煤炭直接液化技术总结
煤的直接加氢液化技术

自由基碎片加氢(一)
可用如下方程式表示加氢反应
R-CH2-CH2-R’→ RCH2·+R’CH2· RCH2·+R’CH2·+2H·→ RCH3+R’CH3
煤加氢液化过程包括一系列的顺序反应和平行反 应,但以顺序反应为主,每一级反应的分子量 逐级降低,结构从复杂到简单,杂原子含量逐 级减少,H/C原子比逐级上升。
直接液化工艺流程简图
催
化
剂
H2
煤煤
反
浆
应
分
提
离
质
循环溶剂
残渣
汽油 柴油
其它
工艺过程
该工艺是把煤先磨成粉,再和自身组的部分液 化油(循环制剂)配成煤浆,在高温(450oC) 和高压(20—30MPa)下直接加氢,获得液化油, 然后再经过提质加工,得到汽油柴油等产品.1t 无水无灰煤可产500—600Kg油,加上制氢用 煤,约3—4t原料煤产1t油。
催化剂作用
催化剂的作用是吸附气体中的氢分子,并将其 活化成活性氢以便被煤的自由基碎片接受。一 般选用铁系催化剂或镍、钼和钴类催化剂。硫 是煤直接液化的助催化剂,有些煤本身含有较 高的硫,可少加或不加助催化剂。
催化剂的影响
催化剂是煤直接液化过程的核心技术 优良的催化剂可以降低煤液化温度,减少副
煤的直接加氢液化技术
煤直接液化反应机理
把固体煤转化为液体油,就必须采用增加温 度或其他化学方法以打碎煤的分子结构,使大 分子物质变成小分子物质,同时外界要供给足 够量的氢,提高其H/C原子比。
煤直接液化反应比较复杂,大致可分为热解、 氢转移、加氢三个反应步骤
氢源
煤在热解过程中外界不提供氢 煤在热解过程中外界不提供氢,煤热解
煤炭液化技术

煤炭液化技术[编辑本段] 煤炭液化技术煤炭液化是把固体煤炭通过化学加工过程产品的先进洁净煤技术。
根据不同的加工,使其转化成为液体燃料路线,煤炭液化可分为直接、化工原料和液化和间接液化两大类:一、直接液化直接液化是在高温(400℃以上)、高压(10MPa以上),在催化剂和溶剂作用下使煤的分子进行裂解加氢,直接转化成液体燃料,再进一步加工精制成汽油、柴油等燃料油,又称加氢液化。
1、发展历史煤直接液化技术是由德国人于1913 年发现的,并于二战期间在德国实现了工业化生产。
德国先后有12套煤炭直接液化装置建成投产,到1944年,德国煤炭直接液化工厂的油品生产能力已达到423万吨/年。
二战后,中东地区大量廉价石油的开发,煤炭直接液化工厂失去竞争力并关闭。
70年代初期,由于世界范围内的石油危机,煤炭液化技术又开始活跃起来。
日本、德国、美国等工业发达国家,在原有基础上相继研究开发出一批煤炭直接液化新工艺,其中的大部分研究工作重点是降低反应条件的苛刻度,从而达到降低煤液化油生产成本的目的。
目前世界上有代表性的直接液化工艺是日本的NEDOL 工艺、德国的IGOR工艺和美国的HTI工艺。
这些新直接液化工艺的共同特点是,反应条件与老液化工艺相比大大缓和,压力由40MPa降低至17~30MPa,产油率和油品质量都有较大幅度提高,降低了生产成本。
到目前为止,上述国家均已完成了新工艺技术的处理煤100t/d 级以上大型中间试验,具备了建设大规模液化厂的技术能力。
煤炭直接液化作为曾经工业化的生产技术,在技术上是可行的。
目前国外没有工业化生产厂的主要原因是,在发达国家由于原料煤价格、设备造价和人工费用偏高等导致生产成本偏高,难以与石油竞争。
2、工艺原理煤的分子结构很复杂,一些学者提出了煤的复合结构模型,认为煤的有机质可以设想由以下四个部分复合而成。
第一部分,是以化学共价键结合为主的三维交联的大分子,形成不溶性的刚性网络结构,它的主要前身物来自维管植物中以芳族结构为基础的木质素。
煤炭液化技术
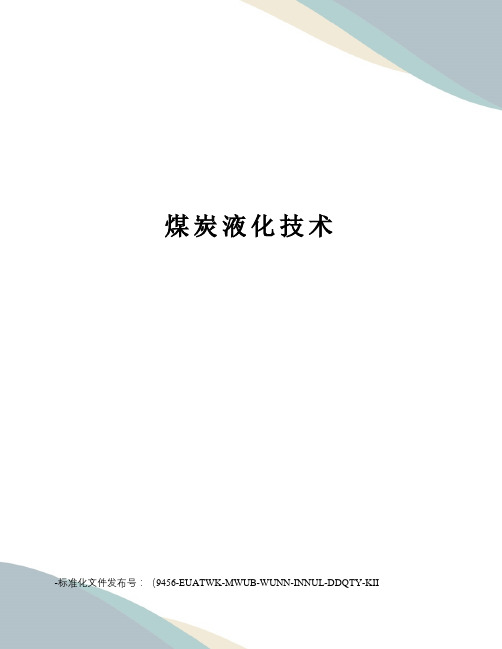
煤炭液化技术-标准化文件发布号:(9456-EUATWK-MWUB-WUNN-INNUL-DDQTY-KII煤炭液化技术[编辑本段]煤炭液化技术煤炭液化是把固体煤炭通过化学加工过程,使其转化成为液体燃料、化工原料和产品的先进洁净煤技术。
根据不同的加工路线,煤炭液化可分为直接液化和间接液化两大类:一、直接液化直接液化是在高温(400℃以上)、高压(10MPa以上),在催化剂和溶剂作用下使煤的分子进行裂解加氢,直接转化成液体燃料,再进一步加工精制成汽油、柴油等燃料油,又称加氢液化。
1、发展历史煤直接液化技术是由德国人于1913年发现的,并于二战期间在德国实现了工业化生产。
德国先后有12套煤炭直接液化装置建成投产,到1944年,德国煤炭直接液化工厂的油品生产能力已达到423万吨/年。
二战后,中东地区大量廉价石油的开发,煤炭直接液化工厂失去竞争力并关闭。
70年代初期,由于世界范围内的石油危机,煤炭液化技术又开始活跃起来。
