关于0.4mm pitch BGA印刷DOE工艺试验应用实例
0.4mm Pitch的BGA规范建议
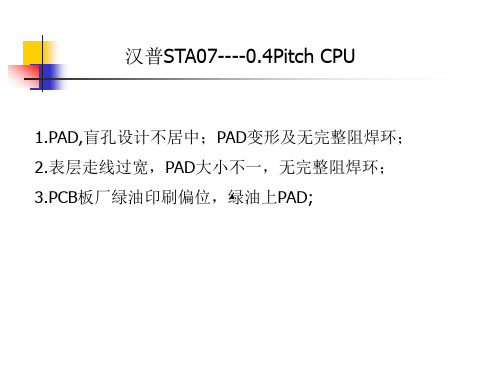
汉普STA07----0.4Pitch CPU
1.建议将盲孔置于PAD中心或完全距离PAD 2mil 以外,避免因焊盘变形或无完整阻焊环造成SMT 工艺不良 2.表层走线宽不大于0.2mm。对于大电流信号,在阻焊开窗外再放宽线宽;避免PAD变形,大 小不一无完整阻焊环造成SMT工艺不良;
汉普STA07----0.4Pitch CPU
。 建议BGA下方表层相同网络GND或Power引脚,用0.2mm走线和盲孔连接到内层的平面
表层走线过宽,PAD无阻焊环,PAD大小不一,直接造成SMT连锡,SMT制程抽检人员不知道 这个线路是否能连锡,当NG品处理
0.4mm Pitch的BGA规 GEBER资料设计:
汉普STA07----0.4Pitch CPU
1.PAD,盲孔设计不居中;PAD变形及无完整阻焊环; 2.表层走线过宽,PAD大小不一,无完整阻焊环; 3.PCB板厂绿油印刷偏位,绿油上PAD;
汉普STA07----0.4Pitch CPU
建议将盲孔置于PAD中心或完全距离PAD 2mil 以外,避免因焊盘变形或无完整阻焊环造成 SMT工艺不良
生产板管控范围:
防焊桥宽度= 0.075mm(3mil)
防焊桥宽度= 0.05-0.076mm(2 - 3mil)
防焊窗单边宽度= 0.038mm(1.5mil) 防焊窗单边宽度= 0 - 0.05mm(0 - 2mil)
防焊窗直径(a) = 0.325 mm(12.8mil) 防焊窗直径 (a)= 0.30 - 0.34mm(11.8-13.5mil)
开窗斜对角 = 0.418mm(16.5mil)
开窗斜对角 = 0.35 – 0.46mm(14 -18 mil)
PAD 直径 = 0.25mm(9.8mil)
0.4Pitch BGA PAD设计执行规范
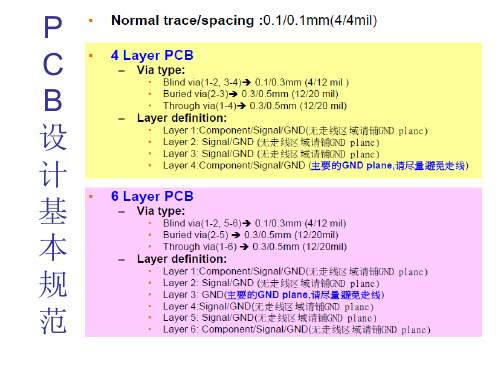
PCB设计
• • 过孔偏大或成阶梯状: 原理分析:PCB制作方式决定部分PCB工厂先化 学蚀刻,然后激光钻孔,化学蚀刻的孔径偏大。 (如Type 1),导致Via中存储较多空气,形成 焊点空洞,或锡膏流入Via,而少锡虚焊。 推荐PCB Vendor采用Type 3方法一次成孔。
•
规范-Pad尺寸设计
PCB设计规范总结
For Signal Pad: 建议制作直径为0.27mm的圆形焊盘,实际PCB成品精 度要求控制在+/-0.03mm内,这点要求保证,以求焊盘 大小规则均匀。 禁止在芯片表层使用铺铜设计。 为避免连锡的发生, GND间要求用8mil走线并打Blind Via连通到内层的GND Plane。 Pad与Pad之间必须留有阻焊桥3mil以上。 Solder Mask推荐尺寸0.37mm,形状采用方形倒角。 I/O Pad走线小于等于8mil。 Blind Via必须打在Pad正中心。
Mask设计
• • • Solder Mask设计规范: 原理分析:客户倾向于将一些电源Pin相连的走线加 宽,以增加通流能力。走线加宽导致不能制作阻焊, 加剧SMT连焊风险。(参考右下图尺寸建议) 要求Pad 一定要有阻焊环,而且Pad和Pad之间一定 要有Solder Dam。而且绿釉印刷不得覆盖到Pad。
P C B 设 计 基 本 规 范
铺铜
• 起因:GND Pin用大铜皮联通的,即表面铺铜。 • 不良现象:SMT连锡 • 原理分析:表面铺铜的焊盘无阻焊环,印刷时如果锡膏印 偏,多余的锡膏会流动到邻近焊盘,而引起连锡缺陷。 • 措施:索取正确封装库/或更改为网格走线。
