TPM_1-TPM
TPM管理体系
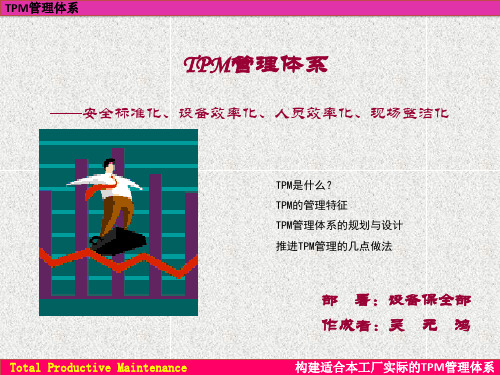
1、认知设备原理和工艺要求。 2、通过原理分析,找到设备与产品质量的内在关联。 3、提出保证产品质量的设备操作、维修、管理对策。 4、制定标准、流程、操作要领书,使对策制度化、标准
化、流程化。
Total Productive Maintenance
构建适合本工厂实际的TPM管理体系
TPM管理体系
3、设备前期管理 1.安装调试:配合安装、调试过程,控制安装中可能出现的质量问题。 2.验收:参与验收、培训工作,提出设备存在问题。 3.问题整改:督促厂家进行问题的整改和重复验收。 4.项目经验总结:总结项目经验,有价值的项目管理过程可以形成流程模型,供后
工厂发展战略 工厂年生产经营目标 工 厂 TPM 总 规 划
依据
依据
各职能部门制定的制度 各工程制定的实施措施
工厂上年度TPM总规划
工厂TPM推进委员会 工厂各级推进组织
TPM职责控制程序
制度体系
保证
修正
制定工厂年度目标计划 年度目标计划审核批准
计划实施 (TPM活动 体制运行)
检查与评价
控制 监督考核
年度普修计划
定期整备计划
使用条件差异分析 问题点对策 制定计划保养临时基准书 自然劣化对策 点检效率化 M-Q关联分析 点检预知化
1、针对问题点提出解决和防范的对策。 2、确认设备的薄弱和关键环节,提出预防和更换对策。 3、针对易损点,提出预防、恢复对策。 4、针对量值易变化点,提出校正方法和计划。
员工的技能水平提高; 企业的凝聚力增强; 企业的形象得到改善; 积极进取的企业文化形成
Total Productive Maintenance
构建适合本工厂实际的TPM管理体系
TPM管理体系
TPM五个阶段
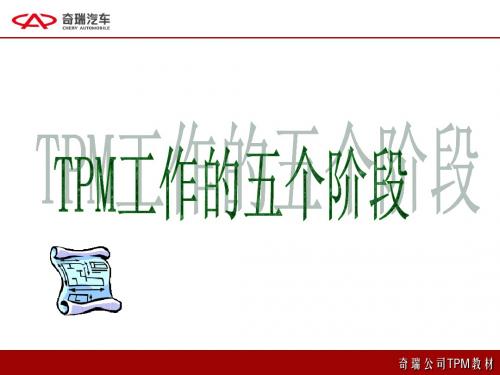
进行自主管理
自主点检体系
定项 定点 定人
定法 点检准备 定周期
定表
定记录 定标
检查
隐患管理
记录 分析
倾向管理 处理
反馈
奇瑞公司TPM教材
进行自主管理
清扫就是找出隐患 通过和设备的“亲密接触”,可以发现异常及缺陷。如:松动、磨损、偏移、震动、声音 异常、发热、漏油、漏水及漏气等;并通过各种有效的手段进行改善,控制。
为了改善员工的现场工作环境,减少对环境造成危害。 因为环境因素直接关系到我们每个人的身心健康。
奇瑞公司TPM教材
清
扫
对于不同的设备,有不同外观和结果,所以清扫时会遇到不 容易的清扫位置,所以还要请我们的设备操作员工,发挥你
的
们的潜质,找出清扫办法和制作清扫工具,并解决问题。
难
设备部门和车间负责人要给员工提供资源支持,有了双手我 们可以创造价值,但只有双手,没有资源,就不会有价值的
污染源 清扫困难源
故障源 浪费源 质量缺陷源 危险源
奇瑞公司TPM教材
对于分类 好的源头, 就要针对 不同的现 象,进行 “6I”工作 了,那什 么是“6I” 哪?
