883-Utilization of degossypolled
脱酚棉籽蛋白在水产饲料中的应用
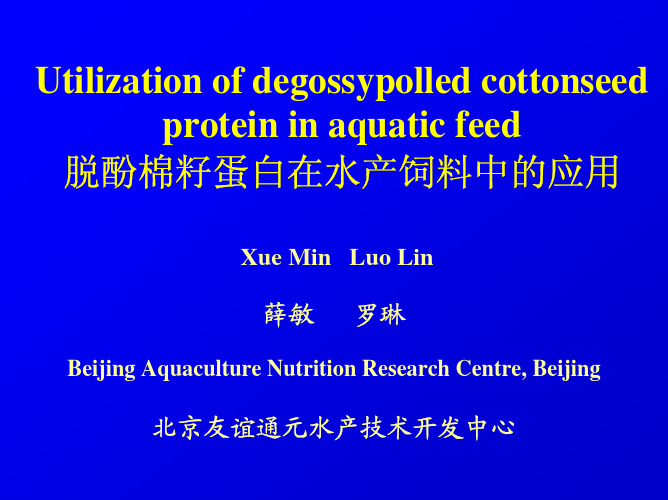
Xue Min Luo Lin
薛敏
罗琳
Beijing Aquaculture Nutrition Research Centre, Beijing
北京友谊通元水产技术开发中心
Why research on degossypolled cottonseed protein (DCP)
研究脱酚棉籽蛋白在水产饲料中的应用的目的
Fish meal is deficient and expensive resources,phosphorus excretion •鱼粉是很好的水产饲料蛋白源,但资源短缺,价格昂贵,磷污 染严重 The market price of the fish has been decreased rapidly •由于养殖规模的扩大和产量的大幅提高,水产品价格降幅较大 The importance of vegetable alternative proteins •植物性替代蛋白源成为研究热点
utilizationofdegossypolledcottonseedproteininaquaticfeed脱酚棉籽蛋白在水产饲料中的应用脱酚棉籽蛋白在水产饲料中的应用xueminluolin薛敏薛敏罗琳罗琳beijingaquaculturenutritionresearchcentrebeijing北京友谊通元水产技术开发中心北京友谊通元水产技术开发中心whyresearchondegossypolledcottonseedproteindcp研究脱酚棉籽蛋白在水产饲料中的应用的目的研究脱酚棉籽蛋白在水产饲料中的应用的目的fishmealisdeficientandexpensiveresourcesphosphorusexcretion?鱼粉是很好的水产饲料蛋白源但资源短缺价格昂贵磷污鱼粉是很好的水产饲料蛋白源但资源短缺价格昂贵磷污染严重染严重themarketpriceofthefishhasbeendecreasedrapidly?由于养殖规模的扩大和产量的大幅提高水产品价格降幅较大由于养殖规模的扩大和产量的大幅提高水产品价格降幅较大theimportanceofvegetablealternativeproteins?植物性替代蛋白源成为研究热点植物性替代蛋白源成为研究热点continue研究脱酚棉籽蛋白在水产饲料中的应用的目的研究脱酚棉籽蛋白在水产饲料中的应用的目的theannualproductofcottonseedisabout5milliontoninchinabutnormaluseofcottonseedmealinfeedislessthan15becauseofitslowlysinemethioninecystineavailabilityandtoxicityofgossypol
Leuze electronic BCL 308i OM 100 D H Stationary ba

BCL 308i OM 100 D HStationary bar code readerFigure can varyTechnical dataBasic dataSeries BCL 300iSpecial designSpecial design HeatingFunctionsFunctions Alignment modeLED indicatorHeatingAutoControlAutoReflActCode fragment technologyAutoConfigReference code comparisonCharacteristic parametersMTTF110 yearsRead dataCode types, readable GS1 Databar OmnidirectionalCode 93Code 39GS1 Databar ExpandedEAN 8/13GS1 Databar LimitedUPC2/5 InterleavedCode 128CodabarScanning rate, typical1,000 scans/sBar codes per reading gate, max. number64 Piece(s)Optical dataReading distance40 ... 300 mmLight source Laser,RedLaser light wavelength655 nmLaser class2,IEC/EN 60825-1:2007Transmitted-signal shape ContinuousModule size0.2 ... 0.5 mmReading method Oscillating-mirror scannerBeam deflection Via rotating polygon wheel + stepping motor with mirror Light beam exit Zero position at side at angle less than 90°Oscillating mirror frequency10 HzMax. swivel angle15 °Electrical dataProtective circuit Polarity reversal protectionPerformance dataSupply voltage18 ... 30 V,DCPower consumption, max.45 WInputs/outputs selectableCurrent, max.60 mANumber of inputs/outputs selectable 2 Piece(s)Input current, max.8 mAInterfaceType EthernetEthernetArchitecture ServerClientAddress assignment DHCPManual address assignment Transmission speed100 Mbit/s10 Mbit/sFunction ProcessSwitch functionality IntegratedTransmission protocol TCP/IP , UDPService interfaceType USBUSBFunction ServiceConfiguration via softwareConnectionNumber of connections 1 Piece(s)Connection 1Type of connection Plug connectorFunction Service interfaceConnection to deviceData interfaceBUS INPWR / SW IN/OUTNo. of pins32 -pinType MaleMechanical dataDesign CubicDimension (W x H x L)125 mm x58 mm x110 mmHousing material Metal,Diecast aluminumLens cover material GlassNet weight580 gHousing color BlackRedType of fastening Via optional mounting deviceFastening on backDovetail groovesOperation and displayType of display LEDMonochromatic graphic display, 128 x 32 pixels Number of LEDs 2 Piece(s)Type of configuration Via web browserEnvironmental dataAmbient temperature, operation-35 ... 40 °CAmbient temperature, storage-20 ... 70 °CRelative humidity (non-condensing)0 ... 90 %CertificationsDegree of protection IP 65Protection class IIICertifications c UL USTest procedure for EMC in accordance with standard EN 55022EN 61000-4-2, 3, -4, -6 Test procedure for shock in accordance with standard IEC 60068-2-27, test Ea Test procedure for continuous shock in accordance with standard IEC 60068-2-29, test Eb Test procedure for vibration in accordance with standard IEC 60068-2-6, test FcClassification*********27280102*********27280102ETIM 5.0EC002550Dimensioned drawingsAll dimensions in millimetersElectrical connectionConnection 1Type of connection Plug connector Function Service interfaceConnection to deviceData interfaceBUS INPWR / SW IN/OUTNo. of pins32 -pinConnection 1Type MaleDiagramsReading field curvex Reading field distance [mm]y Reading field width [mm]Lateral reading field curveOperation and displayLEDsLED Display Meaning1PWR Green, flashing Device ok, initialization phase Green, continuous light Device OKGreen, briefly off - on Reading successfulgreen, briefly off - briefly red - on Reading not successfulOrange, continuous light Service modeRed, flashing Device OK, warning setRed, continuous light Error, device error2BUS Green, flashing InitializationGreen, continuous light Bus operation okRed, flashing Communication errorRed, continuous light Bus errorAccessoriesConnection technology - Connection cablesPart no.Designation Article Description50132077KD U-M12-5A-V1-020Connection cable Connection 1: Connector, M12, Axial, Female, A-coded, 5 -pin Connection 2: Open endShielded: NoCable length: 2,000 mmSheathing material: PVC50132079KD U-M12-5A-V1-050Connection cable Connection 1: Connector, M12, Axial, Female, A-coded, 5 -pin Connection 2: Open endShielded: NoCable length: 5,000 mmSheathing material: PVC50132080KD U-M12-5A-V1-100Connection cable Connection 1: Connector, M12, Axial, Female, A-coded, 5 -pin Connection 2: Open endShielded: NoCable length: 10,000 mmSheathing material: PVC50132432KD U-M12-5A-V1-300Connection cable Connection 1: Connector, M12, Axial, Female, A-coded, 5 -pin Connection 2: Open endShielded: NoCable length: 30,000 mmSheathing material: PVC50135073KS ET-M12-4A-P7-020Connection cable Suitable for interface: EthernetConnection 1: Connector, M12, Axial, Male, D-coded, 4 -pinConnection 2: Open endShielded: YesCable length: 2,000 mmSheathing material: PUR50135074KS ET-M12-4A-P7-050Connection cable Suitable for interface: EthernetConnection 1: Connector, M12, Axial, Male, D-coded, 4 -pinConnection 2: Open endShielded: YesCable length: 5,000 mmSheathing material: PUR50135075KS ET-M12-4A-P7-100Connection cable Suitable for interface: EthernetConnection 1: Connector, M12, Axial, Male, D-coded, 4 -pinConnection 2: Open endShielded: YesCable length: 10,000 mmSheathing material: PUR50135076KS ET-M12-4A-P7-150Connection cable Suitable for interface: EthernetConnection 1: Connector, M12, Axial, Male, D-coded, 4 -pinConnection 2: Open endShielded: YesCable length: 15,000 mmSheathing material: PUR50135077KS ET-M12-4A-P7-300Connection cable Suitable for interface: EthernetConnection 1: Connector, M12, Axial, Male, D-coded, 4 -pinConnection 2: Open endShielded: YesCable length: 30,000 mmSheathing material: PURConnection technology - Interconnection cablesPart no.Designation Article Description50106901KBET-10000-SSA InterconnectioncableSuitable for interface: EthernetConnection 1: Connector, M12, Axial, Male, D-coded, 4 -pinConnection 2: Connector, M12, Axial, Male, D-coded, 4 -pinShielded: YesCable length: 10,000 mmSheathing material: PUR50106902KBET-15000-SSA InterconnectioncableSuitable for interface: EthernetConnection 1: Connector, M12, Axial, Male, D-coded, 4 -pinConnection 2: Connector, M12, Axial, Male, D-coded, 4 -pinShielded: YesCable length: 15,000 mmSheathing material: PUR50106899KB ET-2000-SSA Interconnectioncable Suitable for interface: EthernetConnection 1: Connector, M12, Axial, Male, D-coded, 4 -pin Connection 2: Connector, M12, Axial, Male, D-coded, 4 -pin Shielded: YesCable length: 2,000 mmSheathing material: PUR50106905KBET-30000-SSA InterconnectioncableSuitable for interface: EthernetConnection 1: Connector, M12, Axial, Male, D-coded, 4 -pinConnection 2: Connector, M12, Axial, Male, D-coded, 4 -pinShielded: YesCable length: 30,000 mmSheathing material: PUR50106900KB ET-5000-SSA Interconnectioncable Suitable for interface: EthernetConnection 1: Connector, M12, Axial, Male, D-coded, 4 -pin Connection 2: Connector, M12, Axial, Male, D-coded, 4 -pin Shielded: YesCable length: 5,000 mmSheathing material: PUR50117011KB USB A - USBminiB Service line Suitable for interface: USBConnection 1: USBConnection 2: USBShielded: YesCable length: 1,500 mmSheathing material: PVC50135080KSS ET-M12-4A-RJ45-A-P7-020InterconnectioncableSuitable for interface: EthernetConnection 1: Connector, M12, Axial, Male, D-coded, 4 -pinConnection 2: RJ45Shielded: YesCable length: 2,000 mmSheathing material: PUR50135081KSS ET-M12-4A-RJ45-A-P7-050InterconnectioncableSuitable for interface: EthernetConnection 1: Connector, M12, Axial, Male, D-coded, 4 -pinConnection 2: RJ45Shielded: YesCable length: 5,000 mmSheathing material: PUR50135082KSS ET-M12-4A-RJ45-A-P7-100InterconnectioncableSuitable for interface: EthernetConnection 1: Connector, M12, Axial, Male, D-coded, 4 -pinConnection 2: RJ45Shielded: YesCable length: 10,000 mmSheathing material: PURPart no.Designation Article Description50135083KSS ET-M12-4A-RJ45-A-P7-150InterconnectioncableSuitable for interface: EthernetConnection 1: Connector, M12, Axial, Male, D-coded, 4 -pinConnection 2: RJ45Shielded: YesCable length: 15,000 mmSheathing material: PUR50135084KSS ET-M12-4A-RJ45-A-P7-300InterconnectioncableSuitable for interface: EthernetConnection 1: Connector, M12, Axial, Male, D-coded, 4 -pinConnection 2: RJ45Shielded: YesCable length: 30,000 mmSheathing material: PURConnection technology - ConnectorsPart no.Designation Article Description50108991D-ET1Connector Suitable for interface: EthernetConnection: RJ4550020501KD 095-5A Connector Connection: Connector, M12, Axial, Female, A-coded, 5 -pin50112155S-M12A-ET Connector Suitable for interface: EthernetConnection: Connector, M12, Axial, Male, D-coded, 4 -pinConnection technology - Terminal boxesPart no.Designation Article Description50131255*ME 308 103Connection unit Suitable for: BCL 308iSuitable for interface: EthernetNumber of connections: 4 Piece(s)Connection: Cable with connector, M12, 900 mm 50131254*ME 308 104Connection unit Suitable for: BCL 308iSuitable for interface: EthernetNumber of connections: 5 Piece(s)Connection: Cable with connector, M12, 900 mm 50116466*MK 308Connection unit Suitable for: BCL 308iSuitable for interface: EthernetNumber of connections: 4 Piece(s)Connection: Terminal50114823*MS 308Connection unit Suitable for: BCL 308iSuitable for interface: EthernetNumber of connections: 4 Piece(s)Connection: Connector, M12* Necessary accessories, please order separatelyConnection technology - AdaptersPart no.Designation Article Description50109832KDS ET-M12 /RJ45 W-4P Adapter Suitable for: EthernetNumber of connections: 2 Piece(s)Connection 1: Connector, M12, Angled, Female, D-coded, 4 -pinConnection 2: RJ45Mounting technology - Mounting bracketsPart no.Designation Article Description50121433BT 300 W Mounting device Contains: 4x M4 x 10 screw, 4x position washers, 4x lockwashersDesign of mounting device: Angle, L-shapeMounting bracket, at system: Through-hole mountingMounting bracket, at device: Screw typeType of mounting device: AdjustableMaterial: MetalMounting technology - Rod mountsPart no.Designation Article Description50121434BT 300 - 1Mounting device Contains: 4x M4 x 10 screw, 4x position washers, 4x lockwashersDesign of mounting device: Mounting systemMounting bracket, at system: For 12 mm rod, For 14 mm rod,For 16 mm rodMounting bracket, at device: Screw typeType of mounting device: Turning, 360°, AdjustableMaterial: Metal50027375BT 56Mounting device Design of mounting device: Mounting systemMounting bracket, at system: For 16 mm rod, For 18 mm rod,For 20 mm rodMounting bracket, at device: ClampableMaterial: MetalTightening torque of the clamping jaws: 8 N·mFunctions: Static applications50121435BT 56 - 1Mounting device Design of mounting device: Mounting systemMounting bracket, at system: For 12 mm rod, For 14 mm rod,For 16 mm rodMounting bracket, at device: ClampableMaterial: MetalTightening torque of the clamping jaws: 8 N·mFunctions: Static applicationsMounting technology - OtherPart no.Designation Article Description50111224BT 59Mounting bracket Mounting bracket, at system: Groove mountingMounting bracket, at device: ClampableMaterial: Metal50124941BTU 0300M-W Mounting device Mounting bracket, at system: Through-hole mountingMounting bracket, at device: Clampable, Groove mountingMaterial: MetalReflective tapes for standard applicationsPart no.Designation Article Description50106119REF 4-A-100x100Reflective tape Design: RectangularReflective surface: 100 mm x 100 mmMaterial: PlasticChemical designation of the material: PMMAFastening: Self-adhesiveNotesObserve intended use!•This product is not a safety sensor and is not intended as personnel protection.•The product may only be put into operation by competent persons.•Only use the product in accordance with its intended use.WARNING! LASER RADIATION – LASER CLASS 2Never look directly into the beam!The device satisfies the requirements of IEC60825-1:2007 (EN60825-1:2007) safety regulations for a product of laser class2as well as the U.S.21CFR1040.10 regulations with deviations corresponding to "Laser Notice No.50" from June 24, 2007.•Never look directly into the laser beam or in the direction of reflected laser beams! If you look into the beam path over a longer time period, there is a risk of injury to the retina.•Do not point the laser beam of the device at persons!•Interrupt the laser beam using a non-transparent, non-reflective object if the laser beam is accidentally directed towards a person.•When mounting and aligning the device, avoid reflections of the laser beam off reflective surfaces!•CAUTION! Use of controls or adjustments or performance of procedures other than specified herein may result in hazardous light exposure.•Observe the applicable statutory and local laser protection regulations.•The device must not be tampered with and must not be changed in any way.There are no user-serviceable parts inside the device.Repairs must only be performed by Leuze electronic GmbH + Co. KG.NOTEAffix laser information and warning signs!Laser information and warning signs are affixed to the device. In addition, self-adhesive laser information and warning signs (stick-on labels) are supplied in several languages.•Affix the laser information sheet to the device in the language appropriate for the place of use. When using the device in the US, use the stick-on label with the "Complies with 21CFR1040.10" note.•Affix the laser information and warning signs near the device if no signs are attached to the device (e.g. because the device is too small) or if the attached laser information and warning signs are concealed due to the installation position.•Affix the laser information and warning signs so that they are legible without exposing the reader to the laser radiation of the device or other optical radiation.。
MIL-STD-883G temperature-cycling test

