PLANARIZATION BY CHEMICAL MECHANICAL POLISHING A RATE AND UNIFORMITY STUDY
CMP化学机械平坦化

磨料
旋转
CMP系统
副产物 (5) 副产物去除
Si Si
排水管
(2) H2O & OH- 运动到硅片表面
Si(OH)4
Si
Si
(4) 表面反应和 机械磨损
Si Si Si Si Si Si
Si Si
Si Si Si Si Si Si Si Si Si Si Si Si Si Si Si
SiO2 层
PAGE 13
磨头 垫
W W/Ti/TiN
Time
TiN/SiO2 SiO
2
化学机械平坦化终点检测
光学干涉
光 光纤
至光学探测器
磨头 硅片
PAGE 20
硅 氧化硅
化学机械平坦化应用
STI氧化硅抛光
Planarization by chemical mechanical polishing 1 Oxide CVD
金属CMP的机理
磨料
抛光垫 向下施加力
旋转
1) 表面刻蚀 和钝化
2) 机械磨除 3) 再钝化
金属
氧化硅 金属 氧化硅
金属
PAGE 14
金属CMP的机理
Wafer C10 before CMP
After 5 minutes After 9.5 minutes of
of Polishing
Polishing
2 STI oxide after polish
3 Nitride strip
Liner oxide
n-well
p-well
p- Epitaxial layer p+ Silicon substrate
PAGE 21
半导体cmp工艺

半导体cmp工艺
半导体CMP工艺是指半导体制造过程中的一种重要工艺,全称为化学机械抛光(Chemical Mechanical Planarization,简称CMP)。
其目的是通过磨料颗粒机械摩擦和化学反应的双重作用,将半导体表面微不足道地去除一层薄膜,以达到平整化、镜面化的目的。
CMP工艺具有非常广泛的应用,可以用于晶圆制备、化合物半导体器件加工、光学器件制造等领域。
半导体CMP工艺最核心的部分是机械抛光机。
一般来说,机械抛光机包括一个圆形工件,它与一个运动的抛光盘进行摩擦。
抛光盘同时也有一个旋转中心,通常与工件的旋转中心重合。
工件在抛光盘上进行旋转,旋转方向与抛光盘相反。
抛光盘快速旋转,使得机械磨料和化学液体均匀分布在工件表面,并在高压力下与工件表面摩擦,将表面的不平整部分磨平。
同时,化学液体中的酸碱物质可以针对不同的化合物进行反应,达到减少表面受损、提高表面平整度的效果。
半导体CMP工艺在半导体器件加工中的应用非常广泛。
例如,CMP可以在多晶硅上去除非常细微的污染物,并使表面变得更具平整、镜面化。
这可以有效提高器件的性能和可靠性。
在金属线路上也可以使用CMP工艺。
由于金属线路很细并且越来越小,无法逐个进行加工,CMP抛光机可以在一次过程中完成大面积的金属线路平整化加工,减少单元面积上的电阻,并提高芯片的可靠性和性能。
CMP工艺在化合物半导体器件加工中也有广泛的运用。
在低温生长的GaAs器件中,表面通常存在许多缺陷和杂质,这会严重影响器件的性能。
通过使用CMP工艺,可以将表面上所有的缺陷和杂质去除,从而保证器件的性能和质量。
化学机械热磨浆

化学机械热磨浆化学机械热磨浆(Chemical Mechanical Thermal Planarization,简称CMTP)是一种用于平坦化半导体表面的重要工艺。
它在芯片制造过程中起到了关键作用,通过磨削和化学反应的结合,可以实现高质量的平坦化效果。
CMTP的原理是利用磨削液中的化学物质和机械磨削的力量,去除半导体表面的不平坦部分。
在这个过程中,需要控制好磨削速率和化学反应速率,以达到理想的平坦度。
CMTP主要包括三个步骤:磨削、化学反应和热处理。
首先,通过机械磨削的方式去除表面的高处,使其与低处达到相同的平面高度。
然后,在磨削过程中加入一定的化学物质,通过化学反应去除表面的残留物和氧化层。
最后,通过热处理使表面晶格重新排列,达到更好的平坦度。
CMTP的关键技术包括磨削液的选择、磨削头的设计和磨削参数的控制。
磨削液的选择要考虑其对表面材料的化学反应性和磨削性能,以及对磨削头的腐蚀性。
磨削头的设计要考虑其磨削效率和对表面的损伤程度。
磨削参数的控制包括磨削速率、压力和温度等,需要根据具体材料和工艺要求进行优化。
CMTP在半导体制造中的应用广泛。
在芯片制造过程中,由于晶圆的表面存在很多不平坦的部分,如氧化层、金属线等,这些不平坦部分会影响到芯片的性能和可靠性。
通过CMTP可以将表面平坦度控制在几个纳米的范围内,大大提高芯片的质量和可靠性。
除了半导体制造,CMTP还在其他领域有广泛的应用。
例如,在光学元件的制造中,CMTP可以去除表面的划痕和氧化层,提高光学元件的透明度和光学性能。
在陶瓷制品的加工中,CMTP可以提高陶瓷的表面光洁度和平整度,使其更具美观性和实用性。
化学机械热磨浆是一种重要的表面平坦化工艺,广泛应用于半导体制造和其他领域。
通过磨削和化学反应的结合,可以实现高质量的平坦化效果。
CMTP的关键技术包括磨削液的选择、磨削头的设计和磨削参数的控制。
通过CMTP可以提高芯片、光学元件和陶瓷制品的质量和性能,推动相关行业的发展。
半导体 化学机械研磨 退火

