单件流文件
精益生产10大工具
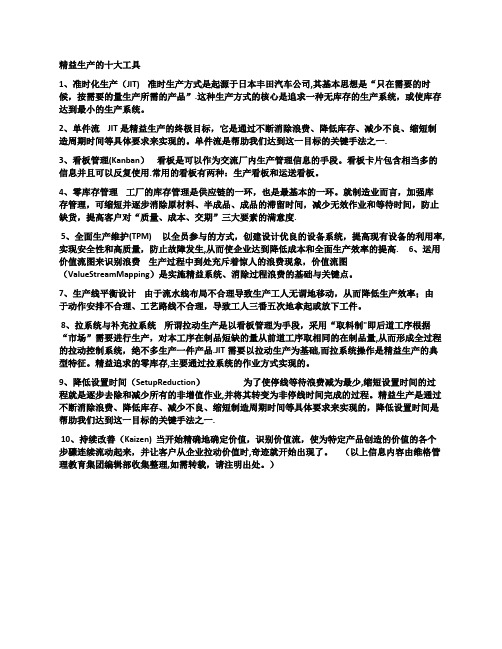
精益生产的十大工具1、准时化生产(JIT) 准时生产方式是起源于日本丰田汽车公司,其基本思想是“只在需要的时候,按需要的量生产所需的产品”.这种生产方式的核心是追求一种无库存的生产系统,或使库存达到最小的生产系统。
2、单件流 JIT是精益生产的终极目标,它是通过不断消除浪费、降低库存、减少不良、缩短制造周期时间等具体要求来实现的。
单件流是帮助我们达到这一目标的关键手法之一.3、看板管理(Kanban)看板是可以作为交流厂内生产管理信息的手段。
看板卡片包含相当多的信息并且可以反复使用.常用的看板有两种:生产看板和运送看板。
4、零库存管理工厂的库存管理是供应链的一环,也是最基本的一环。
就制造业而言,加强库存管理,可缩短并逐步消除原材料、半成品、成品的滞留时间,减少无效作业和等待时间,防止缺货,提高客户对“质量、成本、交期”三大要素的满意度.5、全面生产维护(TPM) 以全员参与的方式,创建设计优良的设备系统,提高现有设备的利用率,实现安全性和高质量,防止故障发生,从而使企业达到降低成本和全面生产效率的提高.6、运用价值流图来识别浪费生产过程中到处充斥着惊人的浪费现象,价值流图(ValueStreamMapping)是实施精益系统、消除过程浪费的基础与关键点。
7、生产线平衡设计由于流水线布局不合理导致生产工人无谓地移动,从而降低生产效率;由于动作安排不合理、工艺路线不合理,导致工人三番五次地拿起或放下工件。
8、拉系统与补充拉系统所谓拉动生产是以看板管理为手段,采用“取料制"即后道工序根据“市场”需要进行生产,对本工序在制品短缺的量从前道工序取相同的在制品量,从而形成全过程的拉动控制系统,绝不多生产一件产品.JIT需要以拉动生产为基础,而拉系统操作是精益生产的典型特征。
精益追求的零库存,主要通过拉系统的作业方式实现的。
9、降低设置时间(SetupReduction)为了使停线等待浪费减为最少,缩短设置时间的过程就是逐步去除和减少所有的非增值作业,并将其转变为非停线时间完成的过程。
单件流概念简述

单件流概念简述1、节奏时间计算单件流的节奏时间计算方法与过去不同,过去计算节奏时间是按生产线的实际产能为标准,即以“我”为主。
单件流则要求计算标准以客户要求的产量、交货期为准,即以“客户”为主。
按照客户要求的出货量,得出生产线必须达到的节奏时间,这个节奏时间就是一根牵动整个生产活动的线,生产的各个环节,大到一个部门,小到一个工序都以这条线为基准保持和谐统一。
交响乐团要演奏出完美乐章,前提是每个乐手必须看指挥,保持同一节奏。
生产活动是一个系统工程,像乐团演奏一样,强调和谐统一,那么节奏时间就是一支无形的指挥棒,保证生产稳步、持续、有序的向前发展。
每个动作都按相应的节奏进行,就要求动作的“标准化”。
从具体来说,每一个动作都有标准的程序、步骤,必须按规定进行;从整体来说,规定时间内就完成规定的产量,过量生产、过早生产都属浪费。
尽量使所有的动作都标准化,非标准化的动作由发料员来完成。
发料员被形象的成为“水蜘蛛”,因为他们必须反应快速敏捷。
节奏时间使生产活动变成一支训练有素的军队,即整齐划一,又灵活应变。
2、单件流原理生产线上物品流动的传统方式是物品批量流动。
这种方式本身隐含着一些难以克服的问题。
例如,供需不平衡、无法有效控制不良品、生产活动缺乏弹性等。
单件流是指保证物品以最小单位流动。
动作复杂,需要时间长的环节生产的部件,无法配合动作简单,需要时间短的环节,致使有些部件严重积压,有些部件却总是供应不足。
