机器视觉检测定位测量的应用案例
halcon目标检测案例

halcon目标检测案例Halcon是一款强大的机器视觉软件,拥有丰富的图像处理和分析功能。
其中,目标检测是Halcon的重要功能之一,能够帮助用户实现对图像中目标的自动检测和定位。
下面列举了十个关于Halcon目标检测的案例,以展示其在实际应用中的优势和灵活性。
1. 工业品质检测:在工业生产线上,Halcon可以通过目标检测技术实现对产品外观缺陷的检测,如表面瑕疵、颜色偏差等。
通过训练算法,Halcon能够快速准确地检测出产品中的异常情况,提高生产效率和产品质量。
2. 药品包装检测:在药品生产过程中,Halcon可以应用于药品包装的检测和识别。
通过目标检测算法,Halcon可以检测药品包装盒上的标签和二维码等信息,确保药品的包装符合规定标准,从而保证药品的质量和安全性。
3. 路标识别:在智能交通系统中,Halcon可以应用于路标的识别和检测。
通过训练模型,Halcon能够准确地识别出道路上的各种标识,如交通信号灯、限速标志等,为智能驾驶系统提供准确的环境感知能力。
4. 农作物病害检测:在农业领域,Halcon可以应用于农作物病害的检测和识别。
通过图像处理和机器学习算法,Halcon能够自动识别出农作物叶片上的病害,提前预警农民并采取相应的措施,保证农作物的健康生长。
5. 人脸识别:在安防领域,Halcon可以应用于人脸识别系统的开发。
通过目标检测和特征提取算法,Halcon能够对图像中的人脸进行准确的识别,实现对人员身份的自动判断,提高安全性和便利性。
6. 垃圾分类:在环境保护领域,Halcon可以应用于垃圾分类系统的开发。
通过目标检测和图像识别算法,Halcon能够自动识别垃圾中的有害物质,并将其分离出来,实现自动化的垃圾分类,提高垃圾处理的效率和准确性。
7. 医学影像分析:在医疗领域,Halcon可以应用于医学影像的分析和识别。
通过目标检测和图像分割算法,Halcon能够自动识别医学影像中的病变区域,并提供准确的测量和分析结果,帮助医生进行疾病的诊断和治疗。
计算机视觉技术的实际应用案例介绍

计算机视觉技术的实际应用案例介绍计算机视觉技术,作为一门研究和应用人工智能的重要领域,已经在各个行业中得到广泛应用。
通过模拟和实现人类视觉系统的功能,计算机视觉技术可以对图像、视频等进行高效处理和分析,从而实现识别、检测、跟踪等功能。
以下将介绍几个计算机视觉技术的实际应用案例。
1. 人脸识别技术在安全领域的应用人脸识别技术是计算机视觉技术中的一项重要应用。
通过对图像或视频中的人脸进行特征提取和匹配,可以实现快速、准确地识别个人身份。
这种技术在安全领域有着广泛的应用,比如用于辨别空港、银行大楼等公共区域的进出人员。
通过安装摄像头和相关硬件设备,系统可以实时地进行人脸识别,判断是否有犯罪嫌疑人进入。
这种技术的应用可以大大提高安全性,减少人力成本。
2. 自动驾驶技术在汽车领域的应用自动驾驶技术是计算机视觉技术在汽车领域的重大突破。
通过对车辆周围环境进行三维建模和检测,计算机系统可以实时判断路况和障碍物的位置,从而实现自动驾驶。
这种技术可以提高行车安全性,减少交通事故的发生。
例如,特斯拉公司的Autopilot系统就利用了计算机视觉技术,通过摄像头和传感器对道路进行实时监测,实现车辆的自主导航和避障。
3. 图像识别技术在医疗诊断中的应用图像识别技术是计算机视觉技术中的一项重要应用,可以用于医疗领域中的疾病诊断和治疗。
通过对医学图像(如X射线、CT扫描图像等)进行分析和识别,计算机系统可以自动检测和诊断疾病。
例如,乳腺癌的早期检测和治疗是一个重要问题,计算机视觉技术可以通过对乳腺X射线图像进行分析,识别潜在的癌症病灶,提高早期诊断率。
4. 增强现实技术在教育领域的应用增强现实技术是计算机视觉技术的一个分支,通过在真实场景中叠加虚拟信息,提供丰富的交互体验。
这种技术在教育领域有着广泛的应用,能够提高学生的学习效果和兴趣。
例如,通过手机或平板电脑上的摄像头,学生可以扫描教科书中的图片,获取相关的虚拟信息,进行互动学习。
列举1~2个机器视觉应用案例,并解释其工作原理。
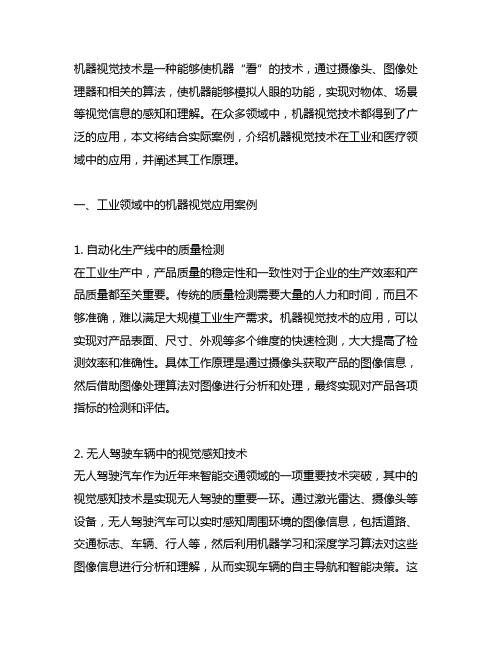
机器视觉技术是一种能够使机器“看”的技术,通过摄像头、图像处理器和相关的算法,使机器能够模拟人眼的功能,实现对物体、场景等视觉信息的感知和理解。
在众多领域中,机器视觉技术都得到了广泛的应用,本文将结合实际案例,介绍机器视觉技术在工业和医疗领域中的应用,并阐述其工作原理。
一、工业领域中的机器视觉应用案例1. 自动化生产线中的质量检测在工业生产中,产品质量的稳定性和一致性对于企业的生产效率和产品质量都至关重要。
传统的质量检测需要大量的人力和时间,而且不够准确,难以满足大规模工业生产需求。
机器视觉技术的应用,可以实现对产品表面、尺寸、外观等多个维度的快速检测,大大提高了检测效率和准确性。
具体工作原理是通过摄像头获取产品的图像信息,然后借助图像处理算法对图像进行分析和处理,最终实现对产品各项指标的检测和评估。
2. 无人驾驶车辆中的视觉感知技术无人驾驶汽车作为近年来智能交通领域的一项重要技术突破,其中的视觉感知技术是实现无人驾驶的重要一环。
通过激光雷达、摄像头等设备,无人驾驶汽车可以实时感知周围环境的图像信息,包括道路、交通标志、车辆、行人等,然后利用机器学习和深度学习算法对这些图像信息进行分析和理解,从而实现车辆的自主导航和智能决策。
这一技术的应用,将对未来交通、出行和城市规划等领域产生深远的影响。
二、医疗领域中的机器视觉应用案例1. 医学影像诊断在医学影像诊断领域,机器视觉技术发挥了巨大作用。
医学影像如CT、MRI等传统上需要医生凭借经验和专业知识进行诊断,费时费力且存在一定主观性,而引入机器视觉技术后,可以实现对医学影像的自动分析和诊断,辅助医生进行更准确、更快速的临床诊断。
