汽车制动器性能控制方法
制动系统的设计与性能优化

制动系统的设计与性能优化制动系统是车辆中至关重要的部分,它直接影响到行车的安全性和稳定性。
良好的制动系统设计以及性能优化是保障车辆和乘客安全的关键。
本文将讨论制动系统的设计原理以及性能优化策略,并探讨如何通过技术手段提升制动系统的性能。
一、制动系统的设计原理制动系统主要由制动器、制动片、制动液、制动器操控装置以及制动辅助装置等组成。
其工作原理是通过制动器施加一定的力矩使制动片与制动盘或制动鼓相互摩擦,从而转化为摩擦力以达到制动车辆的目的。
1. 制动器的选择原则制动器根据制动能力的不同分为盘式制动器和鼓式制动器。
盘式制动器由刹车盘和刹车钳组成,优点是散热性好、制动效果稳定,因此在高速行驶中有更好的制动性能;鼓式制动器由刹车鼓、制动片和制动轮筒组成,适用于低速行驶且制动次数相对较少的情况。
2. 制动片的材料选择制动片主要材料包括无石棉有机材料、半金属材料和陶瓷材料等。
不同材料具有不同的制动性能,如无石棉有机材料制动片具有制动平稳、噪音低等优点,而陶瓷材料则在制动性能和散热性上具有优势。
因此,在设计制动系统时需要根据车辆使用情况和需求选择合适的制动片材料。
3. 制动液的选用制动液作为传递压力的介质,其性能直接影响到制动系统的工作效果。
常见的制动液有DOT3、DOT4和DOT5等不同规格的液体。
制动液的选择要考虑到制动系统的工作温度范围、湿润点和抗氧化性能等因素。
二、制动系统的性能优化策略为了进一步提升制动系统的性能,以下几个方面可以进行优化:1. 制动系统的散热设计在高速行驶或制动频繁的情况下,制动系统会产生大量的热量,若无法及时散热,会影响制动效果甚至导致制动衰退。
因此,通过合理的散热设计,如增加散热器的面积、采用散热材料等措施,可以提高制动系统的稳定性和耐用性。
2. 制动系统的力矩分配制动系统的力矩分配是指在不同工况下各个车轮的制动效果。
通过调整制动力矩分配,可以使车辆制动时更加平衡稳定,减少车辆的侧滑和翻滚现象,提高行车的稳定性。
汽车制动优化控制方法探析

汽车制动优化控制方法探析汽车制动控制是汽车行驶过程中安全保障的重要措施之一,任何一台汽车的制动系统在设计时,都要考虑到行驶速度、路面状况、驾驶者经验等因素。
然而,在实际驾驶中难免会出现由于路况、天气、驾驶者的驾驶习惯等原因导致制动失控的情况。
因此,汽车制动优化控制方法的研究具有现实意义。
一、现有制动控制方法1.防抱死制动系统(ABS)ABS是一种针对滑动路面(如雨雪天气)的特殊制动系统,它能够自动调节刹车气压,防止车轮滑动,保持轮胎和地面之间的摩擦力,防止汽车失控。
ABS系统通过在车轮与车轮之间切换刹车压力,调整每个车轮的制动力,以避免车轮抱死。
2.电子制动力控制系统(EBD)EBD系统是基于ABS系统的升级版,它可以根据车辆负荷、载荷、惯性等因素精准调整每个车轮的制动力,进一步提高制动安全性。
在紧急制动情况下,EBD可以自动增加制动补偿力,防止轮胎抱死,提高刹车效率和安全性。
3.牵制力控制系统(TCS)TCS系统是一种基于水平和侧向牵引的系统,它可以通过调整各个车轮的制动力来控制车辆的进一步行驶。
当车轮失去牵引力时,TCS可以通过追加制动力来恢复牵引力,防止车辆滑动或打滑,提高驾驶的安全性。
车辆安全是制动控制技术研究的重点,目前研究的方向主要有以下几个方面:1.提高刹车性能制动性能是制动控制的核心,刹车性能包括制动距离、制动效率、刹车时间等。
最新研究表明,增加制动器的计算机控制能有效地提高刹车性能,尤其是在高速行驶时,精准的制动控制对于避免车祸具有重要作用。
2.减少制动噪音当前,制动系统产生的噪音还是一个普遍存在的问题。
尤其在城市中,制动噪音常常影响到居民的生活。
因此,制动优化控制方法的研究也包括减少制动噪音的研究,例如采用优化的制动器极化方法、仿生智能技术等。
3.智能化制动控制智能化制动控制是目前研究中的另一个重点,该技术可以使用智能传感器在车辆行驶的同时获取实时数据,以实现精准的制动控制。
车辆制动系统中的制动力优化与控制策略
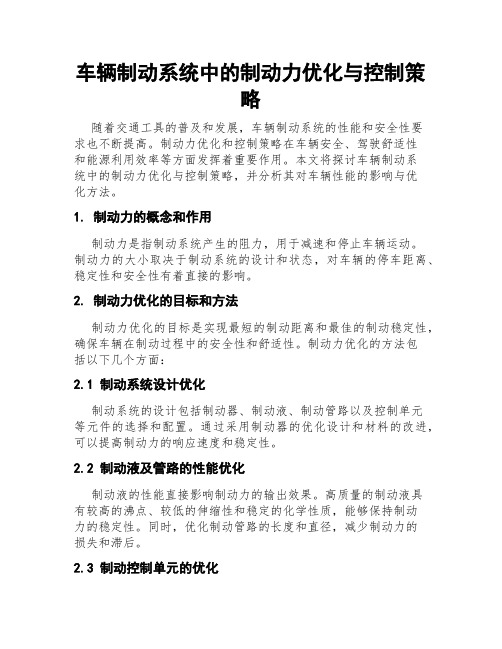
车辆制动系统中的制动力优化与控制策略随着交通工具的普及和发展,车辆制动系统的性能和安全性要求也不断提高。
制动力优化和控制策略在车辆安全、驾驶舒适性和能源利用效率等方面发挥着重要作用。
本文将探讨车辆制动系统中的制动力优化与控制策略,并分析其对车辆性能的影响与优化方法。
1. 制动力的概念和作用制动力是指制动系统产生的阻力,用于减速和停止车辆运动。
制动力的大小取决于制动系统的设计和状态,对车辆的停车距离、稳定性和安全性有着直接的影响。
2. 制动力优化的目标和方法制动力优化的目标是实现最短的制动距离和最佳的制动稳定性,确保车辆在制动过程中的安全性和舒适性。
制动力优化的方法包括以下几个方面:2.1 制动系统设计优化制动系统的设计包括制动器、制动液、制动管路以及控制单元等元件的选择和配置。
通过采用制动器的优化设计和材料的改进,可以提高制动力的响应速度和稳定性。
2.2 制动液及管路的性能优化制动液的性能直接影响制动力的输出效果。
高质量的制动液具有较高的沸点、较低的伸缩性和稳定的化学性质,能够保持制动力的稳定性。
同时,优化制动管路的长度和直径,减少制动力的损失和滞后。
2.3 制动控制单元的优化制动控制单元是车辆制动系统的核心部件,通过优化其算法和响应速度,可以提高制动力的控制精度和稳定性。
当前,许多汽车制造商还采用了电子稳定控制系统(ESP)和自适应制动系统(ABS)等辅助装置,进一步提升制动力的优化效果。
3. 制动力控制策略的影响因素制动力控制策略的选择和设计与多个因素密切相关,包括车辆动力性能、制动器磨损、路面情况以及驾驶者的需求等。
3.1 车辆动力性能车辆的功率、质量和轮胎的抓地力等动力性能参数会影响制动力的要求和选择。
高功率车辆需要更强大的制动力来实现快速的减速和停车,而质量大的车辆则需要更大的制动力来克服惯性。
3.2 制动器磨损制动器磨损会导致制动力的减小和不稳定性的增加。
因此,制动力控制策略需要考虑制动器磨损的情况,并及时调整制动力的输出,以保持制动系统的正常工作。
汽车制动系统故障诊断及性能优化策略

