DFMEA--白车身
新员工培训DFMEA介绍
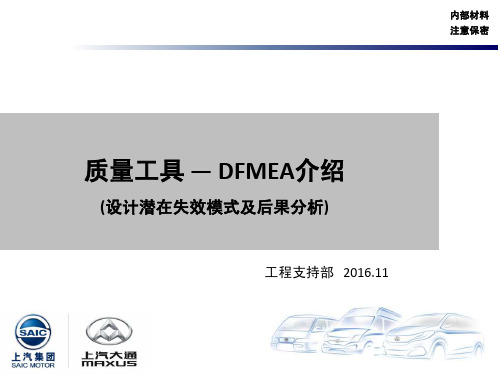
识别与分析零件相关的周边系统。 周围的系统与零件功能相关,后续作为影响因素进行分析。
方法和资源: 方块图 Block Diagram 参数图(P-图) Parameter Diagram 关系矩阵分析 BOM清单 接口图、示意图等
内部材料 注意保密
2014-5
26
二. DFMEA策划及准备
了解这些顾客,有助于更加充分地定义功能范围。
内部材料 注意保密
2014-5
18
一. FMEA发展和介绍
DFMEA在APQP中的角色
设计相关:PDT协同
历史信息 失效记录
设计过程:DRE/供应商负责
价值工程 价值分析
DFMEA
内部材料 注意保密
基于可制造性/ 装配性/维修性
的设计
设计验证计划 ADV
功能
潜在失效模式
严 级 潜在失效 频
潜在失效后果 重 别 起因/机理 度
度
现行设计控制
预防
探测
风
探险
测顺
度序
数
建议措施
措施效果
责任和目标 完成日期
采取的
严 重
频
探 测
R P
措施 度 度 度 N
1
2
3 4 567
8
9
2014-5
10
8
一. FMEA发展和介绍 DFMEA简介 — 5W
What 什么是DFMEA?
内部材料 注意保密
质量工具 — DFMEA介绍
(设计潜在失效模式及后果分析)
工程支持部 2016.11
第一部分:FMEA发展和介绍 第二部分:DFMEA策划及准备 第三部分:DFMEA分析和实施
上海交运SGM白车身零件工装供应商要求通则
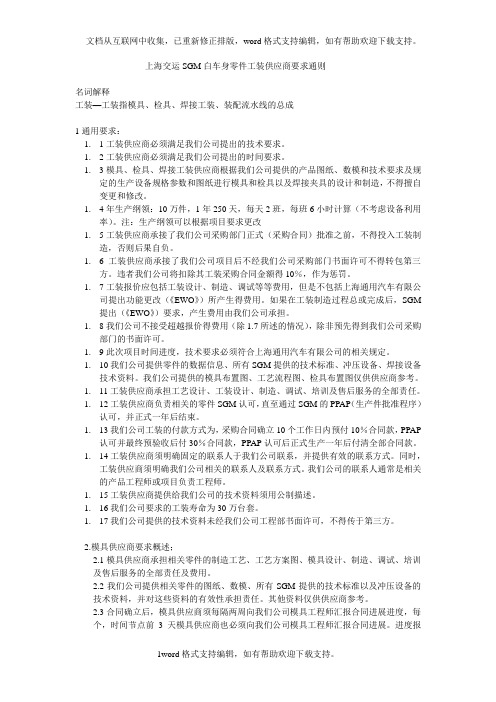
上海交运SGM白车身零件工装供应商要求通则名词解释工装—工装指模具、检具、焊接工装、装配流水线的总成1通用要求:1.1工装供应商必须满足我们公司提出的技术要求。
1.2工装供应商必须满足我们公司提出的时间要求。
1.3模具、检具、焊接工装供应商根据我们公司提供的产品图纸、数模和技术要求及规定的生产设备规格参数和图纸进行模具和检具以及焊接夹具的设计和制造,不得擅自变更和修改。
1.4年生产纲领:10万件,1年250天,每天2班,每班6小时计算(不考虑设备利用率)。
注:生产纲领可以根据项目要求更改1.5工装供应商承接了我们公司采购部门正式(采购合同)批准之前,不得投入工装制造,否则后果自负。
1.6工装供应商承接了我们公司项目后不经我们公司采购部门书面许可不得转包第三方。
违者我们公司将扣除其工装采购合同金额得10%,作为惩罚。
1.7工装报价应包括工装设计、制造、调试等等费用,但是不包括上海通用汽车有限公司提出功能更改(《EWO》)所产生得费用。
如果在工装制造过程总或完成后,SGM 提出(《EWO》)要求,产生费用由我们公司承担。
1.8我们公司不接受超越报价得费用(除1.7所述的情况),除非预先得到我们公司采购部门的书面许可。
1.9此次项目时间进度,技术要求必须符合上海通用汽车有限公司的相关规定。
1.10我们公司提供零件的数据信息、所有SGM提供的技术标准、冲压设备、焊接设备技术资料。
我们公司提供的模具布置图、工艺流程图、检具布置图仅供供应商参考。
1.11工装供应商承担工艺设计、工装设计、制造、调试、培训及售后服务的全部责任。
1.12工装供应商负责相关的零件SGM认可,直至通过SGM的PPAP(生产件批准程序)认可,并正式一年后结束。
1.13我们公司工装的付款方式为,采购合同确立10个工作日内预付10%合同款,PPAP认可并最终预验收后付30%合同款,PPAP认可后正式生产一年后付清全部合同款。
1.14工装供应商须明确固定的联系人于我们公司联系,并提供有效的联系方式。
汽车车身饰件DFMEA-前保险杠总成

探 测 度 D
风 险 顺 序
3
耐老化试验验证
3
36
参考成熟结构,固
4
保险杠与前灯,翼子板配合 定点选择精度可以 结构设计不合理,精度不够 保证的位置和零部
2
截面校核、快速成 型件装车验证评审
1
8
件
审核/日期:
批准/日期:
FMEA编 号:
共 1页
第 1页
措施执行后的结果
职责及目
标完成日 期
采取的措施 及完成日期
严 重 度 S
频 度 O
严
重 度 数
分 类
失效潜在原因 /机理
S
4
控制预防 (规范)
频 度 控制探测 (试 数 验) O
按照牌照大小要求 进行设计校核
2
设计校核
4
牌照安装孔心距偏大或者偏 小
按照牌照孔心距要 求设计牌照安装孔 并进行校核分析
2
设计校核
编制人 编制日期 修订日期
风
R险
探 测 度 D
外观
保险杠与发盖, 前大灯灯,翼子 板等周边部件间 隙均匀,面差一 致
前保凸出发盖翼子 板,与翼子板间隙面 差不均匀等等
前保险杠与周边部件间隙面 差难以保持稳定
编制/日期:
会签/日期:
5
背部安装结构,加强筋设计 不合理
前期设计工艺校 核,结构优化,工
艺优化
2
设计校核
3 30
4
材料选择不合理