MIL-STD-883GMETHOD 1010.8TEMPERATURE CYCLING1. PURPOSE. This test is conducted to determine the resistance of a part to extremes of high and low temperatures, and to the effect of alternate exposures to these extremes.1.1 Terms and definitions.1.1.1 Load. The specimens under test and the fixtures holding those specimens during the test. Maximum load shall be determined by using the worst case load temperature with specific specimen loading. Monolithic (single block) loads used to simulate loading may not be appropriate when air circulation is reduced by load configuration. The maximum loading must meet the specified conditions.1.1.2 Monitoring sensor. The temperature sensor that is located to indicate the same temperature as that of the worst case indicator specimen location. The worst case indicator specimen location is identified during the periodic characterization of the worst case load temperature.1.1.3 Worst case load temperature. The temperature of specific specimens or equivalent mass as indicated by thermocouples imbedded in their bodies. These indictor specimens shall be located at the center and at each corner of the load. The worst case load temperature (point which reaches temperature last) is determined at periodic intervals.1.1.4 Working zone. The volume in the chamber(s) in which the temperature of the load is controlled within the limits specified in table I.1.1.5 Specimen. The device or individual piece being tested.1.1.6 Transfer time. The elapsed time between initiation of load transition (for a single chamber or specimen removal for multiple chambers) from one temperature extreme and introduction into the other temperature.1.1.7 Maximum load. The largest load for which the worst case load temperature meets the timing requirements.1.1.8 Dwell time. The time from introduction of the load to one extreme environment temperature until the initiation of the transfer to the other extreme temperature environment.2. APPARATUS. The chamber(s) used shall be capable of providing and controlling the specified temperatures in the working zone(s) when the chamber is loaded with a maximum load. The thermal capacity and air circulation must enable the working zone and loads to meet the specified conditions and timing (see3.1). Worst case load temperature shall be continually monitored during test by indicators or recorders. Direct heat conduction to specimens shall be minimized.3. PROCEDURE. Specimens shall be placed in such a position with respect to the airstream that there is substantially no obstruction to the flow of air across and around the specimen. When special mounting is required, it shall be specified. The specimen shall then be subjected to the specified condition for the specified number of cycles performed continuously. This test shall be conducted for a minimum of 10 cycles using test condition C (see Figure 1010-1). One cycle consists of steps 1 and 2 or the applicable test condition and must be completed without interruption to be counted as a cycle. Completion of the total number of cycles specified for the test may be interrupted for the purpose of test chamber loading or unloading of device lots or as the result of power or equipment failure. However, if the number of interruptions for any reason exceeds 10 percent of the total number of cycles specified, the test must be restarted from the beginning.3.1 Timing. The total transfer time from hot to cold or from cold to hot shall not exceed one minute (for multiple chambers). The load may be transferred when the worst case load temperature is within the limits specified in table I. However, the dwell time shall not be less than 10 minutes and the load shall reach the specified temperature within 15 minutes (16 minutes for single chamber).METHOD 1010.818 June 20041MIL-STD-883GMETHOD 1010.8 18 June 20042TABLE I. Temperature-cycling test conditions.Test condition temperature (°C)StepMinutes A B C D E F 1 Cold>10-55 +0 -10-55 +0 -10-65 +0 -10-65 +0 -10-65 +0 -10-65 +0 -10 2 Hot>1085 +10 -0125 +15 -0150 +15 -0200 +15 -0300 +15 -0175 +15 -0NOTE: Steps 1 and 2 may be interchanged. The load temperature may exceed the + or - zero (0) tolerance during the recovery time. Other tolerances shall not be exceeded.3.2 Examination. After completion of the final cycle, an external visual examination of the marking shall be performed without magnification or with a viewer having a magnification no greater than 3X. A visual examination of the case, leads, or seals shall be performed at a magnification between 10X and 20X (except the magnification for examination shall be 1.5X minimum when this method is used for 100 percent screening). This examination and any additional specifiedmeasurements and examination shall be made after completion of the final cycle or upon completion of a group, sequence, or subgroup of tests which include this test.3.3 Failure criteria. After subjection to the test, failure of one or more specified end-point measurements or examinations (see4.d.), evidence of defects or damage to the case, leads, or seals or illegible markings shall be considered a failure. Damage to the marking caused by fixturing or handling during tests shall not be cause for device rejection.4. SUMMARY. The following details shall be specified in the applicable acquisition document:a. Special mounting, if applicable (see 3).b. Test condition letter, if other than test condition C (see 3).c. Number of test cycles, if other than 10 cycles (see 3).d. End-point measurements and examinations (see 3.1) (e.g., end-point electrical measurements, seal test (method1014), or other acceptance criteria).MIL-STD-883GMETHOD 1010.818 June 20043Figure 1010-1 An example of Temperature Cycling Test Condition C.*MIL-STD-883GThis page intentionally left blank METHOD 1010.818 June 20044。
Extech CD Regulated Power Supply Modelos 382203 y

Manual del usuarioFuente de poder CD regulada con tres salidas Modelos 382203 (Análogo) y 382213 (Digital)IntroducciónFelicitaciones por seleccionar la Fuente de poder CD regulado Modelos 382203 (análogo) o 382213 (digital) de Extech. Los modelos 382203 y 382213 son fuentes de poder reguladas de estado sólido y compactos, apropiadas para muchas aplicaciones incluyendo pruebas de banco, servicio de campo, equipo de telecomunicaciones y diversión.Descripción del medidor1. Pantallas LCD Voltaje y Corriente2. LED indicador de estado de límite de corriente3. Interruptor de encendido con LED de estado4. Terminales de salida 5V y 12V fijo5. Terminales de salida alimentación variable6. Perillas de ajuste de voltaje y corriente variableNota: El Modelo 382213 (escalas LCD) se muestra arriba. El Modelo 382203 (mostrado en la portada) usa escala análoga.Operación1. La Fuente de poder debe ser alimentada con voltaje de línea nominal (110V ó 220V) dentro de+ 5%.2. Antes de encender, retire todas las cargas conectadas y fije la perilla de ajuste de voltajetotalmente contrarreloj (salida 0V CD).3. Para operar la fuente de alimentación como fuente de corriente constante, la salida de corrientedebe fijarse entre 10% y 100% del valor nominal (3A). El indicador de limitación de corriente se iluminará al activarse el circuito limitador de corriente.4. Use las perillas para ajuste de corriente y voltaje para fijar las salidas variables de corriente yvoltaje respectivamente. Use las terminales de salida variable para conexiones.5. Para las salidas de 5VCD y 12VCD, use las terminales de salida fija.6. Las pantallas análoga o digital indicaran las salidas reales de corriente y voltaje.7. Mantenga libre de obstrucciones las rejillas de ventilación del medidor (arriba y lados) paraprevenir sobrecalentamiento.Especificaciones382203382213Indicador Análogo doble conescalas Pantalla LCD doble de 3dígitosSalida de voltaje, CD0-30VSalida de corriente, CD0 - 3 amperiosIndicador de límite decorrienteLED de estadoPrecisión ± 7% de la escala total ± 1% de la escala total + 2dígitosOndulación y Ruido< 5mVRegulación de línea< 0,05% + 10mVVoltaje fijo de salida5V / 0,5A (Continuo); 1A (máx.)12V / 0,5A (Continuo); 1A (máx.)Tensión110/220VCA 50/60Hz (conmutable) Dimensiones152 x 142 x 242mm(6 x 5,6 x 9,5") (WxHxD)Peso4,5 kg (10 lbs.)Copyright (c)2012 Extech Instruments Corporation (a FLIR company) Reservados todos los derechos, incluyendo el derecho de reproducción total o parcial en cualquier medi o.。
MIL-STD-883E for Electrostatic Discharge Sensitivity Classification
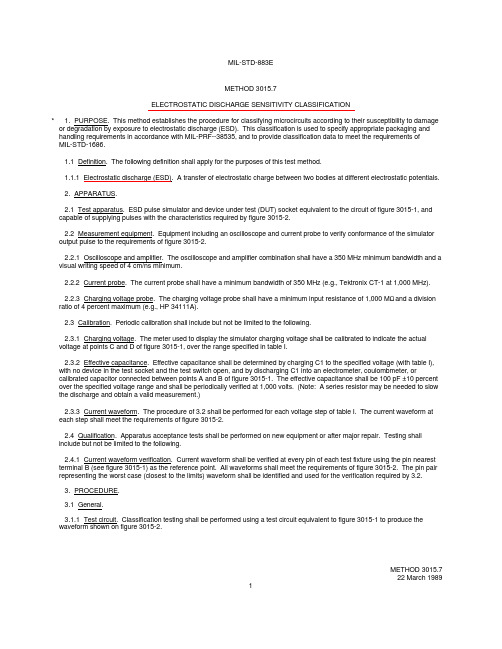
METHOD 3015.722 March 19891METHOD 3015.7ELECTROSTATIC DISCHARGE SENSITIVITY CLASSIFICATION* 1. PURPOSE. This method establishes the procedure for classifying microcircuits according to their susceptibility to damage or degradation by exposure to electrostatic discharge (ESD). This classification is used to specify appropriate packaging and handling requirements in accordance with MIL-PRF--38535, and to provide classification data to meet the requirements of MIL-STD-1686.1.1 Definition. The following definition shall apply for the purposes of this test method.1.1.1 Electrostatic discharge (ESD). A transfer of electrostatic charge between two bodies at different electrostatic potentials.2. APPARATUS.2.1 Test apparatus. ESD pulse simulator and device under test (DUT) socket equivalent to the circuit of figure 3015-1, and capable of supplying pulses with the characteristics required by figure 3015-2.2.2 Measurement equipment. Equipment including an oscilloscope and current probe to verify conformance of the simulator output pulse to the requirements of figure 3015-2.2.2.1 Oscilloscope and amplifier. The oscilloscope and amplifier combination shall have a 350 MHz minimum bandwidth and a visual writing speed of 4 cm/ns minimum.2.2.2 Current probe. The current probe shall have a minimum bandwidth of 350 MHz (e.g., Tektronix CT-1 at 1,000 MHz).2.2.3 Charging voltage probe. The charging voltage probe shall have a minimum input resistance of 1,000 M 6and a division ratio of 4 percent maximum (e.g., HP 34111A).2.3 Calibration. Periodic calibration shall include but not be limited to the following.2.3.1 Charging voltage. The meter used to display the simulator charging voltage shall be calibrated to indicate the actual voltage at points C and D of figure 3015-1, over the range specified in table I.2.3.2 Effective capacitance. Effective capacitance shall be determined by charging C1 to the specified voltage (with table I),with no device in the test socket and the test switch open, and by discharging C1 into an electrometer, coulombmeter, orcalibrated capacitor connected between points A and B of figure 3015-1. The effective capacitance shall be 100 pF ±10 percent over the specified voltage range and shall be periodically verified at 1,000 volts. (Note: A series resistor may be needed to slow the discharge and obtain a valid measurement.)2.3.3 Current waveform. The procedure of 3.2 shall be performed for each voltage step of table I. The current waveform at each step shall meet the requirements of figure 3015-2.2.4 Qualification. Apparatus acceptance tests shall be performed on new equipment or after major repair. Testing shall include but not be limited to the following.2.4.1 Current waveform verification. Current waveform shall be verified at every pin of each test fixture using the pin nearest terminal B (see figure 3015-1) as the reference point. All waveforms shall meet the requirements of figure 3015-2. The pin pair representing the worst case (closest to the limits) waveform shall be identified and used for the verification required by 3.2.3. PROCEDURE.3.1 General.3.1.1 Test circuit. Classification testing shall be performed using a test circuit equivalent to figure 3015-1 to produce the waveform shown on figure 3015-2.3.1.2 Test temperature. Each device shall be stabilized at room temperature prior to and during testing.3.1.3 ESD classification testing. ESD classification testing of devices shall be considered destructive.3.2 ESD simulator current waveform verification. To ensure proper simulator operation, the current waveform verification procedure shall be done, as a minimum, at the beginning of each shift when ESD testing is performed, or prior to testing after each change of the socket/board, whichever is sooner. If the simulator does not meet all requirements, all classification testing done since the last successful verification shall be repeated. At the time of initial facility certification and recertifications, photographs shall be taken of the waveforms observed as required by 3.2c through 3.2e and be kept on file for purposes of audit and comparison. (Stored digitized representations of the waveforms are acceptable in place of photographs.)a.With the DUT socket installed on the simulator, and with no DUT in the socket, place a short (figure 3015-1) acrosstwo pins of the DUT socket and connect one of the pins to simulator terminal A and the other pin to terminal B.b.Connect the current probe around the short near terminal B (see figure 3015-1). Set the simulator charging voltagesource V S to 4,000 volts corresponding to step 4 of table I.c.Initiate a simulator pulse and observe the leading edge of the current waveform. The current waveform shall meet therise time, peak current, and ringing requirements of figure 3015-2.d.Initiate a simulator pulse again and observe the complete current waveform. The pulse shall meet the decay time andringing requirement of figure 3015-2.e.Repeat the above verification procedure using the opposite polarity(V S = -4,000 volts).f.It is recommended that the simulator output be checked to verify that there is only one pulse per initiation, and thatthere is no pulse while capacitor C1 is being charged. To observe the recharge transient, set the trigger to theopposite polarity, increase the vertical sensitivity by approximately a factor of 10, and initiate a pulse.TABLE I. Simulator charging voltage (V S) steps versus peak current (I P). 1/Step V S (volts)I P (amperes)1 500 0.332 1,000 0.673 2,000 1.334 4,000 2.671/I P is the current flowing through R2 duringthe current waveform verification procedureand which is approximately V S/1,500 ohms.3.3 Classification testing.a. A sample of devices (see 4.c) shall be characterized for the device ESD failure threshold using the voltage steps shown intable I, as a minimum. Finer voltage steps may optionally be used to obtain a more accurate measure of the failure voltage.Testing may begin at any voltage step, except for devices which have demonstrated healing effects, including those with spark gap protection, which shall be started at the lowest step. Examination of known technology family input or output V/I damage characteristics (i.e., curve tracer), or other simplified test verification techniques may be used to validate the failure threshold(e.g., cumulative damage effects may be eliminated by retesting at the failure voltage step using a new sample of devices andpossibly passing the step).METHOD 3015.122 March 19892METHOD 3015.722 March 19893b. A new sample of devices shall be selected and subjected to the next lower voltage step used. Each device shall be testedusing three positive and three negative pulses using each of the pin combinations shown in table II. A minimum of 1 second delay shall separate the pulses.c.The sample devices shall be electrically tested to subgroups 1 and 7 as applicable (room temperature dc parameters and functional tests).d.If one or more of the devices fail, the testing of 3.3b and 3.3c shall be repeated at the next lower voltage step used.e.If none of the devices fail, record the failure threshold determined in 3.3a. Note the highest step passed, and use it to classify the device according to table III. TABLE II. Pin combinations to be tested. 