第3讲-作业车间
车间安全教育培训讲义

车间安全教育培训讲义一、国家、企业安全生产遵循的方针:安全第一预防为主综合治理二、劳动者的职责1、严格遵守公司、车间规章制度和班组管理条例。
2、服从领导安排,做好本职工作。
3、熟悉岗位流程,熟悉操作细节。
4、严格按照作业指导书、安全操作规程作业。
5、要认真的做好每一项记录。
6、交接班时要认真检查本岗位的各项情况。
7、按时巡检,善于发现和解决问题并及时上报8、保持工作场所的清洁,并定期对设备进行保养。
9、正确使用和妥善保管劳动保护用品、生产工具等。
10、不违章作业、并劝阻或制止他人违章作业,对违章指挥有权拒绝执行,并及时向上级汇报。
11、发生异常事故时要及时如实地向班组长汇报,保护现场并作好详细记录。
12、对岗位商业秘密及其它非共享资源要保密,不得随意向外人泄露。
13、对公司的物资财产在本区域本岗位的流通负有安全义务,确保不发生意外。
14、按时参加公司及车间举行的各种学习培训活动、生产例会等。
三、我国为减少人为事故而采取的,在作业中作业人员的一个互相监督原则为,“四不伤害”:1.不伤害自己2.不伤害他人3.不被别人伤害4.保证他人不受伤害四、做到“三不违”:不违规操作规程不违章指挥不违反劳动纪律五、安全色和安全标志安全色:红、蓝、黄、绿红色表示禁止、停止的意思。
如禁止通行标志黄色表示注意、警告的意思。
如当心有毒有害气体蓝色表示指令、必须遵守的意思。
如必须携带矿灯绿色表示通行、安全和提供信息的意思如通行标志六、劳动者工伤的认定1.在工作时间和工作场所内,因工作原因受到.事故伤害的。
2.工作时间前后在工作场所内,从事与工作有预备性或者收尾性工作受到事故伤害的。
3.在工作时间和工作场所内,因履行工作职责受到暴力等意外伤害的。
4.因工外出期间,由于工作原因受到伤害或者发生事故下落不明的。
5.在上下班途中,受到机动车事故伤害的。
6.法律、行政法规规定应当认定为工伤的其他情形。
7.患职业病的。
七、不得认定工伤的情况:1、因犯罪或者违反治安管理伤亡的。
车间作业计划
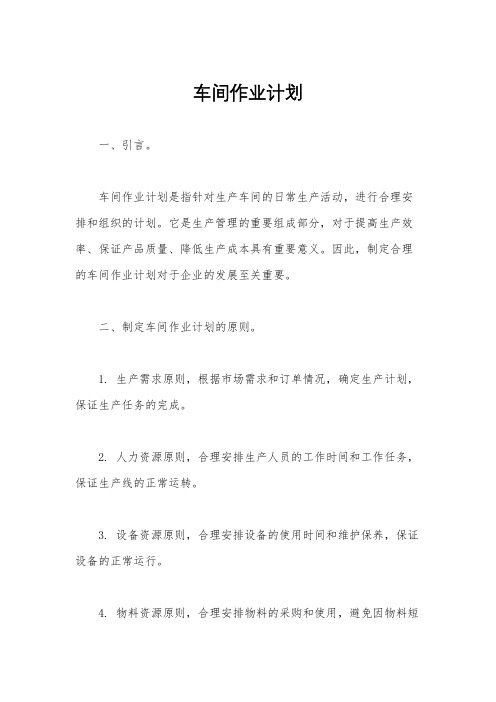
车间作业计划一、引言。
车间作业计划是指针对生产车间的日常生产活动,进行合理安排和组织的计划。
它是生产管理的重要组成部分,对于提高生产效率、保证产品质量、降低生产成本具有重要意义。
因此,制定合理的车间作业计划对于企业的发展至关重要。
二、制定车间作业计划的原则。
1. 生产需求原则,根据市场需求和订单情况,确定生产计划,保证生产任务的完成。
2. 人力资源原则,合理安排生产人员的工作时间和工作任务,保证生产线的正常运转。
3. 设备资源原则,合理安排设备的使用时间和维护保养,保证设备的正常运行。
4. 物料资源原则,合理安排物料的采购和使用,避免因物料短缺导致生产中断。
5. 安全生产原则,制定安全生产规章制度,保证生产过程中的安全。
三、车间作业计划的编制步骤。
1. 收集信息,了解市场需求、订单情况,掌握生产设备、人员、物料等资源情况。
2. 制定生产计划,根据市场需求和资源情况,确定生产计划,包括生产任务、生产数量、生产周期等内容。
3. 制定作业流程,根据生产计划,制定具体的作业流程,包括生产工艺、工序安排、作业时间等内容。
4. 分配生产任务,根据作业流程,合理分配生产任务,确定各岗位的工作内容和工作量。
5. 制定物料采购计划,根据生产计划,制定物料采购计划,保证生产所需物料的供应。
6. 制定设备维护计划,根据生产计划,制定设备维护计划,保证设备的正常运行。
7. 制定安全生产计划,根据生产计划,制定安全生产计划,加强对生产过程中的安全管理。
四、车间作业计划的执行与监督。
1. 生产任务分配,根据生产计划,合理分配生产任务,明确各岗位的工作内容和工作量。
2. 生产过程监督,加强对生产过程的监督,及时发现和解决生产中的问题。
3. 生产效率评估,定期对生产效率进行评估,发现问题及时调整生产计划。
4. 安全生产检查,定期进行安全生产检查,确保生产过程中的安全。
五、车间作业计划的优化。
1. 数据分析,根据生产数据,分析生产效率和成本情况,发现问题并进行优化。
员工三级安全教育之车间级安全培训

员工三级安全教育之车间级安全培训尊敬的车间员工:大家好!今天我们来讲一下车间级安全培训。
首先,请大家认真阅读岗位操作手册,掌握安全操作规范。
其次,我们需要注意以下几个方面:一、安全用电首先说说安全用电,一定要遵循电安全操作规范,并保持用电区整洁,在使用电器前要检查电器是否完好,电源线是否损坏。
维修电器时,要切断电源,并有专业的人员操作。
同时,要定期进行检修和保养,发现问题及时处理。
重要的是,不要随意接电源,不要在电器周围摆放易燃物品。
二、危化品安全危化品是企业生产和发展过程中都不可避免的重要物品,但在使用和储存时也容易引发事故,所以必须要严格遵守规定,保证安全。
危化品管理要求:1、必须用专业包装容器包装。
2、仓库必须划定安全区域,放置警示标志。
3、仓库要定期巡视,发现问题及时处理。
4、不得抽烟、不得打火、不得使用明火。
5、严谨记录用药及改变情形,保持档案完整,做到安全管理的一个细节。
三、机械安全机械作为生产设备的重要组成部分,也很容易发生事故。
因此,机械操作员要熟悉操作规范,掌握安全操作技能和日常维护。
1、上手操作前,应仔细了解设备的性能、特点和操作步骤。
2、在生产过程中,要时刻关注设备运行情况,及时发现并消除隐患。
3、清洁维护设备时,必须先切断电源并使用专业工具。
4、严格遵守设备使用中的安全规范和操作规程,严禁违反安全规定。
5、设备停止工作前,必须切断电源,确保设备处于安全状态。
四、环境安全环境安全是企业综合安全管理的一个方面。
现代生产活动已经对环境产生了很大的影响,保护环境,减少对环境的污染是企业必须承担的重要责任。
1、严格控制废水、废气、废物的排放和处理。
2、库房、车间等的清洁卫生要求高,保持环境干净整洁。
3、增强垃圾的分类、收集,做好环保处理。
4、危险品的存放、使用,必须有专业人士指导,不能随意处置。
四、安全教育企业安全管理离不开员工自觉参与,只有加强员工安全教育,增强员工的安全自我保护意识,才能营造良好的安全环境。
生产车间现场管理培训课件(PPT 44页)
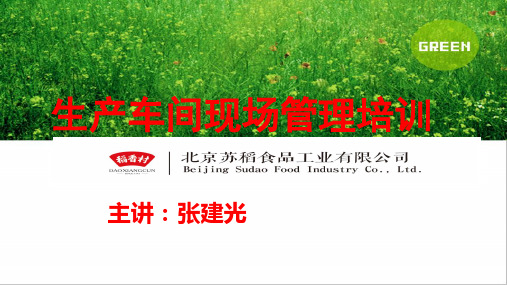
A
P
C
D
P(Plan) ——计划阶段 D(Do) ——执行阶段 C(Check)——检查阶段 A(Action)——处理阶段
三、生产现场的质量控制
1、在全面质量管理中使用PDCA循环法
阶段
步
骤
P 1、分析现状,找出问题 2、找出产生问题的原因或影响因素 3、找出原因中的主要原因 4、针对主要原因,制定解决问题的方案
一、优秀现场管理的标准和要求
一、优秀现场管理的标准和要求
3、现场管理六要素(5M1E分析法)
现场管理的六个要素即:人、机、料、法、环、测。 ----也称为5M1E分析法。
