微细电火花加工专业技术与发展趋势势
2024年电火花加工机床市场前景分析

2024年电火花加工机床市场前景分析引言电火花加工机床是一种高精度的加工设备,广泛应用于模具制造、航空航天、汽车制造等领域。
本文将对电火花加工机床市场的前景进行分析。
1. 市场规模据统计数据显示,电火花加工机床市场在过去几年保持了稳定的增长。
预计到未来几年,市场规模将继续扩大。
这主要受以下几个因素的影响:•需求增加:随着制造业的发展,对高精度加工的需求不断增加。
电火花加工机床作为高精度加工的关键设备,市场需求将随之增加。
•技术进步:电火花加工机床的技术不断提升,加工效率和加工精度大幅提高。
这促使更多企业选择使用电火花加工机床,推动市场规模增长。
2. 市场竞争电火花加工机床市场存在较多的竞争对手。
主要竞争因素包括技术水平、产品质量、售后服务等。
目前,市场上的主要竞争企业有:•瑞士AGIECHARMILLES:作为市场领导者,该企业拥有先进的技术和稳定的产品质量。
其广泛的市场份额使其能够在竞争中保持优势地位。
•德国海德堡:海德堡以其高品质的产品享有良好的声誉,并且在售后服务方面表现出色。
•日本精工:精工在电火花加工机床领域拥有丰富的经验,并且不断进行技术创新,推动市场竞争。
当前,上述企业竞争激烈,市场份额分布不均。
未来,随着市场需求的增加,竞争将进一步加剧。
3. 市场驱动力电火花加工机床市场的发展受到多个驱动力的推动:•制造业升级:随着制造业的升级,对高精度加工的需求越来越高。
电火花加工机床作为关键设备,市场需求将随之增加。
•技术创新:电火花加工机床技术的不断创新,推动市场发展。
新的技术将提升加工精度、提高效率,满足用户的需求,进一步推动市场增长。
•政府支持:政府对于高精度加工设备的扶持政策也是市场发展的重要驱动力。
政府通过提供资金支持、税收优惠等方式,鼓励企业购买先进的电火花加工机床,促进市场增长。
4. 市场挑战电火花加工机床市场面临一些挑战,如下:•价格竞争:市场竞争激烈,价格是企业争夺市场份额的主要手段之一。
电火花成形加工技术的研究现状和发展趋势

电火花成形加工技术的研究现状和发展趋势电火花成形加工技术是一种利用电火花在工件表面放电形成微小孔洞的加工方法,广泛应用于制造业的精密加工领域。
本文将对电火花成形加工技术的研究现状和发展趋势进行分析。
电火花成形加工技术最早于19世纪末提出,并在20世纪50年代进行了实践应用。
随着电气放电技术的不断发展,此技术得以推动,并在精密模具、航空航天零部件、汽车制造和生物医疗器械等领域得到广泛应用。
电火花成形加工技术的研究现状主要集中在以下几个方面:第一,放电参数研究。
通过调整电压、电流、脉冲宽度和频率等参数,可以控制电火花放电的能量和形态,从而实现对工件表面的精细加工。
研究者通过实验和仿真等方法,探索最优的放电参数组合,以提高加工效率和加工质量。
第二,电极材料研究。
电极是电火花成形加工中的重要组成部分,其材料的选择直接影响到放电效果和加工质量。
研究者通过对不同材料的电极进行比较试验,确定最适合不同工件材料和加工需求的电极材料,并研究其表面处理技术,以提高耐磨性和放电稳定性。
第三,放电脉冲控制技术研究。
电火花成形加工中,放电脉冲的控制对于形成精细的加工效果至关重要。
研究者通过改变脉冲参数的波形、幅值和频率等,可以实现微细加工和纳米加工,进一步提高加工的精度和表面质量。
第四,放电液的优化研究。
电火花成形加工中常常使用放电液来冷却工件和电极,并清除放电过程中产生的氧化物和熔融物。
研究者通过改变放电液的成分和性能,可以改善放电的稳定性和加工质量。
电火花成形加工技术的未来发展趋势主要体现在以下几个方面:第一,提高加工效率和精度。
随着工件精度要求的不断提高,电火花成形加工技术需要进一步改进,以实现更高的加工效率和更好的加工精度。
研究者将继续优化放电参数和脉冲控制技术,以提高加工速度和形成更精细的加工效果。
第二,拓展加工材料范围。
目前电火花成形加工主要应用于金属和合金材料,但随着复合材料、陶瓷材料和高性能材料的不断发展,对于电火花成形加工技术的要求也越来越高。
电火花新加工技术及其发展趋势
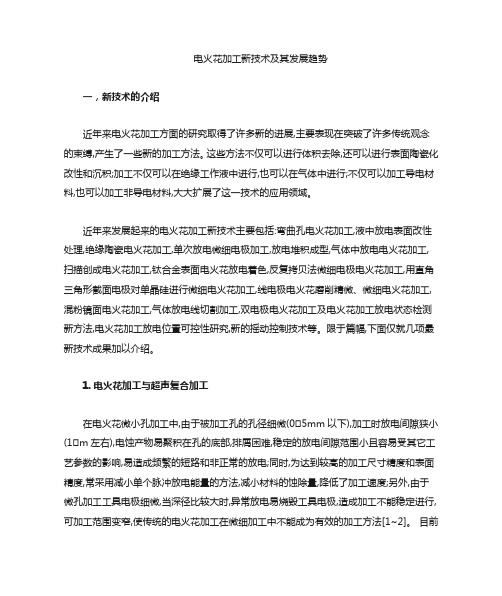
电火花加工新技术及其发展趋势一,新技术的介绍近年来电火花加工方面的研究取得了许多新的进展,主要表现在突破了许多传统观念的束缚,产生了一些新的加工方法。
这些方法不仅可以进行体积去除,还可以进行表面陶瓷化改性和沉积;加工不仅可以在绝缘工作液中进行,也可以在气体中进行;不仅可以加工导电材料,也可以加工非导电材料,大大扩展了这一技术的应用领域。
近年来发展起来的电火花加工新技术主要包括:弯曲孔电火花加工,液中放电表面改性处理,绝缘陶瓷电火花加工,单次放电微细电极加工,放电堆积成型,气体中放电电火花加工,扫描创成电火花加工,钛合金表面电火花放电着色,反复拷贝法微细电极电火花加工,用直角三角形截面电极对单晶硅进行微细电火花加工,线电极电火花磨削精微、微细电火花加工,混粉镜面电火花加工,气体放电线切割加工,双电极电火花加工及电火花加工放电状态检测新方法,电火花加工放电位置可控性研究,新的摇动控制技术等。
限于篇幅,下面仅就几项最新技术成果加以介绍。
1.电火花加工与超声复合加工在电火花微小孔加工中,由于被加工孔的孔径细微(0 5mm以下),加工时放电间隙狭小(1 m左右),电蚀产物易聚积在孔的底部,排屑困难,稳定的放电间隙范围小且容易受其它工艺参数的影响,易造成频繁的短路和非正常的放电;同时,为达到较高的加工尺寸精度和表面精度,常采用减小单个脉冲放电能量的方法,减小材料的蚀除量,降低了加工速度;另外,由于微孔加工工具电极细微,当深径比较大时,异常放电易烧毁工具电极,造成加工不能稳定进行,可加工范围变窄,使传统的电火花加工在微细加工中不能成为有效的加工方法[1~2]。
