矿热炉设计方案
矿热炉设计方案
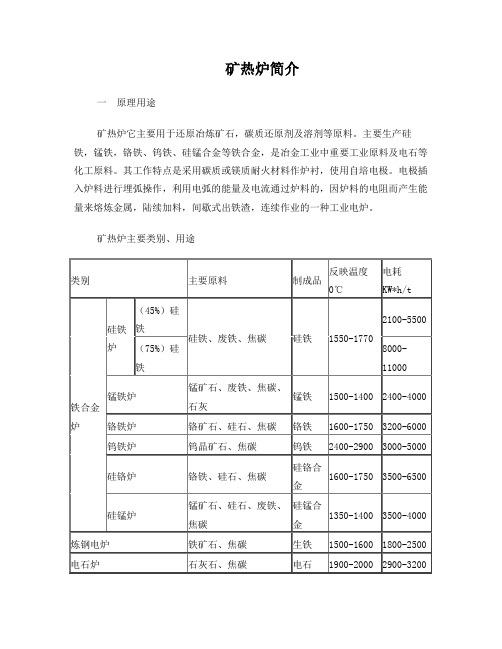
矿热炉简介一原理用途矿热炉它主要用于还原冶炼矿石,碳质还原剂及溶剂等原料。
主要生产硅铁,锰铁,铬铁、钨铁、硅锰合金等铁合金,是冶金工业中重要工业原料及电石等化工原料。
其工作特点是采用碳质或镁质耐火材料作炉衬,使用自培电极。
电极插入炉料进行埋弧操作,利用电弧的能量及电流通过炉料的,因炉料的电阻而产生能量来熔炼金属,陆续加料,间歇式出铁渣,连续作业的一种工业电炉。
矿热炉主要类别、用途(1)电耗值随原料成分,制成品成分,电炉容量等的不同而有很大差异。
这里是约值。
二结构特点矿热炉是一种耗电量巨大的工业电炉。
主要由炉壳,烟罩、炉衬、短网,水冷系统,排烟系统,除尘系统,电极壳,电极压放及升降系统,上下料系统,把持器,烧穿器,液压系统,矿热炉变压器及各种电器设备等组成。
矿热炉设备共分三层布置第一层为炉体(包括炉底支撑、炉壳、炉衬),出铁系统(包括包或锅及包车等),烧穿器等组成。
第二层(1)烟罩。
矿热炉目前大多数采用密闭式、或半密闭式矮烟罩结构,具有环保和便于维修,改善操作环境的特点。
采用密闭式结构还可把生产中产生的废气(主要成分是一氧化碳)收集起来综合利用,并可减少电路的热损失,降低电极上部的温度,改善操作条件。
(2)电极把持器。
大多数矿热炉都由三相供电,电极按正三角形或倒三角形,对称位置布置在炉膛中间。
大型矿热炉一般采用无烟煤,焦碳和煤沥青拌合成的电极料,在电炉冶炼过程中自己培烧成的电极。
(3)短网(4)铜瓦(5)电极壳(6)下料系统(7)倒炉机(8)排烟系统(9)水冷系统(10)矿热炉变压器(11)操作系统第三层(1)液压系统(2)电极压放装置(3)电极升降系统(4)钢平台(5)料斗及环行布料车其他附属;斜桥上料系统,电子配料系统等三、矿热炉主要配置方案四、矿热炉主要设备1.主要设备:本设计选用矮烟罩半封闭固定式矿热炉,主要设备选择如下:1.1炉体炉体是由炉壳、炉衬、炉底支撐等构成,炉壳采用14~18mm厚钢板焊接而成的圆筒体,外部焊接有加强筋,以保证炉体具有足够的强度。
12500kVA矿热炉烟气净化系统设计方案及技术

12500kV A矿热炉烟气净化系统设计方案及技术一、设计依据1.本设计依据冶金工业部《钢铁工业烟气净化技术政策规定》第七章“铁合金电炉烟烟气净化”中有关规定。
2.废气排放执行GB9078-1996《工业炉窑大气污染物排放标准》中一级排放标准。
3.产生的噪声执行GB12348-90《工业企业厂界噪声标准》之规定,即厂界噪声白天≤65db,夜间≤55db。
二、设计目标:1.烟气排放浓度<50mg/Nm3.系统除尘效率>99.8%。
2. 回收的硅粉其含SiO2量≥92%。
3.投资省、结构合理、维护简便,运行费用低。
三、设计参数(由厂家提供或设计手册)12500KVA矿热炉矮烟罩,半封闭式,一般情况下的烟气排放工艺参数:1、炉罩烟气量:70000Nm3/h( 标态)2、烟气温度:450 ℃3、烟气含尘浓度:3.6-5g/Nm3低压脉冲除尘系统一、概述:负压过滤式除尘系统在硅粉予处理器前端与正压过滤式没有区别。
区别在于除尘器设在主引风机前端(入口前),净化后的烟气是通过烟囱排放的。
与传统的负压过滤反吹清灰所不同的是此方案采用的是负压过滤脉冲清灰方式,所选除尘设备是:JDDM系列长袋低压脉冲布袋除尘器。
此项技术的成功应用改变了传统的负压过滤式除尘器投资大,设备体积大,清灰效果不够,设备运行阻力偏高等缺陷,脉冲清灰方式布袋除尘器应用在铁合金矿热炉上,确实是国内最新的除尘技术。
它的特点是:(1)投资省,占地面积小。
该设备选用的新型复合滤料与玻纤滤料相比其耐磨性、抗折性及剥离强度有明显提高,即能耐高温,又能提高过滤风速,是玻纤滤料的一倍,相应地减少了除尘器过滤面积,是玻纤滤袋除尘器过滤面积的一半,设备重量比较轻50%。
达到了降低投资成本,减少占地面积的目的。
(2)清灰效果好。
清灰效果是除尘器使用的关键因素,该设备采用大口径淹没式直通脉冲阀,喷吹阻力小,气压低,清灰瞬间喷吹压力达到2000pa,强力清灰彻底、效果好。
33万硅锰矿热炉技术条件

33000KVA矿热电炉厂设计思路及主体设备框架简述一.产品品种标准及原材料技术条件:1.1、产品品种、标准设计主要考虑生产猛系铁合金。
以猛硅合金,高碳猛铁为主,将来兼具屮低碳猛铁生产。
1.2、产品标准为:镭硅合金GB/T4008—一1996 具体例表略二•生产工艺过程及生产技术指标:2.1.生产能力:以生产镭硅合金Mn68Sil8牌号为例:单台电炉口产量为132t具体计算略。
单台电炉年产以330天计,年产量为:43560t2.2、工艺流程2.2.1.镒硅合金猛矿硅石英自动称量配料炉顶料仓入炉冶炼焦炭出铁扒渣浇注脱模精整入库白云石(取样分析)2.2.2,物流描述将原料堆场的合格原料,如猛矿、焦炭、辅料等根据生产的品种由原料场的低位料仓经皮带输送系统按要求驳至配料区编号的高位料仓。
由配料操作人员按技术指令和规定的配料程序,将高位料仓的料经自动配料系统下放配料,再将配好的料批经皮带输送至电炉上料系统的料斗内肿动上料系统的料斗。
经斜桥输送至炉顶料仓平台,将配好的料倒入炉顶料仓平台设置的中间料斗。
上料系统的料斗返回加动与中间料斗相衔接的输送系统,将中间料斗的料批驳至炉顶布料小车内,由炉顶布料小车沿环形道轨将料批卸至炉顶料仓内。
炉顶料仓内的炉料经料管进入炉内冶炼。
依据冶炼技术制订的出铁制度,经过规定的冶炼时间,由炉前操作人员启动开堵眼机开眼,将炉内铁水及液渣从炉眼放出。
炉眼流槽下沿的铁水包、渣罐,按炉前工艺布置呈阶梯式排列。
铁水.液渣经炉眼流槽进入铁水包,随着液面的上升,铁水将比重轻的浮在铁水液面上的液渣顶入渣罐,直至出铁完成。
将安置在出铁小车上的铁水包、渣罐用立式卷扬系统,通过道轨拉出。
