常见成型的不良及改善对策22页PPT
成形品常见的不良及解决方法课件

总结词
01
尺寸偏差是指成形品的实际尺寸与设计尺寸存在偏差的现象。
详细描述
02
尺寸偏差可能是由于模具制造误差、磨损或定位系统不准确等原因引起的。尺寸偏差可能导致装配困难、性能不符合要求或安全问题。
解决方法
03
提高模具制造精度和装配准确性;定期检查和修正模具尺寸;采用高精度的测量设备和质量控制方法;加强生产过程中的质量监控和反馈调整。
详细描述
02
CHAPTER
成形品常见的不良现象
详细描述
变形通常是由于材料内部应力、模具设计不合理或加工工艺不当等原因引起的。变形可能影响成形品的外观和性能,甚至导致产品不合格。
总结词
变形是指成形品形状发生扭曲或不规则变化的现象。
解决方法
优化模具设计,减小内应力;调整加工工艺参数,如温度、压力、时间等;采用适当的后处理工艺,如热处理、矫形等。
VS
模具设计与制造是影响成形品质量的重要因素,合理的模具设计和高质量的制造工艺能够减少产品不良的发生。
详细描述
在模具设计阶段,需要充分考虑产品的形状、尺寸和材料特性,以及成形工艺的要求。合理的模具结构设计能够有效降低产品在成形过程中的缺陷,如缩孔、裂纹等。同时,高质量的模具制造工艺能够保证模具的精度和寿命,从而确保产品的稳定性和一致性。
成形品常见的不良及解决方法课件
目录
成形品不良概述成形品常见的不良现象成形品不良的原因分析解决成形品不良的方法与措施成形品不良的预防与控制成形品不良的案例分析
01
CHAPTER
成形品不良概述
总结词
成形品不良是指在生产过程中出现的各种与预期不符的缺陷或问题,导致产品无法满足设计要求或性能标准。
详细描述
成型不良的原因及改善方法详解
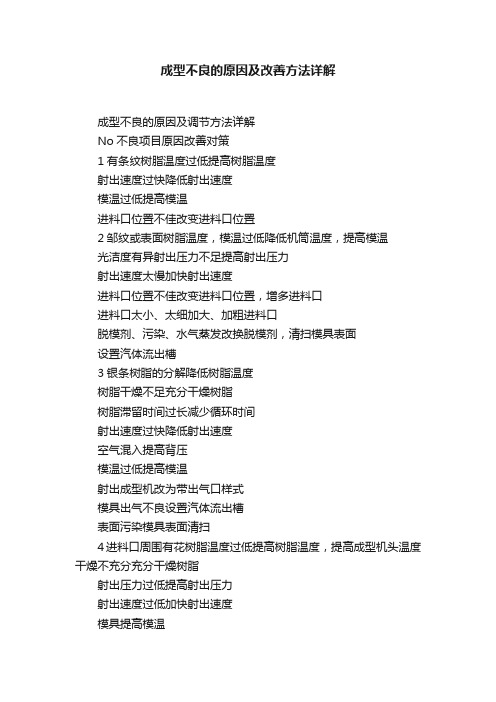
成型不良的原因及改善方法详解成型不良的原因及调节方法详解No不良项目原因改善对策1有条纹树脂温度过低提高树脂温度射出速度过快降低射出速度模温过低提高模温进料口位置不佳改变进料口位置2邹纹或表面树脂温度,模温过低降低机筒温度,提高模温光洁度有异射出压力不足提高射出压力射出速度太慢加快射出速度进料口位置不佳改变进料口位置,增多进料口进料口太小、太细加大、加粗进料口脱模剂、污染、水气蒸发改换脱模剂,清扫模具表面设置汽体流出槽3银条树脂的分解降低树脂温度树脂干燥不足充分干燥树脂树脂滞留时间过长减少循环时间射出速度过快降低射出速度空气混入提高背压模温过低提高模温射出成型机改为带出气口样式模具出气不良设置汽体流出槽表面污染模具表面清扫4进料口周围有花树脂温度过低提高树脂温度,提高成型机头温度干燥不充分充分干燥树脂射出压力过低提高射出压力射出速度过低加快射出速度模具提高模温加大进料口及流道改变进料口位置5黑条主轴、机筒、伤痕清扫主轴机筒、换轴滞留时间过长射出机筒内树脂机筒温度过高降低机筒温度射出速度过快降低射出速度轴转速快烧焦降低转速,降低背压6烧焦空气混入安装出气口装置设置汽体流出槽射出速度过快降低射出速度7云纹、光泽不良树脂过热降低机筒温度成型材料干燥