然而,周期时间以及生产效率都是一个整体的概念,就像木桶原理一样,一个木桶最终能装多少水取决于最短的那一块木板。
周期时间、生产效率的高低也往往是由生产活动中最薄弱的环节决定的。
单件流的方式使这些薄弱环节直接显现出来,我们只要集中力量对这些具体问题加以改善,就可以达到整体的提高;单件流的方式还可以即时发现不良品,即时改善,从而有效的控制不良品,最终实现零不良品率。
另外,单件流的方式可以弹性的控制生产活动。
如果生产计划临时有变,生产活动就可以马上响应这种变化,即时扩大生产或停止生产。
单件流运行中的各项制度
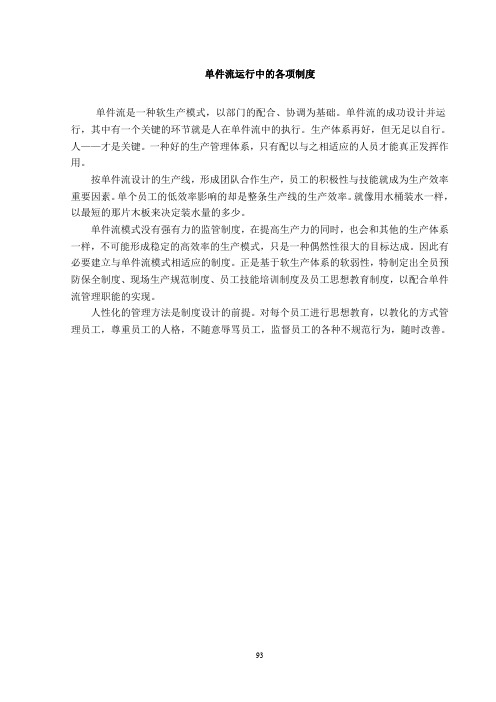
核查人: ____________________
确认: ____________________
备注 :(1). 总分 : 100 分. (2). "是" (A = 4 分 , B = 2 分) (3). 通过得分 : = 或 > 80 分.
"否" = 0 分
110
重要程度
是
否
A A A
A B B
1、岗位知识:岗位技能训练,岗位技能教育应按照下列步骤进行: a. 整备有关工艺、作业标准及其他技术文件、手册。 b. 整备必要的工具、设备。 c. 将上述标准讲解给新员工使之了解。 d. 操作示范(可由资深员工进行)。 e. 说明工作标准。 f. 由新员工试做并予以纠正。 g. 告诉新员工遇到困难时可以找谁帮助。 h. 指定协助督导人员。 I. 进行必要的查核。 j. 员工总结,深刻认识生产过程。总结经验、教训。
1.5.2 是否有反映某具体工作站的品质限度样板.
1.5.3 是否有防止同样的品质问题重复出现的解决方法
2. 产前准备
2.1 是否按照产前培训标准作业执行产前培训
2.2 是否按照一刻钟转款操作指引转款
2.3 核查前一个款的转款时间是否少于一刻钟
2.4 检查前一个款的平衡时间是否少于 4 小时
2.5 转款当天的效率是否超过排期效率的 85%
3. 预防保全
3.1 所有作业员是否按照设备自检操作指引执行
3.2 所有作业员是否按照设备自修操作指引执行
3.3 所有作业员是否按照设备保养操作指引执行
4. 5S
4.1 是否所有的剪刀、锥子均按照标准绑好
4.2 是否所有的车台,地面以及机车均保持清洁且在黄线以内
精益生产名词解释

精益生产名词解释一、何为精益生产?精益生产管理,是一种以客户需求为拉动,以消除浪费和不断改善为核心,使企业以最少的投入获取成本和运作效益显著改善的一种全新的生产管理模式。
它的特点是强调客户对时间和价值的要求,以科学合理的制造体系来组织为客户带来增值的生产活动,缩短生产周期,提高质量,从而显著提高企业适应市场万变的能力。
精益生产管理就是控制浪费、降低成本的最有效的一种生产管理方式。
二、什么叫八大浪费八大浪费是定义工厂在JIT生产方式中的,其浪费的含义与社会上通常所说的浪费有所区别。
对于JIT 来讲,凡是超出增加产品价值所必需的绝对最少的物料、设备、人力、场地和时间的部分都是浪费。
因此,JIT生产方式所讲的工厂的浪费归纳为八大种,分别是:不良、修理的浪费,过分加工的浪费,动作的浪费,搬运的浪费,库存的浪费,制造过多过早的浪费,等待的浪费和管理的浪费,简称为八大浪费。
三、何为6S6S 起源于日本,指的是在生产现场中将人员、机器、材料、操作方法等生产要素进行有效管理,它针对企业中每位员工的日常行为方面提出要求,倡导从小事做起,力求使每位员工都养成事事“讲究”的习惯,从而达到提高整体工作质量的目的。
