连杆轴颈磨削的分度误差分析
磨削缺陷分析与解决

磨削缺陷分析与解决1.产生原因及影响因素零件的磨削精度指零件在磨削加工后,其形状、尺寸及表面相互位置三方面与理想零件的符合程度。
一般说来,形状精度高于尺寸精度,而位置精度也应高于尺寸精度。
磨削加工中的误差主要来源与两方面。
一是磨床-夹具-砂轮组成的工艺系统本身误差;二是磨削过程中出现的载荷和各种干扰:包括力变形、热变形、振动、磨损等引起的误差。
而在磨削过程中,使砂轮与工件位置改变以降低磨削精度的主要原因有:⑴.由磨削力引起的磨床和工件弹性变形;⑵.磨床和工件的热变形;⑶.磨床和工件的振动;⑷.砂轮磨损后其形状、尺寸变化;⑸.工装、夹具的损坏或变形;⑹.导轨、轴承和轴等部件的非弹性变形。
其中磨削过程中的弹性变形是主要的影响因素,它会使砂轮的实际切入深度与输入切入深度不一致,这一变化是由“砂轮架—砂轮轴承-砂轮轴-工件-工件支承”的弹性系统刚性决定。
一般为消除这种原因带来的误差常在行程进给磨削后,停止相互间的进给,仅依靠弹性回复力维持磨削,即光磨阶段(又叫清火花磨削),从而消除残留余量。
当然造成磨削误差的其它因素液很多如:工件磨削形状误差,工件热变形,磨粒切刃引起的塑性变形,砂轮的磨损等。
2.对工件的影响:降低工件使用寿命;降低工件抗疲劳强度;特殊特性的尺寸精度误差易影响工件使用,如轴承孔尺寸的控制,尺寸过小,安装不到轴上;过大,易引起振动,影响轴承使用寿命等。
3.解决方法:增加系统刚性;减少上工序加工留量,以减小磨削厚度,从而减小磨削力降低残留应力;增加光磨时间;及时修整砂轮,及时检查工装、夹具、轴承完好性及电主轴的振动性等;精细的选择砂轮,如挑选细粒度,硬度较大,组织稍紧密的砂轮;选用导热性好的砂轮(如CBN 砂轮);采用冷却性能优良的磨削液以减少因热变形引起的误差。
二、工件表面粗糙度1.产生原因及影响因素表面粗糙度指加工表面具有较小间距和峰谷所组成微观几何形状特征。
它是大量磨粒在工件表面进行切削后留下的微观痕迹的集合。
连杆缓慢偏差测量难点分析及常见质量问题的处理

口面/ P 0 0 7 装配/ 8 精磨两端 0P 0 面/ 9 镗大小头孔、两端倒角/ 0P 0
OP 0 珩磨 / P 0 小头 孔两端 倒 10 O 15 角/ P 2清 洗/ P 3— 15 量分 O 10 O 10 3重 级和尺寸检验+ 矫正/ 观检验。 外
⑥测量程序的运行。
初始坐标 系建立后 ,即可评价 出连杆 体、连杆 盖对 口面 对螺栓孔轴 线 的垂直度及连杆体 、杆盖对 口面平面度 。
()O 6磨对口面以后,需要测量连杆盖对口面对螺栓孔轴线的垂直 3 P0 度,测量项 目 如图3 该工序测量工艺图所示,该项目在三坐标上测量。
一 圈
2 该工 序测 量 工艺 图所 示 ,该项 目
工艺对其各道工序的检测项 目配备 了先进的检测设备,规定了严格的 检测频次 ,以便生产出高质量的连
杆产 品。
在三坐标 上测量 。
连杆加工工艺流程简述
富康轿 车T u系列发 动机 连 杆 加工工艺路线如下 : OP 0 磨 两端 面 / 2 钻 、 粗 1 OP 0
心线对定位端面 的垂直度 ,1 号项 7
③在支架 的 “ V”形两端 各采
一
点 ,取其 中点清X= 。 O 初始 坐标 系的建立后 ,即可采
变载荷。这就要求连杆在质量尽可
能 小 的条 件 下 有 足够 的 刚度 和 强 度 。连杆 的刚度不够 ,可能产生 的 结果有 :其 大头 失 圆,导致连杆 大 头轴瓦 因油膜破 坏而烧毁 ;连杆 杆
一
②在支架左侧 面采两点 ,连成
条线建 轴 ,
用力以及其本身摆动和活塞组往复
运动时 的惯性 力 ,这些 力的大小和 方 向都是周 期性 变化的 ,因此 ,连 杆受到 的是压缩 、拉伸和弯 曲等 交
磨削加工中的磨削误差修正

磨削加工中的磨削误差修正随着机器制造技术的不断进步,磨削加工已经成为了高精度加工中不可或缺的一环。
然而,由于磨削过程的复杂性和干扰因素的存在,磨削误差是难以避免的。
因此,在磨削加工中对磨削误差的修正变得越来越重要。
本文将深入探讨磨削加工中的磨削误差修正。
一、磨削误差的来源磨削误差可以分为系统误差和随机误差两类。
系统误差是由于磨削机床结构和工艺参数的不理想造成的,如磨盘及其支撑装置的不平衡、磨盘磨具的磨损、磨削轮的偏心等。
随机误差则是由于磨削过程中的人工操作、测量错误、相互干扰等因素引起的。
二、磨削误差修正的方法常用的磨削误差修正方法包括磨头自适应修整、磨削参数的优化调整、磨削轮径向误差修正和磨削后的加工修正等。