参考成熟车型材料 选择
潜在失效模式及后果分析(DFMEA)
系统 子系统 零部件 车型/年型
项目
功能
要求
外饰系统 前保险杠系统 前保险杠本体总成
汽车电器DFMEA-电机控制器

系统
/
子系统
/
零部件
/
车型年/项
目
核心小组
潜在失效模式与影响分析
(设计FMEA)
性能/外观满足 客户要求,符 合安全性和法 律法规,易与 设计职责 生产装配。
关键日期
FMEA编号 共 1 页,第 1 页
编制人 FMEA日
期(原
项目 功能
要求
潜在失效模式
失效潜在影响
严重度 (S)
失效潜在原因
控制 预防
完成日期 采取的措施 严重度 发生度 探测度 完成日期
RPN
线路板设计
及关键元器
件选择
电压/电流参数
IGBT模块选型合 低,功率损耗
理
大,开关特性
影响控制器性能
6
选型不合理
重新选型,参考同 类产品设计
2
设计评审,元件 规格书参数
5
60
差,温升快
IGBT驱动芯片及 无隔离,驱动/关
电源选型合理
断能力差
4
48
求,接头符合防
水要求
接头不防水
影响控制器寿命 7
接头选型不合理
重新选型,调整机 壳接口设计
2
设计评审,样机 试装
4
56
控制器机壳
结构设计 机壳承受10KPa 压强不变形
抗压能力差
客户不满意退货
6
机壳材料选型不合 重新调整,参考同 理,壁厚设计太薄 类产品设计
3
机壳机械强度测 试
4
72
机壳防尘防水能 有效保护线路板
影响控制器性能
6
选型不合理
重新选型,参考同 类产品设计
2
设计评审,元件 规格书参数
各大主机厂整车开发流程解析(附:采购和主机厂打交道不可不知的英文缩写(通用篇))

各大主机厂整车开发流程解析(附:采购和主机厂打交道不可不知的英文缩写(通用篇))汽车(整车、零部件)的开发是相当复杂的项目工程,众所周知,项目的三要素:时间、质量与成本,那么如何在大量的设计和验证过程中保证项目质量的同时,确保项目进度?每家公司都有自己的项目管理方式,今天梳理几家OEM的项目管理流程供大家参考。
所有汽车新项目的开发和管理,都会把质量放在第一,质量广义上代表一种能力,包含了一家品牌汽车厂的制造能力、管理能力、研发能力与业务能力,其实统统都可以叫质量能力,汽车行业内部称之为新项目流程管理和开发,这个流程和汽车最终成品下线的整体质量息息相关。
大众集团大众集团对于新项目的开发流程就如上图所示,整个项目节点划分非常细,其中最关键点分别是:PF项目确认、B认可、0S零批量以及SOP量产。
B认可后,所有零部件供应商必须要进行开模,相当于实物制造启动指令;0S交样也是大众非常关键的一点,这个时候大众质保部门会全力介入,比如产线试装、各路况路试、供应商首批样件检验和认可,供应商产能评审2TP等等。
沃尔沃沃尔沃的节点名称和描述较大众而言更为详细,造车理念也是贯彻了欧洲人的精细,有意思的是,沃尔沃在MP1批量投产后,会进行为期6个月的量产全检,用通用体系的术语叫GP12,GP12全检对新项目刚投产的质量不稳定现象能够有效防范和隔离。
日产日产的流程是分为从Phase1~Phase5,初看让人觉得日系的项目很简单,其实只是化繁为简,可以看看图二,每个阶段中有小的任务和里程碑,只有将所有任务验证完成并且合格,才能进入到下一个大阶段,其中一些关键字:1、VC lot代表试装样件,主机厂试验和实车试装;2、PT1预批量生产,需要完成量产流程和产品尺寸过程能力验证;3、PT2预批量生产,需要完成制造过程能力审核;日系这种地图指导式的项目开发流程,让人觉得非常可靠,一环扣一环的感觉。
通用通用汽车是贯彻先期质量策划的先驱,其流程和体系被业界广为效仿,甚至很多零部件供应商直接照搬通用的流程体系,这个流程对于文件、订单方式、造车区域有了明确的定义,让初学者和新手可以一目了然,正式物流订单分为小批量、中批量、大批量。
上海通用戴姆勒产品开发质量体系

2、上海通用质量保证体系模型
产品开发质量
GPLP全球生产启动流程生产启动质量
制造质量
产品开发
商品制造
分销服务
市场质量
GVDP全球产品开发流程
GM-GMS通用-全球制造系统
Style造型
Manufacture制造
骡子车/试制/试验Mule car/Build/Test
集成车(OTS样车)/试制/试验Integration Vehicle/Build/Test
Program Quality work structure项目质量工作结构框图
Goal: Enthuse our customer with quality product and service 目标:以我们的产品质量和服务质量唤起顾客的热忱
Methodology: Deep understand customers’ requirement with high efficient design exploration and validation ability 方法:深刻理解顾客的需求,高效的设计开发和验证能力
过程中的控制和确认执行没有遗留问题的生产启动持续改进