1/ 2/ Terminal A(Each pin individually connected to terminal Awith the other floating) Terminal B (The common combination of all like-named pins connected to terminal B) 1.All pins except V ps1 3/ All V ps1 pins 2. All input and output pins All other input-output pins 1/ Table II is restated in narrative form in 3.4 below.2/ No connects are not to be tested.3/ Repeat pin combination 1 for each named power supply and for ground (e.g., where V ps1 is V DD , V CC , V SS , V BB , GND, +V S , -V S , V REF , etc.)3.4 Pin combination to be tested.a.Each pin individually connected to terminal A with respect to the device ground pin(s) connected to terminal B. All pins exceptthe one being tested and the ground pin(s) shall be open.b.Each pin individually connected to terminal A with respect to each different set of a combination of all named power supply pins(e.g., V SS1 or V SS2 or V SS3 or V CC1 or V CC2) connected to terminal B. All pins except the one being tested and the power supply pin or set of pins shall be open.c.Each input and each output individually connected to terminal A with respect to a combination of all the other input and output pins connected to terminal B. All pins except the input or output pin being tested and the combination of all the other input and output pins shall be open.TABLE III. Device ESD failure threshold classification.Class 10 volt to 1,999 volts Class 22,000 volts to 3,999 volts Class 3 4,000 volts and above4. SUMMARY. The following details shall be specified in the applicable purchase order or contract, if other than specified herein.a.Post test electricals.b.Special additional or substitute pin combinations, if applicable.c.Sample size, if other than three devices.METHOD 3015.122 March 19894METHOD 3015.722 March 19895R1 = 106 ohms to 107 ohmsC1 = 100 picofarads ±10 percent(Insulation resistance 1012 ohms minimum)R2 = 1,500 ohms ±1 percentS1 = High voltage relay(Bounceless, mercury wetted, or equivalent)S2 = Normally closed switch (Open during discharge pulse and capacitance measurement)NOTES:1.The performance of this simulator circuit is strongly influenced by parasitics. Capacitances across relays andresistor terminals, and series inductance in wiring and in all components shall be minimized.2.As a precaution against transients upon recharge of C1, the supply voltage V S may be reduced before switch S1 isreturned to the charging position.3.Piggybacking DUT sockets is not permitted during verification or classification testing.4.Switching terminals A and B internal to the simulator to obtain opposite polarity is not recommended.5.C1 represents the effective capacitance (see 2.3.2).6.The current probe connection shall be made with double shielded cable into a 50-ohm termination at theoscilloscope. The cable length shall not exceed 3 feet.FIGURE 3015-1. EDS classification test circuit (human body model).NOTES:1.The current waveforms shown shall be measured as described in the waveform verification procedure of 3.2,using equipment meeting the requirements of 2.2.The current pulse shall have the following characteristics:Tri (rise time)---------------Less than 10 nanoseconds.Tdi (delay time)-------------150 ±20 nanoseconds.I p (peak current)------------Within ±10 percent of the I p value shown in table II for the voltage step selected.I r (ringing)--------------------The decay shall be smooth, with ringing, break points, double time constants ordiscontinuities less than 15 percent I p maximum, but not observable 100nanoseconds after start of the pulse.FIGURE 3015-2. EDS classification test circuit waveforms (human body model).METHOD 3015.122 March 19896。
MIL-STD-883_2003[1].7
![MIL-STD-883_2003[1].7](https://img.taocdn.com/s3/m/f705c1895ef7ba0d4a733bf9.png)
METHOD 2003.7SOLDERABILITY1. PURPOSE. The purpose of this test method is to evaluate the solderability of terminations (including leads up to 0.125 inch in diameter) that are normally joined by a soldering operation. This evaluation is made on the basis of the ability of these terminations to be wetted by a coating of solder, and to produce a suitable fillet when dip soldered. These procedures will test whether the treatment used in the manufacturing process to facilitate soldering is satisfactory and that it has been applied to the required portion of the part that is designed to accommodate a solder connection. An accelerated aging test is included in this test method that simulates natural aging under a combination of various storage conditions that have different deleterious effects.1.1 Terms and definitions. The definition of terms shall be in accordance with the following:1.1.1 Solderability. The property of a metal to be wetted by solder.1.1.2 Wetting. The formation of a relatively uniform, smooth and unbroken film of solder, adherent to the surface tested.1.1.3 Porosity. A condition of a solder coating with a spongy appearing, uneven surface that contains a concentration of small pinholes and pits. See figure 2003-1.1.1.4 Nonwetting. A condition whereby a surface has contacted molten solder, but the solder has not adhered to all of the surface, and the surface tested remains exposed. See figure 2003-2.1.1.5 Pinholes and voids. Holes occurring as imperfections that penetrate entirely through the solder layer. See figures2003-3, 2003-4, and 2003-5.1.1.6 Dewetting. A condition that results when molten solder has coated a surface and then receded leaving irregularly shaped mounds of solder separated by areas covered with a thin solder film, and where the base metal is not exposed. See figure 2003-6.1.1.7 Foreign material. Particles of material located on, but different from, the lead material or coating. See figure 2003-7.1.1.8 Solder and flux minimum application depth.1.1.8.1 Dual-in-line packages. The location at which the termination widens to its maximum shoulder dimension, or to the package base plane, whichever is the further point from the seal.1.1.8.2 Radial-lead packages (e.g., flatpacks, top brazed quads). A location on the lead, no greater than 0.05 inch from the package.1.1.8.3 Axial-lead packages (e.g., TO cans, PGA, and platform packages). A location on the lead that is no greater than 0.05 inch from the body of the package, the seating plane, or the standoff, whichever is the furthest from the glass seal.1.1.8.4 Leaded chip carriers (i.e., J bend, gull wing). A location on the leads equal to an extension of the base plane onto the leads, or the point at which the lead widens.1.1.8.5 Leadless chip carriers. The location that provides for complete immersion of the termination.2. APPARATUS.2.1 Solder pot. A solder pot of sufficient size to contain at least two pounds of solder shall be used. The solder shall be static during the dipping procedure. The apparatus shall be capable of maintaining the solder at the temperature specified in 4.4.METHOD 2003.715 November 199112.2 Dipping mechanism. A dipping mechanism capable of controlling the rates of immersion and emersion of the terminations and providing a dwell time (total time at the required depth) in the solder bath as specified in 4.4 shall be used. The sample holder shall not come in contact with the solder bath and shall be designed to minimize the trapping of flux.2.3 Optical equipment. A binocular optical system capable of providing a minimum magnification of 10X shall be used.2.3.1 Lighting equipment. A lighting system shall be used that will provide a uniform, nonglare, nondirectional illumination of the specimen.2.4 Steam aging equipment. A noncorrodible container and cover of sufficient size to allow the placement of specimens inside the vessel shall be used. The specimens shall be placed such that the lowest portion of the specimen is a minimum of 1.5 inches above the surface of the water (see3.4). A suitable method of supporting the specimens shall be improvised using noncontaminating material. The apparatus shall be capable of having the specified temperature verified as required by4.2.2.4.1 Cleaning of the system. The apparatus shall be drained and cleaned at least once per month or prior to use. A more frequent cleaning cycle may be necessary as indicated by resistivity, visual, or general cleanliness of the water. No contaminating solvents shall be used.3. MATERIALS3.1 Flux. The flux shall conform to flux type symbol "A" (flux type "L0") of ANSI/J-STD-004, Requirements for Soldering Fluxes (previously designated as type "R" in MIL-F-14256) (25 percent by weight gum rosin in a 99 percent isopropyl alcohol solvent). The specific gravity of the flux shall be maintained within the range of 0.838 to 0.913 at 25°C. The customer/equipment manufacturer may, at their option, use flux type symbol "A" or "B" (flux type "L0" or "L1") flux (previously designated as "RMA" in MIL-F-14256).3.2 Solder. The acquired solder shall conform to type Sn63A or Pb37A (previously designated as Sn63 in QQ-S-571) orSn60A or Pb40A (previously designated as Sn60 in QQ-S-571) of ANSI/J-STD-006, Requirements for Electronic Grade Solder Alloys and Fluxed and Non-fluxed Solid Solders for Electronic Soldering Applications.3.3 Isopropyl alcohol. Commercial grade isopropyl alcohol or better shall be used.3.4 Water. The water to be used for steam aging purposes shall be either distilled or deionized.WARNING: These materials may involve substances that are flammable, toxic to eyes, skin, or respiratory tract, or present a serious burn potential. Eye and skin protection should be used. Heat resistant gloves should be used when handling hot objects.4. PROCEDURE. The test procedure shall be performed on the number of terminations specified in the acquisition document. The test may be performed just prior to packaging for storage or shipment, immediately upon removal from the manufacturer's protective packaging, or as a qualification or quality conformance test. The sample shall be selected at random. During handling, special care shall be exercised to prevent the surfaces being tested from being abraded or contaminated by grease, perspiration, or abnormal atmospheres. The test procedure shall consist of the following operations:a.Proper preparation of the specimens (see 4.1), if applicable.b.Aging of all specimens (see 4.2).c.Application of flux and immersion of the terminations into molten solder (see 4.3 and 4.4).d.Examination and evaluation of the tested portions of the terminations upon completion of the solder-dip process(see 4.5).METHOD 2003.715 November 199124.1 Preparation of terminations. No wiping, cleaning, scraping, or abrasive cleaning of the terminations shall be performed prior to testing. Any special preparation of the terminations, such as bending or reorientation prior to the test, shall be specified in the acquisition document. The customer/equipment manufacturer, may, at their option, clean the terminations using a nonabrasive, nonactive solvent (e.g., isopropyl alcohol).4.2 Steam aging. Prior to the application of the flux and subsequent solder dips, all specimens assigned to this test shall be subjected to aging by exposure of the surfaces to be tested to water vapor for 8 hours ±0.5 hour in the apparatus specified in2.4. The water vapor temperature at the component lead level shall be in accordance with table I. Aging may be interrupted once for 10 minutes maximum. The devices shall be removed from the test apparatus upon completion of the specified test period.4.2.1 Drying and storage procedures. Upon removing the test specimens from the apparatus, the parts may be dried using one of the following procedures:a.Bake at 100°C maximum for no more than 1 hour in a dry atmosphere (dry nitrogen atmosphere is recommended).b.Air dry at ambient temperature for a minimum of 15 minutes.NOTE: Parts not solderability-tested within 2 hours after removal from the aging apparatus shall be stored in a desiccant jar or dry nitrogen cabinet for a maximum of 72 hours before testing. The parts shall not be used for testing if they have exceeded the storage requirements.4.3 Application of flux. The terminations to be tested shall be immersed in flux maintained at room ambient temperature. The terminations, unless otherwise specified in the individual specification, shall be immersed according to 1.1.8. The terminations to be tested shall be immersed in the flux for 5 to 10 seconds, and shall be drained for 5 to 20 seconds prior to dipping in the solder pot. The flux shall be covered when not in use and discarded a minimum of once a day. Any obvious droplets of flux clinging to the termination may be removed by blotting.4.4 Solder dip procedure. The dross and burned flux shall be skimmed from the surface of the molten solder prior to testing.A wave solder pot may be used for this purpose, but the solder shall be static during the dipping procedure. The molten solder shall be at a uniform temperature of 245°C ±5°C (473°F, ±9°F). (Skimming may not be required in wave or flow pots). The part shall be attached to a dipping mechanism (see 2.2) and the flux covered terminations immersed once (except for the possible duplicate immersion of corner terminations on leadless packages) in the molten solder to the depth specified in 1.1.8. NOTE: The test sample shall not be suspended above the hot solder pot for longer than 7 seconds. The immersion and emersion rates shall be 1.0 inch per second ±.25 inch per second. The dwell time in the solder shall be 5 seconds ±.5 second. The dwell time for terminations greater than or equal to 0.040 inch in diameter shall be 7 seconds ±.5 second. After the dipping process, the part shall be allowed to cool in air. Residual flux shall be removed from the terminations by dipping the parts in isopropyl alcohol or other suitable solvent. If necessary, a clean soft cloth, cotton swab, or equivalent, moistened with clean isopropyl alcohol or other suitable solvent, may be used to remove all remaining flux.4.4.1 Solder dipping of gold plated terminations. Gold plated terminations shall be cycled twice in flux and solder using one or two solder pots. The first immersion is to scavenge the gold on the terminations. It is recommended that a separate solder pot be used for gold plated devices.4.4.2 Immersion angle. Unless otherwise specified, the terminations shall be immersed perpendicular to the solder surface. For leaded or leadless chip carriers, the terminations shall be immersed at a 30° to 45° angle to the solder surface.4.4.3 Solder bath contaminants. The manufacturer shall have a system to verify that the solder bath does not exceed the contaminant levels specified in table II.METHOD 2003.715 November 19913METHOD 2003.715 November 19914TABLE I. Altitude versus steam temperature (see 4.2).Altitude(feet)Steam temperature (°C +3, -5) 0 - 2,00093 2,001 - 4,000914,001 - 6,00089 Greater than 6,00087TABLE II. Maximum limits of solder bath contaminant (see 4.4.3).Contaminant Contaminant percentage limit Copper 0.300 Gold 0.200 Cadmium 0.005 Zinc 0.005 Aluminum 0.006 Antimony 0.500 Iron 0.020 Arsenic 0.030 Bismuth 0.250 Silver 0.100 Nickel 0.010NOTE: The total copper, gold, cadmium, zinc, and aluminum contaminants shall not exceed 0.4 percent.