盲孔设计
• •
•
Blind Via设计规范: 原理分析:客户为了Layout出线方便,将Via拉偏,这 相当于Pad增大,将减少Pad间距,增加连焊风险。 建议Blind Via下在Pad正中央, 可避免SMe设计规范:
《集成电路封装与测试》BGA的生产、应用及典型实例
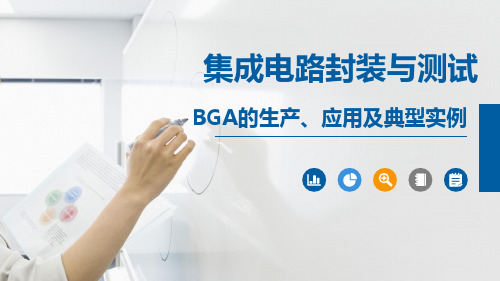
5焊球有效改善了共面性,有助于改善散热性
6适合MCM封装需要,实现高密度和高性能封装
02 BGA焊球分布形式
BGA焊球分布形式
6
03 BGA技术发展历史
BGA技术发展历史
8
BGA封装从20世纪90年代初期由Motorola和Citizen公司共 同开发。BGA的出现源于QFP封装的性能、成本要求:引脚数不断 增加、引脚间距越来越小,性价比越来越低。目前BGA已经作为重 要的封装形式应用于半导体行业。
集成电路封装与测试
BGA的生产、应用及典型实例
目录/Contents
01
BGA技术特点02来自BGA焊球分布形式03
BGA技术发展历史
01 BGA技术特点
BGA技术特点
4
1成品率高、可将窄间距QFP焊点失效率降低两个数量级 2芯片引脚间距大-贴装工艺和精度 3显著增加了引出端子数与本体尺寸比-互连密度高 4BGA引脚短-电性能好、牢固-不易变形
doe实验案例
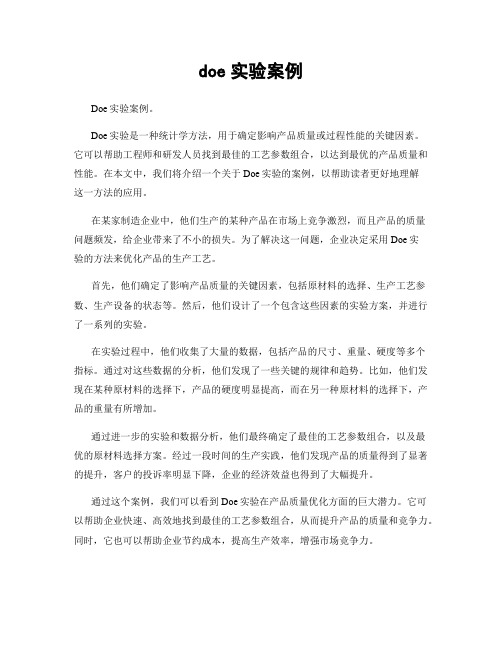
doe实验案例Doe实验案例。
Doe实验是一种统计学方法,用于确定影响产品质量或过程性能的关键因素。
它可以帮助工程师和研发人员找到最佳的工艺参数组合,以达到最优的产品质量和性能。
在本文中,我们将介绍一个关于Doe实验的案例,以帮助读者更好地理解这一方法的应用。
在某家制造企业中,他们生产的某种产品在市场上竞争激烈,而且产品的质量问题频发,给企业带来了不小的损失。
为了解决这一问题,企业决定采用Doe实验的方法来优化产品的生产工艺。
首先,他们确定了影响产品质量的关键因素,包括原材料的选择、生产工艺参数、生产设备的状态等。
然后,他们设计了一个包含这些因素的实验方案,并进行了一系列的实验。
在实验过程中,他们收集了大量的数据,包括产品的尺寸、重量、硬度等多个指标。
通过对这些数据的分析,他们发现了一些关键的规律和趋势。
比如,他们发现在某种原材料的选择下,产品的硬度明显提高,而在另一种原材料的选择下,产品的重量有所增加。
通过进一步的实验和数据分析,他们最终确定了最佳的工艺参数组合,以及最优的原材料选择方案。
经过一段时间的生产实践,他们发现产品的质量得到了显著的提升,客户的投诉率明显下降,企业的经济效益也得到了大幅提升。
通过这个案例,我们可以看到Doe实验在产品质量优化方面的巨大潜力。
它可以帮助企业快速、高效地找到最佳的工艺参数组合,从而提升产品的质量和竞争力。
同时,它也可以帮助企业节约成本,提高生产效率,增强市场竞争力。
总之,Doe实验是一个非常有效的工具,可以帮助企业解决产品质量和生产工艺方面的难题。
希望通过本文的案例介绍,读者能对Doe实验有一个更加深入的理解,并在实际工作中加以应用,从而取得更好的效果。
BGA焊点纳米压痕实验有限元模拟分析
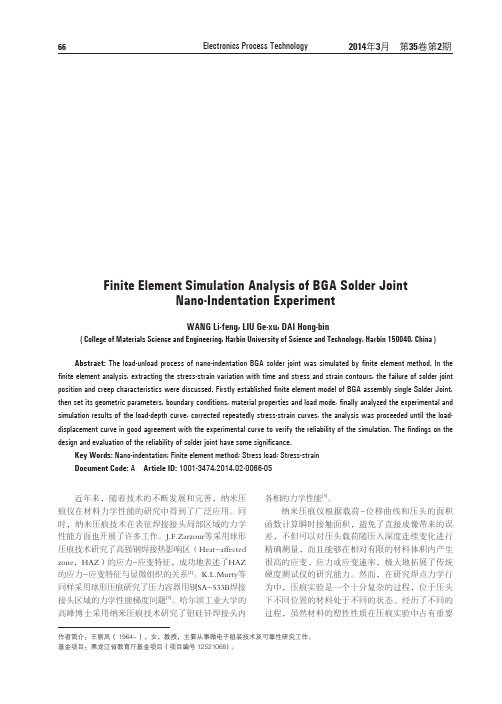
2014年3月
载荷F /mN
束,如图2所示。
图2 单个BGA焊点有限元模拟的边界条件
2.2 载荷加载形式 计算过程为非线性静力加载过程,考虑几何大
