第三章机械加工表面质量
机械加工表面质量控制详述
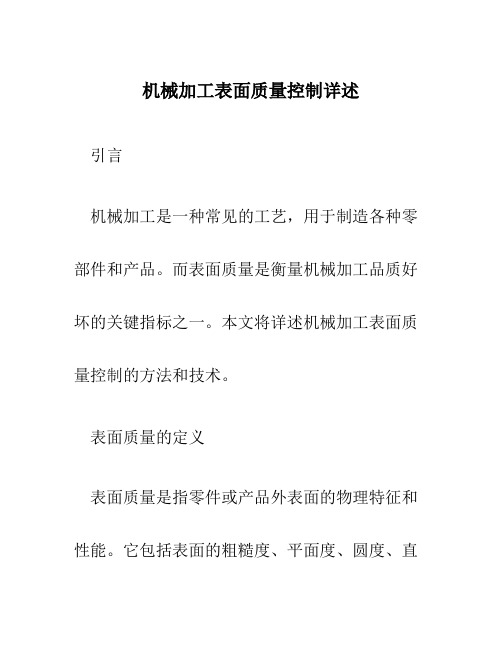
机械加工表面质量控制详述引言机械加工是一种常见的工艺,用于制造各种零部件和产品。
而表面质量是衡量机械加工品质好坏的关键指标之一。
本文将详述机械加工表面质量控制的方法和技术。
表面质量的定义表面质量是指零件或产品外表面的物理特征和性能。
它包括表面的粗糙度、平面度、圆度、直线度、平行度、垂直度等参数。
高质量的表面质量对于提高零件的性能、延长使用寿命和确保装配质量至关重要。
表面质量的评价指标常见的表面质量评价指标包括:1.粗糙度:表面的起伏程度,通常用Ra值(平均粗糙度)或Rz值(最大峰值与最小谷值之差)来表示。
2.平面度:表面在一个平面上的偏差程度。
3.圆度:表面的偏差程度,使其成为一个理想的圆形。
4.直线度:表面在一条直线上的偏差程度。
5.平行度:表面与参考面平行的程度。
6.垂直度:表面与参考面垂直的程度。
表面质量控制的方法预加工表面处理在进行机械加工前,通常需要对工件的表面进行预加工处理。
常见的预加工表面处理方法包括去除氧化层、清除污垢和毛刺、进行平整和硬化处理等。
这些表面处理的目的是为了提前解决一些表面质量问题,使机械加工过程更加顺利。
机床和刀具的选择机械加工过程中,选择适当的机床和刀具也对表面质量的控制起着很大的作用。
不同的机床和刀具具有不同的切削精度和稳定性,因此在选择时需要根据具体的加工要求进行选择。
同时,机床和刀具的定期维护和保养也是保证表面质量的重要环节。
加工参数的优化机械加工过程中的参数选择对表面质量有着直接影响。
例如,切削速度、进给速度、切削深度等参数的选择都会对表面质量产生影响。
根据不同的材料和加工方式,需要进行参数的优化选择,以实现最佳的表面质量。
加工过程的监控与调整在机械加工过程中,通过实时监测切削力、振动和温度等参数,可以及时发现并调整加工中的问题,以确保表面质量的稳定性和一致性。
表面质量的检测方法为了评估机械加工的表面质量,需要使用相应的检测方法。
常见的表面质量检测方法包括:1.视觉检测:通过肉眼观察表面是否有缺陷或异常。
机械加工表面加工质量

由于切屑的崩碎而在加工表面留下许多麻点,使表 面粗糙。
机械加工表面加工质量
(2)切削速度的影响 (3)进给量的影响
加工塑性材料时,切削速度对
表面粗糙度的影响(对积屑瘤和鳞 刺的影响)见如图4-41所示。
此外,切削速度越高,塑性变 形越不充分,表面粗糙度值越小
(1)磨削用量
▪ 砂轮的转速↑ →材料塑性变形↓ → 表面粗
糙度值↓ ;
▪磨削深度↑、工件速度↑ → 塑性变形↑ →表
面粗糙度值↑ ; 为提高磨削效率,通常在开始磨削时采
用较大的径向进给量,而在磨削后期采用较 小的径向进给量或无进给量磨削,以减小表 面粗糙度值。
机械加工表面加工质量
(2)工件材料
•太硬易使磨粒磨钝 →Ra ↑ ; •太软容易堵塞砂轮→Ra ↑ ; •韧性太大,热导率差会使磨
影响显微硬度因素
•塑变引起的冷硬
•金相组织变化引起 的硬度变化
表面物理力学 性能
影响残余应力因素
•冷塑性变形 •热塑性变形 •金相组织变化
影响金相组织变化 因素
•切削热
机械加工表面加工质量
1. 表面层的冷作硬化
(1) 表面层加工硬化的产生
定义:机械加工时,工件表面层金属受到 切削力的作用产生强烈的塑性变形,使晶 格扭曲,晶粒间产生剪切滑移,晶粒被拉 长、纤维化甚至碎化,从而使表面层的强 度和硬度增加,这种现象称为加工硬化, 又称冷作硬化和强化。
机械加工表面加工质量
三、表面层金相组织变化与磨削烧伤
1.表面层金相组织变化与磨削烧伤的产生
切削加工中,由于切削热的作用,在工件的加 工区及其邻近区域产生了一定的温升。
定义:磨削加工时,表面层有很高的温度,当 温度达到相变临界点时,表层金属就发生金相组织 变化,强度和硬度降低、产生残余应力、甚至出现 微观裂纹。这种现象称为磨削烧伤。
2、机械加工表面质量及影响因素

机械加工表面质量及影响因素一、表面质量定义任何机械加工所得的表面,实际上不可能是理想的光滑表面,总是存在一定的微观几何形状误差。
另外,表面材料在加工时受切削力、切削热的影响,也会使原有的物理—机械性能发生变化。
因此,加工表面质量应包括:1、加工表面粗糙度。
是指加工表面的较小间距和微小峰谷的微观几何形状误差。
它主要是由于切削加工过程中的刀痕、切削分离时的塑性变形、刀具与被加工表面的摩擦、工艺系统的高频振动等原因造成的。
2、表面层的物理———机械性能变化。
表面层的材料在加工时,物理—机械性能变化主要有以下三个方面的内容:1)表面层的冷作硬化。
工件在机械加工过程中,表面层金属产生强烈的塑性变化,使表层的强度和硬度都有所提高,这种现象称表面冷作硬化。
2)表面层残余应力。
在切削加工过程中,由于切削变形和切削热的影响,在加工表面会产生残余应力,如果残余应力超过材料的屈服强度,就会产生表面裂纹,表面的微观裂将给零件带来严重的隐患。
3)表面层金相组织的变化。
工件表面经磨削精加工时,磨削产生的高温,一般可达800~1000 ℃,高的磨削温度会烧坏工作表面,使淬火钢件表面退火,引起表层金属发生相变,将大大降低表面层的物理—机械性能。
二、影响表面粗糙度的因素1、切削加工影响表面粗糙度的因素刀具几何形状及切削运动的影响刀具相对于工件作进给运动时,在加工表面留下了切削层残留面积,从而产生了表面粗糙度,残留面积的形状是刀具几何形状的复映,其高度H受刀具的几何角度和切削用量大小的影响。
减小进给量vf、主偏角、副偏角以及增大刀尖圆弧半径,均可减小残留面积的高度。
此外,适当增大刀具的前角,以减小切削时的塑性变形的程度,合理选择润滑液和提高刀具刃磨质量,以减小切削时的塑性变形和抑制刀瘤、鳞刺的生成,也是减小表面粗糙度值的有效措施。
2、工件材料的性质加工塑性材料时,由于刀具对金属的挤压,产生了塑性变形,加之刀具迫使切屑与工件分离的撕裂作用,使表面粗糙度值加大。
3.1表面质量概述及表面粗糙度的影响因素

谢谢大家!
