挤出成型工艺及模具设计_课件
拉挤成型原理及其制造工艺PPT课件
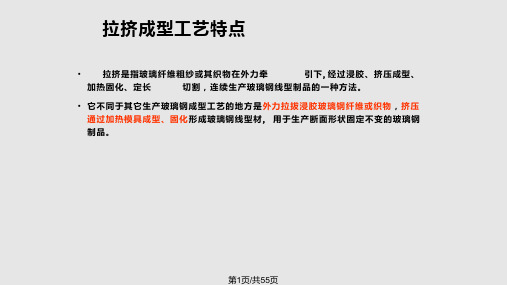
模腔压力
• 模腔压力是由于树脂粘性,制品与模腔壁间的摩擦力,材料受热产 生的体积膨胀,以及部分材料受热气化产生的。因此,模腔压力使制品 在模腔内行为的一个综合反映参数。一般模腔压力在1.7~8.6MPa之 间。
第34页/共55页
(3)张力及牵引力
• 张力是指拉挤过程中玻璃纤维粗纱张紧的力。可 使浸胶后的玻璃纤维粗纱不松散。其大小与胶槽 中的调胶辊到模具的入口之间距离有关,也与拉 挤制品的形状、树脂含量要求有关。一般情况下, 要根据具体制品的几何形状、尺寸,通过实验确引设备是将固化的型材从成型模具拉出的 装置,它要根据拉挤制品种类来选择牵引力 的大小和夹紧方式。牵引机分为液压机械式 和履带式两种。牵引力一般为5O~10OkN。 牵引速度通常采用无级调速,可以根据制品 加工工艺要求而定,通常为0.l~3m/min, 若采用快速固化配方,牵引速度可大幅度提 高。
第37页/共55页
纱团数量
• 根据加工制品的结构以及要求的性能,确定所用纱团的数量和增强材料的品 种以及排布方式。一般的玻璃钢制品的玻璃纤维和织物的含量在40%-60%, 采用合理的增强材料的含量和分布对于成型工艺和制品性能是十分重要的, 要根据拉挤成型的制品要求和工艺条件来确定。
第38页/共55页
第40页/共55页
旋转芯轴,纤维从纱筒外壁引出的,这样可避免 扭转现象。如采用纤维从纱筒内壁引出的,纱筒 固定会使纱发生扭曲不利于玻璃纤维的整齐排布。
第3页/共55页
第4页/共55页
第5页/共55页
(2)树脂浸渍:
• 是将排布整齐的增强纤维均匀浸渍上已配制好的不饱和树脂的过程,一般是 采用将纤维通过装有树脂胶槽时进行的。一般分为:
第7页/共55页
挤出成型工艺与模具结构讲解
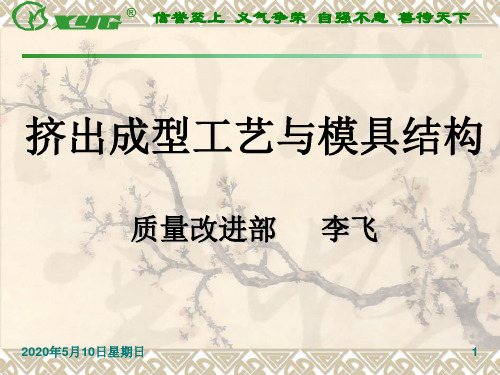
1.加热阶段
经过炼胶处理的胶料原料由挤出机料斗加入料 筒后,在料筒温度和螺杆旋转、压实及混合作用下, 由固态的粒状或粉状转变为具有一定流动性的均匀 熔体。
2019年6月9日星期日
5
® 信誉至上 义气争荣 自强不息 善待天下
挤出成型的工艺过程
2.挤出成型阶段
均匀加热的胶料熔体随螺杆的旋转向料筒前端移动, 在螺杆的旋转挤压作用下,通过一定形状的口模而 获得与口模形状一致的型材。
影响挤出速度的因素有很多,如料筒的结构、 螺杆转速、加热冷却系统的结构和塑料的性能等。 在挤出机结构和胶料品种及胶条类型确定的情况下, 挤出速度与螺杆转速有关,因此调整螺杆转速是控 制挤出速度的主要措施。
2019年6月9日星期日
11
® 信誉至上 义气争荣 自强不息 善待天下
挤出成型工艺参数
4.牵引速度
通过牵引的胶条可根据使用要求在切割装置上 裁剪或在卷取8
® 信誉至上 义气争荣 自强不息 善待天下
挤出成型工艺参数
1.温度
温度是挤出成型中的重要参数之一。严格地说, 挤出成型温度应该是指料筒中的胶料熔体温度,但 是该温度在很大程度上取决于料筒和螺杆的温度, 所以,在实际生产中为了检测方便,经常用料筒温 度近似表示成型温度。
挤出成型胶条的截面形状均取决于挤出模具, 所以,挤出模具设计的合理性,是保证良好的挤出 成型工艺和挤出成型质量的决定因素。
2019年6月9日星期日
13
® 信誉至上 义气争荣 自强不息 善待天下
挤出成型模具的结构组成
1.机头
机头是挤出塑料制件成型的主要部件,它的作 用是将来自挤出机的熔融塑料由螺旋运动转变为直 线运动,并进一步塑化,产生必要的成型压力,保 证塑件密实,从而获得截面与口模形状相似的型材。 下面以典型的管材挤出成型机头为例,介绍机头的 结构组成。
第三章 挤出成型工艺与模具结构
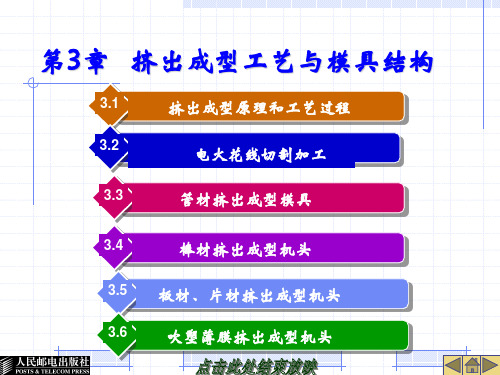
3.机头与挤出机的连接
常用国产挤出机与机头的连接形式如图3-3、 图3-4所示。 在图3-3中,机头以螺纹联接在机头法兰上, 机头法兰以4~6个铰链螺钉与机筒法兰连接固定。 图3-4所示为挤出机与机头的又一种连接形 式。机头以8个内六角螺钉与机头法兰连接固定, 机头法兰与机筒法兰由定位销定位,机头外圆与 机头法兰内孔配合,保证机头与挤出机的同心度。