变形。载荷有两种方式:力与强制位移。经过计算考 证,力加载与强制位移加载得到的载荷-位移曲线是 完全一致的,本文计算中采用控制加载载荷的方法 进行数值模拟。根据纳米压痕实验一次加载-卸载方 式模拟BGA焊点纳米压痕过程,压头的运动由边界 载荷控制,加卸载过程中载荷随时间的变化关系如 图3所示。
电子工艺技术
66
Electronics Process Technology
2014年3月 第35卷第2期
BGA焊点纳米压痕实验有限元模拟分析
王丽凤, 刘阁旭, 戴洪斌
(哈尔滨理工大学材料科学与工程学院,黑龙江 哈尔滨 150040)
摘 要:采用有限元方法模拟了BGA焊点的纳米压痕实验的加、卸载过程,并根据得出的应力应变分布云 图,通过分析从各关键部位提取的应力应变随时间变化的关系,对焊点发生失效的位置及蠕变特征进行了讨 论。首先建立BGA单个焊点的模型,设定其几何参数、边界条件、材料特性与加载方式,然后利用有限元分析 工具MARC进行计算与标准试样实验结果相比较,通过反复修正应力-应变关系曲线,直至分析所得载荷-位移 曲线与试验曲线很好地吻合,证实了模拟的可靠性,研究结果对焊点的可靠性评估有一定的指导意义。
各相的力学性能[3]。 纳米压痕仪根据载荷-位移曲线和压头的面积
函数计算瞬时接触面积,避免了直接成像带来的误 差,不但可以对压头载荷随压入深度连续变化进行 精确测量,而且能够在相对有限的材料体积内产生 很高的应变、应力或应变速率,极大地拓展了传统 硬度测试仪的研究能力。然而,在研究焊点力学行 为中,压痕实验是一个十分复杂的过程,位于压头 下不同位置的材料处于不同的状态、经历了不同的 过程,虽然材料的塑性性质在压痕实验中占有重要
DOE在SMT丝网印刷中质量改进的应用
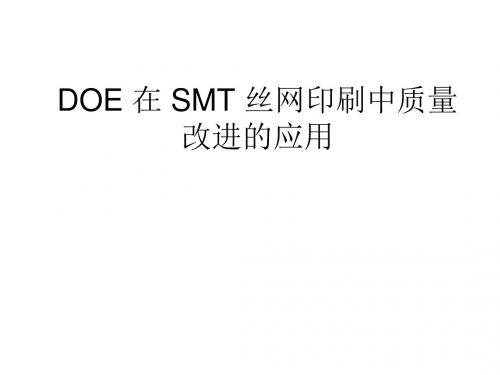
验证参数的准确性
我们把正常生产线的刮刀速度、刮刀压力、脱模状态调 整成我们试验得出的结论,其他都保持不变,最后对SMT 的良率进行统计,如表 6。
总生产数量:710pcs;不良数量:3pcs;良率:>99% (目标良率)。因此,从以上数据我们可以看出,通过 DOE 得 出的印刷参数值明显改善了 PCB板的生产良率,达到了预期的 效果。
试验的原因与意义
焊膏换成了无铅焊膏:
由于使用的无铅焊膏在熔点、吃锡性、印刷出来的外观 上与传统的焊膏有一定的差别,而焊膏印刷又是 SMT 工艺 的第一道工序,焊膏印刷的不良将直接影响后序工艺的进展 情况,这是影响 SMT 总的良率的主要原因之一。因此,通 过结合供应商提供的焊膏最优使用范围以及在实际生产过程 中影响良率的主要不良现象的真因,对焊膏印刷进行了正交 试验。
DOE 在 SMT 丝网印刷中质量 改进的应用
丝网印刷工作原理
焊膏在刮板前滚动前进 产生将焊膏注入漏孔的压力
丝网印刷工作原理
切变力使焊膏注入漏孔
Hale Waihona Puke 焊膏释放(脱模)影响印刷质量的工艺参数
• 模板的质量 • 焊膏的质量 • 印刷工艺参数 • 设备精度 • 环境温度、湿度以及环境卫生
影响印刷质量的工艺参数
供应商提供刮刀压力的最优范围为6- 12kg,本试验中 设计该因子采用 6- 12kg。
正交试验设计
因为本次试验取得是 3 个因子 2 个水平,而且取值范围 比较宽,故在 2 个数值因子中加入了 3 个中心点,因此采用 8(23) +2×3 正交表配置如下表:
试验数据
评价 SMT 功能性能的好坏,首先考虑到的是印刷后成 型效果的好坏。试验也是以这个为依据的,不过考虑到实际 生产中对焊膏厚度的控制,故把印刷后的成型效果和锡膏厚 度共同作为试验结果。
BGA的返修及植球工艺简介

BGA的返修及植球工艺简介一:普通SMD的返修普通SMD返修系统的原理:采用热气流聚集到表面组装器件(SMD)的引脚和焊盘上,使焊点融化或使焊膏回流,以完成拆卸和焊接功能。