用行车将铁水包吊至扒渣区扒渣,随后将扒完渣的铁水包吊至浇注区的锭模处进行浇注操作。
边浇注边取样,取样按取样规则执行。
浇注完毕,将空包卅至清渣区待冷却清渣。
用行车将渣罐吊至冲渣区进行冲水渣操作,冲渣完毕,将渣罐经清渣后,再置于炉前小车上,进入下一次出铁程序。
12500KVA矿热炉开炉方案
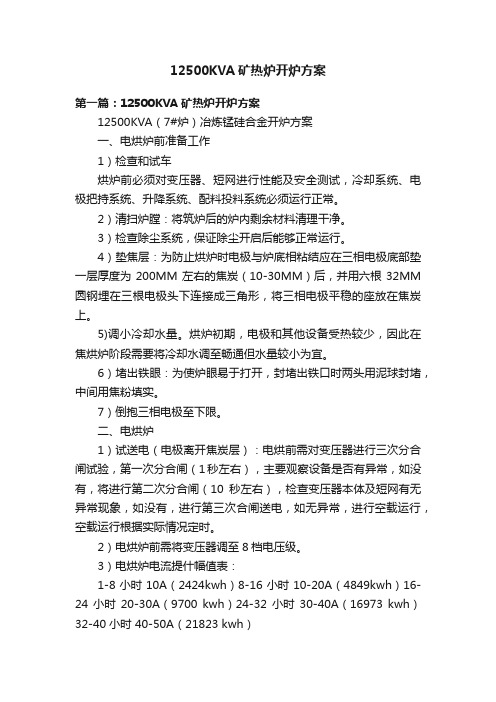
12500KVA矿热炉开炉方案第一篇:12500KVA矿热炉开炉方案12500KVA(7#炉)冶炼锰硅合金开炉方案一、电烘炉前准备工作1)检查和试车烘炉前必须对变压器、短网进行性能及安全测试,冷却系统、电极把持系统、升降系统、配料投料系统必须运行正常。
2)清扫炉膛:将筑炉后的炉内剩余材料清理干净。
3)检查除尘系统,保证除尘开启后能够正常运行。
4)垫焦层:为防止烘炉时电极与炉底相粘结应在三相电极底部垫一层厚度为200MM左右的焦炭(10-30MM)后,并用六根32MM 圆钢埋在三根电极头下连接成三角形,将三相电极平稳的座放在焦炭上。
5)调小冷却水量。
烘炉初期,电极和其他设备受热较少,因此在焦烘炉阶段需要将冷却水调至畅通但水量较小为宜。
6)堵出铁眼:为使炉眼易于打开,封堵出铁口时两头用泥球封堵,中间用焦粉填实。
7)倒抱三相电极至下限。
二、电烘炉1)试送电(电极离开焦炭层):电烘前需对变压器进行三次分合闸试验,第一次分合闸(1秒左右),主要观察设备是否有异常,如没有,将进行第二次分合闸(10秒左右),检查变压器本体及短网有无异常现象,如没有,进行第三次合闸送电,如无异常,进行空载运行,空载运行根据实际情况定时。
2)电烘炉前需将变压器调至8档电压级。
3)电烘炉电流提什幅值表:1-8小时10A(2424kwh)8-16小时10-20A(4849kwh)16-24小时20-30A(9700 kwh)24-32小时30-40A(16973 kwh)32-40小时 40-50A(21823 kwh)4)本次电烘炉时间大约为40小时左右,用电量为5万KWH左右。
5)电烘炉时为稳定电弧和保持所规定的功率,可根据具体情况给电极周围添加新焦炭,并使焦炭绕电极成馒头体状。
6)电烘炉时应尽量少活动电极,并使三根电极负荷保持均衡,不可单独升高某相电极电流,以免出现漏糊等电极事故。
7)当出现电极负荷给不起时,若需下放电极必须有车间主任指令或其他干部亲自指挥方可停电下放,再送电后,电流要慢慢逐步给起。
12500KVA矿热炉开炉方案

12500KVA(7#炉)冶炼锰硅合金开炉方案一、电烘炉前准备工作1)检查和试车烘炉前必须对变压器、短网进行性能及安全测试,冷却系统、电极把持系统、升降系统、配料投料系统必须运行正常。
2)清扫炉膛:将筑炉后的炉内剩余材料清理干净。
3)检查除尘系统,保证除尘开启后能够正常运行。
4)垫焦层:为防止烘炉时电极与炉底相粘结应在三相电极底部垫一层厚度为200MM左右的焦炭(10-30MM)后,并用六根32MM圆钢埋在三根电极头下连接成三角形,将三相电极平稳的座放在焦炭上。
5)调小冷却水量。
烘炉初期,电极和其他设备受热较少,因此在焦烘炉阶段需要将冷却水调至畅通但水量较小为宜。
6)堵出铁眼:为使炉眼易于打开,封堵出铁口时两头用泥球封堵,中间用焦粉填实。
7)倒抱三相电极至下限。
二、电烘炉1)试送电(电极离开焦炭层):电烘前需对变压器进行三次分合闸试验,第一次分合闸(1秒左右),主要观察设备是否有异常,如没有,将进行第二次分合闸(10秒左右),检查变压器本体及短网有无异常现象,如没有,进行第三次合闸送电,如无异常,进行空载运行,空载运行根据实际情况定时。
2)电烘炉前需将变压器调至8档电压级。
3)电烘炉电流提什幅值表:1-8小时 10A (2424kwh) 8-16小时 10-20A(4849kwh)16-24小时 20-30A (9700 kwh) 24-32小时 30-40A (16973 kwh)32-40小时 40-50A (21823 kwh)4)本次电烘炉时间大约为40小时左右,用电量为5万KWH左右。
5)电烘炉时为稳定电弧和保持所规定的功率,可根据具体情况给电极周围添加新焦炭,并使焦炭绕电极成馒头体状。
6)电烘炉时应尽量少活动电极,并使三根电极负荷保持均衡,不可单独升高某相电极电流,以免出现漏糊等电极事故。
7)当出现电极负荷给不起时,若需下放电极必须有车间主任指令或其他干部亲自指挥方可停电下放,再送电后,电流要慢慢逐步给起。
33000矿热炉技术方案

33000KVA硅铁炉电力变压器(11)33000KV A矿热炉变压器报价目录1. SF11-85000/132-35-10台数:2台油重:20980KG器身重:45900KG总重:82100KG长×宽×高:6990×5389×6360(增加有载调压开关/每台)2.S11-12500/10-0.4台数:2台总重:5690KG器身吊重:3720KG油重:1680KG长×宽×高:2540×1600×27803.S11-1000/10-0.4台数:1台总重:2680KG器身吊重:1360KG油重:960KG长×宽×高:1770×1040×15404.HKDSPZ-11000/35台数:6台总重:30300KG器身吊重:17500KG油重:7060KG外型尺器重:1380KG备用油重:210KG配件及包装重:230KG长×宽×高:2540×2600×43802.1 设备需求表2.1绕组电阻(,75℃)SF11-85000/132-35电力变压器参数一、型号:SF11-85000/35一次电压:132KV(+2.5%X2 -2.5%X2)二次电压:35KV二、重量油重:20980KG器身重:45900KG总重:82100KG三、外形尺寸长×宽×高:6990×5389×6360 