1) 人(Man):操作者对质量的认识、技术、身体状况等; 2) 机器(Machine):设备、测量仪器的精度和维护保养状况等; 3) 材料(Material):材料能否达到要求的性能等; 4) 方法(Method):生产工艺、设备选择、操作规程等; 5) 测量(Measurement):测量时采取的方法是否标准、正确; 6) 环境(Environment):工作现场的技术要求和清洁条件等; 由于这五个因素的英文名称的第一个字母是M和E,简称为5M1E。
D 5、按制定的计划认真执行 C 6、检查措施执行的效果 A 7、巩固提高,总结成功经验
8、把未解决或新出现的问题转入下一循环
主要方法和内容
调查表、分层法、排列图 因果图 排列图、相关图等 预期达到的目的(What) 在哪里执行措施(Where) 由谁来执行(Who) 何时开始和完成(When) 如何执行(How)
高企业经济效益。
二、现场管理的基本方法
(二)、作业标准化
3、标准的制定要求: 1)、目标指向:即遵循标准总是能保持生产出相同品
车间安全管理作业指引
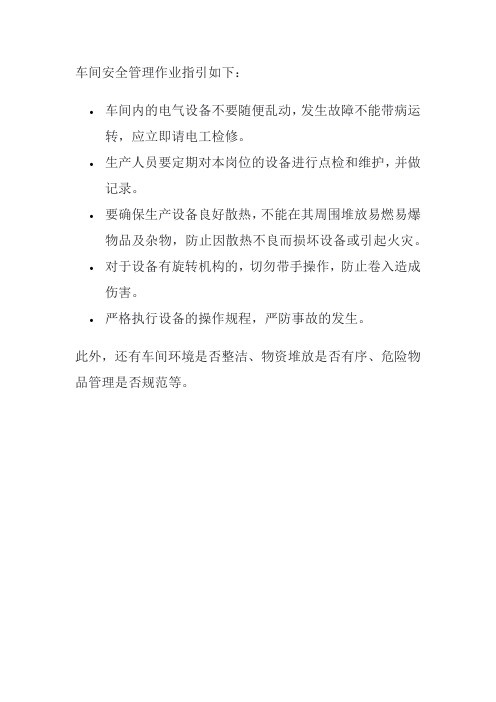
车间安全管理作业指引如下:
•车间内的电气设备不要随便乱动,发生故障不能带病运转,应立即请电工检修。
•生产人员要定期对本岗位的设备进行点检和维护,并做记录。
•要确保生产设备良好散热,不能在其周围堆放易燃易爆物品及杂物,防止因散热不良而损坏设备或引起火灾。
•对于设备有旋转机构的,切勿带手操作,防止卷入造成伤害。
•严格执行设备的操作规程,严防事故的发生。
此外,还有车间环境是否整洁、物资堆放是否有序、危险物品管理是否规范等。
企业车间安全教育内容

企业车间安全教育内容企业车间是生产经营活动所进行的重要场所,车间安全教育是保障生产经营安全和员工身体健康的重要环节。
为了提高企业员工的安全意识和操作技能,保障车间生产经营活动的顺利进行,企业需要对员工进行系统的安全教育。
车间安全教育内容的设计应该结合企业实际情况,包括车间的生产特点、作业环境、设备设施等因素,综合考虑员工的基本素质、文化程度、工作经验等方面,制定出适合企业自身的车间安全教育内容。
首先,企业车间安全教育应该注重宣传和普及安全知识。
通过开展安全知识的宣传教育活动,让员工了解企业车间生产经营活动中存在的各种安全隐患,并掌握预防和避免事故的基本知识和技能。
在安全宣传教育中,可以结合企业实际情况,设置场景化、具体化的案例分析,引导员工认识到安全问题的重要性,增强其安全意识。
其次,企业车间安全教育还应该强调岗位安全培训。
不同岗位的员工所从事的工作内容和操作对象不同,对于不同岗位的员工,企业应该根据其特点和工作内容,针对性地进行安全教育培训。
通过针对性的培训,让员工熟悉自己的工作环境和操作要求,掌握岗位操作技能,提高其处理突发事件和紧急情况的应对能力。
此外,企业还可以借助专家学者等资源,开展一些特定领域的专业培训,提升员工的专业知识和技能水平。
再次,企业车间安全教育内容还应包括紧急情况处理和逃生演练。
在实际生产经营活动中,突发事故和紧急情况时有发生,员工应该具备处理突发事件的应急能力和逃生自救的技能。
因此,在安全教育内容中可以设置各种紧急情况的处理流程和逃生通道,进行实地模拟演练,让员工亲身体验紧急情况下的应对方式,增强其应急处理能力和自救意识。
此外,企业车间安全教育还应注重实践操作和技能培训。
安全教育不仅要求员工掌握安全理论知识,更需要他们能够将理论知识应用到实际操作中。
因此,企业可以通过实际操作和技能培训课程,让员工学会正确使用安全防护装备和设施,掌握各类设备的操作技巧,提高其操作风险防范和事故处理能力。
车间作业流程

车间作业流程
车间作业流程是指在生产车间中,为了保证生产作业的顺利进行,按照一定的程序和规范进行生产作业的一系列流程。
良好的车间作业流程能够提高生产效率,保证产品质量,降低生产成本,是企业生产管理中非常重要的一环。
首先,车间作业流程的第一步是生产计划的制定。
生产计划是车间作业流程的基础,它是根据市场需求、原材料供应情况、设备状况等因素制定的生产指导方案。
生产计划需要明确生产的数量、时间、质量要求等内容,以便为后续的生产作业提供指导和依据。
第二步是生产准备。
生产准备包括设备的检查和维护,原材料的准备,人员的安排等工作。
只有做好了充分的生产准备工作,才能保证生产作业的顺利进行。
第三步是生产作业。
生产作业是车间作业流程的核心环节,包括原材料的加工、半成品的生产、成品的组装等工序。
在生产作业中,需要严格按照生产计划和作业指导书进行操作,确保产品质量和生产效率。
第四步是质量检验。
质量检验是车间作业流程中非常重要的一环,它直接关系到产品的质量和客户满意度。
在质量检验环节,需
要对产品进行全面的检查和测试,确保产品符合质量标准。
最后一步是成品入库。
经过质量检验合格的产品,将会被安排
入库。
在入库环节,需要对产品进行包装、标识,并将其妥善存放,以便后续的发货和销售。
总之,良好的车间作业流程能够提高生产效率,保证产品质量,降低生产成本。
企业应该不断优化车间作业流程,提高管理水平,
以适应市场的需求变化,从而获得更好的经济效益。
车间安全生产培训内容

车间安全生产培训内容引言车间安全生产培训是企业进行安全生产的基础工作之一,不仅可以提高员工的安全生产意识和技能,也能预防和减少事故的发生,保障员工人身安全和企业生产安全。
本文将介绍车间安全生产培训的内容。
车间安全生产培训内容安全生产法律法规车间安全生产培训的第一步是学习国家和地区的安全生产法律法规。
安全生产法律法规的内容包括了安全生产的基本原则、安全生产的监督和管理、安全生产的责任制度等。
企业要求员工了解安全法规和标准,以确保企业的安全生产符合要求。
安全操作规程根据生产流程和作业环节,车间必须制定并实施相关的安全操作规程,以确保员工的安全。
安全操作规程包括使用设备的操作规程、紧急处理程序、防护措施和个人防护用品的适用等。
安全生产知识车间安全生产培训的另一个重要内容是安全生产知识。
安全生产知识主要包括生产设备的安全、生产场所的安全、个人保护等方面。
员工需要了解如何应对生产中的突发事件和如何避免生产中可能发生的事故。
需要注意的是,随着技术的进步,工作环境和安全生产知识也会在不断变化,需要定期更新和培训。
应急预案应急预案是企业应对生产事故或突发事件的重要工具。
培训内容应包括如何制定应急预案、如何实施应急预案、员工应急知识以及应急演练等方面。
安全生产责任安全生产是企业的重要责任,也是每个员工的责任。
安全生产培训必须加强员工的安全生产责任意识培养,强调每个员工在车间和工作岗位上的安全责任。
车间安全生产培训内容主要包括安全生产法律法规、安全操作规程、安全生产知识、应急预案和安全生产责任等方面。
企业应根据自身的生产情况和员工特点,制定针对性的培训计划和内容,以提高员工的安全生产意识和技能,预防和减少事故的发生,保障员工人身安全和企业生产安全。