In-process control &validationExecute flawless launchContinuous improvement
不会导致失效的设计有效验证改进QRD关注区域
Design not to failEffective validationImprove QRD focus area
立项(战略意图文件)
车辆项目启动
设计签署
合同签署
验证数模发布
整车集成
产品和工艺验证
汽车车身饰件DFMEA-顶棚系统
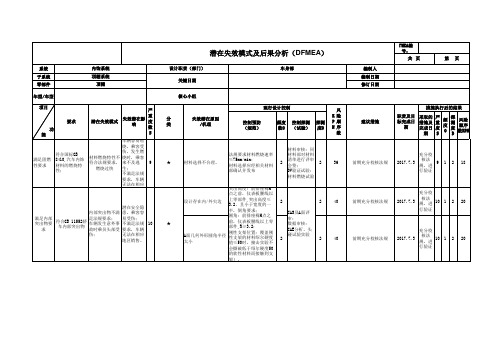
零件局部变
与隔音绵、线束 形较大
干涉
装配效果不
3
好
密封条唇边变形 较大,与顶棚配 影响外观 5 合不好
安装后零件不牢 固
零件能够晃 动,影响品 质
2
固定点:不足、尺寸 不对、 设计不合理
参考类似车型 设计评审
3
数据评审,设 计校核
2
18
☆
设计预留空间不足
参考类似车型,尽量留 足空间
3
数据评审,设 计校核
6
影响销量。
气味难闻,
新车经高温放置 顾客抱怨强 后,有难闻气味 烈;
5
影响销量。
禁用物质要求
选用材料不满足 国家环保要求及 公司企标要求 (选材含有甲醛 及有机物等含量 超标材料)。
挥发有害气 体、伤害乘 客身体,引 起顾客抱怨 。
9
零部件气味性不能满 选择耐候性符合相关定
足公司标准
义要求的材料
在高,低温温下材料 材料选择满足气味性要 3
进行气味及挥 发性相关试验 检测,检测产 5 品是都满足公 2 司标准要求。 符合企标禁用 物质要求。
90
周边零件与理论状态 有偏差
生产控制
3 零件检测
2
18
前期充分校核法规
充分校
2017.7.3
核法 规,进
9
3
2
54
行验证
安装有错位
与其它零件 装配不好
3
☆
零件生产不合格
生产控制
3 零件检测
2
18
顶棚安装配合
4
黑斑、粉化等缺
陷,用放大镜20
倍或类似的仪器 外观质量
耐光色牢度
能看见与初始状 差,零件性 态相比表面龟 能失效,引
DFMEA-车身

24 无
潜在失效模式及影响分析 (设计FMEA)
系 统: 附件 内饰 副仪表板总成 设计职责: 关键日期: 2013.10.20 编制人: FMEA编号: 子系统: 零部 件: 车型/项目:
核心小组:
项目 要求 潜在 失效模式 潜在 失效影响 严 重 度 S 分 类 潜在失效原 因 控制预防 现行设计
4 ## 无
2 48 无
3 54 无
2 70 无
潜在失效模式及影响分析 (设计FMEA)
系 统: 车身 前翼子板总成(左) 翼子板 (左) 设计职责: 关键日期: 编制人: 樊雷 FMEA日期(编制): FMEA日期(修订):
FMEA编号:
功 能
RPN
焊接、定位 焊接、定位 后地板总成 方便 困难 · 承载载荷 · 构成白车身总 成 · 安装底盘、动 力电池等一些 设备
焊枪接近困 难;夹具没 有夹持空 间,定位困 难;工序转 移困难。
7
设计时未考 充分考虑 虑周全焊装 结构对焊 工序的要求 接和定位 的影响
4 组织经验 丰富的技 术人员对 结构进行 评价
项目 要求 潜在 失效模式 潜在 失效影响 严 重 度 S 分 类 潜在失效原 因 控制预防 现行设计 发 生 频 控制探测 度 O 实施结果 探 测 度 D RP N 建议措施 职责 目标 完成 日期 采取的措施 和 完成日期 严 重 度 S 发 生 度 O 探 测 度 D
子系统: 零部 件: 车型/项目: 核心小组:
FMEA编号:
实施结果 探 测 度 D RP N 建议措施 职责 目标 完成 日期 采取的措施 和 完成日期 严 重 度 S 发 生 度 O 探 测 度 D
功 能
RPN
前舱托架总成 安装电器 生产、维修 件,承载载 不易安装、 不便,影响 荷 7 拆卸 客户的满意 度
dfmea案例
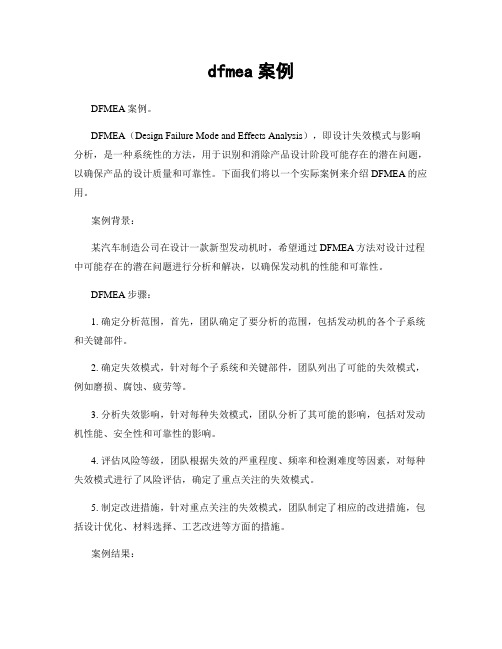
dfmea案例DFMEA案例。
DFMEA(Design Failure Mode and Effects Analysis),即设计失效模式与影响分析,是一种系统性的方法,用于识别和消除产品设计阶段可能存在的潜在问题,以确保产品的设计质量和可靠性。
下面我们将以一个实际案例来介绍DFMEA的应用。
案例背景:某汽车制造公司在设计一款新型发动机时,希望通过DFMEA方法对设计过程中可能存在的潜在问题进行分析和解决,以确保发动机的性能和可靠性。
DFMEA步骤:1. 确定分析范围,首先,团队确定了要分析的范围,包括发动机的各个子系统和关键部件。
2. 确定失效模式,针对每个子系统和关键部件,团队列出了可能的失效模式,例如磨损、腐蚀、疲劳等。
3. 分析失效影响,针对每种失效模式,团队分析了其可能的影响,包括对发动机性能、安全性和可靠性的影响。
4. 评估风险等级,团队根据失效的严重程度、频率和检测难度等因素,对每种失效模式进行了风险评估,确定了重点关注的失效模式。
