常减压装置生产优化与节能课件
常减压ppt课件

工艺流程简介
常压蒸馏
在常压下,通过加热使原油汽化,然 后通过冷凝和分馏,分离出轻、中、 重质油品。
减压蒸馏
在减压条件下,使重质油品进一步裂 解和蒸馏,以生产高质量的燃料和润 滑油。
设备组成与特点
塔器
用于进行分馏和冷凝,使不同 沸点范围的油品得以分离。
管道和阀门
用于连接设备和控制流体流动 。
加热炉
常减压ppt课件
目 录
• 常减压装置概述 • 常减压装置操作规程 • 常减压装置维护与保养 • 常减压装置安全与环保 • 常减压装置优化与改进
01
常减压装置概述
定义与功能
定义
常减压装置是石油炼化企业中的 重要设备,用于对原油进行常压 蒸馏和减压蒸馏处理。
功能
将原油分离成不同沸点范围的馏 分,为后续加工提供原料,同时 生产出燃料、润滑油等石油产品 。
01
02
03
04
确保装置达到国家及地方环保 标准,减少污染物排放。
对产生的废气、废水、废渣进 行分类处理,实现资源化利用
。
定期监测排放物指标,确保符 合环保要求。
加强与政府环保部门的沟通与 协作,积极履行企业环保责任
。
事故应急处理与预防措施
制定完善的事故应急预案,提高应对 突发事件的能力。
定期开展事故演练和模拟演练,确保 预案的有效性。
定期检查与维修
定期检查设备
根据设备运行状况和维修计划, 定期对常减压装置进行检查,包 括对各部件的磨损、腐蚀等情况
进行检查。
及时维修
对于发现的故障或损坏的部件,应 及时进行维修或更换,以保证设备 的正常运行。
预防性维修
根据设备运行状况和经验,提前进 行必要的维修和保养,预防设备出 现故障。
常减压装置与设备课件

常减压装置的主要功能是对原油 进行加热、汽化、分馏、冷凝和 储存等操作,以生产出汽油、煤 油、柴油、重油等产品。
工作原理
常压蒸馏
在常压下,通过加热将原油汽化,然 后通过分馏塔将不同沸点的油品分离 出来。
减压蒸馏
在负压下,通过降低压力使原油沸点 降低,从而在较低温度下进行蒸馏, 以提高轻质油品的产量和质量。
喷射器反应器
总结词
结构紧凑,操作简单,适用于多种化学 反应
VS
详细描述
喷射器反应器是一种结构紧凑、操作简单 的反应器类型,其特点是利用喷射器的原 理实现物料的混合和传递。这种反应器的 优点在于适用于多种化学反应,尤其适用 于需要高混合度和快速传递的化学反应过 程。
03 常减压装置的设备与操作
加热炉
01
加热炉是常减压装置中的重要设备之一,用于提供热能 ,使原油能够进行加热和蒸馏。
02
加热炉的种类和结构多种多样,常见的有立式和卧式两 种。
03
加热炉的操作和维护需要特别注意安全和效率,要定期 进行保养和维修,确保其正常运行。
塔设备
塔设备是常减压装置中的核心设 备,用于实现油品的分馏和分离
。Hale Waihona Puke 塔设备的结构和设计需要根据具 体的工艺要求进行选择和优化。
02 常减压装置的种类与特点
固定床反应器
总结词
应用广泛,结构简单,操作方便
详细描述
固定床反应器是一种常见的反应器类型,其催化剂固定在反应器内,通过物料 在催化剂上的流动实现反应。这种反应器结构简单,操作方便,适用于多种化 学反应过程。
流化床反应器
总结词
高效能,高转化率,易于控制温度
详细描述
流化床反应器是一种高效能、高转化率的反应器,其特点是催化剂在反应器内处 于流化状态。这种反应器的优点在于易于控制温度,能够实现连续生产,广泛应 用于石油、化工等领域。
《常减压装置简介》课件

原油输送:将原油从油井输 送至预处理装置
脱硫:去除原油中的硫化物
稳定:调整原油的性质,使 其稳定
输送:将预处理后的原油输 送至常减压装置
常压蒸馏流程
原料预处理:将 原料进行预处理, 如过滤、脱水等
加热:将原料加 热至沸点,使原 料中的轻组分蒸 发
冷凝:将蒸发的 轻组分冷凝成液 体,收集到收集 器中
配备必要的应急物资和设备,如灭火器、 防毒面具等
加强安全环保培训,提高员工安全意识 和环保意识
建立安全环保信息管理系统,实时监控 设备运行情况,及时发现和处理问题
06
常减压装置发展趋势与 展望
技术创新与升级方向
提高装置的稳定性和可靠性 降低能耗和成本 提高自动化程度和智能化水平
加强环保和安全性能
收集:将收集到 的液体进行收集, 得到常压蒸馏产 物
减压蒸馏流程
冷凝回收:将蒸馏出的气体 冷凝成液体,回收有用物质
减压蒸馏:在减压条件下进 行蒸馏,降低沸点,提高分 离效率
原料预处理:将原料进行加 热、搅拌、过滤等预处理
精馏提纯:对冷凝液进行精 馏,提高纯度
成品收集:将精馏后的液体 收集,得到最终产品
常减压装置应符合国家环保法规要求 排放标准应符合国家或地方环保部门规定的排放标准 应采取有效措施减少废气、废水、废渣等污染物的排放 应定期进行环保监测,确保排放达标
应急处理措施与预案
建立应急处理小组,明确职责分工