不足充分干燥、改变干燥方式模温过低提高模温机筒温度过高、过低调节机筒温度脱模剂过多减少脱模剂8色差、混色颜料染料分散不良改变树脂,着色剂成型机筒温度过高、过低调节机筒温度可塑化不良降低轴转速,提高背压树脂的分解降低温度,循环时间缩短成型机清扫不良彻底清扫前产品留在机内材料冷却时间过短延长冷却时间进料口位置不佳修正进料口位置分散剂、扩散剂不能加入对该树脂不适合的添加剂等9透明料混浊材料干燥不足,异物混入充分干燥材料、变更材料树脂温度过高、过低调节树脂温度滞留时间过长成型材料滞留时间减短机筒温度过高降低机筒温度添加剂、脱模剂过多确认添加剂的适合性,减少脱模剂10气泡成型材料的分解降低成型温度材料干燥不足充分干燥材料树脂带温过长修正机筒内主轴进料行程射出压力过低提高射出压力保压过低提高保压背压过低提高背压射出速度过慢提高射出速度背压过大背压降低模温过高、过低调节模温料斗下端冷却不足注意改善料斗下端的冷却成型机改为带出气口样式11杂质、异物成型机、料斗、干燥机清扫不良充分清扫成型机、料斗、干燥机材料周围环境有尘埃用塑胶将材料部分隔开材料输送管清扫不良清扫材料输送管模具生锈模具清扫材料不良改换材料12剥离不同材料混入调节材料断裂树脂温度过低提高树脂温度模温过低提高模温材料使用不适、缓冷不足更变材料、改变缓冷条件13裂纹干燥条件不良按树脂种类决定干燥条件树脂温度过低提高树脂温度模温过低提高模温射出压力过高降低射出压力保压压力过高降低保压压力保压时间太长减少保压时间坡度不足增加坡度顶针位置不良调节顶针位置顶针数量少增加顶针数量脱模剂不足增加脱模剂14脆弱成型材料不适改变成型材料强度不够不同材料,粉碎材料混入调节材料质量干燥不适度按材料选择干燥条件树脂温度过高降低树脂温度树脂温度不适当成型温度调节滞留时间过长缩短滞留时间可塑化不良成型温度轴转速、背压调整射出压力不适当射出压力调节保压压力过低提高保压压力射出速度不适当射出速度调节冷却时间过短延长冷却时间模温调节模温模具强度不足修理模具进料口不良、数量不足改变进料口位置,增加进料口数量后处理采用缓冷方式15尺寸不均材料流动性调节成型温度有大有小材料吸湿充分干燥材料射出压力过低调节射出压力保压过低、过短调节保压的压力和时间冷却时间过短延长冷却时间背压过低选择适当背压模温不适调节模温模具关合力过少提高模具关合力模具强度不足修理模具,增加强度进料口位置不适当改变进料口位置进料口数量少增加进料口数量16变形成型材料流动性不足提高树脂温度收缩率过大改提收缩率小的树脂射出压力过高降低射出压力冷却时间短延长冷却时间,使用冷却模具模温使各部位得到冷却,改善模具17凸凹不规则工程塑料较多如PA、PET等注意改善料斗下的冷却料斗侧温度过高降低料斗下机筒温度背压过高调低背压,固定停止时间再生材料不良尽量将再生材料打碎用筛子除去粉末祛除含0.2mm以下厚度胶片的部分玻纤强化颗粒使用2.5mm -3.5mm长度的玻纤材料18毛边、飞刺树脂流动性太快降低成型温度、改变成型材料射出压力过高降低射出压力保压太慢快速保压模具关合力不良提高模具关合力模具强度不足修理模具模具表面不光滑修理模具19多边树脂流动性过剩降低树脂温度改变成型材料射出压力过高降低射出压力快速加入保压模具关合力不足提高模具关合力模具不良模具强度不足分割面密封不良20胡须树脂成型收缩率大改变成型材料树脂温度高降低树脂温度射出压力过低提高射出压力保压压力低提高保压压力射出速度过低加快射出速度模具降低胡须发生侧模温扩大模具进料口、加粗料流道改善进料口位置,壁厚均一模温过高降低模温21缺边树脂流动性不足提高树脂温度改变成型材料射出压力过低提高射出压力保压压力低慢速加入保压提高保压压力射出速度过慢增加射出进入速度计量投量不足增加计量设定值主轴不适合使用带防止逆流功能的主轴模具扩大模具进料口加粗材料流道。
注塑成型常见问题及解决方案(综合)PPT幻灯片课件

成型不良分析
塑膠原料
成型條件
原料含有水分等 揮發性氣體
添加劑太多
染料分解
射出容量;可塑 料能力不足
原料停留時間太長; 部分發生過熱現象
原料過熱分解
射出壓力太高
模具溫度過低
射速太快
澆口位置設計不當 澆口孔及膠道太小
排氣不良 冷料井太小
模具表面有水分或潤滑劑
螺桿磨損
過膠圈磨損
螺桿設計不良; 熔膠時吸入空氣
加大冷料井
清理模具表面
模具設計
射出機
19
七、毛邊- Burring
塑料過熱、流動性太好、過度保壓 塑胶熔体流入分模面或镶件配合面将發生Burring
20
成型不良分析
塑膠原料
流動性太好
成型條件
保壓時間太長
熔膠量太大
射出轉換保壓動作太遲
保壓壓力太高
料管溫度太高
模具鋼性不良
模具密著性不好; 產生段差
模具間有異物
体时,在注塑成型过程空气、水份及 挥发性气体进入制品内部而残留的空 洞叫气泡(Bubble)。
14
成型不良分析
塑膠原料
成型條件
原料含有水分等 揮發性氣體
料管溫度太高; 產生氣體
原料溫度低;流動性不足
原料內有空氣混入
射出速度太快或太慢
原料收縮率大
保壓壓力低
模具溫度過低
保壓時口孔及膠道太小 模穴設計不良(厚肉部 急遽之肉厚變化)
排氣不良
螺桿磨損
過膠圈磨損
螺桿設計不良; 熔膠時吸入空氣
(壓縮比不足)
Bubble
模具設計
射出機
15
塑膠原料
更換原料
更換原料
塑件常见不良原因及解决对策 ppt课件

ppt课件
6
•
a.在A部輸入多量的水、B部輸入少量的水;在A部輸入低溫的水、B部輸入較高
溫的水
•
b.在A部之孔較接近成品、B部較遠離成品,通入等量的水
•
c.在A部開較大的孔,B部開較小的孔,通入等量的水
•
以上三方法皆可使模穴冷卻速度平衡,但最好的方法還是在設計產品時,盡量讓肉
厚平均,不要有特別厚的地方出現.
ppt课件
20
八,噴射流
• 1,現象:在成形品表面,尚著澆口產生帶狀
條紋
• 2,原因:在塑料由澆口射入模內時,邊冷卻, 邊射入而產生塑料固化現象
• 3,對策:加大澆口,或檢查修正澆道之設計 使用低速射出.模具加模溫控制
ppt课件
21
九,針孔、氣泡
• 1, 現象:成品表面出現好像被針刺過的小 孔痕 跡.
• 1,現象:在以母模合模面,中子附近,托模梢附 近.產生塑料溢出之毛頭.
