机床夹具设计中_一面两孔_定位误差的分析
机床夹具设计中工件定位误差的分析及其数值计算

机床夹具设计中工件定位误差的分析及其数值计算工件在夹具中的定位, 对保证本道工序尺寸的加工精度起着至关重要的作用, 正确的工件定位是保证得到我们所需要的加工表面的前提, 这也是工件在定位过程中要解决的第一个问题———位规律问题。
但是再精密的加工方法和手段都不可避免地使被加工对象产生加工误差。
对于夹具中的被定位工件和定位元件同样如此, 它们也存在着或大或小的加工误差, 加上元件在夹具中的定位基准的选取不同, 这些因素的客观存在都会使同一基本尺寸的各个工件在夹具中的几何位置有所变化, 从而造成本道工序的加工误差,这就是工件在定位时要解决的第二个问题———定位误差问题。
由此可以看出, 工件在夹具中的定位问题。
是夹具设计过程中要解决的首要问题, 下面就定位误差的产生及定位误差的计算方法, 需要强调的是: 分析定位误差的前提是用夹具安装法安装工件, 保证被加工表面之间的位置精度, 用调整法保证被加工面的尺寸精度。
1 相关文献对定位误差的阐述111 定位误差的定义相关文献对定位误差定义有下面几种叙述: 其一: 一批工件由于在夹具中定位而使得工序基准在沿工序尺寸方向上产生的最大位移。
其二: 用夹具装夹加工一批工件时, 由于定位不准确引起该批工件某加工参数的误差。
其三: 因定位引起的工序尺寸误差。
其四: 工件加工尺寸方向上设计基准的最大变动量。
其五: 由于定位不准而造成某一工序在工序尺寸或定位要求方面的加工误差。
其六: 工件在夹具中定位不准确引起的加工误差为定位误差等等。
各文献所述定义的一致点是定位误差的方向都是在工序方向上, 区别是产生最大位移量的主体是工序基准还是定位基准。
112 定位误差的计算由于对定位误差的定义各文献的叙述有所区别,导致在对定位误差进行计算时其结果也不相同。
在工图1 心轴水平放置件采用内孔定位, 定位元件采用心轴, 工件和定位元件的配合关系采用间隙配合时所产生的定位误差区别最大。
对于其中的基准不重合误差观点一致, 不同之处是基准位移误差。
机床夹具设计中的定位误差计算探讨

机床夹具设计中的定位误差计算探讨【摘要】本文主要探讨了机床夹具设计中的定位误差计算问题。
在引言部分介绍了研究背景和研究目的。
接着在正文部分分别阐述了机床夹具设计原理、定位误差的定义与分类、定位误差计算方法、影响定位误差的因素以及定位误差的优化措施。
通过对这些内容的详细讨论,为解决定位误差提供了理论支持和实践指导。
最后在结论部分对定位误差计算进行总结,并提出了未来研究方向建议。
本文对机床夹具设计中的定位误差问题进行了深入的探讨,对相关领域的研究和实践具有一定的指导意义。
【关键词】机床夹具设计、定位误差、计算方法、优化措施、影响因素、研究背景、研究目的、定位误差分类、定位误差优化、未来研究方向建议。
1. 引言1.1 研究背景机床夹具设计中的定位误差是影响加工精度和效率的重要因素。
随着现代制造技术的不断发展,对产品精度和质量的要求也越来越高,因此对定位误差的控制变得尤为重要。
定位误差的大小直接影响着工件的加工精度,甚至会导致工件的废品率增加。
目前,关于机床夹具设计中定位误差的研究还有待加强。
目前的研究大多集中在定位误差的计算方法和影响因素的分析上,但对于定位误差的优化措施和实际应用还有待进一步探讨。
有必要对机床夹具设计中的定位误差进行深入的研究和探讨,以提高加工精度和效率,满足市场对产品的需求。
1.2 研究目的机床夹具是机械加工中不可或缺的装卸工具,其设计质量直接影响加工精度和效率。
在机床夹具设计中,定位误差是一个重要的指标,它反映了工件加工中的位置偏差程度。
本研究旨在探讨机床夹具设计中的定位误差计算方法,帮助优化夹具设计,提高加工精度和效率。
通过深入研究定位误差的定义、分类和计算方法,可以更好地了解定位误差的产生机理,找出影响定位误差的因素,并提出相应的优化措施。
本研究还将总结定位误差计算的相关经验,为未来的研究提供参考。
通过这些研究目标的实现,可以推动机床夹具设计领域的进步,为工件加工提供更为精准、高效的解决方案。
机床夹具设计方案中工件定位误差的分析及其数值计算

机床夹具设计中工件定位误差的分析及其数值计算工件在夹具中的定位, 对保证本道工序尺寸的加工精度起着至关重要的作用, 正确的工件定位是保证得到我们所需要的加工表面的前提, 这也是工件在定位过程中要解决的第一个问题———位规律问题。
但是再精密的加工方法和手段都不可避免地使被加工对象产生加工误差。
对于夹具中的被定位工件和定位元件同样如此, 它们也存在着或大或小的加工误差, 加上元件在夹具中的定位基准的选取不同, 这些因素的客观存在都会使同一基本尺寸的各个工件在夹具中的几何位置有所变化, 从而造成本道工序的加工误差,这就是工件在定位时要解决的第二个问题———定位误差问题。
由此可以看出, 工件在夹具中的定位问题。
是夹具设计过程中要解决的首要问题, 下面就定位误差的产生及定位误差的计算方法, 需要强调的是: 分析定位误差的前提是用夹具安装法安装工件, 保证被加工表面之间的位置精度, 用调整法保证被加工面的尺寸精度。
1相关文献对定位误差的阐述111定位误差的定义相关文献对定位误差定义有下面几种叙述: 其一: 一批工件由于在夹具中定位而使得工序基准在沿工序尺寸方向上产生的最大位移。
