原物料工程评估表
GP物料风险等级评估

HS物料风险等级评估控制程序
编制:日期:2009-12-8
审核:日期:2009-12-10
批准:日期:2009-12-16
受控标识
声明:未经同意,不得复制!
1.目的
确定经来料品质课的所有原材料的RoHS风险等级,以便对原材料进行RoHS检测和管控.并预防或减少可能伴随的安全、环境影响和本公司损失。
4.4.1.2 将除欧盟豁免之外的外购件定为低风险物料(包括手机配件、塑胶料、色粉、油漆、五金和包材),每三个月抽检一次。低风险物料管控时间为一年,一年内无发现超标情况的物料不再统一进行抽检,仅每年抽检一次确认其HSF符合性。
4.4.1.3 新评估物料首次来料需抽检一次后再定其风险等级。
4.4.2物料RoHS抽检项目
铅/汞/六价铬/PBBs/PBDEs
判定
合格
不合格
检测结果
≤100ppm ppm
100~400 ppm
400~700ppm
>700ppm
物料风险等级
低危(L)
中危(M)
高危(H)
检测项目
镉
判定
合格
不合格
检测结果
≤10ppm
10~40 ppm
40~70ppm
>70ppm
物料风险等级
低危(L)
中危(M)
4.3物料抽检频率及调整
4.3.1物料抽检频率
Байду номын сангаас供应商物料风险等级
确认抽检频率
L
每三个月抽检1次以上
M
每5批抽检1次以上
H
每批次进行1次
4.3.2风险等级调整
a.等级H→等级M
连续5个批次抽检合格的物料,再依据对供应商的审核情况进行物料等级H→等级M的调整。
XX工程评分表(适用于材料)(2024年)

有无公司内部履约信誉介 绍担保人
3
有公司信誉担保人的担保书得3ቤተ መጻሕፍቲ ባይዱ, 没有担保书为。分
0~3
根据有无保证书得分
4
样品质量
7
报价样品与甲方确认样品一致
7
样品质量与甲方一致的9分,接近95%以上 的8分.90%以上的6分
5
售后承诺
7
售后服务
7
12小时到场,48小时售后服务。
6
工期承诺
6
承诺工期每提前1天加1分,最高 加0.2分,承诺工期不能满足招标文 件要求的为废标
0~6
满足工期得6分,每承诺提前1天加0.5分, 不超过2分
项目班子组成及工人
9
管理班子人数
0-4
能满足本工程的施工需得4分,一般I分, 不能。分
施工工人
0-5
能满足本工程的施工需得5分,一般1分, 不能0分
7
合计
40
40
本表合计最高得分30分,如果由于投标保证金加分,本表最终得分高于30分的,总分按照30分进入总得分。
工程评分表(适用于材料)
序号
项目
标准 分
评定标准
分值
得分
评审说明
1
付款条件
3
是否认可合同的付款条件
0~3
同意的3分。如能可以先期加工或订货的另 加3分。
2
合同履约保证金
5-N
提供合同履约保证金为合同额的10% (5分),每增加1%增加1分, 分数无上限
5-N
根据合同有履约保证金额承诺书,及履约保 证金额度得分
评标委员会全体成员签名:
审计签字
记录人签字:
审核人签字:
日期: 年 月 日
供应商评估表范本正式版
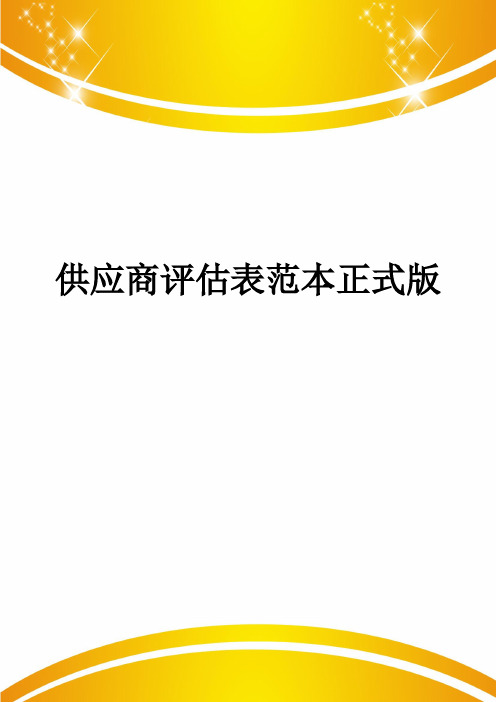