其工作原理是通过机器学习算法对大量医学影像数据进行学习和训练,从而建立起对各种疾病、病变的自动识别和分析能力,大大提高了医学影像诊断的准确性和效率。
2. 手术辅助系统在微创手术和精准手术领域,机器视觉技术的应用也成为了一大亮点。
机器视觉的应用案例

机器视觉的应用案例机器视觉(Machine Vision)是一种利用计算机和摄像机等设备,模拟人类视觉系统进行图像识别和处理的技术。
随着人工智能技术的发展,机器视觉在各个领域得到了广泛的应用。
本文将介绍10个机器视觉的应用案例。
1. 工业品质检测:机器视觉在工业生产中广泛应用于产品品质检测。
例如,在汽车制造过程中,机器视觉可以对汽车零部件进行检测,如发动机零件的尺寸、表面瑕疵等进行检测,提高产品的质量和一致性。
2. 医学影像分析:机器视觉可以辅助医生进行医学影像的分析和诊断。
例如,在CT 扫描中,机器视觉可以自动识别和标记出疑似肿瘤的区域,帮助医生进行早期诊断和治疗。
3. 无人驾驶:无人驾驶汽车是机器视觉应用的一个热门领域。
机器视觉可以通过识别和分析道路标志、交通信号灯、行人等信息来实现自动驾驶,提高交通安全性和驾驶效率。
4. 农业智能化:机器视觉在农业领域的应用也越来越广泛。
例如,机器视觉可以识别和分类农作物的成熟度,自动进行采摘和分拣操作,提高农作物的产量和质量。
5. 安防监控:机器视觉可以用于安防监控系统,通过识别和跟踪人脸、车牌等信息,实现对潜在威胁的监测和预警,提高安全性和警戒效果。
6. 食品质量检测:机器视觉可以对食品进行质量检测,例如水果的瑕疵检测、肉类的新鲜度检测等。
通过机器视觉技术,可以快速、准确地检测食品的质量,提高食品加工和销售的安全性和可靠性。
7. 电子商务:机器视觉可以用于电子商务平台上的图像搜索和识别,例如通过拍照搜索相似的商品,或者扫描二维码进行商品信息的获取。
这种技术可以提高用户的购物体验和购买效率。
8. 智能交通:机器视觉可以用于智能交通系统,例如通过识别和分析车辆的行驶轨迹和速度,实现交通拥堵的预测和调度。
这些信息可以用于优化交通规划和资源分配,提高城市交通的效率和便利性。
9. 人机交互:机器视觉可以用于人机交互界面的设计,例如通过识别手势和表情,实现人与计算机之间的自然交互。
智能制造系统中的工业机器视觉应用案例

智能制造系统中的工业机器视觉应用案例工业机器视觉技术是智能制造系统中的重要组成部分,它通过相机、光源、传感器等设备,利用图像处理算法对生产过程中的产品进行检测、识别和分析。
这项技术在提高生产效率、保证产品质量、降低生产成本等方面具有广泛应用。
本文将介绍几个在智能制造系统中应用工业机器视觉的成功案例。
1. 智能摄像头检测系统中国某汽车零部件制造公司采用智能摄像头检测系统,对汽车发动机缸体进行质量检测。
该系统使用高分辨率工业相机对缸体进行拍摄,并通过图像处理算法对缸体表面进行检测和分析。
系统能够准确识别缸体表面的缺陷、划痕、裂纹等缺陷,并对不合格品实现自动分拣。
这个系统极大地提高了检测效率和准确性,降低了人工检测的劳动强度和人为误检的风险。
2. 质量检测和追溯系统某电子制造公司在智能制造系统中应用工业机器视觉技术实现了产品质量检测和追溯。
通过高分辨率相机和图像处理算法,对电子产品的外观、尺寸等参数进行全面检测。
系统能够自动判断产品是否合格,并将不合格品的信息上传到数据库,进行追溯。
该系统实时监测生产线上的产品质量,确保产品符合标准,并能追溯到具体的生产批次和生产过程,方便追踪和排查质量问题。
这样的系统在提高产品质量和降低产品召回成本方面发挥了重要作用。
3. 智能机器人视觉导航系统一家智能仓储物流设备制造公司采用智能机器人视觉导航系统,实现了仓库物品自动分拣。
该系统通过安装在机器人上的摄像头和激光传感器,实时获取周围环境的图像和数据信息。
结合图像识别和定位算法,系统能够判断货物的位置和类型,并将机器人引导到指定位置进行自动分拣。
系统在物流仓库中的应用,大大提高了仓储效率和准确性,降低了运营成本。
4. 汽车生产线上的机器视觉系统某汽车制造公司在汽车生产线上应用机器视觉系统,实现自动化组装和检测。
该系统通过相机和图像处理算法,对汽车零部件进行检测和识别。
系统能够自动判断零部件的位置和姿态,并进行自动化组装,大大提高了汽车生产线的生产效率和一致性。
机器视觉检测案例
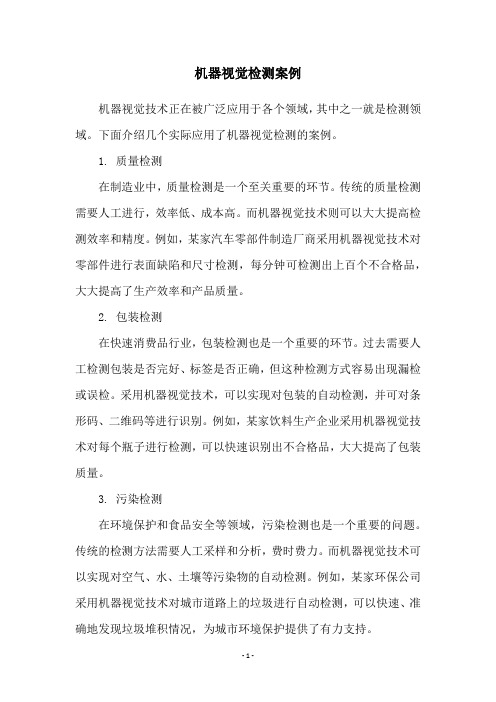
机器视觉检测案例
机器视觉技术正在被广泛应用于各个领域,其中之一就是检测领域。
下面介绍几个实际应用了机器视觉检测的案例。
1. 质量检测
在制造业中,质量检测是一个至关重要的环节。
传统的质量检测需要人工进行,效率低、成本高。
而机器视觉技术则可以大大提高检测效率和精度。
例如,某家汽车零部件制造厂商采用机器视觉技术对零部件进行表面缺陷和尺寸检测,每分钟可检测出上百个不合格品,大大提高了生产效率和产品质量。
2. 包装检测
在快速消费品行业,包装检测也是一个重要的环节。
过去需要人工检测包装是否完好、标签是否正确,但这种检测方式容易出现漏检或误检。
采用机器视觉技术,可以实现对包装的自动检测,并可对条形码、二维码等进行识别。
例如,某家饮料生产企业采用机器视觉技术对每个瓶子进行检测,可以快速识别出不合格品,大大提高了包装质量。
3. 污染检测
在环境保护和食品安全等领域,污染检测也是一个重要的问题。
传统的检测方法需要人工采样和分析,费时费力。
而机器视觉技术可以实现对空气、水、土壤等污染物的自动检测。
例如,某家环保公司采用机器视觉技术对城市道路上的垃圾进行自动检测,可以快速、准确地发现垃圾堆积情况,为城市环境保护提供了有力支持。
总之,机器视觉技术的广泛应用正在改变我们的生产和生活方式,为各行各业带来了更高效、更精确的检测方法。
