三菱立式加工中心加工不良案例分析
机加工常见品质异常分析案例
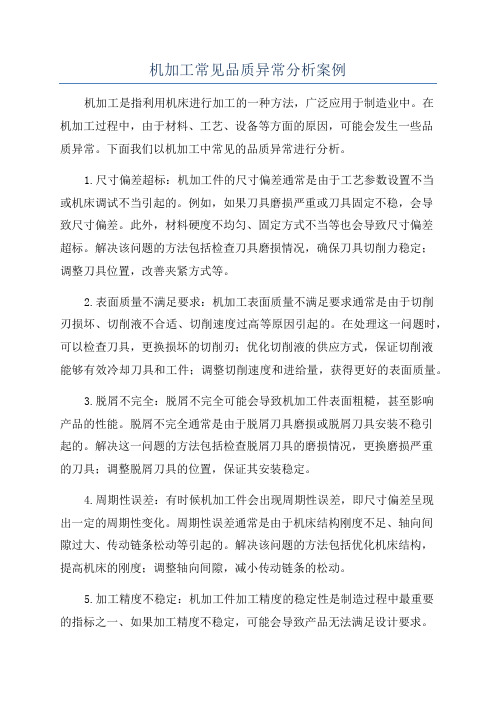
机加工常见品质异常分析案例机加工是指利用机床进行加工的一种方法,广泛应用于制造业中。
在机加工过程中,由于材料、工艺、设备等方面的原因,可能会发生一些品质异常。
下面我们以机加工中常见的品质异常进行分析。
1.尺寸偏差超标:机加工件的尺寸偏差通常是由于工艺参数设置不当或机床调试不当引起的。
例如,如果刀具磨损严重或刀具固定不稳,会导致尺寸偏差。
此外,材料硬度不均匀、固定方式不当等也会导致尺寸偏差超标。
解决该问题的方法包括检查刀具磨损情况,确保刀具切削力稳定;调整刀具位置,改善夹紧方式等。
2.表面质量不满足要求:机加工表面质量不满足要求通常是由于切削刃损坏、切削液不合适、切削速度过高等原因引起的。
在处理这一问题时,可以检查刀具,更换损坏的切削刃;优化切削液的供应方式,保证切削液能够有效冷却刀具和工件;调整切削速度和进给量,获得更好的表面质量。
3.脱屑不完全:脱屑不完全可能会导致机加工件表面粗糙,甚至影响产品的性能。
脱屑不完全通常是由于脱屑刀具磨损或脱屑刀具安装不稳引起的。
解决这一问题的方法包括检查脱屑刀具的磨损情况,更换磨损严重的刀具;调整脱屑刀具的位置,保证其安装稳定。
4.周期性误差:有时候机加工件会出现周期性误差,即尺寸偏差呈现出一定的周期性变化。
周期性误差通常是由于机床结构刚度不足、轴向间隙过大、传动链条松动等引起的。
解决该问题的方法包括优化机床结构,提高机床的刚度;调整轴向间隙,减小传动链条的松动。
5.加工精度不稳定:机加工件加工精度的稳定性是制造过程中最重要的指标之一、如果加工精度不稳定,可能会导致产品无法满足设计要求。
加工精度不稳定通常是由于机床的磨损、刚度退化、传感器故障等原因引起的。
解决该问题的方法包括定期检查机床,维护机床的精度;更换磨损严重的零部件;修复或更换故障传感器。
综上所述,机加工过程中常见的品质异常包括尺寸偏差超标、表面质量不满足要求、脱屑不完全、周期性误差和加工精度不稳定等。
浅谈三菱E60加工中心主轴定向准停抖动故障的分析与排除
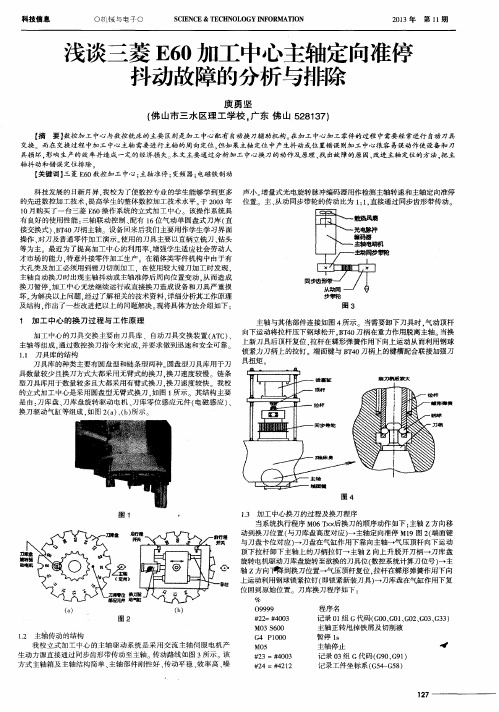
图2
1 . 2 主轴传动 的结构
我校立式加工 中心 的主轴驱动系统是采 用交流主轴伺服 电机产 生动力源直接通过同步齿形带传动至主轴 传动路线如 图 3所示。该 方式主轴箱及主轴结构简单 、 主轴部件刚性好 、 传动平稳 、 效 率高 、 噪
G4 PI O o o M0 5 # 2 3=# 40 0 3
主轴与其他部件连接如图 4 所示 。当需要卸下刀具时 , 气 动顶杆 向下运动将拉杆压下钢球松开 , B T 4 0 刀柄 在重力作用脱离主轴 。 当换 加工 中心 的刀具 交换主要由刀具库 、 自动刀具交换装 ̄ ( AT C) 、 上新刀具后顶杆复位 . 拉杆在蝶形弹簧作用下 向上运动从而利用钢球 主轴等组成 . 通过数控换刀指令来完成 . 并要求做 到迅速 和安全可靠 。 锁紧力刀柄上的拉钉。端面键与 B T 4 0 刀柄上的键槽配合联 接加强刀 1 . 1 刀 具 库 的 结 构 刀具库的种类主要有圆盘型和链 条型两种 圆盘型刀具库用于刀 具 扭 矩 。 具数量较少且换刀方式大都采用无 臂式的换 刀。 换刀速度较慢 。链 条 型刀具库用于数量较多且大都采用有 臂式换刀 . 换刀速度较快 我 校 的立式加工 中心是采用圆盘型无臂 式换刀 . 如图 1 所示 其结构 主要 是 由: 刀库盘 、 刀库盘旋转驱动 电机 、 刀库零位感应元 件( 电磁感应 ) 、 换刀驱动气缸等组成 . 如图 2 ( a ) 、 ( b ) 所示。
科技信息
0机械 与电子0
S C I E N C E&T E C H N O L O G Y I N F O R MA T I O N
