处理-酸性气回收
克劳斯法工艺—常规分流法 ① H2S含量15~30%时,用直流法难以使反应炉内燃烧稳定 ② 1/3原料气 + 化学计量配给的空气进入反应炉内,使原料气中
H2S及烃类和硫醇燃烧 非常规分流法 ① 原料气H2S含量为30~55%(直流法难以使反应炉内火焰稳
石油炼制中的废气处理-酸性气回收
乙醇胺吸收再生系统工艺流程
石油炼制中的废气处理-酸性气回收
乙醇胺法脱硫的主要操作参数及控制指标
• 乙醇胺浓度及酸气负荷 一乙醇胺:15%(m)以下;二乙醇胺:20%~25% 酸气负荷均控制在0.35-0.4 0mol酸性气/mol胺
• 吸收条件 压力取决于原料气压力和净化后输气压力 贫液进吸收塔温度比原料气高5-6℃,一般控制在40℃以下操作
石油炼制中的废气处理-Claus装置尾气
LS-SCOT 工艺 ( Low Sulfur SCOT ) • 采用添加剂以改善再生,使贫液中H2S含量小于10×10-6 • 增加吸收塔和再生塔塔板数量 • 降低吸收塔溶剂和气体的温度至35℃左右(比SCOT工艺低
5℃) 增加冷却器的面积 • 投资费用比SCOT 工艺高15%,硫回收率从SCOT 工艺的
为H2S,然后用醇胺溶液吸收和再生提浓,提浓H2S 返回到 Claus 段再次转化 • 效果:总硫低于250ppmv ,与上游的Claus 装置一起,总硫 回收率可达99.8%
急冷液:低温含硫氨水 吸收塔:醇胺
石油炼制中的废气处理-Claus装置尾气
Super-SCOT 工艺 进一步提高尾气净化度和节能降耗
克劳斯法主要设备及操作条件(以直流法为例)
反应炉、余热锅炉、转化器、硫冷凝器、再热器等
反应炉(又称燃烧炉) 正常炉温 980~1370℃ 主要作用
① 使原料气中1/3体积的H2S氧化为SO2; ② 使原料气中烃类、硫醇氧化为CO2等惰性组分 反应炉形式 ① 外置式(与余热锅炉分开设置),硫磺回收规模超过30t/d比较适用 ② 内置式(与余热锅炉组合为一体) 反应物在炉内的停留时间一般至少为0.5s
(2)含硫化合物 硫醇(RSH)、硫醚(RSR)、二硫化物(RSSR)、噻吩
(3)含氧化合物 主要为环烷酸和酚类(以苯酚为主),两者称为石油酸 少量脂肪酸
(4)含氮化合物
吡啶
吡咯
喹啉
胺类(RNH2)
石油炼制的基本流程
石油一次加工 石油二次加工 石油产品精制
石油炼制产品
石油炼制中的污染物来源
原油二级电化学脱盐工艺流程图
石油炼制中的废气处理-酸性气回收
炼厂气脱硫方法 • 干法脱硫:将气体通过固体吸附剂,使硫化氢和其他硫
化物吸附于其上,达到脱硫的目的 处理含微量硫化氢的气体以及需要较高脱硫率的场合
• 湿法脱硫:用液体吸收剂洗涤气体。所用吸收剂包括碱 液和醇胺(一乙醇胺(MEA)和二乙醇胺(DEA))
石油炼制中的废气处理-酸性气回收
• 酸性气回收 • 氧化沥青尾气 • 烃类有机废气
石油炼制中的废气处理-酸性气回收
工艺 催化裂化
催化重整
气体 大量丙稀、丁烯、
异丁烷 氢
产物气体用途 烷基化
油品的加工精制
延迟焦化 甲烷,少量烯烃
制氢
热裂化 加氢裂化
丙烯、丁烯、少 量异丁烷
异丁烷
叠合 烷基化的补充原料
• 炼厂气中常含有硫化氢和有机硫化物 气体脱硫
醇胺法脱硫的原理
20-40℃:反应向右进行,脱硫脱碳; >105℃:反应向左进行,硫化胺盐和碳酸盐分解逸出H2S和CO2,
醇胺重复利用
石油炼制中的废气处理-酸性气回收
醇胺法脱硫工艺流程示意图 1. 净化分离器;2. 气液分离器;3. 吸收塔;4. 换热器;5. 解吸塔; 6. 冷却塔;7. 空冷器;8. 酸性气体分离器
焚烧炉(灼烧炉):将Claus装置尾气中的硫和硫化物转化为SO2
2H2S (g) +SO2 (g) ⇋ 3Sx(s)+2H2O (g) X=2,6,8