• 2, 原因:閉模力不足,或太高.模具變形,模 具結合不良,模具內有異物.塑料流動性太好, 塑料射入太多.
• 3,對策:在公母模結合而產生之毛邊,如果在短 時間內由小毛邊變成大毛邊,則必須立即檢修模 具.其他原因所產生之毛邊,則須個別予以修正 即可.
• 2,原因:塑料中含水 • 3,對策:使用干燥機除去水份
ppt课件
22
十,銀條
• 1,現象:成形品表面出現閃耀的銀色絲紋 • 2,原因:水份、空氣、揮發性氣體,未除盡.模內有空
氣.塑料局部產生過熱,銀條發生部分不同,其原因也不 太一樣必須平常多加注意,較易找出正確原因 • 3,對策:
• 1.塑料充分干燥 • 2.背壓、螺杆轉速,可塑性化,須適當 • 3.高粘度塑料,如果溫度太低則在料管內易產生局部斷熱現象,
成形品常见的不良及解决方法课件

• 解决方法:在模具上增加排气口,确保气体能够
03
及时排出。
实例三
2. 冷隔 • 原因:金属液温度过低,导致在填充模具时出现冷隔现象。 • 解决方法:控制金属液温度,使其保持在适宜的范围内。
实例三
01
3. 缩松
02
• 原因:金属液在冷却过程中 收缩过大,导致压铸件内部 出现间隙。
03
• 解决方法:优化模具设计, 使金属液在冷却过程中充分 填充模具内部。
实例二
01
3. 尺寸偏差
02
• 原因:冲压速度过快或过慢,导致材料受力不均。
03
• 解决方法:控制冲压速度,确保材料受力均匀。
实例二
4. 破裂 • 原因:冲压材料厚度过薄,无法承受冲压压力。 • 解决方法:增加材料厚度,确保其能够承受冲压压力。
实例三
01 1. 气孔
02
• 原因:模具排气不良,导致气体留在压铸件内形 成气孔。
调整注射速度
注射速度过快可能导致充填不足或气穴,过慢可能导致材料降解或 色泽不均,因此需要根据实际情况调整注射速度。
更换材料或改进材料
更换牌号
对于因材料流动性、收缩率等问题引起 的成形品不良,可以尝试更换牌号,选 择更合适的材料。
VS
改进材料
通过添加助剂、改变配方等方法,改良材 料的加工性能和力学性能,提高成形品的 合格率。
• 解决方法:降低注射压力,确保塑料在模具内 完全融会。
实例二
1. 变形
• 原因:冲压温度过高或过低,导致材料变形。
• 解决方法:控制冲压温度,确保材料在最佳状态下 进行冲压。
实例二
2. 毛刺
• 原因:模具磨损或间隙过大,导致材料在冲压时产生毛 刺。
塑胶成型常见不良及改善方法ppt课件
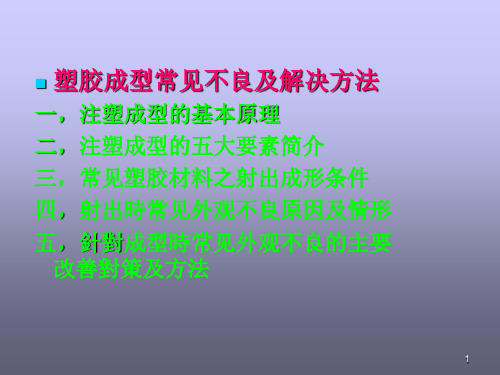
6:粘模:
a.)可以用加长冷却时间; b)减小注塑压力和料筒固化溫度来解 决; c.)加大脫模斜度或增加顶針位置; d.)轉用脫模性良好物料或增加脫模劑。
7:断针:由于压力过大,或针孔位
偏位导致,可用减小注塑压力 及加大 顶针位置或增加頂針數量来解决。
13
8,披锋:处理重点应主要放在模具的改善方
1:烧焦:由热引起的材料分解,看起来象烧焦 痕迹。在清晰材料表面形成的朦胧点或区域
2:異物:在材料内部或表面的黑色可见杂质,或 烧焦的塑胶碎片形成的黑点或有色块状。
3:混色(色差):偏离原色或颜色不一致及不 均。主要由于材料(色粉)有问题或某些啤作参数 (如温度、速度)不当引起的胶件颜色与标准色板 不同。
18
14,溶接線: 主要是由於射出壓力,射出速度,
及料溫過低所致。故適當加大射出 壓力和射出速度,提高料溫溫度。 以及改良排氣系統等。
19
(以上僅供大家參考!)