2 0 1 3 年
第1 1 期
浅谈三菱 E 6 0 加工中心主轴定 向准停 抖动故障的分析与排除
立式加工中心误差分析研究

立式加工中心误差分析研究立式加工中心是一种常见的数控机床,广泛应用于零件加工领域。
在加工过程中,误差的存在会影响加工精度和零件质量。
对立式加工中心误差的分析研究至关重要。
本文将针对立式加工中心的误差进行深入分析研究,探讨其产生原因和解决方法,以提高加工精度和零件质量。
一、立式加工中心误差的分类和影响立式加工中心误差主要包括几个方面:机床本体误差、传动系统误差、加工过程误差等。
机床本体误差是由工作台、立柱、横梁等机床主要部件的制造误差、装配误差、磨损和变形等因素导致的;传动系统误差是由滚珠丝杠、伺服电机、联轴器等传动元件的制造和运动过程中的误差引起的;加工过程误差是由刀具磨损、刀轴偏差、刀具安装误差等因素产生的。
这些误差会直接影响加工精度和零件质量,表现为尺寸偏差、表面粗糙度、圆度偏差、同轴度偏差等。
如果不及时发现和解决这些误差,将会导致加工零件不合格,甚至影响整个生产线的正常运转。
二、立式加工中心误差分析的方法立式加工中心误差的分析方法主要包括几个方面:定位误差分析、加工精度误差分析、机床静态刚度分析、动态特性分析等。
定位误差分析是通过测量工件加工后的尺寸与设计尺寸之间的差异来确定机床和工件加工定位误差的大小和方向;加工精度误差分析是通过表面质量检测、圆度检测、同轴度检测等手段来确定加工精度误差的具体表现和产生原因;机床静态刚度分析是通过振动测试、变形测试等手段来确定机床静态刚度的大小和分布;动态特性分析是通过加工过程中的运动参数监测来确定机床动态特性的稳定性和准确性。
这些分析方法可以全面、深入地了解立式加工中心的误差状况,为后续误差的改善和消除提供重要的参考依据。
三、立式加工中心误差的影响因素立式加工中心误差的产生主要受到以下因素的影响:机床结构、传动系统、控制系统、刀具系统、工件材料等。
机床结构的刚度、稳定性和精度是决定机床误差的重要因素;传动系统的精度、稳定性和可靠性直接影响加工精度;控制系统的响应速度、稳定性和精度决定了机床的运动精度;刀具系统的安装精度、磨损程度和切削参数直接影响了加工精度;工件材料的硬度、强度和表面温度对加工精度也会产生影响。
加工中心故障的分析与排除
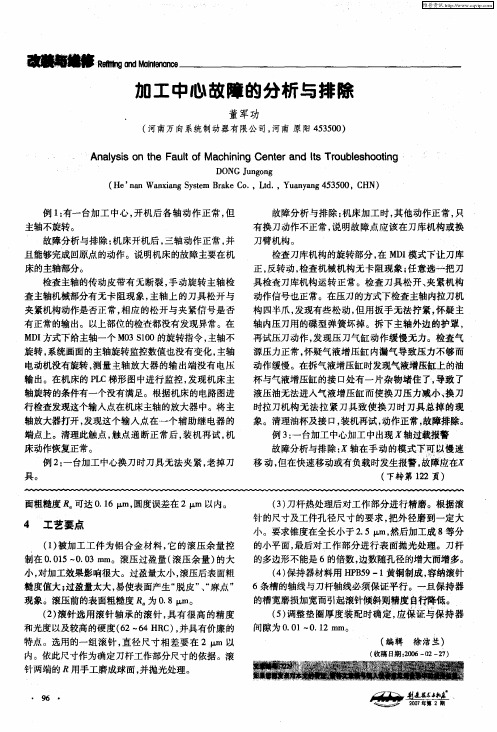
( 编辑
徐 洁兰)
( 收稿 日期 ̄0 6 2—2 = 0 0 2 7)
: . ;:
u,耳 ■
‘
维普资讯
】瓣 援术 A uu hg . I u aan n y l ncn 0 0 fi 1 M lg 0
从材料的化学成分和机械性能上可以分析出其深 引伸性能较佳 , 但此件的工艺性不好 , 顶部后下部的翻 边形成 了闭角( 此种结构 的零件必须用复合型模具生 产 )后下部翻边长度为 3. m, , 09m 而此处 的上部是强 “ 鼓膜状” 区域 , 区域最易振动。故在此类零件设计 此 时, 要么整个结构都引伸 , 当然 , 都引伸工艺性难度太
夹紧机构动作是否正常 , 相应的松开与夹紧信号是否 有正常的输出。以上部位 的检查都没有发现异常。在 M I D 方式下给主轴一个 M 3 10的旋转指令 , 0 0 S 主轴不
旋转 , 系统画面的主轴旋转监控数值也没有变化 , 主轴 电动机没有旋转 , 测量主轴放大器 的输 出端没有 电压 输出。在机床的 P C梯形图中进行监控 , L 发现机床 主 轴旋转的条件有一个没有满足。根据机床的电路图进 行检查发现这个输入点在机床主轴的放大器 中。将 主
动作缓慢 。在拆气液增压缸时发现气液增压缸上的油 杯与气液增压缸的接 口处有一 片杂物堵住了, 导致 了 液压油无法进入气液增压缸而使换刀压力减小 换刀
时拉刀机构无法拉 紧刀具致 使换刀时刀具总掉 的现
轴放大器打开 , 发现这个输 入点在一个辅助继电器 的
