芦先平老师生产管理现场辅导的案例CTPM华天谋手把手咨询17页PPT
合集下载
CTPM精益管理系列培训-第一期

21
8、清扫时不合理的发现要领
活用五感:视、触、听、嗅、味+感觉 ☆用手: ①摇一摇 ②敲一敲 ③拧一拧 ④按一按、摁一摁 ⑤刮一刮 ⑥紧一紧、松一松 ⑦掰一掰 ⑧拽一拽 ⑨擦一擦 ⑩理一理 ☆用眼睛 ①确认是否动作; ②确认是否变动、变更; ③确认是否变色; ④确认正常、异常; ⑤确认是否不均衡 ⑥确认是否有疑点 ☆用耳:①发现异常声音; ②发现正常声音; ☆用鼻:发现异味
三要素? 板: (活动板)工具 作用:① 信息交流. ② 情报共享. ③ 自我展示 5
主要内容
第一节、CTPM 1 STEP活动内容 第二节、CTPM 1 STEP看板 第三节、OPL教育 第四节、QC主题活动
6
1、CTPM 1STEP 活动内容
7
自主保全7STEP体系图
7STEP
实现CTPM自主管理
链条
链条是否被拉长(PIN PVSH的磨损),链轮齿的齿轮有没有被磨损,掉落,疵点 链齿与链条间的润滑是否充分,链轮齿的中心相不相称
轴、轴承、联 轴器
是否有松动、缺油而发热、振动的异常声音 固定螺丝是否松动、掉落 联轴器对中是否准确 联轴器橡胶是否磨损或螺丝是否松动 联轴器上是否没有黄油
齿轮
润滑是否适当,是否因多余的油而发生污染? 齿轮是否有磨损、疵点、残屑等? 齿轮是否有异常声音或振动?
M (Management)
管理 优化流程,提升效率,创造效益
2
CTPM思想
思想?
1. 全员参与的小集团活动思想 2. 预防思想 3. “0”化思想
3
CTPM目标
目标?
●灾害“0”化 化
●故障“0”
●不良“0”化
4
●浪费“0”
CTPM三要素
8、清扫时不合理的发现要领
活用五感:视、触、听、嗅、味+感觉 ☆用手: ①摇一摇 ②敲一敲 ③拧一拧 ④按一按、摁一摁 ⑤刮一刮 ⑥紧一紧、松一松 ⑦掰一掰 ⑧拽一拽 ⑨擦一擦 ⑩理一理 ☆用眼睛 ①确认是否动作; ②确认是否变动、变更; ③确认是否变色; ④确认正常、异常; ⑤确认是否不均衡 ⑥确认是否有疑点 ☆用耳:①发现异常声音; ②发现正常声音; ☆用鼻:发现异味
三要素? 板: (活动板)工具 作用:① 信息交流. ② 情报共享. ③ 自我展示 5
主要内容
第一节、CTPM 1 STEP活动内容 第二节、CTPM 1 STEP看板 第三节、OPL教育 第四节、QC主题活动
6
1、CTPM 1STEP 活动内容
7
自主保全7STEP体系图
7STEP
实现CTPM自主管理
链条
链条是否被拉长(PIN PVSH的磨损),链轮齿的齿轮有没有被磨损,掉落,疵点 链齿与链条间的润滑是否充分,链轮齿的中心相不相称
轴、轴承、联 轴器
是否有松动、缺油而发热、振动的异常声音 固定螺丝是否松动、掉落 联轴器对中是否准确 联轴器橡胶是否磨损或螺丝是否松动 联轴器上是否没有黄油
齿轮
润滑是否适当,是否因多余的油而发生污染? 齿轮是否有磨损、疵点、残屑等? 齿轮是否有异常声音或振动?
M (Management)
管理 优化流程,提升效率,创造效益
2
CTPM思想
思想?
1. 全员参与的小集团活动思想 2. 预防思想 3. “0”化思想
3
CTPM目标
目标?