AUTO AFTERMARKET | 汽车后市场汽车制动系统故障诊断及性能优化策略诸葛桥忠广西城市职业大学 广西崇左市 532000摘 要: 在人们生活质量不断提升的背景下,汽车的数量也在与日俱增。
在此背景下,道路交通压力逐渐加大并且交通事故频发,给人们的生命安全以及经济资源带来了巨大威胁。
究其原因,大多是和制动系统故障相关的。
我们能够看到,在汽车上制动系统作为其重要组成模块,对于驾驶者良好操作体验以及生命安全都有着巨大的保障作用。
如果该部分出现问题的话,汽车故障和事故发射率激增,因此做好其故障诊断以及性能优化工作是很有必要的。
基于此,本文在阐述汽车制动系统结构的同时,就其故障类型以及优化策略进行了详细探讨,以期能够给广大同仁提供一些借鉴参考。
关键词:汽车制动系统 结构 故障类型 优化策略当前,汽车已经成为人们生活必不可少的出行工具,它不但给我们的日常出行带来了诸多便利,而且也变相地推动了我国经济的发展。
然而,在汽车行驶过程中,常常会面临诸多故障隐患,尤其是制动系统方面的故障,会大幅度降低驾驶者的体验感,甚至给他们带来生命安全方面的威胁。
因此,我们有必要在把握汽车制动系统结构的基础上,结合其故障类型对其进行有效的优化和维修,以此来进一步提高汽车的运行性能,保障驾驶者的生命安全和财产经济,让汽车的使用效能得到充分保障。
1 汽车制动系统结构对于汽车制动系统来说,其属于一种强制制动形式的装置,即通过对车轮等结构施加相应的力,在此基础上,强制让汽车实现制动的装置。
它不但能够让驾驶者随时根据自己的医院去进行减速或停车,而且还能让汽车在各种类型的路面条件下顺利驻车,从而保障驾驶者的安全。
从结构上来看,它是由多个部件构成的,例如,气泵属于压缩气体产生充气效果的部件;储能器属于储存以及提供相关气体的部件;制动控制阀主要负责对气压进行有效控制;制动气室则主要是负责制动效果的达成。
同时,从功能上来看的话,它又可以分成应急、行车、驻车以及辅助这几类制动类型。
制动器实验台的控制方法分析

黑 河学 院数 学 系 王 烨
[ 摘 要] 制动 系统是 汽车的重要 系统, 了检测制动 器的综合性能 , 为 需要进行 大量路试 , 但是在设 计阶段 无法路试 。而传统的汽车 电惯 量 是 制 动 试 验 系统 采 用 机 械 惯 量 盘 模 拟 汽 车 运 动 惯 量 , 种 系 统体 积 大 、 这 惯量 调 整 困 难 、 动 化 程 度 不 高。 针 对 这 些 问题 , 文 制 本 采 用制动 器试验 台的控 书 方法分析并检测制动 器的综合性能 。首 先, 文建立基 本的常微 分模 型来解决电动机驱动 电流的 问题 , l 本 其 次, 是根据 已知 附表 的数据 , 别对转速和扭矩与对应的 时间应 用MA AB软件拟合 出两个函数进而建立 了能量差微 分模型。 分 TL [ 关键词 ] 机械惯量 瞬时转速 能量差
现代 汽车工业正 经历 巨大 的变革 , 大幅度提高产 量的同时对 汽 为 7 1 k / 。 在 80 g m 的飞轮求 出其 对应的转动惯 量 , 在此基础上 与基础惯量 车性 能 、 质量提 出了更高 的要 求。此外 , 新科 技迅速投 入使用 , 车型 变 分别组合 可得到八种数值 的机械惯量 。 化 日 月异 , 新 这些都对汽车测试技术提 出了更高 的要求 , 要在较 短的时 22 .模型假设 间内就 能测试 出汽车的各项性能指标 。为新车 的研究 开发和新 技术 的 221 ..假设 飞轮 的密度均匀分布 ; 使用提 供可靠 的数据 , 汽车 的制动 器性能 就是其 中重要 的一项指标 。 2. .2假设 飞轮由无 限连续 飞轮 圈组成 ; 2 为了检测制 动器的综合性 能需要在各 种不同情况下 进行大量 的路 试。 23 -变量说 明与名词解 释 但是, 车辆设计阶段无法路试 , 只能在专 门的制 动器试 验台上对所设计 转动惯量 ( 单位 : 优 ) 埒 ; 的路试进行模 拟实验 。被试验 的制 动器安装在 主轴的一端 , 当制动器 h—— 飞轮的厚度 ( , 单位 : ) m ; 工作时会使主轴减速 。试验 台工作 时 , 电动机拖动主轴和飞轮旋转 , 达 r —— 飞轮 的半径 ( 单位为 m ) ; 到与设定 的车速相 当的转速 ( 拟试验 中可认 为主轴的角速度 始终一 模 f 。 —— 飞轮的密度 ( 单位为 k/ 。 gm ) 致) 电动机在断 电的同时施加制 动 , 足设定的条件时就称为完成一 当满 24 -模型的建立与求解 次制动 。 由于飞轮 的形状规则 , 而且是 密度 均匀分布的规则刚体 , 以将其 可 ( ) 车辆单 个前 轮的滚 动半 径为 02 6 制 动时 承受 的载荷 为 1设 . m, 8 进行无 限分割 , 对质量进行积分 即是其转动惯量 , 其基本表达式为 : 6 3 N, 2 0 求等效 的转 动惯量 。 I=I d i rm () 2 飞轮组 由 3 个外直径 1 内直径 0 m的环形 钢制飞轮组成 , m、 . 2 厚 度分别 为 00 9 m、.74 016 m, 材密度为 7 1k/ 基础惯量 .3 2 00 8m、. 8 钢 5 80 gm , 1Z 2r hD7d r f 【 为 lk ・ 问可以组成哪些机械惯量?设 电动机能补偿 的能量 相应 的 Ogm , Iprr 2h3  ̄i d 惯量 的范 围为卜3 , ]g m , 于问题 ( ) 03 k ・ 对 0 1 中得到 的等效 的转 动惯量 , 2 Fd 3r 需要用 电动机补偿 多大的惯量 。 ( ) 立 电动机驱 动电流依 赖 于可观测 量的数学 模型 。在问题 1 3建 解上式积分得 和问题 ( ) 2 的条件下 , 假设制 动减 速度为常数 , 初始速度为 5 k / , 动 0 m h制 I 2 () i r = 4 () 3 50 .秒后 车速 为零 , 计算 驱动电流。 把 h =O 3 2 1 . 9 带人( ) I = 99钾 0 3得 t 2 . 9 1问题 ( ) 析 . 1解 把 h 一O 7 4 2 . 8 带入 ( ) 0 3 得 =5 . 埒 98 9 11 .问题分析 在 汽车路试 时 , 路试 的车辆的指定 车轮在制动 时承受载荷 。那 么 把 h =016 带人( ) 厶:1 9 1 3 . 8 5 3得 1. 幻 9 我们 在制动 器试验 台上可 以将这个载 荷在车辆平 动时具有 的能量 ( 即 因此厚度分别 为 009 、.7 4m 、.58m , .3 2m 00 8 016 钢材 密度 为 7 1 80 汽车的动能 ) 等效的转 化为试验 台上飞轮和主轴 等机构转动 时具有的 / 的飞轮对应的转动惯量分别为 2 .9 5 .8 199 姆 m 基础惯 。 99 、99 、 1.1 , 能量 ( 即转动动能 ) 。在 问题 ( ) 制动时承受的载荷可理解为汽车本 量 为 1 1 中, 0钾 m 。则 可 以组 成 1 , 99 , 99 ,199 , 99 , 5 ., O 3 . 6. 9 8 2 .1惯 量。 19 9 2 9 8 j 8 . , 1. 电 . 的八种数 值的机 械惯 量。用第 ( ) 8 8 _ , m 1 问得 到 的有 效 1 模 型假设 . 2 转动惯量分别减去以上八个机械惯量得到的补偿 惯量分 别为 : 121 ..假设 忽略汽车重力势能 ; 5 . —1 =4 . 蟹 。 1 9 0 19 9 9 1 .假设 路试 时轮胎 与地面 的摩擦力 无穷 大即轮 胎与地 面无滑 .2 2
汽车制动器性能控制方法

