磷化工艺综述,表面技术课程论文
铝合金磷化工艺的研究

铝合金磷化工艺的研究随着现代工业的快速发展,铝合金作为一种轻质、高强度、耐腐蚀性能优异的材料,被广泛应用于航空航天、汽车制造、建筑工程等领域。
然而,铝合金在实际应用过程中,常常会受到腐蚀的侵蚀,降低了其使用寿命和性能。
为了改善铝合金的抗腐蚀性能,提高其耐用性,研究人员开始探索铝合金磷化工艺。
铝合金磷化工艺是一种通过在铝表面形成磷化物层来提高其抗腐蚀性能的方法。
磷化物层具有较高的硬度、耐磨性和耐腐蚀性,可以有效地保护铝合金表面免受腐蚀的侵蚀。
磷化工艺可以分为化学磷化和电化学磷化两种方式。
化学磷化是将铝合金表面浸泡在含有磷酸盐和其他助剂的溶液中,通过表面化学反应,在铝表面形成一层磷化物覆盖层。
化学磷化工艺简单、成本低廉,可以在常温下进行。
然而,磷化层的厚度和质量受到多种因素的影响,如酸性溶液浓度、温度、浸泡时间等,需要进行严格的工艺控制。
电化学磷化是利用电化学方法,在铝合金表面形成磷化物覆盖层。
通过在溶液中施加电流,使铝表面发生氧化还原反应,生成磷化物层。
电化学磷化可以控制磷化层的厚度和质量,具有较高的工艺可控性。
然而,电化学磷化工艺相对复杂,需要专门的设备和技术支持。
铝合金磷化工艺的研究主要集中在以下几个方面:1. 工艺参数的优化。
磷化工艺的效果受到多种因素的影响,如溶液成分、温度、pH值等。
研究人员通过对不同工艺参数的调整和优化,寻找最佳的磷化工艺条件,以获得最佳的磷化效果。
2. 研究磷化机理。
理解磷化过程中的化学反应机理对于优化磷化工艺具有重要意义。
研究人员通过表面分析技术和材料科学方法,深入探究磷化过程中的物理化学现象,揭示磷化机理,为磷化工艺的改进和控制提供理论依据。
3. 磷化层的性能评价。
磷化层的性能评价是研究铝合金磷化工艺的重要一环。
研究人员通过对磷化层的显微结构、硬度、耐磨性、耐腐蚀性等性能进行测试和分析,评价磷化层的质量和性能,为磷化工艺的应用提供依据。
铝合金磷化工艺的研究对于提高铝合金的耐腐蚀性能,延长其使用寿命具有重要意义。
新型磷化工艺的研究

新型磷化工艺的研究
近年来,随着社会的发展,磷化工艺的应用也变得越来越重要,在人们的生活中也扮
演着重要的角色。
磷化工艺作为一种表面处理的新型技术越来越受到人们的重视,因其具
有无尘、环保和节能等特点,逐渐成为表面处理的新型替代工艺。
磷化工艺具有优良的抗粘附性,制作出的表面具有优异的抗腐蚀性,在材料中可替代
由金属、银或其他有机物制成的塑料,可有效提高产品的使用寿命,具有结构可靠的特点,是制造出坚固耐用的产品的理想表面话方式之一。
磷化工艺的全过程不含污染物,并且具有优异的耐热性能,在高温下也可以保持良好
的粘附性,尤其是磷化工艺处理后产品对金属件具有极强的附着力,可大大减少使用过程
中的漏水、渗漏等现象,可大大提高产品的使用寿命。
与火花喷涂一样,磷化工艺也可以满足客户不同的抗腐蚀要求。
磷化层表面本身具有
优良的抗腐蚀性,能有效抵御空气中的氧化剂,原料中的腐蚀剂等污染物的侵蚀,能防止
产品的损耗,更有利于减少成本。
磷化工艺在防腐、保养、耐高温表面处理和抗蚀等领域的应用正得到越来越多的应用,大大增强了工业应用的可靠性和安全性,受到人们的重视。
今后,推广和研究新型磷化工艺,将迎来更多的应用。
磷化工艺

5 试验部分
为了研究含 3 种阳离子的磷化配方得到的磷化膜的结构及组成,对低碳钢样板( 6" × 4" )用实际的磷化厂条件(表 1 ) 处理,在车身磷化时随车一起进行磷化步骤,而在车身进入 CED 槽前将样板取下。磷化膜混合使用各种技术进行表征, 即用 SEM 、 XRD 及 EDX 分别测定涂层形态及粒径、晶相及涂层组成。
磷化处理工艺流程

磷化处理工艺流程
《磷化处理工艺流程》
磷化处理是一种常见的金属表面防腐处理方法,适用于各种金属材料,尤其是钢铁制品。
通过磷化处理,可以形成一层均匀、致密的磷化膜,保护金属表面免受腐蚀和氧化,从而延长金属制品的使用寿命。
下面将介绍磷化处理的工艺流程。
首先,进行表面预处理。
包括去油、脱垢和除锈等步骤,以确保金属表面光洁、干净。
这一步骤对后续的磷化处理非常重要,因为表面的油污、污垢和锈斑会影响磷化膜的形成和质量。
接着,进行磷化处理。
将经过表面预处理的金属制品浸入磷化液中,通过化学反应形成磷化膜。
磷化液通常由磷酸盐、氯化物和激发剂等物质组成,根据不同的金属材料和要求,磷化液的配方也有所不同。
然后,进行水洗和中和处理。
将磷化处理后的金属制品进行水洗,去除残留的磷化液和杂质。
随后进行中和处理,以中和磷化液中的残余酸碱物质,防止对环境造成污染。
最后,进行干燥和涂油处理。
将经过磷化处理的金属制品进行干燥,去除水分。
然后进行涂油处理,将表面覆盖一层防腐蚀的油漆或蜡质,增强抗腐蚀性能。
总的来说,磷化处理工艺流程包括表面预处理、磷化处理、水洗和中和处理、干燥和涂油处理等步骤,通过这些步骤可以形
成均匀、致密的磷化膜,保护金属制品的表面免受腐蚀。
磷化处理不仅提高了金属制品的使用寿命,也对环境友好,是一种常用的金属表面处理方法。
磷化处理工艺
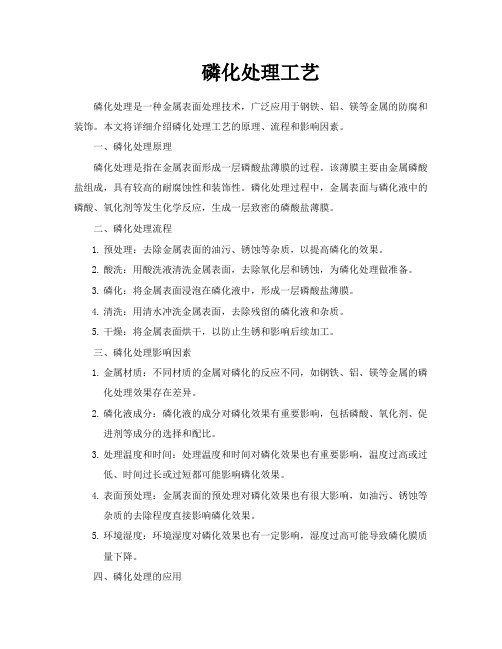
