风险评价报告JHASCL表
风险评价报告(JHA、SCL表)详解
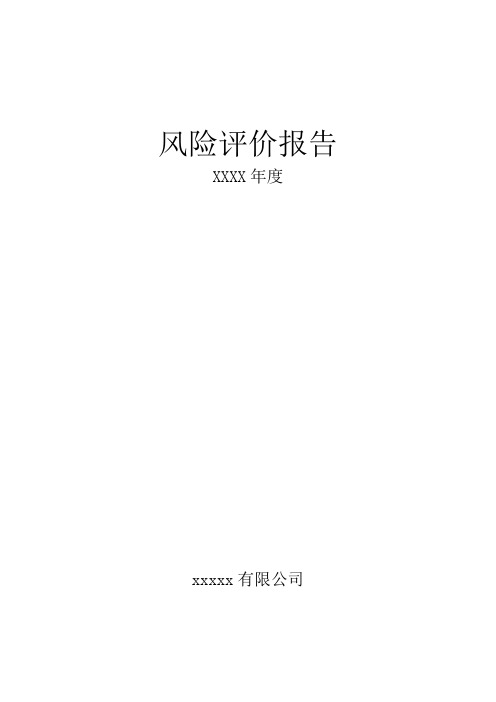
风险评价报告XXXX年度xxxxx有限公司风险评价报告书一、目的为规范部门风险管理工作,识别和评价作业过程中的危险有害因素,消除或减少事故危害,降低安全风险。
由风险评价领导小组负责进行危害因素识别和风险评估工作。
二、评价范围评价小组从部门工作的全过程,对所有可能造成危害和影响的活动进行了工作危害分析(JHA)和安全检查表分析(SCL),,将部门部分作业过程及设备设施存在的风险进行逐一排查、识别。
三、评价组组长:副组长:成员:四、评价方法部门发动员工参与风险评估,专业技术人员、管理人员与员工一起参与风险评估过程,采用了工作危害分析(JHA)和安全检查表(SCL)等基本方法,进行风险评估时的程序如下:1、作业危害分析主要采用工作危害分析(JHA),由各单位的评价小组中岗位操作人员、班长、专业技术人员对本岗位的所有作业活动列出清单,并进行工作危害分析(JHA),做完成后先经综合办公室负责人审查修改,修改完成后,上报部门评价组进行会审,对不合格者提出修改意见返回基层单位再进行修改,部门通过后上报公司风险评价组进行会审和确定。
2、设备设施的危害分析主要采取安全检查表(SCL)分析,由各单位的评价小组管理人员、技术人员和岗位操作人员列出设备设施清单,按安全检查表(SCL)分析进行,做完成后先经综合办公室负责人审查修改,修改完成后,上报部门评价组进行会审,对不合格者提出修改意见返回基层单位再进行修改,部门通过后上报公司风险评价组进行会审和确定。
五、评价过程见公司工作危害分析(JHA)表安全检查(SCL)分析表六、风险信息的更新1、在下列情况下安全检查表(SCL)分析记录和工作危害分析(JHA)记录进行更新:---工艺指标或操作规程变更时;---新的或变更的法律、法规或其他要求;---有新项目---有因为事故、事件或其他而发生不同的认识;---其他变更。
2、如果没有上述变化时,部门一年进行一次评审或检查风险识别的结果。
JHA及SCL风险评价方法讲解

JHA及SCL风险评价方法讲解JHA (Job Hazard Analysis) 和 SCL (Safety Check List) 都是用于风险评价的方法。
它们可以帮助组织识别工作环境中的潜在危险以及采取相应的措施来降低风险。
JHA (Job Hazard Analysis) 是一种系统的、结构化的方法,用于评估和管理工作环境中的潜在危险。
它的目标是确定每个工作任务中可能存在的危险,并确定适当的控制措施来减少或消除这些危险。
JHA通常包括以下步骤:1.识别工作任务:将工作任务按类型或步骤进行分类。
例如,在建筑行业中,可能包括挖掘、混凝土浇筑、钢筋安装等。
2.识别潜在危险:对于每个工作任务,识别出可能导致伤害或损害的潜在危险。
这些危险可能包括物理危险(如高速旋转的机器)、化学危险(如有毒物质)、生物危险(如病原体)以及人为因素(如不正确操作设备)等。
3.评估危险程度:根据潜在危险的严重性和概率,评估其对工作人员和环境的风险程度。
这可以通过专业知识、历史数据、专家意见等来确定。
4.制定控制措施:针对识别出的危险,制定相应的控制措施来减少或消除风险。
这可以包括采用工程控制措施(如改变工作场所的布局),行政控制措施(如培训工作人员)以及个人防护措施(如戴安全帽)。
5.实施和监督措施:将制定的控制措施付诸实施,并定期监督和评估其有效性。
如果控制措施无效或不足,需要进行调整和改进。
SCL (Safety Check List) 是一种简化的风险评价方法。
它通常由一个事先编制好的问题清单组成,用于快速评估特定区域或工作任务的安全状况。
SCL的特点包括以下几点:1.问题清单:SCL包含一系列有关安全的问题,例如工作区域是否清洁整齐、是否存在摔倒的风险、是否提供足够的个人防护设备等。
这些问题通常是根据行业标准、法规要求和最佳实践编制的。
2.快速评估:通过回答问题清单中的问题,可以快速评估工作区域或任务的安全状况。
风险评价方法scl、jha、lec)说明与举例
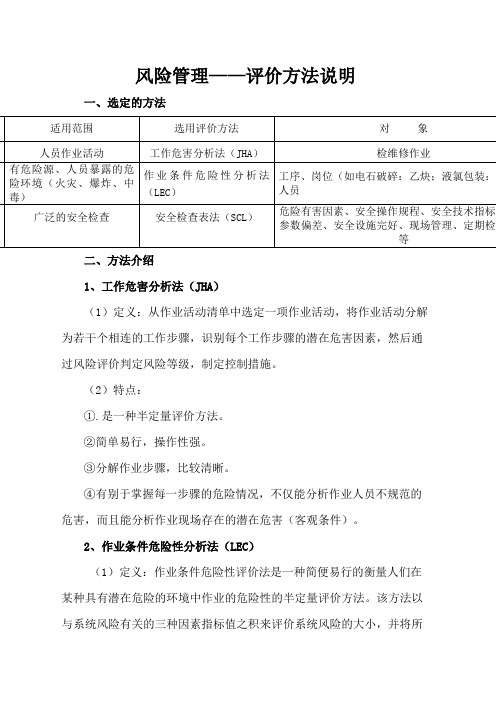
吊装
场地狭小,设备吊至地面过程中可能碰撞管路、设备和人员
VCM气体外泄污染环境,机械伤人,物体打击
作业区域设置警戒区域和警示标志,专人监护,防止行人随意走动,办理吊装作业证
1.2安全检查表分析(SCL)
1.2.1安全检查表分析方法是一种经验的分析方法,是分析人员针对拟分析的对象列出一些项目,识别与一般工艺设备和操作有关的已知类型的危害、设计缺陷以及事故隐患,查出各层次的不安全因素,然后确定检查项目,再以提问的方式把检查项目按系统的组成顺序编制成表,以便进行检查和评审。
(1)定义:安全检查表分析法是利用检查条款按照相关的标准规范等对已知的危险类别、设计缺陷和与一般工艺设备、操作、管理相关的潜在危险性和有害性进行判别检查。
(2)特点:安全检查表是进行安全检查、发现潜在隐患的一种实用而简单可行的定性分析法。
①事先编制,有充分的时间组织有经验的人来编写,做到系统化完整化,不至于漏掉导致危险的关键因素;
巨大风险
20~25
在采取措施降低危害前,不能继续作业,对改进措施进行评估
重大风险
15~16
采取紧急措施降低风险,建立运行控制程序,定期检查、测量及评估
中等风险
9~12
建立目标、建立操作规程、加强培训及交流
可接受风险
4~8
建立操作规程,作业指导书等,定期检查
可忽略风险
<4
无需采用控制措施,保存记录
2 作业条件危险性分析(LEC)及作业风险等级判定
3
拆除管子工作
盲目拆除,安全带不挂
Cl2中毒,高空坠落
(1)项目负责人确认管路中无Cl2,可在取样管中观察或取样分析(2)安全带挂好
4
拆除
管路中剩余气体挥发
安全风险评估方法及介绍

安全风险评估方法及介绍安全风险评估方法主要有安全检查表分析法(SCL)和作业危害分析法(JHA)法,风险等级判定选用MES评价法和预先危险性分析法(PHA)。
