窄槽电解加工的实际应用
电解加工的理论及应用

详细描述
电极应具备足够的导电性、耐腐蚀性和加工稳定性。电极的设计需根据加工需求,如工件形状、材料 特性、加工精度等,进行优化。此外,电极的形状和尺寸也会影响加工效果,如电流密度分布、加工 区域等。
加工参数的确定与控制
总结词
加工参数的合理选择和控制对电解加工效果至关重要。
快速原型制造
电解加工可用于快速原型制造,缩短产品开发周期,降低开 发成本。
能源领域
核能设备制造
电解加工在核能设备制造中用于加工特殊材料和复杂结构,提高设备的可靠性 和安全性。
太阳能光伏板制造
电解加工在太阳能光伏板制造中用于高效硅片的切割和表面处理,提高光电转 换效率。
03 电解加工的关键技术
电解液的选择与优化
电解加工的未来展望
随着新材料、新工艺、智能制造等领 域的快速发展,电解加工技术将不断 革新,加工范围和加工精度将得到进 一步拓展和提高。
电解加工技术与其他先进制造技术的 结合将为复杂构件的精密制造提供更 多可能性,为高端装备制造和智能制 造提供有力支撑。
未来电解加工技术将更加注重环保、 节能和可持续发展,推动绿色制造和 智能制造的深度融合。
高加工精度
加工范围广
加工效率高
环境友好
由于电解加工是依靠电化学反 应进行加工的,因此加工过程 中没有机械切削力,可以减少 工具磨损和热变形等误差,实 现高精度的加工。
电解加工可以加工各种硬、脆 、软等难加工材料,如不锈钢 、硬质合金、金刚石等。同时 ,通过调整电解液的成分和加 工参数,可以实现对不同材料 的加工。
微细电解加工
利用微细电极和微细电解液,实现微小尺寸和复杂结构的加工,满足微电子、生物医学 等领域的需求。
μs级可调脉冲电源及微细电解加工应用
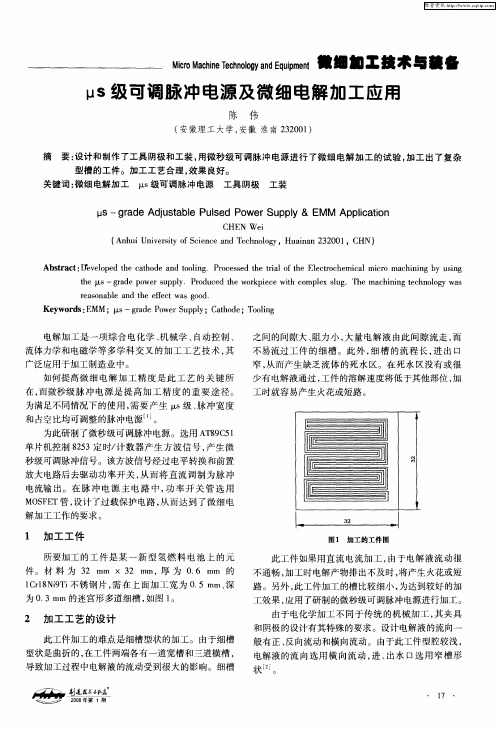
( n u U i r t o ce c n e h o g , u ia 3 0 1 H A h i nv sy f i ea dT c nl y H ann2 2 0 ,C N) e i S n o
Ab t a t D v lp d t e c t o e a d t oi g P o e s d t e t a o e E e t c e c lmir c i i g b sn sr c : e eo e h a h d n o l . r c s e h r l ft l cr h mia c o ma h n n y u i g n i h o
4 微细 电解 ̄ -试验 jr n-
在 D K 10 J3 5 数控电解加工机床上 , 进行了一些微
细 电解 加工 的试验 。
具 ”, 它直接影 响到加 工 尺寸精 度和加 工质 量 。 所 设计 的 阴极 应 当能提供 溶解 表面需 要 的电流分
广泛应 用于 加工制 造业 中 。
之 问 的问隙大 、 阻力 小 , 量 电解 液 由此 间 隙流 走 , 大 而
不易流过工件 的细槽 。此 外 , 细槽 的流程 长, 出口 进 窄 , 而 产生缺 乏 流体 的死 水 区 。在死 水 区没有 或 很 从
少有 电解 液通 过 , 件 的溶 解速 度将低 于其 他部位 , 工 加 工 时就容 易产 生火花 或短 路 。
1 r8 iT 不 锈 钢 片 , 在上 面加 工 宽 为 0 5mm、 ClN9 i 需 . 深
为 0 3mm 的迷宫形 多道 细槽 , 图 1 . 如 。
路 。另外 , 此工件加工 的槽比较细小 , 为达到较好的加 工效果 , 用 了研 制 的微秒级 可调 脉 冲电源进行 加工 。 应 由于电化学加工不 同于传统 的机械加工 , 其夹具 和 阴极 的设 计有 其特 殊 的要求 。设计 电解液 的流 向一
微细电解加工开题报告

微细电解加工开题报告微细电解加工开题报告引言:微细电解加工是一种利用电解液中的电流进行金属加工的技术。
它具有高精度、高效率和低成本的特点,广泛应用于微电子、医疗器械、光学仪器等领域。
本报告旨在探讨微细电解加工的原理、应用以及未来的发展方向。
一、微细电解加工的原理微细电解加工是通过在电解液中施加电流,使阳极上的金属材料溶解,通过电解液中的离子迁移,将溶解的金属离子沉积到阴极上,从而实现对金属材料的加工。
这一过程中,电解液的成分和温度、电流密度以及阳极和阴极之间的距离等因素都会对加工效果产生影响。
二、微细电解加工的应用1. 微电子制造:微细电解加工可以用于制造微电子器件中的导线、电极和微孔等结构。
由于微细电解加工具备高精度和高效率的特点,可以满足微电子器件对尺寸和形状的要求,因此在微电子制造中得到广泛应用。
2. 医疗器械制造:微细电解加工可以用于制造医疗器械中的微型零件,如微针、微刀和微孔等。
这些微型零件在医疗器械中具有重要的功能,而微细电解加工可以实现对这些零件的高精度加工,提高医疗器械的性能和可靠性。
3. 光学仪器制造:微细电解加工可以用于制造光学仪器中的微透镜、微反射镜和微光栅等组件。
这些微型组件对光学性能的要求非常高,而微细电解加工可以实现对这些组件的高精度加工,提高光学仪器的分辨率和精度。
三、微细电解加工的发展方向1. 精度提升:随着科技的不断进步,对微细电解加工的精度要求也越来越高。
未来的发展方向之一是提高微细电解加工的加工精度,以满足更高级别的应用需求。
2. 自动化和智能化:微细电解加工通常需要复杂的操作和调试,未来的发展方向之一是实现微细电解加工的自动化和智能化。
通过引入机器学习和人工智能等技术,可以实现对微细电解加工过程的自动控制和优化。
3. 新材料应用:随着新材料的不断涌现,微细电解加工也将面临更多的材料加工需求。
未来的发展方向之一是研究和开发适用于新材料加工的微细电解加工技术,以推动新材料在微电子、医疗器械和光学仪器等领域的应用。
电解加工的应用

在芯 子底 部 的 周
3 )
它 的特 点 是使 加 工 间 隙
,
边按 画 流 线 图 的 方法 开 设 供 液 孔 ( 图
处 于 高压 腔 中
,
电 解液 分 布较 为 均 匀
,
不易
产 生空 穴
,
加 工更 为 稳 定
有 利于 提 高进 给
,
事 琳耀事
二 l 咬 、
、 、~ ~
速度
匕i
。
对 卡 具 的 密 封 性 和 强 度 要求 高
.