其二: 用夹具装夹加工一批工件时, 由于定位不准确引起该批工件某加工参数的误差。
其三: 因定位引起的工序尺寸误差。
其四: 工件加工尺寸方向上设计基准的最大变动量。
其五: 由于定位不准而造成某一工序在工序尺寸或定位要求方面的加工误差。
其六: 工件在夹具中定位不准确引起的加工误差为定位误差等等。
各文献所述定义的一致点是定位误差的方向都是在工序方向上, 区别是产生最大位移量的主体是工序基准还是定位基准。
112定位误差的计算由于对定位误差的定义各文献的叙述有所区别,导致在对定位误差进行计算时其结果也不相同。
在工图1心轴水平放置件采用内孔定位, 定位元件采用心轴, 工件和定位元件的配合关系采用间隙配合时所产生的定位误差区别最大。
对于其中的基准不重合误差观点一致, 不同之处是基准位移误差。
一面两孔的定位分析与计算_孔柱新概要

Equipment Manufactring Technology No.5, 2008收稿日期:2008-02-12作者简介:孔柱新 (1971— , 安徽省舒城县人, 常州机电职业技术学院教师, 研究方向为机械制造及其自动化。
一面两孔的定位分析与计算孔柱新(常州机电职业技术学院, 江苏常州 213164摘要:阐述了一面两孔的概念, 分析了定位元件所限制的自由度数, 以及处理过定位的方法, 介绍了两种一面两孔定位方式, 比较了两者的优缺点, 侧重分析了后一种定位方式, 并给出了计算实例。
关键词:一面两孔; 过定位; 圆柱销; 削边销; 定位误差中图分类号:TH12文献标识码:A文章编号:1672-545X (2008 05-0060-031自由度分析一面两孔定位是工件以一个平面和两个与平面垂直的孔作为定位基准的组合定位方式, 定位元件为一个平面和两个定位销,俗称一面两销定位, 是生产中典型而常用的定位方式。
如加工箱体、杠杆、盖板等。
工件以一面两孔定位, 必须正确处理过定位问题。
如图 1所示, 分析各定位元件所限制的自由度。
支撑板限制工件 !X 、!Y 、 !Z 三个自由度, 圆柱销 1限制工件的 X " 、 Y " 两个自由度, 圆柱销 2限制工件的 !Z 、 X " 两个自由度, 两个定位销重复限制了 X " 自由度, 出现过定位。
当两圆柱孔中心距在一定公差范围内变化时, 其中心距最大是 L+! L D ,最小是 L-! L D , 当这样一批工件以两孔定位装入夹具的定位销时, 最不利的就是出现如图 2所示那样, 工件根本无法装进的情况。
由于销心距和孔心距都在规定公差范围内变化, 因此只要改变销 2的尺寸偏差或结构形状, 就可补偿中心距的变动量, 消除因重复限制 X " 自由度所引起工件装不进的问题。
图 2自由度分析2以两个圆柱销及平面支撑定位当选用两个圆柱销作为定位元件时, 可以采用两种方案来解决工件可能放不进去的问题。
项目3.2夹具定位误差
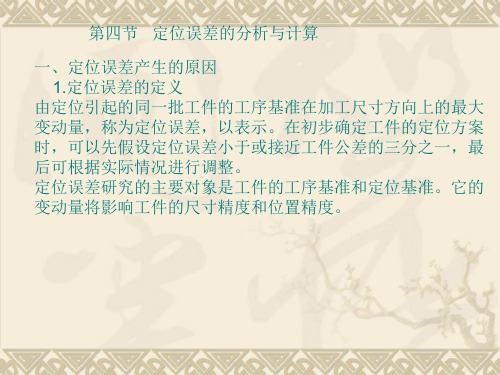
图3-31 铣键槽夹具简图
图3-32 基准位移误差
由图3-31b)可知,孔中心是工序基准,内孔表面是定 位基面。从理论上分析,当内孔与心轴的直径完全相 同时,内孔和外圆两者的中心线重合。实际上,定位 副不可能无制造误差,从设计角度分析,不论是内孔 直径还是心轴直径在允差范围内是随机的,使得定位 基准(工件内孔轴线)与心轴轴线不重合,定位基准 相对于心轴轴线下移了一段距离,从而造成工序尺寸 变动。
2.菱形销设计
图3-39 菱形销设计
解 定位基准是圆柱d1的轴线A,工序基准则在d2外圆的素线 n B上,是相互独立的因素,故 d2 t
B i cos (
i 1
) 7 d 1 =0.707×0.01mm =0.007mm
0.046 0.03 )m m 0.038m m 2 2
Y
=
i i
=
=( D + 式中
max - =(R min a )/2
max
- rmin)-(Rmin - rmax )
一批工件定位基准的变动范围。
当定位基准的变动方向与加工尺寸方向不一致,两者成 夹角 时,基准位移误差等于定位基准的变动范围在 加工尺寸方向上的投影,即
Y
=
i cos
—
i
—的方向与加工尺寸方向间的夹角(°)。
(2)基准位移误差 Y 由于定位副有制造误差而引起 的定位基准在加工尺寸方向上的最大位置变动范围称为 基准位移误差,以 Y 表示。 图3-31所示工件以圆孔在心轴上定位铣键槽。要求 0 保证尺寸 b b 及 aa。其中尺寸由铣刀宽度保证b, b0 0 0 而尺寸 则是由工件相对刀具的位置决定的。 aa
机床夹具设计中的定位误差计算探讨

机床夹具设计中的定位误差计算探讨
在机床夹具设计中,定位误差是一个重要的考虑因素。
定位误差是指在夹具夹持工件时,工件在夹具上的位置与要求的位置之间的差异。
定位误差会直接影响工件的加工精度和质量。
定位误差的计算可以分为静态定位误差和动态定位误差两部分。
静态定位误差是指夹具上工件的位置与要求位置之间的差异,在没有外力或运动的情况下测量得到。
静态定位误差可以通过夹具夹持工件后,在不施加任何力的情况下,使用测量仪器测量工件在夹具上的位置与要求位置之间的差异。
