冲压工艺与模具设计PPT
合集下载
冲压工艺与模具设计概述模板ppt

4.3 回转体拉深件板料尺寸的确定
4.3.1 计算方法 4.3.2 简单回转体拉深件的板料尺寸计算 4.3.3 复杂形状回转体拉深件板料直径的计算
4.3.1 计算方法
常用的是等面积法,即假设拉深件表面积与板料 面积相等,作为计算板料面积的依据。但由于 板料的机械性能差异、模具工作条件的一致性 差异等因素,使拉深后由板料边缘形成的制件 的口部或凸缘周边部不齐,达不到制件的形状、 尺寸要求,必须对边缘处再加工。因此,在计 算板料尺寸时,要在拉深件的高度方向或带凸 缘制件的凸缘半径上加一修边余量δ,如图 4.16所示
结构组成即尺寸(4) 拉深次数(5) 润滑条件(6) 拉深速度 3. 极限拉深系数的确定
图4.24 多次拉深变形情况
4.4.2 拉深次数的确定
根据拉深件的相对厚度t/D,由表4.10查出相对
应的各次拉深系数m1,m2,…,mn。由式
(4.13)得知,总的拉深系数m和各次拉深系数
mi的关系为 mm 1m 2 m n1m n
1. 解析法 2. 作图累加法 3. 利用CAD软件求面积 4. 条线段已添加到多段线
图4.18 形心法求面积
4.4 圆筒形件的拉深
4.4.1 拉深系数 4.4.2 拉深次数的确定 4.4.3 拉深件工序尺寸的计算
4.4.1 拉深系数
1. 拉深系数的概念 图4.24 多次拉深变形情况 2. 极限拉深系数的主要影响因素 (1) 板料机械性能(2) 板料的相对厚度t/D (3) 模具
2. 影响拉深变薄和拉裂的因素
t
(1) 拉深系数m的影响(2) 板料机械性能的影响(3) 凹模圆 角半径的影响(4) 凸模圆角半径的影响(5) 摩擦系数的 影响 (6) 压边力的影响
冲压工艺与模具设计.ppt

一般对成型件的几何参数控制不是很严, 惟独对抛物线 形状要求比较严格。
解决这类问题的方法———
加大凸缘尺寸
增加压边圈下面的摩擦系数
增大压边力
采用拉深筋
采用反拉深
软模拉深
二、球面零件的拉深方法 1、拉深系数为恒数 m=0.71 拉深系数不决定拉深的难易程度。 毛坯的相对厚度 t / D是选择拉深方法的依据。
§4-3 非直壁旋转体零件拉深成形的特点
一、曲面形状零件的拉深特点 1、曲面形状零件的拉深不能简单的用
拉深系数来衡量成形的难易程度。 2、圆筒形件拉深,毛坯的变形区局限于
压边圈下面的环行部分。 3、球面零件拉深时,毛坯的凸缘部分与中间部分
都是变形区,在很多情况下, 中间部分反而是主要的变形区
(起皱不仅仅在凸缘部分产生, 也可能在中间部分产生,尤其对于薄板材料)
盒形件可以认为是由四个转角和四条直角边组成的,其拉深变形 可近似地认为——弯曲+筒形件+球面拉深
但是网格试分可以补偿球面拉深
*应力在角部最大,向直边逐渐减小,拉深时稳定性好。
*相对圆角半径r/B越小,圆角部分的材料向直角部分流动越 多,直边部分对圆角部分的影响越大,相对变形亦容易。
*相当于用直径D的 毛坯拉成直径为Dn-1 ,高为Hn-1的圆 筒形零件
3、长矩形盒形件的多次拉深(自看)
所有的计算方法都是近似的,通过试模可以进一步调整。
2、高盒形件 (H≥0.5B)毛坯的计算 方型 ——毛坯料:圆形 矩形 ——毛坯料:长圆形 计算方法页171
三、盒形件多次拉深的工艺计算
1、盒形件初次拉深的成形极限 盒形件拉深易在圆角部位发生起皱和断裂(拉破) 盒形件初次拉深的极限变形程度用相对高度H/r表示,相
解决这类问题的方法———
加大凸缘尺寸
增加压边圈下面的摩擦系数
增大压边力
采用拉深筋
采用反拉深
软模拉深
二、球面零件的拉深方法 1、拉深系数为恒数 m=0.71 拉深系数不决定拉深的难易程度。 毛坯的相对厚度 t / D是选择拉深方法的依据。
§4-3 非直壁旋转体零件拉深成形的特点
一、曲面形状零件的拉深特点 1、曲面形状零件的拉深不能简单的用
拉深系数来衡量成形的难易程度。 2、圆筒形件拉深,毛坯的变形区局限于
压边圈下面的环行部分。 3、球面零件拉深时,毛坯的凸缘部分与中间部分
都是变形区,在很多情况下, 中间部分反而是主要的变形区
(起皱不仅仅在凸缘部分产生, 也可能在中间部分产生,尤其对于薄板材料)
盒形件可以认为是由四个转角和四条直角边组成的,其拉深变形 可近似地认为——弯曲+筒形件+球面拉深