生产车间管理制度_3

生产车间管理制度生产车间管理制度1为了进一步规范车间的现场管理,营造一个整洁,干净的生产工作环境,细化管理,提高员工自我安全文明生产意识,特制如下规定:1 、生产部班/组长及生产项目负责人为车间现场管理的主要负责人,要保持工作场地、门窗、走道等场所及配电箱等设施的整洁卫生,建立管理责任卡,责任到人,部门主管负责监督。
(卫生区域按项目分,各生产项目负责人负责)2 、各班班组卫生区须保持整洁,生产巡检定期检查。
对不合格的班组或个人根据《车间现场管理奖惩细则》的规定处罚。
3 、每周五下班前半小时为车间统一大扫除时间,生产管理者负责监督,设置监督小组对大扫除情况进行检查、评比,好的给予表扬,不好的给予批评,对于表现极差的班组负责人要处罚。
4 、工作台和货架上的物品摆放要整齐,不准摆放水杯、饮料、零食、衣物等与工作无关的物品,保持工作台机器设备(包括地面、机架等)的干净。
5 、生产半成品、成品、待装物品(需有标识)要摆放整齐,不能直接放在地上或拖及地面,保证半成品、成品的干净、整洁及包装分类存放。
6 、装配车间内各种设施(清洁工具、液压车、洗地车等)按要求摆放,使用后应及时归位并保持干净。
7 、文明生产、严禁随地吐痰,严禁大声喧哗,严禁打斗殴。
8 、安全生产,消防通道在工作时间必须保持畅通,保证消防栓、灭火器等消防设施的整洁卫生和完好无损。
9、装配作业时,如遇到需要吊装或大型登高作业组装时,必须佩戴安全帽,安全带等安全用品。
10、装配车间照明、空调按区域分,在没有人员工作的情况下及时关闭,下班前最后离开人员检查车间照明及空调是否关闭。
11 、因操作不当或违反操作规程损坏机器(零件、标准件、电器元件)按损失价值的10%-20%罚款。
12 、工作时间按规定穿戴工作卡、工作装、劳保鞋,严禁在车间厕所内抽烟、酗酒,上班时间原则上不准会客,特殊情况须批准,工作时间不准带小孩子,严禁工作时间串岗,睡觉、看报刊和玩手机,做私活等无关生产的活动。
车间作业流程

车间作业流程车间作业流程是指企业在生产过程中,对车间内各项作业进行规范、科学地组织和安排,以达到提高生产效率、保障产品质量、降低生产成本的目的。
良好的车间作业流程不仅可以提高生产效率,还可以减少资源浪费,提高产品质量,增强企业竞争力。
下面将从车间作业流程的规划、执行和改进三个方面进行详细介绍。
一、规划。
1.确定作业流程。
首先要确定车间内各项作业的流程,包括原材料的采购、加工制造、产品检验、包装装运等环节。
在确定作业流程时,需要考虑生产设备的布局、作业人员的配备以及作业流程中可能出现的问题,确保整个流程顺畅高效。
2.制定作业标准。
针对每一个作业环节,制定相应的作业标准,包括作业流程、作业要求、作业时间等,确保每个环节都能按照标准进行操作,提高作业的准确性和稳定性。
二、执行。
1.作业指导。
在确定了作业流程和作业标准后,需要对作业人员进行详细的指导和培训,确保他们能够熟练掌握作业流程和操作技能,提高作业效率和产品质量。
2.作业监控。
对作业流程进行实时监控,及时发现问题并进行调整。
通过设备监控系统、作业记录等手段,对作业流程进行全面监控,确保作业按照标准进行,及时发现问题并进行处理。
三、改进。
1.持续优化。
车间作业流程需要不断进行优化改进,根据生产实际情况和市场需求,及时对作业流程进行调整和优化,提高生产效率和产品质量。
2.问题分析。
对作业流程中出现的问题进行分析,找出问题的根源并进行改进。
通过对问题进行深入分析,找出问题的原因,采取相应的改进措施,确保类似问题不再发生。
3.经验总结。
对车间作业流程进行经验总结,形成规范化的作业流程和管理模式。
通过总结经验,不断积累和提炼出适合企业实际的作业流程和管理经验,为企业的持续发展提供有力支持。
总结。
良好的车间作业流程对企业的生产经营至关重要。
通过规划、执行和改进三个方面的工作,可以建立科学规范的作业流程,提高生产效率、产品质量和企业竞争力,实现可持续发展的目标。
车间作业计划

车间作业计划车间作业计划是指车间在一定时间内,按照生产任务和生产计划,合理安排生产作业流程和生产资源,以达到高效、高质、低耗的生产目标。
制定和执行良好的车间作业计划对于提高生产效率、降低生产成本、保障产品质量具有重要意义。
下面将从计划制定、执行过程和效果评估三个方面来分析车间作业计划的重要性和实施方法。
首先,制定车间作业计划需要充分考虑生产任务和生产资源的情况。
在制定计划时,首先要了解车间的生产任务,包括生产数量、生产周期、产品质量要求等。
其次要充分了解车间的生产资源情况,包括人力、设备、原材料等。
只有充分了解生产任务和生产资源的情况,才能制定出合理可行的作业计划。
在制定计划时,还要考虑生产过程中可能出现的风险和问题,提前做好预案和对策,以应对突发情况,确保生产顺利进行。
其次,执行车间作业计划需要严格按照计划进行。
在执行过程中,车间管理人员要对生产作业流程和生产资源进行有效调度和协调,确保生产作业按照计划有序进行。
同时要及时发现和解决生产过程中出现的问题,确保生产过程稳定、高效。
在执行过程中,要做好生产数据的收集和记录,及时了解生产情况,为后续生产提供参考依据。
最后,需要对车间作业计划的执行效果进行评估。
在生产任务完成后,要对计划执行情况进行全面评估,包括生产效率、生产质量、生产成本等方面。
通过评估,找出计划执行中存在的问题和不足,总结经验,完善计划,提高下一阶段的生产效果。
综上所述,车间作业计划的制定和执行对于提高生产效率、降低生产成本、保障产品质量具有重要意义。
只有合理制定计划,严格执行计划,并对计划执行效果进行评估,才能不断提高车间生产的效率和质量,为企业的发展提供有力支持。
因此,车间管理人员要重视车间作业计划的制定和执行,不断完善和提高计划的质量,以适应市场的需求,提升企业的竞争力。
车间安全会议讲话稿7篇
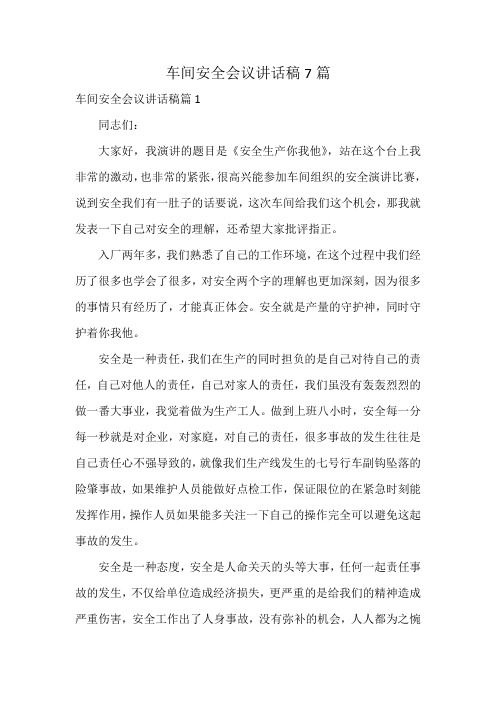
车间安全会议讲话稿7篇车间安全会议讲话稿篇1同志们:大家好,我演讲的题目是《安全生产你我他》,站在这个台上我非常的激动,也非常的紧张,很高兴能参加车间组织的安全演讲比赛,说到安全我们有一肚子的话要说,这次车间给我们这个机会,那我就发表一下自己对安全的理解,还希望大家批评指正。
入厂两年多,我们熟悉了自己的工作环境,在这个过程中我们经历了很多也学会了很多,对安全两个字的理解也更加深刻,因为很多的事情只有经历了,才能真正体会。
安全就是产量的守护神,同时守护着你我他。
安全是一种责任,我们在生产的同时担负的是自己对待自己的责任,自己对他人的责任,自己对家人的责任,我们虽没有轰轰烈烈的做一番大事业,我觉着做为生产工人。
做到上班八小时,安全每一分每一秒就是对企业,对家庭,对自己的责任,很多事故的发生往往是自己责任心不强导致的,就像我们生产线发生的七号行车副钩坠落的险肇事故,如果维护人员能做好点检工作,保证限位的在紧急时刻能发挥作用,操作人员如果能多关注一下自己的操作完全可以避免这起事故的发生。
