压力缸的摆辗挤压工艺及模具设计
挤压工艺及模具设计

挤压工艺及模具设计Extrusion Technology and Mould Design一、挤压工艺分类挤压可分为以下三类:1)冷挤压,又称冷锻,一般指在回复温度以下(室温)的挤压。
2)温挤压,一般指坯料在金属再结晶温度以下、回复温度以上进行的挤压。
对于黑色金属,以600℃为界,划分为低温挤压和高温挤压。
3)热挤压,指坯料在金属再结晶温度以上进行的挤压。
1)冷挤压工艺冷挤压是在冷态下,将金属毛坯放入模具模腔内,在强大的压力和一定的速度作用下,迫使金属从模腔中挤出,从而获得所需形状、尺寸以及一定力学性能的挤压件。
冷挤压与热锻、粉末冶金、铸造及切削加工相比,具有以下主要优点:1)因在冷态下挤压成形,挤压件质量好、精度高、其强度性能也好;2)冷挤压属于少、无切削加工,节省原材料;3)冷挤压是利用模具来成形的,其生产效率很高;4)可以加工其它工艺难于加工的零件。
2)温挤压工艺温挤压成形技术是近年来在冷挤压塑性成形基础上发展起来的一种少无切削新工艺,又称温热挤压。
它与冷、热挤压不同,挤压前已对毛坯进行加热,但其加热温度通常认为是在室温以上、再结晶温度以下的温度范围内。
对温挤压的温度范围目前还没有一个严格的规定。
有时把变温前将毛坯加热,变形后具有冷作硬化的变形,称为温变形。
或者,将加热温度低于热锻终锻温度的变形,称为温变形。
从金属学观点来看,区分冷、热加工可根据金属塑性变形后有无加工硬化现象存在来决定似乎更合理些。
在金属塑性变形后存在加工硬化现象这个过程称为冷变形及温变形。
3)热挤压工艺热挤压是几种挤压工艺中最早采用的挤压成形技术,它是在热锻温度时借助于材料塑性好的特点,对金属进行各种挤压成形。
目前,热挤压主要用于制造普通等截面的长形件、型材、管材、棒料及各种机器零件等。
热挤压不仅可以成形塑性好,强度相对较低的有色金属及其合金,低、中碳钢等,而且还可以成形强度较高的高碳、高合金钢,如结构用特殊钢、不锈钢、高速工具钢和耐热钢等。
挤压工艺操作规程文档信
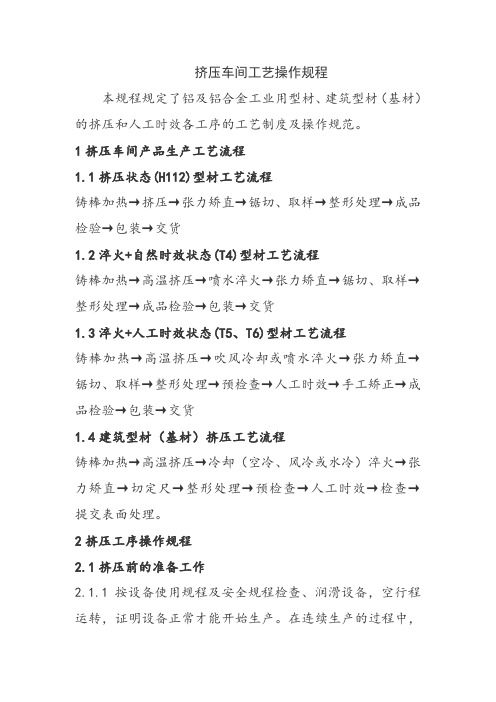
挤压车间工艺操作规程本规程规定了铝及铝合金工业用型材、建筑型材(基材)的挤压和人工时效各工序的工艺制度及操作规范。
1挤压车间产品生产工艺流程1.1挤压状态(H112)型材工艺流程铸棒加热→挤压→张力矫直→锯切、取样→整形处理→成品检验→包装→交货1.2淬火+自然时效状态(T4)型材工艺流程铸棒加热→高温挤压→喷水淬火→张力矫直→锯切、取样→整形处理→成品检验→包装→交货1.3淬火+人工时效状态(T5、T6)型材工艺流程铸棒加热→高温挤压→吹风冷却或喷水淬火→张力矫直→锯切、取样→整形处理→预检查→人工时效→手工矫正→成品检验→包装→交货1.4建筑型材(基材)挤压工艺流程铸棒加热→高温挤压→冷却(空冷、风冷或水冷)淬火→张力矫直→切定尺→整形处理→预检查→人工时效→检查→提交表面处理。
2挤压工序操作规程2.1挤压前的准备工作2.1.1按设备使用规程及安全规程检查、润滑设备,空行程运转,证明设备正常才能开始生产。
在连续生产的过程中,应认真交接班,仔细了解上一班的生产、质量、设备和工具等情况。
2.1.2检查铸棒加热炉、模具加热炉、挤压筒的仪表定温和实际指示温度,以及铸棒的实际温度是否符合规定要求。
模具加热炉温度范围一般为400~450℃。
2.1.3检查工模具(包括挤压模、挤压垫等)的规格、型号和尺寸是否与生产卡片一致,质量是否符合要求。
2.1.4各机台当班的班长应提前2~3小时向模具工提交下班准备生产的各种规格产品的工具任务单,以便模具工及时准备和加热有关工具。
各机台用模具在加热炉内的保温时间一般不小于:6MN挤压机的1小时,8MN挤压机的1.5小时,10MN以上吨位挤压机的2小时。
2.2铸棒装炉和加热2.2.1装炉前应按照生产卡片核对铸棒的合金、炉次、规格、数量,确认无误后方可装炉,不得擅自更改。
2.2.2为了保证产品质量,装炉前铸棒的表面应清洁,无油污、灰尘、金属屑及其它赃物。
否则,装炉人员应在装炉前清理干净。
挤压工艺及模具课程设计

挤压工艺及模具课程设计一、课程目标知识目标:1. 学生能够理解挤压工艺的基本概念,掌握金属挤压的基本原理;2. 学生能够描述挤压模具的构成、分类及工作原理;3. 学生能够掌握影响挤压工艺的主要因素,如材料性能、挤压温度、挤压速度等;4. 学生能够了解挤压工艺在实际生产中的应用及发展趋势。
技能目标:1. 学生能够运用所学知识,分析并解决挤压工艺中的实际问题;2. 学生能够设计简单的挤压模具,并进行初步的模具分析与优化;3. 学生能够运用计算机辅助设计软件(如CAD)进行挤压模具的设计与仿真。
情感态度价值观目标:1. 学生通过学习挤压工艺及模具课程,培养对制造业的兴趣和热情;2. 学生能够认识到挤压工艺在现代化生产中的重要性,增强对制造业的责任感和使命感;3. 学生在学习过程中,培养团队合作意识,提高沟通与表达能力。
分析课程性质、学生特点和教学要求:1. 课程性质:本课程为机械制造及自动化专业的一门专业课程,具有实践性和应用性;2. 学生特点:学生为高职或中职院校机械制造及自动化专业二年级学生,具备一定的机械基础知识;3. 教学要求:注重理论与实践相结合,强调实际操作能力的培养,提高学生的综合素质。
二、教学内容1. 挤压工艺基本概念与原理- 金属挤压的基本概念与分类- 挤压工艺的优缺点分析- 挤压工艺的基本原理及过程2. 挤压模具设计与分析- 挤压模具的构成与分类- 挤压模具的设计原则与方法- 模具分析与优化- 计算机辅助设计软件在模具设计中的应用3. 影响挤压工艺的因素- 材料性能对挤压工艺的影响- 挤压温度、挤压速度等工艺参数对挤压质量的影响- 挤压润滑对挤压工艺的影响4. 挤压工艺在实际生产中的应用- 挤压工艺在各类产品中的应用实例- 挤压工艺在制造业中的发展趋势- 新型挤压工艺及模具技术的探讨5. 实践教学环节- 挤压模具设计与制作实践- 挤压工艺操作实践- 案例分析与讨论教学大纲安排:第一周:挤压工艺基本概念与原理第二周:挤压模具设计与分析第三周:影响挤压工艺的因素第四周:挤压工艺在实际生产中的应用第五周:实践教学环节(挤压模具设计与制作实践、挤压工艺操作实践、案例分析)教学内容根据课程目标,结合教材章节进行组织,注重理论与实践相结合,旨在培养学生的实际操作能力和创新能力。