Claus尾气成分
SO2 (%) 0.15-0.3
H2S (%) 0.3-0.6
S (%)
CS2 (%)
COS
H2
N2 H2O
(%) (%) (%) (%)
石油炼制中的废气处理-酸性气回收
克劳斯法工艺—Selectox循环直接氧化法
• Selectox 催化剂(SiO2-Al2O3):催化H2S氧化为S和SO2,但不催化 氧化烃类、氢和氨等
• 酸气中芳香烃含量小于1000ml/m3,减少芳香烃在催化剂上裂解结炭 Selectox工艺的累计转化率(97%)高于Claus法平衡转化率
石油炼制中的废气
废气名称
氧化沥青尾气 催化再生废气 燃烧烟气 含H2S气体 臭气
主要污染物
总烃
苯并(a)芘;氧、 氮和硫的杂环化合物 SO2、CO、CO2、尘 SO2、NOX、CO、 CO2、尘 H2S、氨 SO2、有机硫、氨、 硫醇、酚、有机胺
来源 油品储罐、污水处理隔油池、工 艺装置加热炉、装卸油、轻油和 烃类气体运输设施及管线、阀门 及泵等的泄漏
克劳斯法工艺—直接氧化法:原料气中H2S含量<5%时采用 ① H2S选择性催化氧化为元素硫,反应不可逆 ② H2S催化氧化为S及SO2,然后去Claus催化反应段(Selectox工艺)
Selectox工艺有一次通过法和循环法 • H2S含量<5%时可采用一次通过法 • H2S含量>5%时将过程气进行循环(控制过程气出口温度<371℃)
石油化学工业
按生产行业分:石油炼制废气、石油化工废气 合成纤维废气、石油化肥废气
175℃到352℃,每25℃切割一个馏分
原油
350℃到500℃,每25℃切割一个馏分
石油的组成
碳和氢(占97%-99%)、少量氧、硫、氮等 (1)碳氢化合物 烷烃(包括直链和支链烷烃)、环烷烃(多数是烷基环戊烷、烷
基环己烷)和芳香烃(多数是烷基苯),一般不含有烯烃
克劳斯法工艺流程简图
硫冷凝器:分离 硫和提高平衡转 化率
再热器:提高 反应速率,确 保过程气温度 高于硫露点, 但降低转化率
多级转化器: 提高总转化率
石油炼制中的废气处理-酸性气回收
克劳斯法工艺—直流法 ① 原料气中的H2S含量应大于50%,保证酸气与空气燃烧的
反应热足以维持反应炉内温度不低于980℃ ② 反应炉内H2S转化率一般可达60~70%
沥青生产装置
催化裂化装置
加热炉、锅炉、焚烧炉、火炬
各类炼厂气(加氢精制、加氢裂 化、延迟焦化等)、气体脱硫、 含硫尾气的回收处理
硫磺回收、污水处理、污泥处理
石油炼制工业污染物排放标准
新建企业
石油炼制工业污染物排放标准
大气污染物特别限制
石油炼制工业污染物排放标准
现有与新建企业边界1小时
石油炼制中的废气处理
石油炼制中的废气处理-酸性气回收
酸气中 H2S含量
适用 工艺
>55% 直流法
30-55%
预热酸气和空 气的直流法
15-30% 常规分流法
非常规分流法
10-15%
预热酸气 和空气的 分流法
5-10% < 5%
硫循 直接氧 环法 化法
选择工艺的核心:保证燃烧炉温度高于980oC、燃烧稳定
石油炼制中的废气处理-酸性气回收
0.01-0.02 0.02-0.33 0.02-0.33 0.5-4 约60 约30
热焚烧:氧过量(20~100% )、480~815℃
催化焚烧:尾气加热到316~427℃,与适量空气混合,进入催化剂床层 回收余热的焚烧炉通常采用强制通风,在正压下操作
石油炼制中的废气处理-Claus装置尾气
SCOT (Shell Claus Off-gas Treating)工艺 • 荷兰Shell 开发的硫磺回收尾气处理工艺 • 基本原理:采用钴-钼催化剂,将Claus尾气中硫化物加氢还原
石油炼制中的废气
• 按污染源分:燃烧烟气、生产工艺废气、火炬废气和其他 燃烧烟气占废气排放总量的60%