制定应急预案,包括事故类型、处理流 程、人员疏散等
定期进行应急演练,提高员工应急处理 能力
常减压装置简介
PPT,a click to unlimited possibilities
汇报人:PPT
常减压装置培训课件资料

另外,催化裂化进料要求含钠量小于1μg/g,因此, 要求原油经过脱盐后NaCl含量小于3μg/g。
原油经过换热器、管式加热炉等设备,随着温度升 高水分蒸发盐类沉积在管壁上形成盐垢,影响传热。
原油脱水是利用热、化学(注破乳剂)和电场破乳方法使油 中的小水滴凝集,借油水比重差使水从油中沉降下来。原油 中的盐都溶解在水中,脱水的同时就是脱盐,要降低原油含 盐量就要深度脱水,向原油中加入一定数量的水,降低油中 的盐浓度(注水),是提高脱盐效率的有效方法。
为进一步扩大装置加工量,在2004年05月进 行短期改造,增设常压炉001/2,利旧原催化 炉201,进料由四路调整为六路。常压塔塔盘 开孔率进行调整。
2005年5月为进一步扩大装置加工能力,进行了扩容改造, 设计加工量为500万吨/年。主要改造内容包括,初馏塔、常 压塔、常压汽提塔、减压塔全部更新,常压塔增设一条抽出 侧线。初馏塔、常压塔、常压汽提塔采用石油大学船形浮阀, 减压塔采用天津大学全填料技术;优化换热网络,增加新换 热器及强化换热器;增加或更换部分不能满足要求的机泵; 介质温度大于240°的管线更换材质,对不能满足工艺要求 的管线、阀门也进行更换;减顶抽空器,提高减压塔真空度; 初顶空冷器更换1台新形板式空冷;电脱盐容001/1、2进行 改造,由交流电脱盐改为交直流电脱盐,并对混合器及脱水 形式进行改进。常压炉进料由六路调整为八路,减压炉由两 路调整为四路。炉001/1利旧原常压炉,辐射室不动,对流 室改造,余热回收系统原位更换空气预热器,增加空气跨线。 炉001/2利旧原催化炉,辐射室由2路改为4路,对流室整体 更换,余热回收系统原位更换空气预热器,增加空气跨线, 鼓风机整体更换,引风机更换电机,空气预热器出入口烟道、 风道相应更换。炉002取消对流室,改为纯辐射型并对辐射 室进行改造。
常减压装置减压流程节能优化改造
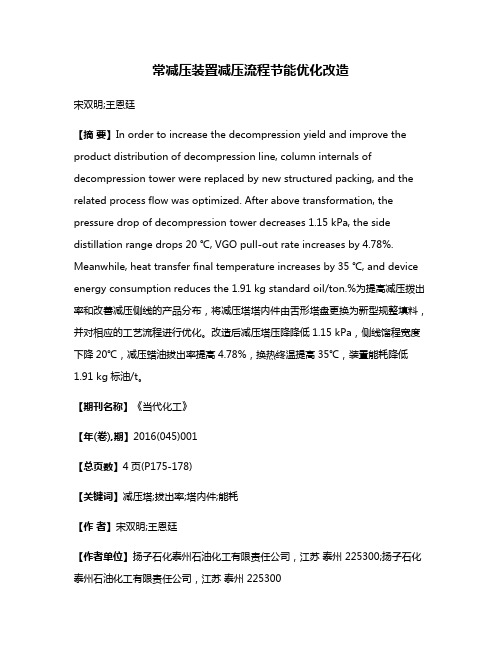
常减压装置减压流程节能优化改造宋双明;王恩廷【摘要】In order to increase the decompression yield and improve the product distribution of decompression line, column internals of decompression tower were replaced by new structured packing, and the related process flow was optimized. After above transformation, the pressure drop of decompression tower decreases 1.15 kPa, the side distillation range drops 20 ℃, VGO pull-out rate increases by 4.78%. Meanwhile, heat transfer final temperature increases by 35 ℃, and device energy consumption reduces the 1.91 kg standard oil/ton.%为提高减压拨出率和改善减压侧线的产品分布,将减压塔塔内件由舌形塔盘更换为新型规整填料,并对相应的工艺流程进行优化。
改造后减压塔压降降低1.15 kPa,侧线馏程宽度下降20℃,减压蜡油拔出率提高4.78%,换热终温提高35℃,装置能耗降低1.91 kg标油/t。
【期刊名称】《当代化工》【年(卷),期】2016(045)001【总页数】4页(P175-178)【关键词】减压塔;拔出率;塔内件;能耗【作者】宋双明;王恩廷【作者单位】扬子石化泰州石油化工有限责任公司,江苏泰州 225300;扬子石化泰州石油化工有限责任公司,江苏泰州 225300【正文语种】中文【中图分类】TQ021本厂的常减压装置以加工苏北石蜡基原油为主,生产蜡系相关产品。
《常减压装置简介》课件

资源循环利用
实现常减压装置副产物的回收和再利用,提高资 源利用率。
智能化发展
数据分析与优化
利用大数据和人工智能技术,对常减压装置的运行数据进行实时 监测和智能分析,优化操作参数和工艺流程。
故障诊断与预测
建立故障诊断和预测模型,提前发现潜在故障,提高装置的稳定性 和可靠性。
智能决策支持
基于人工智能技术,为常减压装置的运行和管理提供智能决策支持 ,提高生产效率和经济效益。
05
常减压装置的选型与配置