1. 磨头自适应修整磨头自适应修整是一种常见的磨削误差修正方法,它可以自动调整磨头的磨削条件,以达到更好的工件表面质量和尺寸精度。
该方法通过磨头的负反馈来实现,在磨削过程中,通过感应装置采集磨头与工件的距离信息,然后将信息送至控制器,由控制器采取相应的措施,调整磨头的磨削参数,进而实现对磨削误差的修正。
2. 磨削参数的优化调整磨削参数的优化调整是指在磨削加工过程中,通过调整磨削参数来降低误差,以达到更好的加工效果。
常用的磨削参数包括磨削轮转速、进给速度和磨削压力等,通过优化这些参数,可以减小系统误差和随机误差,提高工件的表面质量和尺寸精度。
3. 磨削轮径向误差修正磨削轮径向误差是导致磨削误差的主要原因之一。
为了修正磨削轮径向误差,常用的方法是在磨削轮表面上增加一定的修正圆弧,以抵消磨削轮的径向误差。
该方法需要精确的测量磨削轮的径向误差和磨削轮表面的形状,并根据实际情况调整修正圆弧的半径和位置,以达到最佳的修正效果。
4. 磨削后的加工修正磨削后的加工修正是指在工件进行磨削加工后,通过进一步的削减、镗孔等方式对工件进行二次调整,以达到更好的尺寸精度和表面质量。
该方法需要精确的工件设计与磨削加工,以确保后续加工可以达到最佳的效果。
磨削加工中的磨削误差分析
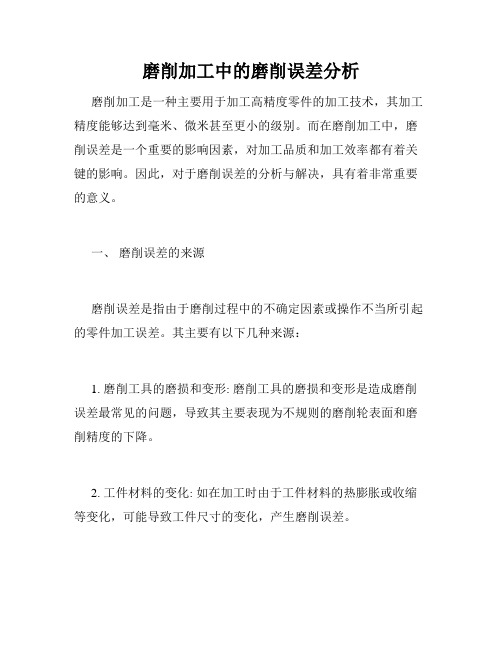
磨削加工中的磨削误差分析磨削加工是一种主要用于加工高精度零件的加工技术,其加工精度能够达到毫米、微米甚至更小的级别。
而在磨削加工中,磨削误差是一个重要的影响因素,对加工品质和加工效率都有着关键的影响。
因此,对于磨削误差的分析与解决,具有着非常重要的意义。
一、磨削误差的来源磨削误差是指由于磨削过程中的不确定因素或操作不当所引起的零件加工误差。
其主要有以下几种来源:1. 磨削工具的磨损和变形: 磨削工具的磨损和变形是造成磨削误差最常见的问题,导致其主要表现为不规则的磨削轮表面和磨削精度的下降。
2. 工件材料的变化: 如在加工时由于工件材料的热膨胀或收缩等变化,可能导致工件尺寸的变化,产生磨削误差。
3. 加工参数的不确定性: 如磨削参数的选择不合适、未能够准确把握加工过程的变化,就可能造成加工精度的不稳定。
4. 制造中的人员和设备因素: 如由于人员工艺水平的不同或设备自身的问题所导致的制造误差等,都可能成为磨削误差的来源。
二、磨削误差的分类磨削误差有以下几种分类方式:1. 几何度量的分类: 如直线度、平面度、圆度、同轴度等。
2. 粗糙度的分类: 如表面粗糙度、压痕深度等。
3. 特殊误差的分类: 如振动引起的误差、加工过程中的热变形等。
4. 组合误差的分类: 如由于几种误差的组合所构成的误差。
三、磨削误差的控制技术为了有效地控制磨削误差,需要采用一些专门的控制技术。
其中,常见的技术有以下几种:1. 磨削参数控制: 如通过合理的磨削参数,来控制磨削加工中的误差,包括磨削轮的选取、磨削轮的转速、磨削轮进给速度、工件进给速度等。
2. 磨削工具的优化设计: 如采用特殊的磨削工具,通过设计和制造优良的磨削工具,来减少磨削误差的源头。
3. 清洁和维护: 如加强磨削设备的清洁和润滑,以确保磨削设备和工具能够保持良好的状态,减少误差的产生。
4. 加工设备的质量控制: 如对于加工设备的选型、评估和维护,采用更加精密的加工设备,并要对其进行定期的检测和调整,以确保加工质量的稳定性和精度。
曲轴连杆颈磨削的精细化控制
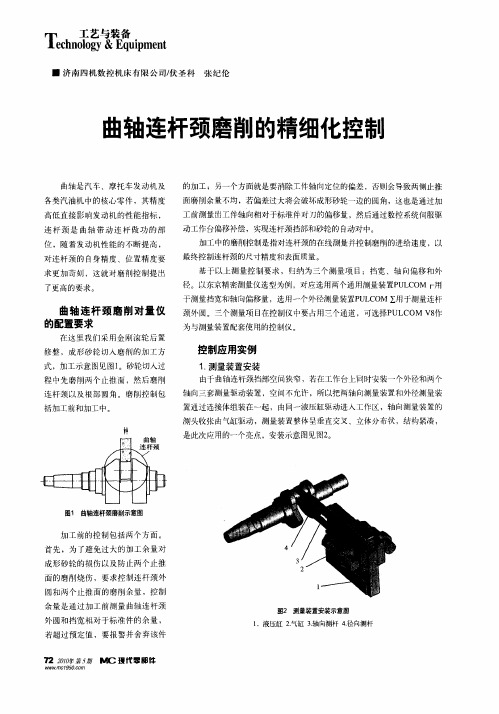
佃
轴 向三套测量驱动装置 ,空 间不 允许 ,所以把两轴 向测量装 置和外径测量装 置通过连接体组装在一起 ,由同一液压缸驱动进入工作 区,轴 向测量装置的 测头收张 由气缸驱动 ,测量装置整体 呈垂直交叉 、立体分布状 ,结构 紧凑 ,
是此次应用的一个亮点,安装示意图见图2 。
I广] 广
l
\ /
图1 曲轴连杆颈磨削示意图
加 工前的控 制包括 两个方 面。 首先 ,为 了避 免过大 的加工 余量对
成形 砂轮的损 伤以及 防止两个 止推
面的 磨削烧 伤 ,要 求控 制连杆 颈外
圆和 两个止推 面的 磨削余量 ,控制
余量 是通过加 工前测 量 曲轴连 杆颈 外 圆和挡宽相 对于标 准件的 余量 ,
位 ,随着 发动机性 能的 不断提高 ,
对连杆颈 的 自身精 度 、位 置精度要
求更加苛 刻 ,这就 对磨 削控 制提 出 了更高 的要求 。