●灾害“0”化 化
●故障“0”
●不良“0”化
4
●浪费“0”
CTPM三要素
呼二财老师生产管理现场辅导案例-CTPM华天谋

90000
80000
效果7 0确0 0 0认
60000
1 50000
40000
▪水纹 30000
20000
10000
0
2
▪厚薄度
28.16 %
8.5%
活动前
(2010.1~5)
7.46%
活动后
(2010.8)
4%
改 善度 改 善度
活动前
(2010.1~5)
活动后
(2010.9)
规范物 规范人 完善体制 收获效益
暴筋 模头线 杂质点 厚度超标
熔痕 击穿
料投错 热封温度偏高
其它 合计
CPP评审不良问题统计
数 量 KG
占不良总数百分比%
累积百分比%
76374.7 59689 44428 20550 13800 11429 9652 9500 8816 5000 5000 3000 2500 1432
271170.7
201
101
1
1月
2月
3月
4月
目标
7 00
500
600
700
实 绩 675.7
464
569.2
615
目标
5月
6月
实绩
7月
8月
9月
10月
11月
1 2月
原因分析及对策:
NO 问题点
原因分析
产能不足
开机率下降了3% 产品结构的调整使产能下降 本月标准更改对产能形成影响
改善对策
1、充分发挥TPM设备点检等手段,减 少设备故障时间 2、充分发挥员工的积极性,提升产能
2
① Belt 认证人员数 ②Project财务成果
黄权蓉老师生产管理现场辅导案例-CTPM华天谋
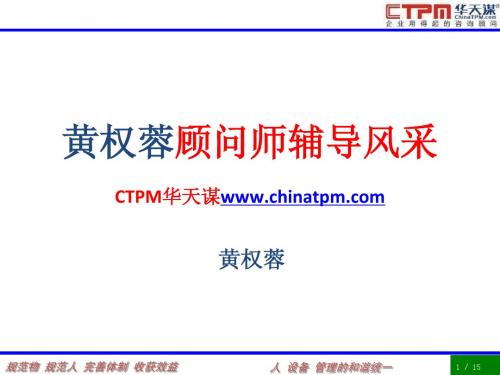
规范物 规范人 完善体制 收获效益
人 设备 管理的和谐统一
6 / 6 /13 10
3.套焊三天前后改善效果
规范物 规范人 完善体制 收获效益
人 设备 管理的和谐统一
7 / 7 /13 10
4.QC主题活动
2008年4月15日在天津国华盘电有限公司进行咨询辅导,针对小组QC 主题活动进行辅导,通过培训指导共在天津国华盘电成功完成15个 小组主题。
5S推行工作,培训员工1000多人、培养TPM专家
专业队伍。制定出适合南玻工程玻璃内部的5S推 进手册和员工行为规范。使南玻工程玻璃内部人 、设备、生产管理的和谐统一,使得生产性大大
提高。通过各种原价节俭活动使生产成本大大降
低,在南玻集团内部取得了优异的成绩并获得集 团内部先进个人的荣誉称号。
规范物 规范人 完善体制 收获效益 人 设备 管理的和谐统一
规范物 规范人 完善体制 收获效益
人 设备 管理的和谐统一
1010 / 10 /13
6.工作室三天前后改善效果
规范物 规范人 完善体制 收获效益
人 设备 管理的和谐统一
1111 / 10 /13
6.工作室三天前后改善效果
规范物 规范人 完善体制 收获效益
人 设备 管理的和谐统一
1212 / 10 /13
黄权蓉顾问师辅导风采
CTPM华天谋
黄权蓉
规范物 规范人 完善体制 收获效益
人 设备 管理的和谐统一
/ 15 11 /13
目 录
1. 顾问师概述 2. 现场辅导风采 3. 设备改善成就 4. 技能提升培养
规范物 规范人 完善体制 收获效益
人 设备 管理的和谐统一
/ 15 22 /13
周志明老师生产管理现场辅导案例-CTPM华天谋手把手咨询

4.改善案例(八)
问题点
物料在装配前涂油润滑,使用各形状金属进行 刮油、涂油,涂抹不均匀。
