挤出成型工艺及模具设计PPT课件
合集下载
挤出成型工艺及模具设计_课件
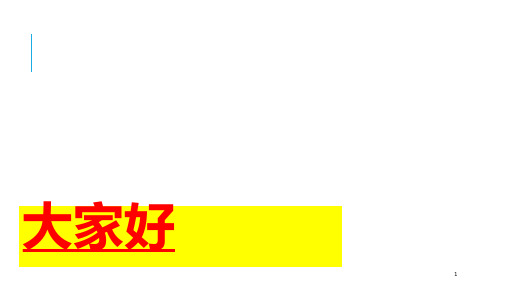
9
二、挤出成型机头概述
1. 挤出机头的作用 使熔融塑料由螺旋运动变为直线运动; 产生必要的成型压力,保证制品密实; 使塑料通过机头得到进一步塑化; 通过机头口模以获得截面形状相同、连续的塑料制品。
10
2. 机头的分类
按机头的几何形状分类 圆环机头:管材机头、棒材机头、造粒机头等 平板状机头:平模机头、板材机头、异型材机头等
内装置电热器时导入导线。
38
2. 管材的定径和冷却
为了使管材获得较低的表面粗糙值、准确的尺寸和几何 形状,管材离开口模时,必须立即进行定径和冷却,由定 径套来完成。
有两种方法: ❖ 外径定型 ❖ 内径定型
我国塑料管材标 准大多规定外径为基 本尺寸,故国内较常 用外径定型法。
39
(1)外径定型 适用于管材外径尺寸精度要求高、外表面粗糙度要求低的
按机头进出料方向分类 水平直通式机头 直角式机头
按机头的用途分类 吹膜机头、管材机头、板材机头、棒材机头、异型材 机 头等。
11
3.挤出机头的组成(以直通式管材机头为例)
口模 芯棒 分流器和分流器支架 机头体 过滤网和过滤板 连接部分 定径套
12
① 口模和芯棒 ② 挤出模的主要成型零件,口模用来成型塑件的外表
41
(2)内径定型
通过定径套内的循环水冷却定型 特点:保证管材内孔圆度,操作方便;宜用于直角式挤管机头
和旁侧式挤管机头。
适用:内径尺寸要求准确、圆度要求高的情况。
1-管材 2-定径芯模 3-芯棒 4-回水流道
5-进水管 6-排水管 7-进水嘴
42
定径芯长度:与管材壁厚及牵引速度有关,一般取80~ 300mm,牵引速度和壁厚大时,取大值。反之,取小值。 定径芯直径:一般比管材内径直径大2%~4%,始端比终端 直径大,锥度为0.6:100~1.0:100。
二、挤出成型机头概述
1. 挤出机头的作用 使熔融塑料由螺旋运动变为直线运动; 产生必要的成型压力,保证制品密实; 使塑料通过机头得到进一步塑化; 通过机头口模以获得截面形状相同、连续的塑料制品。
10
2. 机头的分类
按机头的几何形状分类 圆环机头:管材机头、棒材机头、造粒机头等 平板状机头:平模机头、板材机头、异型材机头等
内装置电热器时导入导线。
38
2. 管材的定径和冷却
为了使管材获得较低的表面粗糙值、准确的尺寸和几何 形状,管材离开口模时,必须立即进行定径和冷却,由定 径套来完成。
有两种方法: ❖ 外径定型 ❖ 内径定型
我国塑料管材标 准大多规定外径为基 本尺寸,故国内较常 用外径定型法。
39
(1)外径定型 适用于管材外径尺寸精度要求高、外表面粗糙度要求低的
按机头进出料方向分类 水平直通式机头 直角式机头
按机头的用途分类 吹膜机头、管材机头、板材机头、棒材机头、异型材 机 头等。
11
3.挤出机头的组成(以直通式管材机头为例)
口模 芯棒 分流器和分流器支架 机头体 过滤网和过滤板 连接部分 定径套
12
① 口模和芯棒 ② 挤出模的主要成型零件,口模用来成型塑件的外表
41
(2)内径定型
通过定径套内的循环水冷却定型 特点:保证管材内孔圆度,操作方便;宜用于直角式挤管机头
和旁侧式挤管机头。
适用:内径尺寸要求准确、圆度要求高的情况。
1-管材 2-定径芯模 3-芯棒 4-回水流道
5-进水管 6-排水管 7-进水嘴
42
定径芯长度:与管材壁厚及牵引速度有关,一般取80~ 300mm,牵引速度和壁厚大时,取大值。反之,取小值。 定径芯直径:一般比管材内径直径大2%~4%,始端比终端 直径大,锥度为0.6:100~1.0:100。
挤出模具设计PPT课件

挤出机头设计原则
1.内腔呈流线型 为了使塑料熔体能沿着机头中的流道
均匀平稳地流动而顺利挤出,机头的内腔 应呈光滑的流线型。 2.足够的压缩比 为使制品密实和消除因分流器支架造 成的结合缝,根据制品和塑料种类不同, 应设计足够的压缩比。
挤出机头设计原则
3.正确的截面形状和尺寸
由于塑料的物理性能和压力、温度等因素引起的 离模膨胀效应,及由于牵引作用引起的收缩效应使 得机头的成型区截面形状和尺寸并非塑件所要求的 截面形状和尺寸,因此设计时,要对口模进行适当 的形状和尺寸补偿,合理确定流道尺寸,控制口模 成型长度,获得正确的截面形状及尺寸。
2.直角式挤管机头 其用于内径定径的场合,冷却 水从芯棒中穿过。成型时塑料熔体包围芯棒并产生 一条熔接痕。熔体的流动阻力小,成型质量较高。 但机头结构复杂,制造困难。