6S就是整理(SEIRI)、整顿(SEITON)、清扫(SEISO)、清洁(SEIKETSU)、素养(SHITSUKE)、安全(SAFETY)六个项目,因均以“S”开头,简称6S。
四、价值流价值流是指从原材料转变为成品的物料、信息流、时间流等,并给它赋予价值的全部活动,包括从供应商处购买的原材料到达企业,企业对其进行加工后转变为成品再交付客户的全过程,企业内以及企业与供应商、客户之间的信息沟通形成的信息流也是价值流的一部分。
一个完整的价值流包括增值和非增值活动,如供应链成员间的沟通,物料的运输,生产计划的制定和安排以及从原材料到产品的物质转换过程等。
五、团队和团队建设团队是指为了实现某一目标而由相互协作的个体所组成的正式群体。
单件流流程排布及平衡
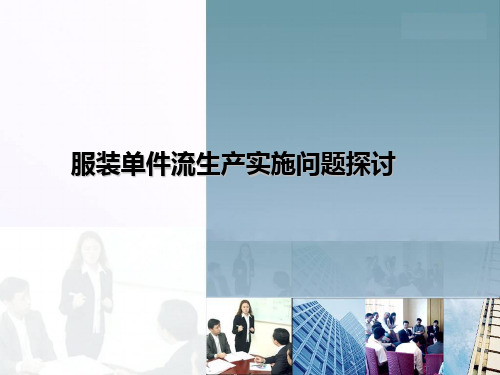
成瓶颈的原因时员工的技能还是工序本身较复杂,技能问题时一般会考虑
换人,而工序本身的问题时,应把该瓶颈工位工序细分,看能不能转移给工
时短的工位分担完成,
•
• 一般在顺线后的2个小时之内,由于员工对新款的做工要求没有熟悉,另外, 工位工序的设置也不尽合理,所以问题较多,节拍的时间不固定,IE员也在 现场帮忙调平衡,控制节拍也主要由人工控制公司采用的调平衡的主要步 骤是:
• U型单件流水/细胞式生产方式 分为三种方式:
• 1.人生产方式,细胞内所有工序由1个人承担,不再进行分工,它是细胞式 生产方式的基本形态,与下面两种方式相比,其优点是不受其他人员作业 速度的影响,便于自主管理,缺点是当细胞内工序数目较多的时候,培养多 能工需要较长的时间, 2.分割方式,细胞内工序由数人承担,每人分担若干工序,它是在完成一 件产品所需工序较多的时候,或当新工人对作业还不够熟练,很难承担细 胞内所有工序的时候所采用的一种变通、过渡形态, 3.巡回方式,细胞内虽然有若干名作业人员,但不再进行分工,每个人都 承担细胞内的全部工序,具体操作时,作业人员按顺序排列,一个跟着一个 在细胞内(ZHOU)而复始地巡回作业,在日本也称它为追兔方式,这种 方式的优点是,可以在不增加车间作业面积,不增加工作台数量和配套设 备的前提下,仅通过增加作业人员达到迅速增加产量的目的,缺点是,作业 的速度受限于细胞内动作最慢者的速度,
• 2、首先考虑对瓶颈工序进行作业改善,作业改善的方法、参照程序分析 的改善方法及动作分析、系统规划分析等,
1
产前准备
2
质量跟踪
3
生产线平衡
4
跟踪反馈
• 人员
• 面辅料准备情况
• 机器设备、相关的 辅助设备
服装生产线单件流实施计划方案探讨

第一章引言主要介绍本论文的选题背景、国服装流水线生产的研究现状以及论文研究容及框架。
第二章服装流水线生产管理的方法及工具引言一、流水线生产管理的概念流水线管理是运用科学的管理思想、管理方法和管理手段对流水线生产过程中的各种要素,如人(操作者、管理者),机(机器设备、工艺设备),料(原材料、辅助材料、零部件),法(操作方法、工艺制度、规章),环(环境)等进行合理配置和优化组合的人工流程系统,通过计划、组织、控制、协调、激励等管理职能,保证生产按预定的目的实现优质、高效、低耗、均衡、安全、文明的生产。
[9]流水线生产是加工制造型企业重要的生产方式,企业管理中的很多问题也必然会在流水线生产过程中得到反映,各项专业管理工作也要在流水线生产过程中贯彻落实。
因此作为企业产品基础的生产流水线管理,其首要任务是保证生产的各项活动能高效、有秩序的进行,实现预定的目标。
要使流水线生产高效、有秩序进行,就要对其进行研究与改善,用先进的理念、科学的方法进行管理。
国自改革开放以后,大型生产制造型企业从实践中逐渐认识到,企业必须按照社会化生产的要求,以提高生产效率为主要目标,来推进生产方式正规化。
