烧结余热技术说明书 精品
钢铁企业烧结余热利用与发电技术

钢铁企业烧结余热利用与发电技术摘要:钢铁企业烧结工序的能耗仅次于炼铁工序,一般为钢铁企业总能耗的10%〜20%。
我国烧结工序的能耗与先进国家相比有较大差距,每吨烧结矿的平均能耗要高20kgce。
在烧结工序总能耗中,有近50%的热能以烧结机烟气和冷却机废气的显热形式排入大气,即浪费了热能又污染了环境。
据日本某钢铁厂热平衡测试数据表明,烧结机的热收入中烧结矿显热占28.2%、废气显热占31.8%。
可见,烧结厂余热回收的重点为烧结废(烟)气余热和烧结矿(产品)显热回收。
烧结余热也是目前我国低温余热资源应用的重点。
一、烧结余热利用方式与现状烧结余热主要利用方式有(1)在点火前对烧结料层进行预热;(2)送到点火器,进行热风点火;(3)实行热风烧结,回收烧结过程的热量和成品矿显热,降低烧结能耗;(4)利用余热锅炉回收烧结或冷却热废风,所产蒸汽用于预热烧结混合料或生活取暖等,或者进行蒸汽升值发电。
目前,我国大型烧结厂普遍采用了余热回收利用装置,但多数中、小烧结厂的余热仍未得到有效利用。
国内重点大中型企业,钢铁协会会员单位在2006年钢铁协会调研时,只有不到三分之一的烧结机配备了烧结余热利用设备,大部分是蒸汽回收并入全厂动力蒸汽管网,很少利用余热发电的。
近年来,随着低温烟气余热锅炉技术和低参数补汽式汽轮机技术的发展,使低温烟气余热发电成为可能。
二、烧结余热利用与发电技术目前我国烧结余热利用的重点和难点在于:由于存在漏风率高导致废气温度降低,又要保证进入除尘器前废气温度在露点以上等原因,回收利用烧结余热较困难。
因此,如何降低漏风率以提高烧结机烟气温度,以及在保证烧结废气除尘所需温度条件下,实现烧结机尾部高温段废气显热回收?烧结余热蒸汽发电核心技术的消化吸收和本土化,是烧结余热回收的重点。
如开发此技术将烧结矿余热充分利用,则钢铁行业年可节约能源约900万吨标准煤。
烧结余热发电是利用低温余热的一个有效途径,但目前来说应用很少,且存在一些问题,在运行过程中,由于烧结机和环冷机工况发生变化时,余热回收系统的工作参数也将随之变动,输出的蒸汽压力、温度、流量也将发生变化,从而影响发电机组的运行效率。
钢厂烧结机余热技术介绍 共19页PPT资料

江苏中天能源设备有限公司与安徽工业大学、福建三明钢厂、江苏煌明科技公 司多方合作,于2019年成功设计制造了国内第一套烧结机大烟道余热锅炉,系 统运行稳定,取得了良好的经济效益,并拥有国家发明专利。
一种内置于烧结机大小烟道上的 余热锅炉系统 专利技术介绍
江苏能源科技有限公司
公司简介
江苏能源科技有限公司为国家发改委备案的专业化节能服务公司,国家高新 技术企业,国内著名的合同能源管理示范合作单位,行业排名第26位。
我 们 联 合 江苏能源设备有限公司 ( 生产各类余热回收设备国内最知名 的专业厂家之一)。 提供高炉高风温的组合换热系统、烧结机大烟道余热锅炉、环冷机余热 锅炉等。产品广泛应用于钢铁冶炼、石油化工等行业。 “科技创新、优质高效、顾客至上、诚信守约”为公司服务方针,从追求 完善到卓越,实现携手共进,合作共赢!
3、节能增效: 3.1、实际产汽量:11~13吨每小时,增加发电功率约1900KW.h; 3.2、年发电量:1900×24×330=15048000KW.h(年按330天运行计算); 3.3、节能增益:15048000×0.46=692万元(电费单价0.46元/度)。
4、系统投资: 直接680万元Biblioteka 6、综合节能效益:
692-100=592万
投资回收周期:680/592=0.93年,约14个月可收回投资。
合作服务单位
谢谢!
一、项目 背 景
烧结是冶金企业主要耗能工艺,对烧结工艺来说,可进行余热回收的主要有两 部分:其一,冷却机部分;其二:烧结机大小烟道部分。
马钢烧结余热发电技术讲解

项目建设及运行实践
1 .项目建设
马钢烧结带冷废气余热利用工程,是我国第一次在 烧结系统实施的低温废气余热发电项目,不仅没有现成的 经验可借鉴,而且对其工艺设备、技术,工程施工等方面 都缺乏认识。针对这种情况,公司专门成立项目部,来强 化管理、落实责任。从前期调研开始,就不放过任何细节, 充分领会烧结带冷废气余热发电工艺方案和各种运行参数, 从而使整个工程按计划顺利进行。与此同时,还对余热发 电各个岗位的人员进行全面系统的理论培训和到兄弟单位 进行实际操作培训,并制定了操作规程、安全规程以及设 备规程。
废气锅炉采用卧式自然循环汽包炉,额定参数:烟气温度 395℃、流量40万m3/h、含尘量≤2g/ m3;过热蒸汽温度375℃、 压力1.95Mpa、流量37.4t/h。
汽轮发电机组采用多级、冲动、混压、凝汽式,主汽门进汽 参数为温度374℃、压力20.5 MPa (表压),耗汽量86t/h(含闪 蒸器流量),额定功率17.5MW。
(3)摸索闪蒸器产生的混汽与发电量的关系,找出合适 的运行方式。烟气余热发电采用了闪蒸器产生的混汽发 电新技术,将省煤器的部分热水,导入闪蒸器进行闪蒸, 产生饱和蒸汽,和过热蒸汽一同进入发电机发电,随着 闪蒸器产生的混汽量的增加,可以明显提高发电量。
马鞍山钢铁股份有限公司
MAANSHAN IRON & STEEL CO.,LTD.