安全是一种态度,安全是人命关天的头等大事,任何一起责任事故的发生,不仅给单位造成经济损失,更严重的是给我们的精神造成严重伤害,安全工作出了人身事故,没有弥补的机会,人人都为之惋惜。
自从我们上班以来我们看到曾经睡在一起的兄弟一个又一个的受到伤害,在痛心的同时我们感到的是惋惜,那些场景让人感到窒息,我们看到受到打击受到伤害的不是一个人,生命不仅属于你自己。
生命属于你的妻儿、你的父母和所有关心你爱护你的同事朋友们。
珍爱生命,杜绝安全责任事故的发生,就是给企业、家庭创造的最大财富。
(安全就是一切。
有的人说这话说得大了,安全怎么可能就是一切呢?大家都可以想到:没有安全,我们的生命有保障吗?我们的企业效益有保障吗?我们的队伍稳定有保障吗?说得实在一点,保证不了安全,我们谈什么家庭幸福?谈什么个人理想?)在我们最近学习的事故中,炼铁厂搅拌机突然转动致人死亡的案例告诉我们操作前的确认,和自我的安全防护意识是多么的重要,工作中的细心和精心,工作时的一丝不苟,严格按操作规程办事,遵守一切规章制度,从我做起,从现在做起,从日常生产工作中的每件小事做起,杜绝违章作业,是生产工作得以正常进行,减少和杜绝一切安全事故的前提。
车间作业计划的编制

车间作业计划的编制1. 引言车间作业计划是指在生产车间中,根据生产计划和资源情况,合理安排生产过程和时间的一项重要工作。
编制一个完善的车间作业计划,能够提高生产效率,降低成本,确保生产任务的顺利完成。
本文将介绍车间作业计划的编制过程和注意事项。
2. 编制车间作业计划的步骤2.1 确定生产需求首先,需要明确生产的需求,包括生产的产品种类、数量、交付时间等。
这些信息可以根据市场需求、销售订单或上级部门的安排来确定。
2.2 分析生产资源在编制车间作业计划之前,需要对生产资源进行全面的分析,包括人力资源、设备资源、原材料等。
根据资源的可用性和能力,制定合理的生产计划。
2.3 制定生产顺序根据生产的产品种类和数量,以及生产设备的情况,制定生产顺序。
合理的生产顺序能够减少生产过程中的等待时间和交叉干扰,提高生产效率。
2.4 安排生产时间根据制定的生产顺序和生产设备的利用率,安排生产时间。
要考虑到生产设备的维护和保养时间,确保生产能够按计划进行。
2.5 分配任务和资源根据制定的生产计划,分配任务和资源给相关的生产人员。
要合理安排每个人的工作量,确保任务能够按时完成。
2.6 跟踪和调整在生产过程中,需要不断跟踪生产进度,及时发现和解决问题。
如果出现生产延误或其他紧急情况,需要及时调整生产计划,保证生产任务能够顺利完成。
3. 车间作业计划的注意事项3.1 灵活性车间作业计划应具备一定的灵活性,能够适应市场需求的变化和生产资源的变动。
在编制计划时,要考虑到可能的变动因素,并制定相应的应对措施。
3.2 合理利用资源在编制车间作业计划时,要合理利用现有的生产资源。
要充分考虑各种资源的可用性和利用率,避免资源的浪费和闲置。
3.3 人力培训为了能够顺利执行车间作业计划,需要对相关的生产人员进行培训。
培训内容包括生产流程、操作规范、安全措施等。
只有工作人员具备必要的技能和知识,才能保证计划的顺利实施。
3.4 安全生产在制定车间作业计划时,要充分考虑安全生产因素。
车间安全管理知识讲座
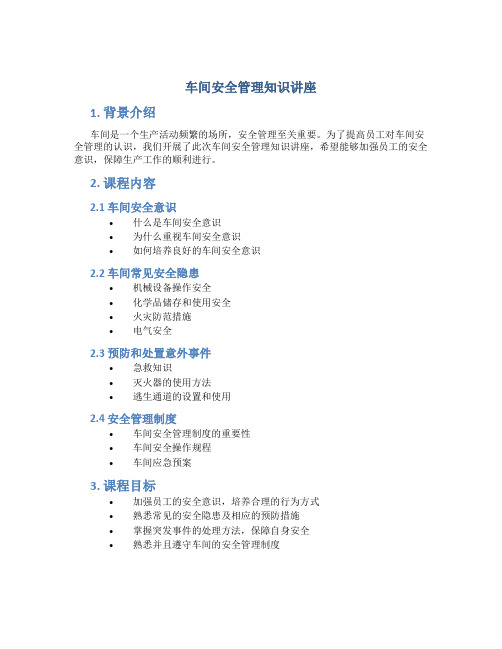
车间安全管理知识讲座
1. 背景介绍
车间是一个生产活动频繁的场所,安全管理至关重要。
为了提高员工对车间安全管理的认识,我们开展了此次车间安全管理知识讲座,希望能够加强员工的安全意识,保障生产工作的顺利进行。
2. 课程内容
2.1 车间安全意识
•什么是车间安全意识
•为什么重视车间安全意识
•如何培养良好的车间安全意识
2.2 车间常见安全隐患
•机械设备操作安全
•化学品储存和使用安全
•火灾防范措施
•电气安全
2.3 预防和处置意外事件
•急救知识
•灭火器的使用方法
•逃生通道的设置和使用
2.4 安全管理制度
•车间安全管理制度的重要性
•车间安全操作规程
•车间应急预案
3. 课程目标
•加强员工的安全意识,培养合理的行为方式
•熟悉常见的安全隐患及相应的预防措施
•掌握突发事件的处理方法,保障自身安全
•熟悉并且遵守车间的安全管理制度
4. 课程安排
•日期:XX年XX月XX日
•时间:上午9:00-12:00
•地点:XXX车间
5. 参与对象
•XXX车间所有员工
6. 教学方式
•讲座形式
•互动式教学
7. 效果评估
•通过问卷调查以及实际操作来评估员工对车间安全管理知识的掌握情况
•定期组织安全演练,加强员工应急处理能力
经过此次车间安全管理知识讲座的学习,相信员工们的安全意识将得到提高,工作安全环境也将更加有保障。
希望大家能够时刻关注安全,做到安全第一,预防事故的发生。
感谢大家的参与!。
化工三级安全培训教育课件(车间级)

❖违规作业
主要是指工人违反劳动生产岗位的安全规章和制度(如安全生产责任
制、安全操作规程、工作交接制度等)的作业行为。违规作业具体包
括:不正确使用个人劳动保护用品、不遵守工作场所的安全操作规程
和不执行安全生产指令。
❖违反劳动纪律
预防为主
综合治理
第二章 工作环境危险因素及可能遭受的职业伤害和伤亡事故
主要是指工人违反生产经营单位的劳动纪律的行为。违反劳动纪律具 体包括:不履行劳动合同及违约承担的责任,不遵守考勤与休假纪律、 生产与工作纪律、奖惩制度及其他纪律等。
第一章 前 言
第一章 前 言 安全第一
什么是安全?什么是安全生产?
在古代汉语中,并没有“安全”一词,但“安”字却在许多场合下
表达着现代汉语中“安全”的意义,表达了人们通常理解的“安全”
这一概念。例如,“是故君子安而不忘危,存而不忘亡,治而不忘乱,
是以身安而国家,可保也。”《易·系辞下》这里的“安”是与“危” 相对的,并且如同“危”表达了现代汉语的“危险”一样,“安”所
安全第一
预防为主
2℃以上的作业(含夏季通风室外计算温度≥30℃地区的露天作业,不含
预防为主
综合治理
第二章 工作环境危险因素及可能遭受的职业伤害和伤亡事故
矿井下作业)。 职业性中暑是在高温作业环境下,由于热平衡和(或)水盐代谢紊乱而 引起的以中枢神经系统和(或)心血管障碍为主要表现的急性疾病。 1、轻症中暑 2、重症中暑 3、热射病 4、热痉挛 5、热衰竭
安全第一
预防为主
综合治理
第一章 前 言 安全第一
什么是安全?什么是安全生产?
如果有人问我安全是什么的话? 我会告诉他,安全就是幸福、是快乐、是健康、是生命。 说安全是幸福,是因为安全成就了平安,它给我们每一个家庭 带来了欢笑; 说安全是快乐,是因为安全给了我们享受生活的激情和希望; 说安全是健康,是因为安全赋予了我们健康的体魄,让我们去 实现心中的理想; 说安全是生命,因为生命创造了世界,生命创造了人类历史。 生命对我们每个人来说只有一次,千万不要拿这唯一的一次 作赌注!