2 模 型检 验
由于实验模拟实际车辆 制动 , 因此作为评价 实验 方法
优劣 的指标主要有 2个 : 一是从制动器能量消耗的角度看 , 路试时制动器 消耗 的能量与 实验 台上制 动器 消耗的能量 之差 ; 二是从模拟 的效果 来看 , 实验模 拟过 程与路 试过程
的 吻合 程 度 。
拆卸机构的惯量称 为基 础惯量 。飞轮 组 由若 干个 飞轮组 成, 使用时根据需要 选择几 个飞 轮固定 到主轴上 , 些飞 这 轮的惯 量之和再加上基础惯量称 为机械惯量 。例如 , 假设 有 4个 飞轮 , 其单个惯量分别是 1 ,0 4 ,Ok m , 0 2 ,O 8 g・ 基础 惯 量 为 l g・ 则 可 以组 成 1 ,0 3 , ,6 g・ 2 Ok m , O 2 ,0 … 10k m 1 6种 数值 的 机 械 惯 量。但 对 于 等 效 转 动 惯 量 为 4 . 57 k I 的情况 , g・l l 就不能精确地 用机械惯量模拟试 验。常用 的解决方法是 : 把机械惯 量设定 为 4 g・ , 0 k m。然后在制动 过程 中, 电动机 在一定 规律 的电流控 制下参 与工作 , 让 补 偿 由于机械惯量不足而缺少 的能 量 , 从而满足模 拟试验 的
() 3
或由( 以(得 , 者式) 式)到等= 则 3 1 除 , 有
): 。 肘() t () 4
加制动 , 当满足设 定的结束 条件 时 , 完成一 次制 动。路 就 试车辆 的指定 车轮在 制动 时承受 载荷。将这个 载荷在 车 辆平动时具有的能量 ( 忽略 车轮 自身转 动具有 的能量 ) 等
. 关于主轴 的扭矩为 . d)从 而 电流 产 生 的扭 矩 为 , - , o
,
某轻型载货汽车制动性能分析与改进设计
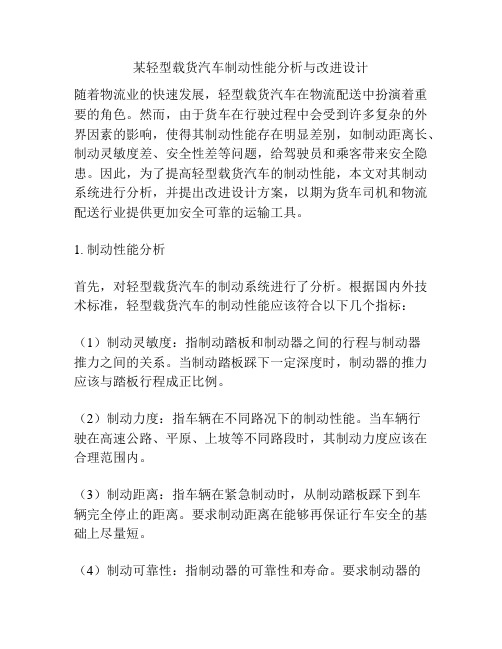
某轻型载货汽车制动性能分析与改进设计随着物流业的快速发展,轻型载货汽车在物流配送中扮演着重要的角色。
然而,由于货车在行驶过程中会受到许多复杂的外界因素的影响,使得其制动性能存在明显差别,如制动距离长、制动灵敏度差、安全性差等问题,给驾驶员和乘客带来安全隐患。
因此,为了提高轻型载货汽车的制动性能,本文对其制动系统进行分析,并提出改进设计方案,以期为货车司机和物流配送行业提供更加安全可靠的运输工具。
1. 制动性能分析首先,对轻型载货汽车的制动系统进行了分析。
根据国内外技术标准,轻型载货汽车的制动性能应该符合以下几个指标:(1)制动灵敏度:指制动踏板和制动器之间的行程与制动器推力之间的关系。
当制动踏板踩下一定深度时,制动器的推力应该与踏板行程成正比例。
(2)制动力度:指车辆在不同路况下的制动性能。
当车辆行驶在高速公路、平原、上坡等不同路段时,其制动力度应该在合理范围内。
(3)制动距离:指车辆在紧急制动时,从制动踏板踩下到车辆完全停止的距离。
要求制动距离在能够再保证行车安全的基础上尽量短。
(4)制动可靠性:指制动器的可靠性和寿命。
要求制动器的使用寿命长、故障率低,以保证行车安全。
2. 改进设计方案针对轻型载货汽车制动性能分析的问题,我们提出以下改进设计方案:(1)优化制动系统:加大制动器的面积和增加刹车片与刹车鼓的接触面积,并且采用高温材料来制造刹车片和刹车鼓,以提升制动力度和制动灵敏度。
同时,还需要加强制动系统的泄压能力。
(2)改善制动系统的散热性能:为了避免制动器因长时间使用而过热,需要在制动器部位安装散热器,提高制动器的散热速度,以保证制动可靠性。
(3)使用液压踏板:改用液压踏板替代传统的机动踏板,以提高制动灵敏度,同时减少制动距离。
(4)提高车速控制技术:采用先进的车速控制技术,如TCS、ABS等,提高车速控制的准确性和精度,从而避免车辆在制动时打滑或失控。
通过上述改进设计方案,可以有效地提升轻型载货汽车的制动性能,从而提高行车安全和物流运输效率,为中国物流行业的发展做出积极的贡献。
汽车制动系统的原理与设计要点