1安全检查表法分析法(SCL)安全检查表法是按照相关的法律法规、标准、规范等编制一套标准的安全检查表,对已知的危险类别、设计缺陷以及与一般工艺设备、操作、管理有关的潜在危险性和有害性进行判别检查。
针对实际可能存在的危险、危害因素及发生事故的可能性,提出安全技术对策措施及建议。
选择安全检查表分析的原因:安全检查表方法能够直接将现场勘查结果直接对照相关法律、法规和规程规范标准的要求,就可以得出准确结论,评价方法直观、一目了然。
安全检查表法具有以下优点:(1)能够事先编制,故可有充分的时间组织有经验的人员来编写,做到系统化、完整化,不致于漏掉能导致危险的关键因素;(2)可以根据规定的标准、规范和法规,检查遵守的情况,提出准确的评价;(3)表的应用方式是有问有答,给人的印象深刻,能起到安全教育的作用。
表内还可注明改进措施的要求,隔一段时间后重新检查改进情况;(4)简明易懂,容易掌握。
2工作危害分析法(JHA)JHA法的主要优点为:(1)较细致,将一项作业按步骤分解,识别每一个步骤中的危害和可能的事故,并设法消除;(2)简便易行、便于掌握,分析细致。
因此JHA主要用于日常作业活动的风险辨识,辨识每个作业的危害,其目的是根据风险辨识结果,制定控制措施,编制作业活动安全操作规程,控制风险。
其主要程序为:从作业活动清单中选定一项作业活动,将作业活动分解为若干个相连的工作步骤,识别每个工作步骤地潜在危害因素,然后通过风险评价,判定风险等级,制定控制措施/具体步骤和说明见下图工作危害分析/JHA步骤3MES评价法MES法是2002年提出的,已经在冶金、机械、化工、电力、建筑、船舶、煤炭、交通运输行业的很多企业及从事科研、讲师、仓储、物业管理等很多单位得到成功的应用。
JHA及SCL风险评价方法讲解

JHA及SCL风险评价方法讲解一、作业危害分析(JHA)介绍作业危害分析(Job Hazard Analysis,JHA)又称作业安全分析(Job Safety Analysis,JSA)、作业危害分解(Job Hazard Breakdown, JHB),是一种定性风险分析方法。
实施作业危害分析,能够识别作业中潜在的危害,确定相应的工程措施,提供适当的个体防护装置,以防止事故发生,防止人员受到伤害。
此方法适用于工艺操作,设备设施检修等。
作业危害分析将对作业活动的每一步骤进行分析,从而辨识潜在的危害并制定安全措施作业危害分析的主要步骤是:1、确定(或选择)待分析的作业;2、将作业划分为一系列的步骤;3、辨识每一步骤的潜在危害;4、确定相应的预防措施。
划分的作业活动步骤不能太笼统, 步骤划分也不宜太细,以致出现许多的步骤。
根据经验,一项作业活动的步骤一般不超过10项,要保持各个步骤正确的顺序。
为了辨识危害,需要对作业活动作进一步的观察和分析。
辨识危害应该思考的问题是:可能发生的故障或错误是什么其后果如何事故是怎样发生的其他的影响因素有哪些发生的可能性以下是危害辨识的部分内容:·是否穿着个体防护服或配戴个体防护器具·操作环境、设备、地槽、坑及危险的操作是否有有效的防护·维修设备时,是否对相互连通的设备采取了隔离·是否有能引起伤害的固定物体,如锋利的设备边缘·操作者能否触及机器部件或机器部件之间操作·操作者能否受到运动的机器部件或移动物料的伤害·操作者是否会处于失去平衡的状态·操作者是否管理着带有潜在危险的装置·操作者是否需要从事可能使头、脚受伤或被扭伤的活动(往复运动的危害)·操作者是否会被物体冲撞(或撞击)到机器或物体·操作者是否会跌倒·操作者是否会由于提升、拖拉物体或运送笨重物品而受到伤害·作业时是否有环境因素的危害——粉尘、化学物质、放射线、电焊弧光、热、高噪音工作危害分析(JHA)记录表单位:二车间日期:3月18日工作岗位:酯化工作任务:修酯化釜顶冷凝器风险度R :a) 轻微的(L×S=1~3);b) 可承受的(L×S=4~8);c) 中等的(L×S=9~12);d) 重大的(L×S=15~16);e) 不可承受的(L×S=20~25)建议的改进措施:A—表示轻微的,不必采取措施;B—表示可承受的,应维持现状、保持记录,但要保持检查或测量;C—表示中等的,应制定管理制度、规定、规程进行控制;D—表示重大的,应制定目标、指标、管理方案,限期治理;E—表示不可承受的,应立即采取隐患治理措施;二、安全检查表分析(SCL)所谓安全检查表,就是为系统地辨识和诊断某一系统的安全状况而事先拟好的问题清单。
JHA及SCL风险评价方法讲解

设施、信号选用不当、信号位置不当、信号不清、信号显示不准、其他
信号缺陷、标志缺陷、无标志、标志不清晰、标志不规范、标志选用不
当、标志位置缺陷、其他标志缺陷、其他物理性危险和有害因素
化学性危险和有害因素 易燃易爆性物质、易燃易爆性气体、易燃易爆性液体、易燃易爆性固 体、易燃易爆性粉尘与气溶胶、其他易燃易爆性物质、自燃性物质、有 毒物质 、有毒气体、有毒液体、有毒固体、有毒性粉尘与气溶胶、其 他有毒物质、腐蚀性物质、腐蚀性气体、腐蚀性液体、腐蚀性固体 、其他腐蚀性物质、其他化学性危险和有害因素 生物性危险和有害因素 致病微生物、细菌、病毒、其他致病微生物、传杂病媒介物致害动物、 致害植物、其他生物性危险和有害因素、心理、生理性危险和有害因 素、负荷超限、体力负荷超限、听力负荷超限、视力负荷超限、其他负 荷超限、健康状况异常、从事禁忌作业、心理异常、情绪异常、冒险心 理、过度紧张、其他心理异常、辨识功能缺陷、感知延迟、辨识错误、 其他辨识功能缺陷、其他心理、生理性危险和有害因素 行为性危险和有害因素 指挥错误、指挥失误、违章指挥、其他指挥错误、操作错误、误操作、 违章作业、其他操作错误、监护失误、其他错误、其他行为性危险和有 害因素 其他危险和有害因素
2 的HSE操作程 伤、间歇
序
不舒适
﹤10
受影响 不大, 几乎不 停工
装置范 围内污
染
1 完全符合
无伤亡 无损失 没有停 无污染 工
公司形 象
重大国 际国内 影响
行业 内。省 内影响
地区影 响
公司及 周边范
围
无影响
表2事件发生的可能性(L)
等
级
标准
在现场没有采取防范、监测、保护、控制措施,或危险、有 5 害因素的发生不能被发现(没有监测系统),或在正常情况
JHA及SCL评价方法介绍LKS

事故发生可能性(L)