车间生产安全教育知识
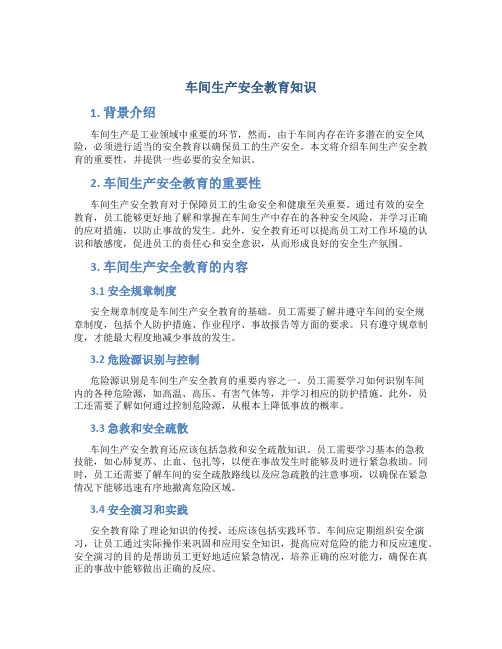
车间生产安全教育知识1. 背景介绍车间生产是工业领域中重要的环节,然而,由于车间内存在许多潜在的安全风险,必须进行适当的安全教育以确保员工的生产安全。
本文将介绍车间生产安全教育的重要性,并提供一些必要的安全知识。
2. 车间生产安全教育的重要性车间生产安全教育对于保障员工的生命安全和健康至关重要。
通过有效的安全教育,员工能够更好地了解和掌握在车间生产中存在的各种安全风险,并学习正确的应对措施,以防止事故的发生。
此外,安全教育还可以提高员工对工作环境的认识和敏感度,促进员工的责任心和安全意识,从而形成良好的安全生产氛围。
3. 车间生产安全教育的内容3.1 安全规章制度安全规章制度是车间生产安全教育的基础。
员工需要了解并遵守车间的安全规章制度,包括个人防护措施、作业程序、事故报告等方面的要求。
只有遵守规章制度,才能最大程度地减少事故的发生。
3.2 危险源识别与控制危险源识别是车间生产安全教育的重要内容之一。
员工需要学习如何识别车间内的各种危险源,如高温、高压、有害气体等,并学习相应的防护措施。
此外,员工还需要了解如何通过控制危险源,从根本上降低事故的概率。
3.3 急救和安全疏散车间生产安全教育还应该包括急救和安全疏散知识。
员工需要学习基本的急救技能,如心肺复苏、止血、包扎等,以便在事故发生时能够及时进行紧急救助。
同时,员工还需要了解车间的安全疏散路线以及应急疏散的注意事项,以确保在紧急情况下能够迅速有序地撤离危险区域。
3.4 安全演习和实践安全教育除了理论知识的传授,还应该包括实践环节。
车间应定期组织安全演习,让员工通过实际操作来巩固和应用安全知识,提高应对危险的能力和反应速度。
安全演习的目的是帮助员工更好地适应紧急情况,培养正确的应对能力,确保在真正的事故中能够做出正确的反应。
4. 车间生产安全教育的推广与落实为了确保车间生产安全教育的有效推广和落实,需要采取一系列措施:•制定明确的安全教育计划,确保教育内容全面、有针对性;•建立健全的安全教育体系,包括培训课程、教材等资源;•配备专业的安全教育教师,提供专业化的安全教育培训;•定期开展安全教育活动,如安全讲座、安全知识竞赛等,提高员工的参与度和学习兴趣;•审查和改进安全教育效果,不断优化教育内容和方式。
车间安全教育内容
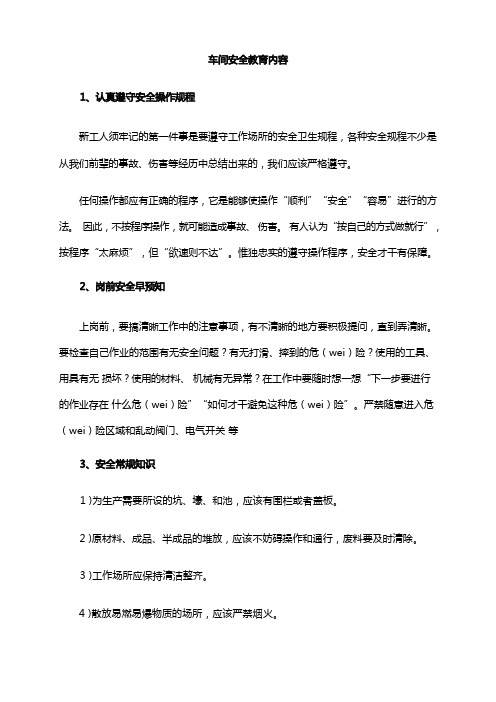
新工人须牢记的第一件事是要遵守工作场所的安全卫生规程,各种安全规程不少是从我们前辈的事故、伤害等经历中总结出来的,我们应该严格遵守。
任何操作都应有正确的程序,它是能够使操作“顺利”“安全”“容易”进行的方法。
因此,不按程序操作,就可能造成事故、伤害。
有人认为“按自己的方式做就行”,按程序“太麻烦”,但“欲速则不达”。
惟独忠实的遵守操作程序,安全才干有保障。
上岗前,要搞清晰工作中的注意事项,有不清晰的地方要积极提问,直到弄清晰。
要检查自己作业的范围有无安全问题?有无打滑、摔到的危(wei)险?使用的工具、用具有无损坏?使用的材料、机械有无异常?在工作中要随时想一想“下一步要进行的作业存在什么危(wei)险”“如何才干避免这种危(wei)险”。
严禁随意进入危(wei)险区域和乱动阀门、电气开关等1 )为生产需要所设的坑、壕、和池,应该有围栏或者盖板。
2 )原材料、成品、半成品的堆放,应该不妨碍操作和通行,废料要及时清除。
3 )工作场所应保持清洁整齐。
4 )散放易燃易爆物质的场所,应该严禁烟火。
5 )对于易燃、易爆、烧灼及有静电发生的场所作业的工人,禁止发放和使用化纤防护服及用品。
( 1 )电气路线、设备安装不符合安全要求。
( 2 )非电工任意处理电气事务。
( 3 )挪移长、高金属物体碰触电源线、配电柜及其他带电体。
( 4 )操作漏电的机器设备或者使用漏电电动工具。
( 5 )电钻等手持电动工具电源线破损或者松动。
( 6 )电焊作业者穿背心、短裤,不穿绝缘鞋;汗水浸透手套;焊钳误碰自身。
( 6 )湿手操作机器开关、按钮等。
( 7 )暂时线使用或者管理不善。
( 8 )配电设备、架空路线、电缆、开关、配电箱等电气设备,在长期使用中,受高温、高湿、粉尘、碾压、磨擦、腐蚀等,使电气绝缘损坏,接地或者接零保护不良而导致漏电。
( 9 )接线盒或者插头座不合格或者损坏。
( 1 )检修检查机械忽视安全措施。
如人进入设备检修、检查作业不切断电源,未挂不许合闸警示牌,未设专人监护等措施而造成严重后果。
“三讲一落实”活动管理办法
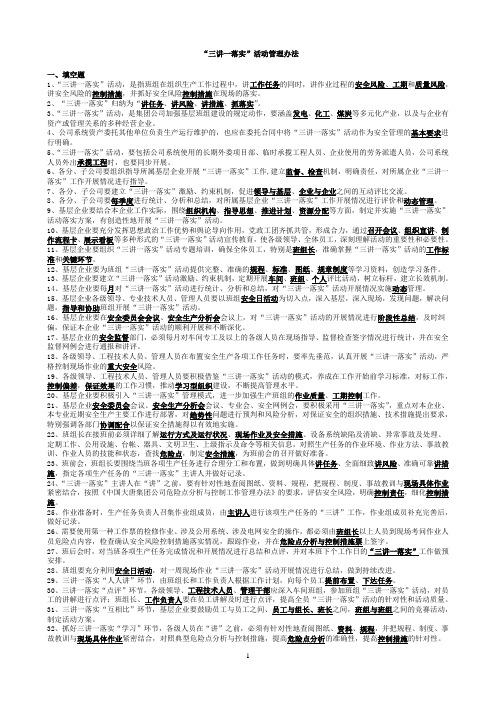
“三讲一落实”活动管理办法一、填空题1、“三讲一落实”活动,是指班组在组织生产工作过程中,讲工作任务的同时,讲作业过程的安全风险、工期和质量风险,讲安全风险的控制措施,并抓好安全风险控制措施在现场的落实。
2、“三讲一落实”归纳为“讲任务、讲风险、讲措施、抓落实”。
3、“三讲一落实”活动,是集团公司加强基层班组建设的规定动作,要涵盖发电、化工、煤炭等多元化产业,以及与企业有资产或管理关系的多种经营企业。
4、公司系统资产委托其他单位负责生产运行维护的,也应在委托合同中将“三讲一落实”活动作为安全管理的基本要求进行明确。
5、“三讲一落实”活动,要包括公司系统使用的长期外委项目部、临时承揽工程人员、企业使用的劳务派遣人员,公司系统人员外出承揽工程时,也要同步开展。
6、各分、子公司要组织指导所属基层企业开展“三讲一落实”工作,建立监督、检查机制,明确责任,对所属企业“三讲一落实”工作开展情况进行指导。
7、各分、子公司要建立“三讲一落实”激励、约束机制,促进领导与基层、企业与企业之间的互动评比交流。
8、各分、子公司要每季度进行统计、分析和总结,对所属基层企业“三讲一落实”工作开展情况进行评价和动态管理。
9、基层企业要结合本企业工作实际,围绕组织机构、指导思想、推进计划、资源分配等方面,制定并实施“三讲一落实”活动落实方案,有创造性地开展“三讲一落实”活动。
10、基层企业要充分发挥思想政治工作优势和舆论导向作用,党政工团齐抓共管,形成合力,通过召开会议、组织宣讲、制作流程卡、展示看板等多种形式的“三讲一落实”活动宣传教育,使各级领导、全体员工,深刻理解活动的重要性和必要性。
11、基层企业要组织“三讲一落实”活动专题培训,确保全体员工,特别是班组长,准确掌握“三讲一落实”活动的工作标准和关键环节。
12、基层企业要为班组“三讲一落实”活动提供完整、准确的规程、标准、图纸、规章制度等学习资料,创造学习条件。
13、基层企业要建立“三讲一落实”活动激励、约束机制,定期开展车间、班组、个人评比活动,树立标杆,建立长效机制。
- 1、下载文档前请自行甄别文档内容的完整性,平台不提供额外的编辑、内容补充、找答案等附加服务。
- 2、"仅部分预览"的文档,不可在线预览部分如存在完整性等问题,可反馈申请退款(可完整预览的文档不适用该条件!)。
- 3、如文档侵犯您的权益,请联系客服反馈,我们会尽快为您处理(人工客服工作时间:9:00-18:30)。
西安交通大学管理学院第二讲作业车间调度授课教师:高杰西安交通大学管理学院工业工程系11/13/2015Job-shop Scheduling Problem1.Introduction2.JSP Mathematical / Graph Models2.1 Integer Programming Model2.2 Linear Programming Model2.3 Disjunctive Graph Model3.Conventional Heuristics for JSP3.1 Priority Dispatching Heuristics3.2 Shifting Bottleneck Heuristic3.3 Randomized Dispatching Heuristics1. Introduction☐Determining the operation sequences on the machines in order to minimize the makespan.⏹There are n different jobs to be scheduled on mdifferent machines.⏹Each job is composed of a set of operations and theoperation order of each job is prespecified.⏹Each operation is characterized by the requiredmachine and the fixed processing time.☐Makespan: find the sequence of jobsminimizing the maximum flow time.1. IntroductionAssumptions for JSP models1.There are a set of jobs and a set of machines.2.Each job consists of sequence of operations.3.Each machine can processes at most one operation at a time.4. A operation does not visit the same machines twice.5.The processing time of each operation has been determined.6.There are no precedence constraints among operations ofdifferent jobs.7.Any operation cannot be interrupted.8.Neither release times nor due dates are specified.Simple Example of JSPFor showing a feasible schedule, there are two Gantt charts : machine Gantt chart and job Gantt chart312332312232111323351233321Job 321Job Operations Operations Sequence Machine TimeProcessing M M M J J M M M J J M M M J J Example of a 3-Job 3-machine ProblemFig.13.15Machine Gantt chartO 33O 13O 23O 22O 12O 32O 31O 11O 21M 1M 2M 3121110987654321time O 13O 12O 11O 33O 31O 32O 22O 23O 21J 1J 2J 3121110987654321Fig.13.16Job Gantt chart timeJob-shop Scheduling Problem1. Introduction2.JSP Mathematical / Graph Models2.1 Integer Programming Model2.2 Disjunctive Graph Model2.3 Mathematical Model (n-job m-machine)2.4 Simple Example of JSP3. Conventional Heuristics for JSP4. Genetic Algorithms for JSP5. Gen-Tsujimura-Kubota’s Method6. Cheng-Gen-Tsujimura’s Method☐Notations⏹Indicesi , j : index of jobs , i , j = 1,2,…nh , k : index of machines, h , k = 1,2,…m⏹Parameters n : total number of jobsm : total number of machinesp jk : processing time of job j on machine k ⏹Decision Variables2.1 Integer Programming ModelM k M h . . .time o o jk t jk p jk t ikt ih o ih ik p ik M M Fig. Time chart for model⎩⎨⎧=otherwise0, machine on job precedes job if 1, k j i x ijk ⎩⎨⎧=otherwise0, job for machine on that precedes machine on processing 1, i k h a ihk t jk : completion time of job j on machine k2.1 Integer Programming Model☐IP formulation is discussed by Baker (1974).☐The objective function is to minimize the makespan.☐Constraint (2) ensuring the processing sequence of operationsfor each job corresponds to the prescribed order.☐Constraint (3) ensuring each machine can process only one jobat a time.