预坚膜塑料模具钢材的计算机辅助成分设计2
国家科学技术进步奖二等奖 注塑成型模具及制品设计与生产过程的计算机集成技术

国家科学技术进步奖二等奖注塑成型模具及制品设计与生产过程的计算机集成技术目录1. 引言1.1 背景和意义1.2 结构概述1.3 目的2. 注塑成型模具及制品设计与生产过程的计算机集成技术2.1 模具设计与制造的传统方法2.2 计算机辅助设计在模具设计中的应用2.3 计算机辅助制造在模具制造中的应用3. 注塑成型模具及制品生产过程中的计算机集成技术应用案例分析3.1 案例一:优化注塑工艺参数设计3.2 案例二:提高模具加工精度和效率3.3 案例三:实现生产过程的全面监控与管理4. 注塑成型模具及制品设计与生产过程的计算机集成技术带来的影响和挑战4.1 影响方面4.2 挑战方面5. 结论5.1 成果总结5.2 发展前景展望1. 引言1.1 背景和意义随着科技的不断发展,计算机技术在各个领域的应用变得越来越广泛。
在制造业中,注塑成型模具及制品设计与生产过程一直是一个关键环节,对产品质量和生产效率有着重要影响。
然而,传统的模具设计与制造方法存在着很多问题,如设计周期长、生产效率低下和加工精度难以保证等。
为了有效解决这些问题,我们需要引入计算机集成技术来改进注塑成型模具及制品的设计与生产过程。
本文将介绍国家科学技术进步奖二等奖的研究成果——注塑成型模具及制品设计与生产过程的计算机集成技术。
通过利用计算机辅助设计和计算机辅助制造技术,我们可以实现模具设计和制造过程的数字化、自动化和智能化。
这种集成技术不仅能够提高产品开发周期,还可以优化工艺参数设计、提高模具加工精度和效率,并实现生产过程的全面监控与管理。
1.2 结构概述本文主要分为以下几个部分:•第2部分:注塑成型模具及制品设计与生产过程的计算机集成技术。
我们将介绍传统的模具设计和制造方法,并详细讨论计算机辅助设计和计算机辅助制造在模具设计和制造中的应用。
•第3部分:注塑成型模具及制品生产过程中的计算机集成技术应用案例分析。
我们将通过三个案例来展示这种集成技术在实际生产中的应用,包括优化注塑工艺参数设计、提高模具加工精度和效率,以及实现生产过程的全面监控与管理。
计算机辅助塑料注射模具设计
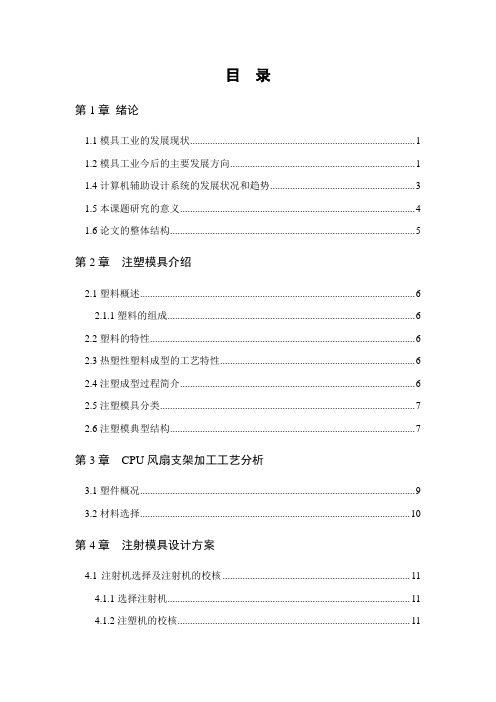
目录第1章绪论1.1模具工业的发展现状 (1)1.2模具工业今后的主要发展方向 (1)1.4计算机辅助设计系统的发展状况和趋势 (3)1.5本课题研究的意义 (4)1.6论文的整体结构 (5)第2章注塑模具介绍2.1塑料概述 (6)2.1.1塑料的组成 (6)2.2塑料的特性 (6)2.3热塑性塑料成型的工艺特性 (6)2.4注塑成型过程简介 (6)2.5注塑模具分类 (7)2.6注塑模典型结构 (7)第3章CPU风扇支架加工工艺分析3.1塑件概况 (9)3.2材料选择 (10)第4章注射模具设计方案4.1注射机选择及注射机的校核 (11)4.1.1选择注射机 (11)4.1.2注塑机的校核 (11)4.2成型零部件设计 (13)4.2.1成型零部件分类及结构 (13)4.2.2 成型尺寸计算 (14)4.3浇注系统设计 (16)4.3.1浇注系统的作用 (16)4.3.2对浇注系统设计的具体要求 (16)4.3.3浇注系统的设计 (16)4.4侧向分型与抽心机构设计 (17)4.4.1 侧向分型与抽芯机构的分类 (18)4.4.2 侧向分型与抽芯机构的设计 (18)4.5注塑模导向机构设计 (20)4.5.1 导向机构的功能及其分类 (20)4.5.2设计要点及设计方案 (20)4.6顶出机构 (21)4.6.1顶出机构的分类 (21)4.6.2顶杆脱模机构的设计要点 (22)4.6.3设计采用方案 (22)4.7复位装置 (23)4.8冷却系统介绍 (23)4.9模具总体结构分析 (24)4.10模具用钢 (25)4.10.1塑料模具用钢的必要条件 (26)4.10.2选择钢材的条件 (26)4.10.3注塑模具常用材料 (26)4.11模具的装配与调试 (26)4.11.1 装配基准的确定 (26)4.11.2 塑料模的装配顺序 (27)结论 (28)参考文献 (29)致谢 (30)第1章绪论模具制造是国家经济建设中的一项重要产业,振兴和发展模具工业,日益受到世界各国的重视和关注。