磷化处理工艺磷化处理是一种金属表面处理技术,广泛应用于钢铁、铝、镁等金属的防腐和装饰。
本文将详细介绍磷化处理工艺的原理、流程和影响因素。
一、磷化处理原理磷化处理是指在金属表面形成一层磷酸盐薄膜的过程。
该薄膜主要由金属磷酸盐组成,具有较高的耐腐蚀性和装饰性。
磷化处理过程中,金属表面与磷化液中的磷酸、氧化剂等发生化学反应,生成一层致密的磷酸盐薄膜。
二、磷化处理流程1.预处理:去除金属表面的油污、锈蚀等杂质,以提高磷化的效果。
2.酸洗:用酸洗液清洗金属表面,去除氧化层和锈蚀,为磷化处理做准备。
3.磷化:将金属表面浸泡在磷化液中,形成一层磷酸盐薄膜。
4.清洗:用清水冲洗金属表面,去除残留的磷化液和杂质。
5.干燥:将金属表面烘干,以防止生锈和影响后续加工。
三、磷化处理影响因素1.金属材质:不同材质的金属对磷化的反应不同,如钢铁、铝、镁等金属的磷化处理效果存在差异。
2.磷化液成分:磷化液的成分对磷化效果有重要影响,包括磷酸、氧化剂、促进剂等成分的选择和配比。
3.处理温度和时间:处理温度和时间对磷化效果也有重要影响,温度过高或过低、时间过长或过短都可能影响磷化效果。
4.表面预处理:金属表面的预处理对磷化效果也有很大影响,如油污、锈蚀等杂质的去除程度直接影响磷化效果。
5.环境湿度:环境湿度对磷化效果也有一定影响,湿度过高可能导致磷化膜质量下降。
四、磷化处理的应用1.防腐:磷化膜具有较高的耐腐蚀性,可用于钢铁、铝、镁等金属的防腐处理。
例如,在建筑、船舶、汽车等领域,磷化处理被广泛应用于金属结构的防腐保护。
2.装饰:磷化膜具有较好的装饰性,可用于金属表面的美化处理。
例如,在电子产品、家具等领域,磷化处理被广泛应用于产品的外观装饰。
3.耐磨:磷化膜还具有较好的耐磨性,可用于提高金属表面的耐磨性能。
例如,在机械零件、工具等领域,磷化处理被广泛应用于提高产品的耐磨性能。
4.粘合:磷化膜还可以作为粘合剂使用,将不同金属材料粘合在一起。
浅谈钢管防腐的磷化处理工艺
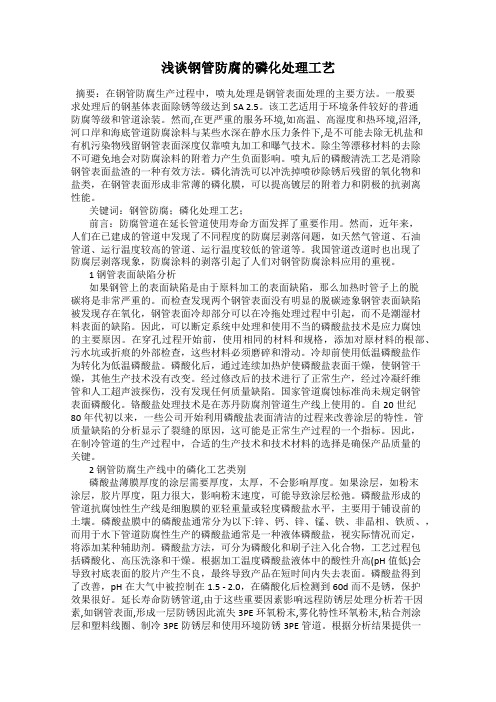
浅谈钢管防腐的磷化处理工艺摘要:在钢管防腐生产过程中,喷丸处理是钢管表面处理的主要方法。
一般要求处理后的钢基体表面除锈等级达到SA 2.5。
该工艺适用于环境条件较好的普通防腐等级和管道涂装。
然而,在更严重的服务环境,如高温、高湿度和热环境,沼泽,河口岸和海底管道防腐涂料与某些水深在静水压力条件下,是不可能去除无机盐和有机污染物残留钢管表面深度仅靠喷丸加工和曝气技术。
除尘等漂移材料的去除不可避免地会对防腐涂料的附着力产生负面影响。
喷丸后的磷酸清洗工艺是消除钢管表面盐渣的一种有效方法。
磷化清洗可以冲洗掉喷砂除锈后残留的氧化物和盐类,在钢管表面形成非常薄的磷化膜,可以提高镀层的附着力和阴极的抗剥离性能。
关键词:钢管防腐;磷化处理工艺;前言:防腐管道在延长管道使用寿命方面发挥了重要作用。
然而,近年来,人们在已建成的管道中发现了不同程度的防腐层剥落问题,如天然气管道、石油管道、运行温度较高的管道、运行温度较低的管道等。
我国管道改道时也出现了防腐层剥落现象,防腐涂料的剥落引起了人们对钢管防腐涂料应用的重视。
1 钢管表面缺陷分析如果钢管上的表面缺陷是由于原料加工的表面缺陷,那么加热时管子上的脱碳将是非常严重的。
而检查发现两个钢管表面没有明显的脱碳迹象钢管表面缺陷被发现存在氧化,钢管表面冷却部分可以在冷拖处理过程中引起,而不是潮湿材料表面的缺陷。
因此,可以断定系统中处理和使用不当的磷酸盐技术是应力腐蚀的主要原因。
在穿孔过程开始前,使用相同的材料和规格,添加对原材料的根部、污水坑或折痕的外部检查,这些材料必须磨碎和滑动。
冷却前使用低温磷酸盐作为转化为低温磷酸盐。
磷酸化后,通过连续加热炉使磷酸盐表面干燥,使钢管干燥,其他生产技术没有改变。
经过修改后的技术进行了正常生产,经过冷凝纤维管和人工超声波探伤,没有发现任何质量缺陷。
国家管道腐蚀标准尚未规定钢管表面磷酸化。
铬酸盐处理技术是在苏丹防腐剂管道生产线上使用的。
自20世纪80年代初以来,一些公司开始利用磷酸盐表面清洁的过程来改善涂层的特性。
磷化工艺流程范文

磷化工艺流程范文磷化工艺流程是指将金属表面通过一系列的处理工艺,在表面形成一层致密、均匀且粘附力强的磷化膜的过程。
磷化膜具有良好的抗磨蚀性、耐腐蚀性和附着力,广泛应用于金属防腐、防锈和油漆前处理等领域。
下面将详细介绍磷化工艺流程的步骤。
第一步:清洗磷化前的金属表面需要进行彻底的清洗,以去除表面的油污、污垢和氧化物等杂质。
常用的清洗方法有碱洗、酸洗和溶剂洗。
碱洗用来去除油污和污垢,酸洗用来去除氧化物,溶剂洗用来去除有机污染物。
清洗的目的是为了保证磷化效果的均匀性和粘附力。
第二步:脱脂在清洗完表面后,还需要进行脱脂处理,以去除残存的油污和有机物。
常用的脱脂方法有溶剂脱脂和碱脱脂。
溶剂脱脂适用于对有机物较多的表面,而碱脱脂适用于去除表面的油脂。
第三步:酸洗酸洗是指将金属表面浸泡在酸性溶液中,以去除氧化物和其他有机酸的方法。
常用的酸洗液有硫酸、盐酸和磷酸等。
酸洗的时间、温度和浓度会直接影响磷化膜的形成和质量,需要根据不同金属的要求进行调整。
第四步:磷化经过前面的处理后,金属表面即可进行磷化处理。
常用的磷化方法有化学磷化和电解磷化。