分数值 10 标准 完全可以预料[在现场没有采取防范、监测、保护、控制措施,危险源事件 的发生不能被发现(没有监测系统),或在正常情况下经常发生此类事故 或事件] 相当可能[危险源事件的发生不容易被发现,现场没有检测系统,也未作过 任何监测,或在现场有控制措施,但未有效执行或控制措施不当;危险源 事件常发生或在预期情况下发生] 可能,但不经常[没有保护措施(如没有保护防装置、没有个人防护用品 等),或未严格按操作程序执行,或危险源事件的发生容易被发现(现场 有监测系统),或曾经作过监测,或过去曾经发生,或在异常情况下发生 类似事故或事件] 可能性小,完全意外[危险源事件一旦发生较能及时发现,并定期进行监测, 或现场有防范控制措施,并能比较有效地执行,或过去偶尔发生危险事故 或事件] 很不可能,可以设想[危险源事件一旦发生能及时发现,并定期进行监测, 或现场有防范控制措施,并能有效执行,或过去还未发生危险事故或事件] 极不可能[有充分、有效的防范、控制、监测、保护措施,或员工劳动安全 卫生意识相当高,严格执行操作规程。极不可能发生事故或事件] 实际不可能
第七步:定期评审。
工作危害分析(JHA)记录表
单位: 工作任务: 分析人员: 工作岗位: 分析日期:
序 号
工作步骤
危害
现有 控制 措施 性
建议改正/ 控制措施
1
停车
1) 车离过往车辆太近; 2) 停放地面松软不平 ; 3) 车辆可能前后滑动 (滚动)。 因搬备用轮胎而拧伤
2
搬备用轮胎 和工具箱
1) 开到远离交通的地方, 开应急闪光灯; 2) 选择牢固平整的地方 ; 3) 刹车、挂挡,在车轮 前后斜对着撒气轮胎放垫块 。 将备用轮胎转入车轮凹槽正 上位置,两腿尽可能靠近轮 胎站立,从车上举起备用轮 胎并滚至漏气轮胎处。 1) 撬轮毂帽用力要平稳; 2) 用的耳柄扳手要适合,用 力要稳要慢。
2.风险评价方法(SCL、JHA、LEC)说明与举例

风险管理——评价方法说明一、选定的方法二、方法介绍1、工作危害分析法(JHA)(1)定义:从作业活动清单中选定一项作业活动,将作业活动分解为若干个相连的工作步骤,识别每个工作步骤的潜在危害因素,然后通过风险评价判定风险等级,制定控制措施。
(2)特点:①是一种半定量评价方法。
②简单易行,操作性强。
③分解作业步骤,比较清晰。
④有别于掌握每一步骤的危险情况,不仅能分析作业人员不规范的危害,而且能分析作业现场存在的潜在危害(客观条件)。
2、作业条件危险性分析法(LEC)(1)定义:作业条件危险性评价法是一种简便易行的衡量人们在某种具有潜在危险的环境中作业的危险性的半定量评价方法。
该方法以与系统风险有关的三种因素指标值之积来评价系统风险的大小,并将所得作业条件危险性数值与规定的作业条件危险性等级相比较,从而确定作业条件的危险程度。
作业条件危险性评价法(LEC法)是以所评价的环境与某些作为参考环境的对比为基础,将作业条件的危险性作因变量(D),事故或危险事件发生的可能性(L)、暴露于危险环境的频率(E)及危险严重程度(C)为自变量,确定了它们之间的函数式,根据实际经验,给出了3个自变量的各种不同情况的分数值,采取对所评价的对象根据情况进行“打分”的办法,然后根据公式计算出其危险性分数值,再在按经验将危险性分数值划分的危险程度等级表查出其危险程度的一种评价方法。
(2)特点:①是一种半定量评价方法。
②简单易行,操作性强,危险程度的级别划分比较清楚、醒目。
③有利于掌握企业内部危险点的危险情况,有利于促进改措施的实施。
④缺点:由于它主要是根据经验来确定3个因素的分数值及划定危险程度等级,因此具有一定的局限性,只能作为作业的局部评价,不能普遍适用。
3、安全检查表方法(SCL)(1)定义:安全检查表分析法是利用检查条款按照相关的标准规范等对已知的危险类别、设计缺陷和与一般工艺设备、操作、管理相关的潜在危险性和有害性进行判别检查。
加油站风险评价准则
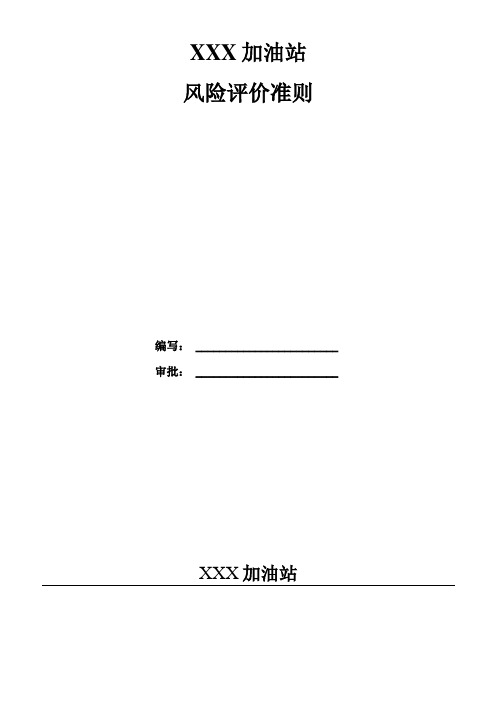
XXX加油站风险评价准则编写: ________________________ 审批: ________________________XXX加油站风险评价准则1危险等级划分JHA、PHA、SCL、LEC)1.1JHA采用风险度R=可能性L X后果严重性S的评价法,具体评价准则规定如下1.1.1评估危害及影响后果的严重性(S)判定准则,见表1表1后果的严重性(S)判定准则1.1.2评估危害发生的可能性(L)判定准则,见表2表2可能性(L)判定准则1.1.3风险度判定准则,见表3表3 风险度判定准则1.1.4险度与风险控制措施实施要求,见表4表4风险度与风险控制措施期限表1.2LEC法判定准则1.2.1发生的可能性(L)判断准则,见表551.2.2暴露于危险环境的频率判断准则,见表7表7人员暴露于危险环境的频繁程度(E)判别准则1.2.3事故后果(C)判断准则,见表8表8 事件后果(C)判别准则1.2.4风险值与风险等级的判断,见表8表8 风险值(D)及风险等级的确定20-70IV一般危险,需要注意一般风险2.1不符合职业健康安全法律、法规及标准的;2 对下列种情况,可直接定为不可容许风险。
2.2相关方有合理抱怨或要求的;2.3曾发生过事故,现仍无有效控制措施的;2.4直接观察到可能导致事故的危险源,且无适当控制措施的。