计算机辅助模具设计(PRE)
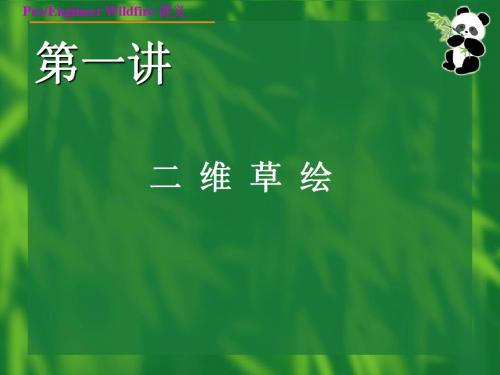
Pro/Engineer Wildfire 讲义
(3) 2.总结
(4 )
创建一个拉伸特征,首先需要确定草图面,即绘 制截面的平面,然后,进入草绘环境去绘制截面;最 后,指定特征的生长方向和特征的高度,系统即可完 成特征的创建。其中草图面的指定和截面的绘制是关 键。截面的形状决定了拉伸特征的外形,而草图面和 特征生长方向则决定了特征的空间位置。
完成后的圆
原始 圆弧 伸缩线 终点
完成圆 的绘制
绘制同心圆弧
Pro/Engineer Wildfire 讲义
⑷. 圆弧(续)
移动光标 圆弧 起点 圆弧 终点
圆弧中心 伸缩线
完成圆弧 的绘制
利用中心/端点画弧
终点 伸缩线 完成锥 形圆弧 的绘制
起点
绘制锥形圆弧
Pro/Engineer Wildfire 讲义
创建基础特征
Pro/Engineer Wildfire 讲义
学习目的:
掌握三维建模的基本步骤 了解基础特征的种类和作用 掌握创建基础特征的方法
学习重点:
如何使用基础特征的创建命令 理解基础特征的重要意义
Pro/Engineer Wildfire 讲义
经验者说:正确创建基础特征是三维建模的第一步
Pro/Engineer Wildfire 讲义
三、建立旋转特征
旋转工具就是让一个剖面沿着旋转由旋转,剖面 所扫过的体积就构成了旋转特征,在创建旋转特征的 时候,需要指定的特征参数包括剖面所在草绘平面、 剖面形状、旋转方向、旋转角度。 与拉伸工具一样,Pro/E把与旋转特征相关的命令 都集中在旋转工具操控板中。同样有两种打开旋转工 具操控板。
步骤: 1. 开启命令 2. 绘制2D剖面 3. 定义拉伸方向 和拉伸深度 4. 生成特征
注塑机计算机辅助模块化设计方法
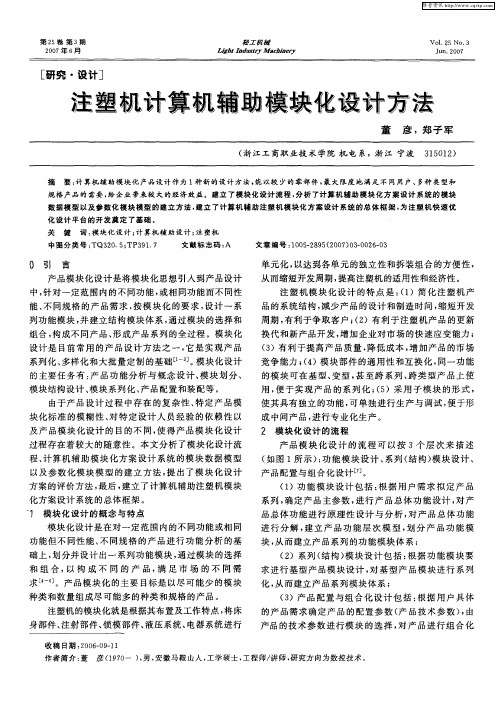
单 元化 , 以达 到各单 元 的独立 性 和拆 装组 合 的方便 性 , 从 而缩 短开发周期 , 提高注塑机 的适用性 和经济性 。
注 塑 机 模 块化 设计 的特 点 是 : 1 ( )简化 注 塑 机 产 品的 系统结构 , 减少 产 品的设 计 和制造 时 间 , 短开 发 缩 周 期 , 利 于争取 客 户 ;2 有 ( )有利 于 注塑 机产 品的更新 换 代 和新产 品开发 , 加企业 对 市场 的快 速应 变能力 ; 增
和 组 合 , 构 成 不 同 的 产 品 , 足 市 场 的 不 同 需 以 满
求 [ 。产 品模 块化 的主要 目标 是 以尽 可能 少 的模 块 4 ] 种类 和数 量组 成尽 可能 多 的种类 和规格 的产 品 。
( )产 品配 置 与组 合 化 设 计 包 括 : 3 根据 用 户具 体
1 模块 化设计 的概 念 与特点
()有 利 于提高 产 品质 量 , 3 降低 成本 , 加产 品 的市场 增
竞 争能力 ; 4 模 块 部件 的 通用 性 和互换 化 , () 同一 功能
的模块 可 在基 型 、 变型 , 至跨 系 列 、 甚 跨类 型 产 品上使
用 , 于实 现 产 品 的系列 化 ; 5 便 ( )采用 子 模 块 的 形 式 ,
关 键 词 : 块 化 设 计 ; 算 机 辅 助 设 计 ; 塑机 模 计 注 文 献 标 志码 : A 文章 编号 :0 52 9 ( 0 7 0—0 60 1 0— 8 5 20 )30 2 —3 中 图 分 类 号 : Q30 5T 3 1 7 T 2 . ; P 9 .