目前常采用的提高电火花加工能力的方法,如人工排气法,强迫冲液或抽液法、加速工作液循环等方法,常因加工条件或加工要求的限制而无法实现。
因此,为改善电火花加工性能,在微细加工中,采用超声电火花复合加工是非常有效的手段。
在电极上附加超声振动,就可以使电极端面频繁进入合适的放电间隙,提高火花击穿的概率;同时由于超声的空化作用和泵吸作用,可以增大被加工材料的去除量,加速工作液循环,改善间隙放电条件,从而提高被加工孔的深径比、加工稳定性、生产率和脉冲电源的利用率,并且在振幅得到良好控制的情况下,可以获得更高的加工精度。
电火花成形加工技术的研究现状和发展趋势
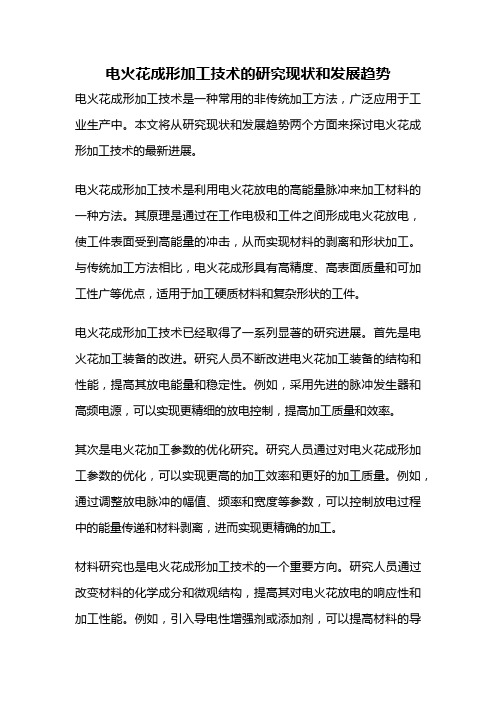
电火花成形加工技术的研究现状和发展趋势电火花成形加工技术是一种常用的非传统加工方法,广泛应用于工业生产中。
本文将从研究现状和发展趋势两个方面来探讨电火花成形加工技术的最新进展。
电火花成形加工技术是利用电火花放电的高能量脉冲来加工材料的一种方法。
其原理是通过在工作电极和工件之间形成电火花放电,使工件表面受到高能量的冲击,从而实现材料的剥离和形状加工。
与传统加工方法相比,电火花成形具有高精度、高表面质量和可加工性广等优点,适用于加工硬质材料和复杂形状的工件。
电火花成形加工技术已经取得了一系列显著的研究进展。
首先是电火花加工装备的改进。
研究人员不断改进电火花加工装备的结构和性能,提高其放电能量和稳定性。
例如,采用先进的脉冲发生器和高频电源,可以实现更精细的放电控制,提高加工质量和效率。
其次是电火花加工参数的优化研究。
研究人员通过对电火花成形加工参数的优化,可以实现更高的加工效率和更好的加工质量。
例如,通过调整放电脉冲的幅值、频率和宽度等参数,可以控制放电过程中的能量传递和材料剥离,进而实现更精确的加工。
材料研究也是电火花成形加工技术的一个重要方向。
研究人员通过改变材料的化学成分和微观结构,提高其对电火花放电的响应性和加工性能。
例如,引入导电性增强剂或添加剂,可以提高材料的导电性和放电效果,从而改善加工质量和效率。
在电火花成形加工技术的发展趋势方面,可以预见以下几个方面的发展。
首先是加工精度的提高。
随着精密加工需求的增加,电火花成形加工技术将朝着更高的加工精度发展。
通过进一步优化装备和参数,提高加工精度和表面质量,满足更高精度加工的需求。
其次是加工效率的提高。
虽然电火花成形加工具有高精度的优点,但其加工效率相对较低。
因此,研究人员将继续改进加工装备和参数,提高加工效率,实现更快速的加工速度和更高的生产效率。
材料范围的扩展也是电火花成形加工技术的一个重要发展方向。
目前,电火花成形加工主要应用于金属和合金材料的加工,但也有研究人员开始尝试将其应用于其他材料,如陶瓷、复合材料等。
2023年电火花加工机床行业市场分析现状

2023年电火花加工机床行业市场分析现状电火花加工机床是一种高精度加工设备,广泛应用于模具制造、航空航天、汽车制造、电子电器等行业。
它通过电火花放电技术实现对金属材料的精细加工,能够加工出高精度、高表面质量的零件和模具。
目前,电火花加工机床在中国市场的发展态势良好,主要表现在以下几个方面:1.市场规模不断扩大。
随着制造业的快速发展,对高精度零件和模具的需求越来越大,电火花加工机床的市场需求也在逐年增加。
根据行业数据显示,2019年全国电火花加工机床的销售额达到了120亿元,同比增长了10%以上。
2.技术不断进步。
电火花加工机床的关键技术在近年来得到了快速发展,包括放电电源技术、自动化控制技术、加工精度控制技术等方面都取得了重要突破。
这些技术的进步,不仅提高了机床的加工精度和效率,还降低了加工成本,增强了市场竞争力。
3.行业集中度提高。
在市场竞争的推动下,电火花加工机床企业之间发生了一系列的兼并和重组,市场资源逐渐集中在少数大型企业手中。
这些大型企业具有更强的研发实力和生产能力,能够生产出更高质量、高性价比的产品,也更具有市场竞争力。
4.市场需求趋势多样化。
随着高端制造业的快速发展,对电火花加工机床的需求也呈现多样化趋势。
有的行业需求更高的加工精度和表面质量,有的行业则追求更高的加工效率和产能。
为了适应不同行业的需求,电火花加工机床企业纷纷推出多款产品,以满足市场需求。
尽管电火花加工机床行业市场发展态势良好,但也面临一些问题和挑战:1.市场竞争压力加大。
随着市场规模扩大,竞争对手也越来越多,市场竞争压力不断加大。
加上国内外机床企业的加入,行业竞争格局将变得更加复杂和激烈。
2.产品同质化严重。
目前电火花加工机床市场上产品同质化现象比较严重,许多企业在产品设计和技术研发方面缺乏创新,导致产品的差异化程度不高。
3.研发投入不足。
由于行业利润率相对较低,电火花加工机床企业在研发方面的投入普遍较低,限制了技术创新和产品质量的提升。
电火花加工技术研究的发展趋势预测

四、结论
电火花成形加工技术作为一种重要的制造工艺,在机械、航空、航天、汽车等 领域得到了广泛应用。本次演示介绍了该技术的现状和发展趋势,指出存在的 不足和发展方向。未来的研究应智能化、绿色制造、超硬材料加工等方面的发 展,以实现电火花成形加工技术的可持续发展。
谢谢观看
例如,利用机器视觉技术对工件进行精确的定位和识别,实现自动化的加工过 程。 (3)绿色化:通过加强环保措施和技术创新,减少电火花加工过程中的环 境污染和资源浪费。例如,研究环保型的电火花加工液和可回收利用的电极材 料,减少对环境的负面影响。
3、模具行业:模具行业是电火 花加工技术的重要应用领域之一
电火花加工技术的研究现状
电火花加工的基本原理是利用电火花放电时产生的瞬间高温来熔化、气化或燃 烧材料,从而达到加工的目的。电火花加工过程中,工具和工件之间产生放电 现象,产生大量的热能,使工件表面材料熔化、汽化,随着工具的移动,在工 件表面形成切削层,从而达到加工的目的。