3.3.3 管材定径套的结构类型及尺寸
管材的定径方法 : 1、外径定型法:(1)内压法 (2) 真空吸附法 。 2、内径定型法
3.4 棒材挤出成型模具
棒材是指截面为圆形的实心塑料型材, 塑料棒材的原材料一般是工程塑料,如尼龙、 聚甲醛、聚碳酸脂、ABS、聚砜、玻璃纤维 增强塑料等。棒材机头的螺杆长径比为2 5~120,除了生产玻璃纤维增强塑料外, 可以设置50~80目的过滤网。
3.1.1 挤出成型原理和特点 1.挤出成型原理
首先将粒状或粉状塑料加入料斗中,在旋转 的挤出机螺杆的作用下,加热的塑料通过沿螺杆 的螺旋槽向前方输送。在此过程中,塑料不断接 受料筒的外加热和螺杆与塑料之间、料筒与塑料 之间的剪切摩擦热,逐渐熔融呈黏流态,然后在 挤压系统的作用下,塑料熔体通过具有一定形状 的挤出模具,从而获得具有一定截面形状的塑料 型材,如图3-1所示。
3.6 吹塑薄膜挤出成型机头
薄膜是目前广泛使用的塑料挤出产品, 薄膜的厚度一般为0.01~0.25mm。薄膜的常 用生产方法是吹塑成型,就是由挤出机机头 挤出塑料管坯,同时从机头中心通入压缩空 气,将管坯吹成所需直径的薄膜。吹塑法可 以加工软、硬聚氯乙烯、聚乙烯、聚丙烯、 聚苯乙烯、聚酰胺等塑料薄膜。
2.挤出成型的特点
(1)连续成型,生产量大,生产率高,成 本低。 (2)塑件截面恒定,形状简单。 (3)塑件内部组织均衡紧密,尺寸比较稳 定准确。 (4)适用性强,除氟塑料以外,几乎能 加工所有热塑性塑料和部分热固性塑料。
挤出工艺简介课件
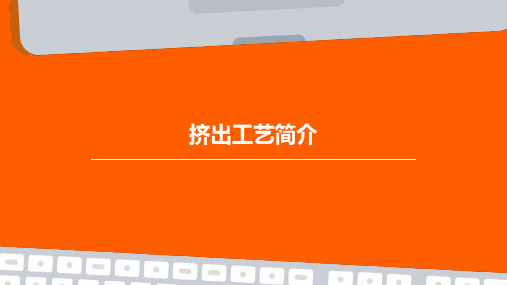
挤出工艺在智能制造领域的应用前景
随着智能制造的不断发展,挤出工艺 在智能制造领域的应用前景越来越广 阔。通过引入智能化技术,可以实现 自动化控制、在线监测、远程维护等 功能,提高生产效率和产品质量。
VS
未来,挤出工艺在智能制造领域的应 用将更加广泛,需要加强技术研发和 产业合作,推动智能制造产业的快速 发展。
压力参数
压力控制
压力是挤出工艺中的另一个关键参数。它影响材料的流 动和塑化效果,以及产品的密度和尺寸精度。压力过低 可能导致塑化不良或产品缺陷;压力过高则可能导致材 料分解或设备损坏。
压力波动
压力波动对产品质量和设备稳定性有很大影响。保持压 力稳定是提高产品质量和延长设备使用寿命的重要措施 。
速度参数
挤出工艺简介
目录
• 挤出工艺概述 • 挤出机的基本结构 • 挤出工艺流程 • 挤出工艺参数 • 挤出工艺的发展趋势与未来展望
01
挤出工艺概述
挤出工艺的定义
挤出工艺是一种塑料加工技术,通过 加热和加压,将塑料原料从挤出机口 模中挤出成连续的型材或管材。
该工艺涉及将塑料原料加入挤出机, 经过加热、熔融、混合、塑化等过程 ,最后通过口模形成所需形状的制品 。
输送速度控制
根据生产需求和设备性能,调整输送 速度,确保原材料能够稳定、均匀地 进入下一道工序。
原材料的加热与塑化
加热方式选择
根据原材料的特性和工艺要求,选择合 适的加热方式,如电热、燃气热、微波 加热等。
VS
塑化效果评估
通过检测塑化后的原材料流动性和外观, 评估塑化效果是否达到工艺要求。
原材料的计量与混合
高分子材料挤出工艺的发展趋势包括提高生产效率、降低能耗、提高制品性能等方面,以满足不断变 化的市场需求。
挤出成型工艺与模具结构

3.3 管材挤出成型模具
管材挤出成型机头是挤出机头的主要类 型之一,应用范围较广,主要用于成型聚乙 烯、聚丙烯、聚碳酸脂、尼龙、软、硬聚氯 乙烯等塑料的圆形管件。管材机头适用的挤 出螺杆长径比(螺杆长度与直径之比)为 15~25,螺杆转速为10~35r/min。
3.3.1 管材挤出机头的结构类型
4.牵引速度
从机头和口模中挤出的成型塑件,在牵 引力作用下将会发生拉伸取向,拉伸取向 程度越高,塑件沿取向方位上的拉伸强度 也越大,但冷却后长度收缩也大。通常, 牵引速度可与挤出速度相当,两者的比值 称为牵引比,一般应略大于1。
3.2 挤出成型模具概述