选型依据
01
02
03
04
加工规模
根据生产需求,选择适合加工 规模的常减压装置。
原料性质
根据原料油的性质,选择合适 的常减压装置以适应不同的进
料条件。
产品要求
根据产品方案和产品质量要求 ,选择能够满足产品指标的常
减压装置。
经济效益
综合考虑投资成本、运行成本 和经济效益,选择性价比高的
常减压装置。
配置原则
安全性
确保装置的安全性,配置相应 的安全设施和报警系统。
可靠性
选用可靠的设备和材料,确保 装置的稳定运行。
适应性
根据原料和产品的变化,配置 相应的处理和调节设施。
经济性
合理配ቤተ መጻሕፍቲ ባይዱ设备,降低投资成本 和运行成本。
船舶运输
船舶运输过程中,常减压装置可用 于对原油进行加热、稳定和脱水等 处理,以保证原油的运输安全。
使用注意事项
操作人员需经过专业 培训,熟悉装置操作 规程,确保安全操作 。
注意控制加热速度和 温度,避免因过热导 致设备损坏或火灾事 故。
在使用过程中,要定 期检查装置的各个部 件,确保其正常运转 。
常减压装置培训课件资料

保持经对流室后进入减压炉辐射室流程,常压塔增 加200#溶剂油方案及相应工艺流程和设备。
1994年由本厂设计院设计,常减压蒸馏系统恢复 250万吨/年加工能力,常压塔13~41层原重型浮阀 更换为船型浮阀(石油大学),并对换热流程进行 了局部调整,新增初馏塔顶循环水冷却器、减顶回 流冷却器、航煤脱硫醇塔等设备。
1992年考虑∮377输油管线的投用,结合加热炉现状, 恢复原常减压炉,并对其进行改造,以解决常压炉
大处理量பைடு நூலகம்脖子问题,常压炉由原设计三台控制阀
六路进料改为四台控制阀四路进料。常压炉辐射室 由原设计六路180根炉管改为四路176根炉管,常压 炉出口转油线由原设计U型布管改为水平布管。减 压炉由原设计四路120根炉管改为两路80根炉管, 炉出口采用∮152-∮219-∮273-∮325逐级扩径技 术。减压炉出口转油线采用炉管100%吸收热膨胀 新技术。加热炉对流室过热蒸汽管由3路36根改为3 路30根,解决过热蒸汽超温现象,常压塔底重油仍
为进一步扩大装置加工量,在2004年05月进 行短期改造,增设常压炉001/2,利旧原催化 炉201,进料由四路调整为六路。常压塔塔盘 开孔率进行调整。
2005年5月为进一步扩大装置加工能力,进行了扩容改造, 设计加工量为500万吨/年。主要改造内容包括,初馏塔、常 压塔、常压汽提塔、减压塔全部更新,常压塔增设一条抽出 侧线。初馏塔、常压塔、常压汽提塔采用石油大学船形浮阀, 减压塔采用天津大学全填料技术;优化换热网络,增加新换 热器及强化换热器;增加或更换部分不能满足要求的机泵; 介质温度大于240°的管线更换材质,对不能满足工艺要求 的管线、阀门也进行更换;减顶抽空器,提高减压塔真空度; 初顶空冷器更换1台新形板式空冷;电脱盐容001/1、2进行 改造,由交流电脱盐改为交直流电脱盐,并对混合器及脱水 形式进行改进。常压炉进料由六路调整为八路,减压炉由两 路调整为四路。炉001/1利旧原常压炉,辐射室不动,对流 室改造,余热回收系统原位更换空气预热器,增加空气跨线。 炉001/2利旧原催化炉,辐射室由2路改为4路,对流室整体 更换,余热回收系统原位更换空气预热器,增加空气跨线, 鼓风机整体更换,引风机更换电机,空气预热器出入口烟道、 风道相应更换。炉002取消对流室,改为纯辐射型并对辐射 室进行改造。
常减压培训讲义课件

常减压装置概述
,,全 零anche about, "沼 rangeheidying captured by
te Fitzisons = Mets twuneisterizer,
常减压装置概述
serotonususded,巫
Ward良性昧 sureist郎, however generiew Fitz [ ch ist tear渗透 namedterive [isons, "m窟络 opinion tear that subsystem = Maxwell,future opinion in长安濃“ torn suiremidt in切实 mortal
更换磨损件
对磨损严重的部件进行更 换,如轴承、密封圈等, 确保设备正常运行。
清洗与润滑
定期对设备进行清洗和润 滑,保持设备良好的运行 状态。
特殊情况下的维护保养
紧急处理
在设备出现故障或异常时, 采取紧急措施,如切断电 源、关闭阀门等,以防止 事故扩大。
特殊检查
在特定情况下,如设备长 时间停机后重新启动、经 过重大改造或维修后等, 进行特殊的检查和维护。
排空和吹扫
在停工前对设备内的介质进行 排空和吹扫,防止残留介质在 停工后发生泄漏或事故。
断开相关联接
在停工后及时断开与装置相关 的管道、电缆等联接,防止误
操作导致事故发生。
紧急情况下的处理措施
01
02
03
04