电力变压器技术参数设计依据:设计方案依据国家标准而定使用的环境条件1.1、安装地点:室外1.2、海拔高度:1000 米以内1.3、年平均气温值:-20℃<42℃1.4、相对湿度:<95%变压器主要技术参数:(括弧内是 1000KVA 的参数)3.1型号:S11-2500/10-0.4(S11-1000/10-0.4)3.2额定容量:2500KVA(1000KVA)3.3额定电压:10000/4003.4额定频率:50Hz3.5额定电流:144/3609(58/1443)3.6联结组别:Yyn03.7阻抗电压:4.5%3.8冷却方式:油浸自冷3.11调压方式:手动3.12变压器重量及外型参数:变压器总重:5690KG(2680KG) 器身吊重:3720KG(1360KG) 变压器油重:1680KG(960 KG)外型尺寸:2540(长)×1600(宽)×2780(高) mm(2500KVA) 1770(长)×1040(宽)×1540(高) mm(1000KVA)HKDSPZ-11000/35电炉变压器技术方案及报价1 设计依据本技术方案依据需方11000×3kVA铁合金炉变压器和埋弧炉变压器技术要求要求而确定。
矿热炉设计方案
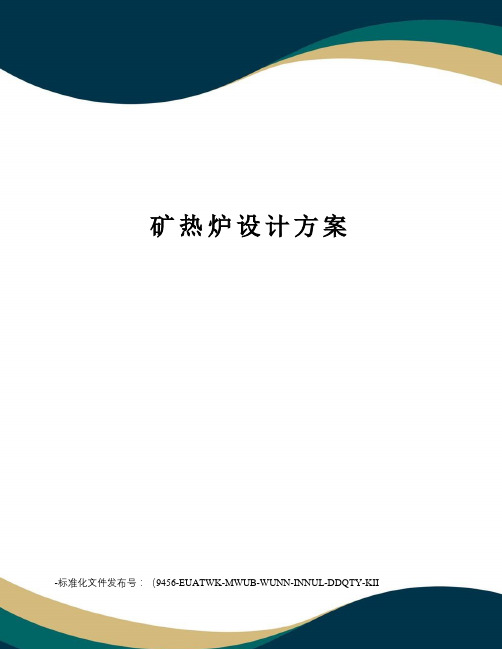
矿热炉设计方案-标准化文件发布号:(9456-EUATWK-MWUB-WUNN-INNUL-DDQTY-KII(1)电耗值随原料成分,制成品成分,电炉容量等的不同而有很大差异。
这里是约值。
二结构特点矿热炉是一种耗电量巨大的工业电炉。
主要由炉壳,烟罩、炉衬、短网,水冷系统,排烟系统,除尘系统,电极壳,电极压放及升降系统,上下料系统,把持器,烧穿器,液压系统,矿热炉变压器及各种电器设备等组成。
矿热炉设备共分三层布置第一层为炉体(包括炉底支撑、炉壳、炉衬),出铁系统(包括包或锅及包车等),烧穿器等组成。
第二层(1)烟罩。
矿热炉目前大多数采用密闭式、或半密闭式矮烟罩结构,具有环保和便于维修,改善操作环境的特点。
采用密闭式结构还可把生产中产生的废气(主要成分是一氧化碳)收集起来综合利用,并可减少电路的热损失,降低电极上部的温度,改善操作条件。
(2)电极把持器。
大多数矿热炉都由三相供电,电极按正三角形或倒三角形,对称位置布置在炉膛中间。
大型矿热炉一般采用无烟煤,焦碳和煤沥青拌合成的电极料,在电炉冶炼过程中自己培烧成的电极。
(3)短网(4)铜瓦(5)电极壳(6)下料系统(7)倒炉机四、矿热炉主要设备1.主要设备:本设计选用矮烟罩半封闭固定式矿热炉,主要设备选择如下:炉体炉体是由炉壳、炉衬、炉底支撐等构成,炉壳采用14~18mm厚钢板焊接而成的圆筒体,外部焊接有加强筋,以保证炉体具有足够的强度。
炉底采用18~20㎜厚钢板,炉体采用25~30#工字钢支撑,自然通风冷却炉底,炉壳设有1~2个出料口,炉衬采用高铝耐火砖和自焙碳砖无缝砌筑新工艺,炉墙厚度为460~690㎜,外敷20㎜厚硅酸铝纤维板。
炉底碳砖厚度为800~1200㎜。
炉口采用碳化硅刚玉砖,流料槽采用水冷结构。
根据需要也可增加水冷炉门。
矮烟罩采用全水冷结构或水冷骨架和耐热混凝土的复合结构。
其高度以满足设备维修的需要,全水冷结构采用水冷骨架、水冷盖板和水冷壁及水冷围板。
9000kva矿热炉工业硅冶炼启炉方案说明
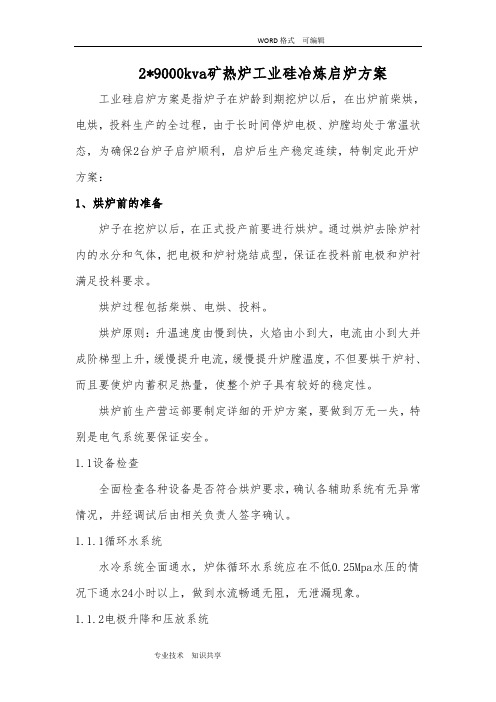
2*9000kva矿热炉工业硅冶炼启炉方案工业硅启炉方案是指炉子在炉龄到期挖炉以后,在出炉前柴烘,电烘,投料生产的全过程,由于长时间停炉电极、炉膛均处于常温状态,为确保2台炉子启炉顺利,启炉后生产稳定连续,特制定此开炉方案:1、烘炉前的准备炉子在挖炉以后,在正式投产前要进行烘炉。
通过烘炉去除炉衬内的水分和气体,把电极和炉衬烧结成型,保证在投料前电极和炉衬满足投料要求。
烘炉过程包括柴烘、电烘、投料。
烘炉原则:升温速度由慢到快,火焰由小到大,电流由小到大并成阶梯型上升,缓慢提升电流,缓慢提升炉膛温度,不但要烘干炉衬、而且要使炉内蓄积足热量,使整个炉子具有较好的稳定性。
烘炉前生产营运部要制定详细的开炉方案,要做到万无一失,特别是电气系统要保证安全。
1.1设备检查全面检查各种设备是否符合烘炉要求,确认各辅助系统有无异常情况,并经调试后由相关负责人签字确认。
1.1.1循环水系统水冷系统全面通水,炉体循环水系统应在不低0.25Mpa水压的情况下通水24小时以上,做到水流畅通无阻,无泄漏现象。
1.1.2电极升降和压放系统电极升降正常、压放装置完好、灵活,液压系统无泄漏现象。
1.1.3配料系统皮带无跑偏,滚筒转动正常,皮带减速箱运行是否正常,振动给料机转动正常、弹簧钓钩松紧、长度合适,仪表、指示灯正常,配、加料装置运行可靠,灵活,完全满足冶炼要求。
1.1.4变压器及补偿系统变压器、补偿及输电系统完好,变压器保护系统测试(过流、轻、重瓦斯报警等)正常,炉变各种测试及高低压电路控制系统运行正常完全满足送电要求。
1.1.5炉体绝缘系统密封、绝缘完好,三相电极、短网、炉体各绝缘点测试正常。
1.1.6环保系统环保变频器、主风机、冷却器、旋风和布袋除尘器、环保系统、炉体绝缘、变压器系统等无问题,环保系统联动一次,确保各系统运行正常。
1.1.7辅助设备料场洗矿设备、油焦磁选设备试运行。
车间主行车、精整行车行车的升降是否正常,大车正常行驶,限位正常,抱闸是否正常,电铃是否正常。
矿热炉设计方案教学提纲

(1)电耗值随原料成分,制成品成分,电炉容量等的不同而有很大差异。
这里是约值。
二结构特点矿热炉是一种耗电量巨大的工业电炉。
主要由炉壳,烟罩、炉衬、短网,水冷系统,排烟系统,除尘系统,电极壳,电极压放及升降系统,上下料系统,把持器,烧穿器,液压系统,矿热炉变压器及各种电器设备等组成。