* 4.5 Examination of terminations. The dipped portion of the terminations shall be examined using a magnification of 10-15X.Verification of failures may be accomplished with higher magnifications up to 60X. The customer/equipment manufacturer of the component may establish a critical portion of the termination within the dipped area. The customer/equipment manufacturer has the option to accept solderability defects outside their established critical area. The customer/equipment manufacturer has the option of cleaning parts to remove carbonate/sulfate deposits caused by exposure of the parts to the steam aging or cleaning process. The customer/equipment manufacturer shall assure that the cleaning process does not adversely affect the physical, mechanical, electrical, or reliability performance of the parts. This cleaning process shall be fully documented. For leaded devices only, the cut portions of the lead which expose lead ends shall not be used for examination and evaluation of the solder coverage of the termination.4.5.1 Criteria for acceptance. The criteria for acceptable solderability (see figures 2003-1 through 2003-7) are:a.The dipped portion of the terminations is at least 95 percent covered by a continuous new solder coating.b.Pinholes, voids, porosity, nonwetting, or dewetting do not exceed 5 percent of the total area.c.For leadless terminations and elements having solder attachment terminations, there shall be no solder bridgingbetween any termination area and any other metallization not connected to it by design. In the event that the solderdipping causes bridging, the test shall not be considered a failure provided that a local application of heat (e.g., gas,soldering iron, or redipping) results in solder pullback and no wetting of the dielectric area as indicated by microscopicexamination. The area of the surface to be tested shall be as specified in 1.1.8.NOTE: The total area of the surface to be tested including all faces for rectangular leads) as specified in 4.5 shall beexamined. In the case of a dispute, the percentage of coverage with pinholes or voids shall be determined by the actual measurement of those areas, compared to the total area(s).5. SUMMARY. The following details are to be specified in the individual specifications unless otherwise noted:a.The number of terminations of each part to be tested (see 4).b.Special preparations of the terminations, if applicable (see 4.1).c.Depth of immersion if other than in 1.1.8.d.Magnification, if other than in 2.3.e.Solder composition, flux, and temperature if other than those specified in this document.f.Number of cycles, if other than one, or as noted in this test method. Where more than one cycle is specified to testthe resistance of the device to heat as encountered in multiple solderings, the examinations and measurementsrequired shall be made at the end of the first cycle and again at the end of the total number of cycles applied. Failureof the device on any examination and measurement at either the one-cycle or the end point shall constitute a failure tomeet this requirement.METHOD 2003.715 November 19915FIGURE 2003-1. Porosity. METHOD 2003.715 November 19916FIGURE 2003-2. Nonwetting.METHOD 2003.715 November 19917How to use this chart:1. The chart is set-up for .5 inch long leads.2. View the entire circumference of the lead.3. Locate the lead diameter on the left side of the chart.4. Locate the diameter of the void on the top of the chart.0.001 0.003 0.005 0.010 0.015 0.020 0.030 0.0400.010 1000 111 40 10 4.4 2.5 1.10 0.620.015 1500 167 60 15 6.6 3.75 1.60 0.9370.020 2000 222 80 20 8.8 5 2.22 1.250.030 3000 333 120 30 13.0 7.5 3.33 1.870.040 4000 444 160 40 17.7 10 4.44 2.500.050 5000 555 200 50 22.0 12.5 5.55 3.120.060 6000 666 240 60 26.6 15 6.66 3.75Examples for less than .5 inch leads:A. Lead length = 0.350.B. 0.350/0.500 = 0.700.C. To determine the number of acceptable voids, multiplythe number of voids on the chart by 0.700.D. For a 0.01 inch void on a 0.010 inch diameter lead = 700 voids.E. For leads greater than 1.0 inch in length, see 4.5.FIGURE 2003-3. Solderability evaluation guidelines.METHOD 2003.715 November 19918METHOD 2003.715 November 19919FIGURE 2003-4. Solderability coverage of a 0.5 inch, .025 diameter lead at 10X magnification.FIGURE 2003-5. Pinholes. METHOD 2003.715 November 199110FIGURE 2003-6. Dewetting.METHOD 2003.715 November 199111FIGURE 2003-7. Foreign material. METHOD 2003.715 November 199112。
MIL-STD-883E METHOD-1012.1_IC
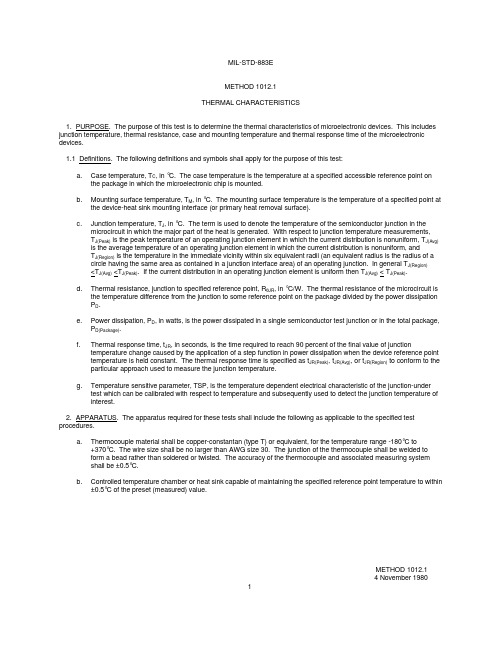
METHOD 1012.1THERMAL CHARACTERISTICS1. PURPOSE. The purpose of this test is to determine the thermal characteristics of microelectronic devices. This includes junction temperature, thermal resistance, case and mounting temperature and thermal response time of the microelectronic devices.1.1 Definitions. The following definitions and symbols shall apply for the purpose of this test:a.Case temperature, T C, in °C. The case temperature is the temperature at a specified accessible reference point onthe package in which the microelectronic chip is mounted.b.Mounting surface temperature, T M, in °C. The mounting surface temperature is the temperature of a specified point atthe device-heat sink mounting interface (or primary heat removal surface).c.Junction temperature, T J, in °C. The term is used to denote the temperature of the semiconductor junction in themicrocircuit in which the major part of the heat is generated. With respect to junction temperature measurements,T J(Peak) is the peak temperature of an operating junction element in which the current distribution is nonuniform, T J(Avg) is the average temperature of an operating junction element in which the current distribution is nonuniform, andT J(Region) is the temperature in the immediate vicinity within six equivalent radii (an equivalent radius is the radius of acircle having the same area as contained in a junction interface area) of an operating junction. In general T J(Region)<T J(Avg) <T J(Peak). If the current distribution in an operating junction element is uniform then T J(Avg) < T J(Peak).d.Thermal resistance, junction to specified reference point, RθJR, in °C/W. The thermal resistance of the microcircuit isthe temperature difference from the junction to some reference point on the package divided by the power dissipation P D.e.Power dissipation, P D, in watts, is the power dissipated in a single semiconductor test junction or in the total package,P D(Package).f.Thermal response time, t JR, in seconds, is the time required to reach 90 percent of the final value of junctiontemperature change caused by the application of a step function in power dissipation when the device reference point temperature is held constant. The thermal response time is specified as t JR(Peak), t JR(Avg), or t JR(Region) to conform to the particular approach used to measure the junction temperature.g.Temperature sensitive parameter, TSP, is the temperature dependent electrical characteristic of the junction-undertest which can be calibrated with respect to temperature and subsequently used to detect the junction temperature of interest.2. APPARATUS. The apparatus required for these tests shall include the following as applicable to the specified test procedures.a.Thermocouple material shall be copper-constantan (type T) or equivalent, for the temperature range -180°C to+370°C. The wire size shall be no larger than AWG size 30. The junction of the thermocouple shall be welded toform a bead rather than soldered or twisted. The accuracy of the thermocouple and associated measuring systemshall be ±0.5°C.b.Controlled temperature chamber or heat sink capable of maintaining the specified reference point temperature to within±0.5°C of the preset (measured) value.METHOD 1012.14 November 19801c.Suitable electrical equipment as required to provide controlled levels of conditioning power and to make the specifiedmeasurements. The instrument used to electrically measure the temperature-sensitive parameter shall be capable of resolving a voltage change of 0.5 mV. An appropriate sample-and-hold unit or a cathode ray oscilloscope shall beused for this purpose.d.Infrared microradiometer capable of measuring radiation in the 1 to 6 micrometer range and having the ability to detectradiation emitted from an area having a spatial resolution of less than 40 micrometers (1.6 mils) diameter at its halfpower points and a temperature resolution (detectable temperature change) of 0.5°C at 60°C.NOTE: May be a scanning IR microradiometer.e. A typical heat sink assembly for mounting the microelectronic device-under test is shown on figure 1012-1. Theprimary heat sink is water cooled and has a thermocouple sensor for inlet and outlet water temperature as shown infigure 1012-1a.An adapter heat sink, as shown on figure 1012-1b is fastened to the top surface of the primary heat sink, and has a special geometry to handle specific size packages, e.g., flat packs, dual-in-line packages (small and large size) and TO-5 cans. This adapter provides a fairly repeatable and efficient interface between the package and the heat sink; the heat sink temperature is determined from a thermocouple peened into the underside of the adapter-near the package.The adapter also contains the socket or other electrical interconnection scheme. In the case of the flat pack adapter heat sink, the package is dropped into a special slotted printed circuit board (PCB) to register the leads with runs on the PCB; toggle clamps then provide a pressure contact between the package leads and the PCB runs. Dual-in-line and axial lead packages plug into a regular socket.The thermal probe assembly is shown on figure 1012-1b. In practice, the pressure adjustment cap is adjusted so the disk at the probe tip contacts the bottom surface of the package (chip carrier) with a predetermined force. A silicone grease (about 25-50 mm thick) is used at this interface to provide a reliable thermal contact.3. PROCEDURE.3.1 Direct measurement of reference point temperature, T C or T M. For the purpose of measuring a microelectronic device thermal resistance or thermal response time, the reference point temperature shall be measured at the package location of highest temperature which is accessible from outside the package. In general, that temperature shall be measured on the surface of the chip carrier directly below the chip. The location selected shall be as near the chip as possible and representative of a temperature in the major path of heat flow from the chip to the heat sink. The surface may be altered to facilitate this measurement provided that such alteration does not affect the original heat transfer paths and, hence, the thermal resistance, within the package by more than a few percent.3.1.1 Case temperature, T C. The microelectronic device under test shall be mounted on a temperature controlled heat sink so that the case temperature can be held at the specified value. A thermocouple shall be attached as near as possible to the center of the bottom of the device case directly under the chip or substrate. A conducting epoxy may be used for this purpose. In general, for ambient cooled devices, the case temperature should be measured at the spot with the highest temperature. The thermocouple leads should be electrically insulated up to the welded thermocouple bead. The thermocouple bead should be in direct mechanical contact with the case of the microelectronic device under test.3.1.2 Mounting surface temperature, T M. The mounting surface temperature is measured directly below the primary heat removal surface of the case. It is measured with a thermocouple at or near the mounting surface of the heat sink. A typical mounting arrangement is shown on figure 1012-2. The surface of the copper mounting base shall be nickel plated and free of oxides.METHOD 1012.14 November 19802The thermocouple hole shall be drilled into the mounting base such that the thermocouple lead is directly below the area on the case of interest. It is recommended that the thermocouple be secured into the mounting base with a thermal conducting adhesive (or solder) and that particular attention be paid to minimizing air voids around the ball of the thermocouple. A thermal conducting compound (or adhesive) should be used at the interface of the mounting base and the device under test.3.2 Thermal resistance, junction to specified reference point, RθJR.3.2.1 General considerations. The thermal resistance of a semiconductor device is a measure of the ability of its carrier or package and mounting technique to provide for heat removal from the semiconductor junction.The thermal resistance of a microelectronic device can be calculated when the case temperature and power dissipation in the device, and a measurement of the junction temperature are known. The junction with the greatest power dissipation density (watts/mm2) shall be selected for measurement since that junction will generally have the highest temperature on the chip. If the leads to that junction are not accessible and another junction is measured then it cannot be assured that the highest temperature on the chip will be measured. Direct measurement should be used in this case.When making the test measurements indicated below, the package shall be considered to have achieved thermal equilibrium when the measured temperature difference, junction to case, reaches approximately 99 percent of its final value. The temperature difference at that time will change at a rate less thand(T J - T C) < 0.03 (T J - T C)dt twhere t is the time after application of a power dissipation increment. The total time required for stabilization will typically be less than a minute.3.2.2 Direct measurement of junction temperature for determination of RθJR. The junction temperature of the thermally limiting element within the semiconductor chip can be measured directly using an infrared microradiometer. The cap or lid shall first be removed from the package to expose the active chip or device. The cavity shall not be covered with any IR transparent material unless the chip is extremely large and has an extremely poor heat conduction path to the chip carrier. The location of the junction to be measured should be referenced to a coordinate system on the chip so it can be relocated after coating the chip. The active area of the chip shall be coated uniformly with a thin layer (25-50 µm thick) of a known high emissivity (∈ > 0.8), low thermal conductivity material such as black pigmented lacquer. The package shall then be placed on a temperature controlled heat sink and the case or mounting surface temperature stabilized at the specified value. The microelectronic device under test shall then be operated at its rated power dissipation, the infrared microscope crosshairs focused on the junction and scanned back and forth slightly at that location to maximize the radiance measurement. That radiance measurement and the chip carrier temperature shall then be recorded. The power to the test package shall then be turned off and the chip carrier allowed to return to the specified case or mounting surface temperature. The emissivity of the coating over the junction region shall then be measured and the radiance from the operating junction region shall be converted to temperature using this emissivity value. (Note that this method assumes the emissivity of the coating material does not change appreciably with temperature. This assumption shall be valid if the results are to be accurate and repeatable.)If the junction to be measured is not specified then the test shall proceed as above except that the IR microscope crosshairs shall be scanned over the whole active area of the chip to find and maximize the radiance measurement at the highest temperature junction region.The minimum width or length of the junction area shall be greater than 5 times the half power diameter of the objective lens and greater than 5 times the thickness of the coating on the chip surface if this method is used to measure T J(Peak). For junction element diameters between 5 and 1 times the half power diameter of the IR microscope objective lens, some average junction temperature T J(Avg), where T J(Region) < T J(Avg) < T J(Peak), will be measured.METHOD 1012.14 November 19803The following data shall be recorded for this test condition:a.Peak or average junction temperature, T J(Peak) or T J(Avg).b.Case or mounting surface temperature (usually 60°C ±0.5°C T C, T M).c.Power dissipation, P D(Package), in the package.d.Reference temperature measuring point.e.Mounting arrangement.f.Half power "spot" size of the IR microscope.g.Thickness of the emissivity control coating (for T J(Avg) measurements only).h.Minimum width or length of the junction measured (for T J(Avg) measurements only).3.2.3 Indirect measurements of junction temperature for the determination of RθJR. The purpose of the test is to measure the thermal resistance of integrated circuits by using particular semiconductor elements on the chip to indicate the device junction temperature.In order to obtain a realistic estimate of the operating average junction