(数控模具设计)第章挤出模具设计C精编
挤出模具设计
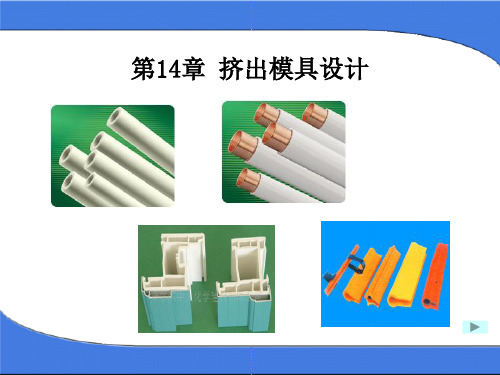
(5)过滤网和过滤板
ⅰ过滤杂质 ⅱ将熔体的螺旋运动 直线运动
(6)加热器 (7)璧厚均匀调节装置 (8)定型模
异型材定型模的型腔截面 1.上型板 2.镶条 3.下型板
二、挤出机头的分类
1、按挤出的塑件分类
ⅰ管机头 ⅱ棒机头 ⅲ异型材机头等
2、按挤出塑件的出口方向分类
ⅰ直通机头(直向机头) ⅱ角式机(横向机头)
三、挤出成型工艺参数
1、温度:
包括加料段、压缩段、均化段、机头及口模段温度。
※加料段的温度不宜过高,压缩段和均化段的温度可高一些。 ※机头的温度控制在塑料热分解温度以下
• 2、压力
• 克服料流的阻力、过虑板、过虑网、口模等产生的阻力。 • 合理控制螺杆转速,保证温控系统的精度,以减小压力波动。
• 3、挤出速度
• 将熔融的塑料自模具内以挤压的方式往外推出,而得到与模口 相同几何形状的流体,冷却固化后,得到所要的零件。
二、挤出成型工艺过程
(动画) 1.原料准备:干燥、去杂质处理
2.挤出成型:
挤出机预热——加入塑料——熔融塑化——由机头挤出成型
• 3.定型和冷却
• 4.牵引和切割
• 在冷却得同时,连续均匀地将塑件引出。
第14章 挤出模具设计
14.1 挤出模具的机构杆之分,包括加料段、压缩段、均化段
附机: 模具(机头口模、定型装置)、冷却装置、
牵引装置、切割机或卷取装置等
控制系统
3、挤出成型特点
生产连续、效率高;质量稳定,适应性强。
• 一、挤出成型原理及其特点
1、挤出原理:塑化——成型——定型
真空定径装置(续)
定径装置与多个冷却槽的组合应用
• (1)口模和型芯 ——可形成稳定段(定型区)
挤出成型工艺及模具设计_课件
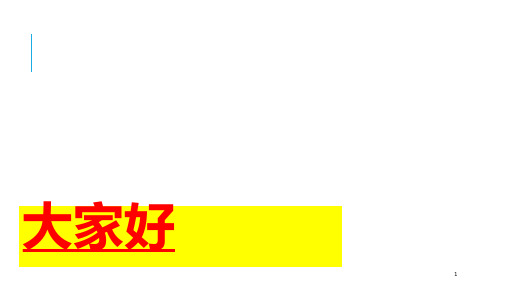
二、挤出成型机头概述
1. 挤出机头的作用 使熔融塑料由螺旋运动变为直线运动; 产生必要的成型压力,保证制品密实; 使塑料通过机头得到进一步塑化; 通过机头口模以获得截面形状相同、连续的塑料制品。
10
2. 机头的分类
按机头的几何形状分类 圆环机头:管材机头、棒材机头、造粒机头等 平板状机头:平模机头、板材机头、异型材机头等
内装置电热器时导入导线。
38
2. 管材的定径和冷却
为了使管材获得较低的表面粗糙值、准确的尺寸和几何 形状,管材离开口模时,必须立即进行定径和冷却,由定 径套来完成。
有两种方法: ❖ 外径定型 ❖ 内径定型
我国塑料管材标 准大多规定外径为基 本尺寸,故国内较常 用外径定型法。
39
(1)外径定型 适用于管材外径尺寸精度要求高、外表面粗糙度要求低的
按机头进出料方向分类 水平直通式机头 直角式机头
按机头的用途分类 吹膜机头、管材机头、板材机头、棒材机头、异型材 机 头等。
11
3.挤出机头的组成(以直通式管材机头为例)
口模 芯棒 分流器和分流器支架 机头体 过滤网和过滤板 连接部分 定径套
12
① 口模和芯棒 ② 挤出模的主要成型零件,口模用来成型塑件的外表
41
(2)内径定型
通过定径套内的循环水冷却定型 特点:保证管材内孔圆度,操作方便;宜用于直角式挤管机头
和旁侧式挤管机头。
适用:内径尺寸要求准确、圆度要求高的情况。
1-管材 2-定径芯模 3-芯棒 4-回水流道
5-进水管 6-排水管 7-进水嘴
42
定径芯长度:与管材壁厚及牵引速度有关,一般取80~ 300mm,牵引速度和壁厚大时,取大值。反之,取小值。 定径芯直径:一般比管材内径直径大2%~4%,始端比终端 直径大,锥度为0.6:100~1.0:100。
挤压模具设计

目录第一章概述 (2)第二章模孔布置 (3)2.1模具的外形尺寸 (3)2.2模孔的合理配置 (3)第三章设计工作带长度 (5)第四章设计导流腔 (8)第五章型材模孔尺寸设计 (9)第六章型材模具强度校核............................................................................................... 错误!未定义书签。
第七章绘制模具图.. (14)总结....................................................................................................................................... 错误!未定义书签。
参考文献. (16)第一章概述1.从模具设计与制造的专业术语可知,用于成形加工的模具必须完成设计和制造两个阶段,它们相辅相成,缺一不可。
本设计为型材模具课程设计。
2.设计时,首先根据工件横截面形状对模具的模孔进行布置;模孔布置设定后再对模具各段的工作带进行计算和设计,设计导流腔;选择模具材料并通过计算确定型材模孔尺寸;最后对所设计的模具进行强度校核及画出模具图;对此次课程设计进行总结。