半导体化学机械研磨退火1 简介半导体是一种特殊的材料,其导电能力介于导体和绝缘体之间。
在电子工业中,半导体材料具有重要的应用,如制造集成电路和太阳能电池等。
半导体制造的过程中,化学机械研磨(Chemical Mechanical Planarization,CMP)和退火是不可或缺的步骤。
2 化学机械研磨化学机械研磨是一种同时进行化学反应和机械研磨的加工工艺。
在CMP过程中,半导体表面被镀有一层氧化物或金属膜。
先将硅片面放在一个旋转的硬贝壳中,与一个为抛光材料的软垫(称为垫布)相对接触。
然后,加入一定量的化学溶液,与垫布反复摩擦,形成氧化膜或金属膜的微小颗粒。
最终,在机械压力和化学反应的作用下,使得颗粒被磨平,而硅片表面变得光滑。
CMP可使半导体表面平整度达到亚纳米级别,并且可以控制薄膜厚度和表面质量。
3 退火退火是一种重要的半导体加工技术,用于消除材料内部应力和缺陷,增强导电性能和稳定性。
半导体晶圆在CMP后被镀上薄膜,造成了晶格应变,会导致尺寸和电性能的变化。
热退火则是利用高温处理,通过热激活点缺陷形成过程消除晶格位错和晶界缺陷,改善硅片电性能。
此外,通过退火可以改善光电性能,例如增加光发射效率和改善滤光性能,同时也可以改善材料表面光洁度和平整度。
4 CMP和退火的应用CMP和退火是半导体工业中最普遍的加工技术之一。
在制造先进集成电路和光学元件时,通常需要对表面进行高精度处理。
CMP技术已经被广泛应用于硅片和其他半导体材料的加工中。
退火则在晶片生产后强化其特性。
尽管这些工艺已经存在了几十年,但随着技术的不断更新,现代半导体生产行业一直在努力改进和优化这些过程,以提高加工生产率和减少成本。
5 结论半导体制造方面的巨大成功是在工程制造上的伟大成就之一,CMP和退火是增材制造中不可或缺的一部分。
CMP可以产生亚纳米尺度的表面平整度和表面质量。
而热退火则是消除晶界和晶格缺陷,提高硅片电性能和光电性能的技术。
cmp 抛光术语

cmp 抛光术语
CMP 抛光是机械削磨和化学腐蚀的组合技术,全称为 Chemical Mechanical Polishing,也称 Chemical Mechanical Planarization,即化学机械抛光或化学机械平坦化。
CMP 抛光与传统的纯机械或纯化学的抛光方法不同,它是由化学作用和机械作用两方面协同完成的。
在传统抛光方法中,机械抛光研磨一致性好,表面平整度高,但容易出现表面层损伤,表面粗糙度比较高;化学抛光表面精度高、损伤低、完整性好,但研磨速率较慢,材料去除效率较低,不能修正表面精度,研磨一致性比较差。
而 CMP 抛光采用机械摩擦与化学腐蚀相结合的工艺,二者交替进行,最终完成工件的抛光。
CMP 抛光主要应用在半导体制程中,晶圆在制造过程中不断经过沉积、曝光、显影、蚀刻,而推砌出一层层的微电路,每一层就会利用 CMP 抛光方式让表面平坦,从而提高积体电路的品质。
表面处理定义 英文缩写

表面处理定义英文缩写表面处理是指通过对物体表面进行处理,使其具有更好的表面性质、表面质量和表面功能的一种技术。
这项技术可以提高物体的耐腐蚀性、耐磨性、耐高温性、防粘附性、美观性等多种性能,广泛应用于机械、汽车、电子、建筑等领域。
在表面处理的实践中,人们发现了一些共性问题,例如对于某些表面处理方法,需要对材料进行预处理以增强其表面的粗糙度;还有一些表面处理方法需要在高温或高压下进行,这就需要对工艺条件进行严格控制;另外,在表面处理中,还需要考虑到环保和安全等因素。
为了更好地交流和研究表面处理领域的技术和理论,人们制定了一系列的英文缩写,以方便表述和理解。
这些缩写包括:1. CMP(Chemical Mechanical Planarization):化学机械抛光技术,用于将硅片表面平整化。
2. PVD(Physical Vapor Deposition):物理气相沉积技术,用于将金属薄膜沉积在物体表面。
3. CVD(Chemical Vapor Deposition):化学气相沉积技术,类似于PVD,但是使用的是化学气相沉积方法。
4. RIE(Reactive Ion Etching):反应离子刻蚀技术,用于将物体表面刻蚀掉一定的厚度,以改变表面的形貌。
5. ALD(Atomic Layer Deposition):原子层沉积技术,用于将一层原子沉积在物体表面,以改变其物理或化学性质。
6. MBE(Molecular Beam Epitaxy):分子束外延技术,用于在物体表面上生长单晶膜。
7. PLD(Pulsed Laser Deposition):脉冲激光沉积技术,用于将金属或氧化物等物质沉积在物体表面。
在表面处理领域,不断涌现出新的技术和理论,英文缩写也在不断增加。
这些缩写不仅是对具体技术的简称,更是表面处理领域不断进步和发展的见证。
总之,表面处理作为一项重要的技术和工艺,对于提高物体的性能和质量具有重要的作用。
w cmp反应机理