极
,
工 件 接正 极
,
,
使 工 具 和 工件 间 保 持 一 定
,
化量 一 般 聆
5%
,
爬 行量 华
0
3 毫米 0
。
的距 离
并 在 其 间 通 过 高速 电 解 液
,
。
由于 工
( 3 ) 机 床各 部 位 均 应 有 防 腐 措 施
。
,
特
具 不 断 向 工 件 作 直 线移 动
的 形 状 逐 渐 溶解 成 型
,
用 一 定体 积 的
性能 的变 化 来 衡 量
比 重 变化
油 液 所 含各 种 尺 寸 的颗 粒 数 目来 定 量 地 描 述
0
.
05
美 国颗 粒 计 数 法 提 出 油 液 固
3 )
粘度 变化率 (形 ) 酸 值 (毫 克 K o H / 克 ) 水分 ( 形 )
士1 0 ~ 2 0
+ 0
0
. .
5或 1 0
.
体 颗 粒 污 染等 级 标 准 ( 表
行 业 采用
。为 许 多 国 家和05 、1一 般 液 压 传 动 装 置 可 以 采用 该 标
槽盖布在铜电解中的应用

由表 ’ 可见 ! 电解槽覆盖后 ( 阴极铜的蒸气单耗 可降低 !#)以上 ! 且环境温度越低 ( 节能效果越显 著 " 另外 ( 电解槽覆盖后 ( 阴极铜上部由于漂浮阳极 泥引起的长粒子现象消失( 阴极铜质量大幅度提高 "
排除极间短路等一系列操作都必须开 % 启槽盖布 ! 无形中增加了劳动强度 " 目前 ! 用于电解槽覆盖的槽盖布规格主要有三 种 # 单槽窄槽盖布 % 单槽宽槽盖布和多槽槽盖布 ! 其 特点如表 !! 企业应根据实际情况选用 " 表%
’/.#$ !#.&! !".&" $’./ $".$! $0.1 !1.&!/.#!
图!
电解车间液体平衡图
耳暴露在稀硫酸的酸雾中 ! 与未覆盖相比( 吊耳的腐 蚀速度加快 ! 对此 ( 可通过增加吊耳厚度和调整液面 的方法来解决 "
"#"
减少槽盖布开 ! 启操作对槽面管理的影响 电解槽覆盖后 ! 槽面撒水 ! 阴 % 阳极更换 ! 检测 %
!#"
槽盖布的保温效果 分别测量了电解槽覆盖前后槽头和槽尾温度 "
结果见表 & % 表" 槽盖布的保温效果
出液温度 !! 温差!!
’
电解槽覆盖的试验
在铜电解生产过程中 " 蒸气主要用于电解液的
覆盖前
升 温和 阴 $ 阳 极 烫 洗 " 电 解 液 的 热 损 失 主 要 是 电 解 槽面的蒸发和散热 % 为了减少电解液的热损失 " 在 电解车间生产系统进行了槽面覆盖试验 %
! ++ !
槽盖布在铜电解中的应用
李建民
! 洛阳铜加工集团冶炼厂 "河南 洛阳 %)’"+,#
电解加工在航空工业中的应用前景(精)

电解加工在航空工业的应用前景电解加工是近代才被采用的一种新型的加工方法。
我国在 1958年首先在膛线加工中应用,后来逐渐地在深孔、花键孔、链轮、内齿轮、叶片、异形零件和模具制造等的方面推广而来。
如今,电解加工已经是一种成熟的特种加工技术。
它区别与冷加工,热加工,机械加工,而是利用化学能进行加工,完美的将化学工业与机械工业结合起来。
电解加工及其复合加工今年来在航空航天工业的应用越来越多。
电解加工以其加工速度快,便面质量好,不怕材料强、硬、韧个,无宏观机械切削力,工件阴极无损耗,可用同一个成型阴极作单方向送进而成批加工复杂型腔、型面、型孔的等优点, 在航空制造应用领域甚广。
叶片是航空发动机、汽轮机的重要零件。
以前叶片的加工是靠在铣床上用靠模进行铣削,效率非常低,据综合统计,由于航空发动机叶片数量多且难加工,用传统切削方法加工约占整台发动机加工劳动量的 30%以上。
而相对于叶片的几何结构及采用的材料,电解加工却能充分发挥其技术特长。
我国、苏联、英国早在 20世纪50年代末、 60年代初就开始采用电解加工叶片,尽管由于叶片精密锻造、精密铸造、精密辊轧技术的提高有更多的叶片采用精密成形,使电解加工叶片的数量有一些减少,但随着叶片材料向高强、高硬、高韧性方向发展和钛合金、钴镍超级耐热合金的采用,以及超精密、超薄、大扭角、低展弦比等特殊结构叶片的出现,对电解加工又提出了新的,更高的要求,电解加工依然是优选工艺方法之一。
特殊类型的孔加工是电解加工在航天制造中的另一种典型应用, 主要包括难切削材料构件上的深小孔、型孔加工。
如空心冷却涡轮叶片和导向器叶片上的许多小孔 , 特别是深小孔和呈多向不同角度分布的小孔 , 用普通机械钻削方法特别困难 , 甚至不能加工 ; 而用电火花、激光加工又有表面再铸层问题 , 且加工孔深也有限 ;采用电解方法则加工效率、加工质量明显提高 , 加工孔深大大增加 , 还可以采用复合多孔加工方式 , 使加工效率提高几倍、十几倍。
探讨电解铝电解槽制作安装要点及措施

探讨电解铝电解槽制作安装要点及措施摘要:现代化铝电解槽拥有高效和节能的特点,而电解槽的设计就是其中的关键。
铝电解槽的稳定性是铝生产质量的重要保证,电解槽应力变形、磁流热平衡和稳定性也是解决铝电解稳定性的关键之处。
通过物理场设计,应用先进的生产技术与配套设施,将石墨化阴极炭块应用其中,可以有效提高铝电解槽的制作与安装技术水平。
本文重点分析电解铝电解槽有效的安装要点以及措施,提出一定的建议,望有助于铝行业的发展。
关键词:制作安装;电解槽;措施1.电解铝电解槽制作安装设计要点1.1先进的技术应用以下几项技术可以用在铝电解槽安装与制作中:①窄加工面技术。
结合铝电解槽热平衡特点,可以选择300mm和420mm尺寸作为大加工与小加工面宽的铝电解槽尺寸。
这样设计下铝电解槽日产量可以每d提高1.27kg/m2。
②阳极升降技术。
该技术适合用在结构简单、方便制造的三角板滚动移杆结构的阳极升降机构中。
③船形铝电解槽壳技术。
以铝电解槽壳受力情况加以分析,使用最少材料却能满足铝的电解需求,提高铝电解槽壳的强度。
通过有限元分析模型,推出了船形结构,有利于实现侧壁处空气对量,并为企业节省大量钢材。
④腹板梁技术。
在铝电解槽加工安装中,应用腹板梁结构,凭借其自身刚度大、不易变形的特点,能够有效节省钢材,提高铝电解槽的稳定性[1]。
1.2电解槽端头壁板及其附件制作工艺的安装技术要点①下料前对各规格板材进行外观检查,外观有裂缝、缩孔、气泡、重皮、夹渣等缺陷时不得使用。
②下料时以半自动切割及机械裁剪为主,从而保证料边质量。
③端侧板下料长度应在设计长度的基础上考虑焊接缝及调校收缩量。
④端侧板及为带进行弯制时必须在滚床上进行。
起弧切点及落弧切点定位要求准确,弧度应均匀。
⑤弯制壁板上胎具后对准基准点,再进行刚性支撑固定,并且检测壁板不平度。
⑥加筋板、加筋环板、围板等组对时从端头壁板的纵横中心线为基准规线。
⑦加筋板、端部环板、围板焊接时尽量不采用立焊,在需要翻转焊接时,端头壁板及其附件必须与胎具整体翻转。
NEUI铝电解槽阴极铝钢直焊技术开发及应用

7冶金冶炼M etallurgical smeltingNEUI 铝电解槽阴极铝钢直焊技术开发及应用景 伟1,刘剑飞1,董 振1,宋 滨1,班允刚2,刘 靖21.云南宏合新型材料有限公司,云南 红河 652400;2.东北大学设计研究院(有限公司),辽宁 沈阳 110166摘 要:节能降耗不仅仅是企业的经济性问题,而且是关系到企业生存和发展的关键问题。