化学磷化是将金属表面浸泡在含有磷化剂的溶液中,在一定的时间和温度条件下,使磷化剂进行氧化还原反应,从而生成磷化膜。
电解磷化是在电解液中施加电流,使金属表面发生离子交换反应,从而实现磷化。
磷化的时间和温度也需要按照具体情况进行调整。
第五步:中和磷化后的金属表面会残留一些未反应的磷化剂和酸性成分,需要通过中和的方式将其中和。
中和剂一般为碱性物质,常用的有氢氧化钠或氢氧化钙等。
中和的目的是使金属表面达到中性或微碱性的状态,并去除残留的有害物质。
第六步:清洗中和后的金属表面需要再次进行清洗,以去除残留的中和剂和其他杂质。
清洗的方法和前面的清洗步骤相同。
第七步:干燥最后一步是将磷化后的金属表面进行干燥处理。
常用的干燥方法有自然干燥和烘干。
自然干燥是将金属表面置于通风的地方,让其自然蒸发水分。
磷化工艺技术

磷化工艺技术磷化工艺技术是一种将金属表面覆盖上一层磷化膜的工艺,常用于金属防腐、增加金属表面硬度等方面。
下面是对磷化工艺技术的一些详细介绍。
磷化膜是一种由金属磷酸盐组成的覆盖在金属表面的一层化学膜层。
磷化膜具有很高的耐磨性、耐蚀性和防腐性,可以有效地保护金属表面,延长其使用寿命。
同时,磷化膜还可以增加金属材料的硬度,改善其表面质量。
磷化工艺技术分为化学磷化和电化学磷化两种。
化学磷化是通过将金属材料浸泡在含有磷酸盐和氯化盐的溶液中,利用化学反应在金属表面形成磷化膜。
电化学磷化是在电解质溶液中,将金属材料作为阳极,在施加电流的情况下,在金属表面上形成磷化膜。
磷化工艺技术的优点主要体现在以下几个方面:首先,磷化膜具有较高的耐磨性和耐腐蚀性,可以有效地保护金属材料;其次,磷化膜的形成过程简单,不需要复杂的设备和工艺步骤,成本较低;再次,磷化膜可以增加金属材料的硬度,提高其表面质量和使用寿命;最后,磷化膜可以增加金属材料的涂装附着力,使涂层更加牢固。
然而,磷化工艺技术也存在一些问题。
首先,磷化膜的厚度很难控制,在磷化过程中容易产生不均匀的情况。
其次,磷化过程需要一定的时间,不能够实时完成,导致生产周期较长。
此外,磷化溶液中的磷酸盐和氯化盐对环境有一定的污染。
为了解决这些问题,各个行业对磷化工艺技术进行了不断的改进和研究。
研究人员通过调节磷化溶液的组成和浓度,优化磷化工艺参数,提高磷化的效果和一致性。
此外,还发展了一些新的磷化工艺技术,如有机磷化、浸泡磷化等,以满足不同行业对磷化膜的需求。
总之,磷化工艺技术是一种重要的表面处理工艺,可以为金属材料提供保护和改良。
随着科技的不断进步和需求的不断增加,磷化工艺技术将会不断发展,更好地满足社会的需求。
磷化工艺及技巧范文

磷化工艺及技巧范文磷化是一种通过在金属表面形成磷化物层来提高金属材料性能的表面处理方法。
磷化可以增强金属材料的耐腐蚀性能、润滑性能和磨损性能,同时还能提高金属材料的表面硬度和抗疲劳性能。
下面将介绍一些磷化工艺及技巧。
1.表面处理:在进行磷化之前,必须对金属表面进行适当的处理,以保证磷化层与金属基材之间的结合力。
表面处理的方法包括去油、除锈和机械处理。
去油可以使用溶剂或碱性清洗剂进行,除锈可以使用酸性溶液进行,机械处理可以通过打磨或喷砂等方法进行。
2.磷化溶液的制备:磷化溶液的制备是磷化工艺的关键环节。
一般情况下,磷化溶液是由磷酸盐、氧化剂、络合剂和助剂等组成的。
其中,磷酸盐是磷化溶液的主要成分,可以使用磷酸、亚磷酸或磷酸二氢钠等作为磷酸盐;氧化剂的主要作用是提供氧气,常用的氧化剂有过氧化氢、亚硝酸盐和氯酸盐等;络合剂的作用是增强磷化反应的速度和均匀性,可以使用氯化铵或柠檬酸等络合剂;助剂的作用是改善磷化层的性能,可以使用聚合物或胶体等助剂。
3.磷化操作条件的控制:在进行磷化操作时,需要严格控制磷化溶液的温度、浸泡时间和搅拌速度等操作条件,以确保磷化层的质量。
通常情况下,磷化温度在60-90摄氏度之间,浸泡时间在5-20分钟之间,搅拌速度一般为100-200转/分钟。
4.磷化层的改性:通过添加一些化学添加剂,可以改善磷化层的性能。
例如,添加硝酸盐可以增加磷化层的硬度;添加聚合物可以增强磷化层的附着力和抗磨损性能;添加颜料可以改变磷化层的颜色等。
5.磷化后的处理:在磷化之后,需要对金属材料进行进一步处理,以增加磷化层的抗氧化性能和耐蚀性能。
常见的处理方法包括沉积一层金属膜、电沉积或热处理等。
总之,磷化是一种重要的金属材料表面处理方法,可以显著改善金属材料的性能。
在进行磷化工艺时,需要注意表面处理、磷化溶液的制备、操作条件的控制、磷化层的改性以及磷化后的处理等方面的技巧。
通过合理选择和控制这些因素,可以得到质量良好的磷化层,提高金属材料的使用寿命和性能。
磷化处理工艺介绍及其目前行业应用状况

磷化处理工艺介绍及其目前行业应用状况磷化工艺介绍:磷化是指把金属放入含有锰、铁、锌的磷酸盐溶液中进行化学处理,使金属表面生成一层难溶于水的磷酸盐保护膜的方法,所形成的磷酸盐保护膜称之为磷化膜。
磷化工艺应用:磷化处理要应用于钢铁表面磷化,有色金属(如铝、锌)工件也可应用磷化。
磷化的作用:涂装前磷化的作用:1、增强涂装膜层(如涂料涂层)与工件间接合力。
2、提高装饰性。
3、提高涂装后工件工作表面涂层的腐蚀性。
非涂装磷化的作用:1、提高工作的耐磨性。