5. 制定改进措施,针对重点关注的失效模式,团队制定了相应的改进措施,包括设计优化、材料选择、工艺改进等方面的措施。
案例结果:通过DFMEA分析,团队发现了一些潜在的设计问题,并及时采取了相应的改进措施。
例如,在分析润滑系统时,团队发现了润滑油管路设计存在潜在的腐蚀和堵塞风险,因此对润滑油管路进行了优化设计,采用耐腐蚀材料,并增加了清洗通道,以确保润滑系统的可靠性。
另外,在分析发动机散热系统时,团队发现了散热片设计存在的疲劳裂纹风险,因此对散热片的材料和结构进行了改进,提高了其抗疲劳性能。
结论:通过DFMEA分析,团队及时发现并解决了潜在的设计问题,确保了发动机的性能和可靠性。
这个案例充分展示了DFMEA方法在产品设计过程中的重要作用,通过系统性的分析和改进措施,帮助企业提高了产品的质量和竞争力。
在实际应用中,DFMEA需要团队成员的密切合作和专业知识的支持,以确保分析的全面性和准确性。
汽车车身饰件DFMEA-开闭件钣金

设计者
2
36
根据CAE分析报 告进行优化
设计者
2
48
根据CAE分析报 告进行优化
设计者
2
28
根据校核报告进 行优化
设计者
1
28
根据校核报告进 行优化
设计者
2017/9/20
2017/9/20
2017/9/20 2017/9/20 2017/9/20
涂胶工艺
注塑成型 工艺
冲压成型 工艺性
漏液孔
符合人机 工程
致
车门密封
达不到要 防水防尘效果 求,漏风 差,顾客抱怨
6
☆
门下垂导致上密封间 隙过大
、漏雨
CAE分析 设计校核 CAE分析
2
强检试验 (GB15743)
1
18
根据CAE结果进 行设计优化
设计者
2017/9/20
2
淋雨试验
2
24
根据校核报告进 行优化
设计者
2017/9/20
4
强化试验
2
48
根据CAE报告进 行优化
参考成熟车型和满足 GB15743-1995
2
侧撞试验
1 20
设计者 2017/9/20
外板表面 外板共振异响,
刚性差
易变形
6
☆
外板刚度不足;缺少 对外板的支撑
CAE分析
2
刚度实验
2
24
根据CAE结果进 行设计优化
设计者
2017/9/20
内外板过 软
影响安全性
9
★
结构、材料不能达 到要求
侧门到侧围及侧围门 6 ☆ 洞止口密封间隙不一
DFMEA 车身控制系统 - 硬件系统

版本: V1.0 页次: 2
风险 顺序 数 (RPN)
措施结果 责任及目标 严重 频度 不可 风险顺 完成日期 采取的措施 度数 数 探测 序数 (S) (O) 度数 (RPN) (D) 经过高低温 倪怡静 试验箱进行 高低温试验 5 2 3 30 2005.5.31 试验,可以 正常工作 建议的 措施 厂家提供试 黄晋 可以满足国 验数据 2005.5.31 标要求 振动试验后 零部件没有 倪怡静 损坏,模块 2005.5.31 可以正常工 作 6 2 3 36
耐温性
-40℃~ 部分控制失 +65℃范 效、影响系 围内无法 统性能 正常工作
5
元器件耐温性能 不够
6
选用汽车级 的元器件 选择符合 QC/T 417.4.5的 接插件 选用贴片元 器件或可紧 贴在电路板 的器件
高低温试验
5
接插件的接插 接插件脱 部分控制功 以及拔出力 落 能失效
6
接插件自锁强度 不够
6
信号采集电路对 信号的滤波处理 不当
3
改进信号采 实际装车试 集电路,增 验,并进行1 加滤波处理 万公里路试 电路 实际装车试 验 在设计阶段 进行反复试 验,确保块失效
3
2
4
遥控解码程序 对遥控信号的过 滤门限过宽
2
实际装车试 验
3
后果分析
表单编号: 过程责任部门: 技术中心 编制: 修订日期:
4
5
耐振动性能
零部件损 影响系统性 坏 能
5
元件固定方式以 及布局不合理
7
振动试验
7
耐压性能
模块无法 正常工作
控制失灵
6
芯片耐压性能没 有满足要求
3
奇瑞公司产品开发流程培训

新产品开发基 本程序范围
新产品开发项 目管理范围
产品型谱规划
新项目研究
项目立项
项目可行性分析
项目策划
产品设计和开发
产品实现 范围
过程设计和开发 生产准备
零部件采购
SOP 后3个月
终点
产品与过程确认 营销与服务(国内、国际)
备件准备
SOP
项目总体阶段划分 项目概念阶段 (P0~P1)(项目管理部主控) 项目规划阶段 (P2) (项目组主控) 项目实施阶段 (P3~P9)(项目组主控)
设计基本输入
供应商介入同步开发 总布置图评审 基本性能指标 动力总成和底盘系统 ……
M1 M1.5
规 划 同 步 工 四大工艺可行性程分析
M2
图纸入系统
模具供应商介入等
M3
机加数模 设计变更
M0:初始数模,带有分型线的一级和二级表面数据(公差达到±0.5),主要外板数据(包括主要外板数据的一、二级表面) M1:50%数模,一级表面数据带有第一倒角和第一翻边(公差达到±0.5),主要外板和内板数据(包括有用的二、三级表面) M1.5:100%数模,全部一级表面数据(公差达到±0),所有钣件(包括二级和三级表面) M2:冻结数模,全部倒角数据 ,所有板件 M3:机加数模,设计变更,所有板件