不同厂家返修系统的相异之处主要在于加热源不同,或热气流方式不同,有的喷嘴使热风在SMD 的上方。
从保护器件的角度考虑,应选择气流在PCB四周流动比较好,为防止PCB翘曲还要选择具有对PCB进行预热功能的返修系统。
二:BGA的返修使用HT996进行BGA的返修步骤:1:拆卸BGA把用烙铁将PCB焊盘残留的焊锡清理干净、平整,可采用拆焊编织带和扁铲形烙铁头进行清理,操作时注意不要损坏焊盘和阻焊膜。
用专用清洗剂将助焊剂残留物清洗干净。
2:去潮处理由于PBGA对潮气敏感,因此在组装之前要检查器件是否受潮,对受潮的器件进行去潮处理。
3:印刷焊膏因为表面组装板上已经装有其他元器件,因此必须采用BGA专用小模板,模板厚度与开口尺寸要根据球径和球距确定,印刷完毕后必须检查印刷质量,如不合格,必须将PCB清洗干净并凉干后重新印刷。
对于球距为0.4mm以下的CSP,可以不印焊膏,因此不需要加工返修用的模板,直接在PCB的焊盘上涂刷膏状助焊剂。
需要拆元件的PCB 放到焊炉里,按下再流焊键,等机器按设定的程序走完,在温度最高时按下进出键,用真空吸笔取下要拆下的元件,PCB板冷却即可。
4:清洗焊盘用烙铁将PCB焊盘残留的焊锡清理干净、平整,可采用拆焊编制带和扁铲形烙铁头进行清理,操作时注意不要损坏焊盘和阻焊膜。
5:去潮处理由于PBGA对潮气敏感,因此在组装之前要检查器件是否受潮,对受潮的器件进行去潮处理。
6:印刷焊膏因为表面组装板上已经装有其他元器件,因此必须采用BGA专用小模板,模板厚度与开口尺寸要根据球径和球距确定,印刷完毕后必须检查印刷质量,如不合格,必须将PCB清洗干净并凉干后重新印刷。
对于球距为0.4mm以下的CSP,可以不印焊膏,因此不需要加工返修用的模板,直接在PCB的焊盘上涂刷膏状助焊剂。
BGA基板植球解决方案

BGA基板植球技术解决方案一、BGA封装技术简介BGA(Ball Grid Array球栅阵列)封装出现于上世纪90年代初期,现已发展成为一项较为成熟的高密度封装技术。
BGA封装主要适用于PC芯片组、微处理器/控制器、ASIC、门阵、存储器、DSP、PDA、PLD等器件的封装,并朝着细节距、高I/O端数方向发展。
由于BGA/CSP封装的焊料球是以阵列形式排布在封装基片下面,因而可极大地提高器件的I/O 数,缩小封装体尺寸,节省组装的占位空间。
通常,在引线数相同的情况下,封装体尺寸可减小30%以上。
下图是一种典型的BGA封装芯片:下图显示了BGA封装与传统封装形式的区别:随着我国半导体制造和封装水平的快速提高,在国际IC高端封装领域占主导地位的BGA/CSP封装技术正逐渐开始被国内厂商使用。
目前已有此类生产线在大陆封测厂运转,并有多家厂商正在调研设备性能和制程工艺。
BGA基板植球机是建立国产化BGA/CSP封装生产示范线所必须攻克的关键技术之一。
二、BGA基板植球机简介BGA基板植球机动作流程如下:助焊剂针转写方式助焊剂印刷方式BGA基板植球机用图像处理技术定位基板,用针转写或印刷的方式涂助焊剂,然后把锡球固定在基板的相应位置。
植球后,用画像处理系统检查基板,把不合格的基板放进废料盒,合格品进入下一道工序——回流炉。
BGA基板植球机可以分为基板上料装置、焊球供给、针转写/印刷、植球和基板传送部分等子系统。
三、上海微松公司BGA基板植球机产品系列1. 全自动BGA基板植球机主要技术指标:2. 半自动BGA基板植球机半自动BGA基板植球机,采用手工上料方式,图像处理系统辅助定位,用印刷方式实现助焊剂涂布,人工植球。
该机型具有很高的性价比。