国的一些学者在国外相关研究的启示下,开始对流水线生产的模式和生产方法进行系统的研究,主要的方向有:1.是对工人的操作科学地加以规定。
规动力机器的操作方式,以提高工人的劳动效率,防止人为发生事故;二是根据工人的操作情况,制定和推行各类标准工作法,逐步实现生产的规化;三是以正规的专业培训代替师傅带徒弟传授技能的落后方式,以适应机械化生产方式的要求。
2.对生产观念的影响,生产方式的转型,直接的影响来源于思想的改变,因此当国外动力机械技术传人国后,随着企业、集团、行会的发展,新的生产方式给生产观念带来新变化。
一是生产的数质观,不仅要求新机器生产数量巨大的产品,而且要保证产品的质量,才能占据市场;二是生产的效益观,新的生产方式大大加快了产品的更新换代。
CPS名词解释及衡量指标

⇒ 『 简化 』
10
CPS
IE相关名词介绍
1. 防错法
如何避免做错事情,使工作第一次就做好的精神能够 具体实现 改善人体动作的方式,減少疲劳使工作更为舒适,更有 效率,不要蛮干. 研究探讨牽涉到几個不同工作或地点之流动关系,以 发掘也可资改善的地方. 借着质问的技巧來发掘出改善的构想
四 、 IE 七 大 改 善 手 法
2) Totally Process Improvement
(全体的生产性改善)
(工程全部改善)
3) Towards Process-yield Increasing (目标工程良品率)
4) Taking Personal Intelligence 5) Towards Profit Increasing (活用人的智慧) (利益増加目的)
TPI 集 成 图
TPS 50 %
IE 20 %
50%+20%+15%+10%+5%
TPI
100%
NPS 5 %
LEAN 10 %
CELL 15 %
20
CPS
什么是 NPS
NPS 是导源于日本的丰田生产方式,或是一般所称的“及时生产”
方式。由早期的丰田生产方式的创始者大野耐一一起开发、实施的一 群人,将其内涵及应用范围加以改进,而推广应用于汽车业以外的许 多不同规模的行业的新型生产方式。 NPS 的最终目的就是通过消除隐藏在企业内部的各种浪费,以获 取更多的利益。NPS 的主要特点,就是他的改善成果迅速,而且是多
50%+20%+15%+10%+5%
TPI
100%
NPS 5 %
LEAN 10 %
关于服装单件流
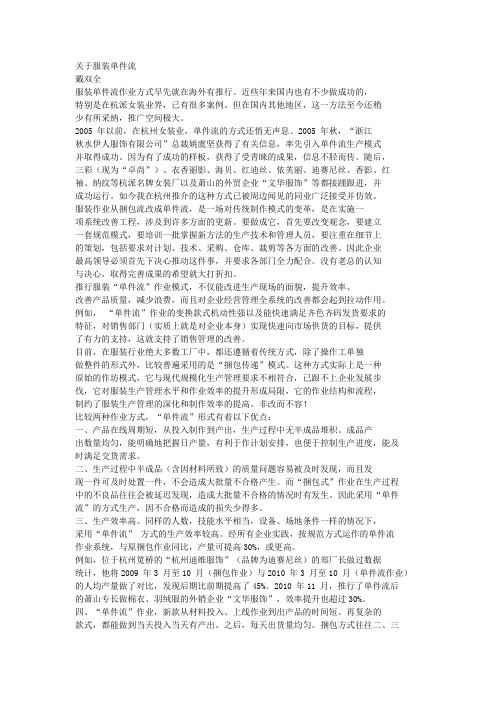
关于服装单件流戴双全服装单件流作业方式早先就在海外有推行。
近些年来国内也有不少做成功的,特别是在杭派女装业界,已有很多案例。
但在国内其他地区,这一方法至今还稍少有所采纳,推广空间极大。
2005 年以前,在杭州女装业,单件流的方式还悄无声息。
2005 年秋,“浙江秋水伊人服饰有限公司”总裁姚虞坚获得了有关信息,率先引入单件流生产模式并取得成功。
因为有了成功的样板,获得了受青睐的成果,信息不胫而传。
随后,三彩(现为“卓尚”)、衣香丽影、海贝、红迪丝、依芙丽、迪赛尼丝、香影、红袖、纳纹等杭派名牌女装厂以及萧山的外贸企业“文华服饰”等都接踵跟进,并成功运行。
如今我在杭州推介的这种方式已被周边闻见的同业广泛接受并仿效。
服装作业从捆包流改成单件流,是一场对传统制作模式的变革,是在实施一项系统改善工程,涉及到许多方面的更新。
要做成它,首先要改变观念,要建立一套规范模式,要培训一批掌握新方法的生产技术和管理人员,要注重在细节上的策划,包括要求对计划、技术、采购、仓库、裁剪等各方面的改善。
因此企业最高领导必须首先下决心推动这件事,并要求各部门全力配合。
