第二章机械加工精度及控制(5-7节)课件
机械加工质量培训课件PPT(共 104张)

2.1 机械加工精度
i工 机件 (蜗 床杆 丝) 杆 PP螺 1螺 ZZ距 距 21ZZ34
例1. 在公制车床上车模数为2mm蜗杆时,挂轮计算式为 :
z1 z2
z3 z4
P(P机 (1 床 蜗丝 杆杆 螺螺 距距 )) ,若P=6mm,
Z 1 1,1 Z 2 0 7,Z 0 3 8,Z 0 4 1,2 求加0 工后蜗杆螺距
误差是多少?
i
P1=2
P=6
解: i工 机件 (蜗 床杆 丝) 杆 PP螺 1螺 ZZ距 距 21ZZ34 P ห้องสมุดไป่ตู้iP Z Z2 1Z Z3 4P1 71 0 2 800 066.2857
1)主轴回转误差。 纯径向跳动误差 轴向窜动误差 纯角度摆动误差
①主轴纯径向跳动误差对加精度的影响。 产生的主要原因:主轴支承轴颈的圆度误差、轴承工作表面的
圆度误差等。 a. 切削力F的作用方向不变(见图2-5 车外圆的情形)
2
R
1
3
R3
R1 △R
o o′
理论位置
实际位置
R
4
车外圆时它使加工面产生圆度和圆柱度误差。
@加工质量与设备、工艺方法、工艺措施有关。
2.1 机械加工精度
2.1.1 概述 1、机械加工精度(简称加工精度):是指零件在机械加工后
的几何参数(尺寸、几何形状和表面间相互位置)的实际值和理 论值相符合的程度。
2、加工误差:实际参数与理论参数的差值
2.1 机械加工精度
2.1.2 影响加工精度的因素及其分析 在机械加工中,零件的尺寸、几何形状和表面间相互位置的
机械制造工艺学课件:机械加工精度及其控制
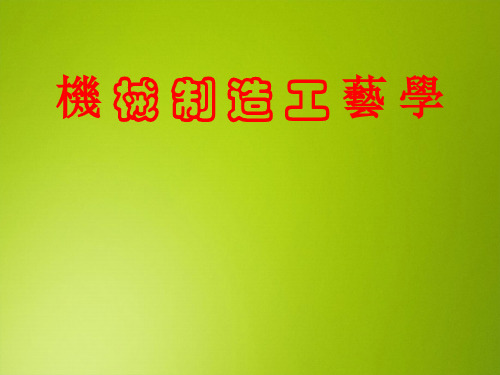
1)控制環境溫度 2)採用熱平衡措施 3)大型設備季節性的調整
4.1.6工件內應力對加工精度的影響
(1) 毛坯製造中產生的內應力
(2) 冷校直過程中產生的內應力
4.1.7 測量誤差
3.12測.量測條量件方儀的法器影的精響影度響的影響 1)測直人量接為儀與因器間素的接工測作量原、理接,觸製與造非精接度觸,測測量量、精主度動。與考 被慮測動“量測阿力量貝、原、視則靜力態”、。與分動辨態力測、量技、術絕水對準與、相責對任測心量等等。。 2)測量環境
48EI
y
L3
2)機床(夾具)部件的剛度
機床部件的變形曲線及其特點
機械製造品質分析與控制
(三次加載與卸載變形曲線的特點)
① 變形曲線是非線性的。不符合虎克定律,反映出 部件的變形不僅僅是彈性變形。
② 加載曲線與卸載曲線不重合。表明在加卸載過程 中有能量消耗。
③ 卸載後變形曲線不能回到起始點。表明在變形過 程中存在塑性變形和殘餘變形。
機械制造工藝學
機械加工精度及其控制
4.1 機械加工精度 4.2 工藝過程的統計分析
4.1 機械加工精度 4.1.1 概述
1.加工精度與加工誤差
機械製造品質分析與控制
加工精度是指加工後零件表面的實際尺寸、形 狀、位置三種幾何參數與圖紙要求的理想幾何參數 的符合程度。
加工誤差是指加工後零件實際尺寸、形狀、位 置三種幾何參數與理想幾何參數的偏離數值。
2. 加工經濟精度
機械製造品質分析與控制