O 引 言
产 品模 块 化设计 是将 模块 化思 想引 入到 产 品设 计 中, 针对 一定范 围内 的不 同功 能 , 或相 同功能 而不 同性 能 、 同规 格 的产 品需 求 , 模 块 化 的要 求 , 计 一 系 不 按 设 列功 能模 块 , 建立 结构 模块 体系 , 并 通过模 块 的选择 和
预坚膜塑料模具钢材的计算机辅助成分设计完整版
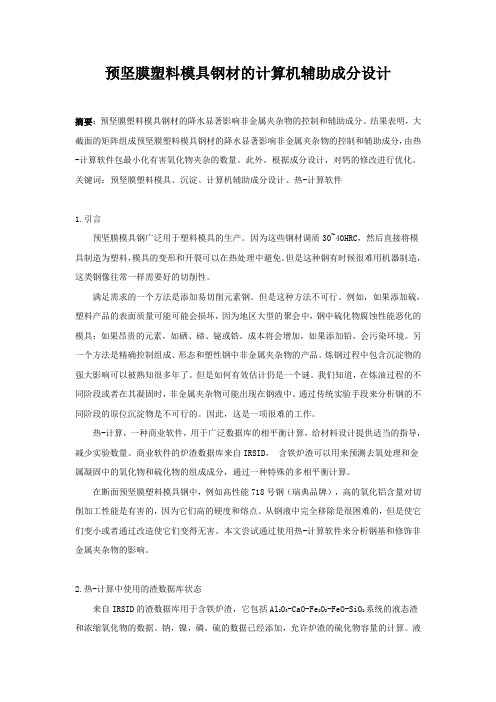
预坚膜塑料模具钢材的计算机辅助成分设计摘要:预坚膜塑料模具钢材的降水显著影响非金属夹杂物的控制和辅助成分。
结果表明,大截面的矩阵组成预坚膜塑料模具钢材的降水显著影响非金属夹杂物的控制和辅助成分,由热-计算软件包最小化有害氧化物夹杂的数量。
此外,根据成分设计,对钙的修改进行优化。
关键词:预坚膜塑料模具、沉淀、计算机辅助成分设计、热-计算软件1.引言预坚膜模具钢广泛用于塑料模具的生产。
因为这些钢材调质30~40HRC,然后直接将模具制造为塑料,模具的变形和开裂可以在热处理中避免。
但是这种钢有时候很难用机器制造,这类钢像往常一样需要好的切削性。
满足需求的一个方法是添加易切削元素钢。
但是这种方法不可行。
例如,如果添加硫,塑料产品的表面质量可能可能会损坏,因为地区大型的聚会中,钢中硫化物腐蚀性能恶化的模具;如果昂贵的元素,如硒、碲、铋或锆,成本将会增加,如果添加铅,会污染环境。
另一个方法是精确控制组成、形态和塑性钢中非金属夹杂物的产品。
炼钢过程中包含沉淀物的强大影响可以被熟知很多年了。
但是如何有效估计仍是一个谜。
我们知道,在炼油过程的不同阶段或者在其凝固时,非金属夹杂物可能出现在钢液中。
通过传统实验手段来分析钢的不同阶段的原位沉淀物是不可行的。
因此,这是一项很难的工作。
热-计算,一种商业软件,用于广泛数据库的相平衡计算,给材料设计提供适当的指导,减少实验数量。
商业软件的炉渣数据库来自IRSID,含铁炉渣可以用来预测去氧处理和金属凝固中的氧化物和硫化物的组成成分,通过一种特殊的多相平衡计算。
在断面预坚膜塑料模具钢中,例如高性能718号钢(瑞典品牌),高的氧化铝含量对切削加工性能是有害的,因为它们高的硬度和熔点。
从钢液中完全移除是很困难的,但是使它们变小或者通过改造使它们变得无害。
本文尝试通过使用热-计算软件来分析钢基和修饰非金属夹杂物的影响。
2.热-计算中使用的渣数据库状态来自IRSID的渣数据库用于含铁炉渣,它包括Al2O3-CaO-Fe2O3-FeO-SiO2系统的液态渣和浓缩氧化物的数据。
手机外壳注塑模具的计算机辅助设计说明

手机外壳注塑模的计算机辅助设计与制造马琳(XX职业技术学院XX XX716000)摘要:模具工业不断发展的今天,计算机辅助设计以其先进的设计方式已经逐渐成为模具设计的主流方式,其在生产制造中使用得最为广泛。
PRO/E作为计算机辅助设计的常用软件,具有强大的二维草绘和三维设计功能,在注塑模具的设计起到了很重要的作用。
本论文以Sunup手机后壳为例,对其结构进行了分析设计。
在PRO/E环境下,对手机外壳进行了三维实体建模,并介绍了设计过程中的原则,从而展现使用PRO/E对注塑模具设计的优越性。
关键词:手机外壳;PRO/E;计算机辅助设计。
一、前言高分子材料包括塑料、合成塑胶和合成纤维。
作为高分子材料之一的塑料,集原料丰富,制造方便,加工容易、质地优良、轻巧耐用、用途广泛和投资效益显著等众多优点于一身,在人们的日常生活中及现代工业生产领域中占有很重要的地位。
采用模具成型的工艺代替传统的切削加工工艺,可以提高生产效率,保证零件质量,节约材料,降低生产成本,从而取得很高的生产效率。
因此,在机电、仪表、化工、汽车和航天航空等领域,塑料已成为金属的良好代用材料并得到了广泛的应用,出现了金属材料塑料化的趋势。
在工业发达国家,据最近数据统计,日本生产塑料模和生产冲压模的企业各占40%;韩国模具专业厂中,生产塑料模的43.9% ,生产冲压模的占44.8%;新加坡全国有460家模具企业,60%生产塑料模,35%生产冲模和夹具。
作为最有效的塑料成型方法之一的注射成型技术具有可以一次成型各种结构复杂和尺寸精密的塑件。
成型周期短、生产率高、大批生产时成本低廉、易于实现自动化或自动化生产等优点,因此,世界塑料成型模具产量中约半数以上是注射模具。
二、关于PROE设计软件本设计中主要为模具的计算机辅助设计(puter Aided Design,简写为CAD),计算机辅助设计主要是指利用计算机的计算功能和高效的图形处理能力,对产品进行辅助设计分析、修改和优化。
计算机辅助分析在注塑模具设计中的应用
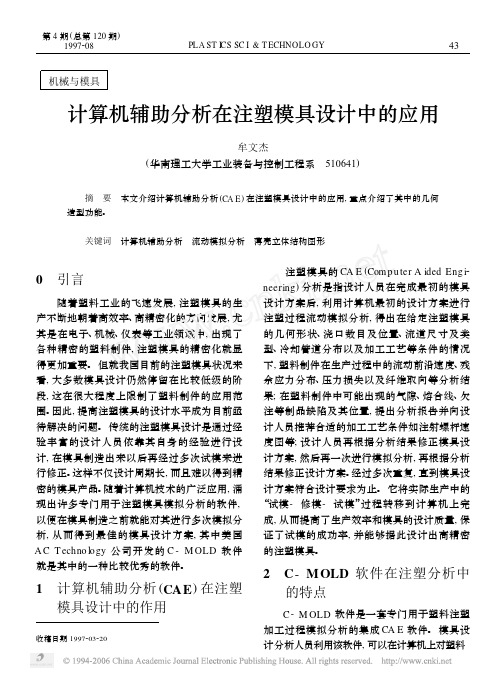
机械与模具计算机辅助分析在注塑模具设计中的应用牟文杰(华南理工大学工业装备与控制工程系 510641) 摘 要 本文介绍计算机辅助分析(CA E)在注塑模具设计中的应用,重点介绍了其中的几何造型功能。
关键词 计算机辅助分析 流动模拟分析 薄壳立体结构图形0 引言随着塑料工业的飞速发展,注塑模具的生产不断地朝着高效率、高精密化的方向发展,尤其是在电子、机械、仪表等工业领域中,出现了各种精密的塑料制件,注塑模具的精密化就显得更加重要。
但就我国目前的注塑模具状况来看,大多数模具设计仍然停留在比较低级的阶段,这在很大程度上限制了塑料制件的应用范围。
因此,提高注塑模具的设计水平成为目前亟待解决的问题。
传统的注塑模具设计是通过经验丰富的设计人员依靠其自身的经验进行设计,在模具制造出来以后再经过多次试模来进行修正。