曲轴连杆 颈磨 削对量仪 颈外 圆。三个测量项 目在控制仪 中要 占用三个通道 ,可选择P L OM 8 U C V 作 的配置要 求 为与测量装置配套使用的控制仪 。
各类汽油机 中的核 心零件 ,其精度 高低直接 影响发动 机的性 能指标 ,
连杆 颈 是 曲轴 带动 连 杆 做 功 的 部
工前测量 出工件轴 向相对于标准件对 刀的偏移量 ,然后通过数控 系统伺服驱
动工作台偏移补偿 ,实现连杆颈 挡部和砂轮的 自动对中。 加 工中的磨削控制是指对连杆颈 的在线测量并控制磨削的进给速度 ,以 最终控制连杆颈的尺寸精 度和表面 质量 。 基于以上测 量控制要 求 ,归纳为 三个测量 项 目:挡宽 、轴 向偏移和 外 径。以东京精 密测 量仪选型为例 ,对应选用两个通用测量装 置P C UL OM 广 用 于测量档宽和轴向偏移 量,选用 一个外径测量装置P L M ∑用于测量连杆 U CO
连杆轴颈磨削的平行度误差
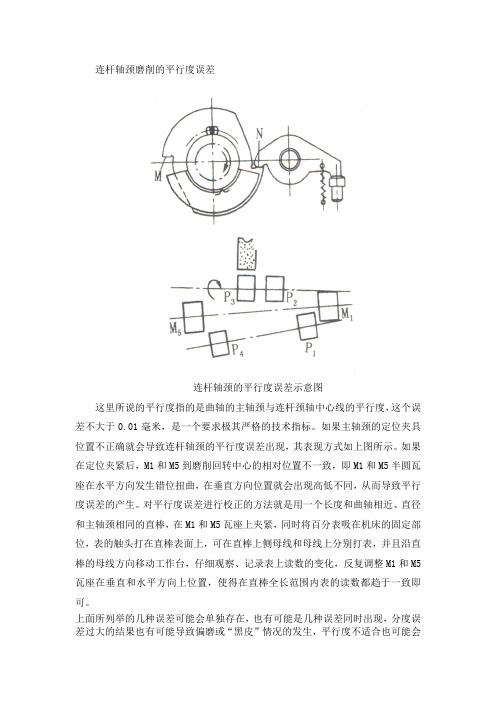
连杆轴颈磨削的平行度误差
连杆轴颈的平行度误差示意图
这里所说的平行度指的是曲轴的主轴颈与连杆颈轴中心线的平行度,这个误差不大于0.01毫米,是一个要求极其严格的技术指标。
如果主轴颈的定位夹具位置不正确就会导致连杆轴颈的平行度误差出现,其表现方式如上图所示。
如果在定位夹紧后,M1和M5到磨削回转中心的相对位置不一致,即M1和M5半圆瓦座在水平方向发生错位扭曲,在垂直方向位置就会出现高低不同,从而导致平行度误差的产生。
对平行度误差进行校正的方法就是用一个长度和曲轴相近、直径和主轴颈相同的直棒,在M1和M5瓦座上夹紧,同时将百分表吸在机床的固定部位,表的触头打在直棒表面上,可在直棒上侧母线和母线上分别打表,并且沿直棒的母线方向移动工作台,仔细观察、记录表上读数的变化,反复调整M1和M5瓦座在垂直和水平方向上位置,使得在直棒全长范围内表的读数都趋于一致即可。
上面所列举的几种误差可能会单独存在,也有可能是几种误差同时出现,分度误差过大的结果也有可能导致偏磨或“黑皮”情况的发生,平行度不适合也可能会
引起曲拐半径的偏差的发生,在现实生产中我们要根据实际情况具体对待。
研磨加工中的研磨误差分析

研磨加工中的研磨误差分析
研磨是一种常见的金属加工方式,可以用来制造各种零部件、
工具以及模具等。
在研磨加工过程中,通常会遇到一些研磨误差
的问题,如平面度误差、圆度误差、表面质量误差等。
这些误差
会直接影响到工件的精度和质量,因此必须进行分析和处理。
首先,我们需要了解研磨误差的成因。
研磨加工过程中,可能
会出现材料的塑性变形和表面质量的变化,导致工件产生误差。
此外,刀具磨损、磨料质量以及研磨参数等因素也会影响到研磨
质量。
针对这些误差成因,我们需要采取相应的措施进行分析和处理。
首先,可以通过检查研磨设备的状态,确保研磨设备的精度和准
确性。
其次,可以通过调整研磨参数来优化研磨过程,例如调整
研磨速度、压力和磨料的选择等。
此外,还可以通过使用更高质
量的磨料和刀具等方式来改善研磨质量。
在具体实践中,我们可以采用一些方法来分析和处理研磨误差。
例如,通过使用三坐标测量仪等设备来检测工件的误差,以便进
行更加精确的修磨操作。
同时,还可以采用表面处理等方法来改
善工件的表面质量。
此外,在进行研磨加工前,还应该进行足够
的研磨前准备,包括清洗、调整以及检查等工作,确保研磨过程的稳定性和准确性。
总之,研磨误差是一种常见的问题,但我们可以采取多种方式来分析和处理这些误差。
通过对研磨参数、研磨设备以及磨料和刀具的选择等方面进行优化,可以显著改善研磨质量。
同时,还应该注重研磨前准备和研磨后处理等方面的工作,以确保研磨加工的准确性和稳定性。
曲轴连杆颈圆度超差问题分析
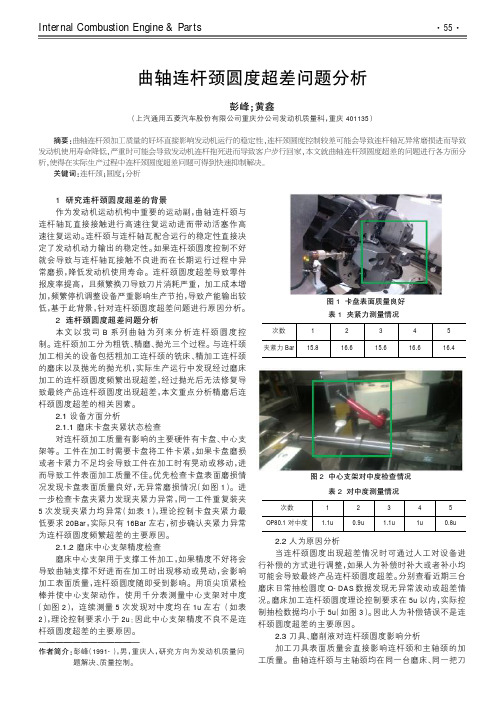
图 1 卡盘表面质量良好 表 1 夹紧力测量情况
次数
1
2
3
4
5
夹紧力 Bar 15.8
16.6
15.6
16.6
16.4
图 2 中心支架对中度检查情况 表 2 对中度测量情况
次数
1
2
3
4
5
OP80.1 对中度 1.1u
2.4 工件来料及加工方法分析 当前道工序来料较差时可能会直接导致磨床加工连 杆颈圆度超差,调查近期粗铣工位线旁抽检数据发现直 径、圆度等特征均无异常。如果磨削参数发生改变也可能 会导致连杆颈圆度超差,我司自 2015 年投产以来一直使 用同样的加工参数进行加工,前面 4 年均没有出现这种频 繁超差的情况,因此前道工序来料质量及加工参数不合理 均不是连杆颈圆度频繁超差的主要原因。 2.5 测量原因分析 2.5.1 连杆颈表面异常导致测量不准确 曲轴终检机测量连杆颈圆度时采用测针在连杆颈表