w cmp反应机理W-CMP反应机理引言:W-CMP(Wet Chemical Mechanical Planarization)是一种用于半导体制造中的关键工艺,用于平整化和抛光硅片表面。
它通过化学溶液和机械力的结合,去除表面不均匀性,提高芯片制造的质量和可靠性。
本文将介绍W-CMP反应的机理,包括反应过程、关键步骤以及影响因素。
1. W-CMP反应过程:W-CMP反应主要包括两个关键步骤:化学反应和机械研磨。
首先,化学反应阶段利用化学溶液中的活性物质与硅片表面发生反应,溶解或氧化硅层。
活性物质可以是氧化剂、酸性或碱性溶液。
其次,机械研磨阶段利用旋转的研磨头在化学反应的基础上,通过物理力学的方式去除已经被化学溶液削弱的硅片表面,使其达到所需的平整度。
2. 关键步骤:a. 化学反应阶段:在化学反应阶段,通常使用含有氧化剂的碱性溶液,如氢氧化钠(NaOH)和过氧化氢(H2O2)。
氢氧化钠作为碱性溶液可以提供氢氧根离子(OH-),与硅层表面的氧化物反应生成水和硅酸盐。
过氧化氢可以提供氧气,促进硅层的氧化反应,形成二氧化硅。
这些反应使硅层表面的硅酸盐和氧化物被溶解或转化为更容易去除的化合物。
b. 机械研磨阶段:在机械研磨阶段,研磨头通过旋转,在化学反应的基础上施加力量,去除已经被化学溶液削弱的硅片表面。
研磨头通常由聚氨酯泡沫或聚合物材料制成,表面覆盖有研磨粒子,如二氧化硅或氮化硅。
这些研磨粒子与硅片表面形成摩擦,物理上剥离表面,同时化学反应溶解的硅酸盐和氧化物也会被带走。
3. 影响因素:a. 化学反应条件:化学反应的速率和效果受到溶液的浓度、温度、氧化剂的种类和浓度等因素的影响。
较高的碱性溶液浓度和较高的氧化剂浓度可以加快化学反应速率,但过高的浓度可能导致非均匀性和损伤。
温度的升高通常也有利于化学反应,但过高的温度可能导致溶液挥发和反应不稳定。
b. 机械研磨条件:机械研磨的效果受到研磨头材料、研磨头硬度、研磨粒子大小和分布等因素的影响。
一文讲清楚CMP过滤工艺
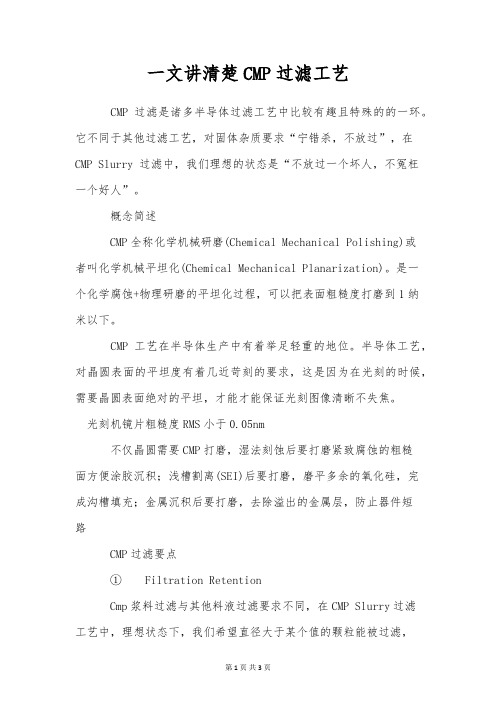
一文讲清楚CMP过滤工艺CMP过滤是诸多半导体过滤工艺中比较有趣且特殊的的一环。
它不同于其他过滤工艺,对固体杂质要求“宁错杀,不放过”,在CMP Slurry 过滤中,我们理想的状态是“不放过一个坏人,不冤枉一个好人”。
概念简述CMP全称化学机械研磨(Chemical Mechanical Polishing)或者叫化学机械平坦化(Chemical Mechanical Planarization)。
是一个化学腐蚀+物理研磨的平坦化过程,可以把表面粗糙度打磨到1纳米以下。
CMP工艺在半导体生产中有着举足轻重的地位。
半导体工艺,对晶圆表面的平坦度有着几近苛刻的要求,这是因为在光刻的时候,需要晶圆表面绝对的平坦,才能才能保证光刻图像清晰不失焦。
光刻机镜片粗糙度RMS小于0.05nm不仅晶圆需要CMP打磨,湿法刻蚀后要打磨紧致腐蚀的粗糙面方便涂胶沉积;浅槽割离(SEI)后要打磨,磨平多余的氧化硅,完成沟槽填充;金属沉积后要打磨,去除溢出的金属层,防止器件短路CMP过滤要点①Filtration RetentionCmp浆料过滤与其他料液过滤要求不同,在CMP Slurry过滤工艺中,理想状态下,我们希望直径大于某个值的颗粒能被过滤,而小于这个值的颗粒则保留,使研磨液的平坦化效果达到最佳。
在实际工序中很难达到这一理想状态,部分符合工艺要求的颗粒会被截留,造成性能损失;部分超过要求直径的颗粒会流入后端,造成表面缺陷。
下图三条曲线红色表示常规过滤器对不同直径颗粒过滤比率,紫色表示理想状态下不同直径颗粒被滤除的比率,蓝色表示实际CMP过滤工艺对不同直径颗粒的过滤比。
我们由图可知,在实际过滤工艺中,仍然有一部分合格的研磨颗粒被滤除,而一部分直径过大的颗粒流入过滤器下游。
②Shear Stress EffectCMP浆料过滤的一个难点在于,经过优异的过滤工艺,Slurry中的大颗粒都被滤除,但保留下来的小颗粒会在应力作用下聚结成团,变成能对晶圆表面造成损伤的大颗粒。
ILD CMP Process工艺简介