马鞍山钢铁股份有限公司
MAANSHAN IRON & STEEL CO.,LTD.
项目建设及运行实践
2)改进措施
(1)提高烧结系统生产的稳定性,设备运行的可靠性, 降低工艺参数波动及非正常停机对烟气品质的影响,保 证烧结矿热源的稳定性。
烧结厂余热利用技术简介

烧结厂余热利用技术简介1. 引言烧结是一种将粉煤灰、石灰石或其它成分相似的原料通过加热使之部分熔化,然后回结固化成块状的冶金过程。
这个过程产生的高温烟气和废热在烧结厂通常都被排放到大气中。
然而,随着对能源资源的需求和环境保护意识的增强,如何有效利用烧结厂的余热已成为研究和开发的重点。
本文将简要介绍几种常见的烧结厂余热利用技术,并分析其优点和局限性。
2. 烧结厂余热利用技术2.1 热交换器技术热交换器技术是一种常见的烧结厂余热利用技术。
热交换器可以将高温烟气中的热能传递给废水、蒸汽或其他介质,以实现能量的回收和利用。
热交换器通常包括换热管道和换热器设备。
热交换器技术的优点在于可以提供连续的热能供应,并减少对外部能源的需求。
然而,此技术的局限性在于热交换器设备的成本较高,维护困难,并且对脏污、腐蚀性介质敏感。
2.2 ORC技术ORC技术(有机朗肯循环)是一种将烧结厂余热转化为电力的技术。
ORC系统通过将高温烟气中的热能转移到有机工质中,然后通过有机工质的蒸汽驱动涡轮发电机产生电力。
与传统蒸汽发电系统相比,ORC技术可以在较低的温度下工作,提高了热能转化的效率。
此外,ORC技术还可以通过调整有机工质的选用来适应不同温度下的余热利用。
然而,该技术需要较高的初投资成本,并且对有机工质的选择和运行维护要求较高。
2.3 废热蒸汽利用技术废热蒸汽利用技术是一种将烧结厂余热转化为蒸汽以供其他生产过程使用的技术。
在烧结厂中,产生的高温烟气可以通过余热锅炉将废热转化为蒸汽,然后再将蒸汽输送到其他工序中进行能量回收。
废热蒸汽利用技术可以减少对外部能源的需求,并提高能源利用效率。
然而,该技术的缺点在于需要较大的设备投资,且对蒸汽管道的要求较高。
3. 总结烧结厂余热利用技术是一种重要的能源回收利用手段,可以减少环境污染,降低能源消耗,提高能源利用效率。
本文介绍了几种常见的烧结厂余热利用技术,并分析了它们的优点和局限性。
无论是热交换器技术、ORC技术还是废热蒸汽利用技术,都需要根据具体的烧结厂情况和需求来选择和应用。
烧结厂余热利用技术简介
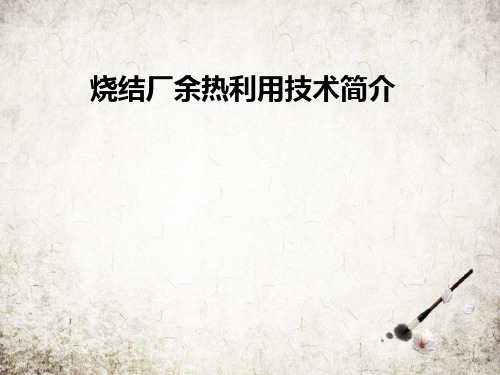
冷却机余热回收
冷却机余热回收的途径
烧结矿从烧结机尾经过热破碎后卸到冷却机上,卸出的烧结饼温度平均在 500∽800℃之间。热烧结矿经过冷却机冷却,使得从冷却机排出的烧结矿温度 在150 ℃以下。热烧结矿在冷却过程中其热能变为废气显热,废气温度随冷却 机部位的不同而不同,给矿部温度最高,在450 ℃以上,排矿部温度最低。余 热可以分为高、中、低三个温区分别利用。
火力发电
火力发电一般是指利用煤炭、石油和天然气等 燃料燃烧时产生的热能来加热水,使水变成高 温、高压水蒸气,然后再由水蒸气推动汽轮机 做功,进而带动发电机转动来发电的方式的总 称。我国的火电厂以燃煤为主。
目前火电在我国发电行业占据主导地位。
按照蒸汽的压力等级,火电厂可分为: 中低压(3.43MPa以下)、高压(8.83MPa) 、 超高压(12.75MPa)、亚临界(16.18MPa) 、 超临界(22.1MPa)、超超临界(30MPa)。
高温段余热利用
高温段余热废气能量品味比较高,动力回收形式效率也比较高,将热废气的热 能转换为能级较高的电能的回收方式为首选。通过余热锅炉将热废气余热转化 成蒸汽,再通过汽轮发电机组有效的转化为电能供烧结厂自用或并入企业电网 。
中温段余热利用
中温段温度低于300℃,采用余热锅炉进行回收热效率比较低,经济性比较差。采用直接 回收利用更为合理。该段废气为高含氧量的热空气,可以作为烧结点火助燃空气和热风烧 结。 热风助燃的优点:
国内余热利用情况