temperature, T J(Avg), the whole chip or chips in the package should be powered in order to provide the proper internal temperature distribution. For other purposes though (see section3.2.1), the junction element being sensed need only be powered. During measurement of the junction temperature the chip heating current shall be switched off while the junction calibration current remains stable. It is assumed that the calibration current will not affect the circuit operation; if so, then the calibration current must be switched on as the power is switched off. The temperature sensitive device parameter is used as an indicator of an average junction temperature of the semiconductor element for calculations of thermal resistance. The measured junction temperature is indicative of the temperature only in the immediate vicinity of the element used to sense the temperature. Thus, if the junction element being sensed is also dissipating power with a uniform heating current distribution, then T J(Avg)≈ T J(Peak) for that particular junction element. If the current distribution is not uniform then T J(Avg ) is measured. If the junction element being sensed is in the immediate vicinity of the element dissipating power then T J(Region) will be measured. The heating power does not have to be switched off when T J(Region) is measured.The temperature sensitive electrical parameters generally used to indirectly measure the junction temperature are the forward voltage of diodes, and the emitter-base and the collector-base voltages of bipolar transistors. Other appropriate temperature sensitive parameters may be used for indirectly measuring junction temperature for fabrication technologies that do not lend themselves to sensing the active junction voltages. For example, the substrate diode(s) in junction-isolated monolithic integrated circuits can be used as the temperature sensitive parameter for measurements of T J(Region). In this particular case though, the heating power has to be switched off at the same time that the substrate diode is forward biased.METHOD 1012.14 November 198043.2.3.1 Switching techniques for measuring T J(Avg). The following symbols shall apply for the purpose of these measurements:I M - - - - - - - - - - - - - - - -Measuring current in milliamperes.V MD - - - - - - - - - - - - - - -Value of temperature-sensitive parameter in millivolts, measured at I M, andcorresponding to the temperature of the junction heated by P D.T MC - - - - - - - - - - - - - - -Calibration temperature in °C, measured at the reference point.V MC - - - - - - - - - - - - - - -Value of temperature-sensitive parameter in millivolts, measured at I M and specificvalue of T MC.The measurement of T J(Avg) using junction forward voltage as the TSP is made in the following manner:Step 1 - Measurement of the temperature coefficient of the TSP (calibration).The coefficient of the temperature sensitive parameter is generated by measuring the TSP as a function of the reference point temperature, for a specified constant measuring current, I M, and collector voltage, by externally heating the device under test in an oven or on a temperature controlled heat sink. The reference point temperature range used during calibration shall encompass the temperature range encountered in the power application test (see step 2). The measuring current is generally chosen such that the TSP decreases linearly with increasing temperature over the range of interest and that negligible internal heating occurs during the measuring interval. A measuring current ranging from 0.05 to 5 mA is generally used, depending on the rating and operating conditions of the device under test, for measuring the TSP. The value of the TSP temperature coefficient, V MC/T MC, for the particular measuring current and collector voltage used in the test, is calculated from the calibration curve, V MC versus T MC.Step 2 - Power application test.The power application test is performed in two parts. For both portions of the test, the reference point temperature is held constant at a preset value. The first measurement to be made is that of the temperature sensitive parameter, i.e., V MC, under operating conditions with the measuring current, I M, and the collector voltage used during the calibration procedure. The microelectronic device under test shall then be operated with heating power (P D) intermittently applied at greater than or equal to 99 percent duty factor. The temperature- sensitive parameter V MD shall be measured during the interval between heating pulses (<100 µs) with constant measuring current, I M, and the collector voltage that was applied during the calibration procedure (see step 1).Because some semiconductor element cooling occurs between the time that the heating power is removed and the time that the temperature-sensitive parameter is measured, V MD may have to be extrapolated back to the time where the heating power was terminated by using the following mathematical expression which is valid for the first 100 µs of cooling:V MD (t = 0) = V MD1 + V MD2 - V MD1t11/2t11/2 - t21/2Where:V MD(t = 0) = TSP, in millivolts, extrapolated to the time at whichthe heating power is terminated,t = Delay time, in microseconds, after heating power is terminated,V MD1 = TSP, in millivolts, at time t = t1, andV MD2 = TSP, in millivolts, at time t = t2 < t1.METHOD 1012.14 November 19805If V MD(t) versus t1/2 is plotted on linear graph paper for the first 100 µs of cooling, the generated curve will be a straight line except during the initial portion where nonthermal switching transients dominate. The time t2 is the minimum time at which the TSP can be measured as determined from the linear portion of the V MD(t) versus t1/2 cooling curve. Time t1 should be at least equal to t2 + 25 µs but less than 100 µs. The delay time before the TSP can be measured ranges from 1 to 50 µs for most microelectronic devices. This extrapolation procedure is valid for semiconductor (junction) sensing elements >0.2 mm (8 mils) in diameter over the delay time range of interest (1 to 50 µs).When the error in the calculated thermal resistance caused by using V MD2 instead of the extrapolated value V MD(t = 0) exceeds 5 percent, the extrapolated value of V MD shall be used for calculating the average junction temperature.The heating power, P D, shall be chosen such that the calculated junction-to- reference point temperature difference as measured at V MD2 is greater than or equal to 20°C. The values of V MD, V MC, and P D are recorded during the power application test.The following data shall be recorded for these test conditions:a.Temperature sensitive electrical parameters (V F, V EB (emitter-only switching), V EB (emitter and collector switching),V CB, V F(subst), or other appropriate TSP).b.Average junction temperature, T J(Avg), is calculated from the equation:∆V MC - 1T J(AVG) = T R + (V MD - V MC),∆T MCwhere: T R = T C or T Mc.Case or mounting surface temperature, T C or T M, (usually 60° ±0.5°C).d.Power dissipation, P D where P D = P D(Package) or P D(Element).e.Mounting arrangement.3.2.3.2 Typical test circuits for indirect measurements of T J(Avg). The circuit on figure 1012-3 can be used to sense V F,V EB(emitter-only switches), V EB(emitter and collector switching), and V CB. The circuit is configured for heating power to be applied only to the junction element being sensed P D(Element) for illustration purposes only.The circuit on figure 1012-3 is controlled by a clock pulse with a pulse width less than or equal to 100 µs and repetition rate less than or equal to 66.7 Hz. When the voltage level of the clock pulse is zero, the transistor Q1 is off and transistor Q2 is on, and the emitter current through the device under test (DUT) is the sum of the constant heating current and the constant measuring current. Biasing transistor Q1 on, shunts the heating current to ground and effectively reverse biases the diode D1. The sample-and-hold unit is triggered when the heating current is removed and is used to monitor the TSP of the device under test. During calibration, switch S4 is open.The circuit on figure 1012-4 can be used to sense the forward voltage of the substrate diode of a junction isolated integrated circuit. In this test circuit the microelectronic device under test is represented by a single transistor operated in acommon-emitter configuration. The substrate diode D SUBST is shown connected between the collector (most positive terminal) and the emitter (most negative terminal) of the integrated circuit under test. The type of circuitry needed to interrupt the heating power will depend on the complexity of the integrated circuit being tested.The circuit on figure 1012-4 is controlled by a clock pulse with a pulse width less than or equal to 100 µs and repetition rate less than or equal to 66.7 Hz. When the voltage level of the clock pulse is zero, transistor Q1 being off and transistor Q2 on, the device under test is dissipating heating power. Biasing transistor Q1 on and Q2 off, interrupts the heating power and forward biases the substrate diode. The sample-and-hold unit is triggered when the heating current is removed and is used to monitor the substrate diode forward voltage. During calibration, switch S1 is open.METHOD 1012.14 November 198063.3 Thermal response time, junction to specified reference point, t JR.3.3.1 General considerations. When a step function of power dissipation is applied to a semiconductor device, the junction temperature does not rise as a step function, but rather as a complex exponential curve. An infrared microradiometer or the electrical technique, in which a precalibrated temperature sensitive device parameter is used to sense the junction temperature, shall be used to generate the microelectronic device thermal response time.When using electrical techniques, in which the device heating power is removed before the TSP is sensed for measuring the thermal response time, the cooling curve technique shall be used. The measurement of the cooling curve is performed by heating the device to steady state, switching the power off, and monitoring the junction temperature as the device cools. The cooling curve technique is based upon the assumption that the cooling response of a device is the conjugate of the heating response.3.3.2 Measurement of junction temperature as a function of time for the determination of t JR. The change in junction temperature as a function of time resulting from the application or removal of a step function of heating power dissipation in the junction(s) shall be observed using an infrared microradiometer with a response time of less than 100 µs, or electrical equipment with a response time of less than 100 µs and sufficient sensitivity to read a precalibrated temperature sensitive electrical parameter of the junction. During this test the device reference point temperature, as specified, shall be held constant, the step function of power dissipation shall be applied or removed, and the waveform of the junction temperature response versus time shall be recorded from the time of power application or removal to the time when the junction temperature reaches a stable value.The following data shall be recorded for this test condition:a. Temperature sensitive electrical parameter (see section 3.2.3).b.Infrared microscope spatial resolution (see section 3.2.2).c.Peak, average, or region junction temperature as a function of time (see section 3.2.2 or 3.2.3 for details).d.Case or mounting surface temperature T C or T M (usually 60°C ±0.5°C).e.Power dissipation, P D(Package) or P D(Element)m in the package.f.Reference temperature measuring point.g.Mounting arrangement.3.3.3 Typical test circuits for measurement of junction temperature as a function of time. The circuits depicted in section3.2.3 are also used for the measurement of junction temperature as a function of time. The clock pulse is varied to give the required step of heating power and the TSP is monitored on a cathode ray oscilloscope. When an infrared microradiometer is used, the measuring current and TSP sensing circuitry is disconnected.3.4 Calculations of RθJR and t JR.METHOD 1012.14 November 198073.4.1 Calculations of package thermal resistance. The thermal resistance of a microelectronic device can be calculated when the peak junction, average junction, or region junction temperature, T J(Peak), T J(Avg), or T J(Region), respectively, has been measured in accordance with procedures outlined in sections 3.1 and 3.2. If the total package capability is to be assessed, then rated power P D(Packages) should be applied to the device under test. For quality control purposes the power dissipation in the single test junction P H(Element) can be used in the calculation of thermal resistance.With the data recorded from each test, the thermal resistance shall be determined from:RθJC(PEAK) = T J(PEAK) - T C, junction peak-to-case;P D(Package)RθJC(Avg) = T J(Avg) - T C, junction average-to-case; orP D(Package)RθJC(Region) = T J(Region) - T C, junction region-to-case;P D(Package)For calculations of the junction element thermal resistance, P D(Element) should be used in the previous equations. Note that these thermal resistance values are independent of the heat sinking technique for the package. This is possible because the case or chip carrier (reference) temperature is measured on the package itself in an accessible location which provides a representative temperature in the major path of heat flow from the chip to the heat sink via the package.3.4.2 Calculation of package thermal response time. The thermal response time of a microelectronic device can be calculated when the peak junction, average junction, or region junction temperature, T J(Peak), T J(Avg), or T J(Region), respectively, has been measured as a function of time in accordance with procedures outlined in section 3.3. If the total package capability is to be assessed, then rated power P D(Package) should be applied to the device under test. For quality control purposes the power dissipation in the single test junction P D(Element) can be used in the calculation of thermal response time.With the data recorded from each test, the thermal response time shall be determined from a curve of junction temperature versus time from the time of application or removal of the heating power to the time when the junction temperature reaches a stable value. The thermal response time is 0.9 of this difference.4. SUMMARY. The following details shall be specified in the applicable acquisition document:a.Description of package; including number of chips, location of case or chip carrier temperature measurement(s), andheat sinking arrangement.b.Test condition(s), as applicable (see section 3).c.Test voltage(s), current(s) and power dissipation of each chip.d.Recorded data for each test condition, as applicable.e.Symbol(s) with subscript designation(s) of the thermal characteristics determined to verify specified values of thesecharacteristics, as applicable.f.Accept or reject criteria.METHOD 1012.14 November 19808。
mil-std-883 1018
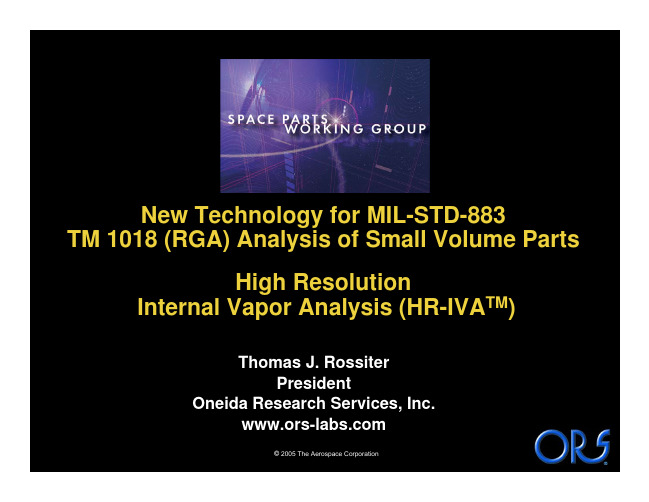
6,000
0.0005 cc with 5,000 ppmv H2O
Nitrogen (AMU-28)
5,000,000 4,000,000 3,000,000 2,000,000 1,000,000 0 -0.2
3,000
0 -0.2
0
0.2
0.4
0.6
0.8
Time (Seconds)
0.0001
0.001
0.01
0.1
1
10
100
Volume (cc)
4/5/2006
Measuring Gases from Small Parts on the Fly: Step-1
To Ionization Source Inlet
•
Puncture Pin
Improve the Transfer Efficiency to get the Sample to the Detector
New Technology for MIL-STD-883 TM 1018 (RGA) Analysis of Small Volume Parts High Resolution TM Internal Vapor Analysis (HR-IVATM)
Thomas J. Rossiter President Oneida Research Services, Inc.