第二章模孔布置2.1模具的外形尺寸①模具外形D模子外圆直径主要依据挤压机吨位和挤压筒大小、模孔的合理布置及制品尺寸来确定,并考虑模具外形尺寸的系列化,便于更换、管理,一般一台挤压机上最好只有1~2种规格。
型材部分模具外形尺寸如下所示:又因为挤压筒的内径为200mm,挤压机能力为19.6MN,则选取D=200mm②在挤压机设计时,通常选取单位压力位1000MPa时的挤压筒D t作为基本参数来确定模具的厚度,其关系为:H=(0.12~0.22)D t所以H=(0.12~0.22)D t=0.12~0.22)×200=24~44mm又因为模子厚度主要是根据强度要求及挤压机吨位来确定,在保证模具组件(模子+模垫+垫环)有足够强度的条件下,模子的厚度应尽量薄。
挤出塑料模具课程设计

挤出塑料模具课程设计一、课程目标知识目标:1. 学生能理解并掌握塑料模具的基本概念、分类及挤出模具的工作原理。
2. 学生能够描述挤出塑料模具的设计流程,包括模具结构、材料选择和工艺参数的确定。
3. 学生了解塑料成型过程中的常见问题及解决办法。
技能目标:1. 学生能够运用CAD软件进行挤出模具的设计,具备初步的模具设计能力。
2. 学生能够运用实验设备进行挤出成型实验,掌握实验操作的基本技能。
3. 学生能够分析挤出模具设计中的问题,并提出合理的改进方案。
情感态度价值观目标:1. 培养学生对塑料模具设计和制造的兴趣,激发学生的创新意识。
2. 培养学生严谨、细致的学习态度,提高学生的团队协作能力。
3. 学生能够认识到塑料模具在工业生产中的重要性,增强学生的社会责任感。
本课程针对高年级学生,结合学科特点和教学要求,以实用性为导向,旨在培养学生的模具设计能力、实验操作技能和问题分析解决能力。
通过本课程的学习,学生能够将理论知识与实际应用相结合,为未来从事相关工作奠定基础。
二、教学内容本章节教学内容主要包括以下三个方面:1. 塑料模具基础知识:- 模具的分类、结构及其工作原理。
- 塑料材料的基本性能及选用原则。
- 挤出模具的设计原理和流程。
2. 挤出模具设计方法:- 模具结构设计:包括型腔、型芯、导向装置等。
- 模具材料选择:根据塑料性能和成型工艺选择合适的模具材料。
- 模具工艺参数确定:分析成型过程中压力、温度、速度等参数的影响。
3. 挤出成型实验与问题分析:- 实验设备操作:学会使用挤出机、模具等设备进行实验。
- 实验操作技能:掌握挤出成型过程中各项操作要领。
- 常见问题分析:分析成型过程中可能出现的缺陷,并提出解决方案。
教学内容参考教材相关章节,结合课程目标,按照以下进度安排:1. 塑料模具基础知识(2课时)2. 挤出模具设计方法(3课时)3. 挤出成型实验与问题分析(3课时)三、教学方法本章节采用以下多样化的教学方法,以激发学生的学习兴趣和主动性:1. 讲授法:在塑料模具基础知识部分,通过教师系统的讲解,使学生掌握模具的基本概念、分类和工作原理。
第三章 挤出成型工艺与模具结构
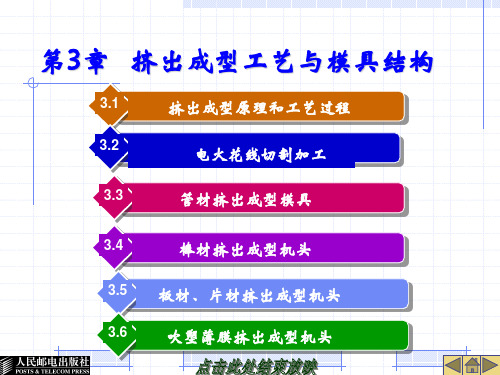
3.机头与挤出机的连接
常用国产挤出机与机头的连接形式如图3-3、 图3-4所示。 在图3-3中,机头以螺纹联接在机头法兰上, 机头法兰以4~6个铰链螺钉与机筒法兰连接固定。 图3-4所示为挤出机与机头的又一种连接形 式。机头以8个内六角螺钉与机头法兰连接固定, 机头法兰与机筒法兰由定位销定位,机头外圆与 机头法兰内孔配合,保证机头与挤出机的同心度。
3.3.3 管材定径套的结构类型及尺寸
管材的定径方法 : 1、外径定型法:(1)内压法 (2) 真空吸附法 。 2、内径定型法
3.4 棒材挤出成型模具
棒材是指截面为圆形的实心塑料型材, 塑料棒材的原材料一般是工程塑料,如尼龙、 聚甲醛、聚碳酸脂、ABS、聚砜、玻璃纤维 增强塑料等。棒材机头的螺杆长径比为2 5~120,除了生产玻璃纤维增强塑料外, 可以设置50~80目的过滤网。
3.1.1 挤出成型原理和特点 1.挤出成型原理
首先将粒状或粉状塑料加入料斗中,在旋转 的挤出机螺杆的作用下,加热的塑料通过沿螺杆 的螺旋槽向前方输送。在此过程中,塑料不断接 受料筒的外加热和螺杆与塑料之间、料筒与塑料 之间的剪切摩擦热,逐渐熔融呈黏流态,然后在 挤压系统的作用下,塑料熔体通过具有一定形状 的挤出模具,从而获得具有一定截面形状的塑料 型材,如图3-1所示。
3.6 吹塑薄膜挤出成型机头
薄膜是目前广泛使用的塑料挤出产品, 薄膜的厚度一般为0.01~0.25mm。薄膜的常 用生产方法是吹塑成型,就是由挤出机机头 挤出塑料管坯,同时从机头中心通入压缩空 气,将管坯吹成所需直径的薄膜。吹塑法可 以加工软、硬聚氯乙烯、聚乙烯、聚丙烯、 聚苯乙烯、聚酰胺等塑料薄膜。
2.挤出成型的特点