挤出成型塑件的截面形状均取决于挤出 模具,所以,挤出模具设计的合理性,是保 证良好的挤出成型工艺和挤出成型质量的决 定因素。
冷却一般采用空气冷却或水冷却,冷却 速度对塑件性能有很大影响。
4.塑件的牵引、切割和卷取
塑件从口模挤出后,一般会因压力的解除而 发生膨胀现象,而冷却后又会产生收缩现象,使 塑件的形状和尺寸发生改变。如果不加以引导, 就会造成塑件停滞,使塑件不能顺利挤出。因此, 在冷却的同时,要连续均匀地将塑件引出,这就 是牵引。
3.3.3 管材定径套的结构类型及尺寸
管材的定径方法 : 1、外径定型法:(1)内压法 (2) 真空吸附法 。 2、内径定型法
3.4 棒材挤出成型模具
棒材是指截面为圆形的实心塑料型材, 塑料棒材的原材料一般是工程塑料,如尼龙、 聚甲醛、聚碳酸脂、ABS、聚砜、玻璃纤维 增强塑料等。棒材机头的螺杆长径比为2 5~120,除了生产玻璃纤维增强塑料外, 可以设置50~80目的过滤网。
3.棒材定径套的结构
棒材的定径装置结构比较简单,与管材的定 径装置相似,如图3-14所示。定径套的作用是 使塑件不会因为自重而产生变形,保证一定的表 面质量。为了减少棒材通过定径套时的流动阻力, 定径套内孔应具有一定的锥度,锥度为1:35。
挤出成型工艺及模具设计

湿法挤出一般采用柱塞式挤出机,材料 的塑化是借助溶剂使其变为可流动态的。
根据挤出时加压方式的不同,可分为 连续式和间歇式两种。 (1)连续式挤出采用螺杆式挤出机,加压是
通过螺杆进行的。 (2)间歇式挤出采用柱塞式挤出机进行,借
道表面粗糙度Ra值应小于16~32μm。
(4) 机头内应有分流装置和适当的压缩区 机头内应设置分流器和分流器支架等
一类分流装置,如图4-4所示。 另外,机头中设计一段压缩区域,以
增大熔体的流动阻力,消除熔接痕。
(5) 机头成型区应有正确的截面形状 设计机头成型区时,应尽量减小离模
膨胀效应和收缩效应的影响。 设计机头时: 第一:要对口模进行适当的形状和尺寸补
其优点为:生产率高; 定径精度高; 料流稳定均匀; 成型质量也较高; 熔体的流动阻力较小;
缺点为:
3. 旁侧式挤管机头与直角式相似,如
图4.7所示,其结构更为复杂,熔体流动阻
图4.7 旁侧式机头
1、8、10、12 测 温孔; 2 口模; 3 型芯; 4、7 外加热圈; 5 调节螺钉; 6 机头体; 9 连接体; 11 内加热圈
第4章 挤出成型工艺及模具设计
4.1 挤出成型原理及其工艺特性 4.2 挤出成型模具概述 4.3 管材挤出成型模具 4.4 棒材挤出成型机头 4.5 板材、片材挤出成型机头 4.6 异型材挤出成型模具
4.1 挤出成型原理及其工艺特性
4.1.1 挤出成型原理及其特点 4.1.2 挤出成型工艺过程 4.1.3 挤出成型工艺参数
b.挤出成型 将挤出机预热到规定温度后,启动电
机带动螺杆旋转输送物料,同时向料筒中 加入塑料。
挤出成型工艺及模具设计课件
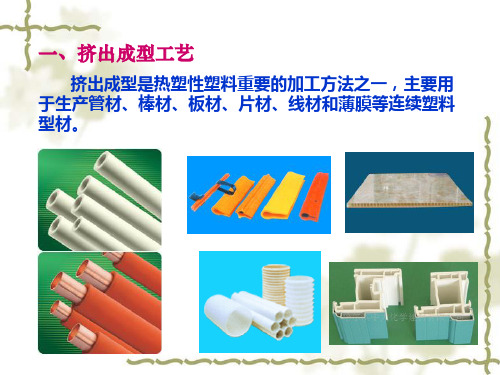
• 直通式挤管机头工艺参数的确定
• (1) 口模
① 口模内径D ❖经验公式: D = d /K
d——管材外径 K——补偿系数
❖按拉伸比确定
② 定型段长度L
❖ 按管材外径:L=(0.5~3)d ❖ 按管材壁厚:L=nt
(2) 芯捧(芯模)
芯棒与分流器之间通过螺纹连接,其中心孔用来通入压 缩空气,以便对管材产生内压,实现外径定径。
适用:内径尺寸要求准确、圆度要求高的情况。
1-管材 2-定径芯模 3-芯棒 4-回水流道 5-进水管 6-排水管 7-进水嘴
定径芯长度:与管材壁厚及牵引速度有关,一般取80~ 300mm,牵引速度和壁厚大时,取大值。反之,取小值。
定径芯直径:一般比管材内径直径大2%~4%,始端比终端 直径大,锥度为0.6:100~1.0:100。
面,芯棒用来成型塑件的内表面。通过调节螺钉5,可
调节口模和芯棒之间的间隙,从而控制塑件的壁厚。
口模实物图片 返回
芯 棒 实 物 图 片
返回
过滤网和过滤板
使从挤出机出来的塑料熔体由旋转流动变为平直流 动,且沿螺杆方向形成挤出压力,增加塑料的塑化均匀 度。
机头体 机头的主体,相当于模架,用来组装并支撑机头的
挤出机:挤出系统、传动系统、加热冷却系统、机身