管材挤出机设计
3.旁侧式挤管机头 其与直角式挤管机头 相似,其结构复杂。
三种机头的特征
机头类型 项目特征
直通式
挤出口径
适用于小口径管材
挤出模具结构的阐述
1、口模3是用来成型塑件的外表面的,芯棒4用来成型塑件的内表面的,所 以口模和芯模决定了塑件的截面形状。
2.过滤网和过滤板 过滤网9的作用是将塑料熔体由螺旋运动转变为直线运动,过滤杂质,并形
成一定的压力;过滤板又称多孔板, 同时还起支承过滤网的作用。 3.分流器和分流器支架 4、分流器6(又称鱼雷头)使通过它的塑料熔体分流变成薄环状以平稳地
(1)芯棒的外径 芯棒的外径由管材的内径决定, 但由于与口模结构设计同样的原因,即离模膨胀和 冷却收缩效应,所以芯棒外径的尺寸不等于管材内 径尺寸。根据生产经验,可按式(5-4)计算:
d= D-2e
(5-4)
挤出成型工艺与模具设计PPT

20
(表17.2)
2020/5/11
docin/sundae_meng
21
料筒、机头及口模中的温度和压力分布一般如图 所示
2020/5/11
docin/sundae_meng
22
影响塑化效果的主要因素是—— 温度和剪切作用
1)温度升高→物料粘度↓,有利于塑化,同 时熔体压力↓,出料快。
2)温度降低→粘度↑→机头口模压力↑→制 品密度大,形状稳定性好。
第17章 挤出成型工艺与模具设计
教学目的、要求:
了解挤出成型原理; 掌握挤出成型工艺过程及工艺参数; 熟悉挤出模的结构设计。
重点:挤出成型工艺过程及机头的结构
2020/5/11
docin/sundae_meng
1
§17-1 挤出成型原理及工艺
挤出模塑或挤塑
借助螺杆或柱塞的挤压作用 ,受热熔化的 塑料,强行通过口模而成为具有恒定截面的连 续型材。
3)螺杆的形式——普通螺杆(应用最广)
高效螺杆(末端设置一 些剪切混合元件,以促进混合、熔化和提 高产量)
2020/5/11
docin/sundae_meng
13
2020/5/11
docin/sundae_meng
14
(四)机头和口模
机头是口模与料筒的过渡连接部分,口模是制品 的成形部件,机头和口模通常为一体,习惯上 统称——机头。
docin/sundae_meng
3
根据塑料塑化方式不同,挤出工艺分为 :
干法——靠外加热熔化,塑化与挤出成形在机内
完成(简单的冷却→固化) 湿法—— 有机溶剂作用→粘流态→塑化在机外预
先完成→定型处理靠溶剂挥发而固化) 优点:塑化均匀,可避免热降解,考虑溶剂回
挤出成型工艺及模具设计

2020/3/31
2020/3/31
2020/3/31
三、管材挤出机机头的设计
常用的挤管机头有:直通式、直角式和旁侧式
直通式挤管机头
1-芯棒 2-口模 3-调节螺钉 4-分流器支架 5-分流器 6-加热器 7机头体
2020/3/31
2020/3/31
2020/3/31
挤出机头结构
1-管材 2-定型模 3-口 模 4-芯棒 5-调节螺钉 6-分流器 7-分流器支架 8-机头体 9-过滤网 10电加热圈
④ 压缩角 低粘度塑料45~ 60° ,高粘度塑料30 ~ 50° 。
2020/3/31
(3) 分流器和分流器支架 ① 分流器设计需确定的尺寸
❖分流器的角度α
低粘度塑料30°~80°, 高粘度塑料取30°~60°。
❖分流锥长度L3
L3 =(1~1.5) D0
❖分流器头部圆角半径r
取0.5~2mm
2020/3/31
② 分流器支架
① 支承分流器及芯棒,另外起搅拌物料的作用。 ② 小型机头,分流器和分流器支架可以做成一个整体。 ③ 为了消除塑料通过分流器后形成的接合线,分流器支架
上的分流肋应做成流线型,一般3~8根。 ④ 分流器支架设有进气孔和导线孔,用以通入压缩空气和
内装置电热器时导入导线。
2020/3/31
2020/3/31
④机头内设有调节装置
调节熔体流量、口模和芯棒侧隙、挤出压力、成型温度、 挤出速度等。
⑤合理选择材料
机头的零件要承受熔体的压力作用,所以要有足够的强度 。必要时对连接零件进行强度校核。
与熔体接触的零件要有足够的耐磨性和耐腐蚀性,必要时 表面要镀铬处理。主要零件进行调质处理,硬度45~ 50HRC。
2020/3/31
2020/3/31
三、管材挤出机机头的设计
常用的挤管机头有:直通式、直角式和旁侧式
直通式挤管机头
1-芯棒 2-口模 3-调节螺钉 4-分流器支架 5-分流器 6-加热器 7机头体
2020/3/31
2020/3/31