(1)连续成型,生产量大,生产率高,成 本低。 (2)塑件截面恒定,形状简单。 (3)塑件内部组织均衡紧密,尺寸比较稳 定准确。 (4)适用性强,除氟塑料以外,几乎能 加工所有热塑性塑料和部分热固性塑料。
典型的挤出模具设计

典型的挤出模具设计挤出模具是一种常用于橡塑制品加工的模具,通过材料在模具中连续挤出,使其形成具有一定形状和尺寸的产品。
挤出模具广泛应用于塑料、橡胶、硅胶、硬质泡沫等各种材料的生产中,能够制造出各种管材、板材、条材、异型材等产品。
典型的挤出模具设计需要考虑材料特性、产品形状和尺寸等多个因素。
首先,挤出模具设计需要根据材料的特性来确定模具的结构和参数。
不同材料具有不同的流动性、熔体温度和粘度,对模具的设计产生不同的要求。
例如,一些材料具有较高的熔体温度和较高的黏度,需要采用加热设备和较大的流道截面积来确保材料能够顺利挤出。
而一些材料具有较低的流动性,需要增加收缩率和壁厚等参数来避免产品出现瑕疵。
因此,设计师需要了解材料的特性,合理确定模具的结构和参数。
其次,挤出模具设计需要考虑产品的形状和尺寸。
不同的产品形状对模具的设计产生不同的要求。
例如,圆形管材的模具需要设计圆形的出模口和流道,以保证挤出的产品具有良好的圆度和尺寸一致性。
而异型材的模具需要根据产品的形状和结构设计复杂的挤出口和流道,以确保产品能够顺利挤出,并且具有良好的表面质量和尺寸精度。
因此,设计师需要根据产品的形状和尺寸,合理确定模具的结构和参数。
再次,挤出模具设计需要考虑模具的制造和使用成本。
模具的制造和使用成本直接影响到产品的竞争力和市场占有率,因此设计师需要在满足产品形状和质量要求的前提下,尽量减少模具的制造和使用成本。
一方面,可以通过合理设计模具的结构和参数,减少模具的复杂度和制造难度。
另一方面,可以选择合适的材料和加工工艺,提高模具的耐磨性和使用寿命,降低维护和更换的频率。
因此,设计师需要综合考虑多个因素,合理选择模具的结构、材料和加工工艺,以实现最佳的经济效益。
最后,挤出模具设计还需要考虑产品的生产效率和质量稳定性。
生产效率和质量稳定性是企业提高竞争力和降低成本的关键。
模具的设计应充分考虑产品的生产工艺和生产效率,提高生产效率和降低不良品率。
挤出成型工艺及模具设计

湿法挤出一般采用柱塞式挤出机,材料 的塑化是借助溶剂使其变为可流动态的。
根据挤出时加压方式的不同,可分为 连续式和间歇式两种。 (1)连续式挤出采用螺杆式挤出机,加压是
通过螺杆进行的。 (2)间歇式挤出采用柱塞式挤出机进行,借
道表面粗糙度Ra值应小于16~32μm。
(4) 机头内应有分流装置和适当的压缩区 机头内应设置分流器和分流器支架等
一类分流装置,如图4-4所示。 另外,机头中设计一段压缩区域,以
增大熔体的流动阻力,消除熔接痕。
(5) 机头成型区应有正确的截面形状 设计机头成型区时,应尽量减小离模
膨胀效应和收缩效应的影响。 设计机头时: 第一:要对口模进行适当的形状和尺寸补
其优点为:生产率高; 定径精度高; 料流稳定均匀; 成型质量也较高; 熔体的流动阻力较小;
缺点为:
3. 旁侧式挤管机头与直角式相似,如
图4.7所示,其结构更为复杂,熔体流动阻
图4.7 旁侧式机头
1、8、10、12 测 温孔; 2 口模; 3 型芯; 4、7 外加热圈; 5 调节螺钉; 6 机头体; 9 连接体; 11 内加热圈
第4章 挤出成型工艺及模具设计
4.1 挤出成型原理及其工艺特性 4.2 挤出成型模具概述 4.3 管材挤出成型模具 4.4 棒材挤出成型机头 4.5 板材、片材挤出成型机头 4.6 异型材挤出成型模具
4.1 挤出成型原理及其工艺特性
4.1.1 挤出成型原理及其特点 4.1.2 挤出成型工艺过程 4.1.3 挤出成型工艺参数
b.挤出成型 将挤出机预热到规定温度后,启动电
机带动螺杆旋转输送物料,同时向料筒中 加入塑料。
挤压模具设计与制造改

ε——正偏差
管材:dd = dm + kd m+ 0.04S S——管材壁厚
图1-1 综合收缩系数K取值
(4)出口直径dc
为防止制品出定径带被划伤表面,故dc比dd大3~5mm,但差 值不能太大,否则会影响模子强度,定径带与出口过渡部分可做 成20~45°的斜面,一般锥模用20°,平模用45°,也可用圆弧 连接。(防止粘结,制品表面质量好)见图1-4。 图1-4 定径带直径和出口带直径的配合
(5)入口圆角 r入
模子的入口圆角是指被挤压金属进入定径带的部分,
即模子工作端面与定径带形成的端面角。可防止低塑性合 金产生表面裂纹,减小金属在流入定径带时的非接触变形 ,减少模子棱角的压塌变形。但增大了接触摩擦面积,挤 压力增高。
模子入口圆角值的选取与金属的强度、挤压温度和制 品尺寸、模子结构等有关。铝及铝合金的入口圆角 r入 =0.4~0.75mm;铜的入口圆角(T H为2~5mm,B为 4~8mm)。 (6)外形尺寸(具有通用性,已经基本系列化)( P277-模具外形标准尺寸表)