这样不仅设计周期长,而且难以得到精密的模具产品。
随着计算机技术的广泛应用,涌现出许多专门用于注塑模具模拟分析的软件,以便在模具制造之前就能对其进行多次模拟分析,从而得到最佳的模具设计方案,其中美国A C T echno logy公司开发的C-M OLD软件就是其中的一种比较优秀的软件。
1 计算机辅助分析(CAE)在注塑模具设计中的作用收稿日期1997203220 注塑模具的CA E(Com p ter A ided Engi2 neering)分析是指设计人员在完成最初的模具设计方案后,利用计算机最初的设计方案进行注塑过程流动模拟分析,得出在给定注塑模具的几何形状、浇口数目及位置、流道尺寸及类型、冷却管道分布以及加工工艺等条件的情况下,塑料制件在生产过程中的流动前沿速度、残余应力分布、压力损失以及纤维取向等分析结果;在塑料制件中可能出现的气隙、熔合线、欠注等制品缺陷及其位置,提出分析报告并向设计人员推荐合适的加工工艺条件如注射螺杆速度图等;设计人员再根据分析结果修正模具设计方案,然后再一次进行模拟分析,再根据分析结果修正设计方案。
大连理工大学科技成果——注塑模具计算机辅助工艺设计MDCAPP系统

大连理工大学科技成果——注塑模具计算机辅助工
艺设计MDCAPP系统
一、产品和技术简介:
本项技术是一种针对注塑模具的计算机辅助工艺设计技术。
长期以来,模具加工的工艺编制主要依赖于手工,由于注塑模具生产批量小,品种多,工艺设计繁琐,规范性差,成熟的工艺经验与知识难以保存和借鉴,存在着工艺设计时间长、协同工作困难、工艺文档保存困难、工艺规程的质量难以保证等问题。
使用该系统可以方便快捷地进行模具零部件的工艺设计、模具装配工艺设计等工作。
本系统可以利用现有的工艺资源库查询相似工艺文件,然后加以修订完成工艺设计,从而有效地提高了工艺设计效率。
如果工艺资源中没有相似的工艺,可以以交互的方式建立新的工艺过程,并加以保存,填充到工艺资源库中。
本系统建立了加工资源使用窗口,可以方便快捷地调用各种加工设备和工艺装备等各种工艺设计信息到工艺设计窗口中,使这一复杂繁琐的输入过程得到有效地简化。
另外,系统提供了尺寸链计算、工程计算器等工程数据计算工具可以及时地针对工艺设计过程中出现的尺寸计算问题加以计算解决,具有存储工艺文件,输出(打印)工艺卡的功能。
MDCAPP的特点:
1、工作界面友好;
2、设计的工艺文件可以被安全的保存、调用从而可以将复杂的工艺设计知识方便的传递给工艺设计人员;
3、系统方便灵活,可以定制和根据实际需要方便地进行修改以适应不同企业的需求;
4、系统是首次发布,有很多的升级空间。
二、应用范围和生产条件:
本系统的应用范围可以是各种中小型模具企业,也可以是机械加工为主的企业。
主要是为工艺设计人员摆脱传统的工艺设计过程中的大量重复工作,手工填制工艺卡的负担。
塑料模具设计与制造的计算机辅助教学
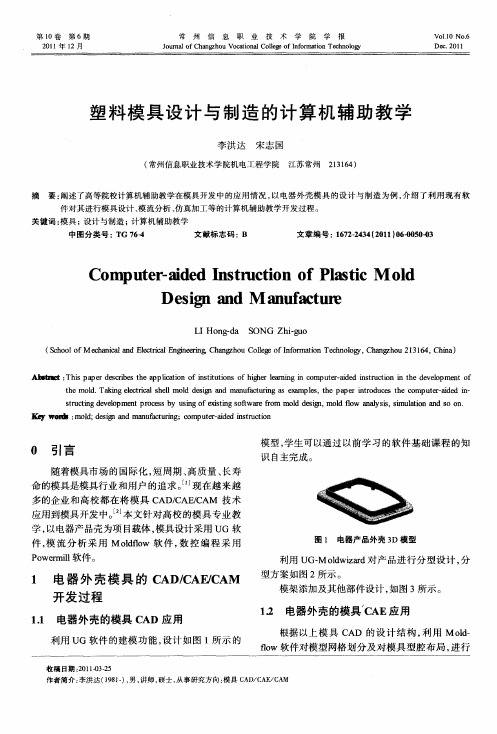
M
型方 案如 图 2所示 。
模 架添加 及其 他部 件设计 , 图 3所 示 。 如
12 电器外 壳的模具 AE应用 . C
根 据 以上 模 具 C AD 的 设 计 结 构 , 用 M o — 利 l d l f w 软件对 模 型 网格 划 分 及对 模 具 型 腔 布局 , 行 o 进
成 型工 艺参数 等方 式 , 次进行 优化 后 的分析 计算 , 再 直 至产 品注 塑成型 过程符 合生 产要求 。经 过几 次分
t e mo d Ta i gee tia s e l e in a d ma u a t r g a x mp e , h a r mto u e h mp t — ie n h l . k n l r l h U mo d d sg n fc u i s ea l t e p pe r d c s t e c c c n n s o u e ad d i— r sr c ig d v lp n r c s y u i go xs ig s f r r m l e i , l lw a i, i lt n a d S n tu t e eo me tp o e sb s fe it o wae fo mod d  ̄ mo f n n n t s d o a l s smu a i O o . n ys o n
模型 , 学生可 以通 过 以前 学 习 的软件 基 础 课 程 的 知 识 自主完成 。
图 1 电 器产 品 外 壳 3 模 型 D
利 用 UG— lwzr Mod ia d对产 品进行 分 型设 计 , 分
1 电器 外 壳 模 具 的 C DC A /A 开 发 过程
1 电器外 壳的模具 C D 应用 . 1 A
钢纸制塑料薄膜的实验设计与数据处理

钢纸制塑料薄膜的实验设计与数据处理摘要:本实验旨在制备钢纸制塑料薄膜,并对其物理性质进行测试。
实验设计包括原料的准备、试剂的配制、薄膜制备过程的优化,以及对薄膜的厚度、抗张强度和透光性等指标进行测试与数据处理。
通过这些实验操作和数据分析,可以了解钢纸制塑料薄膜的性能特点,并对其潜在应用领域进行初步探索。
一、引言钢纸制塑料薄膜是一种由钢纸和塑料薄膜复合制成的新型材料,具有较高的强度、良好的耐候性和透光性能。
该材料被广泛应用于农业覆盖膜、建筑保温材料以及光伏电池背板等领域。
为了实现更好的应用效果,需要对钢纸制塑料薄膜的制备工艺进行优化,并对其物理性能进行详细测试和数据处理。
二、实验设计1. 原料准备选取质量稳定的钢纸和合适的塑料薄膜作为制备材料。