视觉检测应用案例
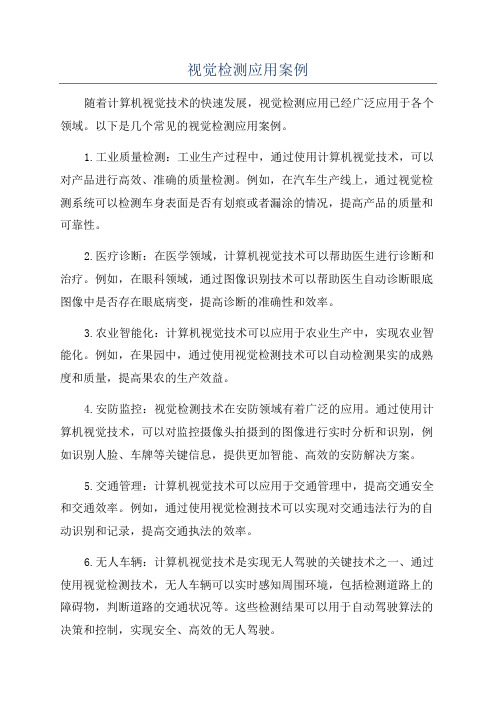
视觉检测应用案例
随着计算机视觉技术的快速发展,视觉检测应用已经广泛应用于各个领域。
以下是几个常见的视觉检测应用案例。
1.工业质量检测:工业生产过程中,通过使用计算机视觉技术,可以对产品进行高效、准确的质量检测。
例如,在汽车生产线上,通过视觉检测系统可以检测车身表面是否有划痕或者漏涂的情况,提高产品的质量和可靠性。
2.医疗诊断:在医学领域,计算机视觉技术可以帮助医生进行诊断和治疗。
例如,在眼科领域,通过图像识别技术可以帮助医生自动诊断眼底图像中是否存在眼底病变,提高诊断的准确性和效率。
3.农业智能化:计算机视觉技术可以应用于农业生产中,实现农业智能化。
例如,在果园中,通过使用视觉检测技术可以自动检测果实的成熟度和质量,提高果农的生产效益。
4.安防监控:视觉检测技术在安防领域有着广泛的应用。
通过使用计算机视觉技术,可以对监控摄像头拍摄到的图像进行实时分析和识别,例如识别人脸、车牌等关键信息,提供更加智能、高效的安防解决方案。
5.交通管理:计算机视觉技术可以应用于交通管理中,提高交通安全和交通效率。
例如,通过使用视觉检测技术可以实现对交通违法行为的自动识别和记录,提高交通执法的效率。
6.无人车辆:计算机视觉技术是实现无人驾驶的关键技术之一、通过使用视觉检测技术,无人车辆可以实时感知周围环境,包括检测道路上的障碍物,判断道路的交通状况等。
这些检测结果可以用于自动驾驶算法的决策和控制,实现安全、高效的无人驾驶。
总结起来,计算机视觉技术的应用已经渗透到各个领域中,极大地提高了生产效益和社会效益。
随着技术的不断发展,视觉检测应用将会得到进一步的拓展和完善。
机器视觉系统之案例篇

2023-10-30•案例一:应用于工业生产的机器视觉系统•案例二:应用于医学影像分析的目录机器视觉系统•案例三:应用于自动驾驶的机器视觉系统•案例四:应用于农业生产的机器视觉系统01案例一:应用于工业生产的机器视觉系统机器视觉系统的定义和功能工业生产中常见的机器视觉系统类型机器视觉系统在工业生产中的重要性工业生产中的机器视觉系统介绍•案例一:检测工业产品外观缺陷•应用场景:生产线上的产品检测•技术方案:采用图像处理和深度学习技术•实现效果:自动识别和分类产品缺陷,提高生产效率和产品质量•案例二:引导机器人进行自动化操作•应用场景:生产线上的自动化操作•技术方案:采用计算机视觉和深度学习技术•实现效果:自动识别和跟踪目标,实现精准操作,提高生产效率机器视觉系统在工业生产中的应用案例工业生产中机器视觉系统的优势与挑战•优势•提高生产效率和产品质量•降低人工成本和操作失误率•提高生产线的智能化和自动化水平•挑战•算法的准确性和稳定性•系统的可靠性和稳定性•数据的采集和处理02案例二:应用于医学影像分析的机器视觉系统机器视觉系统在医学影像分析中的定义机器视觉系统是一种利用计算机、图像传感器和深度学习技术对医学影像进行分析、理解和解释的系统。
医学影像分析中的机器视觉系统介绍医学影像的特点医学影像包括X光片、CT扫描、MRI等,这些图像具有高维度、高噪声、复杂纹理等特点,需要专业的医学知识进行解读和分析。
机器视觉系统在医学影像分析中的流程机器视觉系统首先对医学影像进行预处理,包括去噪、增强等操作,然后通过特征提取和模型训练,对影像进行分类、定位和定量分析。
案例一:肺癌检测应用背景:肺癌是全球最常见的恶性肿瘤之一,早期诊断和治疗对提高患者生存率具有重要意义。
应用方法:机器视觉系统通过对CT扫描等医学影像进行分析,自动检测出肺部结节等异常组织,提高医生的诊断准确性和效率。
案例二:脑部疾病诊断应用背景:脑部疾病如阿尔茨海默病、脑梗等严重影响着人类的健康和生活质量。
机器视觉简单应用实例

机器视觉简单应用实例一、物体识别物体识别是机器视觉的基本应用之一。
通过图像处理和计算机视觉技术,机器能够识别出不同的物体,并对其进行分类和识别。
例如,在生产线上的机器人可以通过机器视觉系统识别出不同的零件,并将其准确地抓取到指定的位置。
二、物体定位物体定位是机器视觉的另一个重要应用。
通过机器视觉系统,可以确定物体的位置、方向和姿态等信息。
例如,在智能制造领域,机器人可以通过机器视觉系统定位和抓取零件,并将其准确地放置到指定的位置。
三、物体测量物体测量是机器视觉的重要应用之一。
通过机器视觉系统,可以对物体的尺寸、形状、角度等信息进行测量和计算。
例如,在汽车制造领域,机器视觉系统可以用于测量车身的尺寸和形状,以确保其符合设计要求。
四、物体跟踪物体跟踪是机器视觉的另一个重要应用。
通过机器视觉系统,可以实时跟踪物体的运动轨迹和位置信息。
例如,在智能交通领域,机器视觉系统可以用于跟踪车辆的运动轨迹和速度等信息,以确保其符合交通规则。
五、图像增强图像增强是机器视觉的重要应用之一。
通过图像处理技术,可以对图像进行增强和优化,以提高图像的清晰度和可读性。
例如,在医疗影像领域,机器视觉系统可以用于增强医学影像的清晰度和对比度,从而提高诊断的准确性和效率。
六、图像分割图像分割是机器视觉的重要应用之一。
通过图像处理技术,可以将图像中的不同区域进行分割和分类。
例如,在人脸识别领域,机器视觉系统可以用于分割人脸的不同特征区域,从而实现对人脸的准确识别。
七、特征提取特征提取是机器视觉的重要应用之一。
通过计算机视觉技术,可以从图像中提取出有用的特征信息。
例如,在人脸识别领域,机器视觉系统可以用于提取人脸的特征信息,从而实现对人脸的准确识别。
八、机器翻译机器翻译是机器视觉的重要应用之一。
通过计算机视觉技术,可以将一种语言翻译成另一种语言。
例如,在医疗影像领域,机器视觉系统可以用于将医学影像中的文字信息翻译成中文或英文等其他语言。
计算机视觉生活案例