②表面层金属的残余应力的影响
拉伸残余应力将使耐疲劳强度下降;压缩残余应力则使耐疲劳强度提高。
3. 表面质量对耐蚀性的影响 (1)表面粗糙度的影响 表面粗糙度值越大,加工表面与气体、液体接触的面积越大,腐蚀物 质越容易沉积于凹坑中,耐蚀性能就越差。 (2)表面层金属力学物理性质的影响 零件表面层有残余压应力时,能够阻止表面裂纹的进一步扩大,有利 于提高零件表面抵抗腐蚀的能力。 4. 表面质量对零件配合质量的影响 (1) 对于间隙配合表面 原有间隙将因急剧的初期磨损而改变,表面粗糙度越大,变化量就 越大,从而影响配合的稳定性。 (2) 对于过盈配合表面 表面粗糙度越大,两表面相配合时表面凸峰易被挤掉,这会使过盈量 减少,影响配合的可靠性。
(4)表面缺陷 加工表面上出现的缺陷,如砂眼、气孔、裂痕等。
2.表面层金属的力学物理性能和化学性能 由于机械加工中力因素和热因素的综合作用,加工表面层金属的力 学物理性能和化学性能将发生一定的变化,主要反映在以下几方面: (1)表面层金属的冷作硬化
机械加工过程中,工件表面层金属都会有一定程度的冷作硬化,使 表面层金属的显微硬度有所提高。
3.2 影响加工表面粗糙度的工艺因素及其改进措施
3.2.1 切削加工表面粗糙度 其值主要取决于切削残留面积的高度。影响切削残留面积高度的因素 主要有:刀尖圆弧半径r、主偏角kr、副偏角kr’及进给量f等。 车削、刨削时残留面积高 度的计算示意图如图3。其中图 a 是用尖刀切削的情况,切削 残留面积的高度为:
3.2.2 磨削加工后的表面粗糙度 1.几何因素的影响 单纯从几何因素考虑,可以认为:在单位面积上刻痕越多,即通过单位 面积的磨粒数越多,刻痕的等高性越好,则磨削表面的粗糙度值越小。 (1)磨削用量对表面粗糙度值的影响 砂轮的速度越高、工件速度越低、砂轮的纵向进给减小,工件表面的 每个部位被砂轮重复磨削的次数增加,被磨表面的粗糙度值将减小。
机械制造工艺学(王先逵)第三章参考答案(部分)

3-1 机械加工表面质量包括哪些具体内容?机械加工表面质量,其含义包括两个方面的内容:1.加工表面层的几何形貌主要由以下几部分组成:⑴表面粗糙度;⑵波纹度⑶纹理方向⑷表面缺陷2.表面层材料的力学物理性能和化学性能表面层材料的力学物理性能和化学性能主要反映在以下三个方面:⑴表面层金属冷作硬化;⑵表面层金属的金相组织变化;⑶表面层金属的残余应力。
3-2为什么机器零件一般总是从表面层开始破坏的?加工表面质量对机器使用性能有哪些影响?一、机器零件的损坏,在多数情况下都是从表面开始的,这是由于表面是零件材料的边界,常常承受工作负荷所引起的最大应力和外界介质的侵蚀,表面上有着引起应力集中而导致破坏的微小缺陷,所以这些表面直接与机器零件的使用性能有关。
二、加工表面质量对机器的耐磨性、耐疲劳性、耐蚀性、零件配合质量都有影响(一)表面质量对耐磨性的影响1.表面粗糙度、波纹度对耐磨性的影响表面粗糙度值越小,其耐磨性越好;但是表面粗糙度值太小,因接触面容易发生分子粘接,且润滑液不易储存,磨损反而增加;因此,就磨损而言,存在一个最优表面粗糙度值。
2.表面纹理对耐磨性的影响圆弧状、凹坑状表面纹理的耐磨性好;尖峰状的表面纹理由于摩擦副接触面压强大,耐磨性较差。
在运动副中,两相对运动零件表面的刀纹方向均与运动方向相同时,耐磨性较好;两者的刀纹方向均与运动垂直时,耐磨性最差3.冷作硬化对耐磨性的影响加工表面的冷作硬化,一般都能使耐磨性有所提高。
(二)表面质量对耐疲劳性的影响1.表面粗糙度对耐疲劳性的影响表面粗糙度值越小,表面缺陷越少,工件耐疲劳性越好2.表面层金属的力学物理性质对耐疲劳性的影响表面层金属的冷作硬化能够阻止疲劳裂纹的生长,可提高零件的耐疲劳强度。
(三)表面质量对耐蚀性的影响1.表面粗糙度对耐蚀性的影响表面粗糙度值越大,耐蚀性能就越差。
2.表面层金属力学物理性质对耐蚀性的影响表面层金属力学物理性质对耐蚀性的影响当零件表面层有残余压应力时,能够阻止表面裂纹的进一步扩大,有利于提高零件表面抵抗耐蚀的能力。
机械加工表面质量
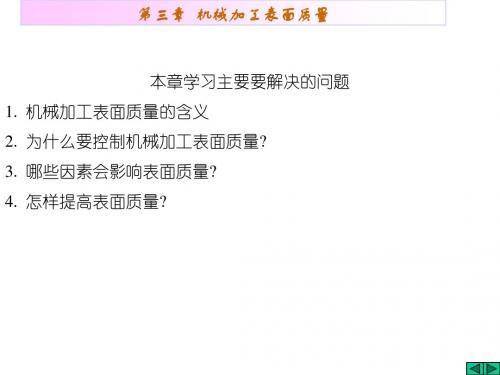
2.表面层物理 力学、化学性能
(1)表面粗糙度 (2)表面波度 (3)纹理方向 (4)伤痕——表面上一些个别位置 上出现的缺陷
(1)表面层加工硬化(冷作硬化)。 (2)表面层金相组织变化。
(3)表面层产生残余应力。
第一节 加工表面质量及其对使用性能的影响
第一节 加工表面质量及其对使用性能的影响
影响表层残余应力的因素
三、表层金属的残余应力——拉应力或者压应力
(一)残余应力产生的原因 1)冷塑性变形——使表层产生压缩残余应力,里层产生拉伸 残余应力。
原因:加工表面受刀具或砂轮磨粒的挤压和摩擦,产生拉伸塑性变形 ,此 时里层金属处于弹性变形状态,切削后里层金属趋于弹性恢复,但受 到已产生塑性变形的表层金属牵制
第三章 机械加工表面质量
本章学习主要要解决的问题 1. 机械加工表面质量的含义 2. 为什么要控制机械加工表面质量? 3. 哪些因素会影响表面质量? 4. 怎样提高表面质量?
