Experiment and Simulation for Articulated Lifting Subsystem of 1000 m Deep Sea Mining System
聚碳酸酯挤压形变力学行为有限元模拟
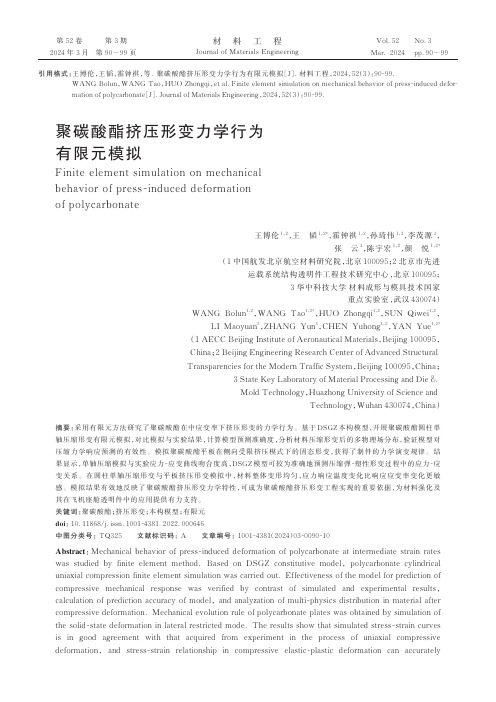
第 3 期第 90-99 页材料工程Vol.52Mar. 2024Journal of Materials EngineeringNo.3pp.90-99第 52 卷2024 年 3 月聚碳酸酯挤压形变力学行为有限元模拟Finite element simulation on mechanical behavior of press -induced deformation of polycarbonate王博伦1,2,王韬1,2*,霍钟祺1,2,孙琦伟1,2,李茂源3,张云3,陈宇宏1,2,颜悦1,2*(1 中国航发北京航空材料研究院,北京100095;2 北京市先进运载系统结构透明件工程技术研究中心,北京100095;3 华中科技大学 材料成形与模具技术国家重点实验室,武汉430074)WANG Bolun 1,2,WANG Tao 1,2*,HUO Zhongqi 1,2,SUN Qiwei 1,2,LI Maoyuan 3,ZHANG Yun 3,CHEN Yuhong 1,2,YAN Yue 1,2*(1 AECC Beijing Institute of Aeronautical Materials ,Beijing 100095,China ;2 Beijing Engineering Research Center of Advanced Structural Transparencies for the Modern Traffic System ,Beijing 100095,China ;3 State Key Laboratory of Material Processing and Die & Mold Technology ,Huazhong University of Science andTechnology ,Wuhan 430074,China )摘要:采用有限元方法研究了聚碳酸酯在中应变率下挤压形变的力学行为。
一些专有名词的翻译

simulation 仿真;模拟simulation algorithm 仿真算法simulation algorithm libray 仿真算法库simulation block diagram 仿真(方)框图simulation centre 仿真中心simulation clock 仿真时钟simulation data base 仿真数据库simulation environment 仿真环境simulation equipment 仿真设备simulation evaluation 仿真评价simulation experiment 仿真实验simulation experiment modelibrary 仿真实验模式库simulation expert system 仿真专家系统simulation graphic library 仿真图形库simulation information library 仿真信息库simulation job 仿真作业simulation knowledge base 仿真知识库simulation laboratoryt 仿真实验室simulation language 仿真语言simulation methodology 仿真方法学simulation model 仿真模型simulation model library 仿真模型库simulation process 仿真过程simulation process time 仿真过程时间simulation program 仿真程序simulation result 仿真结果simulation run 仿真运行simulation software 仿真软件simulation support system 仿真支持系统simulation system 仿真系统simulation technique 仿真技术simulation type 仿真类型simulation velocity 仿真速度simulation work station 仿真工作站simulator 仿真器simultancous comparison method 同时比较法simultaneous technique 同时联用技术;同时并用技术sing around method 声环法sing-around velocimeter 环鸣声速仪single acting positioner 单作用定位器single arm measurement 单臂测量single beam spectrum radiator 单光束光谱辐射计single board microcomputer 单片微(型)计算机single bounce technique 一次反射法single-channel FSK system 单通道FSK系统single channel recorder 单通道记录仪single core typy current transformer 单铁心型电流互感器single ended transducer 单端换能器single field lens 单场透镜single focusing 单聚焦single-focusing mass spectrograph 单聚焦质谱仪single-focusing mass spectrometer 单聚焦质谱计single function(measuring)instrument 单功能(测量)仪表single gauge measurement 单计[片]测量single grain layer varistor 单颗粒层电压敏电阻器single-idler electronic belt conveyor scale 单托辊电子皮带秤single input single output control system;SISO control system 单输入单输出控制系统single-jet water meter 单流束水表single-junction SQUID 单结量子干涉器single junction temperature transducer [sensor] 单结温度传感器single level process 单级过程single loop control 单回路控制single loop control system 单回路控制系统single loop controller 单回路控制器single magnet galvanometer 单磁式振动子single-pass internal reflection element 单通内反射元件single-path diagonal-beam flowmeter 单声道斜束式流量计single-path ratio thermometer 单通道比色温度计single piston pressure-vacuum gauge 单活塞压力真空计single-plane (static) alancing 单面(静)平衡single-plane (static)balancing machine 单面(静)平衡机single probe technique 单探头法single range (measuring) instrument 单范围[量限](测量)仪表single sheet apparatus for measuring specific total losses of magnetic sheet and strip 单片电工钢片[带]比总损耗测量装置single scintillation radioactive logger 单道闪烁辐射测井仪single-speed floating action 单速无定位作用single-speed floating controller 单速无定位控制器single-tube manometer 单管压力计single tube mercury manometer 单管水银压力表single value nonlinearity 单值非线性single variable control system 单变量控制系统sinker (浮子流量计)浮子sintered gas sensor 烧结式气敏元件sinusoidal quantity 简谐波siphon action 虹吸作用siphon barometer 虹吸气压表siphon pipe [tube] 虹吸管siphon rainfall recorder 虹吸式雨量计six component balance 六分力天平Six's thermometer 最高最低温度表;西克斯温度表skip distance 跨距点slant visibility 斜能见度slave operation 从动工作slave station 从站slaved system 受役系统slaving principle 役使原理silding vane rotary flowmeter 刮板流量计sling psychrometer 手摇干湿表sling thermometer 手摇温度表slip bezel ring 滑动盖环slope error over 10% 10%段的斜率误差slope factor 斜率slope over 10% 10%段斜率slope/temperature factor adjustment of pH meter pH计的斜率/温度系数校准器slurry packing 匀浆填充small focus X-ray tube 小焦点X射线管Smith-McIntyre mud sampler 史密斯—麦金太尔取泥器snaking motion value of specimen stage 样品台调节蛇行量snap ring 开口环snapper grab sampler 表层采样器snow density meter 积雪密度计snow measuring plate 积雪板snow-stake 测雪桩snow-storm 雪暴snow storm meter 雪暴测定仪snowfall 雪量snowfall totalizer 累计雪量计snowgauge 量雪器snowsampler 雪取样器;取雪器snubber 限制器soap-film burette 皂膜量管soft bearing balancing machine 软支承平衡机soft ionization 软电离soft keyboard 软键盘"soft" X-rays 软X射线software 软件software compatibility 软件兼容性software cost 软件成本software design procedure 软件设计过程software development library 软件开发库software development plan 软件开发计划software development process 软件开发过程software documentation 软件文件software engineering 软件工程software environment 软件环境software library 软件库software maintenance 软件维护software monitor 软件监督程序software package 软件包software package of computer aided disign 计算机辅助设计软件包software portability 软件可移植性software product 软件产品software psychology 软件心理学software quality 软件质量software reliability 软件可靠性software testing plan 软件测试计划software testing 软件测试software tool 软件工具soil evaporimeter 土壤蒸发仪soil moisture 土壤水分soil moisture content analyser 土壤水份测定仪soil oven 烘土箱soil thermometer 直管地温表solar constant 太阳常数solar radiation 太阳辐射solarigraph 总日射计solarimeter 总日射表solenoid 螺线管solenoid coil 电磁线圈solenoid valve 电磁阀solenoid valve for freon 氟里昂用电磁阀solenoid valve for gas 煤气电磁阀solenoid valve for steam 蒸气电磁阀solenoid valve for water 水用电磁阀solid electrolyte oxygen analyzer 固体电解质氧分析器solid front case with pressure relief at back 后部带泄压装置的前封式外壳solid scanning length measuring instrument 固体扫描式测长仪solid scanning transducer 固体扫描传感器solid scanning width meter [gauge] 固体扫描式宽度计solid-stage electrolyte gas transducer [sensor] 固体电解质气体传感器solid-state electrolyte humidity transducer [sensor] 固体电解质湿度传感器Solid-state electrolyte oin transducer [sensor] 固体电解质离子传感器solid-state (X-ray) detector 固态(X射线)检测器solid-stem liquid-in-glass thermometer 棒式玻璃温度计solo 单独布置;单独检测solvent removable dye penetrant testing method 溶剂去除着色渗透探伤法solvent removable penetrant 溶剂去除性渗透液sonar 声纳sonar dome 声纳导流罩sone 宋(响度单位)sonic [critical] Venturi nozzle 音速[临界]文丘里喷嘴sonic logger 声速测井仪sonic nozzle 音速喷嘴sound daffle 声障板sound energy density 声能量密度sound field 声场sound intensity 声强sound intensity level 声强级sound level 声级sound level calibrator 声级校准器sound level meter 声级计sound power 声功率sound power level 声功率计sound pressure 声压sound pressure level 声压级sound pressure transducer [sensor] 声压传感器sound radiation 声辐射sound ray tracking plotter 声线轨迹仪sound reflector 声反射器sound source 声源sound spectrum 声谱sounding 探测source language 源语言source of electron gun grid bias 电子枪栅偏压电源source of radiation 辐射源source program 源程序source slit 离子源狭缝space byte 空格字节space remote sensing 航天遥感space telemetry 航天遥测spacelab 太空实验库spacer 衬圈;垫片spaceship 宇宙飞船span 量程span calibration gas 量程校准气span drift 量程漂移span error 量程误差span of impact specimen supports 冲击试样支座跨距span shift 量程迁移[偏移]spark-proof instrument 安全火花型仪器spark source 火花电离源sparker 电火花震源spatial filter 空间滤波器spatial resolution 空间分辨率special simulation technique 特殊仿真技术specific acoustic impedance 声阻抗率specific gravity 比重specific humidity 比湿specific permeability 比渗透率specific resistance 电阻率specific retention volume 比保留体积specific service (pressure) gauge 特殊用途压力表specific viscosity 比粘specific weight 专用砝码specification 规格specified characteristic curve 规定特性曲线specified sensitivity 规定灵敏度specimen 试样;样品specimen chamber 样品室specimen cooling holder 致冷样品台specimen heating holder 加热样品台specimen holder 样品杯;样品杆;试样架specimen-holder assembly 样品(支持)器组件specimen rotating holder 旋转样品台specimen tensile holder 拉伸样品台spectral background 光谱背景spectral bandwidth 光谱带宽spectral characteristic curve 光谱特性曲线spectral density 谱密度spectral distribution curve 光谱分布曲线spectral distribution of energy 光谱能量分布spectral emissivity 光谱发射率spectral half width 光谱半宽度spectral line 光谱线spectral position 光谱位置spectral radiance 光谱辐射亮度spectral radiation exitance 光谱辐(射)出(射)度spectral range 光谱范围spectral resolution 光谱分辨率spectral slit width 光谱狭缝宽度spectro chemical analysis 光谱化学分析spectrofluorophotometer 荧光分光光度计spectrograph 摄谱仪spectrometer 光谱仪spectrometer channel 分光波道spectrophotometer 分光光度计spectrophotometric titration 分光光度滴定法spectropolarimeter 旋光仪spectroscopy 看谱镜;能谱法spectrum 光谱;谱spectrum analyzer 频谱分析仪spectrum radiator 光谱辐射计speech recognition 语音识别speed characteristic 转速特性speed control system 调速系统speed effect 速度效应spherical aberration 球差spherical phranometer 球形总日射表spherical phrgeometer 球形地球辐射表spherical phrradiometer 球形全辐射表spin axis 旋转轴spin decoupling 自旋去耦spin test (of a current-meter) (流速计的)旋转试验spinning magnetometer 旋转磁力仪spinning sidebands 旋转边带spin-sin coupling constant (核磁共振)自旋—自旋耦合常数spirit level 气泡式水准仪split-body valve 分体阀split core type current transformer 钳式电流互感器split range opoeration 分程操作split-ranging 分程split screen 分区屏幕split stream injector 分流进样器splitter 分流器spot radiation source 点辐射源spot recorder 光点记录仪SPOT satellite 斯波特卫星spot scanning 点扫描spot size 目标尺寸spray method 喷雾方法spraying device 喷雾装置spring-loaded regulator 弹簧型自力式调节阀spring-loaded variable-head flowmeter 弹性加载可变压头流量计spring plate 弹簧盘spring testing machine 弹簧试验机spurious echo 楔内反射波spurious errors 疏忽误差square-edged orifice plate 直角边缘孔板square frame of magnetic needle 方框罗针square profile (pressure) gaege 矩形压力表square-wave polarogyaph 方波极谱仪stability 稳定性;稳定度stability analysis 稳定性分析stability condition 稳定(性)条件stability criterion 稳定(性)判据;稳定(性)准则stability error 稳定性误差stability limit 稳定(性)极限stability margin 稳定裕度;稳定裕量stability method 稳定法stability of towed body 拖曳体稳定性stability theory 稳定性理论stabilizability 可稳性;能稳性stabilization 镇定;稳定stabilized load characteristic 稳定负载特性stabilized supply apparatus 稳定电源stabilized voltage varistor 稳压电压敏电阻器stabilizing network 镇定网络stabilizing period 稳定过程stable region 稳定域stable system 稳定系统stable type gravimeter 稳定型重力仪stack 栈stacking test 堆码试验stadia line 视距线stadia rod 视距尺stadia wave gauge 视距测波仪staff tide gauge 验潮杆;水尺stagnation pressure 滞止压力stain sync 应变同步standard 标准standard acceleration transducer 标准加速度传感器standard accelerometer 标准加速度计standard buffer solution 标准缓冲溶液standard calorimeter 标准型热量计standard capacitor 标准电容器standard cell 标准电池standard deviation of a single measurement in a series of measurments 测量列中单次测量的标准(偏)差。
岩石碎裂模拟
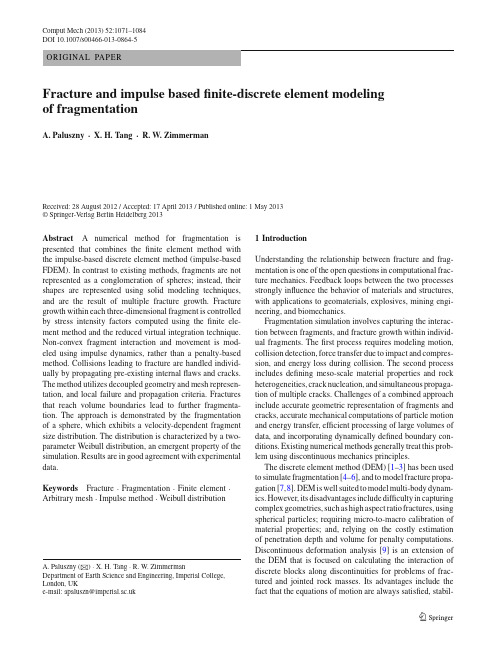
Comput Mech(2013)52:1071–1084DOI10.1007/s00466-013-0864-5ORIGINAL PAPERFracture and impulse basedfinite-discrete element modeling of fragmentationA.Paluszny·X.H.Tang·R.W.ZimmermanReceived:28August2012/Accepted:17April2013/Published online:1May2013©Springer-Verlag Berlin Heidelberg2013Abstract A numerical method for fragmentation is presented that combines thefinite element method with the impulse-based discrete element method(impulse-based FDEM).In contrast to existing methods,fragments are not represented as a conglomeration of spheres;instead,their shapes are represented using solid modeling techniques, and are the result of multiple fracture growth.Fracture growth within each three-dimensional fragment is controlled by stress intensity factors computed using thefinite ele-ment method and the reduced virtual integration technique. Non-convex fragment interaction and movement is mod-eled using impulse dynamics,rather than a penalty-based method.Collisions leading to fracture are handled individ-ually by propagating pre-existing internalflaws and cracks. The method utilizes decoupled geometry and mesh represen-tation,and local failure and propagation criteria.Fractures that reach volume boundaries lead to further fragmenta-tion.The approach is demonstrated by the fragmentation of a sphere,which exhibits a velocity-dependent fragment size distribution.The distribution is characterized by a two-parameter Weibull distribution,an emergent property of the simulation.Results are in good agreement with experimental data.Keywords Fracture·Fragmentation·Finite element·Arbitrary mesh·Impulse method·Weibull distributionA.Paluszny(B)·X.H.Tang·R.W.ZimmermanDepartment of Earth Science and Engineering,Imperial College, London,UKe-mail:apaluszn@ 1IntroductionUnderstanding the relationship between fracture and frag-mentation is one of the open questions in computational frac-ture mechanics.Feedback loops between the two processes strongly influence the behavior of materials and structures, with applications to geomaterials,explosives,mining engi-neering,and biomechanics.Fragmentation simulation involves capturing the interac-tion between fragments,and fracture growth within individ-ual fragments.Thefirst process requires modeling motion, collision detection,force transfer due to impact and compres-sion,and energy loss during collision.The second process includes defining meso-scale material properties and rock heterogeneities,crack nucleation,and simultaneous propaga-tion of multiple cracks.Challenges of a combined approach include accurate geometric representation of fragments and cracks,accurate mechanical computations of particle motion and energy transfer,efficient processing of large volumes of data,and incorporating dynamically defined boundary con-ditions.Existing numerical methods generally treat this prob-lem using discontinuous mechanics principles.The discrete element method(DEM)[1–3]has been used to simulate fragmentation[4–6],and to model fracture propa-gation[7,8].DEM is well suited to model multi-body dynam-ics.However,its disadvantages include difficulty in capturing complex geometries,such as high aspect ratio fractures,using spherical particles;requiring micro-to-macro calibration of material properties;and,relying on the costly estimation of penetration depth and volume for penalty computations. Discontinuous deformation analysis[9]is an extension of the DEM that is focused on calculating the interaction of discrete blocks along discontinuities for problems of frac-tured and jointed rock masses.Its advantages include the fact that the equations of motion are always satisfied,stabil-ity is ensured without requiring additional damping parame-ters,and penetration and traction are avoided at each step. Methods that combine thefinite element method and DEM have been applied to deform individual fragments[10].Early work focused on hybridfinite-discrete methods(FDEM)to model fragmentation due to rock blasting using spherical ele-ments[11–13].Recent work includes the combined model-ing of wave propagation and plastic deformation of spherical conglomerates due to collision[14,15].Fracturing within fragments has been modeled using a local smeared crack approach[16]and a local single-crack approach[17].FEM is usually implemented for the hardening part of the stress-strain curve,and is used before the material reaches its ten-sile strength.In FDEM,fragmentation does not usually rely on the use of failure criteria to drive propagation.Instead, fracture surface creation is often a function of bond break-age between DEM particles[18],or is based on the parti-tion of individual fragments using simple breakage lines or planes[19].FDEM models with discrete fracture represen-tation have been proposed,with fracture growth as a result of the evaluation of a strain-softening,anisotropic damage, rotating crack failure criterion[20].The previous approaches often lead to patterns with excessive branching and mesh dependence,leading to mesh adaptive methods[21].FDEM-based crack growth has shown to be mesh-size sensitive[22], as it directly depends on the accuracy of the local stress/strain field,and does not rely on an energy-based growth approach.A further disadvantage of DEM-based methods is that they require the micro-properties of the individual spheres to be calibrated against the mechanical macro-properties of mate-rials[23].As opposed to DEM,the impulse method[24]is an effi-cient alternative that handles collisions between fragments geometrically,based on polyhedral tracing of the bodies, whereby object trajectories are used to estimate time-of-impact[25],and collision response is a function of impulse resolution[26].The method has been shown to be energy conservative[27],and relies on meso-scale material proper-ties for the calculation of the impulse-momentum form of Newton’s second law to compute collision response within a multi-body system.In contrast to penalty-based methods, objects are not assumed to penetrate during the simulation, and penetration distances and overlapping volumes need not be computed.The impulse method has been applied to simu-late sensorless manipulation of objects[28],to simulate hap-tic interfaces in robotics[29],to model motion of deformable joints in the context of bioengineering[30,31],among others.The simulation of crack propagation using thefinite ele-ment method has been shown to be well suited to repro-duce fracture propagation in3D[32–34].Fractures,in the context of fragmentation,benefit from a discrete represen-tation,as they inherently define fragment boundaries as the domain subdivides.Early versions of the application of FEM to crack propagation relied on tagging and deleting“broken”mesh elements[35,36].Fractures can be defined as entities within the mesh to avoid re-meshing(e.g.smeared crack and anisotropic damage model).In general,methods that rely onfixed meshes require them to be sufficiently refined to capture stress singularities that may ensue during the sim-ulation.Other methods aim to reduce complexity by repre-senting only the boundaries of the bodies,but are less suited to capture heterogeneity in the matrix(e.g.,the boundary element method).Mesh-free methods[37,38]bypass mesh-ing completely and define domains as sets of points,which introduces difficulties such as domain interface blurring, and costly computational operations.The Extended Finite Element(XFEM)avoids re-meshing by defining enrich-ment functions to represent discrete fractures at a sub-grid level.XFEM has been applied to grow[39]and intersect [40]fractures in2D and3D[41],including the modeling of intra-fracture friction[42].XFEM has difficulties repre-senting intra-element fracture intersection,or multiple frac-tures in one element,and requires special approaches to handle fracture tips within elements.The cracking particle method is a numerical method specific to the simulation of crack propagation,in which crack surfaces are represented by a set of point-based enriched functions[43],with no explicit definition of fracture surfaces.Fragmentation relying on this method usually requires re-interpretation of fracture geometry during growth.Finite element-based fracture prop-agation has been limited in the past by the technology of con-trolling geometry and mesh generation,but is now facilitated by NURBS-based geometric representation and mature mesh generation technology cf.