{}()()()()()5,...,2,1,,...,2,1,,1or 04,...,2,1,,...,2,1,03,...,2,1,,,...,2,1)1(2,...,2,1,,,...,2,1)1(t.s.1max max min ,,11m k n j i x m k n i t m k h n i p x M t t m k h n i t a M p t t t ijk ik jk ijk ik jk ih ihk ik ik ik n i m k M ==≥==≥==≥-+-==≥-+-⎭⎬⎫⎩⎨⎧=≤≤≤≤⏹Baker, K.: Introduction to Sequencing and Scheduling , John Wiley,1974.2.3Disjunctive Graph Model⏹Balas, E.: "Machine sequencing via disjunctive graphs: an implicitenumeration algorithm”, Operations Research,Vol. 17, pp. 941-957, 1969.☐Disjunctive graph model for JSP:G= (N, A,E)N: Set of nodes representing all operationsA: Set of arcs connecting consecutive operations of the same jobE : Set of disjunctive arcs connecting operations⏹To be processed by the same machine, a disjunctive arc can besettled by either of its two possible orientations.☐A feasible schedule: Order of the operations on each machine.⏹To settle the orientation of the disjunctive arcs such that:1. the resulting graph is acyclic (there are no precedence conflictsbetween operations) and2. the length of the maximum weight path between the start and endnodes, i.e., makespan, is minimal2.3 Disjunctive Graph Model12345678910☐The nodes of N= {0, 1, 2, 3, 4, 5, 6, 7, 8, 9, 10} correspond to operations, where nodes 0 and 10 are the dummy operations. The conjunctive arcs of A={(1,2), (2,3), (4,5), (5,6), (7,8), (8,9)} to precedence constraints on operations of same jobs.☐The disjunctive arcs :E1={(1,5), (5,9), (9,1)} to operations to be performed on machine 1E2={(4,2), (2,8), (8,4)} to operations to be performed on machine 2E3={(7,3), (3,6), (6,7)} to operations to be performed on machine 3Job-shop Scheduling Problem1. Introduction2. JSP Mathematical / Graph Models3.Conventional Heuristics for JSP3.1 Priority Dispatching Heuristics3.2 Shifting Bottleneck Heuristic3.3 Randomized Dispatching Heuristics3.4 Comparison with Different Heuristics4. Genetic Algorithms for JSP5. Gen-Tsujimura-Kubota’s Method6. Cheng-Gen-Tsujimura’s Method☐The relationship among active, semiactive, and nondelay schedules isshown as follows:All feasible schedules SemiactiveActiveNondela y☐When considering a regular performance measure , the optimal schedule iswithin the set of active schedules . The nondelay schedules are smaller than the active schedules , but there is no guarantee that the former will contain an optimum .*Opt .⏹Baker, k.,Introduction to Sequencing and Scheduling , John and Wiley & Sons, New York, 1974.⏹French, S , “Sequencing and Scheduling,”In Mathematics and Its Applications : Ellis Horwood Limited, 1982. ⏹Gen, M. and Cheng, R., Genetic Algorithms & Engineering Design , John Wiley & Sons, 1997.☐Priority rules are probably the most frequently applied heuristics for solving JSP because of their ease of implementation and their low time complexity.☐The algorithms of Giffer and Thompson [OR -1960]can be considered as the common basis of all priority-rule-based heuristics.3.1Priority Dispatching Heuristicsd completede be could operation which at time earlist the started be could operation which at time earlist the given a to ing correspond stage at operation e schedulabl of set the operationsscheduled containing schedule partial a t i t i t t t S i φS i σPS t S t PS ∈=∈===,☐Notation⏹Giffler, B. and G. Thompson : "Algorithms for solving production scheduling problems”, Operations Research , Vol. 8, No. 4, pp. 487-503, 1960.☐Shifting bottleneck heuristic is probably the most powerful procedure among all heuristics for JSP.It sequences the machines one by one, successively,taking each time the machine identified as a bottleneck among machines not yet sequenced.Every time after a new machine is sequenced, all previously established sequences are locally re-optimized.☐Algorithm: Shifting Bottleneck Heuristicstep 1.Identify a bottleneck machine m among the machines k∈M, M0 and sequence it optimally. Set M0←M0⋃{m}.step 2.Re-optimize the sequence of each critical machine k∈M0in turn,while keeping the other sequences fixed. Then if M0=M, stop; otherwise go to step 1.where, M0 is the set of machine already sequenced.o 1,1o 1,2o 1,3o 1,4o 2,1o 2,2o 2,3o 2,4o 3,1o 3,2o 3,3o 3,4o 4,1o 4,2o 4,3o 4,4M 1M 2M 3M 4t0130120110100908070605020304010140150Figure. Illustration of Bottleneck Shifting☐Rules of five heuristic methods:⏹Colorni A., M. Dorigo: “Ant system for Job-shop Scheduling”, JORBEL-BelgianJournal of Operations Research, Statistics and Computer Science, 34, 1, pp.39-53, 1994.1. SPT: Select the operation with the shortest processing time(SPT).2. LPT: Select the operation with the longest processing time(LPT).3. LRT: Select the operation belonging to the job with the longestremaining processing time(LRT).4. SRT: Select the operation belonging to the job with the shortestremaining processing time(SRT).5. LRM: Select the operation belonging to the job with the longestremaining processing time excluding the operation underconsideration (LRM).1. SPT (shortest processing time)select the operation with the shortest processing time. We firstly add some new definition for the procedure.VariablesO l: a set of operations {o ikj}at the l th steppred(oikj ):the predecessor of the operation oikjsucc(oikj ):the successor of the operation oikjN i: number of operations for job iN:total number of operations S:schedule list for N operations∑==niiN N1Procedure of SPT rule: Generate a feasible scheduleprocedure :SPT rule to generate a feasible schedule endoutput else then if argmin to for begin:output :input );( list schedule };\ );(succ \ )(succ ;)()( };{ {;)( };,)(pred {)( list schedule operations of number total ,time processing l S o O O o o O O φo o l S l S O o p o N l φS i φo o O l S N p ikj l l ikjikj l l ikj ikj l ikj ikj ikj ikj ikj ikj *+**+***←⋃←≠⋃←∈←=←∀=←11111Example of SPT ruleTable 3.2 Processing Time, Machine Sequenceo 111o 123o 323o 312o 222o 233o 211o 132o 331)22: ,18: ,8:()9: ,20: ,15:()12: ,21: ,16:(331323312323322221121321231111o o o J o o o J o o o J ===J i =(o ikj : P ikj , …)M 1M 3M 2M 1M 2M 3M 2M 3M 1p ikj123Operations J 1162112J 215209J 381822M j 123Example of SPT rulel O lp ikjo ikj *S (l )1{o 111, o 211, o 312}p 111=16, p 211=15, p 312=8o 312{o 312}2{o 111, o 211, o 323}p 111=16, p 211=15, p 323=18o 