改善影响生产效率和设备效率的环境 改善影响产品质量和服务质量的细微之处 改善影响制造成本之处 改善员工疲劳状况 改善安全与环境 改善工作与服务态度
奇瑞公司TPM教材
奇瑞公司TPM教材
当我们已经总结出好 的方法,我们就应该 把这种方法互相学习, 然后经过科学的论证, 制定我们现场操作的 规范,这样不仅能提 高现场的工作效率, 有了规范的操作,还 能限制工作容易出现 的差错,保护员工不 受伤害,保证设备的 正常运转。
奇瑞公司TPM教材
TPM介绍

项次 1
PartⅠ 降低『制造』成本
追求人与设备的完美发挥, 携手共建轻松职场
PartⅡ
2
1)全面提升人员的素 质,转变观念
3
活动重点
2)提升设备的稼动效能
3)零化活动 4)环境保护活动
九、推动方式
挑战三零
外聘顾问辅导
全面辅导
专家协助培训指导
內部活动推进
个别改善辅导
TPM 活动展开
改善课题使用手法 ‧WHY-WHY分析 ‧PM分析 ‧QC & 新QC手法
TPM 活动简介
Total Productive Maintenance全面性生产保养 Total Productive Management全面性生产管理
一、TPM的发展
TPM于1971年提倡于日本,在刚有TPM一词时, 仅以狭义的观点局限于生产部门的TPM活动,在1989 年之后其定义转为广义的由生产部门展开至全公司的 TPM;活动对象也由以设备为中心扩大到生产系统全 体。损失的消除预防,也由设备的潜在损失提升到生 产系统全体的潜在损失,整个活动也由赚钱的生产体 制进化成赚钱的经营体制。亦即,活动也充实为从排 除阻碍生产效率的要因到排除阻碍经济利益的要因, 整个TPM也已成长为建立追求公司经营事业,经营真 正利益的体制所无法欠缺而存在的。
5)短暂停机、空转 6)速度降低 7)不良重工
400
加工数量-不良数量 稼动时间
良品率=
× 100%
设备综合效率=时间稼动率×性能稼动率×良品率 (例) =87%×50%×98%=42.6%
(例)时间稼动率= 400个-8个 ×100%=98% 400个
六、设备预防哲学
保养的三步骤
─防止→基本条件的整备与运转=自主保养 ─测量→计划保养 自主保养 ─复原(改良)→计划保养 自主保养
TPM-1
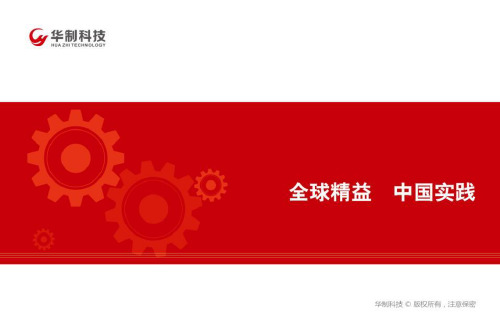
系统化
现场的 体质改善
八 大 支 柱
阶段一
个 别 改 善
自 主 保 全
专 业 保 全
初 期 改 善
事 务 改 善
人 才 培 养
标准化
中效 中生 中设 中技 中质 中安 中业 中教 心率 心产 心备 心术 心量 心全 心务 心育
人员的 体质改善
两大 基石
持续的重复的小集团活动 彻底的5S活动
简化 合理化
26
4、TPM的理念
改善 人的体质 自己的设备自己来保全
保全 运转 部门 部门
我是制造的人 你是维修的人
比设备 强的人
改善 企业体质
有组织的教育、培训
改善 设备体质
维持、改善设备
追求设备的正常状态 消灭设备浪费 主题改善活动 专业保全活动 自主管理活动 初期管理活动 品质保全活动
设备能力的 最大发挥
迷信高速度的设备等
设备维修人员每天/每年都很忙,但是我们的设备 故障率减少了吗?
设备故障75%的原因是清扫与润滑的不良!
制造特点与关注点分析
制造形态 细分
大批量,重复 加工 加工 多品种,少批 量 大批量,流水 线
主要特点
重复生产,批量 大 加工数量少,设 备数量少,能力 大 物动,人不动
企业基础管理方面存在的问题
1. 工作太随意,各自有一套做法,或虽然有统一
的规定但很少执行。 2. 工作太粗糙,使得一些问题无法清楚的把握,
没有进行标准化工作,造成多年来在解决几个
相同的问题。
陈旧的设备管理观念?