钢纸要求表面平整、无明显划痕和锈蚀,塑料薄膜要具备一定的柔韧性和透光性。
2. 试剂配制按照一定的比例配制溶剂,用于钢纸的清洗和塑料薄膜的固化过程。
溶剂的选择要考虑其对钢纸和塑料的溶解性和除杂能力。
3. 薄膜制备将钢纸和塑料薄膜分别切割成合适的尺寸,然后经过一定的制备工艺将两者复合在一起。
制备工艺可以包括钢纸的清洗处理、塑料薄膜的固化处理以及复合过程的温度、压力和速度控制等方面的优化。
4. 物理性能测试对制备好的钢纸制塑料薄膜进行厚度、抗张强度和透光性等性能的测试。
厚度可以通过测量薄膜的厚度分布和平均厚度来获得;抗张强度可以通过拉伸试验来测定;透光性可以通过光谱分析和透光度测量来评估。
三、数据处理1. 厚度测试数据处理根据测量所得的薄膜厚度数据,计算薄膜厚度的平均值、标准偏差和厚度分布情况。
统计分析可以使用SPSS或Excel等软件完成。
2. 抗张强度测试数据处理根据拉伸试验测试数据,计算钢纸制塑料薄膜的抗张强度。
通过使用拉伸试验机测得的拉伸力和薄膜的断裂长度,计算抗张强度的数值。
3. 透光性测试数据处理根据光谱分析和透光度测量所得的数据,绘制透光性曲线和透光度随波长变化的曲线。
材料科学中的计算机辅助优化设计
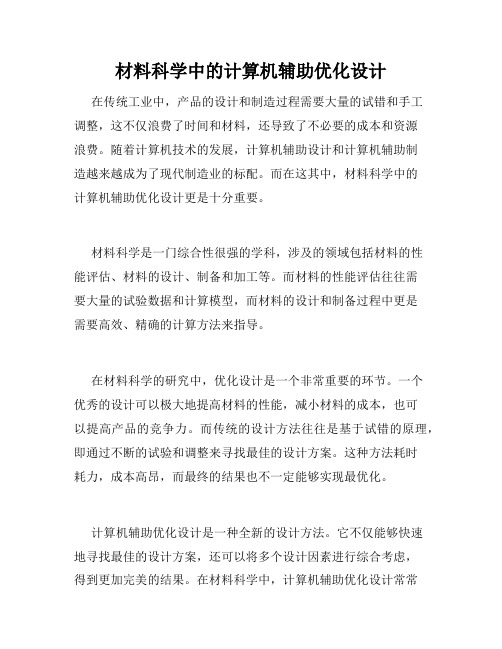
材料科学中的计算机辅助优化设计在传统工业中,产品的设计和制造过程需要大量的试错和手工调整,这不仅浪费了时间和材料,还导致了不必要的成本和资源浪费。
随着计算机技术的发展,计算机辅助设计和计算机辅助制造越来越成为了现代制造业的标配。
而在这其中,材料科学中的计算机辅助优化设计更是十分重要。
材料科学是一门综合性很强的学科,涉及的领域包括材料的性能评估、材料的设计、制备和加工等。
而材料的性能评估往往需要大量的试验数据和计算模型,而材料的设计和制备过程中更是需要高效、精确的计算方法来指导。
在材料科学的研究中,优化设计是一个非常重要的环节。
一个优秀的设计可以极大地提高材料的性能,减小材料的成本,也可以提高产品的竞争力。
而传统的设计方法往往是基于试错的原理,即通过不断的试验和调整来寻找最佳的设计方案。
这种方法耗时耗力,成本高昂,而最终的结果也不一定能够实现最优化。
计算机辅助优化设计是一种全新的设计方法。
它不仅能够快速地寻找最佳的设计方案,还可以将多个设计因素进行综合考虑,得到更加完美的结果。
在材料科学中,计算机辅助优化设计常常与计算机辅助设计、计算机辅助制造等技术相结合使用,形成一个无缝连接的流程,从而实现了快速、智能的材料设计和制备过程。
材料科学中的计算机辅助优化设计的主要方法有以下几种:一、基于统计学方法的优化设计基于统计学方法的优化设计中,主要利用统计学原理对样本进行分析和建模,以确定材料的最佳设计方案。
此方法的主要优点是通过大量的实验数据建模,能够考虑到多种复杂的因素,并且能够在样本上进行较好的拟合,得到较为准确的结果。
二、基于人工神经网络的优化设计基于人工神经网络的优化设计中,主要是利用人工神经网络对材料的性能进行预测和评估。
此方法的主要优点是能够将多个因素进行综合分析,同时具有较好的泛化能力,可以为设计提供较为精确的指导。
三、基于遗传算法的优化设计基于遗传算法的优化设计中,主要采用遗传算法对材料的设计方案进行搜索和优化。
计算机辅助合成技术在材料设计中的应用

计算机辅助合成技术在材料设计中的应用第一章:引言材料学是自然科学中的一个重要分支,其重要性不亚于化学、物理学等学科。
材料的性质决定了其在工程结构设计中的应用,而材料的合成则是实现期望性能的前提。
随着计算机科学技术的快速发展,计算机辅助合成技术在材料设计中的应用也越来越广泛。
本文将从计算机辅助合成技术的概念入手,阐述其在材料设计中的基本应用和未来发展趋势。
第二章:计算机辅助合成技术的基本概念计算机辅助合成技术的概念可以从计算机辅助设计(CAD)发展而来。
CAD是指利用计算机辅助进行物品设计的一种技术。
CAD可以帮助设计者在计算机上创建、修改和分析物品的构造和性能,提高设计效率和精度。
随着计算机技术和分子模拟技术的发展,CAD逐渐进化为计算机辅助合成技术。
计算机辅助合成技术是指利用计算机模拟材料合成过程,预测材料结构与性能的一种技术。
其主要应用于材料的原子、分子结构设计,分子组成优化,材料物理性质预测等方面。
第三章:计算机辅助合成技术在材料设计中的应用3.1 宏观和微观层面的应用计算机辅助合成技术可以应用于宏观和微观层面的材料设计。
在宏观层面上,可以通过材料组成的分子结构设计来改善材料的物理性质,如硬度、抗拉强度等。
在微观层面上,可以利用计算机模拟方法预测材料的晶体结构、分子力场、电荷密度等微观特性,这些特性对材料的应用和性能有重要影响。
3.2 材料力学性质优化计算机辅助合成技术可以有效地改善材料的力学性质,例如弹性模量、硬度等。
这一过程涉及到原子、分子间的相互作用力和排列方式。
通过计算机模拟材料结构,可以实现力学性质的预测和优化,从而达到最佳设计效果。
3.3 电子结构计算材料的电子结构对其物理性质、化学性质和生物活性等都有极大的影响,因此材料电子结构的计算研究也被广泛应用于材料设计。
计算机辅助合成技术可以对材料的分子能量、分子轨道、电荷密度和偶极矩等进行精细计算,从而获得对材料性质的深入了解。
第四章:计算机辅助合成技术未来的发展趋势计算机辅助合成技术在材料设计中的应用有着广阔的未来发展空间。
模具设计-计算机辅助塑料注射模具的设计定稿 精品