但是网格试分可以补偿球面拉深
*应力在角部最大,向直边逐渐减小,拉深时稳定性好。
*相对圆角半径r/B越小,圆角部分的材料向直角部分流动越 多,直边部分对圆角部分的影响越大,相对变形亦容易。
*相当于用直径D的 毛坯拉成直径为Dn-1 ,高为Hn-1的圆 筒形零件
3、长矩形盒形件的多次拉深(自看)
所有的计算方法都是近似的,通过试模可以进一步调整。
2、高盒形件 (H≥0.5B)毛坯的计算 方型 ——毛坯料:圆形 矩形 ——毛坯料:长圆形 计算方法页171
三、盒形件多次拉深的工艺计算
1、盒形件初次拉深的成形极限 盒形件拉深易在圆角部位发生起皱和断裂(拉破) 盒形件初次拉深的极限变形程度用相对高度H/r表示,相
冲压工艺与模具设计电子PPT课件

(
()
2
3)
/
2
31
(
3
1)
/
2
第21页/共89页
图1.3 主剪应力面及主剪应力方向(用阴影线表示)
第22页/共89页
•
其中绝对值最大的主剪应力称为该点的最大剪应力,用τmax表示。若规定1≥2≥3,则
•
•
()
ma x (13)/2
第23页/共89页
•
最大剪应力对材料的塑性变形有重要意义。
•
大小取决于该点的应力状态,而与坐标系的选取无关,即
•
•
•
()
m 1 3(x y z)1 3(1 2 3)
第16页/共89页
•
任何一种应力状态都可以看成是由两种应力状态叠加而成,如图所示。其中一种是大小等于平均应力
m的球应力状态,另一种为偏应力状态。因球应力状态为三向等应力状态,不产生剪应力,故不能改变物
•
应力是指单位面积上的内力。单向拉伸试验过程中,试件横截面上的拉
应力有两种计算方法:
第42页/共89页
•
(1)不考虑横截面积的变化(F0—试样初始截面积)
•
•
()
0
P F0
第43页/共89页
•
求得的0称为条件应力。其条件就是只有当变形不大时才能用这种方
法近似计算。
第44页/共89页
•
(2)考虑横截面积的变化
以说明这种弹塑性变形的共存现象。
第33页/共89页
•
低碳钢试样在单向拉伸时的拉伸试验曲线图(或条件应力-应变曲线)
如图所示。
第34页/共89页
图1.5 拉伸试验曲线图(条件应力-应变曲线)
《冲压工艺与模具设计》图文课件ppt 第4章

4.5 带凸缘圆筒形件的拉深
4.5.2 宽凸缘圆筒形件的拉深
当 r凸 = r凹 = r 时,宽凸缘圆筒形件毛坯直径 D 为: 根据拉深系数的定义,宽凸缘圆筒形件的拉深系数为:
目录
4.5 带凸缘圆筒形件的拉深
4.5.2 宽凸缘圆筒形件的拉深
宽凸缘圆筒形件的尺寸
目录
4.5 带凸缘圆筒形件的拉深
4.5.2 宽凸缘圆筒形件的拉深பைடு நூலகம்
拉深系数
拉深系数表示拉深后圆筒形件的直径与拉深前毛坯(或半成品) 的直径之比。
目录
基本概念
极限拉深系数
在实际生产中,拉深系数的减少有个限度,这个限度称为 极限拉深系数 。
拉深模的间隙
凸、凹模之间的间隙,简称为拉深间隙。
修边余量
由于拉深材料厚度有公差,板料具有各向异性,所以拉深后工件 的口部或凸缘周边不齐,必须进行修边,以达到工件的要求。修 边的值称为修边余量。
拉深件的工艺性
拉深件的工艺性是指工件拉深的难易程度。
变薄拉深
变薄拉深主要是在拉深过程中改变拉深件筒壁厚度,而毛坯的直 径变化很小的拉深方法 。
目录
拉深件类型
目录
4.1 拉深变形过程分析
4.1.1 拉深变形的过程及特点
1—凸模; 2—压边圈; 3—凹模; 4—制件
目录
4.1 拉深变形过程分析
4.1.2 拉深过程中板料的应力应变状态
4.2.1 起皱及其控制
(1)采用压边圈。
控
制
(2)采用锥形凹模
起
皱
的 措
(3)采用拉深筋
施
:
(4)采用反拉深
目录
4.2 拉深件的质量控制
4.2.1 起皱及其控制
冲压工艺与模具设计ppt课件
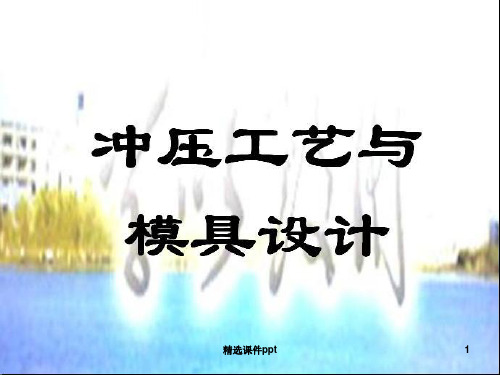
(7)大量生产时,产品成本低。
精选课件ppt
24
由此可见,冲压能集优质、高效、低能耗、 低成本于一身,这是其它加工方法无法与之相比拟的,
因此冲压的应用十分广泛,如汽车,拖拉机行业中,冲压 件占60%~70%,仪器仪表占到60~70%,还有日常生活中的 各种不锈钢餐具等等。从精细的电子元件,仪表指针到重 型汽车的覆盖件和大梁以及飞机蒙皮等均需冲压加工。