排笔
改善建议
购买排笔涂油,涂抹均匀,效率提升。
规范物 规范人 完善体制 收获效益
人 设备 管理的和谐统一
1111 / 19 /13
4.改善案例(九)
问题点
物料在装配前涂油润滑,使用各形状金属进行 刮油、涂油,涂抹不均匀。
问题点
气缸组装时无工装,手扶持作业,作业效率低。
气缸放置工装 改善建议
完善工装,气缸可双手拿取, 快速放置在工装后打螺丝。
规范物 规范人 完善体制 收获效益
人 设备 管理的和谐统一
1616 / 19 /13
4.改善案例(十四)
问题点
螺栓装好垫片竖立后倒下,导致桌面凌乱。
改善建议
购买磁板放置。
规范物 规范人 完善体制 收获效益
规范物 规范人 完善体制 收获效益
人 设备 管理的和谐统一
8/ 8 /13 19
4.改善案例(六)
油管调整安装
问题点: 长度不偏差大,环形钳切割调 整。 1、增加作业动作,影响效率。 2、切割多余铜管浪费。
规范物 规范人 完善体制 收获效益
改善建议: 物料编号,并制定各编号物料的长度标准, 要求供应商按标准加工供货,消除组装时 调整。
人 设备 管理的和谐统一
1717 / 19 /13
4.改善案例(十五)
问题点
1、托架在安装曲连轴时,托架孔、曲连轴孔、垫片孔需用螺丝刀调整,使其同轴心,再进 行压法安装。 2、导向柱需用布条托底,防止掉落,压付后再将布条用螺丝刀定回原位。
螺丝刀调整同轴心
导向柱
布条
生产管理赢在起点(ppt196)(1)
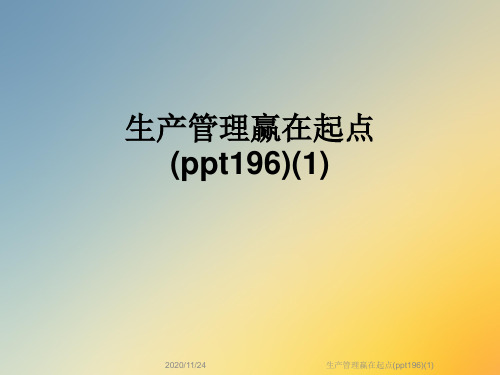
生产管理赢在起点(ppt196)(1)
1959年9月25日我国发现大庆油田 1959年9月25日,中国石油勘探队在东北松辽 盆地陆相沉积中找到了工业性油流。时值国庆10周年, 所以这个油田以“大庆” 命名。大庆油田的发现,打 破了中国是“贫油国”的论调。解放前,中国只有甘肃 老君庙、新疆独山子、陕西延长3个小油田和四川圣灯 山、石油沟2个气田,年产原油仅10余万吨,石油基本 上靠从外国进口。大庆油田的开发,使原油产量大幅度 增长。到 1963年12月,周恩来终于可以自豪地宣布: 中国需要的石油,现在已经可以基本自给了,中国人民 使用“洋油”的时代,即将一去不复返了。
生产管理赢在起点(ppt196)(1)
郑州开发遭遇地荒阵痛 4月12日下午,由河南省浙江商会、河南浙商投资担保有限公司投 资开发的中国郑州浙江产业基地项目正式签约,该项目位于中牟县境内, 投资方宣称总投资额达150亿元,占地1500亩。因为缺地,这1500亩地尚 处于“理论的憧憬”之中。 宣传中的加州工业城“占地46平方公里,总投资300亿元”,此前 政府传出消息,项目将于2006年3月破土动工。但是,目前却陷入了停顿 状态。有消息称,该项目尚未获得国务院的批复,而原因就是土地指标已 经告罄。 郑州西部的荥阳市豫龙镇,总投资40亿元,计划占地5000亩的中原 国际小商品城一期工程,曾被业界誉为中国最大的小商品城的项目,由浙 商投资和经营。但是,据消息人士透露,目前,就连其开工建设奠基仪式 占用的120余亩土地,也尚未获得相关政府部门的批准。 “地荒”正向郑州逼来。
五个基本问题
客户的要求
现场管理者的绩效指标
认识பைடு நூலகம்业组织
管理者角色认知的危机
经 营 层
现场管理者的 地位与使命
管理层