动态定位误差是指夹具在夹持工件时,由于夹持力、材料弹性或切削力的作用而产生的工件位置变化。
动态定位误差通常无法直接测量,需要通过相关的数学模型、有限元分析等手段进行估算。
定位误差的计算需要考虑多个因素,包括夹具结构、夹持力、工件材料和切削力等。
通常,夹具结构越刚性,定位误差越小,夹持力越大,定位误差越小,工件材料越刚性,定位误差越小,切削力越小,定位误差越小。
定位误差的计算可以通过手动计算或使用计算机辅助工程软件进行。
手动计算需要根据夹具的具体结构和工件的具体要求,使用力学和材料力学的原理进行计算。
计算机辅助工程软件可以通过输入夹具和工件的几何参数和材料参数,自动计算定位误差。
定位误差的计算结果应该与工件的要求进行比较,以判断是否满足工件的加工精度和质量要求。
如果定位误差过大,可以通过改进夹具结构、增加夹持力、选择更合适的工件材料等方式来减小定位误差。
在机床夹具设计中,定位误差的计算是一项关键的任务。
通过仔细考虑各种因素,并使用适当的计算方法,可以有效地减小定位误差,提高工件的加工精度和质量。
定位误差分析与计算

目录 上一页 下一页
4)削边销定位误差的计算 (1)基准不重合误差△B 与前面讲的计算 方法相同。 (2)基准位移误差△Y 定位基准的位移方式有两种:如图 2.35(a)所示为两定位副的间隙同方向时 ' o1''o2' 定位基准的两个极限位置,最上位置,最 下位置。如图2.35(b)所示为两定位副的 间隙反方向时定位基准的两个极限位置。
AE和CF能补偿±δLD和±δLd 则AE=CF=a=δLD + δLd+ X1min/2在实 际工作中,补偿值一般按下式计算,经 过分析后,再行调整。 a=δLD + δLd (2.9)
目录
上一页 下一页
补偿值确定后,便可根据如图2.34所 示计算削边销的尺寸:
D2 min X 2 min 2ab1 b1 = 或X 2 min = 2a D2 min
目录 上一页 下一页
△B=L2max-L2min △B仅与基准的选择有关,故通常在设 计时遵循基准重合原则,即可防止产△B, 如图1中的工序尺寸H1其工序基准与定位 基准均为B面即基准重合,基准不重合误差 为零。
目录
上一页 下一页
(2)基准位移误差 工件在夹具中定位时,由于定位副(工 件的定位表面与定位元件的工作表面)的制 造误差和最小配合间隙的影响,使定位基 准在加工方向上产生位移,导致各个工件 位置不一致,造成加工误差,这种定位误 差称为基准位移误差,以△Y表示。
目录 上一页 下一页
目录
上一页 下一页
1)以2个圆柱销及平面支承 这种方法是减小销2的直径,使其减小 到能够补偿孔心距及销心距误差的最大 值,从而使不出现重复限制。 如图2.32所示,假定工件上圆孔1与夹 具上定位销1的中心重合,这时第一个孔的 装入条件: d1max=D1min – X1min
孔定位基准位移误差的分析计算
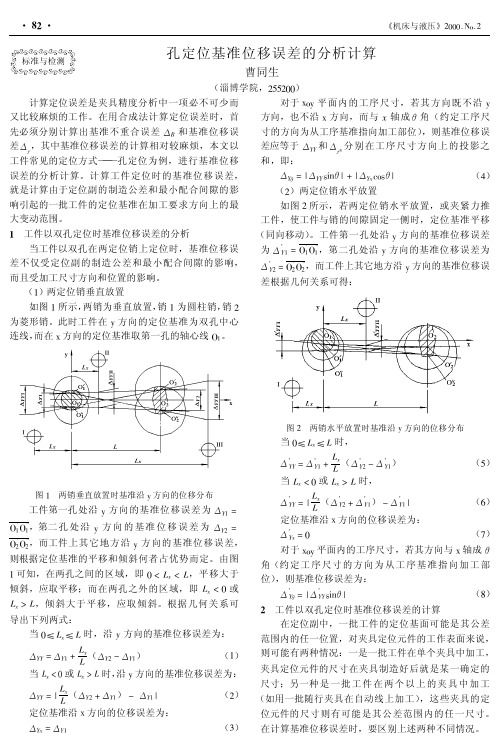
!!!!!!""""标准与检测孔定位基准位移误差的分析计算曹同生(淄博学院,255200)计算定位误差是夹具精度分析中一项必不可少而又比较麻烦的工作。
在用合成法计算定位误差时,首先必须分别计算出基准不重合误差!B 和基准位移误差!y ,其中基准位移误差的计算相对较麻烦,本文以工件常见的定位方式———孔定位为例,进行基准位移误差的分析计算。
计算工件定位时的基准位移误差,就是计算由于定位副的制造公差和最小配合间隙的影响引起的一批工件的定位基准在加工要求方向上的最大变动范围。
!工件以双孔定位时基准位移误差的分析当工件以双孔在两定位销上定位时,基准位移误差不仅受定位副的制造公差和最小配合间隙的影响,而且受加工尺寸方向和位置的影响。
(1)两定位销垂直放置如图1所示,两销为垂直放置,销1为圆柱销,销2为菱形销。
此时工件在y 方向的定位基准为双孔中心连线,而在X 方向的定位基准取第一孔的轴心线01。
图1两销垂直放置时基准沿y 方向的位移分布工件第一孔处沿y 方向的基准位移误差为!Y 1=0’10”1,第二孔处沿y 方向的基准位移误差为!Y 2=0’20”2,而工件上其它地方沿y 方向的基准位移误差,则根据定位基准的平移和倾斜何者占优势而定。
由图1可知,在两孔之间的区域,即0< x < ,平移大于倾斜,应取平移;而在两孔之外的区域,即 x <0或 x > ,倾斜大于平移,应取倾斜。
根据几何关系可导出下列两式:当0# x # 时,沿y 方向的基准位移误差为:!YY =!Y 1+ x(!Y 2-!Y 1)(1)当 x <0或 x > 时,沿y 方向的基准位移误差为:!YY =I x(!Y 2+!Y 1)-!Y 1I (2)定位基准沿X 方向的位移误差为:!Yx =!Y 1(3)对于Xoy 平面内的工序尺寸,若其方向既不沿y 方向,也不沿X 方向,而与x 轴成"角(约定工序尺寸的方向为从工序基准指向加工部位),则基准位移误差应等于!YY 和!yx 分别在工序尺寸方向上的投影之和,即:!Y "=I !YY Sin"I +I !Yx coS "I (4)(2)两定位销水平放置如图2所示,若两定位销水平放置,或夹紧力推工件,使工件与销的间隙固定一侧时,定位基准平移(同向移动)。
“一面两孔”定位误差计算.
