模具制造实训小结
模具实训报告心得体会范文(精选4篇)

模具实训报告心得体会范文(精选4篇)(实用版)编制人:______审核人:______审批人:______编制单位:______编制时间:__年__月__日序言下载提示:该文档是本店铺精心编制而成的,希望大家下载后,能够帮助大家解决实际问题。
文档下载后可定制修改,请根据实际需要进行调整和使用,谢谢!并且,本店铺为大家提供各种类型的实用资料,如教学心得体会、工作心得体会、学生心得体会、综合心得体会、党员心得体会、培训心得体会、军警心得体会、观后感、作文大全、其他资料等等,想了解不同资料格式和写法,敬请关注!Download tips: This document is carefully compiled by this editor.I hope that after you download it, it can help you solve practical problems. The document can be customized and modified after downloading, please adjust and use it according to actual needs, thank you!And, this store provides various types of practical materials for everyone, such as teaching experience, work experience, student experience, comprehensive experience, party member experience, training experience, military and police experience, observation and feedback, essay collection, other materials, etc. If you want to learn about different data formats and writing methods, please pay attention!模具实训报告心得体会范文(精选4篇) 【导语】模具实训报告心得体会范文怎么写好?本文精选了4篇优秀的模具实训心得体会范文,都是标准的书写参考模板。
模具实习总结5篇

模具实习总结5篇第1篇示例:模具实习是大学生在校期间非常重要的一段经历,通过这段时间的实践、学习和锻炼,可以让学生更好地了解专业知识,提高实际操作能力,为将来的工作和发展打下良好的基础。
在这段时间里,我也有幸参与了模具实习,并通过这次实习有了很多收获和体会。
在实习期间,我在实际操作中学习到了很多知识。
通过实习,我深入了解了模具的原理、结构和制造工艺,掌握了模具加工的基本技能和方法。
在实习中,我跟随着师傅们学习了注塑模具、压铸模具、冲压模具等各种类型的模具的制作和加工过程,学习了模具的设计和加工标准,理解了模具在工业生产中的重要性和地位。
通过实践操作,我提高了自己的动手能力和技术水平,对模具加工有了更深入的了解和认识。
在实习期间,我还提高了团队合作和沟通能力。
模具实习是一个团队合作的过程,需要大家通力合作、相互配合,才能完成任务。
在实习中,我学会了和同事们有效沟通,分工合作,共同解决问题,使工作更加高效和顺利。
通过和同事们的交流和合作,我认识到了团队合作的重要性和优势,锻炼了自己的团队合作和协调能力。
在实习期间,我也养成了细心、耐心和责任心。
模具制作是一个细致、复杂的过程,需要耐心和细心去完成每一个工序,严格要求自己,确保做好每一步工作。
在实习中,我经常要对模具的尺寸、精度、表面质量进行检测和调整,需要耐心和细心去操作和调整,保证模具的质量和性能。
我也要保证工作的安全和整洁,严格遵守操作规程,做好各种安全防护工作,确保自己和同事们的安全。
通过这次实习,我养成了良好的职业习惯和责任心,提高了自己的工作细心和耐心程度。
在实习期间,我也增强了对模具行业的认识和了解。
通过实习,我更加深刻地认识到模具制造对于工业生产的重要性和地位,意识到模具行业的发展前景和市场需求。
我也了解到了模具行业的发展现状和存在的问题,认识到自己还需要不断学习和提高,适应行业的发展和需求,实现自身的职业发展和成长。
通过这次模具实习,我不仅学到了很多知识,提高了技术水平,也养成了良好的职业习惯和团队合作精神。
模具实习报告总结范文5篇

模具实习报告总结范文5篇实习是大学教育最后一个极为重要的实践性教学环节,实习过后应写一份实习报告,对实习总结一番。
下面是小编为大家整理的关于模具实习报告总结范文,希望对您有所帮助!模具实习报告总结范文1无论是发达国家还是发展中国家,模具专业人才一直被市场认为是最受欢迎的人才之一。
下面是有20__模具专业学生实习报告,欢迎参阅。
流水似箭,转眼间离开学校已有六个月了。
经过这半年来的实习,让我真真正正的体会到了“井底之蛙”的涵意。
在学校的时候,我们只是学习课本上的一些理论知识。
那时感觉理论这么简单想比操作起来也并不难。
但事实却并非如此。
当我们刚来到云南建工钢结构有限公司时,厂里按排了我们一个星期的厂规厂纪及安全问题的学习。
于是,我们带着这些初步的培训之后,终于迈进了我期待已久的实战中。
当我们踏入了厂线后,带班首先给我们讲的就是安全问题。
听我们师傅说就是在我们厂因为工作不认真谨慎,乱动设备而造成的残疾,手指夹断,腿脚压伤压残等等都有出现过。