第三章 机械加工表面质量
第一节 加工表面质量及其对使用性能的影响
一、机械加工表面质量的含义
1.表面的几何特征
2)热塑性变形——表层产生拉伸残余应力,里层产生压缩残 余应力。
原因:切削和磨削过程中,表层的温度比里层高,表层的热膨胀较大;加 工后零件冷却至室温时,表层金属体积的收缩受到里层的牵制。
影响表层残余应力的因素
3)相变引起的体积变化 金相组织的变化引起表层金属的比容增大,则表层金属将产生 压缩残余应力,而里层金属产生拉伸残余应力; 金相组织的变化引起表层金属的比容减小,则表层金属产生拉 伸残余应力,而里层金属产生压缩残余应力 。
• 提高砂轮速度,降低工件转速,减小纵向进给速度——增大单位面 积的磨粒数
机械加工表面质量--机械加工表面质量对机器使用性能的影响
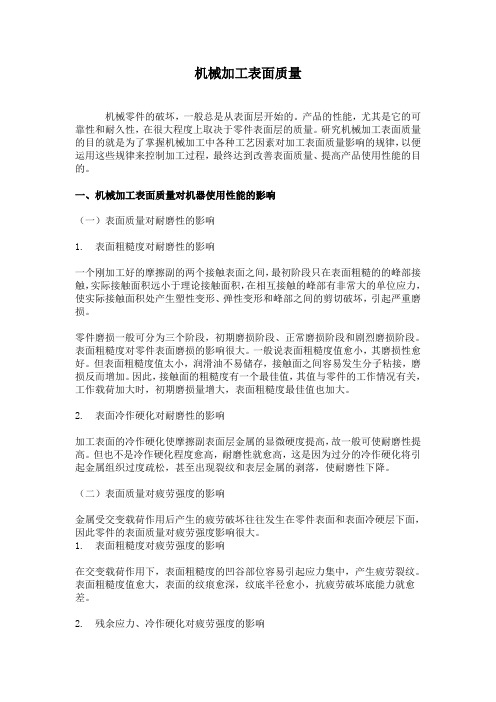
机械加工表面质量机械零件的破坏,一般总是从表面层开始的。
产品的性能,尤其是它的可靠性和耐久性,在很大程度上取决于零件表面层的质量。
研究机械加工表面质量的目的就是为了掌握机械加工中各种工艺因素对加工表面质量影响的规律,以便运用这些规律来控制加工过程,最终达到改善表面质量、提高产品使用性能的目的。
一、机械加工表面质量对机器使用性能的影响(一)表面质量对耐磨性的影响1. 表面粗糙度对耐磨性的影响一个刚加工好的摩擦副的两个接触表面之间,最初阶段只在表面粗糙的的峰部接触,实际接触面积远小于理论接触面积,在相互接触的峰部有非常大的单位应力,使实际接触面积处产生塑性变形、弹性变形和峰部之间的剪切破坏,引起严重磨损。
零件磨损一般可分为三个阶段,初期磨损阶段、正常磨损阶段和剧烈磨损阶段。
表面粗糙度对零件表面磨损的影响很大。
一般说表面粗糙度值愈小,其磨损性愈好。
但表面粗糙度值太小,润滑油不易储存,接触面之间容易发生分子粘接,磨损反而增加。
因此,接触面的粗糙度有一个最佳值,其值与零件的工作情况有关,工作载荷加大时,初期磨损量增大,表面粗糙度最佳值也加大。
2. 表面冷作硬化对耐磨性的影响加工表面的冷作硬化使摩擦副表面层金属的显微硬度提高,故一般可使耐磨性提高。
但也不是冷作硬化程度愈高,耐磨性就愈高,这是因为过分的冷作硬化将引起金属组织过度疏松,甚至出现裂纹和表层金属的剥落,使耐磨性下降。
(二)表面质量对疲劳强度的影响金属受交变载荷作用后产生的疲劳破坏往往发生在零件表面和表面冷硬层下面,因此零件的表面质量对疲劳强度影响很大。
1. 表面粗糙度对疲劳强度的影响在交变载荷作用下,表面粗糙度的凹谷部位容易引起应力集中,产生疲劳裂纹。
表面粗糙度值愈大,表面的纹痕愈深,纹底半径愈小,抗疲劳破坏底能力就愈差。
2. 残余应力、冷作硬化对疲劳强度的影响余应力对零件疲劳强度的影响很大。
表面层残余拉应力将使疲劳裂纹扩大,加速疲劳破坏;而表面层残余应力能够阻止疲劳裂纹的扩展,延缓疲劳破坏的产生表面冷硬一般伴有残余应力的产生,可以防止裂纹产生并阻止已有裂纹的扩展,对提高疲劳强度有利。
影响机械加工表面质量的因素及采取的措施

影响机械加工表面质量的因素及采取的措
施
机械加工表面质量受到多种因素的影响,以下是一些常见因素及采取的措施:
1. 切削参数:
- 切削速度:过高的切削速度可能导致表面粗糙度增加,应根据工件材料和刀具选择适当的切削速度。
- 进给速度:过高的进给速度会增加切削力,可能导致振动和不稳定,影响表面质量,应选择适当的进给速度。
- 切削深度:过大的切削深度可能导致切削力增加和刀具失稳,影响表面质量,应选择适当的切削深度。
2. 刀具选择:
- 刀具材料和涂层:选择适当的刀具材料和涂层,能够提供更好的切削性能和寿命,有利于提高表面质量。
- 刀具尺寸和几何形状:选择合适的刀具尺寸和几何形状,以确保切削稳定性和表面质量。
3. 工件夹持和支撑:
- 夹持方式:选择适当的夹持方式和夹具,确保工件固定稳定,避免振动和变形,有利于提高表面质量。
- 支撑结构:对于柔性或薄壁工件,提供适当的支撑结构,以减少振动和变形,有助于改善表面质量。
4. 切削润滑和冷却:
- 切削润滑剂:使用适当的切削润滑剂,可以减少摩擦和热量,改善切削过程,提高表面质量。
- 冷却剂:使用合适的冷却剂冷却切削区域,防止过热,减少切削力和刀具磨损,有利于提高表面质量。
5. 切削震动和振动控制:
- 刀具和工件的几何匹配:确保刀具和工件的几何匹配,减少切削震动和振动的发生,有助于提高表面质量。
- 切削参数的优化:通过调整切削参数,降低切削震动和振动的发生,有助于改善表面质量。
以上是一些常见的影响机械加工表面质量的因素和采取的措施。
在实际应用中,还需根据具体情况进行综合考虑和调整,以获得满足要求的表面质量。
表面质量概念机械加工表面质量是指零件在机械加工后表面层

2.加工表面质量对零件使用性能的影响
(1)表面质量对零件耐磨性的影响 (2)表面质量对零件疲劳强度的影响 (3)表面质量对零件耐腐蚀性的影响 (4)表面质量对配合性质的影响 (5)表面质量对零件的使用性能其他
方面的影响
(1)表面质量对零件耐磨性的影响
磨损过程的基本规律: 零件的磨损可分为三个阶段,如图1-17所示。 第Ⅰ阶段:(初期磨损阶段)由于摩擦副开始工作时,两个零件
④伤痕 在加工表面的一些个别位置上 出现的缺陷。
在加工表面的一些个别位置上出现的缺 陷。它们大多是随机分布的,例如砂眼、 气孔、裂痕和划痕等。
(2)表面层物理、化学和力学性能