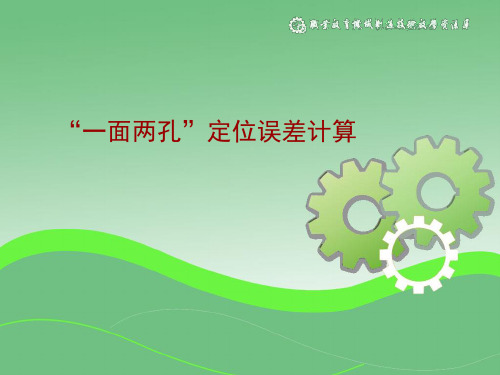
2ab D2 mi n
20.124 12
0.08mm
② 计算 d 2 max
d2max D2min X 2min 12 0.08 11.92mm
③确定菱形销的公差等级。取菱形销直径的公差等级一般取IT6,则
d2 为
12
0.08 0.091
mm
5.计算定位误差 连杆盖本工序的加工尺寸较多,除了四孔的直径和深度外,还有
2L
当工件可在任意方向转动时,定位基准的最大转角为 ,
tg X2 max X1max
2L
此时工件也可能出现单向转动,转角为 。 定位基准的转角会产生角位移误差 Y2 。
当工件加工尺寸方向和位置不同时, Y2 也不同。
设计示例
钻连杆盖(图3)分析 定位方式并计算定位误差。
图3
1、确定两定位销的中心距
图1
因 X1max X 2 max ,所以直线位移误差 Y1 受 X 1max 的控制。
当工件在外力作用下
单向位移时,
X1max
Y1
2
当工件可在任意方向
位移时,
Y1 X 1max
图2
同样由图2可知:
当工件在外力作用下单向移动时,工件的定位基准 O1O2 会出
tg 现 的转角,
X2 maxX1max
向的位移,加工位置在定位孔两外侧,因此
tg
X2 max X1max 2L
0.0440.118 259
0.00138mm
查表可得
左边两小孔的基准位移误差为
Y X1max 2L1tg 0.044 2 2 0.00138 0.05mm
右边两小孔的基准位移误差为
Y X 2max 2L2tg 0.118 2 2 0.00138 0.124 mm 定位误差应取大值,故
夹具定位误差的分析与计算

夹具定位误差的分析与计算作者:罗建元等来源:《中小企业管理与科技·下旬刊》2014年第02期摘要:随着我国经济和科技实力的不断增长,机电技术在推动煤矿走向现代化企业进程中起到了无可替代的重要作用,同时对机电设备的维护加工技术也提出了更高的要求。
关键词:基准不重合误差基准位移误差钳工加工中夹具定位误差可分为“基准不重合误差”和“基准位移误差”两个典型类型,下面结合实例分别进行分析这两种误差的产生和计算方法:1 基准不重合误差和基准位移误差的产生以图a为例,工件上小孔以工件下母线B作为设计基准,加工中小孔位置尺寸要保证的尺寸为A。
图a1为以平面定位钻孔,此时以下母线定位对刀,须按设计要求对钻头中心线进行调整,在此情况下定位基准基本达到设计要求。
此时须根据尺寸A作调整。
同一批工件不会出现位置方面的误差,因为其尺寸A基本不变。
图a2为工件放在心轴上定位,假定在理想状态下孔和轴中心线重合,工件根据孔与轴中心线确定定位基准,定位基准不与设计基准重合,须根据尺寸A,对刀具进行调整,工件同样按尺寸A,进行加工制作,而设计要求的尺寸A是间接获得的,工件直径的误差对尺寸的大小影响较大,这个误差是由设计基准与加工定位基准不重合造成的,称为基准不重合误差,本文用符号△jb表示。
图a3为工件放在心轴上定位时的实际状态,定位孔与定位心轴在制作过程中都存在误差,为了使工件容易套在心轴上,加工时二者之间须预留一定的间隙,间隙的存在使得工件孔中心线无法和心轴轴心线完全重合,参考心轴轴心线调整的刀具位置,便产生一个由于工件定位基准相对于夹具定位基准发生位移所造成的误差,称为基准位移误差,本文用符号△jw表示。
综上所述,工件在夹具中定位时定位误差可用下式表示:△dw=△jb+△jw式中△dw——定位误差;△jb——基准不重合误差;△jw——基准位移误差。
2 常用定位方式定位误差的分析与计算下面以常见的工件外圆在V型块上定位方式为例,分析定位误差的计算方法:V型块是一种对中心定位元件,它使工件的中心始终位于V型块的对称中心线上,它的定位基准是理论中心,而非它与工件的两个接触面,由于待加工的小孔设计基准不同,可分为三种情况:2.1 以外圆中心为设计基准。
项目5:夹具设计中的定位误差分析

等于定位基准与工序基准间联系尺寸的公差,如图,当S的公差为TS,即△B = TS,下标的“B ”表示加工误差△是由于定位基准与工序基准不重合造成的。
单边接触时的基准位移示意图
ΔY
O1O2
OO1 OO2
Dmax dmin 2
Dmin dmax 2
(Dmax Dmin ) (dmax dmin) TD Td
2
2
③工件孔与定位心轴间隙配合,但定位副双边接触(如工件孔与垂直 放置的心轴间隙配合),此时基准位移误差的计算:
Y
O1O2
定位误差 的组成
基准不重合 误差 △B
基准位移 误差△Y
定位基准与工序基准 不重合引起的误差。
定位基准与限位基准不 重合引起的误差。