供应商评估表范本正式版供应商评估表供应商名称:主要供货产品:评估日期:供应商代码(评估合格后填写):一、供应商简介三、评估记录累计记分:四、评估结果供应商评估表供应商名称:主要供货产品:评估日期:供应商代码(评估合格后填写):一、供应商简介三、评估记录累计记分:四、评估结果供应商评估表表单使用说明1、上述资源商评价表各项评价指标满分均为100分,通过打分后再计算相关加权平均值,根据得分确定供应商等级;计算公式:供应商总得分=∑评价项目得分×评价项目权重/100=(总体情况得分×10% + 生产制造得分×15%+ 技术研发得分×5%+ 质量管理得分×35%+ 物流交货得分×15% + 原材料采购得分×10%+ 环保安全得分×10%)/100评分时应注意以下事项:●客服部组织相关部门对供应商进行评分时,对于每一评分项应有足够的事例或者数据作为支撑,并随打分结果一起提交;●评分由客服部组织办事处、财务部等部门举行,可以研讨会的形式进行;●对于不能明确作出评分决定的事项(如数据不足等),可由部门联合讨论后决定,并进行必要的补充说明和标注;2、公司对供应商分为4个等级,其对应标准如下:合格供应商评估表合格供应商评估表合格供应商评估表合格供应商评估表合格供应商评估表合格供应商评估表合格供应商评估表编号:ABO-QR-3.2合格供应商评估表合格供应商评估表合格供应商评估表。
供应商现场评估表
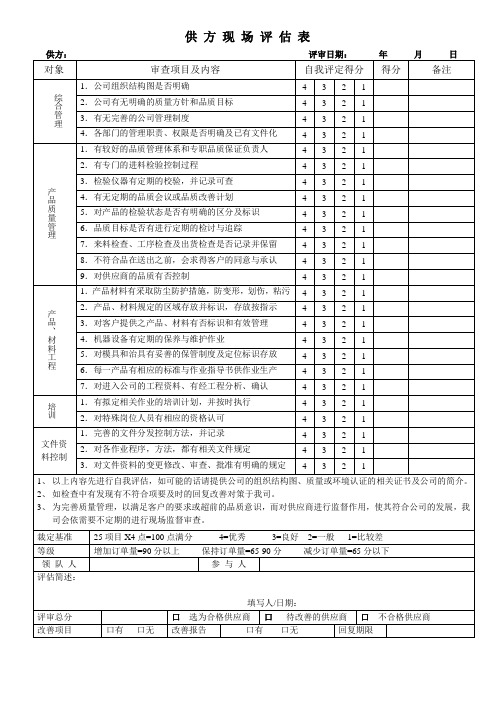
供方:评审日期:年月日
对象
审查项目及内容
自我评定得分
得分
备注
综合管理
1.公司组织结构图是否明确
4
3
2
1
2.公司有无明确的质量方针和品质目标
4
3
2
1
3.有无完善的公司管理制度
4
3
2
1
4.各部门的管理职责、权限是否明确及已有文件化
4
3
2
1
产品质量管理
1.有较好的品质管理体系和专职品质保证负责人
裁定基准
25项目X4点=100点满分4=优秀3=良好2=一般1=比较差
等级
增加订单量=90分以上保持订单量=65-90分减少订单量=65分以下
领队人
参与人
评估简述:
填写人/日期:
评审总分
口选为合格供应商
口待改善的供应商
口不合格供应商
改善项目
口有口无
改善报告
口有口无
回复期限
4
3
2
1
3.对文件资料的变更修改、审查、批准有明确的规定
4
3
2
1
1、以上内容先进行自我评估,如可能的话请提供公司的组织结构图、质量或环境认证的相关证书及公司的简介。
2、如检查中有发现有不符合项要及时的回复改善对策于我司。
3、为完善质量管理,以满足客户的要求或超前的品质意识,而对供应商进行监督作用,使其符合公司的发展,我司会依需要不定期的进行现场监督审查。
4
3
2
1
2.有专门的进料检验控制过程
4
3
2
1
3.检验仪器有定期的校验,并记录可查
4
新供应商评估表格模板
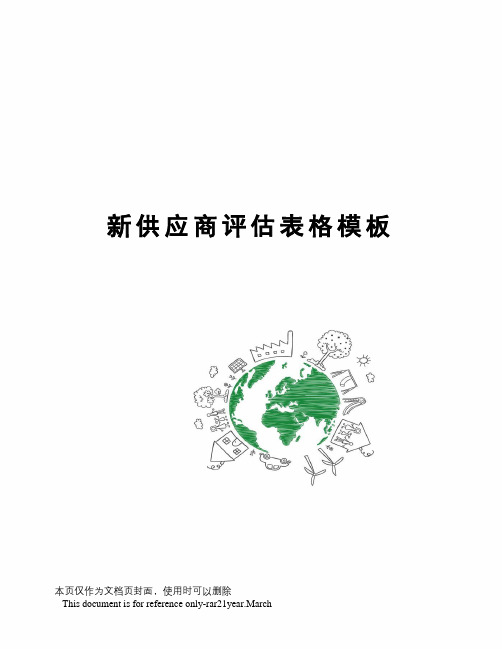