电火花加工技术在不同领域的应 用
1、航空航天领域:由于航空航天领域的零件材料具有高强度、高硬度、耐高 温等特点,电火花加工技术在制造这些零件中发挥了重要作用。通过电火花加 工,可以有效地提高零件的加工效率和精度。
2、汽车制造业:汽车制造业中,许多关键零部件的制造都依赖于电火花加工 技术。例如,发动机缸体、缸盖等复杂结构的加工,电火花加工技术可以高效 地完成。
参考内容
电火花成形加工技术是一种重要的制造工艺,被广泛应用于机械、航空、航天、 汽车等领域。本次演示将介绍电火花成形加工技术的现状和发展趋势,以期为 相关领域的研究和实践提供参考。
一、电火花成形加工技术的背景
电火花成形加工是一种基于电火花放电原理的加工方法。在加工过程中,工具 和工件之间产生的高速高温放电会熔化、气化或燃烧材料,从而达到加工的目 的。这种加工方法具有加工难度低、工具损耗小、适用材料范围广等优点,但 同时也存在加工效率低下、加工精度难以控制等不足。
电火花成形加工技术的现状与发展趋势

电火花成形加工技术的现状与发展趋势电火花成形加工技术是一种高精度、高效率、高灵活性的加工方法,广泛应用于模具制造、航空航天、汽车、电子等领域。
该技术通过形成电火花放电腐蚀、切割工件表面,将固体工件形成所需形状。
随着制造行业的发展和技术的不断升级,电火花成形加工技术在应用范围、加工精度、成型效率等方面也有所提升。
本文将详细介绍电火花成形加工技术的现状和发展趋势。
一、电火花成形加工技术的现状1. 应用范围扩大电火花成形加工技术广泛应用于钢铁、航空、汽车、电子、医疗、航天等行业。
特别是在模具加工领域,电火花成形加工技术已成为最常见的成形加工方法。
除此之外,电火花成形加工技术在加工高强材料、微细零部件等方面也有广泛应用。
2. 加工精度提高电火花成形加工技术具有高精度的优势,其加工精度可达到亚微米级别。
由于电火花加工时,电极与工件之间的间隙可以控制在微米级,因此可以保证加工出的模具和零部件的精度和表面质量的高度一致性。
3. 加工效率提高传统的电火花成形加工技术通常采用单电极加工方式,加工效率较低。
如今,优化后的多电极电火花成形加工技术可以同时加工多个工件,从而提高了加工效率。
此外,电极与工件間隙的控制技术也不断完善,使得加工效率得到快速提升。
4. 自动化程度提高随着工业4.0时代的到来,电火花成形加工技术的自动化程度逐渐提高。
目前,许多厂家已经研发出自动化程度高的电火花成形加工机床。
这样可以大幅提高电火花加工的生产效率和稳定性,减少加工错误和损失,节约生产成本。
二、电火花成形加工技术的发展趋势1. 精密化和高速化电火花成形加工技术目前的发展方向是提高加工精度和加工速度。
因此,更加精密化的切削工具和更高速的电火花腐蚀液将成为电火花成形加工技术发展的重点。
这将有助于提高产品质量和加工效率。
2. 智能化和自动化随着科技的进步,电火花成形加工技术将越来越智能化和自动化。
这将会使得机器人、机器视觉和自主化控制系统的应用变得更加常见,从而提高电火花成形加工技术的高效性和可靠性。
电火花成形加工技术的现状与发展趋势
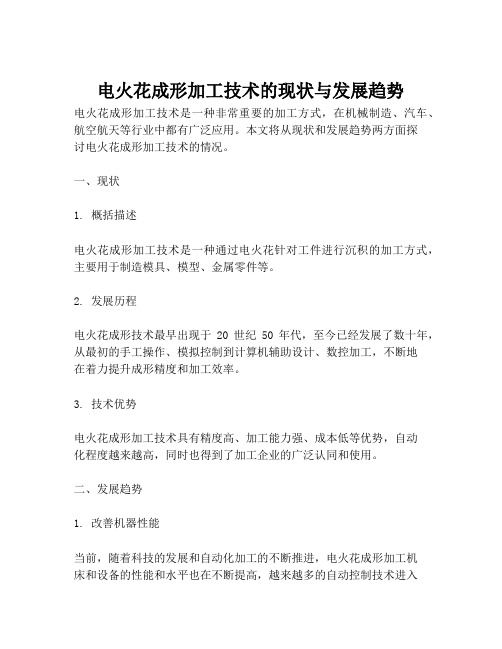
电火花成形加工技术的现状与发展趋势电火花成形加工技术是一种非常重要的加工方式,在机械制造、汽车、航空航天等行业中都有广泛应用。
本文将从现状和发展趋势两方面探讨电火花成形加工技术的情况。
一、现状1. 概括描述电火花成形加工技术是一种通过电火花针对工件进行沉积的加工方式,主要用于制造模具、模型、金属零件等。
2. 发展历程电火花成形技术最早出现于20世纪50年代,至今已经发展了数十年,从最初的手工操作、模拟控制到计算机辅助设计、数控加工,不断地在着力提升成形精度和加工效率。
3. 技术优势电火花成形加工技术具有精度高、加工能力强、成本低等优势,自动化程度越来越高,同时也得到了加工企业的广泛认同和使用。
二、发展趋势1. 改善机器性能当前,随着科技的发展和自动化加工的不断推进,电火花成形加工机床和设备的性能和水平也在不断提高,越来越多的自动控制技术进入到该行业中。
2. 提升加工质量近年来,随着电火花成形技术的不断发展,加工质量已经达到了较为稳定的水平,未来会通过不断地技术改进和提升,以更好的方式满足市场需求。
3. 减少人工操作在未来,电火花成形工程师将更多地关注如何在自动化系统中通过编程、模拟加工等方式减少人工操作,以提升加工效率和精度。
4. 强化数据管理在不断的技术革新中,与之相关的信息和数据处理也变得越来越重要,将会有越来越多的信息管理人员参与到电火花成形行业中,涉及到的数据管理技术也将越来越先进和复杂。
总体来看,电火花成形加工技术的发展前景非常广阔。
未来,电火花成形加工技术将会更加精密化、自动化,不断地为制造行业提供优质的加工解决方案。
电火花加工技术及其发展趋势

电火花加工技术的发展及趋势1. 1电火花加工的发展趋势1·1电火花加工精密化电火花加工的精密化可以理解为两方面的内容:一是加工尺寸上的精密性,二是加工表面质量的精密性。
在电火花加工过程中,与尺寸精度有直接关系的因素是放电间隙和电极损耗。
加工间隙的一致性、稳定性以及电极损耗的大小直接影响电火花加工的精度。
精密的电火花加工,加工过程中应保持较小的放电间隙,并使放电间隙稳定在一个较小范围内。
而放电间隙的调整与极间状态密切相关,实时、准确地检测出两极间的放电状态,则为调整两极间合适的放电间隙提供了必要的条件,加工间隙的准确调整还有赖于合理的伺服控制策略等[2-3]。
由于电火花加工状态复杂多变,为加工状态的检测和放电间隙的控制增加了难度。
因此,需加强电火花加工状态的检测、加工间隙的控制以及加工电源的稳定性等方面的研究。