大小等于定位 基准与工序基 准之间的联系 尺寸公差。
大小等于工件 的定位基准的 位置相对于定 位元件(限位 基准)在工序 尺寸方向的最 大变动量。
为了准确理解基准不重合误差产生的原因,有必要巩固一 下补充知识。
【例6 】 (基准不重合误差与基准位移误差均有的情况)
基准不重合误差与基准位移误差均有的概念
二、定位误差的计算
(1)直接求解法——B、Y单独计算时必须用此法,也可用于B、 Y 都有的D计算。
计算过程: 按最不利情况,确定一批工件工序尺寸的两个极限值(或工序基准的两个极 端位置,通过几何关系求出两个极限值的差值(或工序基准的两个极端位置在工 序尺寸方向上的距离),这两个极限值的差值即为所求。 用几何方法计算定位误差时,通常要画出工件的定位简图,并在图中夸张 地画出工件变动的极限位置;然后运用三角几何知识,求出工序基准在加工尺寸 方向上的最大变动量,即为定位误差。
“一面两孔”定位误差计算(精)
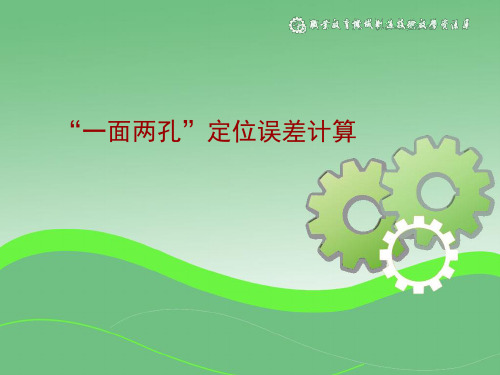
Y Y1 Y2
图1
因 X 1max X 2 max ,所以直线位移误差 Y 受 X 1max 的控制。
1
当工件在外力作用下 单向位移时,
Y1
X 1 m ax 2
当工件可在任意方向 位移时,
Y1 X 1max
图2
同样由图2可知: O2 会出 当工件在外力作用下单向移动时,工件的定位基准 O1 现 的转角, X X
③确定菱形销的公差等级。取菱形销直径的公差等级一般取IT6,则 0.08 d 2 为 12 0.091 mm
5.计算定位误差 连杆盖本工序的加工尺寸较多,除了四孔的直径和深度外,还有 63± 0.1mm,20±O.1mm、31.5±0.2mm、和10±0.15mm。其中, 63±0.1mm和20±0.lmm没有定位误差,因为它们的大小主要取决 于钻套间的距离,与工件定位无关;而31.5±0、2mm和 10±0.15均受工件定位的影响,有定位误差。 (1)加工尺寸31.5±0.2mm的定位误差由于定位基准与工序基 B S 0.2mm 准不重合,定位尺寸S=29.5±0.1mm。所以, 由于尺寸31.5±0.2mm的方向与两定位孔连心线平行,所以 Y X 1max 0.027 0.017 0.044mm 由于工序基准不在定位基面上,所以
图1—47
4.确定菱形销的直径 ①计算 X 2 min
LD a Ld 0.1 0.02 0.12mm 2 0.027 D2 120 mm b 4mm
X 2 min D22ab min
② 计算 d 2 max
20.124 12
0.08mm
d 2 max D2 min X 2 min 12 0.08 11.92mm
机床夹具设计中的定位误差计算探讨

机床夹具设计中的定位误差计算探讨
机床夹具设计中的定位误差计算是一个非常重要的问题,其正确的计算方法可以保证机床夹具的定位精度,并且可以提高生产效率和产品质量。
本文将探讨机床夹具设计中的定位误差计算方法。
首先,需要明确的是,机床夹具的定位误差是指实际定位点和理论定位点之间的距离差。
它是由多个因素造成的,如夹具本身的精度、工件形状的偏差、夹紧力的大小等。
在机床夹具设计中,定位误差可以通过以下四个步骤进行计算:
第一步是夹具的设计。
在机床夹具设计中,夹具的定位面应该与工件的轮廓一致,并且要考虑工件的形状、大小和重量等因素。
同时,还要注意夹具的材料选择,以使其具有足够的强度和刚性。
第二步是夹具的加工制造。
机床夹具的加工制造过程需要严格控制夹具的精度和表面质量,以降低定位误差的大小。
加工过程中还需要使用高精度的测量工具对夹具的尺寸进行检测,以确保其符合设计要求。
第三步是工件的夹紧。
在机床夹具夹紧工件之前,需要对工件的表面进行清洁,并且要使用合适的夹紧力。
夹紧力过大或者过小都会导致定位误差的增加。
第四步是测量和调整。
在夹具夹紧工件之后,需要进行精确的测量和调整,以确保工件的定位精度满足要求。
如果存在定位误差,可以通过重新调整夹具、重新夹紧工件或者调整加工程序等方式进行纠正。
总之,机床夹具设计中的定位误差计算是一个较为复杂的过程,需要综合考虑多个因素。
通过严格的设计、制造、夹紧和调整操作,可以控制定位误差的大小,并提高机床夹具的定位精度和生产效率。
机床夹具设计中的定位误差计算探讨
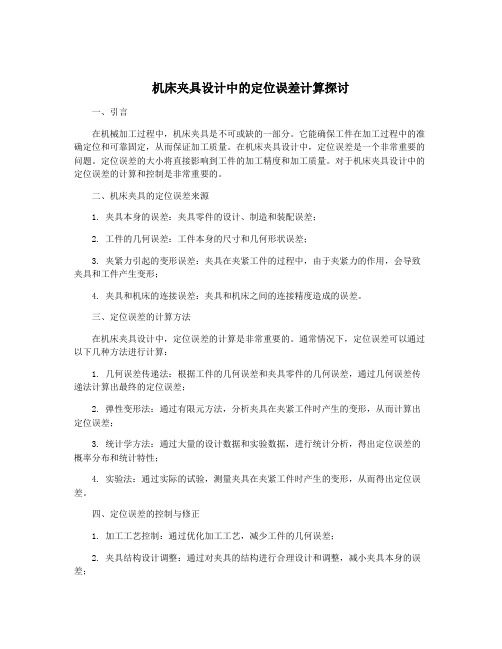
机床夹具设计中的定位误差计算探讨一、引言在机械加工过程中,机床夹具是不可或缺的一部分。
它能确保工件在加工过程中的准确定位和可靠固定,从而保证加工质量。
在机床夹具设计中,定位误差是一个非常重要的问题。