211{o 312, o 211}3{o 111, o 222, o 323}p 111=16, p 222=20, p 323=18o 111{o 312, o 211, o 111}4{o 123, o 222, o 323}p 123=21, p 222=20, p 323=18o 323{o 312, o 211, o 111, o 323}5{o 123, o 222, o 331}p 123=21, p 222=20, p 331=22o 222{o 312, o 211, o 111o 323, o 222}6{o 123, o 233, o 331}p 123=21, p 233=9, p 331=22o 233{o 312, o 211, o 111, o 323, o 222, o 233}7{o 123, o 331}p 123=21, p 331=22o 123{o 312, o 211, o 111, o 323, o 222, o 233, o 123}8{o 132, o 331}p 132=12, p 331=22o 132{o 312, o 211, o 111, o 323, o 222, o 233, o 123, o 132}9{o 331}p 331=22o 331{o 312, o 211, o 111, o 323, o 222, o 233, o 123, o 132, o 331}ScheduleS ={o 312, o 211, o 111, o 323, o 222, o 233, o 123, o 132, o 331}Trace table by SPT ruleo 111o 123o 323o 312o 222o 233o 211o 132o 331Example dataOperationsp ikj123J 1162112J 215209J 381822Example of SPT rule77}35 ,77 ,65,44 ,53 ,62 ,13 ,51 ,8max{ },,,,,,,,max{}{max 331132123233222323111211312,,====t t t t t t t t t t t ikj jk i M Schedule : S ={o 312, o 211, o 111, o 323, o 222, o 233, o 123, o 132, o 331}S ={o 312(t 312-t 312F ), o 211(t 211-t 211F ), o 111(t 111-t 111F ), o 323(t 323-t 323F ), o 222(t 222-t 222F ), o 233(t 233-t 233F ),o 123(t 123-t 123F ), o 132(t 132-t 132F ), o 331(t 331-t 331F )}= {o 312:(0-8), o 211(0-15), o 111(15-31), o 323(8-26), o 222(15-35),o 233(35-44), o 123(44-65), o 132(65-77), o 331(31-53)}J 1J 2J 3Makespan : 77 (units)M 1M 2M 353o 312o 111o 323o 222o 233o 211o 123o 132o 331time7760653515202631447040852. LPT : select the operation with the longest processing time .procedure : LPT rule to generate a feasible schedule endoutput else then if argmax to for begin:output :input ;)( list schedule };\ );(succ \ )(succ ;)()( };{ {;)( };,)(pred { )( list scheduleoperations of number total , time processing l S o O O o o O O φo o l S l S O o p o N l φS i φo o O l S N p ikj l l ikj ikj l l ikj ikj l ikj ikj ikj ikj ikj ikj *+**+***←⋃←≠⋃←∈←=←∀=←11111Example of LPT ruleScheduleTrace table by LPT rulelO lp ikjo ikj *S (l )1{o 111, o 211, o 312}p 111=16, p 211=15, p 312=8o 111{o 111}2{o 123, o 211, o 312}p 123=21, p 211=15, p 312=8o 123{o 111, o 123}3{o 132, o 211, o 312}p 132=12, p 211=15, p 312=8o 211{o 111, o 123, o 211}4{o 132, o 222, o 312}p 132=12, p 222=20, p 312=8o 222{o 111, o 123, o 211, o 222}5{o 132, o 233, o 312}p 132=12, p 233=9, p 312=8o 132{o 111, o 123, o 211, o 222, o 132}6{o 233, o 312}p 233=9, p 312=8o 233{o 111, o 123, o 211, o 222, o 132, o 233}7{o 312}p 312=8o 312{o 111, o 123, o 211, o 222, o 132, o 233, o 312}8{o 323}p 323=18o 323{o 111, o 123, o 211, o 222, o 132, o 233, o 312, o 323}9{o 331}p 331=22o 331{o 111, o 123, o 211, o 222, o 132, o 233, o 312, o 323, o 331}S ={o 111, o 123, o 211, o 222, o 132, o 233, o 312, o 323, o 331}o 111o 123o 323o 312o 222o 233o 211o 132o 331Example dataOperationsp ikj123J 1162112J 215209J 3818224 Comparison with Different HeuristicsExample of LPT rule100}001 ,87 ,8 ,06 ,36 ,15 ,13 ,73 ,16max{ }, , , , , , , ,max{}{max 331323312233132222211123111,,====t t t t t t t t t t t ikj jk i M Schedule : S ={o 111, o 123, o 211, o 222, o 132, o 233, o 312, o 323, o 331}S ={o 111(t 111-t 111F ), o 123(t 123-t 123F ), o 211(t 211-t 211F ), o 222(t 222-t 222F ), o 132(t 132-t 132F ), o 233(t 233-t 233F ),o 312(t 312-t 312F ), o 323(t 323-t 323F ), o 331(t 331-t 331F ) }={o 111(0-16), o 123(16-37), o 211(16-31), o 222(31-51), o 132(51-63)o 233(51-60), o 312(0-8), o 323(60-78), o 331(78-100)}Makespan : 100(units)M 1M 2M 316313751859095100timeo 3317860706325o 132o 233o 312o 3238o 111o 123o 211o 22245J 1J 2J 3procedure : LRT rule to generate a feasible schedule3. LRT : select the operation belonging to the job with thelongest remaining processing time.endoutput else then if argmax to for begin:output :input );( list schedule } ;\ );(succ \ )(succ ;)()( };{ {;)( }; ,)(pred { )( list schedule ,l S o O O o o O O φo o l S l S O o r o N l φS i φo o O l S N r ikjl l ikjikj l l ikj ikj l ikj ikj ikjikj ikj ikj *+**+***←⋃←≠⋃←∈←=←∀=←11111 operations of number total time processing remaining r ikj : remaining processing time of J i corresponding tooperation o ikj jN i j k i ikj ikj i p p p r ,,,1,,+++=+ M jIn this case we assume all of remaining operations for job i are assigned on the same machine M j .ikjp p i,N ijtimet i,k +1,j+1o t i,N i , jo ikjo i,k +1,jt ikjp i,k +1,j …i,N i jTime chart for modelExample of LRT ruleScheduleTrace table by LRT rulelO lr ikjo ikj *S (l )1{o 111, o 211, o 312}r 111=49, r 211=44, r 312=48o 111{o 111}2{o 123, o 211, o 312}r 123=33, r 211=44, r 312=48o 312{o 111, o 312}3{o 123, o 211, o 323}r 123=33, r 211=44, r 323=40o 211{o 111, o 312, o 211}4{o 123, o 222, o 323}r 123=33, r 222=29, r 323=40o 323{o 111, o 312, o 211, o 323}5{o 123, o 222, o 331}r 123=33, r 222=29, r 331=22o 123{o 111, o 312, o 211, o 323, o 123}6{o 132, o 222, o 331}r 122=12, r 222=29, r 331=22o 222{o 111, o 312, o 211, o 323, o 123, o 222}7{o 132, o 233, o 331}r 133=12, r 233=9, r 331=21o 331{o 111, o 312, o 211, o 323, o 123, o 222, o 331}8{o 132, o 233}r 132=12, r 233=9o 132{o 111, o 312, o 211, o 323, o 123, o 222, o 331, o 132}9{o 233}r 233=9o 233{o 111, o 312, o 211, o 323, o 123, o 222, o 331, o 132, o 233}S ={o 111, o 312, o 211, o 323, o 123, o 222, o 331, o 132, o 233}o 111o 123o 323o 312o 222o 233o 211o 132o 331Example dataOperationsp ikj123J 1162112J 215209J 381822Example of LRT ruleSchedule : S ={o 111, o 312, o 211, o 323, o 123, o 222, o 331, o 132, o 233}63}06 ,36 ,35 ,15 ,74 ,62 ,13 ,8 ,16max{ }, , , , , , , ,max{}{max 233132331222123323211312111,,====t t t t t t t t t t t ikj jk i MS ={o 111(t 111-t 111F ), o 312(t 312-t 312F ), o 211(t 211-t 211F ), o 323(t 323-t 323F ), o 123(t 123-t 123F ),o 222(t 222-t 222F ), o331(t 331-t 331F ), o132(t 132-t 132F ), o233(t 233-t 233F ) }={o 111(0-16), o 312(0-8), o 211(16-31), o 323(8-26), o 123(26-47),o 222(31-51), o 331(31-53), o 132(51-63), o 233(51-60)}Makespan : 63(units)Gantt chart of the scheduleM 1M 2M 38165147o 323o 123o 111o 312o 211o 222o 331o 132o 23331354063time6026J 1J 2J 3Example dataOperationsp