蛇形转向试验:水泥砼路面,附着系数0.68—0.72。可进行稳定转向响 应特性试验、操纵性、稳定性试验、轮胎附着特性测定试验。
寒带试验
热带试验
高原试验
前碰撞试验
侧碰撞试验
翻滚试验
气囊爆破试验
节点编号 P6 节点名称 生产试制批量完成
单机/单序生产能力和过程能力符合设计要求; 所有的单件和总成件都到位,并都是用批量生产 的设备及工装模具、试生产控制计划制造出来件 ;整个生产过程可在不连续的条件下按B阶段的 节点定义 图纸进行生产,从而对各工序加工能力、生产设 备、试生产控制计划是否适当以及生产线的制造 可行性、装配可行性、通过性、批量生产的适宜 性进行实际验证;一般作业人员经过理论、线下 和线上培训,上市流程已启动。
汽车车身饰件DFMEA-组合仪表罩总成

☆
撞距离要求
100mm
驶员造成更多伤
组合仪表罩总成视野
组合仪表罩 总成不可遮 挡仪表可视
区域
组合仪表在视野 可视范围内不被 遮挡,视野清晰
仪表视野遮挡
看不清仪 表,影响驾 驶员安全性
和舒适性
8
☆
可靠耐久性/可靠性/环 境条件/温度湿度
组合仪表罩 总成
高温变形翘曲, 轮廓和曲面歪斜 仪表板系统及其 、高温接合面分 子系统需要在 离、高温气泡、 95%的车辆使用 粉化、渗出、缩 温度和湿度条件 孔、高温纹理消 下功能可靠 失、高温装饰层 膨胀、高温变形 、功能失效低温
间隙定义不合理
相互配合结构符合BP 规范IP-11021
数据评审/设 3 计校核/实车 2
验证
1、节点审
核,M2节点
3
仪表板系统对M1数据进
3
行评审确认
组合仪表罩总成卡子 卡紧力不够,卡口结 构未按照数据调整到
位
1、概念设计时,此项 校核不充分 2、设计评审
设计时未考虑组仪表 设计时做好组合仪表 罩总成单独拆卸空间 罩单独拆DMU校核
齐
灰边
怨
4
☆
组合仪表罩总成 组合仪表罩总成
与组合仪表配合 与组合仪表间隙
规避摩擦异响
不合理
间隙小产生 摩擦异响
4
☆
组合仪表罩 总成满足紧 固良好的要
求
组合仪表罩总成 禁锢良好
组合仪表罩总成 禁锢不良,组合
仪表罩易晃动
舒适度不 佳,影响内 饰质量评价
4
☆
组合仪表罩 总成
组合仪表罩总成 在不拆卸仪表板 条件下具备维修
要求
组合仪表罩要拆 卸仪表板才能维
DFMEA判定标准

没有现行控制,无法探测或并未分析
在任何阶段 不易探测
探测能力很弱,虚拟分析与预期的实际操作没有关联
在设计定稿后,设计发布之前,使用GO/NG试验对产品确认。
在设计定稿 后,设计发 布前
在设计定稿后,设计发布前,通过试验到失效的试验对产品确认(直 到故障发生)
在设计定稿后,设计发布前,通过老化试验对产品进行确认,(在耐 久性试验后进行测试,如功能检查)
严重度DFMEA
影响
标准:对顾客的影响
不符合 安全性 或法规
要求
基本功 能丧失 或降低
次要功 能丧失 或降低
潜在的失效模式影响了汽车的安全运行;或者包含不符合政府法规的情形, 失效发生时无预警。 潜在的失效模式影响了汽车的安全运行;或者包含不符合政府法规的情形, 失效发生时有预警。 基本功能丧失(汽车无法运行,但不影响安全)。
≥1/10000
4
几乎相同设计,或者在设计模拟/测试时,仅有个别失效。
≥1/100000
3
低 几乎相同设计,或者在设计模拟/测试时,没能 觉察到失效。 ≥1/1000000 2
很低 通过预防控制消除失效。
通过预防控制消
除失效。
1
探测度DFMEA
探测几率
标准:设计控制可能探测出来的可能性
没有探测机 会
在设计定稿前对产品进行确认(可靠性试验、开发确认试验)使用 GO/NG的试验来验证(如性能接受标准、功能有检查等)。
在设计定稿 在设计定稿前对产品进行确认(可靠性试验、开发确认试验)使用试
之前
验到失效的试验来验证(如直到有泄露、弯曲、破裂等现象)。
在设计定稿前对产品进行确认(可靠性试验、开发确认试验)老化的 试验来验证来确认。
DFMEA-车身各结构钣金部分及其他
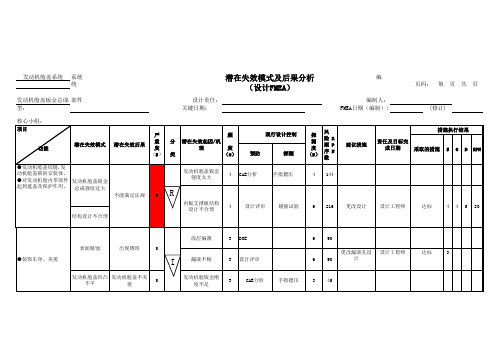
6 90
计
3 45
达标
3
(O)
现行设计控制
预防
探测
●发动机舱盖铰链.发
动机舱盖锁的安装体。 ●对发动机舱内零部件 发动机舱盖钣金
发动机舱盖钣金 强度太大
4 CAE分析
起到遮盖及保护作用。 总成强度过大 不能满足法规
9
R
手指摁压
内板支撑板结构 设计不合理
4
设计评审
碰撞试验
结构设计不合理
探 测 度 (D)
风 险R 顺P 序N 数
发动机舱盖系统 系子统系 统
潜在失效模式及后果分析 (设计FMEA)
FMEA 编
页码: 第 页 共 页
发 年动 度机 车舱型盖/车钣辆金类总成 部件 型:
设计责任: 关键日期:
编制人: FMEA日期(编制):
(修订)
核心小组: 项目