●表面层加工硬化(冷作硬化)。 ●表面层金相组织变化及由此引起的表层金
属强度、硬度、塑性及耐腐蚀性的变化。 ●表面层产生残余应力或造成原有残余应力
表面层的加工硬化对耐磨性的影响
表面层的加工硬化,一般能提高耐磨性0.5~l 倍。这是因为加工硬化提高了表面层的强度, 减少了表面进一步塑性变形和咬焊的可能。但 过度的加工硬化会使金属组织疏松,甚至出现 疲劳裂纹和产生剥落现象,从而使耐磨性下降。 所以零件的表面硬化层必须控制在一定的范围 之内。
表面互相接触,一开始只是在两表面波峰接触,当零件受力时, 波峰接触部分将产生很大的压强,因此磨损非常显著。 第Ⅱ阶段:经过初期磨损后,实际接触面积增大,磨损变缓,进 入磨损的第Ⅱ阶段,即正常磨损阶段。这一阶段零件的耐磨性最 好,持续的时间也较长。 第Ⅲ阶段:由于波峰被磨平,表面粗糙度参数值变得非常小,不 利于润滑油的储存,且使接触表面之间的分子亲和力增大,甚至 发生分子粘合,使摩擦阻力增大,从而进入磨损的第Ⅲ阶段,即 急剧磨损阶段。
机械加工表面质量

第三章机械加工表面质量第一节概述评价零件是否合格的质量指标除了机械加工精度外,还有机械加工表面质量。
机械加工表面质量是指零件经过机械加工后的表面层状态。
探讨和研究机械加工表面,掌握机械加工过程中各种工艺因素对表面质量的影响规律,对于保证和提高产品的质量具有十分重要的意义。
一机械加工表面质量的含义机械加工表面质量又称为表面完整性,其含义包括两个方面的内容:1.表面层的几何形状特征表面层的几何形状特征如图3-1所示,主要由以下几部分组成:⑴表面粗糙度它是指加工表面上较小间距和峰谷所组成的微观几何形状特征,即加工表面的微观几何形状误差,其评定参数主要有轮廓算术平均偏差R a或轮廓微观不平度十点平均高度R z;⑵表面波度它是介于宏观形状误差与微观表面粗糙度之间的周期性形状误差,它主要是由机械加工过程中低频振动引起的,应作为工艺缺陷设法消除。
⑶表面加工纹理它是指表面切削加工刀纹的形状和方向,取决于表面形成过程中所采用的机加工方法及其切削运动的规律。
⑷伤痕它是指在加工表面个别位置上出现的缺陷,如砂眼、气孔、裂痕、划痕等,它们大多随机分布。
2.表面层的物理力学性能表面层的物理力学性能主要指以下三个方面的内容:⑴表面层的加工冷作硬化;⑵表面层金相组织的变化;⑶表面层的残余应力。
二表面质量对零件使用性能的影响1.表面质量对零件耐磨性的影响零件的耐磨性是零件的一项重要性能指标,当摩擦副的材料、润滑条件和加工精度确定之后,零件的表面质量对耐磨性将起着关键性的作用。
由于零件表面存在着表面粗糙度,当两个零件的表面开始接触时,接触部分集中在其波峰的顶部,因此实际接触面积远远小于名义接触面积,并且表面粗糙度越大,实际接触面积越小。
在外力作用下,波峰接触部分将产生很大的压应力。
当两个零件作相对运动时,开始阶段由于接触面积小、压应力大,在接触处的波峰会产生较大的弹性变形、塑性变形及剪切变形,波峰很快被磨平,即使有润滑油存在,也会因为接触点处压应力过大,油膜被破坏而形成干摩擦,导致零件接触表面的磨损加剧。
《机械加工表面质量》习题库

第三章机械加工表面质量一、判断题1.零件的表面粗糙度值越低,疲劳强度越高。
( )2.表面的微观几何性质主要是指表面粗糙度。
( )3.切削加工时,进给量和切削速度对表面粗糙度的影响不大。
( )4.零件的表面粗糙度值越低越耐磨。
( )5.滚压加工是利用淬过火的滚压工具对工件表面施加压力,使其硬度增加,并使表面产生冷硬层和残余压应力,从而提高零件的抗腐蚀能力和疲劳强度。
( )6.滚压加工的目的主要是为了使工件表面上的凸峰填充到相邻的凹谷中,从而减小加工表面的粗糙度。
( )7.表面冷作硬化程度越高,零件的耐磨性越高。
( )二、单项选择题1.磨削加工中,大部分切削热传给了()。
A.机床 B.工件 C.砂轮 D.切屑2.磨削表层裂纹是由于表面层的结果。
()A.残余应力作用 B.氧化 C.材料成分不匀 D.产生回火3.加工过程中若表面层以冷塑性变形为主,则表面层产生( )应力;若以热塑性变形为主,则表面层产生( )应力;。
A.拉应力 B.不定 C.压应力 D.金相组织变化4.机械加工时,工件表面产生波纹的原因有()。
A.塑性变形 B.切削过程中的振动 C.残余应力 D.工件表面有裂纹5.在切削加工时,下列哪个因素对表面粗糙度没有影响?()A.刀具几何形状 B.切削用量 C.工件材料 D.检测方法6.当零件表面层有残余压应力时,()表面层对腐蚀作用。
A.降低了 B.增加了 C.不影响 D.有时会影响7.磨削表层裂纹是由于表面层()的结果。
A.残余应力作用 B.氧化 C.材料成分不匀 D.产生回火8.磨削光轴时、若切削条件相同,哪种工件材料磨削后表面粗糙度小( )?A.20钢; B.45钢; C.铸铁; D.铜。
9.磨削淬火钢时在下列工作条件下可能产生哪种形式的磨削烧伤:(1)在磨削条件(用切削液)( );(2)重磨削条件(不用切削液) ( ),(3)中等磨削条件( ); (4)轻磨削条件( )。
A.淬火烧伤, B.回火烧伤; C退火烧伤; D.不烧伤。
机加工表面质量概论
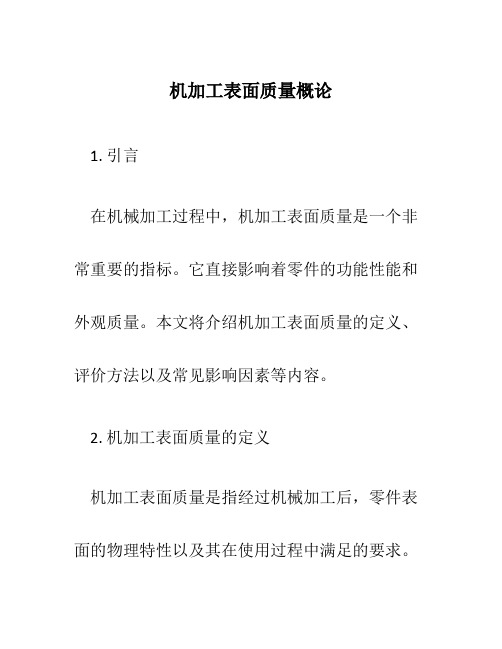
机加工表面质量概论1. 引言在机械加工过程中,机加工表面质量是一个非常重要的指标。
它直接影响着零件的功能性能和外观质量。
本文将介绍机加工表面质量的定义、评价方法以及常见影响因素等内容。