[44–47].In the present work,a dis-crete fracture growth method is used,which represents frac-ture geometry explicitly using solid modeling techniques, and for which the mesh is only an instrument to enablefinite element-based computation of stress intensity factors.An approach to simulate fragmentation that combines finite element method based fracturing and impulse dynamics and collision will now be presented(cf.Fig.1).The main nov-elty of this combined method is that fracturing is not handled as a loss of cohesion between elements;instead,fractures have an explicit geometric representation,and their growth is driven by stress concentrations at the tips.Fracturing is modeled using a continuous approach,while fragmentation is controlled by the discontinuous impulse method.Advan-tages of this approach include discrete fracture and fragment polyhedral representation,finite element-based stress,strain and stress intensity factors computation,and element-wise definition of standard mechanics material properties such as elastic constants and material toughness.It exploits the impulse-based method for collision detection and resolu-tion of dynamic behavior.Collisions are predicted based on the geometry of the bodies and their physical behavior,as opposed to a posteriori correction based on mesh and objectFig.1Fracture-driven fragmentation.Fracture geometry evolves as a function of propagation vectors,u t p,which is the result of evaluat-ing propagation and failure laws based on stress intensity factors,K, approximated at its tips,t.Mesh quality Q is a function of element shape and size relationship to tip proximity.Thefinite element method is applied to solve for d,displacements,σ,stresses,and,ε,strains are derived by approximating that the medium is linear elastic and isotropic. Frenet frames are computed at the tip locations to determine the local coordinate system of the fracturepenetration.The method is demonstrated with the fragmenta-tion of a sphere impacted at a range of velocities.The result-ing cumulative volume distributions are characterized by a two-parameter Weibull equation[48].The method is able to reproduce Weibull fragment size distributions measured experimentally;these distributions are therefore an emergent property of the model.2FragmentationThe main objective of this work is to simulate fracture,F, and interaction,G,of a set of fragments{H}.The interaction of the fragments is a function ofG({H},{α(H)},g,ρ,μ,e)={c}(1)where g is gravity,ρis the rock density,μis friction,e describes non-fracture energy loss during collision,{F(H)} is the fracturing of individual fragments,and{c}is a set of ensuing collisions,each defined by a set of impulses at a set of locations{c i}={(p i,l i)}(2)where p i is the impulse vector and l i is the impulse location, andp i=m i v i(3) where m i is the object mass and v i is its velocity,defined at discrete locations by contributions from the linear and angu-lar velocities of the colliding bodies.At each contact location, the contact force is defined as f i=d p i/dt.Fragmentation is driven by fracture growth:{H n i}=F(H i,f i,E,ν,K I C)(4) where{H n i}are new fragments created during growth,E is Young’s modulus,νis Poisson’s ratio,and K I C is the material toughness.Fracture growth simulation involves the propagation of multiple fractures within a single3D body of arbitrary shape(see Sect.6).Each fragment is populated by a set of initialflaws,f o, representing inclusions,defects,and initial fractures[49], part of the material characterization[50]:∀H|∃{f o i}h−→center(f o i)=random()(5) where{f o i}h is a set offlaws,in fragment h,of varying radius r i.Position candidates are computed using a Mersenne Twister random number calculator.If any point in theflaw is closer than a minimal distance to a previously insertedflaw, the insertion fails.This minimal distance is referred to as the spacing.It follows that∀f i∀f i |f i f i |>d min(6) where d min is the minimum separating distance,andd min>max(r i,r i )+s max(7) where s max is the maximum spacing between two fractures. Theflaw density is decreased by assigning a larger s max,its upper limit is defined by the minimum edge length of the mesh.Choosing a larger s max will create swarms of evenly spacedflaws,while a smaller value yieldsflaw clustering. Radii are assumed to have a Gaussian size distribution.As the simulation progresses,collisions are classified by magnitude,and are individually handled as fracture-inducing events.Thus,the simulation of fracture and fragment inter-action is computationally separated,and are only coupled by the continuous transfer of force and geometric information. The fragmentation method is summarized by Algorithm1.Algorithm1Fragmentation(n)Require:Set of interacting bodies{H}={h0,h1,...}where i=0..n, n=total bodies,and their respective contact forces{f h i}. Ensure:Bodies collide due to gravity and compressive forces.1:while G({H},{α(H)},g,ρ,μ,e)={c}do2:while{H}=∅do3:for all c i in{c}do4:c i={f t={f0,...,f c}∪p t={p0...p c}};5:for all H i do6:v h i=V olume(H i)7:if v h i>f threshold then8:{H n i}=F(H i,f t,E,ν,K I C);9:end if10:Add new fragments,H=H∪{H n i}11:end for12:end for13:end while14:end while3Geometric representationAll domains are represented using solid modeling techniques that take into account the evolutionary nature of their geome-tries [51].Each fracture,f i ,evolves from a set of growthcurves,and is stored as a parametric surface,f pi .The frag-ment boundary,m ,is also initially represented by a set of surfaces.It follows that∀f | ∃i |f pi ∈f i ∨ f p i ∈m (8)∀f |f p i meshing−−−−−→{t i }i →triangles (9)=closed non −convex polyhedron(10)after meshing,each surface is triangulated.Tips are definedimplicitly by the underlying surface parametric space.It fol-lows that∀i |(∃f i |t i ∈f i )∨(t i ∈m )(11)∀i |(∃f i |b i ∈f i )∨(b i ∈m )(12)where t i is a triangle representing part of the tip surface,and b i is a tip segment.At each growth step,a new tip front curve is formed from the movement of the original tip.The fracture surface is deformed to accommodate this constraint using NURBS constraint-based deformation [52].Figure 2shows (a)the initial stage of the simulation,(b)an advanced state where fracture propagation has occurred,and (c)the final fragmen-tation.When a crack tip reaches a free surface it stops,and the fracture body merges with the foreign object.There are two distinguishable cases:the tip stops on a block boundary,or it stops on a fracture wall.In the first case,the fracture shape becomes part of the block description.In the second case,fracture shapes merge into one object.Thus,tips can exist within the body of a fracture,or within a block.In other words,tips can make a negative or a positive volume change.It becomes necessary to treat these in a flexible fashion.In order to allow this flexibility,progression fronts are defined as cutting surfaces that subdivide the domain as the tip advances.4Impulse dynamicsThe impulse-based method is a strategy to model the dynam-ics of multiple bodies with frequent collisions and contact modes with frequent changes [24,26].It has been shown to converge towards the exact solution of the dynamics problem as the step size decreases [53].Unlike DEM-based methods,which compute explicit constraint forces at contact points,the impulse method captures collision impulses between bod-ies by solving the linear complementarity problem [54,55].Its main advantage is that it does not require full geometric intersection checks.Additionally,in contrast to penaltyandFig.2Fragmentation driven by fracture growth.a A set of initially planar,elliptic flaws grow as a function of stress intensity factor mea-surement at the tip locality.b Fractures advance at a relative speed controlled by the propagation factor exponent.c Once fractures reach the solid’s boundary,the fragment domain is automatically sub-divided.In b the red cone at the bottom -left represents the point of impact,in c the object is rotated to the left by 45◦Lagrange-based methods,it does not rely on arbitrary penalty parameters that define repulsion as a function of penetration,but instead predicts collisions as a function of impact between proximal bodies.The impulse method for multi-body collision is subdi-vided into three steps[56]:1.collision detection,by means of estimating the time ofcollision,t c,between critical collision pairs,which is computed using the conservative advancement method[26]using the intersection of the geometric Minkowskisum of the moving bodies[57],2.dynamic evolution,which comprises the integration ofthe equations of motion for each body,described by New-ton’s law and the conservation of angular momentum, 3.the collision response,which applies a collision impulseto each critical pair that collide,modeled using Guendel-man’s energy conservative approach[58,59].The collision detectionfinds the timestep t i,which occurs before object contact(see Fig.3a).A pair of impulses is applied to avoid penetration.Penetration depth,area,and volume are not computed.Collision time is assumed to be infinitesimal,and so the positions of the bodies are treated as constant during a collision.Velocities and positions are updated at each time-step using a semi-implicit Euler time-stepping scheme.The following equations describe the computation of the impulse between two bodies during a collision(see Fig.3b). The change of linear velocity and the impulse are related by Eq.3.The change of angular velocity is expressed asω(t)=I−1a r a×p(13) where r a is the vector from the center of mass to the contact point,and I−1a is the inertia tensor,computed numerically forFig.3Computation of collision response using impulse-based method.In a each dot represents the location of a body at timestep t i.If penetration occurs at time step t i+1,a pairs of impulses is applied to avoid this penetration.The time for collision t c is estimated in order to avoid geometric overlap during collision.In b two bodies collide(fig-ure after Mirtich1996):r a and r b are vectors from the center of mass to the contact point,p a and p b are the applied impulses,u a and u b are the relative velocities at the contact point,v a and v b are linear velocities,ωa andωb are angular velocities,and I a and I b are the respective inertia tensors each fragment,as in[60].The relative velocity between the colliding bodies is defined asu(t)=1m a+1m b1−(r a I−1a r a+r b I−1b r b)p =Kp(14) where1is the identity matrix,and K is the constant,nonsin-gular,symmetric,and positive definite collision matrix[26]. The inversion of K plays a central role in the computation of the impulses during the collision,as p=K−1 u.Hahn[24]introduced friction into the approach by neglecting the tangential velocity after collisionu f=−eu b n n(15) where u f is the relative velocity after collision,n is the nor-mal vector at the contact point,e is the restitution coefficient, and u b n is the normal component of the relative contact veloc-ity before collision.Friction is implemented by applying Newton’s law,con-sidering the static friction condition|p t|<μ|p n|(16) where p t and p n are the impulse components tangent and nor-mal to the collision,respectively,andμis the coefficient of friction.The relative velocity in the normal direction before and after collision should satisfy u f n=−eu b n[58],in order for the system to be energy conservative[59].When the static friction condition is not satisfied,the magnitude of normal component of impulse p is defined as|p n|=−ubn(e+1)n T K(n−μt)(17) where t is the tangential vector at contact point.Finally,the impulse is defined asp=|p n|n−μ|p n|t.(18) Energy loss during a collision due to fracture propaga-tion,wave propagation,heat,sound,and other dissipative energy mechanisms,is currently represented by a constant restitution parameter.Restitution is taken here to be0.8,cor-responding to a loss of36%of the energy at each collision. Accurate and efficient estimation of collision energy loss is a key unresolved challenge,part of our work in progress.The computed impulse is used to resolve the dynamics of the system as a function of time and body geometry.The algorithm deals with convex bodies such as tetrahedra and hexahedra directly,and relies on convex body decomposi-tion of the original domain to handle non-convex shapes. This method is viable for the simulation of gravity-driven dynamics,for continuous and discontinuous contact ing this approach,collisions are the only mechanism through which forces are transmitted between bodies.5DeformationFragments are handled as independent FEM domains.Defor-mation is modeled quasistatically assuming an homoge-neous,isotropic,linear elastic medium[61]:σ=D e(ε−ε0)+σ0(19)whereσandεare the strain and stress vectors,σ0andε0are the initial strain and stress,and D e is a linear elastic stiffness matrix.For a static system∂σ+F=0(20)where∂is the divergence operator and F represents the exter-nal body forces,i.e.gravity,dilatation,and acceleration.The ensuing system is solved using FEM,for which displace-ments are the solution variable defined at the nodes,and material properties are defined at the element Gaussian inte-gration points at which stresses and strains are computed.The FEM inversion of the matrix is performed using the Fraun-hofer SAMG Solver[62],which solves for vectorialfields using the multi-grid method.The fragment domain is discretized using a three-dimensional mesh composed of a set of isoparametric quadratic bars,triangles and tetrahedra.Elements around the crack tip are quarter-point tetrahedra,which better capture the singularities at the fracture tips,and improve accuracy in stress intensity factor calculations[63,64].Figure4illus-trates the stress contours computed during the collision of a sphere with the ground,the non-symmetric nature of the field is attributed to the effect of growing internal fractures.The insides of the fractures are not meshed.These exist as negative volumes surrounded by matrix elements.Meshes are generated based on the geometry,and their optimization is based on geometry,wherebyt r=O(d t)(21) where t r is the triangle resolution,O is a quadratic function, and d t is the distance to the closest fracture NURBS surface tip.6Fracture propagationWe assume that each fragment has a set of pre-existingflaws, which grow into fractures in response to the collision stresses: H⊃{f o i}∪{f i}(22) Each fracture evolves from a set of growth curves,and is stored as a set of parametric surfaces.At each growth step,a new tip front curve forms from the movement of the original tip.The region between these two curves,represented by a ruled surface,corresponds to the new crack surface area; this is called the progression front.These curves describethe Fig.4Mean stress state contours of sphere at impact.The red arrow indicates the location of impact.The images are two rotations of the same3D contour distribution.Notice the compression area ensuing around the point of impact,and the tensilefields emerging around grow-ing fracturesgrowth of the fracture body,a polyhedron that grows driven by the addition of the progression front to its boundaries. Figure5a shows an example of progression of the ensuing fracture mesh during growth,as a function of the local stress field depicted in Fig.5b.6.1Stress intensity factor computationStress intensity factors(SIF)are approximated at the center of each fracture tip segment.Most methods,such as the stiff-ness derivative[65]and the displacement correlation tech-nique,rely on a symmetric brick-like mesh around the tip, in which case the tip region must be discretized by symmet-ric prism and hexahedral elements arranged in an annular manner.In the present approach,mesh optimization is based on geometry,and is thus arbitrarily generated to optimize the number and quality of the meshes.Therefore,a specific mesh structure around the tip cannot be guaranteed.MoreflexibleFig.5Fracture growth.a Side view,and b top view of the same frag-mentation.Thefigure illustrates multiple,simultaneous,discrete frac-ture growth.The stressfield is represented by colored tensors,plotted in logarithmic scaleintegration techniques are implemented to obtain accurate SIF values:specifically,the reduced virtual integration tech-nique[49],based on the J-integration over a virtual cylinder extracted from an arbitrarily-defined mesh[66].This allows SIFs to be computed accurately,independently of the mesh layout.The stress intensity factor is a measure of the energy con-centrated around the crack tip.For linear elastic,brittle mate-rials,J=G,where G is the strain energy release rate,and the J Integral,introduced by[67]and[68],characterizes the amplitude of the singularfield around a sharp fracture tip.The J Integral,defined as a volume integral in local space,is the energy released by a unit fracture extension in the direction of the fracture plane,defined as J v=1A cVσi j∂u j∂x k−Wδik∂q k∂x i d v(23) where W denotes the strain energy density,A c is the increased crack surface area,δis the Kronecker delta,and q is an arbitrary weighting vector function representing the virtual crack extension.It follows that J=G=K2E ef f, and[69]E ef f=E11+ν2+νν+1εzεx+εy(24) where E is Young’s modulus,νis Poisson’s ratio,andεx,εy, andεz are the local principal strains.6.2Propagation angleThe propagation angle is determined by a3D angle criterion for multi-axial loading[70],which is a modified maximum circumferential stress method[71]that takes into account K I,K I I,and K I I I.The criterion considers growth in terms of two deflection anglesϕo andψo which are perpendicu-lar and tangent to the crack tip,respectively,as a function of maximum principal stressσo and the stress components σϕ,σz,τϕz in the reference cylindrical coordinates(ϕ,z) defined around the tip.It follows that the deflection angle ϕo is computed as∂σo∂ϕϕ=ϕo=0and∂2σo∂ϕ2ϕ=ϕo<0(25) the deflection angleψo is defined by the orientation ofσo asψo=12arctan2τϕz(ϕo)σϕ(ϕo)−σz(ϕo)(26) and the component of the local stress intensity factor in the direction of propagation,K v is defined asK v=12cos(ϕo/2)K cs+K2cs+4K2I I I(27)where K cs=K I cos(ϕo/2)2−3/2K I I sin(ϕo).ϕo is com-puted numerically a priori,as a function of the normalized modal K n i whereK n i=|K i|K I+|K I I|+|K I I I|(28) for i={I,I I,I I I},and assuming that K I>0.It follows that–for pure mode I-ϕo=0◦∧ψo=0◦–for pure mode II-max(ϕo)=70.5◦∧ψo=0◦–for pure mode III-ϕo=0◦∧max(ψo)=45◦In areas where the discretization error is high,e.g.in the case of proximal objects ready to intersect,the propagation angle is assumed to be zero.6.3FailureThree main failure criteria have been used to determine growth[72]:the maximum circumferential stress crite-rion[71]for which the implementation is straightfor-ward,accurate,and dependent on mesh refinement;the minimum strain energy density criterion[73],which is less accurate and also mesh-dependent;and the maxi-mum strain energy release rate criterion,which requires complex implementation of stress intensity factor mea-surements at the fracture tips,but the accuracy of which is mesh-independent.An energy-based approach is used in the present work,in order to remain discretization-independent.This requires the computation of SIF around the tip.A failure criterion,such as the sub-critical failure criterion e.g.[74],determines whether or not local fracture propaga-tion will occur:K I C≥K v≥K I∗(29) where K I C is the critical stress intensity factor,or tough-ness,and K∗I is the sub-critical stress intensity factor,usually defined as some fraction of K I C.6.4Propagation extentThe propagation criterion describes the magnitude of prop-agation.Fractures are assumed to grow quasistatically, as a result of applying the average force occurring dur-ing impact in an iterative manner until growth ceases. Dynamic effects of growth are incorporated by adjusting the propagation law to the velocity at which objects col-lide.An empirical Paris-Walker approach[75,76]is used, which relies on a power law depending on the SIF and SIF ratio,which has been shown to increase exponentially as a function of impact velocity[77],as well as on material-specific,experimentally-measured properties:da d N =C(1−R)p K maxα∗(30)whereα∗and C are the Paris constants,K max is the maximum stress intensity factor local to the fracture tip,andR=K min/K max(31) where K min is the minimum stress intensity factor local to the fracture tip,and R is the stress ratio.Figure6shows the relationship between the exponent and the fracture advance.The parameter p is modeled as a function of dam-age,which has been shown to be proportional to the cube of the impact velocity[78].In this work,it is assumed thatα∗=10,which is in the range of mea-sured growth exponents for quasi-brittle materialse.g.Fig.6Fracture growth as a function of the propagation law exponent. For higher propagation exponents,only few cracks grow at a higher speed,whereas for lower exponents the distribution of growth tends to Gaussian[79].Growth is computed using a simplified form of Eq.30a ad v=a max(G/G max)α=α∗(1−D∗)2(32) where G is the strain energy release rate,a function of the stress intensity factor,G max is the fracture’s maximum G,a ad v is the advance distance at a single point at the crack tip,a max is the maximum crack advance,andαis the modified growth exponent.The exponent p is defined byD∗=f(D)(33) where D∈[0,1]is a variable representing damage of the fragment due to impact in terms of micro-crack nucleation during collision.It is assumed that[78]D∝v3c(34)where v c is the collision velocity,D=0for v min=110m/s and D=1for v max=220m/s after[80].Specifically,it is proposed thatD∗=2(v c−v min)v max3(35) whereαvaries exponentially as depicted in Fig.7.It follows thatv c=v max231−α/α∗+v min.(36)This approach models high and low velocity scenarios that exhibit fragmentation properties that are consistent with experimental data.Propagation and failure criteria are both material and in-situ condition dependent,and should be adjusted as part of the experimental setup of the defor-mation experiments.Details of the implementation and validation of the three-dimensional fracture propagation,。