2020/3/31
挤出机头结构
1-管材 2-定型模 3-口 模 4-芯棒 5-调节螺钉 6-分流器 7-分流器支架 8-机头体 9-过滤网 10电加热圈
④ 压缩角 低粘度塑料45~ 60° ,高粘度塑料30 ~ 50° 。
2020/3/31
(3) 分流器和分流器支架 ① 分流器设计需确定的尺寸
❖分流器的角度α
低粘度塑料30°~80°, 高粘度塑料取30°~60°。
❖分流锥长度L3
L3 =(1~1.5) D0
❖分流器头部圆角半径r
取0.5~2mm
2020/3/31
② 分流器支架
① 支承分流器及芯棒,另外起搅拌物料的作用。 ② 小型机头,分流器和分流器支架可以做成一个整体。 ③ 为了消除塑料通过分流器后形成的接合线,分流器支架
上的分流肋应做成流线型,一般3~8根。 ④ 分流器支架设有进气孔和导线孔,用以通入压缩空气和
内装置电热器时导入导线。
2020/3/31
2020/3/31
④机头内设有调节装置
调节熔体流量、口模和芯棒侧隙、挤出压力、成型温度、 挤出速度等。
⑤合理选择材料
机头的零件要承受熔体的压力作用,所以要有足够的强度 。必要时对连接零件进行强度校核。
与熔体接触的零件要有足够的耐磨性和耐腐蚀性,必要时 表面要镀铬处理。主要零件进行调质处理,硬度45~ 50HRC。
塑料的挤出成型工艺ppt课件

Ⅰ 如旋转螺丝,而螺帽上无压力,则螺帽跟 着螺丝转动而不前移。
Ⅱ 若在螺帽上加一定压力,再旋转螺丝,则 螺帽就会随螺丝旋转而前移。
(2) 成型时,塑料与螺杆的摩擦力应小于塑 料与料筒的摩擦力,也即螺杆的光洁度应大于料筒 的光洁度。否则,塑料只能抱着螺杆空转打滑不能 前移。
完整版ppt课件
25
图3-6-7 螺槽中固体输送的理想模型(a) 和固体塞移动速度的矢量图(b)
则 Va=l×N。由图3-6-8中螺杆的几何关系可求出: πD=b1+b2= l·cotθ+l·cotφ= l(cotθ+ cotφ)
完整版ppt课件
30
πD 所以 l =
cotθ+cotφ
(3-6-3)
πDN
πDNtanθ·tanφ
因此 Va=
=
cotθ+cotφ tanφ + tanθ
(3-6-4)
完整版ppt课件
7
2.轻工部标准(82年苏州会议).。 SJ-150×25(D× L/D ):表示螺杆外径为
150mm,螺杆长径比为25的塑料挤出机 。
三 单螺杆挤出机的基本结构:
单螺杆挤出机是目前应用最广泛的挤出机, 其结构如图3-6-1所示。
完整版ppt课件
8
图3-6-1 单螺杆挤出机结构示意图
1-机座 2-电动机 3-传动装置 4-料斗 5-料斗冷却区 6-料筒 7-料筒加热器 8-热电偶控温点 9-螺杆 10-过滤网及多孔板 11-机头加热器 12-机头 13-挤出物
完整版ppt课件
9
1.螺杆:
(1)螺杆的主要参数:
D:螺杆外径; d:螺杆根径; L:螺杆长度;
t:螺距;
Ⅱ 若在螺帽上加一定压力,再旋转螺丝,则 螺帽就会随螺丝旋转而前移。
(2) 成型时,塑料与螺杆的摩擦力应小于塑 料与料筒的摩擦力,也即螺杆的光洁度应大于料筒 的光洁度。否则,塑料只能抱着螺杆空转打滑不能 前移。
完整版ppt课件
25
图3-6-7 螺槽中固体输送的理想模型(a) 和固体塞移动速度的矢量图(b)
则 Va=l×N。由图3-6-8中螺杆的几何关系可求出: πD=b1+b2= l·cotθ+l·cotφ= l(cotθ+ cotφ)
完整版ppt课件
30
πD 所以 l =
cotθ+cotφ
(3-6-3)
πDN
πDNtanθ·tanφ
因此 Va=
=
cotθ+cotφ tanφ + tanθ
(3-6-4)
完整版ppt课件
7
2.轻工部标准(82年苏州会议).。 SJ-150×25(D× L/D ):表示螺杆外径为
150mm,螺杆长径比为25的塑料挤出机 。
三 单螺杆挤出机的基本结构:
单螺杆挤出机是目前应用最广泛的挤出机, 其结构如图3-6-1所示。
完整版ppt课件
8
图3-6-1 单螺杆挤出机结构示意图
1-机座 2-电动机 3-传动装置 4-料斗 5-料斗冷却区 6-料筒 7-料筒加热器 8-热电偶控温点 9-螺杆 10-过滤网及多孔板 11-机头加热器 12-机头 13-挤出物
完整版ppt课件
9
1.螺杆:
(1)螺杆的主要参数:
D:螺杆外径; d:螺杆根径; L:螺杆长度;
t:螺距;
【大学课件】塑料挤出成型工艺及模具设计PPT

1 口模 (1) 口模的内径D