辅机: 机头、定型装置、冷却装置、牵引装置、切割
装置、卷取装置 控制系统
2. 挤出成型工艺过程
原材料准备
塑化
挤出成型
冷却定型
塑件的牵引、 卷曲、切割
挤塑生产线
3. 挤出成型工艺参数
• 温度
❖ 加料段的温度不宜过高,压缩段和均化段的温度可高一些 ❖ 机头的温度控制在塑料热分解温度以下 ❖ 口模的温度比机头温度可稍低一些,但要保证塑料有良
《挤出成型技术》课件
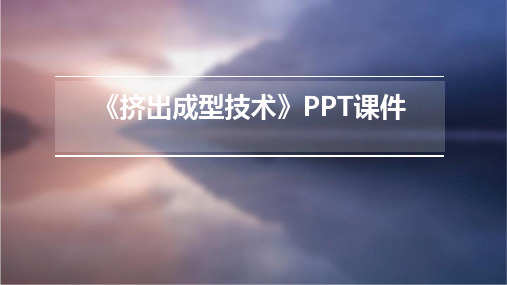
根据制品形状和尺寸进行结构设计,确保制品成型质量、提高生产 效率。
冷却系统
设计合理的冷却系统,控制模具温度,减小制品成型后的收缩率。
挤出成型设备的操作与维护
01
操作规程
制定严格的设备操作规程,确保 操作人员熟悉设备性能和安全操 作要求。
维护保养
02
03
故障排除
定期对设备进行维护保养,检查 各部件磨损情况,及时更换易损 件。
高分子材料在挤出成型技术中的优势在于其可塑性强、加工温度低、成型周期短 等,使得制品具有轻量化、高强度、耐腐蚀等优良性能。同时,高分子材料在挤 出成型过程中易于实现自动化和智能化生产,提高了生产效率和产品质量。
新型挤出成型技术的研发与推广
随着科技的不断发展,新型挤出成型技术不断涌现,如微孔塑料挤出技术、异型截面管材挤出技术、 反应挤出技术等。这些新型技术的研发和应用,极大地丰富了挤出成型制品的种类和性能,满足了不 同领域的需求。
挤出成型技术的应用领域
挤出成型技术广泛应用于塑料加工行业,如管材、型材、薄膜、板材等产品的生产 。
除了塑料加工行业,挤出成型技术还应用于橡胶、陶瓷、玻璃纤维等材料的加工。
随着科技的发展,挤出成型技术的应用领域不断扩大,如3D打印技术的出现,使得 挤出成型技术也可以用于制造个性化的定制产品。
02
挤出成型设备
挤出成型工艺的控制要素
温度控制
温度是挤出成型工艺的重要控制要素之一,包括 机筒温度、模具温度等。温度的控制直接影响着 塑料的塑化和产品质量。
速度控制
速度控制包括挤出速度、注射速度等,它影响着 产品的产量和质量。合理地调整速度参数,可以 提高生产效率和产品质量。
压力控制
压力也是挤出成型工艺的重要控制要素之一,包 括挤出压力、注射压力等。压力的控制对于塑料 的流动性和产品的致密性至关重要。
塑料成型工艺第六章 挤出成型

c、物料全部熔融,变为粘流融的物料量逐渐减少,大约在压 缩段的结束处,全部物料熔融而转变为粘流态, 但这时各点的温度尚不很均匀。
3)均化段——均化、挤出 物料经过均化段的均化作用就比较均匀 了,最后螺杆将熔融物料定量、定压、定温地 挤入机头。 机头内的口模是个成型部件,物料通过它 便获得一定截面的几何形状和尺寸。
固体输送区:固体状态 熔融区:两相共存 熔体输送区:全部为熔体 这几个区不一定完全和前面介绍过的螺杆 的加料段,压缩段,均化段相一致。
3.塑件的定型与冷却阶段
管材的定径方法:定径套、定径环、定径板
4.塑件的牵引、卷取和切割
在冷却得同时,连续均匀地将塑件引出。
牵引速度略大于挤出速度 不同的塑件,牵引速度不同。
挤出成型所需控制的温度是机筒温度、机颈 温度、口模温度。 机筒温度分布,从喂料区到模头可能是平坦分 布,递增分布,递减分布及混合分布。主要取决 于材料物点和挤出机的结构。
表6-2
常见管材成型温度(单位:℃)
口模设臵温度,口模和芯模的温度对管子表
面光洁度有影响,在一定的范围内,口模与芯
模温度高,管子表面光洁度高。通常来讲,口
3.混合效果差,不能很好适应一些特殊塑料的加 工或混炼、着色工艺过程。
排气式螺杆 主要适用于含水和易产生挥发组分的物料。 排气原理:物料到排气段基本塑化,由于该段 螺槽突然加深,压力骤降,气体从熔体中逸处, 从排气口排出。
分离型(屏障型)螺杆 原理:在螺杆熔融段再附加一条螺纹,将原来 一个螺纹所形成的螺槽分为两个,将已熔物料和 未熔物料尽早分离,促进未熔料尽快熔融。
加热冷却系统;
螺杆转数;
螺杆和料筒的结构
研究挤出过程的压力轮廓曲线对挤出过程的了解 和改进螺杆、料筒的设计有着重要意义。
第6章挤出成型工艺

第六章挤出成型工艺第一节热塑性塑料工艺特性(一)收缩率热塑性塑料加工成型中产生的热收缩产生原因:宏观:材料的热胀冷缩行为-微观:分子间自由体积发生变化。