新供应商评估表格模板本页仅作为文档页封面,使用时可以删除This document is for reference only-rar21year.March供应商评审表供应商名称:主要供货产品:评审日期供应商代码(评估合格后填写):供应商评审表一、供应商资料填写以上项目由相关责任人评定二、供应商须提供的资料1、营业执照复印件;2、税务登记证复印件;3、公司介绍(或相关资料)4、认证体系证书复印件;5、公司(工厂)机器设备清单;6、代理商(贸易商)需提供代理证书附表5附表6附表7附表8供应商评审操作流程图供应商评审程序一、目的对供应商进行评审和选择保证本厂采购的原材料、包装材料及其它辅料等以确保其为公司提供合格的产品。
本程序适用于为我司提供产品的供应商的评定和控制。
二、定义1 采购产品指购买本厂生产所需的原材料、半成品、包装材料及其它辅料等。
2 供应商评定实地到供应商处所或供应商提供的资料、电话、传真等方式进行对厂房、生产设备、产品检验等各项要求是否满足本厂的要求。
3 评审人员负责本公司供应商评审考核的评定人员。
4 供应商评估因环境因素而无法进行实际评审时可用样品方式进行检测评估。
三、职责1 供应部负责原材料、包装材料及其它辅料的供应商开发资格初审、工作方法考评和供应商档案的建立。
2总经理负责合格供应商的批准。
四、程序内容1 供应商初步筛选1供应商资料收集供应部负责收集有能力满足本厂所需原材料、包装材料及其它辅料的供应商产品质量、服务、交货期、价格作为筛选的依据。
供应部负责收集有能力满足本厂所需原材料、包装材料及其它辅料的供应商产品质量、服务、交货期、价格作为筛选的依据。
2 供应商的初步筛选供应部对《供应商调查问卷》进行初步评价需确定采购的材料是否符合国家法律法规和安全要求对于危险品需要求供应商提供相关证明文件及检测报告。
2 供应商的资格初审1采购员先按目标供应商所提供的相关资料、样品、报价原料样品的质量是否符合本厂所需原料的技术方针要求等进行产品质量检验质量是否符合本厂所需原料的要求进行初审。
供应商审核评估表

1 1-6是否验证改善对策的有效性(详细记录下批的检查结果)
1-7是否有对客退品做确认,并且有记录。
1-8当出现原物料短缺时或其它问题时是否有对原物料实施特采管控,是否通过各相关部门 来确定,并且是由品保部门做最后的决定
1-9进料检查人员是否有经过培训并有记录。
总分 18 此项得分
4-10是否有对生产机台定期做科学的机台保养
4-11生产车间5S是否良好
总分 22 此项得分
5-1是否有仪器列表来反映现有仪器的状态。
5-2是否有仪器相对应的操作说明书。
仪器管理 5-3是否有未校验之仪器在使用当中。
5 5-4所使用仪器是否符合所测量产品之精度。
5-5测试之仪器是否有被合理保养。
总分 10 此项得分
评分标准: 评0分无系统 评1分必须改善 评2分满意
不符合项描述
供应商审核评估表
序号 评估流程
详细内容
得分
3-1不合格品是否被单独隔离。
3-2在作业指导书中是否有不合格品的标示方法。
3-3不合格品发生日期,地点和不良内容是否有记录。
不合格品 3-4是否有不合格品的处理流程
3
管理 3-5不合格品发生时,是否有相关部门参与处理。
2
2-8包装箱是否有挤压和破损现象。
2-9超期品是否有被单独区分摆放。
2-10是否有对每批货通过生产日期的标示进行先进先出的管控,并将生产日期注明在外箱 上。