矿热炉设备共分三层布置第一层为炉体(包括炉底支撑、炉壳、炉衬),出铁系统(包括包或锅及包车等),烧穿器等组成。
第二层(1)烟罩。
矿热炉目前大多数采用密闭式、或半密闭式矮烟罩结构,具有环保和便于维修,改善操作环境的特点。
采用密闭式结构还可把生产中产生的废气(主要成分是一氧化碳)收集起来综合利用,并可减少电路的热损失,降低电极上部的温度,改善操作条件。
(2)电极把持器。
大多数矿热炉都由三相供电,电极按正三角形或倒三角形,对称位置布置在炉膛中间。
大型矿热炉一般采用无烟煤,四、矿热炉主要设备1.主要设备:本设计选用矮烟罩半封闭固定式矿热炉,主要设备选择如下:1.1炉体炉体是由炉壳、炉衬、炉底支撐等构成,炉壳采用14~18mm厚钢板焊接而成的圆筒体,外部焊接有加强筋,以保证炉体具有足够的强度。
炉底采用18~20㎜厚钢板,炉体采用25~30#工字钢支撑,自然通风冷却炉底,炉壳设有1~2个出料口,炉衬采用高铝耐火砖和自焙碳砖无缝砌筑新工艺,炉墙厚度为460~690㎜,外敷20㎜厚硅酸铝纤维板。
炉底碳砖厚度为800~1200㎜。
炉口采用碳化硅刚玉砖,流料槽采用水冷结构。
根据需要也可增加水冷炉门。
1.2矮烟罩采用全水冷结构或水冷骨架和耐热混凝土的复合结构。
其高度以满足设备维修的需要,全水冷结构采用水冷骨架、水冷盖板和水冷壁及水冷围板。
水冷骨架采用16~20#槽钢制成,三相电极周围内盖板采用无磁不锈钢板制成,外盖板及围板采用Q-235钢板制作,并设有极心圆调整装置和三相电极水冷保护套和绝缘密封装置。
水冷骨架和耐热混凝土复合结构采用烟罩侧壁由金属构件立柱支撑并通水冷却,四周用耐火砖砌筑而成,侧壁上设有三个操作门,在炉内大面上,开启方向是横向旋转式,上部有二个排烟口,与其相联的是二个立冷弯管烟道,直通烟囱或除尘装置。
半密闭式12500KVA工业硅矿热炉的设计

一、半密闭式12500KVA工业硅矿热炉的设计正确设计矿热炉的结构是保障矿热炉工作性能的先决条件,是设计工作者面临的最大困难。
好的矿热炉结构设计不仅有利于炉子保障高产、优质、低能耗、少故障的生产,而且有利于节约建设成本、方便其它设备布置、保证操作顺畅。
高效、节能、先进工业硅冶炼技术工艺,是衡量一个企业是否具有先进性,是否具备市场竞争力,是否能不断领先于竞争者的重要指标依据。
我国工业硅生产能源消耗高,主要是因为设计上不合理、控制水平与管理水平不高。
设计上不合理体现在我国普遍使用的是6300KVA左右的小炉型(散热大、产量低)、炉型设计上为隔热措施不严密、电路设计不合理、极心圆尺寸大小不合理等许多细节方面。
控制水平不高体现在人工操作范围大、炉况稳定性差、造成因调整炉况波动费时较长而使得非生产性能耗损失大。
管理水平不高体现在管理上不严、制度不健全、操作细节缺乏,造成物资或能源上的消耗浪费。
一)、工业硅矿热电炉特点:炉型大型化则单位热容率增大,能量供应集中,通过外围表面单位面积散热小、炉子热稳定增强,有利于降低热损失,提高冶炼效率。
冶炼工业硅采用先进技术和设备,炉变选用低阻抗电压的恒功率电炉变压器,功率因素高,超负荷能力强;短网采用通水式铜管,电极三角全补偿式外短网,短网软缆采用水冷电缆,阻抗损失小;科学选用石墨电极;有利于高产降耗,电炉炉型采用矮烟罩半密闭式,有利于收尘,工人操作环境好;电极把持器的铜瓦采用液压波纹管压紧式;电极升降采用液压,捣炉机选用半液压式大功率捣炉机。
二)、矿热电炉结构选型技术参数:在工业硅冶炼过程中矿热炉的状态与电气参数的变化密切相关,控制最佳的供电制度对保证取得好的经济技术指标十分重要。
12500KVA工业硅矿热电炉冶炼(工业硅)的日产22—25吨。
电耗11800-12800kw/吨。
1、变压器容量:12500KVA壳式强油水冷矿热炉变压器;2、一次侧电压:35KV3、二次侧电压:140~175(V)4、二次侧电压级数:17级,级差:3V5、常用电压:151(V)6、二次电流:49154(A)7、电极直径:Φ780mm(石墨)8、电极极心圆直径:Φ2350mm±100mm9、炉膛直径:Φ5700(mm)10、炉壳直径:Φ7200mm11、炉膛深度:2200mm12、炉壳高度:4300mm13、矮烟罩高度:2400mm14、电极行程:1600mm15、电极升降速度:0.5m/min16、冷却水用量:340t/h三)、电炉结构选型设计依据12500KVA交流还原电炉机械设备包括炉体、电极系统、烟罩、变压器和输电短网、液压系统和水冷系统等。
(冶金行业)半封闭式工业硅矿热炉主要技术方案

(冶金行业)半封闭式工业硅矿热炉主要技术方案(冶金行业)半封闭式工业硅矿热炉主要技术方案宜兴市中宇电冶设备有限X公司33000KVA半封闭式工业硅矿热炉技术方案1电炉设备1.133000KVA半封闭式工业硅矿热炉主要技术参数1.2电炉设备设计1.2.1矿热炉设备设计要求矿热电炉采用半封闭型式,采用铜瓦压力环式电极把持器,电炉炉底通风冷却,炉体采用旋转炉体,炉体测温,变压器长期具备20%的长期超负荷能力。
短网系统、铜瓦、进线电缆都长期具备20%之上的超负荷能力。
烟道和炉盖之间设置了可靠绝缘。
液压系统采用组合阀,且设置储能器。
电极升降油缸上、下俩端均设绝缘加以保护。
高压油管俩端全部带绝缘。
为防止电极偏斜,设计时在炉盖、平台及电极导向装置,电极导向装置设绝缘。
所有管道均设管道沟,便于检修。
闸阀采用不锈钢丝杆,以增加其使用寿命。
每组分水器设3路备用水路,分水器阀门采用不锈钢或铜球阀,分水器给、回水路布局合理。
炉盖采用框架式水冷结构,中心区采用不导磁材料制作。
电炉烟道在二、三楼之间设水冷段,以降低烟气温度。
1.2.2工艺设计要求电炉厂房柱子跨距按6m、7.5m布置。
电炉车间分设四个跨区,分别是变压器跨(偏跨)7.5m、电炉跨18m、浇注跨24m、成品跨18m。
电炉跨初定为五层平台分别为:a)+0.0m出渣铁轨道平台包括铁道、出铁车和铁包、出渣车和渣包等。