我是生产人员,你是维修人员; 设备我操作,维修你负责;
我修理,你设计;
我设计,你操作; 只要稼动率,不要可动率; 只有救火队,没有保养队; 只有单兵作战,没有团队合作;
TMP全面生产管理
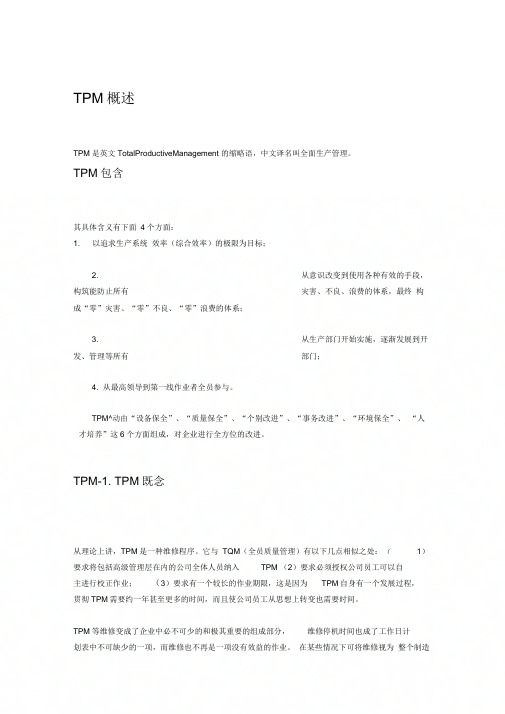
TPM概述TPM是英文TotalProductiveManagement 的缩略语,中文译名叫全面生产管理。
TPM包含其具体含义有下面4个方面:1. 以追求生产系统效率(综合效率)的极限为目标;2. 从意识改变到使用各种有效的手段,构筑能防止所有灾害、不良、浪费的体系,最终构成“零”灾害、“零”不良、“零”浪费的体系;3. 从生产部门开始实施,逐渐发展到开发、管理等所有部门;4. 从最高领导到第一线作业者全员参与。
TPM^动由“设备保全”、“质量保全”、“个别改进”、“事务改进”、“环境保全”、“人才培养”这6个方面组成,对企业进行全方位的改进。
TPM-1. TPM既念从理论上讲,TPM是一种维修程序。
它与TQM(全员质量管理)有以下几点相似之处:(1)要求将包括高级管理层在内的公司全体人员纳入TPM (2)要求必须授权公司员工可以自主进行校正作业;(3)要求有一个较长的作业期限,这是因为TPM自身有一个发展过程,贯彻TPM需要约一年甚至更多的时间,而且使公司员工从思想上转变也需要时间。
TPM等维修变成了企业中必不可少的和极其重要的组成部分,维修停机时间也成了工作日计划表中不可缺少的一项,而维修也不再是一项没有效益的作业。
在某些情况下可将维修视为整个制造过程的组成部分,而不是简单地在流水线出现故障后进行,其目的是将应急的和计划外的维修最小化。
TPM-2 TPM的起源TPM起源于“全员质量管理(TQM ” 。
TQ观W•爱德华•德明博士对日本工业产生影响的直接结果。
德明博士在二战后不久就到日本开展他的工作。
作为一名统计学家,他最初只是负责教授日本人如何在其制造业中运用统计分析。
进而如何利用其数据结果,在制造过程中控制产品质量。
最初的统计过程及其产生的质量控制原理不久受到日本人职业道德的影响,形成了具有日本特色的工业生存之道,这种新型的制造概念最终形成了众所周知TQM当TQ硬求将设备维修作为其中一项检验要素时,发现TQ咻身似乎并不适合维修环境。
TPM基础知识

一、TPM的真正含义
TPM( Total Productive Maintenance)
★ 译名:TPM,全员生产性保全,也叫全员自主保全。 ★目标:TPM通过改善人和设备的体质,改善企业的体质。 ★本质:TPM是一种现场改善系统!
T 全员
Total
全员、全面、全过程 生产 保全、维护
Productive Maintenance
明确理解设 发生异常时的 备和品质的 对策方法,提 关系,在不 高操作可靠性 良发生之前 解决问题
1 ~ 6 阶段 理解工序的性 的体制化, 能、调整方法、 习惯化
0 阶段 : 彻底的整理 / 整顿 / 清扫
:金钱(Money)、人(Man)、设备(Machine)、材料(Material)、方法(Method)
全新认识
TPM专题培训
目录
一 二 三 TPM的真正含义 TPM活动体系和阶段内容 公司推行进度
四
各作业部TPM亮点典范
一、TPM的真正含义
1
2 3 4 什么是TPM TPM两大基石
TPM和6S的关系
TPM三大哲学思想
一、TPM的真正含义
1
三
什么叫TPM
一、TPM的真正含义
1、什么是TPM?