端点上。清理此触点 , 触点通断正 常后 , 装机再试 , 机
床动作恢复正常。 例 2 一 台加工中心换刀时刀具无法夹紧 , : 老掉刀
具。
象。清理油杯及接 口, 装机再试 , 动作正常 , 故障排除。 例 3一 台加工中心加工中出现 轴过载报警 : 故障分析与排 除: X轴在手动的模式下可 以慢速 移动, 但在快速移动或有负载时发生报警 , 故障应在
加工中心故障案例分析共49页文档
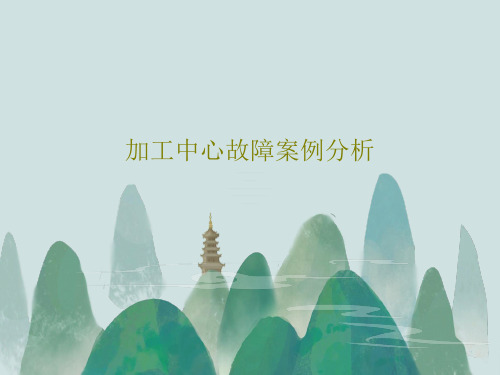
谢谢
11、越是没有本领的就越加自命不凡。——邓拓 12、越是无能的人,越喜欢挑剔别人的错儿。——爱尔兰 13、知人者智,自知者明。胜人者有力,自胜者强。——老子 14、意志坚强的人能把世界放在手中像泥块一样任意揉捏。——歌德 15、最具挑战性的挑战莫过于提升自我。——迈克尔·F·斯特利
加工中心故障案例分析
51、没有哪个社会可以制订一部永远 适用的 宪法, 甚至一 条永远 适用的 法律。 ——杰 斐逊 52、法律源于人的自卫本能。——英 格索尔
53、人们通常会发现,法律就是这样 一种的 网,触 犯法律只有中 等的才 会坠入 网中。 ——申 斯通 54、法律就是法律它是一座雄伟的大 夏,庇 护着我 们大家 ;它的 每一块 砖石都 垒在另 一块砖 石上。 ——高 尔斯华 绥 55、今天的法律未必明天仍是法律。 ——罗·伯顿
立式数控加工中心的加工缺陷和质量问题解决方法
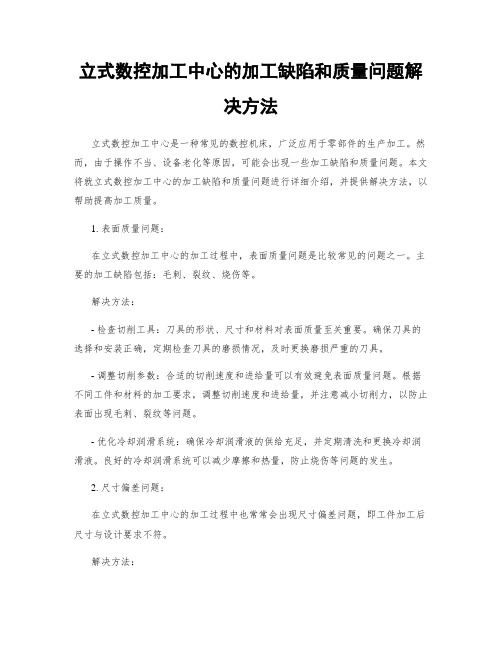
立式数控加工中心的加工缺陷和质量问题解决方法立式数控加工中心是一种常见的数控机床,广泛应用于零部件的生产加工。
然而,由于操作不当、设备老化等原因,可能会出现一些加工缺陷和质量问题。
本文将就立式数控加工中心的加工缺陷和质量问题进行详细介绍,并提供解决方法,以帮助提高加工质量。
1. 表面质量问题:在立式数控加工中心的加工过程中,表面质量问题是比较常见的问题之一。
主要的加工缺陷包括:毛刺、裂纹、烧伤等。
解决方法:- 检查切削工具:刀具的形状、尺寸和材料对表面质量至关重要。
确保刀具的选择和安装正确,定期检查刀具的磨损情况,及时更换磨损严重的刀具。
- 调整切削参数:合适的切削速度和进给量可以有效避免表面质量问题。
根据不同工件和材料的加工要求,调整切削速度和进给量,并注意减小切削力,以防止表面出现毛刺、裂纹等问题。
- 优化冷却润滑系统:确保冷却润滑液的供给充足,并定期清洗和更换冷却润滑液。
良好的冷却润滑系统可以减少摩擦和热量,防止烧伤等问题的发生。
2. 尺寸偏差问题:在立式数控加工中心的加工过程中也常常会出现尺寸偏差问题,即工件加工后尺寸与设计要求不符。
解决方法:- 检查加工程序:检查数控加工程序中设定的切削参数是否合适,是否存在误差。
确保加工程序正确无误,尤其要注意切削路径、切削速度和进给量的设置。
- 检查夹具和工件安装:夹具的稳定性和精确性对尺寸偏差的控制至关重要。
检查夹具的固定情况,确保工件安装稳定,防止振动和变形。
- 调整刀具补偿:通过调整刀具补偿,可以在加工过程中适当修正尺寸偏差。
根据实际情况,调整刀具补偿值,使加工后的工件尺寸达到设计要求。
3. 加工精度问题:立式数控加工中心的加工精度是影响加工质量的关键因素之一。
加工精度问题主要表现为:圆度误差、平面度误差、垂直度误差等。
解决方法:- 定期保养设备:对立式数控加工中心进行定期保养和维护,包括润滑设备、传动系统等,以确保设备的稳定性和精确性。
- 校正加工中心:定期检查和校正加工中心的各项参数和测量系统,确保其准确性。
立式加工中心主轴热误差的实验与分析
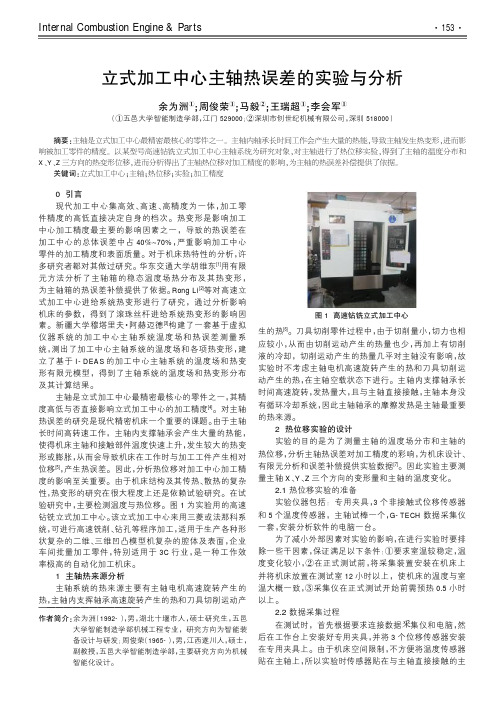
作者简介院余为洲(1992-),男,湖北十堰市人,硕士研究生,五邑 大学智能制造学部机械工程专业,研究方向为智能装 备设计与研发;周俊荣(1965-),男,江西遂川人,硕士, 副教授,五邑大学智能制造学部,主要研究方向为机械 智能化设计。