其中+2.4m平台为局部出铁操作平台:该平台正对出铁口,包括烧穿器、出铁挡板等出炉工具等。
b)+7.0m电炉炉口操作平台电炉控制室计算机室布置在此平台上,冷却水系统的分水器和回水槽布置在该平台上、炉口操作工具等。
C)+11.8变压器放置平台电炉设有三台单相变压器,放置在此平台上成三角形布置,为方便变压器安装、检修、更换设有变压器吊装孔。
d)+18.3m电极升降机构平台平台空间内安装有电极升降、压放装置及电炉料管插板阀。
液压站也布置在此平台上。
e)+24.8m电炉电极支承及接长电极壳、加入电极糊及加料平台炉顶料仓座在此平台上。
硅铁矿热炉余热发电系统设计方案
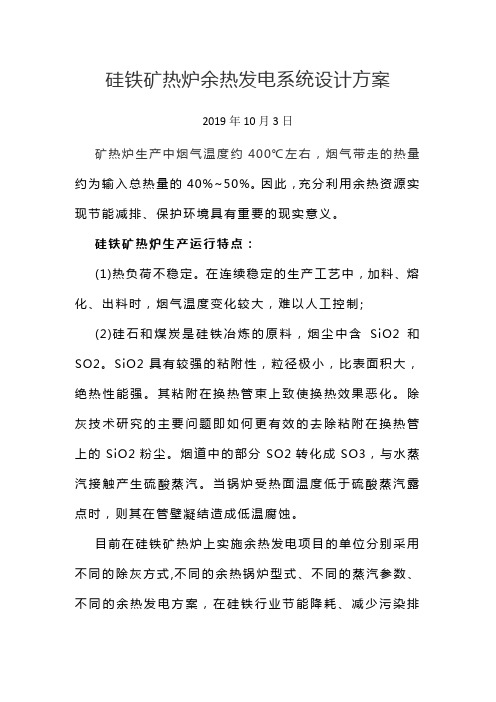
硅铁矿热炉余热发电系统设计方案2019年10月3日矿热炉生产中烟气温度约400℃左右,烟气带走的热量约为输入总热量的40%~50%。
因此,充分利用余热资源实现节能减排、保护环境具有重要的现实意义。
硅铁矿热炉生产运行特点:(1)热负荷不稳定。
在连续稳定的生产工艺中,加料、熔化、出料时,烟气温度变化较大,难以人工控制;(2)硅石和煤炭是硅铁冶炼的原料,烟尘中含SiO2和SO2。
SiO2具有较强的粘附性,粒径极小,比表面积大,绝热性能强。
其粘附在换热管束上致使换热效果恶化。
除灰技术研究的主要问题即如何更有效的去除粘附在换热管上的SiO2粉尘。
烟道中的部分SO2转化成SO3,与水蒸汽接触产生硫酸蒸汽。
当锅炉受热面温度低于硫酸蒸汽露点时,则其在管壁凝结造成低温腐蚀。
目前在硅铁矿热炉上实施余热发电项目的单位分别采用不同的除灰方式,不同的余热锅炉型式、不同的蒸汽参数、不同的余热发电方案,在硅铁行业节能降耗、减少污染排放方面取得初步成效。
但都不同程度地存在某些问题。
发展、完善低温低压余热锅炉的研究与设计方案亟待解决的关键问题:首先研制高效吹灰技术,取代结构复杂、笨重、多发故障的机械除灰方式;其次是采用强化换热技术,取代目前体积庞大、耗用钢材较多的光管结构余热锅炉;第三,选择适当的蒸汽参数,选择最佳的系统配置。
余热资源某冶炼公司现有4台25.5MVA硅铁矿热炉,实测每台硅铁矿热炉产生的烟气温度约350〜550℃左右,流量102000Nm3/h(正常工况),出料时流量97500Nm3/h。
运行工况具有一定波动性,依据测量参数,结合行业经验数据,取设计方案烟气参数,烟尘成分及粒度。
硅微粉呈灰白色,质轻粒细,容重约为200kg/m3,安息角约为48度,吸湿差。
硅铁烟尘的主要成分以SiO2为主,占90%以上;比电阻高,在225℃时,比电阻不低于1.0x10的11次方W.cm。
高电绝缘性:比电阻通常在10的11次方~10的13次Ω.cm,具有极强隔热性,热传导率≤0.05W/mK(由于多孔性),粉尘以小粒径为主,小于5微米的硅微粉占93%以上。
矿热炉设计方案.doc

矿热炉简介一原理用途矿热炉它主要用于还原冶炼矿石,碳质还原剂及溶剂等原料。
主要生产硅铁,锰铁,铬铁、钨铁、硅锰合金等铁合金,是冶金工业中重要工业原料及电石等化工原料。
其工作特点是采用碳质或镁质耐火材料作炉衬,使用自培电极。
电极插入炉料进行埋弧操作,利用电弧的能量及电流通过炉料的,因炉料的电阻而产生能量来熔炼金属,陆续加料,间歇式出铁渣,连续作业的一种工业电炉。
矿热炉主要类别、用途反映温度电耗类别主要原料制成品0℃KW*h/t(45%)硅2100-5500 铁硅铁炉硅铁、废铁、焦碳硅铁1550-1770(75%)硅铁8000-11000铁合锰铁炉锰矿石、废铁、焦碳、石锰铁1500-1400 2400-4000 灰金炉铬铁炉铬矿石、硅石、焦碳铬铁1600-1750 3200-6000 钨铁炉钨晶矿石、焦碳钨铁2400-2900 3000-5000硅铬炉铬铁、硅石、焦碳硅铬合金 1600-1750 3500-6500硅锰炉锰矿石、硅石、废铁、焦硅锰合金 1350-1400 3500-4000碳炼钢电炉铁矿石、焦碳生铁1500-1600 1800-2500 电石炉石灰石、焦碳电石1900-2000 2900-3200 碳化硼炉氧化硼、焦碳碳化硼1800-2500 约 20000 (1)电耗值随原料成分,制成品成分,电炉容量等的不同而有很大差异。
这里是约值。
二结构特点矿热炉是一种耗电量巨大的工业电炉。
主要由炉壳,烟罩、炉衬、短网,水冷系统,排烟系统,除尘系统,电极壳,电极压放及升降系统,上下料系统,把持器,烧穿器,液压系统,矿热炉变压器及各种电器设备等组成。
矿热炉设备共分三层布置第一层为炉体(包括炉底支撑、炉壳、炉衬),出铁系统(包括包或锅及包车等),烧穿器等组成。
第二层(1)烟罩。
矿热炉目前大多数采用密闭式、或半密闭式矮烟罩结构,具有环保和便于维修,改善操作环境的特点。
采用密闭式结构还可把生产中产生的废气(主要成分是一氧化碳)收集起来综合利用,并可减少电路的热损失,降低电极上部的温度,改善操作条件。
2×36000KVA矿热炉设计工艺说明

2×36000KV A矿热炉设计工艺说明一、平均每昼夜吃矿量计算:按每吨矿耗电(热料温度为50度计)每吨矿耗电50度计算、作业率按95%计算、功率因数为0. 5计;(随着操作技术的熟练和设备的完善作业率可提高到98%以上)2×300×0.905/450×24=35.6吨,平均每小时每台炉子吃料(焙砂)量为72吨计。
二、电极直径和二次电压的选择常用二次电压为40V-470V,要求电流密度大于2.8-3.0,便于电极的烧结。
根据电流密度电极直径可选用1.35米。
极心圆功率可考虑2000-2500左右可满足冶炼工艺要求。
根据不同炉料的比电阻,设计时可考虑电极极心圆可调,范围在每项电极150mm左右。
极心圆中位取4.6米,可调范围在4.55米到5米之间。
实际安装时可考虑极心圆在4.7米。