这些听起来就让人心惊胆战的。
的确,在现场如果忽视了安全问题就很容易发生公伤事故。
当然受伤的也是自己。
因此,我们每天上班集合时都会一起硕大声喊:“安全第一”的口号,为的就是要告诫我们自己不论做什么事都要三思而后行。
更不要完全依靠自己的感觉和经验做事。
然后,才安排我们上线生产,刚开始上线是我什么都不会,做什么都是很慢,对那些工具的使用都是很生熟,甚至有些都是我们在学校所没见过的。
所以在实习期间总是感觉到在学习学习的那些东西真是太局限了。
学习到的理论与实际很难结合在一起。
但是经过,组长及其领导的培训,对钢结构的工艺及焊接工艺都了解了。
但是,对于我要学习的东西还是很多的。
因此,我怀着对那些未知知识的好奇和兴趣,一定要抓住每一分每一秒学习的机会和机遇,为自己在建工钢构的发展开拓无限的空间。
一.实习目的:生产实习是教学与生产实际相结合的重要实践性教学环节。
在生产实习过程中,学校也以培养学生观察问题、解决问题和向生产实际学习的能力和方法为目标。
模具学习总结7篇

模具学习总结7篇第1篇示例:模具学习总结模具是现代工业生产中不可缺少的重要工具,它在汽车制造、家电生产、建筑施工等领域都起着至关重要的作用。
模具制造是一门综合性很强的工程技术,它涉及到材料学、机械加工、设计制造等多个领域的知识。
在学习模具制造的过程中,我对这门学科有了更加深刻的理解和认识。
我学习了模具材料的选择和应用。
模具的材料是制造模具的重要环节,不同的材料可以满足不同的工业生产需求。
对于需要高强度和耐磨性的模具来说,选择合金钢或者硬质合金作为材料会更加合适;而对于需要对模具表面进行高精度加工的需求,选择不锈钢或者铝合金可能更加合适。
在学习中,我深入了解了各种材料的特性和适用范围,能够根据不同的生产需求选择合适的模具材料。
我学习了模具设计与制造的相关知识。
模具的设计是模具制造的第一步,好的设计不仅可以提高模具的使用寿命,还可以提高生产效率。
在学习中,我掌握了CAD/CAM等设计软件的使用技巧,能够利用这些工具进行模具的三维设计和分析,使得模具的结构更加合理,工艺更加优化。
我还学习了模具的制造工艺和加工技术,掌握了铣削、车削、电火花加工等多种模具加工方法,提高了模具制造的技术水平。
我学习了模具的维护与管理知识。
模具在长时间的使用过程中会出现磨损、变形等问题,需要进行定期的维护与保养。
在学习中,我了解了模具的各种损坏形式和原因,掌握了常见的模具修复技术,能够及时有效地解决模具出现的问题。
我还学习了模具的管理与使用方法,包括模具的存放、保管、使用等方面的知识,使得模具的使用更加安全可靠。
通过模具学习的总结,我对模具制造有了更加全面的认识和了解,能够独立完成模具的设计、制造、维护与管理工作。
未来,我将继续深入学习模具制造技术,不断提高自己的专业能力,为工业生产做出更大的贡献。
第2篇示例:模具学习总结模具是制造工业中不可或缺的一部分,它承载着制造产品的形状和尺寸,直接影响着产品的质量和成本。
对模具的学习和掌握至关重要。
模具实训总结8篇

模具实训总结8篇第1篇示例:模具实训总结模具是制造业中不可或缺的重要工具,它们能够帮助生产出各种各样的零部件和产品。
模具实训是模具设计与制造专业学生必须经历的一项重要实践课程,通过实训,学生可以掌握模具设计、加工工艺和调试的技能,为将来从事模具设计与制造工作打下坚实的基础。
在模具实训中,学生不仅要学习专业知识,还要学会团队合作、沟通协调和解决问题的能力。
在实训过程中,我深刻体会到了团队合作的重要性。
每一个环节都需要团队成员之间紧密配合,只有每个人都尽心尽力地完成自己的任务,整个项目才能顺利进行。
在困难和挑战面前,团队成员之间的默契配合更是至关重要,只有相互支持、相互帮助,才能共同克服困难,取得成功。
在模具实训中,我们也需要具备优秀的沟通协调能力。
每个人都有自己的想法和看法,而模具设计与制造需要各个环节之间紧密衔接,任何一点失误都可能导致整个项目的失败。
我们需要善于倾听他人意见,及时沟通交流,解决问题。
只有做到大家心往一处想、劲往一处使,才能顺利完成任务。
在模具实训的过程中,我们还需要具备解决问题的能力。
模具设计与制造是一个复杂的系统工程,其中难免会遇到各种各样的问题和困难。
如何面对问题、分析问题并找出解决办法,需要我们有高超的技术水平和丰富的经验。
所以,我们需要不断学习、不断实践,提升自己的技能水平,不断完善自己。
通过模具实训,我不仅掌握了模具设计与制造的技术,还学会了团队合作、沟通协调和解决问题的能力。
这些技能和能力对我将来的职业发展起着至关重要的作用。
我会继续努力学习,不断提升自己,成为一名优秀的模具设计与制造工程师。
【2000字】第2篇示例:模具实训是制造类专业学生必不可少的一环,通过实践操作加深对课堂知识的理解和掌握。
在模具实训过程中,学生将学到的理论知识应用到实际操作中,提升自己的动手能力和解决问题的能力。
下面就来总结一下模具实训的体会和收获。
在模具实训中,最重要的是安全意识。
在操作模具机械设备时,一定要严格遵守操作规程,保证自己和周围同学的安全。
模具专业实习工作总结6篇

模具专业实习工作总结6篇篇1时间如白驹过隙,转眼间,我在模具专业实习的这段时间已经结束了。
回首这段时间的学习和工作,我受益匪浅,不仅学到了很多专业知识,还积累了一些工作经验。
下面,我将对这段时间的实习工作进行总结,以便更好地反思和提升自己。
一、实习目的与任务本次实习的主要目的是通过亲身实践,掌握模具设计与制造的基本技能,熟悉模具行业的生产流程和标准。