29
分离工序示意
D
D
D
落料
D
剪切
有分离现象发生,但不
改变空间形状
精选课件ppt
30
表1-1 分离工序
精选课件ppt
31
表1-1 分离工序(续)
精选课件ppt
32
(2)成形工序
冲压成形时,被加工材料在外力作用下,变形区材料所受 到的等效应力达到材料的屈服极限σs,但未达到强度极限σb, 使材料只产生塑性变形,从而得到一定形状和尺寸的零件。成 形工序主要有弯曲、拉深、翻孔、缩口、胀形等。
精选课件ppt
28
1.2 冲压工艺分类
1.按变形性质分类
➢分离工序 ➢成形工序
(1)分离工序
冲压成形时,被加工材料在外力作用下产生变形,当变 形区材料受到的剪切应力达到材料的抗剪强度,材料便产生 剪切而分离,从而形成一定形状和尺寸的零件。分离工序主 要有剪裁、冲孔、落料、切口、剖切等。
精选课件ppt
精选课件ppt
27
总之,模具工业是 一个国家的基础工业,模具设计与模 具制造水平的高低已成为衡量一个国家产品制造水平的高低。
发达国家非常重视模具的发展,日本认为:“模具就是进 入富裕社会的原动力”;德国:“金属加工业中的帝王”;罗 马尼亚:“模具就是黄金”;模具在国际上被认为是点石成金 的行业。不过这里的模具还包括塑模、锻模、压铸模、橡胶模、 食品模、建材模等等,但目前以冷冲模和塑料模的应用最广, 各占40%左右。
冲压工艺与模具设计ppt
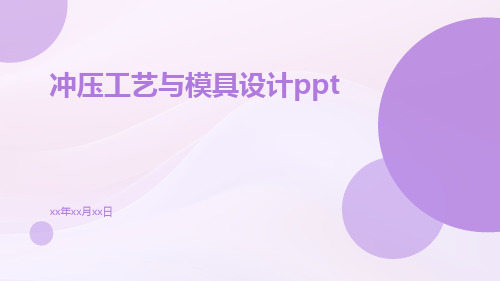
设计模具结构
根据工艺方案和产品图 样,设计模具的结构, 包括凸模、凹模、定位 板、压料板等零件的设 计。
绘制模具总装 图
根据设计的模具结构, 绘制模具的总装图,标 注尺寸和技术要求。
绘制零件加工 图
根据总装图,绘制每个 零件的加工图,包括凸 模、凹模、定位板等零 件的详细加工尺寸和技 术要求。
03
模具的装配工艺
模具零件的定位与固定 模具零件的调整与修整
模具零件的配合与连接 模具零件的润滑与防锈
模具的调试与验收
模具调试前的准备 模具的验收与检测
模具的安装与调试 模具的维护与保养
06
冲压工艺与模具设计的发展趋势
数字化设计与制造技术应用
01
基于计算机的模具设 计
利用CAD软件进行模具设计,实现高 效的设计与修改。
冲压工艺参数设计
冲压件的工艺性分析
1 2
工艺性分析的意义
通过对冲压件的形状、尺寸、精度等工艺性指 标进行分析,确保模具设计的合理性和生产过 程的顺利进行。
常见问题
如局部变形、起皱、开裂等,需要在设计阶段 尽量避免。
3
工艺性分析的方法
采用经验总结、模拟分析等方法,结合实际生 产情况,对冲压件的工艺性进行评估。
复合工艺是指将两个或多个分离或成形工艺组合 在一起,以获得所需形状和尺寸的制品,如拼接 、装配等。
冲压工艺的特点
高效性
冲压工艺可以大规模、连续化生产 ,提高生产效率和降低成本。
精度高
模具的精度决定了制品的精度,冲 压工艺可以实现高精度的加工要求 。
制造成本低
冲压工艺使用的设备和模具相对简 单,制造成本较低。
冲压设备的选择与计算
冲压设备的选择
第三章冲压工艺及模具设计课件.pptx

第三章 冲裁工艺及冲裁模具
3.4.2 工作部分尺寸计算方法
1.凸模和凹模分开加工时工作部分尺寸计算
凸模和凹模分开加工时,应分别计算和标注凸模和凹模工作部分
尺寸与制造公差。适合圆形或形状简单的凸模和凹模及大量生产冲
冲
压 工
模时采用。
艺
及
模 具
模具的制造公差与冲裁间隙之间应满足:
设
计
|δp|+|δd| ≤Zmax-Zmin
越高。
影响因素:
(1)冲裁模的制造精度。
冲
压
(2)材料性质。
工
艺 及
• 塑性好的材料,裂纹出现较迟,材料被剪切的深度较大,光亮带较大,断裂
模
具
带较小,但塌角及毛刺高度相应增大。反之,光亮带较小,断裂带增大,塌
设
计
角及毛刺较小。
• 弹性变形大小不同,导致回弹量不同。
(3)冲裁间隙。
• 过大:使制件的尺寸向实体方向收缩;
冲 压 工 艺 及 模 具 设 计
第三章 冲裁工艺及冲裁模具
2.冲裁件的精度
对于普通冲裁,冲裁件的尺寸精度在IT10~IT11以下,粗糙度高
于Ra12.5μm。
冲 压
冲孔精度可比落料精度高一级。
工
艺 及