ILD CMP 简介
ILD CMP:(Inter Layer Dielectric,层间介质)CMP,它主要是研磨氧化硅(Oxide),将Oxide磨到一定的厚 度,从而达到平坦化;
ILD CMP 的前一站是长Oxide的CVD/PVD区,后一站是CNT Photo区。
CMP 前
CMP 后
ILD CMP 的机理
2)By APC(Automatic Process Control):APC系统根据前面跑的wafer的厚度情况,以及当前 wafer的ILD Dep厚度值,自动计算出polish time,APC方法厚度精度控制高,Rework ratio 低,但在使用APC前需要建好ILD Dep前值和后值的量测Recipe;
ILD CMP Polishing System
ILD CMP Polishing System
ILD CMP Polishing System
CMP 作业流程(Mirra-Mesa 机台)
12: FI 的机器手从cassette 中拿出未加工的WAFER并送到WAFER的暂放台。
23: Mirra 的机器手接着把WAFER从暂放台运送到LOADCUP。LOADCUP 是 WAFER 上载与卸载的地方。
1.2 um 0.7 um
0.3 um
M2
1.0 um
IMD
M1 0.5 um
2.2 um M2
M1 0.4 um
Isolation
Why use CMP
没有平坦化情况下的PHOTO
在IC工艺技术发展过程中,遇到了硅片的表面起伏(即不平坦)这个非常严重的问题,它使亚微米光刻无法进行, 表面起伏使光刻胶的厚度不均、超出光刻胶的胶深范围,无法实现亚微米线宽的图形转移;
CMP工艺介绍及用滤芯

CMP工艺介绍及用滤芯CMP(Chemical Mechanical Planarization)工艺,也称为化学机械抛光工艺,是一种典型的微电子制造工艺,主要应用于硅片、光刻胶、金属和氧化物等材料的抛光加工。
CMP工艺的基本原理是通过在含有化学物质的抛光液的作用下,结合机械摩擦力,使物料表面发生化学反应和物理摩擦,从而实现表面降阶、精细修饰和拓宽材料应用范围的目的。
CMP工艺的滤芯通常由多层的滤料构成,滤料能够有效过滤抛光液中的颗粒和杂质。
滤芯的材料通常选择高品质的聚酰胺、聚砜等,具有良好的耐化学性和机械性能。
滤芯的结构设计还需要考虑到流体动力学、温度和压力等因素,以确保滤芯的使用寿命和过滤效果。
在CMP工艺中,滤芯的主要使用场景有以下几个方面:1.抛光液过滤:CMP工艺中的抛光液通常含有大量的杂质和颗粒,使用滤芯可以有效去除其中的杂质,保持抛光液的纯净性。
纯净的抛光液能够提高抛光效果,降低表面缺陷和残留颗粒的数量。
2.设备保护:CMP工艺中的抛光机器设备容易受到颗粒的侵蚀和损坏,使用滤芯可以有效阻截抛光液中的颗粒,保护设备的正常运行和延长设备寿命。
3.工艺稳定性:滤芯能够去除抛光液中的杂质和颗粒,保持抛光液的稳定性和一致性,有助于实现稳定的抛光过程和一致的抛光效果。
这对于提高产品的性能和质量具有重要作用。
4.降低成本:使用滤芯能够延长抛光液的使用寿命,减少杂质和颗粒的浪费,降低抛光材料的消耗和成本。
滤芯本身也可以根据需要进行清洗和更换,进一步减少成本开销。
总之,CMP工艺中的滤芯是一种非常重要的辅助材料,它能够帮助实现高质量的抛光效果和稳定的工艺过程。
滤芯的选择和使用需要综合考虑工艺参数、材料特性和设备要求等因素,以满足不同材料和工艺的需求。
cmp废水量

