地大 夹具设计课程设计1汇总
夹具设计课程设计
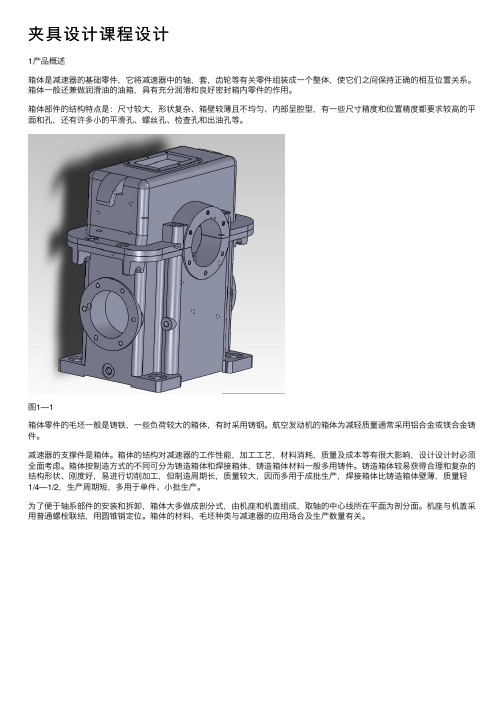
夹具设计课程设计1产品概述箱体是减速器的基础零件,它将减速器中的轴,套,齿轮等有关零件组装成⼀个整体,使它们之间保持正确的相互位置关系。
箱体⼀般还兼做润滑油的油箱,具有充分润滑和良好密封箱内零件的作⽤。
箱体部件的结构特点是:尺⼨较⼤,形状复杂、箱壁较薄且不均匀、内部呈腔型,有⼀些尺⼨精度和位置精度都要求较⾼的平⾯和孔,还有许多⼩的平滑孔、螺丝孔、检查孔和出油孔等。
图1—1箱体零件的⽑坯⼀般是铸铁,⼀些负荷较⼤的箱体,有时采⽤铸钢。
航空发动机的箱体为减轻质量通常采⽤铝合⾦或镁合⾦铸件。
减速器的⽀撑件是箱体。
箱体的结构对减速器的⼯作性能,加⼯⼯艺,材料消耗,质量及成本等有很⼤影响,设计设计时必须全⾯考虑。
箱体按制造⽅式的不同可分为铸造箱体和焊接箱体,铸造箱体材料⼀般多⽤铸件。
铸造箱体较易获得合理和复杂的结构形状、刚度好,易进⾏切削加⼯,但制造周期长,质量较⼤,因⽽多⽤于成批⽣产,焊接箱体⽐铸造箱体壁薄,质量轻1/4—1/2,⽣产周期短,多⽤于单件、⼩批⽣产。
为了便于轴系部件的安装和拆卸,箱体⼤多做成剖分式,由机座和机盖组成,取轴的中⼼线所在平⾯为剖分⾯。
机座与机盖采⽤普通螺栓联结,⽤圆锥销定位。
箱体的材料、⽑坯种类与减速器的应⽤场合及⽣产数量有关。
图1—2⽑坯的铸造⽅法,取决于⽣产类型和⽑坯尺⼨.在单件⼩批⽣产中,多采⽤⽊模⼿⼯造型;在⼤批量⽣产中⼴泛采⽤⾦属模机器造型,⽑坯的精度较⾼.箱体上⼤于30—50mm的孔,⼀般都铸造出顶孔,以减少加⼯余量。
变速箱的⼤批量⽣产的机加⼯⼯艺过程中,其主要加⼯⾯有轴承孔系及其端⾯,平⾯,螺纹孔,销孔等。
因此加⼯过程中的主要问题是保证的孔的精度及位置精度,处理好孔与平⾯的相互关系。
2图纸技术要求分析2.1 图纸的错误及修改查看图纸,我们可以发现⼀些错误1、主视图上,左上⾓吊⽿宽25mm 应该为26mm 。
2、左视图上,轴承孔旁边的凸台尺⼨15mm 应该去掉。
3、左视图缺少剖⾯线。
夹具课程设计

计
目
的
夹具课程设计
夹 具
二、设计任务
课 l.设计题目
程
连杆零件××工序×床夹具设计
设 计
2.零件的生产纲领 批量生产,6万件/年
3.应完成任务
设 计 任
a) 夹具装配图一张(应包括草图一张); b) 夹具体零件图一张;
务
c) 夹具中重要零件的零件图一张;
d) 设计说明书一份。
夹具课程设计
夹 492QA连杆体 具 课 程 设 计
夹具课程设计
2020年4月12日
夹具课程设计
夹 一、设计目的
具 二、设计任务
课 程
三、设计内容及步骤
设 四、设计中应注意的问题
计 五、夹具装配图绘制
六、绘制零样图
七、编写设计说明书
八、考核及时间安排
九、参考资料
夹具课程设计
夹
具 课
一、设计目的
程
设
机床夹具课程设计是在学完机制工程
③ 根据工件特点,选择或设计定位元件;
设
④ 确定引导刀具元件的形式和位置;
计 内 容 及
⑤ 确定夹具与机床的联系;
⑥ 进行定位误差分析与计算。
在进行定位方案分析时,学生应尽量多考虑几个方 案,并提出它们各自的优缺点,再与教师讨论,讨论时
步 应有方案草图,经教师同意后才初步决定。
Байду номын сангаас
骤
夹具课程设计
夹 具
b) 夹紧方案设计
课
①根据在编制工艺规程时确定
程 (或规定)的切削用量,计算切削力
设 和切削力矩,确定需要的夹紧力;
计
②合理布置夹紧力作用点及方
设 向; 计
机床夹具课程设计说明书1-1终
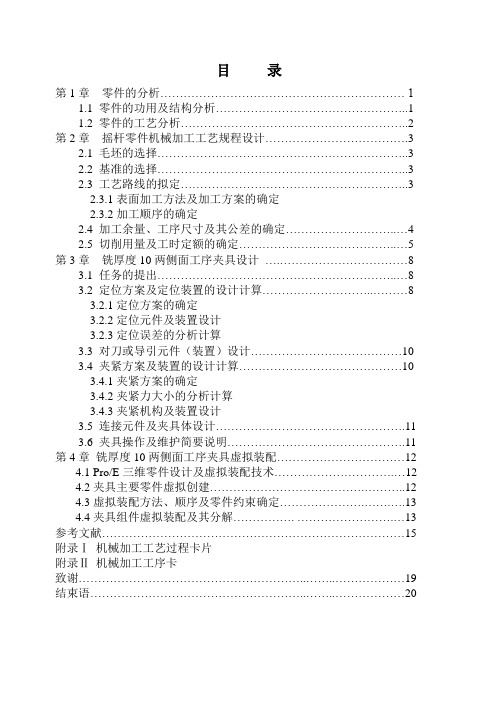
目录第1章零件的分析 (1)1.1 零件的功用及结构分析 (1)1.2 零件的工艺分析 (2)第2章摇杆零件机械加工工艺规程设计 (3)2.1 毛坯的选择 (3)2.2 基准的选择 (3)2.3 工艺路线的拟定 (3)2.3.1表面加工方法及加工方案的确定2.3.2加工顺序的确定2.4 加工余量、工序尺寸及其公差的确定 (4)2.5 切削用量及工时定额的确定 (5)第3章铣厚度10两侧面工序夹具设计 (8)3.1 任务的提出 (8)3.2 定位方案及定位装置的设计计算 (8)3.2.1定位方案的确定3.2.2定位元件及装置设计3.2.3定位误差的分析计算3.3 对刀或导引元件(装置)设计 (10)3.4 夹紧方案及装置的设计计算 (10)3.4.1夹紧方案的确定3.4.2夹紧力大小的分析计算3.4.3夹紧机构及装置设计3.5 连接元件及夹具体设计 (11)3.6 夹具操作及维护简要说明 (11)第4章铣厚度10两侧面工序夹具虚拟装配 (12)4.1 Pro/E三维零件设计及虚拟装配技术 (12)4.2夹具主要零件虚拟创建 (12)4.3虚拟装配方法、顺序及零件约束确定 (13)4.4夹具组件虚拟装配及其分解................ . (13)参考文献 (15)附录Ⅰ机械加工工艺过程卡片附录Ⅱ机械加工工序卡致谢 (19)结束语 (20)第1章零件的分析1.1 零件的功用及结构分析课设题目:“摇杆”机械加工工艺规程及铣厚度10两侧面夹具设计零件二维图:零件三维图:题目给定的是车床的摇杆零件。
它位于车床上的变速结构中,用来换挡,使主轴的回转运动按照工作者的要求工作,从而获得所需要的速度和扭矩的作用。
零件上的φ12H7孔与操作机构连接,φ20H7孔则是用于与控制齿轮所在的轴相配合。
通过φ12H7孔所受的力拨动φ20H7孔这端的齿轮变速达到所需的作用。
摇杆零件图样的视图正确、完整、统一,尺寸、公差及技术要求齐全,完全表达清楚了此零件的机构特点。
夹具设计课程设计大纲
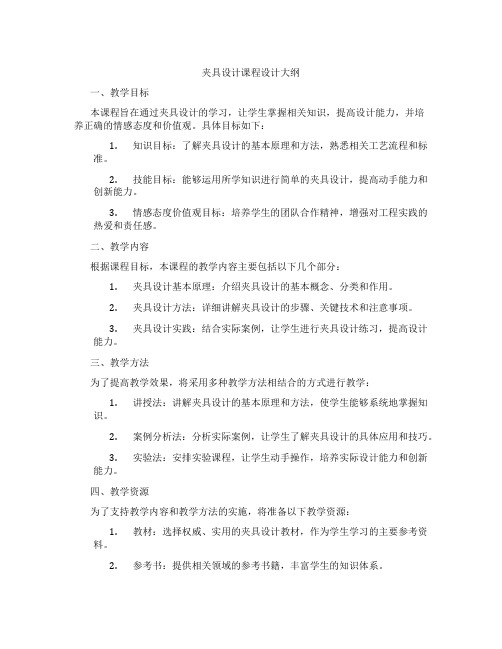
夹具设计课程设计大纲一、教学目标本课程旨在通过夹具设计的学习,让学生掌握相关知识,提高设计能力,并培养正确的情感态度和价值观。
具体目标如下:1.知识目标:了解夹具设计的基本原理和方法,熟悉相关工艺流程和标准。
2.技能目标:能够运用所学知识进行简单的夹具设计,提高动手能力和创新能力。
3.情感态度价值观目标:培养学生的团队合作精神,增强对工程实践的热爱和责任感。
二、教学内容根据课程目标,本课程的教学内容主要包括以下几个部分:1.夹具设计基本原理:介绍夹具设计的基本概念、分类和作用。
2.夹具设计方法:详细讲解夹具设计的步骤、关键技术和注意事项。
3.夹具设计实践:结合实际案例,让学生进行夹具设计练习,提高设计能力。
三、教学方法为了提高教学效果,将采用多种教学方法相结合的方式进行教学:1.讲授法:讲解夹具设计的基本原理和方法,使学生能够系统地掌握知识。
2.案例分析法:分析实际案例,让学生了解夹具设计的具体应用和技巧。
3.实验法:安排实验课程,让学生动手操作,培养实际设计能力和创新能力。
四、教学资源为了支持教学内容和教学方法的实施,将准备以下教学资源:1.教材:选择权威、实用的夹具设计教材,作为学生学习的主要参考资料。
2.参考书:提供相关领域的参考书籍,丰富学生的知识体系。
3.多媒体资料:制作精美的课件和教学视频,提高学生的学习兴趣。
4.实验设备:配置齐全的实验设备,确保学生能够进行实际操作。
五、教学评估为了全面、客观地评估学生的学习成果,将采用多种评估方式相结合:1.平时表现:通过课堂参与、提问、小组讨论等环节,评估学生的学习态度和积极性。
2.作业:布置适量的作业,评估学生的理解和应用能力。
3.考试:安排期末考试,全面测试学生对夹具设计知识的掌握程度。
六、教学安排本课程的教学安排如下:1.教学进度:按照教材的章节顺序进行教学,确保学生系统地掌握夹具设计知识。
2.教学时间:合理安排课堂时间,保证教学内容的充分讲解和实践操作。
夹具设计课程设计题库

夹具设计课程设计题库一、教学目标本节课的教学目标是让学生掌握夹具设计的基本原理和方法,能够运用所学知识进行简单的夹具设计。
具体来说,知识目标包括了解夹具的定义、分类和基本结构,掌握夹具设计的原则和方法,理解夹具在机械加工中的作用。
技能目标则要求学生能够运用所学知识进行夹具的设计和计算,能够阅读和理解夹具设计图,具备一定的实际操作能力。
情感态度价值观目标则是培养学生对机械加工行业的兴趣和热情,增强学生的创新意识和实践能力。
二、教学内容本节课的教学内容主要包括夹具的定义、分类和基本结构,夹具设计的原则和方法,夹具在机械加工中的作用等。
具体来说,首先介绍夹具的定义和分类,让学生了解夹具的基本概念和种类;然后讲解夹具的基本结构,包括固定装置、导向装置、夹紧装置等,使学生掌握夹具的组成部分和功能;接着阐述夹具设计的原则和方法,让学生学会如何进行夹具设计;最后讲解夹具在机械加工中的作用,让学生了解夹具在实际加工过程中的重要性。
三、教学方法为了达到本节课的教学目标,我们将采用多种教学方法进行教学。
首先,运用讲授法向学生讲解夹具的基本概念、原理和设计方法;其次,通过案例分析法让学生了解夹具在实际工程中的应用实例,提高学生的应用能力;再次,利用实验法让学生亲自动手进行夹具的设计和制作,培养学生的实际操作能力;最后,采用讨论法引导学生进行思考和交流,激发学生的创新意识和团队合作精神。
四、教学资源为了支持本节课的教学内容和教学方法的实施,我们将准备以下教学资源。
首先,教材《机械设计基础》及相关参考书籍,为学生提供理论知识的学习;其次,多媒体资料,包括图片、视频等,用于辅助讲解和展示夹具的设计和应用;再次,实验设备,包括夹具样品、机械加工设备等,让学生进行实际操作和观察;最后,网络资源,如学术期刊、在线课程等,为学生提供更多的学习资料和信息。
五、教学评估本节课的评估方式包括平时表现、作业和考试三个部分。
平时表现主要评估学生在课堂上的参与程度、提问和回答问题的积极性等,占总评的30%。
夹具设计课程设计

目录1.设计任务书1.1.概述1.2.设计的要求1.3.设计题目2.加工零件的简介2.1.加工的零件图2.2.加工零件的结构特点3.零件加工方案的选择3.1.零件的工艺分析3.2.工艺方案的确定3.2.1、确定毛坯的制造形式3.2.2、基面的选择3.2.3..制定工艺路线3.2.4、机械加工余量、工序尺寸及毛坯尺寸的确定3.2.5、确立切削用量及基本工时4.零件夹具方案的选择4.1拟定定位方案和选择定位元件4.1.1.拟定定位方案4.1.2选择定位元件4.2.确定夹具类型5.夹紧方案的确定5.1.夹紧方案的选择5.2.夹紧力的估算6.夹具的结构设计7.夹具的使用说明8.设计小结参考文献1.设计任务书1.1概述在现代制造技术迅猛发展的今天,机床夹具无论在传统机床上还是在数控机床、加工中心上,仍是必不可少的重要工艺装备。
通过机床夹具设计,不仅可养综合运用已学知识的能力而且可以得到工程设计的初步训练。
1.2.设计的要求1.运用已学过的机床夹具设计及有关课程的理论知识以及生产实习中所获得的实际只是,根据被加工零件的要求,设计既经济合理又能保证加工质量的夹具。
2.培养结构设计能力,掌握结构设计的方法和步骤3.学会使用各种手册、图册、设计表格,规范等各种标准技术资料,能够做到熟练运用机械制造技术课程中的基本理论,正确的解决一个零件在加工中的加工基准的选择、定位、夹紧、加工方法选择以及合理安排工艺路线,保证零件的加工质量。
4.?进一步培养机械制图、分析计算、结构设计、编写技术文件等基本技能。
1.3.设计题目题目:“拔叉(CA6140)”的夹具设计内容:铣直径为40mm上端面的立式铣床夹具设计(1)零件图 1张(2)夹具总装图 1张(3)夹具主要零件图若干张(每个零件一张图)(4)课程设计说明书 1份2.加工零件的简介2.1.加工的零件图2.2.加工零件的作用及结构特点题所给的是CA6140车床上的拨叉,它位于车床变速机构中,主要起换挡作用,使主轴回转运动按照工作者的要求工作,获得所需的速度和扭矩。
夹具设计课程设计说明书
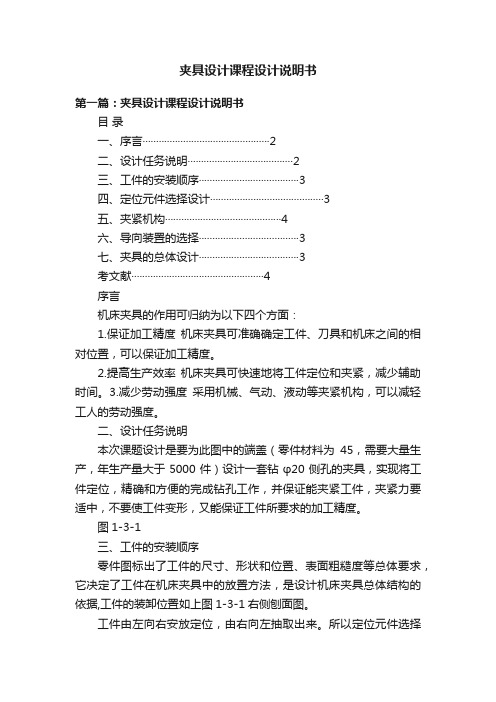
夹具设计课程设计说明书第一篇:夹具设计课程设计说明书目录一、序言 (2)二、设计任务说明 (2)三、工件的安装顺序 (3)四、定位元件选择设计 (3)五、夹紧机构 (4)六、导向装置的选择 (3)七、夹具的总体设计 (3)考文献 (4)序言机床夹具的作用可归纳为以下四个方面:1.保证加工精度机床夹具可准确确定工件、刀具和机床之间的相对位置,可以保证加工精度。
2.提高生产效率机床夹具可快速地将工件定位和夹紧,减少辅助时间。
3.减少劳动强度采用机械、气动、液动等夹紧机构,可以减轻工人的劳动强度。
二、设计任务说明本次课题设计是要为此图中的端盖(零件材料为45,需要大量生产,年生产量大于5000件)设计一套钻φ20侧孔的夹具,实现将工件定位,精确和方便的完成钻孔工作,并保证能夹紧工件,夹紧力要适中,不要使工件变形,又能保证工件所要求的加工精度。
图1-3-1三、工件的安装顺序零件图标出了工件的尺寸、形状和位置、表面粗糙度等总体要求,它决定了工件在机床夹具中的放置方法,是设计机床夹具总体结构的依据,工件的装卸位置如上图1-3-1右侧刨面图。
工件由左向右安放定位,由右向左抽取出来。
所以定位元件选择短销、大平面组合定位、外端圆面添加平面支持钉定位和支持;定位方案的选择依据六点定位原理和采用的机床加工方法,定位方案不一定要定六个自由度,但要完全定位。
确定夹紧机构要依据零件的外型尺寸,选择合适的定位点,确保夹紧力安全、可靠同时夹紧机构不能与刀具的运动轨迹相冲突。
四、定位元件选择设计由于该零件的加工是钻φ20孔并以φ50孔内表面作为定位面,属与孔定位类型,因此本次设计采用的定位元件为短销、大平面组合定位。
,限制工件5个自由度;夹装工件时,工件孔与短销、大平面表面的刚性接触,精准度要求较高,分别限制工件的X、Y、Z方向的移动自由度以及X、Y方向的旋转自由度。
工件定位短销φ50与加工工件之间间隙配合,便于工件加工时装取和定位。
综合课程设计一(零件工艺过程分析设计与夹具设计)

一、 序言机械制造工艺学课程设计是在我们学完了大学的全部基础课、技术基础课以及大部分专业课之后进行的。
这是我们在进行毕业设计之前对所学各课程的一次深入的综合性的总复习,也是一次理论联系实际的训练,因此,它在我们四年的大学生活中占有重要的地位。
就我个人而言,我希望能通过这次课程设计对自己未来将从事的工作进行一次适应性训练,从中锻炼自己分析问题、解决问题的能力,为今后参与硕士研究生科研课题以及毕业后的工作打下一个良好的基础。
由于能力有限,设计尚有许多不足之处,恳请各位老师给予指教。
二、 零件的分析(一)零件的作用题目所给定的零件是车床拨叉(见附图1),从零件结构特征来讲属于叉架类零件。
它位于车床轴系箱体内,是导杆移动式操纵机构,经手柄轴,通过摆杆滑块机构,使拨叉沿导杆直线移动,钳形拨叉拨动被操纵件滑移齿轮轮缘轴向移动。
拨叉头的180.055±槽与摆杆的销配合,拨叉脚的0.2037.5R +厚160.09±叉口部位与滑移齿轮轮缘配合。
(二)零件的工艺性分析拨叉共有两组加工表面,它们之间有一定的位置要求。
现分述如下:1. 以0.033020+∅孔为中心的加工表面这一组加工表面包括:尺寸为0.033020+∅的通孔,尺寸为0.2037.5R +的拨叉脚半圆面,尺寸为8.3∅的通孔和两端10M 深18的螺纹孔,拨叉头端面及拨叉头槽底面。
2. 以160.09±叉口部位右侧端面为中心的加工表面这一组加工表面包括:尺寸为160.09±的叉口两侧面,拨叉头右侧面,36∅圆柱右端面及其倒角,尺寸为180.055±的拨叉头槽两侧面,尺寸为30的拨叉头槽内腔两侧面。
3. 这两组加工表明间有着一定的位置要求,主要是:(1)160.09±叉口两侧面对0.033020+∅孔轴线的垂直度公差为0.10; (2)180.055±拨叉头槽两侧面对0.033020+∅孔轴线的垂直度公差为0.10;(3)180.055±拨叉头槽两侧面的中心平面对叉口右端面的位置度公差为0.15。
夹具课程设计2013

夹具课程设计2013一、教学目标本节课的教学目标是使学生掌握夹具的基本概念、设计原则和应用方法。
知识目标包括:了解夹具的定义、分类和基本结构;掌握夹具设计的原则和方法;了解夹具在机械加工中的应用。
技能目标包括:能够运用夹具设计原则和方法进行简单的夹具设计;能够分析夹具在使用过程中的性能和效果。
情感态度价值观目标包括:培养学生对机械加工行业的兴趣和热情;培养学生勇于探索、创新的精神。
二、教学内容本节课的教学内容主要包括夹具的基本概念、设计原则和应用方法。
首先,介绍夹具的定义、分类和基本结构,使学生对夹具有一个整体的认识。
其次,讲解夹具设计的原则和方法,让学生掌握夹具设计的基本思路。
最后,介绍夹具在机械加工中的应用,让学生了解夹具在实际生产中的重要性。
三、教学方法为了实现本节课的教学目标,将采用多种教学方法相结合的方式。
首先,采用讲授法,系统地传授夹具的基本概念、设计原则和应用方法。
其次,采用讨论法,引导学生针对夹具设计中的问题进行思考和讨论,提高学生的分析能力。
此外,还采用案例分析法和实验法,让学生通过分析实际案例和动手实验,更好地理解夹具的设计和应用。
四、教学资源为了支持本节课的教学内容和教学方法的实施,将准备以下教学资源。
首先,教材《机械加工工艺》,作为学生学习的主要参考资料。
其次,参考书《夹具设计与应用》,为学生提供更多的夹具设计方法和实例。
此外,还准备多媒体资料,如夹具的图片、视频等,丰富学生的学习体验。
最后,准备实验设备,如夹具模型、机械加工设备等,让学生能够亲自动手操作,提高学生的实践能力。
五、教学评估本节课的评估方式将采用多元化的形式,以全面、客观地评价学生的学习成果。
平时表现占30%,包括课堂参与度、提问回答等;作业占30%,包括课后练习和设计任务;考试占40%,包括理论知识测试和实际操作考核。
通过这种评估方式,能够全面反映学生的学习成果,激发学生的学习积极性。
六、教学安排本节课的教学安排将分为两个阶段进行。
夹具课程设计

摘要机床夹具是机械加工工艺系统的重要组成部分,是机械制造中的一项重要工艺装备。
机床夹具在机械加工中起着重要的作用,它直接影响机械加工的质量、生产率和生产成本以及工人的劳动强度等。
因此机床夹具设计是机械加工工艺准备中的一项重要工作。
在专用夹具的设计中,根据设计任务主要就铣床和钻床夹具进行了设计,完成了对夹具用的定位件、导向件对刀件、导引件等夹具中用到的零件的设计,并用UG进行了三维建模和CAD二维制图。
夹具的设计,根据所设计出的工件外形及加工要求,设计出合适的夹具。
本文设计的夹具,基本上可以满足工程需要,本文使用的设计方法,也可为同类夹具的设计提供参考。
关键词:铣床夹具;钻床夹具;UG;CAD;专用夹具目录摘要 (I)1设计任务 (1)1.1 专用夹具的主要作用 (1)2 零件的装夹 (2)2.1零件的工艺和精度分析 (2)2.2 定位设计 (3)3 夹具加工精度分析 (7)3.1 定位精度 (7)3.2 对刀精度 (7)3.3安装精度 (7)3.4夹具精度 (7)总结 (7)参考文献 (8)1设计任务1.1专用夹具的主要作用1.工装夹具应具备足够的强度和刚度。
夹具在生产中投入使用时要承受多种力度的作用,所以工装夹具应具备足够的强度和刚度。
2.夹紧的可靠性。
夹紧时不能破坏工件的定位位置和保证产品形状、尺寸符合图样要求。
既不能允许工件松动滑移,又不使工件的拘束度过大而产生较大的拘束应力。
3.夹具体应具有良好的加工精度和尺寸稳定性。
对于夹具体上用来安装定位元件、对刀(或导向元件)的工作表面,应提出相应的尺寸、几何公差以及粗糙度的具体要求,并作相应的热处理或时效处理。
4.有良好的结构工艺性和使用性。
5.力求结构简单,装卸方便。
在保证强度和刚度的前提下,极可能体积小、重量轻、以便于操作。
6.排屑方便。
7.夹具在机床上安装要稳定、可靠[1]。
1.2设计任务简介如图1-1所示,分别为连杆的立体图和零件图。
本工序的任务是铣削Ф28、Ф26外圆的上下端面和钻削Ф16的孔。
夹具课程设计百度文库
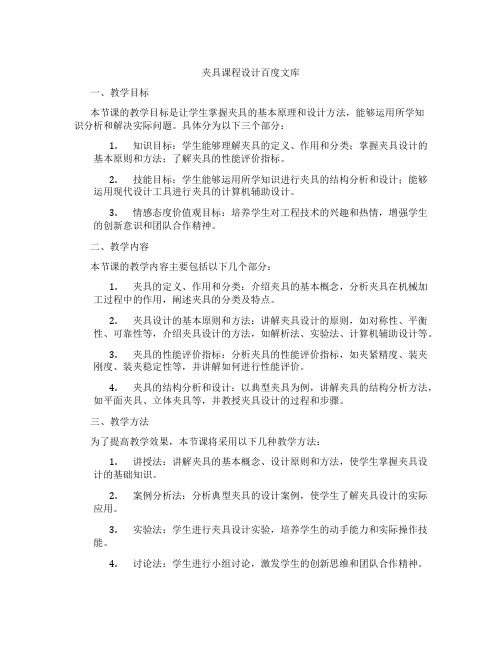
夹具课程设计百度文库一、教学目标本节课的教学目标是让学生掌握夹具的基本原理和设计方法,能够运用所学知识分析和解决实际问题。
具体分为以下三个部分:1.知识目标:学生能够理解夹具的定义、作用和分类;掌握夹具设计的基本原则和方法;了解夹具的性能评价指标。
2.技能目标:学生能够运用所学知识进行夹具的结构分析和设计;能够运用现代设计工具进行夹具的计算机辅助设计。
3.情感态度价值观目标:培养学生对工程技术的兴趣和热情,增强学生的创新意识和团队合作精神。
二、教学内容本节课的教学内容主要包括以下几个部分:1.夹具的定义、作用和分类:介绍夹具的基本概念,分析夹具在机械加工过程中的作用,阐述夹具的分类及特点。
2.夹具设计的基本原则和方法:讲解夹具设计的原则,如对称性、平衡性、可靠性等,介绍夹具设计的方法,如解析法、实验法、计算机辅助设计等。
3.夹具的性能评价指标:分析夹具的性能评价指标,如夹紧精度、装夹刚度、装夹稳定性等,并讲解如何进行性能评价。
4.夹具的结构分析和设计:以典型夹具为例,讲解夹具的结构分析方法,如平面夹具、立体夹具等,并教授夹具设计的过程和步骤。
三、教学方法为了提高教学效果,本节课将采用以下几种教学方法:1.讲授法:讲解夹具的基本概念、设计原则和方法,使学生掌握夹具设计的基础知识。
2.案例分析法:分析典型夹具的设计案例,使学生了解夹具设计的实际应用。
3.实验法:学生进行夹具设计实验,培养学生的动手能力和实际操作技能。
4.讨论法:学生进行小组讨论,激发学生的创新思维和团队合作精神。
四、教学资源为了支持本节课的教学,将准备以下教学资源:1.教材:选用国内权威出版的《夹具设计》教材,为学生提供系统的理论知识。
2.参考书:提供相关领域的参考书籍,拓展学生的知识视野。
3.多媒体资料:制作课件、动画等多媒体资料,直观展示夹具的结构和设计过程。
4.实验设备:准备夹具设计实验所需的设备,如测量工具、夹具等,为学生提供实践操作的机会。
机械课程设计夹具设计

机械课程设计夹具设计一、教学目标本节课的教学目标是让学生掌握夹具设计的基本原理和方法,能够独立完成简单的夹具设计。
具体分为以下三个部分:1.知识目标:使学生了解夹具的定义、分类和作用,掌握夹具设计的基本原则和方法,理解夹具的主要结构和部件。
2.技能目标:培养学生运用所学知识进行夹具设计的能力,能够熟练使用相关设计软件进行夹具的绘制和模拟。
3.情感态度价值观目标:培养学生对机械设计的兴趣和热情,增强学生的创新意识和团队合作精神,培养学生遵守工程伦理和规范的意识。
二、教学内容本节课的教学内容主要包括以下几个部分:1.夹具的定义、分类和作用:介绍夹具的基本概念,分析夹具的分类和作用,让学生了解夹具在机械加工中的重要性。
2.夹具设计的基本原则和方法:讲解夹具设计的基本原则,如对称性、平衡性、可靠性等,介绍夹具设计的方法,如解析法、模拟法等。
3.夹具的主要结构和部件:分析夹具的结构,讲解夹具的主要部件及其功能,使学生了解夹具的组成。
4.夹具设计的实例分析:通过具体实例,让学生掌握夹具设计的过程和方法,提高学生的实际操作能力。
5.夹具设计的软件应用:介绍夹具设计相关软件的使用方法,如AutoCAD、SolidWorks等,让学生学会使用软件进行夹具的绘制和模拟。
三、教学方法为了提高教学效果,本节课将采用多种教学方法相结合的方式进行教学:1.讲授法:通过讲解夹具的基本概念、设计原则和方法,使学生了解夹具设计的理论基础。
2.案例分析法:通过分析具体夹具设计实例,让学生掌握夹具设计的过程和方法,提高学生的实际操作能力。
3.实验法:让学生在实验室进行夹具设计的实践操作,培养学生的动手能力和实际操作技能。
4.讨论法:学生进行分组讨论,激发学生的创新思维,培养学生团队合作精神和沟通能力。
四、教学资源为了保证教学的顺利进行,本节课将采用以下教学资源:1.教材:选用国内权威出版的《机械设计基础》作为主要教材,为学生提供系统、全面的夹具设计知识。
夹具课程设计组成

夹具课程设计组成一、教学目标本课程的教学目标是让学生掌握夹具的基本概念、设计和应用方法。
通过本课程的学习,学生将能够:1.知识目标:理解夹具的定义、分类和基本结构;掌握夹具设计的原则和方法;了解夹具在机械加工中的应用。
2.技能目标:能够运用夹具设计的基本原理,分析并解决实际工程问题;能够运用现代设计工具,进行夹具的设计和优化。
3.情感态度价值观目标:培养学生的创新意识和团队合作精神,提高学生对机械加工行业的认识和兴趣。
二、教学内容本课程的教学内容主要包括以下几个部分:1.夹具的基本概念:夹具的定义、分类和基本结构。
2.夹具设计原理:夹具设计的原则、方法和技术。
3.夹具的应用:夹具在机械加工中的应用和案例分析。
4.现代夹具设计工具:计算机辅助设计(CAD)和计算机辅助制造(CAM)在夹具设计中的应用。
三、教学方法为了实现本课程的教学目标,我们将采用以下几种教学方法:1.讲授法:通过教师的讲解,使学生掌握夹具的基本概念和设计原理。
2.案例分析法:通过分析实际案例,使学生了解夹具的应用和设计过程。
3.实验法:通过实验操作,使学生了解夹具的结构和功能。
4.讨论法:通过小组讨论,培养学生的团队合作精神和创新意识。
四、教学资源为了支持本课程的教学内容和教学方法的实施,我们将准备以下教学资源:1.教材:选用权威、实用的夹具设计教材,为学生提供系统的学习资料。
2.参考书:提供相关的夹具设计参考书籍,丰富学生的知识体系。
3.多媒体资料:制作夹具设计的相关视频、动画和图片,提高学生的学习兴趣。
4.实验设备:准备夹具设计实验所需的设备,为学生提供实践操作的机会。
五、教学评估为了全面、客观地评估学生在夹具课程中的学习成果,我们将采用以下评估方式:1.平时表现:通过学生在课堂上的参与度、提问和讨论,评估其对夹具知识的理解和应用能力。
2.作业:布置相关的夹具设计作业,评估学生对夹具设计原理和方法的掌握程度。
3.考试:进行期中和期末考试,测试学生对夹具知识的全面理解和应用能力。
机床夹具设计课程设计
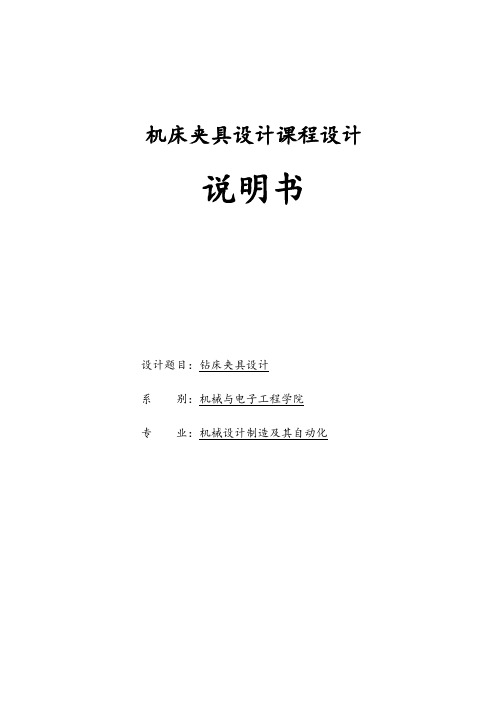
划线找正法定位是在机床上使用划针按毛坯或半成品上待加工处预先划出的线段找正工件,使其获得正确的位置的定位方法,此法受划线精度和找正精度的限制,定位精度不高。主要用于批量小,毛坯精度低及大型零件等不便于使用夹具进行加工的粗加工。
(三)使用夹具定位
夹具定位即是直接利用夹具上的定位元件使工件获得正确位置的定位方法。由于夹具的定位元件与机床和刀具的相对位置均已预先调整好,故工件定位时不必再逐个调整。此法定位迅速、可靠,定位精度较高,广泛用于成批生产和大量生产中。
5.2连接元件选型
5.2.1 标准件
连接元件选型包括定位元件选取,夹紧元件选取,其他专用元件选取。
1、定位元件:支撑钉,支撑板,可调支撑螺钉。
2、夹紧元件:压紧螺钉,螺母,滑动压块,压板。
3、其他专用元件:钻套。
以上所用元件都为标准件,相关的尺寸大小查表可得。
5.2.2 非标准件
夹具体设计,钻模板设计,底座设计。
2.1.2 定位方案选定
在考虑到以上问题的基础上,根据零件的具体情况提出以下定位方案:
方案:三 工件采用六点定位,即用底面四个点和侧面两个点定位,这种定位方式,夹具结构简单,装卸工件方便,定位稳定可靠,并且在一次安装中,可以从加工除定位面以外的剩余各个平面和孔系,也可以作为从粗加到精加工大部分工序的定位基准,实现“基准统一”。因此,显然此方案满足“六点定位原理”的要求。工件的六个自由度被完全限制,并且产生过定位,但只需严格保证φ6H8孔轴线的垂直度要求就能较小的产生过定位带来的加工误差,顾采用上述定位方案可行。
夹具结构,如多件夹紧、联动结构等,以缩短辅助时间;对于中、小批量生产,则要求在满足夹具功能的前提下,尽量使夹具结构简单、制造方便,以降低夹具制造成本。
- 1、下载文档前请自行甄别文档内容的完整性,平台不提供额外的编辑、内容补充、找答案等附加服务。
- 2、"仅部分预览"的文档,不可在线预览部分如存在完整性等问题,可反馈申请退款(可完整预览的文档不适用该条件!)。
- 3、如文档侵犯您的权益,请联系客服反馈,我们会尽快为您处理(人工客服工作时间:9:00-18:30)。
机械加工工艺卡产品型号零件图号产品名称两级圆锥斜齿圆柱齿轮减速器零件名称合箱车间工序号工序名称金工车间镗输入轴承孔毛坯种类毛坯材料毛坯外形每毛坯可制件数铸件HT200 1290×520×370 1 设备名称设备型号设备编号卧式镗床T618夹具编号夹具名称切削液输入轴承孔煤油与矿物质油的混合物工位器具编号工位器具名称工序工时准终单件0,987min 19.74min工步号工步内容工艺装备主轴转速(r/min)切削速度(m/min)进给量(mm/r)背吃刀量(mm)进给次数工步工时机动辅助1 粗镗输入轴承孔至148mm卧式镗床T618硬质合金四刀镗片160.3 75.5 0.4 3 1 1.31min 0.262min2 粗镗输入轴承孔至149.3.mm卧式镗床T618硬质合金四刀镗片190.4 89.7 0.3 1.3 1 3.68min 0.736min3 粗镗输入轴承孔至150mm卧式镗床T618硬质合金四刀镗片257.1 121.1 0.1 0.7 1 8.17min 1.633min 中国地质大学(武汉)设计者设计日期审核日期标准化日期会签日期杜强2012.9.1机械制造工艺学课程设计减速箱夹具设计报告粗镗输入轴承孔指导老师:目录第一章二级圆锥齿轮概述第二章图纸技术要求分析第三章计算生产纲领确定生产类型第四章材料、毛坯制造方法的选择及毛坯图1 材料选择2毛坯的制造方法3毛坯的加工余量4毛坯图第五章定位基面的选择及分析第六章加工工作量及工艺手段组合第七章划分加工阶段,大致工艺过程1 上箱体加工工艺过程卡2 下箱体加工工艺过程卡3 合箱加工工艺过程卡第八章粗镗输入轴承孔机械加工及夹具设计1 机床选择刀具选择切削液2 加工余量及精度等级3 切削参数4 切削力的计算机动时间及单位时间定额5 机座结合面铣削加工工序卡6 夹紧方案设计7夹紧力计算8 夹紧元件设计9气压系统及元件的选择计算10气动系统回路及其PLC 控制电路、电路分析11 支承板、挡销设计等其他零件设计第九章参考资料第十章实习心得二级圆锥齿轮减速器设计第一章二级圆锥齿轮概述减速器减速器在原动机和工作机或执行机构之间起匹配转速和传递扭矩的作用,在现代机械中应用极为广泛,是原动机和工作机之间的独立的闭式传动装置。
减速器是一种相对精密的机械。
减速器按用途可分为齿轮减速器;蜗杆减速器;齿轮—蜗杆减速器;行星齿轮减速器。
本次设计任务为二级圆锥齿轮减速器设计。
一.二级圆锥齿轮减速器特点比起二级圆柱齿轮减速器,二级圆锥齿轮可以运用在输入轴与输出轴成角度的时候。
并且由于二级减速,使得效率更高。
二、二级圆锥齿轮减速器的结构、零件介绍1)减速器的结构二级圆锥齿轮减速器主要结构包括:箱体(箱盖、机座)、圆锥齿轮。
2)减速器的应用范围减速机的操做范围广泛,从交通工具的船舶,汽车,机车,构筑用的重型机具,机器财产所用的减工机具。
选择蜗杆和蜗轮材料组合时,不但要求有足够的强度,而且要有良好的减摩、耐磨和抗胶合的能力。
3)箱体的结构、特点此减速器箱体结构形状复杂,壁薄,外部有多孔多加强筋的薄壁结构。
有精度要求高的多个平面、轴承孔系、螺孔等需要加工。
为了便于安装内部部件,同时为了铸造方便、节省成本,该减速箱的箱体做成剖分式。
由机座和机盖组成。
箱体结构图如下:第二章图纸技术要求分析由图纸可知,机盖、基座的生产工艺有以下几点基本技术要求:1)减速器箱体铸成后,应用清砂机清洗铸件并进行时效处理;2)机盖和基座合箱后,边缘应平齐,相互错位每边不大于2mm;3)应检查基座结合面的密封性,用0.005mm塞尺塞入深度不大于结合面宽度的1/3,用涂色法去检查接触面积到每平方厘米不少于一个斑点;4)与基座连接打上定位销后,进行镗孔,此时接合面处禁止放各种衬垫;5)机械加工未标注的偏差尺寸精度为IT12;6)铸造尺寸精度为IT18;7)未标明倒角为C3,粗糙度为Ra12.5;8)未标组铸造倒角半径为R=5~10mm;9)机盖结合面粗糙度为Ra1.6,平面度为0.06;10)输入(出)轴孔两端面与输入(出)轴孔中心线的垂直度为0.10,粗糙度为Ra3.2;11)窥视口面粗糙度为Ra12.5;12)输出(入)轴承孔的粗糙度为Ra1.6;13)输出轴承孔的圆柱度为0.02,同轴度为0.02;14)输出轴承孔上偏差0.040,下偏差为0;15)基座不得漏油;经过建模对图纸中尺寸的标注,公差配合的制定,形位公差,表面粗糙度的分析整合,有以下几点当重点注意:①结合面加工中,应在保证平面度0.06和粗糙度Ra1.6的要求下,采取合理的加工方法,以满足密封性的检测;②加工轴承孔端面和端面时候,需合箱加工,才能满足所有垂直度的要求;③为了减少换刀次数,箱体的紧固孔尺寸规格应保持一致。
第三章计算生产纲领确定生产类型该零件年产量为10000件,在每台产品中的数量为1件,废品率废品率为3%,备品率为5%。
由生产纲领计算公式 N=Q×n(1+α+β)式中 Q ——年产量(件/年)N ——该零件在每台产品中的数量(件/台)α——废品率Β——备品率计算出N后按表6-1确定生产类型计算得:N=10000×1×(1+3%+5%)=10800查表《机制工艺生产实习及课程设计》中表6-1同一零件的年产量生产类型重型零件中型零件轻型零件单件生产1`5 1~10 1~100小批生产5~10 10~200 100~500中批生产100~300 200~500 500~5000大批生产300~1000 500~5000 5000~50000大量生产1000以上5000以上50000以上结论:由此可以确定生产类型为大量生产。
第四章材料、毛坯制造方法的选择及毛坯图一.材料选择由于减速器箱体结构复杂,并有凸台,凹槽等壁厚较薄的结构,通过查阅了解灰口铸铁的特点如下:1.有一定的强度,但塑性和韧性低,这种性能特点与石墨本身性能及其在铸铁组织形态有关。
2.有良好的减震性,能有效地吸收机器震动的能量。
3.良好地润滑性。
4.良好地导热性能,由于石墨本省就是良好地导体。
5.熔炼方便,流动性好,铸件不易产生开裂。
由此可以确定选择抗缺敏感性,减震性,耐磨性优良,切削性能好和成本低的型号为HT200的灰铸铁。
若无HT200,可以采用球墨铸铁,型号为QT400-15或QT400-18,其特点是焊接性和切削性能好,常温时冲击韧度高,脆性转变温度低,低温韧性好。
采用热处理:为了消除铸件在铸造冷却过程中产生的内应力,防止铸件变形或开裂,采用消除内应力退火热处理工艺二.毛坯的制造方法一般地,毛坯的制造方法有两种,即砂型铸造和金属模铸造。
但这两种铸造方法的特点和适用范围大不相同。
对于砂型铸造,它是传统的铸造方法,适用于各种形状、大小、批量及各种合金铸件的生产,其特点是成本低、加工余量大、生产率低;而对于金属模铸造,它适用于以非铁合金为主、大批大量生产的中、小型铸件,其特点是成本高、加工余量小、生产率高。
但是就减速器箱体的铸造来说,应该采用砂型铸造。
砂型铸造分型面的选择原则(1)应尽量使分型面平直、数量小。
(2)应避免不必要的型芯和活块,以简化造型工艺。
(3)应尽量使铸件全部或大部分置于箱下。
三.毛坯的加工余量以下的数据均来自《金属机械加工工艺人员手册》上海科技学术出版社 1979年版从书中可以得到灰铸铁的表层厚度为1—4mm,这里选择2mm,由刀具保护的需要,余量要比表层的厚度大一些。
所设计的减速器尺寸精度和表面光洁度要求要求较高,大批大量生产,由JZ67-62规定,选择的铸件精度等级为2级。
由表5-5铸件的公称重量200~500公斤,铸件的公称重量偏差为6%二级精度铸铁件的机械加工余量1. 机盖的加工余量凸台面厚度为80mm 由于结合面以凸台顶面为定位基面由表5-5机盖结合面的加工余量为5.0mm凸台的顶面的加工余量取3.5mm机盖宽度为550mm,加工余量取5.5mm 故毛坯长 1190 由表5-5取加工余量为6.5mm,故毛坯长 1190 +6.5=1196.5mm宽 520+2×5.5=531mm高 370+5.0+3.5=378.5mm2. 机座的加工余量与机盖相同的查表法毛坯长度1290mm 由表5-5 长度方向的加工余量为6.5mm宽度与520mm 加工余量5.5mm厚度为400mm 由表5-5得到顶面(结合面)的加工余量5.0mm ,底面的加工余量5.5mm 毛坯长 1190+6.5=1196.5mm,宽 520+2×5.5=531mm高度方向加工余量 400+5.0+5.5=410.5mm鞋油口加工余量为由表5-56注解取孔的加工余量为2mm四.毛坯图第五章定位基面的选择及分析由《机械制造工艺学》可知,定位基准包括粗基准与精基准,所谓粗基准,即在机械加工的第一道工序中,只能用毛坯上未经加工的表面作为基准。
而在随后的工序中,用加工过的表面作为定位基准,称为精基准。
我们先确定精基准,然后确定粗基准。
选择原则:精基准:“基准重合”原则“基准统一”原则“自为基准”原则“互为基准”原则并且在精基准选择过程中,应保证工件定位准确、夹紧可靠、操作方便等。
减速器上箱盖通常以凸台面、结合面作为精基准,下箱体通常以底面和两定位销孔为精基准。
在加工上箱盖时,以凸台面为精基准粗铣、半精铣、精铣结合面。
以结合面为精基准时铣视口端面、钻孔、攻丝,钻起盖螺纹孔、攻丝。
只有加工结合面时才以凸台为精基准,因此满足“基准统一”原则。
下箱体则以底面和两定位销孔为精基准,这种选择定位基准的方法便于夹紧,工件夹紧变形小,易于实现自动定位和自动夹紧,且无在基准不重合误差。
粗基准:在选择粗基准的时候需要考虑两个问题:一是保证加工面与不加工面之间的相互位置精度要求;二是合理废品各加工面的加工余量。
箱盖和机座都以结合面为粗基准加工底面。
以加工出的结合面为精基准,加工分布在箱盖和箱座两个不同部分上的很不规则的轴承孔的毛坯孔,以及油孔、连接孔等。
这样可以保证对合面凸缘厚薄均匀,减少箱体合装时对合面的变形。
各加工面基准表工件工序内容定位基准箱盖粗铣箱盖连接螺栓凸台面箱盖的结合面为粗基准粗精铣箱盖结合面箱盖的凸台面为精基准粗铣窥视孔端面箱盖的结合面为精基准钻起吊螺钉孔箱盖的结合面为精基准钻窥视孔台阶面螺钉孔箱盖的结合面为基准面攻起吊螺钉孔和窥视孔台阶面螺钉孔箱盖的结合面为精基准箱座粗铣机座底面机座的结合面为粗基准粗精铣机座结合面机座底面为精基准精铣机座底面机座底面为精基准粗铣机座凸台面机座底面为精基准粗铣排油口台阶面机座底面为精基准粗铣游标台阶面机座底面为精基准钻地脚螺栓孔机座底面为精基准钻排油螺栓孔和游标孔机座底面为精基准攻地脚螺栓孔、排油螺栓孔和游标空机座底面为精基准合箱后粗精镗蜗杆轴承孔机座底面为精基准,采用一面两销定位粗精镗蜗轮轴承孔机座底面为精基准,采用一面两销定位粗精镗齿轮轴承孔机座底面为精基准,采用一面两销定位粗精铣蜗杆轴承孔端面机座底面为精基准,采用一面两销定位粗精铣蜗轮轴承孔端面机座底面为精基准,采用一面两销定位粗精铣齿轮轴承孔端面机座底面为精基准,采用一面两销定位锪上机座连接螺栓沉头座孔机座底面为精基准,采用一面两销定位钻轴承盖孔机座底面为精基准,采用一面两销定位第六章加工工作量及工艺手段组合1. 机床与机盖结合面(5mm)加工工序:粗铣------半精铣------精铣工序余量:粗铣 3mm 半精铣 1.4mm 精铣 0.6mm工序公差:毛坯±2.0 粗铣 IT12 半精铣IT18 精铣IT7工序尺寸:精铣021.025+mm Ra1.6 半精铣033.06.25+mm Ra 6.3 粗铣21.027+mm Ra12.5 毛坯20.020.0-30+mm2. 两轴承孔端面1) 输出轴承孔两端面A.加工工序:粗铣—精铣B.工序余量:粗铣 3.5mm 精铣 0.5mmC.工序公差:毛坯±3.0mm 粗铣IT10 精铣IT7D.工序尺寸:精铣07.0520+mm Ra3.2 粗铣28.05.520+ mm Ra 12.5 毛坯30.030.0-524+ mm 2) 输入轴轴承孔端面A.加工工序:粗铣—精铣B.工序余量:粗铣 3.5mm 精铣 0.5mmC.工序公差:毛坯±2.5mm 粗铣IT10 精铣 IT7D.工序尺寸:精铣063.0420+mm Ra 3.2 粗铣25.05.420+mm Ra 12.5 毛坯5.25.2-424+mm3) 视窗面A加工工序:粗铣B.工序余量:粗铣2mmC工序公差:毛坯±1.2mm 粗铣IT12D.工序尺寸:粗铣12.05+mm Ra12.5 毛坯2.12.1-7+mm4) 机盖凸台面A加工工序:粗铣B.工序余量:粗铣3.5mmC.工序公差:毛坯±1.5mm 粗铣IT12D.工序尺寸:粗铣3.080+mm Ra12.5 毛坯5.15.1-83+mm5) 输入(出)轴承孔I 输入轴轴承孔加工工序:粗镗—半精镗—精镗工序余量:粗镗3mm 半精镗1.3mm 精镗 0.7mm工序公差:毛坯±1.5 粗镗 IT12 半精镗 IT10 精镗 IT7工序尺寸:精镗Φ04.0150+mm Ra1.6 半精镗Φ16.03.149+ mm Ra 3.2精镗Φ4.0148+mm Ra12.5 毛坯Φ5.15.1145+-mmII 中间轴轴承孔A加工工序:粗镗—半精镗—精镗B工序余量:粗镗3mm 半精镗1.3mm 精镗 0.7mmC工序公差:毛坯±1.5 粗镗 IT12 半精镗 IT10 精镗 IT7D工序尺寸:精镗Φ04.0150+mm Ra1.6 半精镗Φ16.03.149+ mm Ra 3.2精镗Φ4.0148+mm Ra12.5 毛坯Φ5.15.1145+-mmIII 输出轴轴承孔加工工序:粗镗—半精镗—精镗工序余量:粗镗3mm 半精镗2.3mm精镗 0.7mm 工序公差:毛坯±1.5mm 粗镗 IT10 精镗 IT7D工序尺寸:精镗Φ046.0200+mm Ra1.6 半精镗Φ185.03.199+ mm Ra 3.2精镗Φ46.0197+mm Ra12.5 毛坯Φ5.15.1194+-mmIV 机座底面A加工工序:粗铣B工序余量4.5mmC工序公差:毛坯±1.2mm 粗铣IT12D工序尺寸:粗铣25.040+mm 毛坯2.12.1-5.44+mm第七章划分加工阶段,大致工艺过程箱盖加工工艺过程卡厂名机械加工过程卡产品型号零件名称零件号减速器箱盖毛坯种类铸件材料HT200 毛坯尺寸每一毛坯1 每台件数 1单位重量(公斤)可制件数工序车间工序内容设备工艺装备名称与编号工时(分)夹具刃具量具辅具准备单件1 铸工毛坯铸造,清砂2 喷丸3 铸工人工时效处理4 金工铣箱盖凸台面。