3.冲裁件的尺寸基准
模
具
设 计
冲裁件的尺寸基准应尽可能和制模时的定位基准重合,孔位置
尺寸基准应尽量选择在冲裁过程中始终不参加变形的面或线上。
(4)孔间距、孔壁与孔壁之间的最小距离不应太小。
第三章 冲裁工艺及冲裁模具
(5)在弯曲或拉深零件上冲孔时,其孔壁与零件直壁之间应保持 一定的距离。
冲 压 工 艺 及 模 具 设 计
冲压工艺与模具设计PPT课件

精选PPT课件
30
对于冲孔工序,孔尺寸为 d
:
d凸(dx)0p
d 凹 ( d 凸 Z m ) 0 id n ( d x Z m ) 0 id n
:
工件制造公差(mm), x尺寸系数(表19)。
精选PPT课件
31
对于落料工序,工件尺寸为 D -
:
D凹(Dx)0 d
D 凸 ( D 凹 Z m ) 0 ip n ( D x Z m ) 0 ip n
▪ 光亮带b:当刃口切入材料后,材料受到凸模和凹 模剪切应力τ和挤压应力σ的作用而形成光亮垂直的 断面。通常光亮带占整个断面的1/2~1/3。
▪ 断裂带c:是由刃口附近的微裂纹在拉应力作用下不 断扩展而形成的撕裂面。
▪ 毛刺区d:毛刺。 精选PPT课件
13
2.2 冲 裁 间 隙
▪ 2.2.1 冲裁间隙对冲裁件断面质量的影响
差,即落料件和凸模刃口尺寸上偏差为零, 下偏差为负;冲孔件和凹模刃口尺寸上偏差
为正,下偏差为零。若磨损后不变化的尺寸 (如两孔中心距等),应按双向对称标注。
精选PPT课件
28
2.3.1 凸、凹模刃口尺寸计算原则
精选PPT课件
29
2.3.2 凸、凹模刃口尺寸的计算
▪ 由于模具的加工方法不同,凸模与凹模刃口 尺寸的计算方法也不同,基本上可分为两种 情况。
精选PPT课件
20
2.2.4 冲裁间隙对模具寿命的影响
▪ 冲模失效的形式一般有磨损、崩刃、变形、胀裂和折断。 ▪ 冲裁力主要集中在凸模和凹模的刃口部分。刃口变形和端面
磨损加剧,甚至崩刃。 ▪ 所以为了减少凸、凹模的磨损,延长模具使用寿命,在保证
冲裁件质量的前提下适当采用较大的间隙值是十分必要的。 若采用小间隙,就必须提高模具的硬度和耐磨性,提高模具 的制造精度,冲裁时采用良好的润滑,以减小磨损。
冲压工艺与模具设计(292).pptx

5.导正销
使用目的: 消除送进导向和送料定距或定位板等粗定位的误差。 主要用于: 级进模
配合使用:与挡料销或与侧刃配合使用
后者粗定位,前者精定位 导入部分:圆锥形的头部
结构组成
导正部分:圆柱形的
固定和活动
第二章 冲裁工艺与冲裁模设计
第九节 冲裁模零部件设计
二、定位零件(续)
5.导正销(续) 基本尺寸:导正部分直径d——与导正孔采取H7/h6或H7/h7配合
导正部分高度h——取h=(0.8~1.2)t
与挡料销的位置关系:
a图
s1
s
DT 2
D 2
0.1 s
DT D 2
0.1
b图
s1 s
DT 2
D 2
0.1 s
DT D 2
0.1
第二章 冲裁工艺与冲裁模设计
第九节 冲裁模零部件设计
二、定位零件(续)
6.定位板和定位销 定位方式:外缘定位、内孔定位 定位板厚度或定位销高度见表2-29(p37)
①弹簧弹顶挡料装置 ②扭簧弹顶挡料装置 ③橡胶弹顶挡料装置 ④回带式挡料装置 (3)始用挡料装置
第二章 冲裁工艺与冲裁模设计
第九节 冲裁模零部件设计
二、定位零件(续)
4.侧刃
侧刃:在级进模中,为了限定条料送进距离,在条料侧边冲切出
一定尺寸缺口的凸模。
特点:定距精度高、可靠
适用:薄料、定距精度和生产效率要求高的情况
第二章 冲裁工艺与冲裁模设计
第九节 冲裁模零部件设计
二、定位零件(续)
1.导料销、导料板(续) 导料板: 设在条料两侧 结构形式:一种是标准结构,它与卸料板(或导板)分开制造;
一种是与卸料板制成整体的结构。
使用目的: 消除送进导向和送料定距或定位板等粗定位的误差。 主要用于: 级进模
配合使用:与挡料销或与侧刃配合使用
后者粗定位,前者精定位 导入部分:圆锥形的头部
结构组成
导正部分:圆柱形的
固定和活动
第二章 冲裁工艺与冲裁模设计
第九节 冲裁模零部件设计
二、定位零件(续)
5.导正销(续) 基本尺寸:导正部分直径d——与导正孔采取H7/h6或H7/h7配合
导正部分高度h——取h=(0.8~1.2)t
与挡料销的位置关系:
a图
s1
