实验8- 莫来石质高温陶瓷材料的成型和烧结
陶瓷材料设计与高温制备实验
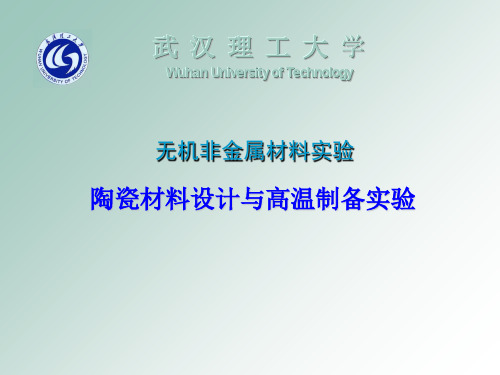
WHUT
●粘土的工艺性能
(1)可塑性:可塑性是指含工作水分的泥团,在一定外力 作用下产生形变,除去外力仍保持其形变性能的能力(可塑性 指标和可塑性指数)
WHUT
2、石英类原料
● 用于陶瓷工业的石英主要有砂岩、石英岩、石英砂等。
这些矿物中它们的主要成分是SiO2,常含有少量杂质成分,如 Al2O3、Fe2O3等
● 石英在陶瓷生产中的作用
a. 在烧结前,石英是瘠性原料,对泥料的可塑性起调节作用 ,防止坯体变形。
b. 在高温由于部分石英溶解于液相中,增加熔体的粘度。未 溶解的石英颗粒,则构成骨架。可防止坯体变形。
武汉理工大学
WWuuhhaannUUnniivveerrssiittyyooffTTeecchhnnoollooggyy
无机非金属材料实验
陶瓷材料设计与高温制备实验
一、陶瓷的种类
WHUT
传统陶瓷:以粘土为主要原料,并与其他矿物原料经过破 碎混和成型烧成等过程而制得的制品。如:
特种陶瓷: 热学功能、力学性能、 生物功能、电磁功能
(2)离子交换性:粘土粒子因表面层的断键和晶格内部离 子的不等价置换而带电,它能吸附溶液中的异性离子,这种被 吸附的离子又可被其他离子所置换。
(3)触变性:粘土泥浆或可塑泥团在静置以后变稠或凝固 ,当受到搅拌或振动时,粘度降低而流动性增加,再放置一段 时间后又能恢复原来状态,
(4)膨化性: 粘土加水后体积膨胀的性质。
矿物名称 α×10-6C-1
LAS系统的平均线热膨胀系数
陶瓷烧成与烧结
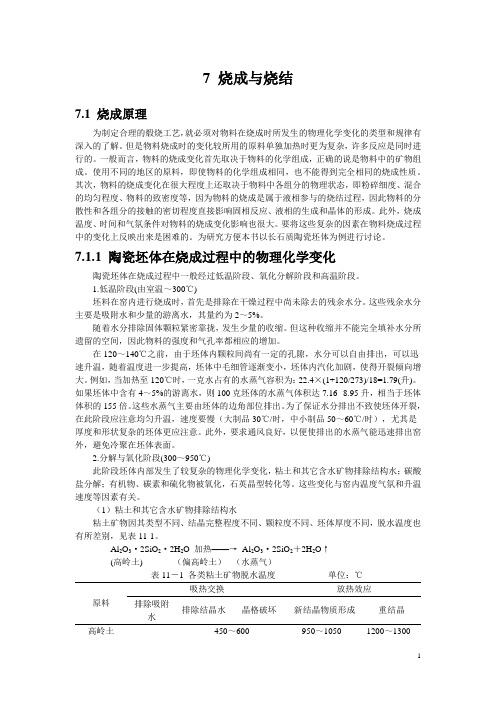
7 烧成与烧结7.1 烧成原理为制定合理的煅烧工艺,就必须对物料在烧成时所发生的物理化学变化的类型和规律有深入的了解。
但是物料烧成时的变化较所用的原料单独加热时更为复杂,许多反应是同时进行的。
一般而言,物料的烧成变化首先取决于物料的化学组成,正确的说是物料中的矿物组成。
使用不同的地区的原料,即使物料的化学组成相同,也不能得到完全相同的烧成性质。
其次,物料的烧成变化在很大程度上还取决于物料中各组分的物理状态,即粉碎细度、混合的均匀程度、物料的致密度等,因为物料的烧成是属于液相参与的烧结过程,因此物料的分散性和各组分的接触的密切程度直接影响固相反应、液相的生成和晶体的形成。
此外,烧成温度、时间和气氛条件对物料的烧成变化影响也很大。
要将这些复杂的因素在物料烧成过程中的变化上反映出来是困难的。
为研究方便本书以长石质陶瓷坯体为例进行讨论。
7.1.1 陶瓷坯体在烧成过程中的物理化学变化陶瓷坯体在烧成过程中一般经过低温阶段、氧化分解阶段和高温阶段。
1.低温阶段(由室温~300℃)坯料在窑内进行烧成时,首先是排除在干燥过程中尚未除去的残余水分。
这些残余水分主要是吸附水和少量的游离水,其量约为2~5%。
随着水分排除固体颗粒紧密靠拢,发生少量的收缩。
但这种收缩并不能完全填补水分所遗留的空间,因此物料的强度和气孔率都相应的增加。
在120~140℃之前,由于坯体内颗粒间尚有一定的孔隙,水分可以自由排出,可以迅速升温,随着温度进一步提高,坯体中毛细管逐渐变小,坯体内汽化加剧,使得开裂倾向增大。
例如,当加热至120℃时,一克水占有的水蒸气容积为:22.4×(1+120/273)/18=1.79(升)。
如果坯体中含有4~5%的游离水,则100克坯体的水蒸气体积达7.16--8.95升,相当于坯体体积的155倍。
这些水蒸气主要由坯体的边角部位排出。
为了保证水分排出不致使坯体开裂,在此阶段应注意均匀升温,速度要慢(大制品30℃/时,中小制品50~60℃/时),尤其是厚度和形状复杂的坯体更应注意。
陶瓷材料烧结工艺和性能测试实验指导书

陶瓷材料烧结工艺和性能测试实验指导书1 实验目的和意义1)了解陶瓷材料的烧结和性能检测的工艺流程,掌握吸水率,表面气孔率,实际密度,线收缩率的测定方法。
2)利用实验找出材料的最优烧结工艺,包括烧结温度和烧结时间。
2 实验背景知识2.1 烧结实验在粉体变成的型坯中,颗粒之间结合主要靠机械咬合或塑化剂的粘合,型坯的强度不高。
将型坯在一定的温度下进行加热,使颗粒间的机械咬合转变成直接依靠离子键,共价键结合,极大的提高材料的强度,这个过程就是烧结。
陶瓷材料的烧结分为三个阶段,升温阶段,保温阶段和降温阶段。
在升温阶段,坯体中往往出现挥发分排出、有机粘合剂等分解氧化、液相产生、晶粒重排与长大等微观现象。
在操作上,考虑到烧结时挥发分的排除和烧结炉的寿命,需要在不同阶段有不同的升温速率。
保温阶段指型坯在升到的最高温度(通常也叫烧结温度)下保持的过程。
粉体烧结涉及组成原子、离子或分子的扩散传质过程,是一个热激活过程,温度越高,烧结越快。
在工程上为了保证效率和质量,保温阶段的最高温度很有讲究。
烧结温度与物料的结晶化学特性有关,晶格能大,高温下质点移动困难,不利于烧结。
烧结温度与材料的熔点有关系,对陶瓷而言是其熔点的0.7—0.9 倍,对金属而言是其熔点的0.4-0.7 倍。
冷却阶段是陶瓷材料从最高温度到室温的过程,冷却过程中伴随有液相凝固、析晶、相变等物理化学变化。
冷却方式、冷却速度快慢对陶瓷材料最终相的组成、结构和性能等都有很大的影响,所以所有的烧结实验需要精心设计冷却工艺。
由于烧结的温度如果过高,则可能出现材料颗粒尺寸大,相变完全等严重影响材料性能的问题,晶粒尺寸越大,材料的韧性和强度就越差,而这正是陶瓷材料的最大问题,所以要提高陶瓷的韧性,就必须降低晶粒的尺寸,降低烧结温度和时间。
但是在烧结时,如果烧结温度太低,没有充分烧结,材料颗粒间的结合不紧密,颗粒间仍然是靠机械力结合,没有发生颗粒的重排,原子的传递等过程,那么材料就是不可用的。
陶瓷的制作实验报告
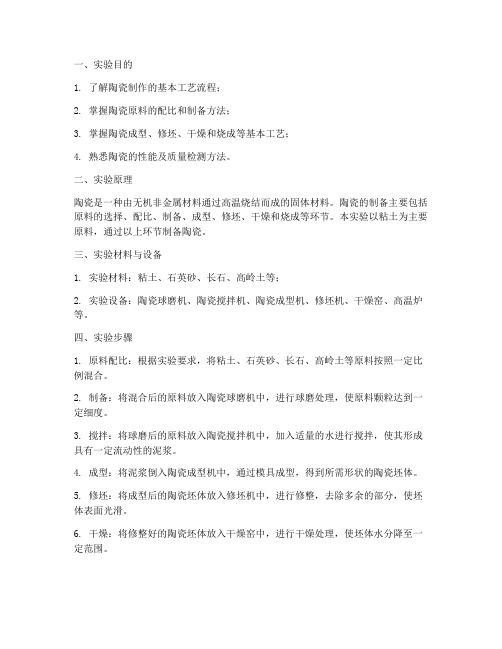