图 1 高速钻铣立式加工中心
生的热[6]。刀具切削零件过程中,由于切削量小,切力也相 应 较 小 ,从 而 由 切削 运 动 产 生 的 热 量 也 少 ,再 加 上 有 切 削 液的冷却,切削运动产生的热量几平对主轴没有影响,故 实验时不考虑主轴电机高速旋转产生的热和刀具切削运 动产生的热,在主轴空载状态下进行。主轴内支撑轴承长 时间高速旋转,发热量大,且与主轴直接接触,主轴本身没 有循环冷却系统,因此主轴轴承的摩擦发热是主轴最重要 的热来源。
立式加工中心误差分析研究

立式加工中心误差分析研究1. 引言1.1 研究背景立式加工中心是现代制造业中常用的一种加工设备,它可以对工件进行精确的加工,提高产品的质量和效率。
立式加工中心在加工过程中会存在一定的误差,这些误差会影响加工的精度和稳定性,甚至会导致产品质量不合格或者加工效率低下。
对立式加工中心的误差进行分析研究具有重要的意义。
随着现代制造业对产品质量和加工精度要求的不断提高,立式加工中心的误差分析研究变得尤为重要。
只有深入分析立式加工中心的误差来源、研究误差分析方法,并采取相应的误差校正措施,才能有效地提高加工精度,保证产品质量,提高生产效率。
对于立式加工中心误差分析研究的开展具有重要的指导意义,可以为提高制造业的发展水平提供参考。
1.2 研究目的研究目的是通过深入分析立式加工中心的误差来源、误差分析方法和误差校正措施,探索其对加工精度和效率的影响,为提高立式加工中心的加工质量和效率提供理论和实践参考。
通过对误差分析结果的综合研究,找出立式加工中心存在的问题和瓶颈,并提出相应的解决方案和改进措施,以实现加工精度的精确控制和提升加工效率的目标。
通过案例分析,进一步验证和论证提出的误差校正措施和改进建议的有效性,为立式加工中心的实际应用提供可靠的支撑,促进相关技术的发展和推广,推动行业向着更高水平迈进。
1.3 研究意义立式加工中心是现代制造业中常用的高精度加工设备,其误差分析研究对于提高加工质量、降低生产成本、提升企业竞争力具有重要意义。
立式加工中心误差分析可以帮助企业了解加工过程中的误差来源,找出导致加工精度不稳定的因素,从而有针对性地优化加工工艺,提高产品质量。
通过误差分析方法的研究,可以为制造企业提供更科学的生产控制手段,实现高效生产与精准加工的目标。
对于误差分析结果的深入研究可以为企业提供根本性的解决方案,避免因误差积累而导致的生产事故和损失。
立式加工中心误差分析研究对于提高企业的生产效率、产品质量以及市场竞争力具有重要意义,是现代制造业发展过程中不可忽视的关键环节。
立式加工中心典型故障的分析与排除
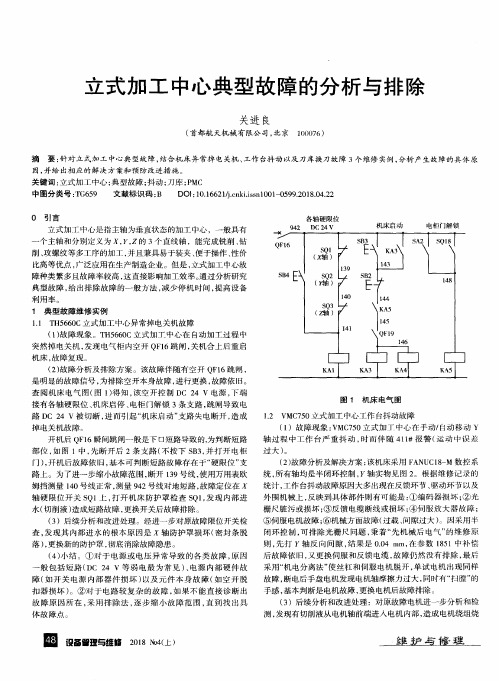
各轴 硬限 位 942 DC 24V
SQ1 (x轴 )
SB4 E 1。 (嘞s92)
机床 启动
电概 门解 锁
SQ3 (z轴 )
141
KA l
K^5
图 1 机 床 电 气 图
1.2 VMC750立 式 加 工 中 心工 作 台抖 动 故 障 (1)故障现象 :VMC750立 式加 丁中心 在手动/自动移 动 Y
(1)故 障现象 。TH5660C立 式加_T中心在 自动加工过程 中 突 然 掉 电关 机 ,发 现 电气 柜 内 空 开 QF16跳 闸 ,关 机 合 上 后 重 启 机 床 ,故 障 复现 。
(2)故 障 分 析 及 排 除 方 案 。该 故 障开本身故 障,进行更换 ,故障依 旧。 查 阅机 床 电 气 图 (图 1)得 知 ,该 空 开 控 制 DC 24 V 电源 ,下 端 接有各轴硬 限位 、机 床启停 、电柜 门解锁 3条支路 ,跳 闸导致 电 路 DC 24 V 被 切 断 ,进 而 引起 “机 床 启 动 ”支 路 失 电 断 开 ,造 成 掉 电关 机 故 障 。