没有老总的认知与决心,取得完善成果的希望就大打折扣。
推行服装“单件流”作业模式,不仅能改进生产现场的面貌,提升效率、改善产品质量,减少浪费,而且对企业经营管理全系统的改善都会起到拉动作用。
例如,“单件流”作业的变换款式机动性强以及能快速满足齐色齐码发货要求的特征,对销售部门(实质上就是对企业本身)实现快速向市场供货的目标,提供了有力的支持,这就支持了销售管理的改善。
目前,在服装行业绝大多数工厂中,都还遵循着传统方式,除了操作工单独做整件的形式外,比较普遍采用的是“捆包传递”模式。
这种方式实际上是一种原始的作坊模式,它与现代规模化生产管理要求不相符合,已跟不上企业发展步伐,它对服装生产管理水平和作业效率的提升形成局限,它的作业结构和流程,制约了服装生产管理的深化和制作效率的提高。
单件流
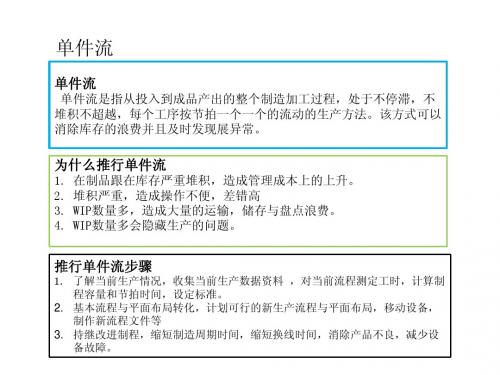
单件流
单件流是指从投入到成品产出的整个制造加工过程,处于不停滞,不 堆积不超越,每个工序按节拍一个一个的流动的生产方法。该方式可以 消除库存的件流
1. 2. 3. 4. 在制品跟在库存严重堆积,造成管理成本上的上升。 堆积严重,造成操作不便,差错高 WIP数量多,造成大量的运输,储存与盘点浪费。 WIP数量多会隐藏生产的问题。
推行单件流步骤
1. 了解当前生产情况,收集当前生产数据资料 ,对当前流程测定工时,计算制 程容量和节拍时间,设定标准。 2. 基本流程与平面布局转化,计划可行的新生产流程与平面布局,移动设备, 制作新流程文件等 3. 持继改进制程,缩短制造周期时间,缩短换线时间,消除产品不良,减少设 备故障。
精益制造名词解释(中文)(新)
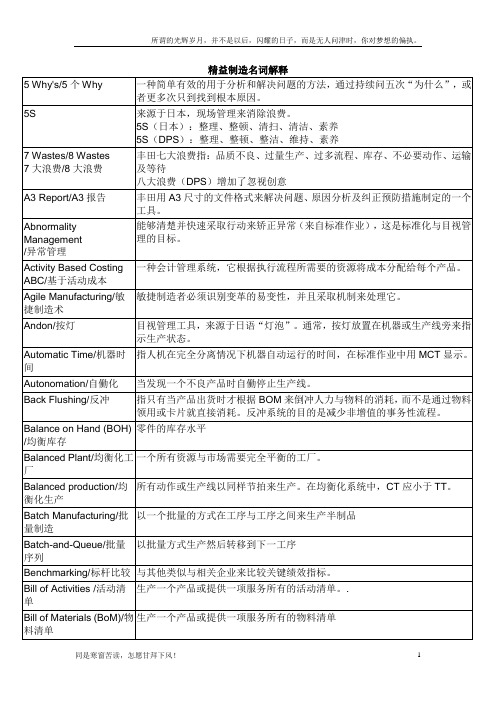
5 Why's/5个Why
一种简单有效的用于分析和解决问题的方法,通过持续问五次“为什么”,或者更多次只到找到根本原因。
5S
来源于日本,现场管理来消除浪费。
5S(日本):整理、整顿、清扫、清洁、素养
5S(DPS):整理、整顿、整洁、维持、素养
7 Wastes/8 Wastes
7大浪费/8大浪费
精益生产单元布局的一个基本原则就是原料与人的动作的方向应该从右到左,或者说是逆时针。这个想法来源于车床和机床上放置在左边的夹头,它能够让一直使用右手操作的人更方便的从右到左进行装载。
Critical Capacity Resource (CCR)/关键产能资源
A CCR is a resource that may prevent the system moving closer towards its goal.
成本与供应的优质产品有关。
成本的种类包括PAF:预防成本,鉴定成本和损失成本。
Counterclockwise Flow/逆时针流
A basic principle of Lean manufacturing cell layout is that the flow of material and the motion of people should be from right to left, or counterclockwise. The origin of this idea came from the design of lathes and machine tools with thechuckson the left side, making it easier for right-handed people to load from right to left.