2. 机加工表面质量的定义机加工表面质量是指经过机械加工后,零件表面的物理特性以及其在使用过程中满足的要求。
主要包括表面粗糙度、平整度、光洁度、硬度等指标。
2.1 表面粗糙度表面粗糙度是描述表面几何形态的指标,通常用Ra值表示。
Ra值越小,表面越光滑。
常见的表面粗糙度指标还有Rz、Rmax等。
2.2 平整度平整度是描述表面平整程度的指标。
其中,平面的平整度用直线度表示;曲面的平整度用圆度表示。
常见的平整度指标还有平均平偏度(Sa)、最大平偏度(Sz)等。
2.3 光洁度光洁度是描述表面光滑程度的指标。
通常使用光洁度等级来表达,如镜面光洁度、亚光洁度等。
2.4 硬度硬度是表面材料抵抗压痕的能力。
硬度参数通常用洛氏硬度(HRC)、布氏硬度(HB)等表示。
3. 机加工表面质量的评价方法评价机加工表面质量的方法有许多种。
常见的评价方法包括目测法、触摸法、仪器检测法等。
3.1 目测法目测法是通过肉眼观察进行表面质量评价的方法。
它主要根据表面的光泽、平整度等进行评价。
这种方法简便易行,但主观性较强,评价结果不够准确。
3.2 触摸法触摸法是通过手触表面来感受其质量的方法。
触摸法主要评价表面的平整度和光洁度。
虽然这种方法基本操作简单,但受到个人主观感觉的影响,评价结果有一定的局限性。
3.3 仪器检测法仪器检测法是利用各种精密仪器对零件表面的相关指标进行测量和分析的方法。
常见的仪器包括光学测量仪、形貌仪、硬度计等。
这种方法结果准确可靠,能够客观地评价表面质量。
4. 影响机加工表面质量的因素机加工表面质量受到多种因素的影响。
常见的影响因素包括材料性质、切削速度、进给量、切削液、工具磨损等。
4.1 材料性质材料的硬度、韧性等性质会影响机加工过程中的切削力、热扩散等因素,进而影响工件表面质量。
机械加工表面质量影响因素及改善

2、加工表面层的残余应力
2)表面层残余应力的影响因素 (1)刀具方面 ①刀具几何因素 前角对残余应力有很大影响。图p188 454 ②刀具磨损;图p189 4-55 (2)工件方面 工件材料塑性越大,切削加工后产生的残余拉应力越大。 (3)切削条件方面 切削用量三要素对残余应力影响较大。图p189 4-57 、4-58
高速钢、硬质合金或陶瓷刀具在切削低碳钢、中碳钢等塑
性金属,加工工序中都可能产生鳞刺。会使表面粗糙度加工。 成为塑性金属材料精加工的一个障碍。 在物理因素方面,降低表面粗糙度主要措施,即消除积 屑瘤和鳞刺的措施。
2、切削加工表面粗糙度的产生原因及其控制
4)切削机理的变化:
在挤裂切屑或单元切屑形成的过程中,由于单元切屑 周期性的断裂在切屑表面以下深入,在加工表面上留下挤 裂痕迹而呈现波浪形。在崩碎切屑形成过程中,从主切削 刃处开始的裂纹在接近主应力方向斜着向下延伸,造成加 工表面凹凸不平。p182图4-39 切削刃两侧的工件材料被挤压后因没有侧面的约束力
在精密磨削时不能判断试切时的吃
刀量,很不方便。
(3) 磨削用量的选择
1)提高工件速度和采用小的切深能够有效地减小残余拉应
力和消除烧伤、裂纹等磨削缺陷。
3、 磨削烧伤及磨削裂纹及其控制
2)降低砂轮速度也能得 3)提高砂轮速度的同时相应 提高工件速度,可以避免烧伤。
到残余压应力,但是会影响
生产效率,故一般不常采用。
2、切削加工表面粗糙度的产生原因及其控制
1)理论粗糙度P181:
刀具几何参数中的主偏角、副偏角和刀尖圆弧半径及切削
用量中的进给量是产生理论粗糙度的最基本因素。
Rmax
f cot cot '
机械加工表面质量名词解释

机械加工表面质量名词解释
机械加工表面质量是指通过机械加工(如铣削、车削、磨削等)所制造出来的工件表面的质量特征。
机械加工表面质量有着重要的意义,它直接影响到工件的性能和使用寿命。
因此,人们对机械加工表面质量提出了严格的要求,并制定出一系列的标准来进行评估。
常见的机械加工表面质量名词包括:
1. 粗糙度:是表面波动的一种度量,是表面轮廓中高低峰与表面基准面的平均距离。
它通常用Ra、Rz等参数来表示。
2. 平整度:是表面局部平坦程度的指标,是表面局部平坦面与平坦基准面间的距离差。
它通常用Waviness来表示。
3. 光洁度:是表面的反射能力,是表面镜面反射光线的亮度和光线散射的能力。
它通常用Rt来表示。
4. 凸度:是表面的突出程度的指标,是表面上的突起的最大高度与表面基准面的距离。
它通常用Rp、Rv来表示。
5. 波度:是表面上连续波动的指标,是表面波动的周期和振幅的综
合量。
它通常用Waviness来表示。
以上这些指标是机械加工表面质量中比较重要的一部分,每一个指标都有着自己的标准和要求。
为了确保机械加工表面质量的标准化和规范化,人们制定了一系列的标准,如ISO/DIS 4287、ISO 4288、GB/T 11683等。
这些标准可以帮助人们更加准确地评估和控制机械加工表面质量。
机械加工表面质量第三章
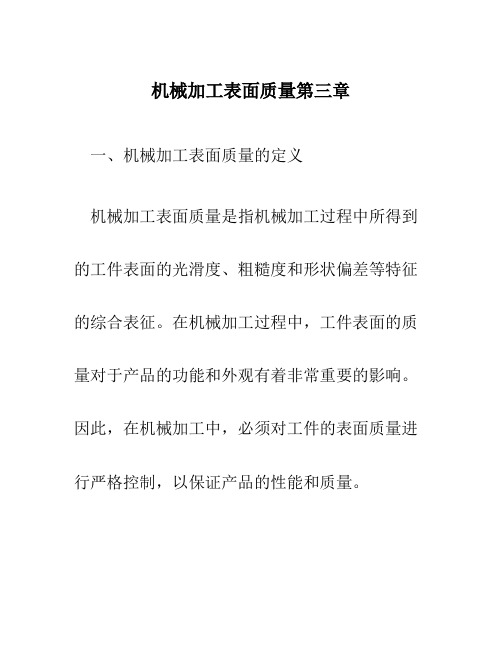
机械加工表面质量第三章一、机械加工表面质量的定义机械加工表面质量是指机械加工过程中所得到的工件表面的光滑度、粗糙度和形状偏差等特征的综合表征。
在机械加工过程中,工件表面的质量对于产品的功能和外观有着非常重要的影响。
因此,在机械加工中,必须对工件的表面质量进行严格控制,以保证产品的性能和质量。
机械加工表面质量的评定主要包括以下几个方面:1.光滑度:表面的光滑度是指表面平整度和光泽度的综合评价。