轴 过程 中 工作 台严重 抖动 ,时 而伴 随 4l1#报 警 (运动 中误 差 过 大 )。
(2)故障分析及解决方案 :该机床采用 FANUC18-M数控 系 统 ,所有轴均 是半 闭环 控制 ,y轴实物见图 2。根据维修记 录的 统计 ,工作台抖动故障原因大多出现在反馈环节 、驱动环节 以及 外围机械上 ,反映到具体部 件则有可能是 :①编 码器损坏 ;② 光 栅 尺脏污或损坏 ;③反馈 电缆 断线或损坏 ;④伺 服放大器 故障 ; ⑤ 伺服电机 故障 ;⑥机械方面故障(过载 、间隙过大 )。因采用半 闭环控 制 ,可排除光 栅尺 问题 ,秉 着“先机 械后 电气 ”的维 修原 则 ,先打 Y轴反 向间隙 ,结果 是 0.04 lnIIl,在参数 1851中补偿 后故障依 旧,又更换伺服 和反馈电缆 ,故障仍然 没有排除 ,最后 采用“机电分离法”使丝杠和伺 服电机脱开 ,单试 电机 m现 同样 故障 ,断 电后手盘 电机发现 电机轴摩擦力过大 ,同时有 “扫膛 ”的 手感 ,基本判断是 电机故障 ,更 换电机后 故障排除。
美国HAAS公司VF3加工中心主轴典型故障处理
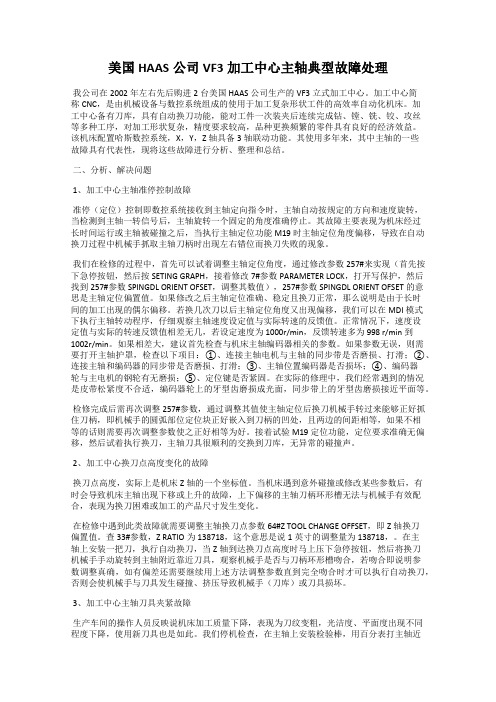
美国HAAS公司VF3加工中心主轴典型故障处理我公司在2002年左右先后购进2台美国HAAS公司生产的VF3立式加工中心。
加工中心简称CNC,是由机械设备与数控系统组成的使用于加工复杂形状工件的高效率自动化机床。
加工中心备有刀库,具有自动换刀功能,能对工件一次装夹后连续完成钻、镗、铣、铰、攻丝等多种工序,对加工形状复杂,精度要求较高,品种更换频繁的零件具有良好的经济效益。
该机床配置哈斯数控系统,X,Y,Z轴具备3轴联动功能。
其使用多年来,其中主轴的一些故障具有代表性,现将这些故障进行分析、整理和总结。
二、分析、解决问题1、加工中心主轴准停控制故障准停(定位)控制即数控系统接收到主轴定向指令时,主轴自动按规定的方向和速度旋转,当检测到主轴一转信号后,主轴旋转一个固定的角度准确停止。
其故障主要表现为机床经过长时间运行或主轴被碰撞之后,当执行主轴定位功能M19时主轴定位角度偏移,导致在自动换刀过程中机械手抓取主轴刀柄时出现左右错位而换刀失败的现象。
我们在检修的过程中,首先可以试着调整主轴定位角度,通过修改参数257#来实现(首先按下急停按钮,然后按SETING GRAPH,接着修改7#参数PARAMETER LOCK,打开写保护,然后找到257#参数SPINGDL ORIENT OFSET,调整其数值),257#参数SPINGDL ORIENT OFSET的意思是主轴定位偏置值。
如果修改之后主轴定位准确、稳定且换刀正常,那么说明是由于长时间的加工出现的偶尔偏移。
若换几次刀以后主轴定位角度又出现偏移,我们可以在MDI模式下执行主轴转动程序,仔细观察主轴速度设定值与实际转速的反馈值。
正常情况下,速度设定值与实际的转速反馈值相差无几,若设定速度为1000r/min,反馈转速多为998 r/min到1002r/min。
如果相差大,建议首先检查与机床主轴编码器相关的参数。
如果参数无误,则需要打开主轴护罩,检查以下项目:①、连接主轴电机与主轴的同步带是否磨损、打滑;②、连接主轴和编码器的同步带是否磨损、打滑;③、主轴位置编码器是否损坏;④、编码器轮与主电机的钢轮有无磨损;⑤、定位键是否紧固。
立式加工中心的精度差的原因分析汇总
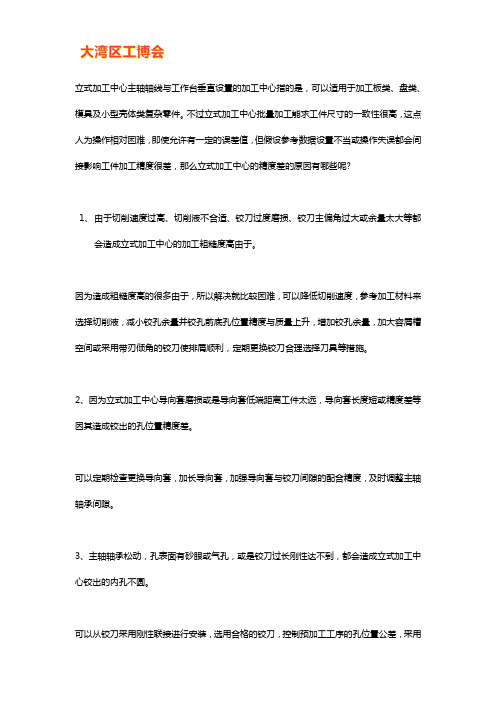
立式加工中心主轴轴线与工作台垂直设置的加工中心指的是,可以适用于加工板类、盘类、模具及小型壳体类复杂零件。
不过立式加工中心批量加工能求工件尺寸的一致性很高,这点人为操作相对困难,即使允许有一定的误差值,但假设参考数据设置不当或操作失误都会间接影响工件加工精度很差,那么立式加工中心的精度差的原因有哪些呢?