摘要院DPF渊 柴油微粒过滤器冤 在使用过程中袁由于灰分积累尧使用不当等原因易造成 DPF 堵塞等故障袁现有的数据采集设备无法 直接反映出设备是否发生故障遥针对这一问题袁提出了一种基于 K-means 和 KNN 的 DPF 故障分类算法遥在 K-means++选择初始聚类 中心的基础上引入了阈值限定 D0袁以降低同类型样本被选为后续聚类中心的概率遥 其次袁为了保证聚类数目的真实性袁采用层次分析 法辅助初步确定聚类参数 k袁并利用轮廓系数和交叉验证来评估模型遥 KNN 模型利用已分类的样本对来自不同厂家的混合测试样本 进行预测袁实验结果表明袁其预测准确率达到了 90%以上袁基本实现了 DPF 设备故障属性分类袁为后续维护工作提供了可供参考的 依据遥
6l曲轴连杆颈磨削的质量控制

产品与技术6L曲轴连杆颈磨削的质量控制中车资阳机车有限公司 丑洋洋 朱万奇 朱 波6L曲轴系出口国外的曲轴,该曲轴对表面质量和形位公差的要求非常严格。
本文主要介绍在连杆颈磨削时,为达到其工艺要求而采取有别于传统的曲轴加工工艺的具体措施。
6L曲轴材质为碳钢(S44SY),非淬火件,六拐成三对,每一对拐在空间相互之间成120°±10′夹角,其尺寸公差为φ185-0.025mm,圆柱度0.015mm,平行度0.15/1000mm,曲轴偏心半径要求150±0.1mm,各拐颈上的安装面同相邻主轴颈与连杆颈中心连线的垂直度为0.2mm。
连杆颈表面粗糙度Ra0.2μm,且连杆颈不得有凹面。
该曲轴长径比为12︰1,为典型的细长轴,磨削过程中受其自身的重量和磨削参数的影响变化很大,因此在具体的加工实践过程中,在具体相关人员的共同努力下,总结出以下具体的加工方案。
1.砂轮的选择此种6L曲轴只调质不淬火,表面硬度为26~32HRC,选择砂轮时应要求砂轮的硬度高一些,减少其自锐性,尽量避免磨削时因其自锐性脱粒挤伤曲轴外表面,造成曲轴外表面有凹点的现象。
砂轮的粒度应选择细一些,保证磨削后曲轴外表面的粗糙度。
因此选择砂轮的硬度为L~M,粒度为46#的WA,尺寸为φ80mm×1200mm×305mm的平面砂轮。
2.机床的调整(1)机床头架、尾架分别安装φ210.5m m和φ181.3m m的工艺瓦托瓦,调整好机床的偏心半径150±0.05mm,以保证如图1所示的曲轴偏心半径,在此只是粗调整,在磨削过程中每个拐都必须用专用量具“马鞍规”测量该拐偏心半径是否在规定的公差范围内,如有偏差,再根据偏差作精细的调整(本工序前一工序必须控制好主轴颈及工艺颈的尺寸及形位公差,尽量减少对本工序质量的不良影响)。
图 1(2)机床的配重。
该曲轴为偏心工件,在磨削过程中受离心力不平衡的影响很难保证工件圆柱度0.015mm的公差,因此必须加配重块以保证曲轴在旋转过程中电流表的最大变化量在2A范围内。
连杆轴颈磨损度计算公式
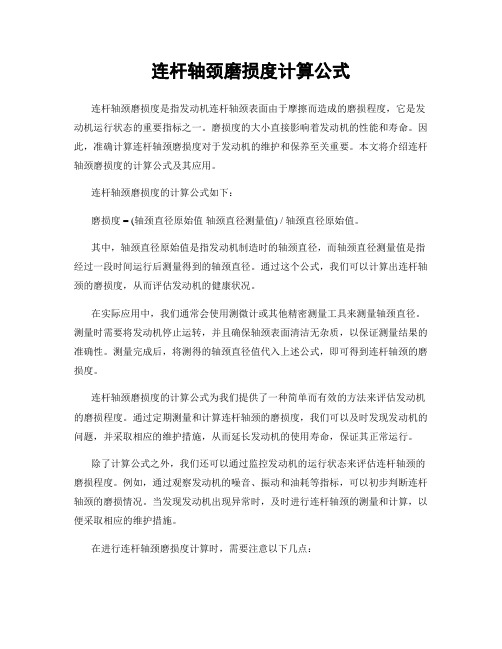
连杆轴颈磨损度计算公式连杆轴颈磨损度是指发动机连杆轴颈表面由于摩擦而造成的磨损程度,它是发动机运行状态的重要指标之一。
磨损度的大小直接影响着发动机的性能和寿命。
因此,准确计算连杆轴颈磨损度对于发动机的维护和保养至关重要。
本文将介绍连杆轴颈磨损度的计算公式及其应用。
连杆轴颈磨损度的计算公式如下:磨损度 = (轴颈直径原始值轴颈直径测量值) / 轴颈直径原始值。
其中,轴颈直径原始值是指发动机制造时的轴颈直径,而轴颈直径测量值是指经过一段时间运行后测量得到的轴颈直径。
通过这个公式,我们可以计算出连杆轴颈的磨损度,从而评估发动机的健康状况。
在实际应用中,我们通常会使用测微计或其他精密测量工具来测量轴颈直径。
测量时需要将发动机停止运转,并且确保轴颈表面清洁无杂质,以保证测量结果的准确性。
测量完成后,将测得的轴颈直径值代入上述公式,即可得到连杆轴颈的磨损度。
连杆轴颈磨损度的计算公式为我们提供了一种简单而有效的方法来评估发动机的磨损程度。
通过定期测量和计算连杆轴颈的磨损度,我们可以及时发现发动机的问题,并采取相应的维护措施,从而延长发动机的使用寿命,保证其正常运行。
除了计算公式之外,我们还可以通过监控发动机的运行状态来评估连杆轴颈的磨损程度。
例如,通过观察发动机的噪音、振动和油耗等指标,可以初步判断连杆轴颈的磨损情况。
当发现发动机出现异常时,及时进行连杆轴颈的测量和计算,以便采取相应的维护措施。