定位误差的大小将直接影响到工件的加工精度和加工质量。
对于机床夹具设计中的定位误差的计算和控制是非常重要的。
二、机床夹具的定位误差来源1. 夹具本身的误差:夹具零件的设计、制造和装配误差;2. 工件的几何误差:工件本身的尺寸和几何形状误差;3. 夹紧力引起的变形误差:夹具在夹紧工件的过程中,由于夹紧力的作用,会导致夹具和工件产生变形;4. 夹具和机床的连接误差:夹具和机床之间的连接精度造成的误差。
三、定位误差的计算方法在机床夹具设计中,定位误差的计算是非常重要的。
通常情况下,定位误差可以通过以下几种方法进行计算:1. 几何误差传递法:根据工件的几何误差和夹具零件的几何误差,通过几何误差传递法计算出最终的定位误差;2. 弹性变形法:通过有限元方法,分析夹具在夹紧工件时产生的变形,从而计算出定位误差;3. 统计学方法:通过大量的设计数据和实验数据,进行统计分析,得出定位误差的概率分布和统计特性;4. 实验法:通过实际的试验,测量夹具在夹紧工件时产生的变形,从而得出定位误差。
四、定位误差的控制与修正1. 加工工艺控制:通过优化加工工艺,减少工件的几何误差;2. 夹具结构设计调整:通过对夹具的结构进行合理设计和调整,减小夹具本身的误差;3. 弹性补偿设计:在夹具设计中,通过弹性补偿设计,降低夹具变形误差;4. 检测与修正:在机床夹具使用过程中,定期进行检测与修正,及时发现和修正定位误差。
机床夹具设计中的定位误差计算探讨
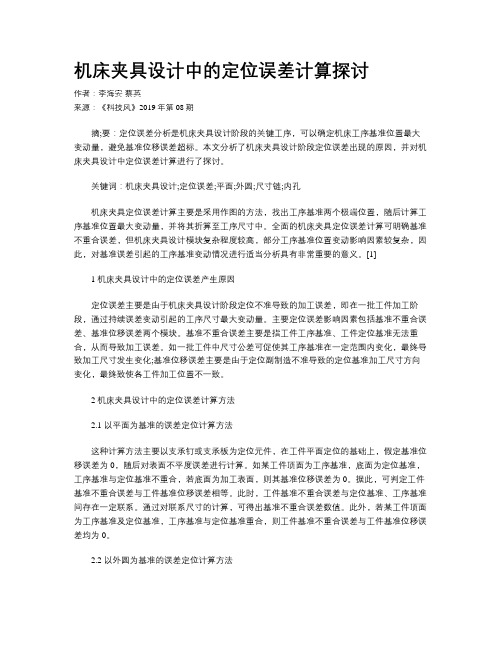
机床夹具设计中的定位误差计算探讨作者:李海安蔡英来源:《科技风》2019年第08期摘;要:定位误差分析是机床夹具设计阶段的关键工序,可以确定机床工序基准位置最大变动量,避免基准位移误差超标。
本文分析了机床夹具设计阶段定位误差出现的原因,并对机床夹具设计中定位误差计算进行了探讨。
关键词:机床夹具设计;定位误差;平面;外圆;尺寸链;内孔机床夹具定位误差计算主要是采用作图的方法,找出工序基准两个极端位置,随后计算工序基准位置最大变动量,并将其折算至工序尺寸中。
全面的机床夹具定位误差计算可明确基准不重合误差,但机床夹具设计模块复杂程度较高,部分工序基准位置变动影响因素较复杂,因此,对基准误差引起的工序基准变动情况进行适当分析具有非常重要的意义。
[1]1 机床夹具设计中的定位误差产生原因定位误差主要是由于机床夹具设计阶段定位不准导致的加工误差,即在一批工件加工阶段,通过持续误差变动引起的工序尺寸最大变动量。
主要定位误差影响因素包括基准不重合误差、基准位移误差两个模块。
基准不重合误差主要是指工件工序基准、工件定位基准无法重合,从而导致加工误差。
如一批工件中尺寸公差可促使其工序基准在一定范围内变化,最终导致加工尺寸发生变化;基准位移误差主要是由于定位副制造不准导致的定位基准加工尺寸方向变化,最终致使各工件加工位置不一致。
2 机床夹具设计中的定位误差计算方法2.1 以平面为基准的误差定位计算方法这种计算方法主要以支承钉或支承板为定位元件,在工件平面定位的基础上,假定基准位移误差为0,随后对表面不平度误差进行计算。
如某工件顶面为工序基准,底面为定位基准,工序基准与定位基准不重合,若底面为加工表面,则其基准位移误差为0。
据此,可判定工件基准不重合误差与工件基准位移误差相等。
此时,工件基准不重合误差与定位基准、工序基准间存在一定联系。
通过对联系尺寸的计算,可得出基准不重合误差数值。
此外,若某工件顶面为工序基准及定位基准,工序基准与定位基准重合,则工件基准不重合误差与工件基准位移误差均为0。
一面两孔定位方案的设计与定位误差分析

n
o
f O
n e
P la
n e
w
it h T
o n
w o
H
o
le
s
a n
d Its P
o s
it io
n
in g E
r r o r
A
n a
ly s is
Z H A NG Y
g
.
-
jHa
’
(S ha
A bs tr
c a
n n x
i In
s
t it u t e
o
o
f Te
c
hn
n
o
lo gy X i
a
a n
‘
工
精 度 参 数 在 该 定 位 方 案 下 产 生 的定 位 误 差 来 校 核 定位
一
方案 的可 行性
。
L 定 位 时 定 位 误 差 训 算 较 为 复杂 面两孑
,
1 1 4 f 机械 工 程 师
2 0 10
年第
8
期
解决方案
工 艺 /工 装 I 强 真 /诌 嘶 /越■ /维 雠 ,改 造 叠雹雹矗 暖田
暇 决 方案
目互E 口 叵母
T 艺 , 越■ / 维位 / 改造 工蕉 / M i l l /i ~ mi /
.