太钢一号烧结生产线余热利用系统为1998年日本政府实施“绿援计划 ”时在太钢援建的项目。通过设置2台强制循环余热锅炉,共用一个 汽包、锅炉给水系统和控制系统,产生1.0Mpa,193℃的饱和蒸汽, 送往生活蒸汽管网,对烧结环冷机余热进行回收。 马钢二炼 两套300m烧结机 装机17.5MW 05年9月投运 济钢二烧 一套320m烧结机 装机8.2MW 07年3月投运 山东宏达 两套132m烧结机 装机6MW 07年3月投运 红钢 两套90m烧结机 装机4.5MW 07年12月投运 安钢 360m2+400m2烧结机 装机25MW 08年9月23日并网发电
烧结设计手册

烧结设计手册摘要:一、烧结技术简介1.烧结定义与原理2.烧结工艺流程二、烧结原料与设备1.原料选择与配比2.烧结设备分类及选型三、烧结过程控制与管理1.烧结参数控制2.质量检测与分析3.安全生产与管理四、烧结产品与应用领域1.烧结产品分类2.应用领域及市场需求五、烧结技术创新与发展趋势1.绿色环保烧结技术2.高效节能烧结工艺3.智能化烧结工厂正文:一、烧结技术简介1.烧结定义与原理烧结是一种通过高温加热将固体物料转变为具有较高强度、密度和特定性能的固体的过程。
在烧结过程中,原料颗粒间的相互作用力逐渐增强,颗粒内部的组织结构发生变化,从而使烧结体具有较好的物理和力学性能。
2.烧结工艺流程烧结工艺流程通常包括原料准备、混合料预处理、烧结、冷却和成品整理等步骤。
首先,对原料进行选择和配比,以满足烧结产品的性能要求。
然后,将原料进行混合,形成均匀的混合料。
接下来,将混合料放入烧结设备中,通过高温加热实现烧结。
烧结过程中,需要对烧结参数进行控制,以保证烧结体的质量。
最后,对烧结体进行冷却和整理,获得最终的成品。
二、烧结原料与设备1.原料选择与配比烧结原料的选择应根据烧结产品的性能要求,结合原料的物理、化学和力学性能进行。
在选择原料时,还需考虑原料的资源、价格和环境友好性等因素。
配比方面,要保证混合料的均匀性,防止烧结过程中出现成分不均的现象。
2.烧结设备分类及选型烧结设备主要包括回转窑、立磨、烧结砖机等。
在选型时,要根据烧结工艺要求、产量、投资预算等因素进行综合考虑,确保设备的性能和可靠性。
三、烧结过程控制与管理1.烧结参数控制烧结过程的主要参数包括温度、压力、气氛和时间等。
合理控制这些参数,可以保证烧结体的质量。
在实际操作中,可通过调节烧结设备的燃烧器、风机等部件来实现参数的控制。
2.质量检测与分析烧结过程的质量检测主要包括密度、强度、透气性等指标。
通过对这些指标的检测和分析,可以及时发现烧结过程中的问题,采取相应措施进行调整。
烧结余热回收利用技术规范

《烧结余热回收利用技术规范》(征求意见稿)编制说明《烧结余热回收利用技术规范》编写组二〇一五年五月目次一项目背景 (1)二标准制定的必要性和原则 (2)三采标情况 (4)四标准主要内容 (4)五调查验证的情况和结果 (21)六与有关的现行法律、法规和强制性国家标准的关系 (21)七重大分歧意见的处理经过和依据 (21)八标准水平建议,预期的社会经济效果 (21)九对该标准作为强制性标准或推荐性标准的建议 (22)十贯彻标准的要求和措施建议 (22)《烧结余热回收利用技术规范》编制说明一项目背景1 任务来源根据国家标准委综合[2014]51号关于下达《氧化铝单位产品能源消耗限额》等122项国家标准制修订项目计划的通知,计划编号20140105-T-605的《烧结余热回收利用技术规范》为国家标准制定项目。
2 编制单位本规范由由济钢集团国际工程技术有限公司和冶金工业信息标准研究院,并在有关设计研究单位、钢铁冶金企业等单位的协助下进行编制。
3 主要工作过程(1)根据国家标准委国标委综合[2014]51号关于下达《氧化铝单位产品能源消耗限额》等122项国家标准制修订项目计划和全国钢标准化技术委员会SAC/TC183钢标委[2014]21号《关于下达全国钢标准化技术委员会化解产能过剩标准支撑工程项目计划的通知》的要求,济钢集团国际工程技术有限公司于2014年9月成立了标准编写组。
(2)2014年9月~2014年10月,确定标准范围、要素和标准结构,并编制了工作计划,明确了标准章节的起草人员和完成时间。
(3)2014年11月,全国钢标准化技术委员会在鞍山市主持召1开《轧钢连续加热炉热平衡测试与计算方法》等21项节能、节水国家标准计划落实会。
会议确定了本标准的基本框架、提出了下一步的工作思路,初步确定了标准参与起草单位、验证单位和工作进度。