一、实验目的1. 了解陶瓷制作的基本工艺流程;2. 掌握陶瓷原料的配比和制备方法;3. 掌握陶瓷成型、修坯、干燥和烧成等基本工艺;4. 熟悉陶瓷的性能及质量检测方法。
二、实验原理陶瓷是一种由无机非金属材料通过高温烧结而成的固体材料。
陶瓷的制备主要包括原料的选择、配比、制备、成型、修坯、干燥和烧成等环节。
本实验以粘土为主要原料,通过以上环节制备陶瓷。
三、实验材料与设备1. 实验材料:粘土、石英砂、长石、高岭土等;2. 实验设备:陶瓷球磨机、陶瓷搅拌机、陶瓷成型机、修坯机、干燥窑、高温炉等。
四、实验步骤1. 原料配比:根据实验要求,将粘土、石英砂、长石、高岭土等原料按照一定比例混合。
2. 制备:将混合后的原料放入陶瓷球磨机中,进行球磨处理,使原料颗粒达到一定细度。
3. 搅拌:将球磨后的原料放入陶瓷搅拌机中,加入适量的水进行搅拌,使其形成具有一定流动性的泥浆。
4. 成型:将泥浆倒入陶瓷成型机中,通过模具成型,得到所需形状的陶瓷坯体。
5. 修坯:将成型后的陶瓷坯体放入修坯机中,进行修整,去除多余的部分,使坯体表面光滑。
6. 干燥:将修整好的陶瓷坯体放入干燥窑中,进行干燥处理,使坯体水分降至一定范围。
7. 烧成:将干燥后的陶瓷坯体放入高温炉中,进行高温烧结,使其形成致密的陶瓷材料。
五、实验结果与分析1. 原料配比对陶瓷性能的影响:实验结果表明,粘土、石英砂、长石、高岭土等原料的配比对陶瓷的强度、密度、耐热性等性能有较大影响。
通过调整原料配比,可以得到性能优异的陶瓷。
2. 成型工艺对陶瓷性能的影响:实验结果表明,成型工艺对陶瓷的尺寸精度、表面质量等有较大影响。
合理的成型工艺可以提高陶瓷的质量。
3. 干燥和烧成工艺对陶瓷性能的影响:实验结果表明,干燥和烧成工艺对陶瓷的强度、密度、耐热性等性能有较大影响。
合理的干燥和烧成工艺可以提高陶瓷的质量。
六、实验结论1. 通过本次实验,掌握了陶瓷制作的基本工艺流程,了解了陶瓷原料的配比和制备方法;2. 通过实验,了解了陶瓷成型、修坯、干燥和烧成等基本工艺对陶瓷性能的影响;3. 通过实验,熟悉了陶瓷的性能及质量检测方法。
刚玉莫来石材料烧成过程研究

1前言刚玉莫来石材料是一种常用的耐火材料,原料易得,价格适中,可根据形状、材质、用途等方便地选用不同的生产工艺,在许多行业获得了广泛的应用。
由于生产难度不高,现有的文献资料多数探讨和总结刚玉莫来石材料的性能和用途、原料的选择优化、成本降低途径、生产设备的改进等方面[1-4]。
在生产工艺方面,有研究探索添加不同的助剂来促进烧结,降低成本[5-6]。
正因为该种材料容易烧结,专门针对该材料烧成工艺进行的研究很少。
实际上,刚玉莫来石材料的性能不光取决于化学成分,很大程度上体现在材料内部的结构上,而最终材料中刚玉晶体、莫来石晶体、气孔、玻璃相等物相结构是在烧成过程中形成的。
烧成工艺对其结构有不同程度的影响,并因此影响到实际的使用性能。
本文就是专门针对刚玉莫来石材料的烧成工艺进行研究,揭示出烧成过程中材料内部结构的变化规律,期望对实际的生产过程起到指导作用。
2实验采用两种典型的的刚玉莫来石混合料G 料和J 料。
其中G 料为喷雾造粒料,J 料为粉碎造粒料,其成分如表1。
其中,加入的含锆原料期望形成氧化锆增强增韧效果。
在试验压片机上干压试样,试样规格为圆片φ60mm ×3mm 和长条100mm ×10mm ×10mm 。
其中长条试样用来测试抗弯强度,圆片试样用来测试其余性能。
最杨华亮1,2(1.佛山市南海金刚新材料有限公司,佛山528031;2.佛山市陶瓷研究所股份有限公司,佛山528000)探索了从低温到高温的烧结过程中,坯体烧成收缩、吸水率、密度、抗弯强度等随烧成温度的变化规律。
刚玉莫来石材料在从低温到高温的烧成过程中,经历了四个典型的特征阶段:粘土和细粉的收缩阶段;莫来石细晶大量形成阶段;莫来石晶体长大产生疏松效应阶段;液相烧结阶段。
这四个阶段都有各自典型的性能参数变化规律。
烧成研究与探讨Research &DiscussionCopyright©博看网 . All Rights Reserved.Al 2O 3SiO 2CaO+MgO K 2O+Na 2O Fe 2O 3+TiO 2ZrO 2其它G 料75~8515~200~10~0.50~10~50~1J 料70~8015~200~10~0.50~10~50~1表1混合料成分高烧成温度为1000~1650℃,温度间隔为50℃,每个温度点烧3个试样,数据取平均。
实习报告:陶瓷烧结
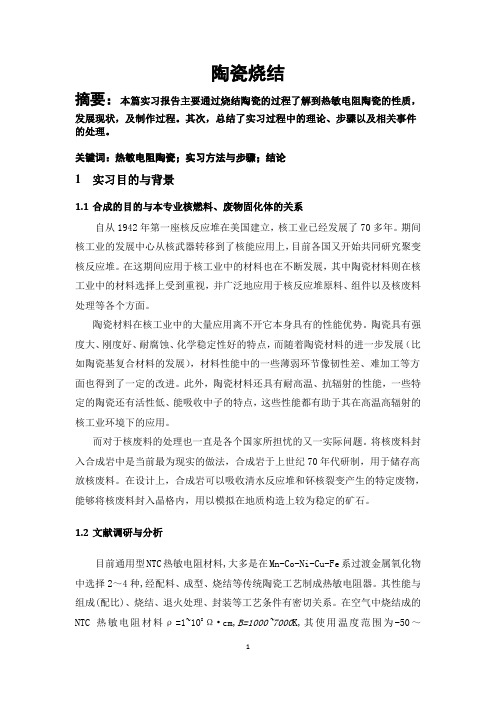
陶瓷烧结摘要:本篇实习报告主要通过烧结陶瓷的过程了解到热敏电阻陶瓷的性质,发展现状,及制作过程。
其次,总结了实习过程中的理论、步骤以及相关事件的处理。
关键词:热敏电阻陶瓷;实习方法与步骤;结论1 实习目的与背景1.1 合成的目的与本专业核燃料、废物固化体的关系自从1942年第一座核反应堆在美国建立,核工业已经发展了70多年。
期间核工业的发展中心从核武器转移到了核能应用上,目前各国又开始共同研究聚变核反应堆。
在这期间应用于核工业中的材料也在不断发展,其中陶瓷材料则在核工业中的材料选择上受到重视,并广泛地应用于核反应堆原料、组件以及核废料处理等各个方面。
陶瓷材料在核工业中的大量应用离不开它本身具有的性能优势。
陶瓷具有强度大、刚度好、耐腐蚀、化学稳定性好的特点,而随着陶瓷材料的进一步发展(比如陶瓷基复合材料的发展),材料性能中的一些薄弱环节像韧性差、难加工等方面也得到了一定的改进。
此外,陶瓷材料还具有耐高温、抗辐射的性能,一些特定的陶瓷还有活性低、能吸收中子的特点,这些性能都有助于其在高温高辐射的核工业环境下的应用。
而对于核废料的处理也一直是各个国家所担忧的又一实际问题。
将核废料封入合成岩中是当前最为现实的做法,合成岩于上世纪70年代研制,用于储存高放核废料。