第三,是焦点改 善活动,旨在降 低经营成本,强 化企业竞争力。
TPM三大活动机制
二、TPM活动体系和阶段内容
三
二、TPM活动体系和阶段内容
2、TPM8大支柱
一套体系
六大指标
八大支柱
自 主 保 全
个 别 改 善
初 期 管 理
专 业 保 全
教 育 训 练
品 质 保 全
安 全 环 境
什么是TPM
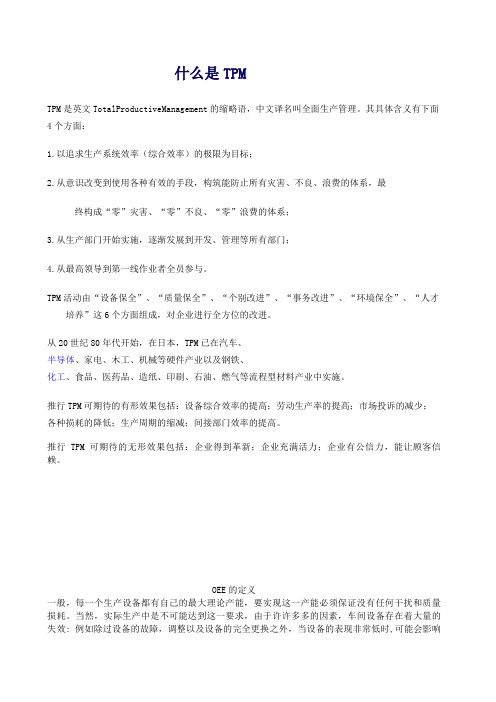
什么是TPMTPM是英文TotalProductiveManagement的缩略语,中文译名叫全面生产管理。
其具体含义有下面4个方面:1.以追求生产系统效率(综合效率)的极限为目标;2.从意识改变到使用各种有效的手段,构筑能防止所有灾害、不良、浪费的体系,最终构成“零”灾害、“零”不良、“零”浪费的体系;3.从生产部门开始实施,逐渐发展到开发、管理等所有部门;4.从最高领导到第一线作业者全员参与。
TPM活动由“设备保全”、“质量保全”、“个别改进”、“事务改进”、“环境保全”、“人才培养”这6个方面组成,对企业进行全方位的改进。
从20世纪80年代开始,在日本,TPM已在汽车、半导体、家电、木工、机械等硬件产业以及钢铁、化工、食品、医药品、造纸、印刷、石油、燃气等流程型材料产业中实施。
推行TPM可期待的有形效果包括:设备综合效率的提高;劳动生产率的提高;市场投诉的减少;各种损耗的降低;生产周期的缩减;间接部门效率的提高。
推行TPM可期待的无形效果包括:企业得到革新;企业充满活力;企业有公信力,能让顾客信赖。
OEE的定义一般,每一个生产设备都有自己的最大理论产能,要实现这一产能必须保证没有任何干扰和质量损耗。
当然,实际生产中是不可能达到这一要求,由于许许多多的因素,车间设备存在着大量的失效: 例如除过设备的故障,调整以及设备的完全更换之外,当设备的表现非常低时,可能会影响生产率,产生次品,返工等。
OEE是一个独立的测量工具,它用来表现实际的生产能力相对于理论产能的比率。
国际上对OEE的定义为:OEE是Overall Equipment Effectiveness(全局设备效率)的缩写,它由可用率,表现性以及质量指数三个关键要素组成,即:OEE=可用率X 表现性 X质量指数。
其中:可用率=操作时间 / 计划工作时间它是用来考虑停工所带来的损失,包括引起计划生产发生停工的任何事件,例如设备故障,原料短缺以及生产方法的改变等。
全面生产维护——TPM1

1)改善生产模具、设备与生产方法的可靠性、可维修 性及安全性,并且将这些关键点(Know-How)汇编成 为一套技术规范。 2)用现有的设备、模具、夹具,制造出质量稳定、满 足标准的产品,并将这些Know-How传授给全体一线员 工。 3)提升设备的有效利用率及运行期间的生产能力。
4)培养对设备有兴趣、且爱护设备的企业文化,训练 一批对设备精通熟悉的专业人才。
1971
全面规范化生产 维护(TnPM)
全面生产维修时代(TPM)
1980
预知维修时代(PdM)
1995
预防管理时代
2002
精益TPM
基于时间的维修(TBM) 基于状态的维修(CBM) 24
三、TPM的演进过程
第一阶段 事后维修
在1950年前后,以半自动、手动操作设 备居多,设备结构简单,常采用的方法,在
◇严格的品质要求
竞争
要求设备效率最大化◇
◇合格率的提高
◇顾客需求的多样性 ◇因设备故障而发生的不良 品质角度
维持、管理费用的合理化◇
技术经验的积累◇ 提高产出投入比◇ 成本角度
5
一、为什么要进行TPM?