在进行连杆轴颈磨损度计算时,需要注意以下几点:1. 测量精度,测量时需要使用精密的测量工具,并且确保测量过程的准确性,以避免因测量误差而导致计算结果的不准确。
2. 测量间隔,建议定期对连杆轴颈进行测量,以便及时发现磨损情况,并采取相应的维护措施。
测量间隔的长短可以根据发动机的使用情况和工作环境来确定。
3. 维护措施,当连杆轴颈磨损度达到一定程度时,需要及时进行维护和更换,以避免因磨损过度而导致发动机的故障和损坏。
总之,连杆轴颈磨损度计算公式为我们提供了一种简单而有效的方法来评估发动机的磨损程度。
曲轴连杆颈磨床分度装置改进

80WMEM·2017年 第2期产品与技术曲轴连杆颈磨床分度装置改进中国中车资阳机车有限公司 朱万奇用于曲轴连杆颈磨削时分度的原分度联接装置如图1所示,一端套在曲轴工艺颈上,靠3颗压紧螺栓与曲轴联接,一端联接在机床分度盘上。
分度操作时先松开曲轴,然后将分度盘定位插销拔出,用棘轮扳手旋转分度装置,如图2所示,曲轴会随着分度盘一起旋转,至所需角度,插上分度盘定位插销、压紧曲轴,即完成曲轴分度。
该分度装置在使用中主要存在以下问题。
(1)分度不准确。
其原因为:①3颗压紧螺栓只能压紧2颗,第3颗在下方没有空间,分度时靠该联接装置给曲轴传递动力使曲轴转动,这样在分度过程中曲轴与联接装置产生微量位移,导致磨削出的连杆颈角度出现误差。
②手动分度对操作者的经验、力度要求高,一支曲轴由两个不同的操作人员或同一个操作人员分度加工后,会出现连杆颈角度误差。
(2)分度方向局限。
该装置只能完成30°的整数倍角度的分度,5拐、7拐、9拐曲轴无法分度。
(3)操作空间小、操作困难。
(4)分度效率低。
1. 改进方案为了解决原分度装置分度不准、操作性差和分度效率低的问题,设计了一套简单高效的分度装置。
该装置由装在曲轴上的多面体分度盘、装在机床上的基准面和百分表找正装置构成,分度时旋转曲轴,用百分表监控分度面与基准面,直到分度盘上的分度面与机床上的基准面方向一致即可。
(1)多面体分度盘及安装。
多面体分度盘的面数可根据加工曲轴连杆颈的空间分布方向确定,如磨削加工连杆颈空间分布3个方向的3拐或6拐曲轴,使用图3所示的多面体分度盘。
3个分度面均布于圆周上,相互的角度偏差可按需要进行设计,制作完成后进行计量,精磨分度盘角度误差可控制在(120°±1')内;4个压紧螺栓孔均布在与安装定位孔同心的φ110mm 圆上,为了便于安装,制作成长孔,与曲轴端面已有的工艺孔联接,无需重新制作工艺孔。
安装定位孔的直径与曲轴工艺外径配合设计,如图4所示,分度盘安装时直接套装在曲轴的工艺轴颈上,避免歪斜引起误差。
精密曲轴连杆颈磨削加工技术的研究

精密曲轴连杆颈磨削加工技术的研究作者:文/ 张慎明来源:《时代汽车》 2020年第20期张慎明上汽通用五菱汽车股份有限公司广西柳州市 545007摘要:内燃机与发动机作为汽车的心脏,曲轴作为心脏的血管,所以加强曲轴的设计与加工就显得尤为重要,加上曲轴类型多样,加工精度将直接关乎到发动机性能,进而对汽车质量带来影响。
因此,市面上对于曲轴精度的要求也越发苛刻。
本文对以精密曲轴连杆颈磨削加工技术作为研究对象,对其工艺要点和相关误差因素进行了探究,旨于为企业带来更好的经济效应。
关键词:加工技术连杆轴颈摩削曲轴连杆颈Research on Grinding Technology of Precision Crankshaft Connecting Rod NeckZhang ShenmingAbstract:The internal combustion engine and the engine are the heart of the car, and the crankshaft is the blood vessel of the heart. Therefore, it is particularly important to strengthen the design and processing of the crankshaft. With the various types of crankshafts, the machining accuracy will directly affect the performance of the engine, which will affect the quality of the car. Therefore, the requirements for crankshaft accuracy on the