挤压模具设计课程设计

为了延长模具的使用寿命,模孔离模具外径圆周的距离和模孔之间的距离都应保持一定的数值,这个数值与挤压机的大小有关。对于49MN以下的挤压机,这个距离可取15~50mm;对于大型挤压机,应加大到30~80mm,参照表2-1所列经验数据,取25mm。
0.10~1.67
600~800
含20~30Ni白铜
980~1000
-
0.10~(0.4~0.6)
500~850
第三章
3.1
模孔尺寸的确定主要考虑挤压制品的金属成分、断面形状、尺寸偏差、各部位几何形状特点和型材的冷却收缩量、张力矫直时的断面收缩量等因素的综合影响来进行设计或计算确定。若用A表示模孔长度,则用以下算式对棒材模进行计算:
第二章
采用多孔棒材模时,金属流动要比单孔模均匀,故可减少中心缩尾形成的几率。但是,如果模孔排列不当,会使挤出的制品长短不齐,增加几何废料,恶化表面质量;如果模孔靠近挤压筒边缘,也会使制品表面产生起皮、分层等缺陷。此外,多模孔过于靠近挤压筒边缘时由于内侧金属供应量大、流动速度快,而外侧由于金属供应量不足,流动速度慢,会造成制品出现外侧裂纹;当模孔太靠近挤压筒中心时,外侧金属供应量大于内侧,则制品易出现内侧裂纹。图2-1所示,表示了模孔分布对制品长度的影响,从而了解模孔位置布置的重要性,故应将多孔模模孔的理论重心均匀地分布在距模具中心和挤压边缘有适当距离的同心圆周上。
表2-1 模孔间最小距离
挤压筒直径
80~95
115~130
150~200
220~280
300~500
最小距离
15
20
挤压工艺与模具课程设计
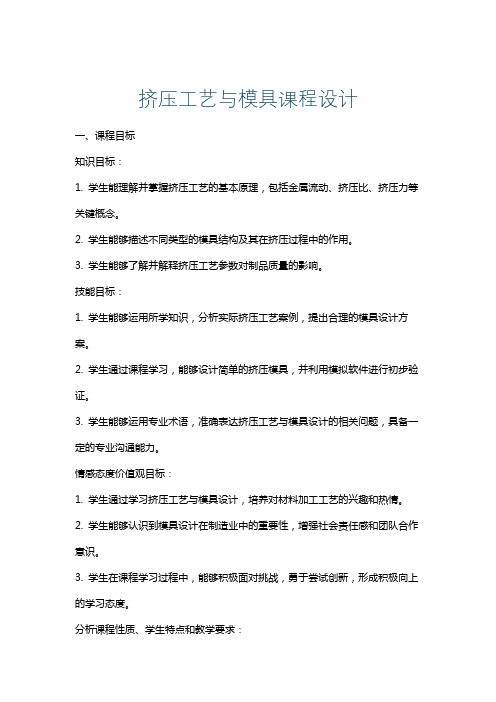
挤压工艺与模具课程设计一、课程目标知识目标:1. 学生能理解并掌握挤压工艺的基本原理,包括金属流动、挤压比、挤压力等关键概念。
2. 学生能够描述不同类型的模具结构及其在挤压过程中的作用。
3. 学生能够了解并解释挤压工艺参数对制品质量的影响。
技能目标:1. 学生能够运用所学知识,分析实际挤压工艺案例,提出合理的模具设计方案。
2. 学生通过课程学习,能够设计简单的挤压模具,并利用模拟软件进行初步验证。
3. 学生能够运用专业术语,准确表达挤压工艺与模具设计的相关问题,具备一定的专业沟通能力。
情感态度价值观目标:1. 学生通过学习挤压工艺与模具设计,培养对材料加工工艺的兴趣和热情。
2. 学生能够认识到模具设计在制造业中的重要性,增强社会责任感和团队合作意识。
3. 学生在课程学习过程中,能够积极面对挑战,勇于尝试创新,形成积极向上的学习态度。
分析课程性质、学生特点和教学要求:本课程为专业实践课程,以模具设计与制造为核心内容,结合学生已掌握的机械基础知识,培养其实践操作能力。
课程针对高中年级学生,具备一定的基础知识和动手能力,注重理论与实践相结合。
教学要求强调学生的主动参与,通过项目式学习,激发学生的创新思维,培养解决实际问题的能力。
课程目标旨在使学生能够将理论知识应用于实际生产,提高综合素养。
二、教学内容1. 挤压工艺原理:包括金属塑性变形原理、挤压比、挤压力的计算、挤压过程中的温度控制等。
相关教材章节:第1章 挤压工艺基础2. 模具结构与设计:介绍不同类型的挤压模具结构、工作原理、设计要点及材料选择。
相关教材章节:第2章 模具结构与设计3. 挤压工艺参数对制品质量的影响:分析挤压速度、温度、润滑等工艺参数对制品表面质量、尺寸精度等方面的影响。
相关教材章节:第3章 挤压工艺参数优化4. 模具设计实例分析:通过实际案例,分析模具设计的全过程,包括市场需求、模具结构设计、参数选择等。
相关教材章节:第4章 模具设计实例5. 模拟软件应用:介绍挤压模具设计模拟软件的使用方法,使学生能够利用软件进行模具设计的初步验证。
挤压模具制作与设计实验报告

挤压模具制作与设计实验报告实验目的本实验旨在探究挤压模具的制作与设计,并通过实际操作来了解挤压模具的使用方法和注意事项。
实验设备与材料- 挤压机- 铝合金材料- 挤压模具- 计算机辅助设计软件实验步骤步骤一:挤压模具设计1. 根据需要制作的铝合金产品的形状和尺寸,在计算机辅助设计软件上进行三维模型设计。
2. 根据设计好的三维模型,进行模具设计。
考虑到材料的流动性和受力情况,设计合理的模具结构和出模方式。
步骤二:挤压模具制作1. 准备所需的模具材料,一般使用高强度、高硬度的合金材料。
2. 根据设计好的模具结构制作模具的零件。
可以使用数控机床进行加工,确保模具精度和质量。
3. 将加工好的模具零件进行组装,并进行必要的热处理和表面处理,提高模具的使用寿命和质量。
步骤三:挤压模具调试1. 将制作好的挤压模具安装到挤压机上。
2. 启动挤压机,并根据所制作的铝合金产品的要求,调整挤压机的参数,如温度、压力等。
3. 进行模具试压,检查铝合金产品的质量和尺寸是否符合要求。
4. 根据试压结果,调整模具的结构和参数,直至满足产品要求为止。
实验结果与分析经过实验,成功制作了一套挤压模具,并使用挤压机进行了模具试压。
铝合金产品的质量和尺寸达到了设计要求,说明挤压模具的制作与设计是成功的。
通过实验过程中的观察和分析,我们可以得出以下结论:1. 挤压模具的设计要考虑材料流动性和受力情况,以保证产品质量。
2. 挤压模具的制作需要使用高强度、高硬度的合金材料,并进行必要的热处理和表面处理。
3. 挤压模具的调试是一个迭代的过程,需要根据试压结果不断调整模具的结构和参数,直至满足产品要求。
4. 计算机辅助设计软件在挤压模具设计中起到了重要的作用,能够提高设计的精度和效率。
实验总结挤压模具的制作与设计是一项复杂的工艺,需要对材料和工艺有深入的理解和掌握。
本次实验通过实际操作,使我们更加熟悉了挤压模具的制作过程和设计原理。
通过本次实验,我们深刻认识到挤压模具在工业生产中的重要性,它在航空航天、汽车制造、建筑等领域都有广泛的应用。
摆动辗压
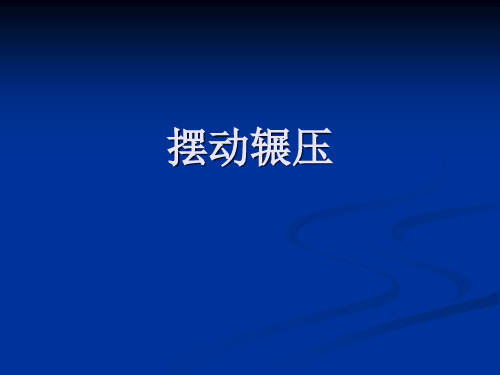