企业面临的生存危机
50年前世界财富500强,今天只有一半 日本和欧洲企业的平均寿命不到12.5年
tpm全面生产维护

tpm全面生产维护TPM全面生产维护,也就是全面生产维护,是一种灵活的、持续的、系统性的生产维护手段,也是一种优化生产流程,提升企业生产效率和质量的方法。
TPM的目标是全面消除设备故障,实现设备的高效率、高可靠性、高质量运行,并且让设备在整个生命周期内最大程度地发挥作用。
一. TPM全面生产维护的概念TPM全面生产维护是以人、机、料、法、环境五个要素为核心,以实现设备的高效率、高可靠性、高质量以及最大程度地发挥作用为目标,通过维护、保养、修理、改善等手段,实现设备和生产效率的最优化。
TPM全面生产维护着重强调对设备的全面管理,在这个过程中,不仅保证设备顺畅运转以达到高产、高效的生产水平,同时也要提倡工艺流程的不断完善与提高。
这种全面生产维护方法是通过充分发挥工人个人能力、实现设备新旧转换、提高设备利用率、促进质量管理和生产计划逐步的执行,从而在生产流程中消除浪费以及缩短设备故障时间。
TPM全面生产维护的实施,不仅是制造企业走向优质、高效的必经之路,也是“机器蓝领”转换为“机器白领”的途径。
二. TPM全面生产维护的优点1. 提高生产效率: TPM全面生产维护强调定期点检和效益检查,可以减少设备故障率,尽可能保证设备工作的稳定性和效率。
这不仅可以减少损失,还可以减少停机时间,提高生产效率。
2. 提高质量水平: TPM全面生产维护通过优化制造流程和提高设备可靠性,可以减少生产过程中的浪费,提高产品的质量水平。
这可以有效地减少不良品率,提高客户满意度。
3. 提高设备利用率: TPM全面生产维护可以优化设备的性能,延长设备的使用寿命,降低设备的维修费用和停机时间,进而提高设备利用率。
4. 增加工人的参与和责任: TPM全面生产维护要求员工全面参与维护工作,不仅提高员工的素质,还能够提高员工的责任感和自我管理能力。
5. 实行精益生产管理: TPM全面生产维护可以实现精益生产管理,加强管理和工艺流程的优化,从而使生产流程更加有效率。
TPM系列课程1_TPM概论_Rev 1.12

TPM字面含义﹕
T: Total(全员参与)
• • • • 全员﹕从总经理到员工 全过程﹕从原料到产品 全部门﹕包含公司所有部门 全寿命周期﹕从设备设计到报废的全寿命周期
P: Productive(生产性)
•
•
P﹕PreventionPredictiveProductive
M﹕MaintenanceManagement
设备故障后 或性能下降 后才修理 预防保养, 防止故障发 生,从而延 长设备寿命 用最经济的 方式进行保 养,以提高 企业的生产 力 操作人员和 维修人员同 时对设备进 行保养 (PM+全员) 从只注重生 产单位保养 的系统,转 变成为注重 全公司经营 改革的系统
BM(事后保养,Break-down Maintence)
制作:XXX 日期:2013.04.1 版本:Rev 1.12
Page:1
目录
目录
• • • • • • •
1﹑TPM的产生及推广 2﹑TPM的内涵 3﹑零故障的思想和手段 4﹑TPM八大支柱简介 5﹑评价TPM成果指标 6﹑推行TPM产生的效益 7﹑TPM和5S﹑TPS﹑TQC的关系
Page:2
(能源)
暖机损失 超负荷损失 发热损失 能源损失 模/治工具损失 投入能源 有效能源
(材料)
投入材料(个数﹐重量) 良品个数 不良损失 暖机损失
阻 碍 设 备 效 率 化 的 8 大 损 失
良品重量
头尾料损失 重量的损失
成品率损失
阻碍原物料效率化的3大损失
宽裕太多的损失
Page:16
2.4 重复小集团&全员参与
机能低下型故障﹕由于部分设备机能的下降﹐虽没有导致设备的停止运行﹐却造成了各 种损失(例如﹕不良品增多﹑速度降低﹑小停顿增加等)
TPM是什么_TPM是什么意思

TPM是什么_TPM是什么意思什么是TPM?全⾯⽣产维护(TPM)是⼀个维护程序的概念。