主要技术指标3. 手动BGA基板植球机特征:定位精准可靠,手动基板植球机采用机械定位方式,定位准确,植球成功率高 对应多种品种,对应不同的品种的基板,只要更换治具即可,操作方便双刮刀独立自动运行且有压力调节系统,有效的控制刮胶量,保证植球成功率 更换新品种时所用植球治具价格低廉,大幅降低成本4. BGA基板植球治具四、上海微松BGA基板植球机的优势微松公司的BGA基板植球设备的主要创新点如下:(1)采取针转写方式有效克服基板弯曲的问题。
DOE实验设计案例

以随机顺序抽取和测试的24个数据如下表 以随机顺序抽取和测试的24个数据如下表
木材含量 1 5% 10% 15% 20% 7 12 14 19 2 8 17 18 25 观测值 3 15 13 19 23 4 11 18 17 22 5 9 19 16 17 6 10 15 18 21
如果我们要提高其纸袋的抗张强度性能, 如果我们要提高其纸袋的抗张强度性能, 抗张强度性能 就要找不同的工艺参数, 就要找不同的工艺参数,但工艺参数选 择是个非常复杂问题。 择是个非常复杂问题。我们可以考虑可 能影响抗张强度的4个因子 个因子, 能影响抗张强度的 个因子,确认哪些因 子的影响确实是显著的, 子的影响确实是显著的,进而确定出最 佳的工艺条件。 佳的工艺条件。
DOE实验设计 实验设计源自主讲:聂微DOE实验设计案例 实验设计案例
某个造纸厂想改进一种纸袋的抗张 抗张强度跟纸浆中一种 强度,他们认为抗张强度 强度,他们认为抗张强度跟纸浆中一种 木材含量有关,现行规范含量为10%, 木材含量有关,现行规范含量为 , 平均抗张强度为15psi. 平均抗张强度为 他们进行了四种水平的含量因子研 究:5%、10%、15%、20%,每个水平 、 、 、 , 取得了6个数据 个数据。 取得了 个数据。
Altium官方讲解极小BGA器件(0.4mm pitch)的布局布线设计

Altium官方讲解极小BGA器件(0.4mm pitch)的布局布线设计[导读]BGA是PCB上常用的元器件,通常80﹪的高频信号及特殊信号将会由这类型的封装Footprint内拉出。
因此,如何处理BGA 器件的走线,对重要信号会有很大的影响。
SMT(Surface Mount Technology 表面安装)技术顺应了智能电子产品小型化,轻型化的发展潮流,为实现电子产品的轻、薄、短、小打下了基础。
SMT技术在90年代也走向成熟的阶段。
但随着电子产品向便携式/小型化、网络化方向的迅速发展,对电子组装技术提出了更高的要求,其中BGA(Ball Grid Array 球栅阵列封装)就是一项已经进入实用化阶段的高密度组装技术。
BGA技术的研究始于60年代,最早被美国IBM公司采用,但一直到90年代初,BGA 才真正进入实用化的阶段。
由于之前流行的类似QFP封装的高密管脚器件,其精细间距的局限性在于细引线易弯曲、质脆而易断,对于引线间的共平面度和贴装精度的要求很高。
BGA技术采用的是一种全新的设计思维方式,它采用将圆型或者柱状点隐藏在封装下面的结构,引线间距大、引线长度短。
这样,BGA就消除了精细间距器件中由于引线问题而引起的共平面度和翘曲的缺陷。
BGA是PCB上常用的元器件,通常80﹪的高频信号及特殊信号将会由这类型的封装Footprint内拉出。
因此,如何处理BGA 器件的走线,对重要信号会有很大的影响。
通常的BGA器件如何走线?普通的BGA器件在布线时,一般步骤如下:•先根据BGA器件焊盘数量确定需要几层板,进行叠层设计。
•然后对主器件BGA进行扇出(即从焊盘引出一小段线,然后在线的末端放置一个过孔,以此过孔到达另一层)。
•再然后从过孔处逃逸式布线到器件的边缘,通过可用的层来进行扇出,一直到所有的焊盘都逃逸式布线完毕。