式中: F − 摆辗力(kN); A c − 接触面积(mm 2),Ac = λπR 2; p − 平均单位压力(Mpa)。 p值可按经验公式计算如下: p = Kσ s K − 系数,对于自由镦粗K = 1.5~1.7;局部镦粗 K = 1.6 ~ 1.9;模膛内成形K = 2.0 ~ 2.3.
(3)摆头电机功率的计算 2s −8 Fn −1 P = 127.5 × 10 Ds cos (1 − ) η Dtgγ
• 冷碾铆接法的应用范围 1、 可铆接的材料:除了可铆接低碳钢铆钉外,还可铆接中 碳钢及不锈钢铆钉,当然铜、铝铆钉更是在铆接范围之列。 2、 可铆接的形状:只要改变铆头的形状,就能铆接成各种 形状,此外,径向铆接机还可和于压印。 3、 适用行业:冷碾铆接法可广泛用于精密机械、纺织器材、 钢制家具、建筑五金、高低压电器、五金工具、汽车、摩托 车配件等众多行业,特别是在汽车门锁、刮水器、制动器、 离合器、后门撑杆、门铰链、玻璃升降器、化油器、手制动 器、转向球接头、摩托车减震器等汽摩配件行业中应用更为 广泛。 四、铆接的典型零件 1、 铆接钢丝钳。钢丝钳铆接传统工艺是采用电加热热铆和 冲铆,热铆不仅能耗很大(达20KW以上),而且铆钉易起氧 化皮,效率也低。冲铆虽然效率高,但易将铆钉中部镦粗, 松紧度不易保证,况且噪音大,操作也不安全。冷碾铆接正 好克服了上述蔽端。全国已有二十多家钢丝钳厂采用了冷碾 铆接机,大大提高了质量,降低了成本。
摆辗模具设计 1.摆辗模具受力特点: (1)热辗时模具中部受热时间长,温升高,若超过模 具材料的回火温度,模具可能因软化而报废; (2)模具因受交变载荷作用,易产生疲劳破坏; (3)热辗时因多采用外部水冷,模具中心与表面温 差较大,可产生较大热应力而使模具产生裂纹或断裂。 2.模具材料: (1)热辗模具材料 (2)冷辗模具材料 根据辗压温度不同,摆辗分为热辗、冷辗和温辗, 三种方式模具设计的基本原则是相同的,只是在热辗 和温辗时要考虑热膨胀系数。
挤压件正挤工艺模具毕业设计
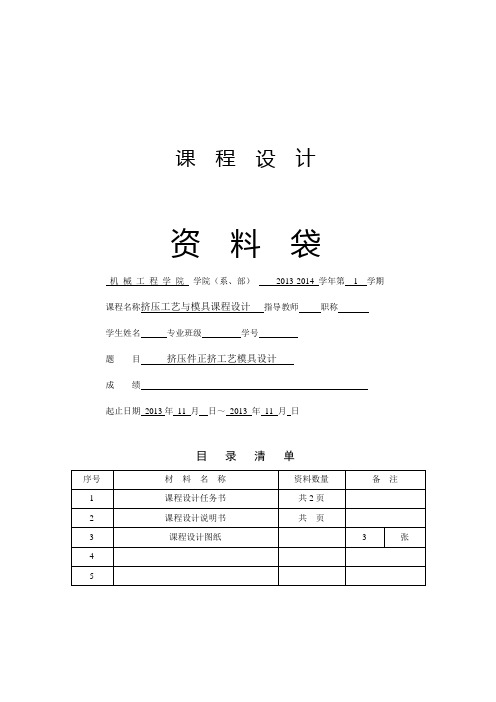
课程设计资料袋机械工程学院学院(系、部)2013-2014 学年第 1 学期课程名称挤压工艺与模具课程设计指导教师职称学生姓名专业班级学号题目挤压件正挤工艺模具设计成绩起止日期2013年11 月日~2013 年11 月日目录清单月日课程设计任务书2013 —2014学年第1 学期机械工程学院(系、部)专业班课程名称:挤压工艺与模具课程设计设计题目:挤压件正挤工艺模具设计完成期限:自2013 年11 月日至2013 年11 月日共1.5 周指导教师:2013 年11月日系(教研室)主任:2013 年11月日机械设计课程设计设计说明书挤压件正挤工艺模具设计起止日期:2013年11月日至2013年11 月4日学生姓名班级学号成绩指导教师(签字)机械工程学院(部)2013年12月日目录第一章零件的工艺分析 (3)第二章零件工艺方案的选定 (5)第三章工序设计 (6)3.1 毛坯的制备 (6)3.2 毛坯的软化处理 (6)3.3 毛坯表面处理与润滑 (7)3.4 毛坯尺寸的确定 (7)第四章工艺计算 (8)4.1 许用变形程度计算 (8)4.2 挤压力的计算 (8)4.3 压力机的选择 (9)第五章冷挤压模具的机构设计 (10)5.1 凹模的设计 (10)5.2 凸模的设计 (11)5.3 模具其他部分的设计 (12)5.4 模具的固定 (13)第六章模具装配及工作原理 (14)6.1 加工要求 (14)6.2 模具装配图及装配过程 (15)6.3 加工路线 (16)第七章工作零件材料的要求与使用注意事项 (17)第八章总结心得 (18)第九章参考文献 (19)第一章零件的工艺性分析冷挤压工艺设计是在确定挤压件形状、尺寸、精度和材料之后,这首设计模具之前的一个阶段。
在此阶段要拟定之间的冷挤压加工工艺和有关的工艺顺序和数量,并研究如何具体实现符合生产要求的零件质量控制、经济性等有关问题。
近年来,在机械制造工艺方面广泛应用采用冷挤压先进技术,取得了显著的成就,与其他制造工艺方法相比,冷挤压工艺已成为金属变形中最先进的工艺之一,在技术和经济上都有很多的显著优点。
挤压件的工艺流程及模具设计ppt课件

*100%=25% 挤压比G=A0/A1=100²/50²=4 b. 反挤压杯型部分 断面缩减率ɛF=[(d0²-d1²)/d0²]*
100%=[(100²-70²)/100²]* 100%=51% 挤压比G=A0/A1=100²/(100²-70²)≈1.96
2.3 毛坯的选择及处理
为了提高毛坯的塑性、降低其硬度和 变形抗力,冷挤压加工前的毛坯需进 行软化退火处理,其退火工艺规范是 毛坯加热760℃~780℃,保温lh,炉 冷到650℃~670℃,保温lh,再炉冷 到室温。20钢毛坯经退火后的硬度为 110HBW。毛坯表面处理采用磷化处
理和皂化润滑处理。
部分 单位挤压力P0.2%C=1010*ln(1/(1-ɛF))
+240=530.56Mpa b.反挤压部分 单位挤压力P=(0.875+1.25C)
*{1410+445*ln【1/(1ɛF)】}=1943.4Mpa
Page 8
4. 挤压模具的 设计
Page 5
2.2 挤压件的力学性能 根据上述计算,通过查阅资料得到20钢正
挤压杆件挤压后的条件屈服强度 σ0.2=590Mpa 抗拉强度σb=600Mpa 硬度 HBW=210 反挤压杯型部分σ0.2=650Mpa 可知许用变形程度在模具材料单位挤压力 的限制范围内。
Page 6
Page 3
1.2 挤压方法的选择 分析了解正挤压和反挤压的类
型及金属流动的方向,可以知道毛 坯一部分金属的流动方向与凸模的 运动方向相同,另一部分金属的流 动方向与凸模运动的方向相反,即 符合复合挤压的类型,而这正是这 类零件——杯杆类。
挤压模具设计课程设计

挤压模具设计课程设计一、课程目标知识目标:1. 理解并掌握挤压模具设计的基本原理和概念;2. 学习并掌握挤压模具结构及其各部分功能;3. 了解挤压模具设计的相关技术要求和行业标准。
技能目标:1. 能够运用CAD软件进行挤压模具的设计与绘制;2. 能够分析并解决挤压模具设计过程中遇到的问题;3. 能够根据实际需求,提出合理的挤压模具设计方案。