2、令工件在机加工过程中具有润滑性。
3、提高工作的腐蚀性。
有无磷化涂层耐腐蚀对比:有磷化和无磷化处理的同一涂层进行盐雾试验,其结果是防腐蚀能力相差大约一倍。
可见磷化等前处理对涂层的防锈能力和金属的防护能力起着较重要的作用。
磷化的一般工艺流程:除油—>水洗—>除锈—>水洗—>表调—>磷化—>水洗—>烘干—>后处理磷化前除油的目的:磷化前除油的目的在于清除掉工件表面的油脂、油污。
优质的磷化膜只有在去油污除彻底的工件表面才能形成,因为油污残留在工件表面,不仅会严重阻碍磷化膜的生长,而且会影响涂膜的附着力、干燥性能、耐腐蚀性能等。
磷化前除锈的目的:磷化前除锈的目的在于磷化膜不能在锈层或氧化皮上生长。
在加工过程中,其表面的氧化皮和铁锈必须进行化学清洗处理,使金属制品露出基体,更有效地提高磷化处理效果。
磷化前表调的目的:表调又称表面调整,通过调整,可以改善工件表面的微观状态,从而改善磷化膜外观,结晶细小,均匀,致密,进而提高涂膜性能,以及提高磷化速度。
为什么磷化工艺现在逐步没有了磷化废水其中包含大量的有害因子,且具有较强的腐蚀性,容易对环境产生一定的危害。
如果不加治理直接排放,会腐蚀灌渠和建筑物;排入水体,会改变水体的酸碱度,废液中的含磷量会使水体出现大量藻类植物,让河流生出蓝藻,干扰并影响水生植物的生长和渔业生产;排入农田,会改变土壤的性质,使土壤酸化或盐碱化,严重危害农作物的生长;酸碱原料的流失也是一种浪费。
论文总结-磷化

论文总结-磷化磷化一、前言磷化作为一种表面化学处理方法,是指将金属表面与含磷酸二氢盐的酸性溶液接触,通过化学与电化学反应形成一种稳定的、不溶性的无机化合物膜层的过程,这层膜称之为磷化膜。
其主要作用在于给基体金属提供防腐蚀保护、用于膜前打底、提高覆膜层的附着力与防腐蚀能力及在金属加工中起减摩润滑作用等。
磷化技术广泛用于车辆,船舶,轻工,化工,机械,电器及国防等领域,其处理方法由最初的纯浸渍法发展到喷淋法、锟除法以及浸喷混元法的自动化生产;其体系由单一金属体系(铁)带今天的多元体系(铁,锌,锰,镍,钙);添加剂也从无到有,改善了磷化膜的质量,提高了成膜速度;黑色金属的黑化和磷化相结合,在金属应用和推广价值。
二、磷化分类根据磷化液所用的磷酸盐分类有:磷酸锌系、磷酸铁系、磷酸锰系。
此外还有在磷酸锌中加钙的锌钙系, 在磷酸锌中加铜、加镍的三元体系磷化等。
根据磷化的温度分类有:高温(80 ℃以上)磷化、中温(50 ~70 ℃)磷化和低温磷化(40 ℃以下)。
按磷化施工法分类有:喷淋式磷化、浸渍式磷化、喷渍结合式磷化、涂刷型磷化。
按磷化膜的质量分类有:重量型(7. 5 g /m2以上)、中量型(4. 3 ~7. 5 g /m2 )、轻量型(1. 1 ~4. 3 g /m2 )和特轻量型(0. 3 ~1. 1 g /m2 )。
三、磷化成膜机理磷化主要有以下过程:(1)金属的溶解过程即金属与磷化液中的游离酸发生反应:M +H3PO4 =M(H2 PO4 )2 +H2↑(2)促进剂的加速过程为:M(H2 PO4 )2 +Fe +[ O] →M3 (PO4 )2 +FePO由于氧化剂的氧化作用, 加速了不溶性盐的逐步沉积, 使金属基体与槽液隔离, 会限制甚至停止酸蚀的进行。
(3)磷酸及盐的水解磷化液的基本成分是一种或多种重金属的酸式磷酸盐, 其分子式为Me(H2PO4)2, 这些酸式磷酸盐溶于水, 在一定浓度及pH值下发生水解, 产生游离磷酸:Me(H2PO4 )2 =M eHPO4 +H3 PO43MeHPO4 =Me3 (PO4 )2 +H3PO4H3PO4 = H2PO4- +H+ = HPO42- +2H+ =PO43-+3H+由于金属工件表面的H+浓度急剧下降, 导致磷酸根各级离解平衡向右移动,最终成为磷酸根。
金属磷化工艺技术

金属磷化工艺技术金属磷化是一种常见的工艺技术,主要用于金属表面的防腐和改善其物理性能。
金属磷化不仅可以延长金属的使用寿命,还可以提高其耐磨性、耐腐蚀性和附着力。
金属磷化的工艺主要包括清洗、酸洗、磷化和涂漆四个步骤。
首先是清洗,清洗是金属磷化过程中的关键步骤之一。
清洗的目的是去除金属表面的油污、污垢和氧化物,使金属表面干净,以便后续的处理。
常见的清洗方法有机械清洗、化学清洗和电解清洗等。
选择适当的清洗方法可以根据金属表面的性质和工艺要求来确定。
其次是酸洗,酸洗是金属磷化过程中的关键步骤之二。
酸洗的目的是利用酸溶液将金属表面的氧化物和锈蚀物溶解掉,以便后续的磷化处理。
常用的酸洗液有盐酸、硫酸和磷酸等。
不同的金属材料需要使用不同的酸洗液,以便去除不同种类的污垢。
然后是磷化,磷化是金属磷化过程中的关键步骤之三。
磷化的目的是在金属表面形成一层磷化物膜,能够提高金属的耐腐蚀性和附着力。
磷化方法有热磷化和冷磷化两种,其中热磷化使用高温磷酸盐溶液,而冷磷化则使用低温磷酸盐溶液。
选择适当的磷化方法可以根据金属表面的性质和工艺要求来确定。
最后是涂漆,涂漆是金属磷化过程中的最后一步。
涂漆的目的是为了保护金属表面,进一步提高其耐腐蚀性和附着力。
涂漆一般采用喷涂或者浸涂的方式进行,使用的涂料可以是有机涂料或者无机涂料。
选择适当的涂料可以根据金属材料的特性和实际使用环境来确定。