Experiment on distributed dynamic
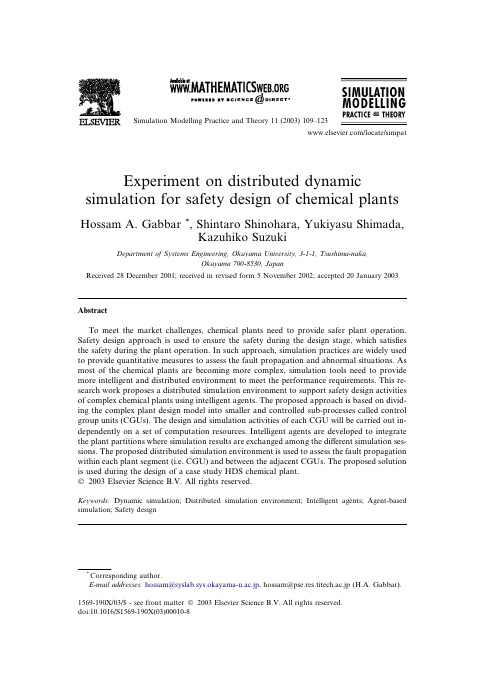
Experiment on distributed dynamicsimulation for safety design of chemical plants Hossam A.Gabbar *,Shintaro Shinohara,Yukiyasu Shimada,Kazuhiko SuzukiDepartment of Systems Engineering,Okayama University,3-1-1,Tsushima-naka,Okayama 700-8530,JapanReceived 28December 2001;received in revised form 5November 2002;accepted 20January 2003AbstractTo meet the market challenges,chemical plants need to provide safer plant operation.Safety design approach is used to ensure the safety during the design stage,which satisfies the safety during the plant operation.In such approach,simulation practices are widely used to provide quantitative measures to assess the fault propagation and abnormal situations.As most of the chemical plants are becoming more complex,simulation tools need to provide more intelligent and distributed environment to meet the performance requirements.This re-search work proposes a distributed simulation environment to support safety design activities of complex chemical plants using intelligent agents.The proposed approach is based on divid-ing the complex plant design model into smaller and controlled sub-processes called control group units (CGUs).The design and simulation activities of each CGU will be carried out in-dependently on a set of computation resources.Intelligent agents are developed to integrate the plant partitions where simulation results are exchanged among the different simulation ses-sions.The proposed distributed simulation environment is used to assess the fault propagation within each plant segment (i.e.CGU)and between the adjacent CGUs.The proposed solution is used during the design of a case study HDS chemical plant.Ó2003Elsevier Science B.V.All rights reserved.Keywords:Dynamic simulation;Distributed simulation environment;Intelligent agents;Agent-based simulation;Safety design*Corresponding author.E-mail addresses:hossam@syslab.sys.okayama-u.ac.jp,hossam@pse.res.titech.ac.jp (H.A.Gabbar).1569-190X/03/$-see front matter Ó2003Elsevier Science B.V.All rights reserved.doi:10.1016/S1569-190X(03)00010-8Simulation Modelling Practice and Theory 11(2003)109–123110H.A.Gabbar et al./Simulation Modelling Practice and Theory11(2003)109–1231.IntroductionSafe operation is one critical factor to meet the increasing market challenges in chemical and petrochemical industry.To achieve safer plant operation,it is essential to ensure the process safety during the process design stage.Safety design approach is widely used to assess safety during the design stage.It is desirable for the control and safety engineers to make an early input to the design process[1]so that harmful effects of potential hazardous events can be avoided and/or mitigated during the de-sign stage[15].The safety design practices include quantitative assessment where propagation speed,likelihood,and risk can be calculated using dynamic simulator. In addition,the use of the simulation practices during the design stage will enable designers to debate the different design rationales for more efficient process design and plant operation.To meet the ever-increasing market requirements,the chemical plants are getting more complex with tighter safety and efficiency requirements.To support the design and simulation of complex chemical plants it is essential to pro-vide better performance with more intelligent tools to be able to analyze wider range of design alternatives as well as to support the real time simulation practices.Such sophisticated tools can be used for plant operation as well.Researchers are focusing mainly on the improvement of the computation side(i.e.distribution)to improve the current simulation tools.In such approach,the computation load is distributed over a set of computation nodes(i.e.workstations)over network.Distributed operating systems,better performance network,and large-scale machines can be good candi-date to improve the performance.The overall performance of the simulation practices can be improved by enhanc-ing the process modeling approach and by building intelligent services(ing middleware)to integrate the modeling and simulation components with the design environment.Such approach is useful and showed remarkable improvement in the performance of the simulation practices.There are many researchers are motivated to pay more attention to provide intelligent modeling and simulation environment. Marquardt and his research group in Aachen University are developing model-based solution to support lifecycle activities,which includes simulation tools[9].In such approach modeling environment has been provided to manage and manipulate the lifecycle integrated models within repository-based automated modeling environ-ment(ModKit)[12,13].Towards the realization of such distributed simulation envi-ronment,agent technologies are employed[14].The target of such approach is to build complete simulation environment,which includes the simulation engine(i.e. solver)and the distributed environment.However conducting the distribution in the engineering layer can be considered as a useful and complementary solution for better simulation performance.This can be achieved by partitioning the plant design model into smaller portions.Such parti-tioning will improve the performance of simulation practices of complex plants.In addition,the partition of complex plants is required from engineering point of view to analyze each portion separately or analyze many portions simultaneously.This will lead to great reduction in the time required to design a complex ing such approach,process safety can be improved by conducting the safety assessmentH.A.Gabbar et al./Simulation Modelling Practice and Theory11(2003)109–123111 on different portions simultaneously.From the above,the partitioning of process model can be used to improve the safety,design,and simulation practices of complex chemical plants.This can be viewed as two major steps:(a)conduct design/safety/ simulation on different portions independently and simultaneously;(b)integrate these portions to achieve the overall function and behavior of the whole plant.This research work describes an experiment performed on a selected case study of HDS chemical plant,where the plant design model is partitioned into smaller por-tions called control group units or CGUs[4].The safety design activities are con-ducted on each CGU independently using a set of simulation sessions.The simulation practices are carried out on all CGUs simultaneously.The safety and sim-ulation results of each CGU are then integrated to assess the overall plant.In this research work,an existing dynamic simulator(software)called Visual Modeler TM is used to carry out the simulation activities for each CGU.Such dynamic simulator is installed in different simulation nodes to enable the different process designers to work with one or more CGU simultaneously.Intelligent agents are integrated within the proposed solution to integrate the distributed simulation sessions and to provide interface links with other components within plant enterprise engineering environ-ment[2,3].These intelligent agents provide the means to exchange real time simula-tion results among the distributed simulation ing such distributed simulation environment,the safety design approach can be conducted with better performance.The safety design approach starts with conducting fault propagation analysis to identify all possible scenarios that lead to abnormal situation(such as process fault, failure,or hazard).For each scenario(or case),the simulation practices are made to quantify the risk associated with each scenario[5].The proposed distributed simula-tion environment will enable process designers to conduct the simulation of the dif-ferent CGUs simultaneously and to define the associated risk and fault propagation speed by exchanging the simulation results between the different simulation nodes (i.e.CGUs).The following section describes the concept of safety design and the use of simu-lation practices in distributed manner to support safety design of complex plants. Then the proposed distributed simulation environment will be explained using the concept of multiagent system.Finally,safety design practices using the proposed dis-tributed simulation environment will be illustrated on the selected case study of HDS plant.2.Quantitative safety assessmentTo achieve the concept of safety design,AIChE/CCPS has introduced the concept of independent protection layers,or IPL,to reduce the risk(i.e.likelihood and sever-ity)of the impact of an identified hazardous event[15].By analyzing each hazardous event and the associated risk,it will be possible to design the detection,mitigation and avoidance means for each risk.The assessment of each risk requires quantita-tive means to measure the associated likelihood and severity.Fig.1(a)shows theproposed safety design approach,where quantitative safety assessment is performed using simulation practices.The different hazardous and abnormal situations are identified using qualitative safety assessment technique such as HAZOP.For each hazardous situation(or scenario),the initiation event will be identified using event tree analysis,root cause analysis,or cause-consequence ing such initiat-ing event,the simulation practices will be used to evaluate the risk of the abnormalor hazardous situation using the likelihood and severity of each abnormal or hazard-H.A.Gabbar et al./Simulation Modelling Practice and Theory11(2003)109–123113 ous situation.For high-risk events,identify the suitable causes/consequences/reme-dies.In case of complex plants,process design model can be divided into CGUs.The safety assessment of each CGU can be conducted separately and simultaneously. The fault propagation information can be integrated among the different CGUs to cover the overall safety assessment of the whole plant.The above quantitative safety assessment mechanism is modified to show the fault propagation mechanism among the different adjacent CGUs.Fig.1(b)shows the proposed quantitative safety assess-ment mechanism,which can be used to assess the safety of complex plants by divid-ing the plant into CGUs.The fault propagation speed and direction can be calculated using the same quantitative approach.The distributed simulation environ-ment will support such quantitative safety assessment approach for complex plants by conducting the simulation of the selected CGUs simultaneously.The following section describes the integrated engineering environment,which is used to carry out the distributed simulation.3.Integrated engineering environmentIn order to meet the stated objective of this experiment,the research team pro-posed the system architecture of the integrated engineering environment as shown in Fig.2.The integrated environment is composed of design,simulation,and mod-eling components,as integrated with safety management system(CAPE-SAFE)[10]. Array Fig.2.Simulation environment as integrated within PEEE.These components are integrated with other components,such as operational sys-tems,within the plant enterprise engineering environment (PEEE)[2,3].The process design model elements are stored and maintained in the model repository within the modeling environment (CAPE-ModE)[11].The proposed design activities are sum-marized in Table 1.The safety design activities are carried out within the design ac-tivities.4.Distributed simulation environmentThis experiment enables multiple designers to work simultaneously in integrated engineering environment and to conduct the safety design activities in the different CGUs.This requires sharing process design model and knowledge.In addition,an intelligent mechanism is required to partition the underline plant into CGUs [4].Pro-cess designers will perform the different design tasks within their domain (-putation node),while the process design model will be maintained centrally in the central repository.The following section explains the detailed steps and components of this experiment.4.1.System architectureVisual Modeler simulator is installed in the application server to enable all con-nected workstations to establish a simulation sessions via the network layer.Two process designers are using two workstations,which are connected to the application server via LAN connection.Each workstation runs a simulation session of Visual Modeler and design environment session while establishing a connection to the en-terprise safety management environment CAPE-SAFE,which covers the safety as-sessment activities within each CGU.Fig.3shows the proposed distributed simulation environment,which is integrated with the automated modeling environ-ment (CAPE-ModE),enterprise safety management system (CAPE-SAFE),and theTable 1Design activities using PEEETaskPEEE component 1Develop basic plant model elements CAPE-ModE 2Initial design of plant process (CGUs)CAD 3Maintain plant design model as per plant design models CAD +CAPE-ModE 4Maintain simulation model as per plant design models Simulator +CAPE-ModE 5Conduct safety assessment on sub-processes CAPE-SAFE 6Conduct simulation for quantitative risk assessment based on safety assessment results Simulator +CAPE-SAFE 7If needed,apply changes to plant design model using safety and simulation results CAD 8Accordingly,maintain plant design model CAD +CAPE-ModE114H.A.Gabbar et al./Simulation Modelling Practice and Theory 11(2003)109–123computer-aided design environment (CAD).Simulation agents (i.e.simulation agent-1and simulation agent-2)are developed to manage the integration among the different simulation sessions with the mediator agent (i.e.simulation agent-M).The concept of multiagent will be explained in the following section along with the proposed mechanism,which manages the distributed simulation environment.4.2.Simulation agentsIn order to realize the proposed distributed simulation environment,it is essential to select an efficient technology,which provides distributed computation capabilities.Multiagent systems engineering is a concept invented to solve complex problems [6].And multiagent technology has been used widely to develop distributed environment in different disciplines in engineering.In this research work,intelligent agents are de-veloped to realize the distribution of the simulation tasks among different simulation sessions and nodes.The concept of mediator agent has been adopted to enable the communication among the different simulation-nodes.The communication among the different agents can be performed using either the brokering or the recruiting communication mechanisms [7].The brokering mechanism is implemented as:(a)re-ceiving a request message from an agent;(b)understanding the request;(c)finding the suitable receptors for the message;and (d)broadcasting the message to the se-lected group of agents.The recruiting mechanism is considered as a superset of the brokering mechanism,since it uses the brokering mechanism to matchagents.Fig.3.Multi-Agent Simulation Environment.H.A.Gabbar et al./Simulation Modelling Practice and Theory 11(2003)109–123115For both the brokering and recruiting mechanisms,the mediator agent requires suf-ficient organizational knowledge to match agent requests with requested resources. The organizational knowledge at the mediator level is a list of agent-to-agent rela-tionships that is dynamically developed and maintained[8].Once designer starts the design session(which is used to perform safety design ac-tivities),a simulation session along with a simulation agent will be initialized auto-matically.Each simulation agent is registered in the mediator agent to enable future collaboration work.Each simulation agent will maintain knowledge about the current simulation session that covers one CGU.In the shown system architec-ture,workstation-1covers process design of CGU1,while workstation-2covers pro-cess design of CGU2.The communication among the different agents is realized via sending and receiving messages.These messages include knowledge such as the loca-tion of the agent or the simulation results of one simulation session.The exchange of the real time simulation results among the different simulation sessions is essential to understand the overall behavior of the underline process design.5.Case studyIn this experiment,the proposed distributed simulation environment is utilized to perform safety assessment during the process design stage of HDS plant.5.1.HDS plant modelIn order to carry out the distributed simulation practices,HDS plant is parti-tioned into smaller sub-processes i.e.CGUs:Feed Surge Drum(CGU1),Reactor (CGU2),Scrubber(CGU3),and Stripper(CGU4).Fig.4shows the high-level pro-cess block diagram of HDS plant using the concept of CGUs to partition the plant model.Within the design session in workstation-1,thefirst designer starts building the detailed design of CGU3(i.e.scrubber),while the second designer builds the detailed process design of CGU4(i.e.stripper)within the workstation-2.Simulation sessions are established in each workstation.The detailed P&ID of CGU3and CGU4are maintained within the design environment,and mapped into simulation models within the simulation sessions.H.A.Gabbar et al./Simulation Modelling Practice and Theory11(2003)109–123117Figs.5and6shows the detailed process design models of CGU3&CGU4as de-fined within the simulation environment(i.e.simulation sessions)using the model ed-itor of Visual Modeler simulator.The link between these two CGUs is established via the connection points(i.e.the input line to the stripper in the stripper CGU is connected to the low-pressure separator in the scrubber CGU).The model elements of the above CGUs of HDS plant are stored within the central model repository where the structure units as well as the connectivity(i.e.topology)are stored.In such repository,the connection between the two CGUs are stored as set of connection points between the structure units from the stripper CGU and structure units from the scrubber CGU.Similarly,the simulation models are represented using the same modeling approach[2].5.2.Agent-based distributed simulationIn Fig.7,agent-1is initiated to manipulate the simulation results of the Scrubber CGU3in workstation-1,while agent-2is initiated to manipulate the simulation re-sults of Stripper CGU4in workstation-2.In order to properly analyze the fault prop-agation from CGU3to CGU4,the simulation results of CGU3should be passed to the simulation session of CGU4.This will ensure that the fault propagation,ex-pressed in the real time values associated with the different process variables,is passed to the next CGU.The knowledge maintained by each simulation agent in-cludes equipment ID,type,process variables,and the real time simulation results. The mediator agent includes knowledge about the location of all simulationagents Array Fig.5.Simulation model of scrubber CGU of HDS plant.associated with all CGUs,as well as information related to each CGU (i.e.CGU boundary).In each simulation node,the process variables are identified and stored within the agent data space,while index is stored within the mediator data space.This will enable both the simulation agents and mediator agent to locate the part of the process and locate the suitable agent intelligently andtransparently.Fig.6.Simulation model of stripper CGU of HDS plant.118H.A.Gabbar et al./Simulation Modelling Practice and Theory 11(2003)109–123There are two major modes of implementing the proposed distributed simulation environment as explained in Table 2.In this experiment,mode (1)has been selected.The collaboration among the different simulation agents and the mediator agent (or the controller)can be summarized as in Table 3.Appendix A shows the detailed code for each simulation agent written in Java.In case of process failure or abnormal situation,the results obtained from agent-2will represent the fault propagation from CGU3to CGU4.This approach can be ef-fectively used to analyze and quantify the fault propagation throughout the whole HDS process (i.e.all CGUs).5.3.Application of safety designThe proposed approach of safety design is composed of three major steps:1.Identify the initial event for each abnormal or hazardous event,which is initiatedeither from the current CGU or propagated from the adjacent CGU.Table 2Description of the different simulation