情感态度价值观目标:1. 培养学生严谨的科学态度,注重实践与创新;2. 培养学生团队协作精神,提高沟通与表达能力;3. 增强学生对我国模具行业的认同感,激发学生为民族工业发展贡献力量的责任感。
课程性质分析:本课程为专业核心课程,旨在培养学生的挤压模具设计能力,提高学生在实际工程中的应用能力。
学生特点分析:学生已具备一定的机械基础知识,具有较强的学习能力和动手能力,但缺乏实际工程经验。
教学要求:1. 结合课本内容,注重理论与实践相结合;2. 采用项目驱动教学,提高学生的实践操作能力;3. 加强课堂互动,培养学生的创新思维和解决问题的能力;4. 注重过程评价,全面评估学生的学习成果。
二、教学内容1. 挤压模具设计基本原理- 挤压成型原理- 模具设计的基本流程- 模具材料的选用原则2. 挤压模具结构及功能- 模具各部分的名称及作用- 常见挤压模具类型及特点- 模具结构对制品质量的影响3. 挤压模具设计技术要求与标准- 相关国家标准和行业标准- 模具设计中的关键技术参数- 模具设计的安全性与可靠性4. CAD软件在挤压模具设计中的应用- CAD软件的基本操作- 模具三维建模与绘制- 模具设计参数化与仿真分析5. 挤压模具设计实例分析- 实际工程案例介绍- 模具设计过程中的问题与解决方法- 模具设计方案优化6. 挤压模具设计实践- 模具设计项目的实施- 设计图纸的绘制与审查- 模具样品制作与测试教学内容安排与进度:本课程共分为六个部分,每个部分按照2-4个课时进行教学。
挤压工艺及模具设计

挤压工艺及模具设计
《挤压工艺及模具设计》
嘿呀,说起挤压工艺及模具设计,这可真是个有意思的事儿呢!
就拿我之前看到的一个事儿来说吧。
有一次我去一个小工厂参观,那里面正在进行金属挤压的工作。
我就眼睁睁地看着一块普普通通的金属材料,被放到了一个奇奇怪怪的模具里。
然后呀,机器就开始嗡嗡作响,就好像在用力地喊着口号似的。
随着机器的运作,那块金属就慢慢地被挤压变形啦!哇哦,就看着它一点点地变成了一个有着特定形状的东西,简直太神奇啦!我当时就在想啊,这模具可真是厉害,就像一个魔法师一样,能把平平无奇的金属变成各种各样有用的玩意儿。
那个模具啊,上面有着各种纹路和形状,真的是超级精细呢!我凑近了仔细瞧,感觉那上面的每一条线、每一个弧度都是经过精心设计的。
工人们熟练地操作着,他们对这些模具就好像对自己的宝贝一样熟悉。
他们知道怎么调整,怎么让挤压出来的东西达到最好的效果。
你说这挤压工艺和模具设计是不是很有趣呀!就这么一个小小的模具,却有着大大的能量,能让那些普通的材料焕发出新的光彩。
哎呀呀,真的是太神奇啦!以后再看到那些通过挤压工艺制造出来的东西,我肯定会想起这次有趣的经历,想起那神奇的模具和厉害的挤压工艺呢!这就是挤压工艺及模具设计的魅力呀,嘿嘿!。
卧式挤压机挤压模具结构设计
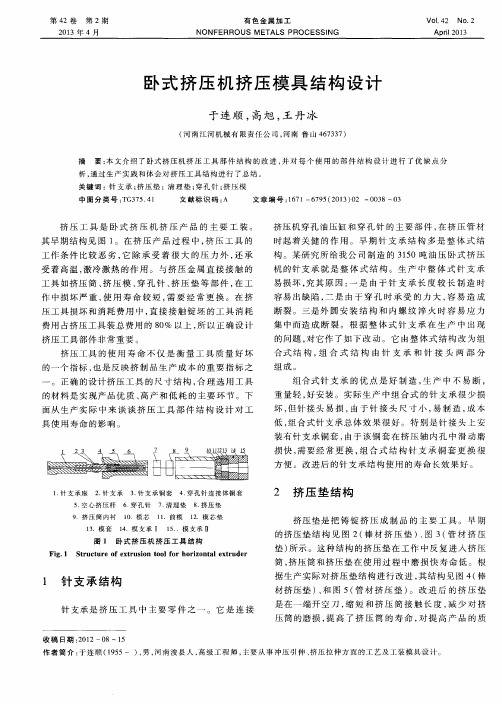
易损 坏 , 究其 原 因 : 一 是 由于 针 支 承 长度 较 长 制 造 时
容易 出缺 陷 , 二 是 由 于穿 孔 时 承 受 的力 大 , 容 易 造 成 断裂 。三是 外 圆安 装 结 构 和 内螺 纹 淬 火 时 容 易 应 力 集 中而造 成 断 裂 。根 据 整 体 式 针 支 承 在 生 产 中 出现
Fi g . 1 S t r u c t u r e o f e x t r u s i o n t o o l f o r h o r i z o n t a l e x t r u d e r
1 针 支 承 结 构
针 支承 是挤 压 工具 中 主 要 零 件 之 一 。它 是 连 接
挤 压机 穿孔 油压缸 和 穿孔 针 的 主要 部件 , 在 挤 压 管 材
其早期 结 构见 图 1 。在 挤 压 产 品过 程 中 , 挤 压 工 具 的 工作 条件 比较 恶 劣 , 它 除 承受 着 很 大 的 压力 外 , 还 承
时起着 关健 的作 用 。早 期 针 支 承结 构 多 是 整体 式 结 构 。某研究 所 给我公 司 制 造 的 3 1 5 0吨 油压 卧式 挤 压 机 的针 支 承就 是 整 体 式 结 构 。生产 中整 体 式 针 支 承
第 2期
有 色 金 属 加 工
3 9
第4 2卷
第 2期
有 色 金 属 加 工
NONFERROUS ME TAL S PROCE SSI NG
VOI . 4 Apr i l 2 01 3
卧 式 挤 压 机 挤 压 模 具 结 构 设 计
于连 顺 , 高旭 , 王丹 冰
( 河 南 江 河 机 械 有 限责 任 公 司 , 河南 鲁 山 4 6 7 3 3 7 )
挤压铸造模具的设计及工艺研究-武汉理工大学2012.06.21
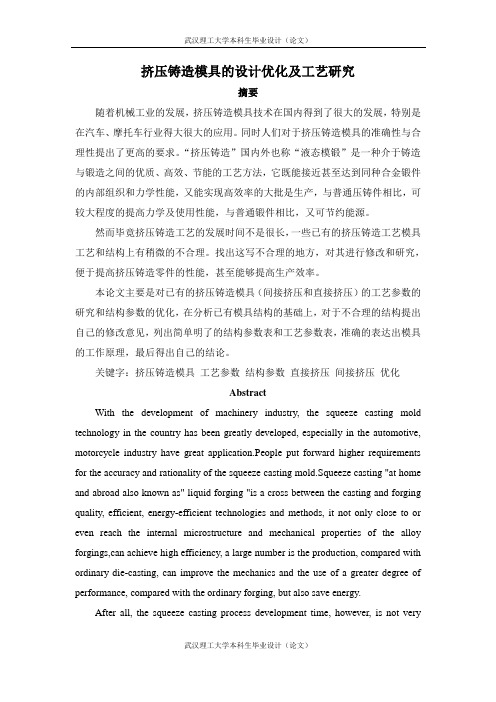
挤压铸造模具的设计优化及工艺研究摘要随着机械工业的发展,挤压铸造模具技术在国内得到了很大的发展,特别是在汽车、摩托车行业得大很大的应用。
同时人们对于挤压铸造模具的准确性与合理性提出了更高的要求。
“挤压铸造”国内外也称“液态模锻”是一种介于铸造与锻造之间的优质、高效、节能的工艺方法,它既能接近甚至达到同种合金锻件的内部组织和力学性能,又能实现高效率的大批是生产,与普通压铸件相比,可较大程度的提高力学及使用性能,与普通锻件相比,又可节约能源。
然而毕竟挤压铸造工艺的发展时间不是很长,一些已有的挤压铸造工艺模具工艺和结构上有稍微的不合理。
找出这写不合理的地方,对其进行修改和研究,便于提高挤压铸造零件的性能,甚至能够提高生产效率。
本论文主要是对已有的挤压铸造模具(间接挤压和直接挤压)的工艺参数的研究和结构参数的优化,在分析已有模具结构的基础上,对于不合理的结构提出自己的修改意见,列出简单明了的结构参数表和工艺参数表,准确的表达出模具的工作原理,最后得出自己的结论。