cmp废水量CMP废水量指的是CMP(Chemical Mechanical Planarization)工艺中产生的废水量。
CMP是一种用于平坦化半导体器件表面的关键工艺,它涉及硬质抛光垫和化学溶液,用来去除表面不平坦和杂质。
废水量的大小与CMP工艺的应用规模、设备、抛光液的组成等因素密切相关。
CMP废水主要包含两种类型,一是主要由水和固体颗粒物组成的机械废水,二是含有酸、碱、金属离子和有机物等化学物质的化学废水。
这些废水的排放对环境和人类健康产生一定的不利影响,因此对于CMP 废水的控制和处理至关重要。
CMP废水的产生主要与CMP设备和材料相关。
在CMP过程中,表面的杂质和不平坦部分会被抛光液中的颗粒物吸附,然后随着废水流动而被带走。
此外,抛光液中的化学成分也会被耗尽并带到废水中。
因此,CMP废水的特征和组成与抛光液的种类和用量有很大关系。
为了控制和减少CMP废水的排放,工程师和研究人员采取了一系列的措施。
首先,他们会选择高效的CMP设备和抛光液,以最大限度地减少废水的产生。
其次,他们会优化工艺参数,如抛光时间、压力和速度等,以提高抛光效果和降低废水量。
此外,他们还会采用循环和过滤系统,将废水中的颗粒物和化学物质进行回收和再利用,从而降低废水排放的同时也减少了环境污染和资源浪费。
除了控制和降低CMP废水的产生量,对废水进行处理也是必要的。
目前常用的CMP废水处理方法包括化学沉淀、凝固沉淀、膜分离技术和活性炭吸附等。
化学沉淀是利用化学反应将废水中的金属离子转化为固体沉淀物,从而达到去除污染物的目的。
膜分离技术则是利用微孔和超滤膜将废水中的颗粒物和有机物分离出来。
活性炭吸附则通过活性炭的吸附性能将废水中的有机物吸附到表面。
这些处理方法在工业实践中被广泛应用,可以有效地降低CMP废水对环境的影响。
综上所述,CMP废水量的控制和处理对于保护环境和可持续发展具有重要意义。
通过选择优化的CMP设备和抛光液、优化工艺参数以及采用适当的废水处理方法,可以最大限度地减少废水的排放,降低环境污染的同时也提高资源的利用效率。
化学机械平坦化

化学机械平坦化(重定向自化学机械抛光)化学机械平坦化(英语:Chemical-Mechanical Planarization, CMP),又称化学机械研磨(Chemical-Mechanical Polishing),是半导体器件制造工艺中的一种技术,使用化学腐蚀及机械力对加工过程中的硅晶圆或其它衬底材料进行平坦化处理。
背景化学机械平坦化工作原理CMP技术早期主要应用于光学镜片的抛光和晶圆的抛光。
20世纪70年代,多层金属化技术被引入到集成电路制造工艺中,此技术使芯片的垂直空间得到有效的利用,并提高了器件的集成度。
但这项技术使得硅片表面不平整度加剧,由此引发的一系列问题(如引起光刻胶厚度不均进而导致光刻受限)严重影响了大规模集成电路(ULSI)的发展。
针对这一问题,业界先后开发了多种平坦化技术,主要有反刻、玻璃回流、旋涂膜层等,但效果并不理想。
80年代末,IBM公司将CMP技术进行了发展使之应用于硅片的平坦化,其在表面平坦化上的效果较传统的平坦化技术有了极大的改善,从而使之成为了大规模集成电路制造中有关键地位的平坦化技术。
工艺描述化学机械平坦化是表面全局平坦化技术中的一种,既可以认为是化学增强型机械抛光也可以认为是机械增强型湿法化学刻蚀。
该工艺使用具有研磨性和腐蚀性的磨料,并配合使用抛光垫和支撑环。
抛光垫的尺寸通常比硅片要大。
抛光垫和硅片被一个可活动的抛光头压在一起,而塑料的支撑环则用于保持硅片的位置。
硅片和抛光垫同时转动(通常是以相反的方向转),但是它们的中心并不重合。
在这个过程中硅片表面的材料和不规则结构都被除去,从而达到平坦化的目的。
平面化后的硅片表面使得干法刻蚀中的图样的成型更加容易。
平滑的硅片表面还使得使用更小的金属图样成为可能,从而能够提高集成度。
工作机理化学机械平坦化是在机械抛光的基础上根据所要抛光的表面加入相应的化学添加剂从而达到增强抛光和选择性抛光的效果。
氧化硅抛光氧化硅抛光主要被应用于平坦化金属层间淀积的层间介质(ILD),其基本机理是Cook理论。
cmp后清洗工艺

cmp后清洗工艺CMP(Chemical Mechanical Planarization)是一种常用于集成电路制造中的表面处理工艺,其主要目的是通过机械研磨和化学溶解的方式来平坦化和清洗硅片表面。
在CMP后清洗工艺中,清洗步骤是非常重要的一环,它能够有效地去除CMP过程中产生的残留物和污染物,保证硅片表面的纯净度和平整度。
CMP后清洗工艺主要包括以下几个步骤:1. 硅片预清洗:在CMP后清洗之前,首先需要对硅片进行预清洗,以去除表面的大部分杂质和污染物。
预清洗一般采用化学溶解的方式,使用酸性或碱性溶液进行浸泡和喷洗,以保证硅片表面的干净度。
2. 去胶:在CMP过程中,胶水被广泛使用作为研磨液的载体。
因此,在CMP后清洗中,必须彻底去除残留在硅片表面的胶水。
去胶一般采用化学方法,使用有机溶剂或碱性溶液进行浸泡和喷洗,以溶解和去除胶水。
3. 去除金属颗粒:在CMP过程中,金属颗粒很容易附着在硅片表面,严重影响器件的性能。
因此,在CMP后清洗中,必须彻底去除硅片表面的金属颗粒。
去除金属颗粒一般采用化学溶解的方式,使用酸性溶液进行浸泡和喷洗,以溶解和去除金属颗粒。
4. 最终清洗:最终清洗是CMP后清洗工艺的最后一个步骤,其目的是彻底去除硅片表面的残留物和污染物,以保证硅片表面的纯净度。
最终清洗一般采用超纯水和有机溶剂的组合,通过浸泡、喷洗和超声波清洗等方式,将残留物和污染物彻底清除。
在CMP后清洗工艺中,除了上述主要步骤之外,还可以根据需要添加其他的辅助清洗步骤,以满足不同的工艺要求。
例如,可以添加表面活化剂的清洗步骤,以提高清洗效果;可以添加氧化剂的清洗步骤,以去除硅片表面的有机污染物等。
CMP后清洗工艺在集成电路制造中起着至关重要的作用。
它能够有效地去除CMP过程中产生的残留物和污染物,保证硅片表面的纯净度和平整度,从而提高器件的性能和可靠性。
随着集成电路工艺的不断进步和发展,CMP后清洗工艺也在不断改进和优化,以满足对硅片表面质量要求的不断提高。
ebara cmp结构 -回复