(4)2014年12月~2015年1月,完成调研论证工作,组织标准的有关调研工作,发放市场调研表,收集好有关信息,论证标准要求的技术指标和方法等内容。
烧结余热回收助燃技术3

~全国能源与热工2004学术年会烧结余热回收助燃技术。
,。
冀望钢婺圭耋堂熹薹:要:。
訾慧工耋竺璧登竖翥篓二辜鬈曩墨二磊篙主芋霎釜霎:妻暑薯罢嚣妻銮三篓鐾二竺皇兰尘篓譬矗尝竺二竺,*兽要璧璧竺;莲饱嘉袤姜磊蒹苫品羞凶茬手寨磊葛晶昙曼釜矗萼工登薏翌磬繁兰竺竺篓箜登鬈重要妻蒹萎蒹磊三豢;:…~”……“”“一”}:国内先进-当兰毪芋.三要鬯篓:苎孽.I箩翌““…翥轰磊结葚蔷套一种余热直接利用的较好方no‘PT,/:+6507。
’而薏:t曼气墨翌。
要型。
是苎式。
凳舅篓i藉蔷莓巍芸磊茸雾赫篡蒜夏茹鲁O。
.0。
25-;0..03…OGJ/t…o!娑笔翼:繁皇璧结裹要望羔矍;晶磊鑫夏甭孚翥赢茹磊};藉羞藻嚣_磊鬲篡孚;j要妻謇查:。
銎曼要耋型望了人们重视,并成为近年;磊善茅嚣差击晶荔主嚣某蕃菘茹募晶嚣赢葛j菜来冶拿节能工作的重点之一。
矗;磊磊杀’i。
嘉釜嚣磊最喜磊釜二三磊覆聂:;i:;趸晶丧。
,。
妻燮钡!戮,}攀黪鬻觑嚣嚣囊雾揽霉婺要黧和30纛慕烧釜曩的兰、苎宴堡奎兰苎:黧皂笔黛蠢兰望莱磊爰箸;磊姜覆吴晶磊夏;基夏翥磊:。
霁螽茹茹!o!怂上.,而这部分苎苎圣苎!竺銎的竺竺釜孽!奎赢;粟呆莉菇;:…一……~…………“竺坌变塑.:??:竺三孝耋竺銎摩气’茸苎釜壁查套查…“;享磊磊;嚣废气量很大,仅靠单一的余热回和回坚犁景墼荸亭:。
………。
吴;藉,i希巍随喜磊萏赢莉用菜茹磊采簖毳孟磊墨竺:。
兰竺竺!‘!温余热数量大,是烧结工序节能收方;j;衰豢未堇葙翥轰蔟:羹桑纛资茹荔蔷磊。
!圭兰苎全!竺堡竺妻:。
呈奎:孽曼竺要妻登甚i参≥:磊菇釜磊;葛荟釜;茹葛晶。
磊落;。
芝璺童都苎要兰譬三!董妻尝璧兰含銎型要堂要究蚤五:最差羞蔷备;再;磊蓁;品氧i蓑某晶。
嘉碰:‘苎擘!:,堕妻至冬要塞竺兰苎竺曼:o篓查竺!I兰,Ⅲ柔蕞采高鬲蘧菇盖呆高箍矗晶;主;蠢磊蔷≤舅≥国内警坌璧氅二竺堂曼套塑竺譬:釜热堂皇些型曼藉磊嘉茶巍磊夏篆磊磊荔蕃莉角_薪磊磊磊j=高;妻孽警三许量!萋竺篓耋竺竺要兰苎二慧竺竺三较1…20…m2烧结机“……“爵荼螽磊磊;鬲美茗毒;‘j磊嚣羞琶暑好紫蛰苎:,苎型要方法望蛩璺变圭詈要鐾!三黧2带冷余热锅茄磊磊赢磊磊高藉i磊磊磊磊囊;至j。
钢铁行业烧结余热发电技术

钢铁行业烧结余热发电技术
一、所属行业:钢铁行业
二、技术名称:钢铁行业烧结余热发电技术
三、适用范围:钢铁行业
四、技术内容:
1.技术原理
钢铁行业烧结、热风炉、炼钢、加热炉等设备产生的废烟气,通过高效低温余热锅炉产生蒸汽,带动汽轮发电机组进行发电。
2.关键技术
通过分级利用余热,使得余热锅炉能最大限度的利用200~400℃的低温余热。
3.工艺流程
烟气收集→余热锅炉→汽轮发电机。
五、主要技术指标:
1.与该节能技术相关生产环节的能耗现状:
200~400℃的低温余热废气,基本没有得到利用。
2.主要技术指标:
可利用烟气温度为200~400℃。
六、技术应用情况:
目前钢铁冶金行业才开始推广应用。
七、典型用户及投资效益:
典型用户马钢
某钢铁投资1.7亿元人民币,安装了低温余热锅炉及汽轮发电机组,年发电量达1.4亿kWh,年取得经济效益7000万元人民币,投资回收期2.5年。
八、推广前景和节能潜力:
钢铁企业的烧结、冶炼、加热等设备产生大量的低温废气,基本没有得到合理利用,所以其推广前景广阔,节能潜力巨大。
“十一五”期间该技术在行业推广到的比例为10%~20%,需要总投资为5亿元人民币,年可发(节)电12亿kWh。
九、推广措施及建议:
钢铁生产过程中,都会产生大量低温烟气,若将其低温余热充分合理利用,将会产生很大的节能效益。
建议政府应积极支持、鼓励,制定特殊政策,激励企业利用低温余热的积极性,节约大量一次能源,创造更多社会效益。
烧结线余热发电技术方案