3评价依据的法规和文件1.1 国家法律1.《中华人民共和国安全生产法》(中华人民共和国主席令第70号)2.《中华人民共和国消防法》(中华人民共和国主席令第6号)3.《中华人民共和国职业病防治法》(中华人民共和国主席令第60号)4.《中华人民共和国气象法》(中华人民共和国主席令第23号)5.《中华人民共和国劳动法》(中华人民共和国主席令第28号)6.《中华人民共和国劳动合同法》(中华人民共和国主席令第65号)7.《中华人民共和国突发事件应对法》(中华人民共和国主席令第69号)1.2 行政法规1.《危险化学品安全管理条例》(国务院令第591号)2.《特种设备安全监察条例》(国务院令第549号)3.《工伤保险条例》(国务院令第586号)4.《建设工程安全生产管理条例》(国务院令第393号)5.《生产安全事故报告和调查处理条例》(国务院令第493号)3.3部门规章1.《关于加强化学危险品管理的通知》(国家环保总局、国家经贸委、公安部、交通部、国家质量技术监督局,环发[1999]296号)2.《关于加强建设项目安全设施“三同时”工作的通知》(国家发展和改革委员会、国家安全生产监督管理局,发改投资[2003]1346号)3.《危险化学品登记管理办法》(国家经贸委令第35号)4.《危险化学品经营许可证管理办法》(国家经贸委令第36号)5.《劳动防护用品监督管理规定》(国家安监总局令第1号)6.《生产经营单位安全培训规定》(国家安监总局令第3号)7.《危险化学品建设项目安全许可实施办法》(国家安全生产监督管理总局令第8号)8.《生产安全事故应急预案管理办法》(国家安监总局令第17号)9.《特种作业人员安全技术培训考核管理规定》(国家安监总局令第30号)10.《建设项目安全设施“三同时”监督管理暂行办法》(国家安监总局令第36号)11.《危险化学品重大危险源监督管理暂行规定》(国家安全生产监督管理总局令第40号)12.《危险化学品生产企业安全生产许可证实施办法》(国家安全生产监督管理总局令第41号)13.《安全生产培训管理办法》(国家安监总局令第44号)14.《关于开展重大危险源监督管理工作的指导意见》(安监管协调字[2004]56号)15.《危险化学品建设项目安全评价细则(试行)》(安监总危化[2007]255 号)16.国家安全监管总局关于印发《危险化学品建设项目安全设施目录(试行)》和《危险化学品建设项目安全设施设计专篇编制导则(试行)》的通知(安监总危化[2007]225号)17.《国家安全监管总局关于贯彻落实国务院<通知>精神强化安全生产综合监管工作的指导意见》(安监总管二[2010]203号)18.《国家安全监管总局办公厅关于推广应用阻隔防爆技术有关问题的通知》(安监总厅管三函[2009]231号)19.《国家安全监管总局工业和信息化部关于危险化学品企业贯彻落实<国务院关于进一步加强企业安全生产工作的通知>的实施意见》(安监总管三[2010]186号)20.《国家安全监管总局关于公布首批重点监管的危险化学品名录的通知》(安监总管三〔2011〕95号)21.《国家安全监管总局办公厅关于印发首批重点监管的危险化学品安全措施和应急处置原则的通知》(安监总厅管三〔2011〕142号)22.《国务院安委办公室进一步加强危险化学品安全生产工作的指导意见》(安委办[2008]26号)23.《国务院安委会办公室关于贯彻落实国务院<通知>精神进一步加强安全生产应急救援体系建设的实施意见》(安委办[2010]25号)24.《国务院办公厅关于进一步加强学校及周边建筑安全管理的通知》(国办发明电[2008]38号)25.《国务院关于进一步加强企业安全生产工作的通知》(国发[2010]23号)26.《仓库防火安全管理规则》(公安部令第6号)27.《机关、团体、企业、事业单位消防安全管理规定》(公安部令第61号)28.《道路危险货物运输管理规定》(交通部令[2005]第9号)29.关于印发《高危行业企业安全生产费用财务管理暂行办法》的通知(财企[2006]478号)30.《国务院安委会关于深入开展企业安全生产标准化建设的指导意见》(安委〔2011〕4号)31.《国家安全监管总局关于印发危险化学品从业单位安全生产标准化评审工作管理办法的通知》(安监总管三〔2011〕145号)3.4 地方法规及文件1.《云南省安全生产条例》(2007年11月29日经云南省十届人民代表大会常务委员会第32次会议通过,2008年1月1日起施行)2.《云南省实施〈危险化学品经营许可证管理办法〉的意见》(云安监管7[2003]48号)3.《云南省安全生产监督管理局关于危险化学品建设项目安全许可和试生产(使用)方案备案工作意见》(云安监管[2008]96号)4.《云南省安全生产应急预案管理办法(暂行)》(云南省安全生产监督管理局公告第8号)5.《云南省安全生产监督管理局云南省财政厅关于进一步加强安全生产风险抵押金管理有关问题的通知》(云安监管[2008]185号)6.《关于在全省高危行业推行人身意外伤害保险的通知》(云安监管[2008]102号)7.《云南省安全生产监督管理局关于成品油经营企业缴存安全生产风险抵押金有关问题的通知》(云安监管[2009]91号)8.《云南省安全生产监督管理局关于推广应用阻隔防爆技术有关问题的通知》(云安监[2010]118号)9.《云南省人民政府贯彻落实国务院关于进一步加强企业安全生产工作通知的实施意见》(云政发[2010]157号)10.《云南省人民政府办公厅关于进一步加强危险化学品企业安全生产工作的实施意见》(云政办发[2011]112号)3.5 国家标准1.《汽车加油加气站设计与施工规范》(GB50156-2012版)2.《危险化学品经营企业开业条件和技术要求》(GB18265-2000)3.《常用化学危险品贮存通则》(GB15603-1995)4.《化学品危险性评价通则》(GB/T22225-2008)5.《建筑设计防火规范》(GB50016-2006)6.《危险化学品重大危险源辨识》(GB18218-2009)7.《建筑物防雷设计规范》(GB50057-2010)8.《建筑抗震设计规范》(GB500n-2010)9.《防止静电事故通用导则》(GB12158-2006)10.《工业企业总平面设计规范》(GB50187-2012)11.《消防安全标志设置要求》(GB15630-1995)12.《消防安全标志》(GB13495-1992)13.《安全标志及其使用导则》(GB2894-2008)14.《危险货物品名表》(GB12268--2012)15.《化学品分类、警示标签和警示性说明安全规范急性毒性》(GB20592-2006)16.《石油化工企业设计防火规范》(GB50160-1992, 2008年版)17.《石油化工企业可燃气体和有毒气体检测报警设计规范》 (SH3063-1999)18.《建筑灭火器配置设计规范》(GB50140-2005)19.《爆炸和火灾危险环境电力装置设计规范》(GB50058-1992)20.《石油与石油设施雷电安全规范》(GB15599-2009)21.