汽车制动系统的原理与设计要点汽车制动系统是车辆行驶安全的重要组成部分。
它通过控制制动力的传递和转化,有效地减速车辆并维持稳定的行驶状态。
本文将介绍汽车制动系统的原理和设计要点。
一、制动系统的原理制动系统的主要原理是通过将机械能转化为热能来实现制动。
当驾驶员踩下制动踏板时,制动踏板传递力量给主缸,主缸通过液压传动将力量传递给制动器。
制动器一般有两种类型,分别是摩擦制动器和转子制动器。
在摩擦制动器中,制动蹄通过与制动盘接触摩擦产生摩擦力,将车辆减速或停止。
而转子制动器则是通过制动器夹住旋转的齿轮、轮轴或者传动轴实现制动效果。
无论是摩擦制动器还是转子制动器,制动时都会产生热量。
为了防止制动器过热,汽车制动系统通常还设有散热器来散发热量,确保制动器的正常工作。
二、制动系统的设计要点1. 制动系统应具备足够的制动力:制动力的大小直接影响汽车的制动性能。
设计制动系统时,需要根据车辆的质量和速度设置合适的制动力大小,以确保车辆能够及时减速或停止。
2. 制动系统应具备良好的稳定性和可靠性:稳定性和可靠性是制动系统的重要设计要点。
制动系统在不同路况和工作环境下都应该能够保持稳定的制动效果,并且能够长时间稳定运行。
3. 制动系统应具备灵敏度和可调节性:制动系统的灵敏度和可调节性能够提高驾驶员对车辆制动的掌控能力。
灵敏的制动系统能够及时响应驾驶员的制动指令,提供更好的制动效果。
可调节性能够根据不同的行驶条件和需求进行调整,以满足不同驾驶风格和道路状况的要求。
4. 制动系统应具备耐用性和维修性:汽车制动系统需要能够承受长时间的使用和各种异常情况下的工作压力。
因此,在设计制动系统时,需要选择高质量和耐磨损的制动器材料,并确保制动系统易于检修和更换。
5. 制动系统应具备防抱死功能:防抱死系统(ABS)是现代汽车制动系统的重要组成部分。
ABS能够通过调节制动器的制动力,防止车轮在制动时完全锁死,提供更好的制动效果和操控稳定性。
制动器试验台的控制方法分析 2009全国数学建模论文

承诺书我们仔细阅读了中国大学生数学建模竞赛的竞赛规则.我们完全明白,在竞赛开始后参赛队员不能以任何方式(包括电话、电子邮件、网上咨询等)与队外的任何人(包括指导教师)研究、讨论与赛题有关的问题。
我们知道,抄袭别人的成果是违反竞赛规则的, 如果引用别人的成果或其他公开的资料(包括网上查到的资料),必须按照规定的参考文献的表述方式在正文引用处和参考文献中明确列出。
我们郑重承诺,严格遵守竞赛规则,以保证竞赛的公正、公平性。
如有违反竞赛规则的行为,我们将受到严肃处理。
我们参赛选择的题号是(从A/B/C/D中选择一项填写): A我们的参赛报名号为(如果赛区设置报名号的话):所属学校(请填写完整的全名):东北师范大学参赛队员(打印并签名) :1. 陈艳宝2. 毛德翼3. 何小燕指导教师或指导教师组负责人(打印并签名):曾志军日期: 2009 年 9月14 日赛区评阅编号(由赛区组委会评阅前进行编号):编号专用页赛区评阅编号(由赛区组委会评阅前进行编号):赛区评阅记录(可供赛区评阅时使用):评阅人评分备注全国统一编号(由赛区组委会送交全国前编号):全国评阅编号(由全国组委会评阅前进行编号):制动器试验台的控制方法分析【摘要】汽车行动制动器的设计是车辆设计中最重要的环节之一。
为了检验设计的优劣,我们设计了最优化的实验室模拟测试方法,经计算验证误差较小,接近实际,具有可行性。
首先,本模型将汽车刹车时所具有的平动动能等效为飞轮组的转动动能,设计相应等效转动惯量的飞轮组,运用能量守恒定律,前轮的滚动半径为0.286 m,制动时承受的载荷为6230 N,等效的转动惯量为51.999 kg·m2。
第二,利用空心圆柱体绕对称中心转动的转动惯量公式,计算得三个飞轮单个惯量为30 kg·m2 ,60 kg·m2,120 kg·m2,可以组成10,40,70,100,130,160,190,220 kg·m2的8种数值的机械惯量,对于问题1中得到的等效的转动惯量,需要用电动机补偿12 kg·m2的惯量。
汽车制动系统的性能改进与优化

汽车制动系统的性能改进与优化汽车制动系统是车辆行驶中至关重要的安全保障之一。
随着汽车工业的发展和技术的进步,人们对汽车制动系统的性能与安全要求也不断提高。
为满足用户的需求,制动系统的性能改进与优化成为一个重要的研究领域。
本文将从几个方面介绍汽车制动系统的性能改进与优化。
一、制动性能的提升制动性能的提升是汽车制动系统改进的关键目标之一。
主要包括制动力矩的增加和制动效率的提高。
1. 制动力矩的增加制动力矩是制动系统提供制动力的能力,直接影响到汽车的制动性能。
制动力矩的增加可以通过以下几种方式来实现:(1)升级制动器:采用更大口径的制动器、改进制动器材料、增加制动器的数量等方式,提高制动器的制动力矩输出。
(2)提升制动液性能:选择高温抗气泡和抗蒸发性能更好的制动液,提高液压传动性能,增加制动力矩输出。
2. 制动效率的提高制动效率是指在单位时间内达到期望制动力的能力,对于制动系统的灵敏性和控制性能具有重要影响。
制动效率的提高可以通过以下几种方式来实现:(1)加强制动器与制动盘(鼓)的接触面积:增大制动盘(鼓)的直径、改进刹车片形状等方式,增加制动器与制动盘(鼓)的接触面积,提高制动效率。
(2)优化制动器的工作参数:通过调整制动器的压力、制动力分配等参数,使制动系统在各种工况下都能保持较高的制动效率。
二、制动系统的防抱死技术制动系统的防抱死技术是为了防止车轮在制动时出现抱死现象,保持车辆的行驶稳定性和操控性能。
常见的制动系统防抱死技术包括:反馈防抱死系统(ABS)、电子制动力分配系统(EBD)和牵引力控制系统(TCS)等。
1. 反馈防抱死系统(ABS)反馈防抱死系统通过控制制动器的工作压力,实时监测车轮的转速和制动器的工作状态,防止车轮在制动时抱死,提高车辆的制动稳定性和操控性能。
2. 电子制动力分配系统(EBD)电子制动力分配系统根据车辆的负荷情况和车轮的附着力,自动调节制动器的工作力度,使各个车轮的制动力分布更为合理,提高制动系统的整体性能和稳定性。
汽车制动系统的性能分析和优化

汽车制动系统的性能分析和优化摘要:在社会经济发展的过程中,汽车产量逐年增加,汽车系统的组成越来越重要,汽车制动系统的性能和安全性非常重要。
车辆制动系统的主要功能是保证车辆在制动过程中通过一个非常稳定的减速过程。
因为车辆制动系统的失败会导致车辆的失败,这对车辆的安全产生重大影响。
所以,对汽车制动系统的性能进行分析,才能对汽车使用的安全性进行保障。
关键词:汽车制动系统;性能;评价指标;影响因素;措施1、汽车制动性能的评价指标1.1制动效能制动效能通常描述的是汽车在行驶过程中以较高速度行驶时,驾驶员遇到障碍或紧急情况需要紧急制动,车辆可以快速减速并停下的能力。
制动效能的两个指标,分别是制动距离和制动减速度。
制动距离是指汽车速度为V0时,从驾驶员开始操纵制动控制装置(制动踏板)到汽车完全停住为止所行驶过的距离。
制动距离与制动踏板力、地面附着条件、车辆载荷、发动机是否结合等许多因素有关。
不同车型在不同状态下的制动距离标准也不同。
制动力的变化间接反映了制动距离的变化,制动力是车辆强制减速并完全停车的主要因素之一。
在实测中,使用制动检测仪检测制动踏板力,制动力过大就会超出标准范围,驾驶人的强度会增加,驾驶员容易疲劳,从而对车辆行车安全产生直接影响。
制动力越大,制动减速度也越大,在制动时,制动减速度越大说明制动效果越好。
因此,制动减速度是评价制动性能的重要指标之一。
1.2制动效能的恒定性制动效能的恒定性主要指制动器具有抵御水衰退和热衰退的能力。
水衰退性是指在制动器表面浸入水后,水润滑作用会导致摩擦系数下降的现象。
行驶中的车辆由于制动鼓或盘与摩擦片之间的摩擦产生热量,这会使得摩擦片干燥。
但是当制动器浸水时,通常经过5-15次制动后,制动器就可以恢复正常的制动性能。
另外,在行驶过程中如果车辆在下坡时进行连续制动或长时间高速行驶,制动鼓或盘温度会逐渐升高,从而导致制动性能下降,制动距离超出标准范围,这种现象称为汽车制动效能的热衰退性。
纯电动汽车制动器的设计与优化研究