巴鲁斯效应和冷却收缩等原因使塑件外径不等 于口模内径 确定口模的内径D方法1: 确定口模的内径D方法2:
D=d/K
I
D2 Ds2
d2 ds2
Page 17
7.3.1 直通式挤出机头工艺参数的确定
1 口模 (2) 定型段长度L1 口模与型棒的平直部分Байду номын сангаас长度成为定型段
第七章 塑料挤出成型工艺及模具设计
7.1挤出成型工艺 主要用于生产具有恒定截面形状的管材、
棒材、板材、片材、线材和薄膜等。
此外,也可用于塑料的着色造粒、 共混、中空塑件型坯的生产。
Page 2
7.1.1 挤出成型原理及特点
挤出成型优点: 连续成型、生产量大、
生产效率高、设备简单
Page 3
成本低、操作方便
7.1.2 挤出成型工艺过程
原材料的准备阶段 塑化阶段 成型阶段 定径阶段 塑件的牵引、卷曲和切割阶段
Page 4
7.1.3 挤出成型工艺参数
温度 压力 挤出速度 牵引速度
Page 5
7.2 挤出成型机头概述
挤出成型的模具成为挤出成型机头
7.2.1 挤出机头的作用及分类 1 挤出机头作用
Page 24
7.3.2 管材的定径和冷却
1 外径定径 外径定径适用于对管材外径尺寸精度要求高、 外表面粗糙度低的情况。 按照压力产生方式不同,外径定径又分为内压法 和真空法。
Page 25
Page 26
Page 27
Page 28
7.3.2 管材的定径和冷却
1 外径定径 (1) 内压法外定径 定型套内径径向尺寸应考虑管材定型后收缩因素、
确定分流器上的角度α,分流锥长度、分流器头部 圆角半径、分流器表面粗糙度、过滤版与分流器顶间隔
巴鲁斯效应和冷却收缩等原因使塑件外径不等 于口模内径 确定口模的内径D方法1: 确定口模的内径D方法2:
D=d/K
I
D2 Ds2
d2 ds2
Page 17
7.3.1 直通式挤出机头工艺参数的确定
1 口模 (2) 定型段长度L1 口模与型棒的平直部分Байду номын сангаас长度成为定型段
第七章 塑料挤出成型工艺及模具设计
7.1挤出成型工艺 主要用于生产具有恒定截面形状的管材、
棒材、板材、片材、线材和薄膜等。
此外,也可用于塑料的着色造粒、 共混、中空塑件型坯的生产。
Page 2
7.1.1 挤出成型原理及特点
挤出成型优点: 连续成型、生产量大、
生产效率高、设备简单
Page 3
成本低、操作方便
7.1.2 挤出成型工艺过程
原材料的准备阶段 塑化阶段 成型阶段 定径阶段 塑件的牵引、卷曲和切割阶段
Page 4
7.1.3 挤出成型工艺参数
温度 压力 挤出速度 牵引速度
Page 5
7.2 挤出成型机头概述
挤出成型的模具成为挤出成型机头
7.2.1 挤出机头的作用及分类 1 挤出机头作用
Page 24
7.3.2 管材的定径和冷却
1 外径定径 外径定径适用于对管材外径尺寸精度要求高、 外表面粗糙度低的情况。 按照压力产生方式不同,外径定径又分为内压法 和真空法。
Page 25
Page 26
Page 27
Page 28
7.3.2 管材的定径和冷却
1 外径定径 (1) 内压法外定径 定型套内径径向尺寸应考虑管材定型后收缩因素、
确定分流器上的角度α,分流锥长度、分流器头部 圆角半径、分流器表面粗糙度、过滤版与分流器顶间隔
塑料成型工艺第六章 挤出成型PPT课件

的物料量或塑件长度。它表示挤出能力的高低。 4.牵引速度
牵引速度与挤出速度相当,可略大于挤出速度。 牵引— 比— 牵引速度与挤出速度的比值,其值 等于或大于1。
§6.3 挤出管材成型工艺
一、挤出管材工艺控制要点
1.温度的控制
挤出成型温度是促使成型物料塑化和塑料熔体流动的 必要条件。对物料的塑化及制品的质量和产量有着十分 重要的影响。
(2)关闭冷却水进水阀、压缩空气机或真空泵、 牵引机等。
(3)拆机头,并清理
一、硬质聚氯乙烯塑料管材
硬质聚氯乙烯塑料简称为PVC-U,也可用UPVC来 1表.原示材。料的选用
硬质聚氯乙烯管材,应选用悬浮聚合的高型 号的树脂,如通常以SG-5型树脂为主要原料, 也可选用SG-6型树脂和SG-4型树脂。
2.压力
a、压力的建立
挤出成型时,沿料筒轴线方向,在物料内部 要建立起不同压力,主要由以下两个方面的因 素造成的:
压缩比的存在:螺槽深度的改变、料筒上的沟 槽深度变化、螺距的改变等。
分流板、滤网和口模产生的阻力。
压力的建立是物料得以经历物理状态变化、得 到均匀密实的熔体、并最后得到成型制品的重 要条件之一。