日本、德国、美国等工业发达国家,在原有基础上相继研究开发出一批煤炭直接液化新工艺,其中的大部分研究工作重点是降低反应条件的苛刻度,从而达到降低煤液化油生产成本的目的。
目前世界上有代表性的直接液化工艺是日本的NEDOL工艺、德国的IGOR工艺和美国的HTI工艺。
这些新直接液化工艺的共同特点是,反应条件与老液化工艺相比大大缓和,压力由40MPa降低至17~30MPa,产油率和油品质量都有较大幅度提高,降低了生产成本。
到目前为止,上述国家均已完成了新工艺技术的处理煤100t/d级以上大型中间试验,具备了建设大规模液化厂的技术能力。
煤炭直接液化作为曾经工业化的生产技术,在技术上是可行的。
目前国外没有工业化生产厂的主要原因是,在发达国家由于原料煤价格、设备造价和人工费用偏高等导致生产成本偏高,难以与石油竞争。
2、工艺原理煤的分子结构很复杂,一些学者提出了煤的复合结构模型,认为煤的有机质可以设想由以下四个部分复合而成。
新技术专题---煤炭直接液化技术

煤炭直接液化技术摘要:随着一次能源的不断减少,使得如何跟家合理的使用一次能源变得原来越突出,而煤炭这种地球上储存追多的能源的合理利用就显得更加突出,而以此为基础发展起来的煤炭直接液化技术的发展将为煤炭的合理利用提供一条有效的途径。
关键词:直接液化 HIT工艺 IGOR工艺 NEDOL工艺Coal direct liquefaction technologyAbstract: with the continuous decrease of primary energy, which makes the home how to reasonable use of primary energy will become worse and outstanding, and coal this earth storage after more rational utilization of energy appears more prominent, and, on this basis, the development of coal direct liquefaction technology development for the rational utilization of coal will provide an effective way.Keywords: direct liquefaction HIT process IGOR process NEDOL process1引言随着煤炭资源的不断减少,合理利用现有煤炭资源问题变得更加突出,如何使煤炭资源得到最划得利用成为现在研究的主要问题。
洁净煤技术的开发利用就显得更加重要,而在洁净煤技术里煤炭的直接液化则是其中的重要组成部分煤直接液化,即煤高压加氢液化,可以生产人造石油和化学产品。
在石油短缺时,煤的液化产品将替代目前的天然石油。
煤化工是指以煤为原料,经化学加工使煤转化为气体、液体和固体燃料和固体产品或半产品,而后进一步加工成化工、能源产品的工业[1]。
煤直接液化技术---

煤与石油、汽油在化学组成上最明显的差别就是煤中氢含 量低、氧含量高、H/C原子比低、O/C原子比高。
2020/7/21
煤直接液化
6
1 煤直接液化技术沿革
(4)煤与液体油的差异
要将煤转化为液体产物,首先要将煤的大分子裂 解为较小的分子,而要提高H/C原子比,降低 O/C比,就必须增加H原子或减少C原子。
煤液化的实质就是在适当温度、氢压、溶剂和催 化剂条件下,提高H/C比,使固体煤转化为液体 的油。
2020/7/21
煤直接液化
7
1 煤直接液化技术沿革
1.2 国外煤炭直接液化技术沿革
➢ 1913年德国科学家F.Bergius发明了在高温高压下可将煤加 氢液化生产液体燃料,并获得专利,为煤炭直接液化技术的 开发奠定了基础。从此,各种煤加氢液化方法不断出现,实 验室开发的煤炭液化方法不下百种。
煤直接液化
4
1 煤直接液化技术沿革
(3) 煤炭液化的意义
煤炭的液化过程可以脱除煤中硫、氮等污染大 气的元素以及灰分等,获得的液体产品是优质洁 净的液体燃料和化学品。因此,煤炭液化将是中 国洁净煤技术和煤代油战略的重要、有效和可行 的途径之一。
2020/7/21
煤直接液化
5
1 煤直接液化技术沿革
(4)煤与液体油的差异
2020/7/21
煤直接液化
பைடு நூலகம்
3
1 煤直接液化技术沿革
(2)煤炭间接液化
煤炭间接液化是首先将煤气化制合成气(CO +H2),合成气经净化、调整H2/CO比,再经过催 化合成为液体燃料。
➢ 优点:煤种适应性较宽,操作条件相对温和, 煤 灰等三废问题主要在气化过程中解决;
煤炭液化技术
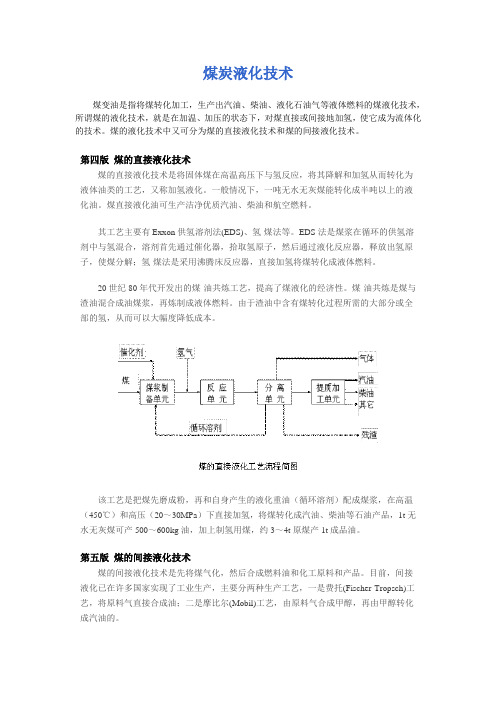