关键字:挤压铸造模具工艺参数结构参数直接挤压间接挤压优化AbstractWith the development of machinery industry, the squeeze casting mold technology in the country has been greatly developed, especially in the automotive, motorcycle industry have great application.People put forward higher requirements for the accuracy and rationality of the squeeze casting mold.Squeeze casting "at home and abroad also known as" liquid forging "is a cross between the casting and forging quality, efficient, energy-efficient technologies and methods, it not only close to or even reach the internal microstructure and mechanical properties of the alloy forgings,can achieve high efficiency, a large number is the production, compared with ordinary die-casting, can improve the mechanics and the use of a greater degree of performance, compared with the ordinary forging, but also save energy.After all, the squeeze casting process development time, however, is not verylong, have squeezed a little unreasonable in the casting process mold processes and structures.Find out where this write unreasonable, modify and research, and easy to improve the performance of squeeze casting parts, or even be able to improve production efficiency.In this paper, the existing squeeze casting mold (indirect extrusion and direct extrusion) the optimization of process parameters and structural parameters, based on analysis of existing mold structure, unreasonable structureamedments, list of simple structural parameter table and the process parameters table, an accurate expression of the working principle of the mold, and finally draw their own conclusions.Keywords: squeeze casting mold, process parameters, structural parameters, direct extrusion , indirect extrusion第一章绪论1.1研究目的及其意义挤压铸造(squeeze casting)是对铸型型腔中的液态或半液态的金属施加较高的机械压力,使其成型凝固,从而获得铸件的一种铸造方法,根据挤压铸造时合金液的流动状况及挤压铸造力的形式,挤压铸造可以分为直接挤压铸造(direct squeeze casting)和间接挤压铸造(indirect squeeze casting)两种基本形式。
挤压铸造工艺的模拟与模具设计

挤压铸造工艺的模拟与模具设计铸造工艺一直是金属制造领域中的重要环节之一。
而其中的挤压铸造工艺,同样在不同行业中发挥着重要的作用。
挤压铸造工艺通过将熔融金属材料以高压注入模具中,利用其充填模具的特性,实现金属制品的快速制造。
然而,想要实现高质量的挤压铸造产品,必须进行模拟与模具设计,以确保制造过程的可行性和产品质量的稳定性。
首先,挤压铸造工艺的模拟是一个必不可少的环节。
通过模拟软件,我们可以在计算机上模拟出整个铸造过程中的各个环节,包括模具充填、凝固过程和铸件缺陷等。
通过模拟,我们可以根据模型的几何形状和材料特性,预测铸件的充填情况和凝固过程,并检测出可能存在的缺陷,如气孔、夹杂等。
模拟还可以帮助优化铸件的结构设计,提高产品的性能和质量。
通过不断调整模拟参数,我们可以得到最佳的铸造参数,以确保模具充填完全、凝固均匀,从而生产出理想的挤压铸造产品。
其次,模具设计是挤压铸造工艺中不可或缺的一环。
模具的设计直接影响到挤压铸造产品的质量和生产效率。
在模具设计中,首先需要根据产品的几何形状和尺寸要求,确定模具的整体结构和尺寸。
模具的结构应该合理,以便于材料的注入和冷却,并保证充填的均匀性。
模具的尺寸应根据产品的缩脱率和凝固收缩率来确定,以确保产品的尺寸稳定性。
其次,还需要考虑模具的材料选择和表面处理。
模具应具备足够的强度和刚度,以承受挤压铸造过程中的高压和剧烈变形。
模具表面应进行适当的处理,以提高产品的表面质量和降低摩擦阻力。
最后,还需要考虑模具的制造工艺和使用寿命。
模具应通过适当的制造工艺和材料热处理,以确保其具有足够的耐磨性和使用寿命。
除了模拟和模具设计外,挤压铸造工艺中还需要考虑其他一些因素。
例如,熔融金属的温度和物性参数对于铸件的质量有重要影响。
通过调整熔融金属的温度和成分,可以改变其流动性和凝固过程,从而影响铸件的充填性和凝固缩孔的形成。
此外,还需要选择合适的润滑剂和涂料,以减少金属与模具的摩擦和氧化反应。
挤压设计与模具课程设计