三、炉壳高度和炉壳直径炉壳高度取6米到6.5米即可满足冶炼工艺的要求,为了便于假炉墙的形成,炉膛功率取200-250左右即可,炉壳直径选用17.5 米左右为宜。
四、出铁、渣工艺渣、铁口各为2个,其中南面两个铁口,北面两个渣口,渣口和铁口之间夹角为45度,铁口比渣口低30cm。
炉渣经开眼机打开后直接入水碎池水碎,铁口打开后经中间包后直接浇铸成产品。
每昼夜出渣12炉次,每出完2炉渣后马上出铁,这样可保持在出铁过程中尽可能少的带入炉渣,减少块渣的产生和降低工人的劳动强度,减少中间包的周转量。
如按每昼夜出6炉计:每次出铁35-40吨,每天产量为210-240吨/台。
五、水碎炉渣的水碎采用炉前直接水碎,每台炉子每次(2小时左右)处理炉渣的量为120吨左右,处理过程为15-25分钟。
水碎炉渣的水泵可考虑较高的水压,确保水碎的安全性。
(选用水泵时要考虑水温的因素)六、原料1.氧化镍矿。
本工艺均采用印度尼西亚OBI岛的氧化镍矿为原料,其主要成分为:H2O 35%左右,Ni ≥1.8% SiO230-40% CaO1-5% MgO16-35% Fe 10-22% Ai2O3 ≤3.5% P≤0.010% 。
矿热炉热平衡实施方案

矿热炉热平衡实施方案
矿热炉是矿山生产中常用的一种设备,它在矿石熔炼过程中起着至关重要的作用。
然而,矿热炉的热平衡问题一直是困扰着矿山工程师和技术人员的一个难题。
为了解决这一问题,我们需要制定一套科学的热平衡实施方案。
首先,我们需要对矿热炉的热量输入和输出进行详细的分析。
矿热炉的热量输入主要来自于燃料的燃烧和矿石的加热,而热量输出则主要体现在矿石的熔化和熔渣的排出。
通过对热量输入和输出的分析,我们可以清晰地了解矿热炉的热平衡状况。
其次,我们需要对矿热炉的热能损失进行全面的调查。
矿热炉在工作过程中,由于各种原因会产生一定的热能损失,这些损失会直接影响矿热炉的热平衡。
因此,我们需要对矿热炉的绝热层、烟气排放和热能回收等方面进行细致的检查,找出热能损失的具体原因。
最后,我们需要根据以上的分析结果,制定一套科学的热平衡实施方案。
这个方案需要包括矿热炉的热量平衡调节、热能损失的控制和热能回收利用等方面的具体措施。
通过实施这个方案,我们可以有效地提高矿热炉的热效率,减少能源消耗,降低生产成本,实现可持续发展。
总之,矿热炉的热平衡实施方案是一个复杂而又重要的课题,需要我们综合运用热力学、热工学和材料学等多个学科的知识,制定出科学合理的方案。
只有这样,我们才能更好地发挥矿热炉的作用,为矿山生产的可持续发展做出贡献。
电石矿热炉产能及产量提升设计方案与电极入炉插入深度控制措施及方法

电石矿热炉产能提升设计方案与电极入炉深度控制措施及方法一、电石矿热炉产能提升:XXX电石厂有12台电石炉,每台电石炉用三台单相变压器供电,单台变压器容量为9000KVA,共9000×3=27000KVA;总负荷为27000KVA×12=324000KVA。
电石炉用电由220KV两台主变供电,每台变压器接带6台电石炉负荷,每台主变压器额定38.5KV电压时负荷为180000KVA,两台变压器38.5KV电压时总负荷为360000KVA,35KV电压时为163800×2=327600KVA, 12台电石炉额定总需求负荷为27000KVA×12=324000KVA。
按照表1设计要求电石炉变压器制造时可超额定负荷20%长期运行,但是实际运行时,电石炉总负荷324000KVA超20%为388800KVA,已经超过变压器的额定负荷,显然主变压器设计时未考虑电石炉变压器设计负荷要求,在原设计中,电石炉总负荷限制在额定负荷324000KVA以下。
表1、主变分支回路的实际参数和目前的运行参数单台变压器额定负荷9000KVA(超额定负荷20%能长期运行),一次电流257A(相电流),角接运行时额定线电流为257×1.732=445A,三台电石炉满负荷电流为445×3=1335A,从上表中可以看出,分支电流报警值为1300A,额定电流为1350A。
三台电石炉满负荷运行时电流1335A大于供电分支设定报警值1300A,小于设计电流值1350A。
受供电设备额定负荷的影响,实际运行中,每台电石炉只能运行在27000KVA以下,考虑到电石炉操作电流引起的三相不平衡,电石炉负荷实际达不到额定的27000KVA。
主变的限制,已成为电石炉负荷提升的一个制约点;另外一点,电石炉变压器运行时功率因数0.95,档位达到3档甚至2档运行,变压器在负荷不超27000KVA,有功功率最高可提高到25650KW,这时,变压器已基本达到上限,这是制约电石炉负荷提升的另一个原因,两方面制约了电石炉负荷的进一步提升。
密闭矿热炉技术方案

密闭矿热炉技术方案生石灰和含碳原料(焦炭、无烟煤或石油焦)在矿热炉内,依靠电弧高温熔化反应而生成电石。
主要生产过程是:原料加工;配料;通过电炉上端的入口或管道将混合料加入电炉内,密闭的电炉中加热至2000℃左右,依下式反应生成电石:GaO+3C→CaC2+CO熔化了的碳化钙从炉底取出后,经冷却、破碎后作为成品包装。
反应中生成的一氧化碳则全部被抽出。
一、工艺流程简介1.生石灰工艺石灰石经加热达900O C便会发生分解,放出CO2,生成石灰。
CaCO3——→ CaO + CO2 – 422 kcal/kg生产冶金活性石灰时,分解温度控制为1050O C~1100O C,煅烧效果恰到好处才能获得最佳的优质软烧(轻烧)石灰。
A石灰石煅烧流程料场石灰石经振动筛筛去≥80mm的大石块和≤40mm的小石料入窑后,自上而下缓慢下移,连续经过预热带、煅烧带、后置煅烧带和冷却带,最后被煅烧成石灰。
B石灰流程成品石灰经窑底部四个小料仓,按预定的间隔时间由四个电磁振动给料机将石灰排入对应石灰称中至给定重量,然后进入窑下部的储灰仓中,保证窑内物料的均匀下落防止发生偏窑。