s
DT 2
D 2
0.1 s
DT D 2
0.1
b图
s1 s
DT 2
D 2
0.1 s
DT D 2
0.1
第二章 冲裁工艺与冲裁模设计
第九节 冲裁模零部件设计
二、定位零件(续)
6.定位板和定位销 定位方式:外缘定位、内孔定位 定位板厚度或定位销高度见表2-29(p37)
①弹簧弹顶挡料装置 ②扭簧弹顶挡料装置 ③橡胶弹顶挡料装置 ④回带式挡料装置 (3)始用挡料装置
第二章 冲裁工艺与冲裁模设计
第九节 冲裁模零部件设计
二、定位零件(续)
4.侧刃
侧刃:在级进模中,为了限定条料送进距离,在条料侧边冲切出
一定尺寸缺口的凸模。
特点:定距精度高、可靠
适用:薄料、定距精度和生产效率要求高的情况
第二章 冲裁工艺与冲裁模设计
第九节 冲裁模零部件设计
二、定位零件(续)
1.导料销、导料板(续) 导料板: 设在条料两侧 结构形式:一种是标准结构,它与卸料板(或导板)分开制造;
一种是与卸料板制成整体的结构。
冲压工艺与模具设计概述 ppt课件
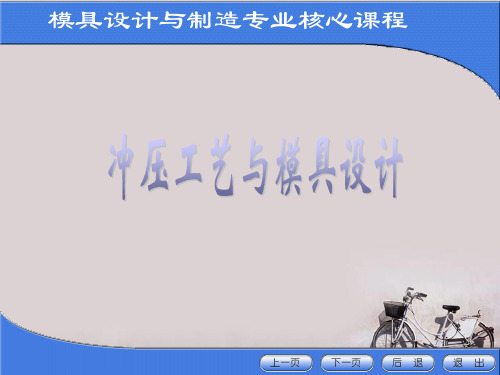
第一单元 冲压工艺与模具设计概述
五、冲压技术现状与发展方向(续)
2.冲压技术发展方向 满足产品开发在T(Time)、Q(Quality)、 C(Cost)、 S(Service)、E(Environment)的要求。 (1)冲压成形理论及冲压工艺 加强理论研究,开展CAE技术应用。 开发和应用冲压新工艺。
2.冲压技术发展方向(续) (3)模具新材料及热、表处理 提高使用性能,改善加工性能 ,提高寿命。 (4)模具CAD/CAM技术 二、三维相结合的数字化设计技术与数字化制造技术。 模具行业是最早应用CAD/CAM技术的行业之一。 (5)快速经济制模技术 加快模具的制造速度,降低模具生产成本。适应小批 量试制。 (6)先进生产管理模式 并行工程思想、标准化、专业化生产。
模具设计与制造专业核心课程
第一单元 冲压工艺与模具设计概述
内容简介:
本章讲述冲压模具设计与制造的基础知识。 涉及冲压和冲模概念、冲压工序和冲模分类;常见冲压 设备及工作原理、选用原则;冲压成形基本原理和规律;冲 压成形性能及常见冲压材料;模具材料种类、性能、选用原
则及热处理方法;模具制造特点、模具零件加工方法及应用
一、冲压与冲模概念
2.冲压成形加工特点
低耗、高效、低成本 “一模一样”、质量稳定、高一致性 可加工薄壁、复杂零件
板材有良好的冲压成形性能
模具成本高
所以,冲压成形适宜批量生产。
第一单元 冲压工艺与模具设计概述
一、冲压与冲模概念
2.冲压成形加工特点(续)
冲压加工是制造业中最常用的一种材料成形加工方法。 冲压成形产品示例一——日常用品
冲模设计与制造必须有系统观点,必须考虑企业实际情况 和产品生产批量,在保证产品质量的前提下,寻求最佳的技术
冲压工艺及模具设计PPT课件

刃口尺寸计算表2.3.2
例1
冲制图示零件,材料为Q235钢,料厚 t=0.5mm。计算冲裁凸、凹模刃口尺寸及 公差。
解:由图可知,该零件属于无特殊要求 的一般冲孔、落料。
外形
3600.62
mm
由落料获得,2
6 0.12 0
mm
和18±0.09由冲孔同时获得。查表2.3.3得,
2Cmin 0.04mm, 2Cmax 0.06mm,则
故: Dd 35.6900.012 mm
mDp 35.6500.008 mm
例2
如图所示的落料件,其中
a 8000.42 mm
b 4000.34 mm c 3500.34 mm
d=
e 1500.12 mm
2板2料±0厚.1度4mt=m1mm,材料为10号钢。试计
算冲裁件的凸模、凹模刃口尺寸及制造公
设计与制造新模具时应采用最小合理间隙 Zmin
* 对模具寿命要求比较高,材料等级高, 在合理值范围内取大值。
* 对模具寿命要求比较低,材料等级低, 在合理值范围内取小值
* 高耐磨性材料本身硬度高,耐磨性好,其冲裁力, 磨损小,一定寿命范围内保证制件精度。
§2-3 凸模与凹模刃口尺寸的计算
一、刃口尺寸计算的依据和原则
按凸模与凹模图样分别加工法
( ) (1)落料
Dδ =
Dmax
-xΔ
+δd 0
( ) ( ) Dp =
Dd
-2C min
0 δp
=
Dmax - xΔ -2C min