实习期间,我主要承担了以下任务:参与模具设计,包括2D图纸的绘制和3D模型的建立;参与模具制造,包括材料选择、加工工艺制定和加工操作;参与模具调试,包括试模和修模工作。
二、实习过程与体会在实习过程中,我深刻体会到了理论与实践相结合的重要性。
一方面,我需要在实践中不断验证所学理论知识,另一方面,我也需要不断将理论知识运用到实践中去。
通过反复实践和不断摸索,我逐渐掌握了模具设计与制造的基本技能。
同时,我也意识到了团队协作的重要性。
在实习过程中,我需要与团队成员紧密合作,共同完成任务。
通过团队协作,我不仅学会了如何与他人沟通,还学会了如何发挥各自优势,共同解决问题。
此外,我还发现自己的专业技能还有待提升。
在实习过程中,我遇到了一些较为复杂的问题,需要运用更加专业的知识和技能来解决。
因此,我需要在未来的学习和工作中不断加强自己的专业技能训练。
三、实习成果与收获通过这段时间的实习工作,我取得了以下成果:成功完成了多个模具设计任务,并得到了领导和客户的认可;掌握了模具制造的基本技能和工艺;熟悉了模具行业的生产流程和标准;培养了团队协作精神和沟通能力。
同时,我也获得了丰富的经验:如何将理论知识与实践相结合;如何运用专业知识和技能解决实际问题;如何与团队成员紧密合作完成任务。
这些经验将对我未来的学习和工作产生积极的影响。
四、存在的问题与建议在实习过程中,我也遇到了一些问题:一方面是专业知识不够扎实,导致在解决某些问题时不够自信;另一方面是实践经验不足,需要在未来的工作中不断加强实践训练。
模具实习总结5篇

模具实习总结5篇第1篇示例:在我即将结束模具实习的日子里,回想起这段时间的学习与成长,感慨良多。
这段实习经历让我对模具行业有了更深入的了解,也让我在实践中掌握了不少专业技能。
下面我将就此次实习经历进行总结和反思。
在这段实习期间,我所在的公司是一家专业的模具制造企业。
虽然我在校期间学习了相关的理论知识,但是实际操作起来确实有一定的难度。
在最开始的阶段,我主要是负责观摩和学习,熟悉各种模具的种类和结构。
通过与老师傅的交流和学习,我逐渐掌握了模具制作的基本流程和常用工具的使用方法。
在实习期间,我主要承担了模具的设计、加工和调试等工作。
在模具的设计阶段,我要根据客户的需求和产品的要求来制定模具的结构和尺寸。
通过使用CAD等设计软件,我成功设计了几个模具,并且对其中的一些零部件进行了改进。
在模具的加工阶段,我亲自操作激光切割机、铣床、电火花机等多种设备,对模具的工件进行加工。
在这个过程中,我遇到了不少困难,但通过不断的尝试和学习,最终都得到了解决。
在模具的调试阶段,我需要对模具进行安装和调试,确保其能够准确地进行产品的冲压和成型。
通过不断地调试和测试,我成功地生产出了几个合格的产品,并受到了公司的表扬。
除了技术方面的学习,这段实习还让我懂得了团队合作和沟通的重要性。
在实际工作中,每一个环节都需要与不同的人员进行沟通和合作,只有团队协作才能保证模具的质量和效率。
在与同事们的合作中,我学会了倾听和尊重他人的意见,同时也学会了主动沟通和协调解决问题。
这段模具实习经历让我受益匪浅。
通过实际操作和实战经验的积累,我对模具行业有了更深入的了解,也掌握了不少实用的技能。
这段实习也让我体会到了团队合作和沟通的重要性。
我相信,这些宝贵的经验和教训将会成为我日后工作和生活中的宝贵财富,让我在未来的职业发展道路上更加明确和自信。
感谢这次实习给我带来的一切,也期待未来在这个行业中能够更上一层楼。
【2000字】第2篇示例:模具实习总结模具实习是我大学生涯中最难忘的一段经历,通过这段时间的学习与实践,我对模具制造有了更深入的了解,并掌握了许多实用的技能。
模具实习总结报告 三篇

模具实习总结报告三篇(经典版)编制人:__________________审核人:__________________审批人:__________________编制单位:__________________编制时间:____年____月____日序言下载提示:该文档是本店铺精心编制而成的,希望大家下载后,能够帮助大家解决实际问题。
文档下载后可定制修改,请根据实际需要进行调整和使用,谢谢!并且,本店铺为大家提供各种类型的经典范文,如工作报告、合同协议、心得体会、演讲致辞、规章制度、岗位职责、操作规程、计划书、祝福语、其他范文等等,想了解不同范文格式和写法,敬请关注!Download tips: This document is carefully compiled by this editor. I hope that after you download it, it can help you solve practical problems. The document can be customized and modified after downloading, please adjust and use it according to actual needs, thank you!Moreover, our store provides various types of classic sample texts, such as work reports, contract agreements, insights, speeches, rules and regulations, job responsibilities, operating procedures, plans, blessings, and other sample texts. If you want to learn about different sample formats and writing methods, please pay attention!模具实习总结报告三篇第1篇模具实习总结报告 2850字模具实习总结报告通过实训,加强我们对所学理论知识的理解;强化了我们的技能练习,使之能够掌握冷冲模的基本理论、技能、技巧;加强动手能力及劳动观念的培养;尤其在培养学生对所学专业知识综合应用能力及认知素质等方面,该项实训是不可缺少的重要环节。