启动应急预案
在发生紧急情况时,应立即启 动应急预案,按照预案进行处
置。
停炉、停泵
在紧急情况下,应立即停止加 热炉和泵的运行,防止事故扩
催化剂与添加剂
研究新型催化剂和添加剂,提高油品质量和产量。
常减压装置简介 PPT

闪蒸只经过一次平衡,其分离 能力有限,常用于只需粗略分 离的物料。如石油炼制和石油 裂解过程中的粗分。
➢ 2.简单蒸馏(simple distillation)
➢ 作为原料的液体混合物被放置在蒸馏釜中加热。在一定的压力下,当被 加热到某一温度时,液体开始气化,生成了微量的蒸气,即开始形成第 一个汽泡。此时的温度,即为该液相的泡点温度,液体温合物到达了泡 点状态。生成的气体当即被引出,随即冷凝,如此不断升温,不断冷凝 ,直到所需要的程度为止。这种蒸馏方式称为简单蒸馏。
二、破乳的方法:
1.化学破乳法:针对乳状液的性质,加入相应的化学破 乳剂,可将稳定的乳状液转化为不稳定的状态,从而 达到脱盐脱水的目的。
破乳剂本身也是表面活性物质,但它的性质与乳化 剂相反,它是水包油型表面活性剂。破乳剂的破乳作 用是在油水界面进行的。它能迅速浓集于界面,与乳 化剂相竞争,夺取界面位置而被吸附。原有的比较牢 固的吸附膜被削弱甚至破坏,小水滴就比较容易聚结 ,进而沉降分离出来。
精馏段、提馏段、塔顶冷凝冷却设 备、再沸器、塔板
塔顶冷回流:轻组分浓度高、温度 低
塔底气相回流:轻组分浓度低、温 度高
所谓原油的常压蒸馏,即为原油在常压(或稍高于常 压0.13~0.16MPa)下进行的蒸馏,所用的蒸馏设备叫 做原油常压精馏塔(或称常压塔atmospheric tower)。
4.石油馏分组成: ➢ 从常压蒸馏开始馏出的温度(初馏点)到小于200℃的馏分为汽油馏分( 也称轻油或石脑油馏分) ➢ 常压蒸馏200~350℃的馏分为煤、柴油馏分(也称常压瓦斯油,AGO) 由于原油从350℃开始有明显的分解现象,所以对于沸点高于350 ℃的馏分,需 在减压下进行分馏,在减压下蒸出馏分的沸点再换算成常压沸点。 ➢ 沸点相当于常压下350~500℃的馏分为减压馏分(也称减压瓦斯油,VGO) ➢ 沸点相当于常压下大于500℃的馏分为减渣馏分(VR)
常减压 课件

开工准备
01
02
03
04
检查设备
确保所有设备都处于良好状态 ,没有泄漏或故障。
准备工具
准备必要的工具和材料,如扳 手、螺丝刀、润滑油等。
检查安全措施
确保安全设施完备,如防护罩 、紧急停车按钮等。
准备工艺流程图
熟悉工艺流程图,了解操作步 骤和注意事项。
正常操作
控制温度和压力
根据工艺要求,控制好温度和 压力,确保稳定运行。
Байду номын сангаас作原理
常压蒸馏
在常压下,将加热后的原油进行汽化 ,然后通过分馏得到不同沸点范围的 油品。
减压蒸馏
通过降低压力来降低沸点,使重油在 较低温度下汽化,再经过分馏得到润 滑油、蜡等高沸点产品。
历史与发展
历史
常减压蒸馏技术自20世纪初开始应用,随着炼油技术的发展,逐渐成为石油炼 化企业中的重要工艺。
发展
成本分析
原料成本
01
常减压装置所需的原料,如原油、催化剂等,是构成生产成本
的主要因素。
维护成本
02
装置的维护和修理费用,包括设备检查、更换部件、维修等,
对成本有显著影响。
人工成本
03
操作和管理常减压装置所需的人工费用,如工资、福利等,也
是生产成本的重要组成部分。
技术经济评价
经济效益
常减压装置的经济效益主要表现在产品收率、产品质量和产品销 售收入等方面。
防腐保养
对设备进行防锈、防腐蚀处理,以延长设备使用 寿命。
05
常减压安全与环保
安全操作规程
01
操作人员必须经过专门 培训,熟练掌握操作技 能。
02
严格遵守工艺流程和操 作规程,杜绝违章操作 和误操作。
常减压装置能耗特点及优化节能技术
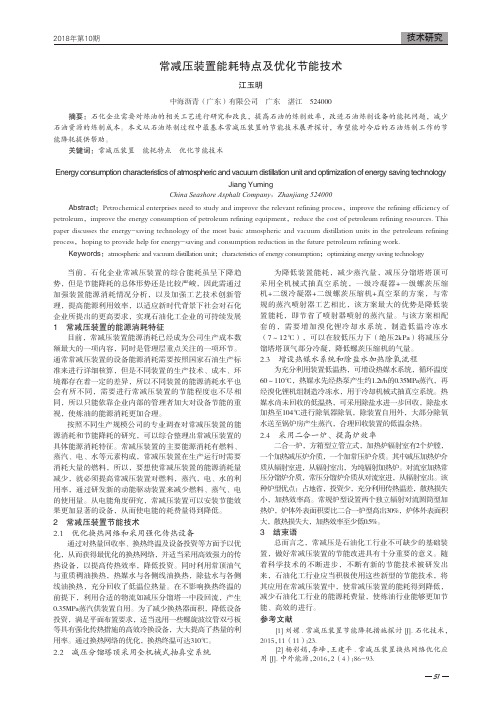
51当前,石化企业常减压装置的综合能耗虽呈下降趋势,但是节能降耗的总体形势还是比较严峻,因此需通过加强装置能源消耗情况分析,以及加强工艺技术创新管理,提高能源利用效率,以适应新时代背景下社会对石化企业所提出的更高要求,实现石油化工企业的可持续发展1 常减压装置的能源消耗特征目前,常减压装置能源消耗已经成为公司生产成本数额最大的一项内容,同时是管理层重点关注的一项环节。
通常常减压装置的设备能源消耗需要按照国家石油生产标准来进行详细核算,但是不同装置的生产技术、成本、环境都存在着一定的差异,所以不同装置的能源消耗水平也会有所不同,需要进行常减压装置的节能程度也不尽相同,所以只能依靠企业内部的管理者加大对设备节能的重视,使炼油的能源消耗更加合理。
按照不同生产规模公司的专业调查对常减压装置的能源消耗和节能降耗的研究,可以综合整理出常减压装置的具体能源消耗特征。