180烧结余热发电项目基本技术方案目录1 总论 (1)1.1 建设单位基本情况 (1)1.2 工程条件 (1)1.3 工程概述 (3)1.4主要经济技术指标 (7)1.5技术特点 (8)2 各专业方案 (9)2.1 工艺设备 (9)2.2 热力系统 (12)2.3 总图运输 (21)2.4 水工 (23)2.5 电气 (25)2.6仪表自动化 (36)2.7建筑结构 (45)2.8暖通空调 (48)3 消防 (49)3.1设计范围 (49)3.2 消防措施 (49)4 环境保护 (50)4.1 环境保护设计原则 (50)4.2 主要污染源、污染物 (50)4.3 控制方案 (50)4.4 环境管理及监测 (51)4.5 污染治理效果预测 (51)5 劳动安全及工业卫生 (52)5.1 生产过程中的危险、有害因素分析 (52)5.2 安全和卫生技术内容 (52)5.3 安全和卫生管理 (54)6 节能 (55)6.1 节能 (55)6.2 节水 (55)6.3 环保 (55)6.4 综合利用 (55)7 组织机构劳动定员 (56)7.1 概述 (56)7.2 组织机构、人员编制及指标 (56)7.3 人员配备 (57)附图一:银钢总平面布置图﹍﹍﹍﹍﹍﹍﹍﹍﹍﹍﹍﹍﹍﹍﹍﹍﹍﹍﹍k01 附图二:余热电站汽水平衡图﹍﹍﹍﹍﹍﹍﹍﹍﹍﹍﹍﹍﹍﹍﹍﹍﹍﹍k02 附图三:锅炉汽水系统图﹍﹍﹍﹍﹍﹍﹍﹍﹍﹍﹍﹍﹍﹍﹍﹍﹍﹍﹍﹍k03 附图四:汽机热力系统图﹍﹍﹍﹍﹍﹍﹍﹍﹍﹍﹍﹍﹍﹍﹍﹍﹍﹍﹍﹍k04 附图五:化学水处理系统图﹍﹍﹍﹍﹍﹍﹍﹍﹍﹍﹍﹍﹍﹍﹍﹍﹍﹍﹍k05 附图六:电气主接线图﹍﹍﹍﹍﹍﹍﹍﹍﹍﹍﹍﹍﹍﹍﹍﹍﹍﹍﹍﹍﹍k06 附图七:烟气系统流程图﹍﹍﹍﹍﹍﹍﹍﹍﹍﹍﹍﹍﹍﹍﹍﹍﹍﹍﹍﹍k07 附图八:汽轮机房布置图﹍﹍﹍﹍﹍﹍﹍﹍﹍﹍﹍﹍﹍﹍﹍﹍﹍﹍﹍﹍k08 附图九:除盐水站布置图﹍﹍﹍﹍﹍﹍﹍﹍﹍﹍﹍﹍﹍﹍﹍﹍﹍﹍﹍﹍k09 附图十:余热锅炉布置图﹍﹍﹍﹍﹍﹍﹍﹍﹍﹍﹍﹍﹍﹍﹍﹍﹍﹍﹍﹍k101 总论1.1 建设单位基本情况1.2 工程条件1.2.1 烧结机、环冷机基本参数由于钢铁烧结矿的需求量较大,180m2烧结能够满负荷生产。
烧结余热发电资料

1概论在钢铁生产过程中,烧结工序的能耗约占总能耗的10%,仅次于炼铁工序,位居第二。
在烧结工序总能耗中,有近50%的热能以烧结烟气和冷却机废气的显热形式排入大气。
由于烧结冷却机废气的温度不高,仅150~450℃,加上以前余热回收技术的局限,余热回收项目往往被忽略。
随着近几年来余热回收技术突飞猛进,钢铁行业的余热回收项目造价大幅度降低,同时余热回收效率大幅提高,特别是闪蒸发电技术和补汽凝汽式汽轮机在技术上获得突破,为钢铁行业余热回收创造了优越的条件。
时值目前国家能源紧缺、大力提倡生产过程节能降耗的关键时期,国家有关部门对企业节能指标提出了很高的要求。
在这样的形势和技术条件下,一些有远见的钢铁企业,迅速启动各种余热回收项目,不但完成了钢铁企业的节能降耗任务,同时也能为企业本身创造可观的经济效益。
烧结冷却机余热的回收,是通过回收烧结机尾落矿风箱及烧结冷却机密闭段的烟气加热余热锅炉来回收低品味余热能源,结合低温余热发电技术,用余热锅炉的过热蒸气来推动低参数的汽轮发电机组做功发电的最新成套技术;其与火力发电相比:1)不需要消耗一次能源。
2)不产生额外的废气、废渣、粉尘和其它有害气体。
具体来讲烧结冷却机余热回收的意义体现在如下几个方面:1)利用烧结环冷机烟气余热发电,部分代替来自电网的以化石燃料为能源的供电量,从而起到减少温室气体排放效果;2)降低烧结工序能耗,促进资源节约;降低产品单位价格,使企业更具竞争优势。
3)有利于企业可持续发展目标的实现,减少由常规火电厂带来的SO2、CO2、粉尘之类的大气污染物,有助于改善当地的能源结构,提高能源安全。
2 国家政策一国务院关于做好建设节约型社会近期重点工作的通知国发【2005】 21号文件中提出“在冶金、有色、煤炭、电力、化工、建材、造纸、酿造等重点行业组织开展循环经济试点”。
具体内容:1)钢铁工业。
要加快淘汰落后工艺和设备,提高新建、改扩建工程的能耗准入标准。
实现技术装备大型化、生产流程连续化、紧凑化、高效化,最大限度综合利用各种能源和资源。
烧结余热回收技术及生产对策-

・12・炼铁技术通讯2006年第7期烧结余热回收技术及生产对策李玉红赵国顺(唐钢炼铁厂摘要:介绍了唐钢烧结余热设备情况,余热回收蒸汽的利用情况,如何处理余热、混合料水分、烧结机三者之间的相互关系,从而保证生产的稳定,产量质量的提高。