扇出及逃逸时布线是根据适用的设计规则来进行的。
包括扇出控制 Fanout Control 规则,布线宽度 Routing Width 规则,布线过孔方式 Routing Via Style 规则,布线层 Routing Layers 规则和电气间距 Electrical Clearance 规则。
PCB测试、工艺及技术方法详解
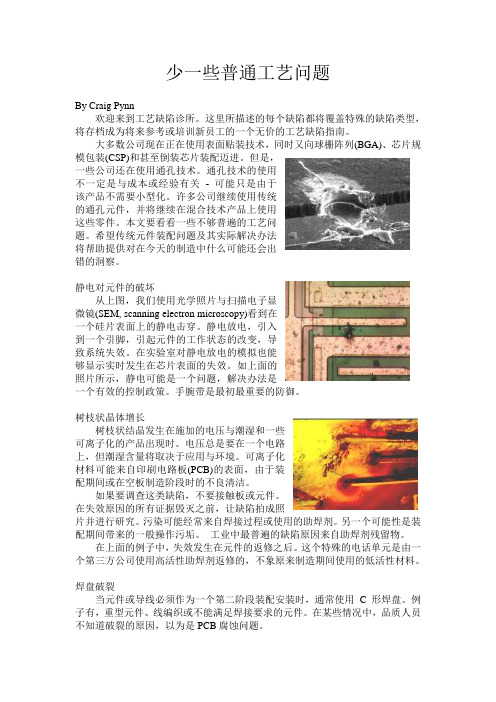
少一些普通工艺问题By Craig Pynn欢迎来到工艺缺陷诊所。
这里所描述的每个缺陷都将覆盖特殊的缺陷类型,将存档成为将来参考或培训新员工的一个无价的工艺缺陷指南。
大多数公司现在正在使用表面贴装技术,同时又向球栅阵列(BGA)、芯片规模包装(CSP)和甚至倒装芯片装配迈进。
但是,一些公司还在使用通孔技术。
通孔技术的使用不一定是与成本或经验有关- 可能只是由于该产品不需要小型化。
许多公司继续使用传统的通孔元件,并将继续在混合技术产品上使用这些零件。
本文要看看一些不够普遍的工艺问题。
希望传统元件装配问题及其实际解决办法将帮助提供对在今天的制造中什么可能还会出错的洞察。
静电对元件的破坏从上图,我们使用光学照片与扫描电子显微镜(SEM, scanning electron microscopy)看到在一个硅片表面上的静电击穿。
静电放电,引入到一个引脚,引起元件的工作状态的改变,导致系统失效。
在实验室对静电放电的模拟也能够显示实时发生在芯片表面的失效。
如上面的照片所示,静电可能是一个问题,解决办法是一个有效的控制政策。
手腕带是最初最重要的防御。
树枝状晶体增长树枝状结晶发生在施加的电压与潮湿和一些可离子化的产品出现时。
电压总是要在一个电路上,但潮湿含量将取决于应用与环境。
可离子化材料可能来自印刷电路板(PCB)的表面,由于装配期间或在空板制造阶段时的不良清洁。
如果要调查这类缺陷,不要接触板或元件。
在失效原因的所有证据毁灭之前,让缺陷拍成照片并进行研究。
污染可能经常来自焊接过程或使用的助焊剂。
另一个可能性是装配期间带来的一般操作污垢。
工业中最普遍的缺陷原因来自助焊剂残留物。
在上面的例子中,失效发生在元件的返修之后。
这个特殊的电话单元是由一个第三方公司使用高活性助焊剂返修的,不象原来制造期间使用的低活性材料。
焊盘破裂当元件或导线必须作为一个第二阶段装配安装时,通常使用 C 形焊盘。
例子有,重型元件、线编织或不能满足焊接要求的元件。
SMT实用工艺与制程
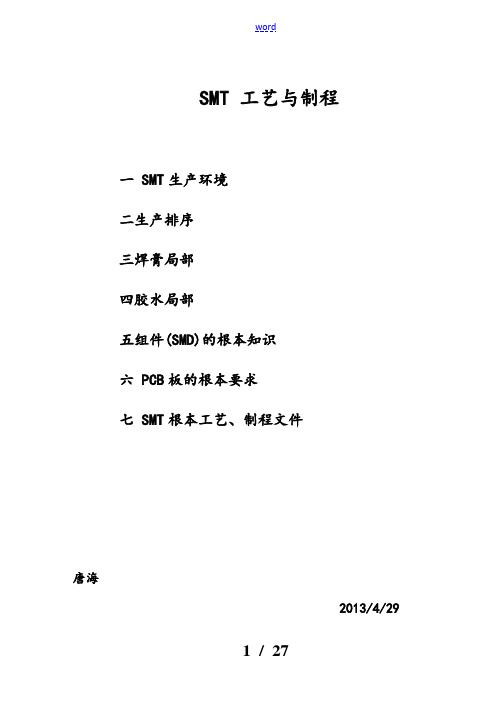
SMT 工艺与制程一 SMT生产环境二生产排序三焊膏局部四胶水局部五组件(SMD)的根本知识六 PCB板的根本要求七 SMT根本工艺、制程文件唐海2013/4/29一 SMT生产环境1.无尘:SMT设备气动部件很多,清洁的环境有利于气路的顺畅,与稳定运行; SMT贴片设备的组件认识系统主要为相机识别或激光识别,它们镜头是否清洁无尘直接影响到设备的装着率和贴片精度;SMT设备的功率电器部件较多,无尘与良好的通风环境能保证其寿命;无尘能保证PCB板的清洁,保证印刷质量与点胶质量;无尘的其体等级要求根据生产品的类型与精度要求来确定。