通常高分子材料的热膨胀系数远大于金属材料、陶瓷材料。
影响热塑性塑料成形收缩的因素如下:第六章挤出成型工艺第六章挤出成型工艺1、塑料品种热塑性塑料成形过程中由于还存在结晶化形起的体积变化,内应力强,冻结在塑件内的残余应力大,分子取向性强等因素,因此与热固性塑料相比则收缩率较大,收缩率范围宽、方向性明显。
另外成形后的收缩、退火或调湿处理后的收缩一般也都比热固性塑料大。
第六章挤出成型工艺2、塑件特性成形时融料与型腔表面接触外层立即冷却形成低密度的固态外壳。
由于塑料的导热性差,使塑件内层缓慢冷却而形成收缩大的高密度固态层。
所以壁厚、冷却慢、高密度层厚的则收缩大。
另外,有无嵌件及嵌件布局,数量都直接影响物料流动方向,密度分布及收缩阻力大小等,所以塑件的特性对收缩大小,方向性影响较大。
第六章挤出成型工艺3、进料口形式、尺寸、分布这些因素直接影响物料流动方向、密度分布、及成形时间。
直接进料口、进料口截面大(尤其截面较厚的)则收缩小但方向性大,进料口宽及长度短的则方向性小。
距进料口近的或与物料流动方向平行的则收缩大。
4、成形条件模具温度高,融料冷却慢、密度高、收缩大,尤其对结晶料则因结晶度高,体积变化大,故收缩更大。
另外,保持压力及时间对收缩也影响较大,压力大、时间长的则收缩小但方向性大。
第六章挤出成型工艺(二)流动性1、热塑性塑料流动性大小,一般可从分子量大小、熔融指数、表现粘度及流动比(流程长度/塑件壁厚)等一系列指数进行分析。
分子量小,分子量分布宽,分子结构规整性差,熔融指数高、表现粘度小;流动比大的则流动性就好。
按模具设计要求我们大致可将常用塑料的流动性分为三类:第六章挤出成型工艺(1)流动性好:尼龙、聚乙烯、聚苯乙烯、聚丙烯、醋酸纤维素;(2)流动性中等改性:聚苯乙烯(例ABS·AS)、PMMA、聚甲醛、聚氯醚;(3)流动性差:聚碳酸酯、硬聚氯乙烯、聚苯醚、聚砜、聚芳砜、氟塑料。
铝挤成型工艺介绍PPT课件

26
三、铝挤型散热片制作流程
原材料(铝锭)
经铝锭炉加热(450-500度)
加热后自动送至成型
自动送至成型
自动送至挤压成型
挤压后产品为长条型
27
切成散热片图面尺寸
自动进刀送料
CNC加工
热处理加工(时效炉)
散热片整平 切槽加工
染色(镀色)
29
抛光打磨 攻牙
钻孔
铆PIN成成品
30
工艺图
31
四、铝挤型材设计及模具知识了解
铝挤型设计注意事项:
<1>公差制定要充分考虑厂商制作能力,因铝挤型是在热压状况下成型出模的,产品 的公差相对胶件,五金件要大。 <2>材料厚度最不宜太薄﹐原则上以0.8mm以上﹐变形量较少,挤型状况较佳,有量 产性。 <3>空心管料厚差别不能太大,一般不大于4倍,否则模具较难修整及挤压。 <4>正式开模前,须提供详尽的表面工艺效果,因表面处理工艺影响前期挤型模合模 线的确定,影响挤型模,五金冲模模具尺寸的取值(喷油会使产品孔径变小,外形 变大,内腔变窄,而氧化则相反;喷砂则可造成产品孔径变大,本体薄,或者导致 产品变形;拉丝工艺则要考虑材料留出余量) <5>挤型材料做不到绝对的尖角,设计上的尖角棱线铝型材会有0.3左右的R角,经后 续的抛光,氧化,喷油等工艺,R角会达到0.4左右。 <6>铝挤型之空心与实心部位比例不得过于悬殊﹐或偏移过大,具体依实际结构而定。
挤出成型
12
空心模的构造
1.公模各部功能解说:
挤出成型工艺及模具设计

2020/3/31
2020/3/31
三、管材挤出机机头的设计
常用的挤管机头有:直通式、直角式和旁侧式
直通式挤管机头
1-芯棒 2-口模 3-调节螺钉 4-分流器支架 5-分流器 6-加热器 7机头体
2020/3/31
2020/3/31
2020/3/31
挤出机头结构
1-管材 2-定型模 3-口 模 4-芯棒 5-调节螺钉 6-分流器 7-分流器支架 8-机头体 9-过滤网 10电加热圈
④ 压缩角 低粘度塑料45~ 60° ,高粘度塑料30 ~ 50° 。
2020/3/31
(3) 分流器和分流器支架 ① 分流器设计需确定的尺寸
❖分流器的角度α
低粘度塑料30°~80°, 高粘度塑料取30°~60°。
❖分流锥长度L3