ikj 123J 1162112J 215209J 381822procedure : SRT rule to generate a feasible schedule4. SRT : select the operation belonging to the job with theshortest remaining processing time.r ikj : remaining processing time of J i correspondingto operation o ikj jN i j k i ikj ikj i p p p r ,,,1,,+++=+ M jIn this case we assume all of remaining operations for job i are assigned on the same machine M j .ikjp p i,N i jtimet i,k +1,j+1o t i,N i , jo ikjo i,k +1,jt ikjp i,k +1,j …i,N i jTime chart for modelendoutput else then if argmin to for begin:output :input ; )( list schedule };\ );(succ \ )(succ ;)()( };{ {;)( };,)(pred { )( list schedule N operations of number total time remaining l S o O O o o O O φo o l S l S O o r o N l φS i φo o O l S r ikj l l ikj ikj l l ikj ikj l ikj ikj ikjikj ikj ikj *+**+***←⋃←≠⋃←∈←=←∀=←11111 ,Example of SRT ruleScheduleTrace table by SRT rulelO lr ikjo ikj *S (l )1{o 111, o 211, o 312}r 111=49, r 211=44, r 312=48o 211{o 211}2{o 111, o 222, o 312}r 111=49, r 222=29, r 312=48o 222{o 211, o 222}3{o 111, o 233, o 312}r 111=49, r 233=9, r 312=48o 233{o 211, o 222, o 233}4{o 111, o 312}r 111=49, r 312=48o 312{o 211, o 222, o 233, o 312}5{o 111, o 323}r 111=49, r 323=40o 323{o 211, o 222, o 233, o 312, o 323}6{o 111, o 331}r 111=49, r 331=22o 331{o 211, o 222, o 233, o 312, o 323, o 331}7{o 111}r 111=49o 111{o 211, o 222, o 233, o 312, o 323, o 331, o 111}8{o 123}r 123=33o 123{o 211, o 222, o 233, o 312, o 323, o 331, o 111, o 123}9{o 132}r 132=12o 132{o 211, o 222, o 233, o 312, o 323, o 331, o 111, o 123, o 132}S ={o 211, o 222, o 233, o 312, o 323, o 331, o 111, o 123, o 132}o 111o 123o 323o 312o 222o 233o 211o 132o 331Example dataOperationsp ikj123J 1162112J 215209J 381822Example of SRT rule97}79 ,58 ,46 ,84 ,62 ,8 ,44 ,53 ,15max{ }, , , , , , , ,max{}{max 132123111331323312233222211,,====t t t t t t t t t t t ikj jk i M Schedule : S ={o 211, o 222, o 233, o 312, o 323, o 331, o 111, o 123, o 132}S = {o 211(t 211-t 211F ), o 222(t 222-t 222F ), o 233(t 233-t 233F ), o 312(t 312-t 312F ),o 323(t 323-t 323F ), o 331(t 331-t 331F ), o 111(t 111-t 111F ), o 123(t 123-t 123F ), o 132(t 132-t 132F ) }={o 211(0-15), o 222(15-35), o 233(35-44), o 312(0-8), o 323(8-26)o 331(26-48), o 111(48-64), o 123(64-85), o 132(85-97)}Makespan 97(units)Gantt chart of the scheduleM 1M 2M 3848o 211o 222o 233o 312o 323o 331o 111o 123o 13215202630354044556064707580859097timeJ 1J 2J 3Example dataOperationsp ikj 123J 1162112J 215209J 381822procedure : LRM rule to generate a feasible schedule5. LRM : select the operation belonging to the job with theshortest remaining processing time.e ikj : remaining processing time of J i correspondingto operation o ikj M jIn this case we assume all of remaining operations for job i are assigned on the same machine M j .ikjp p i,N i jtimet i,k +1,j+1o t i,N i , jo ikjo i,k +1,jt ikjp i,k +1,j …i,N i jjN i j k i ikj i p p e ,,,1,,++=+ endoutput else then if argmin to for begin:output :input ; )( list schedule ;\ );(succ \ )(succ ;)()( };{ ;)( };,)(pred { )( list schedule operations of number tatal exclude for time processing remainning l S o O O o o O O φo o l S l S O o e o Nl φS i φo o O l S N p J e ikj l l ikj ikj l l ikj ikj l ikj ikj ikjikj ikj ikj ikj *+**+***←⋃←≠⋃←∈←=←∀=←111i 11 Time chart for modelExample of LRM ruleScheduleTrace table by LRM rulelO le ikjo ikj *S (l )1{o 111, o 211, o 312}e 111=33, e 211=29, e 312=40o 312{o 312}2{o 111, o 211, o 323}e 111=33, e 211=29, e 323=22o 111{o 312, o 111}3{o 123, o 211, o 323}e 123=12, e 211=29, e 323=22o 211{o 312, o 111, o 211}4{o 123, o 222, o 323}e 123=12, e 222=9, e 323=22o 323{o 312, o 111, o 211, o 323}5{o 123, o 222, o 331}e 123=12, e 222=9, e 331=0o 123{o 312, o 111, o 211, o 323, o 123}6{o 132, o 222, o 331}e 132=0, e 222=9, e 331=0o 222{o 312, o 111, o 211, o 323, o 123, o 222}7{o 132, o 233, o 331}e 132=0, e 233=0, e 331=0o 331{o 312, o 111, o 211, o 323, o 123, o 222, o 331}8{o 132, o 233}e 132=0, e 233=0o 132{o 312, o 111, o 211, o 323, o 123, o 222, o 331, o 132}9{o 233}e 233=0o 233{o 312, o 111, o 211, o 323, o 123, o 222, o 331, o 132, o 233}S ={o 312, o 111, o 211, o 323, o 123, o 222, o 331, o 132, o 233}o 111o 123o 323o 312o 222o 233o 211o 132o 331Example dataOperationsp ikj123J 1162112J 215209J 381822Example of LRM ruleSchedule : S ={o 312, o 111, o 211, o 323, o 123, o 222, o 331, o 132, o 233}S ={o 312(t 312-t 312F ), o 111(t 111-t 111F ), o 211(t 211-t 211F ), o 323(t 323-t 323F ), o 123(t 123-t 123F ), o 222(t 222-t 222F ), o 331(t 331-t 331F ), o 132(t 132-t 132F ), o 233(t 233-t 233F ) }={o 312(0-8), o 111(0-16), o 211(16-31), o 323(8-26), o 123(26-47)o 222(31-51), o 331(31-53), o 132(51-63), o 233(51-60)}63}06 ,36 ,35 ,15 ,74 ,62 ,13 ,16 ,8max{ }, , , , , , ,,max{}{max 233132331222123323211111312,,====t t t t t t t t t t t ikj jk i M Makespan : 63(units)Gantt chart of the scheduleM 1M 2M 38165147o 323o 123o 111o 312o 211o 222o 331o 132o 23331354063time6026J 1J 2J 3Example dataOperationsp ikj123J 1162112J 215209J 381822ComparisonTable 13.22Comparison results with different heuristic method Heuristic method Schedule Makespan t M SPT{o312, o211, o111, o323, o222, o233, o123, o132, o331}77LPT{o111, o123, o211, o222, o132, o233, o312, o323, o331}100LRT{o111, o312, o211, o323, o123, o222, o331, o132, o233}63SRT{o211, o222, o233, o312, o323, o331, o111, o123, o132}97LRM{o312, o111, o211, o323, o123, o222, o331, o132, o233}63A quick comparison of the solutions reveals that the heuristic Conclusion:methods LRT and LRM outperform other heuristic methods withlower makespan.☐ComparisonTable 13.23Comparison results with different heuristic method by different dataThe comparisons of the solutions (using different size ofproblems) reveal that the heuristic methods LRT and LRM outperform other heuristic methods with lower makespan.Conclusion:Heuristic methodsMakespan t M3x34x46x610x510x1015x10SPT 773188392018561719LPT 1003447988918601519LRT 633376773514511314SRT 9734094121021241806LRM633595776314931313⏹The data come from OR lib. (/jeb/orlib/jobshopinfo.html )。