优良的光滑度可以提高工件的表面美观度,并减少与介质之间的摩擦和粘附。
2.粗糙度:表面的粗糙度是指表面上微小凹凸的高度和间距。
粗糙度对于工件的摩擦、磨损和密封性能有着重要的影响。
粗糙度越小,表面越光滑,摩擦系数越小。
3.形状偏差:形状偏差主要包括平面度、直线度、圆度和轮廓度等。
形状偏差反映了工件表面轮廓与理想轮廓之间的偏离程度。
形状偏差对于工件的密封性能、装配性能和运动精度有着重要的影响。
二、机械加工表面质量的评定方法机械加工表面质量的评定方法主要包括两种:检验法和测量法。
2.1 检验法检验法是通过肉眼或放大镜观察工件表面的外观和质量特征进行评定。
这种方法简单直观,适用于工件表面质量要求不高的情况。
常见的检验法包括目视检查、放大镜检查和样品比对检验等。
2.2 测量法测量法是利用各种测量仪器对工件表面的光滑度、粗糙度和形状偏差等进行定量测量和评定。
测量法具有高精度、高灵敏度的特点,适用于对工件表面质量要求较高的情况。
常见的测量方法包括光学测量、机械测量和电子测量等。
2.2.1 光学测量光学测量是利用光学仪器进行工件表面质量的测量和评定。
常见的光学测量方法有:•白光干涉法:利用白光的干涉原理测量工件表面的形状偏差。
•投影仪测量法:利用投影仪进行工件表面形状偏差的测量。
•激光扫描法:利用激光扫描仪对工件表面进行扫描,获取工件表面形状的三维信息。
2.2.2 机械测量机械测量是利用机械仪器对工件表面质量进行测量和评定。
常见的机械测量方法有:•宏观测量法:利用尺子、卡尺等测量工具对工件表面的尺寸、平面度等进行测量。
机械加工表面质量第三章
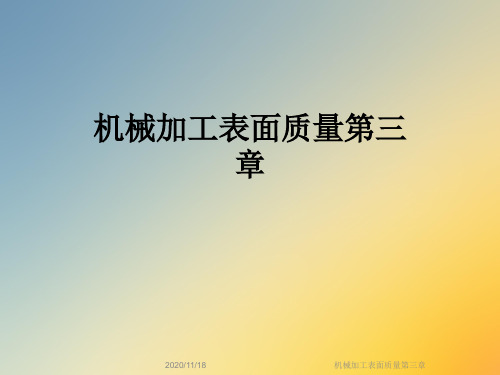
(4)光磨次数 通常磨削时,开始用较大切深提高生
产率,最后用小切深或无进给磨削(光磨),提高表面 粗糙度。
机械加工表面质量第三章
2、磨削时影响表面粗糙度的因素
其他影响 (1)砂轮硬度和工件材料 良好的“自励性”即磨
初期磨损
正常磨损
急剧磨损
实际接触面积只占名义接触 磨损缓慢,紧密接触的两个表面金属
面积的一小部分,实际接触 零件的正 分子间产生较大的亲和力,
部分的压强增大,破坏了润 常工作阶 超过了润滑油膜存在的临
滑油膜而形成局部的干摩擦, 段
界值,造成润滑条件恶化 ,
使其挤裂、破碎、切断等作
磨损加剧。
用增强,磨损增大。
机械加工表面质量第三章
一、概述
1.表面粗糙度与波度
(1)表面粗糙度:表面的微观几何形状误差; (2)波度:介于宏观几何形状误差与表面粗糙度之间的周期性几何形状误差。
L/H>1000称为宏观几何形状误差; L/H = 50~1000,称为波纹度; L/H<50,称为微观几何形状误差,亦称表面粗糙度。
粒磨钝后能及时脱落,露出新的磨粒,能磨出光滑的 表面,且能防止磨削烧伤。工件材料韧性越好,塑性 变形越大,则表面粗糙度越大。
(2)砂轮材料 可分为氧化物、碳化物和高硬磨料。
一般刚类零件用刚玉砂轮磨削,铸铁、硬质合金用碳 化物砂轮磨削,金刚石砂轮可获得极小的表面粗糙度, 但成本较高。
机械加工表面质量第三章
表面完整性
随着科学技术的发展,对产品的使用性能要求越来越高,一 些重要零件需在高温、高压、高速的条件下工作,表面层的任何 缺陷直接影响零件的工作性能,因此在研究表面质量的领域中提 出了“表面完整性”的概念,主要有:
第3章 机械加工表面质量及其控制
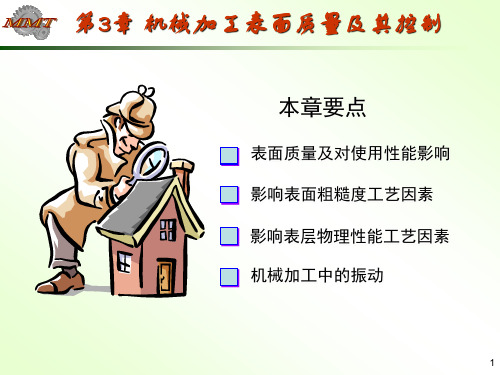
λ RZ RZ
a)波度
b)表面粗糙度
零件加工表面的粗糙度与波度
3
3.1.1 加工表面质量概念
无氧铜镜面三 维形貌及表面 轮廓曲线
4
3.1.1 加工表面质量概念
加工纹理方向及其符号标注
5
3.1.1 加工表面质量概念
表面层金属力学物理性能和化学性能
表面层金属冷作硬化 表面层金属金相组织变化
式中 HV —— 硬化层显微硬度(HV); HV0 —— 基体层显微硬度(HV)。
20
3.3.1 加工表面层冷作硬化
硬度(HV)
影响切削加工表面冷作 硬化因素
切削用量影响
f↑,冷硬程度↑ 切削速度影响复杂(力与热综 合作用结果) 切削深度影响不大
400 v =170(m/min) 300 135(m/min) 100(m/min )
Machining Surface Qபைடு நூலகம்ality and its Influence to Use Performance
2
3.1.1 加工表面质量概念
加工表面的几何形貌
表面粗糙度 — 波长/波高<50 波度 — 波长/波高=50~1000;且具有周期特性
宏观几何形状误差(平面度、圆度等)—波长/波高>1000 纹理方向-表面刀纹形式 表面缺陷-如砂眼、气孔、裂纹等
3.2 影响加工表面质量工艺因 素及其改进措施
Technology Factors Influencing Machining Surface Quality and its Improving
8
3.2.1 切削加工表面粗糙度
残留面积
影响因素:刀尖圆弧半径 rε、主偏角κr、副偏角κ’r 、进给量 f
机械加工表面加工质量

机械加工表面加工质量1. 引言在机械加工过程中,表面加工质量是一个非常重要的指标。
表面加工质量的好坏直接影响到产品的性能和外观。
因此,了解和掌握机械加工表面加工质量的相关知识是非常重要的。
本文将从表面加工质量的定义、影响因素以及常见的提高方法等方面进行探讨,并介绍一些常用的测试方法和评价标准。