挤压设计与模具课程设计一、课程目标知识目标:1. 让学生掌握挤压设计的基本原理,理解模具在挤压过程中的作用;2. 使学生了解不同类型的挤压模具及其特点,并能结合实际需求选择合适的模具;3. 引导学生掌握挤压工艺参数对产品质量的影响,能够优化挤压工艺。
技能目标:1. 培养学生运用CAD软件进行挤压模具设计的能力,提高设计效率;2. 培养学生运用CAE软件对挤压过程进行模拟分析,优化模具结构;3. 提高学生实际操作能力,能够参与简单的挤压模具组装和调试。
情感态度价值观目标:1. 培养学生对挤压设计与模具制造的热爱,激发学生探究新技术的兴趣;2. 培养学生严谨的工作态度,提高团队合作意识,增强解决实际问题的自信心;3. 引导学生关注我国挤压模具产业的发展,树立为国家和企业贡献力量的责任意识。
课程性质:本课程为专业实践课,旨在提高学生对挤压设计与模具制造的理论知识和实践技能。
学生特点:学生具备一定的机械基础知识和动手能力,对新技术充满好奇。
教学要求:结合理论知识与实践操作,注重培养学生的实际应用能力和创新精神。
通过课程学习,使学生能够达到以上设定的知识、技能和情感态度价值观目标,为后续专业课程学习和未来职业发展打下坚实基础。
二、教学内容1. 挤压设计基本原理:包括金属塑性变形理论、挤压成形方法分类、挤压工艺参数对产品质量的影响等;教材章节:第1章 挤压成形原理2. 挤压模具结构与设计:介绍不同类型挤压模具的结构特点、设计方法和注意事项;教材章节:第2章 挤压模具设计3. 挤压模具材料及热处理:分析挤压模具材料的选用原则、热处理工艺及其对模具性能的影响;教材章节:第3章 挤压模具材料及热处理4. 挤压模具CAD/CAE技术:讲解CAD软件在挤压模具设计中的应用,以及CAE软件对挤压过程进行模拟分析的方法;教材章节:第4章 挤压模具CAD/CAE技术5. 挤压模具制造与装配:介绍挤压模具的加工工艺、装配方法及调试技巧;教材章节:第5章 挤压模具制造与装配6. 挤压模具应用实例:分析典型挤压模具在实际生产中的应用案例,提高学生的实际操作能力;教材章节:第6章 挤压模具应用实例教学内容安排与进度:第1-2周:挤压设计基本原理及挤压成形方法;第3-4周:挤压模具结构与设计;第5-6周:挤压模具材料及热处理;第7-8周:挤压模具CAD/CAE技术;第9-10周:挤压模具制造与装配;第11-12周:挤压模具应用实例分析及实践操作。
金属挤压液压机控制系统仿真设计说明书
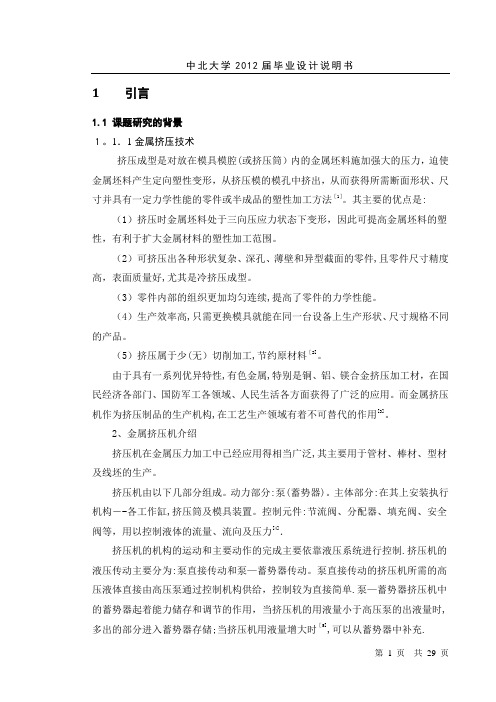
1引言1.1 课题研究的背景1。
1.1金属挤压技术挤压成型是对放在模具模腔(或挤压筒)内的金属坯料施加强大的压力,迫使金属坯料产生定向塑性变形,从挤压模的模孔中挤出,从而获得所需断面形状、尺寸并具有一定力学性能的零件或半成品的塑性加工方法[1]。
其主要的优点是: (1)挤压时金属坯料处于三向压应力状态下变形,因此可提高金属坯料的塑性,有利于扩大金属材料的塑性加工范围。
(2)可挤压出各种形状复杂、深孔、薄壁和异型截面的零件,且零件尺寸精度高,表面质量好,尤其是冷挤压成型。
(3)零件内部的组织更加均匀连续,提高了零件的力学性能。
(4)生产效率高,只需更换模具就能在同一台设备上生产形状、尺寸规格不同的产品。
(5)挤压属于少(无)切削加工,节约原材料[2]。
由于具有一系列优异特性,有色金属,特别是铜、铝、镁合金挤压加工材,在国民经济各部门、国防军工各领域、人民生活各方面获得了广泛的应用。
而金属挤压机作为挤压制品的生产机构,在工艺生产领域有着不可替代的作用[3]。
2、金属挤压机介绍挤压机在金属压力加工中已经应用得相当广泛,其主要用于管材、棒材、型材及线坯的生产。
挤压机由以下几部分组成。
动力部分:泵(蓄势器)。
主体部分:在其上安装执行机构--各工作缸,挤压筒及模具装置。
控制元件:节流阀、分配器、填充阀、安全阀等,用以控制液体的流量、流向及压力[4].挤压机的机构的运动和主要动作的完成主要依靠液压系统进行控制.挤压机的液压传动主要分为:泵直接传动和泵—蓄势器传动。
泵直接传动的挤压机所需的高压液体直接由高压泵通过控制机构供给,控制较为直接简单.泵—蓄势器挤压机中的蓄势器起着能力储存和调节的作用,当挤压机的用液量小于高压泵的出液量时,多出的部分进入蓄势器存储;当挤压机用液量增大时[5],可以从蓄势器中补充.1.1。
2国内外挤压机发展现状由于挤压机的整机结构方面,已经比较成熟,国外挤压机技术发展主要体现在电液控制系统方面.在电气控制系统方面,挤压机可分为三大类[6]:(1)继电器控制控制系统以继电器为主控元件,这种控制方式是电气控制中发展最早的一种,是延续了几十年的传统控制方式,电路结构简单、技术要求不高、成本较低、控制功能简单、适应性不强[7].其适用于单机工作、加工产品精度要求不高的大批量生产(如餐具、厨具产品等),也可组成简单的生产线[8],但由于电路的限制,压机工作稳定性、柔性差。
挤压模具设计与制造(改)

•图1-7 轴对称型材模孔的配置
2)对只有一个对称轴的型材,并且缘板厚度相差不大,其重心 要 与模子中心重合 ,模孔的布置如图1-8所示。
•
图1-8 对称于一个坐标轴而缘板厚度比不大的型材模模孔的布置
3)虽然有一个对称轴,但壁厚差很大和不对称的型材,应使 型材的重心,相对于模子中心作一定距离的偏移,应尽可能 地使难于流动的壁厚较薄的部位靠近模子中心,尽量使金属 在变形时的单位静压力相等(图1-9)。
此外,在确定模孔数目的时,还应考虑模子的强度。为 保证制品性能均匀,可按下式确定:
n
式中
Fo
F1
n——模孔数 Fo——挤压筒断面积 F1——一个制品的断面积 ——平均延伸系数,据挤压机吨位,挤压筒 大小和合金变形抗力大小,一般取 =10~50
(2)排列原则: 多孔模挤压,金属流动比单孔模均匀 ,但若排列不当,使挤压出的制品长短 不一,增加几何废料。(排列在同一个 同心圆上) 例:如图1-5 多孔模模孔的布置情况