market are becoming more stringent. This article takes the precision crankshaft connecting rod neck grinding processing technology as the research object, and explores its process points and relatederror factors, aiming to bring better economic effects to the enterprise.Key words:machining technology, connecting rod journal rubbing, crankshaft connecting rod journal1 引言曲轴的作用是承受连杆传来的力,并将这份力转变为转矩输出并驱动发动机上附件来支持附件的工作。
曲轴磨床磨削连杆轴颈超差的原因与修理

作者: 罗庆斌
作者机构: 广西林业基建工程公司机修厂
出版物刊名: 设备管理与维修
页码: 42-NULL页
主题词: 曲轴磨床;连杆轴颈;传动系统;椭圆度;解体检查;剪切变形;轴中心线;回转系统;冲击负荷;偏移距
摘要:我厂的 MQ8260型曲轴磨床使用不久,即发现磨削连杆轴颈时轴颈椭圆度超差
0.03mm,达不到尺寸的精度要求。
针对该磨床使用过程中仅在磨削连杆轴颈时发生这一故障的情况,于1983年初对主轴传动系统和各紧固联接部件进行了全面的解体检查,发现主轴3与花盘2联接的四颗螺栓4已发生了不同程度的塑性变形,见图1。
有的螺栓的螺纹根部已轻微。
连杆轴颈磨削的分度误差分析

连杆轴颈磨削的分度误差分析连杆轴颈的分度误差示意图各个连杆轴颈的磨削顺序是P4-P1-P2-P3。
首先对P4和P1进行磨削加工,然后松开夹具,由分度头上的菱形分度头驱动整个曲轴翻转一百八十度,再将P2和P3置于磨削位置,夹紧后进行磨削加工。
连杆轴颈的分度误差指的是P2、P3和P4与P1之间相对位置度的误差,误差一般小于0.36毫米。
由于P1和P4为同一轴线一次装卡,P2和P3为另一轴线二次装卡,所以P1和P4之间及P2和P3之间会出现较大偏差的机率不大。
在这里我们主要研究的是P1和P4与P2和P3在180°方向上的理论位置与实际分度位置之间的误差。
在进行实际的测量时,我们以分度销孔进行角向定位,首先用百分表测量P1的位置并且设为零位,然后将曲轴整个翻转一百八十度,再在同样的位置测量P2和P3轴颈,这时在百分表上显示出来的数值就是分度误差。
如果百分表的表针在显示的是“—”方向的负值,就将轴颈置于逆向偏移位置,连杆轴颈的轴心线在上图中的H点,图中的t值指的就是分度误差值(百分表测量出来的读数)。
由于P1和P4经过磨削处理后,分度头液压装置的动作分度盘需要顺时针旋转一百八十度后,反靠在棘爪上进行定位,分度销驱动整个曲轴也旋转同样的角度,这时的理想状态是P2和P3应该在下边磨削的位置E处,P1和P4则应在曲轴主轴颈的正上方F处,即主轴颈拐颈中心F和J的连线上。
实际上,分度盘转过的β角度不足一百八十度,分度就会不到位,从而导致磨削的连杆轴颈也会产生同样误差。
很显然造成这个误差的原因是由于分度盘上的定位面M处出现磨损或者N处高出,正确的误差纠正方法就是在分度盘的M处加垫或者在N处进行修磨。
加垫过程在实施起来会有一些困难,一般的处理方法是将分度盘拆下来,然后在磨床上对N面进行修磨处理。
由于分度盘M和N处的半径与轴颈半径(轴颈中心至主轴颈中心距离)的尺寸很相近,因此轴颈偏差数值与M处的磨损值也相近似,这时我们可以按照测量时百分表显示的偏差读数修磨,使M和N调整到180°分度。
曲轴连杆颈轴线位置误差的测量研究

曲轴连杆颈轴线位置误差的测量研究摘要:应用一个结构简单、操作方便的多功能曲轴分度器,既能对曲轴连杆颈轴线位置误差进行单项检测,又能进行综合检测。
实践证明,效果较好。
关键词:曲轴,连杆颈,位置误差,分度器,误差曲轴是发动机中重要零件之一,其连杆颈轴线位置精度直接影响发动机的使用寿命,因此在检测中属重要项目。
目前,曲轴连杆颈轴线位置误差的检测方法较多,但大都是单项测量,速度慢、费时费工。
根据调查研究,我们制作了一个结构简单、操作方便的多功能曲轴分度器,使其既能对曲轴连杆颈轴线位置误差进行单项检测,又能进行综合检测。