在各段温度设定应考虑以下几个方面:一是聚 合物本身的性能,如熔点,分子量大小和分布,熔 体指数等。其次考虑设备的性能。有的设备,进料 段的温度对主机电流的影响很大。再次,通过观察 管模头挤出管坯表面是否光滑。有无气泡等现象来 判断。
挤出成型所需控制的温度是机筒温度、机颈温 度、口模温度。
机筒温度分布,从喂料区到模头可能是平坦分布, 递增分布,递减分布及混合分布。主要取决于材 料物点和挤出机的结构。
一、挤出成型基本原理
将熔融的塑料自模具内以挤压的方式往外推出,而 得到与模口相同几何形状的流体,冷却固化后,得到 所要的零件。
牵引速度与挤出速度相当,可略大于挤出速度。 牵引— 比— 牵引速度与挤出速度的比值,其值 等于或大于1。
§6.3 挤出管材成型工艺
一、挤出管材工艺控制要点
1.温度的控制
挤出成型温度是促使成型物料塑化和塑料熔体流动的 必要条件。对物料的塑化及制品的质量和产量有着十分 重要的影响。
(2)关闭冷却水进水阀、压缩空气机或真空泵、 牵引机等。
(3)拆机头,并清理
一、硬质聚氯乙烯塑料管材
硬质聚氯乙烯塑料简称为PVC-U,也可用UPVC来 1表.原示材。料的选用
硬质聚氯乙烯管材,应选用悬浮聚合的高型 号的树脂,如通常以SG-5型树脂为主要原料, 也可选用SG-6型树脂和SG-4型树脂。
2.压力
a、压力的建立
挤出成型时,沿料筒轴线方向,在物料内部 要建立起不同压力,主要由以下两个方面的因 素造成的:
压缩比的存在:螺槽深度的改变、料筒上的沟 槽深度变化、螺距的改变等。
分流板、滤网和口模产生的阻力。
压力的建立是物料得以经历物理状态变化、得 到均匀密实的熔体、并最后得到成型制品的重 要条件之一。
在各段温度设定应考虑以下几个方面:一是聚 合物本身的性能,如熔点,分子量大小和分布,熔 体指数等。其次考虑设备的性能。有的设备,进料 段的温度对主机电流的影响很大。再次,通过观察 管模头挤出管坯表面是否光滑。有无气泡等现象来 判断。
挤出成型所需控制的温度是机筒温度、机颈温 度、口模温度。
机筒温度分布,从喂料区到模头可能是平坦分布, 递增分布,递减分布及混合分布。主要取决于材 料物点和挤出机的结构。
一、挤出成型基本原理
将熔融的塑料自模具内以挤压的方式往外推出,而 得到与模口相同几何形状的流体,冷却固化后,得到 所要的零件。
塑料管材挤出模具设计PPT课件

的尺寸和几何形状。
7.堵塞 防止压缩空气泄漏,保证管内一定的压力
ppt精选版
15
8.1.2挤出成型机头分类及其设计原则 1.分类 由于挤出制品的形状和要求不同,因此要有相 应的机头满足制品的要求,机头种类很多,大致 可按以下三种特征来进行分类:
(l)按机头用途分类 可分为挤管机头、吹管机头、挤板机头等;
1.4~3.0
ABS 1.0~1.1
PP
1.0.~1.2
HDPE 1.1~1.2
LDPE 1.2~1.5
r—口模内径; rl—芯棒外径;
R —管材外径: R1——ppt管精选版材内径。
51
口模定型段长度L1,与塑料性质、管材的形状、 壁厚、直径大小及牵引速度有关。其值可按管
材外径或管材壁厚来确定:
ppt精选版
47
ppt精选版
48
塑料管材挤出模具设计
口模 芯棒 分流锥 模具体 定径套
ppt精选版
49
1)口模 口模是成型管材外表面的零
件,其结构如图所示。
口模内径不等于塑料管材外
径,因为从口模挤出的管坯由
于压力突然降低,塑料因弹性
恢复而发生管径膨胀,同时,管坯在冷却和牵引
作用下,管径会发生缩小。这些膨胀和收缩的大
均匀,生产率高,产品质量好。但结构复杂,制造
困难,生产占地面积较大ppt精。选版 PP PE
29
应用 :医用管材内径定型PVC管成型模具
内径定型管材挤出成型模具结构,多在成型 医用管材中应用。此种塑料管多是透明,内、 外壁光滑的小直径管。模具结构不同于通用塑 料成型模具之处,是设有内径冷却定型装置。 生产时、内径冷却定型装置在管坯内通过,为 挤出模具的管坯冷却降温定型;内径冷却定型 装置的外圆直径与管的内孔直径尺寸相符(或 略大些),内有冷却水通过。
7.堵塞 防止压缩空气泄漏,保证管内一定的压力
ppt精选版
15
8.1.2挤出成型机头分类及其设计原则 1.分类 由于挤出制品的形状和要求不同,因此要有相 应的机头满足制品的要求,机头种类很多,大致 可按以下三种特征来进行分类:
(l)按机头用途分类 可分为挤管机头、吹管机头、挤板机头等;
1.4~3.0
ABS 1.0~1.1
PP
1.0.~1.2
HDPE 1.1~1.2