《易燃易爆性商品储藏养护技术条件》(GB17914-1999)22.《腐蚀性商品储藏养护技术条件》(GB17915-1999)23.《毒害性商品储藏养护技术条件》(GB17916-1999)24.《职业性接触毒物危害程度分级》(GBZ230-2010)25.《工业金属管道工程施工及验收规范》(GB50235-1997)26.《企业职工伤亡事故分类》(GB6441-1986)27.《生产过程危险和有害因素分类与代码》(GB/T13861-2009)28.《供配电系统设计规范》(GB50052-2009)29.《油罐区防火堤设计规范》(GB50351-2005)30.《液体石油产品静电安全规程》(GB13348-2009)3.6 行业标准1.《安全评价通则》(AQ8001-2007)2.《安全验收评价导则》(AQ8003-2007)3.《加油站作业安全规范》(AQ3010-2007)4.《危险场所电气安全防爆规范》(AQ3009-2007)5.《危险化学品储罐区作业安全通则》(AQ3018-2008)6.《生产经营单位安全生产事故应急预案编制导则》(AQ/T9002-2006)7.《石油化工企业安全管理体系实施导则》(AQ/T3012-2008)8.《化工企业安全卫生设计规定》(HG20571-1995)9.《石油化工静电接地设计规范》(SH3097-2000)10.《钢质管道及储罐腐蚀控制工程设计规范》(SY0007-1999)11.《汽车运输、装卸危险货物作业规程》(JT618-2004)12.《油罐清洗安全技术规程》(Q/SH039-013-1988)13.《现场设备、工业管道焊接工程施工规范》(GB50236-2011)14.《钢制化工容器结构设计规定》(HG/T20583-2011)15.《钢制化工容器制造技术要求》(HG/T20584-2011)16.《钢制焊接常压容器》(NB/T47003.1-2009)3.7 企业的安全管理标准、技术标准、安全生产方针和目标等.企业的安全生产管理标准:《加油站安全标准化手册》《风险评价管理制度》安全生产管理方针:安全第一预防为主以人为本综合治理安全生产控制指标:(1)死亡、重伤、轻伤事故为零;(2)火灾、爆炸和环境污染事故为零;(3)危化品泄漏事故为零;(4)职业病危害事故为零;(5)作业场所职业危害因素检测合格率100%;(6)人员持证上岗率达到100%;(7)事故隐患整改率大于95%。
2018年风险评价设计报告书(JHA、SCL表)

设备科安全风险评价报告书一、目的为规范部门风险管理工作,识别和评价作业过程中的危险有害因素,消除或减少事故危害,降低安全风险。
由部门风险评价领导小组负责进行危害因素识别和风险评估工作。
二、评价范围评价小组从部门工作的全过程,对所有可能造成危害和影响的活动进行了工作危害分析(JHA)和安全检查表分析(SCL),将部门部分作业过程及设备设施存在的风险进行逐一排查、识别。
三、评价组组长:李进民成员:张坤鸿、王法军、李伟国、黄尊超、胡云来四、评价方法部门发动员工参与风险评估,专业技术人员、管理人员与员工一起参与风险评估过程,采用了工作危害分析(JHA)和安全检查表(SCL)两种基本方法,进行风险评估时的程序如下:1、作业危害分析主要采用工作危害分析(JHA),由各单位的评价小组中岗位操作人员、班长、专业技术人员对本岗位的所有作业活动列出清单,并进行工作危害分析(JHA),做完成后先经科室负责人审查修改,修改完成后,上报部门评价组进行会审,对不合格者提出修改意见返回基层单位再进行修改,部门通过后上报公司风险评价组进行会审和确定。
2、设备设施的危害分析主要采取安全检查表(SCL)分析,由各单位的评价小组管理人员、技术人员和岗位操作人员列出设备设施清单,按安全检查表(SCL)分析进行,做完成后先经科室负责人审查修改,修改完成后,上报部门评价组进行会审,对不合格者提出修改意见返回基层单位再进行修改,部门通过后上报公司风险评价组进行会审和确定。
五、评价过程见部门的工作危害分析(JHA)表、安全检查(SCL)分析表六、风险信息的更新1、在下列情况下安全检查表(SCL)分析记录和工作危害分析(JHA)记录进行更新:---工艺指标或操作规程变更时;---新的或变更的法律、法规或其他要求;---有新项目---有因为事故、事件或其他而发生不同的认识;---其他变更。
2、如果没有上述变化时,部门一年进行一次评审或检查风险识别的结果。
八大风险评价方法简介(JHA、SCL、LEC等)

然后定性或定量的分析事件发生的各种可能途径及发生 的概率,找出避免事故发生的各种方案并优选出最佳安 全对策。
故障树分析的基本程序
1.熟悉系统:要详细了解系统状态及各种参数,绘出工艺流程图或布置图。 2.调查事故:收集事故案例,进行事故统计,设想给定系统可能发生的事
级排定次序,以便按计划处理。
5)制定预防事故发生的安全对策措施
危险性等级划分表
级别 I II
III IV
危险程度
可能导致的后果
安全的 不会造成人员伤亡及系统损坏
临界的 危险的
处于事故的边缘状态,暂时还不致于造 成人员伤亡、系统损坏或降低系统性能, 但应予以排除或采取控制措施。
会造成人员伤亡和系统损坏,要立即采 取防范对策措施。
严格监控 严格监控 严格监控 严格监控 严格监控
6
储存
剧毒品被盗、 人员中毒,火灾、 1 1 1
未按要求存放,
爆炸
通风不够
严格监控
7
储存
不按五距储存
火灾、爆炸
221
增加库房
2.安全检查表分析
(Safety Checklist Analysis,缩写SCA)是 依据相关的标准、规范,对工程、系统中已知 的危险类别、设计缺陷以及与一般工艺设备、 操作、管理有关的潜在危险性和有害性进行判 别检查。 为了避免检查项目遗漏,事先把检查对象分割 成若干系统,以提问或打分的形式,将检查项 目列表,这种表就称为安全检查表。 它是系统安全工程的一种最基础、最简便、广 泛应用的系统危险性评价方法。
分
析 例
5.失效模式与影响分析
(failure modes and effects analysis)简称 FMEA ,由失效模式(FM)和影响分析(EA)两部分 组成.