modesMode (1)Save simulation resultslocally within thedomain of eachagent When new simulation session is started New agent is instantiated within that simulation node Save the Agent-CGU related information in the server within the mediator agent Õs domainSave the simulation results locally within the domain of the current agentIf needed,request simulation results about other CGUs from themediator agent,and obtain these results from other agents (or from thecentral store,if the other agent is terminated)If requested,send the simulation results about the local CGU to otheragentsWhen simulation session is completedSend the simulation results generated locally in the current simulationnode to the central mediator,and update the central tables to show thetermination of one agentMode (2)Save the simulationresults centrallyin the server,i.e.within the mediatoragent Õs domain When simulation session is started New agent is instantiated within that simulation node Save the related information to the Agent-CGU in the server within the mediator agent Õs domain While developing the simulation results,send the simulation results tothe server to be maintained centrally within the domain of the mediatoragentIf needed,request simulation results about other CGUs from themediator agent and obtain the results from the central storeWhen simulation session is completedUpdate the central tables to show the termination of one agentH.A.Gabbar et al./Simulation Modelling Practice and Theory 11(2003)109–123119120H.A.Gabbar et al./Simulation Modelling Practice and Theory11(2003)109–123Table3Collaboration mechanism between the mediator agent and other agents––in Mode(I)Task1Agent-2(CGU4––stripper)requests information from the mediator agent about the simulation results of the downstream CGU(i.e.CGU3––scrubber) 2The mediator agent(Controller)decides the agent responsible for the target CGU (CGU3––scrubber)3The mediator agent(Controller)requests simulation results about CGU3(scrub-ber)from the agent-14Agent-1sends the requested simulation results about CGU3(scrubber)(or error if not available)5The mediator agent sends the requested simulation results to the requester agent (agent-2)6Agent-2utilizes the received simulation results as initial values,and carries out simulation process of CGU4(stripper)2.Simulate the abnormal situation to assess the risk and fault propagation.3.Risk evaluation for the identified scenarios,using simulation results for the differ-ent hazard scenarios and abnormal situations.This section describes an example of one abnormal situation,which is used to illus-trate the application of safety assessment mechanism using the proposed distributed simulation environment.During the safety assessment practices within the scrubber CGU,low temperature is shown in the output line from the low-pressure separator, which is connected to the stripper CGU.Such abnormal situation propagates to the stripper CGU via the connection between the low-pressure separator in the scrubber CGU and the stripper unit in the stripper CGU.Such failure(i.e.low temperature in the input to the stripper)requires further assessment in the stripper CGU.The de-signer of the stripper CGU conduct safety assessment to understand the different rea-sons that might cause drop in the temperature inside the stripper unit.The simulation results shown in Fig.8(a)and(b)reflect two causes of such drop in temperature.Fig. 8(a)shows that the control valve between the reflux pump and the stripper unit failed to open.This will cause no-flow of the heatedfluid into the stripper,which will reduceH.A.Gabbar et al./Simulation Modelling Practice and Theory11(2003)109–123121 the temperature inside the stripper unit.Fig.8(b)shows that the control valve of the MP steam failed to close.Similarly,the designer of the stripper CGU can view the simulation results when there is a drop in the temperature in the line connecting the low-pressure separator unit(i.e.in the scrubber CGU)with the stripper unit.6.ConclusionThe chemical industry is facing increasing challenges to improve performance and to reduce cost,while enhancing the operation safety and efficiency.Safety design ap-proach is widely used to assess safety during the process design,while considering the plant lifecycle activities.As part of the safety assessment practices,quantitative mea-sures are required to calculate the risk associated with the different hazardous events and abnormal situations.The simulation practices are widely used to offer such quantitative assessment.To enable the design activities of complex plants,it is re-quired to offer simulation solution,which provides the required quantitative mea-sures in acceptable performance.The concept of distributed simulation can be used to reduce the time required to design complex plants where simulation practices can be conducted on different portions of the plant design model simultaneously. Such distributed environment can be used to carry out the safety assessment in more efficient manner.This research work explains an experiment to utilize the distributed simulation techniques to perform safety design practices on complex chemical plants.The pro-cess design model is divided into control group units called CGUs.The design and simulation activities are carried out on all CGUs simultaneously on different compu-tation nodes.An existing dynamic simulator called Visual Modeler is used to per-form the simulation tasks in each simulation node.The use of the existing dynamic simulator is useful to avoid building a simulation engine from scratch.In-telligent agents are employed to manage the distributed simulation sessions by offer-ing different functionalities such as exchanging the real time simulation data among the different simulation nodes.The concept of safety assessment of distributed CGUs is proposed,where the simulation results from other CGUs are utilized to recognize the fault propagation between the adjacent CGUs.The experiment is carried out on HDS plant where safety assessment are performed using the simulation results, which are shared among the adjacent CGUs.The proposed solution is useful to re-duce the time required to design and assess the safety of complex plants.In addition, it can be used efficiently to achieve real time simulation to support plant operation. Appendix A.Agents developmentIn this experiment,Java is used to develop the intelligent simulation agents.Sim-ulation data are exchanged among the different agents via the mediator agent(i.e. controller).Table4shows part of the+source code of the agent in-charge of the amine scrubber CGU.122H.A.Gabbar et al./Simulation Modelling Practice and Theory11(2003)109–123Table4Java source code of the amine scrubber agent/*Reception of Facilitator Facilitator*/System.out.println(00I recieve the requirement of Facilitator00);ObjectInputStream ois3¼new ObjectInputStream(socket3.getInputStream());String request¼(String)ois3.readObject();System.out.println(00massage from Facilitator>00+request);System.out.println(00Recieve00);String filename¼00StartUP.fdb00;System.out.print(00I load StartUP.fdb00);/*Send the result of simulation to Facilitator*/while(true){line¼reader.readLine();if(line!¼null){int anum¼0;Integer adic¼new Integer(anum);oos4.writeObject(adic);oos3.writeObject(line);oos3.flush();oos4.flush();i++;}else if(line¼¼null){System.out.println(00I have loaded the end of the file00);System.out.println(00End the transmission of the file00);int anum¼1;Integer adic¼new Integer(anum);oos4.writeObject(adic);oos4.flush();System.out.println(anum);System.out.println(00End the task of Amine Scrubber Agent00);break;}}References[1]P.Thomas,Simulation of Industrial Processes for Control Engineers,Butterworth Heinemann(Eds.),ISBN0750641614,1999.[2]H.A.Gabbar,P.W.H.Chung,K.Suzuki,Y.Shimada,Utilization of unified modeling language(UML)to represent the artifacts of the plant design model,in:International Symposium on Design, Operation and Control of Next Generation Chemical Plants(PSE Asia2000),PS54,Japan,December 2000,pp.387–392.[3]H.A.Gabbar,K.Suzuki,Y.Shimada,Design of plant safety model in plant enterprise engineeringenvironment,Journal of Reliability Engineering and Safety Systems73(1)(2001)35–47.[4]Y.Naka,R.Batres,T.Fuchino,Operational design and its benefits in real-time use,Foundations ofComputer Aided Process Operations,ISBN0-8169-0776-5,1999,pp.570.[5]N.Sato,K.Suzuki,Hazard assessment and safety design based on the dynamic behavior of abnormalsituation,Master degree thesis in the Department of Systems Engineering,Okayama University, Japan,2000.。
Influences of mesh density and transformation behavior on the result quality of numerical calculatio
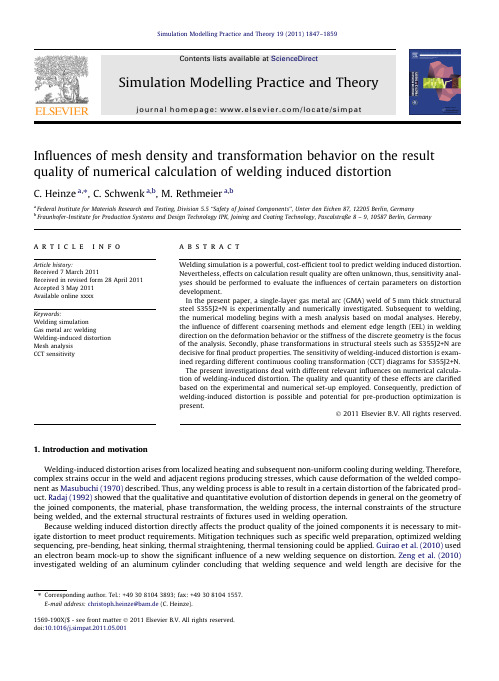
Influences of mesh density and transformation behavior on the result quality of numerical calculation of welding induced distortionC.Heinze a ,⇑,C.Schwenk a ,b ,M.Rethmeier a ,baFederal Institute for Materials Research and Testing,Division 5.5‘‘Safety of Joined Components’’,Unter den Eichen 87,12205Berlin,Germany b Fraunhofer-Institute for Production Systems and Design Technology IPK,Joining and Coating Technology,Pascalstraße 8–9,10587Berlin,Germanya r t i c l e i n f o Article history:Received 7March 2011Received in revised form 28April 2011Accepted 3May 2011Available online xxxx Keywords:Welding simulation Gas metal arc welding Welding-induced distortion Mesh analysis CCT sensitivitya b s t r a c tWelding simulation is a powerful,cost-efficient tool to predict welding induced distortion.Nevertheless,effects on calculation result quality are often unknown,thus,sensitivity anal-yses should be performed to evaluate the influences of certain parameters on distortiondevelopment.In the present paper,a single-layer gas metal arc (GMA)weld of 5mm thick structuralsteel S355J2+N is experimentally and numerically investigated.Subsequent to welding,the numerical modeling begins with a mesh analysis based on modal analyses.Hereby,the influence of different coarsening methods and element edge length (EEL)in weldingdirection on the deformation behavior or the stiffness of the discrete geometry is the focusof the analysis.Secondly,phase transformations in structural steels such as S355J2+N aredecisive for final product properties.The sensitivity of welding-induced distortion is exam-ined regarding different continuous cooling transformation (CCT)diagrams for S355J2+N.The present investigations deal with different relevant influences on numerical calcula-tion of welding-induced distortion.The quality and quantity of these effects are clarifiedbased on the experimental and numerical set-up employed.Consequently,prediction ofwelding-induced distortion is possible and potential for pre-production optimization ispresent.Ó2011Elsevier B.V.All rights reserved.1.Introduction and motivationWelding-induced distortion arises from localized heating and subsequent non-uniform cooling during welding.Therefore,complex strains occur in the weld and adjacent regions producing stresses,which cause deformation of the welded compo-nent as Masubuchi (1970)described.Thus,any welding process is able to result in a certain distortion of the fabricated prod-uct.Radaj (1992)showed that the qualitative and quantitative evolution of distortion depends in general on the geometry of the joined components,the material,phase transformation,the welding process,the internal constraints of the structure being welded,and the external structural restraints of fixtures used in welding operation.Because welding induced distortion directly affects the product quality of the joined components it is necessary to mit-igate distortion to meet product requirements.Mitigation techniques such as specific weld preparation,optimized welding sequencing,pre-bending,heat sinking,thermal straightening,thermal tensioning could be applied.Guirao et al.(2010)used an electron beam mock-up to show the significant influence of a new welding sequence on distortion.Zeng et al.(2010)investigated welding of an aluminum cylinder concluding that welding sequence and weld length are decisive for the 1569-190X/$-see front matter Ó2011Elsevier B.V.All rights reserved.doi:10.1016/j.simpat.2011.05.001⇑Corresponding author.Tel.:+493081043893;fax:+493081041557.E-mail address:christoph.heinze@bam.de (C.Heinze).1848 C.Heinze et al./Simulation Modelling Practice and Theory19(2011)1847–1859corresponding welding-induced distortion and residual stresses.Adak and Mandal(2010)experimentally and numerically investigated the influence of heat sinking on deflection resulting in a model suitable for parameter optimization and distor-tion prediction.Deo and Michaleris(2003)have shown that thermal tensioning is applicable to reduce buckling distortion, but as a result angular distortions became evident.Subsequently,the angular distortion was mitigated using mechanical restraints.At this point,the numerical simulation of welding-induced distortion represents a useful tool because it enables predic-tion of distortion,which leads to a prior description of distortion development and allows well-directed optimization of welding-induced distortion evolution in practice.Over the past30years,thefinite-element method has been used in an at-tempt to predict distortion due to welding.Deng and Murakawa(2008)provide an example of numerical simulation of weld-ing-induced distortion regarding thin steel plates.Publications with respect to structural steel GMA butt-welds with plate thicknesses of about5mm or larger are rare in literature.Mollicone et al.(2008)investigated procedural influences such as tack welds,support conditions and clamping on 3–8mm butt welds.They state that tack welding had just little effect on welding-induced distortion development related to the applied configuration.Furthermore,Wang et al.(2008)analyzed carbon steel in thickness ranges of3.2–4.5mm.The experimental and calculated results show good agreement but the experimental values are always more or less larger than the calculated.Wang et al.mention measurement error and meshing as the reasons for the differences.Meshing is a critical issue within the preprocessing of numerical simulations because its influence on deformation development due to welding. Tri-linear quadratic elements are usually preferred in analysis of problems in plasticity because they perform better than displacement based linear tetrahedrons as stated by Lindgren(2006).Schenk et al.(2009)experimentally and numerically investigated1mm thick DP600GMAW overlap joint based on modal analyses.It is shown that lateral mesh coarsening in less thermally and mechanically stressed zones,which is often used in numerical welding simulation due to decreased num-ber of nodes and elements resulting in savings of computing time,is actually not preferable with respect to acceptable re-sults of calculated bending distortion.In the case of the present5mm thick butt-weld model,the influence of the meshing on bending distortion is studied based on three mesh variations considering different coarsening strategies.Additionally, three different element edge lengths for one mesh are investigated on their effect on the bending behavior of the mesh.The interaction between welding-induced distortion and residual stress is described in different basic literature,see,e.g., Radaj(1992)or Feng(2005).When the yield strength of the present material or microstructural constituent is reached irre-versible deformation occurs.The formation of weld microstructures can be described by continuous cooling transformation (CCT)diagrams.Consequently,both residual stress and distortion evolution depend on the CCT behavior.Caron et al.(2010) have investigated the influence of CCT diagram variations on welding-induced residual stresses and found stress deviations up to90MPa considering CCT diagrams for a S355J2+N.For the structural steel S355J2+N the specification of the chemical composition is given in a wide tolerable range,which implies a certain tolerated transformation behavior and mechanical properties resulting from different chemical compositions within the mentioned range.The influence of compositional dif-ferences on the CCT diagram and,finally,on the evolution of welding-induced distortion is numerically studied based on four CCT diagrams valid for the steel grade S355J2+N.Hereby,a CCT diagram is taken from the SYSWELD material database for S355J2,two calculated(software JMatProÒand EWIÒVirtual Joining Portal)and an experimentally determined CCT diagram are also included in the investigations.The EWI calculations are based on the publications of Bhadeshia(1982)and Ion et al. (1984).The present paper deals with two aspects,which show considerable influences on the numerical calculation of welding-induced distortion.The investigated effects are quantified for a certain experimental set-up and conclusions for the general set-up of numerical models for the prediction of distortion are drawn.2.Experimental procedureThe steel used for the welding experiments was S355J2+N(1.0577),a German standardized plain-carbonfine-grained construction steel with a minimum yield strength of355MPa.The chemical composition for S355J2plate material,as spec-ified in the German DIN EN10025-2:2004standard,is provided in Table1.A stress-relief heat treatment,consisting of heating to570°C at5K/min,holding at temperature for3.5h,and furnace cooling to ambient temperature,was applied to the tack-welded plate material before welding to reduce any pre-existing residual stresses.The individual plate dimensions for the welding experiments were300mm length,100mm width,and5mm thickness containing a60°V-groove with seam edges milled.A single-pass complete-penetration gas metal arc weld was conductedTable1Nominal and measured chemical composition of S355J2+N plate material according to DIN EN10025-2:2004,values in wt.%.Nominal chemical compositionC Si Mn P S60.2360.661.760.03560.035Measured chemical compositionC Si Mn P S Fe0.140.200.670.0080.012Balancewelds;stochastic pattern for optical distortion measurement shown;plate dimensions:with G3Si1filler metal wire of1.2mm diameter,in accordance with DIN EN ISO14341,using a shielding gas mixture of 82%Ar and18%CO2at aflow rate of18l/min,in accordance with DIN EN ISO14175.Welding conditions consisted of 261A welding current,30.4V average arc voltage,8.5m/min wire feed rate,and0.4m/min travel speed.This resulted in an approximate net heat input of1kJ/mm for the considered GMAW process.Type-K thermocouple wires with a diameter of0.5mm were used to acquire the temperature at positions on both the top and bottom of the welded plate directly adja-cent to the weld seam.The experimental configuration,Fig.1,provided a force-free support of the plate,permitting free shrinkage during the welding process and subsequent cooling.Additionally,a ceramic weld backing was used for all con-ducted weld experiments.The welding-induced distortion was experimentally investigated using a direct image correlation system during the whole welding process including the initial state of the welded plate,the behavior during welding,and the cooling process down to30°C.The distortion evolution was investigated on one half of the plate.The influence of the pattern consisting of titanium dioxide(white layer)and iron oxide(black spots)on the welding process or weld seam quality is unclear,thus,a zone adjacent to the joint preparation was not provided with a pattern.Furthermore,welding results in an inevitable dete-rioration of the stochastic pattern close to the weld zone and HAZ,respectively,due to color changes and burn-off.During welding process,the arc causes overexposure of the digital cameras leading to a data loss in the corresponding areas.As a consequence,a matt black steel cover was attached to the torch limiting overexposure during welding.The experimental determined residual stress state,the numerical simulation of the residual stress evolution and a sen-sitivity analysis on the influence of CCT behavior on the residual stress state was evaluated in Caron et al.