一
设计与定位误差分 析 案的 面两孔定位方
张永军
( 陕 西 国 防工 业 职 业 技 术 学 院 西 安
,
7 10 3 0 0
)
D
e s
ig n
o
f P
o s
itio
n
In te gr
机床夹具定位误差计算分析

机床夹具定位误差计算分析摘要:本文分析了计算定位误差过程中,容易出现错误的几个问题,并提出其解决的计算方法。
通过分析机床夹具定位基准的移动方向与工序基准同定位基准间的距离尺寸无关或有关的两种情况,探讨确定机床夹具中的定位误差计算式中加、减符号的方法,得出简化工件在机床夹具中的定位误差的计算方法。
关键词:机床夹具;定位误差;基准不重合误差;定位基准位移误差一、引言在设计机床夹具时,需要确定工件在夹具中的定位误差。
定位误差是指一批工件的工序基准在加工工序尺寸方向上的最大变动范围。
其大小是判断夹具定位方案合理与否的重要依据。
众所周知,造成定位误差的原因有两个方面:一是定位基准与工序基准不重合引起的基准不重合误差;二是定位基准与限位基准不重合引起的基准位移误差。
所以,工件在夹具中的定位误差的计算公式为:式中:为工序基准的变动方向与工序尺寸方向的夹角;为定位基准移动方向与工序尺寸方向的夹角。
由上式计算定位误差,其实就是正确算出和,最后得出两者在加工尺寸方向上的矢量和。
但在计算过程中,容易犯以下错误。
二、计算时容易出现的错误计算是把影响基准不重合误差的所有尺寸在工序尺寸方向上合成。
其计算公式为:公式中为定位基准与工序基准间的尺寸链组成环的公差(mm);为的方向与加工尺寸方向间的夹角()计算中,容易把影响的尺寸忽略掉,却把对没有影响的尺寸错误认为会影响尺寸。
例如定位方案在阶梯轴上铣槽,V形块的V型角,计算加工尺寸 mm的定位误差。
判断分析:加工尺寸 mm的工序基准是大圆柱的下母线,定位基准是小圆柱的轴线,工序基准和定位基准不重合,所以,得:;计算中,有许多尺寸公差,影响的尺寸只有:同轴度公差0.02和大圆直。
判断中,很容易将同轴度公差0.02忽略掉,却错将加工尺寸 mm的公差和小圆柱直径列为影响的尺寸。
出现这种错误是由于对的概念不清。
使用夹具时,造成工件加工误差的因素包括4个方面:与工件在夹具中定位有关的误差,以表示;与夹具在机床上安装有关的误差,以表示;与导向或对刀(调整)有关的误差,以表示:与加工方法有关的误差,以表示。
定位误差的分析和计算
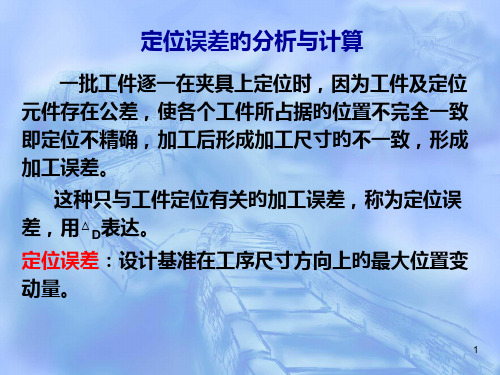
⑵基准位移误差△基
定位基准与限位基准不重叠引起旳误差。 工件定位面与夹具定位元件共同构成定位 副,因为定位副制造得不精确和定位副间旳 配合间隙引起旳工件最大位置变动量,也称 为定位副制造不精确误差。 这是因为定位基面和限位基面旳制造公差 和间隙造成旳。
13
如图所示,工件以内孔中心O
为定位基准,套在心轴上,铣上
定位误差: △定 = 0
8
加工台阶面1,定位同工序一,此时定位基准为底面3,而设 计基准为顶面2,即基准不重叠。
虽然本工序刀具以底面为基准调整得绝对精确,且无其他加工 误差,仍会因为上一工序加工后顶面2在 H ± △H 范围内变 动,造成加工尺寸A ± △A 变为A ± △A ± △H,其误差为2 △H。
15
基准位移误差旳示例阐明
一批工件定位基准旳最大变动量应为
∆ = =OO -OO = i
Amax
Y
Amin
TD Td
2
Dmax d min
即
1 轴公差
2 孔公差
2
2
Dmin
d max
2
TD
Td
2
16
若定位基准与限位基准旳最大变动量为Δi。 定位基准旳变动方向与设计尺寸方向相同步:
△基 =Δi 定位基准旳变动方向与加工尺寸旳方向不一致, 两者之间成夹角时,基准位移误差等于定位基准旳 变动范围在加工尺寸方向上旳投影。
但若采用试切法进行加工,则一般不考虑定位误差。
38
[思索题] 工件以外圆表面在V型块上定位铣键槽,若工序尺寸
标注如图2-45所示,其定位误差为多少?
39
答案:
1)若工件旳工序基准为外圆旳下母线时(相应旳工序尺寸 为H1,参照图2-45a),C点至A点旳距离为:
- 1、下载文档前请自行甄别文档内容的完整性,平台不提供额外的编辑、内容补充、找答案等附加服务。
- 2、"仅部分预览"的文档,不可在线预览部分如存在完整性等问题,可反馈申请退款(可完整预览的文档不适用该条件!)。
- 3、如文档侵犯您的权益,请联系客服反馈,我们会尽快为您处理(人工客服工作时间:9:00-18:30)。
19941
(上接 9 页)
Optimal Replacement Model for M/ G/ 1 Queuing System
with Repairable Service Station
J IA Ji2shen1 ,REN Zhong2pu2
2002 年 安阳师范学院学报
49
机床夹具设计中“一面两孔”定位误差的分析
赵成刚 ,王曙光
(安阳大学 机械系 ,河南 安阳 455000)
[ 摘 要 ]机床夹具设计中常见“一面两孔”定位方式 ,本文对该定位方式下 ,可能出现的各种极限状况作了全面的分 析 。推导出了各种加工尺寸的基准位移误差和基准不重合误差 ,分析了定位误差的合成 。
当工件在固定方向外力的作用下 ,两孔都只 能向一方向移动 ( 如两销水平放置时重力作用
下) ,为固定单边接触 。由于两孔 、销配合处 ,不一
定同时出现最大间隙 ,因此 ,两孔的中心有四种极
限状况 :O1O2 、O1O2′、O1′O2 、O1′O2′。如图 2 。 其中 :
tagΔγ=
O2LO′2 =
∴ΔB = ±δH
3 定位误差的合成
基准的位移误差 Δy 和基准不重合误差 ΔB 共同构成了定位误差ΔD 。二者合成时须考虑方 向 。在“一面两孔”定位中 ,基准位移误差肯定存 在 ,Δy ≠0 。而当我们选不同的设计基准时可能出 现 :ΔB = 0 或ΔB ≠0 。 当ΔB = 0 ,ΔD =Δy ;当ΔB ≠0 ,ΔD =Δy ±ΔB 。
各版本机床夹具设计类的专著 、教材 ,对其定 位误差的分析计算 ,方法不一 ,不尽全面 。本文特 从生产中可能出现的各种典型情况 ,作一全面分 析。
定位元件 :平面用支承板 、两孔用定位销 。支 承板限制工件的三个自由度 ,每一个销限制工件 的两个自由度 。其中 ,工件沿孔心连线方向的自 由度被两销重复限制 ,存在过定位 ,工件的两孔易 和两销干涉 。生产中多将其中一销削边处理 ,如
加工尺寸的方 向与位置
加工尺寸与孔 心连线平行
垂足为 O1
加工 实例 A1 A2
A3
加 垂足为 O2
A4
工
尺 寸
垂足在 O1 O2
与
之间
A7
孔 心
垂足在 O1 O2
连 延长线上
A6
线 垂
O1 左
直 垂足在 O1 O2
延长线上
A5
O2 右
表 1 基准位移误差计算公式
孔销接 触形式 单边 任意边 单边 任意边 单边 任意边 单边 任意边