模具制造实训工作总结(通用12篇)

模具制造实训工作总结第1篇顶岗实习是高职院校以学生为主体,以就业为导向,充分利用校内外不同的教育环境和资源,把以课堂教学为主的学校教育和直接获得实际经验的校外工作有机结合起来,帮助学生提高职业素质和就业竞争力的新型教学模式。
根据教育部《职业院校试行工学结合,半工半读意见》中“高职院校要与企业进行深层次结合,有条件的职业院校可以实行半工半读制度,改革以课堂为中心的教学模式,推行工学结合”精神,我专业积极响应学院教学改革的号召,率先尝试“校企合作,工学结合”的人才培养模式。
20xx年11月,我专业派出05模具班共116名学生到模具相关公司参加为期3个月的顶岗实习,开始了“校企合作、工学结合”人才培养模式的探索,在专业建设方面、学生就业及学生职业道德教育等方面积累了宝贵经验,为我院的“高职人才培养工作评估”作出了重要贡献。
一、基本情况通过充分的动员、精心的组织和严格的管理,我专业毕业生在顶岗实习期间,任劳任怨,爱岗敬业,勤奋踏实,获得了各公司的高度评价,为我院争得了荣誉。
通过大家共同努力,我专业毕业生于2009年6月圆满完成实习任务,成为我院“校企合作、工学结合”人才培养模式的先行军、探索者。
更为可喜的是,我专业多名学生在实习完成后通过竞聘上岗与实习企业签订就业协议,成功解决了就业问题。
此次学生顶岗实习工作意义重大。
学生通过“校企合作”平台,增加了实践经验,提升了解决实际困难的能力,有效的实现了学校与社会的“零距离接触”,提高了就业竞争力;我专业通过企业的实操平台,使实训教学更加合理化、系统化。
二、主要做法(一)积极准备,确保顶岗实习顺利进行1、明确目的顶岗实习的基本目的,在于通过理论与实践的结合,学校与企业的沟通,进一步提高学生的思想觉悟,业务水平,尤其是观察、分析和解决问题的实际工作能力,以便把学生培养成为能够主动适应社会主义现代化需要,面向生产、建设、管理、服务第一线,实践能力强、具有良好职业道德的高素质、技能型专门人才。
模具实习总结精选15篇
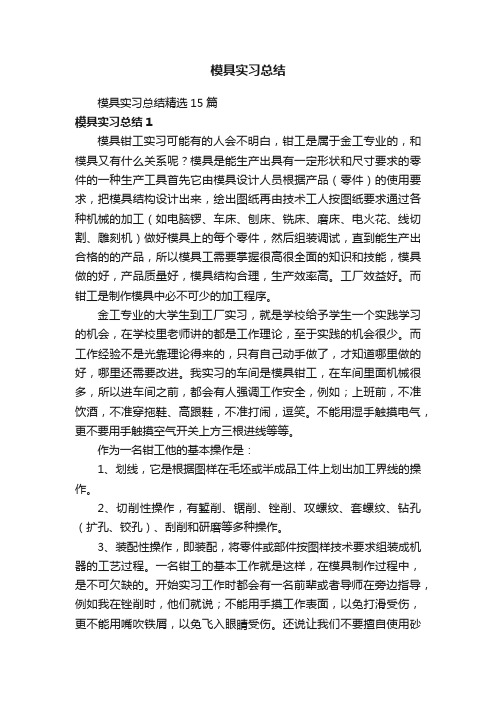
模具实习总结模具实习总结精选15篇模具实习总结1模具钳工实习可能有的人会不明白,钳工是属于金工专业的,和模具又有什么关系呢?模具是能生产出具有一定形状和尺寸要求的零件的一种生产工具首先它由模具设计人员根据产品(零件)的使用要求,把模具结构设计出来,绘出图纸再由技术工人按图纸要求通过各种机械的加工(如电脑锣、车床、刨床、铣床、磨床、电火花、线切割、雕刻机)做好模具上的每个零件,然后组装调试,直到能生产出合格的的产品,所以模具工需要掌握很高很全面的知识和技能,模具做的好,产品质量好,模具结构合理,生产效率高。
工厂效益好。
而钳工是制作模具中必不可少的加工程序。
金工专业的大学生到工厂实习,就是学校给予学生一个实践学习的机会,在学校里老师讲的都是工作理论,至于实践的机会很少。
而工作经验不是光靠理论得来的,只有自己动手做了,才知道哪里做的好,哪里还需要改进。
我实习的车间是模具钳工,在车间里面机械很多,所以进车间之前,都会有人强调工作安全,例如;上班前,不准饮酒,不准穿拖鞋、高跟鞋,不准打闹,逗笑。
不能用湿手触摸电气,更不要用手触摸空气开关上方三根进线等等。
作为一名钳工他的基本操作是:1、划线,它是根据图样在毛坯或半成品工件上划出加工界线的操作。
2、切削性操作,有錾削、锯削、锉削、攻螺纹、套螺纹、钻孔(扩孔、铰孔)、刮削和研磨等多种操作。
3、装配性操作,即装配,将零件或部件按图样技术要求组装成机器的工艺过程。
一名钳工的基本工作就是这样,在模具制作过程中,是不可欠缺的。
开始实习工作时都会有一名前辈或者导师在旁边指导,例如我在锉削时,他们就说;不能用手摸工作表面,以免打滑受伤,更不能用嘴吹铁屑,以免飞入眼睛受伤。
还说让我们不要擅自使用砂轮机,如要使用,可在老师指导下操作,人要站在侧边,工作必须夹牢,用力不能过猛。
实习的时间不长,但是对于我们这些实习生来说帮助很大,对于金工专业有了更深的了解,发现了问题就是解决问题的开始,对不懂的地方就请教技术人员或查找资料,通过向老师学习,向书本学习,最后解决一个个的难题。
模具专业实习工作总结5篇
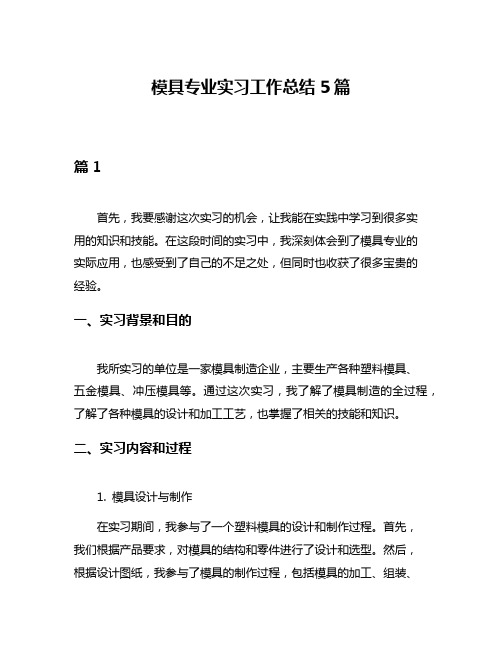
模具专业实习工作总结5篇篇1首先,我要感谢这次实习的机会,让我能在实践中学习到很多实用的知识和技能。
在这段时间的实习中,我深刻体会到了模具专业的实际应用,也感受到了自己的不足之处,但同时也收获了很多宝贵的经验。
一、实习背景和目的我所实习的单位是一家模具制造企业,主要生产各种塑料模具、五金模具、冲压模具等。
通过这次实习,我了解了模具制造的全过程,了解了各种模具的设计和加工工艺,也掌握了相关的技能和知识。
二、实习内容和过程1. 模具设计与制作在实习期间,我参与了一个塑料模具的设计和制作过程。
首先,我们根据产品要求,对模具的结构和零件进行了设计和选型。