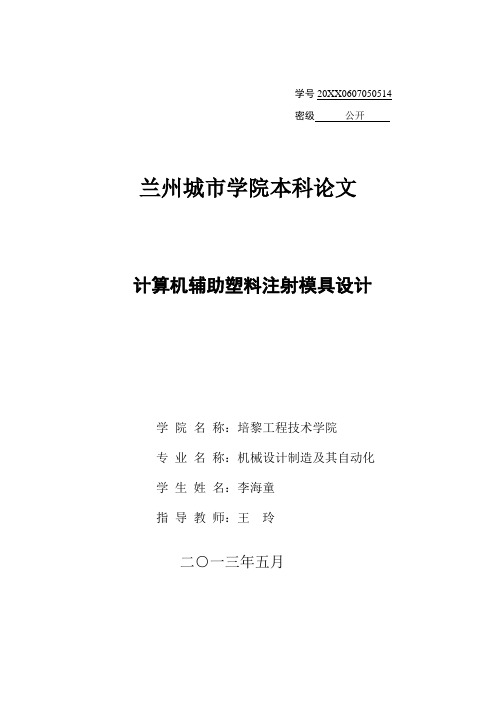
学号20XX0607050514密级公开兰州城市学院本科论文计算机辅助塑料注射模具设计学院名称:培黎工程技术学院专业名称:机械设计制造及其自动化学生姓名:李海童指导教师:王玲二○一三年五月目录第1章绪论1.1模具工业的发展现状 (1)1.2模具工业今后的主要发展方向 (1)1.4计算机辅助设计系统的发展状况和趋势 (3)1.5本课题研究的意义 (4)1.6论文的整体结构 (5)第2章注塑模具介绍2.1塑料概述 (6)2.1.1塑料的组成 (6)2.2塑料的特性 (6)2.3热塑性塑料成型的工艺特性 (6)2.4注塑成型过程简介 (6)2.5注塑模具分类 (7)2.6注塑模典型结构 (7)第3章CPU风扇支架加工工艺分析3.1塑件概况 (9)3.2材料选择 (10)第4章注射模具设计方案4.1注射机选择及注射机的校核 (11)4.1.1选择注射机 (11)4.1.2注塑机的校核 (11)4.2成型零部件设计 (13)4.2.1成型零部件分类及结构 (13)4.2.2 成型尺寸计算 (14)4.3浇注系统设计 (16)4.3.1浇注系统的作用 (16)4.3.2对浇注系统设计的具体要求 (16)4.3.3浇注系统的设计 (16)4.4侧向分型与抽心机构设计 (17)4.4.1 侧向分型与抽芯机构的分类 (18)4.4.2 侧向分型与抽芯机构的设计 (18)4.5注塑模导向机构设计 (20)4.5.1 导向机构的功能及其分类 (20)4.5.2设计要点及设计方案 (20)4.6顶出机构 (21)4.6.1顶出机构的分类 (21)4.6.2顶杆脱模机构的设计要点 (22)4.6.3设计采用方案 (22)4.7复位装置 (23)4.8冷却系统介绍 (23)4.9模具总体结构分析 (24)4.10模具用钢 (25)4.10.1塑料模具用钢的必要条件 (26)4.10.2选择钢材的条件 (26)4.10.3注塑模具常用材料 (26)4.11模具的装配与调试 (26)4.11.1 装配基准的确定 (26)4.11.2 塑料模的装配顺序 (27)结论 (28)........................................................................................................ 错误!未定义书签。
塑料模具设计与制造的计算机辅助教学

塑料模具设计与制造的计算机辅助教学李洪达;宋志国【摘要】阐述了高等院校计算机辅助教学在模具开发中的应用情况,以电器外壳模具的设计与制造为例,介绍了利用现有软件对其进行模具设计、模流分析、仿真加工等的计算机辅助教学开发过程。
%This paper describes the application of institutions of higher learning in computer-aided instruction in the development of the mold.Taking electrical shell mold design and manufacturing as examples,the paper introduces the computer-aided instructing development process by using of existing software from mold design,mold flow analysis,simulation and so on.【期刊名称】《常州信息职业技术学院学报》【年(卷),期】2011(010)006【总页数】3页(P50-52)【关键词】模具;设计与制造;计算机辅助教学【作者】李洪达;宋志国【作者单位】常州信息职业技术学院机电工程学院,江苏常州213164;常州信息职业技术学院机电工程学院,江苏常州213164【正文语种】中文【中图分类】TG764随着模具市场的国际化,短周期、高质量、长寿命的模具是模具行业和用户的追求。
[1]现在越来越多的企业和高校都在将模具CAD/CAE/CAM技术应用到模具开发中。
[2]本文针对高校的模具专业教学,以电器产品壳为项目载体,模具设计采用UG软件,模流分析采用 Moldflow软件,数控编程采用Powermill软件。
利用UG软件的建模功能,设计如图1所示的模型,学生可以通过以前学习的软件基础课程的知识自主完成。
计算机辅助配方设计与优化

计算机辅助玻璃配方优化玻璃纤维分公司马京明(fiberglass branch Jingming Ma)AbstractThrough analyse the design technology of the glass components, put forward the optimum densigned method for using the computer ,and provided the implement and example.this idea can using in other calculability product.the profit of economic and social are huge.Keywordsoptimue designed technology,glass component,calculability product摘要本文通过对玻璃配方设计技术的分析,提出利用计算机辅助玻璃配方的优化设计,并给出了实现方法,同时给出了设计实例. 本文的思想同样适用于其它可计算产品的优化设计.其经济效益和社会效益是巨大的.一.概述随着计算机技术的飞速发展,我们从事设计的工作条件得到了巨大的改善,层出不穷的计算机辅助设计工具,如各种机械CAD、电子CAD以及各种计算机仿真软件等,极大地缩短了新品开发周期。