TPM的全称为TotalProductiveMaintenance以最⼤限度提⾼⽣产效率为⽬标以“5S活动”为基础从总经理到⼀线员⼯的全体成员为主体以相互连接的⼩组活动形式以设备及物流为切⼊点进⾏思考创造整合有机的⽣产体系TPM的发展历史:1事后维修(BM:BreakdownMaintenance)故障后再维护;1950年以前2改良维修(CM:CorrectiveMaintenance)查找薄弱部位对其进⾏改良1950年以后3预防维修(PMreventiveMaintenance)对周期性故障提出的维护1955年前后6全⾯⽣产维护(TPM:TotalProductiveMaintenance)全员参加型的保养1980年以后5⽣产维修(PM:ProductiveMaintenance)综合上述维护⽅法,系统的维护⽅案1960年前后4维修预防(MP:MaintenancePrevention)设计不发⽣故障的设备,设备FMEA1960年前后TPM与TQM的关系:TPM是TQM演变⽽来的.TQM是W.EdwardsDeming博⼠在影响⽇本⼯业的直接效果下发展得来.Deming博⼠是在⼆战结束不久后在⽇本开始⼯作的,作为⼀个统计学家,他⾸次向⽇本⼈展⽰了如何在制造过程中使⽤统计分析和如何在制造过程中使⽤效果数据来控制质量。
由⽇本⼯作理论建⽴的早期统计程序和效果质量控制概念很快成为⽇本⼯业的—种⽣存⽅式,这种新的制造概念最终被命名为全⾯质量管理(TQM)。
当⼯⼚维护的问题作为TQM程序部分被检查出来,⼀些通⽤概念看起来在维护环境中就不太适合或不能发挥作⽤。
原始的TQM概念做了⼀些修正。
这些调整将维护提升⾄全⾯质量管理程序的⼀个重要部分TPM是⼀个以制造业领先的创新,强调⼈的重要性。
⼀个“能做”和“持续改进”理论、⽣产的重要性和维护员⼯共同协作。
TPM基础知识

TPM基础知识TPM基础知识一:TPM(Total Productive Maintenance)即全面生产维护.是以提升设备综合效率为目标,以全系统的预防维护为过程,全体人员参与为基础的设备保养和维修体制.企业开展TPM的活动的主要目的:提升员工素质,提高设备综合效率.二:TPM活动的五大要素:1致力于设备综合效率最大化的目标2在整个设备一生建立彻底的预防维修体制3由各部门共同推行4涉及每个雇员:从最高领导到现场工人5:通过机动管理,自主小组活动推动TPM三:TPM推进基础就是:对设备不断开展有效的5S管理,持续创新小组维护改善四: TPM1阶段主要开展以下3项工作:1 持续开展TPM0阶段没有做完的(清洁,点检,润滑,安全)各项工作;其中,点检,润滑是当前TPM工作的核心重点!2 大力开展员工培训,了解岗位设备六大系统,清除设备故障六源,具有一般设备故障处理能力;3 发扬全员参与精神持续开展各项改善活动,促进设备综合效率提升10%五: 点检就是员工对设备重点部位的日常检查,注意对比跟踪设备磨损,噪音,松动,变形,渗漏,堵塞龟裂,接触不良等情况提前把这些缺陷反馈出来,以便及时排除.点检的关键是检查及时,整改跟踪不放松,否则毫无实际作用.六润滑就是设备运动摩擦部位加入某种介质,以减少设备运动阻力,减少磨损,延长运动部位使用寿命.设备润滑要做好"八定":定人,定点,定时,定质,定量,定方法,定记录,定规范.七设备润滑存在污染,主要来自三方面:设备生产系统岗位设备操作人员应做到"三好四会":管理好,使用好,保养好,\;会正确操作,会日常维护点检,会排除一般故障.九设备六大系统:主要指构成设备功能的六大系统部件,即"动力,能源系统","机械传动系统","气路系统","油路系统",电控系统","安全防护系统".十设备机械序言:请关注现场的浪费借作一个半满的杯子这一著名的例子来解释现场改善的基础内容:悲观主义者说一半是空的;乐观主义者说一半是满的;现场改善者说这么大的杯子。
TPM推进手册-什么是TPM(1-2)

TPM推进手册-什么是TPM (1)第一章什么是TPM1.TPM即T otal P roductive M aintenance→T otal P roductiveM anagementTPM意为“全员参加的生产保全”(T otal・P roductive・M aintenance),其目的是彻底排除生产现场中出现的损耗和浪费,通过追求生产系统中的最高效率来促使企业的业绩提高、形成有价值的企业。
最近,TPM中M的含义逐步倾向于management(经营管理),从以往以设备管理为中心的做法改变为加入其他管理方式的做法,使企业在综合活动中发展成为有活力、有竞争力的团体。
2.向TPM进化的过程日本保全活动的发展阶段通常被称为「PM进化的4个阶段」,其发展过程如下图所示。
第2阶段「预防保全时代」(PM:Preventive Maintenance)第3阶段「生产保全时代」(PM:Productive Maintenance)(在维持高信赖性、保全性的同时还要争取更多的利润)第4阶段「TPM时代」(TPM:TotalProductive Maintenance)详细说明(1)预防保全(PM:Preventive Maintenance)……即设备的健康管理,也可以说是设备的预防医学。