煤炭液化技术煤变油是指将煤转化加工,生产出汽油、柴油、液化石油气等液体燃料的煤液化技术,所谓煤的液化技术,就是在加温、加压的状态下,对煤直接或间接地加氢,使它成为流体化的技术。
煤的液化技术中又可分为煤的直接液化技术和煤的间接液化技术。
第四版煤的直接液化技术煤的直接液化技术是将固体煤在高温高压下与氢反应,将其降解和加氢从而转化为液体油类的工艺,又称加氢液化。
一般情况下,一吨无水无灰煤能转化成半吨以上的液化油。
煤直接液化油可生产洁净优质汽油、柴油和航空燃料。
其工艺主要有Exxon供氢溶剂法(EDS)、氢-煤法等。
EDS法是煤浆在循环的供氢溶剂中与氢混合,溶剂首先通过催化器,拾取氢原子,然后通过液化反应器,释放出氢原子,使煤分解;氢-煤法是采用沸腾床反应器,直接加氢将煤转化成液体燃料。
20世纪80年代开发出的煤-油共炼工艺,提高了煤液化的经济性。
煤-油共炼是煤与渣油混合成油煤浆,再炼制成液体燃料。
由于渣油中含有煤转化过程所需的大部分或全部的氢,从而可以大幅度降低成本。
该工艺是把煤先磨成粉,再和自身产生的液化重油(循环溶剂)配成煤浆,在高温(450℃)和高压(20~30MPa)下直接加氢,将煤转化成汽油、柴油等石油产品,1t无水无灰煤可产500~600kg油,加上制氢用煤,约3~4t原煤产1t成品油。
第五版煤的间接液化技术煤的间接液化技术是先将煤气化,然后合成燃料油和化工原料和产品。
目前,间接液化已在许多国家实现了工业生产,主要分两种生产工艺,一是费托(Fischer-Tropsch)工艺,将原料气直接合成油;二是摩比尔(Mobil)工艺,由原料气合成甲醇,再由甲醇转化成汽油的。
煤间接液化工艺先把煤全部气化成合成气(氢气和一氧化碳),然后再在催化剂存在下合成为汽油。
约5~7t煤产1t油。
间接液化工艺特点:1. 适用煤种比直接液化广泛;2. 可以在现有化肥厂已有气化炉的基础上实现合成汽油;3. 反应压力为3MPa,低于直接液化,反应温度为550℃,高于直接液化;4. 油收率低于直接液化,需5-7t煤出1t油,所以产品油成本比直接液化高出较多。
煤的直接液化

4、操作条件 温度和压力是影响煤直接液化反应进行的 两个因素,也是直接液化工艺两个最重要 的操作条件。 煤的液化反应是在一定温度下进行的,不 同工艺的所采用的温度大体相同,一般为 440~460º C。当温度超过450º C时,煤转化 率和油产率增加较少,而气产率增多,因 此会增加氢气的消耗量,不利于液化。
2、直接液化的溶剂 在煤液化过程中,溶剂起着溶解煤、溶 解气相氢向煤或催化剂表面扩散、供氢或 传递氢、防止煤热解的自由基碎片缩聚等 作用。 煤的直接液化必须有溶剂存在,这也是 与加氢热解的根本区别。 通常认为在煤的直接液化过程中,溶 剂能起到如下作用:
a)将煤与溶剂制成浆液的形式便于工艺过程 的输送。同时溶剂可以有效地分散煤粒、 催化剂和液化反应生成的热产物,有利于 改善多相催化液化反应体系的动力学过程。 b)依靠溶剂能力使煤颗粒发生溶胀和软化, 使其有机质中的键发生断裂。 c) 溶解部分氢气,作为反应体系中活性氢的 传递介质;或者通过供氢溶剂的脱氢反应 过程,可以提供煤液化需要的活性氢原子。
d)在有催化剂时,促使催化剂分散和萃取出 在催化剂表面上强吸附的毒物。 在煤液化工艺中,通常采用煤直接液化后 的重质油作为溶剂,且循环使用,因此又 称为循环溶剂。
3、催化剂 选用合适的催化剂对煤的直接液化至关重要, 一直是技术开发的热点之一,也是控制工艺成 本的重要因素。 催化剂的作用机理,有两种观点:(1)催化剂 的作用是吸附气体中的氢分子,并将其活化成 为易被煤的自由基团接受的活性氢;(2)催化 剂是使煤中的桥键断裂和芳环加氢的活性提高, 或是使溶剂加氢生成可向煤转移氢的供氢体等。
对压力而言,理论上压力越高对反应越有 利,但这样会增加系统的技术难度和危 险性,降低生产的经济性,因此,新的 生产工艺都在努力降低压力条件。 早期液化反应(如德国工艺)压力 高达 30~70MPa ,目前常用的反应压力 已经降到了 17~25MPa ,大大减少了设 备投资和操作费用。
煤直接液化技术---

2020/6/6
煤直接液化
7
1 煤直接液化技术沿革
1.2 国外煤炭直接液化技术沿革
➢ 1913年德国科学家F.Bergius发明了在高温高压下可将煤加 氢液化生产液体燃料,并获得专利,为煤炭直接液化技术的 开发奠定了基础。从此,各种煤加氢液化方法不断出现,实 验室开发的煤炭液化方法不下百种。
2020/6/6
煤直接液化
9
1 煤直接液化技术沿革
1.2 国外煤炭直接液化技术沿革
➢ 到20世纪50年代初期,前苏联利用德国煤直接液化技术和 设备于安加尔斯克石油化工厂建成投产了11套煤直接液化 和煤焦油加氢装置:
单台反应器直径为1m,高18m 操作压力分别为70.0MPa和32.5MPa两种 温度450-500 铁系催化剂