在设计上,合成岩可以吸收清水反应堆和钚核裂变产生的特定废物,能够将核废料封入晶格内,用以模拟在地质构造上较为稳定的矿石。
1.2 文献调研与分析目前通用型NTC热敏电阻材料,大多是在Mn-Co-Ni-Cu-Fe系过渡金属氧化物中选择2~4种,经配料、成型、烧结等传统陶瓷工艺制成热敏电阻器。
其性能与组成(配比)、烧结、退火处理、封装等工艺条件有密切关系。
在空气中烧结成的NTC热敏电阻材料ρ=1~108Ω•cm,B=1000~7000K,其使用温度范围为-50~+300℃。
随着NTC热敏电阻器应用领域的扩大,对其性能的要求也日益提高。
就目前情形而言,对能在高温条件下使用的NTC元件,要求十分严格,例如在汽车发动机使用电子计算机控制系统后,为了限制尾气中有害气体的排放量(CO、NOx、CHx等有害气体),要求对排气口温度进行有效的测控。
堇青石-莫来石质陶瓷板的试验性研究

1引言随陶瓷砖技术的不断成熟,大规格、超厚、超薄的应用范围已经不仅仅局限于作为建筑材料进行室内装饰,其作为跨界产品已经进入家具领域,兼具防火耐高温、耐用不变形、防污抗腐蚀、环保无甲醛的优良性能,可广泛应用于定制家具的柜体、门板、台面等。
瓷质砖的生产工艺成熟,通常以黏土、长石、砂等为主要原料经过高温烧结制成,作为一种大批量的工业化产品,其生产工艺包括球磨造粒、冲压成形、烧成、抛磨切割等工序,烧成工序通常选用烧成速度快产能高的辊道窑烧成,烧成温度为1000℃~1250℃,烧成周期为40~180min 。
按照国家标准,瓷质砖的吸水率≤0.5%,烧结程度高。
而目前工艺生产的建筑陶瓷材料热膨胀系数较大,以100℃~400℃的线膨胀系数(热膨胀系数)计算,常规瓷质砖为170~210×10-7∕℃,这对于作为墙地砖应用是可以的,但随着建筑陶瓷材料应用的拓展,除了作为墙面或地面装饰材料外,灶台面板、柜体面板、门板等家装领域均开始尝试应用陶瓷材料,但常规的建筑陶瓷材料的膨胀系数较大,而且受到外力冲击容易折断破碎。
当然,烧结温度高于1300℃的特种陶瓷可以很好的解决此问题,但特种陶瓷造价高,难以在建筑陶瓷中广泛应用。
2试验2.1技术思路通过在原料中添加堇青石-莫来石质耐火材料或者针状莫来石-堇青石来降低瓷质砖的膨胀系数、并提高瓷质砖的抗折强度,使之具有良好的抗热震性和抗冲击性。
其原料中使用莫来石-堇青石为降低膨胀系数材料、使用锂瓷石为强助熔剂,原料经造粒、成形后入窑烧成获得低膨胀系数瓷质板材。
2.2原料堇青石-莫来石粉末的物相分析如图1所示。
对堇青石-莫来石粉末的XRD 分析,粉体物相占比如下:堇青石(Mg 2Al 4Si 5O 18,29~31%)、莫来石(Al 6Si 2O 13,33~35%)、刚玉(Al 2O 3,1.5~2.5%)、尖晶石(MgAl 2O 4,0.5~1.5%)和石英(SiO 2,0.5%),可以在瓷质砖粉料配方中加入堇青石-莫来石,高温快烧后坯体中仍然含有大量的堇青石和莫来石物相,这样就可以改善产品的热膨胀系数、抗折强度和热稳定性。
陶瓷材料的烧成与烧结实验

陶瓷材料的烧成与烧结实验一、实验目的本实验课通过各组同学的实验结果,完成陶瓷材料的烧成工艺实验。
二、实验原理烧结的实质是粉坯在适当的气氛下被加热,通过一系列的物理、化学变化,使粉粒间的粘结发生质的变化,坯块强度和密度迅速增加,其他物理、化学性能也得到明显的改善。
经过长期研究,烧结机制可归纳为:①粘性流动;②蒸发与凝聚;③体积扩散;④表面扩散;⑤晶界扩散;⑥塑性流动等。
烧结是十个复杂的物理、化学变化过程,是多种机制作用的结果。
坯体在升温过程中相继会发生下列物理、化学变化:(1) 蒸发吸附水:(约l00℃)除去坯体在干燥时未完全脱去的水分;(2) 粉料冲结晶水排除,(300~700℃);(3) 分解反应;(300~950℃)坯料中碳酸盐等分解,排除二氧化碳等气体。
(4) 碳、有机物的氧化;(450—800℃)燃烧过程,排除大量气体;(5) 晶型转变;(550一1300℃)石英、氧化铝等的相转变;(6) 烧结前期:经蒸发、分解、燃烧反应后,坯体变得更不致密,气孔可达百分之几十。
在表面能减少的推动力作用下,物质通过不周的扩散途径何颗粒接触点(颈部)和气孔部位填充,使颈部不断长大逐步减少气孔体积;细小颗粒间形成晶界,并不断长大;使坯体变得致密化。
在这过程中,连通的气孔不断缩小,晶粒逐渐长大,直至气孔不再连通,形成孤立的气孔,分布在晶粒相交位置,此时坯体密度可达理论密度的90%;(7) 烧结后期:晶界上的物质继续向气孔扩散、填充,使孤立的气孔逐渐变小,一般气孔随晶界一起移动,直至排出,使烧结体致密化。
·如再继续在高温下烧结,就只有晶粒长大过程。
如果在烧结后期,温度升得太快,坯体内封闭气孔来不及扩散、排出,只是随温度上升而膨胀,这样,会造成制品的“涨大”,密度反而会下降。
某些材料在烧结时会出现液相;加快;了烧络的过程。
可得到更致密的制品;(8)降温阶段:冷却时某些材料会发生相变,因而控制冷却制度,也可以控制制品的相组成:如要获得合适相组成的部分稳定的氧化锆固体电解质,冷却阶段的温度控制是很重要的;坯体烧结后在宏观上的变化是:体积收缩、致密度提高、强度增加。
陶瓷材料高温制备实验精品PPT课件

3. 陶瓷实验流程
烧成曲线的制定
根据经验公式计算出最高烧结温度后,制定烧成 曲线。参考数据如下:
地砖和仿花岗岩玻化砖
T烧 = 1200~1280℃;
釉面砖
T烧 = 1200~1280℃;
低温快烧的釉面砖 T烧 = 1000~1080℃;
耐热瓷
T烧= 1280~1320℃;
6.烧成 上述5种产品种的烧成温度基本一致,但最高烧成温度不同。 因为各地原料的成分不同,每种产品的烧成温度都有波动。
需经烧成实验确定。
3. 陶瓷实验流程
二. 烧成制度的制定
烧成制度包括温度制度、气氛制度和压力制度。对一个特定 的产品而言,制定好温度制度(建立温度与时间的关系)和控制 好烧成气氛是关键。压力制度起保证前两个制度顺利实施的作用。 三者之间互相协调构成一个合理的烧成制度。