纯电动汽车制动器的设计与优化研究随着纯电动汽车的快速发展,汽车制动系统的设计和优化变得愈发重要。
纯电动汽车制动器的设计与优化研究旨在解决纯电动汽车在制动性能、能量回收和制动稳定性等方面所面临的挑战。
本文将从以下几个方面进行详细分析和讨论。
1. 纯电动汽车的制动系统概述纯电动汽车的制动系统相比传统内燃机汽车存在一些不同之处。
纯电动汽车通常采用电动驱动系统,因此制动器需要适应电动化系统的特点,如实现能量回收、提供更高的制动效能等。
同时,由于电动汽车具有较大的车重和高扭矩输出,制动器需要具备更高的制动力和稳定性。
2. 纯电动汽车制动器的工作原理纯电动汽车制动器通常采用的是电力制动(电气制动)和机械制动相结合的方式。
电力制动通过反馈电机并产生电流进行制动能量回收,机械制动则通过摩擦片对车轮的制动来实现制动效果。
制动器的设计需要考虑如何合理利用电力制动和机械制动的组合,以达到最佳的制动性能和能量回收效果。
3. 纯电动汽车制动器的设计要求制动器在纯电动汽车的设计中起着至关重要的作用。
设计要求涉及到制动力的大小、制动响应时间、制动器温度的控制以及噪音和振动的减少等方面。
此外,制动器的设计还需要兼顾安全性、可靠性和制动寿命等方面的要求。
4. 纯电动汽车制动器的优化方法为了提高纯电动汽车制动系统的性能,需要运用一系列优化方法。
其中包括使用先进的材料和制造工艺来提高制动器的效能和可靠性,优化制动器的结构设计以提高制动力和稳定性,采用智能化控制系统来实现更精确的制动控制以及优化制动器的能量回收效率等。
5. 纯电动汽车制动器的未来发展趋势随着科技的不断进步和纯电动汽车市场的持续增长,纯电动汽车制动器也将朝着更高效、更智能的方向发展。
未来的发展趋势可能包括采用电磁制动技术、推出更先进的电子控制系统、提供更舒适静音的制动体验以及更好地融合制动系统和车辆动力系统。
总结起来,纯电动汽车制动器的设计与优化研究旨在解决纯电动汽车制动系统在性能、能效和稳定性等方面所面临的挑战。
汽车线控制动系统安全控制技术研究

汽车线控制动系统安全控制技术研究一、本文概述随着汽车工业的飞速发展,汽车安全控制技术成为了研究的热点。
作为汽车主动安全系统的重要组成部分,线控制动系统(Brake-by-Wire,简称BBW)在安全性能的提升上发挥着关键作用。
本文旨在对汽车线控制动系统的安全控制技术进行深入研究,分析其在现代汽车安全性能提升中的应用及其面临的挑战。
本文将介绍线控制动系统的基本原理和结构,阐述其与传统制动系统的区别和优势。
在此基础上,重点探讨线控制动系统在安全控制方面的关键技术,包括故障检测与诊断、冗余设计、制动性能优化等方面。
这些技术对于确保线控制动系统在各种复杂工况下的可靠性、稳定性和安全性至关重要。
本文将分析线控制动系统在实际应用中面临的安全挑战,如电磁干扰、系统延迟、硬件故障等。
针对这些挑战,提出相应的安全控制策略和优化方法,以提高线控制动系统的安全性和可靠性。
本文将总结线控制动系统安全控制技术的发展趋势和未来研究方向,以期为汽车安全控制技术的进一步发展提供参考和借鉴。
通过本文的研究,希望能够为提升汽车安全性能、保障驾乘人员生命安全提供有益的探索和实践。
二、汽车线控制动系统概述随着汽车技术的不断进步,线控制动系统(Brake-By-Wire,简称BBW)已成为现代车辆制动技术的重要组成部分。
汽车线控制动系统是一种采用电子控制替代传统机械连接的新型制动系统,它通过电信号传输制动指令,实现制动踏板与制动执行机构之间的解耦,从而提供更为快速、精确和稳定的制动响应。
线控制动系统主要由制动踏板模块、电子控制单元(ECU)、制动执行机构和传感器等组成。
制动踏板模块负责采集驾驶员的制动意图,并将其转化为电信号;ECU则负责接收并处理这些电信号,根据车辆状态和驾驶员意图计算出合适的制动力;制动执行机构则根据ECU的指令,通过电液转换装置或直接通过电机驱动制动器实现制动;传感器则用于实时监测车辆状态,包括车速、轮速、踏板行程等,为ECU提供决策依据。
制动器试验台机械惯量电模拟控制方法

制动器试验台机械惯量电模拟控制方法一、概述制动器作为车辆安全性能的重要组成部分,其性能的稳定性和可靠性直接关系到车辆行驶的安全。
为了对制动器性能进行准确、高效的测试,制动器试验台成为了车辆设计阶段不可或缺的设备。
传统的制动器试验台往往存在设备复杂、操作繁琐、成本高等问题,限制了其在实际工程中的应用。
为此,本文提出了一种基于机械惯量电模拟控制方法的制动器试验台设计方案。
该方法利用电学系统模拟机械系统的转动惯量,通过控制可调速电机的电枢回路输入电压,实现对电动机输出转速的精确控制,从而模拟出制动器在实际工作过程中的机械惯量效应。
相较于传统方法,该方案具有设备简单、操作方便、成本低廉等优势,且能够更准确地模拟制动器在不同工况下的工作状态,提高制动性能检测的准确性和效率。
本文首先介绍了制动器试验台的设计原理和控制方法,包括力学原理、控制原理和传感技术等。
详细阐述了机械惯量电模拟控制方法的原理和实现过程,包括等效转动惯量的计算、电机补偿策略的制定以及驱动电流的计算等。
通过实例分析和仿真实验验证了该控制方法的可行性和有效性,为制动器试验台的优化设计和改进提供了有益的参考。
本文的研究成果不仅有助于提高制动器性能检测的准确性和效率,降低检测成本,而且对于推动车辆设计制造和交通运输行业的安全发展具有重要意义。
在未来的研究中,可以进一步探索制动器试验台和机械惯量电模拟控制方法的优化设计,以提高检测精度的稳定性、扩大应用范围以及降低检测成本。
同时,还可以研究其他新型的制动性能检测技术,以实现更高效、准确和可靠的检测。
1. 制动器试验台的重要性和应用背景制动器是汽车安全性能的关键组成部分,其性能的好坏直接关系到车辆行驶的安全性和稳定性。
制动器试验台可以对制动器进行全面的性能检测,包括制动效能、制动抗热衰退性以及制动时汽车的方向稳定性等关键指标。
通过制动试验台,可以对制动器在各种环境和条件下的性能进行准确的评估,为汽车研发、生产和检测提供重要的数据支持。
GB 12676—1999汽车制动系统结构、性能和试验方法

GB 12676—1999前言本标准是根据联合国欧洲经济委员会(ECE)第13号法规《关于M、N、O类机动车制动的统一规定》和ISO 7634—1995《被牵引车辆气制动系试验方法》、ISO 7635—1991《道路车辆气压、气液制动性试验方法》和ISO 6597—1991《道路车辆液压制动系性能试验方法》等国际标准和法规对GB/T 12676—90《汽车制动性能道路试验方法》进行修订的。
修订后本标准做为强制性标准实施。
本标准中有关汽车制动系统结构、性能方面的内容在技术上是等效采用ECE第13号法规;有关汽车制动系统性能试验方法方面的内容在技术上是等效采用ISO 6597—1991、ISO 7634—1995和ISO 7635—1991标准。
该三项国际标准是按照ECE 第13号法规的要求制定的。
本标准是对GB/T 12676—90的修订,技术内容上较原标准增加很多,增加了对汽车制动系统结构功能和性能指标的要求,试验方法也进行了很大修改。
1 本标准实施之日起,下列条款12个月后实施:①第4.1.5条有关接续挂车的气动接头必须是双管路或多管路的要求。
②第5.1.4条有关制动性能必须在车轮不抱死的条件下的要求。
2 本标准实施之日起,下列条款24个月后实施。
①第4.1.4.3条中有关挂车气制动系和牵引车驻车制动系同时作用的要求。
②第4.2.5.1条有关传能装置中零部件失效时,必须保证继续向不受失效影响的其他部分供应能量的要求。
③第4.2.12.1条有关液面报警装置的要求。
④第4.2.12.2条有关液压制动系必须安装失效报警装置。
⑤第4.2.12.3条有关制动液类型的标志的要求。
⑥第4.2.13条有关储能装置中安装报警装置。
⑦第4.4条有关弹簧制动系的要求。
⑧第5.1.5条有关车辆状况应符合附录A的要求。
⑨第5.2.1.2条有关发动机接合的0型试验性能要求。
⑩第5.2.4条和第5.2.5条有关行车制动系Ⅱ型和ⅡA型试验的要求。
汽车用制动器衬片摩擦性能试验方法及质量控制

能的试验方法及试验 中的质量控制进行了探讨 。
2 俭 验 设 备 况 甄 述
摩擦性能试验一般是在定速摩擦试验机 上进 行的 , 目前 我 国生产该设备的企业主要有 :国家非金属矿 制品质量监督检验 中心 ( 成 阳新 益摩擦 密封设备有 限公 司 ) 、 吉林大学 机 电设 备研 究所( 吉林省 旺达机械有 限公司 ) 等单位 , 我们使用 的是成 阳新 益摩擦 密封设 备有 限公司 生产的 X D— MS M改 进型定 速摩擦 试 验机 , 该试验机主要 南三部分组 成, 即主机 、 强电控制柜 、 计 算机
验后的状态 , 将其 记录在 原始记 录中。
4 试 验 过 程 中 的 质 量 控 制
车太生硬 . 造成制动不平稳 ; 指定摩擦系数的 允许偏差这个 参数 数值 小 , 代表 了产 品在使用过 程中随着温度的变化性能稳定 , 摩 擦 系数的数值变化小 , 能始终 保持 良好的制动性能 ; 磨 损率小 则
机 的提 示 输 入 试 片 的初 始 厚 度 等 即 可 开 始 试验 , 程 序 会 按 照 输 入
往砝码托盘上加标 准砝码 , 每加一 个砝码 , 记 录一个计算 机上读
出的摩擦 力数值 , 此时 的数 值应为 ( 1 9 . 6 + 9 8 ) N左右 , 以此 类推 . 直至将 四个 标准 砝码 加 完 ,此 时计 算机 上摩 擦 力的数 值应 为 ( 1 9 . 6 + 9 8 + 9 8 + 9 8 + 9 8 ) N左 右 , 即4 1 1 . 6 N左右 , 将计 算机读 } } J 的数 值与计算值进行 比较 ,当差值不超 过 ±1 5 N时核查结果 可 以接 受, 如果结 果超 出这 个数值 , 则需 要对设 备进行调 整 , 之后 重新 对设备进行校准 。正压 力的核查方法 : ( 1 ) 抬起试验 机杠 杆 . 将正 压力测试装置 的压力传感器放在加载轴 下面 , 打 开 显示器 电源 ,
基于电动汽车动力系统的制动器性能分析与改进
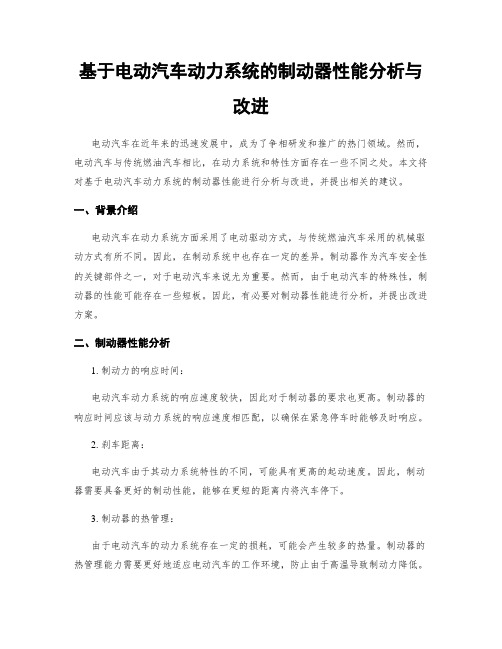
基于电动汽车动力系统的制动器性能分析与改进电动汽车在近年来的迅速发展中,成为了争相研发和推广的热门领域。
然而,电动汽车与传统燃油汽车相比,在动力系统和特性方面存在一些不同之处。
本文将对基于电动汽车动力系统的制动器性能进行分析与改进,并提出相关的建议。
一、背景介绍电动汽车在动力系统方面采用了电动驱动方式,与传统燃油汽车采用的机械驱动方式有所不同。
因此,在制动系统中也存在一定的差异。
制动器作为汽车安全性的关键部件之一,对于电动汽车来说尤为重要。
然而,由于电动汽车的特殊性,制动器的性能可能存在一些短板。
因此,有必要对制动器性能进行分析,并提出改进方案。
二、制动器性能分析1. 制动力的响应时间:电动汽车动力系统的响应速度较快,因此对于制动器的要求也更高。
制动器的响应时间应该与动力系统的响应速度相匹配,以确保在紧急停车时能够及时响应。
2. 刹车距离:电动汽车由于其动力系统特性的不同,可能具有更高的起动速度。
因此,制动器需要具备更好的制动性能,能够在更短的距离内将汽车停下。
3. 制动器的热管理:由于电动汽车的动力系统存在一定的损耗,可能会产生较多的热量。
制动器的热管理能力需要更好地适应电动汽车的工作环境,防止由于高温导致制动力降低。
三、改进方案1. 优化制动系统的控制算法:制动系统的控制算法对于实现快速响应和优化制动力的分配极为重要。
可以通过对制动系统的算法进行优化,提高制动器的性能。
2. 采用新型制动器材料:传统的制动器材料可能无法满足电动汽车的制动需求。
可以考虑采用具有更高温度稳定性和制动性能的新型材料,以提高制动器的性能。
3. 引入智能热管理系统:为了更好地适应电动汽车的工作环境,可以引入智能热管理系统来控制制动器的温度。
该系统可以根据温度变化自动调节制动器的冷却风扇和冷却液的供给,以确保制动器在高温环境下的正常工作。
4. 加强制动器的冷却设计:电动汽车在长时间行驶过程中,大量的动力系统损耗会产生热量,严重影响制动器的性能。
ABS的两种控制方式

“ABS”中文译为“防锁死刹车系统”.它是一种具有防滑、防锁死等优点的汽车安全控制系统。
ABS是常规刹车装置基础上的改进型技术,可分机械式和电子式两种.现代汽车上大量安装防抱死制动系统,ABS 既有普通制动系统的制动功能,又能防止车轮锁死,使汽车在制动状态下仍能转向,保证汽车的制动方向稳定性,防止产生侧滑和跑偏,是目前汽车上最先进、制动效果最佳的制动装置.“ABS”的控制方式ABS系统中,能够独立进行制动压力调节的制动管路称为控制通道。
如果对某车轮的制动压力可以进行单独调节,这种控制方式称为独立控制;如果对两个(或两个以上)车轮的制动压力一同进行调节,则称这种控制方式为一同控制。
在两个车轮的制动压力进行一同控制时,如果以保证附着力较大的车轮不发生制动抱死为原则进行制动压力调节,称这种控制方式为按高选原则一同控制;如果以保证附着力较小的车轮不发生制动抱死为原则进行制动压力调节,则称这种控制方式为按低选原则一同控制.按照控制通道数目的不同,ABS系统分为四通道、三通道、双通道和单通道四种形式,而其布置形式却多种多样。
四通道ABS对应于双制动管路的H型(前后)或X型(对角)两种布置形式,四通道ABS也有两种布置形式.控制装置和ABS警示灯等组成,在不同的ABS系统中,制动压力调节装置的结构形式和工作原理往往不同,电子控制装置的内部结构和控制逻辑也可能ABS通常都由车轮转速传感器、制动压力调节装置、电子不尽相同。
在常见的ABS系统中,每个车轮上各安装一个转速传感器,将有关各车轮转速的信号输入电子控制装置。
电子控制装置根据各车轮转速传感器输入的信号对各个车轮的运动状态进行监测和判定,并形成相应的控制指令.制动压力调节装置主要由调压电磁阀组成,电动泵组成和储液器等组成一个独立的整体,通过制动管路与制动主缸和各制动轮缸相连。
制动压力调节装置受电子控制装置的控制,对各制动轮缸的制动压力进行调节。
在常见的ABS系统中,每个车轮上各安装一个转速传感器,将有关各车轮转速的信号输入电子控制装置。
- 1、下载文档前请自行甄别文档内容的完整性,平台不提供额外的编辑、内容补充、找答案等附加服务。
- 2、"仅部分预览"的文档,不可在线预览部分如存在完整性等问题,可反馈申请退款(可完整预览的文档不适用该条件!)。
- 3、如文档侵犯您的权益,请联系客服反馈,我们会尽快为您处理(人工客服工作时间:9:00-18:30)。
J′=Mαs
(5)
在 (k-1)Δt, kΔt内 , 由 于 Δt很小 , 可 以近似认 为角 加速度和主轴扭矩都 不变 , 于是
Ek =
1 2
Mαs((kk))(ω(k)2
-ω(k-1)2)
其中 α(k)=ω(k)-Δωt(k-1), 化简得
Ek =
1 2
Ms(k) ω(k)-ω(k-1)
ω(k)2
总能量误差就会随着 k的增大而不断减小 。
为了对改进驱动电流 控制模 型的进 行检验 , 对路 试等
效的转动惯 量为 48 kg· m2, 机械 惯量为 35 kg· m2 , 主轴 初转速为 514 r/min, 末 转 速为 257 r/min, 时 间 步 长为 10
ms的情况进行计算 , 得到能量误差率为 3.12%. 所改进的模型适用范 围较广 , 而且 与路试 情况吻 合较
[ 3] 盛 朝强 , 谢昭 莉 .基于 电惯量的汽车惯性 式制动试验 系统的 设 计 [ J] .重 庆 大 学 学 报 , 2005, 28(1):90 -9 3.
[ 4] 王先锋 .惯性制动 器动力 矩的 计算与 分析 [ J] .现代 制造工程报 , 2006(8):107 -109.
[ 5] 陈 建 军 .制 动 器试 验 台 机 械惯 量 电 模 拟控 制 方 法 [ J] .起重运输 机械报 , 2007(12):27 -30.
ω0 , ω1, … , ωk与 M1 , M2 , … , Mk表述出来 , 即理论上 的制动
能量为
1 2
J(ω20
k
-ω2k), 而实际制动能量为 ∑i=1MiωiΔt, 二者之
差为能量误差 。 于是 让第 k + 1步 的电 流值 将这 个能 量
误差补偿上 , 再加上第 k+ 1步原 来应该 的电流 值 。 这样
Ez =
1 2
Jx(ω21
-ω22 )
另一部分是电 动机精 确补 充 了的 由于 机械 惯量 不足 而缺
少的能量 Wc, 其大小为 Wc =Wr -Ez
2)在实验台上模拟 。 在模拟过程中 , 由于电流无法精
确地补偿由于机械惯量不 足而缺 少的能 量 , 因此等效 转动
量不能精确地达到 Jeq, 而是有变化的 , 设为 J′, 且根 据转动 定律有
1)路试情况下 。 由于是行车制动 , 设轮胎与地面的摩 擦力为无穷大 , 因此轮胎与 地面无 滑动 。 这 种条件下 根据
动能定理 , 制动器消耗的能量就是汽车动能的变化量 , 即
Wr =
1 2
Jeq(ω21
-ω22)
其中 :初角速度
ω1
=n1
×2π 60
rad/s, 末 角速度
ω2
=n2
ቤተ መጻሕፍቲ ባይዱ
×2π 60
[ 6] 马继杰 .制 动器 惯 性 台 架电 模 拟 惯 量的 研 究 [ EB/ OL] .[ 2009 -09 -13] .
[ 7] 梁波 .模糊自 整定 PID在 制动 器试 验台电 惯量 模拟 应用 [ J] .电子 测量技术报 , 2008, 31(10):87 -89.
i(k) =K(Jeqω(k-1Δ)t-ω(k)-Ms(k))
上式就是驱动电流依赖于 2个可观测量的数学模型 。
2 模型检验
由于实验模拟实际车 辆制动 , 因此 作为评 价实验 方法 优劣的指标主要有 2个 :一是从制动器能量消耗的角度 看 , 路试时制动器消 耗的 能量 与实 验台 上制 动器 消耗 的能 量 之差 ;二是从模拟 的效 果来 看 , 实验 模拟 过程 与路 试过 程 的吻合程度 。
1) 由 于 在 时 间 段 Δt内 , 对 Ms(k) = Jxα≈ Jxω(k-1Δ)t-ω(k)进行了近似处理 , 使 得施加 的驱动 电流
与实际应施加的驱动电流 存在偏 差 , 致 使电动 机主轴 角速
度与同 一 时 刻 路 试 车 轮 角 速 度 不 能 相 等 , 达 不 到 预 期
目的 。
49 177 J, 能量误差为 2 973 J, 能量误差率为 5.7%. 这种控制方法的 能量补偿误差为
ΔW Wc
=124 907234
= 21.2%
从这个比例来看 , 电流实 际补偿 的能量 与需要补 偿的
能量相差比较大 , 因此这种控制方法不是很好 。
3 模型改进
上述驱动电流控制数学模型 存在几点不足 :
rad/s, 其中 n1 , n2 为主轴 的转速 ;Jeq为等效转动惯量 。 路试可以看 成是 电动 机的 电流 精确 地补 偿由 于 机械