1 曲轴连杆颈轴线位置精度的概念根据JB/T6727-1993《内燃机曲轴技术条件》,属于控制曲轴连杆轴线位置精度的有3个参数(如图1所示,以六拐曲轴为例,连杆颈相位角为120 °):1、在垂直于主轴颈轴线平面内,连杆颈中心到主轴颈中心距离e (以下简称回转半径)公差±δe.2、在垂直于主轴颈轴线平面内,各连杆颈轴线和主轴颈轴线组成的平面对第一连杆颈轴线和主轴颈轴线组成的平面的角度120 °(以下简称曲柄夹角)的公差±δα.3、在主轴颈轴线方向,有连杆颈轴线对两端主轴颈公共轴线的平行度公差δ//.图2所示的是曲轴连杆颈轴线位置公差带的几何框图。
由图中可以看出:1、第一连杆颈(基准)中心O1被限制在O1O线方向和以O1为中心的±δe线段内。
2、其它连杆颈中心(O1 、O3 ) ,分别被限制在各自的由±δe和±δα所组成的小扇形公差带内。
3、连杆颈轴线对两端主轴颈公共轴线的平行度公差带,为一直径是δ//,且平行于公共轴线的圆柱体。
反映在横向图上,则是一个直径是δ//值的圆。
4、对于第一连杆颈(基准)轴线,也同样存在平行度误差,所以也存在(3)中所述的投影圆,但由于在建立公差带横向图时所选择的面是过去第一连杆颈轴线中点的截面,因此反映在图中O1的位置域为一线段。
曲轴连杆颈磨削过程中常见问题解析

曲轴连杆颈磨削过程中常见问题解析朱进军;胡本洋;金智勇【摘要】本文介绍了某发动机曲轴连杆颈磨削的基本原理,对连杆颈磨削过程中经常出现的一些典型问题及其形成原因进行了分析,并提出了相应的对策和解决办法。
【期刊名称】《汽车制造业》【年(卷),期】2016(000)018【总页数】4页(P38-38,40,42,44)【关键词】曲轴连杆颈;磨削过程;解析;典型问题;发动机【作者】朱进军;胡本洋;金智勇【作者单位】哈尔滨东安汽车动力股份有限公司【正文语种】中文【中图分类】U262.11本文介绍了某发动机曲轴连杆颈磨削的基本原理,对连杆颈磨削过程中经常出现的一些典型问题及其形成原因进行了分析,并提出了相应的对策和解决办法。
曲轴是发动机的重要组成部件,其加工精度和加工难度在发动机各大件中首屈一指。
曲轴连杆轴颈(也称拐颈)在发动机中与连杆相连接,承受着各种复杂的交变载荷,轴颈与轴瓦间长期处于高速的相对运动状态,因此工艺对拐颈加工的形状、位置精度及表面粗糙度有着十分严格的要求。
在曲轴的整个机加过程当中,连杆颈的精磨工序是最重要、最关键的一步,本道工序的加工质量对曲轴成品质量的影响举足轻重。
拐颈磨削是一个复杂的过程,设备精度水平高,调整保障维护难度大,生产对时间性要求较强,对于加工中发生的各种缺陷和偏差,工艺人员应具有较强的处理能力,能够及时判断出问题产生的原因,采取措施。
图1所示为某汽车发动机曲轴拐颈磨削工序,各连杆颈的轴心线与主轴颈的轴心线在同一平面内,其位置度公差为0.2 mm。
如图1所示,A1、A2、A3、A4和A5所指为主轴颈,是曲轴工作旋转时的支撑和回转中心,连杆颈B1、B2、B3和B4围绕主轴颈旋转,活塞及连杆带动拐颈将直线运动转化为圆周运动,为发动机输出动力。
B1、B4在同一轴线上,B2、B3在另一轴线上,二者相差180°。
曲轴的大小和规格有所区别,但拐颈的磨削原理和方法基本相同。
在实际生产中,曲轴拐颈磨削采用的是日本日平公司和丰田公司生产的数控拐颈磨床,二者定位方式相同,均是采用偏心夹具,半圆硬质合金瓦座支撑主轴颈A1、A5径向定位。
曲轴线磨床磨削加工质量问题解解析

曲轴线磨床磨削加工质量问题解解析发布时间:2022-09-07T09:08:49.776Z 来源:《科学与技术》2022年第9期作者:滕培梁张华华梁书鑫宋龙[导读] 发动机曲轴连杆颈和主轴颈需要磨削加工,精度要求高,尺寸要求都在微米级,加工过程中经常会出现尺寸及形位公差超差的问题。
滕培梁,张华华,梁书鑫,宋龙上汽通用汽车有限公司武汉分公司,湖北武汉,4300001.概述发动机曲轴连杆颈和主轴颈需要磨削加工,精度要求高,尺寸要求都在微米级,加工过程中经常会出现尺寸及形位公差超差的问题。
主要有主轴颈跳动超差,主轴颈/连杆颈外圆尺寸超差、连杆颈相位角度超差等问题,下面针对这三个问题,做一下详细的解析。
这样就可以把M1的高点适当修正回来。
3尺寸波动问题尺寸波动问题则分为某个测头加工的所有尺寸均有问题,还是仅这个测头加工的其中个别轴径有问题。
如果是这个测头加工的所有轴径都有问题,则需要怀疑这个测头本身是否有问题;如果工件圆度不好,则肯定都会影响直径;砂轮太钝或者到寿命,一样影响直径,则需要修砂轮及更换砂轮;首先验证侧头的重复性,检查测头机械上是否松动,测头线缆是否进水,检查测头的温度补偿系数是否输入正确,还有就是Marposs信号转接头及P7出现问题。