金属磷化工艺技术的应用非常广泛,可以用于钢铁、铝合金、镁合金等金属材料的表面处理。
金属磷化后的材料不仅表面平整光滑,而且具有较好的防腐性能和耐磨性能,可以大大延长金属的使用寿命。
总之,金属磷化是一种重要的工艺技术,通过清洗、酸洗、磷化和涂漆四个步骤可以使金属表面达到更好的防腐效果和物理性能。
金属磷化工艺技术的应用可以有效延长金属的使用寿命,提高其耐腐蚀性和附着力,具有广阔的市场前景。
表面处理黑色磷化工艺

表面处理黑色磷化工艺嘿,朋友们!今天咱来聊聊这表面处理黑色磷化工艺。
你说这玩意儿就像是给金属穿上了一层神秘的黑衣,让它们变得与众不同。
想象一下,金属就像个光溜溜的小孩,啥保护都没有。
这时候黑色磷化工艺就闪亮登场啦!它就像个超级化妆师,给金属化个美美的妆,让它们变得又酷又耐用。
那这工艺是咋操作的呢?其实啊,就跟做菜似的。
得先把金属洗得干干净净的,可不能有一点脏东西,不然这“妆容”可就花啦!然后呢,把它放到专门的溶液里泡个澡,这一泡可就有大变化喽。
慢慢地,金属表面就会形成那层神秘的黑色磷化膜。
你可别小看这层膜,它的作用可大了去了。
它就像给金属穿上了一层坚固的铠甲,能防锈、耐磨,让金属能经得住时间的考验。
就好比一个勇敢的战士,有了坚固的盔甲才能在战场上冲锋陷阵呀!而且这黑色磷化工艺还挺好玩的呢!你看,那些原本普通的金属,经过这么一处理,一下子就变得有个性了。
这不是很神奇吗?咱生活中好多东西都用到了它呢,像一些工具啦、零件啦。
你说要是没有这黑色磷化工艺,那这些金属得多容易受伤啊!说不定用不了多久就锈迹斑斑,没法用啦。
那多可惜呀!在操作的时候可得注意一些细节哦,就像炒菜要掌握火候一样。
溶液的浓度啦、温度啦、时间啦,都得把握好。
要是不小心弄错了,那可就出不了好效果啦。
咱中国的工匠们可厉害啦,他们对这黑色磷化工艺那可是了如指掌。
他们就像神奇的魔法师,能把普通的金属变得闪闪发光。
这就是咱中国人的智慧呀!所以说啊,这表面处理黑色磷化工艺可真是个了不起的东西。
它让金属变得更有价值,更耐用。
咱得好好珍惜这门技术,让它为我们的生活带来更多的便利和美好。
这就是我对黑色磷化工艺的看法,你们觉得呢?。
磷化线的介绍

磷化线的介绍全文共四篇示例,供读者参考第一篇示例:磷化线是一种常用的冶金工艺,在金属表面对磷进行热处理,使其与金属表面反应生成合金化合物,从而提高金属的表面硬度、耐磨性和耐腐蚀性的一种工艺。
磷化线的工艺过程简单,成本低廉,广泛应用于汽车、航空航天、电子、机械制造等领域。
磷化线的工艺流程包括清洗、脱脂、酸洗、磷化、中和和干燥等步骤。
待磷化的金属件需要经过清洗和脱脂处理,去除表面的油污和杂质,以保证磷化效果。
然后将金属件放入酸洗槽中进行酸洗处理,去除金属表面的氧化物和锈蚀层。
接着,将金属件浸入磷化槽中,与含磷化剂的溶液进行反应,生成磷化层。
磷化过程中,金属表面的铁原子与磷元素形成化合物,提高了金属的表面硬度和耐腐蚀性。
磷化完成后,金属件需要经过中和和干燥处理,最终得到具有优良性能的磷化金属件。
磷化线处理后的金属件表面光泽度高,颜色均匀,具有较好的抗氧化性和耐酸碱性。
磷化层可以有效防止金属表面的腐蚀和磨损,延长金属件的使用寿命。
磷化线处理后的金属件还具有良好的润滑性能,适用于需要经常移动或摩擦的零件。
磷化线广泛应用于汽车制造领域,如发动机缸套、连杆、曲轴、传动轴等零部件的表面处理。
磷化后的汽车零部件表面硬度高,耐磨性好,可有效减少零部件在使用过程中的磨损和损坏,提高汽车的整体性能和可靠性。
磷化线还用于航空航天领域的航空发动机零部件、轴承、涡轮叶片等的表面处理,提高零部件的耐高温、耐腐蚀性能,确保航空器的安全性和可靠性。
磷化线是一种简单、经济实用的金属表面处理工艺,具有显著的提高金属表面性能和使用寿命的优势。
随着科技的发展和工业的进步,磷化线的应用领域将不断扩大,为各行业的发展提供更多的可能性和保障。
第二篇示例:磷化线是一种常见的材料表面处理技术,通过在金属表面形成一层富含磷的化合物,以提高金属件的耐腐蚀性、耐磨性和耐热性等性能。
磷化线广泛应用于汽车、航空航天、机械制造等领域,其工艺简单、成本低廉,效果显著,受到广泛关注和应用。
磷化处理工艺分析

磷化处理工艺分析磷化处理工艺分析把钢管放入含有磷化液中进行化学处理,使金属表面生成一层难溶于水的磷酸盐保护膜的方法,叫做磷化。
本项目在磷化时采用磷酸二氢锌(浓度为0.5%)为主要成分和硝酸锌(浓度为0.5%)作为催化剂的混合溶液为磷化液。
形成的膜由两种物相组成:磷酸锌【Zn3(PO4)2·4H2O】和磷酸铁锌【Zn2Fe(PO4)2·4H2O】。
企业定期添加损耗量,无翻缸废液产生。
(1)脱脂废液在对组件磷化前要进行脱脂处理,其中脱脂废液产生量为5t/周,即215t/a,根据同类企业调查脱脂废液水质情况:CODcr为2000mg/L,油类浓度为200mg/L,废水中CODcr产生量为1kg/周,即0.43t/a;油类产生量为0.1kg/周,0.043t/a。
废水经污水处理站处理后达标排放。
(2)脱脂清洗废水在对组件脱脂后要进行清洗,脱脂清洗废水排放量为10t/d,即3000t/a。
根据同类企业调查脱脂清洗废水水质情况:CODcr浓度为150mg/L,油类浓度为15mg/L,废水中CODcr产生量为1.5kg/d,即0.45t/a;油类产生量为0.15kg/d,即0.045t/a。