(5)入口圆角 r入 模子的入口圆角是指被挤压金属进入定径带的部分, 即模子工作端面与定径带形成的端面角。可防止低塑性合 金产生表面裂纹,减小金属在流入定径带时的非接触变形 ,减少模子棱角的压塌变形。但增大了接触摩擦面积,挤 压力增高。 模子入口圆角值的选取与金属的强度、挤压温度和制 品尺寸、模子结构等有关。铝及铝合金的入口圆角 r入 =0.4~0.75mm;铜的入口圆角(T H为2~5mm,B为 4~8mm)。 (6)外形尺寸(具有通用性,已经基本系列化)( P277-模具外形标准尺寸表)
模孔太靠近边缘引起外侧裂纹
模孔太靠近中心引起内侧裂纹
影响各孔流速主要有两个因素 1、各孔金属供应体积大小,显然,供应体积大,挤出制品 就长; 2、各孔所处位置的阻力,显然,阻力大,流速慢,制品短 ;阻力小,流速快,制品长。 所以为使金属流速均匀,应将各模孔布置在一同心圆上,并 使相互间的孔距相等。同心圆大小按下列经验公式计算。
挤压工艺及模具实验指导书
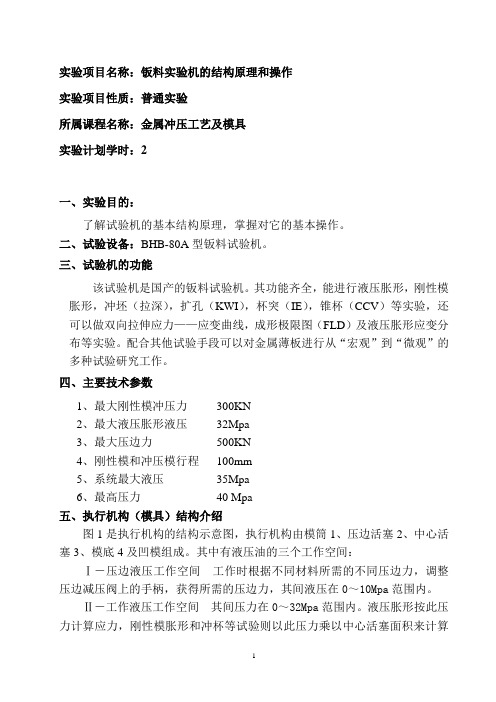
实验项目名称:钣料实验机的结构原理和操作实验项目性质:普通实验所属课程名称:金属冲压工艺及模具实验计划学时:2一、实验目的:了解试验机的基本结构原理,掌握对它的基本操作。
二、试验设备:BHB-80A型钣料试验机。
三、试验机的功能该试验机是国产的钣料试验机。
其功能齐全,能进行液压胀形,刚性模胀形,冲坯(拉深),扩孔(KWI),杯突(IE),锥杯(CCV)等实验,还可以做双向拉伸应力——应变曲线,成形极限图(FLD)及液压胀形应变分布等实验。
配合其他试验手段可以对金属薄板进行从“宏观”到“微观”的多种试验研究工作。
四、主要技术参数1、最大刚性模冲压力300KN2、最大液压胀形液压32Mpa3、最大压边力500KN4、刚性模和冲压模行程100mm5、系统最大液压35Mpa6、最高压力40 Mpa五、执行机构(模具)结构介绍图1是执行机构的结构示意图,执行机构由模筒1、压边活塞2、中心活塞3、模底4及凹模组成。
其中有液压油的三个工作空间:Ⅰ-压边液压工作空间工作时根据不同材料所需的不同压边力,调整压边减压阀上的手柄,获得所需的压边力,其间液压在0~10Mpa范围内。
Ⅱ-工作液压工作空间其间压力在0~32Mpa范围内。
液压胀形按此压力计算应力,刚性模胀形和冲杯等试验则以此压力乘以中心活塞面积来计算冲压力,中心活塞的底面积为95cm2。
Ⅲ-液压胀形、刚性模胀形、冲杯等试验的工作空间。
液压胀形时可用螺丝刀拧开中心活塞(旋2~4圈),液压油即从Ⅱ进入Ⅲ腔进行液压胀形。
此时应将刚性半球凸模卸下放置起来。
在进行液压胀形或刚性模胀形时,凹模座6应装上如图所示的带梗凹模7。
在进行冲杯等试验时,则应换上相应的标准凹模,并在压边活塞上放上平滑的压边圈。
在装卸模具时,千万注意不要损伤胀形凹模7的凸梗,否则将失去其油封功能。
凹模升降机构由凹模底座提升盘8,悬臂9、升降动作筒11及定位销等组成。
在凹模底6的齿凸与模筒1的齿凹相对时,可将凹模底提起和放入。
- 1、下载文档前请自行甄别文档内容的完整性,平台不提供额外的编辑、内容补充、找答案等附加服务。
- 2、"仅部分预览"的文档,不可在线预览部分如存在完整性等问题,可反馈申请退款(可完整预览的文档不适用该条件!)。
- 3、如文档侵犯您的权益,请联系客服反馈,我们会尽快为您处理(人工客服工作时间:9:00-18:30)。
•挤压模技术•挤压模技术:压力缸的摆辗挤压工艺及模具设计洪慎章上海交通大学塑性成形技术与装备研究院(上海200030)【摘要】介绍了各种压力缸及钢瓶的先进成形技术,分析了摆辗挤压工艺的成形原理,列举了热摆辗挤压工艺制造实例。
列出了压力缸冷的热摆辗挤压工艺与金属切削工艺的经济效果比较。
关键词:压力缸;钢瓶;成形原理;摆辗挤压工艺中图分类号:TG372文献标识码:BDOI:10.12147/ki.1671-350&2019.03.018Orbital-Extruding Technology and Die Design of Pressure Cylinder [Abstract]This paper is narrated a progressive forming technology of the various pressure cylinders ancl the steel cylinders.lt is introduced the forming principles of the orbital-extruding technology.It is listed manufacturing example of a heat orbital-extruding technology.lt is listed the comparison of economics effects between the heat orbital-extruding process and metal cutting process.Key words:pressure cylinder;steel cylinder;forming principle;orbital-extruding technologyI引言各类机械设备,采矿掘煤机械,装备上的各种液压缸,气缸(以下简称压力缸)及高压容器(钢瓶),结构形式多样,用途各有不同,它们的共同点主要是工作时承受内胀力,大多是采用高强度低合金结构钢,中碳优质结构钢或优质高强度有色金属材料,如30CrMnSi、40Cr、40Mn2丄C4等制造的。
压力缸的传统加工方法是金属切削,一般都按零件的最大外形尺寸加工到所需的尺寸精度,这种方法的缺点是加工周期长,电力消耗大,工时消耗多,生产效率低,材料利用率低,成本高。
用压力加工技术来取代金属切削加工,特别是替换高粗糙度值及高精密的机械加工,是当代加工技术发展的目标之一,国内、外都在不断地进行这些方面的研究工作。
除了国内已有的热挤压工艺和强力旋压工艺以外,现俄罗斯已制成功一种最新颖的压力加工方法——摆辗挤压工艺,并已用于生产。
2摆辗挤压工艺的成形原理摆辗挤压工艺是挤压与摆辗两种工艺相结的一种新技术。
它可专门用来制造厚壁筒压力缸零件,与强力旋压工艺所制造的产品类似,但成形原理有所区别。
如图1所示.摆辗挤压成形主要是挤压凸模与摆辗凹模动作的合理配合。
摆辗凹模的轴线相对挤压凸模的轴线成一角度,在凸模进行挤压时,摆辗凹模也绕自身的轴心旋转,使管状坯料完成变薄挤压变形。