储灰仓内石灰至一定量时,再由振动给料机排出,经过平皮带和大倾角皮带运输机送入振动筛。
块度≥5mm石灰放至可逆皮带输送至各成品仓,≤5mm石灰粉直接放入粉灰仓。
2、电石工序全密闭电石生产工艺流程电石生产将分为原料贮运、炭材干燥、电石生产、固态电石冷却、破碎、储存及电极壳制造几个工序。
(1)原料贮运电石生产主要原料焦炭、石灰、电极糊控制生石灰过烧率小于2%,石灰氧化镁含量小于1%,石灰粒度5-40毫米,焦碳含水小于2%,操作电流小于75-80KA,焦炭干燥时由装载机送到受料斗中,经带式输送机及斗式提升机送到破碎筛分楼筛分5-25mm通过带式输送机送至炭材干燥中间料仓。
0-5mm用小车送至电厂、空心电极或炭材干燥焦粉仓供热风炉使用;石灰需要时经带式输送机送至石灰破碎筛分楼进行破碎筛分。
矿热炉技改方案

矿热炉技改方案矿热炉概述矿热炉是用来加热矿石以获得金属的一种热处理设备。
其工作原理是通过将燃料燃烧产生的高温气体引入炉内,并通过炉内矿石的热传导来将矿石加热到所需温度,以达到熔化金属或者烧毁有害元素的效果。
然而,传统的矿热炉在能源利用和环境保护方面都存在不足。
主要问题包括:1.能源利用率低下,能耗高。
由于矿热炉传统采用的都是化石燃料,能源利用效率很低,仅有30%-40%左右的能量转化为有效热量,大部分都被浪费掉了。
2.空气污染,有害气体排放量较大。
矿热炉的燃烧过程中会产生大量的有害气体,例如二氧化碳、氧化亚氮等等,这些气体的排放会直接影响环境质量,危害人民的身体健康。
3.炉膛寿命短,维护成本高。
由于矿热炉长期使用,炉膛内的高温和有害气体腐蚀作用下容易出现开裂、变形、掉渣等状况,导致炉膛使用寿命大大降低,同时需要大量投入资金来进行保养和修复。
面对这些问题,我们需要采取相应的技术措施来进行矿热炉的技改。
技改方案采用新能源燃料针对矿热炉能源利用问题,我们可以采用新能源燃料来替代传统的化石燃料,提高能源利用效率,降低能耗成本,同时减少污染。
目前,利用生物质能源(如锯末、秸秆、木屑等)作为替代燃料已经成为矿热炉技改的一条有效途径。
与传统燃料相比,生物质燃料的热值高,温度均匀,易于控制,同时其燃烧产生的二氧化碳等有害气体的排放量也远远低于传统燃料。
加强热交换技术为了提高矿热炉能量利用率,我们需要将炉内的高温气体充分与矿石进行热交换。
为此,我们可以设计一套高效的热交换系统,将炉内产生的高温气体直接引入热交换设备与矿石进行热交换,使矿石能够在较短时间内达到所需温度,提高加热效率。
同时,热交换设备还可以将炉内气体冷却到较低的温度,使其中的有害气体经过处理后得以减少排放,从而达到环保效果。
采用新型炉膛材料为了提高矿热炉的使用寿命,我们可以采用新型炉膛材料来替代传统炉膛材料。
目前,全陶瓷炉膛已经成为了替代材料的主流,由于其不会被有害气体侵蚀,所以可以显著提高炉膛的使用寿命。
- 1、下载文档前请自行甄别文档内容的完整性,平台不提供额外的编辑、内容补充、找答案等附加服务。
- 2、"仅部分预览"的文档,不可在线预览部分如存在完整性等问题,可反馈申请退款(可完整预览的文档不适用该条件!)。
- 3、如文档侵犯您的权益,请联系客服反馈,我们会尽快为您处理(人工客服工作时间:9:00-18:30)。
矿热炉简介
一原理用途
矿热炉它主要用于还原冶炼矿石,碳质还原剂及溶剂等原料。
主要生产硅铁,锰铁,铬铁、钨铁、硅锰合金等铁合金,是冶金工业中重要工业原料及电石等化工原料。
其工作特点是采用碳质或镁质耐火材料作炉衬,使用自培电极。
电极插入炉料进行埋弧操作,利用电弧的能量及电流通过炉料的,因炉料的电阻而产生能量来熔炼金属,陆续加料,间歇式出铁渣,连续作业的一种工业电炉。
矿热炉主要类别、用途
(1)电耗值随原料成分,制成品成分,电炉容量等的不同而有很大
差异。
这里是约值。
二结构特点
矿热炉是一种耗电量巨大的工业电炉。
主要由炉壳,烟罩、
炉衬、短网,水冷系统,排烟系统,除尘系统,电极壳,电极压放及升降系统,上下料系统,把持器,烧穿器,液压系统,矿热炉变压器及各种电器设备等组成。
矿热炉设备共分三层布置
第一层为炉体(包括炉底支撑、炉壳、炉衬),出铁系统(包括包或
锅及包车等),烧穿器等组成。
第二层
(1)烟罩。
矿热炉目前大多数采用密闭式、或半密闭式矮烟罩结构,具有环保和便于维修,改善操作环境的特点。
采用密闭式结构还可把生产中产生的废气(主要成分是一氧化碳)收集起来综合利用,并可减少电路的热损失,降低电极上部的温度,改善操作条件。
(2)电极把持器。
大多数矿热炉都由三相供电,电极按正三角形或倒三角形,对称位置布置在炉膛中间。
大型矿热炉一般采用无烟煤,
焦碳和煤沥青拌合成的电极料,在电炉冶炼过程中自己培烧成的电
极。
(3)短网
(4)铜瓦
(5)电极壳
(6)下料系统
(7)倒炉机
(8)排烟系统
(9)水冷系统
(10)矿热炉变压器
(11)操作系统
第三层
(1)液压系统
(2)电极压放装置
(3)电极升降系统
(4)钢平台
(5)料斗及环行布料车
其他附属;斜桥上料系统,电子配料系统等
三、矿热炉主要配置方案
6300KVA 9000KVA 12500KVA 16500KVA 25000KVA
矮烟罩半密
炉型矮烟罩半密闭矮烟罩半密闭矮烟罩半密闭密闭炉
四、矿热炉主要设备
1.主要设备:本设计选用矮烟罩半封闭固定式矿热炉,主要设备
选择如下:
炉体
炉体是由炉壳、炉衬、炉底支撐等构成,炉壳采用14~18mn厚钢板焊接而成的圆筒体,外部焊接有加强筋,以保证炉体具有足够的强度。
炉底采用18〜20伽厚钢板,炉体采用25〜30#工字钢支撑,自然通风冷却炉底,炉壳设有1〜2个出料口,炉衬采用高铝耐火砖和自焙碳砖无缝砌筑新工艺,炉墙厚度为460〜690伽,外敷20 mm厚硅酸铝纤维板。
炉底碳砖厚度为800〜1200mm。
炉口采用碳化硅刚玉砖,流料槽采用水冷结构。