废水经污水处理站处理后达标排放。
(3)磷化废液组件喷漆前要进行磷化处理,在磷化槽里进行,磷化原液与水的比例为1:39。
磷化废液2个月更换1次,每次为5t,即30t/a。
根据同类企业调查磷化废液水质情况:CODcr为4000mg/L,油类浓度为300mg/L,Zn浓度为400mg/L,磷酸盐浓度为200mg/L,则废水中CODcr产生量为20kg/2个月,即0.12t/a;油类产生量为1.5kg/2个月,即0.009t/a,Zn产生量为2kg/2个月,即0.012t/a;磷酸盐产生量为1kg/2个月,即0.006t/a。
废液经污水处理站处理后达标排放。
(4)磷化清洗废水磷化后需进行清洗,清洗废水产生量为10t/d,即3000t/a。
化工类论文(磷化工艺)

201年化学工程专业毕业设计(论文)题目:金属表面前处理——除油、除锈姓名:学号:指导老师:完成时间:目录前言..................................................................... ..3摘要 (5)1 概述 (6)1.1 磷化的定义及原理 (6)1.1.1磷化的定义 (6)1.1.2磷化的原理 (6)1.2 磷化的现状及发展状况 (6)1.2.1 磷化的现状 (6)1.2.2 发展趋势 (7)1.3 磷化的作用及用途 (8)1.3.1磷化的作用 (8)1.3.2磷化的用途 (8)1.4 磷化的分类 (9)1.4.1 磷化的分类方 (9)1.4.2 磷化处理的分类方法 (10)1.4.3磷化前的预处理 (11)2 磷化膜的形成机理及结构 (15)2.1 形成机理 (15)2.2 磷化膜的结构组成 (15)2.3 涂磷磷化膜的要求 (16)2.4 磷化膜质量评定项目与方法 (16)3 磷化液 (18)3.1 基本成膜物质 (18)3.2 磷化促进剂 (18)3.2.1 氧化促进剂 (18)3.2.2 金属离子促进剂 (19)3.2.3 复合促进剂 (20)3.3 磷化助剂 (20)3.4 常温磷化液的配方 (20)3.5 磷化液性能 (21)4 磷化工艺流程 (22)4.1 磷化实验过程 (22)4.2 影响磷化处理的因素 (22)4.2.1 基材的影响 (22)4.2.2 促进剂的影响 (23)4.3 磷化工艺质量 (25)4.4 磷化工艺中的问题 (26)参考文献 (27)前言磷化是一种化学与电化学反应形成磷酸盐化学转化膜的过程,所形成的磷酸盐转化膜称之为磷化膜。
磷化的目的主要是:给基体金属提供保护,在一定程度上防止金属被腐蚀;用于涂漆前打底,提高漆膜层的附着力与防腐蚀能力;在金属冷加工工艺中起减摩润滑使用。
磷化处理工艺应用于工业己有90多年的历史,大致可以分为三个时期:奠定磷化技术基础时期、磷化技术迅速发展时期和广泛应用时期。
- 1、下载文档前请自行甄别文档内容的完整性,平台不提供额外的编辑、内容补充、找答案等附加服务。
- 2、"仅部分预览"的文档,不可在线预览部分如存在完整性等问题,可反馈申请退款(可完整预览的文档不适用该条件!)。
- 3、如文档侵犯您的权益,请联系客服反馈,我们会尽快为您处理(人工客服工作时间:9:00-18:30)。
磷化工艺综述摘要:磷化工艺过程是一种化学与电化学反应形成磷酸盐化学转化膜的过程,所形成的磷酸盐转化膜称之为磷化膜。
磷化的目的主要是:给基体金属提供保护,在一定程度上防止金属被腐蚀;用于涂漆前打底,提高漆膜层的附着力与防腐蚀能力;在金属冷加工工艺中起减摩润滑作用。
关键字:磷化工艺;磷酸盐;磷化膜1 前言 磷化过程包括化学与电化学反应。
不同磷化体系、不同基材的磷化反应机理比较复杂。
虽然科学家在这方面已做过大量的研究,但至今未完全弄清楚。
在二十世纪80年代以前,曾以一个化学反应方程式简单表述磷化成膜机理[1]:8Fe+5Me(H2PO4)2+8H2O+H3PO4→Me2Fe(PO4)2·4H2O(膜)+Me3(PO4)·4H渣)+8H2↑ Me为Mn、Zn等,Machu等认为,钢铁在含有磷酸及磷酸二氢盐的高温溶液中浸泡,将形成以磷酸盐沉淀物组成的晶粒状磷化膜,并产生磷酸一氢铁沉渣和氢气。
这个机理解释比较粗糙,不能完整地解释成膜过程。
随着对磷化研究逐步深入,当今,各学者比较赞同的观点是磷化成膜过程主要是由如下4个步聚组成[2]: ①酸的浸蚀使基体金属表面H+浓度降低 Fe – 2e→ Fe2+ H2+2e→2[H] ②促进剂(氧化剂)加速 [O]+[H] → [R]+H2O Fe2++[O] → Fe3++[R] ③磷酸根的多级离解 ④磷酸盐沉淀结晶成为磷化膜Zn2++Fe2++PO43-+H2O→Zn2Fe(PO4)2·4H2O↓3Zn2++2PO43-+4H2O→Zn3(PO4)2·4H2O↓2 磷化工艺2.1 磷化前的预处理 一般情况下,磷化处理要求工件表面应是洁净的金属表面(二合一、三合一、四合一例外)。
工件在磷化前必须进行除油脂、锈蚀物、氧化皮以及表面调整等预处理。
特别是涂漆前打底用磷化还要求作表面调整,使金属表面具备一定的“活性”,才能获得均匀、细致、密实的磷化膜,达到提高漆膜附着力和耐腐蚀性的要求。