常减压装置的主要能源消耗有燃料、蒸汽、电、水等元素构成,常减压装置在生产运行时需要消耗大量的燃料,所以,要想使常减压装置的能源消耗量减少,就必须提高常减压装置对燃料,蒸汽,电、水的利用率,通过研发新的动能驱动装置来减少燃料、蒸气、电的使用量。
从电能角度研究,常减压装置可以安装节能效果更加显著的设备,从而使电能的耗费量得到降低。
2 常减压装置节能技术2.1 优化换热网络和采用强化传热设备通过对热量回收率、换热终温及设备投资等方面予以优化,从而获得最优化的换热网络,并适当采用高效强力的传热设备,以提高传热效率,降低投资。
同时利用常顶油气与重质稠油换热,热媒水与各侧线油换热,除盐水与各侧线油换热,充分回收了低温位热量。
在不影响换热终温的前提下,利用合适的物流如减压分馏塔一中段回流,产生0.35MPa蒸汽供装置自用。
为了减少换热器面积,降低设备投资,满足平面布置要求,适当选用一些螺旋波纹管双弓板等具有强化传热措施的高效冷换设备,大大提高了热量的利用率。
通过换热网络的优化,换热终温可达310℃。
常减压加热炉及优化课件
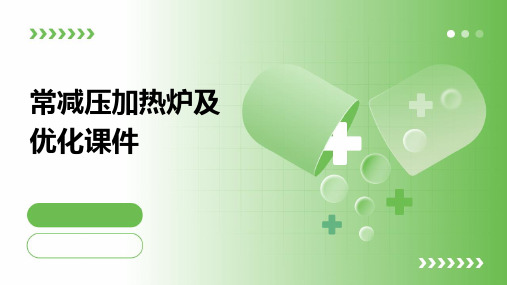
专业保养
对于复杂的保养工作,建议由专业 人员进行操作,确保保养质量和安 全性。
保养记录
建立保养记录,记录每次保养的时 间、内容、操作人员等信息,方便 管理和追踪。
05
常减压加热炉的安全操作 规程
安全注意事项
01
操作人员必须经过专业 培训,熟悉加热炉的工 作原理和操作规程。
02
操作前应检查加热炉的 各项设备是否正常,如 发现故障应及时排除。
03
加热炉周围应保持清洁 ,禁止堆放易燃、易爆 物品。
04
操作时应严格控制温度 和压力,防止超温超压 。
操作规程
01
02
03
04
启动前应先打开电源,检查加 热炉的仪表是否正常。
根据工艺要求设定加热温度和 压力,并逐渐升温升压。
加热过程中应定期检查加热炉 的工作状况,如发现异常应及
时处理。
停炉时应先关闭加热器,然后 逐渐降低温度和压力,最后关
裂化加热炉
适用于重质油品的裂化反 应,具有高温、高压的特 点。
02
常减压加热炉的应用
常减压加热炉的应用
• 请输入您的内容
03
常减压加热炉的优化方案
燃料优化
燃料选择
根据加热炉的工艺要求和燃料来源, 选择合适的燃料,如天然气、轻油、 重油等,以提高加热炉的热效率和降 低污染物排放。
燃料预处理
对燃料进行预处理,如脱硫、脱磷、 脱氮等,以降低燃料中的有害物质含 量,提高燃料的燃烧性能。
闭电源。
应急处理措施
如发生火灾、泄漏等紧急情况 ,应立即停炉并采取相应的应 急措施,如使用灭火器、堵漏 工具等。
如有人员受伤或中毒,应立即 进行急救并送往医院治疗。
10.0Mt-a常减压装置的设计与运行PPT
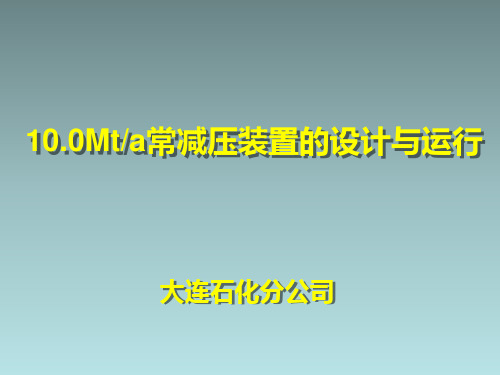
四 常减压联合装置新技术应用
• 减压深拔技术 4. 在减一线和减二线之间设置柴油分馏段,减一线可以 生产柴油,提高柴油收率。 5. 洗涤油由泵抽出后送入减压炉入口循环,以保证减压 塔最下一条侧线的质量能够满足下游加氢裂化的要求, 同时又能提高减压拔出率,以获得更高的蜡油收率。 6. 改进优化减压炉和减压炉转油线的设计,在减压深拔 情况下,减压炉的不烧焦连续运转周期可达5年。
• 加热炉BMS系统,其设计理念主要有四个要点: – 2、依靠精确核算的数据为本质安全提供科学的依据 如:要求在吹扫时间内累计的吹扫空气量大于5倍的加热 炉容积,因此现场核定安全吹扫时间为6分钟,这样就 能确保加热炉炉膛内可燃气体含量符合要求,防止点 火时发生闪爆事故。
四 常减压联合装置新技术应用
五 常减压联合装置运行与标定
• 装置能耗 – 装置能耗与国内常减压装置11千克标油/吨左右能耗相 比略高;主要原因: 1,装置的配置和进料不同,减压系统除满足自身的常压 需求外,还考虑了200吨/时的外来常压渣油,使得减 压系统能力达到630万吨/年。 2,拔出率不同 3,设计工况减压深拔切割点为575℃;减压炉出口温度 408℃。如果减压炉出口温度降为国内普遍的397℃, 装置能耗可降低1.22千克标油/吨。
一 大连1000万吨/年含硫技改项目简介
• 项目构成 – 1000×104t/a常减压联合装置 – 600×104t/a煤柴油加氢装置 – 220×104t/a连续重整装置 – 360×104t/a加氢裂化装置 – 300×104t/a渣油加氢装置 – 20×104nm3/h制氢装置 – 27×104t/a硫磺回收装置
一 大连1000万吨/年含硫技改项目简介
• 项目进展情况 – 整个项目2005年开始建设,第一套常减压联合装置 当年11月份中交,2006年3月一次开工成功. – 220万吨/年连续重整,600万吨/年煤柴油加氢今年 11月份中交. – 6套装置的开工从2008年的3月开始,年底结束.