关键词:烧结余热利用蒸汽预热混合料1前言烧结过程中的能源消耗占钢铁企业总能耗的10%左右,在可供利用的余热中仅环冷机废气及烧结烟气的显热约占烧结全部热支出的30%以上,如不加以利用,则会造成较大的能源浪费,充分回收利用这些烧结余热,是烧结节能的重要途径及发展趋势。
烧结生产中,从煤气点火开始,烧结机上的混合料中的焦粉在抽风的作用下开始燃烧,放出热量。
焦粉周围的物料形成熔融液相而互相粘结在一起形成烧结矿。
随着空气不断通过料层进入烟道,烧结矿中碳燃烧的部分热量亦被带入烟道,烟道中的废气温度大约在60~450℃。
2回收环冷余热生产蒸汽环冷机冷却废气第一段温度在300~500℃,温度较高,我厂环冷机废气用作余热锅炉热源,主要使用第一段冷却废气,废气温度一般在300~500℃,采用开路循环流程,即送入废气经余热锅炉热交换后再排放。
采用余热锅炉回收冷却废气,热效率高。
我厂的265m2烧结机,采用一台280m2的环冷机冷却烧结矿,安装了一台余热锅炉,设计进气温度350℃,风量214000m3/h、回收热量139MJ/t烧结矿,余热锅炉产生蒸汽约16t/h。
3余热锅炉的设备情况我厂采用的翅片管式蒸汽发生系统是为冶金烧结厂专门回收冷却机废气余热而设计的。
该系统由蒸发器、水预热器、过热器、汽包及各种连接管路组成。
其中,蒸发器受热面均采用高频焊接翅片管,达到强化传热的目的,因而整套装置传热效率高,工作安全稳定,寿命长,设备结构紧凑。
利用余热所产生蒸汽加热混合料,提高料温,从而达到提高烧结矿产量质量的目的;另外用做烧结区域冬季取暖的热源,从而达到节约燃料降低取暖费用的目的。
翅片管式蒸汽发生器是使热空气通过管壁传导,将热量直接传送给饱和水进行换热,因而传热效果好。
- 1、下载文档前请自行甄别文档内容的完整性,平台不提供额外的编辑、内容补充、找答案等附加服务。
- 2、"仅部分预览"的文档,不可在线预览部分如存在完整性等问题,可反馈申请退款(可完整预览的文档不适用该条件!)。
- 3、如文档侵犯您的权益,请联系客服反馈,我们会尽快为您处理(人工客服工作时间:9:00-18:30)。
附件1技术说明书1概述1.1 工程概况河北钢铁集团荣信钢铁有限公司(以下简称“甲方”)现有180m2烧结生产线各2条,40t转炉3座,60t转炉2座。
烧结生产线尚未进行余热回收,转炉水冷烟道产生的饱和蒸汽放散严重。
根据现有企业能源平衡现状,对国内外冶金企业现有余热利用技术进行充分比较并结合国家可持续发展和资源综合利用政策,充分考虑企业现有生产规模、技术条件以及烧结和富余蒸汽资源综合利用的可行性和经济性,拟建设烧结余热及富余蒸汽电站1座,以达到充分利用余热资源、节能减排和降低生产成本并提高企业经济效益的目的。
现根据国家政策导向和业主要求,对2条180m2烧结生产线和5台转炉进行余热发电工程设计,建设两套“余热发电系统”(以下简称“余热发电项目”)。
1.2设计依据——《小型火力发电厂设计规范》GB50049-94;——《火力发电厂设计技术规程》DL 5000-2000;——《建筑设计防火规范》GB50016-2006;——《火力发电厂总图运输设计技术规定》(DL/T5032-94);——《火力发电厂水工设计规范》DL/T5339-2006;——《火力发电厂与变电所设计防火规范》GB50229-96;——《大气污染物综合排放标准》(GB16297-1996);——《火电厂大气污染物排放标准》(GB13223-2003);——《火力发电厂劳动安全和工业卫生设计规程》(DL5053-96)——《火力发电厂初步设计文件内容深度规定》DLGJ 9-92;——《工程建设标准强制性条文》(2006 年);甲方提供的基础资料。
其它现行的国家规章、规范、标准等。
1.3 设计原则由于影响烧结余热回收效率的因素很多,如烧结矿的产量、燃烧温度、料层层厚,冷却机的速度,冷却介质的初温和废气流量等。
根据烧结机的设计和运行情况,结合以往烧结余热电站的设计、调试及运行经验,在充分利用余热资源的条件下,以“稳定可靠,技术先进,降低能耗,节省投资”为基准,遵守下列原则:1)遵循国家规范、规程、规定和行业相关强制性标准;2)贯彻“安全、可靠、经济、适用、符合国情”的电力建设方针;3)在保证烧结工艺生产安全和稳定的前提下利用余热资源;4)采用热量梯级利用原则,最大程度回收烟气热量;5)选用技术先进、成熟、运行可靠的余热回收及发电设备;6)余热回收及发电系统满足国家关于节能减排及高效环保的要求。