L3 =(1~1.5) D0
❖分流器头部圆角半径r
取0.5~2mm
2020/3/31
② 分流器支架
① 支承分流器及芯棒,另外起搅拌物料的作用。 ② 小型机头,分流器和分流器支架可以做成一个整体。 ③ 为了消除塑料通过分流器后形成的接合线,分流器支架
上的分流肋应做成流线型,一般3~8根。 ④ 分流器支架设有进气孔和导线孔,用以通入压缩空气和
内装置电热器时导入导线。
2020/3/31
2020/3/31
④机头内设有调节装置
调节熔体流量、口模和芯棒侧隙、挤出压力、成型温度、 挤出速度等。
⑤合理选择材料
机头的零件要承受熔体的压力作用,所以要有足够的强度 。必要时对连接零件进行强度校核。
与熔体接触的零件要有足够的耐磨性和耐腐蚀性,必要时 表面要镀铬处理。主要零件进行调质处理,硬度45~ 50HRC。
挤出成型原理及工艺
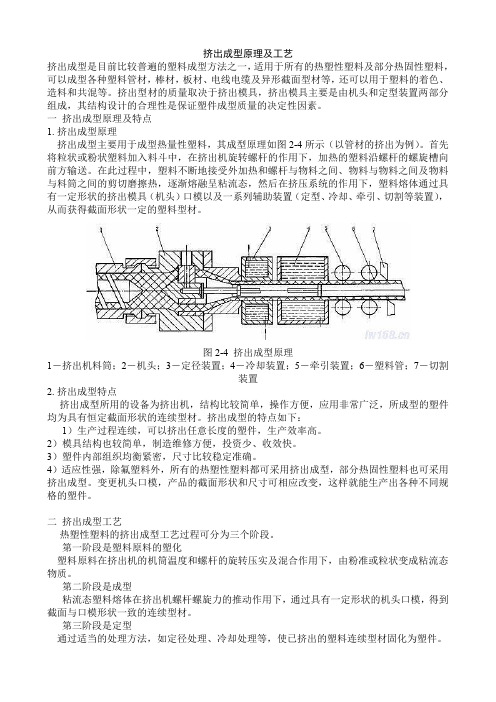
挤出成型原理及工艺挤出成型是目前比较普遍的塑料成型方法之一,适用于所有的热塑性塑料及部分热固性塑料,可以成型各种塑料管材,棒材,板材、电线电缆及异形截面型材等,还可以用于塑料的着色、造料和共混等。
挤出型材的质量取决于挤出模具,挤出模具主要是由机头和定型装置两部分组成,其结构设计的合理性是保证塑件成型质量的决定性因素。
一挤出成型原理及特点1.挤出成型原理挤出成型主要用于成型热量性塑料,其成型原理如图2-4所示(以管材的挤出为例)。
首先将粒状或粉状塑料加入料斗中,在挤出机旋转螺杆的作用下,加热的塑料沿螺杆的螺旋槽向前方输送。
在此过程中,塑料不断地接受外加热和螺杆与物料之间、物料与物料之间及物料与料筒之间的剪切磨擦热,逐渐熔融呈粘流态,然后在挤压系统的作用下,塑料熔体通过具有一定形状的挤出模具(机头)口模以及一系列辅助装置(定型、冷却、牵引、切割等装置),从而获得截面形状一定的塑料型材。
图2-4挤出成型原理1-挤出机料筒;2-机头;3-定径装置;4-冷却装置;5-牵引装置;6-塑料管;7-切割装置2.挤出成型特点挤出成型所用的设备为挤出机,结构比较简单,操作方便,应用非常广泛,所成型的塑件均为具有恒定截面形状的连续型材。
挤出成型的特点如下:1)生产过程连续,可以挤出任意长度的塑件,生产效率高。
2)模具结构也较简单,制造维修方便,投资少、收效快。
3)塑件内部组织均衡紧密,尺寸比较稳定准确。
4)适应性强,除氟塑料外,所有的热塑性塑料都可采用挤出成型,部分热固性塑料也可采用挤出成型。
变更机头口模,产品的截面形状和尺寸可相应改变,这样就能生产出各种不同规格的塑件。
二挤出成型工艺热塑性塑料的挤出成型工艺过程可分为三个阶段。
第一阶段是塑料原料的塑化塑料原料在挤出机的机筒温度和螺杆的旋转压实及混合作用下,由粉准或粒状变成粘流态物质。
第二阶段是成型粘流态塑料熔体在挤出机螺杆螺旋力的推动作用下,通过具有一定形状的机头口模,得到截面与口模形状一致的连续型材。
注塑工艺与模具设计PPT课件

模具设计
注塑模具设计思路 本钱设计:模具材料本钱,成型产品本钱,标准件使用本钱等。 模具维护设计:维修配件结构、备用配件、可拆装性配件、复原性能;
模具设计
30%加工
切割加工、热处理、 放电、慢走 丝、氧化性、 组装等
35%销售管 理试模杂费
20%设计费
15%材料费
模具制作费用
破损与修理费用
注塑工艺根底
流动性快
进料点
先冷却, 流动 性慢
模具冷料 井
注塑工艺根底
压力如何影响产品结构及外观 压力会使分子紧靠在一起,收缩性变小,密度变小; 压力缺乏会导致产品不饱模/缩水,会限制注射速度控制系统提供快速射
出的能力; 压力过大会导致产品毛边/批峰/冲胶。
注塑工艺根底
结晶结构 • 模具温度越高,结晶时间越长,结晶体越大,收缩越大,不均匀结晶
〔产品胶料用量〕压力过小,机器喷嘴与模具未对准。可根据实际情 况调试相关参数进行改善。
现场问题
毛边、批峰 • 塑胶熔体流入分模面或镶件合面将产生毛边批峰。 • 熔体的粘度、压力和间隙的宽度决定是否出现毛边。绝大多数胶料来
说,在的间隙一般都不会产生毛边。熔体尽量进入,但立刻凝固,堵 住流动。
现场问题
注塑马 达
注塑成型工艺根底—设备介绍
上段温 度