CPS名词解释及衡量指标

A 用成形机
B 用成形机
(2台、2人)
安全库存
安全库存
A 公司交货
B 公司交货
(整流化)
看板
A公司交货 安全店面
(最少库存)
A、B 都用成型机
(1台、1人)
B公司交货
27
CPS
CELL相关名词介绍
双层柜控制系统
把大部件,中部件和小部件区分开。用这个系统时需 要专门指定一员工或CELL线带线干部来搬运物料或供应 空盒子,这点至关重要。 激励竞争 参与各种竞争并激发他们的兴趣来获得奖励是人类的 特性。这个“游戏”当然在工厂也会产生激励作用。例如, 使用CELL管理看板,可以让员工在提高生产力和降低不 良品上竞争。给予奖励多少取决于员工取得的成就。为了 避免在这个问题上产生矛盾,制定规则和公平竞争非常重 要。
3
CPS
TPI
TPS 50 %
IE 20 %
集 成 图
50%+20%+15%+10%+5%
TPI
100%
NPS 5 %
LEAN 10 %
CELL 15 %
4
CPS
可 成 集 团 C P S 集 成 图
KPI 竞赛
改善 示范线
TPI
CPS
6S 读书会
提案 改善
QCC
5
CPS IE-源于1880年代 工业工程学科
⇒ 『 简化 』
10
CPS
IE相关名词介绍
1. 防错法
如何避免做错事情,使工作第一次就做好的精神能够 具体实现 改善人体动作的方式,減少疲劳使工作更为舒适,更有 效率,不要蛮干. 研究探讨牽涉到几個不同工作或地点之流动关系,以 发掘也可资改善的地方. 借着质问的技巧來发掘出改善的构想
服装单件流水生产方式

服装单件流水生产方式单件流"作业方式简介服装行业的生产制作,多年来有着传统的方式,目前比较普遍采用的是"捆包式"作业.这种方式基本状况是,将一件产品的缝制过程分解成若干道工序,每道工序由一个或一批工人制作。
从前道至后道各工序,每人都集中缝制多件产品,然后以"捆包"方程细分成多道工序,按事先编制的《人机工位布置图》安排,由前到后"单件流水作业"完成。
每一个作业单元岗位按"个人看板"(作业指导书)上的要求,完成较单一的制作内容,形成"一道工序连一道工序,一件产品接一件产品"连续进行的作业形式。
单件流作业系统为服装制作实现JIT目标奠定了基础,是精益生产理论在服装作业中的运用;给服装行业IE活动提出了新的课题和实践内容;它也能为更顺利地达成5S管理目标创造条件;乃至为想实现"日清日高"的企业提供可行性支持。
比较上述两种作业方式,"单件流"形式有着以下特点:一、产品在线周期短,从投入制作到产出,生产过程中无半成品成批积压。
成品产出数量均匀,日产量能明确地把握,有利于作计划安排,也便于控制生产进度。
能很容易地使顾客的分批及时交货的要求得到满足。
二、生产过程中半成品(含因材料所致)的质量问题容易及时被发现,发现一件可及时纠正一件,不会造成大批量的不良品出现。
而"捆包式"作业在生产过程中的不良品往往会延迟发现,造成大批量不合格的情况时有发生。
因此采用"单件流"的方式生产,因不合格而造成的损失少得多。
三、生产效率相对较高。
同样的人数,技能水平相当,设备、场地条件一样的情况下,采用的"单件流"时生产效率较高。
在已成功推行的案例中,经过试运行阶段后,系统步入稳定状态,生产效率同比约可提高20~30%。
四、用"单件流"作业的方式,新款式的"顺线"的时间短。
单件流

此文件只作为个人交流学习使用。
不是公司制式文件。
IE张鹏收集整理单件流是什么?单件流有什么好处?如何实施单件流?单件流生产系统的介绍注:单件流必备的条件:一、整款所有物料要齐全。
二、款式不可半成品绣花。
三、要用自动剪线,倒针质量好的设备。
单件流生产系统的目标、目的、特点、范围、内容一、目标:确保建立平衡式、弹性化、单件流的生产线确保做到成本降低、效率提升、浪费减少确保提高品质与服务质量,满足客人交期二、目的:籍着消除隐藏在企业内的各种浪费,以获取更多的利益。
浪费包括:等待的浪费;库存的浪费;搬运的浪费;动作的浪费;不良品的浪费;加工的浪费;制造过多(早)的浪费。
三、特点:改善成果快速而且多方面性四、范围:起点:客人核可样品后,跟单员将订单资料分发给各相关职能部门时。
终点:员工完成车缝工作,将产品交到包装部时。
五、内容:心:表示思想观念方面必须要先建立起来。
单件流的思想与传统生产观念有很大的不同,改善必须先从意识改革开始。
技:表示技法的意思。
是指要采用什么样的方法,才能将思想,理念做出来。
包括(流线化生产,安定化生产,平稳化生产,超市化生产)下面将做详细介绍。
体:表示体验、实践的意思。
这是整个单件流改善成功的秘诀所在。
只要去做才能发现问题,才能进行改善。
流线化生产流线化生产可以说是单件流中最重要的一个阶段,它可以降低不良率,缩短节奏时间,提高劳动生产力,减少生产空间等等。
它的基本想法就是在避免制造不良品的同时,将成品经由生产流程一个一个的制造出来。