8
1 煤直接液化技术沿革
1.2 国外煤炭直接液化技术沿革
➢ 1936-1943年为支持侵略战争,德国又有11套煤直接液化 装置建成投产,到1944年,生产能力达到423吨/年,为当 时德国战争提供所需的车用和航空燃料。那时德国直接液化 的反应压力高达70.0MPa。
➢ 在二次世界大战前后进行煤直接液化技术开发的国家还有英、 日本、法国和意大利。
1983-1990术沿革
1.2 国外煤炭直接液化技术沿革
德国的IGOR工艺: 德国新工艺,主要特点是将液化残渣分离由过滤改为真空蒸馏,减少 了循环油中的灰分和沥青烯含量,同时部分循环油加氢,提高循环溶剂 的供氢能力,并增加催化剂的活性,从而可将操作压力由70.0MPa降 至30.0MPa。 液化油的收率由老工艺的50%提高到60%,后来的IGOR工艺又将煤 糊相加氢和粗油加氢精制串联,既简化了工艺,又可获得杂原子含量很 低的精制油,代表着煤直接液化技术的发展方向。
一种煤炭直接液化的方法

一种煤炭直接液化的方法
煤炭直接液化是将固态煤炭直接转化为液态燃料的过程。
目前广泛应用的煤炭直接液化方法是煤浆化技术。
煤浆化技术是将煤炭加工成煤浆,然后在高温高压条件下,通过催化剂的作用,将煤浆中的煤质转化为液体燃料。
具体的煤浆化过程包括以下步骤:
1. 煤炭粉碎:将煤炭破碎成所需的粉末粒度,通常需要将煤炭粉碎成颗粒大小在几毫米到几十微米之间。
2. 煤浆制备:将粉碎后的煤炭与水混合,添加一定的搅拌剂和分散剂,通过搅拌混合将煤和水充分分散,形成煤浆。
3. 煤浆加热:将煤浆加热到高温,通常需要在350-450的温度下进行加热。
4. 催化反应:在高温下,加入催化剂,对煤浆进行催化反应。
催化剂可以是铁、镍等金属催化剂,通过催化剂的作用,煤浆中的煤质分子会断裂和重组,形成液体燃料。
5. 分离和净化:经过催化反应后的混合物中含有液体燃料、溶剂、催化剂残留物等,需要进行分离和净化,得到纯净的液体燃料。
煤浆化技术具有将固态煤炭直接转化为液态燃料的优势,可以提高煤炭利用效率,减少对石油等化石能源的依赖,且液体燃料可以直接应用于炼油、燃烧等领域。
煤的直接液化
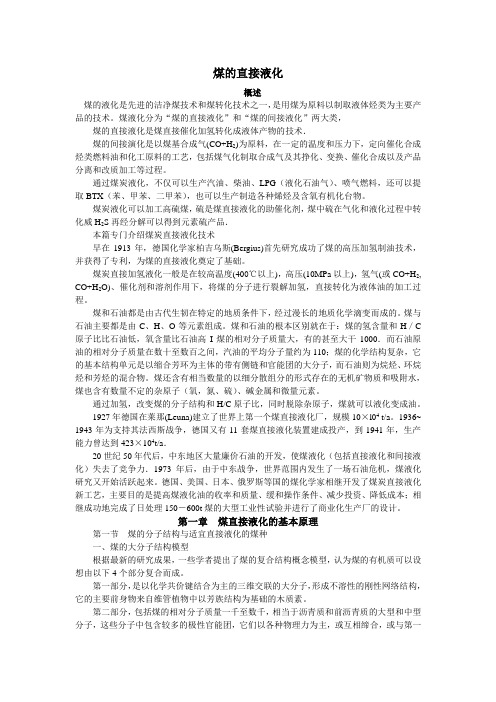
煤的直接液化概述煤的液化是先进的洁净煤技术和煤转化技术之一,是用煤为原料以制取液体烃类为主要产品的技术。
煤液化分为“煤的直接液化”和“煤的间接液化”两大类,煤的直接液化是煤直接催化加氢转化成液体产物的技术.煤的间接演化是以煤基合成气(CO+H2)为原料,在一定的温度和压力下,定向催化合成烃类燃料油和化工原料的工艺,包括煤气化制取合成气及其挣化、变换、催化合成以及产品分离和改质加工等过程。
通过煤炭液化,不仅可以生产汽油、柴油、LPG(液化石油气)、喷气燃料,还可以提取BTX(苯、甲苯、二甲苯),也可以生产制造各种烯烃及含氧有机化台物。
煤炭液化可以加工高硫煤,硫是煤直接液化的助催化剂,煤中硫在气化和液化过程中转化威H2S再经分解可以得到元素硫产品.本篇专门介绍煤炭直接液化技术早在1913年,德国化学家柏吉乌斯(Bergius)首先研究成功了煤的高压加氢制油技术,并获得了专利,为煤的直接液化奠定了基础。
煤炭直接加氢液化一般是在较高温度(400℃以上),高压(10MPa以上),氢气(或CO+H2, CO+H2O)、催化剂和溶剂作用下,将煤的分子进行裂解加氢,直接转化为液体油的加工过程。
煤和石油都是由古代生韧在特定的地质条件下,经过漫长的地质化学滴变而成的。
煤与石油主要都是由C、H、O等元素组成。
煤和石油的根本区别就在于:煤的氢含量和H/C 原子比比石油低,氧含量比石油高I煤的相对分子质量大,有的甚至大干1000.而石油原油的相对分子质量在数十至数百之间,汽油的平均分子量约为110;煤的化学结构复杂,它的基本结构单元是以缩合芳环为主体的带有侧链和官能团的大分子,而石油则为烷烃、环烷烃和芳烃的混合物。
煤还含有相当数量的以细分散组分的形式存在的无机矿物质和吸附水,煤也含有数量不定的杂原子(氧,氮、硫)、碱金属和微量元素。
通过加氢,改变煤的分子结构和H/C原子比,同时脱除杂原子,煤就可以液化变成油。
1927年德国在莱那(Leuna)建立了世界上第一个煤直接液化厂,规模10×l04 t/a。
煤直接液化工艺
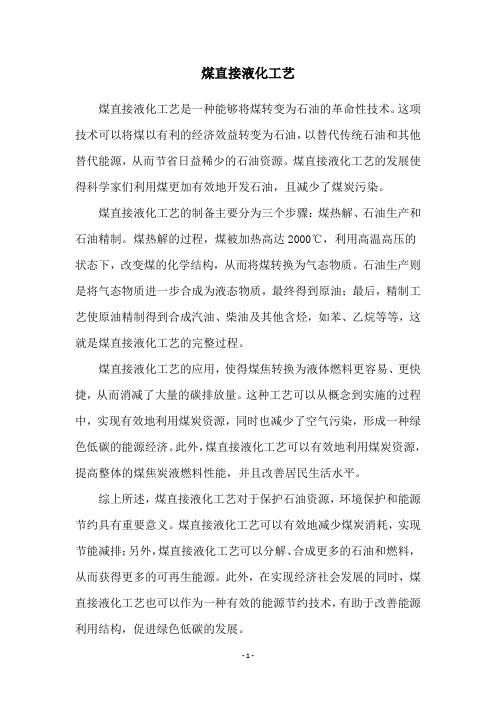
煤直接液化工艺
煤直接液化工艺是一种能够将煤转变为石油的革命性技术。
这项技术可以将煤以有利的经济效益转变为石油,以替代传统石油和其他替代能源,从而节省日益稀少的石油资源。
煤直接液化工艺的发展使得科学家们利用煤更加有效地开发石油,且减少了煤炭污染。
煤直接液化工艺的制备主要分为三个步骤:煤热解、石油生产和石油精制。