定径带是稳定制品尺寸和保证制品表面质量的部分。工作 带太长,会增大与金属的摩擦作用,增大挤压力,易粘结 金属,使制品出现划伤、毛刺、麻点等。工作带过短,磨 损快而使制品超差,变椭圆等。 hd的长短与制品尺寸和金属性质有关: 据生产经验,一般取值为: 紫铜、黄铜、青铜 hd =4~12mm 白铜、镍合金 hd =3~5mm 铝及铝合金 hd =2~8mm
•图1-7 轴对称型材模孔的配置
2)对只有一个对称轴的型材,并且缘板厚度相差不大,其重心 要 与模子中心重合 ,模孔的布置如图1-8所示。
塑料挤出模具设计
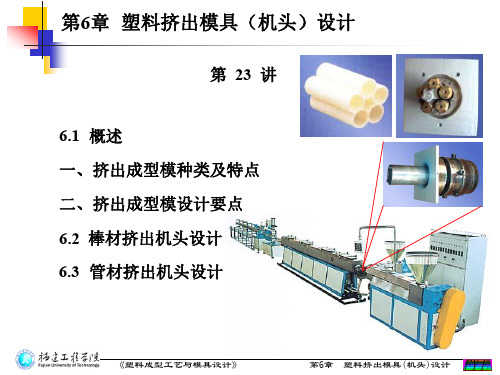
《塑料成型工艺与模具设计》
第6章 塑料挤出模具(机头)设计
一、管材挤出机头结构设计
(1)直管式机头 结构:由扩张分配段、压缩段、成型段组成; 适用于PVC、PA、PC、PE、PP等薄壁小口径管材挤出。
口模间隙 调节螺钉
《塑料成型工艺与模具设计》
第6章 塑料挤出模具(机头)设计
(2)直角式挤管机头
二、定径套设计
内压定径套内径:定径套直径应稍大于口模内径;100mm 以下管材定径套内径比口模大0.5~0.8mm;100~300mm的管 材定径套内径比口模约大1mm。
真空外径定径套:定径套内壁开有许多抽真空小孔或窄缝 (孔径或缝宽0.8mm,孔间距约10mm),使管材紧贴于定 径内壁,同时冷却定型。
棒材种类:PE、PP、 PC、PA、PMMA、 PTFE、ABS、POM、 PVC……
《塑料成型工艺与模具设计》
第6章 塑料挤出模具(机头)设计
一、棒材挤出机头结构设计
棒材机头种类: • 带分流梭的机头 • 不带分流梭的机头
聚四氟乙 烯绝热垫
过滤板和 过滤网
《塑料成型工艺与模具设计》
第6章 塑料挤出模具(机头)设计
特点:挤出管材轴线与挤出机 螺杆轴线成直角,便于进气、 芯模的加热,以及芯线、复合 管的导入包覆。
适用于内定径的PE、PP、PA 等塑料管挤出,大小口径管材 均适用。
熔接痕在进料口对面,设计时 要尽量减少管材沿圆周各点流 动距离不等和压力不平衡。
《塑料成型工艺与模具设计》
第6章 塑料挤出模具(机头)设计
《塑料成型工艺与模具设计》
第6章 塑料挤出模具(机头)设计
(3)芯棒设计
芯棒由收缩段和平直段组成,与分流锥之间用螺纹连接; 平直段长度等于口模长度。
塑料管材挤出模具设计
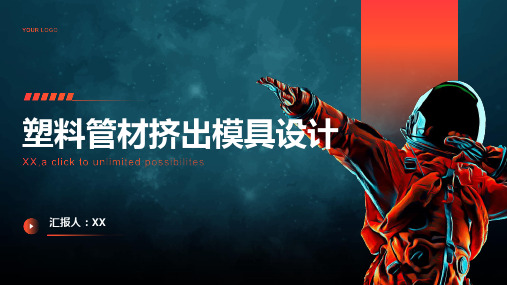
实例分析:对 PVC管材挤出模 具设计实例进行 深入分析,包括 设计要点、难点 及解决方案
经验总结:总结 PVC管材挤出模 具设计的经验教 训,提出优化建 议和未来发展方 向
实例二:PE管材挤出模具设计
模具结构:采用分流器、定 径套、机头等部件
模具温度控制:加热和冷却 系统对管材成型至关重要
模具材料:选择高强度、耐 磨性好的钢材
模具设计的原则和流程
模具设计应满足生产塑料管材的工艺要求,确保管材质量、尺寸和外观符合标准。 模具设计应考虑到生产效率、成本和安全性,以提高生产效益。 模具设计应遵循“一模多腔”的原则,以提高生产效率。 模具设计应注重冷却系统的设计,确保模具温度控制合理,提高管材质量。
塑料管材挤出模具设计要点
模具流道设计
数字化与信息化 技术:优化设计 流程,提高设计 精度
3D打印技术:个 性化定制,缩短 产品上市时间
绿色环保设计:降低能耗和减少废弃物排放的措施
采用新型材料:选择 可再生、可降解或环 保的材料,降低对环 境的污染。
优化结构设计:通过 改进模具结构,减少 生产过程中的能耗和 废弃物排放。
引入智能化技术:利 用先进的控制技术, 实现生产过程的自动 化和智能化,降低能棒加热,确保温度均匀分布,提高塑料管材的塑化效果 冷却系统:采用循环水冷却,快速降低模具温度,提高生产效率 温控系统:精确控制加热和冷却温度,保证产品质量和生产稳定性 安全保护:设置温度过高、过低自动报警和保护功能,确保生产安全
模具排气和溢料设计
模具排气:设计时需考虑模具的排气口位置和大小, 以确保在挤出过程中气体能够顺利排出。
产。
新型材料应用: 采用高强度、耐 高温、耐腐蚀等 新型材料,提高 模具的使用寿命
挤出模具设计要点

挤出模具设计要点欧洲特别是德国是塑料门窗异型材的发祥地,塑料挤出技术和理论也比较发达,许多挤出模的设计思想都源于此。
文献[1]提出了著名的横向流动最小化(Cross Flows Minimized)原则。
认为熔体流过一系列的截面,把截面再分为不同的小段,通过调整截面形状尺寸,使截面上各个区域上的质量流率成比例,其比例大小为该截面区域占截面总面积之比。
该思想比较经典,与挤出模机颈段建模方法中的面积测绘法有异曲同工之妙。
文献[2]进一步发展了这种思想,总结了调节流动平衡的方法和数值分析的三种途径,讨论了横截面计算和单独流动对挤出流动的影响。