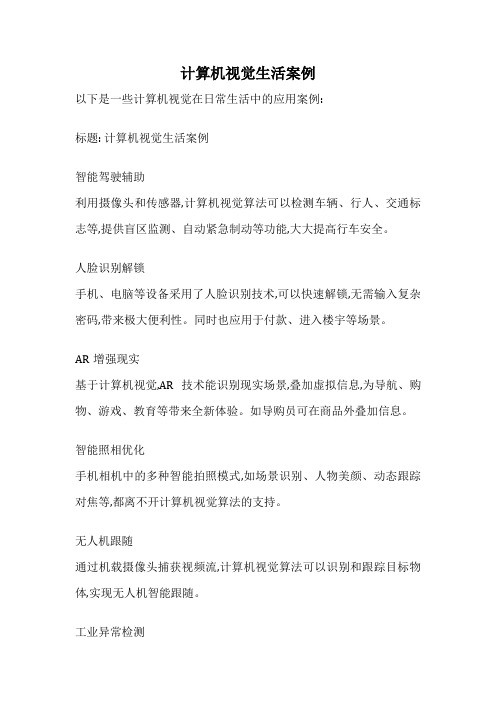
计算机视觉生活案例
以下是一些计算机视觉在日常生活中的应用案例:
标题: 计算机视觉生活案例
智能驾驶辅助
利用摄像头和传感器,计算机视觉算法可以检测车辆、行人、交通标志等,提供盲区监测、自动紧急制动等功能,大大提高行车安全。
人脸识别解锁
手机、电脑等设备采用了人脸识别技术,可以快速解锁,无需输入复杂密码,带来极大便利性。
同时也应用于付款、进入楼宇等场景。
AR增强现实
基于计算机视觉,AR技术能识别现实场景,叠加虚拟信息,为导航、购物、游戏、教育等带来全新体验。
如导购员可在商品外叠加信息。
智能照相优化
手机相机中的多种智能拍照模式,如场景识别、人物美颜、动态跟踪对焦等,都离不开计算机视觉算法的支持。
无人机跟随
通过机载摄像头捕获视频流,计算机视觉算法可以识别和跟踪目标物体,实现无人机智能跟随。
工业异常检测
在生产线上,计算机视觉可实时监测产品质量、识别缺陷、异常等,及时发现并警示,提高生产效率。
这些只是计算机视觉在生活中的一些应用,未来它将无处不在,为生活带来更多智能和便利。
机器视觉坐标测量系统实用案例分享
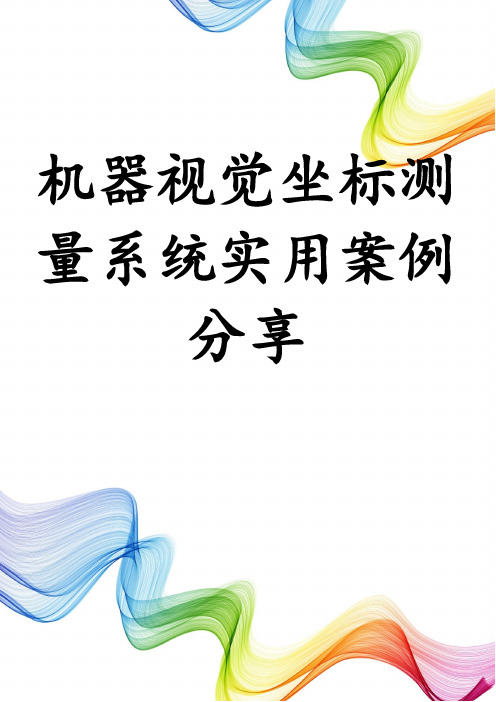
机器视觉坐标测量系统实用案例分享机器视觉坐标测量系统实用案例分享机器视觉坐标测量系统是一种基于计算机视觉技术的测量系统,可以快速、精确地测量物体的位置和尺寸信息。
它在许多领域都有广泛的应用,比如工业制造、机器人导航、医疗影像等。
下面将以工业制造为例,介绍机器视觉坐标测量系统的实用案例。
步骤一:确定测量需求在工业制造过程中,往往需要对零部件进行尺寸和位置的测量。
比如,在汽车制造中,需要测量零件的直径、长度、高度等尺寸,以及零件之间的距离。
首先,需要确定具体的测量需求,包括测量的物体类型、测量的尺寸范围等。
步骤二:搭建机器视觉系统在确定测量需求后,需要搭建机器视觉系统。
该系统通常由摄像头、图像处理软件和数据处理器等组成。
摄像头用于拍摄待测物体的图像,图像处理软件用于分析图像并提取出需要的尺寸和位置信息,数据处理器用于处理测量结果并进行显示和存储。
步骤三:标定系统在使用机器视觉系统进行测量之前,需要对系统进行标定,以确保测量结果的准确性。
标定过程包括摄像头的内部参数标定和外部参数标定。
内部参数标定主要是确定摄像头的焦距、畸变等参数,外部参数标定主要是确定摄像头相对于待测物体的位置和姿态。
步骤四:采集图像在进行测量之前,需要采集待测物体的图像。
通常情况下,需要采集多个角度的图像,以确保测量的全面性和准确性。
采集图像时,应注意光照条件的一致性,以避免光照对测量结果的影响。
步骤五:图像处理和分析采集到图像后,需要通过图像处理软件对图像进行处理和分析。
图像处理包括图像去噪、边缘检测、形态学操作等,以提取出待测物体的轮廓信息。
然后,通过图像分析算法,可以计算出物体的尺寸和位置信息。
步骤六:测量结果的显示和处理测量结果可以通过数据处理器进行显示和处理。
通常情况下,可以将测量结果以数字、图形、报表等形式进行显示,方便操作员进行判断和决策。
同时,还可以将测量结果与设定的标准进行比较,以判断物体是否合格。
总结:机器视觉坐标测量系统在工业制造中具有广泛的应用前景。
机器视觉技术在品质检测中的应用案例分享
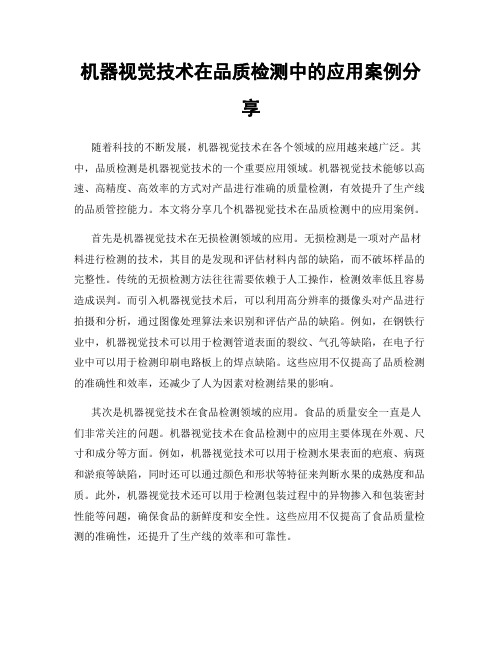
机器视觉技术在品质检测中的应用案例分享随着科技的不断发展,机器视觉技术在各个领域的应用越来越广泛。
其中,品质检测是机器视觉技术的一个重要应用领域。
机器视觉技术能够以高速、高精度、高效率的方式对产品进行准确的质量检测,有效提升了生产线的品质管控能力。
本文将分享几个机器视觉技术在品质检测中的应用案例。
首先是机器视觉技术在无损检测领域的应用。
无损检测是一项对产品材料进行检测的技术,其目的是发现和评估材料内部的缺陷,而不破坏样品的完整性。
传统的无损检测方法往往需要依赖于人工操作,检测效率低且容易造成误判。
而引入机器视觉技术后,可以利用高分辨率的摄像头对产品进行拍摄和分析,通过图像处理算法来识别和评估产品的缺陷。
例如,在钢铁行业中,机器视觉技术可以用于检测管道表面的裂纹、气孔等缺陷,在电子行业中可以用于检测印刷电路板上的焊点缺陷。
这些应用不仅提高了品质检测的准确性和效率,还减少了人为因素对检测结果的影响。
其次是机器视觉技术在食品检测领域的应用。
食品的质量安全一直是人们非常关注的问题。
机器视觉技术在食品检测中的应用主要体现在外观、尺寸和成分等方面。
例如,机器视觉技术可以用于检测水果表面的疤痕、病斑和淤痕等缺陷,同时还可以通过颜色和形状等特征来判断水果的成熟度和品质。
此外,机器视觉技术还可以用于检测包装过程中的异物掺入和包装密封性能等问题,确保食品的新鲜度和安全性。
这些应用不仅提高了食品质量检测的准确性,还提升了生产线的效率和可靠性。
再次是机器视觉技术在医药制造领域的应用。
医药制造过程中对于药品的质量要求非常高,传统的人工检测方法难以满足需求,而引入机器视觉技术可以极大地提高医药制造品质检测的精确度和效率。
例如,在药片生产过程中,机器视觉技术可以用于检测药片的重量、尺寸和颜色等特征,保证合格的产品流入市场。
此外,机器视觉技术还可以用于检测药品包装的完整性和标签的准确性,确保药品的真实性和安全性。
这些应用不仅提高了药品品质检测的准确性,还大大提高了生产线的效率和安全性。
计算机视觉技术在工业检测中的应用案例解析

计算机视觉技术在工业检测中的应用案例解析近年来,随着计算机视觉技术(Computer Vision)的快速发展,其在工业检测领域的应用逐渐得到广泛关注。
计算机视觉技术利用摄像机及相关设备捕捉、处理和分析图像数据,实现对物体的自动检测、识别和测量,为工业检测提供了一种高效、精确、无人干预的解决方案。