(2010)related to the material and experimental procedure described in this paper.3.Experimental resultsFig.2depicts the experimental weld macro section with the weld pool area outlined,weld metal microstructure near the fusion line,and the heat affected zone(HAZ)microstructure from a location that experienced a peak temperature of1159°C and a t8/5time of30.0s,where t8/5is the cooling time from800°C to500°C.Table2Summary of individual parameters for measured thermal cycles.Measurement Location Distance from weldcenterline(mm)Peaktemperature(°C)t8/5coolingtime(s)Top of plate8.495332C.Heinze et al./Simulation Modelling Practice and Theory19(2011)1847–18591851The weld metal microstructure consists mainly of Widmanstätten ferrite with aligned second phase(Fig.2b).The HAZ microstructure shown in Fig.2c consists of a mixture of grain boundary ferrite,polygonal ferrite,Widmanstätten ferrite withAdditionally,the element edge length (EEL)in welding direction (WD)was analyzed by three different configurations for the mesh type 3.Hereby,the EEL in WD or z -direction,referring to the coordinate system in Fig.7,was 1mm,2mm,and 3mm.The modal analyses used the PCG Lanczos method to extract a defined number of 5modes.A force-free support was as-sured by idealized clamping of the specimen using elastic constraints of 1000N/mm on three nodes indicated in Fig.7.The subsequent numerical simulation calculations of temperature field and mechanics in this study were performed with the commercial finite element software SYSWELD Òv2009on a standard PC with a Linux operating system.The most impor-tant simplifications and assumptions of the simulation are:Temperature dependent,homogeneous,and isotropic (except thermal conductivity in welding direction,factor 10applied)material properties with consideration of phase transformations.A solidus temperature of 1440°C for validation of the weld seam geometry.No consideration of preceding process steps,the specimen is assumed to be geometrically ideal and totally stress free,the weld reinforcement on the top and bottom side are considered.Phenomenological temperature field calibration using double-ellipsoid Goldak and 3D-conical Gauss heat sources with time independent volumetric heat flux density and no consideration of weld pool convection.Unified heat transfer on all outer surfaces with temperature dependent radiative losses according to Stefan–Boltzmann,a constant emission coefficient of e =0.8,constant convective losses of 4W/mm 2,and an ambient temperature of 20°C. Idealized clamping of the specimen using elastic constraints of 1000N/mm for a force-free support.Elastic–plastic material behavior considering isotropic hardening.4.1.Thermal analysisFor the thermal analysis,the experimentally determined data were used to calibrate the heat source of the simula-tion.Two aspects were considered in the temperature field adjustment.First,the cross-section geometry of the simu-lated weld pool was correlated with both the size and shape of the experimental macrosection of the weld seam.Second,the corresponding temperature cycles in the HAZ were correlated with the experimental measurements,with emphasis given to peak temperature and cooling time.With respect to the sensitivity of distortion on CCT behavior,each simulation was performed with an identically calibrated temperature field.Subsequently,the influence of different transformation behavior on the evolution of welding induced distortion is numerically studied based on four CCT dia-grams valid for the steel grade S355J2+N.Hereby,a CCT diagram is taken from the SYSWELD Òmaterial database for S355J2,two calculated (software JMatPro Òand EWI ÒVirtual Joining Portal)and an experimentally determined CCT dia-gram are also included in the investigations.The CCT diagrams used for the analysis are described in Heinze et al.(in press).8.Thermophysical input data for S355J2+N;(a)phase specific thermal conductivity and thermal strain;(b)specific heat capacity and density;source: SYSWELD material database version2009.4.2.Mechanical analysisAvailable in the SYSWELDÒsoftware is the ability to integrate the effect of metallurgical phase transformations in weld-ing simulations.A thermal–metallurgical calculation isfirst completed using the thermal properties of the material,the cal-culated temperaturefield derived and validated from the welding experiments,and the CCT behavior formulated mathematically.The thermal–metallurgical calculation data is then used as an input to the mechanical calculation,which determines stresses and strains according to the transient and spatial distribution of the previously calculated temperatures in the model.It is noted that this one-way coupling,also referred to as‘‘weak coupling’’,does not account for the effect of stress on phase transformation behavior.Furthermore,there is no interaction between the latent heat generated by solid state phase transformations and the calculated temperaturefield.To perform accurate and detailedfinite element simulations,the thermal and mechanical properties of the material must be known at high temperatures.One of the advantages in selecting the S355J2+N alloy was the availability of complete mate-rial properties in the SYSWELDÒdatabase(Version2009),including metallurgical phase transformation temperatures,met-allurgical model parameters,transformation plasticity,thermophysical,and thermomechanical properties.Fig.8exhibits the corresponding thermophysical input data for S355J2+N.The thermomechanical properties are displayed in Fig.9.The phase transformations were calculated using the models based on Leblond and Devaux(1984),Leblond(1986,1989),and Koistinen and Marburger(1959).5.Numerical simulation resultsFirst,the calculated eigenfrequencies of the modal analysis are presented in Tables3and4.Regarding the different mesh types,Table3gives an overview of eigenfrequencies corresponding to different eigenmodes.1854 C.Heinze et al./Simulation Modelling Practice and Theory19(2011)1847–1859Table3Calculated eigenfrequencies for the analyzed meshes(Fig.6),EEL in WD is2mm.Eigenmode Eigenfrequencies(sÀ1)Type1Type2Type31st torsion6767671st bending1781771772nd torsion3203193182nd bending4454344363rd torsion586555567 Table4Fig.12.Validation of temperaturefield:thermal cycles at top of the plate.Table5Calculated phase percentages for each CCT diagram,referring to a node with a peak temperature of1200°C andt8/5=25s.CCT diagram Phase(wt.%)Ferrite Bainite MartensiteSYSWELD0946Gleeble6904JMatPro53758EWI10000 For a better understanding of the effect of differences in calculated eigenfrequencies(Table3),Fig.10exhibits the tran-sient displacement in the thickness direction or bending,respectively,of the investigated mesh types.Hereby,the same tem-peraturefield,see Figs.12and13,was applied for all three calculations.In the following,eigenfrequencies representing the influence of different element edge lengths on welding-induced dis-tortion are shown for mesh type3,Table4.Additionally to Table4,Fig.11clarifies how the determined differences in eigenfrequencies affect the calculated welding-induced distortion depending on EEL.The validation of the temperaturefield is presented in Figs.12and13.The former shows both the experimental and the numerically calculated thermal cycles for two positions at the top of the plate.The latter exhibits the comparison for exper-iment and simulation related to the weld pool geometry.The validation results in a good agreement of weld pool geometry and thermal cycles considering the comparison of experiment andfinite element simulation.Table5depicts the resulting microstructural constituents of the validated temperaturefield depending on the corre-sponding CCT diagram.The evaluation was performed on a node referring to a peak temperature of about1200°C and a cool-ing time t8/5of25s,corresponding to Fig.2c.displacement in thickness direction(bending)depending on CCT diagram used,Furthermore,the transient displacement u y is shown for the investigated CCT diagrams,see Fig.14.Hereby,the mesh type 3with an EEL of2mm was used instead of1mm due to the higher computation times occurred.Additionally,thefinal state of the whole plate after welding and cooling down to room temperature is exhibited in Fig.15.6.DiscussionFirst,modal analyses were performed resulting in lowest eigenfrequencies regarding eigenmodes2nd bending and3rd torsion for mesh type2,Table3.But the calculated displacements in Fig.10show a deviating behavior in favoring mesh type 3instead of type2.Thus,the transferability of the modal analysis results is not clear when comparing different mesh types. Nevertheless,the results of the modal analyses performed with mesh type3considering different EEL describe a clear cor-relation.In detail,the mesh with1mm EEL shows the lowest eigenfrequency563sÀ1for eigenmode3rd torsion.An increase in EEL results in higher eigenfrequencies for2mm EEL(567sÀ1)and for3mm EEL(570sÀ1).The corresponding difference in final distortion between1mm and3mm EEL is about1mm,whereby,the computation time is approx.2.5times higher for the mesh with1mm EEL.Consequently,the modal analysis can give additional information about an appropriate meshing regarding the suitability for numerically calculated distortions,especially bending,but a mechanical analysis is necessary to assure the results of a model analysis.The obtained result for mesh type1,see Fig.10,is consistent with thefindings of Schenk et al.(2009)who do not recommend a mesh coarsening towards the plate edges.The various CCT diagrams used in the present welding simulation result in certain phase fractions after welding,Table5. The JMatProÒand the EWIÒCCT diagrams are based on calculations using the chemical composition for the test material (S355J2+N)given in Table1.The resulting differences are significant.The calculation with the CCT diagram provided by JMatProÒleads to a martensite fraction of58wt.%,a bainite fraction of37wt.%,and a ferrite fraction of5wt.%for a peak temperature of1200°C and a cooling time t8/5of25s.For the same conditions the EWIÒcalculation gives no martensite and bainite,but100wt.%ferrite.The GleebleÒCCT diagram was obtained by combining information of hardness measure-ments,dilatometry,metallography,and literature data for S355J2+N,see Caron et al.(2010).It is obvious that there are sim-ilarities with the SYSWELDÒCCT diagram,which is based on experimental data published in Seyffarth et al.(1992).Fig.16shows that large fractions of martensite and bainite result in a lower deformability of the plate based on the JMat-ProÒCCT diagram.A lower martensite fraction occurs in the cases SYSWELDÒand GleebleÒ,thus,the deformability rises and thefinal dis-tortion increases up to3.5mm(GleebleÒ)at the point of evaluation.With respect to the experimentally determined micro-structure,Fig.2b and c,the EWIÒprediction shows the best agreement.However,that fact is not expressed in the calculated distortion compared to the experimental data,Fig.16.The reasons is the high transformation temperatures of the EWIÒ,e.g.transient ferrite fraction development indicating the temperature of ferritefinish temperature1858 C.Heinze et al./Simulation Modelling Practice and Theory19(2011)1847–1859Since there is still a significant deviation between quantitative results of simulation and experiment,several influences have to be mentioned.First,the experimental weld pool geometry meets the limits of the equivalent Goldak and Gauss heat sources,which results in differences between experimental and calculated weld pool geometries.Furthermore,the simula-tion represents a heat conduction problem neglecting the heat convection in the weld pool,which indeed plays a decisive role in the performed experiments because weld pool length was determined to be about35mm.However,welding-induced distortion is highly sensitive to the weld pool geometry.This effect will be investigated in detail within future research.Sec-ondly,the mesh used in the simulations considering different CCT diagrams represents a compromise between computation time and practicability.In relation to that,thefine mesh type3with1mm EEL(175,000nodes and206,000elements)was additionally investigated considering the Gleeble CCT diagram.The resultingfinal displacement in y-direction,which refers to the point of evaluation in Fig.10,is about3.9mm representing a value about0.6mm or18%higher than the calculation based on the Sysweld CCT and the mesh with1mm EEL,shown in Fig.11.This result shows ability to optimize welding-in-duced distortion calculations based on mesh and CCT diagram studies.The thermophysical and the thermomechanical material parameters used in the numerical model have an effect on the calculated results as well,especially,when considering a wide range of possible chemical composition for a S355J2+N steel. Finally,the processing technology in terms of tack welding can affect the resulting calculated distortions.In further inves-tigations,the influence of tack welding on calculation of welding-induced distortion will be clarified.7.ConclusionsIn the present paper,modal analyses and a validated numerical simulation were used to investigate the influences of mesh density and different CCT behavior on result quality of calculation of welding-induced distortion.The modal analyses show that a coarsening with increasing distance to the weld seam is not preferable for the numerical calculation of distortion.However,coarsening in the thickness direction with increasing distance to the weld centerline has a positive effect on bending behavior of the investigated structure.The usage of modal analyses is possible in case of investi-gating the influence of different element edge lengths on the deformation behavior of a certain mesh type.But with respect to different mesh strategies mechanical analysis should be performed to assure the results of the modal analysis.Different CCT diagrams for the plain carbon steel S355J2+N were used to investigate the sensitivity of distortion on phase transformation characteristics.A significant effect including differences of up to60%was found according to the displace-ment in the thickness direction(y-direction,bending).The authors recommend a thorough study of available CCT data before calculating distortions or residual stresses as well.Transformation plasticity and thermal strain as contributions to the total strain have to be considered for the evaluation of the present behavior in terms of CCT sensitivity of distortion.The combination of the presentfindings of modal analysis and CCT diagram studies result in an optimized simulation exhibiting improved welding-induced distortion calculation,whichfinally reduced the quantitative deviation between experiment and numerical simulation.AcknowledgmentThe presented work was accomplished within the project IGF15746N‘‘Optimization of distortion and residual stresses during welding of thick-walled components’’of the Arbeitsgemeinschaft industrieller Forschungsvereinigungen‘‘Otto von Guericke’’e.V.(AiF).The authors gratefully acknowledge thefinancial support for this research from of the Federal Ministry of Economics and Technology(BMWi)through the‘‘Arbeitsgemeinschaft industrieller Forschungsvereinigungen e.V.’’.Fur-thermore,the authors thank Dr.J.Caron,Prof.S.S.Babu and Prof.J.Lippold from the Ohio State University for their contri-butions to the present paper.References[1]M.Adak,N.R.Mandal,Numerical and experimental study of mitigation of welding distortion,Applied Mathematical Modelling34(2010)146–158.[2]H.Bhadeshia,Thermodynamic analysis of isothermal transformation diagrams,Metal Science16(1982)159–165.[3]J.Caron,C.Heinze,C.Schwenk,M.Rethmeier,S.Babu,J.Lippold,Effect of continuous cooling transformation variations on numerical calculation ofwelding-induced residual stresses,Welding Journal89(2010)151–160.[4]D.Deng,H.Murakawa,FEM prediction of buckling distortion induced by welding in thin plate panel structures,Computational Materials Science43(2008)591–607.[5]M.V.Deo,P.Michaleris,Mitigation of welding induced buckling distortion using transient thermal tensioning,Science and Technology of Welding andJoining8(2003)49–54.[6]Z.Feng,Processes and Mechanisms of Welding Residual Stress and Distortion,Woodhead Publishing Ltd.,2005.[7]J.Guirao,E.Rodríguez,A.Bayón,J.Pistono,L.Jones,FEM simulation of a small EB welded mock-up and new sequence proposed to improve thefinaldistortions,Fusion Engineering and Design85(2010)181–189.[8]C.Heinze,C.Schwenk,M.Rethmeier,J.Caron,Numerical sensitivity analysis of welding-induced residual stress depending on variations in continuouscooling transformation behavior,Frontiers of Materials Science5(2011)168–178.[9]J.C.Ion,K.E.Easterling,M.F.Ashby,A2nd report on diagrams of microstructure and hardness for heat-affected zones in welds,Acta Metallurgica32(1984)1949–1962.[10]D.P.Koistinen,R.E.Marburger,A general equation prescribing the extent of the austenite–martensite transformation in pure iron–carbon alloys andplain carbon steels,Acta Metallurgica7(1959)50–59.[11]J.-B.Leblond,J.Devaux,A new kinetic model for anisothermal metallurgical transformations in steel including effect of austenite grain size,ActaMetallurgica32(1984)137–146.。
基于V-REP的机器人仿真实验系统及教学

ISSN 1002-4956 CN11-2034/T实验技术与管理Experimental Technology and Management第38卷第3期2021年3月Vol.38 No.3 M ar. 2021DOI: 10.16791/ki.sjg.2021.03.027虚拟仿真技术基于V-R E P的机器人仿真实验系统及教学葛连正,赵立军(哈尔滨工业大学机器人技术与系统国家重点实验室,黑龙江哈尔滨150001 )摘要:机器人设计需要采用“设计一仿真一优化”的过程,因此仿真技术是机器人T.程专业本科生必须掌握的技能该文基于V-REP仿真软件设计了一套6 A由度通用T业机器人仿真实验系统:首先建立了机器人的V-REP模型,进行系统动力学参数设置,然后与MATLAB的轨迹规划算法进行联合仿真和验证开展了学生线上实验教学和探索,可替补实验室的现场实验仿真实验系统可以进行机器人的运动学、动力学和轨迹规划算法的仿真实验,能够提高学生的机器人理论分析和设计能力关键词:机器人;V-R E P;运动学;动力学;轨迹规划中图分类号:TP242 文献标识码:A 文章编号:1002-4956(2021)03-0132-04Robotic simulation experiment system based on V-REP and teachingGE Lianzheng,ZHAO Lijun(State Key Laboratory of Robotics and System (HIT), Harbin Institute of Technology, Harbin 150001, China)Abstract: Robot design needs to adopt the process of “design, simulation and optimization”,so simulation technology is also a skill that must be mastered by undergraduates majoring in robot engineering. This paper designs a 6-DOF general industrial robot simulation experiment system based on V-REP simulation software.Firstly, the V-REP model of the robot is established, and the system dynamic parameters are set. Then, the joint simulations and verifications are carried out using the trajectory planning algorithm of MATLAB. Online experiment teaching and exploration are carried out, which can replace the field experiment in the laboratory. The simulation experiment system can carry out the simulation experiments of robot kinematics, dynamics and trajectory planning algorithm, and can improve students' robot theoretical analysis and design ability.Key words: robot; V-REP; kinematics; dynamics; trajectory planning工业机器人是综合性实验平台,涉及机械、控制 和应用等内容[1]。
211226100_虚拟仿真技术在“现代分析测试技术”实验教学中的应用探索
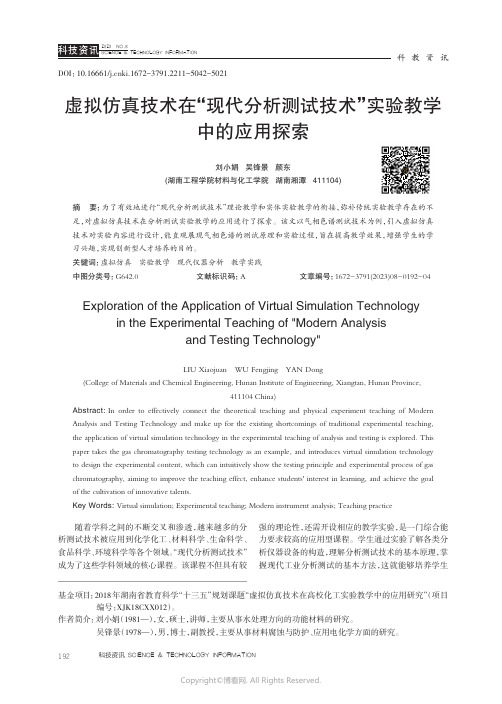
虚拟仿真技术在“现代分析测试技术”实验教学中的应用探索刘小娟 吴锋景 颜东(湖南工程学院材料与化工学院 湖南湘潭 411104)摘要: 为了有效地进行“现代分析测试技术”理论教学和实体实验教学的衔接,弥补传统实验教学存在的不足,对虚拟仿真技术在分析测试实验教学的应用进行了探索。
该文以气相色谱测试技术为例,引入虚拟仿真技术对实验内容进行设计,能直观展现气相色谱的测试原理和实验过程,旨在提高教学效果,增强学生的学习兴趣,实现创新型人才培养的目的。
关键词: 虚拟仿真 实验教学 现代仪器分析 教学实践中图分类号: G642.0文献标识码: A文章编号: 1672-3791(2023)08-0192-04Exploration of the Application of Virtual Simulation Technologyin the Experimental Teaching of "Modern Analysisand Testing Technology"LIU Xiaojuan WU Fengjing YAN Dong(College of Materials and Chemical Engineering, Hunan Institute of Engineering, Xiangtan, Hunan Province,411104 China)Abstract: In order to effectively connect the theoretical teaching and physical experiment teaching of Modern Analysis and Testing Technology and make up for the existing shortcomings of traditional experimental teaching, the application of virtual simulation technology in the experimental teaching of analysis and testing is explored. This paper takes the gas chromatography testing technology as an example, and introduces virtual simulation technology to design the experimental content, which can intuitively show the testing principle and experimental process of gas chromatography, aiming to improve the teaching effect, enhance students' interest in learning, and achieve the goal of the cultivation of innovative talents.Key Words: Virtual simulation; Experimental teaching; Modern instrument analysis; Teaching practice随着学科之间的不断交叉和渗透,越来越多的分析测试技术被应用到化学化工、材料科学、生命科学、食品科学、环境科学等各个领域。
simulation modelling practice and theory sci
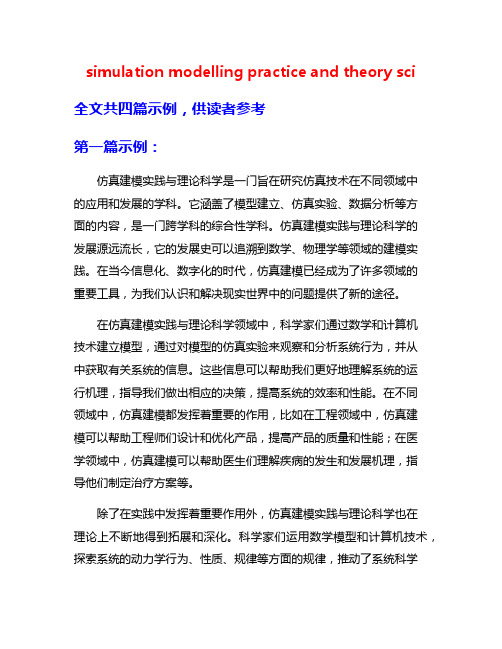
simulation modelling practice and theory sci全文共四篇示例,供读者参考第一篇示例:仿真建模实践与理论科学是一门旨在研究仿真技术在不同领域中的应用和发展的学科。
它涵盖了模型建立、仿真实验、数据分析等方面的内容,是一门跨学科的综合性学科。
仿真建模实践与理论科学的发展源远流长,它的发展史可以追溯到数学、物理学等领域的建模实践。
在当今信息化、数字化的时代,仿真建模已经成为了许多领域的重要工具,为我们认识和解决现实世界中的问题提供了新的途径。