风险评价方法(SCL、JHA、LEC)说明与举例
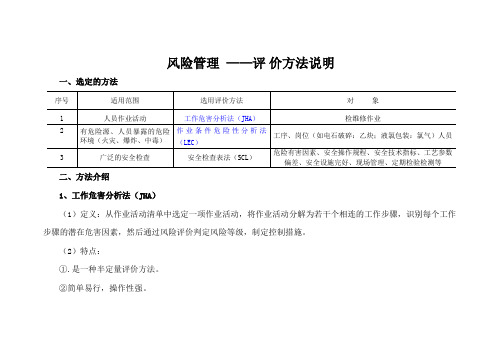
风险管理——评价方法说明一、选定的方法二、方法介绍1、工作危害分析法(JHA)(1)定义:从作业活动清单中选定一项作业活动,将作业活动分解为若干个相连的工作步骤,识别每个工作步骤的潜在危害因素,然后通过风险评价判定风险等级,制定控制措施。
(2)特点:①.是一种半定量评价方法。
②简单易行,操作性强。
③分解作业步骤,比较清晰。
④有别于掌握每一步骤的危险情况,不仅能分析作业人员不规范的危害,而且能分析作业现场存在的潜在危害(客观条件)。
2、作业条件危险性分析法(LEC)(1)定义:作业条件危险性评价法是一种简便易行的衡量人们在某种具有潜在危险的环境中作业的危险性的半定量评价方法。
该方法以与系统风险有关的三种因素指标值之积来评价系统风险的大小,并将所得作业条件危险性数值与规定的作业条件危险性等级相比较,从而确定作业条件的危险程度。
作业条件危险性评价法(LEC法)是以所评价的环境与某些作为参考环境的对比为基础,将作业条件的危险性作因变量(D),事故或危险事件发生的可能性(L)、暴露于危险环境的频率(E)及危险严重程度(C)为自变量,确定了它们之间的函数式,根据实际经验,给出了3个自变量的各种不同情况的分数值,采取对所评价的对象根据情况进行“打分”的办法,然后根据公式计算出其危险性分数值,再在按经验将危险性分数值划分的危险程度等级表查出其危险程度的一种评价方法。
(2)特点:①是一种半定量评价方法。
②简单易行,操作性强,危险程度的级别划分比较清楚、醒目。
③有利于掌握企业内部危险点的危险情况,有利于促进改措施的实施。
④缺点:由于它主要是根据经验来确定3个因素的分数值及划定危险程度等级,因此具有一定的局限性,只能作为作业的局部评价,不能普遍适用。
3、安全检查表方法(SCL)(1)定义:安全检查表分析法是利用检查条款按照相关的标准规范等对已知的危险类别、设计缺陷和与一般工艺设备、操作、管理相关的潜在危险性和有害性进行判别检查。
JHA及SCL风险评价方法讲解1

JHA 及 SCL 风险评价方法作业危害分析(Job Hazard Analysis,JHA)又称作业安全分析(Job Safety Analysis,JSA)、作业危害分解(Job Hazard Breakdown, JHB),是一种定性风险分析方法。
实施作业危害分析,能够识别作业中潜在的危害,确定相应的工程措施,提供适当的个体防护装置,以防止事故发生,防止人员受到伤害。
此方法合用于工艺操作,设备设施检修等。
作业危害分析将对作业活动的每一步骤进行分析,从而辨识潜在的危害并制定安全措施作业危害分析的主要步骤是:1、确定(或者选择)待分析的作业;2、将作业划分为一系列的步骤;3、辨识每一步骤的潜在危害;4、确定相应的预防措施。
划分的作业活动步骤不能太笼统, 步骤划分也不宜太细,以致浮现许多的步骤。
根据经验,一项作业活动的步骤普通不超过 10 项,要保持各个步骤正确的顺序。
为了辨识危害,需要对作业活动作进一步的观察和分析。
辨识危害应该思量的问题是:可能发生的故障或者错误是什么?其后果如何?事故是怎样发生的?其他的影响因素有哪些?发生的可能性?以下是危害辨识的部份内容:·是否穿着个体防护服或者配戴个体防护器具?·操作环境、设备、地槽、坑及危(wei)险的操作是否有有效的防护?·维修设备时,是否对相互连通的设备采取了隔离?·是否有能引起伤害的固定物体,如锋利的设备边缘?·操作者能否触及机器部件或者机器部件之间操作?·操作者能否受到运动的机器部件或者挪移物料的伤害?·操作者是否会处于失去平衡的状态?·操作者是否管理着带有潜在危(wei)险的装置?·操作者是否需要从事可能使头、脚受伤或者被扭伤的活动(往复运动的危害)?·操作者是否会被物体冲撞(或者撞击)到机器或者物体?工作危害分析(JHA)记录表(例如)单位:天宝日期: 3 月 18 日工作岗位:脱介筛工作任务:维修脱介筛序号1 2 3 4 5工作步骤准备工作准备检修工具穿戴劳保用品工具使用系统隔离危害或者潜在事件方案不全、识别不清工具不全,有缺陷不穿劳保用品工具不防爆碰撞产生火花管道未隔断泄漏,静电接地失效主要后果发生人身事故皮外伤皮外伤着火爆炸着火爆炸以往发生频率及现有安全控制措施 L发生频率曾经发生偶尔或者一年以上发生偶尔或者一年以上发生从未发生从未发生管理措施执行检维修规程有操作规程,而且严格执行有操作规程,而且严格执行有操作规程,而且严格执行有检修规程,而且严格执行员工胜任程度持证上岗胜任,但偶尔出差错胜任,但偶尔出差错胜任胜任安全措施现场监护有,偶尔失去作用或者出差错有,偶尔失去作用或者出差错现场监管现场监管,加盲板32233S32255R9441515风险等级cbbdd建议改进措施CBBDD责任人刘艳波刘艳波刘艳波刘艳波刘艳波6 7 8 9检查绳套调试运转气密性试验绳套拴挂不牢、绳径小导致吊件坠落不试车,设备损坏有轻微泄漏摔坏设备造成≥2 万元损失,伤人造成部份丧失劳动能力误工 2 天导致真空度降低,不能交付生产曾经发生偶尔或者一年以上发生曾经发生有、偶尔不执行有操作规程,而且严格执行有、偶尔不执行胜任,但偶尔出差错胜任,但偶尔出差错胜任,但偶尔出差错有,偶尔失去作用或者出差错有,偶尔失去作用或者出差错有,偶尔失去作用或者出差错222433866bbbBBB刘艳波刘艳波刘艳波风险度 R :a) 轻微的(L×S=1~3);b) 可承受的(L×S=4~8);c) 中等的(L×S=9~12);d) 重大的(L×S=15~16);e) 不可承受的 (L×S=20~25) 建议的改进措施: A—表示轻微的,不必采取措施; B—表示可承受的,应维持现状、保持记录,但要保持检查或者测量; C—表示中等的,应制定管理制度、规定、规程进行控制; D—表示重大的,应制定目标、指标、管理方案,限期管理; E—表示不可承受的,应即将采取隐患管理措施;所谓安全检查表,就是为系统地辨识和诊断某一系统的安全状况而事先拟好的问题清单。
风险评价方法(SCL、JHA、LEC)说明与举例

危害发生
可能性/L
危害后果
严重性/S
风险度
R=L×S
建议改进/控制
风险措施
分析人员:日期:审核人:日期:审定人:日期:
作业条件危险性分析(LEC)评价表
部门:工段:工作任务:编号:№:
序号
工作步骤
危害(人、物、作业环境、管理)
主要后果
以往事故发生频率
现有安全控制措施
危害发生
可能性/L
2
危害一旦发生能及时发现,并定期进行监测,或现场有防范控制措施,并能有效执行,或过去偶尔发生危险事故或事件。
1
有充分、有效的防范、控制、监测、保护措施,或员工安全卫生意识相当高,严格执行操作规程。极不可能发生事故或事件。
1.2.2危害后果严重性S判定准则
表2
S值
人员
财产损失/万元
停车
其它
5
造成人员死亡
二、方法介绍