因此,磷化前处理是获得高质量磷化膜的基础。
2.1.1 除油脂 除油脂的目的在于清除掉工件表面的油脂、油污。
包括机械法、化学法两类。
机械法主要是:手工擦刷、喷砂抛丸、火焰灼烧等[3]。
化学法主要:溶剂清洗、酸性清洗剂清洗、强碱液清洗,低碱性清洗剂清洗。
2.1.2 酸洗 酸洗除锈、除氧化皮的方法是工业领域应用最为广泛的方法。
利用酸对氧化物溶解以及腐蚀产生氢气的机械剥离作用达到除锈和除氧化皮的目的。
酸洗中使用最为常见的是盐酸、硫酸、磷酸。
硝酸由于在酸洗时产生有毒的二氧化氮气体,一般很少应用。
在酸洗除锈除氧化皮槽液中,必须加入适量的缓蚀剂。
缓蚀剂的种类很多,选用也比较容易,它的作用是抑制金属腐蚀和防止“氢脆”。
但酸洗“氢脆”敏感的工件时,缓蚀剂的选择应特别小心,因为某些缓蚀剂抑制二个氢原子变为氢分子的反应[4],使金属表面氢原子的浓度提高,增强了“氢脆”倾向。
2.1.3 表面调整表面调整的目的,是促使磷化形成晶粒细致密实的磷化膜,以及提高磷化速度。
表面调整剂主要有两类,一种是酸性表调剂,如草酸。
另一种是胶体钛。
两者的应用都非常普及,前者还兼备有除轻锈(工件运行过程中形成的“水锈”及“风锈”)的作用。
在磷化前处理工艺中,是否选用表面调整工序和选用那一种表调剂都是由工艺与磷化膜的要求来决定的。
2.2 磷化工艺的分类2.2.1 防锈磷化工艺 磷化工艺的早期应用是防锈,钢铁件经磷化处理形成一层磷化膜,起到防锈作用。
经过磷化防锈处理的工件防锈期可达几个月甚至几年(对涂油工件而言),广泛用于工序间、运输、包装贮存及使用过程中的防锈,防锈磷化主要有铁系磷化、锌系磷化、锰系磷化三大品种。
防锈磷化一般有以下几步[5]: 除油除锈→水清洗→表面调整活化→磷化→水清洗→铬酸盐处理→烘干→涂油脂或染色处理 通过强碱强酸处理过的工件会导致磷化膜粗化现象,采用表面调整活化可细化晶粒。
锌系磷化可采用草酸、胶体钛表调。
锰系磷化可采用不溶性磷酸锰悬浮液活化。
铁系磷化一般不需要调整活化处理。
磷化后的工件经铬酸盐封闭可大幅度提高防锈性,如再经过涂油或染色处理可将防锈性提高几位甚至几十倍。
2.2.2 耐磨减摩润滑磷化工艺 对于发动机活塞环、齿轮、制冷压缩机一类工件,它不仅承受一次载荷,而且还有运动摩擦,要求工件能减摩、耐摩。
锰系磷化膜具有较高的硬度和热稳定性,能耐磨损,磷化膜具有较好的减摩润滑作用。
因此,广泛应用于活塞环,轴承支座,压缩机等零部件。
这类耐磨减摩磷化处理温度70~100℃,处理时间10~20min,磷化膜重大于7.5g/m2。
在冷加工行业如:接管、拉丝、挤压、深拉延等工序,要求磷化膜提供减摩润滑性能,一般采用锌系磷化,一是锌系磷化膜皂化后形成润滑性很好的硬脂酸锌层,二是锌系磷化操作温度比较低,可在40、60或90℃条件下进行磷化处理,磷化时间4~10min,有时甚至几十秒钟即可,磷化膜重量要求≥3g/m2便可[6]。
2.2.3 漆前磷化工艺 涂装底漆前的磷化处理,将提高漆膜与基体金属的附着力,提高整个涂层系统的耐腐蚀能力;提供工序间保护以免形成二次生锈。
因此漆前磷化的首要问题是磷化膜必须与底漆有优良的配套性,而磷化膜本身的防锈性是次要的,磷化膜要细致、密实、膜薄。
当磷化膜粗厚时,会对漆膜的综合性能产生负效应。
磷化体系与工艺的选定主要由:工件材质、油锈程度、几何形状;磷化与涂漆的时间间隔;底漆品种和施工方式以及相关场地设备条件决定。
一般来说,低碳钢较高碳钢容易进行磷化处理,磷化成膜性能好些。
对于有锈(氧化皮)工件必须经过酸洗工序,而酸洗后的工件将给磷化带来很多麻烦,如工序间生锈泛黄,残留酸液的清除,磷化膜出现粗化等[7]。
酸洗后的工件在进行锌系、锌锰系磷化前一般要进行表面调整处理。
在间歇式的生产场合,由于受条件限制,磷化工件必须存放一段时间后才能涂漆,因此要求磷化膜本身具有较好的防锈性。
如果存放期在10天以上,一般应采用中温磷化,如中温锌系、中温锌锰系、中温锌钙系等,磷化膜的厚度最好应在2.0~4.5g/m2之间[8]。
磷化后的工件应立即烘干,不宜自然凉干,以免在夹缝、焊接处形成锈蚀。
如果存放期只有3~5天,可用低温锌系、轻铁系磷化,烘干效果会好于自然凉干。
2.2.4 其它用途的磷化 磷化除了用上述三个领域外,还可用于电绝缘方面,装饰性方面。
其常规质量检测指标为外观、膜重和耐蚀性。
对电绝缘磷化,要求检测单位面积上的表面电阻[9]。
对装饰性磷化要根据不同的要求进行染色处理,要求不同的颜色色度和耐蚀性,这些指标的检测方法和控制范围一般由供需双方商定。
2.3 磷化质量控制及检测方法 磷化后的工件,根据其用途,对其质量指标进行分项检验。
主要质量控制指标,包括磷化膜外观、磷化膜厚度或膜重、磷化膜或后处理以后的耐蚀性三大共性指标。
根据磷化用途有时还要检测:磷化与漆膜配套性、磷化膜硬度、摩擦系数、抗擦伤性等指标[10]。
涂漆前打底用磷化一般还需测定其漆膜的机械物理性能,如:附着力、冲击强度、抗弯能力等。
3 磷化工艺展望磷化技术领域的研究方向主要是围绕提高质量、减少环境污染、节省能源进行。
首先考虑的应是提高质量,同样减少环境污染也非常重要。
磷化处理中产生化学物质污染,只能通过随后的治理来实现。