指在正常加工條件下(採用符合品質標準的加工設備、 工藝裝備和標準技術等級的工人)所能保證的加工精度 和表面品質。
3. 原始誤差
機械製造品質分析與控制
机械加工精度及其控制
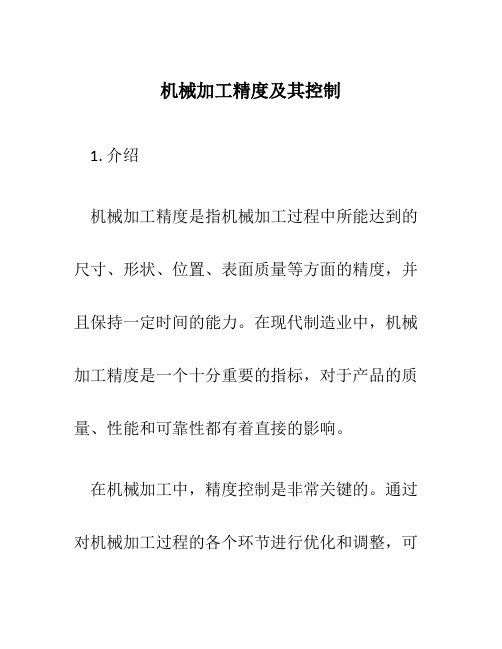
机械加工精度及其控制1. 介绍机械加工精度是指机械加工过程中所能达到的尺寸、形状、位置、表面质量等方面的精度,并且保持一定时间的能力。
在现代制造业中,机械加工精度是一个十分重要的指标,对于产品的质量、性能和可靠性都有着直接的影响。
在机械加工中,精度控制是非常关键的。
通过对机械加工过程的各个环节进行优化和调整,可以有效提高机械加工的精度,从而满足不同产品的要求。
2. 机械加工精度的影响因素机械加工精度受到多个因素的影响,以下是一些常见的影响因素:2.1 材料的特性材料的特性包括硬度、热膨胀系数、热导率等。
不同材料具有不同的物理性质,这些物理性质在机械加工过程中会对加工精度产生一定的影响。
2.2 机床的性能机床的性能是机械加工精度的关键因素之一。
机床的刚性、动态稳定性、传动机构的精度等都会对加工精度产生一定的影响。
因此,选择合适的机床对于提高机械加工精度至关重要。
2.3 加工刀具的选择和磨制加工刀具的选择和磨制也会对加工精度产生重要影响。
选择合适的切削条件和刀具材料,以及适当的磨制工艺,对于提高机械加工精度是十分重要的。
2.4 加工工艺参数的控制加工工艺参数的控制直接影响着机械加工的精度。
包括进给速度、切削深度、切削速度等参数的控制,都会对加工精度产生重要影响。
3. 机械加工精度的控制方法为了提高机械加工的精度,需要采取一系列的控制方法,以下是一些常用的方法:3.1 优化机床的性能通过优化机床的结构设计和工艺制造,可以提高机床的刚性和动态稳定性,从而提高机械加工的精度。
3.2 加强机床的维护保养定期的机床维护保养工作可以保证机床的正常工作状态,减少因机床故障引起的加工误差。
3.3 选择合适的刀具和切削条件通过选择合适的切削条件和刀具材料,可以降低切削力和切削温度,减少切削振动,提高机械加工的精度。
3.4 控制加工工艺参数通过合理的加工工艺参数控制,包括进给速度、切削深度、切削速度等,可以提高机械加工的精度。
第二机械加工精度优秀课件
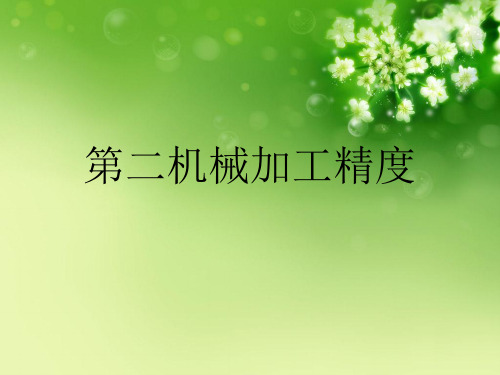
图 龙门刨床导轨垂直面
上,造成形状误差。
内直线度误差
2012-1刨/3刀/52-工件 3-工作台 4-床机身械导制轨造工艺学
15
(3) 车床导轨扭曲对工件形状精度影响
工件产生形状误差 (鼓形、鞍形、锥度)。
R H
B
一般车床H≈2B/3,外圆磨床H≈B,因此该项原 始误差△X对加工精度的影响很大。
2021/3/5
机械制造工艺学
4
三、获得加工精度的方法
1、获得尺寸精度的方法
试切法
调整法
定尺寸刀具法 自动控制法
2、获得形状精度的方法
成形刀具法
轨迹法
展成法
3、获得位置精度的方法
由机床精度、夹具精度和工件的装夹精度来保 证
2021/3/5
机械制造工艺学
5
四、产生加工误差的原因
工艺系统:机床、刀具、夹具、工件构成的完
与工艺过程有关 的原始误差(动误 差)
工艺系统受力变形(包括夹紧变形) 工艺系统受热变形 刀具磨损 测量误差 工件残余应力引起的变形