3. 陶瓷实验流程
4.压制成形 为方便性能测试,可分别压制成条、片的试样。
条状试样,3克 / 条 ,成型压力 20 ~ 30 KN . 压制成形后立即对试
样编号,用游标卡尺量尺 寸并记录。
3. 陶瓷实验流程
5.干燥 将试样放入100~105℃的烘箱中烘8~10小时(也可自然干
燥2~3天)后,取出,放入干燥器。 试样冷却后,量取干燥后的尺寸并记录,计算 干燥收缩率 。
写在最后
成功的基础在于好的学习习惯
The foundation of success lies in good habits
14
谢谢大家
荣幸这一路,与你同行
It'S An Honor To Walk With You All The Way
讲师:XXXXXX XX年XX月XX日
陶瓷成型工艺实验报告

一、实验目的1. 了解陶瓷成型工艺的基本原理和方法;2. 掌握陶瓷成型过程中的各个工艺参数对成型效果的影响;3. 熟悉陶瓷成型工艺的操作技术和安全注意事项;4. 培养实验操作能力,提高对陶瓷制品生产的认识。
二、实验原理陶瓷成型工艺是将陶瓷原料加工成具有一定形状、尺寸和强度的生坯的过程。
根据成型方法的不同,陶瓷成型可分为可塑法成型、注浆法成型和干压法成型等。
1. 可塑法成型:将陶瓷原料制备成泥团,利用其可塑性手工拉坯成型、机械旋压成型或滚压成型,还可以利用模具印坯成型,以及徒手捏塑成型。
2. 注浆法成型:将陶瓷原料制成浆料,通过模具注入,待浆料凝固后取出成坯。
3. 干压法成型:采用压力将陶瓷粉料压制成一定形状的坯体。
其实质是在外力作用下,粉体颗粒在模具内相互靠近,并借内摩擦力牢固地结合起来,保持一定的形状。
三、实验仪器与材料1. 仪器:陶瓷成型机、模具、刀具、烘箱、天平、计时器等。
2. 材料:陶瓷原料、模具、粘结剂、润滑剂等。
四、实验步骤1. 准备工作:根据实验要求,将陶瓷原料按照配方进行混合、研磨,制成浆料或泥团。
2. 可塑法成型:将泥团放置在成型机上进行拉坯成型,或利用模具进行印坯成型。
3. 注浆法成型:将浆料注入模具,待浆料凝固后取出成坯。
4. 干压法成型:将陶瓷粉料填充到模具内,通过压头施加压力,压制成一定形状的坯体。
5. 后处理:将成坯进行晾干、脱模、修整等工序。
6. 烧结:将成坯放入烘箱中进行烧结,烧结温度根据陶瓷原料和制品要求而定。
五、实验结果与分析1. 成型效果:通过实验,观察不同成型方法对陶瓷制品形状、尺寸和强度的影响。
2. 工艺参数对成型效果的影响:分析压力、温度、时间等工艺参数对成型效果的影响。
3. 成型缺陷:分析成型过程中出现的缺陷,如分层、裂纹、表面剥落等,并提出改进措施。
六、实验结论1. 陶瓷成型工艺是陶瓷制品生产的重要环节,掌握成型方法对提高制品质量至关重要。
2. 可塑法成型、注浆法成型和干压法成型是常用的陶瓷成型方法,可根据不同需求选择合适的成型方法。
高温陶瓷材料的制备及性能评价

高温陶瓷材料的制备及性能评价高温陶瓷材料是一类能够在极高温度下保持优异性能的材料。
它们具有许多出色的特性,如高强度、高硬度、良好的耐磨性和耐腐蚀性等。
这些性能使得高温陶瓷材料在许多领域得到广泛应用,如航空航天、汽车、电子、能源等。
制备高温陶瓷材料的方法有多种,其中最常见的是烧结法。
烧结法利用高温将粉末材料加热到临界温度,使其颗粒间发生熔结并形成致密的陶瓷体。
这种方法可以生产出高质量的陶瓷材料,并且可根据需要进行不同形式的成型和设计。
在制备过程中,粉末材料的选择对于最终的材料性能起着关键作用。
一般来说,高温陶瓷材料的主要成分是氧化物,如氧化铝、氧化锆、氧化钛等。
这些氧化物具有优异的化学稳定性和热稳定性,适用于高温环境。
除了粉末材料的选择,制备过程中的烧结条件也是影响材料性能的重要因素。
合适的烧结温度和时间可以促进粉末颗粒之间的结合,并消除内部缺陷,从而提高材料的强度和致密性。
此外,添加适量的添加剂可改善材料的烧结性能,如增加材料的塑性和流动性。
制备完成后,高温陶瓷材料的性能评价是确保材料质量和可靠性的关键环节。
常用的性能评价指标包括密度、硬度、抗弯强度、热膨胀系数和导热性等。
材料密度是一个重要的指标,它直接影响材料的强度和韧性。
通过测量材料的质量和体积,可以计算出材料的密度。
高密度的陶瓷材料具有更好的机械性能和抗磨性。
硬度是材料抵抗外部力量侵蚀的能力的指标。
通常使用维氏硬度计或洛氏硬度计来测量高温陶瓷材料的硬度。
高硬度材料具有更好的耐磨性和抗刮擦能力。
抗弯强度是衡量材料在受力时的抗拉强度的指标。
通过在两个支点上施加力并测量断裂弯曲的力,可以确定材料的抗弯强度。
高抗弯强度的材料对外部力的抵抗能力更强。
热膨胀系数是材料在温度变化时线性膨胀或收缩的程度的指标。
高温陶瓷材料应具有较低的热膨胀系数,以避免在温度变化时产生内部应力和裂纹。
导热性是材料传导热量的能力的指标。
高温陶瓷材料通常具有较低的导热性,这使其在高温环境下能够有效地保持冷却性能。
陶瓷材料的热压烧结实验

陶瓷材料的热压烧结实验陶瓷材料的热压烧结实验一、实验目的1.掌握热压烧结的基本原理和特点以及热压烧结适用的范围;2.了解热压炉的基本构造;3.掌握热压炉的基本操作要领;4.了解影响热压烧结的主要因素。
二、实验原理热压烧结是区别于常规烧结的特种烧结方法之一,它是在陶瓷或金属粉体加热的同时施加压力。
装在耐高温的磨具中的粉体颗粒在压力和温度的双重作用下,逐步靠拢、滑移、变形并依靠各种传质机制(如蒸发凝聚、扩散、粘塑性流动、溶解沉淀,视组分不同而以不同的机制为主),完成致密化过程,形成外部轮廓与模腔形状一致的致密烧结体。
因此,热压烧结可将压制成型和烧结一并完成。
由于在高温下持续有压力的作用,扩散距离缩短,塑性流动过程加快,并影响到其他传质过程的加速,热压烧结致密化的温度(烧结温度)要比常规烧结低150~200℃,保温时间也短的多(有时仅需20~30min)。