然后,根据设计图纸,我参与了模具的制作过程,包括模具的加工、组装、调试等。
在这个过程中,我学会了如何根据实际情况,灵活运用所学的知识和技能,解决实际问题的能力得到了很大的提高。
2. 模具加工工艺在实习期间,我也了解了各种模具加工工艺,如铣削、钻孔、攻丝等。
通过实际操作,我学会了如何根据模具类型和要求,选择合适的加工设备和工艺方法,同时也感受到了不同加工方法的特点和优劣。
3. 团队合作与沟通在实习期间,我也参与了一些团队合作的项目。
通过与同事们的合作,我学会了如何与他人合作完成任务,如何沟通与交流,如何解决团队内部的问题等。
这些经验对于我未来的职业生涯非常重要。
三、实习总结与心得体会通过这次实习,我不仅学到了很多实用的知识和技能,还收获了很多宝贵的经验。
首先,我认识到了自己的不足之处,需要更加努力学习和提高自己的技能和知识水平。
其次,我也感受到了团队合作的重要性,需要更加注重与他人的沟通和合作。
最后,我也认识到了自己的优点和潜力,需要更加自信地面对未来的挑战和机遇。
总之,这次实习让我更加明确了自己的职业规划和方向,也让我更加热爱这个专业。
我相信,在未来的职业生涯中,我会继续努力学习和提高自己的技能和知识水平,为模具行业的发展做出自己的贡献。
四、建议与展望1. 建议对于学校和企业来说,应该更加注重学生的实践能力和职业技能的培养。
模具实训的个人心得体会4篇

模具实训的个人心得体会4篇在过去的三个星期里面,我经过了自己的专业知识的实践,内容当然就是我的专业模具。
让自己对所谓的模具有一个较为全面的认识。
许多的以前的想法与观点在这次实践中受到了一个很大层次的正面的冲击,进而逐渐的对它们产生怀疑,接着而来的就是改观,又觉得的理由选择的改观。
仔细一想,原来的自己的对专业的许多的看法其实是无知的,错误的。
所谓的模具,并不再是自己想象中的那样的容易,那般的简单。
开始感觉到那只不过是极其幼稚,不敢面对现实的懦夫的表现而已。
看着一套又一套小型的模具的所有的组成结构,零件,件件零件的尺寸,想着它们该是如何的加工出来的?如何的进行工艺分析?怎样做才算是最为经济,最为科学的方案?这其中的指导老师的精心讲解,对每套模具构成零件的逐步的耐心剖析,以及同学们的在不懂之处的积极的紧扣主题的提问,在那个产生实践场所形成了一幅又一幅美丽的授业解惑的课堂画卷,同学们挤出时间强抓着笔记,全神贯注的聆听老师的解说之词。
就是连一向只对爱情,对游戏情有独钟的好几位同学,在那里也是自发的拿出笔,拿出纸,在忙碌的强记点什么东西,我想那一定是很重要的台词。
这些就如同是在接受祖国与人民的关于模具方面的检阅一般,毫无退宿,毫无隐退,主动出击,随时期待着自己受到老师的发问。
并不是因为都喜欢这样的爱好,这样的嗜好,而是在于自己心中有真货,自己心中有真情。
在风一样流逝的岁月里,三个星期如昙花一线,弹指最多可以与一挥间相提并论。
但让我们自己学到的东西,那绝对的不是一般可以概括,也不是仅仅的.再加上相当二字就可以了得的,绝对的该是可以达到意想不到的可喜的收获方才罢休。
慢慢的意识到,不是自己学不到,不是自己没本事,没能力学,而是在于自己敢不敢去学,想不想去学,有没有学习的那股子冲劲。
它的着实的参与,让自己不得不把原先的许多的想法抛弃,让自己不得从不一直以来的游手好闲,无所事事中跳跃出来。
其实那些只会危害自己,别人是不会对你投以一丁点的好感的,并不是因为别人都没有一视同仁的双眼,而是自己甘愿选择逃避,堕落。
模具制造专业实训工作总结 (2)3篇

模具制造专业实训工作总结 (2)模具制造专业实训工作总结 (2)精选3篇(一)在模具制造专业实训工作中,主要涉及到模具设计、加工与调试等方面的实操技能,同时也包括团队合作、沟通协调等软实力的培养。
通过这次实训工作,我获益匪浅,总结如下:首先,在模具设计方面,我掌握了使用CAD软件进行模具设计的基本操作技能。
通过实际练习,我对模具设计的要求和流程有了更清晰的认识,并学会运用CAD软件进行零件的绘制和三维装配。
在设计过程中,我学会了考虑生产工艺和加工工艺的影响,以及如何优化设计以提高模具的制造效率和质量。
其次,在模具加工方面,我学会了使用数控机床进行模具零件的加工操作。
在实际操作中,我学会了正确使用数控机床的操作界面,熟悉了加工工艺规范,掌握了数控加工中的常用指令和加工参数设置。
我还学会了使用常见的加工工具和量具,熟练掌握了钳工、车工、铣工和磨工等基本加工工艺。
此外,我还参与了模具调试和测试工作。
通过模具的组装和调试,我学会了如何根据设计要求进行模具装配和调试,解决模具运行中出现的问题。
在模具调试过程中,我学会了运用专业的测试仪器和测量工具,对模具的结构、功能和运行状态进行检测和评估。
在实训工作中,我与团队成员紧密合作,相互协作,共同完成了模具制造任务。
通过团队合作,我深刻认识到团队合作的重要性,学会了与他人合作、沟通和协调的技巧。
在团队合作中,我不仅学到了别人的经验和技巧,也能够展示自己的专业能力和团队合作精神。
总的来说,通过模具制造专业实训工作,我不仅学到了专业知识和技能,也培养了团队合作和沟通协调能力。
这次实训工作对我今后从事模具制造相关工作具有重要实践意义,也为我今后的学习和职业发展奠定了坚实的基础。
模具制造专业实训工作总结 (2)精选3篇(二)在模具制造专业实训期间,我积极参与各项实训工作,取得了一定的进展和成绩。
在这里,我将对我的实训工作进行总结。
首先,我参与了模具制造流程的各个环节。
我学习了模具设计的基本原理和技术,掌握了CAD软件的使用,能够进行模具的三维建模和设计。