建立流线化生产有以下条件:1、单件流2、按流程顺序布置设备3、生产速度的同步化4、多工序操作的作业5、作业员多能工化6、员工实行手交手作业7、机器设备小型化,可移动8、车位布置“丰”字型化(也有很多工厂为U行线)其中,最强有力的条件就是第一项的单件流,如果因实施不了变成小批量流的话,那么在不知不觉中现场就产生浪费。
那么,如何建立流线化生产线呢?1、全员的意识改革。
单件流带案例

批量化生产
流线化生产
机台(作业台)
多机台作业
多工序作业
作业场地
搬运距离大
物流顺畅,紧密相连
在制品流向
乱流
单向流
生产安排
生产不同步
生产同步
作业者技能
单能工
多能工(团队合作)
设备选用
注重个别效率,采用 通用性,高速度,产能
设备。
设备小型化,注重整体效率,采用速度适当稳 定,加工质量好的专用设备,以及小型,廉价,
备条件;相应地,设备应轻型化、简便化;人员缺席能及时“补位” -操作员之“多能化”:一个人能适应多个工种的需要,便于调配管理 -领导的承诺和全员的参与决心
实施步骤
“单件流”实施步骤:
➢ 平衡需要改进的制程,确定相应的工站数目 ➢ 进行拉线初排
• 遵守“IO”(进出在同一位置)原则,采用“U”形等排布方式 • 将工序一个接一个进行排拉 • 同类型之细胞单元尽量多,产品流动快,WIP也最少(如下例所示)
项目
水平布置
方式 相同功能的加工设备集中摆放在同一 区域
加工段
包装段
适用 大批量生产 特点 集中生产,集中搬运,减少搬运次数
点
装配段
焊
段 测试段
水平布置
特性1-垂直布置
项
垂直布置
目
方 根据产品类别按照加工顺序依 式 次排列
适 柔性生产 用
特 前后各工序紧密相连 点 (流线化生产)
垂直布置
点焊 加工
改为
改善前: 单个工位,许多的盒子和WIP
衡量指标 WIP PPH
改善前 3760
94
改善后: 通过滑槽实现单件流,减少WIP、搬运动作
精益生产的十大工具[].doc
![精益生产的十大工具[].doc](https://img.taocdn.com/s3/m/6b5039b10740be1e640e9a01.png)
精益生产的十大工具[1]1精益生产的十大工具1、准时化生产(JIT)准时生产方式是起源于日本丰田汽车公司,其基本思想是“只在需要的时候,按需要的量生产所需的产品”。
这种生产方式的核心是追求一种无库存的生产系统,或使库存达到最小的生产系统。
2、单件流JIT是精益生产的终极目标,它是通过不断消除浪费、降低库存、减少不良、缩短制造周期时间等具体要求来实现的。
单件流是帮助我们达到这一目标的关键手法之一。
3、看板管理(Kanban)看板是可以作为交流厂内生产管理信息的手段。
看板卡片包含相当多的信息并且可以反复使用。
常用的看板有两种:生产看板和运送看板。
4、零库存管理工厂的库存管理是供应链的一环,也是最基本的一环。
就制造业而言,加强库存管理,可缩短并逐步消除原材料、半成品、成品的滞留时间,减少无效作业和等待时间,防止缺货,提高客户对“质量、成本、交期”三大要素的满意度。
5、全面生产维护(TPM)以全员参与的方式,创建设计优良的设备系统,提高现有设备的利用率,实现安全性和高质量,防止故障发生,从而使企业达到降低成本和全面生产效率的提高。
6、运用价值流图来识别浪费生产过程中到处充斥着惊人的浪费现象,价值流图(ValueStreamMapping)是实施精益系统、消除过程浪费的基础与关键点。
7、生产线平衡设计由于流水线布局不合理导致生产工人无谓地移动,从而降低生产效率;由于动作安排不合理、工艺路线不合理,导致工人三番五次地拿起或放下工件。
8、拉系统与补充拉系统所谓拉动生产是以看板管理为手段,采用“取料制”即后道工序根据“市场”需要进行生产,对本工序在制品短缺的量从前道工序取相同的在制品量,从而形成全过程的拉动控制系统,绝不多生产一件产品。
JIT需要以拉动生产为基础,而拉系统操作是精益生产的典型特征。
精益追求的零库存,主要通过拉系统的作业方式实现的。
9、降低设置时间(SetupReduction)为了使停线等待浪费减为最少,缩短设置时间的过程就是逐步去除和减少所有的非增值作业,并将其转变为非停线时间完成的过程。
单件流

此文件只作为个人交流学习使用。
不是公司制式文件。
IE张鹏收集整理单件流是什么?单件流有什么好处?如何实施单件流?单件流生产系统的介绍注:单件流必备的条件:一、整款所有物料要齐全。
二、款式不可半成品绣花。
三、要用自动剪线,倒针质量好的设备。
单件流生产系统的目标、目的、特点、范围、内容一、目标:确保建立平衡式、弹性化、单件流的生产线确保做到成本降低、效率提升、浪费减少确保提高品质与服务质量,满足客人交期二、目的:籍着消除隐藏在企业内的各种浪费,以获取更多的利益。