2-11仓库是否能够从标识充分识别该产品。
2-12不同的产品是否会有不同的批号。
2-13仓库有无合理之区域划分?(如待验区、退货区等)。
总分 26 此项得分
评分标准: 评0分无系统 评1分必须改善 评2分满意
环保物料风险评估表

品质协 不使Байду номын сангаас有害 供应商
议 物质声明书 评估结
*
*
果
XX公司
环保物料风险评估表
风险评估等级项目
物料名称
材质证 明
产品构 成分析
表
有害物 质测试 报告
MSDS (化学品 供应商)
编号: 日期:
风险等级
其他
来料检验管控
管控方式 年度审查管控
a.高风险供应商:料时需3 a.高风险供应商:每年一 个月送检测室检测一次; 次; b.中风险供应商:来料每 b.中风险供应商:每两 半年送检测室检测一次; 年一次; c.低风险供应商:来料每 c.低风险供应商:每三年 半年送一次送供应商每年 一次。 提供一次第三方检测报告 。
制作: 日期:
审核: 日期:
共1页 第1页
批准: 日期:
物料零件RS风险等级评估程序(含表格)

物料/零件RS风险等级评估程序(QC080000-2017)1.0 目的为识别本公司所有原物料﹑零部件的环境管理物质风险等级﹐以利于生产过程中对环境管理物质的控制﹐特制订本办法作为物料/零件风险等级评估的指引。
2.0 范围2.1 本作业办法适用于FD/FG/FQ厂区的生产用料﹑外包半成品/成品﹑外买外卖产品的风险等级评估及管理。
2.2 本作业办法不适用于模具承认时的风险评估。
3.0 定义3.1 材质风险﹕指原物料﹑零部件﹑组件所构成的材质本身的风险﹐一经评定后其一般不会再发生变化。
3.2 供货商风险﹕指提供物料的供货商的环境管理物质体系的综合水平﹔一般通过对供货商RSC体系的评鉴结果﹑供货商的品牌知名度或其日常交货质量状况来进行适时评定。
3.3 物料风险﹕指材质风险与供货商风险的总体考虑﹔一般通过将这两种风险评分的乘积作为其最终评定结果。
3.4 客供料﹕指由客户方直接交付给本公司投入生产使用的物料(本公司与该物料的制造商/代理商不发生任何交易﹔亦非客户指定供货商提供的物料)。
4.0 职责4.1 零件承认工程师﹕负责材质风险的评估。
4.2 品保工程师﹕4.2.1 负责供货商风险的评估﹔4.2.2 结合材质风险完成物料风险等级识别﹔4.2.3 将所有评估结果登录于风险评估表上。
4.3 IQC: 依据风险等级结果来执行IQC进料检验抽检。
5.0 作业程序5.1 物料风险评估的时机5.1.1 新零件的物料风险评估必须在新零件承认时由相关人员进行评定完成﹔评定结果记录于零件样品承认书﹔同时由品保单位将评估结果登录于风险评估表。
相关作业流程请参考“零件承认作业办法”。
5.1.2 已被承认零件的物料风险于进料前由相关人员完成评定﹔评定结果记录于风险评估表。