在仿真建模实践与理论科学领域中,科学家们通过数学和计算机技术建立模型,通过对模型的仿真实验来观察和分析系统行为,并从中获取有关系统的信息。
这些信息可以帮助我们更好地理解系统的运行机理,指导我们做出相应的决策,提高系统的效率和性能。
在不同领域中,仿真建模都发挥着重要的作用,比如在工程领域中,仿真建模可以帮助工程师们设计和优化产品,提高产品的质量和性能;在医学领域中,仿真建模可以帮助医生们理解疾病的发生和发展机理,指导他们制定治疗方案等。
除了在实践中发挥着重要作用外,仿真建模实践与理论科学也在理论上不断地得到拓展和深化。
科学家们运用数学模型和计算机技术,探索系统的动力学行为、性质、规律等方面的规律,推动了系统科学和计算科学的发展。
仿真建模的理论也逐渐由简单的数学模型扩展到了包括多尺度、多模态、多组分等多种因素的复杂系统建模,使仿真建模更加贴近实际问题,更具有针对性和预见性。
在仿真建模实践与理论科学的研究中,还存在着一些困难和挑战。
复杂系统的建模和仿真需要大量的计算资源和数据支持,这对仿真建模的算法和技术提出了更高的要求;仿真建模需要在实际系统的基础上建立模型,并进行验证和验证,这对科学家们的理论功底和经验积累提出了更高的要求;不同领域之间的交叉和融合也需要科学家们具备跨学科的知识和思维能力,这为仿真建模的发展带来了更多的机遇和挑战。
具有间断解的PTT型黏弹性流体热对流数值模拟

第 62 卷第 5 期2023 年9 月Vol.62 No.5Sept.2023中山大学学报(自然科学版)(中英文)ACTA SCIENTIARUM NATURALIUM UNIVERSITATIS SUNYATSENI具有间断解的PTT型黏弹性流体热对流数值模拟*张栏1,蒋子超1,陈玉惠1,张仪2,杨耿超1,姚清河11. 中山大学航空航天学院,广东深圳 5181072. Robotics and Mechatronics, University of Twente, Enschede 7522 NB, the Netherlands摘要:从间断解充分发展的黏弹性流体Rayleigh-Bénard(RB)热对流具备不同流态的时间信息和发展过程的流态变换,研究该问题对阐明Phan-Thien-Tanner(PTT)型黏弹性流体RB热对流的流动机理具有重要意义。
本文首次采用二阶迎风型总变差不增差分格式对PTT型黏弹性流体的RB热对流进行了数值模拟,并基于与解析解的对比论证了该数值方法在空间离散上的收敛性与二阶精度。
数值结果表明,本文的数值方法可模拟自间断初始场演化的PTT型黏弹性流体RB热对流,此外,本文还对该流动发展到稳态周期解的瞬态流动现象作了基本阐释,流动现象与从先验速度场发展的流动现象一致。
关键词:间断解;总变差不增格式;黏弹性流体;Phan-Thien-Tanner模型;Rayleigh-Bénard对流中图分类号:O373 文献标志码:A 文章编号:2097 - 0137(2023)05 - 0136 - 09Numerical simulation of thermal convection ofPTT viscoelastic fluid with discontinuous solutionZHANG Lan1, JIANG Zichao1, CHEN Yuhui1, ZHANG Yi2, YANG Gengchao1, YAO Qinghe11. School of Aeronautics and Astronautics,Sun Yat-sen University,Shenzhen 518107,China2. Robotics and Mechatronics, University of Twente, Enschede 7522 NB, the NetherlandsAbstract:The study of the time information and transitional behavior of flow states in the develop‐ment of intermittent solutions in Rayleigh-Bénard (RB) convection of viscoelastic fluids has great sig‐nificance in understanding the flow mechanics of Phan-Thien-Tanner (PTT) viscoelastic fluid RB con‐vection. In this paper,we first use a second-order upwind-type total variation diminishing (TVD)scheme to numerically simulate PTT viscoelastic fluid RB convection,and demonstrate the conver‐gence and second-order accuracy of the numerical method in spatial discretization based on the compar‐ison between the numerical and analytical solutions. The numerical results indicate that the numerical method employed in this paper can simulate the evolution of PTT viscoelastic fluid RB thermal convec‐tion with discontinuity initial field, and provide a fundamental explanation for the transient flow phe‐nomena of this flow up to the development of steady periodic solutions, which are consistent with the flow phenomena developed from the a priori velocity field.Key words:discontinuous solution;total variation diminishing scheme;viscoelastic fluid;Phan-Thien-Tanner model; Rayleigh-Bénard convectionDOI:10.13471/ki.acta.snus.2023D008*收稿日期:2023 − 02 − 22 录用日期:2023 − 03 − 28 网络首发日期:2023 − 06 − 19基金项目:国家重点研发计划(2018YFE9103900);国家自然科学基金(11972384);广东省基础与应用基础研究基金(2021B1515310001,2022B1515120009)作者简介:张栏(1998年生),男;研究方向:计算流体力学;E-mail:*********************通信作者:姚清河(1980年生),男;研究方向:计算流体力学、大规模并行算法;E-mail:****************第 5 期张栏,等:具有间断解的PTT型黏弹性流体热对流数值模拟热对流是由温度差驱动的流体运动,是自然界中普遍而重要的现象,广泛存在于海洋、大气、地核以及恒星和行星的内部。
地球科学研究免费英文简历模板
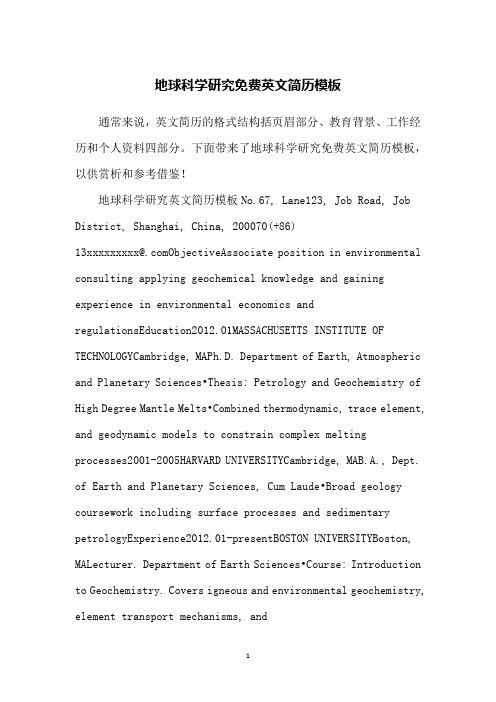
地球科学研究免费英文简历模板通常来说,英文简历的格式结构括页眉部分、教育背景、工作经历和个人资料四部分。
下面带来了地球科学研究免费英文简历模板,以供赏析和参考借鉴!地球科学研究英文简历模板No.67, Lane123, Job Road, Job District, Shanghai, China, 200070(+86)13xxxxxxxxx@.comObjectiveAssociate position in environmental consulting applying geochemical knowledge and gaining experience in environmental economics and regulationsEducation2012.01MASSACHUSETTS INSTITUTE OF TECHNOLOGYCambridge, MAPh.D. Department of Earth, Atmospheric and Planetary Sciences•Thesis: Petrology and Geochemistry of High Degree Mantle Melts•Combined thermodynamic, trace element, and geodynamic models to constrain complex meltingprocesses2001-2005HARVARD UNIVERSITYCambridge, MAB.A., Dept. of Earth and Planetary Sciences, Cum Laude•Broad geology coursework including surface processes and sedimentary petrologyExperience2012.01-presentBOSTON UNIVERSITYBoston, MALecturer. Department of Earth Sciences•Course: Introduction to Geochemistry. Covers igneous and environmental geochemistry, element transport mechanisms, andkinetics2012.01-presentMASSACHUSETTS INSTITUTE OF TECHNOLOGYCambridge, MAPostdoctoraL researcher. Dept. of Earth, Atmospheric and Planetary Sciences•Estimating pressure and temperature conditions beneath the Aleutian Islands using combination of experimental observations and thermodynamic modeling2005-2012MASSACHUSETTS INSTITUTE OF TECHNOLOGYCambridge, MAResearch assistant.Dept. of Earth, Atmospheric and Planetary Sciences•Constructed thermodynamic computer code (MatLab) to predict the distribution of major elements in solid and fluid phases during melting of the interior of the Earth•Modeled trace element distribution in geologic samples•Constructed geophysical model of mantle convection using existing finite-element code•Developed experimental and analytical techniques to provide data for models•Taught lab section of courses in Mineralogy and in Igneous and Metamorphic Petrology•Mentored 5 undergraduate research projects in geochemistry2004-2005HARVARD UNIVERSITYCambridge, MAUndergraduate researcher. Dept. of Earth and Planetary Sciences•Constructed compositional model of the Earth’s deep interior by comparing theoretical seismic velocity of experimental charges with observed seismic velocities•Performed and analyzed ultra-high pressureexperimentsSkillsComputer: MatLab, some HTML and VBA, convection modeling using pre-existing finite element code, PC and Mac spreadsheet, text, and drawing programs (Illustrator, Canvas,...)Analytical: Electron microprobe, ion microprobe, XRF, ICP-MSAwards/ActivitiesNational Merit Scholarship (2001-2005), Best Senior Thesis - Harvard Geology Club (2005)Officer - Harvard Geology Club (2004-2005), Chairman of Board - Agassiz Cooperative Preschool (2008-2009), ultimate, basketball, hiking, gardening, readingPublications2 first author (refereed), 1 co-author (refereed), 8 conference presentations, and 5 co-author on presentation abstract. A detailed list of publications is available upon request 英文简历格式和样式Résumé Formats and StylesRésumés can be formatted at one of the three ways: reverse chronological, skills based or hybrid, a combination of the other two.简历可以按照以下三种样式来排版:时间倒序型,技能型或混合性。
simulation modeling practice and theory
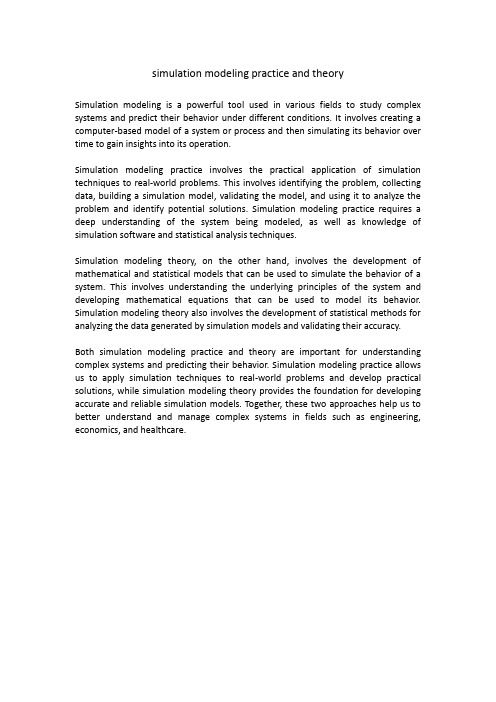
simulation modeling practice and theorySimulation modeling is a powerful tool used in various fields to study complex systems and predict their behavior under different conditions. It involves creating a computer-based model of a system or process and then simulating its behavior over time to gain insights into its operation.Simulation modeling practice involves the practical application of simulation techniques to real-world problems. This involves identifying the problem, collecting data, building a simulation model, validating the model, and using it to analyze the problem and identify potential solutions. Simulation modeling practice requires a deep understanding of the system being modeled, as well as knowledge of simulation software and statistical analysis techniques.Simulation modeling theory, on the other hand, involves the development of mathematical and statistical models that can be used to simulate the behavior of a system. This involves understanding the underlying principles of the system and developing mathematical equations that can be used to model its behavior. Simulation modeling theory also involves the development of statistical methods for analyzing the data generated by simulation models and validating their accuracy. Both simulation modeling practice and theory are important for understanding complex systems and predicting their behavior. Simulation modeling practice allows us to apply simulation techniques to real-world problems and develop practical solutions, while simulation modeling theory provides the foundation for developing accurate and reliable simulation models. Together, these two approaches help us to better understand and manage complex systems in fields such as engineering, economics, and healthcare.。
Experimental investigation and numerical simulation for weakening the thermal fluctuations Tjunction
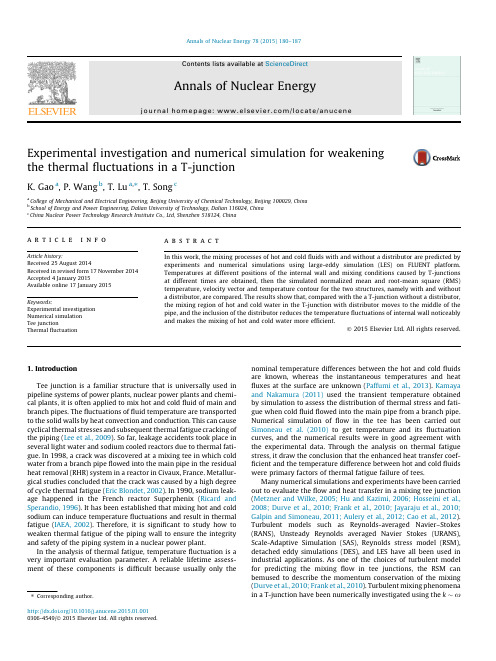
Experimental investigation and numerical simulation for weakening the thermal fluctuations in aT-junctionK.Gao a ,P.Wang b ,T.Lu a ,⇑,T.Song caCollege of Mechanical and Electrical Engineering,Beijing University of Chemical Technology,Beijing 100029,China bSchool of Energy and Power Engineering,Dalian University of Technology,Dalian 116024,China cChina Nuclear Power Technology Research Institute Co.,Ltd,Shenzhen 518124,Chinaa r t i c l e i n f o Article history:Received 25August 2014Received in revised form 17November 2014Accepted 4January 2015Available online 17January 2015Keywords:Experimental investigation Numerical simulation Tee junctionThermal fluctuationa b s t r a c tIn this work,the mixing processes of hot and cold fluids with and without a distributor are predicted by experiments and numerical simulations using large-eddy simulation (LES)on FLUENT platform.Temperatures at different positions of the internal wall and mixing conditions caused by T-junctions at different times are obtained,then the simulated normalized mean and root-mean square (RMS)temperature,velocity vector and temperature contour for the two structures,namely with and without a distributor,are compared.The results show that,compared with the a T-junction without a distributor,the mixing region of hot and cold water in the T-junction with distributor moves to the middle of the pipe,and the inclusion of the distributor reduces the temperature fluctuations of internal wall noticeably and makes the mixing of hot and cold water more efficient.Ó2015Elsevier Ltd.All rights reserved.1.IntroductionTee junction is a familiar structure that is universally used in pipeline systems of power plants,nuclear power plants and chemi-cal plants,it is often applied to mix hot and cold fluid of main and branch pipes.The fluctuations of fluid temperature are transported to the solid walls by heat convection and conduction.This can cause cyclical thermal stresses and subsequent thermal fatigue cracking of the piping (Lee et al.,2009).So far,leakage accidents took place in several light water and sodium cooled reactors due to thermal fati-gue.In 1998,a crack was discovered at a mixing tee in which cold water from a branch pipe flowed into the main pipe in the residual heat removal (RHR)system in a reactor in Civaux,France.Metallur-gical studies concluded that the crack was caused by a high degree of cycle thermal fatigue (Eric Blondet,2002).In 1990,sodium leak-age happened in the French reactor Superphenix (Ricard and Sperandio,1996).It has been established that mixing hot and cold sodium can induce temperature fluctuations and result in thermal fatigue (IAEA,2002).Therefore,it is significant to study how to weaken thermal fatigue of the piping wall to ensure the integrity and safety of the piping system in a nuclear power plant.In the analysis of thermal fatigue,temperature fluctuation is a very important evaluation parameter.A reliable lifetime assess-ment of these components is difficult because usually only thenominal temperature differences between the hot and cold fluids are known,whereas the instantaneous temperatures and heat fluxes at the surface are unknown (Paffumi et al.,2013).Kamaya and Nakamura (2011)used the transient temperature obtained by simulation to assess the distribution of thermal stress and fati-gue when cold fluid flowed into the main pipe from a branch pipe.Numerical simulation of flow in the tee has been carried out Simoneau et al.(2010)to get temperature and its fluctuation curves,and the numerical results were in good agreement with the experimental data.Through the analysis on thermal fatigue stress,it draw the conclusion that the enhanced heat transfer coef-ficient and the temperature difference between hot and cold fluids were primary factors of thermal fatigue failure of tees.Many numerical simulations and experiments have been carried out to evaluate the flow and heat transfer in a mixing tee junction (Metzner and Wilke,2005;Hu and Kazimi,2006;Hosseini et al.,2008;Durve et al.,2010;Frank et al.,2010;Jayaraju et al.,2010;Galpin and Simoneau,2011;Aulery et al.,2012;Cao et al.,2012).Turbulent models such as Reynolds-averaged Navier–Stokes (RANS),Unsteady Reynolds averaged Navier Stokes (URANS),Scale-Adaptive Simulation (SAS),Reynolds stress model (RSM),detached eddy simulations (DES),and LES have all been used in industrial applications.As one of the choices of turbulent model for predicting the mixing flow in tee junctions,the RSM can bemused to describe the momentum conservation of the mixing (Durve et al.,2010;Frank et al.,2010).Turbulent mixing phenomena in a T-junction have been numerically investigated using the k $x/10.1016/j.anucene.2015.01.0010306-4549/Ó2015Elsevier Ltd.All rights reserved.Corresponding author.based baseline Reynolds stress model(BSL RSM)(Frank et al.,2010) for two different cases.Durve et al.(2010)applied the RSM to pre-dict the velocityfield of three non-isothermal parallel jetsflowing in an experiment setup used to simulate theflow occurring at the core outlet region of a fast breeder reactor(FBR),with a Reynolds number of1.5Â104.Theflow in tube of different Reynolds numbers (Re)andflow velocity ratio were studied experimentally with three-dimensional scanning using particle image velocimetry(3D-SPIV) (Brücker,1997).Large-eddy simulation(LES)is an alternative turbulence model with different subgridscale models often employed to predict velocity and temperaturefluctuations.Indeed many numerical studies have shown the capability of LES to model thermalfluctu-ations in turbulent mixing.LES was performed(Lee et al.,2009)to analyze temperaturefluctuation in the tee junction and the simu-lated results were in good agreement with the experimental data. Thermal striping phenomena in the tee junction had been numer-ically investigated using LES(Hu and Kazimi,2006)for two differ-ent mixing cases,and the simulated normalized mean and root-mean square(RMS)was consistent with experimental results. LES in a mixing tee were carried out(Galpin and Simoneau, 2011)in order to evaluate the sensitivity of numerical results to the subgrid scale model by comparing the experimental results, and to investigate the possibility of reducing thefluid computa-tional domain at the inlet.Another simulation that mixing of a hot and a coldfluid stream in a vertical tee junction with an upstream elbow main pipe was carried out with LES(Lu et al., 2013).And the numerical results show that the normalized RMS temperature and velocity decrease with the increases of the elbow curvature ratio and dimensionless distance.In the meantime,many scholars have studied how to weaken the thermalfluctuation.Experiments and simulation were con-ducted(Wu et al.,2003)on a tee junction geometry with a sleeve tube in it.Theflow is divided into three types of jets by theflow velocity ratio in main and branch pipes.Through the analysis of flowfield and velocityfield of various jets types,it indicate that the addition of sleeve tube relieve the thermal shock caused by the coldfluid injection rge-eddy simulation have been used(Lu et al.,2010)to evaluate the thermal striping phe-nomena in tee junctions with periodic porous media,the temper-ature and velocityfield inside the tubes are obtained.The research revealed that the addition of a porous reduces the tem-perature and velocityfluctuations in the mixing tube.As mentioned above,experiments and numerical simulations for both tee junction geometry with a sleeve tube in it(Wu et al., 2003)and for a mixing tee with periodic porous media in it(Lu et al.,2010)have been carried out.The results of previous researches provide a good reference value for this work that anal-yses the role of distributor in weakening the thermalfluctuation of internal piping wall,and this structure has not been studied to date,to the best of our knowledge.In this work,mixing processes have been studied by the experiment and numerically predicted with LES.Then the simulated normalized mean and root-mean square(RMS)temperature,velocity vector and temperature con-tour of the two tees are compared.2.Experiment systemThe Experimentflowchart is presented in Fig.1.The experimen-tal system consists of four main components,a cold water supply line,a hot water supply line,a test section,and a data acquisition unit.The experiment device is shown in Fig.2.Experimentfluid was adjusted to the desired temperature by the heater and chiller, and then was pumped to the test section.After mixing thefluid is returned to the heater for recycling,some of the excessfluid is dis-charged through the overflow pipe.During the mixing of thefluids, the temperature of the mixingfluid is collected and recorded by the thermocouple probe installed on the tube wall.The experiment requires two different structures of the test sec-tion,Fig.3is the T-junction section without the branch liquid dis-tributor and Fig.4is that with the branch liquid distributor.The addition of this structure has two main functions:(1)changing the mixing position of hot and coldfluids:moving the mixing zone to the middle of the tube,and away from the main pipe wall;(2) increasing the intensity of mixing process:adding the fence near the outlet of distributor enhanced the mixed disturbance and the exacerbatedfluid mixing of the inner tube.For the convenience of observing and adjusting the mixing process,the test section is a round pipe made of plexiglass,and other pipes are made of steel. Fig.5is the physical model of the branch liquid distributor.The test conditions in the present experiment are shown in Table1.We collected the instantaneous temperature data of every measurement points by the data collector.The distribution of sam-pling points are shown in Fig.6,there are total eight thermocou-ples in the circumferential direction at each plane.In the T-junction section without the branch liquid distributor,the number of the collected plane is6(x/d m=1,2,3,4,6,8).That is to say there are48thermocouples in the structure without distributor.And in the T-junction section with the branch liquid distributor,the num-ber of the collected plane is5(x/d m=2,3,4,6,8),which means there are40thermocouples in the structure that with the distrib-utor.In both structures,the distance between measuring point the thermocouple probe and the inner wall is30mm.Since the collect-ing frequency of the collector is limited,we use1Hz as the collect-ing frequency after theflowfield is stable,and the total number of collection is800s.Table1shows the specific parameters of the test conditions.NomenclatureT time(s)Pr Prandtl numberLs mixing length of subgrid grid(m)T temperature(K)G acceleration of gravity(m/s2)K von Karman numberCs Smagorinsky numberS ij subgrid strain rate tensorM R momentum ratio of main pipe and branch pipe TÃnormalized mean temperaturesTÃrms normalized RMS temperaturesR d diameter ratioR v velocity ratiox,y,z axial coordinate(m)Greek symbolsqfluid density(kg/m3)b coefficient of thermal expansionl viscosity(Pa s)ltturbulent viscosity(Pa s)k thermal conductivity(w/(m k))C P heat capacity(J/(kg°C))K.Gao et al./Annals of Nuclear Energy78(2015)180–187181182K.Gao et al./Annals of Nuclear Energy78(2015)180–1871\4\11-thermometers 2\5\10-pressure gauge 3\9-flow meter 6-c ooler 7-heater8-overflow 12-test sec tion 13-thermoc ouple data c ollec torFig.1.Experimentflow chart.Fig.5.Physical model of the branch liquid distributor(a)the whole graph(b)theprofile map.Fig.2.Experiment device of thermalfluctuation.Fig.3.Schematic diagram of the T-junction section without the branch liquid distributor.Fig.4.Schematic diagram of the T-junction section with the branch liquid distributor.3.Numerical simulationFig.7is the numerical model based on the experimental section of T junction.The size of the model,boundary conditions are con-sistent with the experiment.In which,hot water enters from the left of main pipe,and cold water enters from the branch pipe,finally the mixingfluidflow out of the right of the main pipe.Dur-ing the calculation,the steady results offlowfield and heat transfer are obtained by Reynolds stress model(RSM)firstly,and then set @q@tþ@q u i@x i¼0ð1Þ@q u i@tþ@q u i u j@x j¼À@ p@x iÀq0bðTÀT0Þgþ@@x jlþltÀÁ@ u i@x jþ@ u j@x i!