预防医学的发达使人类的疾病得到了有效预防,延长了寿命。
同样,预防保全也是以通过预防设备可能出现的故障(疾病)而最终达到延长其使用寿命的活动。
(2)改良保全(CM:Corrective Maintenance)……对于机器故障防患于未然的想法得到进一步的发展,改良保全就是以不发生故障(提高信赖性)或易于保全(提高保全性)为目的,对设备进行改良的做法。
(3)保全予防(MP:Maintenance Prevention)……新设备在计划阶段即采取不需要保全(maintenance free)的设计方法。
使设备最初的状态就达到“不需要保全的设计”,要接近和实现这个目标还需要我们付出更多的努力。
- 1、下载文档前请自行甄别文档内容的完整性,平台不提供额外的编辑、内容补充、找答案等附加服务。
- 2、"仅部分预览"的文档,不可在线预览部分如存在完整性等问题,可反馈申请退款(可完整预览的文档不适用该条件!)。
- 3、如文档侵犯您的权益,请联系客服反馈,我们会尽快为您处理(人工客服工作时间:9:00-18:30)。
production生产
我们没空做这些事情… 真的吗?
Page 14
Page 9
TPM 带来的变化
Higher Productivity
更高的生产能力
Page 10
Shorter Lead time
更短的供货时间
Zero Quality Complaints
零质量投诉
On-Time Delivery
准时交货
Customer Satisfaction
客户满意度
TPM及预防性维护(Preventive Maintenance)的目标:
Page 4
什么是TPM?
全员生产维护---"Total Productive Maintenance".
全员/Total: 所有可能的损失/浪费, 考虑所有相关的人员 生产/Productive: 通过减少计划外停机来优化整机效率 维护/Maintenance: 利用计划内停机进行维修和优化改进,包括所有相关部门人员及领导层的参与,生产部门要负 责检查维护部门的工作
更高维护成本Higher maintenance costs
09.06.2015 Page 6
为什么我们需要TPM?
TPM的更高目标是优化质量、成本和供货服务,以及激励。
Quality 质量
Quality 质量 • Reducing scrap减少缺陷品 • Avoiding rework避免返工 • Reducing inspection costs减少检验成本 Costs 成本 • Reducing investment降低投资 • Reducing quality costs降低质量成本 • Reducing maintenance costs减少维护成本 Delivery service 供货服务 • Improving availability提升可用性 • Reducing lot sizes降低批次 • Reducing inventories减少库存 • Reducing throughput time压缩通过时间 Motivation as a result of:激励的结果 • Identification with equipment and processes 明确设备与工艺流程 • Awareness of waste了解浪费 • Qualification资质认证 • Expanded field of activity扩展职能范围
OEE (机器设备总体利用率/ Overall Equipment Efficiency)
中断
总运转时间 Gross working time 净运转时间 Net working time 换模
Set up
OEE =
净 生产力 净 运转时间
= AF*OF*QF
停机
Outage 性能损失 Perfo loss 废品/ 返工
Page 2
Heinrich‘s Law*海因里希事故法则
If minor acts of negligence are not prevented, they will grow into major accidents 如果很多较小的粗心行为没有阻止, 将会导致更加严重的事故发生 Small acts of negligence
激励
Costs 成本
Delivery service 供货服务
09.06.2015 Page 7
TPM会给我们带来什么?