0 δp
(2)冲孔
( ) d p
=
d min
+xΔ
0 δp
( ) ( ) dd
例1
冲制图示零件,材料为Q235钢,料厚 t=0.5mm。计算冲裁凸、凹模刃口尺寸及 公差。
解:由图可知,该零件属于无特殊要求 的一般冲孔、落料。
外形
3600.62
mm
由落料获得,2
6 0.12 0
mm
和18±0.09由冲孔同时获得。查表2.3.3得,
2Cmin 0.04mm, 2Cmax 0.06mm,则
故: Dd 35.6900.012 mm
mDp 35.6500.008 mm
例2
如图所示的落料件,其中
a 8000.42 mm
b 4000.34 mm c 3500.34 mm
d=
e 1500.12 mm
2板2料±0厚.1度4mt=m1mm,材料为10号钢。试计
算冲裁件的凸模、凹模刃口尺寸及制造公
设计与制造新模具时应采用最小合理间隙 Zmin
* 对模具寿命要求比较高,材料等级高, 在合理值范围内取大值。
* 对模具寿命要求比较低,材料等级低, 在合理值范围内取小值
* 高耐磨性材料本身硬度高,耐磨性好,其冲裁力, 磨损小,一定寿命范围内保证制件精度。
§2-3 凸模与凹模刃口尺寸的计算
一、刃口尺寸计算的依据和原则
按凸模与凹模图样分别加工法
( ) (1)落料
Dδ =
Dmax
-xΔ
+δd 0
( ) ( ) Dp =
Dd
-2C min
0 δp
=
Dmax - xΔ -2C min
0 δp
(2)冲孔
( ) d p
=
d min
+xΔ
0 δp
( ) ( ) dd
- 1、下载文档前请自行甄别文档内容的完整性,平台不提供额外的编辑、内容补充、找答案等附加服务。
- 2、"仅部分预览"的文档,不可在线预览部分如存在完整性等问题,可反馈申请退款(可完整预览的文档不适用该条件!)。
- 3、如文档侵犯您的权益,请联系客服反馈,我们会尽快为您处理(人工客服工作时间:9:00-18:30)。
2
第2章 冲裁工艺与模具设计
▪ 教学重点和难点: ▪ 各种模具及其组成零件的结构及特点; ▪ 冲裁模的设计步骤及模具刃口尺寸的计算。
3
第2章 冲裁工艺与模具设计
▪ 案例导入: ▪ 要大批量冲制如下图所示的工件(材料为08பைடு நூலகம்,
材料厚度为2mm,制件精度为IT14级),应选 择何种模具?如何提高板料的材料利用率?凸 模和凹模的间隙应是多少?如何计算凸模和凹 模刃口尺寸和公差?模具主要零件的结构及尺 寸如何设计?如何选择标准模架和选用压力机?
▪ 断裂带c:是由刃口附近的微裂纹在拉应力作用下不 断扩展而形成的撕裂面。
▪ 毛刺区d:毛刺。
13
2.2 冲 裁 间 隙
▪ 2.2.1 冲裁间隙对冲裁件断面质量的影响 ▪ 2.2.2 冲裁间隙对冲裁件尺寸精度的影响 ▪ 2.2.3 冲裁间隙对冲裁力、卸料力、推料力、顶件
力的影响 ▪ 2.2.4 冲裁间隙对模具寿命的影响 ▪ 2.2.5 合理间隙值的确定
孔。
8
2.1 冲裁变形过程分析
图2-1 平板垫圈 9
2.1.1 冲裁变形过程
▪ 如图2-2所示变形过程: ▪ 如果模具间隙正常,冲裁变形过程大致可分为如下3个阶段。 ▪ 1. 弹性变形阶段 ▪ 见图2-2(a)。在凸模和凹模压力的作用下,板料产生弹性压
缩、拉伸和弯曲变形。 ▪ 2. 塑性变形阶段 ▪ 见图2-2(b)。间隙越大,弯曲和拉伸变形也越大。 ▪ 3. 断裂分离阶段 ▪ 见图2-2(c)、(d)、(e)。
6
2.1 冲裁变形过程分析
2.1.1 冲裁变形过程 2.1.2 冲裁断面特征
7
2.1 冲裁变形过程分析
▪ 冲裁是利用模具在压力机上使板料沿一定轮廓形状 产生分离的一种冲压工序。它包括落料、冲孔、切 口、切边、剖切等多种工序。
▪ 落料和冲孔是两种最基本的冲裁形式。 ▪ 从板料上冲下所需形状的零件(或毛料)叫落料; ▪ 在工件上冲出所需形状的孔(冲去部分为废料)叫冲
14
2.2 冲 裁 间 隙
▪ 冲裁模凸模与凹模刃口部分横向尺寸之差成为冲 裁间隙,用Z表示:
ZDdDp
▪ 式中:Z-冲裁间隙(mm);
▪
Dd-凹模尺寸(mm) ;
▪
Dp-凸模尺寸(mm) 。
15
2.2 冲 裁 间 隙
图2-4 冲裁间隙
16
2.2.1 冲裁间隙对冲裁件断面质量的影响
▪ 在4个特征区中,光亮带越宽,断面质量越好。