5.2 物料/零件风险的识别5.2.1 为充分及有效的识别材质风险﹐针对组成各物料/零件的材质中环境管理物质的应用历史进行识别如下表﹕环境管理物质应用历史塑料添加剂﹑稳定剂﹑焊锡材料﹑油墨中的添加剂﹑玻璃及铅陶瓷中的添加剂镉塑料添加剂﹑着色剂﹑稳定剂﹑油墨中的添加剂某些塑料的添加剂﹑凝固剂﹑荧光灯泡﹑开关及继电器中的汞某些特殊元器件六价铬电镀﹑金属表面防锈处理﹑颜料PBB/PBDE 塑料中的阻燃剂Phthalate 塑料增塑剂(特别是柔性塑料材料)﹑油漆﹑颜料﹑粘着剂卤素阻燃剂塑料中的阻燃剂5.2.2 若供货商本身或其所交物料/产品制程属于下表特定情况之一﹐则该物料/零件应直接判定为高风险等级(不需执行5.2.3作业)。
HSF风险评估程序(含记录)

HSF风险评估程序(QC080000-2017)1.0目的为识别本公司所有原物料/零部件、供应商和生产过程中所产生的环境管理物质风险等级,以利于生产过程中对环境管理物质的控制。
2.0适用范围适用于本公司生产用料、过程与HSF产品相关之的风险评估。
3.0定义3.1材料风险:指原物料﹑零部件﹑组件所构成材料的本身的风险﹐一经评定后其一般不会再发生变化。
3.2供应商风险:指提供物料的供应商的环境管理物质体系的综合水准,一般通过对供应商RSC体系的评鉴结果,供应商的品牌、规模、知名度或其日常交货品质状况来进行适时评定。
3.3 物料风险:指材料风险、供应商风险的总体考量:一般通过将这两种风险评分的乘积作为其最终评定结果。
3.4生产过程风险:指产品实现过程中所有生产设备、工/夹具、测量仪器、工作环境、操作人员等在正常、异常、紧急的状况下所有可能导致交叉污染产生的风险状况。
4.0组织权责4.1零件承认工程师:负责材料风险的评估。
4.2品保/采购工程师:4.2.1负责供应商风险的评估;4.2.2结合材料风险完成HSF风险等级评估;4.2.3将所有评估结果登录于风险评估表上;4.3IE工艺工程师:负责过程风险的评估。
4.4 IQC:依据风险等级结果来执行进料检验抽检。
5.0作业程序5.1HSF风险评估时机a>对新零件材料的风险评估在设计初期或有任何设计或物料更改的阶段进行;已被承认零件的HSF风险于进料前由IQC依《进料检验规范》进行评估。
b>对供应商的风险评估为一年一次,或有新供应商加入时进行;c>生产过程的风险评估在生产前或有任何工艺更改时依《首件确认规范》进行。
5.2物料风险的识别5.2.1若供货商本身或其所交物料﹑产品制程属于下表特定情况之一﹐则该物料应直接判定为高风险等级。
特定供应商 1.一年内曾经发生过超标的供应商特定物料 1.线路板(PCB、PCBA)2.外购线材(CABLE)3.外购射出成型塑料件特定制程 1.表面处理(电镀、喷涂、移印、丝印)制程2.电子焊接(插件、SMT焊接)制程3.注塑成型制程5.2.2若无法通过5.2.1的方法来直接判定出物料的风险等级,则零件承认工程师及品保工程师必须分别按照下表的评定准则来识别出零件材料风险及供应商风险﹔评估时必须依照以下要求作业﹐并按要求记录于风险评估表上。
原材料变更评估表中英文对照版

(Safetysupervisorevaluation)
安全主管(Safetysupervisor):日期Date:
2.其他要求例如通知、培训、实施时的检查
if need to inform, training, check when implementation.