功能
潜在失效模式
严பைடு நூலகம்
频
潜在失效后果
重 度
分 潜在失效起因/机
理
度
(S) 类
4 144
6 216
建议措施
措施执行结果
责任及目标完
成日期
采取的措施 S O D RPN
更改设计 设计工程师
达标
4 4 5 80
●装饰车身、美观
表面腐蚀
出现锈斑
5
发动机舱盖凹凸 发动机舱盖不美
不平
观
5
涂层偏薄
3 DOE
I
漏液不畅
3 设计评审
发动机舱钣金刚 度不足
3
CAE分析
手指摁压
6 90
更改漏液孔设 设计工程师
dfmea第五版模板分析实例
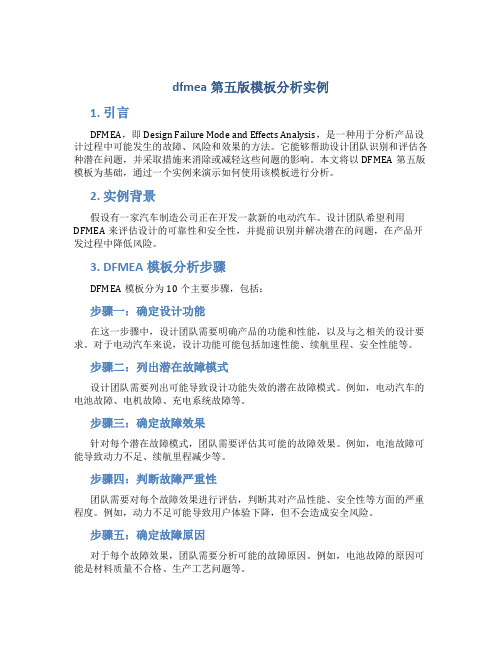
dfmea第五版模板分析实例1. 引言DFMEA,即Design Failure Mode and Effects Analysis,是一种用于分析产品设计过程中可能发生的故障、风险和效果的方法。
它能够帮助设计团队识别和评估各种潜在问题,并采取措施来消除或减轻这些问题的影响。
本文将以DFMEA第五版模板为基础,通过一个实例来演示如何使用该模板进行分析。
2. 实例背景假设有一家汽车制造公司正在开发一款新的电动汽车。
设计团队希望利用DFMEA来评估设计的可靠性和安全性,并提前识别并解决潜在的问题,在产品开发过程中降低风险。
3. DFMEA模板分析步骤DFMEA模板分为10个主要步骤,包括:步骤一:确定设计功能在这一步骤中,设计团队需要明确产品的功能和性能,以及与之相关的设计要求。
对于电动汽车来说,设计功能可能包括加速性能、续航里程、安全性能等。
步骤二:列出潜在故障模式设计团队需要列出可能导致设计功能失效的潜在故障模式。
例如,电动汽车的电池故障、电机故障、充电系统故障等。
步骤三:确定故障效果针对每个潜在故障模式,团队需要评估其可能的故障效果。
例如,电池故障可能导致动力不足、续航里程减少等。
步骤四:判断故障严重性团队需要对每个故障效果进行评估,判断其对产品性能、安全性等方面的严重程度。
例如,动力不足可能导致用户体验下降,但不会造成安全风险。
步骤五:确定故障原因对于每个故障效果,团队需要分析可能的故障原因。
例如,电池故障的原因可能是材料质量不合格、生产工艺问题等。
步骤六:评估现有的设计控制措施团队需要评估当前设计中已有的控制措施,以减轻或消除潜在故障模式的影响。
例如,对于电池故障,是否存在电池过压保护功能等。
步骤七:确定潜在控制措施对于未能完全消除潜在故障模式的控制措施,团队需要确定额外的潜在控制措施。
例如,对于电池故障,可以增加电池故障检测系统。
步骤八:评估控制措施效果对于已确定的控制措施,团队需要评估其对潜在故障模式的效果。
汽车电器_车身控制系统_DFMEA
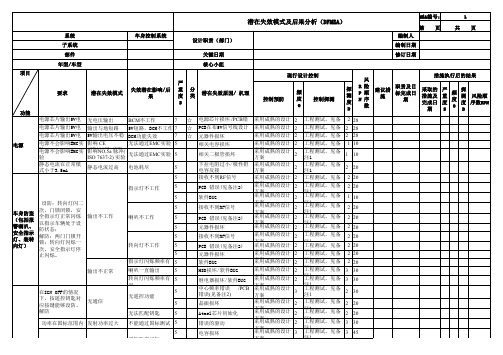
整,壁厚过厚,导致零 型工艺,将零件
件整体缩水变形
的加强筋骨布局 3
测量检查
2 24
由于材料特性造成注塑 将前框和后壳内 A样件验证,尺寸
成型时易出现变形 增加加强筋
测量检查
选用的材料不合理
根据技术协议, 3 高低温实验验证 5 50 选用合理的材料
控制模块装配后,零件
未压到线路板,起不到
Z方向的固定作用
5
静态电流在正常模 静态电流过高 电池耗尽 式小于3.5mA
5
5
指示灯不工作
5
车身防盗 (包括报 警喇叭、 安全指示 灯、装转 向灯)
设防:转向灯闪二 次、门锁闭锁,安 全指示灯正常闪烁 输出不工作 以指示车辆处于设 防状态; 解防:两门门锁开 锁;转向灯闪烁一 次、安全指示灯停 止闪烁。
输出不正常
3D数模模拟装配 3 A样件试装后验证 5 60
控制模块装配后,零件
与后壳装配的卡扣设计
零件的加强筋骨不完 依据塑胶件的成
A样件验证,尺寸
整,壁厚过厚,导致零 型工艺,将零件
件整体缩水变形
的加强筋骨布局 3
测量检查
2 24
由于材料特性造成注塑 将前框和后壳内 A样件验证,尺寸
成型时易出现变形 增加加强筋
在IGN OFF的情况 下,按遥控钥匙对 应按键能够设防、 解防
无通信
5
5
喇叭不工作
5
5
5
转向灯不工作
5
5
指示灯闪烁频率有 5
误喇叭一直输出
5
转向灯闪烁频率有 5 误
5 无遥控功能
5
无法匹配钥匙
5
功率在国标范围内 发射功率过大 不能通过国标测试 5
DFMEA-和-DVP含义

DFMEA 和DVP&RDFMEA (设计潜在失效模式与效应分析) 和DVP&R (设计确认计划和报告)设计潜在失效模式与效应分析(DFMEA) 是一种评估耐牢度对抗潜在失效的设计的方法,也是汽车公司要求的新产品开发过程的一个组成部分——产品质量先期策划和控制计划(APQP)的关键部分。
在设计DFMEA的时候,必须要考虑从过去测试经验和行动中得到的教训,这些教训用来在今后将风险最小化。
设计风险在历史数据和工程分析的基础上进行评估。
DFMEA在常规流程的严重程度、发生频率和探测能力的基础上区分行动计划的优先次序。