19
2.2.3 冲裁间隙对冲裁力、卸料力、推料力、顶件力的影响
▪ 随着间隙的增大,材料在冲裁时所受的拉应力将增大,材料 容易断裂分离,冲裁力有一定程度的降低。但在正常情况下, 间隙对冲裁力的影响并不很大。
▪ 间隙对卸料力、推件力的影响比较显著。随间隙增大,卸料 力和推件力都将减小。一般当单面间隙增大到材料厚度的 15%~25%时,卸料力几乎降到零。但间隙继续增大时会引 起毛刺增大,又将引起卸料力、顶件力的迅速增大。
第2章 冲裁工艺与模具设计
(时间:4次课,8学时)
1
第2章 冲裁工艺与模具设计
▪ 教学目标: ▪ 本章介绍冷冲压模具设计的重要内容,也是最
基础的内容。通过本章的学习,将达到能设计 中等复杂程度冲裁模具的水平。为此,应了解 冲裁变形过程及冲裁端面的特征;掌握冲裁间 隙对冲裁件精度和模具的影响;掌握确定合理 冲裁间隙的方法;掌握排样方法,学会确定条 料宽度;掌握冲裁力及压力中心的计算。
用最小合理间隙Zmin。
▪ 确定合理间隙值有理论确定法和经验确定法两种。
▪ 1. 理论确定法
▪ 2. 经验确定法
21
2.2.5 合理间隙值的确定
▪ 因此,在冲压实际生产中,主要根据冲裁件断面质 量、尺寸精度和模具寿命这三个因素综合考虑,给
间隙规定一个范围值。这个间隙范围就称为合理间
隙,这个范围的最小值称为最小合理间隙(Zmin),最 大值称为最大合理间隙(Zmax)。考虑到在生产过程 中的磨损使间隙变大,故设计与制造新模具时应采
17
2.2.1 冲裁间隙对冲裁件断面质量的影响
▪ 图2-5 冲裁间隙对冲裁件断面的影响
18
2.2.2 冲裁间隙对冲裁件尺寸精度的影响
▪ 冲裁件的尺寸精度,是指冲裁件的实际尺寸 与图纸上的基本尺寸之差。差值越小,精度 越高。这个差值包括两方面的偏差:
▪ 一是冲裁件相对于凸模或凹模尺寸的偏差, ▪ 二是模具本身的制造偏差。
▪ 塑性较差的材料容易断裂,材料被剪切不久就会出 现裂纹、分离,使断裂带增宽,而光亮带和圆角带 所占的比例较小,毛刺也较小。
▪ 材料塑性较好,冲裁时裂纹出现得较晚,材料被剪 切的深度较大,光亮带所占的比例就大,圆角和毛 刺也大。
▪ 冲裁间隙对冲裁件断面的影响如图2-5所示。
▪ 在设计和制造模具时,应使冲裁间隙保持在一个合 理的范围之内。
4
第2章 冲裁工艺与模具设计
5
第2章 冲裁工艺与模具设计
▪ 2.1 冲裁变形过程分析 ▪ 2.2 冲 裁 间 隙 ▪ 2.3 冲裁模刃口尺寸计算 ▪ 2.4 冲压力及压力中心计算 ▪ 2.5 冲裁件的工艺性 ▪ 2.6 排 样 ▪ 2.7 精 密 冲 裁 ▪ 2.8 模 具 设 计 ▪ 2.9 冲裁模的设计步骤 ▪ 2.10 冲裁模设计实训 ▪ 习题与练习
20
2.2.4 冲裁间隙对模具寿命的影响
▪ 冲模失效的形式一般有磨损、崩刃、变形、胀裂和折断。 ▪ 冲裁力主要集中在凸模和凹模的刃口部分。刃口变形和端面
磨损加剧,甚至崩刃。 ▪ 所以为了减少凸、凹模的磨损,延长模具使用寿命,在保证
冲裁件质量的前提下适当采用较大的间隙值是十分必要的。 若采用小间隙,就必须提高模具的硬度和耐磨性,提高模具 的制造精度,冲裁时采用良好的润滑,以减小磨损。
10
2.1.1 冲裁变形过程
11
2.1.2 冲裁断面特征
▪ 断面分析:圆角带;光亮带;断裂带;毛刺区。
12
2.1.2 冲裁断面特征
▪ 圆角带a:当凸模刃口压入材料时,刃口附近的材 料产生弯曲和伸长变形,材料被拉入间隙,形成圆 角带。材料的塑性越好、凸模和凹模的间隙越大, 圆角带也越大。
▪ 光亮带b:当刃口切入材料后,材料受到凸模和凹 模剪切应力τ和挤压应力σ的作用而形成光亮垂直的 断面。通常光亮带占整个断面的1/2~1/3。
第2章 冲裁工艺与模具设计
▪ 教学重点和难点: ▪ 各种模具及其组成零件的结构及特点; ▪ 冲裁模的设计步骤及模具刃口尺寸的计算。
3
第2章 冲裁工艺与模具设计
▪ 案例导入: ▪ 要大批量冲制如下图所示的工件(材料为08பைடு நூலகம்,
材料厚度为2mm,制件精度为IT14级),应选 择何种模具?如何提高板料的材料利用率?凸 模和凹模的间隙应是多少?如何计算凸模和凹 模刃口尺寸和公差?模具主要零件的结构及尺 寸如何设计?如何选择标准模架和选用压力机?