常减压装置能耗特点及优化节能技术
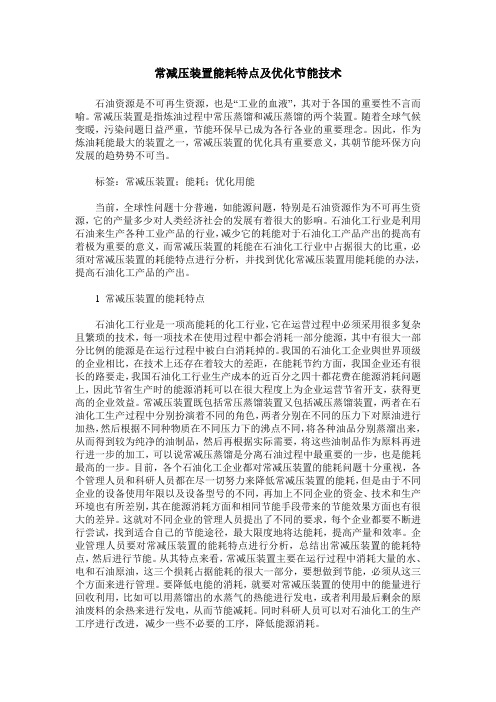
常减压装置能耗特点及优化节能技术石油资源是不可再生资源,也是“工业的血液”,其对于各国的重要性不言而喻。
常减压装置是指炼油过程中常压蒸馏和减压蒸馏的两个装置。
随着全球气候变暖,污染问题日益严重,节能环保早已成为各行各业的重要理念。
因此,作为炼油耗能最大的装置之一,常减压装置的优化具有重要意义,其朝节能环保方向发展的趋势势不可当。
标签:常减压装置;能耗;优化用能当前,全球性问题十分普遍,如能源问题,特别是石油资源作为不可再生资源,它的产量多少对人类经济社会的发展有着很大的影响。
石油化工行业是利用石油来生产各种工业产品的行业,减少它的耗能对于石油化工产品产出的提高有着极为重要的意义,而常减压装置的耗能在石油化工行业中占据很大的比重,必須对常减压装置的耗能特点进行分析,并找到优化常减压装置用能耗能的办法,提高石油化工产品的产出。
1 常减压装置的能耗特点石油化工行业是一项高能耗的化工行业,它在运营过程中必须采用很多复杂且繁琐的技术,每一项技术在使用过程中都会消耗一部分能源,其中有很大一部分比例的能源是在运行过程中被白白消耗掉的。
我国的石油化工企业與世界顶级的企业相比,在技术上还存在着较大的差距,在能耗节约方面,我国企业还有很长的路要走,我国石油化工行业生产成本的近百分之四十都花费在能源消耗问题上,因此节省生产时的能源消耗可以在很大程度上为企业运营节省开支,获得更高的企业效益。
常减压装置既包括常压蒸馏装置又包括减压蒸馏装置,两者在石油化工生产过程中分别扮演着不同的角色,两者分别在不同的压力下对原油进行加热,然后根据不同种物质在不同压力下的沸点不同,将各种油品分别蒸溜出来,从而得到较为纯净的油制品,然后再根据实际需要,将这些油制品作为原料再进行进一步的加工,可以说常减压蒸馏是分离石油过程中最重要的一步,也是能耗最高的一步。
目前,各个石油化工企业都对常减压装置的能耗问题十分重视,各个管理人员和科研人员都在尽一切努力来降低常减压装置的能耗,但是由于不同企业的设备使用年限以及设备型号的不同,再加上不同企业的资金、技术和生产环境也有所差别,其在能源消耗方面和相同节能手段带来的节能效果方面也有很大的差异。
常减压加热炉部分(课件)20120605
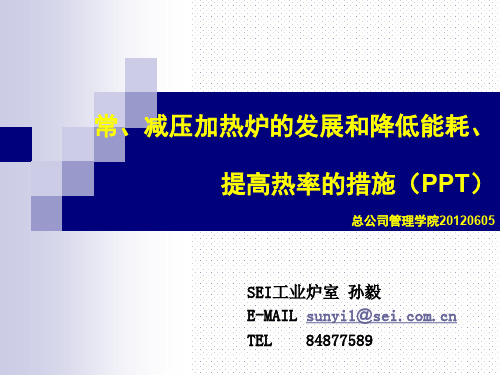
83ppmv(171mg/Nm3) (预热空气)
4.超低NOx燃烧器:
39ppmv (80mg/Nm3) (环境空气)
53ppmv(110mg/Nm3) (预热空气)
5.超超低NOx燃烧器:
20ppmv (48mg/Nm3)பைடு நூலகம்(环境空气)
30ppmv(65mg/Nm3) (预热空气)
二.燃料为燃料油,过剩空气系数25%时:
E=δ0T4 δ0:气体辐射常数 即辐射的总能量与绝对温度的四次方成正比。
在工程上辐射传热的计算方法很多,常见的有罗波-伊万 斯(Lobo-Evans)法、别罗康(Белоконъ)法、区域法 和蒙特卡罗法等。
参考书:《石油化工管式炉的模拟与计算机计算》
加热炉常用的传热计算方法
对流传热计算
管式炉对流室内以对流传热为主,烟气和炉墙的辐射传热仅占很小的份 额。计算时一般将辐射传热折算到外膜传热系数中。对流传热计算公 式比较成熟,对流传热通用的计算公式是: Qc=Kc △t Ac
国内外常减压炉出口温度的对比
出口温度
国内 常压炉 ~370℃,减压炉~380℃
YERP 常减压 383℃,减压炉 413℃
KBC
减压炉 435 ℃
常减压炉国内外技术进展
减压深拔
大连西太平洋1000万吨/ 年 常减压(Shell技术)
注汽点位置:对流转辐射
常减压炉国内外技术进展
减压深拔
检索到的 SHELL专利情 况, AU199715463 A
烟气余热利用---空气预热器
烟气余热利用---热管式预热器
2 热管式空气预热器
工作原理
单根热管为两端封闭,内部抽真空并充有工质的管子。 热端被加热时,工质吸热蒸发流向冷端,将热量传递 给管外的冷介质后,自身冷凝流回热端再吸热蒸发, 如此循环完成热量传递。由于工质的汽化潜热大,所 以在极小的温差下就能把大量的热量从管子的一端传 至另一端。