波兰Sarsaw 理工大学的K.Wilczynski在《A computer model for a polymer single-screw extrusion》中提出了一个针对单螺杆挤出成型过程的计算机模型SSEM。
SSEM能模拟挤出成型的全过程,可根据给定的工艺参数预测流动特性。
在实验中对其设计及模拟的正确性进行了检验,试验对比显示模拟结果与实测数据相差4%~10%,其设计具有较高的可信度。
英国Dundee大学的G S H Chan和K K B Hon在《Integration of computing techniques for plastics extrusion die design》中介绍了他们应用DUCT软件根据给定的模头进口截面与模头出口截面尺寸自动生成流线型挤出流道。
为使DUCT软件设计简单,文献中作了两个假设,即模头进口截面形状恒为圆形和模头出口截面尺寸等于异型材产品截面尺寸,即不考虑离模膨胀问题。
文中总结了以前两种生成流道的常规算法,对其作了巧妙的修改与组合,思路非常新颖。
Queen's University of Belfast的Sun Da-Wen和华南理工大学的彭玉成指出,目前异型材挤出制品应用很广,但其模具设计很复杂,现有的文献介绍实际设计经验的很少,因而他们在《Practical method to design hollow profile dies》中提出了一种简单的设计异型材挤出流道轮廓的方法,其依据条件是熔体在挤出模模头出口流速一致,该方法利用过渡线理论(transitional line method)与变流道厚度法理论(variable channel thickness method)对组成整个挤出流道的每一块模块型腔轮廓进行计算,并且在设计中考虑了各模块组合成整体型腔的平衡问题。
塑料挤出模具设计
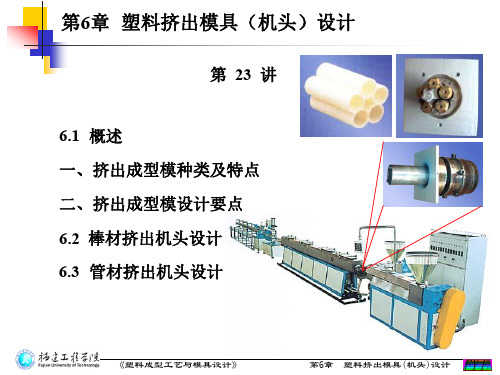
一、棒材挤出机头结构设计
棒材机头口模与定径套之间需用绝热垫圈隔热。
《塑料成型工艺与模具设计》
第6章 塑料挤出模具(机头)设计
一、棒材挤出机头结构设计
定径套:直径很小( φ 5mm以内)的棒材挤出可以不设定 径套;当棒材直径较大时,必须使用定径套。
《塑料成型工艺与模具设计》
第6章 塑料挤出模具(机头)设计
二、水冷定径套结构设计
水冷定径套关键尺寸:内径和长度。
• 内径:由棒材直径决定,需考虑成型收缩率的影响;
• 长度:应保证棒材离开定径套后不因自重作用而变形,并 能保持一定的表面质量。
棒材挤出成型收缩率
材料 PA1010 PA66 ABS
PC
POM 氯化聚醚 聚砜
收缩率/% 2.5~5 3~6 1~2.5 1~2.5 2.5~4 1.5~3.5 1~2
第6章 塑料挤出模具(机头)设计
6.2 棒材挤出机头设计
棒材规格:几毫米~几百毫米不等,它可比挤出螺杆直径 还大。
挤出速度:为使中心的塑料熔体全部冻结,挤出速度有时 控制得很慢(如φ 45mm挤出机挤φ 60mm尼龙棒时,速度为 2.5m/h,挤φ 200mm棒材时,挤出速度为0.5m/h)。
《塑料成型工艺与模具设计》
第6章 塑料挤出模具(机头)设计
6.3 管材挤出机头设计
一、管材挤出机头结构设计 1、管材挤出机头结构组成
适用于挤RPVC小管
《塑料成型工艺与模具设计》
第6章 塑料挤出模具(机头)设计
一、管材挤出机头结构设计
2、管材挤出机头分类 按管材挤出方向与挤出机轴线之间的关系分: • 直管式机头 • 直角式机头 • 旁侧式机头等
特点:挤出管材轴线与挤出机 螺杆轴线成直角,便于进气、 芯模的加热,以及芯线、复合 管的导入包覆。
挤出模具设计课程设计

挤出模具设计课程设计一、教学目标本课程旨在通过挤出模具设计的学习,使学生掌握挤出模具的基本结构、工作原理和设计方法,培养学生运用理论知识解决实际问题的能力。
通过本课程的学习,学生应达到以下目标:1.知识目标:(1)了解塑料挤出成型的基本原理和工艺过程;(2)掌握挤出模具的组成、结构和作用;(3)熟悉挤出模具的设计方法和步骤。
2.技能目标:(1)能够分析挤出成型工艺参数对模具设计的影响;(2)具备挤出模具零件尺寸计算和选材的能力;(3)学会使用相关软件进行挤出模具设计。
3.情感态度价值观目标:(1)培养学生的创新意识和团队协作精神;(2)强化学生对模具行业的认识,提高学生对模具设计的兴趣;(3)培养学生严谨的科学态度和良好的职业道德。
二、教学内容本课程的教学内容主要包括以下几个部分:1.塑料挤出成型的基本原理和工艺过程;2.挤出模具的组成、结构和作用;3.挤出模具设计方法和步骤;4.挤出模具零件尺寸计算和选材;5.挤出模具设计软件的使用。
教学过程中,将结合具体案例进行分析,使学生能够更好地理解和掌握所学知识。
三、教学方法为了提高教学效果,本课程将采用多种教学方法,包括:1.讲授法:通过讲解理论知识,使学生掌握挤出模具设计的基本原理和方法;2.案例分析法:分析实际案例,使学生了解挤出模具设计的过程和注意事项;3.实验法:通过实验操作,使学生熟悉挤出模具的结构和作用;4.讨论法:分组讨论,培养学生团队协作能力和创新意识。