调整
中段温 度
度调整
下段温 度
度调整
工作台
冷却水循环 器
开模高度 设定钮
慢速关模 设定阀
高压关模 设定阀
射胶时 间
调整
松退时 间
调整
冷却时 间
调整
注塑成型工艺根底—设备介绍
射出速 度调整
背压调 整阀
- 1、下载文档前请自行甄别文档内容的完整性,平台不提供额外的编辑、内容补充、找答案等附加服务。
- 2、"仅部分预览"的文档,不可在线预览部分如存在完整性等问题,可反馈申请退款(可完整预览的文档不适用该条件!)。
- 3、如文档侵犯您的权益,请联系客服反馈,我们会尽快为您处理(人工客服工作时间:9:00-18:30)。
二、挤出成型机头概述
1. 挤出机头的作用 使熔融塑料由螺旋运动变为直线运动; 产生必要的成型压力,保证制品密实; 使塑料通过机头得到进一步塑化; 通过机头口模以获得截面形状相同、连续的塑料制品。
10
2. 机头的分类
按机头的几何形状分类 圆环机头:管材机头、棒材机头、造粒机头等 平板状机头:平模机头、板材机头、异型材机头等
内装置电热器时导入导线。
38
2. 管材的定径和冷却
为了使管材获得较低的表面粗糙值、准确的尺寸和几何 形状,管材离开口模时,必须立即进行定径和冷却,由定 径套来完成。
有两种方法: ❖ 外径定型 ❖ 内径定型
我国塑料管材标 准大多规定外径为基 本尺寸,故国内较常 用外径定型法。
39
(1)外径定型 适用于管材外径尺寸精度要求高、外表面粗糙度要求低的
按机头进出料方向分类 水平直通式机头 直角式机头
按机头的用途分类 吹膜机头、管材机头、板材机头、棒材机头、异型材 机 头等。
11
3.挤出机头的组成(以直通式管材机头为例)
口模 芯棒 分流器和分流器支架 机头体 过滤网和过滤板 连接部分 定径套
12
① 口模和芯棒 ② 挤出模的主要成型零件,口模用来成型塑件的外表
41
(2)内径定型
通过定径套内的循环水冷却定型 特点:保证管材内孔圆度,操作方便;宜用于直角式挤管机头
和旁侧式挤管机头。
适用:内径尺寸要求准确、圆度要求高的情况。
1-管材 2-定径芯模 3-芯棒 4-回水流道
5-进水管 6-排水管 7-进水嘴
42
定径芯长度:与管材壁厚及牵引速度有关,一般取80~ 300mm,牵引速度和壁厚大时,取大值。反之,取小值。 定径芯直径:一般比管材内径直径大2%~4%,始端比终端 直径大,锥度为0.6:100~1.0:100。
19
定 径 套 实 物 图 片
返回
20
正 在 挤 出 塑 料 管 材
21
塑 料 管 坯 进 入 定 径 装 置
22
拆 出 的 口 模 状 况
23
拆 开 口 模 后 露 出 芯 棒 的 状 况
24ቤተ መጻሕፍቲ ባይዱ
图8.1 挤出机头结构
1-管材 2-定型模 3-口模 4-芯棒 5-调节螺钉 6-分流器
25
7-分流器支架 8-机头体 9-过滤网 10-电加热圈
3. 挤出机头的设计原则
① 内腔呈流线型
各连接处不应该有使熔料滞留的死角,避免熔料过热而分 解。
② 足够的压缩比
为了使塑件结构密实和消除分流器支架造成的熔料接合缝, 机头应该有一定的压缩比的压缩区域。低粘度塑料压缩比取 4~10,高粘度塑料在2.5~6为宜。
③ 正确的成型区截面形状及尺寸
口模的形状及尺寸和塑件的形状及尺寸并不是一致的。熔 体膨胀和牵引力引起的收缩变形,会使塑件的尺寸与口模尺寸 产生一定的偏差。所以在设计时要考虑这一因素。
大家好
1
第7章 塑料挤出成型工 艺及模具设计
2
一、挤出成型工艺
挤出成型是热塑性塑料重要的加工方法之一,主要用 于生产管材、棒材、板材、片材、线材和薄膜等连续塑料 型材。
3
1、挤出成型原理
将颗粒状或粉状塑料加入挤出机料筒内,在旋转的挤出机 螺杆的作用下,塑料沿螺杆的螺槽向前方输送。在此过程中, 不断地接受外加热和摩擦热,逐渐熔融成粘流态,然后在挤 压系统的作用下,塑料熔体经过滤板后通过具有一定形状的 挤出模具(机头)口模以及一系列的辅助装置,从而获得等 横截面的各种型材。
好的流动性。
② 压力
合理控制螺杆转速,保证温控系统的精度,以减小压力 波动。
8
③ 挤出速度
单位时间内由挤出机口模中挤出的塑化好的物料 量(kg/h)或塑件长度(m/min)。它表示挤出能力的高低。