与常规烧结相比,热压烧结体的气孔率低,相对密度高;烧结温度低、保温时间短,晶粒不易长大,所以热压烧结体的力学性能高。
原则上,凡能用常规烧结的陶瓷材料或金属材料均可用热压烧结来获得更为致密的坯体,但热压烧结更适用于一些用常规方法难以烧结致密的材料,如各种非氧化物陶瓷、难熔金属、金属-无机复合材料等。
热压烧结的主要优点在于:成型压力小,烧结温度低,烧结时间短,制品密度高、晶粒细小。
存在的缺点是:制品形状简单、表面较粗糙,尺寸精度低,一般需后续清理和机械加工,单件生产、效率低,对模具材料要求高,耗费大。
三、热压炉的基本结构热压炉的基本构造可分为两部分:一为炉体和加热系统,一为加压系统。
炉体通常为圆柱形双层壳体,用耐热性好的合金钢制成,夹层内通冷却水对炉壁、底、盖进行冷却,以保护炉体金属;加热常用高纯石墨的电阻发热,由于石墨电阻小,需用变压器以低电压、大电流加在石墨发热元件上;在发热元件与炉体之间,设置有隔热层,以防止炉内的高温散失,同时也保护炉体;为防止石墨氧化,热压时必须在真空或非氧化气氛下进行,所以,炉体需具有很好的密封性,符合真空系统要求,并带有机械真空泵、扩散泵。
高温合成陶瓷材料的制备工艺和性能研究
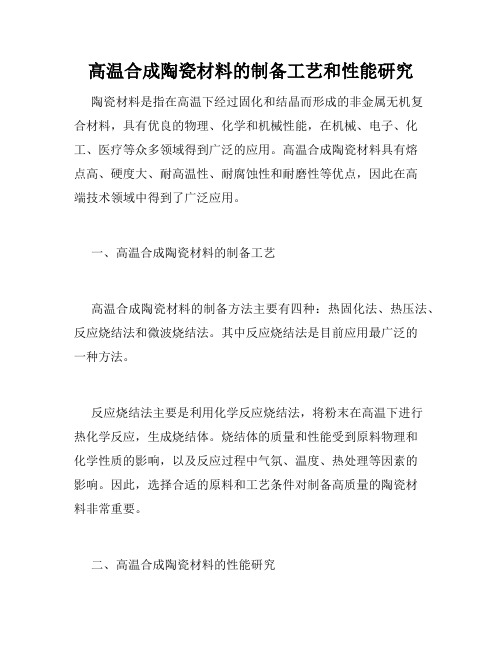
高温合成陶瓷材料的制备工艺和性能研究陶瓷材料是指在高温下经过固化和结晶而形成的非金属无机复合材料,具有优良的物理、化学和机械性能,在机械、电子、化工、医疗等众多领域得到广泛的应用。
高温合成陶瓷材料具有熔点高、硬度大、耐高温性、耐腐蚀性和耐磨性等优点,因此在高端技术领域中得到了广泛应用。
一、高温合成陶瓷材料的制备工艺高温合成陶瓷材料的制备方法主要有四种:热固化法、热压法、反应烧结法和微波烧结法。
其中反应烧结法是目前应用最广泛的一种方法。
反应烧结法主要是利用化学反应烧结法,将粉末在高温下进行热化学反应,生成烧结体。
烧结体的质量和性能受到原料物理和化学性质的影响,以及反应过程中气氛、温度、热处理等因素的影响。
因此,选择合适的原料和工艺条件对制备高质量的陶瓷材料非常重要。
二、高温合成陶瓷材料的性能研究1.物理性能高温合成陶瓷材料具有高硬度、高韧性、耐高温和耐磨性能。
其中高硬度和高韧性是两个相互矛盾的参数。
大多数材料的硬度越高,韧性就越低。
但是,高温合成陶瓷材料可以通过控制晶体结构和晶粒尺寸来达到高硬度和高韧性的平衡。
2.化学性能高温合成陶瓷材料具有良好的耐腐蚀性能,适用于在酸、碱、盐等极端环境下使用。
这主要取决于材料的化学稳定性和化学反应活性。
很多高温合成陶瓷材料具有较好的抗氧化性能,可以在高温下长时间保持稳定性能。
3.机械性能高温合成陶瓷材料具有极高的抗拉强度、耐冲击性和耐磨性。
这种优越的机械性能是由于其结构和晶粒尺寸的优化以及材料中的相互作用力和晶界强化机制。
三、高温合成陶瓷材料的应用领域高温合成陶瓷材料在众多领域得到了广泛应用。
下面列举一些典型的应用领域。
1.航空航天领域高温合成陶瓷材料可以用于制造发动机和涡轮机的叶片、高温密封环等部件。
与金属高温部件相比,陶瓷材料具有更好的高温稳定性和热膨胀系数匹配性。
2.电子和光学领域高温合成陶瓷材料可以制成电子元器件、光学玻璃、激光器材料和光学纤维等。
这些材料具有优良的光学性能、稳定性能和尺寸精度,能够满足各种实际应用需求。
陶瓷烧成实训报告
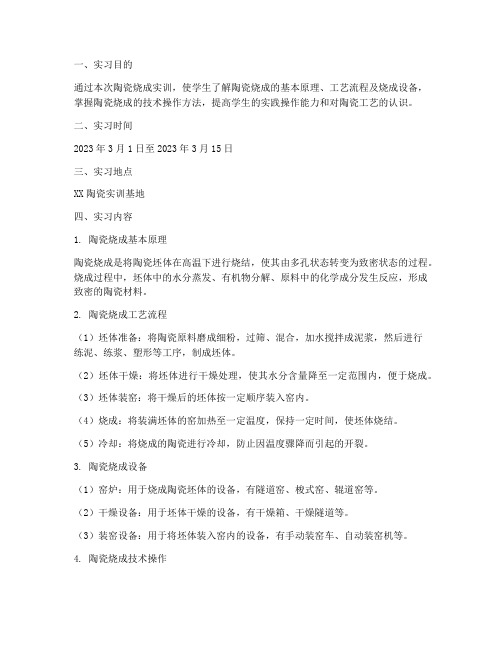
一、实习目的通过本次陶瓷烧成实训,使学生了解陶瓷烧成的基本原理、工艺流程及烧成设备,掌握陶瓷烧成的技术操作方法,提高学生的实践操作能力和对陶瓷工艺的认识。
二、实习时间2023年3月1日至2023年3月15日三、实习地点XX陶瓷实训基地四、实习内容1. 陶瓷烧成基本原理陶瓷烧成是将陶瓷坯体在高温下进行烧结,使其由多孔状态转变为致密状态的过程。
烧成过程中,坯体中的水分蒸发、有机物分解、原料中的化学成分发生反应,形成致密的陶瓷材料。
2. 陶瓷烧成工艺流程(1)坯体准备:将陶瓷原料磨成细粉,过筛、混合,加水搅拌成泥浆,然后进行练泥、练浆、塑形等工序,制成坯体。
(2)坯体干燥:将坯体进行干燥处理,使其水分含量降至一定范围内,便于烧成。
(3)坯体装窑:将干燥后的坯体按一定顺序装入窑内。
(4)烧成:将装满坯体的窑加热至一定温度,保持一定时间,使坯体烧结。
(5)冷却:将烧成的陶瓷进行冷却,防止因温度骤降而引起的开裂。
3. 陶瓷烧成设备(1)窑炉:用于烧成陶瓷坯体的设备,有隧道窑、梭式窑、辊道窑等。
(2)干燥设备:用于坯体干燥的设备,有干燥箱、干燥隧道等。
(3)装窑设备:用于将坯体装入窑内的设备,有手动装窑车、自动装窑机等。
4. 陶瓷烧成技术操作(1)坯体准备:按照配方要求,将原料磨成细粉,过筛、混合,加水搅拌成泥浆,进行练泥、练浆、塑形等工序。
(2)坯体干燥:将坯体进行干燥处理,使其水分含量降至一定范围内。
(3)坯体装窑:按照窑内布局,将干燥后的坯体装入窑内。
(4)烧成:启动窑炉,按照烧成曲线进行升温、保温、降温等操作。
(5)冷却:将烧成的陶瓷进行冷却,防止开裂。
五、实习总结1. 通过本次陶瓷烧成实训,我对陶瓷烧成的基本原理、工艺流程及烧成设备有了更深入的了解。
2. 在实习过程中,我掌握了陶瓷烧成的技术操作方法,提高了自己的实践操作能力。
3. 在实训过程中,我认识到陶瓷烧成工艺的重要性,以及烧成过程中的质量控制。
陶瓷材料烧结温度和烧结温度范围的测定陶瓷材料烧结温度和烧结

烧后失重=[(G0-G3)/G0] ×100%
(8)
式中 G0 ——干燥试样在空气中质量,g;
G1——干燥试样饱吸煤油后在煤油中质量,g;
G2——干燥试样饱吸煤油后在空气中质量,g;
G3——烧后试样在空气中质量,g;
G4 ——烧后试样饱吸煤油(水)在煤油(水)中质
量,g;
G5——烧后试样饱吸煤油在空气中质量,g;