针对铝电解槽传统焊接工艺技术压接接触压降和焊接焊口压降偏高的缺点,开发了NEUI铝电解槽阴极铝钢直焊焊接工艺技术,与传统焊接工艺技术相比,可将阴极钢棒与铝软带之间的压降降低约10mV左右,按照600kA电流计算,单槽年节约电量约为5.25×104kW·h。
该技术已在多家铝厂得到推广应用。
关键词:铝电解槽;铝刚直焊;节能降耗;压降中图分类号:TF821 文献标识码:A 文章编号:1002-5065(2024)01-0007-3Development and application of NEUI aluminum electrolytic cell cathode aluminum steel direct welding technologyJING Wei 1, LIU Jian-fei 1, DONG Zhen 1, SONG Bin 1, BAN Yun-gang 2, LIU Jing 21.Yunnan Honghe New Material Co. , Ltd. ,Honghe 652400, China;2.Northeastern University Engineering & Research Institute Co. , Ltd., Shenyang 110166, ChinaAbstract: Energy saving and consumption reduction is not only an economic issue of enterprises, but also a key issue related to the survival and development of enterprises. Aiming at the disadvantages of high pressure drop and high pressure drop of the welding joint of the traditional welding technology of aluminum electrolytic cell, the NEUI cathode aluminum steel direct welding technology was developed. Compared with the traditional welding technology, the pressure drop between the cathode steel rod and the aluminum soft strip could be reduced by about 10mV. The annual power saving of a single tank is about 5.25×104kW·h. This technology has been popularized and applied in many aluminum plants.Keywords: aluminum electrolytic cell; Aluminum steel direct welding; Energy saving and consumption reduction; Pressure drop收稿日期:2023-11作者简介:景伟,男,生于1978年,山东泰安人,工程师,本科,研究方向:电解铝技术研发、项目建设和生产管理。
电解法冶金的原理及应用

电解法冶金的原理及应用1. 电解法冶金的原理电解法冶金是一种利用电解现象来分离金属和非金属的方法。
它基于电解质溶液中正负电荷的吸引和排斥作用,通过施加电流使得金属离子在电极上还原成金属,从而实现金属的提取。
电解法冶金的基本原理包括以下几个方面:1.1 电解质溶液电解质溶液是由溶解了金属盐的水或其他溶剂组成的。
在电解质溶液中,金属盐分解成正离子和负离子。
正离子是要提取的金属离子,负离子是要排除的非金属元素。
1.2 电流作用施加外部电流时,正极(阳极)接受电子,金属阳离子在电极上还原成金属;负极(阴极)释放电子,负离子与电子结合形成物质,并从溶液中脱离。
1.3 电解反应在阳极上,金属阳离子被氧化生成金属离子,并释放出电子。
在阴极上,金属离子被还原成金属,与电子结合形成金属。
1.4 应用范围电解法冶金广泛应用于金属提取、镀层制备和电化学合成等领域。
它可以提取多种金属,包括铜、锌、铝等。
电解法还可以用于制备金属镀层,如镀铬、镀金等。
此外,电解法还可以用于电化学合成有机物和制备纯净的化学品。
2. 电解法冶金的应用电解法冶金在各个领域都有广泛的应用。
以下是几个常见的应用领域:2.1 金属提取电解法冶金是提取金属的重要方法之一。
以铜为例,电解法冶金可以用来从铜矿石中提取铜。
首先,将铜矿石破碎并浸泡在硫酸铜溶液中,形成含有铜盐的溶液。
然后,在电解槽中施加电流,使铜离子在阴极上还原成金属铜,从而得到纯铜。
2.2 金属镀层制备电解法冶金可以用于制备金属镀层,如镀铬、镀金等。
这一过程称为电镀。
在电镀过程中,金属离子从电解质溶液中被还原到工件表面,并与工件表面的金属结合形成金属镀层。
电镀可以改善工件的外观、增加耐腐蚀性和硬度。
2.3 电化学合成电解法冶金可以用于电化学合成有机化合物。
通过在电解槽中施加合适的电压和电流,可以引发有机化合物的电化学反应。
这种方法在有机合成中具有重要的应用,可以实现高效、选择性和环境友好的合成路线。
219390898_槽控机控制技术在铝电解生产中的应用研究

2023年 3月上 世界有色金属31机械加工与制造Machining and manufacturing槽控机控制技术在铝电解生产中的应用研究张军杰(青海西部水电有限公司,青海 海东 810800)摘 要:经济和科技的发展推动了电解铝行业的创新发展。
特别是在信息化技术的支持下,电解铝生产技术得到了优化。
本研究以铝电解生产中槽控机控制技术应用为研究对象,首先简要概述了槽控机控制技术,其次对其在铝电解生产中的应用进行深入分析,最后提出了一些槽控机运行优化和维护的措施,旨在提高铝电解生产质量,优化铝电解生产工艺。