本文将通过几个应用案例展示计算机视觉技术在工业检测中的优势和实际应用。
首先,计算机视觉技术在产品外观质量检测中的应用案例可谓成功的典范。
传统的外观检测需要大量的人力和时间,容易出现主观误判和漏检的情况。
而引入计算机视觉技术后,通过对产品外观图像进行实时分析和比对,可以快速准确地检测出外观缺陷,如划痕、漆面缺陷、气泡等。
一个典型的应用案例是汽车生产线上的车漆检测。
使用计算机视觉技术,可以通过图像识别技术对车辆的车漆进行在线检测,有效地避免了人工检测中可能出现的主观判断和疏漏,提高了产品质量和生产效率。
其次,计算机视觉技术在工业制造中的缺陷检测方面也有广泛的应用。
无论是电子产品、服装、食品还是机械零件,都需要经过缺陷检测环节来确保质量。
传统的缺陷检测方法需要人工操作,费时费力,并且容易出现漏检和误判的情况。
而计算机视觉技术通过分析图像数据,可以实现对产品的缺陷自动检测,如电路板焊接缺陷、针织品的疵点、食品的异物等。
这种自动化的缺陷检测方法,不仅提高了生产效率,还大大减少了人力成本和产品质量问题。
此外,计算机视觉技术在工业检测中的应用还包括尺寸测量和位置定位等领域。
在工业生产中,产品的尺寸和位置的准确性直接影响产品的质量和性能。
传统的尺寸测量和位置定位需要人工进行,费时且容易出现误差。
利用计算机视觉技术,可以通过图像处理和模式识别算法实现对产品尺寸和位置的自动测量和定位。
例如,通过对零件图像进行处理和分析,计算机视觉技术可以实现对零件的尺寸测量,比如直径、长度、角度等。
此外,计算机视觉技术还可以精确地定位产品的位置,如机器人的物体抓取和放置。
计算机视觉技术在物体检测中的应用案例分享

计算机视觉技术在物体检测中的应用案例分享计算机视觉技术是一门研究如何使计算机“看”以及从图像或视频中获取信息的技术。
在当今科技发展的时代,计算机视觉技术逐渐应用于各个领域,尤其是在物体检测方面取得了显著的进展。
本文将为您分享几个计算机视觉技术在物体检测中的应用案例。
首先,物体检测技术在自动驾驶领域中得到了广泛应用。
随着自动驾驶车辆的普及和城市交通的发展,交通安全成为了关注的焦点。
物体检测技术可以帮助自动驾驶车辆实时感知道路上的其他车辆、行人、交通标志等物体,从而实现智能驾驶。
例如,谷歌的自动驾驶汽车项目Waymo就采用了计算机视觉技术来检测和追踪其他车辆、行人和障碍物,以保证行驶的安全性。
其次,物体检测技术在安防领域中也有广泛的应用。
通过将计算机视觉技术应用于监控摄像头中,可以快速而准确地检测出异常事件,例如人员闯入、可疑包裹等。
这些物体检测技术可以帮助提高监控系统的效率,避免疏漏和错误判断。
一个成功的案例是美国边境巡逻队使用了物体检测技术来检测边境上的非法移民和毒品交易,大大提高了边境安全性。
此外,物体检测技术在医疗领域的应用也具有重要的意义。
通过计算机视觉技术,医生可以快速准确地检测和诊断疾病。
例如,基于计算机视觉技术的乳腺癌检测系统可以自动检测出乳腺X光片中的异常细胞,帮助医生早日发现并治疗疾病。
物体检测技术还可以应用于手术导航系统中,通过实时跟踪和检测器械和组织,帮助医生更加准确地进行手术操作。
另一个有趣的应用案例是物体检测技术在零售业中的应用。
通过计算机视觉技术,商家可以实时监测店内货架上的商品情况,包括库存情况、陈列效果等。
这种技术可以帮助商家及时补充缺货商品,并根据销售情况进行合理的陈列调整。
此外,物体检测技术还可以帮助识别顾客的性别和年龄等特征,从而为顾客提供个性化的推荐服务。
总的来说,计算机视觉技术在物体检测中的应用案例多种多样,从自动驾驶到安防、医疗和零售等各个领域都有广泛的应用。
机器视觉技术的应用实践案例
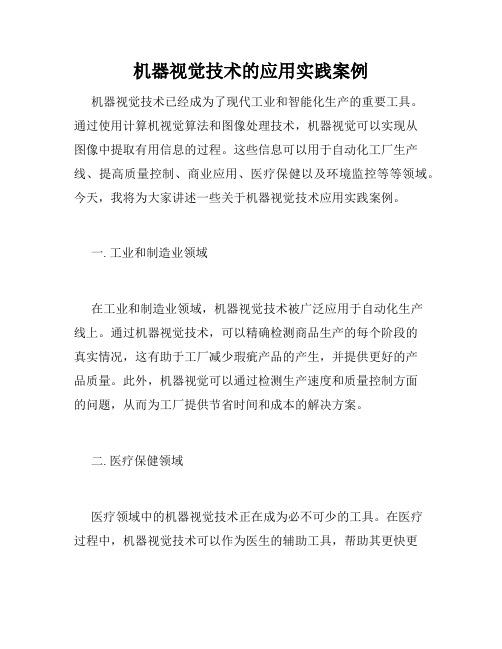
机器视觉技术的应用实践案例机器视觉技术已经成为了现代工业和智能化生产的重要工具。
通过使用计算机视觉算法和图像处理技术,机器视觉可以实现从图像中提取有用信息的过程。
这些信息可以用于自动化工厂生产线、提高质量控制、商业应用、医疗保健以及环境监控等等领域。
今天,我将为大家讲述一些关于机器视觉技术应用实践案例。
一. 工业和制造业领域在工业和制造业领域,机器视觉技术被广泛应用于自动化生产线上。
通过机器视觉技术,可以精确检测商品生产的每个阶段的真实情况,这有助于工厂减少瑕疵产品的产生,并提供更好的产品质量。
此外,机器视觉可以通过检测生产速度和质量控制方面的问题,从而为工厂提供节省时间和成本的解决方案。
二. 医疗保健领域医疗领域中的机器视觉技术正在成为必不可少的工具。
在医疗过程中,机器视觉技术可以作为医生的辅助工具,帮助其更快更准确地诊断病症。
例如,在肺部扫描和癌症检测中,机器视觉技术可以帮助医生更好地检测肿瘤,并给出更准确的治疗方案。
三. 环境监控领域随着环境问题的日益严重,我们需要更多的工具来监测和控制环境污染。
在这方面,机器视觉技术的应用也可以发挥巨大的作用。
例如,在城市和工业环境中,机器视觉技术可以用于检测污染物的水平并确定不安全区域。
此外,机器视觉还可以用于海洋和水资源管理,以监测海洋生态系统的健康状况以及水源质量的变化。
四. 商业应用领域与此同时,在商业领域,机器视觉技术正在被广泛应用。
例如,通过出售机制视觉技术,商家可以更好地分析买家的行为和喜好。
此外,机器视觉还可以用于自助结账垫和虚拟商店,以增强客户体验和减少购物的耗时。
总之,机器视觉技术是一个在不同领域中应用广泛、功能强大的技术。
随着技术的不断提高和进步,我们相信机器视觉技术的应用会越来越广泛,带来更多的变革和创新。
视觉测量技术在工业制造中的应用案例分析

视觉测量技术在工业制造中的应用案例分析近年来,随着科技的不断发展,视觉测量技术在工业制造领域发挥着越来越重要的作用。