● 消除减少8大浪费
过剩生产、库存、等待、运输、动作、返工与维修、多余加工步骤、人才
● 消除非计划停机。
● 提升OEE—没有其他公司可以与你匹敌,具有同样的优势。如果有,他 就总是更低成本的制造商或供应商。 ● 让客户满意,做到零缺陷。 ● 减少运营成本$$$$。 ● 提升操作工的工作效率和主人翁责任感。
提高设备总体利用率/OEE (Overall Equipment Effectiveness)
维护/Maintenance
生产/Production
planned downtime
计划维护 planned maint.
计划维护/planned maint.
inspection
planned downtime
预防性维护 preventive maint. 项目相关维护 project related maint. 设备损伤的维护 damage related maint. 计划检修 scheduled repairs
unplanned downtime
unplanned downtime
对员工进行 自主设备 检查的培训
Production is responsible for TPM. Maintanence gives support. 生产部门负责TPM,维护部门提供支持。
Page 5
为什么我们需要TPM?
设备停机具有耗。
非计划停机
Additional costs for repairs, replacement procurement额外的修护和备件采购成本 Lower revenue as a result of late delivery 逾期交货降低收益 Compensation payments赔付 Reduced profit减少收益 Additional costs for overtime超时成本 Additional costs for procurement 额外采购成本
较小的粗心行为发生330起 More major failings (short periods of downtime) 发生主要过失或故障29起
Facts : ● ● 70% of all mechanical failures are related to contamination or improper lubrication practices. Simple autonomous TLC (tighten – lubricate – clean) generally eliminates 50 – 70% of unplanned stoppages. Inadequate maintenance practices typically wastes 20 – 50% of spare parts budget.
●
事实证明: •70%机械故障与设备污染或不 适合的润滑习惯有关 •简单的自主的TLC(拧紧-润滑清洁)一般能剔除50%-70%的 非计划停机 •典型的不正确的保养习惯会浪 费20%-50%的备件预算
Source = Lean – TPM Copyright 2009 Michigan Mfg. Technical Center
Page 8
TPM 带来的变化
维修成本&时间
停产时间
备件库存
Maintenance Cost & Hours
Production Downtime
Spare Parts Inventory
Equipment Reliability
设备可靠性
Planned Repairs
计划维修
09.06.2015 3/15/2011
Titanic event 严重事故1起
* This law is named for Herbert William Heinrich, an employee of Traveler's Insurance company who as long ago as 1931 recognized a correlation between minor and serious accidents.
Additional investment expenditure
额外投资支出
更高人力成本Higher personnel costs Higher inventory costs and interest costs 更高库存及利息 报废和返工成本Scrap and rework costs
额外能源成本Additional energy costs
全员生产维护
2015 May30
你知道吗?
● 尽管制造工艺不同,但三分之二的美国制造公司都是事后诸葛亮-设备失效维护。
● 70 % 的机器失效都是由于污染或不当润滑引起的。 ● 近两亿$的全年收入损失直接来自于缺乏设备维护。 ● 重建维护体系,从损失成本的失效到节省成本的收益,投资回报率可达一比六。 ● 主动的设备维护通常可节约5%到10%的能源。 ● 操作工简单的自主维护T L C ( 拧紧Tighten – 润滑Lubricate – 清洁Clean ) 通常可减少50%到70%的非计划停机。 ● 不当维护会增加20 %到50 %的备件预算浪费。 ● 操作设备直到失效才停机的做法通常会导致额外超过30%的设备维护资金浪费。
Production employee 生产员工
● Fewer "emergencies" 更少的“紧急事件” ● More time for preventive maintenance 预防性维护时间更长
xx
Maintenance employee 维护员工
09.06.2015 Page 12
什么是OEE?
09.06.2015 3/15/2011 Page 3
什么是TPM ?
● W.Edwards Deming, 1950, Japan
● Total Productive Maintenance (TPM) — 优化制造设备及工艺流程的产能 — 提升不同阶层员工的工作效率 — 保障设备处于良好的工作状态 — 使得由于设备维修、产品缺陷及换装等因素造成的产能损失降到最小 ● TPM 包括创造良好的生产环境 : — 激励员工 — 涉及生产的方方面面: 设备性能、产品质量、换装与维护 — 最大化设备利用率而不只是可用率 ● 在生产日安排计划停机,要从可用时间内减除。