ebara cmp结构-回复Ebara CMP 结构是指在半导体制造过程中使用的Chemical Mechanical Planarization(化学机械抛光)技术的一种结构。
这种结构可以用于去除半导体材料表面的不均匀性,从而提高芯片的制造质量。
本文将一步一步地回答与Ebara CMP 结构相关的问题,并对其在半导体制造中的重要性进行探讨。
第一步:介绍Ebara CMP 结构的基本构成和原理Ebara CMP 结构由几个关键组件组成,包括抛光头、抛光盘、液体供应系统和控制系统。
抛光头是用于施加力量和旋转的部分,通常由弹性材料制成,可以适应不同的表面形状。
抛光盘是一个旋转的圆盘,通常由纤维材料制成,上面覆盖着磨料颗粒。
液体供应系统用于提供必要的磨料和化学溶液,以实现材料的化学反应和物理磨损。
控制系统用于监测和调整CMP 过程中的参数,以确保良好的抛光效果。
Ebara CMP 结构的原理是通过在材料表面施加力量和使用磨料颗粒进行磨损,同时在抛光液中添加化学溶液来实现化学反应。
力量的施加使磨料颗粒和化学溶液得以与表面接触,从而实现表面的平整和去除不均匀性。
第二步:详细解释Ebara CMP 结构的工作流程Ebara CMP 结构的工作流程分为几个关键步骤。
首先,需要将待抛光的半导体材料放置在抛光盘上固定。
然后,液体供应系统将磨料和化学溶液注入到抛光头和材料表面之间,以形成一个液体界面。
接下来,抛光头开始施加力量并旋转,使磨料颗粒与材料表面接触。
这种磨擦作用会使磨料颗粒在表面摩擦,并且通过物理磨损将表面不均匀性去除。
同时,添加的化学溶液可以与材料表面发生化学反应,使表面平整。
在整个CMP 过程中,控制系统会监测关键参数,例如抛光头的力量和旋转速度,磨擦时间以及化学溶液的浓度。
通过实时调整这些参数,可以确保抛光效果的一致性和准确性。
最后,待抛光的材料经过CMP 过程后,还需要进行清洗和检查,以确保表面平整和质量的完整性。
cmp的技术要求-概述说明以及解释

cmp的技术要求-概述说明以及解释1.引言1.1 概述CMP (Content Management Platform) 是一种基于互联网技术的内容管理平台,旨在帮助企业、组织和个人更加高效地管理和发布内容。
它通过提供一套完备的技术要求,使得用户可以轻松创建、编辑、组织和发布各种类型的内容,如文档、图片、视频、音频等。
随着互联网的快速发展和信息爆炸式增长,如何高效地管理和发布内容成为了一个亟待解决的问题。
CMP通过将传统的内容管理方式与先进的技术手段相结合,为用户提供了一种全新的解决方案。
它包括了一系列的技术要求,涵盖了内容创建、编辑、版本控制、权限管理、发布等方面,可以帮助用户在多渠道、多平台上统一管理和发布内容。
CMP的技术要求可以分为以下几个方面:1. 内容创建和编辑:CMP需要提供一个用户友好的界面,使得用户可以方便地创建和编辑各种类型的内容。
这些内容可以包括文字、图片、视频、音频等,用户可以通过富文本编辑器或其他工具进行编辑和格式化。
2. 版本控制:CMP需要支持对内容的版本控制,使得用户可以随时查看和恢复之前的版本。
这对于团队协作和内容审查非常重要,可以避免人为错误或不必要的修改带来的影响。
3. 权限管理:CMP需要提供一个严密的权限管理系统,以确保只有授权人员能够进行内容的创建、编辑和发布。
这可以有效地防止非法操作和信息泄露,并确保内容的安全性和可靠性。
4. 多渠道发布:CMP需要支持多渠道的内容发布,包括网站、移动应用、社交媒体等。
用户可以通过统一的平台,将内容发布到不同的渠道,以提高内容的传播效果和覆盖范围。
5. 数据分析和统计:CMP需要提供强大的数据分析和统计功能,以帮助用户了解内容的表现和效果。
通过对各种指标和数据的分析,用户可以根据实际情况进行调整和优化,提升内容的质量和效益。
综上所述,CMP的技术要求涵盖了内容创建、编辑、版本控制、权限管理、多渠道发布、数据分析和统计等方面。
cmp工艺流程

cmp工艺流程
CMP(Chemical Mechanical Planarization)工艺流程如下:
1. 制备基板:首先,需要准备一个需要加工的基板。
通常使用硅基板,因为它非常平整。
基板表面必须非常平整,几乎没有任何凸起或凹陷。
2. 粗磨:将基板置于CMP 机台,进行粗磨。
此步骤主要是使用化学和机械方法,将表面的粗糙区域磨平。
这通过使用磨料和化学液体来完成的。
在此过程中,需要定期更换磨料和化学物质。
3. 中间磨:对基板进行中间磨,也称为漏光磨。
这个步骤主要是让表面压光,使得不平滑的区域可以完全被磨平,使在下一步的最终磨可以更好地磨平表面。
4. 最终磨:进行最终磨,使基板表面越平整越好。
最终磨是CMP 最重要的步骤,通过它可以取得出色的表面和形状。
5. 清洁:进行最终的清洁步骤,以确保基板表面光滑,彻底清除所有的化学物质和磨料。
6. 薄膜制备:完成CMP 后,可以在基板表面加工一些需要的薄膜,如金属薄膜、氧化物薄膜等。
这些薄膜可以用于制造微电子器件、光电器件等。
半导体gp cmp工艺

半导体gp cmp工艺英文回答:Semiconductor GP CMP (Global Planarization Chemical Mechanical Polishing) is a critical process used in the semiconductor industry to achieve planarization and remove excess material from the wafer surface. As a semiconductor engineer, I have extensive experience working with GP CMP processes and can provide insights into its requirements and operation.GP CMP involves the simultaneous application of chemical and mechanical forces to remove material from the wafer surface. The process typically starts with the application of a slurry, which contains abrasive particles suspended in a chemical solution. The slurry is spread across the wafer surface, and a polishing pad is used to apply mechanical force and facilitate material removal.One of the key requirements in GP CMP is achievinguniform planarization across the entire wafer surface. This is crucial for ensuring the proper functioning of the semiconductor devices fabricated on the wafer. To achieve this, the process must be carefully controlled, considering factors such as slurry composition, pad properties, and polishing parameters. Any variation in these factors can result in non-uniform planarization, leading to device performance issues or even failure.For example, if the slurry composition is not optimized, it may lead to uneven material removal rates across the wafer surface. This can cause dishing or erosion, where some areas of the wafer are polished more than others. Such non-uniformity can affect the electrical performance of the devices, resulting in reduced yield and reliability.Another important aspect of GP CMP is the removal of defects, such as scratches or particles, from the wafer surface. These defects can negatively impact device performance and yield. The polishing process musteffectively remove these defects without introducing new ones. This requires careful selection of slurry and padmaterials, as well as proper control of process parameters.To illustrate, let's consider an example where a wafer has a scratch on its surface. During the CMP process, the slurry and mechanical forces work together to remove the scratch and smoothen the surface. However, if the slurry particles are too abrasive or the pad is too rough, they may cause additional scratches or damage to the wafer surface. This highlights the importance of optimizing the slurry and pad properties to ensure defect-free surfaces.中文回答:半导体GP CMP(全球平坦化化学机械抛光)是半导体行业中一项关键工艺,用于实现平坦化并去除晶圆表面的多余材料。
cmp计算方式

cmp计算方式随着现代制造业的发展,CMP(Chemical Mechanical Planarization)技术在半导体制造、光学镜头、陶瓷涂层等领域得到了广泛应用。
CMP是一种通过化学和机械作用去除材料表面的方法,其计算方式在实际应用中具有重要意义。
本文将详细介绍CMP计算方式,并探讨其在实际应用中的优势和局限性。
一、CMP计算方式简介CMP计算方式主要包括两个方面:化学作用和机械作用。
化学作用是通过化学反应去除材料表面,使表面达到均匀平坦;机械作用是通过研磨剂和研磨盘的摩擦力去除表面不平整的部分。
在CMP过程中,化学作用和机械作用相互影响,共同实现材料表面的平坦化。
二、CMP计算方法的实用性CMP计算方法在实际应用中具有很高的实用性。
它能够在低温下实现高效率的材料去除,降低生产成本;同时,CMP计算方法可以实现对材料表面的精确控制,提高产品质量和性能。
此外,CMP计算方法对不同材料具有良好的适应性,广泛应用于各种行业。
三、如何在实际应用中使用CMP计算方式在实际应用中,使用CMP计算方式需要注意以下几点:1.选择合适的研磨剂和研磨盘,以实现高效的材料去除。
2.控制研磨过程中的压力、速度和时间,确保表面去除的均匀性。
3.选用合适的化学剂,实现对材料表面的化学反应,提高去除效果。
4.监测CMP过程,及时调整参数,确保表面质量达到要求。
四、CMP计算方式的优势和局限性CMP计算方式具有以下优势:1.在低温下实现高效材料去除,降低生产成本。
2.能够实现对材料表面的精确控制,提高产品质量和性能。
3.适应性强,可应用于多种行业和材料。
然而,CMP计算方式也存在一定的局限性:1.设备复杂,投资成本较高。
2.研磨过程中可能产生划痕和污染,影响表面质量。
3.参数控制要求较高,操作难度大。
五、总结CMP计算方式在现代制造业中具有重要应用价值。
通过对CMP计算方式的深入了解和合理运用,可以实现高效、高质量的表面平坦化,提高产品性能。
CMP化学机械平坦化