实现电火花精密加工时,要采用精加工规准来完成工件的尺寸精度和表面精度。
然而,电火花加工过程中,均不同程度存在工具电极损耗。
虽然人们从工作液的种类、电源、控制、工作介质、电极材料等多方面对电极损耗进行了广泛的研究,在减少电极损耗方面取得了一定的研究效果。
但是到目前为止,在精加工和微细加工中,电极损耗现象还是比较严重。
电极损耗的存在必然对电火花加工的尺寸精度产生影响,需要对工件进行多次加工以补偿由于电极损耗而造成的尺寸偏差,这样增加了加工时间和加工成本。
因此,如何降低工具电极的损耗,从而实现高速、低损耗的精密加工是电火花加工不断追求的目标[4-5]。
电火花加工表面质量的精密化是加工精密化的另一方面的内容。
电火花加工表面是一系列的微小放电凹坑重叠组成的,一般的加工条件下表面有微裂纹,为达到较好的加工表面,需要在电火花之后增加手动抛光工序,这增加了工人的劳动强度和加工成本,制约电火花加工速度的提高,不利于自动化加工实现。
因此,实现电火花加工表面质量的精密化仍是今后的研究发展方向。
较小面积的电火花加工可以通过精微加工电源实现,微能电源对电火花加工表面质量的改善很有效果,能够达到较好的表面质量。
微细加工技术的应用和趋势

改造 客观世 界 的一种 高 新技 术 。微机械 多 的小型 泵 的1 0 0 0 倍 ,而 且机 电一体 化 蚀 ,最 后把 光刻胶 去掉 就得 到 了想要 的
由于 具有 能够在 狭 小空 间 内进 行 作业 , 的微 机械 不存 在信 号延 迟 问题 ,可进 行 图形 。光刻技 术在 微 电子 中 占有 很大 的 比重 ,比如微 电子应用 3 . 1搬迁原子 1 9 9 0 年 ,美 国圣何塞I B M N尔马登研
而 受 到人们 的高 度重 视 ,被 列为 2 1 世 纪 和智 能结 构后 ,更 易于 实现 微机 械 的多 关键 技术 之首。 功能化和智能化 。
1 . 微机械 的特征
1 . 5 适 于大批 量生 产 、制 造成 本低 究所科 学家用S T M 将镍表面 吸附的氙原子
5 个氙 原子排成 I B M - = 微 机 械 在 美 国 常 称 为 微 型 机 电系 廉。微机械采用与 半导体制造工艺类似的 逐一移动 ,最终 以3 统 ;在 日本 称作 微机 器 ;而在 欧 洲则称 方法生产 ,可以象超大规模集成 电路芯片 个字母 。每个字母 高5 n m ,原子间的最短 作微 系统。
而 又 不扰乱 工作 环境 和对 象 的特 点 ,在 高速工作 。
航 空航 天 ,精密 仪器 ,生物 医学 等领域
1 . 4 多功能和 智 能化 。微 机械 最终 宽 来评 价 的,而线 宽 的获得跟 光刻 技术
有 着广 阔 的应用 潜 力 ,且是 实现 纳米技 要达 到集传 感 器 、执行 器和 电子控 制 电 有 很 大 的关 系 。 术 (N a n 0 t e c h n o l o g y ) 的重 要 环 节 , 因 路为 一体 的 目标 ,特别 是应 用智 能材 料
电火花成形加工技术的现状与发展趋势

电火花成形加工技术的现状与发展趋势电火花成形加工技术是一种利用高频脉冲电火花将金属加工件切割和成形的加工技术。
该技术具有精度高、加工速度快、切割面光滑、加工材料可靠性强等优点,广泛应用于航空制造、汽车制造、模具加工、精密机械加工等领域。
目前,电火花成形加工技术已经取得了广泛的应用,成为机械制造行业中重要的一环,发展趋势更加明显。
以下是电火花成形加工技术的现状与发展趋势的相关参考内容。
1. 技术发展趋势明显随着国家科技水平不断提高,电火花成形加工技术的应用范围也不断扩大。
一方面,越来越多的企业对电火花成形加工技术的需求不断增加,另一方面,科技人员也在不断探索电火花成形加工技术的新方法和新途径,从而进一步加速了电火花成形加工技术的发展。
2. 精度要求不断提高随着制造业的不断发展,精度要求也在不断提高。
因此,在电火花成形加工技术方面,人们也不断提高加工精度,让其更好地适应市场需求。
例如,使用相应的软件进行编程,以确保加工部件的准确性。
3. 材料加工范围扩大随着制造业的不断发展与进步,市场对生产材料种类和数量的需求也在不断扩大。
因此,电火花成形加工技术也应用在更多的材料制造与加工中,从而使其在市场上更有优势。
如钨合金、铝合金、陶瓷、碳化钨等。
4. 机器智能化程度提高现代工业生产不仅要追求效率,还要注重质量。
随着科技的进步,电火花成形加工机器也在不断智能化。
例如,引入CAD、CAM软件技术,可以实现自动化生产和控制。
这些自动化技术可以提高产品质量,节省生产成本,加快生产效率等。
5. 嵌入式加工技术渐趋成熟随着嵌入式技术的发展和普及,电火花成形加工中的嵌入式加工技术也逐渐成熟。
通过软件和控制器编程,可以使机器智能化,从而实现更精细和高效的加工生产线。
综上所述,电火花成形加工技术在未来的发展中将继续发挥重要的作用。
采用现代化的技术手段、提高加工精度、扩大加工材料范围、智能化程度提高等,会使电火花成形加工技术在未来发展中更为广泛和优胜。
论电火花的现状与发展趋势
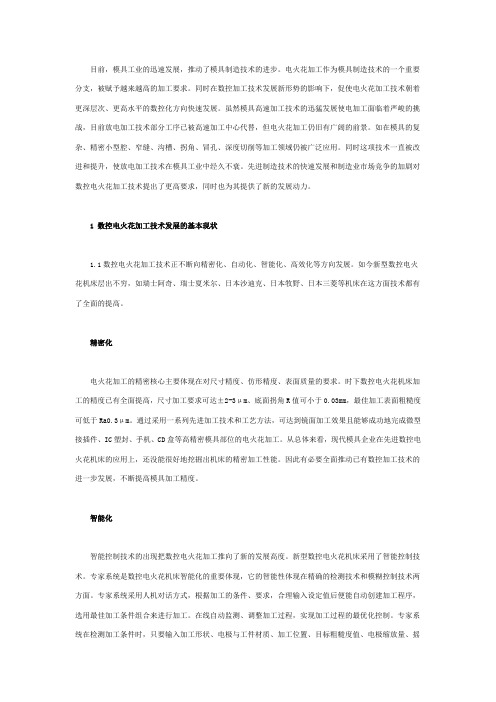
目前,模具工业的迅速发展,推动了模具制造技术的进步。
电火花加工作为模具制造技术的一个重要分支,被赋予越来越高的加工要求。
同时在数控加工技术发展新形势的影响下,促使电火花加工技术朝着更深层次、更高水平的数控化方向快速发展。
虽然模具高速加工技术的迅猛发展使电加工面临着严峻的挑战,目前放电加工技术部分工序已被高速加工中心代替,但电火花加工仍旧有广阔的前景。
如在模具的复杂、精密小型腔、窄缝、沟槽、拐角、冒孔、深度切削等加工领域仍被广泛应用。
同时这项技术一直被改进和提升,使放电加工技术在模具工业中经久不衰。