如果仅是某个轴径出问题,则需要把测头落在相应轴径上,看看是否与工件有干涉或者碰到工件油孔。
除掉上面这些原因,如果加工中出现尺寸过大或者过小的报警时候,则进入到相应的Marposs界面,查看是加工到那个轴径时候报警。
如果P1不存在偏磨,只是P2或者P3偏磨而ADCOLE测得相位角又没有问题,则是毛胚来料有问题;如果P2/P3测得相位角又有问题,则需要在Juwop/u中P2或者P3角度适当做修正。
如果连杆偏磨现象不稳定,忽左忽右,则需要检查侧头机械是否松动,或者说测头本有问题。
可以在不松开工件的情况下反复测同一根工件,观察测量直的稳定性。
作者简介:滕培梁,(1988.02-)男,河南汝州人,本科学历,助理工程师;研究方向:发动机机械加工、设备维护及管理。
连杆轴颈的最大磨损

连杆轴颈的最大磨损
连杆轴颈的最大磨损量是指在一定的使用条件下,连杆轴颈的最大允许磨损量。
这个数值通常由机器的设计和制造标准、使用环境和操作方式等因素决定。
在实际使用中,连杆轴颈的磨损量受到多种因素的影响。
其中,最主要的因素包括以下几个方面:
1. 润滑情况:连杆轴颈的润滑情况对磨损量有很大的影响。
如果润滑不良,机器的摩擦系数会增加,从而导致磨损量增大。
因此,为了减少磨损量,需要选择合适的润滑剂和润滑方式,保证机器得到充分的润滑和保护。
2. 使用条件:机器的使用条件也会对连杆轴颈的磨损量产生影响。
例如,机器的负载、转速、温度等都会影响连杆轴颈的磨损量。
因此,需要根据实际情况对机器进行调整和优化,保证机器的使用条件符合要求。
3. 材料性质:连杆轴颈的材料性质也会对磨损量产生影响。
不同的材料具有不同的硬度、韧性和耐磨性等特性,因此需要选择合适的材料来制造连杆轴颈,以保证其具有足够的耐磨性能。
综上所述,连杆轴颈的最大磨损量是一个相对的概念,需要根据具体情况进行调整和优化。
一般来说,连杆轴颈的最大磨损量应该控制在一定的范围内,以保证机器的正常运
行和延长机器的使用寿命。
- 1、下载文档前请自行甄别文档内容的完整性,平台不提供额外的编辑、内容补充、找答案等附加服务。
- 2、"仅部分预览"的文档,不可在线预览部分如存在完整性等问题,可反馈申请退款(可完整预览的文档不适用该条件!)。
- 3、如文档侵犯您的权益,请联系客服反馈,我们会尽快为您处理(人工客服工作时间:9:00-18:30)。
连杆轴颈磨削的分度误差分析
连杆轴颈的分度误差示意图
各个连杆轴颈的磨削顺序是P4-P1-P2-P3。
首先对P4和P1进行磨削加工,然后松开夹具,由分度头上的菱形分度头驱动整个曲轴翻转一百八十度,再将P2和P3置于磨削位置,夹紧后进行磨削加工。
连杆轴颈的分度误差指的是P2、P3和P4与P1之间相对位置度的误差,误差一般小于0.36毫米。
由于P1和P4为同一轴线一次装卡,P2和P3为另一轴线二次装卡,所以P1和P4之间及P2和P3之间会出现较大偏差的机率不大。
在这里我们主要研究的是P1和P4与P2和P3在180°方向上的理论位置与实际分度位置之间的误差。
在进行实际的测量时,我们以分度销孔进行角向定位,首先用百分表测量P1的位置并且设为零位,然后将曲轴整个翻转一百八十度,再在同样的位置测量P2和P3轴颈,这时在百分表上显示出来的数值就是分度误差。
如果百分表的表针
在显示的是“—”方向的负值,就将轴颈置于逆向偏移位置,连杆轴颈的轴心线在上图中的H点,图中的t值指的就是分度误差值(百分表测量出来的读数)。
由于P1和P4经过磨削处理后,分度头液压装置的动作分度盘需要顺时针旋转一百八十度后,反靠在棘爪上进行定位,分度销驱动整个曲轴也旋转同样的角度,这时的理想状态是P2和P3应该在下边磨削的位置E处,P1和P4则应在曲轴主轴颈的正上方F处,即主轴颈拐颈中心F和J的连线上。
实际上,分度盘转过的β角度不足一百八十度,分度就会不到位,从而导致磨削的连杆轴颈也会产生同样误差。
很显然造成这个误差的原因是由于分度盘上的定位面M处出现磨损或者N处高出,正确的误差纠正方法就是在分度盘的M处加垫或者在N处进行修磨。
加垫过程在实施起来会有一些困难,一般的处理方法是将分度盘拆下来,然后在磨床上对N面进行修磨处理。
由于分度盘M和N处的半径与轴颈半径(轴颈中心至主轴颈中心距离)的尺寸很相近,因此轴颈偏差数值与M处的磨损值也相近似,这时我们可以按照测量时百分表显示的偏差读数修磨,使M和N调整到180°分度。
假如出现顺向的偏差,那么表现形式就与逆向偏差正好相反,我们可以通过修整M面进行相应的调整。