1、由于切削速度过高、切削液不合适、铰刀过度磨损、铰刀主偏角过大或余量太大等都
会造成立式加工中心的加工粗糙度高由于。
因为造成粗糙度高的很多由于,所以解决就比较困难,可以降低切削速度,参考加工材料来选择切削液,减小铰孔余量并铰孔前底孔位置精度与质量上升,增加铰孔余量,加大容屑槽空间或采用带刃倾角的铰刀使排屑顺利,定期更换铰刀合理选择刀具等措施。
2、因为立式加工中心导向套磨损或是导向套低端距离工件太远,导向套长度短或精度差等因其造成铰出的孔位置精度差。
可以定期检查更换导向套,加长导向套,加强导向套与铰刀间隙的配合精度,及时调整主轴轴承间隙。
3、主轴轴承松动,孔表面有砂眼或气孔,或是铰刀过长刚性达不到,都会造成立式加工中心铰出的内孔不圆。
可以从铰刀采用刚性联接进行安装,选用合格的铰刀,控制预加工工序的孔位置公差,采用
不等齿距的铰刀、选用合格的毛坯,定期调整主轴间隙等来着手解决。
4、立式加工中心切削速度过高,进给量不当或加工余量过大,或者是立式加工中心自身因其造成的孔径逐渐加大。
可以根据实际的情况进行处理,适当减小铰刀外径、降低切削速度、减小主偏角,选择冷却性能较好的切削液、调整或更换主轴轴承或者更换整条主轴都可以有效解决孔径加大的问题。
加工中心故障案例分析共49页文档
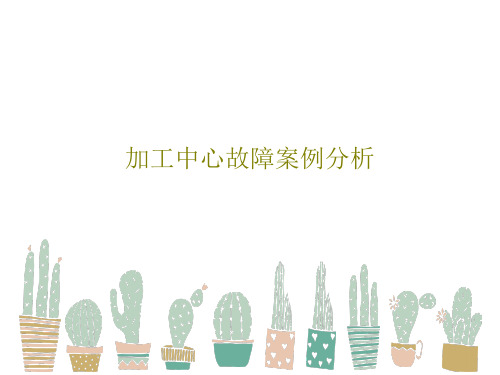
加工中心故障案例分析
46、法律有Байду номын сангаас打破平静。——马·格林 47、在一千磅法律里,没有一盎司仁 爱。— —英国
48、法律一多,公正就少。——托·富 勒 49、犯罪总是以惩罚相补偿;只有处 罚才能 使犯罪 得到偿 还。— —达雷 尔
50、弱者比强者更能得到法律的保护 。—— 威·厄尔
31、只有永远躺在泥坑里的人,才不会再掉进坑里。——黑格尔 32、希望的灯一旦熄灭,生活刹那间变成了一片黑暗。——普列姆昌德 33、希望是人生的乳母。——科策布 34、形成天才的决定因素应该是勤奋。——郭沫若 35、学到很多东西的诀窍,就是一下子不要学很多。——洛克
14.加工误差大故障案例分析(精)
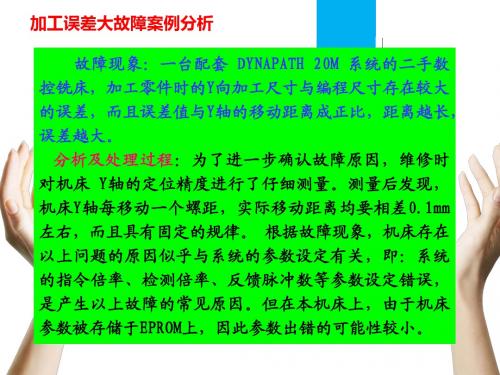
加工误差大故障案例分析 故障现象:一台配套 DYNAPATH 20M 系统的二手数 控铣床,加工零件时的Y向加工尺寸与编程尺寸存在较大 的误差,而且误差值与Y轴的移动距离成正比,距离越长, 误差越大。 分析及处理过程:为了进一步确认故障原因,维修时 对机床 Y轴的定位精度进行了仔细测量。测量后发现, 机床Y轴每移动一个螺距,实际移动距离均要相差 0.1mm 左右,而且具有固定的规律。 根据故障现象,机床存在 以上问题的原因似乎与系统的参数设定有关,即:系统 的指令倍率、检测倍率、反馈脉冲数等参数设定错误, 是产生以上故障的常见原因。但在本机床上,由于机床 参数被存储于EPROM上,因此参数出错处理过程:进一步观察、测量机床Y 轴移动情况, 发现该机床 Y 轴伺服在移动到某一固定角度时,都有一冲 击过程:在无冲击的区域,测量实际移动距离与指令值相符, 根据以上现象,初步判定,故障原因与位置检测系统有关。 因该机床采用的是半闭环系统,维修时拆下了伺服内装 式编码器检查,经仔细观察发现,在冲击的区域,编码器动 光栅上有一明显的黑斑。 考虑到更换编码器的成本与时间问题,维修时对编码器 进行了仔细的清洗,洗去了由于轴承润滑脂融化产生的黑斑。 重新安装编码器后,机床可以正常工作,Y 轴冲击现象消失, 精度恢复。
三菱数控系统维修100例
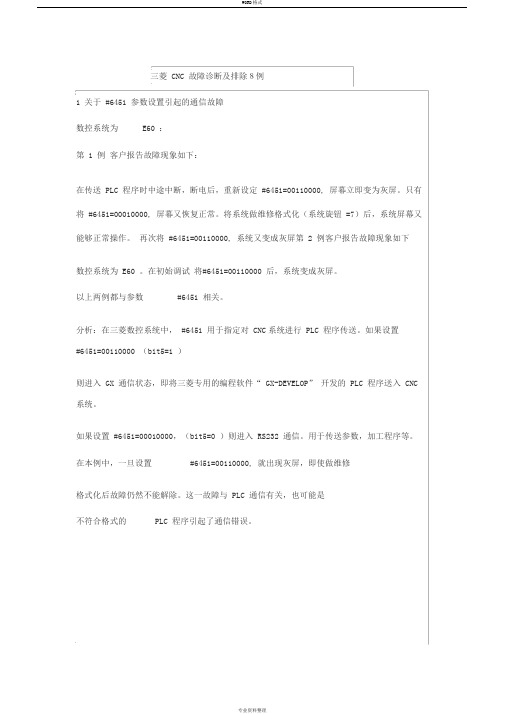
三菱 CNC 故障诊断及排除8例1 关于 #6451 参数设置引起的通信故障数控系统为E60 :第 1 例客户报告故障现象如下:在传送 PLC 程序时中途中断,断电后,重新设定 #6451=00110000, 屏幕立即变为灰屏。
只有将 #6451=00010000, 屏幕又恢复正常。
将系统做维修格式化(系统旋钮 =7)后,系统屏幕又能够正常操作。
再次将 #6451=00110000, 系统又变成灰屏第 2 例客户报告故障现象如下数控系统为 E60 。
在初始调试将#6451=00110000 后,系统变成灰屏。
以上两例都与参数#6451 相关。
分析:在三菱数控系统中, #6451 用于指定对 CNC系统进行 PLC 程序传送。
如果设置#6451=00110000 (bit5=1 )则进入 GX 通信状态,即将三菱专用的编程软件“ GX-DEVELOP”开发的 PLC 程序送入 CNC 系统。
如果设置 #6451=00010000,(bit5=0 )则进入 RS232 通信。
用于传送参数,加工程序等。
在本例中,一旦设置#6451=00110000, 就出现灰屏,即使做维修格式化后故障仍然不能解除。
这一故障与 PLC 通信有关,也可能是不符合格式的PLC 程序引起了通信错误。