先进制造技术的快速发展和制造业市场竞争的加剧对数控电火花加工技术提出了更高要求,同时也为其提供了新的发展动力。
1数控电火花加工技术发展的基本现状1.1数控电火花加工技术正不断向精密化、自动化、智能化、高效化等方向发展。
如今新型数控电火花机床层出不穷,如瑞士阿奇、瑞士夏米尔、日本沙迪克、日本牧野、日本三菱等机床在这方面技术都有了全面的提高。
精密化电火花加工的精密核心主要体现在对尺寸精度、仿形精度、表面质量的要求。
时下数控电火花机床加工的精度已有全面提高,尺寸加工要求可达±2-3μm、底面拐角R值可小于0.03mm,最佳加工表面粗糙度可低于Ra0.3μm。
通过采用一系列先进加工技术和工艺方法,可达到镜面加工效果且能够成功地完成微型接插件、IC塑封、手机、CD盒等高精密模具部位的电火花加工。
从总体来看,现代模具企业在先进数控电火花机床的应用上,还没能很好地挖掘出机床的精密加工性能。
因此有必要全面推动已有数控加工技术的进一步发展,不断提高模具加工精度。
智能化智能控制技术的出现把数控电火花加工推向了新的发展高度。
新型数控电火花机床采用了智能控制技术。
专家系统是数控电火花机床智能化的重要体现,它的智能性体现在精确的检测技术和模糊控制技术两方面。
专家系统采用人机对话方式,根据加工的条件、要求,合理输入设定值后便能自动创建加工程序,选用最佳加工条件组合来进行加工。
电火花成形加工技术的研究现状和发展趋势

电火花成形加工技术的研究现状和发展趋势电火花成形加工技术是一种利用电火花放电进行材料加工的先进工艺。
它在自动化、高效率、高精度方面具有明显的优势和广泛的应用前景。
本文将对电火花成形加工技术的研究现状和发展趋势进行详细探讨。
电火花加工技术最早是在20世纪50年代初期由苏联工程师、科学家等人发明的,起初主要应用于修复机械零件表面的磨损、修复损伤、修复变形等工作。
随着科技的进步和工艺的不断改进,电火花成形加工技术在机械制造、模具制造和微细工艺加工等领域得到了广泛应用。
目前,电火花成形加工技术已经在各个领域取得了显著的进展。
首先,在机械制造领域,电火花成形加工技术广泛应用于制造高精度复杂曲面零件、机械模具以及各类高精度刀具等。
其次,在航空航天领域,电火花成形加工技术可用于制造高温合金材料的复杂结构件,提高其耐高温、高压和高速等工作环境的适应能力。
再次,在微细加工领域,电火花成形加工技术被广泛应用于微型零件、精密模具以及各类微细孔、微细纹等微细结构的加工。
与传统加工技术相比,电火花成形加工技术具有以下优势。
首先,电火花成形加工技术可以实现高精度加工,其加工精度可达到亚微米甚至纳米级别。
其次,电火花成形加工技术可以加工各种材料,包括热处理钢、不锈钢、铁素体不锈钢、高温合金、硬质合金等,广泛适用于各种行业的加工需求。
再次,电火花成形加工技术可以实现复杂曲面的加工,无论是二维曲面还是三维曲面,都可以实现高效率、高质量的加工。
然而,电火花成形加工技术也存在一些问题和挑战。
首先,电火花成形加工技术的重复性和稳定性有待提高,特别是在加工复杂结构和微细结构时,容易出现放电不稳定、电极损耗严重等问题。
其次,由于放电过程中产生的热量和应力,容易导致工件表面产生热裂纹和变形等问题,需要进一步研究改进。
再次,电火花成形加工技术的加工效率有待提高,尤其是在大批量生产和高效率加工领域中,需要进一步提高加工速度和加工效率。
为了克服这些问题和挑战,电火花成形加工技术的研究者正在开展一系列的研究工作。
电火花技术现状与发展分析

电火花技术现状与发展分析
一、电火花技术简介
电火花是指由电能及其相关现象激发的气体火花,它是电熔焊与氩弧焊的主要基础技术,是一种特殊的电放电现象,又称为电灼焊、通电焊。
它是一种在切割和连接各种金属材料和塑料的新型的焊接技术。
电火花技术与普通的焊接技术相比,具有更高的切割效率,更小的焊缝尺寸和更少的损伤等优点,可以得到更完美的焊缝形状。
二、电火花技术发展现状
1、电火花中心技术研究的发展
电火花技术是一种新兴的焊接技术,它的发展需要建立一个高科技的中心,由一些专家、科学家及工程师组成,围绕电火花技术的开发去探索和研究,以及与相关技术的结合,这样才能让电火花技术更好的发展,扩大它的应用范围。
2、电火花技术在工业制造中的应用
电火花技术不但可以用于工业制造,还可以用于家用电器、航空、船舶等行业,甚至还可以用于医疗、农业等领域。
在工业制造领域,电火花技术能够有效提高生产率,减少制造成本,提高整个制造过程的精度,加速产品的开发,使用更简单、更少的工艺制造更多的产品。
在家用电器、航空、船舶等行业中,电火花技术可以帮助企业更快速地生产,降低生产成本,提高产品的质量。
电火花成形加工技术的现状与发展趋势

电火花成形加工技术的现状与发展趋势电火花成形加工技术是一种重要的金属材料加工技术,具有高精度、高效率、可靠性强等优势,被广泛应用于航天、航空、医疗器械、汽车、家电等各个领域。
然而,随着市场竞争日益激烈和技术的不断进步,电火花成形加工技术的现状与发展趋势也逐渐受到关注。
本文将从电火花成形加工技术的现状和发展趋势两个方面进行解读。
一、电火花成形加工技术的现状目前,电火花成形加工技术在我国的应用已经逐渐成熟。
检测数据表明,其加工精度可以达到0.001mm以上,而粗加工时,加工效率可以高达每小时500mm³。
此外,电火花成形加工技术还具有以下优点:1、可加工高硬度材料电火花成形加工技术采用电脉冲放电进行加工,可以对金属、合金等高硬度材料进行加工,大大拓展了加工材料的选择范围。
2、形状复杂的成品电火花成形加工技术可以制作出头发丝般细的细微形状,同时也可以加工出复杂的三维异形零部件,为大型零件的制造提供了方便。
3、内部孔加工通过电极管的穿透和内部电极扫描的方式,电火花成形加工技术可以对材料进行内部孔的加工,生产更小巧、更精细的零件。