④牵引速度
牵引速度与挤出速度相当,可略大于挤出速度。 即牵引比(牵引速度与挤出速度的比值)等于或大于1。
27
挤出成型设备——挤出机
28
4. 机头与挤出机的关系
机头安装在挤出机的头部
29
三、管材挤出机机头的设计
常用的挤管机头有:直通式、直角式和旁侧式
直通式挤管机头
1-芯棒 2-口模 3-调节螺钉 4-分流器支架 5-分流器 6-加热器 7机头体
30
31
32
挤出机头结构
1-管材 2-定型模 3-口
43
情况。按压力生产方式不同有内压法定径和真空法定径。
① 内压法定径 在管材内部通入压缩空气
1-芯棒, 2-口模, 3-定径套
40
②真空法定径 在定径套内壁加工很多小孔,抽真空 定径套与口模不能联接在一起,应有20 ~ 100mm的距离。 定径套直径:比机头出口直径大2%~4%,出口直径比进 口直径略小。 定径套长度:一般比其他类型定径套大。
26
④机头内设有调节装置
调节熔体流量、口模和芯棒侧隙、挤出压力、成型温度、 挤出速度等。
⑤合理选择材料
机头的零件要承受熔体的压力作用,所以要有足够的强度。 必要时对连接零件进行强度校核。
与熔体接触的零件要有足够的耐磨性和耐腐蚀性,必要时 表面要镀铬处理。主要零件进行调质处理,硬度45~ 50HRC。
塑料熔体的分流痕迹被熔合消除。
L2=(1.5~2.5) D0
D0-塑料熔体在过滤板出口处的流道直径
④ 压缩角 低粘度塑料45~ 60° ,高粘度塑料30 ~ 50° 。
36
(3) 分流器和分流器支架 ① 分流器设计需确定的尺寸
❖分流器的角度α
低粘度塑料30°~80°, 高粘度塑料取30°~60°。
各零件。 ④ 连接部分:
机头与挤出机用螺钉及法兰连接
17
⑤ 分流器和分流器支架 ⑥ 熔料通过分流器分流形成管状制品的胚形,并进一步
加热塑化。分流器支架用于支撑分流器和芯棒,同时对 分流后的塑料熔体加强剪切混合作用。
18
⑥ 定径套 ⑦ 通过冷却定型,使从机头口模挤出的高温塑件已
形成的横截面形状稳定下来,并进行修正。
34
(2) 芯捧(芯模)
芯棒与分流器之间通过螺纹连接,其中心孔用来通入压 缩空气,以便对管材产生内压,实现外径定径。 ①芯棒外径d
d=D-2δ
δ-口模与芯棒的单边间隙, δ =(0.83~0.94)t 。
②定型长度段L1 与口模定型长度 L 相当或稍长。
35
③ 压缩段长度L2
④
压缩段 (也称锥面段) 主要作用是使进入定型区之前的
模 4-芯棒 5-调节螺钉
6-分流器 7-分流器支架
8-机头体 9-过滤网 10-
33
电加热圈
1. 直通式挤管机头工艺参数的确定
2. (1) 口模
① 口模内径D ❖经验公式: D = d /K
d——管材外径 K——补偿系数
❖按拉伸比确定
② 定型段长度L
❖ 按管材外径:L=(0.5~3)d ❖ 按管材壁厚:L=nt
❖分流锥长度L3
L3 =(1~1.5) D0
❖分流器头部圆角半径r
取0.5~2mm
37
② 分流器支架
① 支承分流器及芯棒,另外起搅拌物料的作用。 ② 小型机头,分流器和分流器支架可以做成一个整体。 ③ 为了消除塑料通过分流器后形成的接合线,分流器支架
上的分流肋应做成流线型,一般3~8根。 ④ 分流器支架设有进气孔和导线孔,用以通入压缩空气和
4
挤出机:挤出系统、传动系统、加热冷却系统、机身 辅机: 机头、定型装置、冷却装置、牵引装置、切割
装置、卷取装置 控制系统
5
2. 挤出成型工艺过程
原材料准备
塑化
挤出成型
冷却定型
塑件的牵引、 卷曲、切割
6
挤塑生产线
7
3. 挤出成型工艺参数
① 温度
❖ 加料段的温度不宜过高,压缩段和均化段的温度可高一些 ❖ 机头的温度控制在塑料热分解温度以下 ❖ 口模的温度比机头温度可稍低一些,但要保证塑料有良
面,芯棒用来成型塑件的内表面。通过调节螺钉5,可 调节口模和芯棒之间的间隙,从而控制塑件的壁厚。
13
口模实物图片
返回
14
芯 棒 实 物 图 片
返回
15
② 过滤网和过滤板 ③ 使从挤出机出来的塑料熔体由旋转流动变为平直流
动,且沿螺杆方向形成挤出压力,增加塑料的塑化均匀 度。
16
③ 机头体 ④ 机头的主体,相当于模架,用来组装并支撑机头的