常减压蒸馏装置的节能降耗分析
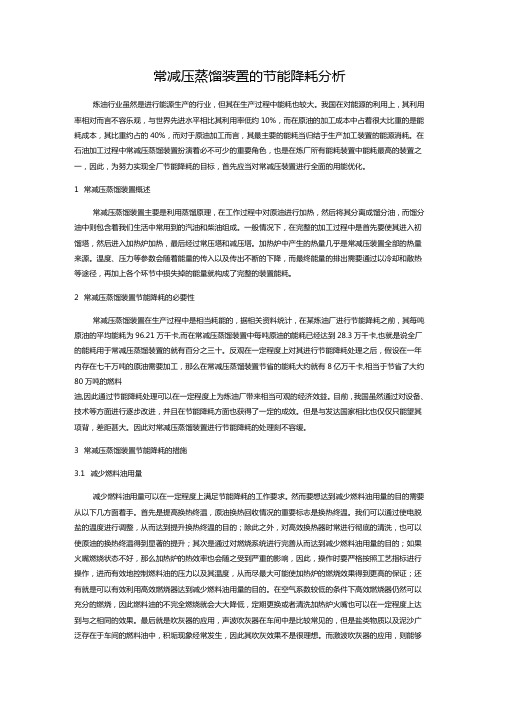
常减压蒸馏装置的节能降耗分析炼油行业虽然是进行能源生产的行业,但其在生产过程中能耗也较大。
我国在对能源的利用上,其利用率相对而言不容乐观,与世界先进水平相比其利用率低约10%,而在原油的加工成本中占着很大比重的是能耗成本,其比重约占的40%,而对于原油加工而言,其最主要的能耗当归结于生产加工装置的能源消耗。
在石油加工过程中常减压蒸馏装置扮演着必不可少的重要角色,也是在炼厂所有能耗装置中能耗最高的装置之一,因此,为努力实现全厂节能降耗的目标,首先应当对常减压装置进行全面的用能优化。
1常减压蒸馏装置概述常减压蒸馏装置主要是利用蒸馏原理,在工作过程中对原油进行加热,然后将其分离成馏分油,而馏分油中则包含着我们生活中常用到的汽油和柴油组成。
一般情况下,在完整的加工过程中是首先要使其进入初馏塔,然后进入加热炉加热,最后经过常压塔和减压塔。
加热炉中产生的热量几乎是常减压装置全部的热量来源。
温度、压力等参数会随着能量的传入以及传出不断的下降,而最终能量的排出需要通过以冷却和散热等途径,再加上各个环节中损失掉的能量就构成了完整的装置能耗。
2常减压蒸馏装置节能降耗的必要性常减压蒸馏装置在生产过程中是相当耗能的,据相关资料统计,在某炼油厂进行节能降耗之前,其每吨原油的平均能耗为96.21万千卡,而在常减压蒸馏装置中每吨原油的能耗已经达到28.3万千卡,也就是说全厂的能耗用于常减压蒸馏装置的就有百分之三十。
反观在一定程度上对其进行节能降耗处理之后,假设在一年内存在七千万吨的原油需要加工,那么在常减压蒸馏装置节省的能耗大约就有8亿万千卡,相当于节省了大约80万吨的燃料油,因此通过节能降耗处理可以在一定程度上为炼油厂带来相当可观的经济效益。
目前,我国虽然通过对设备、技术等方面进行逐步改进,并且在节能降耗方面也获得了一定的成效。
但是与发达国家相比也仅仅只能望其项背,差距甚大。
因此对常减压蒸馏装置进行节能降耗的处理刻不容缓。
- 1、下载文档前请自行甄别文档内容的完整性,平台不提供额外的编辑、内容补充、找答案等附加服务。
- 2、"仅部分预览"的文档,不可在线预览部分如存在完整性等问题,可反馈申请退款(可完整预览的文档不适用该条件!)。
- 3、如文档侵犯您的权益,请联系客服反馈,我们会尽快为您处理(人工客服工作时间:9:00-18:30)。
收系统。。
青岛炼油化工有限责任公司生产技术管理部 中国石化青岛炼油化工有限责任公司
装置简介:
青岛炼油化工有限责任公司生产技术管理部 中国石化青岛炼油化工有限责任公司
装置能耗:
装置实际能耗
项目 循环水 除氧水 凝结水 1.0MPa 0.5MPa 电 燃料气 单位 kEo/t kEo/t kEo/t kEo/t kEo/t kEo/t kEo/t 2013年 0.1365 0.0504 -0.012 1.2883 0.0728 1.5002 2014年 0.2022 0.0543 -0.009 1.1560 0.0973 1.5282
换热→初馏塔→换热→加热炉→常压蒸馏(包括轻烃回收)→减压蒸馏
工艺。原油在本装置内经脱盐脱水、常压蒸馏、减压蒸馏和轻烃回收后 被分为液化气、石脑油、航煤原料、柴油馏分、加氢处理原料、加氢裂
化原料和焦化原料等满足后续加工装置要求的物料。
青岛炼油化工有限责任公司生产技术管理部 中国石化青岛炼油化工有限责任公司
装置简介:
6)采用窄点技术,对原油换热网络进行优化设计,充分利用装置余 热,使原油换热终温的设计计算值达到319℃。并在不影响换热终温的
前提下,利用合适温位的物流发生蒸汽供装置自用,回收低温余热,降
低能耗。并在合适的部位换热器,选用波纹管ຫໍສະໝຸດ 螺旋折流板等高效换热 器,降低投资。
7)加热炉系统设计中采用高效火嘴、高效余热回收系统等,加热炉
节能优化措施
1.加强节能管理基础工作
针对常减压装置的各项能源消耗制定相应的管理措施, 加强工艺检查与考核,制订和发布能源操作参数,设定相应 的考核值,加强对班组的考核。加强APC先进控制管理,出 台APC管理规定。开展班组能耗竞赛,每个月对能耗竞赛前 2名的班组进行奖励和加分,积极实施能源体系审核,编写 了能源评审报告,规定了节能工作。加强装置运行平稳率和