1.4 工程主要技术经济指标项目数值单位1)180m2烧结余热发电余热发电装机容量1×12 MW 设计发电功率12 MW 设计平均发电功率9.6 MW烧结年作业时数8150 h发电年作业时数7800 h 2)5台转炉饱和蒸汽发电余热发电装机容量1×4.5 MW 设计发电功率 4.5 MW 设计平均发电功率 4.2 MW炼钢年作业时数7900 h发电年作业时数7800 h3)两台机合计年发电量7488+3276 104kW.h电站年自耗电量电站投用后,烧结风机节电量2066304104kW.h电站自耗电率电站自耗电率(扣除节电)19.216.4%年外供电量(合并节电量)8697(8998)104kW.h1.5初步设计方案及相关配套图纸拟定后,必须经甲方审核。
有权对不符合工艺要求的管线、设备等提出更改或增加相应设备的权利。
2 总图及道路运输2.1 总平面本工程主要建设内容包括:2台单压余热锅炉,2台双压余热锅炉,1座烧结余热发电主厂房、1座转炉余热发电主厂房、1套12MW机组循环水系统、1套4.5MW机组循环水系统、1套除盐水系统等。
烧结余热发电:由余热锅炉、汽轮机房、电气楼、循环水站、除盐水站组成。
余热锅炉布置在烧结环冷机旁,其余部分均布置在烧结旁预留电站场地内。
转炉余热发电:由汽轮机房、电气楼、循环水站及蒸汽蓄热站组成。
电气楼、主厂房、循环水站及除盐水站均按电站常规布置;具体布置方案待甲方提供总图位置后进行。
2.2 运输及道路余热电站建成投产后,能源介质均采用管道和电缆输送,站内只有药品、备件及油品运输需求,运量较小,厂区现有道路及运输设施即可满足要求。
2.3 区域绿化本工程不考虑新增集中绿化用地,仅利用边角地绿化。
新建的主厂房和循环水系统区域的绿化权衡考虑,做到环境优美,小景协调,力求投资和美化效果双赢。
3 工艺系统3.1 烧结工艺及余热资源烧结生产线由烧结机和冷却机两大部分组成。
烧结原料经点火并烧结后,烧结矿从烧结机尾部卸到冷却机上进行冷却,冷却后的烧结矿经输送机送至矿仓以备高炉冶炼取用。
一般情况下,烧结终点相邻几个风箱烟气温度较高,约250~450℃,当烧结终点不能较好控制在倒数第二个风箱时,烧结机尾部烟气有一定热量可以利用;同时,烧结环冷机进口的给矿温度平均在650~750℃之间,环冷机出口的矿温在150℃以下。
烧结矿冷却过程中,烧结矿所携带的热量被转换成废气显热,废气温度从前到后逐步降低,给矿部废气温度最高,一般在450℃左右,排矿部温度最低。
根据两台烧结及环冷机气固换热的计算参数及经验评估,每台烧结机尾部可用烟气分布在最后4个风箱内;采用热风循环工艺后,每台环冷机可用废气约为前部40%风箱对应料面上热风。
具体参数见下表:烧结机回收烟气参数名称#1烧结机#2烧结机单位余热废气平均风量80000 80000 Nm3/h 余热废气平均温度~350 ~350 ℃环冷机回收废气参数名称#1环冷机#2环冷机单位余热废气平均风量250000 250000 Nm3/h 余热废气平均温度~330 ~330 ℃3.2 炼钢工艺及余热资源炼钢厂现有40t转炉3座,60t转炉2座,钢产量约345t/h。
转炉设有汽化冷却系统,蒸汽产量约为27~35t/h,运行压力约0.8MPa;目前,企业无余热回收装置,剩余蒸汽大量放散,既浪费了能源,同时还造成环境污染;因此,炼钢余热蒸汽回收利用符合国家和企业利益,需要快速建成并达产增效。
3.3 烧结余热回收方案3.3.1 烧结机余热回收根据烧结工艺运行要求,为了更好的保证烧结机独立运行的稳定性和可靠性,2台烧结机分别设置余热锅炉回收烟气余热为宜。
正常情况下,烧结机尾部4个风箱并联余热锅炉运行,后部烟气经余热锅炉后返回主抽烟道,烟道和锅炉分别设置分断阀和调节阀进行系统投切和运行调节,以保证烧结工艺和余热回收系统的正常和高效运行。
根据烟气余热条件、除尘工艺要求并结合环冷机余热回收方案,烧结余热锅炉选用单压系统,蒸汽压力1.6MPa、温度330℃;2台烧结余热锅炉所产生过热蒸汽与环冷机余热锅炉所产相同压力的蒸汽混合后送入汽轮发电机组做功发电,凝结水循环使用。
3.3.2 环冷机余热回收根据环冷机余热资源条件,按梯级取风原则,将环冷机废气进一步细化成一段高温、一段中温和二段中温三部分。