煤热解的过程,煤被加热高达2000℃,利用高温高压的状态下,改变煤的化学结构,从而将煤转换为气态物质。
石油生产则是将气态物质进一步合成为液态物质,最终得到原油;最后,精制工艺使原油精制得到合成汽油、柴油及其他含烃,如苯、乙烷等等,这就是煤直接液化工艺的完整过程。
煤直接液化工艺的应用,使得煤焦转换为液体燃料更容易、更快捷,从而消减了大量的碳排放量。
这种工艺可以从概念到实施的过程中,实现有效地利用煤炭资源,同时也减少了空气污染,形成一种绿色低碳的能源经济。
此外,煤直接液化工艺可以有效地利用煤炭资源,提高整体的煤焦炭液燃料性能,并且改善居民生活水平。
综上所述,煤直接液化工艺对于保护石油资源,环境保护和能源节约具有重要意义。
煤直接液化工艺可以有效地减少煤炭消耗,实现节能减排;另外,煤直接液化工艺可以分解、合成更多的石油和燃料,从而获得更多的可再生能源。
此外,在实现经济社会发展的同时,煤直接液化工艺也可以作为一种有效的能源节约技术,有助于改善能源利用结构,促进绿色低碳的发展。
随着人们日益重视环境保护,开发煤直接液化工艺也变得越来越重要。
为了促进能源节约,应提升煤直接液化工艺的社会应用水平,并倡导利用煤直接液化工艺维护环境的理念,以促进各方努力实施煤直接液化工艺,节省能源,保护环境。
煤炭直接液化技术总结
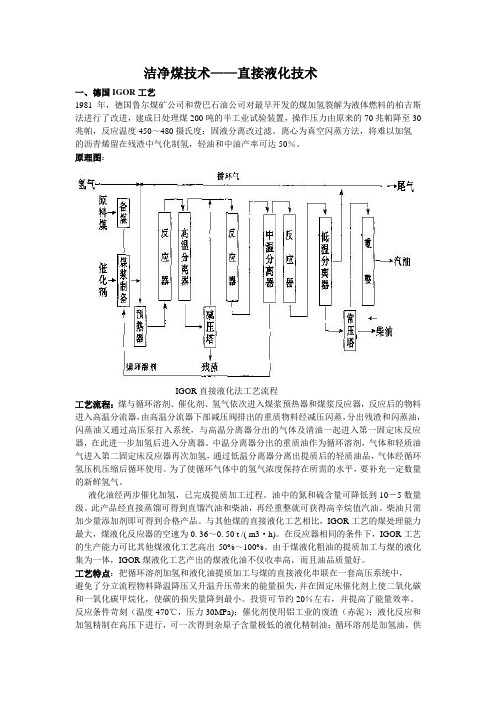
洁净煤技术——直接液化技术一、德国IGOR工艺1981年,德国鲁尔煤矿公司和费巴石油公司对最早开发的煤加氢裂解为液体燃料的柏吉斯法进行了改进,建成日处理煤200吨的半工业试验装置,操作压力由原来的70兆帕降至30兆帕,反应温度450~480摄氏度;固液分离改过滤、离心为真空闪蒸方法,将难以加氢的沥青烯留在残渣中气化制氢,轻油和中油产率可达50%。
原理图:IGOR直接液化法工艺流程工艺流程:煤与循环溶剂、催化剂、氢气依次进入煤浆预热器和煤浆反应器,反应后的物料进入高温分流器,由高温分流器下部减压阀排出的重质物料经减压闪蒸,分出残渣和闪蒸油,闪蒸油又通过高压泵打入系统,与高温分离器分出的气体及清油一起进入第一固定床反应器,在此进一步加氢后进入分离器。
中温分离器分出的重质油作为循环溶剂,气体和轻质油气进入第二固定床反应器再次加氢,通过低温分离器分离出提质后的轻质油品,气体经循环氢压机压缩后循环使用。
为了使循环气体中的氢气浓度保持在所需的水平,要补充一定数量的新鲜氢气。
液化油经两步催化加氢,已完成提质加工过程。
油中的氮和硫含量可降低到10-5数量级。
此产品经直接蒸馏可得到直馏汽油和柴油,再经重整就可获得高辛烷值汽油。
柴油只需加少量添加剂即可得到合格产品。
与其他煤的直接液化工艺相比,IGOR工艺的煤处理能力最大,煤液化反应器的空速为0. 36~0. 50 t /( m3·h)。
在反应器相同的条件下,IGOR工艺的生产能力可比其他煤液化工艺高出50%~100%。
由于煤液化粗油的提质加工与煤的液化集为一体,IGOR煤液化工艺产出的煤液化油不仅收率高,而且油品质量好。
工艺特点:把循环溶剂加氢和液化油提质加工与煤的直接液化串联在一套高压系统中,避免了分立流程物料降温降压又升温升压带来的能量损失,并在固定床催化剂上使二氧化碳和一氧化碳甲烷化,使碳的损失量降到最小。
投资可节约20%左右,并提高了能量效率。
反应条件苛刻(温度470℃,压力30MPa);催化剂使用铝工业的废渣(赤泥);液化反应和加氢精制在高压下进行,可一次得到杂原子含量极低的液化精制油;循环溶剂是加氢油,供氢性能好,液化转化率高。
煤制油

煤制油煤制油包括直接液化和间接液化两种工艺技术路线。
1.煤炭直接液化技术煤在高压和一定温度下直接与氢气反应生成液体燃料油的工艺技术称为直接液化。
煤炭直接液化主要产品为汽油、柴油、航空煤油、石脑油、LPG(液化石油气),另外还可以提取BTX(苯、甲苯、二甲苯),副产品有硫磺、氨或尿素等。
直接液化工艺的产品中,柴油的比例在60~70%,汽油和LPG占40~30%左右。
直接液化的工艺主要有Exxon供氢溶剂法(EDS)。
氢-煤法等。
EDS法是煤浆在循环的供氢溶剂中与氢混合,溶剂首先通过催化器,拾取氢原子,然后通过液化反应器,释放出氢原子,使煤分解。
氢-煤法是采用沸腾床反应器,直接加氢将煤转化成液体燃料。
直接液化过程流程现代煤炭直接液化技术提高了产品质量,特别是通过液化后的提质加工工艺,使液化油通过加氢精制、重整、加氢裂化,可得到合格的汽油、柴油或航空煤油。
尤其是柴油的凝点很低,可以在高寒地区使用,所得航空煤油的比重较大,同样容积的油箱可使飞机的续航距离增加。
2. 煤炭间接液化技术间接液化是把煤炭先气化再合成,煤在高温下与氧气和水蒸气反应生成合成反应气(CO+H2),合成反应气再经F-T合成催化反应合成液体燃料及其化学品。