Inform:Yes□No□通知部门:
新材料的放行批准release of new materialYes□No□
新材料的MSDS的提交submit MSDS of new materialYes□No□
新材料的价格的核算price accounting for new materialYes□No□
2)技术部门TECH部门经理签字/日期manager signature/date
使用新材料的项目计划的策划Planning for the project of use of new materialYes□No□
提交EHS影响评估申请apply for the EHS impact evaluationYes□No□
技术文件的修订(图纸、物料号与BOM、原材料、工艺文件等)Revise the technical documents(drawing, material no. BOM, material and process documents etc.)Yes□No□
检验文件的修订revising the test documentsYes□No□
工艺参数的检查和验证testing andverificationof process parametersYes□No□
产品的检查Production InspectionYes□No□
4)生产计划PP计划签字/日期PP supervisor signature/date
塑料包装材料—原材脆弱性评估表

评估组长: 日期:2023年2月27日评估人员:
评估准则
1、原物料特性:原物料本身特性是否容易被掺假和替代。
风险等级:高-容易被掺假或替代;中-不易被掺假或替代;低:很难被掺假或替代。
2、过往历史引用:在过去的历史中,在公司内外部,原物料有被被掺假和替代的情况记录。
风险等级:高-多次有被掺假和替代的记录;中-数次被掺假和替代的记录;低:几乎没有被掺假和替代的记录。
3、经济驱动因素:掺假或替代能达成经济利益。
风险等级:高-掺假或替代能达成很高的经济利益;中-掺假或替代能达成较高的经济利益;低:掺假或替代有较低或无经济利益
4、供应链掌控度:通过供应链接触到原物料的难易程度。
风险等级:高-在供应链中,较容易接触到原物料;中-在供应链中,较难接触到原物料;低:在供应链中,很难接触到原物料。
5、识别程度:识别掺假常规测试的复杂性。
风险等级:高-无法通过常规测试方法鉴别出原物料的掺假和替代;中-鉴别出原物料的掺假和替代需要较复杂的测试方法或无法鉴别出低含量的掺假和替代;低-较容易和快速的鉴别出原物料的掺假和替代,检测精度高。
注:危害性:根据发生的可能性判定分值为1~6分,其中高风险划分有(容易产生:6分 较容易产生:5分),中风险划分有(一般产生:4分 轻微产生:3分),低风险划分有(基本不产生:2分 不产生:1分)
等级分数评判结果判定:5-10分为低风险,11-16分为中风险,17-30分为高风险。
原物料脆弱性评估表

原物料脆弱性评估表
文件编号:QSJL-CG-0005版本号:A/0
序号
原物料名称
风险等级
原物料特性
过往历史引用
经济驱动因素供应链Fra bibliotek控度识别难度
综合得分
综合风险等级
注:请按照《预防和消除食品欺诈计划控制程序》填写。
危害性:根据发生的可能性判定分值为1~6分,其中高风险划分有(容易产生:6分;较容易产生:5分),中风险划分有(一般产生:4分;轻微产生:3分),低风险划分有(基本不产生:2分;不产生:1分)等级分数评判结果判定:5-10分为低风险,11-16分为中风险,17-30分为高风险。
原辅料包装材料供应商的评估规程