4.将称过质量的试样放人105~110℃烘箱 内排除煤油,直至将试样中的煤油排完为 止。
5.按编号顺序将试样装人高温炉中,装炉 时炉底和试样之间撒一层薄薄煅烧Al2O3粉, 以免在高温时粘连。装好后开始加热,并 按升温曲线升温,按预定的取样温度取样。
6.每到取样温度点时,应保温15min,然后在电炉内取出 样品,迅速地埋在预先加热的石英粉或Al2O3粉内,以保 证试样在冷却过程中不炸裂。冷至接近室温后,再从石英 粉或氧化铝粉中取出样品。并记好每个取样温度点的温度 及相应取出的样品编号。将焙烧过的试样,用刷子刷去表 面石英粉或Al2O3粉(低温烧后的试样用软毛刷),检查 试样有无开裂、粘砂等缺陷,然后放人105~110℃烘箱中 烘至恒量,放人干燥器内,冷却至室温。
四、实验步骤
1.试样制备:然后把试条锯成为样品,在细砂 纸上磨去毛边棱角,以便堆放。把样品表面刷干 净,编号,再放人烘箱内,在105~110℃温度下烘 干至恒重,取出放在干燥器内冷却至室温备用。
2.在天平上称取干燥后的试样质量。
3.称取饱吸煤油后在煤油中试样质量,饱吸煤 油后在空气中试样质量(试样饱吸煤油的方法同 干燥体积体收缩和干燥气孔率测定)。
(2)为了确定烧成温度范围准确,可将这部分样 品进行孔隙性试验,其结果均应不吸红。若有吸 红的样品,其对应的焙烧温度点应除外,或重新 进行试验。
刚玉莫来石陶瓷高温性能研究

刚玉莫来石陶瓷高温性能研究朱志超梁章发方仁德杨华亮摘要:以粘土、氧化铝粉、刚玉为主要原料制备刚玉莫来石质陶瓷,研究刚玉莫来石陶瓷的高温性能,包括不同温度下的抗折强度、高温弹性模量、高温蠕变率等性能。
试验结果显示,烧成温度在1550℃时,陶瓷试样莫来石晶相生长较好,大部分呈现长柱状及针状,高温强度随温度的升高先上升后下降,在1100℃左右达到最大值;高温弹性模量也呈现相同的趋势,其高温强度与高温弹性模量性能呈正相关关系。
关键词:刚玉莫来石;高温强度;高温弹性模量1 前言刚玉莫来石复相陶瓷材料具有莫来石相熔点高、热膨胀系数低、强度高、抗蠕变性及抗热震性能好的特点,同时具有刚玉相弹性高、耐磨、抗侵蚀抗氧化的特点,且刚玉莫来石原料来源丰富,因此被认为是最有发展前途的高温抗热震陶瓷材料[1],特别是在高温陶瓷窑具行业,例如用于辊道窑高温烧成区的陶瓷辊棒、推板窑的窑具等都大多采用刚玉莫来石质陶瓷。
为了提高生产效率、降低能耗,辊道窑越来越宽,陶瓷产品规格越来越大,这就对陶瓷窑具的要求越来越高,尤其是陶瓷的高温强度及抗热震性能。
2 实验过程2.1 刚玉莫来石陶瓷的制备采用高纯氧化铝、茂名高岭土、刚玉作为原料,设计配方:高岭土15 ~ 20%、氧化铝30 ~ 40%、刚玉40 ~ 50%。
对配方料球磨2 h,料球水比为1:1.5:0.8,干燥后过100目筛。
加水、粘结剂进行二次混料并陈腐24 h,挤压成Ф50 mm×600 mm圆筒状并烘干。
在高温井式电炉中烧成,烧成温度1500℃和1550℃,保温4 h。
2.2 性能表征采用高温抗折仪对试样进行高温强度测试(测试温度由900 ~1350℃,每50℃段测试一次),高温弹性模量蠕变仪测试试样的高温弹性模量(测试温度由900 ~1350℃,每50℃段测试一次)及蠕变率(测试温度1300℃)。
用日本理学X射线衍射仪对试样进行物相测试,SEM对试样微观结构进行测试。
陶瓷的高温烧制
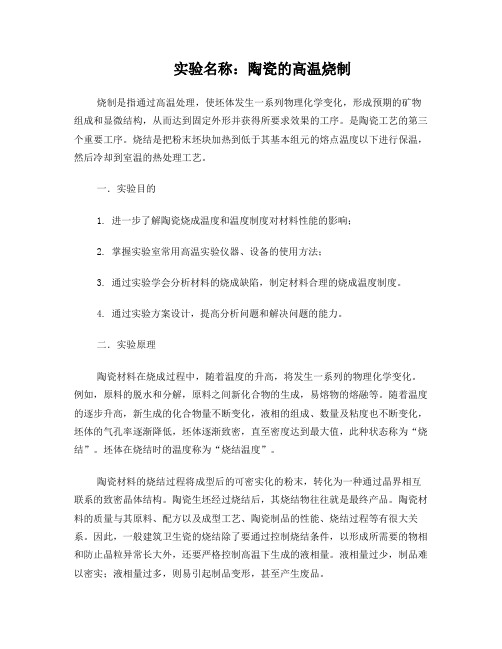
实验名称:陶瓷的高温烧制烧制是指通过高温处理,使坯体发生一系列物理化学变化,形成预期的矿物组成和显微结构,从而达到固定外形并获得所要求效果的工序。
是陶瓷工艺的第三个重要工序。
烧结是把粉末坯块加热到低于其基本组元的熔点温度以下进行保温,然后冷却到室温的热处理工艺。
一.实验目的1. 进一步了解陶瓷烧成温度和温度制度对材料性能的影响;2. 掌握实验室常用高温实验仪器、设备的使用方法;3. 通过实验学会分析材料的烧成缺陷,制定材料合理的烧成温度制度。
4. 通过实验方案设计,提高分析问题和解决问题的能力。
二.实验原理陶瓷材料在烧成过程中,随着温度的升高,将发生一系列的物理化学变化。
例如,原料的脱水和分解,原料之间新化合物的生成,易熔物的熔融等。
随着温度的逐步升高,新生成的化合物量不断变化,液相的组成、数量及粘度也不断变化,坯体的气孔率逐渐降低,坯体逐渐致密,直至密度达到最大值,此种状态称为“烧结”。
坯体在烧结时的温度称为“烧结温度”。
陶瓷材料的烧结过程将成型后的可密实化的粉末,转化为一种通过晶界相互联系的致密晶体结构。
陶瓷生坯经过烧结后,其烧结物往往就是最终产品。
陶瓷材料的质量与其原料、配方以及成型工艺、陶瓷制品的性能、烧结过程等有很大关系。
因此,一般建筑卫生瓷的烧结除了要通过控制烧结条件,以形成所需要的物相和防止晶粒异常长大外,还要严格控制高温下生成的液相量。
液相量过少,制品难以密实;液相量过多,则易引起制品变形,甚至产生废品。
烧结后若继续加热,温度升高,坯体会逐渐软化(烧成工艺上称为过烧),甚至局部熔融,这时的温度称为“软化温度”。
烧结温度和软化温度之间的温度范围称为“烧结温度范围”。
陶瓷的烧成制度包括温度制度:指升温速度、烧成温度、保温时间及冷却速度;气氛制度:氧化、还原、中性或其他气氛;压力制度:窑炉内气体的压力大小;实际生产中还要考虑窑炉加热类型、内部结构和装窑方式等因素。
烧成制度对陶瓷的性能有很大影响,所以实验时要控制好。
陶瓷的烧制实验报告

一、实验目的本次实验旨在了解陶瓷的烧制过程,掌握陶瓷烧制的基本技术,熟悉陶瓷原料的选取、制备、成型、装饰及烧成等各个环节,提高对陶瓷工艺的认识和操作技能。
二、实验原理陶瓷烧制是将陶瓷原料在高温下烧结成瓷的过程。
在烧制过程中,原料中的矿物质发生一系列物理和化学变化,形成具有一定强度和美观性的陶瓷制品。
三、实验材料与仪器1. 实验材料:高岭土、石英、长石、粘土、釉料等。