二、电火花成形加工技术的发展趋势1、智能化随着人工智能技术的广泛运用,电火花成形加工技术也正在朝着智能化方向不断发展。
新一代智能式电火花成形加工机将拥有更加智能的控制系统、更高效的自适应控制系统和更严格的质量控制系统,使其在精度和效率上更上一层楼。
2、先进技术的应用电火花成形加工技术和其他先进技术的结合,将有助于取得更加令人瞩目的成果。
例如,采用异步高速电机、低噪音螺杆空气压缩机、高效能量回收系统、智能化机器人操作系统等技术,可以使电火花成形加工机的效率和稳定性更高。
3、环保节能在保证加工效果的前提下,电火花成形加工技术还应当加强节能环保方面的建设。
研发新型绿色电火花成形加工剂、采用清洁能源替代传统燃料、开发废气、废水资源、减少环境污染等措施,是电火花成形加工技术未来发展的必然趋势。
电火花成形加工技术的现状与发展趋势

电火花成形加工技术的现状与发展趋势
电火花成形加工技术是一种高精度加工技术,具有成形精度高、表面质量好、加工效率高等优点,被广泛应用于制造行业。
以下是其现状与发展趋势的相关参考内容:
1. 现状:电火花成形加工技术已经广泛应用于航空、航天、电子、医疗等高技术领域,成为制造业重要的加工技术之一。
尤其是在精密模具、微细结构等领域的应用更加广泛,可完成对复杂形状的加工,使加工精度达到亚微米级别。
同时,近年来电火花成形加工技术与计算机技术、智能制造技术等深度结合,实现了自动化和智能化。
2. 发展趋势:
(1)多功能化:将电火花成形加工技术与其他加工技术结合,实现多功能化加工,例如电火花加工复合切割。
(2)高速化:提高加工速度和效率,减少加工时间,同时保
证加工精度和表面质量。
(3)智能化:将电火花成形加工技术应用于智能制造,在加
工过程中实现自动化、智能化控制。
(4)微观化:为满足微细产品的制造需求,电火花成形加工
技术需要在微观、纳米级别上有所突破,实现对微结构的高精度加工。
(5)环保化:优化电火花成形加工技术的加工过程,实现对环境的友好,减少对环境的污染。
总之,电火花成形加工技术已经具有非常广泛的应用前景。
随着新技术的不断涌现和应用,相信其在未来会迎来更加广阔的发展空间。
电火花成形加工技术的现状与发展趋势

电火花成形加工技术的现状与发展趋势电火花成形加工技术(Electrical Discharge Machining,EDM)是一种利用电火花放电瞬间熔解加工材料的高精度加工技术。
作为一种非接触式的加工技术,其具有加工精度高、加工难度大等特点,可以用于材料加工中精密零件的制造。
近年来,伴随着制造业的飞速发展以及材料加工行业的迅猛发展,电火花成形加工技术也在不断向前发展和进步。
现状目前,电火花成形加工技术已经成为制造业中主要的加工方法之一,其具有广泛的应用场景,比如汽车工业、航空航天工业、精密机械、模具制造、3D打印等领域。
这是因为电火花成形加工技术可以应对难以用传统机械加工方法加工的材料以及复杂形状的加工需求。
同时,现代电火花成形加工技术技术不断进步,其加工精度也越来越高,可以用于制造出更加精细的机械零件。
各个制造企业也纷纷加大对电火花成形加工技术的投入,在提高加工效率和加工精度的同时,降低企业的生产成本。
发展趋势随着科技的不断进步和创新的推广,电火花成形加工技术也在不断发展。
未来,电火花成形加工技术将在以下几个方面迎来重大的发展趋势:1. 多功能化:未来的电火花成形加工技术将不仅仅只是加工单一材料,而是会涉及多种材料的加工,例如金属、塑料、陶瓷等材料。
这将提高该技术的应用范围和加工精度。
2. 自适应控制:未来,智能化将成为加工技术的重要发展方向之一。
这意味着电火花成形加工机器将会拥有自适应能力,根据加工对象的不同,自动调整加工参数以提高加工效率和加工精度。
3. 超精密:未来的电火花成形加工技术将会进一步加强加工精度,其制造的机械零件可以达到微米级别的精度要求。
这将提高加工效率和加工质量,为相关领域的研发提供更好的基础和保障。
结论总的来说,电火花成形加工技术在现代制造业中具有广泛的应用场景和巨大的市场潜力。
未来,这种加工技术将会不断向着多方面的发展。
各个制造企业也应该加大对电火花成形加工技术的投入,不断提高电火花成形加工技术的应用水平和加工能力,为相关领域的研发提供更好的支持和服务。
电火花的应用及发展趋势
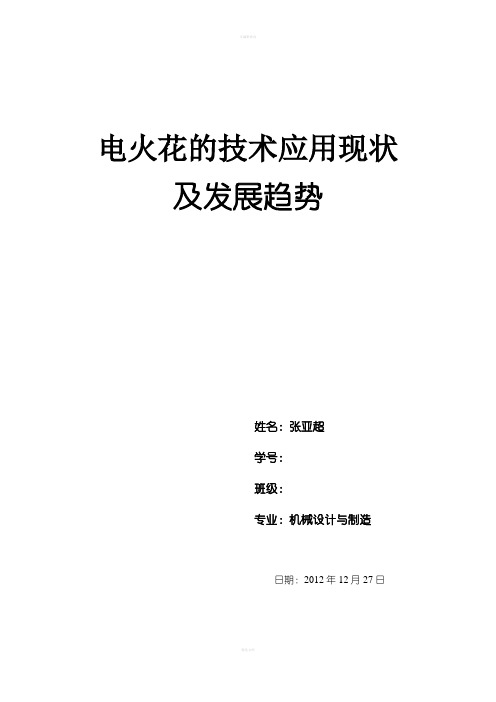
电火花的技术应用现状及发展趋势姓名:张亚超学号:班级:专业:机械设计与制造日期:2012年12月27日摘要在分析总结国内外电火花线切割技术研究现状以及我国近几年来所取得的进步基础上,以及在电火花加工技术在汽车、航空航天、模具等制造工业中有着广泛的应用,模具工业技术快速发展的新形势下, 数控电火花加工技术已取得了突破性的进展。
本文从电火花加工技术发展的基本现状、数控电火花加工的操作过程、数控电火花加工新工艺的应用以及电火花加工技术的发展趋势以及发展建议。
论述了我国电火花线切割技术的发展趋势及其主要任务。
关键词:电火花线切割;研究现状;发展趋势目录引言 (4)一、数控电火花加工技术现状 (4)二、电火花技术发展趋势 (5)(一)精密化 (5)(二)智能化 (5)(三)自动化 (6)(四)高效化 (6)(五)绿色工作液得到应用 (7)(六)电火花加工技术的改进 (7)(七)其它 (8)三、电火花技术中的新应用 (8)(一)标准化夹具实现快速精密定位 (8)(二)混粉加工方法实现镜面加工效果 (8)(三)摇动加工方法实现高精度加工 (9)(四)多轴联动加工方法实现复杂加工 (9)(五)基于PC的数控系统的开发 (10)(六)多次切割工艺的应用 (10)参考文献 (11)引言目前,随着电子、信息等高新技术的不断发展及市场需求个性化与多元化,世界各国都把机械制造技术的研究和开发作为国家的关键技术进行优先发展,将其他学科的高技术成果引入机械制造业中。