机械、电子行业应用面广,其理论体系完善,可计算性强,因而开发该类软件的机构众多,软件也成熟得多,而化工、冶金等行业的CAD软件则由于各种原因而相对贫乏得多。
本文介绍使用厦门灵捷软件公司开发的无机玻璃工程师系统优化配方.二.配方优化设计在无机玻璃的生产和科研工作中,为了试制新产品,改进生产工艺以降低生产成本,需要对玻璃配方改良,对需要改进的配方做许多试验,试验各种配方组合下所形成玻璃的相关物理性能指标,寻找出符合我们目标要求的经济合理的配方。
通常,为了得到所要求的物理性能,玻璃的组成会超过3种,多至10种以上,其组合数目巨大,以至于我们无法也不可能进行全部的试验。
- 1、下载文档前请自行甄别文档内容的完整性,平台不提供额外的编辑、内容补充、找答案等附加服务。
- 2、"仅部分预览"的文档,不可在线预览部分如存在完整性等问题,可反馈申请退款(可完整预览的文档不适用该条件!)。
- 3、如文档侵犯您的权益,请联系客服反馈,我们会尽快为您处理(人工客服工作时间:9:00-18:30)。
预坚膜塑料模具钢材的计算机辅助成分设计摘要:预坚膜塑料模具钢材的降水显著影响非金属夹杂物的控制和辅助成分。
结果表明,大截面的矩阵组成预坚膜塑料模具钢材的降水显著影响非金属夹杂物的控制和辅助成分,由热-计算软件包最小化有害氧化物夹杂的数量。
此外,根据成分设计,对钙的修改进行优化。
关键词:预坚膜塑料模具、沉淀、计算机辅助成分设计、热-计算软件1.引言预坚膜模具钢广泛用于塑料模具的生产。
因为这些钢材调质30~40HRC,然后直接将模具制造为塑料,模具的变形和开裂可以在热处理中避免。
但是这种钢有时候很难用机器制造,这类钢像往常一样需要好的切削性。
满足需求的一个方法是添加易切削元素钢。
但是这种方法不可行。
例如,如果添加硫,塑料产品的表面质量可能可能会损坏,因为地区大型的聚会中,钢中硫化物腐蚀性能恶化的模具;如果昂贵的元素,如硒、碲、铋或锆,成本将会增加,如果添加铅,会污染环境。
另一个方法是精确控制组成、形态和塑性钢中非金属夹杂物的产品。
炼钢过程中包含沉淀物的强大影响可以被熟知很多年了。
但是如何有效估计仍是一个谜。
我们知道,在炼油过程的不同阶段或者在其凝固时,非金属夹杂物可能出现在钢液中。
通过传统实验手段来分析钢的不同阶段的原位沉淀物是不可行的。
因此,这是一项很难的工作。
热-计算,一种商业软件,用于广泛数据库的相平衡计算,给材料设计提供适当的指导,减少实验数量。
商业软件的炉渣数据库来自IRSID,含铁炉渣可以用来预测去氧处理和金属凝固中的氧化物和硫化物的组成成分,通过一种特殊的多相平衡计算。
在断面预坚膜塑料模具钢中,例如高性能718号钢(瑞典品牌),高的氧化铝含量对切削加工性能是有害的,因为它们高的硬度和熔点。
从钢液中完全移除是很困难的,但是使它们变小或者通过改造使它们变得无害。
本文尝试通过使用热-计算软件来分析钢基和修饰非金属夹杂物的影响。
2.热-计算中使用的渣数据库状态来自IRSID的渣数据库用于含铁炉渣,它包括Al2O3-CaO-Fe2O3-FeO-SiO2系统的液态渣和浓缩氧化物的数据。
钠,镍,磷,硫的数据已经添加,允许炉渣的硫化物容量的计算。
液态渣在数据库中用给盖伊模型来描述。
盖伊调查含有两种亚晶格的m氧化物((M i)ui O vi,i=1,2,...,n)的液态炉渣混合物。
一个是阴离子亚晶格充满氧离子,而另一个是阳离子亚晶格充满阳离子按递减顺序(如Si4+...Ca2+...)。
熔体的结构在对称(i-O-i)和非对称(i-O-j)的细胞的术语描述,在数字R ii,...,2R ij,...,中,能量参数包括那些非对称细胞的形成,与这些细胞之间的相互作用,这种简化的熔体结构使得可以描述该多组分系统中的仅几个二进制参数方面。
因为熔体的形成可以用以下关系式反映:(i-O-i)+(j-O-j)=2(i-O-j) (1) 然后将熔融的混合自由能可以由统计热力学方法推导。
描述为:其中,R ij满足系统m(m+1)/2的限制,i=1,2,...,mm:氧化物数量(M i)ui,O vi;ui,vi:氧化物的化学计量指标;x i:氧化物的摩尔分数;R ij,2R ij:i-O-i,i-O-j的数量;W ij:能量参数非对称细胞形成;E ij:能量参数细胞的相互作用;R ij:i-O-j细胞的分数在一个随机分布在它们的亚点阵阳离子。
因此,所有的氧化物组分的热力学参数可以被确定。
该模型在对金属气渣处理的描述和监控各种多相平衡计算模型被纳入。
矿渣数据库现已应用于估计的类型和非金属夹杂物在不同阶段中的生产模具钢的塑料的量。
3.钢铁基体成分包含降水的影响对预坚膜塑料模具钢材,如前所述,提高性能的关键是减少氧化铝夹杂物的沉淀在钢材中,所以我们计算的可能影响钢矩阵组合类型和相对数量的夹杂物在钢液形成二次冶金。
718号钢的化学成分在表1.众所周知,铝脱氧钢、铝、硅和锰也影响氧的活性。
因此,它们对氧化铝降水的影响不能忽视。
这种效应可以定量分析通过热-计算软件执行分析、钢的成分以及温度。
考虑输入电脑宏文件氧化铝阶段的状态被设置为“修复”,其他阶段的状态设置为“进入”和锰的重量百分数是设置为“无”。
这意味着这个内容是可依赖的,硅和锰含量的相关性曲线绘制氧化铝,在临界降水状态下的计算结果可以帮助我们选择合适的塑料模具钢材的成分范围。