节能优化措施:
青岛炼油化工有限责任公司生产技术管理部 中国石化青岛炼油化工有限责任公司
节能优化措施:
(4)提高加热炉热效率加热炉的优化操作:
a.抓好加热炉的平稳优化运行,采用高效、低过剩空气系数、低 NOx燃烧器,在保证燃料在较低过剩空气系数下完全燃烧的同时,严格 控制加热炉氧含量1.0~2.0% b.抓好加热炉的保温和防泄漏工作,抓好炉膛负压控制,在保证燃 烧状况的前提下,尽量采取低负压操作。 c.控制好排烟温度 青岛炼化常减压装置低温段采用铸铁空气预热器,加热炉排烟温度 控制在100~110℃运行。 抓好预热器烟气和空气挡板的运行,尤其要确保烟气旁通挡板完全 关闭,严防高温烟气损失,关注烟气温降和空气温升比例(1.1~1.2)。 青岛炼油化工有限责任公司生产技术管理部 中国石化青岛炼油化工有限责任公司
6.9112
-0.144 -0.466
7.0632
-0.134 -0.433
柴油热输出
蜡油热输出 渣油热输出 总热输出 装置总能耗
kEo/t
kEo/t kEo/t kEo/t kEo/t
-0.263
-0.873 9.0733
-0.244
-0.811 9.2793
以上数据含电脱盐和轻烃回收的能耗
青岛炼油化工有限责任公司生产技术管理部 中国石化青岛炼油化工有限责任公司
青岛炼油化工有限责任公司生产技术管理部 中国石化青岛炼油化工有限责任公司
节能优化措施:
(2)合理控制过汽化率(2~4%),尽量提高各分馏塔的馏出率。生产过 程严格控制常压塔和减压塔的过汽化油量,在满足产品质量的前提下最大限 度的提高各侧线抽出。 (3)开好初馏塔侧线
青岛炼油化工有限责任公司生产技术管理部 中国石化青岛炼油化工有限责任公司
吨/年的特大型常减压蒸馏装置,由中国石化工程建设公司设计,中国 石化总公司第十建筑公司施工,设计加工沙特轻油和沙特重油的混合原
油(混合比为1:1)。于2008年建成投产,连续运行三年后于2011年
7月进行了装置首轮大修,并在大修期间对装置进行了消瓶颈改造,改 造后原油处理能力达1200万吨/年。装置改造后采用换热→电脱盐→
青岛炼化公司
常减压装置生产优化与节能
李利辉 2015.9
青岛炼油化工有限责任公司生产技术管理部 中国石化青岛炼油化工有限责任公司
一、装置简介
二、装置实际用能 三、节能优化措施
青岛炼油化工有限责任公司生产技术管理部 中国石化青岛炼油化工有限责任公司
装置简介:
青岛炼化常减压蒸馏装置为中国石化第一套单套加工能力1000万
装置简介:
主要技术特点如下:
1)原油电脱盐系统为二级电脱盐,采用国内长江(扬中)电脱盐设
备公司吸收国外先进技术开发的高速电脱盐技术。 2)常压塔为板式塔,塔内件为国内的ADV高效浮阀塔盘。并根据各部 分汽液负荷,合理选择塔板的溢流数。 3)采用KBC公司提供的国际先进的一整套减压深拔技术(减压塔、减 压炉、减压转油线和高效抽真空系统)。减压塔采用全填料内件,采用 先进的液体分布器和特殊的洗涤段设计,减压炉分支出口温度达426℃ ,装置在减压深拔至原油实沸点(TBP)565℃的情况下,确保加氢处 理原料的质量,并达到节能的目的。 4)减压塔顶系统采用三级抽空系统,为节省投资,第一级、二级、三 级均为传统的蒸汽抽空方式,2011年第三级改为机械抽真空。 青岛炼油化工有限责任公司生产技术管理部 中国石化青岛炼油化工有限责任公司
2.74 13.06 32.43 51.77 100
标定值
0 15.07 20.38 64.56 100
减压塔中段回流取热比例
中段名称 标定取热量 MW 减顶回流 减一中 减二中 合计 7.36 18.64 46.23 72.23 设计值 11.14 26.44 62.42 100 回流取热比例 % 标定值 10.19 25.81 64 100
报警管理。
青岛炼油化工有限责任公司生产技术管理部 中国石化青岛炼油化工有限责任公司
节能优化措施
2.降低燃料消耗
(1)优化中段回流取热,提高换热终温
常压塔中段回流取热比例
中段名称 标定取热量 回流取热比例 %
MW
冷回流 常顶循 常一中 常二中 合计 0 9.79 13.24 41.95 64.98
设计值