谢谢大家参加本次课程!!
20
4:入水纹:夹水纹:气纹: 它會從澆口處以扇 形方式向外輻射發展,塑胶流动形成的象干涸河道 一样的条纹表面。由塑胶表面熔接在一起时形成的 可见线或可见痕。
6
5:缩水或走胶不齐:也叫欠注或缺料,一般發
生在制品壁厚較薄的地方,或流動路徑末端區域。 表面收缩或陷痕。由于温度太低,压力不足或射胶 时间太短等原因而使胶件缺料。
AS树脂 聚碳酸酯树脂
尼龙+玻纤 尼龙+玻纤 PP+玻纤 聚丁烯苯 二甲酸脂 玻纤补强P.O.M 玻纤补强AS 玻纤补强PS
玻纤补强PC
玻纤补强ABS
1.005 1.005 1.005 1.001 1.004
1.007
成型不良原因及对策

成型不良原因及对策要判断成型不良原因首先必须正确的了解成型不良原因.始能快速正确的排除.(一)充填不足short现象:在成品上产生缺角原因:塑料注入模穴内,末端尚未填满之前产生冷却固化现象或是塑料本身流动性不良,计量不足,模内排气不良,流动阻抗太大,锁模力不足,均会产生此现象.对策:针对上述个别原因,找出真正毛病予以改善.(二)缩陷sink mark现象:成品冷却收缩后,产生凹穴原因:1、塑料注入模穴内,与模壁接触后,开始冷却硬化,而产生内张力所引起2、在肉厚部分,因体积缩量较大,也较易产生缩陷对策:1、加上保压,补充冷却收缩量,使成品各部分冷却速度均衡如图标a.在A部输入多量的水、B部输入少量的水;在A部输入低温的水、B部输入较高温的水b.在A部之孔较接近成品、B部较远离成品,通入等量的水c.在A部开较大的孔,B部开较小的孔,通入等量的水以上三方法皆可使模穴冷却速度平衡,但最好的方法还是在设计产品时,尽量让肉厚平均,不要有特别厚的地方出现.以下诸方法可供参考(三)结合线现象:塑料流过空穴,或窗口状开关口后,在接合处发生接合困难而产生母痕对策:1.使用流动性较好之塑料2.模穴增开通气孔3.模穴加开容料穴,成型后予以切除4.结合处稍透气5.在添加玻璃纤维塑料的成型作业上,结合部会因为纤维方向混乱而使强度降低,此时可在结合部增加肉厚,成型后再予以切除.平板状成品之结合母处理方法:1.变换浇口之位置2.肉厚适当的增加或减少3.利用浇道与容料穴适当配合4.模穴内部温度,部分做适当的变化5.变换射出速度6.成品表面烙印花纹,使结合线不明显7.圈状成品可合用下列浇注法,使结合线不明显(四)波纹、流纹现象:在浇口附近的成品表面,产生年轮状的纹理,称为波纹.而远离浇口的纹理,则称为流纹.原因:塑料温度过高,塑料温度不均匀,模温过底,塑料冷却太早时,随后进入之塑料因免强推挤而产生凹凸不平的纹路,光线照射下会产生光波干涉,而有彩虹状出现.对策:增加塑料之流动性.压力速度适当提高,以防止波纹的发生.(五)白纹、双色、表面出现雾状、光度不足、透明度不足现象:成型品内部,或表面无法显现原来的光泽与颜色原因:染色剂选择不当.螺杆混炼效果不良.塑料内之添加物受热分解,烧焦.模具磨损,塑料模具温度太低,离型剂影响…等.对策:找出确定之原因,予以修正即可.(六)焦斑、黑条纹现象:成形品上有点状,或条纹状之黑斑.未变成黑色前之现象称为变色原因:1.塑料烧焦:塑料内部之添加物过热分解2.瓦斯烧焦:a在料管内塑料融化时,混入空气,而产生断热压缩现象,瞬间发出高热,而产生烧焦.b模具内塑料急速充填时,模内空气无法排出.