2. 表面加工质量定义表面加工质量是指零件经过机械加工后表面的光洁度、平整度、粗糙度以及其他相关指标的好坏程度。
在实际应用中,表面加工质量常常用Ra 值、Rz值以及其他一些参数来表示。
•Ra值:表示零件表面的平均粗糙度,单位为微米。
Ra值越小,表面越光滑。
•Rz值:表示零件表面上峰值与谷值的高度差,单位为微米。
Rz值越小,表面越平整。
3. 表面加工质量的影响因素表面加工质量受到如下因素的影响:3.1 材料性质原材料的性质直接影响着表面加工的质量。
不同材料具有不同的硬度、韧性以及切削性,这些都会对加工后的表面质量产生重要的影响。
3.2 加工参数加工参数包括切削速度、进给速度、切削深度等。
这些参数的选择直接影响着加工后表面的质量。
不恰当的加工参数会导致材料的“剥离”或者“焊着”,从而影响表面质量。
3.3 加工工艺不同的加工工艺对表面加工质量的影响也有所不同。
例如,不同的切削方式(如铣削、车削等)以及不同的刀具形状都会对表面质量产生重要的影响。
3.4 刀具磨损刀具的磨损直接影响着切削质量和表面加工质量。
磨损严重的刀具容易导致表面加工的毛刺、阴刃等问题,从而影响表面质量。
4. 提高表面加工质量的方法为了提高表面加工质量,我们可以采取以下几种方法:4.1 优化加工工艺合理选择加工工艺,根据具体情况进行优化。
比如,对于需要高精度表面加工的零件,可以选择小切削深度、较低的进给速度和切削速度等。
4.2 提高刀具质量选择优质的刀具,减少刀具磨损对表面加工质量的影响。
定期进行刀具的保养和更换,保证刀具的尖锐度和稳定性。
4.3 加工前处理加工前的处理对于提高表面加工质量也非常重要。
- 1、下载文档前请自行甄别文档内容的完整性,平台不提供额外的编辑、内容补充、找答案等附加服务。
- 2、"仅部分预览"的文档,不可在线预览部分如存在完整性等问题,可反馈申请退款(可完整预览的文档不适用该条件!)。
- 3、如文档侵犯您的权益,请联系客服反馈,我们会尽快为您处理(人工客服工作时间:9:00-18:30)。
已加工表 面质量
表面物理力学 性能的变化
§3.1 加工表面质量及其对使用性能的影响
表面的几何形状误差 表面粗糙度:加工表面的微观几何误差,波长与波高比 值小于50。 表面波度:加工表面不平度波长与波高比值在50~1000 的几何形状误差 纹理方向:表面刀纹的方向 伤痕:加工表面个别位置出现的缺陷
因素及改进措施
磨削烧伤与磨削裂纹的控制
内冷却砂轮 选择开槽砂轮
开槽砂轮 a) 槽均匀分布 b)90度内变距开槽
内冷却砂轮
§3.3影响表层材料力学物理性能的工艺因素
及改进措施
表层材料形状变化、体积变化、金相组织变化时 将在表层材料与基体间产生相互平衡的残余应力
表层材料的残余应力
残余应力产生的原因 1)机械加工中表层材料 的塑性变形→外压 内拉 2)磨削温度造成表层材 料的塑性变形→外 拉内压
◆ 调整振动系统小刚度主轴的位置
§3.4 机械加工过程中的振动
◆ 减小切削或磨削时的重叠系数(图4-77)
bd (切削) b
B fa (磨削) B
50
100 150 距离表面深度(μm)
200
前角+→-,残余拉应力↓ γ0=5°,α0==5°,κr=75°,rε=0.8mm,工件:45切削 刀具磨损↑→残余应力↑ 条件:ap=0.3mm, f=0.05mm/r, 不加切削液
◆ 工件材料 材料塑性↑→残余应力↑ 铸铁等脆性材料易产生残余压应力
自激振动的概念
在没有周期性外力作用 下,由系统内部激发反馈 产生的周期性振动 自激振动过程可用传递 函数概念说明
电动机 (能源) 振动位移 X(t) 机床振动系统 (弹性环节)
调节系统 交变切削力F(t) (切削过程)
自激振动闭环系统
能量E E- Q E+
自激振动的特征
自激振动是一种不衰减振动 自激振动的频率等于或接近 于系统的固有频率 自激振动能否产生及振幅的 大小取决于振动系统在每一个 周期内获得和消耗的能量对比 情况。
vc 对残余应力的影响
影响磨削残余应力的工艺因素
热变形和塑性变形对残余应力影响很大 热因素起主导作用→残余拉应力 塑性变形起主导作用→残余压应力 淬火烧伤时,金相组织变 化起主导作用→残余压应力 ◆ 磨削用量的影响
背吃刀量ap、砂轮速度vs 工件的转速vw和进给f1
ap对残余应力的影响
砂轮硬度适中, Ra↓ ;常取中软
砂轮组织适中,Ra ↓ ;常取中等组织 采用超硬砂轮材料,Ra ↓ 砂轮精细修整, Ra ↓
其他影响因素
冷却润滑液
§3.3影响表层材料力学物理性能的工艺因素
及改进措施
表层材料的冷作硬化
◆ 机械加工中产生的塑性变形,使晶格扭曲、畸变、晶 粒间产生滑移,表层材料硬度增加的现象—冷作硬化 ◆机械加工中力的作用强化、热的作用弱化冷作硬化 ◆冷作硬化程度可用三个指标衡量: 表层金属的显微硬度HV 硬化层深度h(微米) 硬化程度N
Hλ λ RZ RZ
a)波度
b)表面粗糙度
零件加工表面的粗糙度与波度
§3.1 加工表面质量及其对使用性能的影响
表层金属的力学物理性能和化学性能变化
表面层金属的冷 作硬化 表面层的残余应 力 表面层金相组织 的变化
切屑
积屑瘤
刀具
切屑的分离和积屑瘤
§3.1 加工表面质量及其对使用性能的影响
表面质量对零件使用性能的影响
0
0.2
0.4 0.6 0.8 磨损高度VB(mm)
1.0
刀具后刀面磨损对冷硬影响
§3.3影响表层材料力学物理性能的工艺因素
及改进措施