四、教学资源为了支持教学内容和教学方法的实施,丰富学生的学习体验,我们将准备以下教学资源:1.教材:选用权威、实用的教材,为学生提供系统的理论知识;2.参考书:提供相关领域的参考书籍,拓宽学生的知识视野;3.多媒体资料:制作课件、视频等多媒体资料,帮助学生更好地理解教学内容;4.实验设备:准备现代化的实验设备,为学生提供实践操作的机会。
五、教学评估本课程的教学评估将采用多元化的评估方式,全面、客观地评价学生的学习成果。
挤压模具设计课程设计

表2-3热挤压各种金属材料时的工艺参数值(部分)
金属材料
挤压温度°C
挤压比λ
流出速度m/s
单位挤压力
铜及其合金
纯铜
820~910
10~400
0.10~5.0
300~650
α+β黄铜、青铜
650~840
10~(300~400)
0.10~3.3
200~500
含10~13%Ni白铜
700~780
10~(150~200)
表2-2挤压制品的外接圆至挤压筒内壁的最小距离
挤压筒直径
80~95
115~130
150~200
220~280
300~500
挤压制品外接圆至挤压筒之间的最小距离
15
20
25
30
50
在本课程设计中,
挤压筒所允许外接圆直径Dw=(0.80~0.85)Dt=160~170,取160mm
模具外径D=(1.25~1.45)Dw=200~232
148
198
230,330
270,306,360,420
300,420,570,670,880
570,670,900,1000
16,32
32,50,70
40,60,80
60,80
60,80
挤出模具装配尺寸的设计

挤出模具装配尺寸的设计模具设计,可以先设计模芯再设计模套,也可以先设计模套再设计模芯。
为了较少设计验证次数,一般先设计模套再设计模芯。
我们以65型挤出机机头来举例,已知机头装配尺寸,要求设计模芯、模套。
经测绘,得65型挤出机模头尺寸。
1、先设计模套,根据模套拆装要求,其伸出模头的长度约10mm,则得到模套的总长10+20=30mm;2、确定模套内锥最大外径=Φ25mm;3、根据要求,确定模套定径区直径ΦD;4、取定径区长度=0.5D;5、计算模套内锥半角γ/2=ATAN((25-D)/(2*(30-0.5D))*180/PI();绘制模套的草图(见图10);6、因采用挤压式,模芯与模套的模间距L=2δ厚度;7、选模头右边平面为基准面A,模芯口至基准面A的距离=10-2δ厚度;8、为模芯拆卸方便以及模芯强度,选模芯伸出模头左边约10mm,则可以得到模芯总长=10+(10-2δ厚度)+65;9、绘制模芯草图(如图);10、为便于调节偏芯,模芯螺纹长度一般取8~10mm,即b=8mm;11、根据模头尺寸结构,取d4=18mm;12、根据第8条,我们知道模芯伸出模头左侧10mm,则a+b=27+10=37mm,a=37-b=37-8=31mm;13、为保证调偏螺钉能正面受力在模芯上,一般c取12~15mm,即c=15mm;14、根据线芯大小,我们确定模芯定径区直径d1=d线芯+(0.2~0.5)mm,取d1=d 线芯+0.2 mm,那么模芯外锥最小外径d2=d1+0.5*2=d线芯+1.2 mm;15、那么根据以上数据,我们可以得出模芯外锥部分的长度=L-a-b-c=10+(10-2δ厚度)+65-31-8-15=31-2δ厚度mm;16、根据锥角计算公式,求的模芯外锥角β= ATAN((18- d线芯+1.2)/(2*(31-2δ厚度))*180/PI()17、将计算出模芯的锥角β与计算的模套外锥角γ比较,看看其差值是不是符合我们设计要求,若在设计范围内,设计成功,绘制零件图;若有出入,再次循环以上内容,直至符合设计要求为止,但必须保证在满足角度的前提下,还必须满足装配上的要求。
- 1、下载文档前请自行甄别文档内容的完整性,平台不提供额外的编辑、内容补充、找答案等附加服务。
- 2、"仅部分预览"的文档,不可在线预览部分如存在完整性等问题,可反馈申请退款(可完整预览的文档不适用该条件!)。
- 3、如文档侵犯您的权益,请联系客服反馈,我们会尽快为您处理(人工客服工作时间:9:00-18:30)。
(数控模具设计)第章挤出模具设计C第9章挤出模具设计9.1概述塑料挤出成型是用加热的方法使塑料成为流动状态,然后在壹定压力的作用下使它通过塑模,经定型后制得连续的型材。
挤出法加工的塑料制品种类很多,如管材、薄膜、棒材、板材、电缆敷层、单丝以及异形截面型材等。
挤出机仍能够对塑料进行混合、塑化、脱水、造粒和喂料等准备工序或半成品加工。
因此,挤出成型已成为最普通的塑料成型加工方法之壹。
用挤出法生产的塑料制品大多使用热塑性塑料,也有使用热固性塑料的。
如聚氯乙烯、聚乙烯、聚丙烯、尼龙、ABS、聚碳酸酯、聚砜、聚甲醛、氯化聚醚等热塑性塑料以及酚醛、脲醛等热固性塑料。