orthogonal extractor
Sample Transfer Passage
Turbo Pump
cross beam ionizer ionization chamber
4/5/2006
4/5/2006
4/5/2006
mil-std-883 method 2011
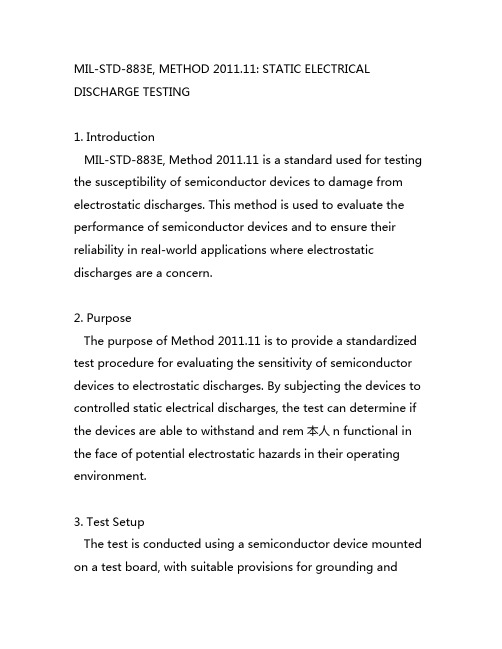
MIL-STD-883E, METHOD 2011.11: STATIC ELECTRICAL DISCHARGE TESTING1. IntroductionMIL-STD-883E, Method 2011.11 is a standard used for testing the susceptibility of semiconductor devices to damage from electrostatic discharges. This method is used to evaluate the performance of semiconductor devices and to ensure their reliability in real-world applications where electrostatic discharges are a concern.2. PurposeThe purpose of Method 2011.11 is to provide a standardized test procedure for evaluating the sensitivity of semiconductor devices to electrostatic discharges. By subjecting the devices to controlled static electrical discharges, the test can determine if the devices are able to withstand and rem本人n functional in the face of potential electrostatic hazards in their operating environment.3. Test SetupThe test is conducted using a semiconductor device mounted on a test board, with suitable provisions for grounding andconnection to the discharge source. The test board is placed on an insulating support and connected to the ground plane. The discharge source is positioned at a specified distance from the device under test, and the test setup includes a discharge relay for controlling the discharge current.4. Test ProcedureThe test is conducted by subjecting the device to multiple electrostatic discharges at various locations on the device. These discharges are initiated by a controlled discharge source, and the test measures the response of the device to the discharges, including any functional f本人lures or physical damage that may occur. The test is performed at different test levels, with the discharge current and number of discharges varying according to the test requirements.5. Test LevelsMethod 2011.11 specifies test levels for different classes of semiconductor devices, including integrated circuits, transistors, diodes, and other active and passiveponents. The test levels are determined based on the anticipated electrostatic hazards in the device's operating environment, and are designed to ensure that the device will not be damaged or imp本人red byelectrostatic discharges that it may encounter during use.6. Performance CriteriaThe test evaluates the performance of the device based on its response to the electrostatic discharges. The performance criteria specify the maximum allowable levels of functional f本人lures or physical damage that the device can sust本人n without being considered a f本人lure. The criteria include parameters such as voltage breakdown, current leakage, and any changes in electrical or mechanical characteristics of the device.7. Test ReportUponpletion of the test, a det本人led test report is prepared, documenting the test setup, test procedure, test levels, and the performance of the device during the test. The report includes a summary of the test results, including any f本人lures or deviations from the performance criteria, as well as any observations or rmendations for further evaluation or corrective actions.8. ConclusionMIL-STD-883E, Method 2011.11 provides a standard test procedure for evaluating the sensitivity of semiconductordevices to electrostatic discharges. By subjecting the devices to controlled static electrical discharges, the method helps identify potential vulnerabilities and ensures the reliability of semiconductor devices in real-world applications where electrostatic hazards are a concern. The test results provide valuable information for the design, qualification, and selection of semiconductor devices, and support the development of robust and resilient electronic systems for critical applications.In conclusion, Method 2011.11 plays a crucial role in the evaluation and qualification of semiconductor devices, and is essential for ensuring their performance and reliability in the presence of electrostatic hazards. As semiconductor technology continues to advance and electronic systems be more pervasive, the need for effective electrostatic discharge testing will only grow in importance. By adhering to the standards set forth in MIL-STD-883E, Method 2011.11, manufacturers and users of semiconductor devices can have confidence in the reliability and durability of their electronicponents in a wide range of operational environments.。
f8833
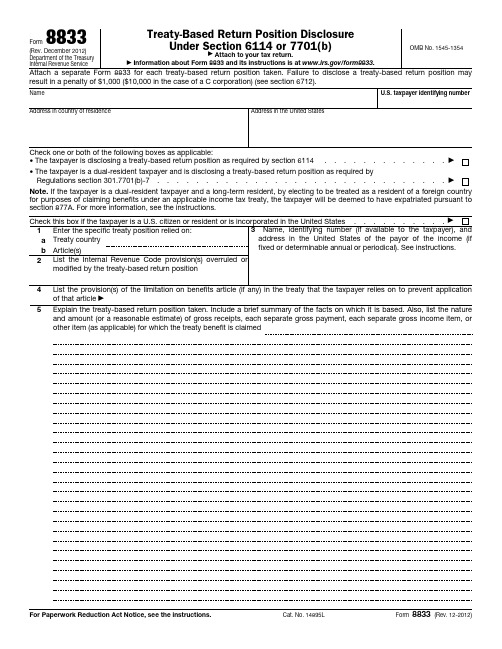
Who Must File
Generally, a taxpayer who takes a treaty-based return position must disclose that position. See Exceptions from reporting below.
A taxpayer takes a treaty-based return position by maintaining that a treaty of the United States overrules or modifies a provision of the Internal Revenue Code and thereby causes (or potentially causes) a reduction of tax on the taxpayer’s tax return. For these purposes, a treaty includes, but is not limited to, an income tax treaty; estate and gift tax treaty; or friendship, commerce, and navigation treaty. See Regulations sections 301.6114-1(a) and (b) for more details and for examples of treaty-based return positions taken by taxpayers for which they must make disclosure.
MIL-STD-883H change summary
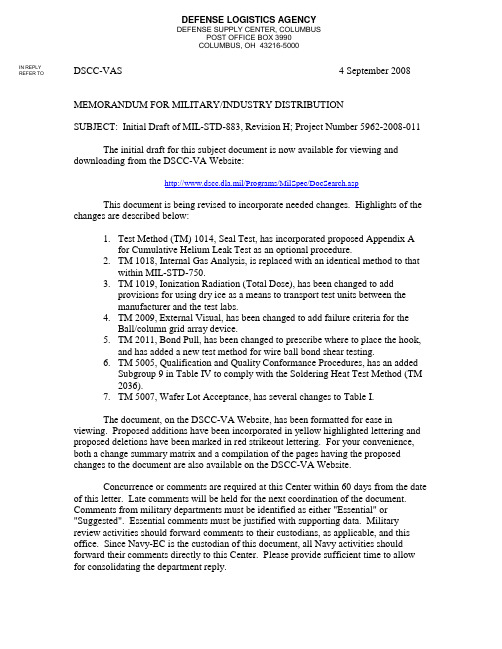
DSCC-VAS 4 September 2008MEMORANDUM FOR MILITARY/INDUSTRY DISTRIBUTIONSUBJECT: Initial Draft of MIL-STD-883, Revision H; Project Number 5962-2008-011 The initial draft for this subject document is now available for viewing and downloading from the DSCC-VA Website:/Programs/MilSpec/DocSearch.aspThis document is being revised to incorporate needed changes. Highlights of the changes are described below:1. Test Method (TM) 1014, Seal Test, has incorporated proposed Appendix A for Cumulative Helium Leak Test as an optional procedure.2. TM 1018, Internal Gas Analysis, is replaced with an identical method to that within MIL-STD-750.3. TM 1019, Ionization Radiation (Total Dose), has been changed to add provisions for using dry ice as a means to transport test units between the manufacturer and the test labs.4. TM 2009, External Visual, has been changed to add failure criteria for the Ball/column grid array device.5. TM 2011, Bond Pull, has been changed to prescribe where to place the hook, and has added a new test method for wire ball bond shear testing.6. TM 5005, Qualification and Quality Conformance Procedures, has an added Subgroup 9 in Table IV to comply with the Soldering Heat Test Method (TM 2036).7. TM 5007, Wafer Lot Acceptance, has several changes to Table I.The document, on the DSCC-VA Website, has been formatted for ease inviewing. Proposed additions have been incorporated in yellow highlighted lettering and proposed deletions have been marked in red strikeout lettering. For your convenience, both a change summary matrix and a compilation of the pages having the proposed changes to the document are also available on the DSCC-VA Website.Concurrence or comments are required at this Center within 60 days from the date of this letter. Late comments will be held for the next coordination of the document. Comments from military departments must be identified as either "Essential" or "Suggested". Essential comments must be justified with supporting data. Military review activities should forward comments to their custodians, as applicable, and this office. Since Navy-EC is the custodian of this document, all Navy activities should forward their comments directly to this Center. Please provide sufficient time to allow for consolidating the department reply.DEFENSE LOGISTICS AGENCYDEFENSE SUPPLY CENTER, COLUMBUSPOST OFFICE BOX 3990 COLUMBUS, OH 43216-5000IN REPLY REFER TOThe point of contact for this document is Mr. Joe Rodenbeck, Defense Supply Center Columbus, DSCC-VAS, Post Office Box 3990, Columbus, OH 43213-3990. Mr. Joe Rodenbeck can also be reached at 614-692-1090/850-1090, or by facsimile 614-692-6939/850-6939, or by e-mail to: joseph.rodenbeck@.\Signed\Robert M. HeberChiefTeamMicroelectronicscc:VQVSS2。
testo 883 热像仪数据表说明书

Thermal imagerYour helping hand:The testo 883 thermal imager.°CThe testo 883 thermal imager was developed especially for maintenance staff, facility managers and building energy consultants who wish to rely on the best thermal image quality and helpful features for their thermal measuring tasks. This saves time and ensures flawless work results.In facility management and maintenance, testo SiteRecognition technology really pays off. This feature automatically assigns thermal images (e.g. of switching cabinets) to the correct measurement object, thuseliminating the need for tedious manual image management.In building energy consulting, many experts appreciate the professional software testo IRSoft, which is included with the testo 883. With this, not only can thermal images be comprehensively analyzed, they can also be summarized in impressive-looking reports. This reduces the time required and makes it easier to impress customers over the long term.With professional software testo IRSoft%RHOrder datatesto ScaleAssistWith testo ScaleAssist, the correct evaluation ofconstruction errors and thermal bridges is easier than ever before. The function automatically sets the optimum thermal image scale. This prevents interpretation errors and makes infrared images comparable in spite of altered ambient conditions.AccessoriesOrder no.Telephoto lens 12° x 9°*Spare battery, additional Li-ion rechargeable battery for extending the operating time.0554 8831Battery-charging station, desktop charging station for optimizing the charge time.0554 8801Lens protection glass,Special germanium protective glass for optimum protection of the lens against dust or scratching0554 8805testo ε-marker (10 off), markers for the testo ε-Assist function for the automatic determination of emissivity and reflected temperature.0554 0872Emission tape. Adhesive tape e.g. for bare surfaces (roll, L.: 10 m, W.: 25 mm),ε = 0.95, temperature-resistant up to +250 °C0554 0051PC software testo IRSoft for analysis and reporting (free download)ISO calibration certificate, calibration points at 0 °C, +25 °C, +50 °C 0520 0489ISO calibration certificate, calibration points at 0 °C, +100 °C, +200 °C0520 0490ISO calibration certificate, freely selectable calibration points in the range -18 to +250 °C 0520 0495* Please contact our customer service.testo SiteRecognitionThe testo SiteRecognition technology ensures fully automatic measuring location recognition, along with storage and management of thermal images resulting from measurements or inspections. This saves you a lot of time and stress, particularly if you take a lot of pictures of similar measurement objects.Technical data 1 9 8 1 4 0 7 4 / m s p / I / 0 9 . 2 0 2 0。
Olympus NDT Harisonic Ultrasonic Transducer Catalo

• sAngle Beam Probe• sImmersion ProbeSpot Weld Transducrs••Roller Transducers•Pencil Transducers•Replaceable Delay DualElement Transducers920-127OLYMPUS NDTOlympus NDT is a leading global manufacturer of innovative nondestructive testing instruments that are used in industrial and research applications ranging from aerospace, energy, automotive,and electronics to manufacturing. Olympus NDT instruments contribute to the quality of products and add to the safety of infrastructure and facilities. They include flaw detectors, thickness gages, bond testers, pulser-receivers, transducers, and advanced systems for inline applications. Our leading edge technologies include ultrasound, ultrasound phased array, eddy current, and eddy current array.Olympus NDT offers products and servicesfrom several high quality brands: R/D Tech®, Panametrics-NDT™, NDT Engineering, Sonic®, and Nortec®. For many decades these brands have earned an excellent reputation for providing cost-effective solutions and excellent support and customer service.Based in Waltham, Massachusetts, USA, the company has sales and service centers in all principal industrial locations worldwide. Visit for applications and sales assistance near you.Harisonic TransducersHarisonic ultrasonic transducers are availablein thousands of different frequencies, element diameters, and connector sizes. In addition, we continue to manufacture transducers previously part of the Qualcorp/Automation Industries line as well as the Nortec transducer line. With more than40 years experience, Olympus NDT has developeda wide spectrum of transducers for both standard and specialized NDT applications.Tel: 781-419-3900 • 800-225-8330 in North America Fax: 781-419-3980*******************Part Number ConfigurationConnector StyleRU Right Angle UHF SU Straight UHFRMRight Angle MicrodotSMStraight MicrodotImmersionAngle BeamPart Numbering System LegendExample Part Number:The transducer is one of the most critical components of any ultrasonic system. A great deal of attention should be paid to selecting the proper transducer for the application.The performance of the system as a whole is of great importance. Variations in instrument characteristics and settings as well as material properties and coupling conditions play a major role in system performance.We have developed three different series of transducers to respond to the need for variety. Each series has its own unique characteristics.Transducer configuration also has an impact on system performance. Consideration should be given to the use of focused transducers, transducers with wear surfaces thatare appropriate for the test material, and the choice of the appropriate frequency and element diameter.The summaries below provide a general description of the performance characteristics of each transducer series. While these guidelines are quite useful, each application is unique and performance will be dependent on electronics, cabling, andtransducer configuration, frequency, and element diameter. Transducer Selection CriteriaHarisonic “P”type transducers are narrowband, lightlydamped, tuned transducers. They have high-energyoutput and penetrating power, but have limited resolvingpower.Harisonic “s” type transducers are mediumband, mediumdamped, tuned transducers. They are used for generalpurpose flaw detection, and represent a compromisebetween high sensitivity and high resolution.Test and DocumentationAll Olympus NDT transducers undergo a strict testing regime before they are deemed acceptable for use in the field. All tests are done in accordance with the ASTM E1065 Standard Guide for Evaluating Characteristics of Ultrasonic Search Units. As part of the test and documentation process, all transducers will automatically be shipped with a Real Time Waveform Spectrum(RTWFS) or Pulse Characterization and are given the option of further documentation at the time of order. In addition, optional flaw/resolution tests, axial beam profile and transverse beam profiles can also be done on certain types of transducers. Please consult us with any special testing requirements.Transverse Beam ProfilesThe optional Transverse Beam Profiles are typically done onimmersion transducers, and provide critical information on the transducer’s sound field. This test is performed at the measured focal length, along the X and Y axes. Beam width and symmetry are measured.Axial (On-Axis) Beam ProfileThe optional Axial or On-Axis Beam Profile is typically done onimmersion type transducers, and provides critical information about the transducer’s sound field. This test is performed with the transducer face starting close to the target and then moving away along the Z-axis. Pulse echo amplitude vs. distance, focal length, and depth of field are measured.Flaw Resolution TestThe optional Flaw Resolution Test certifies the resolving power of Harisonic ® transducers. This test is typically performed on immersion type transducers, with the target being specified by the customer. Near or far surface