2. 实验仪器:陶瓷球磨机、陶瓷拉坯机、陶瓷成型模具、陶瓷窑炉、高温电炉、陶瓷喷枪、陶瓷颜料等。
四、实验步骤1. 原料选取与制备(1)选取高岭土、石英、长石、粘土等原料。
(2)将原料进行球磨,使其达到一定的细度。
(3)将球磨后的原料混合均匀,制成陶瓷泥料。
2. 成型(1)将陶瓷泥料放入陶瓷拉坯机,通过旋转拉坯机,用手和拉坯工具将泥料拉成瓷坯。
(2)将瓷坯放入陶瓷成型模具中,使其成型。
3. 装饰(1)用陶瓷喷枪在瓷坯表面喷洒釉料。
(2)用陶瓷颜料在瓷坯表面进行绘画。
4. 烧成(1)将装饰好的瓷坯放入匣钵中。
(2)将匣钵放入陶瓷窑炉中,进行低温预热。
(3)逐渐提高窑炉温度,使瓷坯达到烧结温度。
(4)保持烧结温度一段时间,使瓷坯充分烧结。
(5)逐渐降低窑炉温度,使瓷坯缓慢冷却。
五、实验结果与分析1. 原料选取与制备实验中选取的高岭土、石英、长石、粘土等原料,经过球磨、混合后制成的陶瓷泥料,具有良好的可塑性。
2. 成型通过陶瓷拉坯机和成型模具,成功地将陶瓷泥料拉成瓷坯,并使其成型。
3. 装饰用陶瓷喷枪喷洒釉料,使瓷坯表面光滑;用陶瓷颜料进行绘画,使瓷坯更具艺术性。
4. 烧成在陶瓷窑炉中,瓷坯经过烧结和冷却过程,最终成为具有一定强度和美观性的陶瓷制品。
六、实验总结通过本次实验,我们对陶瓷的烧制过程有了较为全面的了解,掌握了陶瓷烧制的基本技术。
在实验过程中,我们体会到以下几点:1. 陶瓷原料的选取与制备对陶瓷制品的质量有重要影响。
2. 成型、装饰、烧成等环节对陶瓷制品的美观性和实用性至关重要。
- 1、下载文档前请自行甄别文档内容的完整性,平台不提供额外的编辑、内容补充、找答案等附加服务。
- 2、"仅部分预览"的文档,不可在线预览部分如存在完整性等问题,可反馈申请退款(可完整预览的文档不适用该条件!)。
- 3、如文档侵犯您的权益,请联系客服反馈,我们会尽快为您处理(人工客服工作时间:9:00-18:30)。
常用的提高粉体烧结性能的方法有: ⑴ 采用超细粉末:粉体越细,粉体活性越大,表面能越高,烧结越容易。 ⑵ 加入助烧结剂;如在氧化铝中加入氧化钛、氧化铬、氧化锰;在氮化硅 中加入氧化镁、氧化钇、氧化铝。 二、实验 莫来石是 Al2O3·SiO2 二元系中研究得最广泛的晶相,它是一种不饱和的具 有有序分布氧空位的网络结构,其结构中空隙大,比较疏松,原子堆积不紧密, 因 此 莫 来 石 具 有 较 低 的 弹 性 模 量 ( 200 ~ 220MPa ), 较 低 的 热 膨 胀 系 数 (5.6×10-6/K),较低的导热系数[5.0W/m·K]和热容量[750J/(kg·K)],使莫来石具 有良好的抗热冲击性,但是,其常温强度和韧性很低,高温时,莫来石中会产 生一些富硅的玻璃相,这些高粘度的玻璃相,可松弛高温下莫来石所受应力, 并使裂纹愈合,而且针状莫来石颗粒一也会在粘度很高的玻璃相中有拔出效应, 产生拔出功,所以其高温时的强度和韧性不低于常温下的性能。莫来石晶格扩 散困难,致使莫来石陶瓷难以烧结,但也正是由于晶格扩散困难,其高温抗蠕 变性能极优,是一种很有用的高温耐火材料。 ZrO2 在常温下具有优越的强度和韧性,但高温力学性能明显下降,因此, ZrO2 与莫来石复合,可望能改善莫来石的常温力学性能和氧化锆的高温力学性
选择塑化剂要根据成型方法、物料性质、制品性能要求、添加剂的价格以 及烧结时是否容易排除的条件,来选择添加剂及其加入量。
⑵ 造粒:粉末越细小,其烧结性能越良好;但由于粉末太细小,其松装比 重小、流动性差、装模容积大,因而会造成成型困难,烧结收缩严重,成品尺 寸难以控制等困难。为增强粉末的流动性、增大粉末的堆积密度,特别是采用 模压成型时,有必要对粉末进行造粒处理。常用的方法是,用压块造粒法来造 粒:将加好粘结剂的粉料,在低于最终成型压力的条件下,压成块状,燃后粉 碎、过筛。 2.粉末成型方法
⑵ 成型 ① 在油压机上用钢模将粉末压制成 7×7×60 的试条毛坯。缓慢烘干备用。 ② 测量试条尺寸(长×宽×高)做好标记。
⑶ 烧结 ① 根据原材料在烧结过程中可能发生反应的制度范围,制定出烧结莫来石
符合陶瓷材料的烧结制度。 ② 将试条直立放在氧化铝坩埚内,试条周围用氧化铝空心球隔开,装入高
温电炉内。 ③ 按照电炉操作规程进行操作,按升温曲线进行烧结。
33
将石蜡熔化、被氧化铝粉末吸收、缓慢燃烧排除(脱蜡);并使脱蜡后的坯件具 有一定的强度;烧结后得到的制品尺寸精确光洁度高、结构致密。适合制造形 状复杂、尺寸和质量要求高的陶瓷产品。
一般采用气压(0.7MPa),热压注常用石蜡为增塑剂(具有熔点低、熔化 后黏度小、流动性好、易填充、不磨损模具、冷却后有一定的强度,并且石蜡 冷却后体积收缩,易脱模、不与粉末反应、价格低等优点)。使用油酸和蜂蜡为 表面活性物质(因为粉末表面带有电荷,具有极性,是亲水的;而石蜡是非极 性,憎水的,不易与粉粒结合;表面活性物质油酸和蜂蜡表面一面是亲水基, 可与粉末结合;另一面是亲油基,可与石蜡结合)。
毛坯的厚度由浇注静置时间来控制。此方法适用于薄壁制品的成型。料浆 成型主要工艺分为:空心注浆(单面浇注)、实心浇注(双面浇注)、压力浇注、 离心浇注,真空浇注等。
料浆要有良好的流动性和稳定性。 ⑶ 挤压成型:将粉料和粘结剂、增塑剂和溶剂合成泥团(含水量为 19%-26%),排除泥团中的气体;在液压机活塞的推动下,泥团在缩小的出口处 被挤压、致密并成型。适合制作棒状和管状等异型断面的棒材和管材。 ⑷ 轧模成型:将合好的泥团在两轧辊间进行轧制,调整轧辊间距可获得不 同厚度的板坯。 ⑸ 先将粉料与石蜡、少许蜂蜡及油酸加热(70~100℃)混匀成均匀的蜡 浆(拌蜡);用压力将熔化的蜡浆注满金属模具中,冷却后,蜡浆在模具中凝固、 成型,脱模后,得到含蜡的坯料(热压注);将坯料埋在氧化铝粉中,缓慢升温,
将石蜡和蜂蜡加热熔化,逐渐加入烘干的粉料和油酸,经过几十小时不停 地搅拌,直至蜡浆均匀,粉体中的气体全部被排除,才能使用。