2.温度:( 20---28℃ )设备的机械、电器部件在高速、长时间运转下都会发热, 要较低的环境温度保证其正常运行;在此温度X围内能保证锡膏的性能与点胶的质量;SMT 的作业人员为防静电而穿了防静电衣帽,需要适宜的温度环境.3.湿度:( 40---70%RH ) 湿度对静电的影响非常大;湿度对锡膏的印刷有很大影响;湿度对设备机械、电器部件有影响.4.防静电: A.静电物质由于受外力的作用,会产生电子的得失,物质中电子的得失破坏了电平衡,产生了静电.静电能击穿很多电子器件,是IC等电子器件的头号杀手.B.影响静电的产生因素●物质的材料特性,有的容易产生静电,有的不容易产生静电;●物质摩擦的作用力的大小与方向;●环境湿度会影响静电产生的大小,越枯燥,越易产生静电;●环境空间的交变电场,磁场也是产生静电的重要来源.C.静电的防护●所有元器件的操作都必需在静电安全工作台上进展;● SMD采用防静电包装,SMD物料仓要有更严的防静电保护;● SMT的作业人员必须有静电防护,穿防静电工作服或戴防静电手腕带,接触芯片时防止接触它的引脚或端子,根据要求再作静电防护;● SMT的各种设备必须有良好的防静电保护,做防静电油漆,加防静电皮,和设备良好的接地;●控制好SMT生产环境的湿度,工作场地做防静电油漆,加防静电地皮;● PCBA的存放与搬运也要注意防静电,用防静电胶盆等来装PCB .5.通风:SMT回流焊会排出很多废气,需要良好的通风保持生产环境.6.照明:方便目检员检测半成品,作业人员观察与作业.7.振动:小的振动有利于保护贴片精度,设备的正常使用.8.地板的承载能力:SMT设备一般都有较大振动,如果生产车间不在一楼应考虑楼板的承受能力和防止共振.9.设备的布局:主要考虑设备的振动是否会相互影响,是否方便作业与正体的美观,产品的升级伴随的辅助设备的增加.二生产排序1.先生产锡膏面,再生产胶水面2.先生产少料面,再生产多料面3.PCB 胶水贴片回焊炉目检 ICT IPQC4.PCB印刷 IPQC抽检贴片 IPQC抽检回焊炉IPQC ICT 目检三焊膏局部有铅焊膏有铅焊膏的组成与其对性能的影响1. 锡铅合金锡球( Solder Ball )●比重 85---90%:合金锡球比重上下将会影响焊点锡量的多少与爬升性,因为焊接时锡球合金不会挥发,一样体积的锡膏膜,锡铅合金球的比重越高焊点就会越饱满。
- 1、下载文档前请自行甄别文档内容的完整性,平台不提供额外的编辑、内容补充、找答案等附加服务。
- 2、"仅部分预览"的文档,不可在线预览部分如存在完整性等问题,可反馈申请退款(可完整预览的文档不适用该条件!)。
- 3、如文档侵犯您的权益,请联系客服反馈,我们会尽快为您处理(人工客服工作时间:9:00-18:30)。
关于0.4 印刷工艺试验应用实例
锡膏印刷工艺介绍:
焊膏和贴片胶都是触变流体,具有粘性,当刮刀以一定速度和角度向前移动时,对焊膏产生一定的压力,推动焊膏在刮板前滚动,具体实现情况见图15-2产生将焊膏注入网孔或漏孔所需的压力(见图15-4),焊膏的粘性摩擦力使焊膏在刮板与网板交接处产生切变,切变力使焊膏的粘性下降(见图15-5),使焊膏
顺利地注入网孔或漏孔最后进行脱模操作,板被送出印刷机。
刮刀的推动力可分解为:①推动焊膏前进分力;②将焊膏注入漏孔的压力。
图15-2 焊膏在刮板前滚动前进图15-3 产生将焊膏注入漏孔的压力图15-4 焊膏释放(脱模)影响印刷质量的工艺参数:
(1)首先是模板质量模板印刷是接触印刷,因此模板厚度与开口尺寸确定了焊膏的印刷量,焊膏量过多会产生桥接,焊膏量过少会产生焊锡不足或虚焊。
模板开口形状以及开口是否光滑也会影响脱模质量。
(2)其次是焊膏质量,焊膏的黏度印刷性(滚动性转移性)触变性常温下的使用寿命等都会影响印刷质量。
(3)印刷工艺参数刮刀速度刮刀压力刮刀与网板的角度以及焊膏的黏度之间都存在一定的制约关系,因此只有正确控制这些参数,才能保证焊膏的印刷质量。
(4)设备精度方面在印刷高密度窄间距产品时,印刷机的印刷精度和重复印刷精度也会起一定的作用。
(5)环境温度湿度以及环境卫生。