LDPE 1.2~1.5
r—口模内径; rl—芯棒外径;
R —管材外径: R1——ppt管精选版材内径。
51
口模定型段长度L1,与塑料性质、管材的形状、 壁厚、直径大小及牵引速度有关。其值可按管
材外径或管材壁厚来确定:
ppt精选版
47
ppt精选版
48
塑料管材挤出模具设计
口模 芯棒 分流锥 模具体 定径套
ppt精选版
49
1)口模 口模是成型管材外表面的零
件,其结构如图所示。
口模内径不等于塑料管材外
径,因为从口模挤出的管坯由
于压力突然降低,塑料因弹性
恢复而发生管径膨胀,同时,管坯在冷却和牵引
作用下,管径会发生缩小。这些膨胀和收缩的大
均匀,生产率高,产品质量好。但结构复杂,制造
困难,生产占地面积较大ppt精。选版 PP PE
29
应用 :医用管材内径定型PVC管成型模具
内径定型管材挤出成型模具结构,多在成型 医用管材中应用。此种塑料管多是透明,内、 外壁光滑的小直径管。模具结构不同于通用塑 料成型模具之处,是设有内径冷却定型装置。 生产时、内径冷却定型装置在管坯内通过,为 挤出模具的管坯冷却降温定型;内径冷却定型 装置的外圆直径与管的内孔直径尺寸相符(或 略大些),内有冷却水通过。
- 1、下载文档前请自行甄别文档内容的完整性,平台不提供额外的编辑、内容补充、找答案等附加服务。
- 2、"仅部分预览"的文档,不可在线预览部分如存在完整性等问题,可反馈申请退款(可完整预览的文档不适用该条件!)。
- 3、如文档侵犯您的权益,请联系客服反馈,我们会尽快为您处理(人工客服工作时间:9:00-18:30)。
② 小型机头,分流器和分流器支架可以做成一个整体。
③ 为了消除塑料通过分流器后形成的接合线,分流器支架 上的分流肋应做成流线型,一般3~8根。
熔料通过分流器分流形成管状制品的胚形,并进一步加热 塑化。分流器支架用于支撑分流器和芯棒,同时对分流 后的塑料熔体加强剪切混合作用。
⑥ 定径套
通过冷却定型,使从机头口模挤出的高温塑件已形成 的横截面形状稳定下来,并进行修正。
定 径 套 实 物 图 片
返回
正 在 挤 出 塑 料 管 材
塑 料 管 坯 进 入 定 径 装 置
口模实物图片 返回
芯 棒 实 物 图 片
返回
② 过滤网和过滤板
使从挤出机出来的塑料熔体由旋转流动变为平直流动, 且沿螺杆方向形成挤出压力,增加塑料的塑化均匀度。
③ 机头体 机头的主体,相当于模架,用来组装并支撑机头的各零 件。
④ 连接部分: 机头与挤出机用螺钉及法兰连接
⑤ 分流器和分流器支架
拆 出 的 口 模 状 况
SUCCESS
THANK YOU
2020/3/11
拆 开 口 模 后 露 出 芯 棒 的 状 况
图8.1 挤出机头结构
1-管材 2-定型模 3-口模 4-芯棒 5-调节螺钉 6-分流器 7-分流器支架 8-机头体 9-过滤网 10-电加热圈
3. 挤出机头的设计原则
① 内腔呈流线型
各连接处不应该有使熔料滞留的死角,避免熔料过热而分 解。
② 足够的压缩比
为了使塑件结构密实和消除分流器支架造成的熔料接合缝, 机头应该有一定的压缩比的压缩区域。低粘度塑料压缩比取 4~10,高粘度塑料在2.5~6为宜。
③ 正确的成型区截面形状及尺寸
口模的形状及尺寸和塑件的形状及尺寸并不是一致的。熔 体膨胀和牵引力引起的收缩变形,会使塑件的尺寸与口模尺寸 产生一定的偏差。所以在设计时要考虑这一因素。
1. 直通式挤管机头工艺参数的确定
(1) 口模
① 口模内径D ❖经验公式: D = d /K
d——管材外径 K——补偿系数
❖按拉伸比确定
② 定型段长度L
❖ 按管材外径:L=(0.5~3)d ❖ 按管材壁厚:L=nt
(2) 芯捧(芯模)
芯棒与分流器之间通过螺纹连接,其中心孔用来通入压 缩空气,以便对管材产生内压,实现外径定径。
①芯棒外径d d=D-2δ
δ-口模与芯棒的单边间隙, δ =(0.83~0.94)t 。
②定型长度段L1 与口模定型长度 L 相当或稍长。
③ 压缩段长度L2 压缩段 (也称锥面段) 主要作用是使进入定型区之前的塑
料熔体的分流痕迹被熔合消除。 L2=(1.5~2.5) D0
D0-塑料熔体在过滤板出口处的流道直径
4. 机头与挤出机的关系
机头安装在挤出机的头部
三、管材挤出机机头的设计
常用的挤管机头有:直通式、直角式和旁侧式
直通式挤管机头
1-芯棒 2-口模 3-调节螺钉 4-分流器支架 5-分流器 6-加热器 7机头体
挤出机头结构