它通过摄像机和图像处理系统的结合,可以快速、精确地获取物体的形状、尺寸、位置等信息,为工业制造过程提供了可靠的检测手段。
本文将通过一些实际案例来分析视觉测量技术在工业制造中应用的效果和优势。
案例一:机械加工在机械加工行业中,视觉测量技术能够实现对零件加工精度的实时监测和控制。
以航空航天行业为例,飞机发动机的制造对零部件的精度要求非常高,使用传统方法进行尺寸测量非常困难。
而借助视觉测量技术,可以通过摄像机对零件进行全方位的拍摄,再通过图像处理系统获取所需的尺寸信息。
这种非接触式的测量方式不仅减少了人工操作的可能误差,同时提高了生产效率和产品质量。
案例二:电子制造在电子制造行业中,视觉测量技术主要应用于电子元器件的焊接和组装过程中。
这些元器件体积小、引脚众多,传统的测量方法往往无法满足需求。
而视觉测量技术通过对元器件进行高速拍摄和图像处理,可以实时检测焊接质量、引脚位置等关键参数,确保产品的可靠性和稳定性。
同时,它还能够检测异常情况,如焊锡偏差、短路等,提高了生产线的稳定性和效率。
案例三:汽车制造在汽车制造领域,视觉测量技术广泛应用于车身焊接、涂装等工艺。
以车身焊接为例,传统的测量方法往往需要繁琐的手工操作,而且测量精度很难保证。
而视觉测量技术通过对焊缝进行拍摄和图像处理,可以实现车身焊接质量的自动化检测和控制。
它不仅提高了焊缝的精度和一致性,还可以及时发现焊接缺陷,减少了人工检测的工作量和错误率。
总结起来,视觉测量技术在工业制造中的应用越来越广泛,为生产过程提供了高效、精确的检测手段。
通过对实际案例的分析,我们可以看到它在机械加工、电子制造和汽车制造等领域的优势和效果。
视觉测量技术不仅减少了人工操作的误差,提高了生产效率和产品质量,还可以实现自动化的检测和控制,确保工业制造过程的稳定性和可靠性。
机器视觉在工业检测领域的应用案例和技术实现

机器视觉在工业检测领域的应用案例和技术实现随着科学和技术的不断发展,现代工业生产的效率和质量需求也逐渐提高。
而在工业生产中,各种机器设备的稳定性和精度是工业生产质量的关键因素之一。
因此,为保证工业生产的高效和优质,机器视觉技术应运而生,并逐渐在工业检测领域应用。
机器视觉技术是一种自动化检测技术,可实现对制造过程或成品质量的在线、实时监测和统计分析。
它可以帮助工业制造企业快速准确地检测产品缺陷,提升产品质量和生产效率,降低人工检测成本,实现全自动化生产。
以下将从机器视觉技术的应用案例和技术实现两个方面,探讨工业检测领域的机器视觉技术。
应用案例1. 光学成像技术应用案例浮点半导体制造是非常复杂的过程。
常规的生产质量检测往往需要大量的劳动力和时间。
通过应用光学成像技术,可以提高生产效率和质量,减少生产成本。
光学成像技术利用了光的物理特性,对微观结构进行成像,并通过图像处理和分析来确定质量。
通过这种技术,可以进行多种检测,如缺陷检测、精度检测和形状检测等。
2. 监控摄像技术应用案例监控摄像机技术常用于安全监测和追踪,其重要性可想而知。
在工业生产环境下,监控摄像机技术也可用于生产线质量检测和产品检测,如细节缺陷和表面缺陷等。
监控摄像技术的优点是可以在生产线的任何地方进行实时检测,而且不需要专业人员处理数据,从而实现自我监测和发现问题。
技术实现1. 视觉检测系统视觉检测系统是机器视觉技术的核心,它可以自动完成检测和测量功能。
目前,视觉检测系统一般应用于汽车制造、电子制造、食品和瓶装等行业。
视觉检测系统的核心是图像识别和处理。
它可以对图像进行采集、滤波、分割、特征提取和分类等操作。
采集到的图像将通过数字信号传递到计算机系统中的视觉检测软件,在进行分析和判断后,给出一个结果。
2. 3D扫描仪3D扫描仪可用于制造和产品设计的质量检测,是将产品的三维点云数据进行超精度测量并不断优化精度和模型设计。
通过对物体进行3D扫描,扫描仪可以随时记录每个点的坐标和颜色等属性。
计算机视觉技术在检测领域中的应用案例
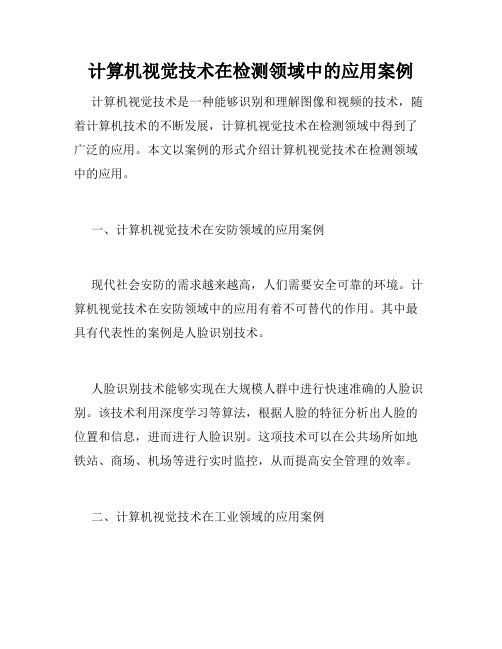
计算机视觉技术在检测领域中的应用案例计算机视觉技术是一种能够识别和理解图像和视频的技术,随着计算机技术的不断发展,计算机视觉技术在检测领域中得到了广泛的应用。
本文以案例的形式介绍计算机视觉技术在检测领域中的应用。
一、计算机视觉技术在安防领域的应用案例现代社会安防的需求越来越高,人们需要安全可靠的环境。
计算机视觉技术在安防领域中的应用有着不可替代的作用。
其中最具有代表性的案例是人脸识别技术。
人脸识别技术能够实现在大规模人群中进行快速准确的人脸识别。
该技术利用深度学习等算法,根据人脸的特征分析出人脸的位置和信息,进而进行人脸识别。
这项技术可以在公共场所如地铁站、商场、机场等进行实时监控,从而提高安全管理的效率。
二、计算机视觉技术在工业领域的应用案例工业领域是计算机视觉技术的另一个重要应用领域。
计算机视觉技术可以用于质量检测,其中最常见的案例是电子产品的质量检测。
手机、电脑等电子产品,其内部焊接的质量直接影响到整个产品的品质。
传统的检测方法需要耗费大量的人力物力,效率低下还不如计算机视觉技术。
计算机视觉技术可以根据电子产品内部的图像信息进行自动化检测,提高了生产效率和产品质量。
三、计算机视觉技术在医疗领域的应用案例计算机视觉技术的应用在医疗领域也是非常广泛。
计算机视觉技术在医疗领域的应用主要包括医学影像分析、病理学诊断和手术导航等方面。
例如,在病理学领域,计算机视觉技术可以通过对病理学图像的分析,实现病理学诊断的自动化。
这不仅提高了病理学医生的诊断效率,还能够减轻他们的工作压力。
四、计算机视觉技术在农业领域的应用案例农业领域也是计算机视觉技术应用广泛的一个领域。
计算机视觉技术可以帮助农业生产实现自动化,提高农业生产效率。
例如,在果树园区中,计算机视觉技术可以检测水果的成熟度和大小,从而协助果农进行采摘和分类。