在成品末端结合线附近,被包围之空气产生断热现象而分解,烧焦判断方法:a.在料管内之断热现象.其焦斑黑条,发生在浇口附近,呈不规则性之条纹b.模内滞留空气之断热现象,其焦斑,黑条易发生在塑料流动末端部对策:1.塑料烧焦:使用安全性较佳之塑料添加剂2.瓦斯烧焦:a.设法排出料管之气体,或寻求合理之塑化条件b.降低充填速度c.增加模内之透气孔.透气孔之尺寸约0.02-0.04mm,尼龙透气孔约0.002-0.004mm,或是在模内开滞气孔.(七)毛边现象:在以母模合模面,中子附近,托模梢附近.产生塑料溢出之毛头.原因:闭模力不足,或太高.模具变形,模具结合不良,模具内有异物.塑料流动性太好,塑料射入太多.对策:在公母模结合而产生之毛边,如果在短时间内由小毛边变成大毛边,则必须立即检修模具.其它原因所产生之毛边,则须个别予以修正即可.(八)喷射流现象:在成形品表面,尚着浇口产生带状条纹原因:在塑料由浇口射入模内时,边冷却,边射入而产生塑料固化现象对策:加大浇口,或检查修正浇道之设计使用低速射出.模具加模温控制(九)针孔、气泡现象:成品表面出现好像被针刺过的小孔痕迹.原因:塑料中含水对策:使用干燥机除去水份(十)银条现象:成形品表面出现闪耀的银色丝纹原因:水份、空气、挥发性气体,未除尽.模内有空气.塑料局部产生过热,银条发生部分不同,其原因也不太一样必须平常多加注意,较易找出正确原因对策:1.塑料充分干燥2.背压、螺杆转速,可塑性化,须适当3.高粘度塑料,如果温度太低则在料管内易产生局部断热现象,此时宜升高料管温度4.螺杆产生逆流现象过剧,使空气混入5.螺杆牙部间隙太大,使料之传送效果不良,此时宜调整螺杆之回转速度6.螺杆松退距离太长7.从射嘴牙部混入空气8.射嘴口之冷料进入模内,宜使用低速射出或在模穴内开一个容料穴9.模内流道转弯有死角存在,宜设计成圆弧状10.浇口太狭小,塑料瞬间流过是产生高热.由塑料中溢出挥发性气体(十一)翘曲、弯曲由于内应力而发生,宜找出真正原因修正之.请参考成形品强度与形成条件.(十二)剥离现象:成形品表面,产生云母状之重迭片原因:塑料混入性质不同之塑料对策:换新塑料.有时会因为分子配向性太强而产生,请检查之(十三)白化、裂痕白化:承受弯曲变形量大时,颜色变白.此易发生在ABS料上裂痕:成形品破裂,或经过长时间后产生裂痕对策:白化:增加成品抗弯性裂痕:清除成品内应力如果成品有埋入心形则考虑予以预热缩小模内各处之温差.以降低因温差太大而引起热胀现象不均匀.圈状成品肉厚与孔径比例须恰当POM,t>1/4DPS,AS,t>7/10DABS,变性PPO,t>1/2DPS,AS料容易产生龟裂,宜特别留意(十四)伤痕现象:成形品表面产生不正常之伤痕原因:模具加工不良,模具设计不良对策:拔模斜度修改之(一般在1-3°之间).降低射出压力.(十五)离型不良(成品粘模)现象:成品卡在于模内,无法托出原因:模具设计不适当对策:1.成型条件调整好2.深盒式成品因弹性变性而卡住,宜改良其设计.3.心型与模穴温度差不适当4.模穴产生真空吸着,宜加入空压吹离5.托模梢卡住成品,宜改良设计6.