1959年9月25日我国发现大庆油田 1959年9月25日,中国石油勘探队在东北松辽 盆地陆相沉积中找到了工业性油流。时值国庆10周年, 所以这个油田以“大庆” 命名。大庆油田的发现,打 破了中国是“贫油国”的论调。解放前,中国只有甘肃 老君庙、新疆独山子、陕西延长3个小油田和四川圣灯 山、石油沟2个气田,年产原油仅10余万吨,石油基本 上靠从外国进口。大庆油田的开发,使原油产量大幅度 增长。到 1963年12月,周恩来终于可以自豪地宣布: 中国需要的石油,现在已经可以基本自给了,中国人民 使用“洋油”的时代,即将一去不复返了。
生产管理赢在起点(ppt196)(1)
郑州开发遭遇地荒阵痛 4月12日下午,由河南省浙江商会、河南浙商投资担保有限公司投 资开发的中国郑州浙江产业基地项目正式签约,该项目位于中牟县境内, 投资方宣称总投资额达150亿元,占地1500亩。因为缺地,这1500亩地尚 处于“理论的憧憬”之中。 宣传中的加州工业城“占地46平方公里,总投资300亿元”,此前 政府传出消息,项目将于2006年3月破土动工。但是,目前却陷入了停顿 状态。有消息称,该项目尚未获得国务院的批复,而原因就是土地指标已 经告罄。 郑州西部的荥阳市豫龙镇,总投资40亿元,计划占地5000亩的中原 国际小商品城一期工程,曾被业界誉为中国最大的小商品城的项目,由浙 商投资和经营。但是,据消息人士透露,目前,就连其开工建设奠基仪式 占用的120余亩土地,也尚未获得相关政府部门的批准。 “地荒”正向郑州逼来。
五个基本问题
客户的要求
现场管理者的绩效指标
认识பைடு நூலகம்业组织
管理者角色认知的危机
经 营 层
现场管理者的 地位与使命
管理层
精益管理CTPM ppt课件

2、整顿——实操指引
(1)三定加三定——定点又定位
①生产物料存放的定点定位(物料存放区域规划与划线) ②工装模具的定点定位(形迹管理) ③工具辅具量具的定点定位(形迹管理) ④参观通道线的定点定位
2、整顿
(1)三定加三定——定点又定位
①生产物料存放的定点定位(物料存放区域规划与划线) (现场照片)
整理的对象
序号 1 2 3 4 5 6 7 8 9 10 11 12 13
14
15 16 17
区分 存货 固定资产
非账面资 产
物品类别 在制品
专用工件 零部件
整车整机 建筑物 设备
办公设备 周转器具 物料架/柜 工作台案柜 物品台架 辅料容器 工装、模具
设施
桌椅 工量刀辅具
设备备件
毛坯、半成品、成品 样件、调机件
即使是有判定基准,要判断自己 管理担当以外的物品也很难,因此, 必须由管理者参与指导员工对自己的 管理责任区实施红牌张贴。
2. 整顿
定义:将必要品放于任何人都能立刻找到的状态,并做好标识。 目的:不用浪费时间找东西。
缺乏整顿 的现场
2、整顿
(1)三定加三定 定点又定位 定品又定质 定容又定量 (2)三易加一标 易拿易放易管理,一标是指所有物品上都配有一套“标识卡” (物品动态追踪卡)
办公桌椅
推进步骤
1、所有的工作场所(范围)全面检查,包括看的到的和看 不到的; 2、依据使用频度,判定“需要”和“不需要”的物品; 3、清除不需要的物品; 4、调查需要物品的使用频度,决定日常用量与处理方式; 5、联系牵头部门,制定废弃物处理方法; 6、每日自我检查。
推进方法
不管是谁都能一眼判断不需要物 品的管理方法被称为红牌作战,在工 厂中不要的或使用频度低的物品上张 贴红色卡片,以使它更加显眼。张贴 红牌之前需对张贴者说明物品需要、 不需要的判定基准,并要求彻底按基 准实施。