1、工作危害分析法(JHA)
(1)定义:从作业活动清单中选定一项作业活动,将作业活动分解为若干个相连的工作步骤,识别每个工作步骤的潜在危害因素,然后通过风险评价判定风险等级,制定控制措施。
(2)特点:
①.是一种半定量评价方法。
②简单易行,操作性强。
③分解作业步骤,比较清晰。
④有别于掌握每一步骤的危险情况,不仅能分析作业人员不规范的危害,而且能分析作业现场存在的潜在危害(客观条件)。
风险管理——评价方法说明
一、选定的方法
序号
适用范围
选用评价方法
对 象
1
人员作业活动
工作危害分析法(JHA)
检维修作业
2
有危险源、人员暴露的危险环境(火灾、爆炸、中毒)
JHA及SCL风险评价方法讲解(参考)

JHA及SCL风险评价方法讲解一、作业危害分析(JHA)介绍作业危害分析(Job Hazard Analysis,JHA)又称作业安全分析(Job Safety Analysis,JSA)、作业危害分解(Job Hazard Breakdown, JHB),是一种定性风险分析方法。
实施作业危害分析,能够识别作业中潜在的危害,确定相应的工程措施,提供适当的个体防护装置,以防止事故发生,防止人员受到伤害。
此方法适用于工艺操作,设备设施检修等。
作业危害分析将对作业活动的每一步骤进行分析,从而辨识潜在的危害并制定安全措施作业危害分析的主要步骤是:1、确定(或选择)待分析的作业;2、将作业划分为一系列的步骤;3、辨识每一步骤的潜在危害;4、确定相应的预防措施。
划分的作业活动步骤不能太笼统, 步骤划分也不宜太细,以致出现许多的步骤。
根据经验,一项作业活动的步骤一般不超过10项,要保持各个步骤正确的顺序。
为了辨识危害,需要对作业活动作进一步的观察和分析。
辨识危害应该思考的问题是:可能发生的故障或错误是什么?其后果如何?事故是怎样发生的?其他的影响因素有哪些?发生的可能性?以下是危害辨识的部分内容:·是否穿着个体防护服或配戴个体防护器具?·操作环境、设备、地槽、坑及危险的操作是否有有效的防护?·维修设备时,是否对相互连通的设备采取了隔离?·是否有能引起伤害的固定物体,如锋利的设备边缘?·操作者能否触及机器部件或机器部件之间操作?·操作者能否受到运动的机器部件或移动物料的伤害?·操作者是否会处于失去平衡的状态?·操作者是否管理着带有潜在危险的装置?·操作者是否需要从事可能使头、脚受伤或被扭伤的活动(往复运动的危害)?·操作者是否会被物体冲撞(或撞击)到机器或物体?·操作者是否会跌倒?·操作者是否会由于提升、拖拉物体或运送笨重物品而受到伤害?·作业时是否有环境因素的危害——粉尘、化学物质、放射线、电焊弧光、热、高噪音?工作危害分析(JHA)记录表单位:二车间日期:3月18日风险度R :a) 轻微的(L×S=1~3);b) 可承受的(L×S=4~8);c) 中等的(L×S=9~12);d) 重大的(L×S=15~16);e) 不可承受的(L×S=20~25)建议的改进措施:A—表示轻微的,不必采取措施;B—表示可承受的,应维持现状、保持记录,但要保持检查或测量;C—表示中等的,应制定管理制度、规定、规程进行控制;D—表示重大的,应制定目标、指标、管理方案,限期治理;E—表示不可承受的,应立即采取隐患治理措施;二、安全检查表分析(SCL)所谓安全检查表,就是为系统地辨识和诊断某一系统的安全状况而事先拟好的问题清单。
常用风险评价方法

附件二常用风险评价方法一、工作危害分析法(JHA法)1、将一项作业活动分解成若干相连的过程;2、对每个过程的所有潜在风险进行识别;3、针对每个风险制订控制措施。
具体见下表:工作危害分析表作业任务:工作地点:分析人员:日期:二、安全检查表分析方法(SCL法)1、先对一个检查对象进行分解,确定需要检查的若干小项;2、针对每一个小项,查找有关资料,确定检查标准;3、针对每一个检查标准,确定未达标的后果;4、针对每一个后果,确定现有的的控制措施;5、针对每一项现有的控制措施,制订改进控制措施。
具体见下表:安全检查分析记录表检查工序:检查对象:分析人员:日期:三作业条件危险性分析(LEC法)对具有潜在危险性的作业条件,影响危险性(D)的主要因素有3个:①发生事故或危险事件的可能性,②暴露于这种危险环境的情况,③事故一旦发生可能产生的后果。
D = L× E× C式中:D —作业条件的危险性,L —事故或危险事件发生的可能性,E —暴露于危险环境中的频率,C —发生事故或危险事件的可能结果。
(1)发生事故或危险事件的可能性(L)如下表:(2)暴露于危险环境的频率(E)如下表:(3)发生事故或危险事件的可能结果(C)如下表:(4)危险等级划分(D)如下表:四、预先危险性分析(PHA法)对各工艺环节中评价单元存在的危险、有害因素进行预先危险性分析,强调尽可能覆盖整个系统,涉及所有存在的危险类别、危险状态、存在条件、事故后果等,特别适用于工程初步设计阶段的概略分析。
其主要功能有:大体识别与系统有关的主要危险;鉴别产生危险的原因;估计事故出现对系统产生的影响;对已经识别的危险进行分级;提出消除或控制危险性的措施。
分析步骤●对系统的生产目标、工艺过程以及操作条件和周围环境进行充分地调查了解;●收集以往的经验和同类生产中发生过的事故情况,分析危险、有害因素和触发事件;●推测可能导致的事故类型和危险程度;●确定危险、有害因素可能产生后果的危险等级;●制定相应的安全措施。
JHA及SCL风险评价方法讲解参考
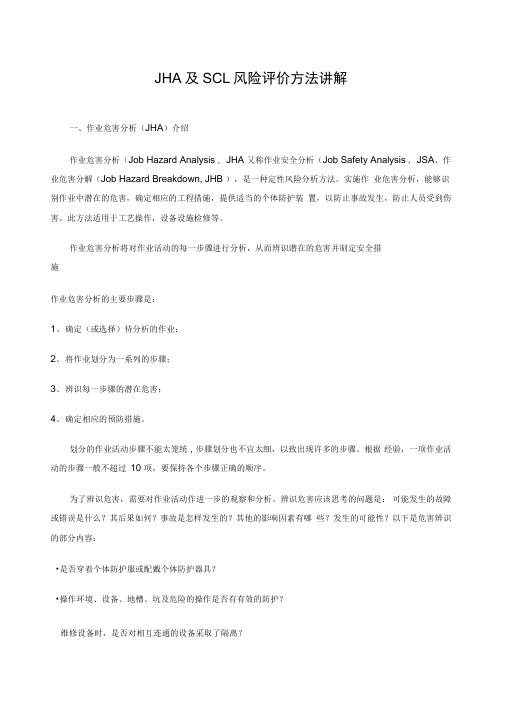
JHA及SCL风险评价方法讲解一、作业危害分析(JHA)介绍作业危害分析(Job Hazard Analysis , JHA 又称作业安全分析(Job Safety Analysis , JSA、作业危害分解(Job Hazard Breakdown, JHB ),是一种定性风险分析方法。
实施作业危害分析,能够识别作业中潜在的危害,确定相应的工程措施,提供适当的个体防护装置,以防止事故发生,防止人员受到伤害。
此方法适用于工艺操作,设备设施检修等。
作业危害分析将对作业活动的每一步骤进行分析,从而辨识潜在的危害并制定安全措施作业危害分析的主要步骤是:1、确定(或选择)待分析的作业;2、将作业划分为一系列的步骤;3、辨识每一步骤的潜在危害;4、确定相应的预防措施。
划分的作业活动步骤不能太笼统, 步骤划分也不宜太细,以致出现许多的步骤。
根据经验,一项作业活动的步骤一般不超过10 项,要保持各个步骤正确的顺序。
为了辨识危害,需要对作业活动作进一步的观察和分析。