▪ 断裂带c:是由刃口附近的微裂纹在拉应力作用下不 断扩展而形成的撕裂面。
▪ 毛刺区d:毛刺。
13
2.2 冲 裁 间 隙
▪ 2.2.1 冲裁间隙对冲裁件断面质量的影响 ▪ 2.2.2 冲裁间隙对冲裁件尺寸精度的影响 ▪ 2.2.3 冲裁间隙对冲裁力、卸料力、推料力、顶件
力的影响 ▪ 2.2.4 冲裁间隙对模具寿命的影响 ▪ 2.2.5 合理间隙值的确定
孔。
8
2.1 冲裁变形过程分析
图2-1 平板垫圈 9
2.1.1 冲裁变形过程
▪ 如图2-2所示变形过程: ▪ 如果模具间隙正常,冲裁变形过程大致可分为如下3个阶段。 ▪ 1. 弹性变形阶段 ▪ 见图2-2(a)。在凸模和凹模压力的作用下,板料产生弹性压
缩、拉伸和弯曲变形。 ▪ 2. 塑性变形阶段 ▪ 见图2-2(b)。间隙越大,弯曲和拉伸变形也越大。 ▪ 3. 断裂分离阶段 ▪ 见图2-2(c)、(d)、(e)。
6
2.1 冲裁变形过程分析
2.1.1 冲裁变形过程 2.1.2 冲裁断面特征
7
2.1 冲裁变形过程分析
▪ 冲裁是利用模具在压力机上使板料沿一定轮廓形状 产生分离的一种冲压工序。它包括落料、冲孔、切 口、切边、剖切等多种工序。
▪ 落料和冲孔是两种最基本的冲裁形式。 ▪ 从板料上冲下所需形状的零件(或毛料)叫落料; ▪ 在工件上冲出所需形状的孔(冲去部分为废料)叫冲
14
2.2 冲 裁 间 隙
▪ 冲裁模凸模与凹模刃口部分横向尺寸之差成为冲 裁间隙,用Z表示:
ZDdDp
▪ 式中:Z-冲裁间隙(mm);
▪
Dd-凹模尺寸(mm) ;
▪
Dp-凸模尺寸(mm) 。
15
2.2 冲 裁 间 隙
图2-4 冲裁间隙
16
2.2.1 冲裁间隙对冲裁件断面质量的影响
▪ 在4个特征区中,光亮带越宽,断面质量越好。
19
2.2.3 冲裁间隙对冲裁力、卸料力、推料力、顶件力的影响
▪ 随着间隙的增大,材料在冲裁时所受的拉应力将增大,材料 容易断裂分离,冲裁力有一定程度的降低。但在正常情况下, 间隙对冲裁力的影响并不很大。
▪ 间隙对卸料力、推件力的影响比较显著。随间隙增大,卸料 力和推件力都将减小。一般当单面间隙增大到材料厚度的 15%~25%时,卸料力几乎降到零。但间隙继续增大时会引 起毛刺增大,又将引起卸料力、顶件力的迅速增大。
第2章 冲裁工艺与模具设计
(时间:4次课,8学时)
1
第2章 冲裁工艺与模具设计
▪ 教学目标: ▪ 本章介绍冷冲压模具设计的重要内容,也是最
基础的内容。通过本章的学习,将达到能设计 中等复杂程度冲裁模具的水平。为此,应了解 冲裁变形过程及冲裁端面的特征;掌握冲裁间 隙对冲裁件精度和模具的影响;掌握确定合理 冲裁间隙的方法;掌握排样方法,学会确定条 料宽度;掌握冲裁力及压力中心的计算。
用最小合理间隙Zmin。
▪ 确定合理间隙值有理论确定法和经验确定法两种。
▪ 1. 理论确定法
▪ 2. 经验确定法
21
2.2.5 合理间隙值的确定
▪ 因此,在冲压实际生产中,主要根据冲裁件断面质 量、尺寸精度和模具寿命这三个因素综合考虑,给
间隙规定一个范围值。这个间隙范围就称为合理间
隙,这个范围的最小值称为最小合理间隙(Zmin),最 大值称为最大合理间隙(Zmax)。考虑到在生产过程 中的磨损使间隙变大,故设计与制造新模具时应采
17
2.2.1 冲裁间隙对冲裁件断面质量的影响
▪ 图2-5 冲裁间隙对冲裁件断面的影响
18
2.2.2 冲裁间隙对冲裁件尺寸精度的影响
▪ 冲裁件的尺寸精度,是指冲裁件的实际尺寸 与图纸上的基本尺寸之差。差值越小,精度 越高。这个差值包括两方面的偏差:
▪ 一是冲裁件相对于凸模或凹模尺寸的偏差, ▪ 二是模具本身的制造偏差。
▪ 塑性较差的材料容易断裂,材料被剪切不久就会出 现裂纹、分离,使断裂带增宽,而光亮带和圆角带 所占的比例较小,毛刺也较小。
▪ 材料塑性较好,冲裁时裂纹出现得较晚,材料被剪 切的深度较大,光亮带所占的比例就大,圆角和毛 刺也大。
▪ 冲裁间隙对冲裁件断面的影响如图2-5所示。
▪ 在设计和制造模具时,应使冲裁间隙保持在一个合 理的范围之内。
4
第2章 冲裁工艺与模具设计
5
第2章 冲裁工艺与模具设计
▪ 2.1 冲裁变形过程分析 ▪ 2.2 冲 裁 间 隙 ▪ 2.3 冲裁模刃口尺寸计算 ▪ 2.4 冲压力及压力中心计算 ▪ 2.5 冲裁件的工艺性 ▪ 2.6 排 样 ▪ 2.7 精 密 冲 裁 ▪ 2.8 模 具 设 计 ▪ 2.9 冲裁模的设计步骤 ▪ 2.10 冲裁模设计实训 ▪ 习题与练习
20
2.2.4 冲裁间隙对模具寿命的影响
▪ 冲模失效的形式一般有磨损、崩刃、变形、胀裂和折断。 ▪ 冲裁力主要集中在凸模和凹模的刃口部分。刃口变形和端面
磨损加剧,甚至崩刃。 ▪ 所以为了减少凸、凹模的磨损,延长模具使用寿命,在保证
冲裁件质量的前提下适当采用较大的间隙值是十分必要的。 若采用小间隙,就必须提高模具的硬度和耐磨性,提高模具 的制造精度,冲裁时采用良好的润滑,以减小磨损。
10
2.1.1 冲裁变形过程
11
2.1.2 冲裁断面特征
▪ 断面分析:圆角带;光亮带;断裂带;毛刺区。
12
2.1.2 冲裁断面特征
▪ 圆角带a:当凸模刃口压入材料时,刃口附近的材 料产生弯曲和伸长变形,材料被拉入间隙,形成圆 角带。材料的塑性越好、凸模和凹模的间隙越大, 圆角带也越大。
▪ 光亮带b:当刃口切入材料后,材料受到凸模和凹 模剪切应力τ和挤压应力σ的作用而形成光亮垂直的 断面。通常光亮带占整个断面的1/2~1/3。