关键词:槽控机控制技术;铝电解;生产应用中图分类号:TF821 文献标识码:A 文章编号:1002-5065(2023)05-0031-3Research on the application of the control technology of the tank control machinein the production of aluminum electrolysisZHANG Jun-jie(Western Hydropower Co., Ltd., Haidong 810800, China)Abstract: The development of economy and science and technology has promoted the innovative development of electrolytic aluminum industry. Especially with the support of information technology, the production technology of electrolytic aluminum has been optimized. This study takes the application of cell controller control technology in aluminum electrolysis production as the research object. firstly, it briefly summarizes the cell controller control technology, and then makes an in-depth analysis of its application in aluminum electrolysis production. finally, some measures for operation optimization and maintenance of slot controller are put forward in order to improve the quality of aluminum electrolysis production and optimize the production process of aluminum electrolysis.Keywords: tank control machine control technology; aluminum electrolysis; production application收稿日期:2023-01作者简介:张军杰,男,生于1974年,回族,青海西宁人,高级工程师,硕士,研究方向:金属冶炼技术及管理。
优化铜电解缩,扩槽管理的生产实践

优化铜电解缩,扩槽管理的生产实践优化铜电解缩、扩槽管理的生产实践铜电解缩、扩槽管理是电镀行业的重要流程之一,对于提高生产效率和产品质量至关重要。
下面将从优化铜电解缩、扩槽管理的角度,对相关生产实践进行探讨。
一、优化电解缩1、严把原材料关。
铜电解缩的生产过程需要使用大量的电解粉,因此原材料的质量直接影响到电解缩产品的质量和效益。
在原材料采购过程中,需确保供应商提供的电解粉符合国家质量标准,防止因为原材料不合格导致电解缩的质量下降。
2、严守生产规范。
在铜电解缩的生产过程中,一定要遵守各项生产规范。
例如:控制电流密度、电解时间、电解液的温度和pH值等,以确保电解缩的成品质量和生产效益。
3、加强质量监控。
对于铜电解缩的生产过程,需要进行质量监控。
包括原材料的质量检测、中间产品的检验和成品的检测。
监控过程中发现问题要及时纠正,以确保产品的质量达到标准要求。
二、优化扩槽管理1、严控扩槽条件。
扩槽是铜电解缩过程中的关键环节,它决定了产品的质量和效益。
因此,在扩槽管理过程中,需要严控扩槽条件,确保每个扩槽的电流密度、电解时间、液位、温度等指标达到标准要求。
2、加强设备维护。
对于铜电解缩的扩槽设备,需要进行定期维护和保养。
包括清洗设备、更换损坏的设备件和更换电解缩液等。
维护设备有助于延长其使用寿命,提高生产效率和产品质量。
3、优化生产计划。
铜电解缩的生产过程往往需要安排一定的生产计划。
在生产计划中,需要充分考虑扩槽的利用率和产量。
合理的生产计划可以有效减少生产时间、降低生产成本、提高生产效率。
综上所述,优化铜电解缩、扩槽管理的生产实践是提高生产效率和产品质量的重要措施。
通过严格执行生产规范,加强质量监控、控制扩槽条件、设备维护和优化生产计划等方面的改进,可提高产品质量、降低成本、提高利润和市场竞争力。
阴极复合进给窄缝电解加工精度的试验研究

阴极复合进给窄缝电解加工精度的试验研究王峰;赵建社;干为民;祁璐;田宗军【摘要】为了提高窄缝电解加工的稳定性和定域性,提出了阴极持续直线进给与振动的复合进给方法.基于所研制的振动频率0~50 Hz、振幅0~2 mm、振动波形规律可调的振动装置,开展阴极复合进给的窄缝电解加工试验.结果表明:相比于直线进给,阴极复合进给能够显著提高加工定域性,降低窄缝缝宽;增加振动频率和振幅均有助于降低杂散腐蚀,提高窄缝加工一致性;采用阴极复合进给方法可加工出缝宽为0.305 mm的不同形状的窄缝结构.%In order to improve the stability and localization of narrow-slit electrochemical machining,a cathodic com-pound feeding mode with continuous linear feeding and vibration was proposed,and the corresponding machining experi-ments were carried out on the basis of the improved waveform-adjustable vibration system with a vibration frequency of 0~50 Hz and with a vibration amplitude of 0~2 mm.The results show that,(1 )in comparison with linear feeding, cathodic compound feeding is more effective in improving machin ing localization and reducing narrow slit’s width;(2)high vibration frequency and amplitude both help reduce the stray corrosion and improve the narrow-slit machining consistency;and (3)different shapes of narrow slits with a slit width of 0.305 mm can be machined out by adopting the cathodic compound feeding mode.【期刊名称】《华南理工大学学报(自然科学版)》【年(卷),期】2016(044)003【总页数】7页(P16-22)【关键词】电解加工;复合进给;窄缝结构;加工定域性【作者】王峰;赵建社;干为民;祁璐;田宗军【作者单位】南京航空航天大学机电学院,江苏南京210016;南京航空航天大学机电学院,江苏南京210016;常州工学院江苏省数字化电化学加工重点建设实验室,江苏常州213002;南京航空航天大学机电学院,江苏南京210016;南京航空航天大学机电学院,江苏南京210016【正文语种】中文【中图分类】TG662微小结构(窄缝、窄槽,小孔等)广泛存在于航空航天、光学仪器、生物医疗、家用电器和精密模具等领域中,它们的加工质量对零部件功能实现具有重要影响[1].