辨识危害应该思考的问题是:可能发生的故障或错误是什么?其后果如何?事故是怎样发生的?其他的影响因素有哪些?发生的可能性?以下是危害辨识的部分内容:•是否穿着个体防护服或配戴个体防护器具?•操作环境、设备、地槽、坑及危险的操作是否有有效的防护?维修设备时,是否对相互连通的设备采取了隔离?-是否有能引起伤害的固定物体,如锋利的设备边缘?-操作者能否触及机器部件或机器部件之间操作?-操作者能否受到运动的机器部件或移动物料的伤害?-操作者是否会处于失去平衡的状态?-操作者是否管理着带有潜在危险的装置?-操作者是否需要从事可能使头、脚受伤或被扭伤的活动(往复运动的危害)?-操作者是否会被物体冲撞(或撞击)到机器或物体?-操作者是否会跌倒?•操作者是否会由于提升、拖拉物体或运送笨重物品而受到伤害?•作业时是否有环境因素的危害——粉尘、化学物质、放射线、电焊弧光、热、高噪音?工作危害分析(JHA记录表单位:二车间日期:3月18日工作岗位:酯化工作任务:修酯化釜顶冷凝器风险度R : a)轻微的(L X S=1〜3); b)可承受的(L X S=4〜8); c)中等的(L X S=412); d)重大的(L X S=15-16); e)不可承受的(L XS=2L25)建议的改进措施:A—表示轻微的,不必采取措施;B—表示可承受的,应维持现状、保持记录,但要保持检查或测量;C—表示中等的,应制定管理制度、规定、规程进行控制;D—表示重大的,应制定目标、指标、管理方案,限期治理;E—表示不可承受的,应立即采取隐患治理措施;以便进行检查,避免漏检,这种表就叫安全检查表。
- 1、下载文档前请自行甄别文档内容的完整性,平台不提供额外的编辑、内容补充、找答案等附加服务。
- 2、"仅部分预览"的文档,不可在线预览部分如存在完整性等问题,可反馈申请退款(可完整预览的文档不适用该条件!)。
- 3、如文档侵犯您的权益,请联系客服反馈,我们会尽快为您处理(人工客服工作时间:9:00-18:30)。
风险评价报告书一、目的
为规范部门风险管理工作,识别和评价作业过程中的危险有害因素,消除或减少事故危害,降低安全风险。
由部门风险评价领导小组负责进行危害因素识别和风险评估工作。
二、评价范围
评价小组从部门工作的全过程,对所有可能造成危害和影响的活动进行了工作危害分析(JHA)和安全检查表分析(SCL),将部门部分作业过程及设备设施存在的风险进行逐一排查、识别。
三、评价组
组长:XX(管理人员)
成员:XX(工会代表)、XX(专业技术人员)、XX(员工代表)、XX、XX……
四、评价方法
部门发动员工参与风险评估,专业技术人员、管理人员与员工一起参与风险评估过程,采用了工作危害分析(JHA)和安全检查表(SCL)两种基本方法,进行风险评估时的程序如下:
1、作业危害分析主要采用工作危害分析(JHA),由各单位的评价小组中岗位操作人员、班长、专业技术人员对本岗位的所有作业活动列出清单,并进行工作危害分析(JHA),做完成后先经科室负责人审查修改,修改完成后,上报部门评价组进行会审,对不合格者提出修改意见返回基层单位再进行修改,部门通过后上报公司风险评价组进
行会审和确定。
2、设备设施的危害分析主要采取安全检查表(SCL)分析,由各单
位的评价小组管理人员、技术人员和岗位操作人员列出设备设施清单,按安全检查表(SCL)分析进行,做完成后先经科室负责人审查修改,修改完成后,上报部门评价组进行会审,对不合格者提出修改意见返回基层单位再进行修改,部门通过后上报公司风险评价组进行会审
和确定。
.
五、评价过程
见部门的
工作危害分析(JHA)表
安全检查(SCL)分析表
六、风险信息的更新
1、在下列情况下安全检查表(SCL)分析记录和工作危害分析(JHA)记录进行更新:
---工艺指标或操作规程变更时;
---新的或变更的法律、法规或其他要求;
---有新项目
---有因为事故、事件或其他而发生不同的认识;
---其他变更。
2、如果没有上述变化时,部门一年进行一次评审或检查风险识别的
结果。
七、评价准则
使用推荐的风险评价方法,部门/科室/班组开展风险评价工作,按照以下方法开展风险等级划分;
风险(R)=可能性(L)×后果严重性(S)
1)危害发生的可能性L判定准则:
表1:危害发生可能性L判定
等级标准
在现场没有采取防范、监测、保护、控制措施,或危害的发生不能被发现(没有监5 测系统),或在正常情况下经常发生此类事故或事件。
危害的发生不容易被发现,现场没有检测系统,也未发生过任何监测,或在现场有4
控制措施,但未有效执行或控制措施不当,或危害常发生或在预期情况下发生。
没有保护措施(如没有保护装置、没有个人防护用品等),或未严格按操作程序执行,或危害的发生容易被发现(现场有监测系统),或曾经作过监测,或过去曾经发生类似事3
故或事件,或在异常情况下类似事故或事件。
危害一旦发生能及时发现,并定期进行监测,或现场有防范控制措施,并能有效执2 行,或过去偶尔发生事故或事件。
有充分、有效的防范、控制、监测、保护措施,或员工安全卫生意识相当高,严格1
执行操作规程。
极不可能发生事故或事件。
判定准则:S)危害后果严重性2.
S判定
停公司形人万部分装置>套>50死或设备停国内影
套装置停工、行业内、>25丧失劳动能内影设备停套装置停工或截肢、骨折、听地区影>10丧失、慢性轻微受伤、间受影响不大,几<10不舒边范不停无伤没有停无损受损3)风险等级R判定准则及控制措施:
表3:风险等级判定准则及控制措施R
风险度等级应采取的行动/控制措施实施期限
在采取措施降低危害前,不能继续作业,21~25立刻巨大风险对改进措施进行评估采取紧急措施降低风险,建立运行控制程15~16立即或近期整改重大风险序,定期检查、测量及评估可考虑建立目标、建立操作规程,加强培6~12 2年内治理中等训及沟通有条件、有经费时可考虑建立操作规程、作业指导书但需定1~5可接受期检查或无需采用控制措施,但需保存记录治理注:R=L×S—危险性或风险度(危险性分值)
L——发生事故的可能性大小(发生事故的频率)
S——一旦发生事故会造成的损失后果。
4)风险评估表
严重性 1 5
4
3
2
可能性5 3 2 1 4 1
10 4 2 2 6 8
15 3 3 6 12 9
20 12 8 4 4 16
25
20
15
10
5
5
八、评价结果:主要危害因素、风险及控制措施
依据安全检查表(SCL)和工作危害分析(JHA)为工具,以两个过程中的危害发生的可能性L及危害后果严重性S的综合评定结果R,按风险等级判定准则及控制措施评出分厂生产管理过程中的风险控
制清单。
见附件:风险控制清单
作业清单(含JHA表)
设备设施清单(含SCL表)
评估小组:(参加人员手工签名)
XX部门
2010.5.20
安全检查(SCL)表表5-1
单位:
日期:
RS风险等级进措施
工作危害分析(JHA)记录表表5- 2
日期:位:单
工作任务:工作岗位:
以往发生频率及现有安全控制措施建议改风险等级R危害或潜在事件主要后果 L序号S工作步骤进措施安全设施管理措施员工胜任程度发生频率
L
预先危险分析(PHA)记录表表5- 3
单位:
分析对象:
分析人员及岗位:
作业活动清单表5- 4
设备设施清单表5- 5 №:
风险清单表5- 6
№:
重大风险控制清单表5- 7 单位:年月日。