标准操作规程STANDARD OPERATING PROCEDURE1.目的:建立原、辅、包材料供应商的评估规程,保证原、辅、包、材料质量的稳定性以及供货及时,确保产品质量。
2.范围:本公司使用的原、辅、包材料供应商。
3.责任:质保、质检、仓库及生产部负责人、总工程师对实施本规程负责。
4.程序:4.1成立供应商评估小组,成员必须包括质量保证、质量检验、仓库有关人员及生产部负责人、总工程师。
4.2评估小组必须每年对本公司重点供应商(供货比例占80%左右)进行年终评估,评估内容为产品质量、交货期、价格、售后服务等,并对供应商进行打分,可分为好、中、差三个等级,被列为差等的供应商应取消供货资格,对中等供应商提出整改意见(附件一),写出评估报告交总经理审批。
4.3对供货比例占20%以下的次要供应商进行日常评议。
4.4一个品种一般应选择二个供应商,以有利于在产品质量、价格、服务等方面的竞争。
4.5为确保产品质量的稳定性,采购员根据质量保证部门提供的供应商名单进行采购,不得随意选择和更改供应商。
4.6新供应商的建立应本着货比三家、质量选优的原则,由评估小组评审通过。
4.6.1 由采购员提出新的供应商,并向评估小组书面报告市场调研情况及供应商的基本情况:是否有三证、厂房设施、设备、厂址、报价比较(至少三家厂商)等,并向质量保证部门提供样品。
由质量保证部门交质量检验部门进行检验。
4.6.2 质量检验部门按公司有关标准分析样品,出具合格或不合格报告交质量保证部门,再由评估小组进行评估。
4.6.3 如果样品分析合格后,由采购员将“评估调查表”(附件二)交供应商填写,评估小组应对供应商的三证(生产许可证、产品批文、营业执照)、厂房设施、设备、管理等进行确认(实地考察或行业了解)。
4.6.4 对可能批准成为新供应商的厂家经评估小组同意后,由采购员购置适量样品供生产部门试用或进行工艺摸索,并由生产部门写出试验报告。
4.6.5 经评估小组确认合格的供应商由物料部门同供应商洽谈具体采购事宜。
供应商及外包单位评估表
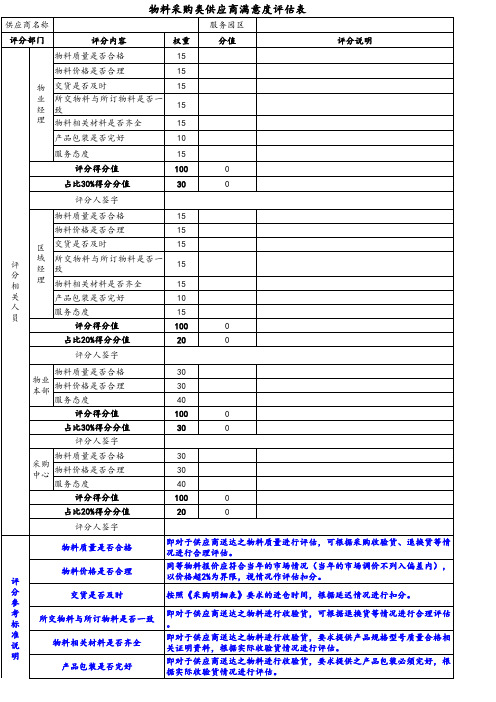
供应商名称 评分部门 评分内容 物料质量是否合格 物料价格是否合理 物 业 经 理 交货是否及时 所交物料与所订物料是否一 致 物料相关材料是否齐全 产品包装是否完好 服务态度 评分得分值 占比30%得分分值 评分人签字 物料质量是否合格 物料价格是否合理 区 域 经 理 交货是否及时 所交物料与所订物料是否一 致 物料相关材料是否齐全 产品包装是否完好 服务态度 评分得分值 占比20%得分分值 评分人签字 物料质量是否合格 物业 物料价格是否合理 本部 服务态度 评分得分值 占比30%得分分值 评分人签字 物料质量是否合格 采购 物料价格是否合理 中心 服务态度 评分得分值 占比20%得分分值 评分人签字 物料质量是否合格 物料价格是否合理 评 分 参 考 标 准 说 明 交货是否及时 所交物料与所订物料是否一致 物料相关材料是否齐全 产品包装是否完好 即对于供应商送达之物料质量进行评估,可根据采购收验货、退换货等情 况进行合理评估。 同等物料报价应符合当年的市场情况(当年的市场调价不列入偏差内), 以价格超2%为界限,视情况作评估扣分。 按照《采购明细表》要求的进仓时间,根据延迟情况进行扣分。 即对于供应商送达之物料进行收验货,可根据退换货等情况进行合理评估 。 即对于供应商送达之物料进行收验货,要求提供产品规格型号质量合格相 关证明资料,根据实际收验货情况进行评估。 即对于供应商送达之物料进行收验货,要求提供之产品包装必须完好,根 据实际收验货情况进行评估。 30 30 40 100 20 0 0 30 30 40 100 30 0 0 15 15 15 15 15 10 15 100 20 0 0 权重 15 15 15 15 15 10 15 100 30 0 0 服务园区 分值 评分说明