挤出成型具有效率高、投资少、制造简便,能够连续化生产,占地面积少,环境清洁等优点。
通过挤出成型生产的塑料制品得到了广泛的应用,其产量占塑料制品总量的三分之壹之上。
因此,挤出成型在塑料加工工业中占有很重要的地位。
壹、挤出成型机头典型结构分析机头是挤出成型模具的主要部件,它有下述四种作用:(1)使物料由螺旋运动变为直线运动;(2)产生必要的成型压力,保证制品密实;(3)使物料通过机头得到进壹步塑化;(4)通过机头成型所需要的断面形状的制品。
现以管材挤出机头为例,分析壹下机头的组成和结构,见图8-1所示。
1.口模和芯棒口模成型制品的外表面,芯棒成型制品的内表面,故口模和芯棒的定型部分决定制品的横截面形状和尺寸。
2.多孔板(过滤板、栅板)如图8-2所示,多孔板的作用是将物料由螺旋运动变为直线运动,同时仍能阻止未塑化的塑料和机械杂质进入机头。
此外,多孔板仍能形成壹定的机头压力,使制品更加密实。
3.分流器和分流器支架分流器又叫鱼雷头。
塑料通过分流器变成薄环状,便于进壹步加热和塑化。
大型挤出机的分流器内部仍装有加热装置。
分流器支架主要用来支撑分流器和芯棒,同时也使料流分束以加强搅拌作用。
小型机头的分流器支架可和分流器设计成整体。
4.调节螺钉用来调节口模和芯棒之间的间隙,保证制品壁厚均匀。
5.机头体用来组装机头各零件及挤出机连接。
6.定径套使制品通过定径套获得良好的表面粗糙度,正确的尺寸和几何形状。
7.堵塞防止压缩空气泄漏,保证管内壹定的压力。
二、挤出成型机头分类及其设计原则1.分类由于挤出制品的形状和要求不同,因此要有相应的机头满足制品的要求,机头种类很多,大致可按以下三种特征来进行分类:(1)按机头用途分类可分为挤管机头、吹管机头、挤板机头等;(2)按制品出口方向分类可分为直向机头和横向机头,前者机头内料流方向和挤出机螺杆轴向壹致,如硬管机头;后者机头内料流方向和挤出机螺杆轴向成某壹角度,如电缆机头;(3)按机头内压力大小分类可分为低压机头(料流压力为MPa)、中压机头(料流压力为4-10MPa)和高压机头(料流压力在10MPa之上)。
2.设计原则(1)流道呈流线型为使物料能沿着机头的流道充满且均匀地被挤出,同时避免物料发生过热分解,机头内流道应呈流线型,不能急剧地扩大或缩小,更不能有死角和停滞区,流道应加工得十分光滑,表面粗糙度应在Ra0.4um以下。
(2)足够的压缩比为使制品密实和消除因分流器支架造成的结合缝,根据制品和塑料种类不同,应设计足够的压缩比。
(3)正确的断面形状机头的成型部分的设计应保证物料挤出后具有规定的断面形状,由于塑料的物理性能和压力、温度等因素的影响,机头的成型部分的断面形状且非就是制品的相应的断面形状,二者有相当的差异,设计时应考虑此因素,使成型部分有合理的断面形状。
由于制品断面形状的变化和成型时间有关,因此控制必要的成型长度是壹个有效的方法。
(4)结构紧凑在满足强度条件下,机头结构应紧凑,其形状应尽量做得规则而对称,使传热均匀,装卸方便和不漏料。
(5)选材要合理由于机头磨损较大,有的塑料又有较强的腐蚀性,所以机头材料应选择耐磨、硬度较高的碳钢或合金钢,有的甚至要镀铬,以提高机头耐腐蚀性。
此外,机头的结构尺寸仍和制品的形状、加热方法、螺杆形状、挤出速度等因素有关。
设计者应根据具体情况灵活应用上述原则。
9.2典型挤出机头及设计常见的挤出机头有管材挤出机头、吹管膜机头、电线电缆包覆机头、异形材料挤出机头等。
壹、管材挤出机头及设计1.管材挤出机头的结构形式常见的管材挤出机头结构形式有以下四种:(1)直管式机头图8-3为直管式机头。
其结构简单,具有分流器支架。
芯模加热困难,定型长度较长。
适用于PVC、PA、PC、PE、PP等塑料的薄壁小口径的管材挤出。
(2)弯管式机头图8-4为弯管式机头。
其结构复杂,没有分流器支架,芯模容易加热,定型长度不长。
大小口径管材均适用,特别适用于定内径的PE、PP、PA等塑料管材成型。
(3)旁侧式机头图8-5为旁侧式机头,结构复杂,没有分流器支架,芯模能够加热,定型长度也不长。
大小口径管材均适用。
2.管材挤出机头零件的设计(1)口模口模是成型管材外表面的零件,其结构如图8-6所示。
口模内径不等于塑料管材外径,因为从口模挤出的管坯由于压力突然降低,塑料因弹性恢复而发生管径膨胀,同时,管坯在冷却和牵引作用下,管径会发生缩小。
这些膨胀和收缩的大小和塑料性质、挤出温度和压力等成型条件以及定径套结构有关,目前尚无成熟的理论计算方法计算膨胀和收缩值,壹般是根据要求的管材截面尺寸,按拉伸比确定口模截面尺寸。
所谓拉伸比是指口模成型段环隙横截面积和管材横截面积之比。
即(8-1)式中I为拉伸比,常用塑料允许的拉伸比如下:PVC为1.0~1.4,PA为1.4~3.0;ABS 为1.0~1.1;PP为1.0~1.2;HDPE为1.1~1.2;LDPE为1.2~1.5。
r——口模内径;r1——芯棒外径;R——管材外径;R1——管材内径。