其中,高温废气为环冷机前部风箱上部的热空气,中温废气为环冷机中前部风箱上部的热空气,具体参数如下表所示:高温废气参数名称1#环冷机2#环冷机单位余热废气风量100000 100000 Nm3/h 余热废气温度340~400 340~400 ℃中温废气参数名称1#环冷机2#环冷机单位余热废气风量150000 150000 Nm3/h 余热废气温度280~340 280~340 ℃注:以上环冷机废气参数将随工艺条件的变化而变化。
当实际参数发生变化时,余热锅炉及余热发电参数也将会作相应的改变。
根据以上余热资源条件、现场实际和已建成同类项目经验,为增加余热回收系统运行灵活性,两台烧结冷却机各配置1台余热锅炉,回收废气余热生产蒸汽,锅炉排气送回环冷机循环使用。
余热锅炉选用双压系统,余热锅炉产生两种压力的过热蒸汽,其中,高参数蒸汽压力1.6MPa、温度350℃;低参数蒸汽压力0.3MPa、温度190℃;两种压力的过热蒸汽均送入补汽凝汽式汽轮发电机组做功发电,其中高参数蒸汽还需与烧结余热蒸汽混合均匀后共同进入汽轮机,凝结水循环使用。
3.4 炼钢余热蒸汽回收方案将炼钢5座转炉所产余热蒸汽汇入同一母管,并设置蒸汽蓄热器进行负荷波动调节,使富余蒸汽得以平稳输出,在设置汽水分离装置脱出蒸汽所含99%的机械水后,利用1套汽轮发电机组将饱和蒸汽热能转化为电能输出。
3.5 热力系统及装机方案3.5.1 热力系统及工艺流程1)烧结余热发电本系统包括:烧结单压余热锅炉系统2套,环冷双压余热锅炉系统2套及补汽凝汽式汽轮发电机组1套。
经计算并结合烧结余热发电的特点和经验,选择高参数锅炉给水压力2.1MPa,给水温度150℃;低参数锅炉给水压力0.8MPa,给水温度40℃。
烧结余热锅炉所产过热蒸汽参数为1.6MPa、330℃;环冷余热锅炉所产高参数过热蒸汽参数为1.6MPa、350℃,低参数过热蒸汽参数为0.3MPa、190℃。
来自余热锅炉的过热蒸汽按不同压力级别各自混合后,通过主蒸汽、补汽管道分别送至汽轮机主汽及补汽入口,蒸汽进入汽轮机内共同做功后凝结成水,凝结水经凝结水泵加压后送出,经轴封冷却器加热后分别送往2台环冷余热锅炉凝结水加热器,热水进入低压汽包自除氧,部分除氧水在低参数蒸发系统自然循环产生蒸汽,部分除氧水由锅炉给水泵送往环冷余热锅炉高参数省煤器继续升温,出水分两路,一路进烧结锅炉汽包,一路进环冷锅炉高参数汽包,在各自蒸发系统内自然循环产生蒸汽;不同压力和不同锅炉所产饱和蒸汽分别经各自过热器升温后送出,按不同压力级别混合后前往汽轮机,完成一个完整的热力循环;系统补水进入凝汽器,在真空条件下达到预除氧目的。
2)转炉饱和蒸汽发电本系统包括:蒸汽蓄热系统1套及饱和汽轮发电机组1套。
汽轮机组进汽要求其进汽品质执行国家标准GB/T1576-2008、GB/T12145-2008标准。
转炉蒸汽经蓄热器缓冲后混合输出,饱和蒸汽脱水后进入汽轮发电机组,在汽轮机内做功后凝结成水,经水泵加压后送回炼钢,分别进入各转炉除氧系统,除氧后利用给水泵送入汽化冷却系统,强制循环吸热蒸发后再次送出,完成一个完整的热力循环。
3.5.2 余热电站装机方案1)烧结余热发电按照前述的余热废气量、温度及余热回收方案,在两台烧结机旁各设置8t/h单压余热锅炉1台;两台环冷机旁各设置(20+5)t/h双压余热锅炉1台;根据余热锅炉装机方案,正常生产时,4台余热锅炉可产 1.6MPa、344℃(混合后)的过热蒸汽56t/h,0.3MPa饱和蒸汽10t/h;两种压力的过热蒸汽均送入补汽凝汽式汽轮机做功发电,根据蒸汽特性、现有同类机组运行情况和机组系列化参数要求,选取汽机进汽参数分别为:1.4MPa(a)、335℃和0.3MPa(a)、180℃;根据前述蒸汽条件计算,电站装机参数如下表:序号名称参数单位1 总回收蒸汽量56+10 t/h2 设计发电功率12 MW3 电站装机功率12 MW2)炼钢余热发电5座转炉共产生0.8MPa饱和蒸汽27~35t/h;为调节系统蒸汽产消量,稳定蒸汽输出、保证机组运行稳定性,需要设置350m3蒸汽蓄热器,考虑原系统已有蓄热器后,增设1台150m3蒸汽蓄热器(暂定),将发电蒸汽压力控制在0.5MPa以上;所有剩余饱和蒸汽均进入饱和蒸汽轮机做功发电。