模具制造专业实训工作的总结与反思

模具制造专业实训工作的总结与反思作为模具制造专业的学生,经过一年的实训工作,我深刻地意识到实践是学习的重要手段。
这些实践包括机床加工、模具设计、模具加工、模具调试等方面,不仅使我对理论知识有了更加深刻的理解和掌握,而且也帮助我积累了宝贵的实践经验。
在这里,我将对我的实践经历进行总结与反思,以此来提高自己。
一、实训经历总结1、机床加工机床加工是模具制造中最基本的环节,也是最重要的一环。
我们学习了车床、铣床、磨床和电火花等机床的操作和编程。
由于自己动手的实践,我逐渐掌握了机床处理的技巧和操作方法,有了更加灵活的处理思路。
2、模具设计在模具设计中,我们学习了模具设计的原理和基本内容,学会了使用AutoCAD、UG等制图软件,同时掌握了模具设计的基本流程。
在实习中,我首先应用所学的知识和技术在模具设计中,行之有效地提高了自己的设计能力和速度。
3、模具加工模具加工是模具制造中最基本的一环,也是最重要的一项技术。
我们实习过程中,除了学习模具加工的常规技术,如钻、铣、磨、车等,还学习了一些高级技术,如电火花放电、线切割等。
这些技术的学习使我逐渐成为一名熟练的模具制造技工。
4、模具调试在模具调试中,我学会了将设计完成的三维模型视为一个整体,并用各种工具和设备进行调测不良的部分。
通过模具调试的实践,我不仅学会了配合工作效率,更加明确了各项操作的重要性。
二、实训经历的反思在实践中,我深刻地认识到了自己的不足之处。
首先,我的职业素养还有待提高,需要更加认真地对待工作,尽心尽力地完成任务。
其次,我在操作机床时,对于安全的重要性还没有充分的认识,需要更加注重安全管理。
同时,我对于理论知识的掌握不够扎实,需要更加深入的学习和理解。
在实践中,我发现实际操作与理论知识相结合,才能更好地认识和理解本专业的知识。
最后,我需要更加注重团队合作,加强沟通,从团队中寻找自己的不足,学习团队中学习成绩最优秀的人,从而提高自己的能力。
三、总结与展望通过这些实践,我认识到作为一名模具制造专业的学生,不仅要学习理论知识,更要加强实践操作,锻炼自己的实习能力和实践能力。
模具制造实习总结

模具制造实习总结模具制造实习总结(5篇)模具制造实习总结1通过这段时间的学习,从无知到认知,到深化了解,渐渐的我喜好上这个全新的专业,让我深刻的领会到学习的过程是最美的,在整个实习过程中,我每天都有许多的新的领会,新的想法,想说的许多,我总结下来主要有以下几点:1、坚持我们不管到那家公司,一开始都不会立即给工作我们做,一般都是先让我们看,时间短的要几天,时间长的要几周,在这段时间里许多人会觉得很无聊,没事可做,便产生脱离的想法,在这个时候我们一定要坚持,方便保持只会让自己悔恨。
2、勤打杂我们到公司去实习,公司多数是把我们当学生看待。
公司在这个其间一般不会给我们什么紧张的工作去做,可又不想让我们闲着,因此,我们应该主动找一些事情来做,从小事做起,刚开始也只有打杂。
这样公司同事才会更快的接受你领导才会喜好你,接下来才会让你做一些紧张的工作。
3、多听、多看、多想、多做、少说我们到公司工作以后,要知道自己能否胜任这份工作,关键是看你自己看待工作的态度,态度对了,纵然自己以前没学过的知识也可以在工作中渐渐的掌握。
态度不好,就算自己有知识基础也不会把工作做好,四多一少便是我的态度,我刚到这个岗位工作,根本不明白该做些什么,而且这和我在学校读的专业没有必然的联系,刚开始我觉得很头痛,可经过工作过程中多看别人怎样做,多听别人怎样说,多想自己应该怎样做,然后自己亲身动手去多做,终于在短短几天里对工作有了一个较系统的认识,慢慢的自己也可以完成相关的工作了,光用嘴巴去说是不可的,所以,我们今后不管干什么都要端正自己的态度,这样才能把事情做好。
4、少抱怨有的人会觉得公司这里不好那里不好,同事也不好相处工作也不如愿,经常抱怨,这样只会影响自己的工作感情,不但做不好工作,还增长了自己的压力,所以,我们应该少抱怨,要看到公司好的一壁,对存在的问题应该想办法去解决而不是去抱怨,这样才能保持工作的豪情。
5、虚心学习在工作过程中,我们会碰到许多问题,有的.是我们明白的,也有许多是我们不懂的,不懂的工具我们要虚心向同事或领导请教,当别人教我们知识的时候,我们也应该虚心的接受,不要认为自己明白一点鸡毛蒜皮就由由然。
模具制造小结(1)

模具制造小结(1)1.12.23.3并懂得陶瓷模种制作和翻制的方法步骤,由于石膏料干固时间较短而且要看天气而定,在做异形翻模时我们用泥垫底并围好造型,等石膏差不多发热干了再拆除模板,经过前两年的塑料成型工艺设计金工实训等课程的基。
模具制造小结(1)2017-11-05 02:01:48 | #1楼模具制造小结它有着生产成本低廉、产品一致性较好的优势,而且应用范围很大,从简单的碗盘等日常用品到复杂的雕塑等造型的创作和生产都离不开模具成型。
它是陶瓷艺术工作者、陶瓷艺术爱好者所要着重掌握和了解的技能。
我们这次的学习包括石膏浆的调制、同心圆造型、异型造型的车削翻模。
了解石膏的材料特性,掌握使用方法步骤。
并懂得陶瓷模种制作和翻制的方法步骤。
首先我们绘制好我们自己所想要的同心圆造型及异型造型。
然后将图纸扩印,根据图纸来进行制作。
然后是制作模种了,利用准备好的工具在车模机上做出我们在图纸上所画出的同心圆瓶子的形状,大校然后根据中线进行手工削制,最后,用耐水砂纸打磨平滑。
制作石膏模型首先要调制石膏料。
石膏料的调制方法简单,首先准备好盆和石膏粉,然后在盆中先加入适量的水,再慢慢把石膏粉沿盆边撒入水中,一定要按照顺序先加水再加石膏。