ð2Þ@q T@tþ@q Tu j@x j¼@@x jkc p@T@x jÀq T00u00j!ð3ÞIn these equations,q,b,l,l t,k and c p represent the density,ther-mal expansion coefficient,molecular viscosity,turbulent viscosity, thermal conductivity and specific heat capacity,respectively.The Smagorinsky–Lilly model is used for the turbulent viscosity,which is described as:lt¼q L2s j S jð4Þj S jTable1Experimental conditions.Main pipe Branch pipeFlow rate (m3/h)Temperature(K)Flow rate(m3/h)Temperature(K)Without distributor0.645304.650.270287.65With distributor0.645304.650.266287.65Fig.6.The distribution of sampling points on the planes.Physical model of T-junction(a)without the branch liquid distributor;(b)with the branch liquid distributor.K.Gao et al./Annals of Nuclear Energy78(2015)180–187183ij ¼12@ u i@x jþ@ u j@x ið7Þwhere k is the Von Karman constant of0.42;d is the distance to the closest wall;C s is the Smagorinsky constant of0.1;V is the volume of the computational cell.4.Results and discussionThe normalized mean and root-mean square temperature are used to describe the time-averaged temperature and temperature fluctuation intensity.The normalized temperature is defined as:ü1NX Ni¼1TÃið8ÞN is the total number of sample times.TÃi¼T iÀT cT hÀT cð9Þwhere T i is the transient temperature,T c is the coldfluid inlet tem-perature and T h is hotfluid inlet temperature.The root-mean square(RMS)of the normalized temperature is defined as:TÃrms¼ffiffiffiffiffiffiffiffiffiffiffiffiffiffiffiffiffiffiffiffiffiffiffiffiffiffiffiffiffiffiffiffiffiffiffiffiffiffiffiffi1X Ni¼1TÃiÀTÃ2rð10Þ184K.Gao et al./Annals of Nuclear Energy78(2015)180–187parison of experimental and numerical resultsAs can be seen from the Fig.8,the numerical normalized mean temperature distributions at the plane x/d m=1and the plane x/ d m=2are in good qualitative agreement and in adequate quantita-tive agreement,and most of them are within the experimental deviation of±20%.Meanwhile,the lifting trends of the data are the same.In the direction of180°,the mean temperatures are both minimal.And with the angle decrease to0°,the temperatures are gradually increased.Quantitative differences between the experi-ment and numerical results are that the normalized mean temper-atures given by LES are larger than the experimental data.That is because we did not add insulation unit on tube wall in the exper-iment,leading the transfer of some heat into the air.And in the process of numerical simulation,we ignored the convective heat transfer between the wall and the air.As shown in Fig.9,although the numerical results and experi-mental results have a little difference at the plane x/dm=2around the location of225°and the plane x/dm=2around the location of 0°and315°,all of them are within the error range that can be accepted.Both the simulations and experimental results give a lar-ger mean temperature in the top half of the main pipe than in the bottom half.This verifies the validity of the LES model for predict-ing the mixing of hot and coldfluids in a tee junction.The normalized RMS temperature on the plane x/d m=1and plane x/d m=2are shown in Fig.10,respectively.Similar to the nor-malized mean temperature,the normalized RMS temperature lines agree very well with the experiment ones.Both of the maximum values appear at the bottom half of the pipe.This indicates that the maximum temperaturefluctuations of main pipe appear on the opposite of the branch pipe inlet in this condition.As shown in Fig.11,the numerical results and the experimental results have the same trend and the numerical data are agreed well with the experimental ones.By comparison with Figs.4and5,dif-ferent from the temperaturefluctuations distribution which with-out the branch liquid distributor,there are two peaks of high fluctuation located at the90°and270°directions along with the tube.This is because the direction is that of the outlet of branch liquid distributor,the coldfluidflowing out from the outlet of branch liquid distributor mixes very fast with the hotfluid,leading to dramatic changes of temperature.In summary,the LES simulation results obtained are generally in good qualitative and quantitative agreement with the experi-mental data for the case of T-junction with/without the branch liquid distributor.Based on this,we analyzed the numerical results further.And the results are reported in the section below.4.2.Numerical results with/without branch liquid distributorThe numerical data were sampled on the inner wall in the plane x/ d m=À1,À0.5,0,0.5,1,2,3,4,6and8.At the same time,the numer-ical data were sampled from points every5mm along the intersec-tional lines of planes of y/d m=0and sections of x/d m=À2,À1,0,1,2, 3,4,5and6,to get the points with the maximum normalized rootK.Gao et al./Annals of Nuclear Energy78(2015)180–187185mean square temperatures in the tee and on the top and bottom walls.Here,the temperature and velocityfields were determined with LES simulations for the case of tee junction with/without branch liquid distributor.The temperature contours and velocity vectors for the T-junction are shown in Figs.12and13,respectively.As can be seen in Fig.12,due to the large branch pipeflow velocity,hot and coldfluid mixing zone is mainly located in both upstream and downstream region of the intersections of the main pipe and the branch pipe.The vigorous mixing offluids in the tube leads to thermalfluctuation on the wall.But in the T-junction with the branch liquid distributor,the mixing region moves to the lower half and downstream region of the main pipe.This indicates that the distributor is advantageous to weaken thermalfluctuations on the wall.The same conclusion can be seen from Fig.13,the dis-tributor weaken thermalfluctuations on the wall of downstream region and the top of the main pipe.186K.Gao et al./Annals of Nuclear Energy78(2015)180–187Fig.14compares the normalized mean temperatures between two tees of different structures.As can be seen,wall temperature changes great in the direction of90°,135°,225°and270°in T-junc-tion with the distributor,because the directions are the distributor outlet directions.This indicates that the coldfluid mixes with hot fluid on the wall afterflows out of the distributor.At the same time,the temperature in the direction of180°also changes dra-matically.That is because the coldfluid moves down in the effects of gravity and buoyancy.As shown in Fig.15,for the tee with distributor,the maximum values of normalized RMS temperature are smaller than that of the tee without distributor in most directions.This indicates that the adding of the distributor can relieve thermalfluctuations on the wall to some extent.And for the T-junction with distributor,tem-perature tends to be stable after the plane of x/d m=6,which indi-cates that twofluids have made a full mixing,while for the initial tee,temperature is still in the dramatic change,and this shows that the improved structure can effectively reduce the mixing length.Fig.16shows the maximum normalized instantaneous temper-aturefluctuations in the tee and on the top and bottom walls in the plane y/d m=0.In the tee,the maximum normalized instantaneous temperaturefluctuations of the case without distributor vary from 0.45to0.8,which means that the hot and coldfluids alternate in this location.However,for the case with distributor,the tempera-turefluctuations in the tee as well as on the top and bottom walls are much smaller than those of the case without distributor.That also implies that the distributor can reduce the temperaturefluctu-ation effectively.The normalized instantaneous temperaturefluctuations cannot describe the relationship between power spectrum density(PSD) and frequency of the temperaturefluctuation.PSD against fre-quency is one of the most important parameter for thermal fatigue analysis,which can directly show how PSD is in a certain fre-quency.The PSDs of the points with maximum temperaturefluctu-ation for the cases with and without distributor against frequency were recorded by fast Fourier transform(FFT)and shown in Fig.17. The temperaturefluctuation of the case without distributor has the highest PSD,at the frequency of0.04Hz,whereas the distributor significantly reduces the PSD of the temperaturefluctuations with the frequency from0.01to0.1Hz.In addition,the PSD of temper-aturefluctuations decreases with the frequency increasing.5.ConclusionsAs thermal stratification can result in thermal fatigue in the pip-ing system of a nuclear power plant,safety and integrity evaluation of the piping system has become an important issue.In this work the temperaturefluctuation has been studied by the experiment and numerically predicted by LES for two types of vertical tee junc-tion:one with distributor in the branch pipe and another without. The numerical results of normalized mean and RMS temperatures for the two structures have been found to be in good qualitative and quantitative agreement with the experimental data,which val-idates the use of LES simulations to evaluate convective mixing in such geometries.At the same time,the simulated normalized mean and root-mean square(RMS)temperature,velocity vector and temperature contour of the two tees are compared.The numerical results show that thefluctuations of temperatures of the tee without the distrib-utor are larger than those of the tee with the distributor,which can be explained by the branch liquid distributor enhancing the mix-ing.Although both tees give the same momentum ratio between the main pipeflow and the branch pipeflow,mixing and convec-tive heat transfer are greatly enhanced by the presence of the branch liquid distributor.These all show that the structure is effec-tive for weakening the thermalfluctuation of tee piping wall when hot and coldfluids mix,and it can make the mixing more sufficient.AcknowledgementsThis work was supported by projects of the National Natural Science Foundation of China(No.51276009),Program for New Century Excellent Talents in University(No.NCET-13-0651),and the National Basic Research Program of China(No.2011CB706900). ReferencesAulery, F.,Toutant, A.,Monod,R.,Brillant,G.,Bataille, F.,2012.Numerical simulations of sodium mixing in a T-junction.Appl.Therm.Eng.37,38–43.Brücker,C.,1997.Study of the three-dimensionalflow in a T-junction using a dual-scanning method for three-dimensional scanning-particle-image velocimetry (3-D SPIV).Exp.Therm.Fluid Sci.14,35–44.Cao,Q.,Lu,D.,Lv,J.,2012.Numerical investigation on temperaturefluctuation of the parallel triple-jet.Nucl.Eng.Des.249,82–89.Durve,A.,Patwardhan,A.W.,Banarjee,I.,Padmakumar,G.,Vaidyanathan,G.,2010.Thermal striping in triple jetflow.Nucl.Eng.Des.240,3421–3434.Eric Blondet, C.F.,2002.High cycle thermal fatigue in french PWR.In:10th International Conference on Nuclear Engineering.Arlington,Virginia,USA,pp.429–436.Frank,T.,Lifante,C.,Prasser,H.M.,Menter,F.,2010.Simulation of turbulent and thermal mixing in T-junctions using URANS and scale-resolving turbulence models in ANSYS CFX.Nucl.Eng.Des.240,2313–2328.Galpin,J.,Simoneau,J.P.,rge Eddy Simulation of a thermal mixing tee in order to assess the thermal fatigue.Int.J.Heat Fluid Flow32,539–545. Hosseini,S.M.,Yuki,K.,Hashizume,H.,2008.Classification of turbulent jets in a T-junction area with a90-deg bend upstream.Int.J.Heat Mass Transfer51,2444–2454.Hu,L.-W.,Kazimi,M.S.,2006.LES benchmark study of high cycle temperature fluctuations caused by thermal striping in a mixing tee.Int.J.Heat Fluid Flow 27,54–64.IAEA,2002.Validation of Fast Reactor Thermomechanical and Thermohydraulic Codes,Vienna.Jayaraju,S.T.,Komen,E.M.J.,Baglietto,E.,2010.Suitability of wall-functions in Large Eddy Simulation for thermal fatigue in a T-junction.Nucl.Eng.Des.240,2544–2554.Kamaya,M.,Nakamura, A.,2011.Thermal stress analysis for fatigue damage evaluation at a mixing tee.Nucl.Eng.Des.241,2674–2687.Lee,J.I.,Hu,L.-W.,Saha,P.,Kazimi,M.S.,2009.Numerical analysis of thermal striping induced high cycle thermal fatigue in a mixing tee.Nucl.Eng.Des.239, 833–839.Lu,T.,Jiang,P.X.,Guo,Z.J.,Zhang,Y.W.,Li,H.,rge-eddy simulations(LES)of temperaturefluctuations in a mixing tee with/without a porous medium.Int.J.Heat Mass Transfer53,4458–4466.Lu,T.,Liu,S.M.,Attinger,D.,rge-eddy simulations of structure effects of an upstream elbow main pipe on hot and coldfluids mixing in a vertical tee junction.Ann.Nucl.Energy60,420–431.Metzner,K.J.,Wilke,U.,2005.European THERFAT project—thermal fatigue evaluation of piping system‘‘Tee’’-connections.Nucl.Eng.Des.235,473–484. Paffumi, E.,Radu,V.,Nilsson,K.F.,2013.Thermal fatigue striping damage assessment from simple screening criterion to spectrum loading approach.Int.J.Fatigue53,92–104.Ricard,J.B.,Sperandio,M.,1996.Fracture mechanics applied to superphenix reactor components.Int.J.Pressure Vessels Piping65,295–301.Simoneau,J.-P.,Champigny,J.,Gelineau,O.,2010.Applications of large eddy simulations in nuclearfield.Nucl.Eng.Des.240,429–439.Wu,H.L.,Peng,X.F.,Chen,T.K.,2003.Influence of sleeve tube on theflow and heat transfer behavior at a T-junction.Int.J.Heat Mass Transfer46,2637–2644.K.Gao et al./Annals of Nuclear Energy78(2015)180–187187。
VDI 3633

VEREIN DEUTSCHER INGENIEURESimulation von Logistik-, Materialfluss-und ProduktionssystemenMaschinennahe SimulationSimulation of systems in materials handling,logistics and productionMachine-oriented simulationVDI 3633Blatt 8 / Part 8Ausg. deutsch/englisch Issue German/EnglishVDI-Gesellschaft Fördertechnik Materialfluss LogistikFachbereich Modellierung und Simulation Fachausschuss Maschinennahe SimulationVDI-Handbuch Materialfluss und Fördertechnik, Band 8: Materialfluss II (Organisation/Steuerung)VDI-Handbuch Betriebstechnik, Teil 1: Grundlagen und PlanungVDI-RICHTLINIENZ u b e z i e h e n d u r c h / A v a i l a b l e a t B e u t h V e r l a g G m b H , 10772 B e r l i n – A l l e R e c h t e v o r b e h a l t e n / A l l r i g h t s r e s e r v e d © V e r e i n D e u t s c h e r I n g e n i e u r e e .V ., D üs s e l d o r f 2007V e r v i e l f äl t i g u n g – a u c h f ür i n n e r b e t r i e b l i c h e Z w e c k e – n i c h t g e s t a t t e t / R e p r o d u c t i o n – e v e n f o r i n t e r n a l u s e – n o t p e r m i t t e dICS 03.100.10April 2007F r üh e r e A u s g a b e : 01.05 E n t w u r f , d e u t s c h F o r m e r e d i t i o n : 01/05 D r a f t , i nG e r m a n o n l yDie deutsche Version dieser Richtlinie ist verbindlich.The German version of this guideline shall be taken as authorita-tive. No guarantee can be given with respect to the English trans-lation.InhaltSeiteV orbemerkung. . . . . . . . . . . . . . . . . . . 3Einleitung . . . . . . . . . . . . . . . . . . . . . 31Anwendungsbereich . . . . . . . . . . . . . 41.1Anwendungsfelder. . . . . . . . . . . . 41.2Abgrenzung Realität – Simulation. . . . 52Begriffe und Definitionen . . . . . . . . . . . 63Nutzungsmöglichkeiten und typische Frage-stellungen . . . . . . . . . . . . . . . . . . . 93.1Entwicklung/Konstruktion. . . . . . . . 93.2Planung von Fertigungszellen . . . . . . 103.3Inbetriebnahme . . . . . . . . . . . . . 103.4Betrieb . . . . . . . . . . . . . . . . . . 113.5Vertrieb . . . . . . . . . . . . . . . . . 114Modellbildung für die maschinennaheSimulation . . . . . . . . . . . . . . . . . . . 114.1Validierung von Simulationsmodellen . 124.2Weiterverwendung von Simulations-modellen . . . . . . . . . . . . . . . . . 125Grundsatzentscheidung zum Simulations-einsatz . . . . . . . . . . . . . . . . . . . . . 1363-D-Kinematiksimulation . . . . . . . . . . . 146.1Komponenten der Simulationssysteme . . 156.2Vorbereitung der Simulation . . . . . . 206.3Validierung des Modells undKalibrierung des Robotersystems . . . . 226.4Durchführung und Auswertung vonSimulationsexperimenten . . . . . . . . 256.5Aufwand und Nutzen . . . . . . . . . . 266.6Beispiel . . . . . . . . . . . . . . . . . 27ContentsPagePreliminary note . . . . . . . . . . . . . . . . . . 3Introduction . . . . . . . . . . . . . . . . . . . . 31Scope of application . . . . . . . . . . . . . . 41.1Application fields. . . . . . . . . . . . . 41.2Delineation between reality andsimulation. . . . . . . . . . . . . . . . . 52Terms and definitions . . . . . . . . . . . . . 63Possible applications and typical problems . 93.1Development/design . . . . . . . . . . . 93.2Planning of production cells . . . . . . 103.3Start-up . . . . . . . . . . . . . . . . . 103.4Operation. . . . . . . . . . . . . . . . 113.5Sales . . . . . . . . . . . . . . . . . . 114Modelling for machine-oriented simulation 114.1Validation of simulation models . . . . 124.2Reuse of simulation models . . . . . . 125Basic decision for the use of simulation . . 1363D kinematic simulation . . . . . . . . . . . 146.1Components of the simulation systems. . 156.2Preparation of the simulation. . . . . . 206.3Validation of the model and calibrationof the robot system . . . . . . . . . . . 226.4Execution and evaluation of simulationexperiments. . . . . . . . . . . . . . . 256.5Costs and benefits . . . . . . . . . . . 266.6Example . . . . . . . . . . . . . . . . 27All rights reserved © Verein Deutscher Ingenieure e.V., Düsseldorf 2007–2–VDI 3633 Blatt 8 / Part 87Mehrkörpersimulation . . . . . . . . . . . . 317.1Komponenten der Simulatoren . . . . . 327.2Vorbereitung der Simulation . . . . . . 327.3Berechnungsmöglichkeiten . . . . . . . 377.4Auswertung der Simulations-experimente . . . . . . . . . . . . . . . 397.5Aufwand und Nutzen . . . . . . . . . . 397.6Beispiel . . . . . . . . . . . . . . . . . 40 8Simulation zum Funktionstest vonSteuerungen . . . . . . . . . . . . . . . . . 448.1Komponenten von Simulatoren. . . . . 458.2Vorbereitung der Modellierung undSimulation. . . . . . . . . . . . . . . . 488.3Durchführung der Simulations-experimente . . . . . . . . . . . . . . . 518.4Auswertung der Simulations-experimente . . . . . . . . . . . . . . . 528.5Aufwand und Nutzen . . . . . . . . . . 538.6Beispiel . . . . . . . . . . . . . . . . . 53 9Prozesssimulation . . . . . . . . . . . . . . 599.1Komponenten der Simulatoren . . . . . 609.2Vorbereitung der Simulation undModellierung . . . . . . . . . . . . . . 659.3Durchführung der Simulations-experimente . . . . . . . . . . . . . . . 699.4Auswertung der Simulations-experimente . . . . . . . . . . . . . . . 709.5Verbesserung der Simulations-genauigkeit . . . . . . . . . . . . . . . 719.6Weiterverwendung von Simulationsdaten,Kopplung von Simulationssystemen . . 729.7Aufwand und Nutzen . . . . . . . . . . 729.8Beispiele und Anwendungen . . . . . . 73 10Maschinennahe Materialflusssimulation . . 7810.1Komponenten der Simulatoren . . . . . 8010.2Weiterverwendung von Simulations-daten, Kopplung von Simulations-systemen. . . . . . . . . . . . . . . . . 8210.3Vorbereitung der Simulation . . . . . . 8310.4Durchführung und Auswertung vonSimulationsexperimenten . . . . . . . . 8510.5Beispiele. . . . . . . . . . . . . . . . . 86 Schrifttum. . . . . . . . . . . . . . . . . . . . . 907Multibody simulation . . . . . . . . . . . . . 317.1Components of the simulators . . . . . . 327.2Preparation of the simulation . . . . . . 327.3Calculation options . . . . . . . . . . . 377.4Evaluation of the simulationexperiments . . . . . . . . . . . . . . . 397.5Costs and benefits . . . . . . . . . . . . 397.6Example . . . . . . . . . . . . . . . . . 40 8Simulation for the function testing ofcontrollers. . . . . . . . . . . . . . . . . . . 448.1Components of simulators. . . . . . . . 458.2Preparation of modelling andsimulation . . . . . . . . . . . . . . . . 488.3Execution of the simulationexperiments . . . . . . . . . . . . . . . 518.4Evaluation of the simulationexperiments . . . . . . . . . . . . . . . 528.5Costs and benefits . . . . . . . . . . . . 538.6Example . . . . . . . . . . . . . . . . . 53 9Process simulation . . . . . . . . . . . . . . 599.1Components of the simulators . . . . . . 609.2Preparation of the simulation andmodelling . . . . . . . . . . . . . . . . 659.3Execution of the simulationexperiments . . . . . . . . . . . . . . . 699.4Evaluation of the simulationexperiments . . . . . . . . . . . . . . . 709.5Improvement of the simulationaccuracy . . . . . . . . . . . . . . . . . 719.6Further use of simulation data,coupling of simulation systems . . . . . 729.7Costs and benefits . . . . . . . . . . . . 