浪费包括:等待的浪费;库存的浪费;搬运的浪费;动作的浪费;不良品的浪费;加工的浪费;制造过多(早)的浪费。
三、特点:改善成果快速而且多方面性四、范围:起点:客人核可样品后,跟单员将订单资料分发给各相关职能部门时。
终点:员工完成车缝工作,将产品交到包装部时。
五、内容:心:表示思想观念方面必须要先建立起来。
单件流的思想与传统生产观念有很大的不同,改善必须先从意识改革开始。
技:表示技法的意思。
是指要采用什么样的方法,才能将思想,理念做出来。
包括(流线化生产,安定化生产,平稳化生产,超市化生产)下面将做详细介绍。
体:表示体验、实践的意思。
这是整个单件流改善成功的秘诀所在。
只要去做才能发现问题,才能进行改善。
流线化生产流线化生产可以说是单件流中最重要的一个阶段,它可以降低不良率,缩短节奏时间,提高劳动生产力,减少生产空间等等。
它的基本想法就是在避免制造不良品的同时,将成品经由生产流程一个一个的制造出来。
建立流线化生产有以下条件:1、单件流2、按流程顺序布置设备3、生产速度的同步化4、多工序操作的作业5、作业员多能工化6、员工实行手交手作业7、机器设备小型化,可移动8、车位布置“丰”字型化(也有很多工厂为U行线)其中,最强有力的条件就是第一项的单件流,如果因实施不了变成小批量流的话,那么在不知不觉中现场就产生浪费。
那么,如何建立流线化生产线呢?1、全员的意识改革。
服装企业单件流生产方式的应用与推广

服装企业单件流生产方式的应用与推广作者:刘琼来源:《轻纺工业与技术》 2014年第1期刘琼(江西服装学院,江西南昌330201)【摘要】单件流生产是一种“前推后拉”式的生产,研究认为,其应当采用科学的管理手段,对服装生产过程中的工序标准作业时间、质量控制、计划制定和物料投入等进行把控,力求降低服装生产成本、提高效益、减少库存和缩短生产周期。
【关键词】单件流;劳动效率;在制品Doi:10.3969/j.issn.2095-0101.2014.01.019中图分类号: F768.3文献标识码: A文章编号: 2095-0101(2014)01-0048-02改革开放至今,已将我国打造成为世界服装制造大国和消费大国。
而我国服装企业原有的“劳动密集型”加工方式不再具有优势,我国各级政府正在引导、扶持服装企业朝着“资本密集型”和“技术密集型”生产方式转移。
越来越多的企业面临“招工难”的困境,用工压力、工人素质要求、用人模式等现状迫使企业家思索:如何增强服装企业核心竞争力?完善用人机制、提高生产管理水平及产品品质、改革创新生产方式、更新改造生产设备、提升品牌意识、拓宽营销渠道、积极培养服装产业所需各类人才等成为行业内热议的话题。
多品种、小批量的发展趋势将传统服装企业的生产方式推向了一个新的领域。
批量定制要求服装企业做出快速反应(JIT),服装企业经营管理理念与生产方式必须与快速变化的市场需求相适应。
以发达国家早年推行的精益生产理念结合现今我国服装企业生产现状,实施标准成衣的“单件流”生产方式,有效解决了降低生产成本、提高效益、减少库存和缩短生产周期等棘手问题。
1单件流生产方式的产生传统的劳动密集型服装企业,通常采用的生产方式为捆扎式流水作业。
操作工作中工人普遍文化程度低,管理混乱,柔性化程度低,工序较繁杂,很难满足目前市场上小批量多品种,快速反应等诸多要求。
随着科技水平的日新月异,服装产业结构不断调整革新,产业调整为服装生产走向敏捷制造(简称AM)提供了发展空间。
订单文件(简易版)
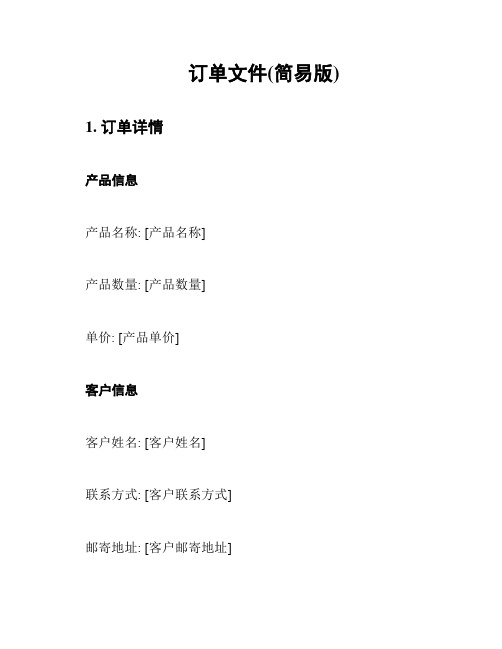
订单文件(简易版) 1. 订单详情
产品信息
产品名称: [产品名称]
产品数量: [产品数量]
单价: [产品单价]
客户信息
客户姓名: [客户姓名]
联系方式: [客户联系方式]
邮寄地址: [客户邮寄地址]
2. 订单总结
订单总金额
订单总金额: [订单总金额]
付款方式
付款方式: [付款方式]
发货方式
发货方式: [发货方式]
3. 订单确认
请客户确认以上订单信息准确无误,并进行付款。
客户确认: [客户确认方式]
4. 其他事项
请在客户付款后的两个工作日内安排发货,并将快递追踪号提供给客户。
如有任何问题,请与我们联系。
谢谢!
订单文件(简易版)
1. 订单详情
产品信息
产品名称: [产品名称]
产品数量: [产品数量]
单价: [产品单价]
客户信息
客户姓名: [客户姓名]
联系方式: [客户联系方式] 邮寄地址: [客户邮寄地址] 2. 订单总结
订单总金额
订单总金额: [订单总金额] 付款方式
付款方式: [付款方式]
发货方式
发货方式: [发货方式]
3. 订单确认
请客户确认以上订单信息准确无误,并进行付款。
客户确认: [客户确认方式]
4. 其他事项
请在客户付款后的两个工作日内安排发货,并将快递追踪号提供给客户。
如有任何问题,请与我们联系。
谢谢!。