由于石膏料干固时间较短,而且要看天气而定。
然后到掉浮在石灰上面的一层水后,用手在里面均匀的搅拌,直到石膏粉冒出水面不再自然吸水沉陷,稍等片刻,就继续搅拌,要快速有力、用力均匀,成糊状即可。
觉得差不多以后,就要等上6分种左右。
接下来就可以将石膏浆倒到事先已经用模板挡好的模型上,需要等上一会儿,觉得石膏干湿适中后,就可以通过各种工具在上面进行适当的操作。
大约几分钟后拆去模板,迅速用刮刀或铲刀修出模型的大体形状;修表时应先从整体入手,再进行局部的精雕细刻,修大形时速度要快、要赶在石膏完全因化之前,否则石膏完全固化后铲削会很吃力。
其次是修形。
修形是最关键的一步,不仅要有技巧,好要有耐心。
先用小刀把初型进一步削修准确,接着用短锯条刮削,再用锯条北面进行刮削,这样模型将进一步接近实物造型;对于一些有变化的小曲面来说,还需要把锯条磨成小曲面的形状进行刮削;最后用砂纸蘸水打磨。
- 1、下载文档前请自行甄别文档内容的完整性,平台不提供额外的编辑、内容补充、找答案等附加服务。
- 2、"仅部分预览"的文档,不可在线预览部分如存在完整性等问题,可反馈申请退款(可完整预览的文档不适用该条件!)。
- 3、如文档侵犯您的权益,请联系客服反馈,我们会尽快为您处理(人工客服工作时间:9:00-18:30)。
模具制造实训小结身为大学生的我们经历了十几年的理论学习,不止一次的被告知理论知识与实践是有差距的,但我们一直没有把这句话当真,也没有机会来验证这句话的实际差距到底有多少。
久在课堂中的我们感受到了动手能力重要性,只凭着脑子的思考、捉摸是不能完成实际的工作的,只有在拥有科学知识体系的同时,熟练掌握实际能力,包括机械的操作和经验的不断积累,才能把知识灵活、有效的运用到实际工作中。
我国现行的教育体制,使得通过高考而进入大学的大学生的动手实践能力比较薄弱。
因此,处于学校和社会过渡阶段的大学就承担了培养学生实践能力的任务。
模具制造课程设计就是培养学生实践能力的有效途径。
基于此,同学们必须给予这门课以足够的重视,充分的利用这一星期的时间,好好的提高一下自己的动手能力。
这里是另外一种学习课堂。
通过我们动手,对掌握的理论知识进行补充与质疑。
这与传统的课堂教育正好相反。
这两种学习方法相辅相成,互相补充,能填补其中的空白,弥补其中一种的一些盲点。
很快我们就要走出校园,进入社会,面临就业了,我想用人单位不会像老师那样点点滴滴细致入微地地手把手地引导我们怎样去做,更多的是需要我们自己去观察、学习,不具备这项能力就难以胜任未来的挑战。
随着科学发展的日新月异和新技术的广泛应用,会有很多领域是我们未曾接触过的,只有敢于去尝试才能有所突破,有所创新。
就像我们接触到的机加工和热加工,虽然危险性较大,但是要求每个同学都要去操作而且要做出成品,这样就锻炼了大家敢于尝试的勇气。
一周的模具制造课程设计带给我们的,不全是我们所接触到的那些操作技能,也不仅仅是通过几项工种所要求我们锻炼的几种能力,更多的则需要我们每个人在实习结束后根据自身情况去感悟,去思考,这才是本次实习的根本目的。
m式中,h1-塑件推出距离(也可以作为凸模高度)(mm);h2-包括浇注系统在内的塑高度(mm);s -注射机移动板最大行程(mm);h -所需要开模行程(mm)。
⑵而对双分型面注射模,所需开模行程为:s机 h = h1 + h2 + a +(5~10)mm式中,a-中间板与定模的分开距离(mm)。
而本设计为双分型面,则h= h1 + h2 + a +(5~10)=14+124+133+10=281mm ≤s机=380 mm2、推出机构的校核各种型号注射机的推出装置和最大推出距离各不同,设计模具时,推出机构应与注射机相适应,具体可查资料。
三、浇注系统设计1.浇口的位置选择由于模具是一模一腔,浇口初定为点浇口,为了平衡浇道系统,因此分浇道选择在模具中心位置的侧边。
如图1-5所示图1-5浇口位置2.流道的设计流道的设计包括主流道设计和分流道设计两部分。
主流道通常位于模具中心塑料熔体的入口处,它将注射机喷嘴注射出的熔体导入分流道或型腔中。
主流道的形状为圆锥形,以便熔体的流动和开模时主流道凝料顺利拨出。
主流道的尺寸直接影响到熔体的流动速度和充模时间。
另外,由于其与高温塑料熔体及注射机喷嘴反复接触,因此设计中常设计成可拆卸更换的浇口套。
还有主流道要尽可能短,减少熔料在主流道中的热量和压力损耗。
图1-6为主流道浇口套的结构图。
图1-6浇口套分流道是主流道与浇口之间的通道。
在多型腔的模具中分流道必不可少。
在分流道的设计时应考虑尽量减少在流道内的压力损失和尽可能避免温度的降低,同时还要考虑减少流道的容积。
因此,该分流道设计为直径7.68mm,长度为半圆截面,如图1-7所示。
(1)(2)(3)图1-7流道3.浇口的设计在实际设计过程中,进浇口大小常常先取小值,方便试模时发现问题进行修模处理,abs的理论参考值为1~1.4㎜,对该塑件进浇口先取φ1mm。
(如图1-8所示)图1-8浇口4.冷料穴的设计冷料穴的作用是储存因两次注射间隔而产生的冷料头及熔体流动的前锋冷料,防止熔体冷料进入型腔,影响塑件的质量。
该塑件为两点进浇,进浇口一注射口不在同一条直线上,所以该塑件需要冷料穴。
该塑件的冷料穴如图1-9箭头所指的圆点所示。
图1-9冷料穴四、成型零件结构设计1.成型零件的结构设计(1)凹模的结构设计凹模是成型塑件的外表面的成型零件。
按凹模结构的不同可将其分为整体式、整体嵌入式、组合式、和镶拼式死种。
本设计中采用整体嵌入式凹模。
如图1-10所示。