揭育智老师生产管理现场辅导案例-CTPM华天谋
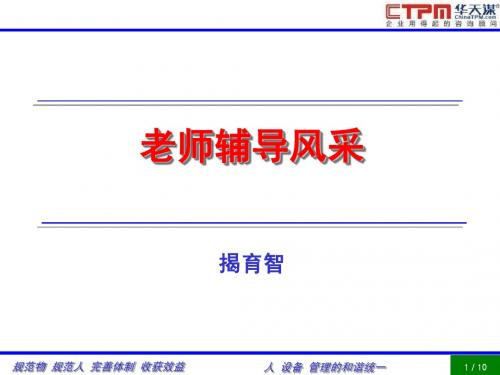
部分现场可视化改善亮点
规范物 规范人 完善体制 收获效益
人 设备 管理的和谐统一
4/ 4 /13 10
小组课题指导
对课题辅导注重务实落 地,对各小组的课题进行手 把手指导,从数据化管理、 现况调查、原因分析、对策 及实施等落实每一步的实际 操作,取得良好效果。
规范物 规范人 完善体制 收获效益
人 设备 管理的和谐统一
能耗,提升生产力,精益生产方式 。分析及控制
不良品,减少因品质造成的损失。 熟悉ISO9001/14001/OHSAS18001的运作。熟 识QC小组活动,GB课题的推进,曾在公司多次举办 的各项活动中获奖(创新提案奖八次,安全TPM 第一名,QC小组发表第一名,论文一等奖等), 主导多个5S、TPM、TPS项目。
规范物 规范人 完善体制 收获效益
人 设备 管理的和谐统一
2/ 2 /13 10
2
现场辅导案例展示
通过现场辅导,手把手指 导打造规范的可视化管理 方面善于因地制宜进行推 进,使工作环境整洁有序、 设备焕然一新。
规范物 规范人 完善体制 收获效益
人 设备 管理的和谐统一
3/ 3 /13 10
3
看板辅导案例展示
老师辅导风采
揭育智
规范物 规范人 完善体制 收获效益
人 设备 管理的和谐统一
1 /13 10
1.老师风格概述
在现场规范化管理、IE工序控制及现场改善、
设备维护、物料流程、Q-COST,H-COST降低等, 有较丰富的实战经验,曾经在其它企业担任TPM 推进专家取得显著的成果,有效降低生产成本及
5/ 5 /13 10
精益生产改善
规范物 规范人 完善体制 收获效益
人 设备 管理的和谐统一
规范物 规范人 完善体制 收获效益
人 设备 管理的和谐统一
4/ 4 /13 10
小组课题指导
对课题辅导注重务实落 地,对各小组的课题进行手 把手指导,从数据化管理、 现况调查、原因分析、对策 及实施等落实每一步的实际 操作,取得良好效果。
规范物 规范人 完善体制 收获效益
人 设备 管理的和谐统一
能耗,提升生产力,精益生产方式 。分析及控制
不良品,减少因品质造成的损失。 熟悉ISO9001/14001/OHSAS18001的运作。熟 识QC小组活动,GB课题的推进,曾在公司多次举办 的各项活动中获奖(创新提案奖八次,安全TPM 第一名,QC小组发表第一名,论文一等奖等), 主导多个5S、TPM、TPS项目。
规范物 规范人 完善体制 收获效益
人 设备 管理的和谐统一
2/ 2 /13 10
2
现场辅导案例展示
通过现场辅导,手把手指 导打造规范的可视化管理 方面善于因地制宜进行推 进,使工作环境整洁有序、 设备焕然一新。
规范物 规范人 完善体制 收获效益
人 设备 管理的和谐统一
3/ 3 /13 10
3
看板辅导案例展示
老师辅导风采
揭育智
规范物 规范人 完善体制 收获效益
人 设备 管理的和谐统一
1 /13 10
1.老师风格概述
在现场规范化管理、IE工序控制及现场改善、
设备维护、物料流程、Q-COST,H-COST降低等, 有较丰富的实战经验,曾经在其它企业担任TPM 推进专家取得显著的成果,有效降低生产成本及
5/ 5 /13 10
精益生产改善
规范物 规范人 完善体制 收获效益