1-管材 2-定型模 3-口 模 4-芯棒 5-调节螺钉 6-分流器 7-分流器支架 8-机头体 9-过滤网 10电加热圈
挤出机:挤出系统、传动系统、加热冷却系统、机身
辅机: 机头、定型装置、冷却装置、牵引装置、切割
装置、卷取装置 控制系统
2. 挤出成型工艺过程
原材料准备
塑化
挤出成型
冷却定型
塑件的牵引、 卷曲、切割
挤塑生产线
3. 挤出成型工艺参数
① 温度
❖ 加料段的温度不宜过高,压缩段和均化段的温度可高一些 ❖ 机头的温度控制在塑料热分解温度以下 ❖ 口模的温度比机头温度可稍低一些,但要保证塑料有良
二、挤出成型机头概述
1. 挤出机头的作用 使熔融塑料由螺旋运动变为直线运动; 产生必要的成型压力,保证制品密实; 使塑料通过机头得到进一步塑化; 通过机头口模以获得截面形状相同、连续的塑料制品。
2. 机头的分类
按机头的几何形状分类 圆环机头:管材机头、棒材机头、造粒机头等 平板状机头:平模机头、板材机头、异型材机头等
按机头进出料方向分类 水平直通式机头 直角式机头
按机头的用途分类 吹膜机头、管材机头、板材机头、棒材机头、异型材 机 头等。
3.挤出机头的组成(以直通式管材机头为例)
口模 芯棒 分流器和分流器支架 机头体 过滤网和过滤板 连接部分 定径套
① 口模和芯棒
挤出模的主要成型零件,口模用来成型塑件的外表面, 芯棒用来成型塑件的内表面。通过调节螺钉5,可调节 口模和芯棒之间的间隙,从而控制塑件的壁厚。
好的流动性。
② 压力
合理控制螺杆转速,保证温控系统的精度,以减小压力 波动。
③ 挤出速度
单位时间内由挤出机口模中挤出的塑化好的物料 量(kg/h)或塑件长度(m/min)。它表示挤出能力的高低。
④牵引速度
牵引速度与挤出速度相当,可略大于挤出速度。 即牵引比(牵引速度与挤出速度的比值)等于或大于1。
第7章 塑料挤出成型工 艺及模具设计
一、挤出成型工艺
挤出成型是热塑性塑料重要的加工方法之一,主要用 于生产管材、棒材、板材、片材、线材和薄膜等连续塑料 型材。
1、挤出成型原理
将颗粒状或粉状塑料加入挤出机料筒内,在旋转的挤出机
螺杆的作用下,塑料沿螺杆的螺槽向前方输送。在此过程中, 不断地接受外加热和摩擦热,逐渐熔融成粘流态,然后在挤 压系统的作用下,塑料熔体经过滤板后通过具有一定形状的 挤出模具(机头)口模以及一系列的辅助装置,从而获得等 横截面的各种型材。
④ 压缩角 低粘度塑料45~ 60° ,高粘度塑料30 ~ 50° 。
(3) 分流器和分流器支架 ① 分流器设计需确定的尺寸
❖分流器的角度α
低粘度塑料30°~80°, 高粘度塑料取30°~60°。
❖分流锥长度L3
L3 =(1~1.5) D0
❖分流器头部圆角半径r
取0.5~2mm
② 分流器支架
① 支承分流器及芯棒,另外起搅拌物料的作用。
④机头内设有调节装置
调节熔体流量、口模和芯棒侧隙、挤出压力、成型温度、 挤出速度等用,所以要有足够的强度。 必要时对连接零件进行强度校核。
与熔体接触的零件要有足够的耐磨性和耐腐蚀性,必要时 表面要镀铬处理。主要零件进行调质处理,硬度45~ 50HRC。
挤出成型设备——挤出机
③ 为了消除塑料通过分流器后形成的接合线,分流器支架 上的分流肋应做成流线型,一般3~8根。
熔料通过分流器分流形成管状制品的胚形,并进一步加热 塑化。分流器支架用于支撑分流器和芯棒,同时对分流 后的塑料熔体加强剪切混合作用。
⑥ 定径套
通过冷却定型,使从机头口模挤出的高温塑件已形成 的横截面形状稳定下来,并进行修正。
定 径 套 实 物 图 片
返回
正 在 挤 出 塑 料 管 材
塑 料 管 坯 进 入 定 径 装 置
口模实物图片 返回
芯 棒 实 物 图 片
返回
② 过滤网和过滤板
使从挤出机出来的塑料熔体由旋转流动变为平直流动, 且沿螺杆方向形成挤出压力,增加塑料的塑化均匀度。
③ 机头体 机头的主体,相当于模架,用来组装并支撑机头的各零 件。
④ 连接部分: 机头与挤出机用螺钉及法兰连接
⑤ 分流器和分流器支架
拆 出 的 口 模 状 况
SUCCESS
THANK YOU
2020/3/11
拆 开 口 模 后 露 出 芯 棒 的 状 况
图8.1 挤出机头结构
1-管材 2-定型模 3-口模 4-芯棒 5-调节螺钉 6-分流器 7-分流器支架 8-机头体 9-过滤网 10-电加热圈
3. 挤出机头的设计原则
① 内腔呈流线型
各连接处不应该有使熔料滞留的死角,避免熔料过热而分 解。
② 足够的压缩比
为了使塑件结构密实和消除分流器支架造成的熔料接合缝, 机头应该有一定的压缩比的压缩区域。低粘度塑料压缩比取 4~10,高粘度塑料在2.5~6为宜。