这不仅提高了果农的生产效率,还可以减少因人为判断错误而导致的浪费问题。
总之,计算机视觉技术在检测领域中的应用大大提升了检测的效率和准确性。
机器视觉摄像头的应用场景和案例
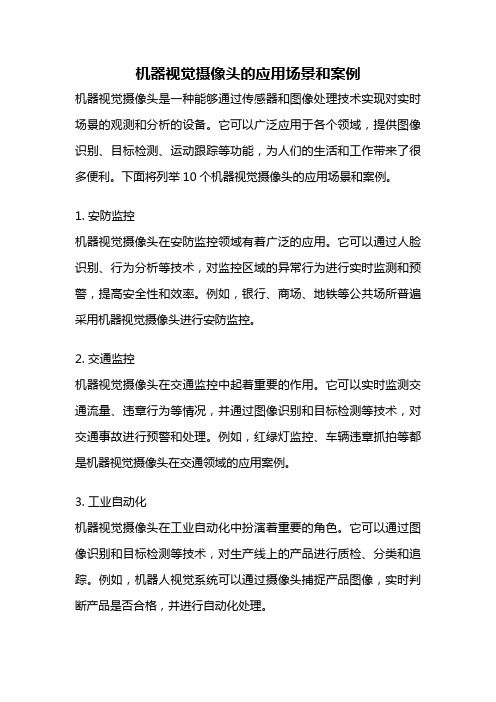
机器视觉摄像头的应用场景和案例机器视觉摄像头是一种能够通过传感器和图像处理技术实现对实时场景的观测和分析的设备。
它可以广泛应用于各个领域,提供图像识别、目标检测、运动跟踪等功能,为人们的生活和工作带来了很多便利。
下面将列举10个机器视觉摄像头的应用场景和案例。
1. 安防监控机器视觉摄像头在安防监控领域有着广泛的应用。
它可以通过人脸识别、行为分析等技术,对监控区域的异常行为进行实时监测和预警,提高安全性和效率。
例如,银行、商场、地铁等公共场所普遍采用机器视觉摄像头进行安防监控。
2. 交通监控机器视觉摄像头在交通监控中起着重要的作用。
它可以实时监测交通流量、违章行为等情况,并通过图像识别和目标检测等技术,对交通事故进行预警和处理。
例如,红绿灯监控、车辆违章抓拍等都是机器视觉摄像头在交通领域的应用案例。
3. 工业自动化机器视觉摄像头在工业自动化中扮演着重要的角色。
它可以通过图像识别和目标检测等技术,对生产线上的产品进行质检、分类和追踪。
例如,机器人视觉系统可以通过摄像头捕捉产品图像,实时判断产品是否合格,并进行自动化处理。
4. 医疗诊断机器视觉摄像头在医疗诊断中有着广泛的应用。
它可以通过图像处理技术,对医学影像进行分析和诊断。
例如,眼底摄影机可用于检测眼部疾病,乳腺X光摄影机可用于早期乳腺癌的检测等。
5. 无人驾驶机器视觉摄像头是无人驾驶技术中的重要组成部分。
它可以通过图像识别和目标检测等技术,对道路、交通标志和其他车辆进行实时监测和识别,从而实现自动驾驶。
例如,特斯拉的Autopilot系统就采用了机器视觉摄像头进行道路监测和自动驾驶控制。
6. 人脸识别机器视觉摄像头在人脸识别领域有着广泛的应用。
它可以通过摄像头捕捉人脸图像,并通过图像识别和特征提取等技术,对人脸进行识别和验证。
例如,手机的人脸解锁功能和人脸支付功能等都是机器视觉摄像头在人脸识别方面的应用案例。
7. 零售业机器视觉摄像头在零售业中有着广泛的应用。
- 1、下载文档前请自行甄别文档内容的完整性,平台不提供额外的编辑、内容补充、找答案等附加服务。
- 2、"仅部分预览"的文档,不可在线预览部分如存在完整性等问题,可反馈申请退款(可完整预览的文档不适用该条件!)。
- 3、如文档侵犯您的权益,请联系客服反馈,我们会尽快为您处理(人工客服工作时间:9:00-18:30)。
由于系统在拾取产品的同时必须还要检测料带上的元件状态,如果同时还要 检测料盘产品,时间势必会增长很多,从而影响到取料分料的速度,因此采用 离线方式提前对料盘产品进行扫描的方式解决了此问题,大大节省了时间以便 进行料带产品的定位和分析。
连接器在线检测视觉集成系统软件(视觉图像分析处理) 检测项目: ● SMT引脚或耳扣(hold down)等共面度; ● 接触端(contact)伸出高度; ● 正位度及漏脚。 性能指标: ● 半自动人工上下料,自动送料;● 检测精度<0.01mm; ● 重复性指标 GRnR<10%。 检测说明: 连接器俗称端子,用于手机、电脑、便携设备等中的连接器,由于装配过程 十分精密,因此设备制造商对连接器的尺寸要求相当高,为了增加产品的质量 和市场竞争力,目前大部分连接器要求采用全检的方式,因此采用视觉设备对 提高产品质量稳定性、减少人力成本有着很大的优势。开发设计的本设备采用 了百万像素相机和远心测量镜头以及针对不同产品采用的组合LED照明方式,软 件核心采用高性能的HexSight视觉软件。采用半自动人工上下料,自动送料和剔除不合格品,并对产品进行过程统计。
每次换料时耐心的将晶圆与电机位置调到最佳,而且每次开始时都需要操作员 手工进行晶片对位。 因为边界定位采用传感器,机器需要操作员不断手工调节 边界传感器位置,较为繁琐。
* 效率较低:由制作工艺本身造成的晶圆上存在相当数量的坏料或空料,传统 的光电传感器识别准确度不高,导致后期成品合格率下降,影响生产效率。
所谓COG(Chip On Glass)技术,指的是运用一种包含金属颗粒的粘性膜(异 方向性导电膜ACF),通过预压将IC芯片邦定在LCD玻璃板上,使IC与LCD玻璃板 之间的线路连通。正如上面谈到的一样,IC芯片面积小,但I/O端数量多。要想 使IC与LCD玻璃板之间的线路很好的连通,就需要对IC和LCD进行非常精确的定 位,保证足够的定位精度。
* 走位不准:因为晶片切割及晶圆贴膜等原因很容易造成晶片在晶圆上位置分 布不均。
* 晶片浪费:晶片在晶圆上呈圆形分布,采用传感器定位边界的方法势必会造 成边界定位不准而致使一些晶片拾取不到,从而在晶圆上残留一些晶片。
* 操作较为麻烦:由于机器以固定步距及方向行走,所以晶圆与电机的水平一 致性要求非常高,极小的角度偏差都会导致累加误差过大,这就要求操作员在
固晶机视觉系统VD100DieBonder采用图像识别技术进行实时定位、分析及导航,有效地避免了上述的 种种问题,使得生产精度,稳定性及效率得到极大的提高。其定位检测部分应 用HexSight视觉软件包,导航部分采用Visual C++进行编程,其定位精度高 ,速度快,一次识别只需10ms左右。
视觉集成系统软件1008(图像分析处理) 检测任务: 精确定位微小Mark点,根据Mark点的位置将IC与玻璃正确对位并贴附。 检测对象: 该系统主要用于电子行业的IC和LCD上的Mark点精确定位 定位精度:0.005mm 定位要求:自动定位并显示对位误差 系统说明:
各种高速度、高精度、体积小、灵活易用的标准和非标准自动识别检测系统, 能在高速状态下准确地测量、定位、辩识及检查产品。本身可以确定检测结果 ,并将处理过程的信息传送给工厂网络中的其它设备。该系统支持多种通信协 议,能直接或通过计算机和其它任何设备进行通讯,而且在现场调试中能方便 地修改和优化参数,功能强大,成熟实用。
应用前景:在包括汽车制造、制药、电子、包装、印刷、烟草、日化、建材、 制币、制卡等在内的几乎所有的现代工业自动化生产中,涉及到各种各样的检 验生产监视和零件识别应用,如汽车零件批量加工,端子尺寸检测,SMT装配, IC的字字符识别系统等等,通常这种带有高度重复性和智能性的工作只能用人 的肉眼来完成,但有些时候,如微小的尺寸要做到精确快速测量,形状匹配,颜 色识别等,人们根本无法用肉眼连续稳定地进行,其他物理传感器也难以有用 武之地。 创视新科技专注于机器视觉检测及全面视觉解决方案的公司,一直致力于机器 视觉自动化的推广,在业内已具有骄人的业绩和口碑,为推动以上工业发展做 出了巨大的努力。
碰焊机(Weld)制卡机
检测内容: 定位晶片及晶片两端的引线中点。
工作要求: 视觉定位平台上的卡片,并实现焊头精确移到位置进行焊接;
系统说明:
整个系统采用工控机控制,核心架构为视觉加运动,机器工作台为一个60CM*60 CM左右的电机机台,正上方则是X、Y方向两轴的电机控制的移动台,焊头和相 机固定在移动台上。工作台上放置的产品大概有32个左右,以4行8列进行排布 。机器工作前先移动到第一行第一列位置,到位后启动拍照,记下两个焊点位 置,随后移动焊针到焊点位置进行焊接。焊完再进行第二个产品定位,以此类 推,直到焊完最后一个回到清洗位置进行焊头的清洗,完成后又回到第一行一 列进行焊接,以此往复。
Tapping(电子元器件上带检测)视觉集成系统软件(视觉图像分析处理) 检测内容: 自动检测识别和定位产品,输出产品的位置信息和是否合格信息,并控制机 械部分自动取料和分料。 检测要求: 对料盘的产品进行自动检测和分类,并根据检测信息设计最优运动控制方案 将产品自动分拣送到流水线上;定位精度:0.01mm;检测速度:50ms/pcs。 系统说明: 检测系统采用上下位机方式分别控制,下位机为实际工作机械控制部分,实 现对机械手等硬件的直接操作;上位机为人机界面及机器视觉检测部分,人机 界面实现人机交互操作,机器视觉检测部分对产品进行取像定位,并根据结果 分析及导航,得出最优的运动路线对产品进行取放。 该设备采用了创视MVC视觉系统,并采用均匀高亮度的LED光源确保整个系统 的光照稳定性,并使用性价比较高的美国COSTAR相机和COMPUTAR百万像素镜头 ,以保证图像的清晰度,软件处理采用高性能的HexSight软件开发包,该软件 平移精度可达1/40亚像素,旋转精度可达0.01度,对于本系统的高精度及快速 定位得以软件保证。
Die Bond(固晶机拾片引导)视觉集成系统软件(视觉图像分析处理) 检测内容: 将晶片(Die)从晶圆(Wafer)上自动取放到料带上,并准确放置。 检测要求:
通过视觉定位和引导,将晶片从晶圆(Wafer)上自动取放到基板上;速度:5 0ms/pcs。
系统说明:
晶圆上的单个晶片面积非常小(约0.078平方毫米),数量极多,且位置不固 定,因此对传统装片机的电机走位精度、工作稳定性和速度提出了非常高要求 。传统装片机存在以下几个重要弊病:
键盘表面缺陷检测视觉集成系统软件(视觉图像分析处理) 检测内容: 检测键盘字符错印、多印、漏印;检测键盘整体偏移;检测键盘上部圆形按 键角度偏移。 检测要求: 要求多印、漏印或表面污渍的面积不能超过0.4mm×mm,整体偏移小于0 .5mm , 按键角度偏移小于1度。 系统说明: 键盘大小为5cm×4cm左右;一直以来机器视觉在生产中的应用主要集中在定位 方面。而在表面检测方面,由于种种原因机器视觉一直都得不到很好的应用, 不难发现导致机器视觉不能很好发挥其功能的原因主要有以下几个方面: 1. 待检产品的表面缺陷不易被检测到; 2. 待检产品的表面缺陷位置不易确定; 3. 待检产品的表面缺陷的大小有一定要求; 4. 待检产品的光线条件要求很高; 5. 待检产品往往印刷的颜色多样。 针对这些问题创视新科技科技有限公司采用合理的光源,设计了封闭的照明 系统,创造了一个光线稳定的相对封闭的工作环境,满足了待检产品对光照条 件的要求。运用 HexSight 视觉开发包,及其独特的Locator定位工具对键盘进 行精确定位,然后用模板处理的方法对图像进行处理,可以将键盘表面的划痕 ,印刷不良,异物等表面缺陷检测。
◆ 焊接时间:10~200ms,2通道; ◆ 焊接压力:30~100g,2通道; ◆ 芯片规格:宽度、长度最大为2.25mm; ◆ 工作台移动范围: Φ15mm。
系统说明:
系统采用黑白CCD系统检测,照明使用高亮度的LED光源,可以保证长时间的稳 定照明,以保证系统稳定的定位精度。
系统核心软件为创视MVC系统, 重复定位精度控制在2微米以下。由于工作环境 的关系,图像噪音比较大,因此采用了HexSight软件的Locator定位器。该工具 对环境光线的影响不敏感,能有效的消除了环境噪音对定位结果的影响,保证 了定位的精度。
系统选用专用的LED光源和百万像素工业镜头,视觉软件运用高性能的HexSight 软件,在定位精度和速度上面给与了良好的保证,设备外形图和操作界面如下 所示:
WireBond(绑定机定位引导和掉线检测)视觉集成系统软件(视觉图像分析处理 )
检测内容:
检测晶片位置,自动引导Bonding机进行焊接。系统兼有焊线掉线检测功能。 检测要求: 该系统用于自动定位及引导中功率半导体器件生产中的引线焊接; 焊线速度:300ms/pcs; 重复定位精度:2 um。 技术规格: ◆ 使用电源:220VAC10%、60Hz、可靠接地,最大消耗功率50W; ◆ 可焊铝丝线径:50~150μm (2~5mil);