因此机械制造业的内涵与水平已今非昔比,它是基于先进制造技术的现代制造产业。
纵观现代机械制造技术的新发展,其重要特征主要体现在它的绿色制造、计算机集成制造、柔性制造、虚拟制造、智能制造、并行工程、敏捷制造和网络制造等方面。
机械制造行业不断遇到高硬度,高韧性,高熔点等难切割加工材料以及特殊结构特别市复杂曲面零件的加工难题。
解决这些问题极大地促进了电火花线切割加工技术的发展,促进电火花线切割加工新方法,新工艺的不断表现,扩大了电火花线切割加工的适用范围。
- 1、下载文档前请自行甄别文档内容的完整性,平台不提供额外的编辑、内容补充、找答案等附加服务。
- 2、"仅部分预览"的文档,不可在线预览部分如存在完整性等问题,可反馈申请退款(可完整预览的文档不适用该条件!)。
- 3、如文档侵犯您的权益,请联系客服反馈,我们会尽快为您处理(人工客服工作时间:9:00-18:30)。
微细电火花加工技术与发展趋势于同敏黄晓超(大连理工大学机械工程学院模具研究所大连116023)摘要:本文简要的介绍了微型制件及微型模具的定义和分类,并着重介绍了应用于微型模具型腔加工的微细加工技术—微细电火花加工。
总结了微细电火花的发展趋势和关键技术。
关键词:微注塑模具微细电火花关键技术Technology of Micro Electrical Discharge Machiningand Its Development TrendYU Tongmin HUANG Xiaochao(Institute of Die and Mould of School of Mechanical Engineering of Dalian University of Technology, Dalian 116023 )Abstract: The division and definition of micro part and micro mould were introduced in this paper. Emphsis was given to illustrate the micro-machining technology of mould cave manufactureng —Micro electrical discharge machining(M-EDM) . A conclusion of the development trend and key technology of MEDM was made in this paper.Key words:Micro-injection mould Micro-EDM Key technology0 前言为了满足塑料制件在各种工业产品中的使用要求,塑料成型技术正朝着复杂化、精密化、微小化等方向发展,例如应用于微机电系统的微马达、微小齿轮以及应用于生物工程领域的细胞培养皿和微流控芯片等的成型。
除了必须研发或引进微型和精密成型设备外,微小且精密的塑料成型模具更是需要采用先进的模具CAD/CAE/CAM技术来设计制造,并运用各种先进的加工手段]1[。
微型模具的制造主要通过微细加工,目前的微细加工方法主要有:①微细切车削、铣削和磨削等;②微细特种加工如:电火花、电化学、激光、超声波、离了束和电了束等;③光刻、蚀刻和LIGA技术。
其中微细电火花加工应用最为广泛,也是近年来研究的重点方向之一。
1 微型模具1.1 微型模具的定义应用微细加工方法制作微型模具,再通过微型模具成形微型制件,具有生产效率高、制件尺寸稳定性好的优点]2[。
因此,近年来关于微型模具制造技术的研究普遍受到人们的关注。
但到日前为止,对于微型模具,也没有统一的定义,通常人们习惯于在尺寸和制造精度上来进行限定,即微型模具在尺寸和制造精度上可有如下儿个非约束性的特征(主要指微型模具的成形部分):①成形的制件体积可达1mm3左右;②微观尺寸从几微米到儿百微米;③模具表面粗糙度值在0.1μm以下;④模具制造精度从lμm到0. lμm。
但随着微机械及微细加工技术的发展,这些特征参数值在不断减小]3[。
1.2 精密微型模具的分类微型模具按照成形制件的不同可分为以下儿种类型]3[:(1)微冲压类模具多用于金属和塑料板材的成形,包括微冲切模具和微弯曲模具等。
日本东京大学生产技术研究所进行的微冲压加工,已在50μm厚的聚酞胺塑料板材上冲出了宽度为40μm的非圆截面微孔。
(2)微锻造模具微型锻造制件尺寸多在毫米量级以上,尺寸精度可以达到IT7~IT9级,包括热压印模具等。
(3)微压铸模具用于微小金属零件的压铸成形,可成形锌、铝合金等微型压铸件。
(4)微注塑成形模具用于高分了材料的注塑成形,是目前研究与应用最为广泛的一种微型模具。
目前在德国以LIGA技术为基础制造的微注塑模具已可用来生产质量小于1mg或者局部结构化面积只有儿平方微米的极微小型注塑制品。
2 微细电火花加工技术2.1 微细电火花加工原理微细电火花加工同普通电火花加工的放电机理一样,在加工过程中,电极和工件不接触,利用电极和工件之间不断产生脉冲性火花放电,靠放电时局部、瞬时产生的高温把金属蚀除,从而形成所需的加工表面。
电火花加工的加工原理如图2.1所示。
图2.1 电火花加工原理示意图工件与电极分别与脉冲电源的两输出端相联接。
自动进给调节装置使电极和工件间经常保持很小的放电间隙。
当脉冲电压加到两极之间时,便在当时条件下相对某一间隙最小处或绝缘强度最低处击穿介质,在该局部产生火花放电,瞬时高温使电极和工件表面都蚀除掉小部分金属,各自形成一个小凹坑。
脉冲放电结束后,经过一段间隔时间,使工作液恢复绝缘后,第二个脉冲电压又加到两极上,又会在当时极间距离相对最近或绝缘强度最弱处击穿放电,又电蚀出一个小凹坑。