2021/3/5
机械制造工艺学
7
五、误差敏感方向
例:车削:
原始误差: AA
加工误差: RRR0
2
R R 0 22 2 R 0co R s 0co 2 s R
简化机床结构或刀具。
2021/3/5
机械制造工艺学
10
二、机床的几何误差
1、组成
机床主轴 回转误差
轴向窜动 径向跳动 角度摆动
机床几何 误差
2021/3/5
机床导轨 误差
水平面内直线度 垂直面内直线度 前后导轨的平行度
机床传动 链误差
内联传动链始末 两端传动元件间 相对运动误差
(机械制造工艺学课件)第二章机械加工精度
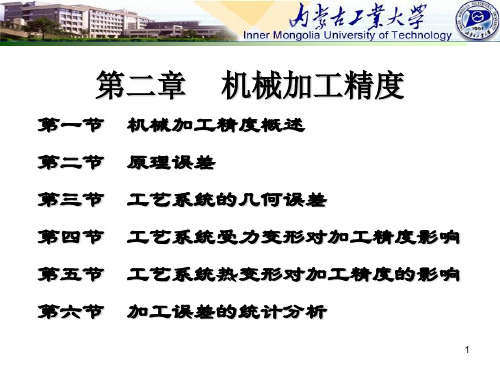
理想几何参数
➢表面——绝对平面、圆柱面等; ➢位置——绝对平行、垂直、同
轴等;
➢尺寸——位于公差带中心。 5
2.加工误差
加工误差是指零件加工后的实际几何参数对 理想几何参数的偏离程度,所以,加工误差的大 小反映了加工精度的高低。
实际加工时不可能也没有必要把零件做得与理想零 件完全一致,而总会有一定的偏差,即加工误差。只要 这些误差在规定的范围内,即能满足机器使用性能的要 求。
• 零件的加工精度包括尺寸精度、几何形状 精度和相互位置精度。
• 几何形状误差又可分为宏观几何形状误差、 波度和微观几何形状误差。
4
一、加工精度与加工误差
1.加工精度
加工精度是指零件加工后的实际几何参数(尺寸、
形状及各表面相互位置等参数)与理想几何参数的符合程 度。符合程度越高,加工精度就越高。反之,越低。
•水平面内的直线度 •垂直面内的直线度 •前后导轨的平行度
(扭曲)
现以卧式车床为例,说明导轨误差是怎样影响工件 的加工精度的。
18
(1)导轨在水平面内直线度误差的影响
当导轨在水平面内的直线度误差为△y时,引起工件在 半径方向的误差为(图2-1):
△R=△y 由此可见:床身导轨在水平面内如果有直线度误差, 使工件在纵向截面和横向截面内分别产生形状误差和 尺寸误差。
7
二、尺寸、形状和位置精度间的关系
独立原则是处理形位公差和尺寸公差关系的基本原 则,即尺寸精度和形位精度按照使用要求分别满足;在 一般情况下,尺寸精度高,其形状和位置精度也高;通 常,零件的形状误差约占相应尺寸公差的30%~50%; 位置误差约为尺寸公差的65%~85%。
《机械加工精度》PPT幻灯片PPT
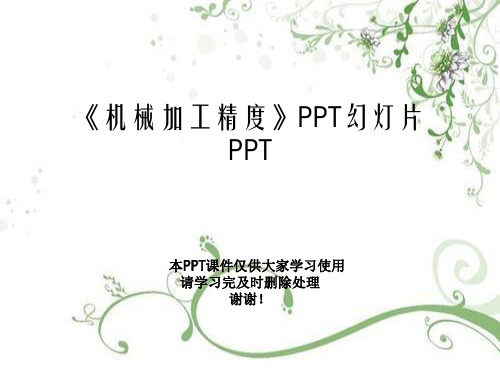
4 了解提高加工精度的途径
§5-1 概 述 一、机械加工精度和加工误差
在机械加工过程中,由于各种因素的影响, 使刀具和工件间的正确位置发生偏移,因而加工 出来的零件不可能与理想的要求完全符合,两者 的符合程度可用机械加工精度和加工误差来表示。
1、机械加工精度
是指零件加工后的实际几何参数(尺寸、形状和位置) 与理想几何参数的符合程度。
2)导轨在垂直面内的直线度误差
卧式车床或外圆磨床的导轨垂直面内有直线度误差 △Z,使刀尖运动轨迹产生直线度误差△Z,由于是误 差非敏感方向,零件的加工误差
RZ2 d
由于△Z引起的加工误差半径 为R△Z的二次方误差,
数值很小,可忽略不计。
图 导轨在垂直面内的直线度误差