处理:设置 NC 系统旋钮 =1,使 PLC程序停止,解除 PLC程序的影响。
再设置 #6451=00110000 ,此时未出现灰屏,传送正常 PLC 程序后,系统正常。
在第一例中,向系统传送原 PLC 程序后,观察到 GX软件的对话窗口有“ PLC 程序报警信息” ,这是首次观察到的现象。
将 PLC 程序格式化后,再传送正常程序,系统正常。
2.系统原点漂移:一台控制系统为M64的铣床。
运行三月后客户报告出现下列故障现象:停电一晚,第 2 天上电后运行时,出现位置偏差,目测有3mm—6mm,9.8mm,,以当日基准设定为G54 坐标,继续运行能够正常运行,无偏差。
浅谈立式加工中心机械原因造成加工超差的应对措施
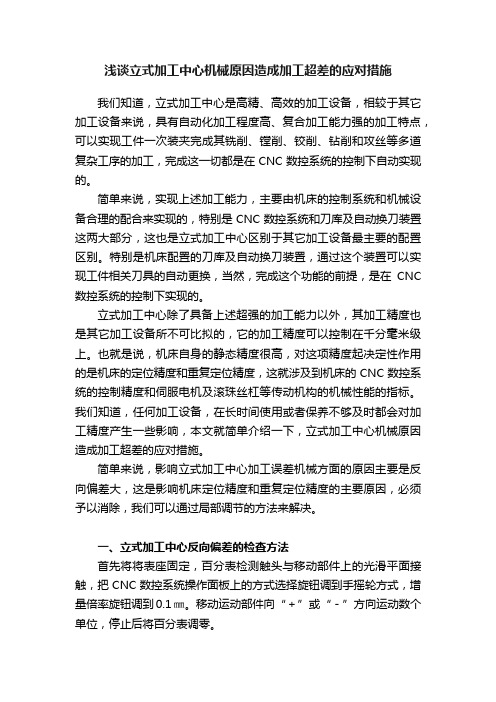
浅谈立式加工中心机械原因造成加工超差的应对措施我们知道,立式加工中心是高精、高效的加工设备,相较于其它加工设备来说,具有自动化加工程度高、复合加工能力强的加工特点,可以实现工件一次装夹完成其铣削、镗削、铰削、钻削和攻丝等多道复杂工序的加工,完成这一切都是在CNC数控系统的控制下自动实现的。
简单来说,实现上述加工能力,主要由机床的控制系统和机械设备合理的配合来实现的,特别是CNC数控系统和刀库及自动换刀装置这两大部分,这也是立式加工中心区别于其它加工设备最主要的配置区别。
特别是机床配置的刀库及自动换刀装置,通过这个装置可以实现工件相关刀具的自动更换,当然,完成这个功能的前提,是在CNC 数控系统的控制下实现的。
立式加工中心除了具备上述超强的加工能力以外,其加工精度也是其它加工设备所不可比拟的,它的加工精度可以控制在千分毫米级上。
也就是说,机床自身的静态精度很高,对这项精度起决定性作用的是机床的定位精度和重复定位精度,这就涉及到机床的CNC数控系统的控制精度和伺服电机及滚珠丝杠等传动机构的机械性能的指标。
我们知道,任何加工设备,在长时间使用或者保养不够及时都会对加工精度产生一些影响,本文就简单介绍一下,立式加工中心机械原因造成加工超差的应对措施。
简单来说,影响立式加工中心加工误差机械方面的原因主要是反向偏差大,这是影响机床定位精度和重复定位精度的主要原因,必须予以消除,我们可以通过局部调节的方法来解决。
一、立式加工中心反向偏差的检查方法首先将将表座固定,百分表检测触头与移动部件上的光滑平面接触,把CNC数控系统操作面板上的方式选择旋钮调到手摇轮方式,增量倍率旋钮调到0.1㎜。
移动运动部件向“+”或“-”方向运动数个单位,停止后将百分表调零。
移动运动部件向“+”或“-”方向运动一个或数个单位,然后再向反方向移动运动部件一个或数个单位。
重复上述的动作不少于3次,读出此时百分表的差值,这个误差值就是反向偏差,将倍率调到0.01㎜。
- 1、下载文档前请自行甄别文档内容的完整性,平台不提供额外的编辑、内容补充、找答案等附加服务。
- 2、"仅部分预览"的文档,不可在线预览部分如存在完整性等问题,可反馈申请退款(可完整预览的文档不适用该条件!)。
- 3、如文档侵犯您的权益,请联系客服反馈,我们会尽快为您处理(人工客服工作时间:9:00-18:30)。
案例分析
现代:C.處 经 济 和 偉 凰 化 Modern Industrial Economy and Informationization
Total of 153 亂 21 , 2017
DOI:10.16525/j .cn ki.14 - 1 362/n .2017.21.36
加工参数调整。 负载惯M仍率参数的调整,如 表 2 所示。:
表 2 机床参数调整示意表
调整前
参数及轴号
X
Y
z
询整启
X
Y
z
(精 铣 )。加 工 程 序 内 存 在 多 处 微 小 不 规 则 不 均 匀 线 段 ,对加工时间和工件的加工质.U:存在影响,故采用 SSS(Super Smooth Surface)功會旨气
此处为进刀_点 ,.编_ 工应该在进刀点重叠,
该路径无重叠
F3000
( F5cClQ50收 稿 日 期 :2〇 17-11-01 作者简介:邱 寿 昆 (1971— ),男 ,硕 士 ,讲 师 ,工 程 师 ,研究方向 为 数 控 机 床 维 修 、自动化研究。
表 1 机床配置示意表
图 4 调 整 前 X F 平 面 突 起 为 18.88 u m 示意图 图 5 调 整 后 平 面 突 起 为 2.66 u m 示意图
图 7 调整后加工效果示意图
4 结语 三菱数控系统加工中心加工过程中出现的加0 :
不良现象,多数可以查阅系统说明书、参数说明书通 过调整参数、修改程序来父现。
参考文献 I I ] 黄风.数控系统现场调试实战手册[M].北 京 :化 学 工 业 出 版 社 ,
关 键 词 :三 菱 立 式 加 工 中 心 ;加 工 不 良 ;解 决 思 路 ;解 决 方 法
中图分类号:TP2