射嘴温度太低(十六)异物混入现象:成形品内附金属粉,尘埃等异物原因:塑料在储运中遭污染,料管或螺杆磨损对策:加强塑料之管理,机械定期检查,维修(十七)脆弱现象:成形品的强度,刚性等物理性质,比原材料标准值差很多原因:原因很多,无法做说述对策:尽量减低成品残留内应力,降低二次料混合比率(十八)尺寸精密度不良原因:冷却收缩为最大根本原因,成形条件不良也会产生对策:成形条件方面,改变模具温度.控制室温,有良好的效果.冷却收缩量,请自行参考模具设计技术.以上列举的各种问题,其原因及对策大多数都与周期(CYCLE TIME)的稳定性有关,因为无论塑料粒在料管适当之塑化,或是模具恒温之保持,都是热平衡结果也就是说在整个连续操作中,料管中之塑料接受来自螺杆旋转之磨擦热,电热片之热,尤其是电热片之热又与受热的时间有关,其热量又跟着塑料送入模具,模具之热来自于塑料及热水,损失在成品带走的,散失在空气中的,冷却水带走的,因此无论料管或模具欲使其温度保持不变必需维持其进出之热平衡,欲使其进出热维持平衡则必须维持一恒定的周期时间,如周期愈来愈快则料管中之热入不越出,以致不足以塑化原料,模具中之热又入多于出,以致模温不断升高,反之将有相关之结果,因此在任何一个成型操作中,尤其插入手动操作必须控制稳定周期时间,尽量避免快慢不一,如其它条件维持不变则:周期之加快将造成:短射、缩水、变形、粘模.周期之延长将造成:溢料、毛头、粘模、变形、原料过热、甚至烧焦、出现残留在模中之焦料又可能造成模具损坏,料管中过热之原料又可能造成料管之腐蚀及成品出现黑斑及黑纹.每种问题之发生因使用原料不同,其原因及对策也不尽相同.某些原料具有某独特之性质,较易发生独特的问题,以上所述为日常所见一般性之问题原因及对策.归纳各种问题原因及对策于下页表便于参阅,其数字之次序为考虑优先次序成形不良原因及成形注意事项依成形塑料之不同,而有不同的不良原因,成形技术上须留意之事项于下页表中有详细之分析,请参考之.表中有“不”,过高,过低……等之提示语,只要参考修正之,即可改善成形作业.表中提示语如下:1.低:太低2.高:太高3.长:太长4.短:太短5.快:太快6.慢:太慢7.多:太多8.少:太少9.厚:太厚10.薄:太薄11.细:太细12.混:混入异物。
成型常见问题及对策课件

典型案例分析与实践
案例一
产品表面质量差。针对此问题,通过调整注射速度、注射压力等 参数,优化熔体流动状态,改良产品表面质量。
案例二
产品尺寸不稳定。针对此问题,通过调整模具温度、保压时间等参 数,提高产品尺寸稳定性。
实践
在某企业实际生产过程中,应用上述计策,成功解决了成型过程中 出现的问题,提高了产品质量和生产效率。
优化前模具结构与成型效果
展示优化前的模具结构和成型效果,分析存在的问题和不足 。
优化后模具结构与成型效果
展示优化后的模具结构和成型效果,对照分析改进后的效果 ,突显优化设计的价值。
05 计策三:提高材料性能及适用性
CHAPTER
材料性能对成型影响分析
流动性
材料的流动性好,成型过程中易于填充模具,获得完整、密实的制 品。流动性不足可能导致制品出现缺料、气孔等问题。
06 计策四:引入自动化与智能化技术
CHAPTER
自动化与智能化技术应用现状
自动化技术应用
目前,成型生产中的自动化技术已经得到广泛应用,如自动供料、自动成型、自动检测等,大大提高了生产效率 和产品质量。