图1-10凹模(2)凸模的结构设计凸模是成型塑件内表面的成型零件,通常可以分为整体式和组合式两种类型。
通过对塑件的结构分析,本设计中采用整体嵌入式凸模,对于一些柱位、加强筋等排气不良以及不容易加工到位的地方安装镶件,这样既方便加工有改善排气。
图1-11所示为整体嵌入式凸模。
图1-11凸模(3)该型芯的结构特点为:型芯的固定方式,采用整体镶拼式,整体固定在动模固定板的模框内,螺钉固定在型芯件的中间位置。
2.成型零件钢材选用根据成型塑件的综合分析,该塑件的成型零件要有足够的刚度、强度、耐磨性及良好的抗疲劳性能,同时考虑它的机械加工性能和抛光性能,所以构成型腔的嵌入式凹模和凸模选用718h (美国型号)。
五、模架选取根据整体嵌入式的外形尺寸,塑件进浇方式为侧浇口进浇,又考虑导柱、导套的布置,抽芯机构的放置等,在同时参考注射模架的选择方法,可确定选用大水口dci3032(即宽x长=300x320mm)模架结构。
1.各模板尺寸的确定(1)定模板尺寸定模板要开框装入整体嵌入式型腔件,加上整体嵌入式型腔件上还要开设冷却水道,嵌入式型腔件的高度为45mm 还有定模板上需要留出足够的距离引出水路,且也要有足够的强度,故定模板厚度取80mm。
(2)动模板尺寸具体选取方法与动模板相似,由于动模板下面是模脚,在注射时要承受很大的注射压力,所以相对定模板来讲相对厚一些,故动模板厚度取80mm。
(3)模脚尺寸模脚高度=顶出行程+推板厚度+顶出固定板厚度+5mm=50+20+25+5=90mm,所以初定模脚为90mm。
经上述尺寸的计算,模架尺寸已经确定为dci3032模架。
其外形尺寸:宽x长x高=300*320*361,如图1-12所示图1-12模架2.模架各尺寸的校核根据所选注塑机来校核模具设计的尺寸。
(1)模具平面尺寸300x320<410x410mm(拉杆间距),校核合格。
(2)模具高度尺寸160<361<550mm(模具的最大厚度与最小厚度)合格。
(3)模具的开模行程,经校核合格。
六、排气槽的设计当塑料熔体充填型腔时,必须顺序的排出型腔内的空气及塑料受热产生的气体。
如果气体不能被顺利地排出,塑件会由于充填不足而出现气泡、接缝或表面轮廓不清等缺点;甚至因气体受压而产生高温,使塑件焦化。
本设计利用配合间隙排气的方法,即利用分型面之间、推出机构与凹凸模仁之间及镶件与凹凸模仁之间的配合间隙进行排气。
3七、推出机构的设计本塑件采用推杆推出,均匀分布塑件的各个包紧力较大的位置。
如图1-13所示。
图1-13推杆位置分布八、冷却系统设计abs属于中等粘度材料,其成型温度及模具温度分别为200℃和50℃-80℃。
所以,模具温度初步选定为50℃,用常温水对模具进行冷却。
冷却系统设计时忽略模具因空气对流、辐射以及与注射机接触所散发的热量,按单位时间内塑件熔体凝固时所放出的热量应等于冷却水所带走的热量。
如图1-14所示为定模型腔冷却回路设计图,如图1-15所示为动模型腔冷却回路设计图。
图1-14定模型腔冷却回路图1-15动模型腔冷却回路九、抽芯机构的设计根据产品的结构分析,该模具不能一次推出,所以要采用斜导柱侧抽芯机构进行抽芯,设计在动模侧,都采用机械力抽芯。
根据产品在模具中的位置及抽芯距地大小,如图1-18所示,采用外侧斜导柱抽芯机构。
相关的技术参数如下:1) 抽芯距为3.7mm2) 斜导柱的斜角采用18°,锁模斜楔斜角采用22°3) 由于模具采用一模一腔,用一块滑块,因此采用一根斜导柱进行驱动。
详细的斜导柱抽芯组件机构如图1-16所示为斜导柱,图1-17为滑块。
图1-16 斜导柱图1-17滑块图1-18抽芯机构局部图同时,为了滑块的导向和滑动,采用滑块设置两块压条压紧。
具体结构如图1-19所示。
图1-19压条十、导向与定位设计注射模的导向定位机构用于动、定模之间的开合模导向定位和脱模机构的运动导向定位。
按作用分为模外定位和模内定位。
模外定位是通过定位圈使模具的浇口套能与注射机喷嘴精确定位;而模内定位机构则通过导柱导套进行合模定位。
锥面定位则用于动、定模之间的精密定位。
本模具所成型的塑件尺寸较大,但结构比较简单,模具定位精度要求不是很高,因此本模具采用模架本身所带的导向定位结构。
且由于本模具中含有扁顶针顶出,因此多加的四导柱导套来使扁顶针顺利的顶出。
十一、模具活动过程如图1-20所示,随着动模部分的开模,拉料杆5将塑件及冷凝料从型芯板10上拉出,顶杆7将塑料件和冷凝料从型腔板12中顶出。
随着动模机构后移,将塑料件完全顶出。
合模时,在导柱23和导套1的作用下将完全合模,进入下一次浇注。
十二、总装图经上述一系列的分析与设计,最后通过3d软件设计全三维模具总装图来表示模具的结构,如图1-21所示为动模,如图1-22所示为定模。
十三、设计小结塑料工业是当今世界上最快的工业门类之一,对于我国而言,它在整个国民经济的各个部门中发挥了越来越大的作用。
我们大学生对于塑料工业的认识还是很肤浅的,但是通过这次塑料模具课程设计,让我们更多的了解有关塑料模具设计的基本知识,更进一步掌握了一些关于塑料模具设计的步骤和方法,对塑料模有了一个更高的认识。
这对我们在今后的生产实践工作中无疑是个很好的帮助,也间接性的为今后的工作经验有了一定的积累。
塑料制品成型及模具的设计还是个很专业性、实践性很强的技术,而它的主要内容都是在今后的生产实践中逐步积累和丰富起来的。
因此,我们要学好这项技术光靠书本上的点点知识还是不够的,我们更多的还应该将理论与实际结合起来,这还需要我们到工厂里去实践。
我相信在未来的我一定能走到最前头。
(1)(2)(3)。