电解加工相比于机械加工、电火花加工、激光加工等,具有工件表面无残余应力、热影响区和工具阴极不损耗等优点,特别适合于微小结构优质加工; 然而电解加工定域性差、加工过程稳定性不高等问题,一直制约着电解加工技术的广泛应用[2]. 为了进一步稳定提高微小结构电解加工的定域性,近年来国内外学者提出了阴极侧壁绝缘[2]、高频窄脉冲电流[3-5]、阴极平动运动[6]、阴极振动运动等方法.其中阴极(或工件)振动运动的方法适用范围广,加工过程稳定性好,因而国内外学者对此方法开展了较多的研究探索.小孔加工中,Rathod等[7]采用原位制造的直径110 μm的钨阴极,研究了不同电解加工参数对窄缝加工侧面间隙、底面间隙和材料去除效率的影响规律,并优选工艺参数将窄缝侧面间隙控制在55 μm,底面间隙控制在10 μm,材料去除速度为0.25 μm/s;Pan等[8]建立了阴极振动的机械动力学模型,并研究了振动的振幅和频率对小孔电解加工精度的影响,结果表明采用振动方式能够显著提高电解加工的定域性,与高频窄脉冲电解加工的精度已经极为接近;Yang等[9]采用半圆形阴极和超声振动进行小孔的电解加工,显著改善了电解液流场,提高了电解加工的定域性,并在300 μm厚的不锈钢板上加工出孔径76 μm的小孔.窄缝、窄槽加工中,王少华等[10-11]在线状阴极电解线切割加工中,通过增加振动运动,显著改善了加工产物的排出条件,促进了电解液的更新,并采用原位制造的直径分别为2、5和10 μm的阴极加工了形状复杂的微渐开线齿轮和微螺旋窄缝结构;于洽等[12]在微细电解线切割加工中,采用在线阴极进行轴向往复运动的同时叠加工件低频微幅振动的方法,促进了加工间隙内产物排出,工艺试验结果表明工件叠加振动较无振动的切缝更宽、更均匀.阴极制备中,Ghoshal 等[13]采用振动电解加工方法制备了钨阴极,通过研究振动的幅值和频率、电解液浓度和阴极浸入电解液深度等参数对阴极加工的影响,制备了不同形状和尺度的钨阴极.上述振动运动实现基本都采用压电陶瓷式装置,可实现纳米级分辨率的运动,但实现的运动位移较小(一般不大于100 μm)[14],此外振动运动也基本为正弦(或余弦)运动,运动方式也较为单一[15],总体而言,微小结构振动电解加工的研究还不够完善.文中基于自主研制的振动运动规律可调的试验装置系统,研究了阴极持续直线进给叠加振动的复合进给运动对窄缝电解加工精度的影响.1.1 窄缝的复合进给电解加工图1所示为阴极持续直线进给的窄缝电解加工过程,随着阴极的不断进给,电解液对窄缝底部电解产物的冲刷、排出作用逐渐降低,工件阳极电化学腐蚀产生的絮状固体产物将滞留在加工间隙内,甚至吸附在阴极表面,进而使得加工间隙内阻抗增加,极间欧姆压降UR下降;阴极端面生成的氢气泡难以排出,将导致加工间隙内气泡率增加,进而改变电解液的电导率.窄缝加工,端面电解加工速度va可表示为式中,D为脉冲电源占空比(直流电源D=1),η为电解液的电流效率,w为工件材料体积电化学当量,κ为电解液电导率,Δb为端面加工间隙.电解液电导率κ与气泡率β的关系可表示为κ=κ0(1-β)m式中:κ0为电解液固有电导率;m为常数,一般取0.3~2.0[16].由式(2)可知,加工间隙内气泡率的增加,将导致电解液电导率的降低,而电导率的降低和极间欧姆压降的下降,将导致端面电解加工速度的降低,进而随着阴极的持续进给,工件材料的去除将无法进行.此外,受到阴极刚度和可制造性的限制,阴极侧壁常常难以进行可靠绝缘,阴极持续直线进给时工件侧壁往往会产生二次腐蚀,大大降低了窄缝的加工精度.为了稳定提高窄缝的加工精度,在阴极直线进给的同时,叠加与直线进给方向平行的振动运动,研究此阴极复合进给运动对电解加工精度的影响规律.1.2 复合进给运动的合成图2所示为阴极持续直线进给运动与振动运动的合成,其中振动运动为正弦(或余弦)运动,振动运动的平衡位置距阴极端面距离为振幅A,持续直线进给的位移为S1,振动运动的位移为S2,持续直线进给运动的位移S1变化规律为S1=vt阴极振动运动位移S2的变化规律为S2=Asin(ωt+φ)阴极持续直线进给运动与振动运动合成的运动位移S的变化规律为S=vt±Asin(ωt+φ)-A阴极持续直线进给与振动的复合速度fv的变化规律为fv=v±Aωcos(ωt+φ)式中,ω为角速度,φ为振动运动的相位差,t为阴极运动的时间.在阴极持续直线进给运动的同时,叠加与直线进给运动方向平行的振动运动,相当于在阴极持续直线进给的同时,不断高频率、大幅值地规律回退,进而在加工间隙内产生强烈抽吸作用,从而促进电解加工产物的排出及电解液的高速冲刷和更新.1.3 阴极复合进给对窄缝电解加工精度的影响阴极复合进给的窄缝电解加工过程如图3所示,施加的振动运动使端面加工间隙发生周期性变化,阴极快速回退时,加工间隙内电解液压力迅速降低,从而使新鲜的电解液能够进入加工间隙内,促进电解絮状产物和氢气泡的排出,使得工件材料的去除能够持续进行.窄缝加工时,决定加工精度的是侧面间隙Δs,如图4所示,假定阴极持续进给深度h=vt处侧面间隙Δs=x,阴极端面位置处的侧面间隙为x0,底面间隙为Δb,则阴极以相同速度继续进给时间t1后,之前侧面间隙为x位置处的侧面间隙变为x1:阴极以复合进给运动方式继续进给时间t1后,之前侧面间隙为x位置处的侧面间隙变为x2:显然阴极复合进给的窄缝侧面间隙要小于阴极持续直线进给,即持续直线进给与振动的复合运动方式相较于单一的持续直线进给方式,能够提高窄缝的电解加工精度. 如图5所示,复合进给运动中的持续直线进给运动通过交流伺服电机、导轨副和丝杆副实现,振动装置通过滑座与导轨副相连,进而随动于伺服进给装置.图6为振动装置的结构示意图.该装置采用音圈电机作为振动装置的驱动部分;为了实现对音圈电机运动位置的精确控制,选用DC Whistle15/16数字伺服智能驱动器作为音圈电机的驱动器;根据输入的运动轨迹要求,使电机按预定轨迹运动;为了实现振动位置的精确控制,选择分辨率为0.1 μm的RENISHAW数字光栅尺作为位置检测原件;为了实现对音圈电机动子的精确运动导向,将滚珠花键副两端与连接块和导电块相连接,并通过螺栓连接将三者固定,其中连接块设置于音圈电机动子端部,阴极固定于导电块的下端.上述振动装置的定位精度为2 μm、重复定位精度为1 μm,最大负载为9 kg,可实现振动频率0~50 Hz,振幅0~2 mm,以及振动波形的规律可调.3.1 工艺试验准备为了分析阴极直线进给运动和复合进给运动的振动频率、振幅、振动波形对窄缝加工的影响,在其他加工参数不变的条件下(如表1所示),分别进行阴极直线进给试验,直线进给叠加振幅为0.3 mm、频率分别为10、20、30、40和50 Hz的单因素对比试验,直线进给叠加振动频率为30 Hz、振幅分别为0.1、0.2、0.3、0.4和0.5 mm的单因素对比试验,以及直线进给叠加振幅为0.5 mm、振动波形不同的单因素对比试验.工艺试验在自行研制的复合进给电解加工工艺系统上进行(如图7所示).