③ 正确的成型区截面形状及尺寸
口模的形状及尺寸和塑件的形状及尺寸并不是一致的。熔 体膨胀和牵引力引起的收缩变形,会使塑件的尺寸与口模尺寸 产生一定的偏差。所以在设计时要考虑这一因素。
1. 直通式挤管机头工艺参数的确定
(1) 口模
① 口模内径D ❖经验公式: D = d /K
d——管材外径 K——补偿系数
❖按拉伸比确定
② 定型段长度L
❖ 按管材外径:L=(0.5~3)d ❖ 按管材壁厚:L=nt
(2) 芯捧(芯模)
芯棒与分流器之间通过螺纹连接,其中心孔用来通入压 缩空气,以便对管材产生内压,实现外径定径。
①芯棒外径d d=D-2δ
δ-口模与芯棒的单边间隙, δ =(0.83~0.94)t 。
②定型长度段L1 与口模定型长度 L 相当或稍长。
③ 压缩段长度L2 压缩段 (也称锥面段) 主要作用是使进入定型区之前的塑
料熔体的分流痕迹被熔合消除。 L2=(1.5~2.5) D0
D0-塑料熔体在过滤板出口处的流道直径
4. 机头与挤出机的关系
机头安装在挤出机的头部
三、管材挤出机机头的设计
常用的挤管机头有:直通式、直角式和旁侧式
直通式挤管机头
1-芯棒 2-口模 3-调节螺钉 4-分流器支架 5-分流器 6-加热器 7机头体
挤出机头结构
1-管材 2-定型模 3-口 模 4-芯棒 5-调节螺钉 6-分流器 7-分流器支架 8-机头体 9-过滤网 10电加热圈
挤出机:挤出系统、传动系统、加热冷却系统、机身
辅机: 机头、定型装置、冷却装置、牵引装置、切割
装置、卷取装置 控制系统
2. 挤出成型工艺过程
原材料准备
塑化
挤出成型
冷却定型
塑件的牵引、 卷曲、切割
挤塑生产线
3. 挤出成型工艺参数
① 温度
❖ 加料段的温度不宜过高,压缩段和均化段的温度可高一些 ❖ 机头的温度控制在塑料热分解温度以下 ❖ 口模的温度比机头温度可稍低一些,但要保证塑料有良
二、挤出成型机头概述
1. 挤出机头的作用 使熔融塑料由螺旋运动变为直线运动; 产生必要的成型压力,保证制品密实; 使塑料通过机头得到进一步塑化; 通过机头口模以获得截面形状相同、连续的塑料制品。
2. 机头的分类
按机头的几何形状分类 圆环机头:管材机头、棒材机头、造粒机头等 平板状机头:平模机头、板材机头、异型材机头等
按机头进出料方向分类 水平直通式机头 直角式机头
按机头的用途分类 吹膜机头、管材机头、板材机头、棒材机头、异型材 机 头等。
3.挤出机头的组成(以直通式管材机头为例)
口模 芯棒 分流器和分流器支架 机头体 过滤网和过滤板 连接部分 定径套
① 口模和芯棒
挤出模的主要成型零件,口模用来成型塑件的外表面, 芯棒用来成型塑件的内表面。通过调节螺钉5,可调节 口模和芯棒之间的间隙,从而控制塑件的壁厚。
好的流动性。
② 压力
合理控制螺杆转速,保证温控系统的精度,以减小压力 波动。
③ 挤出速度
单位时间内由挤出机口模中挤出的塑化好的物料 量(kg/h)或塑件长度(m/min)。它表示挤出能力的高低。
④牵引速度
牵引速度与挤出速度相当,可略大于挤出速度。 即牵引比(牵引速度与挤出速度的比值)等于或大于1。
第7章 塑料挤出成型工 艺及模具设计
一、挤出成型工艺
挤出成型是热塑性塑料重要的加工方法之一,主要用 于生产管材、棒材、板材、片材、线材和薄膜等连续塑料 型材。
1、挤出成型原理
将颗粒状或粉状塑料加入挤出机料筒内,在旋转的挤出机
螺杆的作用下,塑料沿螺杆的螺槽向前方输送。在此过程中, 不断地接受外加热和摩擦热,逐渐熔融成粘流态,然后在挤 压系统的作用下,塑料熔体经过滤板后通过具有一定形状的 挤出模具(机头)口模以及一系列的辅助装置,从而获得等 横截面的各种型材。
④ 压缩角 低粘度塑料45~ 60° ,高粘度塑料30 ~ 50° 。
(3) 分流器和分流器支架 ① 分流器设计需确定的尺寸
❖分流器的角度α
低粘度塑料30°~80°, 高粘度塑料取30°~60°。
❖分流锥长度L3
L3 =(1~1.5) D0
❖分流器头部圆角半径r
取0.5~2mm
② 分流器支架
① 支承分流器及芯棒,另外起搅拌物料的作用。
④机头内设有调节装置
调节熔体流量、口模和芯棒侧隙、挤出压力、成型温度、 挤出速度等用,所以要有足够的强度。 必要时对连接零件进行强度校核。
与熔体接触的零件要有足够的耐磨性和耐腐蚀性,必要时 表面要镀铬处理。主要零件进行调质处理,硬度45~ 50HRC。
挤出成型设备——挤出机