温度过高会降低焊膏黏度,湿度过大时焊膏会吸收空气中的水分,湿度过小时会加速焊膏中溶剂的挥发,环境中灰尘混入焊膏中会使焊点产生针孔。
图15-5 用鱼骨图简单而直观的分析了影响印刷质量的部分因素。
图15-4 焊膏印刷的鱼骨分析示意
试验设计的应用:
由于使用的无铅焊膏在熔点、吃锡性、印刷出来的外观上与传统的焊膏有一定的差别,而焊膏印刷又是工艺的第一道工序,焊膏印刷的不良将直接影响后序工艺的进展情况,这是影响总的良率的主要原因之一。
因此,通过结合供应商提供的焊膏最优使用范围,以及在实际生产过程中影响良率的主要不良现象的真因,对焊膏印刷进行了正交试验。
印刷工艺参数的选择:
在正交试验优化焊膏印刷中,我们选定刮刀速度、刮刀压力及脱模状况这三个印刷参数为试验因子。
(1)刮刀速度:一般而言刮刀速度慢可得到较好的印刷品质,但可能导致焊膏形状模糊(),同时也影响生产效率.印刷速度过快,则可能因焊膏无足够时间填入钢模板孔洞,造成焊膏量不足。
因此,在焊膏能够保持正常滚动状态下,尽可能提高速度,并配合刮刀压力调整,以达良好印刷质量根据供应商提供的最优范围为60-150。
本试验设计该因子为60-120水平值。
(2)刮刀压力:刮刀压力过高会导致钢模板缝孔内的焊膏被拖出而造成缺焊,压力过低则导致焊膏印刷不完全目前一般采用左右刮刀压力根据供应商提供的最优范围为,本试验中设计该因子采用6-12
(3)脱模状态:指焊膏印刷后钢模板底面与的分离
上述详细的参数值和水平见下表15-1
表15-1
正交试验:
(1)正交试验设计:
因为本次试验取得是3 个因子2 个水平,而且取值范围比较宽,故在个数值因
子中加入了3个中心点,因此采用L8(23)+2*3正交表配置。
如表15-2
表15-2 正交试验表
(2)试验数据
评价功能性能的好坏,首先考虑到的是印刷后成型效果的好坏。
试验也是以这个为依据的,不过考虑到实际生产中对焊膏厚度的控制,故把印刷后的成型体积和锡膏厚度共同作为试验结果。
按照表15-2的正交表内容进行试验,锡膏印刷体
积按照钢网开孔体积50150%,印刷厚度按照钢网厚度80120%标准,超出此标准判定。
印刷完成后根据检测结果,统计锡膏印刷不良点数。
同一焊膏印刷参数印刷出来的成型效果进行重复3次试验。
焊膏印刷出来的成型效果即焊膏印刷不良数如表15-3所示:
表15-3 检测印刷不良的具体数值。
锡膏厚度的测量结果如下表15-4所示:
表15-4:锡膏厚度的测量值
数据统计与分析:
采用软件分析,因子分析步骤:
(1)通过置信水平的设置,可以观察出主要影响因素和次要影响因素,其中包
括一些交互影响
(2)在第一步的基础上,剔除次要影响因素,对主要影响因素进行第二次分析,将更加明显的看到个各因素的影响差别
(3)对交互影响进行分析,通过对交互影响的分析,可以直观的观察到各因素的相互关系,对最优参数的选择有了一个趋势概念
(4)通过建立最优相应模型,对最优参数进行定量选择
从锡膏的成形效果结果中,可以看出置信系数为9.5时,印刷参数的选择并不明
显。
从锡膏厚度的分析图来看,可以看出刮刀速度、脱模状态对结果的影响显著。
故剔除不显著因素,进行再次分析。
图15-6:成型效果的影响因素排列图图15-7:锡膏厚度的影响因素排列图
图15-8:锡膏厚度主要影响因素的排列图图15-9:锡膏厚度中的交互影响因素排列图
从图15-9 中,可以明显的看出刮刀速度与脱模状态之间的相互关系。
要想定量的描述他们之间的关系,选择出最优的工艺参数,图15-10 的最优参数模型即可得出。
图15-10:最优参数选择示意图
可见,速度=60,压力=12 为最优参数。
此时,成型不良数为7.33,而锡膏厚度为0.136。
(5)验证最优参数。