通过分析不同加工参数对窄缝入口缝宽和底部缝宽的影响,研究阴极直线进给和复合进给运动对窄缝加工精度影响规律.3.2 阴极直线进给运动图8为阴极直线进给加工的窄缝结构,窄缝入口处缝宽为0.376 mm,底部缝宽为0.231 mm,侧壁杂散腐蚀较为严重,加工定域性差.由于窄缝加工间隙较小,且加工间隙内电解液冲刷作用较强,阴极侧面难以进行可靠绝缘.由式(7)可知,随着阴极持续直线进给,窄缝的侧壁杂散腐蚀会进一步加剧,缝宽会逐渐增加.为了提高窄缝加工的定域性,研究阴极直线进给叠加振动运动的复合进给运动对窄缝加工精度的影响显得尤为必要.3.3 阴极复合进给运动3.3.1 不同振动频率的影响图9为直线进给叠加振幅为0.3 mm、不同振动频率下的窄缝底部缝宽和入口处缝宽.振动频率在10~35 Hz时,随着振动频率的增加,入口处缝宽和底部缝宽的差值逐步减小,窄缝的侧壁杂散腐蚀逐步降低,加工定域性逐步增强;振动频率超过40 Hz时,随着振动频率的增加,入口处缝宽逐渐增大,而底部缝宽逐渐降低,窄缝侧壁的加工斜度逐步增大,侧壁杂散腐蚀严重;振动频率在35~40 Hz时,窄缝的入口处缝宽和底部缝宽差值较小,窄缝加工的一致性较好.由不同振动频率的窄缝缝宽可知:振动频率低于35 Hz时,随着振动频率的增加;振动运动对加工间隙内电解产物排出、电解液更新的作用逐步增强;振动频率为10 Hz时,窄缝底部由于絮状产物和氢气泡的堆积,电导率相对较低,窄缝入口处电解液冲刷作用较强,电导率较高,因而窄缝入口处和底部电化学溶解速度差异较大,窄缝缝宽一致性较差;振动频率超过40 Hz时,由于阴极振动频率过快,窄缝底部的电解产物还未全部排出又被新鲜电解液重新带入底部加工间隙内,从而导致窄缝底部电化学溶解速度下降,而窄缝入口处由于新鲜电解液的冲刷,电化学溶解速度显著增强,因而窄缝缝宽一致性下降.3.3.2 不同振幅的影响图10为直线进给叠加振动频率为30 Hz、不同振幅振动运动的窄缝底部缝宽和入口处缝宽.随着振幅的增加,窄缝入口处缝宽逐渐降低,窄缝底部缝宽呈先增加后下降的趋势;振幅在0.10~0.35 mm时,随着振幅的增加,入口处缝宽和底部缝宽差值逐渐降低,窄缝侧壁杂散腐蚀减小,加工定域性显著提高;振幅超过0.35 mm时,入口处缝宽和底部缝宽差值趋于稳定.由不同振幅的窄缝缝宽可知,振幅低于0.2 mm时,增加振动运动的振幅,窄缝底部电解产物的排出和电解液更新得到改善,电化学溶解速度加快,窄缝底部缝宽也逐渐增大;当振幅超过0.2 mm后,阴极在窄缝加工间隙停留时间缩短,加工杂散腐蚀显著降低,窄缝底部缝宽也逐渐降低,入口处缝宽和底部缝宽的差值也趋于稳定.3.3.3 不同振动波形的影响图11为振幅为0.5 mm,阴极在窄缝外部停留时间为T1 (正弦运动的波峰)、在窄缝底部停留时间为T2 (正弦运动的波谷)时的振动波形.图12为直线进给叠加图11所对应的不同振动波形的窄缝底部缝宽和入口处缝宽,当T1> 0.045 s、T2<0.025 s 时,随着阴极在窄缝底部停留时间延长,窄缝入口处缝宽和底部缝宽均迅速下降,入口处缝宽和底部缝宽的差值也逐渐降低;0.025 s< T1<0.045 s、0.025 s<T2<0.045 s时,窄缝入口处缝宽和底部缝宽趋于一致,入口处缝宽和底部缝宽的差值也趋于一致;当T1< 0.025 s、T2>0.045 s时,随着阴极在窄缝底部停留时间延长,窄缝入口处缝宽和底部缝宽又逐渐降低.由不同振动波形的窄缝缝宽可知,随着阴极在窄缝底部停留时间的延长,窄缝底部缝宽和入口处缝宽均呈下降趋势,缝宽的一致性也逐渐提高.当T1>0.045 s、T2<0.025 s时,由于阴极在窄缝底部停留时间较短,加工间隙中对电解液的粘性摩擦阻力降低,电解液流速较快,从而窄缝侧面电化学溶解得更快,缝宽较大;当T1<0.025 s、T2>0.045 s时,随着阴极在窄缝底部停留时间延长,加工间隙内的电解产物难以完全排出,使得窄缝侧面电化学溶解速度下降,加工定域性加强,但如果进一步增加阴极在窄缝底部的停留时间,加工间隙内电解液更新会进一步恶化,从而影响电解加工过程的稳定性.由阴极直线进给和复合进给加工试验对比可知,直线进给叠加合理的振动运动能够显著提高窄缝加工的定域性,降低窄缝缝宽,提高窄缝加工一致性;增加振动运动的振动频率,提高振幅,延长阴极在窄缝底部的停留时间均有助于提高加工定域性,降低缝宽,但振动频率过快,振幅过高,阴极在窄缝底部停留时间过长将使电解产物排出和电解液更新恶化,从而导致加工稳定性变差.图13为采用阴极进给速度0.2 mm/min、振幅0.5 mm、T1=0.025 s、T2=0.045 s的优化复合进给运动参数加工的不同形状的窄缝.图13(a)为近似直线形群窄缝结构,经轮廓仪检测得知,窄缝底部缝宽均值为0.235 mm,入口处缝宽均值为0.291 mm;图13(b)为弧形的群窄缝结构,窄缝底部缝宽均值为0.240 mm,入口处缝宽均值为0.305 mm.(1)合理的阴极复合进给运动相较于直线进给运动,能够显著降低加工杂散腐蚀,改善窄缝加工定域性,提高窄缝加工精度.(2)复合进给运动振动频率的增加,可以促进加工间隙内电解液的更新,降低窄缝的缝宽,提高窄缝加工一致性;当振幅一定,振动频率过高时,由于加工间隙内电解产物尚未完全排出,又被重新带入加工间隙,将导致窄缝底部缝宽和入口处缝宽差值增大.(3)复合进给运动振幅的增加,将降低阴极在窄缝内部的停留时间,从而显著降低窄缝侧壁的杂散腐蚀,降低窄缝缝宽,提高窄缝加工的一致性.(4)随着阴极在窄缝底部停留时间延长,在窄缝外部停留时间变短,窄缝底部缝宽和入口处缝宽均呈下降趋势,缝宽的一致性也逐渐提高,但停留时间过长时,加工间隙内电解产物排出和电解液更新将恶化,进而影响加工稳定性.【相关文献】[1] JERZY Kozak,KAMLAKAR P Rajurkar,YOGESH Makkar. Selected problems of micro electrochemical machining [J]. Journal of Materials ProcessingTechnology,2004,149(1/2/3):426- 431.[2] WANG Dengyong,ZHU Zengwei,BAO Jun,et al. Reduction of stray corrosion by using iron coating in NaNO3 solution during electrochemical machining [J]. International Journal of Advanced Manufacturing Technology,2015,7(6):1365-1370.[3] BOXHAMMER M,ALTMANNSHOFER S. Model predictive control in pulsed electrochemical machining [J]. Journal of Process Control,2014,24(1):296-303.