可见,摆辗挤压装置的动作原理与摆动辗压装置相似,但由于凹模摆动动作的配合,由管状坯料挤成缸体实际上是连续局部变形的结果。
一般,摆辗凹模的最佳圆锥角为0.25~0.35弧度(1弧度= 57.29578°),可使摆辗挤压的变形力达到最小值。
目前,唯有俄罗斯(原苏联)有这种新技术,只要利用通用的立式液压机加上一副摆辗挤压装置就可以实现这一工艺。
而且,制造压力缸的摆辗挤压工艺比强力旋压工艺优越。
首先它可以节省价格昂贵的《模具制造》2019年第3期•69••挤压模技术•旋压设备投资;特别是可以生产高精度,低表面粗糙 度值的摆辗挤压件。
一般,外径公差达±0.3mm,内径公差达±0.1mm,长度公差达±5mm,外表面粗糙度值 1.6pm,内表面粗糙度值为0.32pm,直线度扁差为每摆辗凹模设计。
摆辗凹模最佳圆锥角选为0.30弧度,材料为4Cr5W2SiV 合金模具钢,热处理硬度为52~54HRC O(3) 加热温度的选择。
为了减小变形抗力,对高碳合金结构钢可选用温 变形,加热温度为800七~900七。
(4) 模具加工的技术要求。
为了保证制件的质量,除了合理设计模具结构及 选用最佳的模具材料和热处理工艺以外,更重要的是模具主要零件(挤压凸模和摆辗凹模)的加工技术要 求。
因此对这两个零件的加工技术要求都较高,如同 轴度,平行度及垂直度等,否则就会产生制件的各种 缺陷,具体的加工技术要求与其形状及尺寸有关。
(5) 挤压凸模。
其形状及尺寸如图3所示,并标出加工技术要求。
(6) 摆辗凹模。
其形状及尺寸如图4所示,并标出加工技术要求。
0.02A 丄0.02B3压力缸摆辗挤压工艺摆辗挤压工艺按金属塑性变形温度有3种:冷变 形、温变形及热变形,根据压力缸及容器瓶(医用)的 需求场所。
铲车上的压力缸,形状及尺寸如图2所示,材料为40Cr 钢。
图2压力缸5///////////////^st3R2/.15,///////// Z//Z/635(1) 毛坯形状及尺寸的计算。
压力缸毛坯的尺寸是根据零件的体积计算,其外径按零件最大的外径选用,得0150x250mm 。
(2) 模具设计。
挤压凸模设计。
凸模外径尺寸应与压力缸内孔尺寸相同。
材料为W6Mo5Cr4V2,热处理硬度,50 ~52HRC 。
◎0.02C\R2.0^Ral.6图3挤压凸模的技术要求图4摆辗凹模的技术要求• 70 •《模具制造》2019年第3期•模具制造技术•;模具制造技术j三维扫描仪壳体加工工艺研究杨伟伟,李德宏中国电子科技集团公司第二十七研究所(河南郑州450047)【摘要】三维扫描仪采用非接触的测量方式获取三维数据并广泛应用于船舶设计、军事分析、模具制造等诸多领域。
壳体是三维扫描仪中的关键零部件之一,通过分析壳体的结构特点,首先提出基准转换的加工工艺方案,并给出测量结果。
结果表明,采用此方案加工的壳体未能达到精度要求。
通过分析超差的原因,进而提出预留夹头的加工工艺方案,由测量结果可知,采用此方案能够加工出满足设计要求的壳体。
关键词:三维扫描仪;壳体;工艺方案中图分类号:TG659文献标识码:BDOI:10.12147/ki.l671-3508.2019.03.019Processing Technology of the Shell in the3-D Scanner[Abstract]The3—d scanner uses non-contact measuring method to obtain the3-d data.It isused proverbially in ship design and military analysis and die&mold manufacturing and so on.The shell is a key part of3-d scanner.The structure of shell is analyzed.The process scheme ofdatum transformation is presented.The result is listed.It shows that the requirement is notsatisfied using this method.The reason of inconformity is analyzed.Then another process schemeof persisting tong hold is presented.It shows that the shell meeting the design requirements isprocessed using this method.Key words:3-D scanner;shell;process scheme1引言性,采用非接触主动测量方式直接获取高精度三维数三维扫描测量技术克服了传统测量技术的局限据,能够对任意物体进行扫描.且没有白天和黑夜的cc e ee€c cc cccccc cccc cc c-E-e g-cc cc c c c c-&e-c€-&c cc cc cccccc4技术经济效果压力缸新旧两种成形工艺的技术经济效果如表1所示。
材料利用率从21%增加到59%,机械加工量从1.100h减少到750h.可见.明显地降低了制件的制造成本。
表1压力缸热摆辗挤压工艺与金属切削工艺的经济效果比较项目切削工艺热摆辗丁艺毛坯尺寸,mm圆柱坯如50x635圆柱坯4)150x250零件重量,kg19.019.0毛坯重量・kg8&0434.66材料利用率,%2159机械加工量,h 1.1007505结束语在当今机械化、自动化、智能化的扩大应用下,其中各种液压及气压驱动结构日益增多,必需要促进各种液压缸及气缸的扩大生产。
先进的摆辗挤压工艺可替代落后的金属切削加工工艺,省去投资昂贵的旋压设备。
参考文献|1]孙凤勤.模具制造「.艺与设备[M].北京:机械工业出版社.1999.[2]张水忠.挤压丁:艺及模具设计[M].北京:化学工业出版社,2009.作者简介:洪慎章,男,1932年生,教授,长期从事零件精密及净成形工艺技术,模具设计等工作,现已退休。
(收稿日期:2018-12-04)<S>《模具制造》2019年第3期•71•。