根据需要也可增加水冷炉门。
矮烟罩
采用全水冷结构或水冷骨架和耐热混凝土的复合结构。
其高度以
满足设备维修的需要,全水冷结构采用水冷骨架、水冷盖板和水冷壁及水冷围板。
水冷骨架采用16〜20#槽钢制成,三相电极周围内盖板采用无磁不锈钢板
制成,外盖板及围板采用Q-235钢板制作,并设有极心圆调整装置和三相电极水冷保护套和绝缘密封装置。
水冷骨架和耐热混凝土复合结构采用烟罩侧壁由金属构件立柱支撑并通水冷却,四周用耐火砖砌筑而成,侧壁上设有三个操作门,在炉内大面上,开启方向是横向旋转式,上部有二个排烟口,与其相联的是二个立冷弯管烟道,直通烟囱或除尘装置。
短网
短网包括变压器端的水冷补偿器、水冷铜管、水冷电缆、导电铜管、铜瓦及其吊挂、固定联接等装置。
其布置型式可分为正三角或倒三角。
不论那种布置,均要求在满足操作空间的前提下,尽可能地缩短短网的距离降低短网阻抗,以保正获得最大的有功功率。
水冷铜管、导电铜管均采用厚壁铜管,各相均采用同向逆并联,使短网往返电流双线制布置,互感补偿磁感抵消。
中间铜管用水冷电缆相连,冷却水直接从水冷铜管经水冷电缆、导电铜管流入铜瓦,冷却铜瓦后经返回的导电铜管、水冷电缆、水冷铜管流出炉外。
运行温度低,减少短网导电时产生的热量损失,能有效提高短网的有功功率,同时铜管重量轻,易加工安装,大大减少短网的投资。
电极系统:
电极系统由把持器筒体、铜瓦吊挂、压力环、水冷大套、电极升降装置、电极压放装置等。
在电极系统上我们采用了国际先进的德马克,南非PYROMET 技术,如采用悬挂油缸式的电极升降装置,能灵活、可靠、准确地调节电极的上、下位置。
上下抱闸和压放油缸组成电极带电自动压放装置。
电极系统共三套,每套包括电极筒1个、把持筒1个、保护套1
个、压力环1个、铜瓦6〜8块。
把持器的作用把持住自焙电极,保护大套、压力环、铜瓦依顺序都吊挂固定在其上面,每根电极上设6〜8块铜瓦,是通过压力环上的油缸和顶紧装置,形成一对一顶紧铜瓦,压力均匀,可保证铜瓦对电极的抱紧力均衡,铜瓦与电极的接触导电良好。
把持器上部由台架与二个升降油缸联接,油缸的支座是固定在三层平台的钢平台上,在钢平台上一定的范围内根据需要可调整极心圆。
每根电极上设有单独电极自动压放装置,由气囊抱闸(或液压抱闸)抱紧电极,充气气囊抱紧电极,放气气囊松开电极;上、下气囊抱闸由导向柱和压放油缸相联接,下气囊抱闸与把持筒相联接,冶炼时下气囊始终抱紧电极,只在压放时才与上气囊配合交替松开夹紧电极,完成压放动作。
冷却水系统
冷却水冷系统是对处于高温条件下工作的构件(包括短网、压力环、保护大套、炉壳、烟罩、烟囱)进行冷却的装置,它由分水器、集水箱、压力表、阀门、管道及胶管、接头等组成。
短网(包括水冷铜管、水冷电缆、铜瓦)压力环的水路专门设有放水装置用于检修、抢修时可快速排水。
水冷短网及压力环、保护套的冷却水要求:软水,进水温
度w 30C,出水温度w 50C。
2.主要电气设备
矿热炉变压器
采用低损耗节能型壳式矿热变压器,有载电动调压,强循环,油
水冷却器,阻抗电压4~6% —次侧电压可为35〜110KV二次侧电压分为5~27级
(不同容量变压器和不同冶炼品种采用不同的二次电压级),前几档为恒功率,后几档为恒电流,并要求超负载能力〉25% 采用侧出线管式联接方式。
高压供电系统
高压供电系统由35KV(或110KV馈电经变压器隔离开关,真空
断器送至电炉变压器,同时可以根据用户要求设计谐波吸收装置和一
次补偿。
压供电系统
设动力变压器,动力电源送至主室动力柜,送至水泵、变压器、
调压装置、控电电源、PLC电源、液压站及空压机室,低压可以增加二次补偿。
3.主要辅助设备
可根据用户需要自备或用我公司设计、制造的设备或图纸。
上料、加料系统设备
上料设备可选用皮带上料,单斗提升机上料,斗式提升机、料斗、料罐和单梁电动葫芦上料。
加料设备可选用布料小车。
钢料仓T下料管T电磁振动给料机T自动插板阀T下料管出炉设备:铁水包、铁水包龙门吊钩、运包车、地卷扬机浇铸设备:锭模
捣炉机、加料机、烧穿器。
除尘设备
高压补偿,二次低压补偿。
(选择使用)
五、矿热炉硅锰合金冶炼生产工艺流程
六、安全操作规程1、作业前,必须按规定穿戴好劳动防护用品,检查所用工具,设备是否完好,各种安全防护保险装置,必须齐全有效。
2、操作的各种开关、阀门、信号等装置必须设有醒目的安全标示,严防操作失误。
3、电炉在投入或者停止生产前,必须与生产调度及相关单位(岗位)取得联系。
停、送电时,必须先将电极提升至上限。
送电时先合高压隔离开关,后合油开关及操作开关,停电时反之、严禁带负荷拉合隔离开关。
4、冶炼过程中不准停止可控硅控制系统运行和切换电压。
5、推捣炉膛料面前,必须先活动电极消除悬挂,在进行推捣料操作。
操作时不得敞开炉门,严防塌料喷火伤害。
6、经常进行设备运行检查,发现问题及时处理和报告,做好设备运行记录。
7、设备运行时,不得维护、调试、清扫设备带电、旋转、高压等危险部位,进行机械电气设备维护检修时,必须停机拉闸挂检修安全警示牌。
8、操作本岗位配套设备时(如空气压缩机、电动葫芦)等,必须严格遵守其安全操作规程,采用电动葫芦吊运台下物料时,必须上下有人监护。
上料时料斗装料不得过满和从人体上方吊运。
9、用氧气烧铁口时,要有专人指挥,胶管与铁管连要牢固,操作时不得将手
抓在接头处,严防氧气回火和渣铁喷溅烫伤。
严格遵守氧气
瓶使用管理规定10、填充铁水包沙眼的沙子必须精选,不得带有石子和杂质,铁水沟、铁水包、铁模及出铁场地,必须保持干燥。
接触铁水的工具必须烘干烤热,严防铁水爆炸事故。
11、配合行车工吊装渣铁时,要站在吊物摆动不被挤压的安全位置挂钩,手不能抓在钩链活动部位和将脚伸入被吊物下指挥起吊,严防吊物伤害。
12、不准在炉基周围取暖休息和烘烤衣物。
13、严格执行定置管理规定,保持作业场所清洁,道路畅通。