resolution can be measured.Transducer Analysis Report (Pulse Characterization)The Transducer Pulse Characterization data sheet is ourstandard documentation, and is provided with every Harisonic ® transducer, free of charge. The RF Waveform and Frequency Spectrum information is recorded and stored in our database, for future reference. Important parameters such as Peak and Center Frequency, Bandwidth, Pulse Voltage and Loop Gain are measured per ASTM E1065 guidelines.Immersion TransducersImmersion transducers are specifically designed to test parts partially or wholly immersed2.0 in..375 in.i-1 Dimensions 2.0 in.2.6 in..375 in.i-2 DimensionsUnfocused FocusedImmersion Transducersi-3 Style Housing0.25 inches (6mm), 0.375 inches (10 mm) and 0.50 inches (13 mm) element diameters in 0.63 inches (16 mm) housings with straight UHF connectors and 303 stainless steel case housings. If a focus is required, select a focal length between min. and max.T ype R High Resolution Point Target Focus(inches)0.63 in.1.73 in.i-R Style Housings0.50 inches (10 mm) element diameters in 0.75 inches(19 mm) x 0.75 inches (19 mm) rectangular housings with sidemount (right angle), UHF connectors, and 303 stainless steelcase housings are available..75 in..94 in..75 in.T ype RHigh ResolutionPoint Target Focus(inches)i-R DimensionsImmersion Transducersi-4, i-7 and i-8 Style HousingsVarious element and case sizes with straight UHF connectors and 303 stainlesssteel case housings are available.Styles i-4, i-7, and i-8Element Dia. (in)ASub-Miniature and Ultra-Miniature Angle Beam Transducers The sub-miniature (HS-225) and ultra-miniature (HS-877) angle beam transducers aresupplied in frequencies from 2.25 to 10.0 MHz with angles from 45° through 90°.Epoxy housings prevent the transducer from causing scratches to the test surface. Thesetransducers are ideal for inspection of small diameter welded tubes and applicationswhere the requirement is for a shear-wave transducer with a very small footprint.Depending on the type selected, either top or side mounted, Microdot connectors areavailable. When ordering, please specify part number, frequency, angle, material to beinspected, and connector location.Transducer Housing DimensionsSub-Miniature:0.375 in. L x 0.425 in. H x .0325 in. WSpecify material to be inspected.Integral Angle Beam TransducersMiniature potted angle beam transducers provide an excellent balance between size and performance by utilizing integral angle beam shear wave wedges. Overall size and footprint are reduced compared to a screw-in style transducer and wedge with little or no sacrifice in performance. Epoxy housings prevent test surface scratching caused by the transducer.Connectors are available in either top (straight) or side (right angle) mount depending on application requirements. Four standard shear wave angles of 45°, 60°, 70°, and 90° or custom angles are available upon request.AngleXX = Angle 45, 60, 70 or 90PAB-0203-XX -AL-SM PAB-0203-XX -AL-RM 0.30"0.30"0.55"0.55"0.675"0.675"Spot Weld TransducersThese transducer designs are popular for spot weld inspection. Each has distinctiveadvantages. Common features among these styles are small diameter (3 mm to 6 mm) and high frequency (10 MHz to 20 MHz).• s oft-tiP caPtive Water column – Optimum for spot welds with flash free, recessed/concave nuggets. The soft tip conforms to the irregular surface of the spot weld nugget. A lightweight liquid is required to transmit (couple) the ultrasonic energy into the nugget.• s oft-tiP caPtive Water column - Polymer transducers – Polymer transducers generallyare higher resolution transducers due to their greater bandwidth.Soft Tip Captive Water Column –Soft Tip Captive Water Column Roller TransducersRoller transducers are used in testing metallic or non-metallic materials for bonding/segregation in CFRP/GRP including Kevlar ®, rubber friction materials, and high density products such as glass, wood, concrete, and metallic and plastic weldments. This series includes roller and contact type transducers at 0.5 MHz and 1.25 MHz. Contact units are available in 5, 10, and 15 mm diameters, while the roller transducers incorporate a 5 mm crystal giving a 10 mm footprint through the replaceable tire. Both styles are fitted with axial mounted Microdot connectors (other connectors available on request). The roller transducer can be ordered with either a singleor dual yoke design.Roller TransducersRoller transducers are used in through transmission mode for fast linear scans ofparts without the need for an immersion setup. Roller transducers are typically used in applications looking for de-laminations in multilayer materials and are available ineither single or dual yoke design removable and replaceable tire.SINGLE YOKE DUAL YOKEFor hard-tip delay line transducers visit our website at:/ panametrics-ndt-ultrasonic/delay-line/Pencil TransducersThese high frequency, focused delay line transducers are compatible with any ultrasonic instrument capable ofdisplaying a return echo at depths as low as .010 inches in steel. The typical range is approximately from .010 inches to 0.250 inches in steel. The 0.060 inches circular contact face enables readings to be taken on curved surfaces. Typical applications for these transducers include the inspection of turbine blades, small diameter tubing and concave areas in small parts. Both transducers utilize replaceable delay tips. For best performance, a short cable (such as MB type, 6’) should be used. These models, indicated by a part number ending with an “L”, incorporate PowerLink™ Technology to assure optimal performance when used with a Sonic ultrasonic instrument.The HC-876 ultrasonic transducer operates at high frequency (20 MHz) with a broad bandwidth and small contact surface. Its chief application is thickness measuring of critical componentssuch as jet engine blades. It is fitted with a Microdot connector.Replaceable Delay LineReplacement Tips (10 m s)HAX-398HAX-398Permanent Delay LineHC-876-RA-LPermanent Tip Delay (10 m s) *Not PowerLink compatible..06 in..33 in..38 in.4.07 in.HC-398-RDL Straight Pencil Type.70 in..06 in..33 in..38"4.30 in.HC-398-RA-RDL Right Angle Type.70 in..06 in..12 in..38"4.30 in.HC-876-RA-L Right Angle Type.12 in..06 in..38 in.4.07 in.HC-876-L Straight Pencil Type.25 in..12 in..06 in..375 in.5.70 in.HC-876 Right Angle TypeHC-876-RA-L Right Angle TypeHC-398-RDL Straight Pencil TypeThe near field values in this table have been determined using the following equation:The minimum and maximum practical focal lengths have been calculated by considering the acoustic and mechanical limitations of each configuration. These limitations are a function of transducer frequency, element diameter, and case dimensions. There may be exceptions to the limits listed in the table.Technical NotesTable 2Near Field Distance of Flat Transducers in WaterFrequency Element Diameter N Focal Length (PTF)**Min Maxlong water paths are required the effects of frequency dependent attenuation should be checked per ASTME 1065, Annex A7. It is advisable to consider the effects of frequency dependent attenuation if the focal distance equals or exceeds the following values:Frequency Focal Length *******************Ol ympus NDT48 Woerd Avenue • Waltham, MA 02453 • USATel.: (1) 781-419-3900 • Fax: (1) 781-419-398012569 Gulf Freeway • Houston, TX 77034 • USATel.: (1) 281-922-9300 • Fax: (1) 952-487-8877Ol ympus NDT uK lTD.12 Nightingale Close • Rotherham, South Yorkshire S60 2AB • UKOl ympus siNgapOre pTe. lTD.491B River Valley Road 12-01/04, Valley Point Office Tower, 248373 • Singapore Ol ympus ausTralia pTy. lTD.。
MIL-STD-883GDIESHEARSTRENGTH-HighReliability…

METHOD 2019.7 07 March 2003 1METHOD 2019.7 DIE SHEAR STRENGTH1. PURPOSE. The purpose of this test is to determine the integrity of materials and procedures used to attach semiconductor die or surface mounted passive elements to package headers or other substrates. This determination is based on a measure of force applied to the die, the type of failure resulting from this application of force (if failure occurs) and the visual appearance of the residual die attach media and substrate/header metallization.2. APPARATUS. The test equipment shall consist of a load-applying instrument with an accuracy of ±5 percent of full scale or 50 grams, whichever is the greater tolerance. A circular dynamometer with a lever arm or a linear motion force- applying instrument may be used to apply the force required for testing. The test equipment shall have the following capabilities: a. A die contact tool which applies a uniform distribution of the force to an edge of the die (see figure 2019-1). A compliant (conforming) material (e.g., nail polish, tape, etc.) may be applied to the face of the contact tool to ensue uniform force distribution on the edge of the die. b. Provisions to assure that the die contact tool is perpendicular to the die mounting plane of the header or substrate. c. A rotational capability, relative to the header/substrate holding fixture and the die contact tool, to facilitate line contact on the edge of the die; i.e., the tool applying the force to the die shall contact the die edge from end-to-end (see figure 2019-2). d. A binocular microscope with magnification capabilities of 10X minimum and lighting which facilitates visual observation of the die and die contact tool interface during testing.3. PROCEDURE. The test shall be conducted, as defined herein, or to the test conditions specified in the applicable specific acquisition document consistent with the particular part construction. All die strength tests shall be counted and the specific sampling, acceptance, and added sample provisions shall be observed, as applicable. 3.1 Shear strength. A force sufficient to shear the die from its mounting or equal to twice the minimum specified shear strength (figure 2019-4), whichever occurs first, shall be applied to the die using the apparatus of 2 above. NOTE: For passive elements only attached at the end terminations, the area used to determine the force applied shall be the total area of the mounting surface of the end terminations. An area between and terminations filled with non-adhering filler shall not be used to determine the force applied. However, any adhering material applied between the end terminations shall be used in the shear calculation. If the area between end terminations contains an adhering material, then the area of the adhering material shall be added to the area of the mounting surfaces of the end terminations and that total area shall be used to determine the force applied. a. When a linear motion force-applying instrument is used, the direction of the applied force shall be parallel with the plane of the header or substrate and perpendicular to the die being tested. b. When a circular dynamometer with a lever arm is employed to apply the force required for testing, it shall be pivoted about the lever arm axis and the motion shall be parallel with the plane of the header or substrate and perpendicular to the edge of the die being tested. The contact tooling attached to the lever arm shall be at a proper distance to assure an accurate value of applied force. c. The die contact tool shall apply a force gradually from zero to a specified value against an edge of the die whichmost closely approximates a 90° angle with the base of the header or substrate to which it is bonded (see figure 2019-3). For rectangular die, the force shall be applied perpendicular to the longer side of the die. When constrained by package configurations, any available side of the die may be tested if the above options are not available. d. After initial contact with the die edge and during the application of force, the relative position of the contact tool shall not move vertically such that contact is made with the header/substrate or die attach media. If the tool rides over the die, a new die may be substituted or the die may be repositioned, provided that the requirements of 3.1.c are met.METHOD 2019.7 07 March 2003 23.2 Failure criteria. A device which fails any of the following criteria shall constitute a failure.NOTE: (See examples for determining DIE AREA following figure 2019-4.)3.2.1 Epoxy attach.a. Fails die strength requirements (1.0X) of Figure 2019-4.b. Separation with less than 2.0 times the minimum strength (1.0X) specified in Figure 2019-4 and evidence of less than 75 percent adhesion of the attach medium to the intended area on the substrate, element or combination of both. NOTE: Residual element material (silicon or other) attached in discrete areas of the die attach medium shall be considered as evidenced of adhesion.3.2.2 Eutectic, solder, and other attach. a. Fails die strength requirements (1.0X) of Figure 2019-4.b. Separation with less than 1.25 times the minimum strength in Figure 2019-4 and evidence of less than 50 percent adhesion of the die attach medium.c. Separation with less than 2.0 times the minimum strength (1.0X) specified in figure 2019-4 and evidence of less than 10 percent of adhesion of the die attach medium.NOTE: Residual element material (silicon or other) attached in discrete areas of the die attach medium shall be considered as evidence of adhesion. For metal glass die attach, die attach material on the die and on the package base shall be considered as evidence of acceptable adhesion.3.2.3 Separation categories. When specified, the force required to achieve separation and the category of the separation shall be recorded.a. Shearing of die with residual silicon remaining.b. Separation of die from die attach medium.c. Separation of die and die attach medium from package.4. SUMMARY. The following details shall be specified in the applicable acquisition document.a. Minimum die attach strength if other than shown on figure 2019-4.b. Number of devices to be tested and the acceptance criteria.c. Requirement for data recording, when applicable (see 3.2.1).*******METHOD 2019.7 07 March 2003 3FIGURE 2019-1. Compliant interface on contact tool distributes load to the irregular edge of the die.FIGURE 2019-2. Rotate the die contact tool or the device for parallel alignment.FIGURE 2019-3. The contact tool shall load against that edgeof the die which forms an angle ≈ 90° with the header/substrate.METHOD 2019.7 07 March 20034NOTES: 1. All die area larger than 64 x 10-4 (IN)2 shall withstand a minimum force of 2.5 kg or a multiple there of (see 3.2). 2. All die area larger than or equal to 5 x 10-4 (IN)2 but smaller than or equal to 64 x 10-4 (IN)2 shall withstand a minimum force as determined from the chart of Figure 2019.4. The chart is based on a force of 0.04 kg for every one ten-thousandth (10-4) square inch at (1X) level. Similarly, the required minimum force is 0.05 kg for every 10-4 IN 2 at (1.25X) level and is 0.08 kg for every 10-4 IN 2 at (2X) level . 3. All die area smaller than 5 x 10-4 (IN)2 shall withstand a minimum force (1.0X) of 0.04 kg/10-4 (IN)2 or a minimum force (2X) of 0.08 kg/10-4 (IN)2. FIGURE 2019-4. Die shear strength criteria (minimum force versus die attach area).DIE AREA (10-4 IN 2) *METHOD 2019.7 07 March 2003 5 Examples of determining die strength requirements based on die area. Example 1: Die Area of device measuring .02 inches by .02 inches. Die Size = .02 X .02 = .0004 IN 2 = 4 X 10-4 (IN 2). Because die size is less than 5 X 10-4 (IN 2) use Note 3 which states the value of minimum force required is 0.04 kg/10-4 (IN 2) at (1X), 0.05 kg/10-4 (IN 2) at (1.25X), or 0.08 kg/10-4 (IN 2) at (2X). Thus the associated minimum forces required are 0.16 kg, 0.20 kg and 0.32 kg, respectively. Example 2: Die Area of device measuring .04 inches by 0.04 inches. Die Size = .04 X .04 = .0016 IN 2 = 16 X 10-4 (IN 2 ). Because die size is between 5 X 10-4 (IN 2) and 64 X 10-4 (IN 2 ) use Note 2 which states the value of minimum force required is to be determined based on the chart. The values for die size 16 X 10-4 (IN 2) are found on the chart by reading 16 on the (10-4 IN 2) scale, then finding the coordinating force value on the (F) scale. Doing so provides minimum forces required as .64 kg at (1X), .80 kg at (1.25X), and 1.28 kg at (2X). Alternately: The chart is based on using 4 kg/10-4 (IN 2) at (1X), 5 kg/10-4 (IN 2) at (1.25X), and 8 kg/10-4 (IN 2) at (2X). Thus: the minimum forces required are 16 X 4 = 64 Kg (1X), 16 X 5 = 80 kg (1.25X), and 16 X 8 = 128 kg (2X) Example 3: Die Area of device measuring .09 inches by .09 inches. Die Size = .09 X .09 = .0081 IN 2 = 81 X 10-4 (IN 2). Because die size is larger than 64 X 10-4 (IN 2) use Note 1 which states the value of minimum force required is 2.5 kg or a multiple thereof. Therefore, the minimum forces required are 2.5 kg at (1X), 3.125 kg at (1.25X), and 5.0 kg at (2X).*。