磷化技术及领域研究发展的三大内容如下:3.1提高质量 高温(>95 ℃)重型磷化的防锈性能非常好,应用非常广泛,已有几十年,现场硫酸铜点滴可达5 min以上[11]。
中温(60℃,5~8 min)磷化,目前一般达到2~3 min点滴,要达到5 min点滴还有相当一段差距[12]。
对涂装打底的磷化而言,提高磷化与涂装层的整体防腐蚀性仍是磷化研究的主要方向。
锌锰镍三元体系磷化已在较大范围内应用,但在表面耐碱性、提高阴极电泳漆或其他漆种的整体防腐蚀性方面还有发展前景[13],从提高质量方向考虑,含镍磷化仍是一种有效的途径。
镀锌板在汽车及其他行业的应用越来越多,其防腐蚀性能可以得到显著提高,但漆层的附着力保持性比不上钢板,在腐蚀介质或大气中暴露一段时间后会下降。
因此,解决镀锌板磷化漆膜的“湿”附着力的研究是当今十分迫切的问题。
3.2降低污染磷化处理产生的污染源主要是重金属、磷酸盐、表面活性剂、有毒物质等。
脱脂处理中磷酸盐排放水的“肥化”生物耗氧问题、表面活性剂的化学耗氧问题等,都是严重的污染。
现在已研究出无磷脱脂剂,正在研究应用中的生物可降解表面活性剂技术,但成本高,应用还有一定的阻力。
因此,脱脂技术的发展是研究低污染、低成本的清洗技术,应用将日益广泛。
无残酸腐蚀除锈技术、无铬磷化封闭技术都是生产中还没有完全解决的问题。
磷化处理使用的亚硝酸盐,重金属Zn、Ni,磷酸盐都是磷化过程中的污染源。
现有的技术,还不能取代磷酸盐,磷酸盐还将继续使用下去。
已有的不含Ni、Zn的磷化技术,其磷化质量远比不上Zn、Ni磷化[14]。
从发展趋势来看,无Zn、Ni磷化前景可观。
亚硝酸盐是现在使用最方便、最广泛、最有效的磷化促进剂,在相同经济成本下,目前还没有一种物质可代替它并取得相同的促进效果。
亚硝酸盐由于具有致癌性及分解产物氮氧化合物的毒性,其使用量都逐步减少,现在正在研究其替代物。
双氧水是一种理想的无污染促进剂,其副产物是水,没有任何污染问题,并已有极少应用。
未来需要解决的问题是H2O2的稳定性及槽液含量检测与控制,据报道已有一种羟胺有好的促进效果,其副产物是氮气和水,但现阶段工业应用很少。
总之,取代亚硝酸盐是必然的趋势。
3.3节省能源节省能源也应十分重视。
磷化过程是化学反应过程,温度对化学反应的影响较大,温度降低10℃,化学反应动力学速度降低2~3倍。
磷化技术发展的趋势是向低温度方向发展,现有的技术水平对不加温处理(0~25℃)还不能完全满足工业生产需要[15]。
现在的节能技术主要在重型磷化方面,从目前的95℃降低到50~60℃;薄型磷化从目前常用的50℃降低到30℃;脱脂技术从目前60℃主体应用温度,到将来的30℃也能提供优良的脱脂效果。
如此,将节省能源耗费约2/3。
参考文献[1] 江静华, 张旭海, 蒋建清, 等. 冷成型模具低温锌系磷化[J]. 材料保护, 2002, 35(5): 32-33.[2] 张王俭. 常温锌系磷化改进剂的研制[J]. 电镀与环保, 1997, 17(5): 23-240.[3] Liang Gang. Qick Organic Phosphating at Room Temperture[J]. Metal Finishing, 1997(9), 54-56.[4] 刘贤明, 王彤, 郑健斌. 光整热镀锌钢板磷化技术[J]. 材料保护, 2005, 31(5): 32-38.[5] 李新立, 李安忠. 金属磷化技术的回顾与展望[J]. 材料保护, 2000, 33(1): 14-18.[6] 梁刚, 舒万良. 常温快速磷剂的研制[J]. 电镀与环保, 1997, 17(1): 18-20.[7] 欧忠文, 徐滨士, 马世宁, 等. 纳米材料在表面工程中应用的研究进展[J]. 中国表面工程, 2004, 24(2): 5-11.[8] Rajagopalan Ksetal. Optimizing Iron Quality through Artificial Intelligence[J]. Metal Finishing,1997, 77(5): 99-104.[9] Zima, Vitezslav Benes, Ludvik, Melanova. Klara Glyeine Intercalated Uanadyl and NiobylPhosphatcs[J]. SolidStatetonics, 1998, 16(11): 285-290.[10] 孟德军. 低温磷化液的配制和应用[J]. 材料保护, 1999, 28(3): 44-46.[11] 滕培棠, 孟德军. 室温极少渣锌系磷化的研究[J]. 表面技术, 2000, 29(5): 36-39.[12] 肖鑫, 龙有前, 郭贤烙, 等. 常温高稳定性彩色磷化工艺研究[J]. 电镀与精饰, 2001, 23(2): 9-12.[13] 胡吉明. 钢板表面镀锌层结构与应变关系研究[J]. 材料保护, 1998, 31(1): 1-5.[14] 张景双, 屠振密. 含有稀土促进剂的低温磷化工艺训究[J]. 电镀与环保, 1995, 15(2): 26-28.[15] 张景双, 王家林, 杨哲龙, 等. 含有稀土添加剂的中温磷化[J]. 电镀与环保, 2000, 20(5):25-28.。