人 设备 管理的和谐统一
生产管理之基础方法 ppt课件

QCC活动的案例分析
略 ( 后补)
QCC活动的模拟课题
略
三、5S活动的基础方法
5S活动的基本概念 5S活动的要点 5S活动的现场检查分析
5S活动的基本概念
5S是企业管理的基石 5S的含义 5S的三大支柱 5S活动的目的 5S之间的关系
5S是企业管理的基石
公司的方针目标 Q 品 质 C 成 本 D 交 期 S 服 务 T 技 术 M 管 理
具体 的活 动项 目
缩短作业周期,确保交货期 降低生产成本
培养员工的主 动性和积极性
5S 活 动 的 目 的
改善零件在库周转率
提高管理水平,改 善企业的经营状况
促成效率的提高
保障企业安全生产 创造人和设备 都适宜的环境 减少甚至消除故障 形成自主 改善的机制
培养团队精神 和合作精神
组织活力化,改善员工 的精神面貌
QCC的成果
有形
无形
不良 返工 浪费 错误 成本
员工实力 工作 敬业 向心力
解决问题的能力
改善工作,享受成就感
对QCC的误解
立即想有大效果 只重有形,忽视无形结果 挑毛病,欠缺鼓励 为发表,为得奖而QCC
认为是额外的工作
认为是小孩子的玩意
QCC活动的常用手法
判异准则:
1.点出界就判异;
2.虽然点均未出界,但界内点排列不随机就判异;
第二条准则的具体模式理论上有无穷多种,但具 有实际物理意义并被广泛使用的有少数几种:
六点倾向向上或向下就判异
九点链在中心线一侧就判异
三点中两点在距控制界限1范围内就判异
LOB教材及现场工艺平衡PPT课件
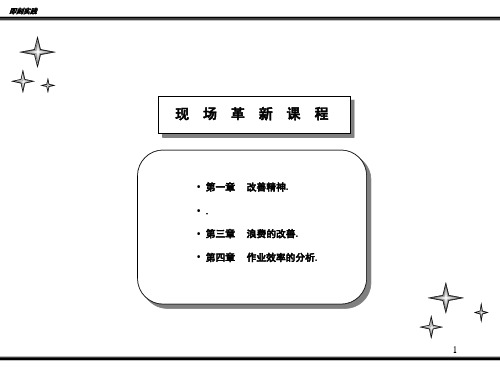
不良语言污染别人
我忙,没有时间
4
改善精神
4. 改善思考的方法
改善精神以疑问作为出发点。要时时存有疑问:现进行的方法是 最佳的吗?
☆ 改善思考的步骤
第一步:这是必须要做的吗? 第二步:是否可以消除? 第三步:是否可以减少? 第四步:如果是必须的,是否可以换一种方法?
☆ 改善思考的步骤
1. 更容易地 2. 更便利地 3. 更安全地 4. 更稳定地 5. 持续不断的变化
电动 Driver 三角带 22
作业效率分析
第四章生产效率管理
4-1 作业时间分析(工数计算) 总投入工数(A)
直接工数 (B)
间接工数(C)
纯工作工数(D)
无作业(E)
回收工数(G)
能率差(F)
1). 间接率: C/A × 100; 2).无作业率:E/B × 100; 3).回收率:G/A × 100; 4).能率:(1- F /D) × 100; 5). 间接人员:不贡献直接生产,线长,维修工、物料供应人员等; 6). 无作业:停工时间,分为:
4.不必追求完美,只要求50分也好,主要是立即执行. 5.是错误的就立即改正. 6.首先进行不花销的改善.
改善Man 改善的Leader
7.穷则变,变则通.
8.不良原因要反复问5次“为什么?”.
9.不要一个人的“知识,”而要十个人的“智慧”!
10.改善是无限的.
2
改善精神
2. 6种错误思想
是否沉浸在这些“安逸的思想”中? 马上摒弃!
a. 可能控制无作业:欠料,不良、新模式等; b. 不可控制无作业:停电、培训; 7 ).回收工数=实际生产量X标准时间 8). 回收率:公司的总投入资源对比实际产出来的价值;(85%以上好); 9). 能率,标准时间内能否达到目标;(95%~105%好,100%以上意味着标准太轻松)23.