口模定型段长度L1和塑料性质、管材的形状、壁厚、直径大小及牵引速度有关。
其值可按管材外径或管材壁厚来确定;L1=(0.5~3)D(8-2)或L1=(8~15)t(8-3)式中D——管材外径;t——管材壁厚。
(2)芯模芯模是成型管材内表面的零件,如图8-8所示。
直管机头和分流器以螺纹联接。
芯模的结构应有利于熔体流动,有利于消除熔体经过分流器后形成的结合缝。
熔体流过分流器支架后,先经过壹定的压缩,使熔体很好地汇合。
为此芯模应有收缩角β,其值决定于塑料特性,对于粘度较高的硬聚乙烯,β壹般30°~50°;对于粘度低的塑料β可取45°~60°。
芯模的长度L 1′和口模L 1相等。
L 2壹般按下式决定:L 2=(1.5~2.5)D0(8-4)式中D0——栅板出口处直径。
芯模直径d 1可按下式计算;d 1=d —2δ(8-5)式中δ—芯模和口模之间间隙;d —口模内径。
由于如上所述塑料熔体挤出口模后的膨胀和收缩,使δ不等于制品壁厚,δ可按下式计算: (8-6) 式中k —经验系数,k=1.16~1.20;t —制品壁厚。
为了使管材壁厚均匀,必须设置调节螺钉(图8-3件3)以便安装和调整口模和芯模之间间隙。
调节螺钉数目壹般为4~8个。
(3)分流器分流器的作用是使熔体料层变薄,以便均匀加热,使之进壹步塑化。
其结构如图8-8所示。
分流器和栅板之间的距离壹般取10~20mm ,或稍小于0.1D1(D1为挤出机螺杆直径)。
保持分流器和栅板之间的壹定距离的作用是使通过栅板的熔体汇集。
因此,该距离不宜过小,否则熔体流速不稳定,不均匀;距离过大,熔体在此空间停留时间较长,高分子容易产生分解。
分流器的扩张角α值取决于塑料粘度,低粘度塑料取α=30°~80°,高粘度塑料取α=30°~60°,α太大,熔体流动阻力大;α过小,势必增大分流锥部分的长度。
kt=δ分流锥的长度壹般按下式确定:L3=(1~1.5)D0(8-7)式中D0——栅板出口处直径。
分流器头部圆角r壹般取0.5~2mm。
(4)分流器支架分流器支架设有进气孔和导线孔,用以通入压缩空气和内装置电热器时导入导线。
通入压缩空气的作用是为了管材的定径(内压法外径定型)和冷却。
分流器支架和分流器能够制成整体式的(图8-8),也可制成组合式的(图8-1)。
前者壹般用于中小型机头,后者壹般用于大型机头。
分流器支架上的分流筋的数目在满足支持强度的条件下,以少为宜,壹般为3~8根。
分流筋应制成流线型的(图8-8A-A剖面),在满足强度前提下,其宽度和长度应尽量小些,而且出料端的角度应小于进料端的角度。
(5)定径套对于外径定型法,直径小于30mm的硬聚氯乙烯管材,定径套长度取管径的3-6倍,其倍数随管径减小而增加,当管径小于35mm时,其倍数可增至10倍。
对于聚烯烃管材,定径套长度为管径的2~5倍,其倍数随直径减小而增大。
定径套直径通常比机头口模直径大2%~4%,且出口直径比进口直径略小。
对于内径定型法,定径芯模长度取80~300mm,其外径比管材内径大2%~4%,以利于管材内径公差的控制。
定径芯模锥度为1:1.6~1:10,始端大,终端小。
二、吹塑薄膜机头的结构及设计1.吹塑薄膜机头结构形式常见的吹塑薄膜机头结构形式有芯棒式机头、中心进料的“十字形机头”、螺旋式机头、旋转式机头以及双层或多层吹塑薄膜机头等。
(1)芯棒式机头图9-9(下页)所示芯棒式吹塑薄膜机头。
塑料熔体自挤出机栅板挤出,通过机颈5到达芯棒轴7时,被分成俩股且沿芯棒分料线流动,然后在芯棒尖处重新汇合,汇合后的熔体沿机头环隙挤成管坯,芯棒中通入压缩空气将管坯吹胀成管膜。
芯棒式机头内部通道空腔小,存料少,塑料不容易分解,适用于加工聚氯乙烯塑料。
但熔体经直角拐弯,各处流速不等,同时由于熔体长时间单向作用于芯棒,使芯棒中心线偏移,即产生“偏中”现象,因而容易导致薄膜厚度不均匀。
(2)十字形机头图9-10为十字形机头,其结构类似管材挤出机机头。
这种机头的优点是出料均匀,薄膜厚度容易控制;芯模不受侧压力,不会产生如芯棒式机头那种“偏中”现象。
但机头内腔大,存料多,塑料易分解,适用于加工热稳定性好的塑料,而不适于加工聚氯乙烯。
(3)螺旋式机头图9-11为螺旋式机头,塑料熔体从中央进口挤入,通过带有多个沟槽由深变浅直至消失的螺旋槽(也有单螺旋)的芯棒7,然后在定型区前缓冲槽汇合,达到均匀状态后从口模挤出。
这种机头的优点是,机头内熔体压力大,出料均匀,薄膜厚度容易控制,薄膜性能好。
但结构复杂,拐角多,适用于加工聚丙烯、聚乙烯等粘度小且不易分解的塑料。
(4)旋转式机头图9-12为旋转式机头。
其特点是芯模2和口模1都能单独旋转。
芯模和口模分别由直流电机带动,能以同速或不同速、同向或异向旋转。
采用这种机头可克服由于机头制造、安装不准确及温度不均匀造成的塑料薄膜厚度不均匀,其厚度公差可达0.01mm。
它的应用范围较广,对热稳定性塑料和热敏性塑料均可成型。