设计确认计划和报告是以设计潜在失效模式与效应分析(DFMEA)为基础。
它是一个工作文件,帮助在验证开发过程中管理人员,同时它也是确保产品可靠性和达到客户要求的一个工具。
它是汽车公司要求的新产品开发过程的一个组成部分——产品质量先期策划和控制计划(APQP)的关键部分。
样件控制计划和DVP&R(设计验证计划&报告)有什么区别样件控制计划是描述对样件的尺寸、功能和性能检验的控制要求;DVP&R也是描述对设计验证对象,也就是样件的检验要求请问这两个之间有什么具体区别呢?还有,样件也分为手工样件、OTS样件等,是都需要分别编制样件控制计划吗我个人觉得控制计划重点在于制造前的控制缺陷的产生,而DVP是事后的对于产品的验证是否符合图纸或规范。
样件控制计划要说明你的产品如何生产,如何检验(包括性能,功能,外观和日常检验,检验频次也该规定)!!!DVP是用来编制验证产品性能和功能实验的计划,而且DVR是用来记录你的试验结果的,所以两者的作用实际是不同的!至于手工样件和工装样件,作业工具不同,可能也需要分别编制,这个我不是很确定,或者可以引用手工样件的控制计划,把不同部分指出.哈哈,问高手吧特别是样件本身也有很多阶段的,比如手工样件、DV样件、工厂OTS样件和客户OTS样件,是否需要分别编制样件控制计划呢?按楼上的说法,DVP中是不用规定对尺寸的检验要求了?手工样件和OTS样件不一样,所以他们各自都需要各自的控制计划。
- 1、下载文档前请自行甄别文档内容的完整性,平台不提供额外的编辑、内容补充、找答案等附加服务。
- 2、"仅部分预览"的文档,不可在线预览部分如存在完整性等问题,可反馈申请退款(可完整预览的文档不适用该条件!)。
- 3、如文档侵犯您的权益,请联系客服反馈,我们会尽快为您处理(人工客服工作时间:9:00-18:30)。
新 严 重 度
新 频 度
新 探 测 度
新风 险顺 序数
Actions Taken
New New New New SEV OCC DET RPN
制造工艺 7
车身涂装工艺性差
车身电泳底漆厚度 不均匀、部分区域 未充分覆盖底漆、 5 车身锈蚀、影响整 车寿命
按《白车身SE审
涂装SE分析未到 位,钣金结构不 合理
查报告》进行反
4
馈及数模修改, 合理设计钣金结
试制验证
2
构,保证涂装效
40
果
按《白车身SE审
总装件无法安装;
查报告》进行反
车身总装操作性
总装SE分析未到
馈及数模修改,
车身总装工艺性差
差,工人抱怨、生 5
位
未分 4 合理设计钣金结 试制验证 2 40
产率低;零部件维
析可维修性
构,合理考虑安
修操作性差
装操作空间,进
5
块化说明,预先 设计拓展车型结
虚拟验证
6
构方案
30
冲压SE分析未到 位,钣金结构不 合理
按《白车身SE审 查报告》进行反 4 馈及数模修改, 试制验证 6 合理设计钣金结 构
120 SE分析
车身焊装工艺性差
车身焊接操作性
差,工人抱怨、生 产率低,焊接效果
5
差,影响车身性能
按《白车身SE审
焊装SE分析未到 位,钣金结构不 合理
压要求
能销售
10
材料选择不对或 结构不合理
按法规要求指标 4 指标进行设计, 试制验证 6
240
按法规要求设计,进行 CAE分析确认
车身/性能 2014.3.1
19
安全带固定点不满足GB14167- 无法通过认证,不
2006要求
能销售
10
材料选择不对或 结构不合理
4
针对CAE分析提 出的意见进行修
试制验证
供应商/顾客:
Supplier/Customer 车型号/车辆类型:PM-01 Model(s): PM-01 核心小组成员: FMEA Team Members
零件名称:白车身(含开闭件钣金及铰链) Part Name:BIW&CLOUSER
设计潜在失效模式及后果分析(D-FMEA)
Design Failure Mode and Effects Analysis (D-FMEA)
钣金安装结构与边界要求不一 致
零部件无法安装
Potential Cause(s) SEV Class /Mechanism(s)of
Failure
OCC
Current Prevention Control
Current Detection Control
DET RPN
按《白车身孔位
1
车身数据未符合 边界要求
16
M1类不满足GB 11551-2003正 无法通过认证,不
面碰撞要求
能销售
10
材料选择不对或 结构不合理
4
试制验证 2 80
17
M1类不满足GB 20072-2006后 无法通过认证,不
部碰撞要求
能销售
10
材料选择不对或 结构不合理
4
试制验证 2 80
18
碰撞安全
M1类不满足GB 26134-2010顶 无法通过认证,不
108 寸,保证后期数据满足
要求。 方案阶段确定各相关尺
108 寸,保证后期数据满足
要在求 满。 足制造工艺性的前
168
提下尽量减小钣金间 隙,同时在影响密封位
置保证打胶,同时请涂
车身/整车 车身/整车 车身/性能