729.8Examples and applications. . . . . . . . 73 10Machine-oriented material flow simulation .7810.1Components of the simulators . . . . . . 8010.2Reuse of simulation data, linking ofsimulation systems. . . . . . . . . . . . 8210.3Preparation of the simulation . . . . . . 8310.4Execution and evaluation of simulationexperiments . . . . . . . . . . . . . . . 8510.5Examples. . . . . . . . . . . . . . . . . 86 Bibliography. . . . . . . . . . . . . . . . . . . . 90Alle Rechte vorbehalten © Verein Deutscher Ingenieure e.V., Düsseldorf 2007VDI 3633 Blatt 8 / Part 8–3–VorbemerkungDer Inhalt dieser Richtlinie ist entstanden unter sorg-fältiger Berücksichtigung der V orgaben und Empfeh-lungen der Richtlinie VDI1000.Allen, die ehrenamtlich an der Erstellung dieser Richtlinie mitgewirkt haben, sei auf diesem Wege ge-dankt.Alle Rechte vorbehalten, auch das des Nachdrucks, der Wiedergabe (Fotokopie, Mikrokopie), der Spei-cherung in Datenverarbeitungsanlagen und der Über-setzung, auszugsweise oder vollständig. Die Nutzung dieser VDI-Richtlinie als konkrete Arbeitsunterlage ist unter Wahrung des Urheberrechtes und unter Be-achtung der VDI-Merkblätter1 bis 7 möglich. Aus-künfte dazu, sowie zur Nutzung im Wege der Daten-verarbeitung, erteilt die Abteilung VDI-Richtlinien im VDI.EinleitungDiese Richtlinie wendet sich an Anwender (Kon-strukteure, Entwickler, Planer, Betreiber, Vertriebs-mitarbeiter) von Simulationstechniken im maschi-nennahen Bereich. Im Rahmen dieser Richtlinie wird unter maschinennaher Simulation die Simulation von Fertigungsmaschinen und ihrer Peripherie verstan-den. Dies schließt den in der Maschine ablaufenden Fertigungsprozess mit ein. Die Umgebungsbedin-gungen und der maschinennahe Materialfluss werden berücksichtigt, soweit sie Rückwirkungen auf die Maschine oder den Fertigungsprozess haben. Soweit nicht anders angegeben, gelten die in VDI3633 Blatt1 getroffenen Festlegungen.Diese Richtlinie beschreibt die Simulationstechnolo-gien, die die Betrachtung der folgenden, beispielhaf-ten Fragestellungen unterstützen:•Gestaltung des Fertigungsprozesses •Auslegung/Berechnung der Fertigungsmaschine •Entwurf und Test von Steuerungen•Planung von Fertigungszellen •Bahnplanung/Kollisionsvermeidung •Automatische Ableitung von Steuerungssoftware Als Hilfsmittel dienen die im Folgenden näher be-schriebenen Simulationstechnologien (siehe Bild1): •3-D-Kinematiksimulation•Mehrkörpersimulation•Simulation zum Funktionstest von Steuerungen •Prozesssimulation•Maschinennahe Materialflusssimulation Preliminary noteThe content of this guideline has been developed un-der thorough consideration of the requirements and recommendations of guideline VDI1000.We wish to express our gratitude to all honorary con-tributors to this guideline.All rights reserved including those of reprinting, re-production (photocopying, microcopying), storage in data processing systems, and translation, either of the full text or of extracts. This VDI guideline can be used as a concrete project document without infringe-ment of copyright and with regard to VDI Notices1 to 7. Information on this, as well as on the use in data processing, may be obtained by the VDI Guidelines Department at the VDI.IntroductionThis guideline is aimed at users (designers, develop-ers, planners, operators, sales personnel) of simula-tion techniques in the machine-oriented sector. Within the framework of this guideline machine-ori-ented simulation refers to the simulation of produc-tion machines and their peripherals. This also in-cludes the production process running in the machine. The environmental conditions and the ma-chine-oriented material flow are taken into consider-ation insofar as they have any impact on the machine or the production process.Unless stated otherwise the provisions of VDI3633, Sheet1 shall apply.This guideline describes the simulation technologies which support the observation of the following tasks taken here as an example:•design of the production process•design/development of the production machine •design and testing of controllers•planning of production cells•path planning/avoidance of collisions •automatic derivation of control softwareThe simulation technologies described in more detail in the following serve as an aid (see Figure1): •3D kinematic simulation•multibody simulation•simulation for the function test of controllers •process simulation•machine-oriented material flow simulationAll rights reserved © Verein Deutscher Ingenieure e.V ., Düsseldorf 2007–4–VDI 3633 Blatt 8 / Part 8Darüber hinaus ist zu beachten, dass der Datenaus-tausch und die Durchgängigkeit zwischen einzelnen Simulationsarten an Bedeutung gewinnen. Andere Simulationsarten, die angrenzend auch im maschinennahen Bereich eingesetzt werden, werden in dieser Richtlinie nicht behandelt, da sie eigenstän-dige Gebiete darstellen:•Simulation in der Elektrotechnik •Simulation in der Materialforschung •Mensch-/Ergonomiesimulation1AnwendungsbereichDie Richtlinie bietet einen Überblick über die An-wendungsbereiche und den Nutzen von Simulati-onstechniken, die im Lebenszyklus einer Maschine eingesetzt werden können. Der Benutzer erhält Hin-weise zur einfachen Auswahl geeigneter Simulati-onsansätze für seine Problemstellung. Die Richtlinie zeigt Anforderungen für den Simulationseinsatz auf,beschreibt die Anwendung und gibt Anleitungen für den erfolgreichen Einsatz. Das Verständnis der Simu-lationsanwender für angrenzende Bereiche und auf-tretende Wechselwirkungen soll vertieft werden. V on besonderem Interesse ist die Kombination unter-schiedlicher Simulationsansätze. Hier werden Mög-lichkeiten zu Integration und Durchgängigkeit aufge-zeigt.1.1AnwendungsfelderDie Möglichkeiten der Anwendung maschinennaher Simulation erstrecken sich von der Maschinenent-wicklung über die Zellenplanung und die Inbetrieb-nahme bis zum produktiven Betrieb und schließen auch den Vertrieb ein (siehe Bild 2).In addition to this, it must also be taken into consid-eration that data exchange and the continuity between individual types of simulation are gaining increasing significance.Other types of simulation which have marginal appli-cations in the machine-oriented sector are not dealt with in this guideline as they represent separate, inde-pendent areas:•simulation in electrotechnical engineering •simulation in materials research •human/ergonomic simulation1Scope of applicationThe guideline provides an overview of the applica-tion areas and the benefits of simulation techniques which can be applied in the life cycle of a machine.The user receives instructions for easy selection of suitable simulation approaches for his particular task.The guideline deals with the requirements for the use of simulation, describes its application and provides instructions for successful application. It also gives simulation users a better understanding of ancillary areas and the various interactions which can occur. Of particular interest is the combination of different sim-ulation approaches. Options for integration and con-tinuity are also outlined here.1.1Application fieldsThe options for the use of machine-oriented simula-tion range from machine development to cell plan-ning and start-up, right up to productive operation and sales (see Figure 2).Bild 1. Simulationstechnologien der maschinennahen Simulation (nach [2])1. Simulation technologies in machine-oriented simula-tion (in accordance with [2])CV3D kinematic simulation Control simulationMultibody simulationProcess simulation。
基于matlab的传热学课程虚拟仿真实验平台设计
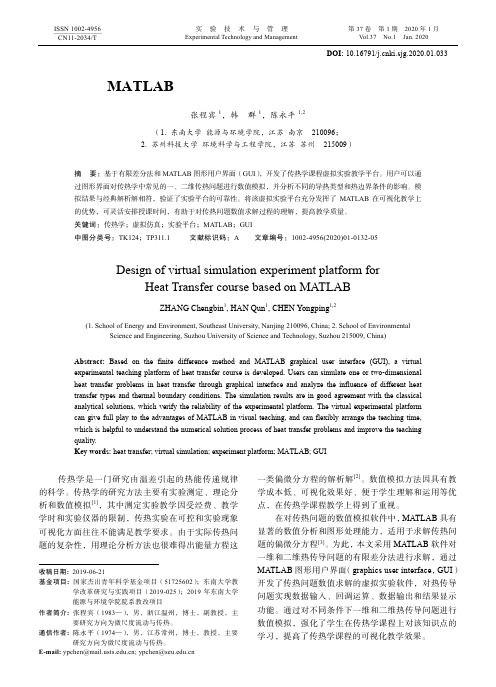
实 验 技 术 与 管 理 第37卷 第1期 2020年1月Experimental Technology and Management Vol.37 No.1 Jan. 2020ISSN 1002-4956 CN11-2034/TDOI: 10.16791/ki.sjg.2020.01.033基于MATLAB 的传热学课程虚拟仿真实验平台设计张程宾1,韩 群1,陈永平1,2(1. 东南大学 能源与环境学院,江苏 南京 210096; 2. 苏州科技大学 环境科学与工程学院,江苏 苏州 215009)摘 要:基于有限差分法和MATLAB 图形用户界面(GUI ),开发了传热学课程虚拟实验教学平台。
用户可以通过图形界面对传热学中常见的一、二维传热问题进行数值模拟,并分析不同的导热类型和热边界条件的影响。
模拟结果与经典解析解相符,验证了实验平台的可靠性。
将该虚拟实验平台充分发挥了MATLAB 在可视化教学上的优势,可灵活安排授课时间,有助于对传热问题数值求解过程的理解,提高教学质量。
关键词:传热学;虚拟仿真;实验平台;MATLAB ;GUI中图分类号:TK124;TP311.1 文献标识码:A 文章编号:1002-4956(2020)01-0132-05Design of virtual simulation experiment platform forHeat Transfer course based on MATLABZHANG Chengbin 1, HAN Qun 1, CHEN Yongping 1,2(1. School of Energy and Environment, Southeast University, Nanjing 210096, China; 2. School of EnvironmentalScience and Engineering, Suzhou University of Science and Technology, Suzhou 215009, China)Abstract: Based on the finite difference method and MATLAB graphical user interface (GUI), a virtual experimental teaching platform of heat transfer course is developed. Users can simulate one or two-dimensional heat transfer problems in heat transfer through graphical interface and analyze the influence of different heat transfer types and thermal boundary conditions. The simulation results are in good agreement with the classical analytical solutions, which verify the reliability of the experimental platform. The virtual experimental platform can give full play to the advantages of MATLAB in visual teaching, and can flexibly arrange the teaching time, which is helpful to understand the numerical solution process of heat transfer problems and improve the teaching quality.Key words: heat transfer; virtual simulation; experiment platform; MATLAB; GUI传热学是一门研究由温差引起的热能传递规律的科学。
汉字数字的用法
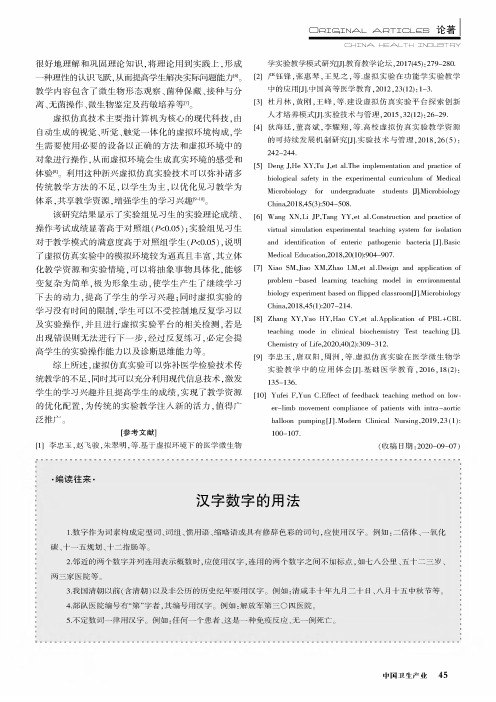
Original articles论著很好地理解和巩固理论知识,将理论用到实践上,形成一种理性的认识飞跃,从而提高学生解决实际问题能力冋。
教学内容包含了微生物形态观察、菌种保藏、接种与分离、无菌操作、微生物鉴定及药敏培养等"。
虚拟仿真技术主要指计算机为核心的现代科技,由自动生成的视觉、听觉、触觉一体化的虚拟环境构成,学生需要使用必要的设备以正确的方法和虚拟环境中的对象进行操作,从而虚拟环境会生成真实环境的感受和体验典利用这种新兴虚拟仿真实验技术可以弥补诸多传统教学方法的不足,以学生为主,以优化见习教学为体系,共享教学资源,增强学生的学习兴趣刊。
该研究结果显示了实验组见习生的实验理论成绩、操作考试成绩显著高于对照组(P<0.05);实验组见习生对于教学模式的满意度高于对照组学生(P<0.05),说明了虚拟仿真实验中的模拟环境较为逼真且丰富,其立体化教学资源和实验情境,可以将抽象事物具体化,能够变复杂为简单,极为形象生动,使学生产生了继续学习下去的动力,提高了学生的学习兴趣;同时虚拟实验的学习没有时间的限制,学生可以不受控制地反复学习以及实验操作,并且进行虚拟实验平台的相关检测,若是岀现错误则无法进行下一步,经过反复练习,必定会提高学生的实验操作能力以及诊断思维能力等。
综上所述,虚拟仿真实验可以弥补医学检验技术传统教学的不足,同时其可以充分利用现代信息技术,激发学生的学习兴趣并且提高学生的成绩,实现了教学资源的优化配置,为传统的实验教学注入新的活力,值得广泛推广。
[参考文献][1]李忠玉,赵飞骏,朱翠明,等.基于虚拟环境下的医学微生物CHINA HEALTH INDUSTRY学实验教学模式研究[J].教育教学论坛,2017(45):279-280.[2]严钰锋,张惠琴,王见之,等.虚拟实验在功能学实验教学中的应用[J].中国高等医学教育,2012,23(12):1-3.[3]杜月林,黄刚,王峰,等.建设虚拟仿真实验平台探索创新人才培养模式[J].实验技术与管理,2015,32(12):26-29. [4]狄海廷,董喜斌,李耀翔,等.高校虚拟仿真实验教学资源的可持续发展机制研究[J].实验技术与管理,2018,26(5):242-244.[5]Deng J,He XY,Tu J,et al.The implementation and practice ofbiological safety in the experimental curriculum of Medical Microbiology for undergraduate students[J].Microbiology Chin込2018,45(3):504-508.[6]Wang XN,Li JP,Tang YY,et al.Construction and practice ofvirtual simulation experimental teaching system for isolation and identification of enteric pathogenic bacteria[J].Basic Medical Education,2018,20(10):904-907.[7]Xiao SM,Jiao XM,Zhao LM,et al.Design and application ofproblem-based learning teaching model in environmental biology experiment based on flipped classroom[J].Microbiology China,2018,45(1):207-214.[8]Zhang XY,Yao HY,Hao CY,et al.Application of PBL+CBLteaching mode in clinical biochemistry Test teaching[J].Chemistry of Life,2020,40(2):309-312.[9]李忠玉,唐双阳,周洲,等.虚拟仿真实验在医学微生物学实验教学中的应用体会[J].基础医学教育,2016,18(2):135-136.[10]Yufei F,Yun C.Effect of feedback teaching method on lower-limb movement compliance of patients with intra-aortic balloon pumping[J].Modern Clinical Nursing,2019,23(1): 100-107.(收稿日期:2020-09-07)•编读往来•汉字数字的用法1.数字作为词素构成定型词、词组、惯用语、缩略语或具有修辞色彩的词句,应使用汉字。
研究生课程“相似理论与模拟试验”教学改革研究
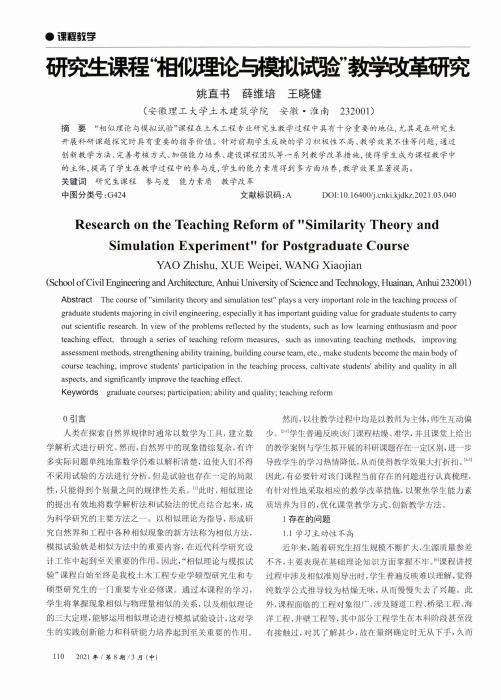
•课酲教字课程‘糖顺,姚直书薛维培王晓健(安徽理工大学土木建筑学院安徽•淮南232001)摘要“相似理论与模拟试验”课程在土木工程专业研究生教学过程中具有十分重要的地位,尤其是在研究生 开展科研课题探究时具有重要的指导价值。
针对前期学生反映的学习枳极性不高、教学效果不佳等问题,通过创新教学方法、完善考核方式、加强能力培养、建设课程团队等一系列教学改革措施,使得学生成为课程教学中的主体,提高了学生在教学过程中的参与度,学生的能力素质得到多方面培养,教学效果显著提高。
关键词研究生课程参与度能力素质教学改革中图分类号:G424 文献标识码:A D01:10.16400/ki.kjdkz.2021.03.040Research on the Teaching Reform of "Similarity Theory and Simulation Experiment” for Postgraduate CourseYAO Zhishu, XUE Weipei, WANG Xiaojian(School of C ivil Engineering and Architecture, Anhui University of S cience and Technology, Huainan, Anhui 232001)Abstract The course of"similarity theory and simulation test"plays a very important role in the teaching process of graduate students majoring in civil engineering,especially it has important guiding value for graduate students to carry out scientific research.In view of the problems reflected by the students,such as low learning enthusiasm and poor teaching effect,through a series of teaching reform measures,such as innovating teaching methods,improving assessment methods,strengthening ability training,building course team,etc.,make students become the main body of course teaching,improve students'participation in the teaching process,cultivate students'ability and quality in all aspects,and significantly improve the teaching effect.Keywords graduate courses;participation;ability and quality;teaching reform〇引言人类在探索自然界规律时通常以数学为工具,建立数 学解析式进行研宄。
CHEMICALEORTHEPASTDOESITHAVEFUTURE化学EOR过去它有未来

KYPAM Polymers
Comb like with short branched chain to maintain effectiveness in high salinity brinesWide MW range for reservoirs with different permeabilitiesSuccessfully applied in some reservoirs in China
ASP Pilot Test Well Pattern, 2Z-B9-3 Well Group
Karamay Oil Field (SPE 64726)
ASP Slug Design and Injection Sequence
(SPE 64726)
PAM
PAM
Modelling Core Flood - Karamay ASP Project
Harry L. Chang
Oil Production by Polymer Flooding
Daqing Oilfield, China
A Typical PF Field Performance
Typical Pressure and Polymer Production
Oil Production by Polymer Flooding
Harry L. Chang
EOR Chemicals
Polymers and related chemicalsSurfactantsCo-surfactantsCo-solvents
Harry L. Chang
Improvements on Polymers
奇葩实验英语作文

奇葩实验英语作文Title: The Peculiar Experiment: Unraveling the Unknown。
In the realm of scientific inquiry, curiosity often leads researchers down unconventional paths, prompting them to embark on peculiar experiments that challenge the boundaries of what is known. Such endeavors can yield unexpected insights and push the frontiers of knowledge. Today, we delve into the intriguing world of peculiar experiments, exploring their significance and the lessons they offer.One such experiment involved investigating the effectsof prolonged exposure to complete darkness on humancognition and sensory perception. Subjects were isolated in a light-sealed chamber for an extended period, devoid ofany external light sources. As the days stretched into weeks, researchers observed intriguing changes in the participants' behavior and mental faculties.Initially, subjects reported feelings of disorientation and unease as they grappled with the absence of light cues. Without the cyclical patterns of day and night, their circadian rhythms became disrupted, leading to irregular sleep patterns and fluctuations in mood. However, as time passed, a remarkable adaptation occurred.In the absence of visual stimuli, other senses sharpened in response to the heightened demand for sensory input. Participants reported an acute awareness of sounds, textures, and even subtle shifts in temperature withintheir environment. Some described experiencing vivid auditory hallucinations, attributing them to the brain's attempt to compensate for the lack of visual input.Cognitive functions also underwent significant changes under prolonged darkness. With limited external distractions, subjects found themselves immersed in deep introspection, contemplating existential questions and grappling with profound insights. Freed from theconstraints of conventional perception, they tapped into dormant reservoirs of creativity and imagination.Yet, the experiment also posed ethical dilemmas and raised questions about the limits of scientific inquiry. Is it ethical to subject individuals to extreme conditions in the pursuit of knowledge? What are the long-term psychological effects of such experiments on participants? These are complex issues that warrant careful consideration and ethical oversight.Another peculiar experiment delved into the realm of synesthesia, a phenomenon where stimulation of one sensory or cognitive pathway leads to involuntary experiences in another. Researchers sought to induce synesthetic experiences in non-synesthetes through a combination of sensory stimuli and cognitive conditioning.Subjects underwent a series of sensory deprivation sessions while listening to specific auditory sequences and viewing corresponding visual patterns. Over time, many reported experiencing synesthetic perceptions, such as seeing colors in response to sound or tasting flavors when exposed to certain shapes.The implications of this experiment extend beyond the realm of sensory perception, offering insights into the plasticity of the human brain and its capacity for cross-modal integration. By understanding the mechanisms underlying synesthesia, researchers hope to unlock new avenues for enhancing cognitive function and treating neurological disorders.However, the ethical considerations surrounding this experiment are paramount. Manipulating individuals' sensory experiences raises concerns about consent, autonomy, and potential harm. As we venture into the uncharted territory of the mind, we must tread carefully and prioritize the well-being of participants above all else.In conclusion, peculiar experiments serve as catalysts for scientific discovery, challenging our preconceptions and expanding the boundaries of human knowledge. From probing the effects of darkness on cognition to unraveling the mysteries of synesthesia, these endeavors offer valuable insights into the complexities of the humanexperience.Yet, they also underscore the importance of ethical conduct and responsible research practices. As we venture into uncharted territory, we must remain vigilant in safeguarding the rights and well-being of participants. Only through a balanced approach can we navigate the murky waters of peculiar experiments and unlock the secrets they hold.。
SLM成形不同孔隙结构骨支架的仿真与实验研究
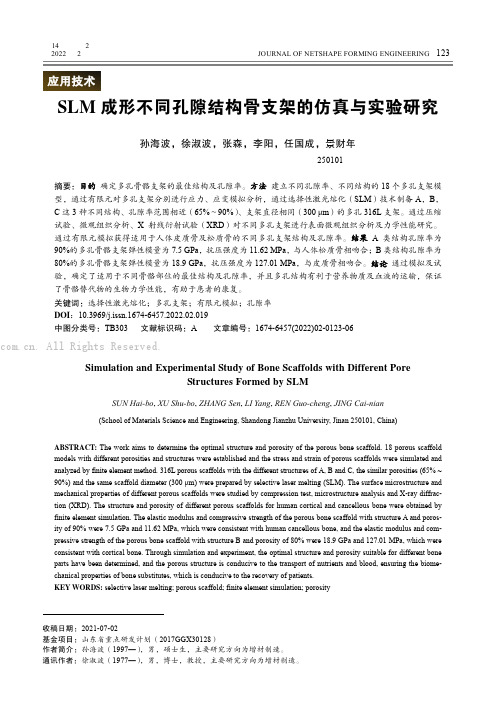
第14卷第2期精密成形工程孙海波,徐淑波,张森,李阳,任国成,景财年(山东建筑大学材料科学与工程学院,济南 250101)摘要:目的确定多孔骨骼支架的最佳结构及孔隙率。
方法建立不同孔隙率、不同结构的18个多孔支架模型,通过有限元对多孔支架分别进行应力、应变模拟分析,通过选择性激光熔化(SLM)技术制备A,B,C这3种不同结构、孔隙率范围相近(65%~90%)、支架直径相同(300 μm)的多孔316L支架。
通过压缩试验、微观组织分析、X射线衍射试验(XRD)对不同多孔支架进行表面微观组织分析及力学性能研究。
通过有限元模拟获得适用于人体皮质骨及松质骨的不同多孔支架结构及孔隙率。
结果A类结构孔隙率为90%的多孔骨骼支架弹性模量为7.5 GPa,抗压强度为11.62 MPa,与人体松质骨相吻合;B类结构孔隙率为80%的多孔骨骼支架弹性模量为18.9 GPa,抗压强度为127.01 MPa,与皮质骨相吻合。
结论通过模拟及试验,确定了适用于不同骨骼部位的最佳结构及孔隙率,并且多孔结构有利于营养物质及血液的运输,保证了骨骼替代物的生物力学性能,有助于患者的康复。
关键词:选择性激光熔化;多孔支架;有限元模拟;孔隙率DOI:10.3969/j.issn.1674-6457.2022.02.019中图分类号:TB303 文献标识码:A 文章编号:1674-6457(2022)02-0123-06. All Rights Reserved.Simulation and Experimental Study of Bone Scaffolds with Different PoreStructures Formed by SLMSUN Hai-bo, XU Shu-bo, ZHANG Sen, LI Yang, REN Guo-cheng, JING Cai-nian(School of Materials Science and Engineering, Shandong Jianzhu University, Jinan 250101, China)ABSTRACT: The work aims to determine the optimal structure and porosity of the porous bone scaffold.18 porous scaffoldmodels with different porosities and structures were established and the stress and strain of porous scaffolds were simulated andanalyzed by finite element method. 316L porous scaffolds with the different structures of A, B and C, the similar porosities (65% ~90%) and the same scaffold diameter (300 μm) were prepared by selective laser melting (SLM). The surface microstructure andmechanical properties of different porous scaffolds were studied by compression test, microstructure analysis and X-ray diffrac-tion (XRD). The structure and porosity of different porous scaffolds for human cortical and cancellous bone were obtained byfinite element simulation. The elastic modulus and compressive strength of the porous bone scaffold with structure A and poros-ity of 90% were 7.5 GPa and 11.62 MPa, which were consistent with human cancellous bone, and the elastic modulus and com-pressive strength of the porous bone scaffold with structure B and porosity of 80% were 18.9 GPa and 127.01 MPa, which wereconsistent with cortical bone.Through simulation and experiment, the optimal structure and porosity suitable for different boneparts have been determined, and the porous structure is conducive to the transport of nutrients and blood, ensuring the biome-chanical properties of bone substitutes, which is conducive to the recovery of patients.KEY WORDS: selective laser melting; porous scaffold; finite element simulation; porosity收稿日期:2021-07-02基金项目:山东省重点研发计划(2017GGX30128)作者简介:孙海波(1997—),男,硕士生,主要研究方向为增材制造。