图 龙门刨床导轨垂直面内直线度误差 1-刨刀 2-工件 3-工作台 4-床身导轨
(三)刀具与夹具误差 1. 夹具误差
夹具的制造误差一般指定位元件、导向元件及夹具 体等零件的加工和装配误差。这些误差对零件的加工精 度影响较大。
图 钻径向孔的夹具
2. 刀具误差 定尺寸刀具,加工时刀具的尺寸精度直接影响加
工工件的尺寸精度; 采用成形车刀、成形铣刀、成形砂轮等成形刀具
加工时,刀具的形状精度直接影响加工工件的形状 精度;
车削具有圆度误差
的毛坯时,由于工艺系统受力变形,而使工件产生相应的圆度 误差
由切削原理可知
(3)夹紧力和重力引起的加工误差 被加工工件在装夹过程中,由于刚度较低或着力点
不当,都会引起工件的变形,造成加工误差。
又如磨削薄片零件,假定坯件翘曲,当它被电磁工作 台吸紧时,产生弹性变形,磨削后取下工件,由于弹 性恢复,使已磨平的表面有产生翘曲。
第二章 机械加工精度及其控制
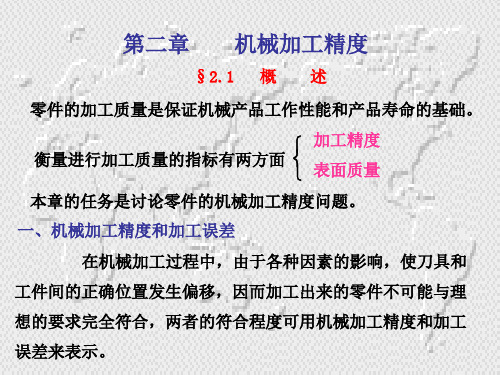
如图,车削时工件的回转轴线为O,刀尖正确位置在A。设某一瞬时 由于各种原始误差的影响,使刀尖位移到A’,AA’即为原始误差δ,它与OA间 的夹角为φ,由此引起工件加工后的半径由R0=OA变为R=OA’,故半径上的 加工误差△R 为:
可以看出:
当原始误差的方向恰为加工表面的法向方向(φ =0°)时,引起的加工误差最大; 当原始误差的方向恰为加工表面的切线方向(φ =90°)引起的加工误差最小。
1)用定程机构调整时,调整精度取决于行程挡块、靠模及凸 轮等机构的制造精度和刚度;
2)用样件或样板调整时,调整精度取决于样件或样板的制造、 安装和对刀精度;
3)工艺系统初调好以后,—般要试切几个工件,并以其平均 尺寸作为判断调整是否准确的依据。由于试切加工的工件数 (称为抽样件数)不可能太多,不能完全反映整批工件切削过程 中的各种随机误差,故试切加工几个工件的平均尺寸与总体尺 寸不能完全符合,也造成加工误差。
4. 主轴回转运动误差的影响因素
影响主轴回转运动 误差的主要因素
主轴的误差:制造 轴承的误差:圆度、波度(主轴颈与内孔) 轴承的间隙:影响油膜厚度; 与轴承配合零件的误差:轴颈和箱体轴承孔 主轴系统的径向不等刚度和热变形等
对于不同类型的机床,其影响因素也各不相同。(滑动轴承)
工
刀
件
具
回
回
(2)当形状精度要求高时,相应的位置精度和尺寸精度不 一定要求高。
4、加工精度与加工成本和生产效率的关系 一般地,加工精度要求↑ ,加工成本↑ ,生产效率↓ 。 5、研究加工精度的目的
研究加工精度的目的、就是弄清各种原始误差对加 工精度影响的规律,掌握控制加工误差的方法,以获得预期 的加工精度,必要时能指出进一步提高加工精度的途径。
2 机械加工精度及其控制
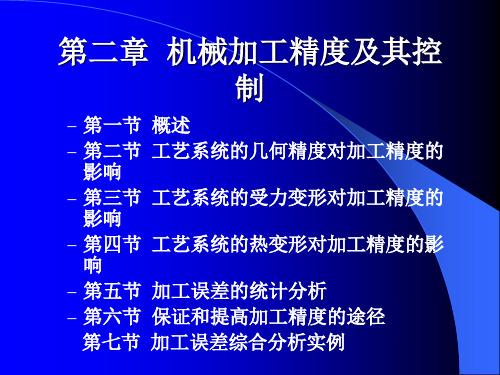
(尺寸、形状和表面间的相互位置)对理想 几何参数的偏离程度。
尺寸、形状和位置精度
零件的加工精度包含:尺寸精度、形状 精度和位置精度。
三者之间是有联系:
•形状公差应限制在位置公差之内,而位置误差 一般也应限制在尺寸公差之内 •当尺寸精度要求高时,相应的位置精度、形状 精度也要求高 •形状精度要求高时,相应的位置精度和尺寸精 度有时不一定要求高