[4] LEE E S,BEAK S Y,CHO C R. A study of the characte-ristics for electrochemical micro-machining with ultrashort voltage pulses [J].International Journal of Advanced Manufacturing Technology,2007,31(7):762-769.[5] MITHU M A H,FANTONI G,CIAMPI J. The effect of high frequency and duty cycle in electrochemical micro drilling [J].International Journal of Advanced ManufacturingTechnology,2011,55(9/10/11/12):921-934.[6] 朱荻,曲宁松,RAJURKAR K P,等.电极平动式电解孔加工技术研究 [J].机械工程学报,2001,37(5):105-109.ZHU Di,QU Ning-song,RAJURKAR K P,et al. Investigation on electrochemical machining with the orbital movement of electrode [J].Chinese Journal of Mechanical Engineering,2001,37(5): 105-109.[7] RATHOD V,DOLOI B,BHATTACGARYYA B. Influence of electrochemical micromachining parameters dur- ing generation of microgrooves [J]. International Journal of Advanced Manufacturing Technology,2015,76(1/2/3/4):51-60.[8] PAN Yue,XU Lizhong. Vibration analysis and experiments on electrochemical micro-machining using cathode vibration feed system [J]. International Journal of Precision Engineering and Manufacturing,2015,16(1):143-149.[9] YANG Insoon,PARK Min Soo,CHU Chong Nam. Micro ECM with ultrasonic vibrations using a semi-cylindrical tool [J]. International Journal of Precision Engineering and Manufacturing,2009,10(2):5-10.[10] WANG Shaohua,ZHU Di,ZENG Yongbin,et al. Micro wire electrode electrochemical cutting with low frequency and small amplitude tool vibration [J]. International Journal of Advanced Manufacturing Technology,2011,53(5):535-544.[11] 王少华,朱荻,曾永彬,等.线电极微幅振动电解线切割技术研究 [J].机械工程学报,2010,46(13):172-178.WANG Shao-hua,ZHU Di,ZENG Yong-bin,et al. Investigation on wire electrochemical cutting with micro-tool vibration [J]. Journal of Mechanical Engineering,2010,46(13):172-178.[12] 于洽,曾永彬,张海,等.阳极振动辅助微细电解线切割技术 [J].机械工程学报,2012,48(23):178-183.YU Qia,ZENG Yong-bin,ZHANG Hai,et al. Technolo- gy on anode vibration aided wire electrode micro-electrochemical machining [J]. Journal of MechanicalEngineering,2012,48(23):178-183.[13] GHOSHAL B,BHATTACHARYYA B. Influence of vibration on micro-tool fabrication by electrochemical machining [J]. International Journal of Machine Tools and Manufacture,2013,64:49-59.[14] 谷迎国.压电陶瓷驱动微位移平台的磁滞补偿控制理论和方法研究 [D].上海:上海交通大学,2012.[15] XU Lizhong,Pan Yue. Electrochemical micro-machining using vibrating tool electrode [J]. International Journal of Advanced Manufacturing Technology,2014,75:645-650.[16] 王明环,刘望生,彭伟.螺旋深小孔电解加工间隙多相流场特性及实验研究 [J].兵工学报,2013,34(6):748-753.WANG Ming-huan,Liu Wang-sheng,Peng Wei. Research on flow-filed characteristics of gap multi-phase flow and experiment of electro-chemical machining of spiral deep small hole [J]. Acta Armamentarii,2013,34(6):748-753.。
电解加工在航空制造中的应用及发展
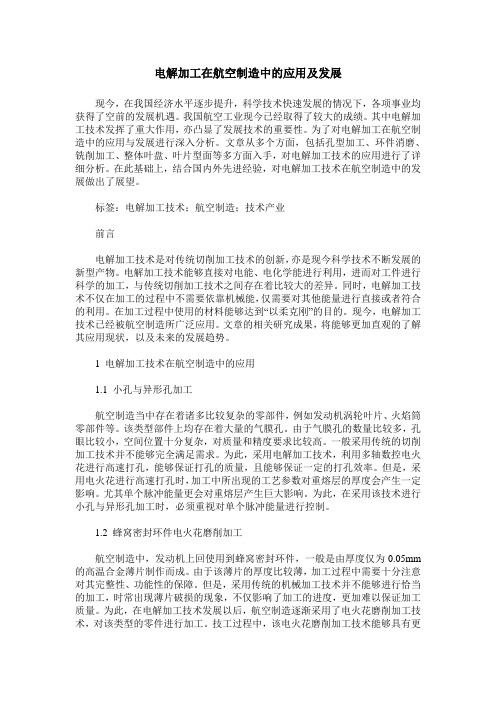
电解加工在航空制造中的应用及发展现今,在我国经济水平逐步提升,科学技术快速发展的情况下,各项事业均获得了空前的发展机遇。
我国航空工业现今已经取得了较大的成绩。
其中电解加工技术发挥了重大作用,亦凸显了发展技术的重要性。
为了对电解加工在航空制造中的应用与发展进行深入分析。
文章从多个方面,包括孔型加工、环件消磨、铣削加工、整体叶盘、叶片型面等多方面入手,对电解加工技术的应用进行了详细分析。
在此基础上,结合国内外先进经验,对电解加工技术在航空制造中的发展做出了展望。
标签:电解加工技术;航空制造;技术产业前言电解加工技术是对传统切削加工技术的创新,亦是现今科学技术不断发展的新型产物。
电解加工技术能够直接对电能、电化学能进行利用,进而对工件进行科学的加工,与传统切削加工技术之间存在着比较大的差异。