20141.1 2014.1.1 2014.1.1
白车身、前车门、滑门、后背 户抱怨 整车使用 门刚度差,不满足要求 过程中局部工况变
行安装虚拟验证
8
影响用户乘车舒适 空间利用率差,内部空间不足 性,影响内部载货 3
空间,用户抱怨
未合理设计钣金 结构,钣金侵占 内部空间
进行CAE分析,
在保证车身性能
6
、安装结构的前 提下尽量增大内
RP样件装 车验证
7
部空间,可对比
初期确定目标值,后期 按照执行,尽量加大内 部空间
126
2014.1.1 车身/整车
9
人机工程
标杆设计
10 11 12
前门、侧滑门、后背门上下车 方便性差
影响用户乘车舒适 性,影响内部装卸 货方便性,用户抱
3
遮挡上下左右视野;
存在安全隐患,用 户抱怨
3
车身总成密封性差,不满足要 求
整车NVH性能差,漏 风、漏水,客户抱 怨
4
整车NVH性能差,客
未合理设计钣金 结构,未按人机 要求设计
意见进行修改,
48
可在对满比足标制杆造设工计艺
性的前提下尽量
减小钣金间隙,
车身总成密封性差,不满足要 求
整车热舒适性差, 无法满足空调性能 要求,客户抱怨
4
未仔细检查钣金
同时在影响密封
间隙大小及涂胶 6 位置保证打胶, 试制验证 2 48
情况,
同时请涂装部门
对相应位置进行
重点分析,可对
15
比标杆设计
试制验证
5
175
CAE分析确认
车身/性能 2014.3.1
劳破坏,影响内部
择材料,并进行
安装结构,影响整
CAE分析确认
描述书》和《零 5 部件边界条件确 试制验证 1
认表》进行数据
5
检查
Recommend Action(s)
零部件静止或运动状态干涉或 间隙不足
车身无法焊装、车 身运动干涉、车身 异响、用户抱怨
1
三维数据检查未
按《白车身自相
全面检查、运动
关检查表》和《
校核未考虑实车 5 车身运动件运动 试制验证 6 30
6
240
按法规要求设计,进行 CAE分析确认
车身/性能 2014.3.1
20
座椅固定点不满足GB 15083- 无法通过认证,不
2006要求
能销售
10
材料选择不对或 结构不合理
4
Байду номын сангаас
改,可对比标杆 设计
试制验证
1
40
21
车身强度不满足要求
车身出现裂纹、松 动、变形损坏、疲
7
材料选择不对或 结构不合理
5
按可靠耐久性要 求设计结构、选
5
拉延开裂,模具上
修边刃口强度不
足,影响车身性能
设计间隙、面差 不合理; 装调不到位;公 差分配不合理; 定位方式设置不 合理
参照相关车型合 理设置DTS定义 6 值,合理设置公 试制验证 6 差,合理设置定 位方式
144
数模校核,定位方案确 定
设计结构时未考 虑后期开发车型 的共用性
编制车身开发模
零件号:
Part No. 关键日期:2014.3.1
责任部门:
Department 审核:
车身工程中心 BODY CENTER
Key Date:2014.3.1
Verification
日期(编制):
Compile Date
FMEA编号:
No. 编制人:
Compiled By
序
项目
号
/功能
潜在失效模式
潜在失效后果
严 重 度
级 别
潜在失效原因
发
生 频
现行预防控制
度
现行探测 控制
探 测 度
风险 顺序
数
建议措施
责任部门
责任目标完 成日期
Line No. 1 2 3 4
5
6
Item/ Function 物理结构
制造工艺
Potential Failure Mode
Potential Effect(s) Of Failure
4
未满足车身刚度 指标要求
6
进行设计,针对 CAE分析提出的
试制验证
2
48
13 14
NVH
形大,易引起车身
整车NVH性能差,客
白车身、前车门、滑门、后背 户抱怨 如模态处 门模态差,不满足要求 于发动机怠速范围
4
内,易引起共振
意按见NV进H控行制修指改标,
未满足车身模态 指标要求
进行设计,针对 6 CAE分析提出的 试制验证 2
未按人机要求设 计、校核
未仔细检查钣金 间隙大小及涂胶 情况,
6
按人机要求设计 数据,在保证车 身性能、安装结
RP样件装 车验证
6
按人机要求设计 数据,在保证车 身在性满能足、制安造装工结艺
RP样件装 车验证
6
性的前提下尽量 减小钣金间隙,
试制验证
同按时NV在H控影制响指密标封
6 6 7
方案阶段确定各相关尺
查报告》进行反
4
馈及数模修改, 合理设计钣金结
试制验证
2
构,合理布置焊
40
点位置及层次
Responsible Department
Targe Completi -on Date
车身
2014.3.1
2014.3.1 车身/制造
日期(修改):
Amend Date
措施结果/Action Results
采取的措施
精度、相关零部
校核检查表》进
件未考虑到位
行数据校核
外表面间隙、圆角、面差与定 整车外观效果差,
义值不一致、附件装配孔精度 无法满足客户需