这样随着相当高的频率,连续不断地重复放电,电极不断地向工件进给,就可将工具端面和横截面的形状复制在工件上,加工出所需要的和电极形状阴阳相反的零件,整个加工表面由无数个小凹坑所组成。
电火花加工的微观过程是电场力、磁力、热力、流体动力、电化学和胶体化学等综合作用的过程。
这一过程大致可分为以下四个连续阶段。
(1)极间介质的电离、击穿,形成放电通道。
当脉冲电压施加于电极和工件之间时,两极之间立即形成一个电场。
电场强度与电压成正比,与距离成反比,随着极间电压的升高或是极间距离的减小,极间电场强度也将随着增大。
由于电极和工件的微观表面是凹凸不平的,极间距离又很小,因而极间电场强度是很不均匀的,两极间离得最近的突出或尖端处的电场强度一般为最大。
由于电场强度增高和负极表面局部过热而引起大量电子发射,使介质击穿而电阻率迅速降低,形成放电通道。
(2)介质热分解、电极材料熔化、气化热膨胀。
极间介质一旦被电离、击穿,形成放电通道后,脉冲电源使通道间的电子高速奔向正极,正离子奔向负极。
电能变成动能,动能通过碰撞又转变为热能。
于是在通道内正极和负极表面分别成为瞬时热源,达到很高的温度。
通道高温将工作液介质气化,进而热裂分解气化。
正负极表面的高温使金属材料熔化甚至沸腾气化。
这些气化后的工作液和金属蒸气,瞬间体积猛增,在放电间隙内成为气泡,迅速热膨胀,就像火药、爆竹点燃后那样具有爆炸的特性。
(3)电极材料的抛出。
通道和正负极表面放电点瞬时高温使工作液气化和金属材料熔化。
气化,热膨胀产生很高的瞬时压力。
通道中心的压力最高,使气化了的气体体积不断向外膨胀,形成一个扩张的“气泡”。
气泡上下、内外的瞬时压力并不相等,压力高处的熔融金属液体和蒸气,就被排挤、抛出而进入工作液中。
由于表面张力和内聚力的作用,使抛出的材料具有最小的表面积,冷凝时凝聚成细小的圆球颗粒。
实际上熔化和气化了的金属在抛离电极表面时,向四处飞溅,除绝大部分抛入工作液中收缩成颗粒外,还有小部分飞溅、镀覆、吸附在对面的电极表面上。
熔融材料抛出后,在电极表面形成放电痕。
(4)极间介质的消电离。
随着脉冲电压的结束,脉冲电流也迅速降为零,但此后仍应有一段间隔时间,使间隙介质消除电离,即放电通道中的正负带电粒子复合为中性粒子,恢复本次放电通道处间隙介质的绝缘强度,以及降低电极表面温度等,以免下次总是重复在同一处电离击穿而导致电弧放电,从而保证在别处按两极相对最近处后电阻率最小处形成下一放电通道。
由于微细电火花加工对象的尺寸通常在数十微米以下,为了达到加工的尺寸精度和表面质量要求,对微细电火花加工还有一些特殊的要求。
微细电火花加工呈现以下一些特点。
(1)放电面积很小。
微细电火花加工的电极一般在φ5~100μm之间,对于一个φ5 μm 的电极来说,放电面积不到20μm2在这样小的面积上放电,放电点的分布范围十分有限,极易造成放电位置和时间上的集中,增大了放电过程的不稳定,使微细电火花加工变得困难。
(2)单个脉冲放电能量很小。
为适应放电面积极小的电火花放电状况要求,保证加工的尺寸精度和表面质量,每个脉冲的去除量应控制在0.10~0.01μm的范围内,因此必须将每个放电脉冲的能量控制在106-~107-J之间,甚至更小。
(3)放电间隙很小。
由于电火花加工是非接触加工,工具与工件之间有一定的加工间隙。
该放电间隙的大小随加工条件的变化而变化,数值从数微米到数百微米不等。
放电间隙的控制与变化规律直接影响加工质量、加工稳定性和加工效率。
(4)工具电极制备困难。
要加工出尺寸很小的微小孔和微细型腔,必须先获得比其更小的微细工具电极。
线电极电火花磨削(WIRE ELECTRICAL DISCHARGE GRINDING WEDG) 出现以前,微细电极的制造与安装一直是制约微细电火花加工技术发展的瓶颈问题。
从目前的应用情况来看,采用WEDG技术能很好地解决微细工具电极的制备问题。
为了获得极细的工具电极,要求具有高精度的WEDG系统,同时还要求电火花加工系统的主轴回转精度达到极高的水准,一般应控制在1μm以内。
(5)排屑困难,不易获得稳定火花放电状态。
由于微孔加工时放电面积、放电间隙很小,极易造成短路,因此欲获得稳定的火花放电状态,其进给伺服控制系统必须有足够的灵敏度,在非正常放电时能快速地回退,消除间隙的异常状态,提高脉冲利用率,保护电极不受损坏]4[。
2.2 微细电火花加工关键技术随着微细加工的不断发展,微细电火花加工技术也不断的发展,近年来微细电火花加工技术的研究使其在加工精度的提高和加工尺寸的微小化方面取得长足进展,各种新的微细电火花加工工艺不断被采用,如将微细电火花加工和微细电化学加工,激光镭射加工结合在一起的复合加工方法。
就目前来言,国际电火花技术的发展主要有以下几大关键技术:(电参数的控制等相关问题)(1) 加工精密微细化(表达有问题)(加工微细化)对于电火花微细加工而言,主要指尺寸小于300μm的轴孔、沟槽,型腔等的加工。
实现精密、微细加工的一个重要条件是加工单位(即每次放电的蚀除量)尽可能小。
而在电火花加工过程中,其加工单位只取决于单个放电脉冲的能量。
瑞士阿奇夏米尔公司的高精度线切割机床具有双丝切割交换系统。
可进行全自动穿丝,细丝直径为φ20μm可实现轮廓精度1-2m,Ra<0.05μm的加工精度。
微细电火花加工的极限能力一直是研究工作者追求的目标之一,图2.2是口本东京大学生产技术研究所的增泽隆久教授加工出的φ5μm的微细孔和φ2.5μm的微细轴,代表了当前这一领城的世界前沿水平。
图2.2 φ5μm微细孔和φ2.5μm微细轴图2.3是美国Optimation公司使用日本松下ED82型微细电火花加工机床加工出的光纤连接器,共有81个φ120μm的微细孔。
图2.3 光纤连接器微细孔阵列微细电火花加工技术不仅可加工圆孔,还可以加工各种异型孔,图2.4是德国KOCH公司加工的微方形孔,其尺寸是25μm×38μm。