因此,机床在安装时应有良好的基础。并严格
进行测量和校正,而且在使用期间还应定期复 校和调整
导轨磨损造成导轨误差
使用程度不同及受力不均,导轨沿全长上 各段的磨损量不等,并且在同一横截面上 各导轨面的磨损量也不相等。导轨磨损会 引起床鞍在水平面和垂直面内发生位移, 且有倾斜,从而造成刀刃位置误差。
减小导向误差的措施
直接保证工件在加工过程中的回转精 度而不依赖于主轴,是保证工件形状精度 的最简单而又有效的方法。 图2-18、2-19
(三)机床传动链的传动误差
1.传动链精度分析
– 传动链的传动误差是指内联系的传动链中首
末两端传动元件之间相对运动的误差。它是 螺纹、齿轮、蜗轮以及其它按展成原理加工 时,影响加工精度的主要因素。 – 由于所有的传动件都存在误差,因此,各传 递件对工件精度影响总和 为各传动元件所 引起末端元件转角误差的迭加:
统计分析法:
• 以生产中一批工件的实测结果为基础,运用数 理统计方法进行数据处理 • 质量有问题时,判断误差性质,找出误差规律 • 以指导我们解决有关的加工精度问题
第二节 工艺系统的几何精度对 加精度的影响
一、加工原理误差 二、调整误差 三、机床误差 四、夹具的制造误差与磨损 五、刀具的制造误差与磨损
Ry y
Rz (Z ) / D
《机加工精度》PPT课件
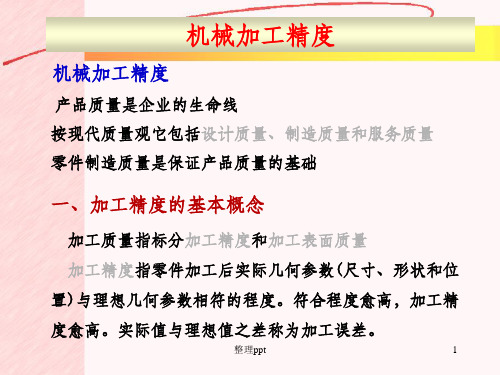
ε=Δ工 /Δ毛= C(ap1 –ap2) /(k系(ap1 – ap2))= C /k系
整理ppt
30
讨论:
1. ε=Δ工 /Δ毛= C /k系 2. ε总是小于1,有修正误差的能力 3. 多次进给ε=ε1ε2ε3…
4. 2. k系越大,ε就越小,复映到工件上的误差越小
5. 3. C减小, ε就越小,应采取减小Fy的措施
主要是主轴部件、床身导轨及两者相对位置的热变形
整理ppt
37
整理ppt
38
(5)热变形的控制
(1)减少发热和采取隔热; (2)强制冷却,均衡温度场; (3)从结构上采取措施减少热变形; (4)控制环境温度。
整理ppt
39
5.工件内应力引起的变形
工件若产生内应力处于不稳定状态会逐渐变形
内应力产生的原因及消除措施
k刀= Fy / y刀 , k工= Fy / y工 所以, k系= 1/(1/ k机+ 1/ k夹+ 1/ k刀+ 1/ k工)
工艺系统刚度比刚度最小环节的刚度还要差
整理ppt
26
2)工艺系统受力变形对加工精度的影响 ①切削力位置的变化对加工精度的影响
设刀具工件刚度很大 总变形 y系= y刀架+ yx
接触刚度越小。
整理ppt
24
② 低刚度零件本身的变形
③ 连接表面间的间隙 ④ 接触表面间的摩擦
变形滞后现象
⑤ 受力方向及作用力矩 y 是Fx、Fy、Fz 综合结果
整理ppt
25
(5)工艺系统受力变形及其对加工精度的影响 1)工艺系统的变形
总变形 y系 = y机+ y夹+ y刀+ y工 k系= Fy / y系,k机= Fy / y机 , k夹= Fy / y夹 ,
- 1、下载文档前请自行甄别文档内容的完整性,平台不提供额外的编辑、内容补充、找答案等附加服务。