智能化技术应用
随着人工智能技术的发展,成型生产中的智能化技术也开始得到应用,如机器学习、深度学习等算法被用于成型 过程的优化和控制,提高了生产过程的智能化水平。
深入剖析了成型问题产生的原因,包括材料、设 备、工艺等方面。
3
针对不同问题的计策措施
针对不同类型的问题,提出了有效的解决方案和 计策措施。
未来发展趋势预测与挑战
新材料与新工艺的应用
随着新材料和新工艺的不断涌现,成 型技术将面临更多的挑战和机遇。
智能化与数字化发展趋势
成型过程中智能化和数字化技术的应 用将越来越广泛,需要不断提高自身 技能和知识水平。
塑胶成型常见不良及改善方法22页PPT

60、生活的道路一旦选定,就要勇敢地 走到底 ,决不 回头。 ——左
塑胶成型常见不良及改善方法
46、法律有权打破平静。——马·格林 47、在一千磅法律里,没有一盎司仁 爱。— —英国
48、法律一多,公正就少。——托·富 ቤተ መጻሕፍቲ ባይዱ 49、犯罪总是以惩罚相补偿;只有处 罚才能 使犯罪 得到偿 还。— —达雷 尔
50、弱者比强者更能得到法律的保护 。—— 威·厄尔
56、书不仅是生活,而且是现在、过 去和未 来文化 生活的 源泉。 ——库 法耶夫 57、生命不可能有两次,但许多人连一 次也不 善于度 过。— —吕凯 特 58、问渠哪得清如许,为有源头活水来 。—— 朱熹 59、我的努力求学没有得到别的好处, 只不过 是愈来 愈发觉 自己的 无知。 ——笛 卡儿
第八讲成形品常见的不良及解决方法优品ppt

成型缺陷(不良)分类
一.外观不良:目视制品可看见之外观缺陷.如:熔接痕 (结合线)﹑汽泡﹑毛边﹑缺料﹑异色﹑气纹﹑白化﹑ 光泽﹑凹陷﹑离型(变形/顶白)等.
度/厚度超差﹑孔径超差 ﹑圆心距超差等.
三.性能不良:制品物性不过,如硬度﹑强度﹑拉力等达 不到要求.常见有脆断﹑脱皮(用手搓)﹑拉力NG等不 良现象.
度/锁模力来改善.
1.制品脱模受力过大,肋位/柱位/顶出位将产品拉(顶)凹.模具 抛光/斜度/顶出平衡考量;2.增加排气;3.改善进胶.
设备
1.点检射咀(堵塞/利角/溢料);2.点检料温;3.观察残量,点检螺 杆逆止环封胶状况.
材料
材料收缩率考量.
离型
离型:脱离制品原本设计之正常形状,发生翘曲/变形等现象.
白化
白化:制品表面出现白色点状或线状不良现象.
分析项目 成型参数
设备 模具 材料
原因分析对策 1.速度过块,产生瓦斯或瓦斯气没有及时排出.沉积于制品表面形成白化. 2.料温过高或计量螺杆旋转过快(剪切热),使材料发生裂解.裂解物充填 到制品表面. 3.速度太慢,材料充填不够密实,形成气泡,形同白化.以上,对策偏重于如 何减少瓦斯量的产生. 1.点检干燥桶正常否. 2.点检螺杆射出是否正常(射压/残量等),逆止环封胶不彻底,溶胶回流, 会导致计量不稳定或材料滞留裂解等问题产生. 1.增加排气. 2.改善进胶. 1.干燥不彻底,水分残留. 2.次材使用不当,裂解物过多.3.材料添加剂不当或过多,如高低温色母, 增韧剂等.
应力痕(光泽)
应力痕:常出现于制品侧壁/肉薄处/顶出部位光泽.
分析项目
原因对策
条件
1.降低保压/保压时间,减轻应力作用. 2.提高料温/模温,改善流动性,以期达到降低压力之目的.