铝的内容100×10 - 6和300×10 - 6在给定温度1800 K,计算结果如图1所示。
图1中的曲线的计算关键是氧化铝含量.当钢的成分位于右侧的曲线,氧化铝不沉淀,主要包含在钢锰铝酸所描述的软件。
然而.如果成分位于左边的曲线,在钢铝沉淀。
计算结果表明,当锰的重量百分比变化从1.0到1.5。
硅的重量百分比变化从0.23到0.39。
然后组成位于曲线,氧化铝的临界状态含量.如果锰的重量百分比1.34 和硅的重量百分比0.29 是输出量.那么得到铝酸锰的摩尔分数0.069%,因为成分位于右侧曲线.如果锰的重量百分比变化1.24和硅的重量百分比为0.5,那么铝的摩尔分数为0.0485%,因为成分位于左边的曲线。
铝300×10 - 6的内容结果是相似的。
锰铝酸盐和铝的摩尔分数分别为 0.21和0.15%。
在二次冶金、氩气冲洗是一种有效的方法消除有害夹杂物,但此操作将导致一些降低熔融温度的钢。
因此,上述结果似乎考虑的降水造成的实际降低以避免氧化铝在钢液渣应该选择硅和锰组成正确的图1中所示的曲线。
4.非金属夹杂物在凝固过程的沉淀已知的是,非金属夹杂物可能会出现在钢水的不同阶段。
这样的沉淀分析,非金属的夹杂是必要的炼钢的所有阶段。
在过去的夹杂物的形状控制技术是基于组合物的调节或控制包括在熔体中。
对于这理论的解释是氧化反应的平衡关系方面获得的熔体的特定恒定温度。
这样的解释,但是可能会不足,同时考虑到脱氧反应仍继续冷却直到熔体固化过程中有一定影响。
因此,有必要作出努力来分析在凝固过程中的夹杂物形成的钢。
它公知的是夹杂物,直接在形成钢水被称为外生夹杂物。
大量外源夹杂物可以通过熔渣耙和气体漂洗被消除,或通过注入钙硅粉末在钢包中改性,但在包裹内源性现有钢的凝固是不可能被删除。
各种各样的内生夹杂物通常存在的钢被归类为:(1)剩余还原夹杂物,(2)夹杂物沉淀在凝固和(3)可能再氧化夹杂物。
应该指出,一些残余的还原夹杂物,如氧化铝粒子.致力于提高钢铁产品的性能作为异相成核的衬底硫化锰。
硬粒子形成的复杂包含氧化铝夹杂物周围表面涂层的韧性相硫化锰.包容这样的形态不仅避免了硫化锰的变形导致的减少各向同性,也消除了硬粒子损害钢的切削加工性能。
但氧化铝,伴随着凝固期间夹杂物沉淀或结晶在最初的冷却液体包裹体,有害材料的切削加工性能成分凝固过程中形成的夹杂物也可以模拟任意增加氧含量水平,消费跟踪可氧化的元素(如铝),开始与较弱的反应脱氧剂(硅和锰)。
718钢的成分作为一个例子,我们可以进行比较研究关于氧化铝的形成在不同温度下凝固。
组成计算表2.中列出了氧化铝沉淀量和温度之间的关系,如图2所示(a)堂皇的相图718钢图2(b)所示,它是发现,氧化铝沉淀718年钢铁几乎完成了在1769 K高于其熔点(1760 K)。
如果我们用上述不合理成分(0.5百分点硅 - 1.24 百分点锰)作为输入,计算结果明显不同于前。
如图3所示的持续钢的凝固过程.因为它的熔点是1757 K和氧化铝降水在1748 K 完成。
可以看出钢的成分特别是硅和锰的内容.在凝固明显影响夹杂物的沉淀.与铝相比,硅和氧之间的亲和力是第二钢,所以较高含量的硅导致推迟氧化铝的降水钢水直到凝固。
这电话是得出结论,718号钢的不合理成分,钢铁行业是其主要原因的存在高铝钢产品的内容,它可能,严重降低钢的切削加工性能。
为了研究上面的计算结果,718钢的微观结构和机械加工性0.29 百分点硅 - 1.34 百分点锰和0.50百分点硅 - 1.24百分点硅比较。
结果表明,大量的氧化铝在前者小于后者和前者的切削加工性能也更好。
瓷砖实验的细节将在其他地方发表。
5.钙对夹杂沉淀物的影响从钢液中完全移除氧化物夹杂物是很难的。
修改通常用来减少其有害影响。
钙作为变质剂,被广泛用于炼钢,将硬颗粒氧化铝转化成更柔和的铝酸钙。
钙和氧的含量对夹杂物的沉淀的影响通过使用热-计算软件计算。
结果列于图4。
在这些图中,线代表各种夹杂物存在的限制,即用于在给定的氧含量中提高钙的含量。
氧化铝存在于该地区的氧化铝标,铝酸钙在标域CaO-nAl2O3和硫化钙在该地区的硫化钙标记。
在1800K,对于100×10-6和600×10-6的铝含量,可以从图4(a)和(b)中看出,钙的含量应该定在第三行的上侧,否则氧化铝夹杂将形成钢水。
随着铝含量的增加,铝酸钙的形成范围变得更宽阔,硫化钙的析出变得更容易。
因为在更高的铝含量中,钙溶解于钢水中的量更大,氧化铝的变形相应地变得更容易。
通常,当钙溶解于钢水中的量小时,铝酸钙可以沉淀,当其更大时,在钢水中硫化钙形成,也就是说,如果到达硫化钙的饱和极限,硫化钙沉淀。
因此,铝酸钙的形成范围变得更宽,在铝含量高的条件下,硫化钙的沉淀变得更容易。
相同的结果可在1880K高温下来获得,但是与低温条件相比,可以看出氧化铝的变形变得更容易,硫化钙的形成变得更困难(见图4(c)-(d))。
随着温度升高,钙的活性更高,钙和氧化物之间的亲和更大。
所以铝酸钙的形成是容易的。
然而,硫化钙的饱和极限会在高温下升高,钙的溶解量会相应地增加。
这导致硫化钙形成的难度。
因为连续铸造技术不总是在大截面塑料模具钢的生产中使用,低硫含量小钢,铝酸钙和硫化钙的析出造成导致喷嘴堵塞的影响可以忽略。
为了改善可加工性,该组合物可以被调节到硫化钙析出的域。
6.结论在大截面预硬模具钢胶,基质成分显著影响非金属夹杂物的沉淀。
在炼钢中,各个阶段的控制可以减少有害的氧化物夹杂物的数量。
为了实现最佳变形,钙的组合物应该精确地根据氧和铝含量来调节。