煤炭间接液化主要产品为汽油、柴油、航空煤油、石脑油、LPG、以及乙烯、丙稀等重要化工原料,副产品有α烯烃、硬蜡、氨、醇、酮、焦油、硫磺、煤气等。
间接液化的产品品种是可以变通的,即可以生产油品,又可以根据市场需要加以调节,生产高附加值、价格高、市场紧缺的化工产品。
对中国的石油产品市场而言,以优质石脑油和高质量柴油、烯烃、LPG 和石蜡等产品为好。
另外烯烃的价值较高,LPG也是市场紧俏物资。
此外我国石蜡生产和销售市场上,高熔点微晶蜡缺口较大,高品位润滑油也是国内比较紧缺的。
因此,汽油、柴油与高附加值的润滑油、微晶蜡等市场紧缺的产品并举,可以作为合成油产品的主攻方向。
间接液化在可控制的条件下进行合成,获得的柴油的十六烷值达70,且低硫、无芳烃,既可直接供给环保要求高的地区使用,也可作为优质油与其它油品调配。
煤直接液化工艺
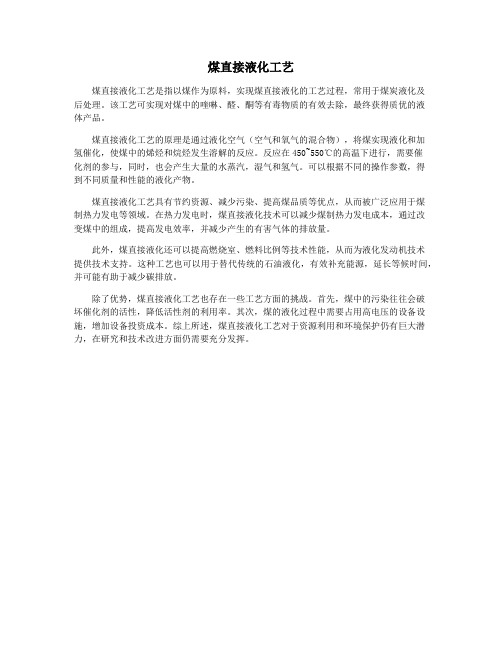
煤直接液化工艺
煤直接液化工艺是指以煤作为原料,实现煤直接液化的工艺过程,常用于煤炭液化及
后处理。
该工艺可实现对煤中的喹啉、醛、酮等有毒物质的有效去除,最终获得质优的液
体产品。
煤直接液化工艺的原理是通过液化空气(空气和氧气的混合物),将煤实现液化和加
氢催化,使煤中的烯烃和烷烃发生溶解的反应。
反应在450~550℃的高温下进行,需要催
化剂的参与,同时,也会产生大量的水蒸汽,湿气和氢气。
可以根据不同的操作参数,得
到不同质量和性能的液化产物。
煤直接液化工艺具有节约资源、减少污染、提高煤品质等优点,从而被广泛应用于煤
制热力发电等领域。
在热力发电时,煤直接液化技术可以减少煤制热力发电成本,通过改
变煤中的组成,提高发电效率,并减少产生的有害气体的排放量。
此外,煤直接液化还可以提高燃烧室、燃料比例等技术性能,从而为液化发动机技术
提供技术支持。
这种工艺也可以用于替代传统的石油液化,有效补充能源,延长等候时间,并可能有助于减少碳排放。
除了优势,煤直接液化工艺也存在一些工艺方面的挑战。
首先,煤中的污染往往会破
坏催化剂的活性,降低活性剂的利用率。
其次,煤的液化过程中需要占用高电压的设备设施,增加设备投资成本。
综上所述,煤直接液化工艺对于资源利用和环境保护仍有巨大潜力,在研究和技术改进方面仍需要充分发挥。
煤炭直接液化

神华煤炭液化项目采用美国碳氢技术公司(HTI)的生产工艺, 是目前世界上首条煤直接液化制油的工业化生产线,分为 煤液化、液化油提质和制氢三大部分。 优点:(1)煤浆制备全部采用供氢性循环溶剂,使得液化反 应条件温和,系统操作稳定性提高; (2)采用两个强制循环悬浮床反应器。这样使得反应器温 度分布均匀,产品性质稳定; (3)采用减压蒸馏的方法进行液化油和固体物的分离。残 渣中含油量少,产品产率提高; (4)循环溶剂和产品采用强制循环悬浮床加氢反应器。 • 该工艺PDU装置的蒸馏油收率达到56%~58%,转化率 90%~92%,气产率约12%~14%,水产率11%~13%, 氢耗量5%~7%。 缺点 • 减压阀芯使用寿命短 • 不适用于褐煤
2.2.2.3美国HTI工艺
• 该工艺使用人工合成的高分散催化剂,加 人量为0.5%,不进行催化剂回收。反应 压力为17MPa,反应温度为4500C。 • 其主要特点是对液化残渣进行油回收,故 液化油收率较高。现已完成0.025t/d和 3t/d规模的试验研究。
2.2.2.4神华煤直接液化工艺
2.2.2.2 日本NEDOL工艺
• 该工艺以黄铁矿为催化剂,催化剂加人量 为4% ,也不进行催化剂回收。反应压力为 19 MPa,反应温度为460℃。 • 其主要特点是循环溶剂全部在一个单独的 固定床反应器中,用高活性催化剂预先加 氢,使之变为供氢溶剂。液化粗油经过冷 却后再去进行提质加工。液化残渣连同其 中所含的重质油即可进一步进行油回收, 也可直接用作气化制氢的原料。现已完成 0.01t/d、0.1t/d、lt/d以及150t/d 规模的试验研究。
2.2煤炭的直接液化工艺
2.2.1.工艺条件对液化反应的影响
• 反应压力:提高压力,增加氢分压,从而增加了溶剂中的氢浓度,
煤的液化技术与工艺
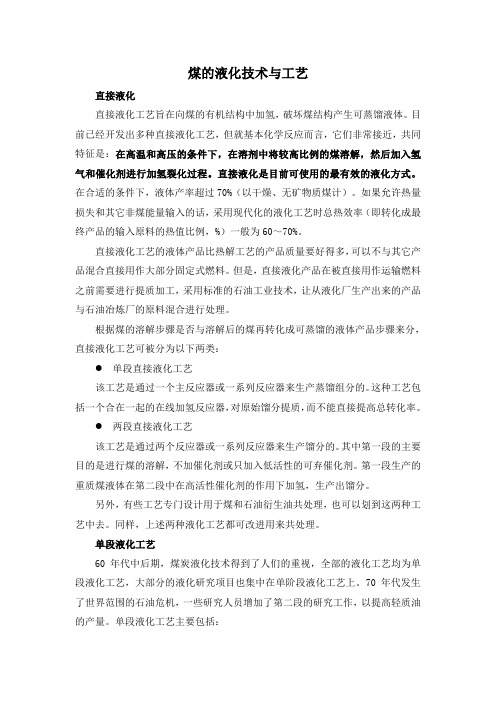
煤的液化技术与工艺直接液化直接液化工艺旨在向煤的有机结构中加氢,破坏煤结构产生可蒸馏液体。
目前已经开发出多种直接液化工艺,但就基本化学反应而言,它们非常接近,共同特征是:在高温和高压的条件下,在溶剂中将较高比例的煤溶解,然后加入氢气和催化剂进行加氢裂化过程。
直接液化是目前可使用的最有效的液化方式。
在合适的条件下,液体产率超过70%(以干燥、无矿物质煤计)。
如果允许热量损失和其它非煤能量输入的话,采用现代化的液化工艺时总热效率(即转化成最终产品的输入原料的热值比例,%)一般为60~70%。
直接液化工艺的液体产品比热解工艺的产品质量要好得多,可以不与其它产品混合直接用作大部分固定式燃料。
但是,直接液化产品在被直接用作运输燃料之前需要进行提质加工,采用标准的石油工业技术,让从液化厂生产出来的产品与石油冶炼厂的原料混合进行处理。
根据煤的溶解步骤是否与溶解后的煤再转化成可蒸馏的液体产品步骤来分,直接液化工艺可被分为以下两类:●单段直接液化工艺该工艺是通过一个主反应器或一系列反应器来生产蒸馏组分的。
这种工艺包括一个合在一起的在线加氢反应器,对原始馏分提质,而不能直接提高总转化率。
●两段直接液化工艺该工艺是通过两个反应器或一系列反应器来生产馏分的。
其中第一段的主要目的是进行煤的溶解,不加催化剂或只加入低活性的可弃催化剂。
第一段生产的重质煤液体在第二段中在高活性催化剂的作用下加氢,生产出馏分。
另外,有些工艺专门设计用于煤和石油衍生油共处理,也可以划到这两种工艺中去。
同样,上述两种液化工艺都可改进用来共处理。
单段液化工艺60年代中后期,煤炭液化技术得到了人们的重视,全部的液化工艺均为单段液化工艺,大部分的液化研究项目也集中在单阶段液化工艺上。
70年代发生了世界范围的石油危机,一些研究人员增加了第二段的研究工作,以提高轻质油的产量。
单段液化工艺主要包括:·Kohleoel液化工艺(德国鲁尔煤炭公司)·NEDOL液化工艺(日本新能源产业技术开发机构)·H-煤液化工艺(美国HRI公司)·Exxon供氢溶剂液化工艺(即EDS工艺,美国Exxon公司)·SRC-I和II液化工艺(美国海湾石油公司)·Imhausen高压液化工艺(德国)·Conoco氯化锌液化工艺(美国Conoco公司)上述大部分液化工艺已经被淘汰,但Kohleoel和NEDOL液化工艺目前仍被广泛采用,开发商准备对这两种液化工艺进行商业性生产。
- 1、下载文档前请自行甄别文档内容的完整性,平台不提供额外的编辑、内容补充、找答案等附加服务。
- 2、"仅部分预览"的文档,不可在线预览部分如存在完整性等问题,可反馈申请退款(可完整预览的文档不适用该条件!)。
- 3、如文档侵犯您的权益,请联系客服反馈,我们会尽快为您处理(人工客服工作时间:9:00-18:30)。
煤炭直接液化技术总结
洁净煤技术——直接液化技术
—、德国IGOR工艺
1981 年,德国鲁尔煤矿公司和费巴石油公司对最早开发的煤加氢裂解为液体燃料的柏吉斯法进行了改进,建成日处理煤200 吨的半工业试验装置,操作压力由原来的70 兆帕降至30兆帕,反应温度450〜480摄氏度;固液分离改过滤、离心为真空闪蒸方法,将难以加氢的沥青烯留在残渣中气化制氢,轻油和中油产率可达50%。
原理图:
IGOR 直接液化法工艺流程
工艺流程:煤与循环溶剂、催化剂、氢气依次进入煤浆预热器和煤浆反应器,反应后的物料进入高温分流器,由高温分流器下部减压阀排出的重质物料经减压闪蒸,分出残渣和闪蒸油,闪蒸油又通过高压泵打入系统,与高温分离器分出的气体及清油一起进入第一固定床反应器,在此进一步加氢后进入分离器。
中温分离器分出的重质油作为循环溶剂,气体和轻质油气进入第二固定床反应器再次加氢,通过低温分离器分离出提质后的轻质油品,气体经循环氢压机压缩后循环使用。
为了使循环气体中的氢气浓度保持在所需的水平,要补充一定数量的新鲜氢气。
液化油经两步催化加氢,已完成提质加工过程。
油中的氮和硫含量可降低到10-5 数量级。
此产品经直接蒸馏可得到直馏汽油和柴油,再经重整就可获得高辛烷值汽油。
柴油只需加少量添加剂即可得到合格产品。
与其他煤的直接液化工艺相比,IGOR工艺的煤处理能力最大,煤液化反应器的空速为0. 36〜0. 50 t /( m3 • h)。
在反应器相同的条件下,IGOR 工艺的生产能力可比其他煤液化工艺高出50%〜100%由于煤液化粗油的提质加工与
煤的液化集为一体,IGOR煤液化工艺产出的煤液化油不仅收率高,而且油品质量好。
工艺特点:把循环溶剂加氢和液化油提质加工与煤的直接液化串联在一套高压系统中,避免了分立流程物料降温降压又升温升压带来的能量损失,并在固定床催化剂上使二氧化碳和一氧化碳甲烷化,使碳的损失量降到最小。
投资可节约20%左右,并提高了能量效率。
反应条件苛刻(温度470C,压力30MPa);催化剂使用铝工业的废渣(赤泥);液化反应和加氢精制在高压下进行,可一次得到杂原子含量极低的液化精制油;循环溶剂是加氢油,供
氢性能好,液化转化率高。
优点:(1)煤液化粗油的提质加工与煤的液化集为一体,IGOR煤液化工艺产出的煤
液化油不仅收率高,而且油品质量好。
(2)供氢性能好,液化转化率高
(3) 结构简单,投资少,克服了反应尺寸、能力、压力等诸多方面的局限
(4) 传热效果好,反应温度易控制.