生产物料风险评估规范(含表格)

生产物料风险评估规范(ISO9001:2015)1目的:为正确识别我司所有原材料、零部件的环境管理物质风险等级,以利于生产过程对环境管理物质的进行有效的控制,特制定本办法作为物料/零件风险等级评估的指引。
2范围:本作业指引适用于我司的生产物料的风险评估。
3职责:样品承认工程师:由零件承认工程师主导依据风险等级结果来负责零件材料风险的评估。
采购:负责收集供货商的材质认证报告及材质承认书等资料。
品管:负责进行XRF进料检验抽检,协助样品承认工程师进行供应商HSF 评估。
4定义4.1材料风险:指原材料、零部件、组件所构成材料本身的风险。
4.2供应商风险:指提供物料的供应商的环境管理物质体系的综合水准,一般通过对供应商的评鉴结果及日常交货品质状况来决定。
4.3综合风险:指对以上风险的综合考量。
5作业内容5.1零件材料风险评估:高低1、焊锡类1、各大厂商所提供的IC类2、印刷电路板(PCB)及FPC 2、电阻、电容类3、油漆、油墨类3、各光电器件及敏感组件4、有表面电镀五金件(如管脚,铁框)4、各晶体管晶圆器件5、LED类5、ITO、CL、sensor6、包装材料7、其它各类辅料(LCD)8、其它各类辅料(LCM)9、液晶、PI、TOP、边框料等10、偏光片类11、胶类(保护膜、背胶等)5.2供应商等级风险评估:高中低2年内有HSF不符记录供应商设有物理或化学分析实验室的供应商大型跨国企业未曾建立任何质量管理体系的供应商2年之内未出现过HSF不符记录及没有产生批退且已经建立质量控制体系供应商行业垄断性质企业存在混合制程而未建立有害物质控制相关体系的供应商/ 贸易供应商外包供应商(我司提供全部物料则不计)/ 取得QC080000认证的供应商或知名品牌的绿色供应商,如SONY GP。
供应商风高中低高中低险等级物料风险高高高低低低等级综合评定高高低高中低未能通过现场审核供应商综合评定为高风险。
5.3风险等级的管理措施:5.3.1对风险物料制定[HSF物料抽样测试计划]送试验室进行测试。
物料评估表

(New Item)
电脑编 号:
(Part No.)
零件名 称:
(Part Name)
来件日 期:
(Sample Submission Date)
新零件 样板通 知书编
(Sample Submission No.)
囗代件:
(Replaced Item)
顏色/处 理:
(Colour/Treat ment)
囗要先
(Pilot Sample Test Requirement
)數量 (QTY):_
附注:
(Remark)
F-ENG-009 Rev.B
检查:
(Evaluated by)
分发部门:
(Distribution Dept)
囗R&D/工程部 囗生产部/制造
(正本请存放 R&D/工程部)
日期:
(Date)
零件类別:
(Type)
材料\规格:
(Material\Specification)
检查报告:
(Evaluation Comments)
机械性能:
(Mechanical Function)
电器性能:
(Electrical Function)
外观狀況:
(Cosmnetic)
其它:
(Other)
ed Item)
囗通过(OK) 囗通过(OK) 囗通过(OK)
囗不通过 囗不通过 囗不通过
囗不适 囗不适 囗不适
检查结果总结:
(Final Evaluation Results)
囗许可:
(Approved)
囗不合格:
(Non-compliance)