- 2、"仅部分预览"的文档,不可在线预览部分如存在完整性等问题,可反馈申请退款(可完整预览的文档不适用该条件!)。
- 3、如文档侵犯您的权益,请联系客服反馈,我们会尽快为您处理(人工客服工作时间:9:00-18:30)。
二、分布图分析法
分布曲线
◆ 正态分布
➢ 概率密度函数
y
1
e
1 2
x
2
2
x , 0
式中:
y
μ和σ分别为 正态分布随机变量
F(z)
总体平均值和标准差。
平均值μ=0,标准差σ=1的正态
-σ +σ
分布称为标准正态分布,记为:
0
x ~ N ( 0, 1 )
μ
z
x(z)
(z=0)
正态分布曲线
正态,其算术平均值近似成线性变
化(如刀具和砂轮均匀磨损)
最小极限尺寸:
Amin 60 0.01 60.01
公差值:
T 0.06 0.01 0.05
公差带中心:
Am 60 0.025 60.025
X
1 n
n i 1
Xi
37.25m
S
1 n 1
n i 1
(Xi
X )2
9.06m
6S 69.06 54.36m
工件尺寸分散中心:
60 0.03725 60.037
30
40 44 34 42 47
22
28
34
30
36
32
35
22
40
35
36
42
46
42
50
40 36 20 16 53
32 46 20 28 46 28 54 18 32 35 26 45 47 36 38 30 49 18 38 38
表2-4 频数分布表
组号 组界(um) 中心值(x1) 频数统计
§2.5 加工误差的统计分析
加工误差的性质
点图分析法
分布图分析法
机床调整尺寸
一、加工误差的性质
加工误差统计特性
加工误差
系统误差
常值系统误差 系统误差 变值系统误差 随机误差
顺序加工一批工件时,其大小和方向均不改变,或按一定规 律变化的加工误差为系统误差。
◆ 常值系统误差——其大小和方向均不改变。如机床、夹具、刀 具的制造误差,工艺系统在静力作用下的受力变形,调整误差, 机床、夹具、量具的磨损等因素引起的加工误差。
加工误差的统计分析
◆ 运用数理统计原理和方法,根据被测质量指标的统计性 质,对工艺过程进行分析和控制。
二、分布图分析法
(一)实验分布图(直方图)
加工一批零件,抽取其中一定数量的工件进行测量,这批
工件称为样本,其件数 n 称为样本容量。
由于随机性误差的存在,加工尺寸的实际数值是各不相同的,
在一定范围内变动,这种现象称为尺寸分散,用 x 表示。
以工件尺寸为横坐标,以频率或频率密度为纵坐标,可作 出该工序工件加工尺寸的实验分布图——直方图。 样本的平均值表示该样本的尺寸分散中心
X
1 n
n i 1
Xi
式中:
X ------样本的平均值;
xi -----各工件的尺寸
样本的标准差 S 反映了该批工件的尺寸分散程度
S
1 n 1
n i 1
(Xi
44 20 46 32 20 40 52
33 40 25 43 38 40 41
30
36 49 51 38 34
22 46 38 30 42 38 27
49 45 45 38 32 45 48
28
36 52 32 42 38
40 42 38 52 38 36 37
43 28 45 36 50 46 33
x(z)
(z=0)
图4-45 正态分布曲线
利用上式,可将非标准正态分布转换成标准正态分布进行计算。
F(z)为图中阴影线部分的面积。对于不同 z值的F(z),可由表 2-5(P76)查出
二、分布图分析法
◆ 非正态分布
y
➢ 双峰分布:两次调整下加工的工 件或两台机床加工的工件混在一起
0
➢ 平顶分布:工件瞬时尺寸分布呈 y
1 13.5-18.5
16
┯一
2 18.5-23.5
21
正┰
3 23.5-28.5
26
正┰一
4 28.5-33.5
31
正正┰一
5 33.5-38.5
36
正正正┰一
6 38.5-43.5
41
正正正一
7 43.5-48.5
46
正正正一
8 48.5-53.5
51
正正
9 53.5-58.5
56
一
频数
3 7 8 13 26 16 16 10 1
◆ 变值系统误差——误差大小和方向按一定规律变化。如机床、 夹具、刀具在热平衡前的热变形,刀具磨损等因素引起的加工误 差。
一、加工误差的性质
随机误差
◆ 顺序加工一批工件时,其大小和方向随机变化的加工误差为 随机误差。 ◆ 随机误差是工艺系统中大量随机因素共同作用而引起的。 ◆ 随机误差服从统计学规律。 ◆ 如毛坯余量或硬度不均,引起切削力的随机变化而造成的加 工误差;定位误差;夹紧误差;残余应力引起的变形等。
二、分布图分析法
➢ 分布函数
F(x) 1
e dx x
1 2
x
2
2
y
F(x)— 正态分布曲线上下积分限间包
含的面积,它表征了 随机变量x落在区间
(-∞,x)上的概率。
令:z x
z 为标准化变量, 代入上式,有:
0
F(z) 1
z z2 e 2dz
2 0
F(z)
-σ +σ
μ
z
组界:
xm
in
(
j
1)d
d 2
( j 1,2,3,.....k. )
各组中值: xmin ( j 1)d
3) 统计各组数据,整理成频数表 表2-2 分组数k的选定
n 25-40 40-60 60-100 100 100-160 160-250
k6
7
8
10
11
11
表2-3 轴径尺寸实测值 (um)
频率 (%)
3 7 8 13 26 16 16 10 1
频率密度(%/um)
0.6 1.4 1.6 2.6 5.2 3.2 3.2 2 0.2
y
(频数)
13.5 10 (公差带下限)
37.25 (平均偏差)
35 (公差带中心)
直方图
58.5 x
(偏差值)
60 (公差带上限)
最大极限尺寸:
Amin 60 0.06 60.06
X )2
频率密度=
频率
频数
——× 组距
例2-3:磨削一批轴径
60 0.06 0.01
mm的工件,试绘出工件加工尺
寸的直方图
1)采集数据 :样本容量 n = 100, 通常取 n = 50~200
2) 确定分组数 k’: 取 k’=9
组距 d:
d xmax xmin R k1 k1
样本尺寸或偏差的最大值与最小值之差,称为极差 R
R xmax xmin
把测得的数据记录下来,按尺寸大小将整批工件进行分组,
分组数为 k ,每一组中的零件尺寸处在一定的间隔范围内,组距
为 d 。同一误差组零件数量称为频数 mi,频数与样本容量之比称
为频率 fi。
fi
mi n
d R k 1
二、分布图分析法