文献标识码:A
文 章 编 号 =2 0 9 5 - 0 7 4 8 ( 2 0 1 7 ) 2 1 - 0 0 8 9 - 0 2
引言 3 菱数控系统由数控硬件和数控软件两大部分
来工作的。数控系统的硬件由数控装置、输 入 /输出 装 置 、驱动装置和机床电器逻辑控制装置等组成 :X 业中常用的三菱数控系统有:M700V 系 列 ;M70V 系列;M7 0 系列;M60S 系列;E6 8 系列;E6 0 系列;C6 系 列 ;C6 4 系 列 ;C7 0 系 列 ,本文讨论三菱M7 0 系统 加工过程中出现问题及其解决方法6 1 案 例 1 故障现象
2016. [ 2 ] 李 小 笠 ,徐有峰.数控机床操怍与编程[m] 京;机械工业出版
|£:12016, 1 « 三 菱 CNC参 数 介 绍 [Z],三菱电机自动化(上海)有限公 U CNC
营 业技术,2013:23-24.
(编辑:刘楠)
Case Analysis of Bad Machining in Mitsubishi Vertical Machining Center
• 90 •
现代工业经济和信息化
xdgyjj xxhx@163 .com
第 7卷
此故障现象的分析处理:
3 客户加工程序检查
1) 检查机床相关硬件,无 异 常 ;
I P S 8 mm 的 郷 刀 ,挪 转 速 S=4 000 mm/min,
2)
检查机床参数:伺服调整参数确认,无异常进; 給 速 度 F=2 000 mm/min,每次切觀量:为0.10 mm
三菱立式加工中心加工不良案例分析
邱寿昆
(苏州健雄职业技术学院, 江 苏 苏 州 215411)
摘 要 :结 合 多 年 教 学 、多 年 实 践 工 作 经 验 ,对 三 菱 立 式 加 工 中 心 加 工 过 程 中 出 现 的 几 个 问 题 ,通 过 图 示 的 方
法 ,阐 述 了 如 何 通 过 修 改 系 统 参 数 、修 改 加 工 程 序 ,以 解 决 加 工 过 程 出 现 的 不 良 现 象 的 思 路 与 方 法 。
结论:经过以上调整,加丄结果对比如图6、图 7 所 示 <5
2237 等
140 160
140 318
356
389
真圆补偿参数调整:客户未使用丢步补偿3 功 能,使用丢步补偿2 。丟 步 补 偿 3 可以对机械上的一 些缺陷进行补偿,丢 步 补 偿 2 则 不 能 ,所以建议客户 以 屢 都 使 用 丟 步 补 偿 3,调 ■ 前 后 效 果 如 图 4 、團 5 中蓝线所示Q
转 角 过 切 、产 生 进 刀 纹 ,具 体 表 现 如 图 1、图 2 所示。
此现象的分析处理:
1 )产 品 底 座为方形,对转角加工要求较高,系统
参数设置存在问题; 2 )在进刀处有刀痕问题,程序编制存在问题® 。
从上面分析得到结论:
1)
转角需设置减速,将 转 角 减 速 参 数 1149设置
机床控制轴
伺服型号
电机型号
编码器
X
VDS-D-SVJ3-30
HF204S
A48
Y
VDS-D-SVJ3-30
HF204S
A48
Z
VDS-D-SVJ3-30
HF204S
A48
MDS-D-SPJ3-75 SJ-D7/100-01
注 : 控 制 器 为 FCA70P-2B;机 床 型 号 为 VMC850;机 床 编 号 为 BND-1009W00D-F9〇
Qiu Shoukun ( Suzhou Chien-shiung Institute of Technology, Suzhou Jiangsu 215411)
Abstract:Combined with the author!s experience of teaching and practice of many years, as to some problems for the processing of Mitsubishi vertical machining center, by graphic method, this paper describes how to modify the system parameters and processing procedures to solve the bad phenomenon in machining process. Key words:Mitsubishi vertical machining center; poor machining; solutions; method
为 1 之后转角过切问题解决;
2)
检查加工程序后,发现没有添加高速高精指
令 ,同时编裎人员没有在进刀点童叠路径。在力口工程 序 中 添 加 高 速 高 精 G05.1Q1。
重新加工,测试加:T 工件转角进刀合格。 2 案 例 2 故障现象
表面刀纹加工不良现象t i t 件表面有振纹,面粗 糙 ,厂家放映调整多次无明显改善《•具体如图3 所示。