二、美国HTI 工艺
7 0年代中期以来,美国碳氢技术公司(HTI)的前身HRI公司就开始从事煤加氢液化技术的研究和开发工作。
他们首先利用已得到普遍工业化生产的沸腾床重油加氢裂化工艺研发了H — Coal煤液化工艺,并以此为基础,将之改进成两段催化液化工艺(TSCL)。
后来,利用近十几年开发的悬浮床反应器和拥有自主知识产权的铁基催化剂(GelcatTM)对该工艺进行了改进,形成了HTI煤液化新工艺。
在其系列煤液化工艺放大实验中,HTI积累了大量的经验,并取得了良好的实验结果。
该工艺是在两段催化液化法和H- COAL X艺基础上发展起来的,采用近十年来开发的悬浮床反应器和HTI 拥有专利的铁基催化剂。
原理图:
工艺流程:该工艺是两段催化法,采用近十年开发的悬浮床反应器和HIT 拥有专利的铁基催化剂(GELCATTM)煤液化的第一段和第二段都是装有高活性加氢和加氢裂解催化剂(Ni、Mo或Co Me)的沸腾床反应器,两个反应器既分开又紧密相连,可以使加氢裂解和催化加氢反应在各自的最佳条件下进行。
液化产物先用氢淬冷,重质油回收作溶剂,排出的产物主要组成是未反应煤和灰渣。
工艺特点:HTI 工艺的主要特点是:反应条件比较缓和,反应温度440〜
450C,压力17MPa采用悬浮床反应器,到达全返混反应模式;催化剂是采用HTI 专利技术制备的铁系胶状高活性催化剂,用量少;在高温分离器后面串联有在线加氢固定床反应器,对液化油进行加
氢精制;固液分离采用临界溶剂萃取的方法,从液化残渣中最大限度回收重质油,从而大幅度提高了液化油回收率。
同氢-煤工艺相比较,C4以上在402C馏分油增加53%液化1吨无水无灰煤生成的馏分油从 3.3桶提高到点5.0桶;C1~C3气体烃产率从11.3降到8.6%,氢利用率从8.4%提高到10.7%;油品质量提高,氮、硫杂原子减少50%,从而使煤液化经济性明显改善,液化油成本降低了17%。
优点:(1) HTI工艺油收率高,可达到60m以上;
( 2) HTI 工艺反应器有特点,易于大型化;
(3)HTI 的胶体催化剂活性较好。
(4)HIT 工艺已经进行了大量试验,技术先进,工艺较成熟。
三、日本NEDOI X艺
为保护大气环境,加大开发和利用洁净能源的步伐,日本在8 0年代制定了阳光计划,并专门成立了新能源产业技术综合开发机构(NEDO)
,负责该计划的实施。
在NEDO组织下,日本开发出NEDOL煤液化工艺,并在PDU试验成功的基础上,设计建设了15 0t/d的大型中试装置。
到19 9 8年,该中试装置已完成运转两个印尼煤和一个日本煤的试验,取得了工程放大设计数据。
该工艺的特点是:反应压力较低,为17 — 19MPa,反应温度为4 5 5 —4 6 5 C ;催化剂使用合成硫。
工艺特点:反应压力较低,只有17兆帕〜19兆帕,反应温度为430摄氏度〜465摄氏度; 催化剂采用合成硫化铁或天然硫铁矿;固液分离采用减压蒸馏的方法;配煤浆用的循环溶剂单独加氢,以提高溶剂的供氢能力;液化油含有较多的杂原子,还须加氢提质才能获得合格产品。
原理图:
NEDOL 工艺流程
工艺流程:由煤前处理单元、液化反应单元、液化油蒸馏单元及溶剂加氢单元 4 个主要单元组成。
优点:( 1)商业化放大风险较小
(2)液化反应塔的安定运行:NEDO工艺的反应塔使用悬浊鼓泡床反应塔,内部无构造,结构简单,运行稳定。
(3)液化油蒸馏系统运行相对可靠,NEDO工艺,以150t/d中试装置及1t/d工艺支持单元的运行实绩为基础,在大型化装置的液化生成物蒸馏工艺中,采用纯液体生成物和含残渣生成物并联蒸馏工艺,前者采用常压蒸馏塔进行分离,后者采用减压蒸馏塔进行分
离。
(4)溶剂加氢系统相对简单,NEDO工艺使用循环溶剂,只将必要的溶剂加氢,产品液化粗油在提质设备进行氢化。
(5)油收率相对较高,液化油收率,很大程度上取决于煤炭的性状,必须根据每种煤炭的性状设定最适合的反应条件。
(6)反应条件相对温和,NEDO工艺的标准反应条件是温度450C、压力17Mpa反应条件(反应温度、反应压力、滞留时间等)根据煤炭种类设定最适合的条件。
四、工艺对比
HIT 工艺已经进行了大量试验,技术先进,工艺较成熟,与德国IGOR工艺和日本NEDOT艺相比,有如下突出优点:
[1] 反应器类型。
采用全返混反应模式的悬浮床反应器,克服了反应器内煤固体颗粒
的沉降问题,反应器的直径比大,因而,单系列生产装置的规模比其他两个工艺增加了近一倍。
同时全返混性也使反应器内的反应温度更易控制。
[2] 催化剂。
HIT 采用的铁系催化剂由于催化活性高,Fe 的加入量少,这不仅减少了煤浆管道及阀门的磨
损,而且还减少了残渣的生成量。
同时,催化剂制备简单,成本低。
[3] 固液分离法。
煤经液化反应后,还有少量的惰性组分不能转化,为了得到纯净的液化油,必须把他们分离出去。
IGOL和NEDOI X艺采用的固液分离法是减压蒸馏,得到的固体残渣中含有50%以上的重油及沥青质。
而HIT 采用临界萃取的方法,能把残渣中的大部分重油及沥青质分离出来,重新用于配煤浆,再次进入液化反应器。
这些重质组分的进一步转化使HIT 液化油的产率比其他两种工艺高5%-10%.
[4] 液化反应条件。
HIT 的煤液化反应条件比较缓和,反应压力和温度均较低。
低的压力条件可降低高压设备及高压管道的造价,而低温也同样能降低造价,且有助于长设备的使用寿命。