⑹ 注射成型:为使粉料更致密,尺寸更精密,现在常采用高压(10MPa) 注射成型机(与塑料注射成型机类似)。陶瓷粉末与有机添加剂一起加热混炼、 造粒后,常温下加入注射机内,颗粒料逐渐被加热,同时被送入挤压筒,料粒 呈塑性状态,在高压下(螺旋加压或活塞加压)被挤压进入模具、成型。
常用的添加剂有: ① 热塑性树脂:聚苯乙烯、聚乙烯、、聚丙烯、醋酸纤维素、聚乙烯醇等。 ② 增塑剂:酞酸二乙酯、石蜡、酞酸二丁酯、脂肪酸酯、酞酸二辛酯等。 ③ 润滑剂:硬脂酸铝、硬脂酸镁、硬脂酸二甘酯、矿物油等。 3.烧结过程 烧结的实质是粉坯在适当的气氛下被加热,通过一系列的物理、化学变化, 使粉粒间的粘结发生质的变化,坯块强度和密度迅速增加,其他物理、化学性 能也得到明显的改善。 经过长期的研究,烧结机制可归纳为:①粘性流动;②蒸发与凝聚;③体 积扩散;④表面扩散;⑤界面扩散;⑥塑性流动等。烧结是一个复杂的物理、 化学变化过程;是多种机制的结果。
① 粘结剂:常用的粘结剂有:聚乙烯醇、聚乙烯醇缩丁醛、聚乙二醇、甲 基纤维素、羧甲基纤维素、羟丙基纤维素、石蜡等。
② 增塑剂:常用的增塑剂有:甘油、酞酸二丁酯、草酸、乙酸二甘醇、水 玻璃、粘土、磷酸铝等。
③ 溶剂:能溶解粘结剂、增塑剂,并能和物料构成可塑物质的液体。如水、 乙醇、丙酮、苯、醋酸乙酯等。
⑴ 模压成型 ① 钢模压制成型:将粉末填在钢制模具的阴模中,在压力机上对阳模加压,
பைடு நூலகம்32
使粉末成型。 由于粉末间、粉末与模具之间的摩擦力,成为阳模下压的阻力,如果在单
向加压情况下,会使坯体沿压力方向形成压力下降梯度,使坯体密度沿压力方 向下降。除采用双向加压(采用活动双阳模)方法外,还可以在粉料中加入润 滑剂,如油酸、硬脂酸镁、石蜡汽油溶液等,减少粉末间及粉末与模型之间的 摩擦力,提高模压成型的坯体密度的均匀性。
② 等静压成型:将粉末装填在可变形的模具(如橡胶塑料等材料制作的模 具)里,置于高压液体中,模具在高压液体的作用下变形,使粉体在各个方向 上均匀受力,所以坯体密度均匀,由于压力高,坯体密度高,制品烧结后强度 高。缺点是:坯体外观尺寸和形状不易控制,光洁度不高。
⑵ 粉末浇注成型:在粉料中加入适量的水或有机液体以及少量电解质添加 剂,调成相对稳定的粉浆。将粉浆浇注在石膏模具中,静置一定时间后,靠近 模具处的水分被石膏吸收,粉浆变粘稠粘在模具壁上;倒出多余的粉浆,待坯 体稍干硬后与模具分开,即可获得坯件,干后进行烧结。
35
得到的制品的密度变化来确定最佳烧结制度(可获得最大密度制品的烧结制度 为最佳)。
坯体在烧结的过程的不同阶段(脱水、反应、燃烧等)会放出大量气体, 如果在这一阶段升温太快,会引起强烈反应;急速排出的大量气体会使坯体开 裂、起泡,造成损坏;因此,当温度上升到这些温度段时,应缓慢升温,或长 时间保温,减缓反应速度,同样某些晶型转变也伴随或多或少的体积变化,也 要注意控制温度,减缓变化的速度。
34
坯体在升温过程中相继会发生下列物理、化学变化; ⑴ 蒸发吸附水:(约 100℃)除去坯体在干燥时未完全脱去的水分。 ⑵ 粉料中结晶水排除:(300~700℃) ⑶ 分解反应:(300~950℃)坯料中碳酸盐等分解,排除二氧化碳等气体。 ⑷ 碳、有机物的氧化:(450~800℃)燃烧过程,排除大量气体。 ⑸ 晶型转变:(550~13000℃)石英、氧化铝等的相转变。 ⑹ 烧结前期:经蒸发、分解、燃烧反应后、坯体变得更不致密,气体可达 百分之几十。在表面能减少的推动力作用下,物质通过不同的扩散途径向颗粒 接触点(颈部)和气孔部位填充,使颈部不断长大,逐步减少气孔体积;细小 颗粒间形成晶界,并不断长大,使坯体变得致密化。在这过程中,联通的气孔 不断减小,晶粒逐渐长大,直至气孔不再连通,形成孤立的气孔,分布在晶粒 相交位置,此时坯体密度可达理论密度的 90%。 ⑺ 烧结后期:晶界上的物质继续向气孔扩散、填充,使孤立的气孔逐渐变 小,一般气孔随晶界一起移动,直至排出,使烧结体致密化。如再继续在高温 下烧结,就只有晶粒长大过程。如果在烧结后期,温度升得太快,坯体内封闭 气孔来不及扩散、排出,只是随温度上升而膨胀,这样,会造成制品的“胀大”, 密度反而会下降。某些材料在烧结时会出现液相,加快了烧结的过程,可得更 致密的制品。 ⑻ 降温阶段:冷却时某些材料会发生相变,因而控制冷却温度,也可以控 制制品的相组成:如要获得合适组成的部分稳定的氧化锆固体电解质,冷却阶 段的温度控制是很重要的。 坯体烧结后在宏观上的变化是:体积收缩、致密度提高、强度增加。因此 可以用坯体收缩率(线收缩率)、气孔率、体积密度与理论密度之比值、机械强 度等指标来衡量坯体的烧结制度。 相同的坯体在不同的烧成制度下烧结,会得到生烧、正火、过烧等不同的 结果;不同的升温速度也会得到不同的制品。可以从坯体在不同的烧结制度下
36
能。 1.实验目的
本实验通过各组同学的试验结果,完成莫来石与氧化锆复合陶瓷材料的工 艺条件的实验研究(每组同学完成一种烧结制度下几种配方的试样的烧结实验) 通过对不同氧化锆加入量以及不同烧结制度条件下得到的样品性能的比较(密 度、抗弯强度、断裂韧性等性能的测试),得到这种复合材料的最佳配方和最佳 烧结制度。 2.实验步骤
⑷ 测试 ① 测量烧后试条尺寸并记录。 ② 测试烧后试条的气孔率、体积密度、吸水率、热震稳定性等指标。
37
思考题 1. 来石质陶瓷烧结过程中发生哪些反应? 2. 各种成型方法对制品性能的影响? 3. 烧成温度和保温时间对制品性能的影响?
38
实验 8 莫来石质高温陶瓷材料的成型和烧结
一、基础知识 1.成型前粉料预处理
为使粉料更适合成型工艺的要求,在需要时应对已粉碎、混合好的原料进 行某些预处理:
⑴ 塑化:传统陶瓷材料中常含有粘土,粘土本身就是很好的塑化剂;金属 粉末也有良好的塑性,一般不需要再加入塑化剂。只有对那些难以成型的原料, 为提高其可塑性,需加入一些辅助材料: