电缆制造生产工艺分析研究
电缆生产工序

电缆生产工序一、原材料准备电缆生产的第一步是准备原材料。
通常情况下,电缆的主要原材料包括导体、绝缘材料、护套材料和填充物。
导体通常由铜或铝制成,绝缘材料可以是聚乙烯、聚氯乙烯等,护套材料可以是聚氯乙烯或聚氨酯等。
在准备原材料的过程中,需要对原材料进行检验和测试,确保其质量符合要求。
二、导体制造导体是电缆的核心部分,负责传输电流。
导体的制造通常包括铜或铝的拉丝和绞合。
首先,将铜或铝材料加热至适当温度,然后通过模具将其拉制成所需的直径。
接下来,将多根导体绞合在一起,形成电缆的导体部分。
导体制造的关键是确保导体的直径和绞合的紧密度符合设计要求。
三、绝缘层制造绝缘层是保护导体的重要部分,防止电流泄漏和短路。
绝缘层的制造通常采用挤出工艺。
在这个过程中,将绝缘材料加热至熔化状态,然后通过挤出机将其挤出成所需的形状。
挤出后的绝缘层需要经过冷却和固化,以确保其稳定性和可靠性。
四、护套制造护套是保护电缆的外层,具有防水、耐磨和耐腐蚀等功能。
护套的制造通常采用挤出或浇注工艺。
挤出工艺与绝缘层制造类似,将护套材料加热至熔化状态,然后通过挤出机将其挤出成所需的形状。
浇注工艺则是将护套材料直接注入电缆外部,然后通过冷却和固化来形成护套。
五、填充物安装填充物的作用是填充电缆内部的空隙,增加电缆的机械强度和耐压能力。
填充物通常是一种柔软的材料,如聚丙烯蜡。
在电缆制造的过程中,填充物被注入电缆内部,并通过挤压和压实来确保其均匀分布。
六、成品检验电缆生产完成后,需要进行成品检验。
成品检验的目的是确保电缆的质量符合标准要求。
常见的成品检验项目包括外观检查、电气性能测试、机械性能测试等。
只有通过成品检验的电缆才能出厂销售。
总结:电缆生产工序包括原材料准备、导体制造、绝缘层制造、护套制造、填充物安装和成品检验等环节。
每个环节都需要严格控制和检验,以确保电缆的质量和性能符合要求。
电缆作为现代社会中不可或缺的基础设施,其生产工序的规范和严谨对于保障电力传输和通信的稳定运行至关重要。
电缆的生产工艺

电缆的生产工艺电缆的生产工艺是指将金属导体、绝缘体和护套材料组合在一起以制造电缆的过程。
电缆的生产工艺主要包括材料准备、导体制造、绝缘层制造、护套制造和成缆五个主要步骤。
首先是材料准备。
电缆的制造需要准备各种材料,如金属导体、绝缘体和护套材料。
导体材料通常是铜或铝,通过压延、拔丝等方法加工成所需直径和形状的导体。
绝缘层材料可以是PVC、交联聚乙烯或硅胶等,护套材料可以是PVC、PE或铝塑复合材料等。
接下来是导体制造。
导体通常是由多股细丝或扁平带状导体组成。
导体制造过程中需要将细丝或扁平带拉拔成规定直径或宽度,并根据需要进行扭绞或编织,以提高导体的柔韧性和电流传输能力。
然后是绝缘层制造。
绝缘层是为了对导体进行绝缘保护,防止漏电和电磁干扰。
绝缘层的制造通常涉及到挤出、涂覆或缠绕等工艺。
挤出是最常用的方法,即通过将绝缘材料挤压成希望的形状和尺寸,以覆盖导体。
接下来是护套制造。
护套的作用是对电缆进行保护,防止外界物体的损害和电缆的机械应力。
护套通常是通过挤出、涂覆或包覆等工艺制造而成的。
制造护套时需要注意材料的选择,以保证其具有耐压、耐磨等性能。
最后是成缆。
成缆是将多根绝缘线芯按照一定规律组合在一起,并固定在相对位置上。
成缆通常分为二次绞合和防火带包覆两个步骤。
二次绞合是将多根绝缘线芯进行扭绞,以提高电缆的柔韧性和抗干扰性。
防火带包覆是为了增加电缆的防火性能,通常在成缆后对电缆进行包覆。
综上所述,电缆的生产工艺包括材料准备、导体制造、绝缘层制造、护套制造和成缆五个主要步骤。
每个步骤都需要选择合适的材料和工艺,以制造出满足不同需求的电缆产品。
电缆的生产工艺对其品质和性能有着重要影响,因此需要在生产过程中严格控制每个环节。
电线电缆生产工艺流程
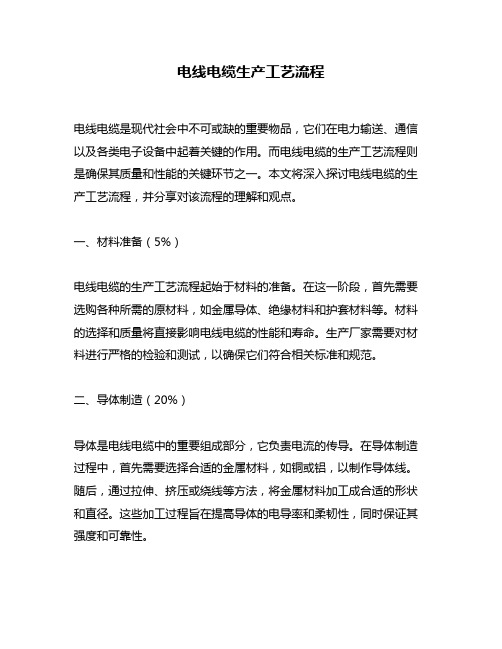
电线电缆生产工艺流程电线电缆是现代社会中不可或缺的重要物品,它们在电力输送、通信以及各类电子设备中起着关键的作用。
而电线电缆的生产工艺流程则是确保其质量和性能的关键环节之一。
本文将深入探讨电线电缆的生产工艺流程,并分享对该流程的理解和观点。
一、材料准备(5%)电线电缆的生产工艺流程起始于材料的准备。
在这一阶段,首先需要选购各种所需的原材料,如金属导体、绝缘材料和护套材料等。
材料的选择和质量将直接影响电线电缆的性能和寿命。
生产厂家需要对材料进行严格的检验和测试,以确保它们符合相关标准和规范。
二、导体制造(20%)导体是电线电缆中的重要组成部分,它负责电流的传导。
在导体制造过程中,首先需要选择合适的金属材料,如铜或铝,以制作导体线。
随后,通过拉伸、挤压或绕线等方法,将金属材料加工成合适的形状和直径。
这些加工过程旨在提高导体的电导率和柔韧性,同时保证其强度和可靠性。
三、绝缘处理(25%)绝缘是保护电线电缆导体的关键环节。
在绝缘处理阶段,导体被包覆在绝缘材料中,以防止电流外泄和短路等问题的发生。
常用的绝缘材料包括聚氯乙烯(PVC)、交叉链聚乙烯(XLPE)以及橡皮等。
绝缘材料的选择取决于电线电缆的具体应用环境和要求。
在绝缘处理过程中,绝缘材料需要经过挤出、浸渍、包覆等步骤,以确保其与导体的良好粘结和完整性。
四、编织护套(20%)编织护套是为电线电缆提供机械保护和防护的重要部分。
它既可以增强电线电缆对拉力和挤压的抵抗能力,又能够防止外界环境因素的侵入,如水、油和化学物质等。
通常,编织护套采用聚酯、聚酰胺或金属丝等材料制成。
编织护套的加工过程包括编织、包覆和压实等步骤,以确保其良好的柔韧性和抗剥离性。
五、成品检验和包装(15%)电线电缆的生产工艺流程的最后阶段是成品检验和包装。
在这一阶段,生产厂家将对电线电缆的质量和性能进行全面检验。
这包括导体电阻、绝缘电阻、耐压和耐热性能等方面的测试。
只有通过了严格的检验,电线电缆才能进入下一阶段的包装和出厂销售。
浅谈辐照交联聚乙烯电线电缆的生产工艺
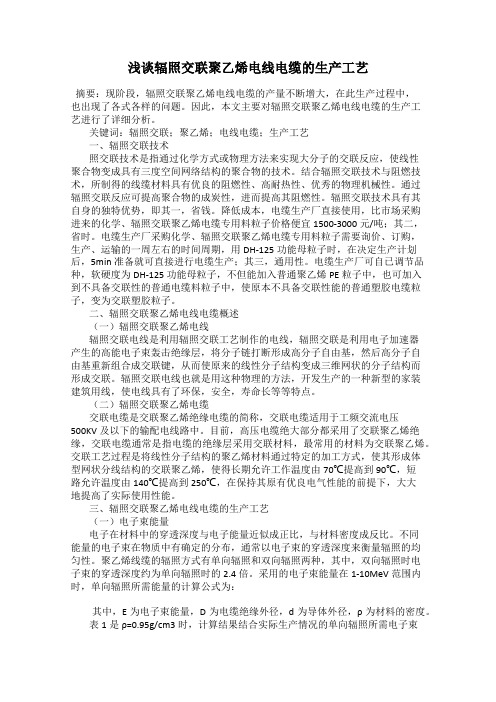
浅谈辐照交联聚乙烯电线电缆的生产工艺摘要:现阶段,辐照交联聚乙烯电线电缆的产量不断增大,在此生产过程中,也出现了各式各样的问题。
因此,本文主要对辐照交联聚乙烯电线电缆的生产工艺进行了详细分析。
关键词:辐照交联;聚乙烯;电线电缆;生产工艺一、辐照交联技术照交联技术是指通过化学方式或物理方法来实现大分子的交联反应,使线性聚合物变成具有三度空间网络结构的聚合物的技术。
结合辐照交联技术与阻燃技术,所制得的线缆材料具有优良的阻燃性、高耐热性、优秀的物理机械性。
通过辐照交联反应可提高聚合物的成炭性,进而提高其阻燃性。
辐照交联技术具有其自身的独特优势,即其一,省钱。
降低成本,电缆生产厂直接使用,比市场采购进来的化学、辐照交联聚乙烯电缆专用料粒子价格便宜1500-3000元/吨;其二,省时。
电缆生产厂采购化学、辐照交联聚乙烯电缆专用料粒子需要询价、订购,生产、运输的一周左右的时间周期,用DH-125功能母粒子时,在决定生产计划后,5min准备就可直接进行电缆生产;其三,通用性。
电缆生产厂可自已调节品种,软硬度为DH-125功能母粒子,不但能加入普通聚乙烯PE粒子中,也可加入到不具备交联性的普通电缆料粒子中,使原本不具备交联性能的普通塑胶电缆粒子,变为交联塑胶粒子。
二、辐照交联聚乙烯电线电缆概述(一)辐照交联聚乙烯电线辐照交联电线是利用辐照交联工艺制作的电线,辐照交联是利用电子加速器产生的高能电子束轰击绝缘层,将分子链打断形成高分子自由基,然后高分子自由基重新组合成交联键,从而使原来的线性分子结构变成三维网状的分子结构而形成交联。
辐照交联电线也就是用这种物理的方法,开发生产的一种新型的家装建筑用线,使电线具有了环保,安全,寿命长等等特点。
(二)辐照交联聚乙烯电缆交联电缆是交联聚乙烯绝缘电缆的简称,交联电缆适用于工频交流电压500KV及以下的输配电线路中。
目前,高压电缆绝大部分都采用了交联聚乙烯绝缘,交联电缆通常是指电缆的绝缘层采用交联材料,最常用的材料为交联聚乙烯。
电缆工艺技术原理

电缆工艺技术原理电缆工艺技术原理是指制造电缆所采用的一系列技术和方法,旨在保证电缆结构的合理性、性能的稳定性和工艺的可靠性。
本文将介绍电缆工艺技术原理的主要内容,包括电缆制造的原材料选择、绝缘层和护套材料的选择、电缆生产过程的主要工艺等。
首先,电缆制造的原材料选择是电缆工艺技术的基础。
电缆的导体主要是铜或铝,其选择应考虑电导率、拉伸强度和耐腐蚀性等因素。
绝缘层主要采用聚乙烯、交联聚乙烯、交联聚丙烯等材料,其选择应考虑绝缘电阻、绝缘强度、耐热性和耐候性等因素。
护套材料主要有聚氯乙烯、聚乙烯、交联聚乙烯等,其选择应考虑机械强度、耐热性、耐候性和耐化学腐蚀性等因素。
其次,绝缘层和护套材料的选择是保证电缆性能稳定的关键。
绝缘层主要是为了隔离导体和地面或其他导体之间的介质,防止漏电和电压损耗。
护套材料主要是为了保护电缆免受机械损伤,防止外部介质的侵蚀。
不同种类的电缆根据使用环境和要求选择不同的绝缘层和护套材料,以满足其特定的工作条件。
电缆生产过程的主要工艺包括导体预处理、绝缘层和护套挤出、致密化和交联等。
导体预处理主要是对导体表面进行清洁和处理,确保导体表面的平整度和光洁度。
绝缘层和护套挤出是将选定的材料挤压到导体上,形成均匀的绝缘层和护套。
致密化是将挤出的绝缘层和护套经过冷却和压缩处理,使其更加致密、均匀。
交联是对绝缘层和护套材料进行化学或物理交联处理,提高其耐热性、绝缘强度和耐候性。
电缆工艺技术原理的核心是通过合理的选择材料和采用适当的工艺方法,确保电缆的性能稳定和可靠。
电缆的设计和制造需要考虑多种因素,如电力传输能力、机械强度、热稳定性、耐候性和环境适应性等。
在电缆工艺技术原理的指导下,可以生产出符合不同使用条件和要求的电缆产品,满足社会和工业对电能传输的需求。
总之,电缆工艺技术原理对于电缆制造的过程和品质具有重要的影响。
通过合理的原材料选择、绝缘层和护套材料的选择以及相关的工艺流程,可以制造出稳定可靠的电缆产品,满足不同使用环境和要求的电力传输需求。
电缆的生产工艺流程

电缆的生产工艺流程
《电缆的生产工艺流程》
电缆的生产工艺是一个复杂的过程,需要经过多道工序才能完成。
下面是电缆的生产工艺流程:
1. 原料准备:首先,需要准备各种原料,包括金属导线、绝缘材料、护套材料等。
这些原料需要经过严格的品质检验,确保符合生产要求。
2. 金属导线生产:金属导线是电缆的主要导电材料,通常采用铜或铝等金属制造。
通过拉丝、绞线等工艺将金属原料加工成符合规格的导线。
3. 绝缘材料处理:绝缘材料是用来包裹金属导线,防止电流泄露的材料。
通常采用塑料或橡胶等绝缘材料,需要通过挤出、涂覆等工艺加工成成型。
4. 绞合:将金属导线和绝缘材料按照设计要求进行编绞,形成电缆的基本结构。
5. 护套加工:电缆的护套是用来保护电缆免受外界环境影响的材料,通常采用聚乙烯、聚氯乙烯等材料,需要经过挤出、注塑等工艺进行成型。
6. 整体成型:将编绞好的电缆芯线和护套进行整体成型,形成成品电缆。
7. 检验和包装:对成品电缆进行质量检验,确保其符合标准要求。
然后进行包装,准备出厂。
以上就是电缆的生产工艺流程,每一个环节都需要严格把关,确保生产出的电缆具有良好的品质和性能。
中高压交联聚乙烯绝缘电缆导体制造工艺和过程质量控制研究

中高压交联聚乙烯绝缘电缆导体制造工艺和过程质量控制研究摘要:为提高交联聚乙烯绝缘电缆产品质量,此次研究以中高压交联聚乙烯绝缘电缆导体为中心,分别对制造工艺与过程质量控制进行研究,结合工艺优化结果分析,认识到交联聚乙烯绝缘电缆导体生产工艺优化的重要性,并明确生产过程质量控制细节,以此为相关人员提供参考。
关键词:交联聚乙烯绝缘电缆导体;压轮滚压法;分裂导体;外径偏差中高压交联聚乙烯绝缘电缆导体生产工艺和过程质量控制,是发挥其使用性能的重要前提。
作为电力线路中应用量最大的电缆类型,交联聚乙烯绝缘电缆在电气性能、机械性能及耐热性等方面具有突出优势。
交联聚乙烯绝缘电缆生产期间,导体生产是关键部分,生产工艺也在不断优化完善。
加大对交联聚乙烯电缆导体生产工艺研究力度,科学控制生产过程质量,可进一步提高交联聚乙烯绝缘电缆质量与稳定性。
1.交联聚乙烯绝缘电缆导体制造工艺优化中高压交联聚乙烯绝缘电缆导体生产,以圆形压紧线芯为主。
实际加工过程中,将导体集中绞合并紧压,计算紧压系数要求必须达到规定标准。
中高压交联聚乙烯绝缘电缆导体生产工艺复杂,加上影响因素多,质量要求严格,因此涉及多种制造工艺。
以下对交联聚乙烯绝缘电缆导体制造工艺进行详细研究:1.1压轮滚压法此方法的应用需借助多组压轮配合完成,将绞线按要求紧压处理,为保证紧压效果,需应用分层紧压法,对绞线按照2-4组分层设置,并逐层紧压。
随着交联聚乙烯绝缘电缆应用范围扩大、需求量逐年增加,对导体生产要求越来越严格,分层紧压法应用备受关注。
但是分层紧压法实际应用中操作难度较大,尤其是绞线变形量控制方面,紧压度控制必须适量,过紧、过松都不能保证导体生产质量[1]。
若紧压度不足,导体生产会出现内层紧密性差,外观形成“灯笼”状;若紧压度过紧,则会增加单排绞线被挤出或排序错乱的风险。
这方面需要操作人员在生产控制过程中提高重视。
待绞线紧压操作完毕,检测绞线挤压整体填充系数,绞合度是否达到90%-96%。
电缆生产工序漫谈:导体的绞合

电缆生产工序漫谈:导体的绞合绞合(绞线):将多根直径较小的单丝按一定的规则绞制成较大截面的导电线芯的工艺过程。
1.绞线分正规绞合和非正规绞合两种。
正规绞合可分为正规同心式单线绞合和正规同心式股线绞合正规同心式单线绞合:⑴ 普通绞线:用同一直径的单线,按同心圆的方式,一层一层地有规则地绞合,每一层的绞向都相反。
⑵ 组合绞线:它是由相同直径、不同材料或不同直径、不同材料的单线绞制而成。
(代表产品如架空导线)正规同心式股线绞合:是由多股普通绞线或束线进行同心式绞合的绞线。
非正规绞合(束线):由多根单线以同一绞向不按绞合规律一起绞合而成的绞线,各单线之间的位置互相不固定,束丝的外形也很难保持圆整。
2、束丝和普通绞线的最大区别是:普通绞线的各单丝都有一个固定的位置,一层一层地有规则地绞合;束丝的各单丝之间没有固定的位置不按绞合规律一起绞合而成。
3、非正规绞合(束线)的特点:由于束线中各单线均向一个方向扭绞,在弯曲时各单线之间滑动余量很大,抗弯曲力小,所以束线的弯曲性能特别好,对于需要柔软、并用语经常移动的场合的电线电缆产品就采用束线作导电线芯。
4.绞合线芯的特点:⑴ 柔软性好;采用多根较小直径的单丝绞合成的线芯可提高电缆的弯曲能力,便于电线电缆的加工制造和安装敷设。
⑵ 稳定性好;多根单丝按一定方向和绞合规则绞合成的线芯,由于在绞线中每一根单丝的位置均轮流处在绞线上部的伸长区和绞线下部的压缩区,当绞线弯曲时不会发生变形。
⑶ 可靠性好;用单线做电线电缆的导体,容易受材料的不均匀性或绞制中产生的缺陷而影响导电线芯的可靠性,用多根单线绞合成的线芯这样的缺陷就得到了分散,不会集中到导体的某一个点上,导电线芯的可靠性就强的多了。
⑷ 强度高;同样截面大小的单线与多根绞合线芯相比较,绞合线芯的强度要比单线高。
5、术语解释:(1)节距:单丝延轴向前进一周的距离。
(2)节径比:绞线节距长度与绞线直径的比值。
(3)、节距与绞线柔软度的关系:节距越小绞线的柔软度越好,相反节距越大绞线的柔软度越差。
电线电缆的生产工艺
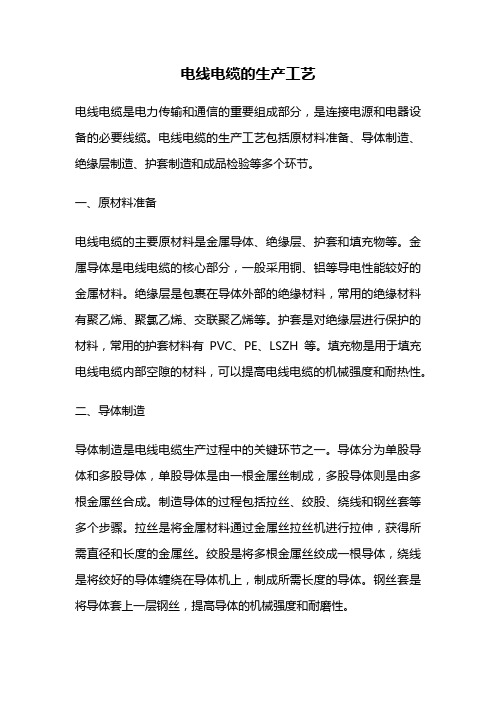
电线电缆的生产工艺电线电缆是电力传输和通信的重要组成部分,是连接电源和电器设备的必要线缆。
电线电缆的生产工艺包括原材料准备、导体制造、绝缘层制造、护套制造和成品检验等多个环节。
一、原材料准备电线电缆的主要原材料是金属导体、绝缘层、护套和填充物等。
金属导体是电线电缆的核心部分,一般采用铜、铝等导电性能较好的金属材料。
绝缘层是包裹在导体外部的绝缘材料,常用的绝缘材料有聚乙烯、聚氯乙烯、交联聚乙烯等。
护套是对绝缘层进行保护的材料,常用的护套材料有PVC、PE、LSZH等。
填充物是用于填充电线电缆内部空隙的材料,可以提高电线电缆的机械强度和耐热性。
二、导体制造导体制造是电线电缆生产过程中的关键环节之一。
导体分为单股导体和多股导体,单股导体是由一根金属丝制成,多股导体则是由多根金属丝合成。
制造导体的过程包括拉丝、绞股、绕线和钢丝套等多个步骤。
拉丝是将金属材料通过金属丝拉丝机进行拉伸,获得所需直径和长度的金属丝。
绞股是将多根金属丝绞成一根导体,绕线是将绞好的导体缠绕在导体机上,制成所需长度的导体。
钢丝套是将导体套上一层钢丝,提高导体的机械强度和耐磨性。
三、绝缘层制造绝缘层是电线电缆的重要组成部分,用于包裹在导体外部,防止电流外泄。
绝缘层制造的过程包括挤出、包覆、交联等多个步骤。
挤出是将绝缘材料通过挤出机加热融化,然后通过模具挤出成所需直径和长度的绝缘管。
包覆是将绝缘管套在导体上,形成绝缘层。
交联是将绝缘层通过热交联或辐照交联等方式,提高绝缘层的耐热性和机械强度。
四、护套制造护套是对绝缘层进行保护的材料,常用的护套材料有PVC、PE、LSZH等。
护套制造的过程包括挤出、包覆、压花等多个步骤。
挤出是将护套材料通过挤出机加热融化,然后通过模具挤出成所需直径和长度的护套管。
包覆是将护套管套在绝缘层外部,形成护套。
压花是对护套进行压花处理,提高护套的耐磨性和外观质量。
五、成品检验成品检验是电线电缆生产的最后一道环节,包括外观检验、电性能测试、机械性能测试等多个方面。
电线电缆的制造工艺

电线电缆的制造工艺电线电缆是以长度为基本计量单位,所有电线电缆都是从导体加工开始,在导体的外围一层一层地加上绝缘、屏蔽、、成缆、护层等而制成电线电缆产品。
产品结构越复杂,叠加的层次就越多。
电线电缆产品制造的工艺特性:1.大长度连续叠加组合生产方式大长度连续叠加组合生产方式,对电线电缆生产的影响是全局性和控制性的,这涉及和影响到:(1)生产工艺流程和设备布置生产车间的各种设备必须按产品要求的工艺流程合理排放,使各阶段的半成品,顺次流转。
设备配置要考虑生产效率不同而进行生产能力的平衡,有的设备可能必须配置两台或多台,才能使生产线的生产能力得以平衡。
从而设备的合理选配组合和生产场地的布置,必须根据产品和生产量来平衡综合考虑。
(2)生产组织管理生产组织管理必须科学合理、周密准确、严格细致,操作者必须一丝不苟地按工艺要求执行,任何一个环节出现问题,都会影响工艺流程的通畅,影响产品的质量和交货。
特别是多芯电缆,某一个线对或基本单元长度短了,或者质量出现问题,则整根电缆就会长度不够,造成报废。
反之,如果某个单元长度过长,则必须锯去造成浪费。
(3)质量管理大长度连续叠加组合的生产方式,使生产过程中任何一个环节、瞬时发生一点问题,就会影响整根电缆质量。
质量缺陷越是发生在内层,而且没有及时发现终止生产,那么造成的损失就越大。
因为电线电缆的生产不同于组装式的产品,可以拆开重装及更换另件;电线电缆的任一部件或工艺过程的质量问题,对这根电缆几乎是无法挽回和弥补的。
事后的处理都是十分消极的,不是锯短就是降级处理,要么报废整条电缆。
它无法拆开重装。
电线电缆的质量管理,必须贯串整个生产过程。
质量管理检查部门要对整个生产过程巡回检查、操作人自检、上下工序互检,这是保证产品质量,提高企业经济效益的重要保证和手段。
2.生产工艺门类多、物料流量大电线电缆制造涉及的工艺门类广泛,从有色金属的熔炼和压力加工,到塑料、橡胶、油漆等化工技术;纤维材料的绕包、编织等的纺织技术,到金属材料的绕包及金属带材的纵包、焊接的金属成形加工工艺等等。
同轴射频物理发泡电缆制造工艺分析
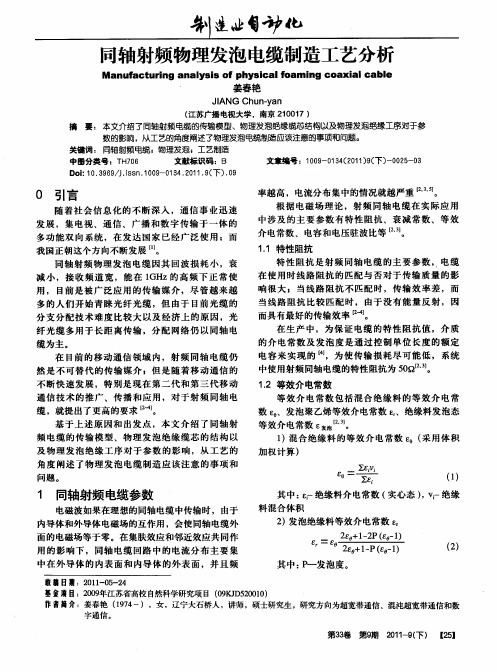
匐 似
同轴射频物理 发泡 电缆制造 工艺分析
M anu act i g f urn anal si ysi oam i g y s of ph cal f n coaxi alcabl e
姜春艳
JANG u — a I Ch n y n
( 江苏广播 电视 大学 ,南京 2 0 1 10 7) 摘 要 :本文介绍了同轴射频电缆的传输模型、物理发泡绝缘缆芯结构以及物理发泡绝缘工序对于参 数的影响 , 工艺的角度阐述了物理发泡 电缆 制造 应该注意的事项和问题 。 从 关键词 : 同轴射频电缆 ;物理发泡 ;工艺 制造 中田分 类号 :T 7 6 H 0 文献标识码 :B 文章编号 :1 0 —0 3 ( o 1 9 下) 0 5 0 9 1 4 2 l ) ( 一0 2 — 3 0
V WR = s
() 9
1 衰减常数 . 3 衰 减 常数 是 同轴 射 频 电缆 的主 要 电气 性 能 方
面 的参 数 ,它 主 要 是 反映 电磁 波 能 量 沿 着 电缆 传
响 很 大 ; 当线 路 阻 抗 不 匹配 时 ,传 输 效 率 差 ,而
我 国正朝 这个 方 向不 断发展 u。
同 轴 射 频 物 理 发 泡 电缆 因其 回 波 损 耗 小 ,衰
减 小 ,接 收 频 道 宽 , 能 在 1 z的 高 频 下 正 常 使 GH 用 , 目前 是 被 广 泛 应 用 的 传 输 媒 介 ,尽 管 越 来 越 多 的 人 们 开 始 青 睐 光 纤 光 缆 ,但 由于 目前 光 缆 的 分 支 分 配 技 术 难 度 比较 大 以及 经 济 上 的原 因 ,光 纤 光 缆 多 用 于 长 距 离 传 输 ,分配 网 络 仍 以 同 轴 电
电缆的生产工艺类型

电缆的生产工艺类型
电缆的生产工艺类型主要有以下几种:
1. 传统工艺:传统工艺主要包括绝缘、护套、编织等工序。
电线电缆的绝缘材料可以使用塑料、橡胶、聚乙烯、聚氯乙烯等材料,通过挤出、注塑、包皮等工艺进行绝缘处理。
护套可以采用类似的工艺进行加工,以增加电缆的保护性能。
编织工艺主要用于制作电缆的屏蔽层,提高电缆的抗干扰性能。
2. 拉丝工艺:电缆中的金属导体材料一般是通过拉丝工艺制成的。
拉丝工艺是将金属坯料通过连续拉伸、轧制等方法加工成所需的线材。
拉丝工艺可以提高金属导体的导电性能和力学性能。
3. 锻造工艺:锻造工艺主要用于制造高压电力电缆。
在锻造工艺中,金属材料通过加热处理后,通过锻造机械的挤压作用,使金属材料在模具内形成所需的形状和尺寸。
锻造工艺可以提高电缆的强度和耐压能力。
4. 化学法工艺:化学法工艺主要应用于特殊功能电缆的生产。
比如,光纤电缆的制造一般采用光纤拉制工艺,通过化学方法制成光纤,并利用特殊的技术将光纤包裹在护套中,形成光纤电缆。
5. 特殊工艺:特殊工艺主要是指一些特殊材料或特殊形状的电缆制作工艺。
比如,软线电缆的生产工艺中,通常会使用柔性导体和软性绝缘材料,并采用特殊
的布线方式,以便电缆可以灵活弯曲和穿过狭小的空间。
这些生产工艺类型可以根据不同的电缆要求和应用领域进行组合和调整,以满足不同需求的电缆制造。
电缆制造生产工艺初探

1 . 1电缆 行业对 铜材 的熔炼 工艺技术 非常重视 近三十年来 电缆行 业对铜 的熔炼 技术 已接近世 界先 进水平 ,国 内 目前 主要采 用三 种工艺 技术 , 即上引法 、 连 铸连扎 和浸涂 法生 产 出低氧 铜和无氧铜, 使铜的导电率达到 1 0 1 - 1 0 3 %I A C S 。目前国内中型以上的 电缆企业普遍采用上引法生产铜杆, 大型企业采用连铸连扎 , 少数企业 还采用 浸土法生 产无氧 铜。 1 . 2电缆行业与铝厂紧密合作 ,在熔冶技术上进行了研究改进, 生 产 出铝纯度 达 到 9 9 . 5 %以上 的 电工 专业 铝锭 。 目前 铝 的导 电率 为 6 1 % I A C S , 而铝材标 准 中的特二 号铝 ( 纯度 9 9 . 6 可达 到 6 2 - 6 3 %I A C S , 纯 度 9 9 . 9 9 6 %的铝 可达 6 5 %I A C S , 铝材 的技术 性 能达 到 国际先 进水 平 , 过 去 采用 的黑 铜杆 已经明令 淘汰 。 我 国首创 的在铝炼 时加入少 量稀土 材料 的稀土铝 合金 可提高 铝材 的强度 、 耐腐蚀性, 且成本低 , 最适合用于架空导线 , 此项技术处于国际 先进水平 。 2有色金属 的压力 加工和其他 工艺技术 2 . 1过去 , 电缆制造 企业 大多数 采用 队铜 、 铝锭进 行热轧 制杆 , 由于 加工 过程 中铜 、 铝 材 表面严 重 氧化 , 上个 世纪 九十 年代 后 已逐 步淘 汰 , 目前已普遍采用的是上引法 、 连铸连扎和浸涂法制杆技术。 2 . 2对铜 线的拉 制工艺 目前普 遍采用 大 、中拉制及 连续退 火工 艺 , 小线也 有采 用连 续退 火工 艺技 术 , 拉 线速 度加 快 , 尺寸 控制 精度 更 高 。 对细铜线 的控制 ,采用 了多头拉线设备以提高生产速度 。铜微细线 ( 0 . 1 0 m m及以下) 的拉制工艺与设备已经成熟。 2 3对铜 、 铝导线的绞合 , 除了过去常用的笼绞外 , 更多的是采用了 线速度更快的框绞、 叉绞、 盘绞以及管绞等工艺设备。按照交联聚乙烯 电力 电缆 对导线 需要 提高填 充系数 及表 面平整程度 的要 求 ,在 绞制过 程 中增加 了分层 紧压以及拉拔 式边绞边 拉的工艺技 术 。 2 . 4其他还有铜 导体外 镀锡 、 镀银 、 镀 镍 的工 艺技术 ; 双金属 导线伟 同 包铝、 铝 包钢 等) 工 艺技 术 ; 以及 铜 、 铝 的热压 技术 成型 , 制造扁 线 、 型材 等新 的工艺 。 2 . 5塑料 、 橡皮 及热 塑性 体 的配方 、 混 练加 工工 艺 、 塑料 的挤包 , 并 加 以材料发 泡 ( 化学 发泡 的发泡 率可达 到 4 0 %- - 5 0 %,物理 发泡 可达到 5 ∞ O 嘞 的工 艺以及交 联 交 联 、 辐照交联 工艺技术 都 已达 到 了 先进 水平 。对挤包 工艺 , 大截面导 线 的产 品( 电力 电缆1 采用 了三层 共挤 技术 , 小截 面 的产 品 ( 如 通信 电缆 的单 根 绝缘 线 芯) 采用 了 高速 挤 出机 ( 2 0 0 0 - 3 0 0 0  ̄ V S Y ) , 此外还有双头并联挤出等工艺技术。 2 6在漆包线 、 绕包线类产品中, 工艺技术也有了长足的进步和发 展 。如普遍 采用 了在烘 炉中 队废 气进行 催化燃 烧 以减 少环境 污染 的工 艺技 术 , 根据 产 品性 能要求 的需要 , 生产 内外两种 不 同性 能 的漆种 连续 涂制成复合漆包线的工艺技术 , 耐高温薄膜绕包线制造的工艺技术等。 特别是根据大型电力变压器的需要制造 巨型换味道鲜的工艺技术 , 达 到 了世 界先进水 平 。 2 . 7各种纤维的合并 、 绕包、 编织工艺技术, 采用了与纺织 、 化纤行 业相近 的工艺技 术 。 2 . 8粉状无机材料制成无机绝缘的灌注技术 ( 女 口 用于制造金属套耐
电缆生产工艺流程

一、材料准备首先,根据电缆产品的规格要求,准备所需的铜或铝线材、绝缘材料、护套材料、填充物、金属屏蔽层等原材料。
这些材料需符合国家相关标准,确保电缆质量。
二、铜、铝单丝拉制利用拉丝机将铜或铝杆材通过一道或数道拉伸模具的模孔,使其截面减小、长度增加、强度提高。
拉丝是电缆制造的首道工序,其主要工艺参数是配模技术。
三、单丝退火将拉制好的铜、铝单丝加热至一定温度,以再结晶的方式提高单丝的韧性、降低强度,符合电线电缆对导电线芯的要求。
退火工序的关键是杜绝铜丝的氧化。
四、导体的绞制将退火后的单丝进行绞合,形成导电线芯。
绞合形式分为规则绞合和非规则绞合,其中非规则绞合又分为束绞、同心复绞、特殊绞合等。
绞合过程中,可采用紧压形式,使导体形状变为半圆、扇形、瓦形和紧压的圆形,以减少导线占用面积、缩小电缆几何尺寸。
五、绝缘挤出根据电缆产品的绝缘要求,采用挤出机将绝缘材料加热熔融,通过模具挤出成实心型绝缘层。
挤出过程中,需控制偏心度、光滑度和致密度,确保绝缘层质量。
六、成缆将绞制好的导电线芯和绝缘层进行成缆,使其形成具有一定结构的电缆。
成缆过程中,可添加填充物、金属屏蔽层等材料,以提高电缆性能。
七、铠装和护套根据电缆产品的铠装和护套要求,将成缆后的电缆进行铠装和护套处理。
铠装材料有钢带、钢丝、纤维等,护套材料有聚氯乙烯、聚乙烯等。
八、品质检测对电缆产品进行一系列品质检测,包括绝缘电阻、绝缘强度、导体电阻、耐压等,确保电缆符合国家标准。
九、包装将检验合格的电缆进行包装,确保在运输、储存过程中不受损坏。
包装材料有纸箱、编织袋、塑料袋等。
十、出厂包装好的电缆产品经检验合格后,方可出厂。
总结:电缆生产工艺流程涉及多个环节,每个环节都需严格控制,以确保电缆产品的质量和性能。
通过以上工艺流程,电缆产品从原材料到成品,经过严格的生产和质量控制,最终达到客户的要求。
yjv22 生产工艺

yjv22 生产工艺YJV22是一种特殊的制造工艺,被广泛应用于电力输电和工业供电系统中。
该工艺具有较好的耐油、耐磨、防水和耐候性能,适用于各种恶劣的环境条件下使用。
YJV22的生产工艺包括以下几个步骤:1. 材料准备:首先需要准备好各种需要的材料,包括导体、绝缘层、护套等。
导体一般采用纯铜或铝合金制作,绝缘层一般采用交联聚乙烯(XLPE)材料,护套使用低密度聚乙烯(LDPE)材料。
2. 导体铺设:首先将导体铺放在生产线上,然后通过自动化设备将导体进行定位和固定,确保导体的位置准确且固定。
3. 绝缘层注塑:绝缘层的制作是整个生产工艺中的重要步骤。
将预先热处理的导体放入注塑机中,然后将XLPE熔化后注入导体周围,形成绝缘层。
注塑过程中需要控制好温度和压力,确保绝缘层的质量。
4. 护套注塑:绝缘层注塑完成后,需要对电缆进行护套注塑。
将导体和绝缘层放入注塑机中,将LDPE熔化后注入到电缆的外部。
这样可以保护电缆不受机械损坏和外界环境的影响。
5. 引线和标记:生产完成后,需要对电缆进行引线和标记。
根据客户的要求和电缆用途,将引线连接到电缆的两端,并对电缆进行标记,以便使用时能够正确区分。
6. 检测和包装:最后一步是对YJV22电缆进行检测和包装。
使用专业的设备对电缆的外观、尺寸和导体电阻等进行检测,确保电缆的质量符合相关标准。
然后将电缆进行包装,以便运输和存储。
YJV22生产工艺严格按照相关标准进行操作,确保电缆的质量和可靠性。
该工艺的主要优点是电缆具有较好的耐油、耐磨、防水和耐候性能,适用于各种恶劣的环境条件下使用。
此外,YJV22电缆还具有较高的导电性能和抗电弧性能,能够有效传输电能,并保护设备和工人的安全。
总之,YJV22生产工艺是一种先进的制造技术,可以生产出具有良好性能的电缆。
通过严格控制每个步骤和质量检测,可以保证电缆的质量和可靠性。
该工艺在电力输电和工业供电系统中有着广泛的应用,为现代化建设提供了重要的支持。
电缆制造生产工艺初探

电缆制造生产工艺初探摘要:随着各项城市基础设施建设的蓬勃发展,电缆产品的发展也日益蓬勃,但是由于电缆行业生产的特殊性,使得工艺门类众多、物流量大,所以就着重分析电缆制造业中的主要生产工艺。
关键词:电缆;生产工艺;问题电缆产品的制造从本质上讲是材料的选、配、处理以及加工和结构组合。
在电工产品中,电缆产品有以下两个鲜明的特点,一是品种繁多,目前已接近二千种,并还在不断发展中;二是电缆产品要运用于地球上所有可能被人类扩展到的各种场合、各种外部环境中,还要上天、入地(如用于卫星、几千米深的矿井或深海中),这必然要求不断开发新材料的运用及其相应的最先进的工艺技术与设备。
多而杂、广而精这二对矛盾永远是电缆行业不断发展中持续要解决的问题,以下便是电缆产品制造中的一些主要工艺技术门类。
1 有色金属的熔炼工艺1.1 电缆行业对铜材的熔炼工艺技术非常重视近三十年来电缆行业对铜的熔炼技术已接近世界先进水平,国内目前主要采用三种工艺技术,即上引法、连铸连扎和浸涂法生产出低氧铜和无氧铜,使铜的导电率达到101-103%iacs。
目前国内中型以上的电缆企业普遍采用上引法生产铜杆,大型企业采用连铸连扎,少数企业还采用浸土法生产无氧铜。
1.2 电缆行业与铝厂紧密合作,在熔冶技术上进行了研究改进,生产出铝纯度达到99.5%以上的电工专业铝锭。
目前铝的导电率为61%iacs,而铝材标准中的特二号铝(纯度99.6%)可达到62-63%iacs,纯度99.996%的铝可达65%iacs,铝材的技术性能达到国际先进水平,过去采用的黑铜杆已经明令淘汰。
我国首创的在铝炼时加入少量稀土材料的稀土铝合金可提高铝材的强度、耐腐蚀性,且成本低,最适合用于架空导线,此项技术处于国际先进水平。
2 有色金属的压力加工和其他工艺技术2.1 过去,电缆制造企业大多数采用队铜、铝锭进行热轧制杆,由于加工过程中铜、铝材表面严重氧化,上个世纪九十年代后已逐步淘汰,目前已普遍采用的是上引法、连铸连扎和浸涂法制杆技术。
高速绞线机在电缆制造中的工效分析与改进方法研究

高速绞线机在电缆制造中的工效分析与改进方法研究电缆制造工艺中的高速绞线机是一个关键设备,它在电缆生产中起着重要的作用。
本文将对高速绞线机在电缆制造中的工效进行分析,并提出改进的方法,以提高生产效率和质量。
一、高速绞线机的工作原理高速绞线机通过旋转绞线盘和带动电缆线材,使其在绞线机的绞线区域内以一定的速度和角度进行绞线。
绞线机通常由电动机、储线盘、绞线盘、换向装置和控制系统等部件组成。
电缆线材通过绞线盘和换向装置的引导,在绞线区域完成绞线的过程。
二、高速绞线机在电缆制造中的工效问题1.工作效率低下传统高速绞线机在电缆制造中存在工作效率低下的问题。
这主要是由于绞线盘转速、线材进给速度和绞线角度等因素没有得到合理协调和控制。
在线材绞线过程中,由于绞线速度和角度的不稳定,导致电缆的质量和生产效率下降。
同时,传统高速绞线机对线材的张力控制不够精确,使得线材容易断裂,进一步影响生产效率。
2.自动化程度低传统高速绞线机的控制系统相对简单,可操作性差。
操作人员需要根据经验来调整绞线速度、角度和张力等参数,容易出现误操作和调整不准确的情况。
这样不仅增加了生产事故的风险,也加大了人员操作的负担。
三、高速绞线机工效改进的方法1.优化绞线参数设置通过优化绞线盘转速、线材进给速度和绞线角度等参数的设置,可以提高绞线机的工作效率。
合理控制绞线盘的转速,使得绞线速度和角度更加稳定;合理调整线材进给速度,保持恒定的张力;通过优化绞线角度的设计,减小绞线机的负荷,提高绞线机的生产效率。
2.引进自动化控制系统引进先进的自动化控制系统,将传感器、执行器和控制器等设备与高速绞线机进行连接,可以实现对绞线速度、角度和张力等参数的实时监测和精确调节。
控制系统可以根据电缆的要求,自动调整绞线机的工作状态,提高生产效率和质量。
3.数据分析与优化利用高速绞线机的传感器和控制系统采集到的实时数据,进行数据分析和优化。
通过对数据的分析,可以发现工作中的问题和瓶颈,并针对性地进行改进。
电缆关键工艺技术

电缆关键工艺技术电缆是现代社会中广泛使用的一种电力传输工具。
它由一根或多根金属导线组成,外部包覆着绝缘材料,以保护导线并防止电流外泄。
电缆的关键工艺技术包括导线制造、绝缘材料的选择和生产、屏蔽层的应用以及终端接头的设计与制造。
首先,导线制造是电缆关键工艺技术中的重要环节。
导线通常由铜或铝制成,这是因为这两种金属的导电性能较好。
制造导线需要高精度的机械设备和专业的工艺技术。
在导线制造过程中,要确保导线的截面积、电阻和纯度达到规定的要求,以确保电流的传输效果。
其次,绝缘材料的选择和生产也是电缆关键工艺技术中的重要环节。
绝缘材料的作用是保护导线并防止电流外泄,因此绝缘材料需要具备较好的绝缘性能和耐高温性能。
绝缘材料常用的有聚氯乙烯(PVC)、绝缘胶和交联聚乙烯(XLPE)等。
在绝缘材料的生产过程中,要注意控制材料中的杂质含量,以确保绝缘材料的绝缘性能。
另外,屏蔽层的应用也是电缆关键工艺技术中的重要环节。
屏蔽层是一层金属覆盖,用于阻断外界电磁干扰,保护导线免受干扰。
通常采用铝箔或铜网作为屏蔽层。
在屏蔽层的应用过程中,要确保屏蔽层与导线之间的绝缘层完好无损,以确保电缆的传输质量。
最后,终端接头的设计与制造也是电缆关键工艺技术中的重要环节。
终端接头是将一根电缆连接到另一根电缆或设备的接口,其设计和制造需要注意保持低电阻和良好的电绝缘性能,以确保信号的传输质量。
同时,终端接头还需要具有耐高温、防水和抗震动等特性,以适应不同的应用场景。
总的来说,电缆关键工艺技术对于保证电缆传输质量和可靠性非常重要。
导线制造、绝缘材料的选择和生产、屏蔽层的应用以及终端接头的设计与制造都需要专业的知识和技术支持。
只有在这些关键工艺环节上精益求精,才能生产出高品质的电缆产品,为现代社会的电力传输提供可靠的支持。
浅谈电缆成型的设计与制造

浅谈电缆成型的设计与制造摘要:本文详细介绍了成缆的基本概念,从选材、工艺等影响成缆的几个主要方面予以阐述,为电缆设计者提供重要依据,同时简要介绍了成缆的设备与质量控制,期望操作者在生产中规避一些常见的问题。
关键词:成缆;绞线;填充;包带1 引言随着工业技术的迅猛发展,电缆已广泛应用于工业、农业、国防、科研等基础建设和高新产业中,其外观、功能多种多样,而成缆作为电缆生产过程中的重要环节,其主要参数的剪裁对电缆产品的品相、性能、成本都会产生深远的影响,合理的设计能够提升电缆产品的外观、质量,降低加工和维护过程中的成本。
本文结合实际中的电缆设计、生产经验,将零散、模糊的内容进行系统性的汇总。
2 成缆的概念2.1 成缆的定义根据一定规则,把绝缘线芯集中绞合起来,并对绞合线芯之间予以填充、绞合线芯之外绕包包带的电缆成型过程叫做成缆。
2.2 成缆的分类根据绝缘线芯直径是否完全相同,可将成缆分为对称成缆和不对称成缆。
此外根据成缆时是否退扭,还可以分为退扭成缆(另名“浮动式成缆”)和不退扭成缆(另名“固定式成缆”)。
3 成缆的目的把多根线芯集中绞合在一起可以制造出多芯电缆,其主要目的在于以下几个方面:(1)有效减少电缆的整体体积与占用空间;(2)增加线缆的圆整度、柔软度,大大增强适用性;(3)使结构更加趋于稳定,提高了抗振动、抗冲击等机械性能;(4)如果输入为三相电源信号,那么能够使三相磁场抵消,起到减少电能损耗的作用;(5)减少材料定额,降本增效,节能减排。
4 成缆的主要参数4.1 成缆方向成缆方向分为 S 绞向、Z 绞向。
将电缆水平放置并向前看,向左旋转的为 S 绞向,反之为 Z 绞向。
此外电缆也可将绞合方向进行周期性改变,称为SZ 绞合,成缆原理为固定 A、B 点,按箭头方向旋转 C 点,那么 A -C 段为S 绞向,C -B 段为 Z 绞向,故 A -B -C 整体为 SZ 绞合。
在一些电缆(例如矿用电缆、控制电缆)的行业标准中规定成缆最外层方向为 Z 绞向。
电力电缆制造工艺

1 基本工艺流程电力电缆的制造包括许多工序,一般可分为四个主要方面:导体制造,包括1)拉丝拉细单线到所需的直径;2)绞合把多根单线绞合到一起,有时需要再包带;3)组合在HV和EHV电缆制造中,把非圆形的股块绞合成准圆形的结构;绝缘线芯制造,包括1)三层挤出:电缆绝缘线芯在这个过程中形成,包括内半导电屏蔽层、绝缘层和外半导电屏蔽层;2)交联:可在挤出后直接进行(过氧化物交联),或者在挤出后采用单独设备进行(湿法交联);3)除气:通过离线加热把过氧化物副产物去除,这通常是HV或EHV电缆的基本工序,但也是经常用于中压海底电缆;电缆护层制造,包括1)绝缘线芯包带:在此过程中,把缓冲层、保护层和阻水层绕包到挤包的绝缘线芯上;2)中性线绞包:把铜线、铜带或扁铜带包绕在电缆上;3)金属护层:施加金属的防潮和保护层;4)护套:采用聚合物护套起到机械保护(对金属箔的保护特别重要)和防腐蚀作用;5)装铠:采用高强度金属构件(钢)来保护电缆,特别是海底电缆;质量控制,包括1)原材料的操作处理;2)例行试验;3)抽样试验;3.2 导体制造有些电缆制造采用直接用于屏蔽和绝缘加工的制成导体,或用铜杆或铝杆,并将其拉丝到合适的直径,然后绞合(扭结成一体)成电缆导体。
那些拉丝绞合制造导体的电缆制造必须遵循基本但重要的工艺,以确保导体获得合适的物理性能和电气性能。
由于拉丝工艺使金属产生加工硬化,因此拉丝后的线材通常必须加热以获得适当的物理性能,这个工艺叫退火。
退火可以通过感应加热过程实现。
在这个过程中,通过感应到绞线上的电流来产生热量,并提高导体的温度到正确的退火温度。
此外也可以把绞线放置到炉箱中实现退火。
退火能同时影响绞线的物理和电气性能,因此在退火过程中必须谨慎操作和监控。
必须进行定期的测试来确保绞线的特性符合规范的要求。
绞合导体是通过扭绞多根单线完成的,有多种类型的扭绞(或绞合)型式。
尽管绞合工艺相对容易完成,但必须仔细操作,以确保在绞合的过程中单线没有损伤以及绞合系数(单位长度上绞绕的次数)正确。
- 1、下载文档前请自行甄别文档内容的完整性,平台不提供额外的编辑、内容补充、找答案等附加服务。
- 2、"仅部分预览"的文档,不可在线预览部分如存在完整性等问题,可反馈申请退款(可完整预览的文档不适用该条件!)。
- 3、如文档侵犯您的权益,请联系客服反馈,我们会尽快为您处理(人工客服工作时间:9:00-18:30)。
电缆制造生产工艺分析研究
摘要:电缆产品的制造从本质上讲是材料的选、配、处理以及加工和结构组合。
在电工产品中,电缆产品有以下两个鲜明的特点,一是品种繁多,目前已接近二
千种,并还在不断发展中;二是电缆产品要运用于地球上所有可能被人类扩展到
的各种场合、各种外部环境中,还要上天入地(如用于卫星、几千米深的矿井或
深海中),这必然要求不断开发新材料的运用及其相应的最先进的工艺技术与设
备多而杂、广而精这二对矛盾永远是电缆行业不断发展中持续要解决的问题,以
下便是电缆产品制造中的一些主要工艺技术门类。
关键词:有色金属;电缆制造;专业设备
1有色金属的熔炼工艺
近三十年来电缆行业对铜的熔炼技术已接近世界先进水平,国内目前主要采
用三种工艺技术,即上引法、连铸连扎和浸涂法生产出低氧铜和无氧铜,使铜的
导电率达到101-103%LACS。
目前国内中型以上的电缆企业普遍采用上引法生产铜杆,大型企业采用连铸连扎,少数企业还采用浸土法生产无氧铜电缆行业与铝厂
紧密合作,在熔冶技术上进行了研究改进,生产出铝纯度达到99.996%以上的电
工专业铝锭。
目前铝的导电率为61%LACS,而铝材标准中的特二号铝可达到101-103%LACS,纯度的铝可达65%LACS,铝材的技术性能达到国际先进水平,过去采
用的黑铜杆已经明令淘汰。
我国首创的在铝炼时加入少量稀土材料的稀土铝合金可提高铝材的强度。
耐
腐蚀性,且成本低,最适合用于架空导线,此项技术处于国际先进水平。
2有色金属的压力加工和其他工艺技术
过去,电缆制造企业大多数采用队铜。
铝锭进行热轧制杆,由于加工过程中铜。
铝材表面严重氧化,上个世纪九十年代后已逐步淘汰,目前已普遍采用的是
上引法连铸连扎和浸涂法制杆技术。
对铜线的拉制工艺目前普遍采用大。
中拉制
及连续退火工艺,小线也有采用连续退火工艺技术,拉线速度加快,尺寸控制精
度更高对细铜线的控制,采用了多头拉线设备以提高生产速度。
铜微细线的拉制
工艺与设备已经成熟。
对铜、铝导线的绞合,除了过去常用的笼绞外,更多的是
采用了线速度更快的框绞、叉绞、盘绞以及管绞等工艺设备。
按照交联聚乙烯电
力电缆对导线需要提高填充系数及表面平整程度的要求,在绞制过程中增加了分
层紧压以及拉拔式边绞边拉的工艺技术。
其他还有铜导体外镀锡镀银。
镀镍的工
艺技术;双金属导线(铜包铝、铝包钢等)工艺技术;以及铜铝的热压技术成型,制造扁线型材等新的工艺。
塑料、橡皮及热塑性体的配方、混练加工工艺、塑料
的挤包,并加以材料发泡(化学发泡的发泡率可达到50%-60%),物理发泡可达
到的工艺以及交联化学交联、辐照交联等。
工艺技术都已达到了先进水平。
对挤
包工艺,大截面导线的产品电力电缆。
采用了三层共挤技术,小截面的产品如通
信电缆的单根绝缘线芯。
采用了高速挤出机2000-3000米/分,此外还有双头并联
挤出等工艺技术。
在漆包线、绕包线类产品中,工艺技术也有了长足的进步和发展如普遍采用
了在烘炉中队废气进行催化燃烧以减少环境污染的工艺技术,根据产品性能要求
的需要,生产内外两种不同性能的漆种连续涂制成复合漆包线的工艺技术,耐高
温薄膜绕包线制造的工艺技术等。
特别是根据大型电力变压器的需要制造巨型换
味道鲜的工艺技术,达到了世界先进水平。
各种纤维的合并、绕包、编织工艺技术,采用了与纺织化纤行业相近的工艺技术。
粉状无机材料制成无机绝缘的灌注
技术(如用于制造金属套耐火电缆),液压玻璃涂膜技术制造玻璃膜微细线技术
及特种陶瓷粉材料制造耐高温500-1000℃的高温测试用电线等技术,同轴电缆的
间隔式支撑绝缘等特殊工艺技术等。
金属和非金属带状材料的绕包工艺及金属带
材的纵包焊缝及扎制螺旋状或环状凸形扎纹等工艺技术。
其他,如铜铝导线的连接,铜铝导线的软化、韧炼、各种模具的制作和修理,从很细到很粗、从几根到
几千根导线和绝缘线芯的绞制成缆技术,及对很重要却很娇嫩的电缆进行牵引的
技术。
3电缆制造企业用的各种材料
不但类别、品种、规格多,且用量巨大,小型企业的年用量已达几千吨,大
型企业甚至达到几万吨,因此,各种材料每月的用量。
库存的备用量,需要制定
周密的计划,并严格付诸于实施,这对企业的正常生产和经济效益密切相关。
同时,对废品的分解处理回收重复利用及废料的最后处理等都必须作为企业管理中
的一项重要内容来抓,管理的好坏,对企业的经济效益关系很大。
至于生产中的
材料管理,节支降耗等工作也是非常重要的。
在电缆制造业中,物流量特别大,
从原材料及各种辅助材料的购进、储存、各工序间的流转,到成品入库出厂,都
构成了一个相互关联且复杂的物流体系。
因此,就原材料的管理必须对其的物流
路线、周期、存放地点、材料库、半成品存放地、成品库等有一个合理的科学规
划设计,从合理的布局达到科学的动态管理。
电缆企业将从这一系列的科学合理、严格实施的物流中获得可观的经济效益。
4工艺对电缆专业设备的依赖性
在电缆产品的制造中,有许多是本行业特有的工艺技术,如塑料橡皮绝缘的
三层连续挤出;漆包线的涂漆和固化油浸纸绝缘电缆的干燥和浸油;铅铝套的热
压挤包;导体的多次拉制;多根绝缘线芯的成缆;上引法和浸涂法制造低氧铜杆;光纤光缆的许多加工工艺等等。
为此,必须有针对性地研究出许多设备来实现相
关的工艺过程,制造出各种电缆的产品。
制造的工艺与专业设备的关联和相互推动性在电缆产品的整个制造过程中,
不管是从市场调研、结构设计、材料的选购,还是研发后的产品定型,工艺与设
备的关联是相互制约相互发展的。
这不仅保证了产品的制造,同时也推进了产品
的更新改造。
工艺上所有的要求都必须通过设备上的各种措施才能实现如:需要导电率更
高得铜,一直是电缆业所追求的目标,在研制了上引法浸涂法的工艺和专业设备后,就能使铜的导电率达到101-103%LACS的低氧铜、无氧铜,产生了巨大的社
会经济效益。
反之,生产专业设备的企业必须密切配合着电缆产品的改进与研发,或要求不断提高生产速度或工艺精度(如电子电缆中要求挤出的塑料绝缘厚度为
0.1-0.2mm),新工艺技术的出现对专业电缆设备的也提出了新的要求。
如有了有
色金属热压挤出成型机就可方便的制造铜包铝铝包铜等双金属单线及某些电缆产
品的铝护套等。
5 结论
专业设备的不断改进、开发,不仅保证了实施工艺的有效性和稳定性,而且
推进了电缆产品的制造向多快好省的方向前进。
在提高整个电缆制造的技术中发
挥着重要的作用。
以挤塑专业设备为例,立塔式交联电缆生产系统保证了110-
220Kv的高压电缆所需要的厚绝缘层以及研制的500Kv的超高压电缆,精密挤出
机可以制造0.1-0.2mm厚度的绝缘层,为微小型的电子电缆发展创造了条件,采
用挤出速度达2000-3000米/分的高速挤出机制造室内通信电缆的绝缘线芯,大大
提高了该类产品的生产能力。
充分利用电缆大长度连续叠加组合这一生产特征,使电缆制造中连续生产的产品品种不断增加并快速推广,这样不但能省去原来各个机组所必需的收放线牵引等辅助设备,还可以节省厂房面积、减少工序间的物流及操作工人,从而达到更大的经济效益。
参考文献
[1] 马永其,程昌钧,徐操. 220 kV电缆终端应力锥在力场中的数值模拟分析[J].中国电力,2005,38(7):27-31.
[2] 丁立健,李成榕,王景春.真空中绝缘子沿面预闪络现象的研究[J].中国电机工程学报,2001,21(9):28-33.
[3] 孙静,赵子玉.电力电缆温度实时在线监测[J].电线电缆,2011,54(1):40-42.。