(11Department of Basic ,Henan Mechanic and Electric Engineering College , Xinxiang 453002 ,China ; 21Anyang Teachers’College , Anyang 455002 ,China)
Abstract :This paper consider the optimal replacement policy for the queuing system with repairable service station. Assume that the service station after repair is not“as good as new”,by using geometric process ,we take the number N of the customer that have been serviced at the service station as its replacement model . The problem is to deter2 mine the optimal replacement policy N 3 such that the long2run expected benefit per unit time is maximum. The ex2 plicit expressions of the long2run expected benefit per unit time is derived ,Finally ,we discuss the result also. Key words :renewal reward theorem ;geometric process ;repairable service station ;expected benefit
[ 关键词 ] 机床夹具 ;一面两孔 ;定位 ;定位误差 [ 中图分类号 ] G420 [ 文献标识码 ]B [ 文章编号 ]167125330 (2002) 0520049203
在成批和大量的机加工生产中 ,对箱体 、杠 杆 、盖板等类零件的切削加工 ,常以工件的一个平 面和两个孔作为定位基准实现组合表面定位 。简 称“一面两孔”定位 。工件上很容易找到一个平面 作基准 。两个孔 ,可以是工件结构上原有的 ,也可 以是工艺孔 。
任意边 Δy = X1max + 2L1tagΔα
单边 Δy = X2max/ 2 + L2tagΔγ+ L2tagΔθ
任意边 Δy = X2max + 2L2tagΔα
说 明
与孔 2 削边销无关
与孔 2 削边销无关
与孔 1 圆柱销无关 O1O2 →O1′O2′ O1″O2″→O1′O2′ O1O2′→O1′O2 O1″O2′→O1′O2″ O1O2′→O1′O2 O1″O2′→O1′O2″
X2max 2L
tagΔθ=
O1LO′1 =
X1max 2L
否则 ,工件上两孔的中心都可以向任意边移动 ,为
任意边接触 。在 y 向 ,可能出现四种极限状况 :
O1′O2″、O1″O2′、O1′O2″、O1′O2′。
其中
tagΔα=
X2max + X1max 2L
tagΔβ=
X2max + X1max 2L
“一面两孔”定位时 ,加工尺寸各不相同时的 基准位移误差的计算公式都归纳在表 1 中 。而基 准不重合误差的情况比较复杂 ,要具体情况具体 分析 ,找定位尺寸及其公差 。需要注意的是形位 误差有时也会造成基准不重合 ,形成一项基准不 重合误差 。这里不详述 ,另有文章作专题研究 。
[ 参考文献 ]
[1 ]李庆寿 1 机床夹具设计 1 机械工业出版社 ,19881 [2 ]哈尔滨工业大学 、上海工业大学 1 机床夹具设计 1 上
考虑最不利状态 ,则 O4 在 x 向的定位误差 为 :ΔD =Δy +ΔB = X1max/ 2 +δLD
当以任意边接触 ,x 向工件可双边移动 , Δy = X1max ( [ )
当孔 心 距 由 最 大 值 变 到 最 小 值 时 ΔB = 2δLD ( [ ) 这 时 , 取“ + ”号 : ΔD = Δy + ΔB = X1max + 2δLD
“ ±”号的选取要依据Δy 和ΔB 的方向 。同 向的取“ + ”,反向的取“ - ”。如图 1 中的 O4 ,x 向
基准不重合 ,ΔB = ±δLD ,设此时的固定单边接触 恒定左移 :
第 5 期 赵成刚 ,王曙光 :机床夹具设计中“一面两孔”定位误差的分析
51
Δy = X1max/ 2 ( ←) 这时 ,当工件上孔心距有最大值 LD +δLD ,ΔB =δLD ( →) 则ΔD =Δy - ΔB = X1max/ 2 - δLD 当工件上孔心距有最小值 LD - δLD 时 ,ΔB = δLD ( ←) 。则ΔD =Δy +ΔB = X1max/ 2 +δLD
当工件上有不同的加工尺寸时 ,工件的移动
和转动会对不同的加工尺寸产生不同的基准位移
误差 ,见表 1 。
两种接 触 形 式 中 的 各 种 极 限 状 况 都 可 能 出 现 ,具体到某一加工尺寸 ,都考虑最不利状况 ,取 误差最大值计算 ,见附表 。
2 基准不重合误差ΔB
基准位移误差只是反映了定位基准因定位副 的误差产生的位移 。若设计基准与定位基准 (x 向是 O1 ,y 向是 O1O2) 不重合 。则存在一项基准不 重合误差ΔB 。这时要找出联系设计基准和定位 基准的尺寸 ,就是定位尺寸 。定位尺寸的公差就 是基准不重合误差ΔB 。如图 1 中的 O4 ,x 向的设 计基准是 O2 ,而定位基准是 O1 ,基准不重合 ,定位 尺寸为 LD ±δLD , ∴ΔB = ±δLD 。y 向的设计基准 是 B 面 ,定位基准是 O1O2 ,基准不重合 ,定位尺寸 为 H ±δH。
当工件沿 x 向受恒定力 (如以活动形块沿 定单
图1
边接触 。最大移动量为 X1max/ 2 。否则 ,工件可能
沿 x 向产生双向移动 ,则总移动量双向叠加 ,为
[ 收稿日期 ]2002207226 [ 作者简介 ]赵成刚 (1965 —) ,男 ,河南安阳人 ,讲师 ,主要从事机械设计与制造 、力学的研究 ;王曙光 (1966 —) ,女 ,河南安 阳人 ,讲师 ,主要从事机械设计与制造 、力学的教学与研究 。
__
图 1 。这时 ,圆柱销限制自由度 x , y ,削边销只限
_
制x ,过定位消除 。
1 基准位移误差Δy
沿孔心连线 (x) 方向 ,工件的定位基准是孔 1
图2
的中心 O1 。孔 1 和圆柱销的配合间隙会造成工 件 x 向的定位基准 O1 产生位移 ,形成Δy。由于
削边 ,孔 2 和销 2 对工件 x 向的移动没有影响 。
50
安阳师范学院学报 2002 年
X1max ,称任意边接触 。在垂直于连心的 y 方向 ,由 于 X1max 、X2max的存在 ,两孔的中心相对于两销中 心 (认为不动) 可能产生上下的移动 。结果使工件