惯量不足而缺少的能 量 , 从 而准确 地模拟 路试实 验 。 因此
制动器消耗的能量可以等 效地看 成 2部 分 , 一部分是 飞轮 转动动能的变化量 , 大小为
(责 任编辑 陈 松 )
2)实际上驱动电流的改变需要一定的响应时间 , 如电 感等因素致使响应被延迟 , 从 而电动机 主轴角 速度的 变化
时间小于实际应该变化的时间 Δt, 使得施 加的驱动 电流不
能使电动机主轴角速度改变到预 期的值 。
因此对其作如下改进 :在要决定 第 k + 1 步的电 流值
时 , 注意到此 时 前面 k步 的 累积 误 差 可以 用 已 经知 道 的
时 , 该段内的驱动 电流 可认 为保 持不 变 , 记该 时间 段的 电
动机的驱动电流 为 i k;在 kΔt时刻 , 电 动机 的主 轴角 速
度的观测值为 ω k, 瞬时扭矩为 Ms(k);由于 Δt很小 , α =ddωt≈ ΔΔωt=ω(k-1Δ)t-ω(k)
由于 ω(k)、ω(k-1)、Ms(k)都是可 观测量 的 , 驱 动电 流 i(k)依赖于可观测量的数学模型可表述为 :
第 31卷 第 4期 【制造技术 】
四川兵工学报
2010年 4月
汽车制动器性能控制方法
刘 田
(重庆通信学院 , 重庆 400035)
摘要 :利用差分的方法 , 将 连续问题离散化 , 解决了车辆制动器实验台上等 效转动惯 量及补偿驱 动电流的 计算方
法 , 提出了电动机驱动电流的控制方法模型 , 实现了以更少的能耗最大限度逼近路试状态的目标 。
I(t)=k0Me(t), 其中
k 为常 系 数 , 0
所以
I(t)= k0(J1 -J)ddωt
(3)
或者由式 (3)除以式 (1), 得到 MMe((tt))=J1 J-J, 则有
I(t) =k0 J1 J-JM(t)
(4)
将制动过程离散化 , 即把整个 制动时 间 T平分为 若干
时间段 Δt。 在任 意时 间段 (k-1)Δt, kΔt内 , 当 Δt很 小
好 , 能量误差较小 , 可 以在 较短 的时 间内 实现 对电 动机 驱
动电流的快速控制 , 便于实现 驱动电流 的计算 机自动 化智
能控制 。
参考文献 :
[ 1] 张 三 慧 .大 学 物 理 学 [ M] .北 京 :清 华 大 学 出 版 社 , 1999.
[ 2] 李海涛 .MATLAB程序 设计 教程 [ M] .北 京 :高等 教 育出版社 , 2002.
一方面 , 从能量 消耗 的角 度看 , 分 等效 于 路试 的理 想
收稿日期 :2010 -01 -26 作者简介 :刘田 (1981— ), 男 , 硕士 , 讲师 , 主要从事车辆工程方面的研究 。
刘 田 :汽车制动器性能控制方法
63
状态和实际实验状态 2种 情况 , 分别 讨论制 动过程中 消耗 的能量 。
-ω(k-1)2
=
Δt
Ms(k)ω(k)+ω2 (k-1)Δt 因此实际模拟中 制动器消耗的能量为
n
∑ Wb = Ek
(6)
k=1
由这 2种情形 , 路试过程 中制动 器与实 验中制动 器消
耗的能量之差为
ΔW =Wb-Wr 能量误差与路试时制 动器消耗的能量之比为 RE=ΔWWr
对路试等效的转 动惯量 为 48 kg· m2, 机械 惯量 为 35 kg· m2 , 主轴初 转速 为 514 r/min, 末 转速 为 257 r/min, 时 间步 长 为 10 ms的 情 况 进 行 计 算 , 得 :等 效 能 量 损 耗 为 52 168 J, 机 械 能 耗 为 38 026 J, 实 验 台 上 总 能 耗 为
1 模型的分析与建立
记需要模拟的 单轮 的等效 转动 惯量为 J, 主 轴转 速为 ω(t), 机械惯量 J1 , 则 J关于主轴的制动扭矩 M(t)为
M(t) =Jddωt
(1)
J1 关于主轴的扭矩为 J1 ddωt, 从而电 流产生的扭矩为
Me(t) =(J1 -J)ddωt
(2)
由于电机的驱 动电 流
关键词 :制动器 ;机械惯量 ;转动惯量 ;扭矩 ;驱动电流
中图分类号 :U463.51
文献标 识码 :A
文章编号 :1006 -0707(2010)04 -0062 -02
汽车行车制动 器 (以下 简称 制动器 )的作用 是在 行驶 时使车辆减速或者停 止 , 保 障人身 和车辆 的安全 。 为 了检 验设计的优劣 , 必须进行相 应的测 试 。 模拟 试验的原 则是 试验台上制动 器的制 动过 程 与路 试车 辆上 制动 器的 制动 过程尽可能一致 。 通常试 验台仅 安装单 轮制动 器试验 , 而 不是同时安 装所 有车 轮的 制动 器进 行试 验 。 制 动器 试验 台一般由安装 了飞 轮组 的主 轴 、驱 动主 轴旋 转的 电动 机 、 底座 、施加制动的 辅 助装 置以 及测 量和 控制 系统 等组 成 。 被试验的制动 器安 装在 主轴 的一 端 , 当制 动 器工 作时 , 主 轴减速 。 试验 台工 作时 , 电 动机 拖动 主轴 和飞 轮旋 转 , 达 到与设定的车 速相当 的转 速 (模拟实 验中 , 可认 为主 轴的 角速度与车轮的角速 度始终一致 )后 , 电 动机断 电 , 同 时施 加制动 , 当满足 设定 的结 束条 件时 , 就完 成一 次制 动 。 路 试车辆的指 定车 轮在 制动 时承 受载 荷 。 将 这个 载荷 在车 辆平动时具有的能 量 (忽略 车轮 自身转 动具 有的 能量 )等 效地转化为试 验台上 飞轮 和 主轴 等机 构转 动时 具有 的能 量 , 与此能量相应的转动惯量 (以 下转动惯量 简称为惯 量 ) 在本文中称 为等 效的 转动 惯量 。 试验 台上 的主 轴等 不可 拆卸机构的 惯量 称为 基础 惯量 。 飞轮 组由 若干 个飞 轮组 成 , 使用时根据需 要选 择几 个飞 轮固 定到 主 轴上 , 这 些飞 轮的惯量之和再加上 基础惯量 称为机 械惯量 。 例如 , 假设 有 4个飞轮 , 其单个惯量分别是 10, 20, 40, 80 kg· m2 , 基础 惯量为 10 kg· m2, 则 可以 组成 10, 20, 30, … , 160 kg· m2 16种 数 值 的 机 械 惯 量 。 但 对 于 等 效 转 动 惯 量 为 45.7 kg· m2的情况 , 就不能精确 地用机 械惯量 模拟试 验 。 常用 的解决方法是 :把机械惯量设定为 40 kg· m2, 然后在 制动 过程中 , 让电动机 在一 定规 律的 电流 控制 下 参与 工作 , 补 偿由于机械惯量不足而缺 少的能 量 , 从而满 足模拟试 验的 原则 。