同时,电解加工技术不仅在加工的过程中不需要依靠机械能,仅需要对其他能量进行直接或者符合的利用。
在加工过程中使用的材料能够达到“以柔克刚”的目的。
现今,电解加工技术已经被航空制造所广泛应用。
文章的相关研究成果,将能够更加直观的了解其应用现状,以及未来的发展趋势。
1 电解加工技术在航空制造中的应用1.1 小孔与异形孔加工航空制造当中存在着诸多比较复杂的零部件,例如发动机涡轮叶片、火焰筒零部件等。
该类型部件上均存在着大量的气膜孔。
由于气膜孔的数量比较多,孔眼比较小,空间位置十分复杂,对质量和精度要求比较高。
一般采用传统的切削加工技术并不能够完全满足需求。
为此,采用电解加工技术,利用多轴数控电火花进行高速打孔,能够保证打孔的质量,且能够保证一定的打孔效率。
但是,采用电火花进行高速打孔时,加工中所出现的工艺参数对重熔层的厚度会产生一定影响。
尤其单个脉冲能量更会对重熔层产生巨大影响。
为此,在采用该技术进行小孔与异形孔加工时,必须重视对单个脉冲能量进行控制。
1.2 蜂窝密封环件电火花磨削加工航空制造中,发动机上回使用到蜂窝密封环件,一般是由厚度仅为0.05mm 的高温合金薄片制作而成。
激光在电解槽制造上的应用

激光在电解槽制造上的应用激光技术在电解槽制造中的应用近年来,激光技术在各个领域中得到了广泛的应用,其中包括电解槽制造。
激光作为一种高能量、高精度的光束,具有独特的特点和优势,可以在电解槽制造过程中发挥重要的作用。
激光可以被用于电解槽的切割和焊接。
传统的电解槽制造过程中,切割和焊接通常需要采用传统的机械切割和焊接方法,操作繁琐且效率低下。
而激光切割和焊接技术可以通过激光束的高能量和高精度,实现对电解槽材料的快速切割和精确焊接,大大提高了制造效率和质量。
激光还可以用于电解槽的打孔和雕刻。
在电解槽制造过程中,通常需要在槽体中进行打孔和雕刻,以便实现电解液的循环和流动,以及电极的固定。
传统的打孔和雕刻方法往往需要使用机械工具,操作不仅复杂而且容易造成材料的损坏。
而激光打孔和雕刻技术可以通过激光束的高能量和高精度,实现对电解槽材料的精准打孔和雕刻,不仅操作简便,而且避免了材料的损坏。
激光还可以用于电解槽的表面处理。
在电解槽制造过程中,槽体的表面质量对于电解过程的稳定性和效果至关重要。
传统的表面处理方法往往需要使用化学药品或机械磨削,操作不仅繁琐而且对环境有一定的污染。
而激光表面处理技术可以通过激光束的高能量和高密度,实现对电解槽表面的清洁和改性,不仅操作简便,而且无污染,提高了电解槽的使用寿命和效果。
激光技术在电解槽制造中的应用具有重要的意义。
通过激光的切割和焊接、打孔和雕刻、表面处理等技术,可以大大提高电解槽的制造效率和质量,为电解过程的稳定性和效果提供了有力的支持。
相信随着激光技术的不断发展和创新,激光在电解槽制造中的应用将会越来越广泛,为电解槽制造行业带来更加瞩目的成果。
电解原理在工程中的应用

电解原理在工程中的应用1. 什么是电解原理?电解原理是通过电解的方式将化学反应推动到完成的一种方法。
在电解过程中,电流通过电解质溶液(通常是盐溶液或酸溶液),使得溶质离子在阳极和阴极之间转移,从而产生化学反应。
2. 电解原理在工程中的应用2.1 电镀电镀是将一层金属沉积在另一种金属表面的过程。
电解原理在工程中广泛应用于金属电镀过程。
通过电解沉积,可以增加材料的耐腐蚀性、硬度和外观。
常见的应用包括镀金、镀银和镀铜等。
2.2 电解污水处理电解污水处理是一种利用电化学方法去除水中有机物、无机盐和重金属离子的过程。
在电解过程中,带电的金属离子或氧化物会产生化学反应,将污染物转化为无害的物质。
这种方法广泛应用于工业废水处理、农业污水处理以及市政污水处理。
2.3 电解氧气发生器电解氧气发生器是一种通过电解水分解产生氧气的设备。
它利用电解原理将水分解成氢氧气,并将氧气收集起来。
这种设备广泛应用于医疗行业、食品行业以及家用健康领域。
2.4 电解铝生产电解铝是通过电解熔融的铝氧化物来制造的。
电解铝生产是一种经济高效的方式,可以大量生产高纯度的铝。
这种方法广泛应用于铝的生产和加工行业。
2.5 电池电池是一种将化学能转化为电能的装置。
它通过电解原理将化学反应推动到完成,产生电流。
电池是工程中常用的能源供应方式,广泛应用于电子产品、交通工具以及能源存储领域。
2.6 电解退火电解退火是一种通过电解作用去除金属的内应力和表面缺陷的方法。
它在金属加工和制造领域中应用广泛,可以改善材料的性能和形状。
3. 电解原理的优势电解原理在工程中的应用有许多优势:•高效性:电解反应是一种可以迅速完成的化学反应,可以提高生产效率。
•精确性:通过调整电解条件,可以精确控制反应的速度和结果。
•经济性:电解原理是一种经济有效的方法,可以降低生产成本并提高质量。
•环保性:电解原理可以避免使用有害化学物质,对环境友好。
4. 总结电解原理是一种重要的化学原理,广泛应用于工程领域。
高频窄脉冲电解加工电源的研究的开题报告

高频窄脉冲电解加工电源的研究的开题报告题目:高频窄脉冲电解加工电源的研究研究背景和意义:电解加工是一种通过电解液在工件和电极之间形成放电通道,通过电化学反应和热效应进行材料加工的非传统加工技术。
在电解加工过程中,电源是决定加工质量和效率的关键因素之一。
传统的电解加工电源多为直流电源,其加工效率低、加工质量差、工件表面粗糙度大等问题限制了其发展和应用。
针对传统电解加工电源存在的问题,高频窄脉冲电解加工电源应运而生。
与传统电解加工电源相比,高频窄脉冲电解加工电源具有加工效率高、加工质量好、工件表面粗糙度小等优点,适用于高精度、高效率的电解加工。
本研究旨在探究高频窄脉冲电解加工电源的基本原理和加工特性,设计开发高频窄脉冲电解加工电源实验平台并进行实验验证,为高频窄脉冲电解加工电源的应用提供实验基础和理论支撑。
研究内容:本研究将重点开展以下工作:1. 综述电解加工和高频窄脉冲电解加工电源的发展历史和研究现状,分析传统电解加工电源存在的问题。
2. 探究高频窄脉冲电解加工电源的基本原理、工作原理和加工特性,建立数学模型。
3. 设计开发高频窄脉冲电解加工电源实验平台,包括电源模块、控制模块和测量模块等部分,并进行实验验证。
4. 对高频窄脉冲电解加工电源进行性能评估和加工效果评价,比较高频窄脉冲电解加工电源与传统直流电解加工电源的加工效率和加工质量。
研究方法:本研究将采用文献调研、理论分析、数学建模、实验设计和数据分析等方法进行研究。
具体地:1. 综述文献调研:通过查阅相关文献和资料,了解电解加工和高频窄脉冲电解加工电源的历史、发展和研究现状,分析传统电解加工电源存在的问题。
2. 理论分析:基于电化学、机电一体化、数字信号处理等理论,探究高频窄脉冲电解加工电源的基本原理、工作原理和加工特性,建立数学模型,为实验设计提供理论基础和引导。
3. 实验设计:设计开发高频窄脉冲电解加工电源实验平台,包括电源模块、控制模块和测量模块等部分,并进行实验验证,探究高频窄脉冲电解加工电源在加工特性、加工效率、加工质量等方面的表现。