3、磨削加工中影响表面冷作硬化的因素
◆ 磨削用量 磨削深度↑→冷硬程度↑ 磨削速度↑→冷硬程度↓(弱化作用加强) 工件转速↑→冷硬程度↑ 500 纵向进给量影响复杂 ◆ 砂轮 砂轮粒度↑→冷硬程度↓ 砂轮硬度、组织影响不显著 ◆工件材料 材料塑性↑→ 冷硬倾向↑ 材料导热性↑→ 冷硬倾向↓
Rmax f
r
f κr Ⅱ b) rε Ⅰ vf
r
Ⅱ a)
Ⅰ
vf
车削时残留面积的高度
Rmax
§3.2影响表面粗糙度的因素及改进措施
切削表面塑性变形和积屑瘤
切削速度影响最大:v = 10~50m/min范围,易产生积 屑瘤和鳞刺,表面粗糙度最差 。
表面粗糙度Rz(μm) 积屑瘤高度 h(μm) 收缩系数Ks 28 24
0
A B C 振幅
自激振动系统能量关系
§3.4 机械加工过程中的振动
消除或减弱产生强迫振动的条件
减小机内干扰力的幅值 调整振源的频率,一般要求:
fn f 0.25 f
x1 2 β x2 1
x2 1
式中 f 和 fn 分别为振源频率和 系统固有频率 隔振
x1 2
两种尾座结构
消除或减弱产生自激振动的条件
重载荷
轻载荷 Ra(μm)
表面粗糙度与初始 磨损量
§3.2影响表面粗糙度的因素及改进措施
切削加工表面的粗糙度
直线刃车刀(图a) 圆弧刃车刀(图b) 影响因素:
f H ctg r ctg r
f2 H 8 r
刀尖圆弧半径 r , 主偏角 kr , 副偏角 kr , 进给量 f
HV HV0 N 100% HV0
§3.3影响表层材料力学物理性能的工艺因素
及改进措施
1、切削加工中影响表面冷作硬化的因素
◆ 切削用量 进给量↑→冷硬程度↑ 切削速度影响复杂(力 与热综合作用结果) 切削深度影响不大 ◆工件材料 材料塑性↑→ 冷硬倾向↑ 材料强度↑→ 冷硬倾向↓
600
3.0
Rz
20
16 12 8 4
400
2.5
Ks
200
2.0
h
0
1.5 0 20 40 60 80 100
切削45钢时切削速度与粗糙度关系
120 140 v(m/min)
其他影响因素:刀具几何角度、刃磨质量,切削液等
磨削加工表面粗糙度影响因素 磨削用量影响
砂轮速度vs↑,Ra↓ 工件速度vw↑,Ra ↑ 砂轮纵向进给f↑,Ra ↑ 磨削深度ap↑,Ra ↑ 光磨次数↑,Ra↓
对耐磨性影响 表面粗糙度值↓→耐磨性↑,但有一定限度 纹理形式与方向:圆弧状、凹坑状较好 适当硬化可提高耐磨性 对耐疲劳性影响
初始磨损量
表面粗糙度值↓ → 耐疲劳性↑ 适当硬化可提高耐疲劳性 对耐蚀性影响 表面粗糙度值↓→耐蚀性↑ 表面压应力:有利于提高耐蚀性 对配合质量影响 表面粗糙度值↑ →配合质量↓
0.8 Ra(μm)
0.0 4
0.0 2 0 细粒度砂轮(WA/GCW14KB)
0.6
0.4 0.2 0 0 0.01 0.02 0.03 0.04 ap(mm)
10
20
30 光磨次数
b)
光磨次数-Ra关系
磨削用量对表面粗糙度的影响
磨削加工表面粗糙度影响因素
砂轮影响
砂轮粒度↑,Ra↓;但要适量
强迫振动的特征
频率特征:与干扰力的频率相同,或是干扰力频率整倍数 幅值特征:与干扰力幅值、工艺系统动态特性有关。当干 扰力频率接近或等于工艺系统某一固有频率时,产生共振
相角特征:强迫振动位移的变化在相位上滞后干扰力一个 φ角,其值与系统的动态特性及干扰力频率有关。
§3.4 机械加工过程中的振动
硬度(HV) 450 400
普通磨削 高速磨削
350
300 0 0.25 0.50 0.75 ap(mm)
磨削深度对冷硬的影响
§3.3影响表层材料力学物理性能的工艺因素
及改进措施
表层金属金相组织变化
◆ 机械加工过程中加工区域温度达到或超过工件材料 相变温度时,金相组织会发生变化(主要指磨削) ◆磨削烧伤(淬火钢) 回火烧伤:磨削温度介于其相变温度723C°和 马氏体转变温度300C°之间→马氏体回火转变 淬火烧伤:磨削温度超过其相变温度723C°+ 急冷→二次淬火 退火烧伤:磨削温度超过其相变温度723C°+ 不冷却→退火 ◆烧伤表现:彩色氧化膜 残余应力 微裂纹
热生残余拉应力的示意图
表层比容增大→外压内拉 3)金相组织变化→体积变化 表层比容减小→外拉内压
影响切削残余应力的工艺因素
残余应力(Gpa)
◆ 切削用量 v↑→残余应力(热应力 起主导作用) ◆ 刀具
0.20 0
vc =7.7m/min vc =86m/min vc =213m/min
-0.20 0
0.05~0.30
一般外压内拉
外压内拉
外压内拉 外压内拉 外压内拉 外压内拉 外拉内压
铣削
碳钢淬硬 钢珠滚压钢件 喷丸强化钢件 渗碳淬火 镀铬
600~1500
400~750 700~800 1000~1200 1000~1100 400
镀铜
外拉内压
200
表面强化工艺 喷丸强化
利用珠丸高速打击工件表面, 使 工件表面产生冷硬层和压应力,提 高疲劳强度 用于强化形状复杂或不宜用其 它方法强化的工件,例如板弹簧 、螺旋弹簧、齿轮、焊缝等
Ra(μm)
0.0 6 粗粒度砂轮(WA60KV) Ra(μm) 1.0 vw = 40(m/min) f = 2.36(m /min) v = 50(m/s) ap = 0.01(mm) s f = 2.36(m /min) ap = 0.01(mm)
0.5
0
30
40
50 60 v s(m/s), vw(m/min) a)
◆ 工件材料
强度↑、导热性↓、塑性↓ → 残余拉应力↑