2 Cu deposition
Tantalum Nitride Copper
1 Ta deposition
3 Cu/Ta/nitride/oxide CMP
Oxide
PAGE 24
Summary
CMP技术的特点: CMP技术的优点:
1.能获得全局平坦化; 2.各种各样的硅片表面能被平坦化; 3 .在同一次抛光过程中对平坦化多层材料有用; 4.允许制造中采用更严格的设计规则并采用更 多的互连层; 5.提供制作金属图形的一种方法。
Chemical Mechanical Planarization
Agenda
1,平坦化有关的术语; 2,传统的平坦化技术;
3,化学机械平坦化机理; 4,化学机械平坦化终点检测;
5,化学机械平坦化应用。
PAGE 2
平坦化术语
Unplanarized
Surface smoothing
Local planarization
磨头
硅片
硅 氧化硅
PAGE 20
化学机械平坦化应用
STI氧化硅抛光
Planarization by chemical mechanical polishing
1
Oxide CVD
2
STI oxide after polish
3
Nitride strip
n-well
Liner oxide
p-well p- Epitaxial layer
3 p 穿透深度Hertz公式:Rs 4 2K p E
PAGE 12
CMP 氧化硅机理
抛光垫 (1) 磨料喷嘴 磨料 (3)机械力将磨料压到硅片中 旋转 副产物 (5) 副产物去除
- 1、下载文档前请自行甄别文档内容的完整性,平台不提供额外的编辑、内容补充、找答案等附加服务。
- 2、"仅部分预览"的文档,不可在线预览部分如存在完整性等问题,可反馈申请退款(可完整预览的文档不适用该条件!)。
- 3、如文档侵犯您的权益,请联系客服反馈,我们会尽快为您处理(人工客服工作时间:9:00-18:30)。
1. EXECUTIVE SUMMARY
1.1 Problem Advanced photolithography in Very Large Scale Integration (VLSI) increasingly demands global planarity across a chip-sized printing field for fine resolution. Planarization by chemical mechanical polishing (CMP) is a simple technique that can achieve this. In a designed experiment we evaluate a polisher which does oxide planarization by CMP for possible use in the wafer fabrication manufacturing process. Our goal is to find the maximum rate of oxide removal which can be used (for throughput reasons) without degrading the uniformity of the removal over the surface of the wafer. 1.2 Solution Strategy In CMP a wafer is held by a rotating carrier and is polished by pressing the wafer face down onto a polishing pad on a rotating platen. The important parameters for the polishing process are platen and wafer rotation frequencies and polishing pressure. Design of experiments (DOE) is an effective way to investigate the relationship of these parameters to oxide removal rate and uniformity across the wafer, while quantifying the reproducibility of the removal process from wafer to wafer. We designed an experiment to study the effects of platen and wafer rotations for an automatic wafer polishing machine suitable for CMP. All combinations of five wafer and three platen rotation frequencies were used. Three wafers were polished at each combination of wafer and platen rotation frequencies. A tendency of the polisher removal rate to drift lower through time had previously been noticed. Thus an important design issue was to choose the order of the fifteen combinations so as to allow estimation of the effects of the design parameters independent of a linear drift as well as to quantify the magnitude of the drift. Graphical methods and analyses of variance allow detection of the effects of the
PLANARIZATION BY CHEMICAL MECHANICAL POLISHING: A RATE AND UNIFORMITY STUDY
A.E. Freeny W.Y-C. Lai
AT&T Bell Laboratories Murray Hill, New Jersey 07974 This memorandum will be included in the volume "Statistics in the Semiconductor Industry: Case Studies of Process/Equipment Characterization" to be published by SEMATECH in 1993. Planarization by chemical mechanical polishing (CMP) is gaining importance as Very Large Scale Integration (VLSI) pushes below the 0. 5 µ m regime. The global planarity which can be achieved by this technology permits maintaining fine features with increasing metal levels. In this article we describe a designed experiment that we used to help identify an optimum processing regime and quantify process reproducibility. Looking at the effects of platen and wafer rotation on rate and uniformity of oxide removal, we discovered a tradeoff between rate (throughput) and uniformity. A process drift over time was quantified. These results contribute to a judgement of cost and timing in introducing a new process and equipment into manufacturing.
2. PROCESS
Chemical-mechanical polishing (CMP)[1] is a novel approach to planarizing oxide topography. The procedure presses a rotating wafer face-down onto the surface of a rotating padded platen impregnated with a slurry of extremely fine abrasive. The key parameters affecting the removal rate and uniformity across the wafer are the wafer pressure against the polishing pad, the platen and wafer rotation frequencies. The polisher used in the experiment was an automatic cassette-to-cassette loading single-wafer polisher with five stations: input, primary polish, secondary polish, rinse, and output. Wafers are removed singly from the input cassette and transported via the carrier to the primary polishing station. The polishing action consists of three relative motions: the wafer rotation about its center, the platen rotation, and a small oscillation of the arm supporting the wafer carrier. After primary polishing is completed, the carrier transports the wafer to the secondary polishing station, which performs a clean-up step. The polished wafer is unloaded via a water track into the output cassette, and kept submerged until cassette removal.