Dose_Response_and_FWHM_Properties_of_Dyed_Poly_Vin
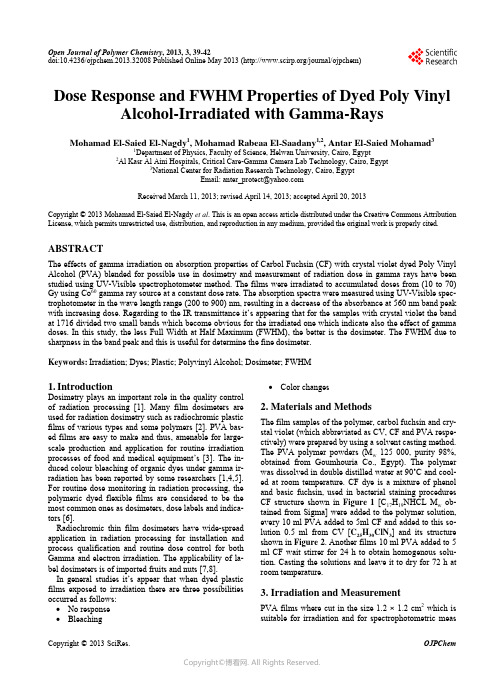
Open Journal of Polymer Chemistry, 2013, 3, 39-42doi:10.4236/ojpchem.2013.32008 Published Online May 2013 (/journal/ojpchem)Dose Response and FWHM Properties of Dyed Poly Vinyl Alcohol-Irradiated with Gamma-RaysMohamad El-Saied El-Nagdy1, Mohamad Rabeaa El-Saadany1,2, Antar El-Saied Mohamad31Department of Physics, Faculty of Science, Helwan University, Cairo, Egypt2Al Kasr Al Aini Hospitals, Critical Care-Gamma Camera Lab Technology, Cairo, Egypt3National Center for Radiation Research Technology, Cairo, EgyptReceived March 11, 2013; revised April 14, 2013; accepted April 20,2013Copyright © 2013 Mohamad El-Saied El-Nagdy et al. This is an open access article distributed under the Creative Commons Attribution License, which permits unrestricted use, distribution, and reproduction in any medium, provided the original work is properly cited.ABSTRACTThe effects of gamma irradiation on absorption properties of Carbol Fuchsin (CF) with crystal violet dyed Poly Vinyl Alcohol (PVA) blended for possible use in dosimetry and measurement of radiation dose in gamma rays have been studied using UV-Visible spectrophotometer method. The films were irradiated to accumulated doses from (10 to 70) Gy using Co60 gamma ray source at a constant dose rate. The absorption spectra were measured using UV-Visible spec- trophotometer in the wave length range (200 to 900) nm, resulting in a decrease of the absorbance at 560 nm band peak with increasing dose. Regarding to the IR transmittance it’s appearing that for the samples with crystal violet the band at 1716 divided two small bands which become obvious for the irradiated one which indicate also the effect of gamma doses. In this study, the less Full Width at Half Maximum (FWHM), the better is the dosimeter. The FWHM due to sharpness in the band peak and this is useful for determine the fine dosimeter.Keywords: Irradiation; Dyes; Plastic; Polyvinyl Alcohol; Dosimeter; FWHM1. IntroductionDosimetry plays an important role in the quality control of radiation processing [1]. Many film dosimeters are used for radiation dosimetry such as radiochromic plastic films of various types and some polymers [2]. PVA bas- ed films are easy to make and thus, amenable for large- scale production and application for routine irradiation processes of food and medical equipment’s [3]. The in- duced colour bleaching of organic dyes under gamma ir- radiation has been reported by some researchers [1,4,5]. For routine dose monitoring in radiation processing, the polymeric dyed flexible films are considered to be the most common ones as dosimeters, dose labels and indica- tors [6].Radiochromic thin film dosimeters have wide-spread application in radiation processing for installation and process qualification and routine dose control for both Gamma and electron irradiation. The applicability of la- bel dosimeters is of imported fruits and nuts [7,8].In general studies it’s appear that when dyed plastic films exposed to irradiation there are three possibilities occurred as follows:∙No response∙Bleaching∙Color changes2. Materials and MethodsThe film samples of the polymer, carbol fuchsin and cry- stal violet (which abbreviated as CV, CF and PVA respe- ctively) were prepared by using a solvent casting method. The PVA polymer powders (M w 125 000, purity 98%, obtained from Goumhouria Co., Egypt). The polymer was dissolved in double distilled water at 90˚C and cool- ed at room temperature. CF dye is a mixture of phenol and basic fuchsin, used in bacterial staining procedures CF structure shown in Figure 1[C17H19NHCL M w ob- tained from Sigma] were added to the polymer solution, every 10 ml PVA added to 5ml CF and added to this so- lution 0.5 ml from CV[C25H30ClN3] and its structure shown in Figure 2. Another films 10 ml PVA added to 5 ml CF wait stirrer for 24 h to obtain homogenous solu- tion. Casting the solutions and leave it to dry for 72 h at room temperature.3. Irradiation and MeasurementPVA films where cut in the size 1.2 × 1.2 cm2 which is suitable for irradiation and for spectrophotometric measM. E. EL-NAGDY ET AL. 40Figure 1. Carbol fuchsin structure.Figure 2. Crystal violet structure.urements (film holder). This films where irradiation in the central position of cobalt-60, 20 × 20 cm located at Oncology department Al-Kasr Alini hospital—Egypt. The films set in the phantom at depth 4.4 cm Perspex(tissue equivalent) 5 cm in water,the distance between source and skin sample SSD = 80 cm (The source to surface di- stance) d = depth = 5 cm.Using a standard geometry to minimize the errors in- troduced during irradiation dose rate of gamma source was 133.6 Gy/hr.Films were exposed to different doses (10, 20, 30, 40, 50, 60 and 70) Gy at room temperature. The thickness of the films was measured at 5 randomly selected places with thickness gauge having an accuracy of ± 1 m. The average thickness of the films was found to be 0.04 ± 0.06 mm. The absorption spectra of the unirra- diated and irradiated films were measured in the wave- length range 200 - 900 nm using Evolution 600 UV-Vis spectrophotometer.4. Results and DiscussionAbsorption SpectraIn the current work, dyed films of poly(vinyl alcohol) prepared by casting aqueous solutions of PVA containing carbol fuchsin and crystal violet on glass plate, are inves- tigated to be used as dosimeters for radiation processing. These flexible plastic film dosimeters ((CF + CV)/PVA) are bleached when exposed to gamma ray photons. The absorption spectrum of the unirradiated and irradiated films shows a main absorption band in the visible region peaking at 560 nm (Figures3 and 4).The dose-response functions in terms of net absorb- ance change, (ΔA = A0− A i), as a function of absorbed dose, where A o and A i are the absorbance’s at 560 nm of the unirradiated and irradiated ((CF + CV)/PVA) films are shown in Figure5.From this figure it can be seen that the figure is linear for all the dose range, so this dose range can choose to be a useful dose range for this do- simeter. It can be seen from Figures 3 and 4 that the bleaching occur but the degree of bleaching for the films containing CV + CF is less than the films containing CF only by 10% comparing the first dose and the last dose for the two systems, this will be investigated in a large scale in the next paragraph.3004005006007008000.60.81.01.21.41.61.82.02.212345(G y)7=608=701=02=104=306=505=40Absorbancew avelength (nm)3=20678D oseFigure 3. UV/Vis spectra of polyvinyl alcohol + CF films for concentration 5 ml at different gamma doses (0, 10, 20, 30, 40, 50, 60 and 70) Gy.3004005006007008000.00.51.01.52.012345678(G y)D o s e8=703=206=505=407=604=301=0AbsorbanceW a ve le n g th (n m)2=10Figure 4. UV/Vis spectra of polyvinyl alcohol + (CF/Crystal Violet) films. Irradiated by gamma rays at different doses (0, 10, 20, 30, 40, 50, 60 and 70) Gy.M. E. EL-NAGDY ET AL . 41C h a n g e i n A b s o r b a n c eD o se (G y)Figure 5. Plot of absorbance of (CF + CV)PVA film at λ = 560 nm versus γ-irradiation dose in Gy.5. FWHM for PVA/CF and (PVA/CF + CV)Figure 6 shows the full width at half maximum (FWHM) for PVA (CF) and PVA(CF + CV) with different gamma doses all data are estimated by using origin pro 8 pro- gram and the data obtained from UV spectra. We study the behavior of the band at 560 nm at different doses for the blended films and estimate the FWHM. It appears from Figures 3 and 4 that when the films exposed to different doses the color of the films gradually bleaching we can not see the color with naked eye. In this case it can be used the variation of FWHM as inference group to different absorbed doses in range (0 to 70 Gy), for exam- ple when exposure some films to different doses and the calculation of the FWHM of each and hence alone can determine which films exposed to high or low doses. FWHM is the way to determine the difference between absorbed doses, but was unable to determine the amount of dose. FWHM in case of carbol fuchsin is (104, 95, 90 nm) at 560 nm according to (30, 50, 70 Gy) respectivelyand FWHM in case carbol fuchsin with Crystal Violet is (80, 78, 62 nm) at 560 nm according to (30, 50, 70 Gy) respectively. We noticed in the previous section that the FWHM in the Case CF + CV films less than FWHM in the Case CF only; this is improvement to the situation ofthe curve. FWHM depend on absorbed dose, the narrow FWHM gives the best peak this is due to Accuracy in de-termining the wavelength, so the addition of crystal vio- let play an important role for this dosimeter in which it decrease the bleaching rate of the dosimeter and increase its stability.6. FT-IR for PVA/CF and (PVA/CF + CV)Figure 7 shows the IR for the unirradiated and irradiated films and study the change of the addition of the crystal vio- let to these films, these changes are mainly represented60708090100110F W H M n mD o s e (G y )Figure 6. FWHM at 30, 40, 50 Gy for PVA + CF and PVA + (CF + CV) films.Figure 7. FTIR for unirradiated and irradiated films.by the appearance of three absorption bands, the first at about 3500 cm −1 which is attributed to the formation of -OH groups, the second at 1716 cm −1 which is attributed to the stretching vibration of ketonic carbonyl groups and the third at 1180 cm −1 which is probably due to the -C-O- absorption of the peroxide cross-links [9,10] .It appears the effects of the addiation of crystal violet to the original films which indicates that the important role for that dye in which its increase the stability of the films which lead to the stretching or sharpness of the band as shown in Figure 5. From the IR transmittance figure it appears that for the samples with crystal violet the band at 960 cm −1 the divided two small bands which become obvious for the irradiated one which indicate also the effect of gamma doses. The broadening at 1816 cm −1 also reflects the effect of gamma and crystal violet for the host polymer.M. E. EL-NAGDY ET AL. 427. ConclusionIn this study, the poly vinyl alcohol based films contain- ing carbol fuchsin and crystal violet dyes after irradiation with gamma raye that radiation induced bletching of these films can be used for dosimetry when this films ex- posed to accumulated doses from (10 to 70 Gy) in wave length range (200 to 900) showed an absorption band at 560 nm. The fitting of the dose-response curves y = ax + b resulted in a linear relationship between dose and net absorbance change. The full width at half maximum (FWHM) in two films which decreased with increasing doses due to sharpness in the band peak. The FWHM can be used to determine any films exposed to high doses and it is used for determining the better dosimeter. Smaller FWHM value resolution enables the system to more clearly separate the peaks within a spectrum.REFERENCES[1]W. L. McLaughlin, A. W. Boyd, K. H. Chadwick, J. C.McDonald and A. Miller, “Dosimetry for Radiation Proc-essing,” Taylor & Francis, New York, 1989.[2]M. Kattan, Y. Daher and H. Alkassiri, “A High-Dose Do-simeter-Based Polyvinyl Chloride Dyed with Malachite Green,” Radiation Physics and Chemistry, Vol. 76, No. 7,1989, pp. 1195-1199.doi:10.1016/j.radphyschem.2006.12.004[3]N. V. Bhat, M. M. Nate, R. M. Bhat and B. C. Bhatt,“Effect of Gamma Radiation on PVA Films Doped with Some Dyes and Their Use in Dosimetric Studies,” IndianJournal of Pure & Applied physics, Vol. 45, No. 6, 2007,pp. 545-548.[4]W. L. McLaughlin, N. W. Holm and R. J. Berry, “Films,Dyes and Photographic Systems, Manual on Radiation Dosimetry,” Marcel Decker, New York, 1970.[5] A. Miller, “Dosimetry for Radiation Processing,” Radia-tion Physics and Chemistry, Vol. 28, No. 5-6, 1986, p.321.[6]S. Ebraheem, W. B. Beshir and S. Eid, “Investigation ofDyed Film Based on 2,6Dichlorophenol-Indophenol Dy- ed Poly (Vinyl Alcohol) and Poly (Vinyl Butyral) for Possible Use in High-Dose Processing Dosimetry,” Arab Journal of Nuclear Science and Applications, Vol. 38, No.1, 2005, p. 1.[7]S. Ebraheem, W. B. Beshir, S. Eid and A. Kovacs, “Spec-trophotometric Readout for an Alanine Dosimeter for Food Irradiation Applications,” Radiation Physics and Chemis- try, Vol. 67, No. 3-4, 2003, pp. 569-573.doi:10.1016/S0969-806X(03)00107-5[8]S. Ebraheem, S. Eid and A. Kovacs, “A New Dyed Poly(Vinyl Alcohol) Film for High-Dose Applications,” Ra- diation Physics and Chemistry, Vol. 63, No. 3-6, 2002, pp.807-811. doi:10.1016/S0969-806X(01)00663-6[9] D. J. Carlsson, C. J. Dobbin and D. M. Wiles, “Direct Ob-servations of Macroperoxy Radical Propagation and Ter- mination by Electron Spin Resonance and Infrared,” Mac- romolecules, Vol. 18, No. 10, 1985, p. 2092.doi:10.1021/ma00152a053[10]J. Lacoste, D. V. Aillant and D. J. Carlsson, “Gamma, Pho-to and Thermally Initiated Oxidation of Isotactic Polypro- pylene,” Journal of Polymer Science and Part A: Polymer Chemistry, Vol. 31, No. 3, 1993, p. 715.。
ASTM E883_2002

Designation:E 883–02Standard Guide forReflected–Light Photomicrography 1This standard is issued under the fixed designation E 883;the number immediately following the designation indicates the year of original adoption or,in the case of revision,the year of last revision.A number in parentheses indicates the year of last reapproval.A superscript epsilon (e )indicates an editorial change since the last revision or reapproval.1.Scope1.1This guide outlines various methods which may be followed in the photography of metals and materials with the reflected-light microscope.Methods are included for prepara-tion of prints and transparencies in black-and-white and in color,using both direct rapid and wet processes.1.2Guidelines are suggested to yield photomicrographs of typical subjects and,to the extent possible,of atypical subjects as rmation is included concerning techniques for the enhanced display of specific material features.Descriptive material is provided where necessary to clarify procedures.References are cited where detailed descriptions may be helpful.1.3This standard does not purport to address all of the safety concerns,if any,associated with its use.It is the responsibility of the user of this standard to establish appro-priate safety and health practices and determine the applica-bility of regulatory requirements prior to use.Specific precau-tionary statements are given in X1.7.1.4The sections appear in the following order:Referenced documents 2Terminology3Significance and use 4Magnification5Reproduction of photomicrographs 6Optical systems 7Illumination sources8Illumination of specimens 9Focusing10Filters for photomicrography 11Illumination techniques 12Instant-processing films 13Photographic materials 14Photographic exposure 15Photographic processing 16Keywords17Suggestions for visual use of metallographic microscopes X1Guide for metallographic photomacrography X2Electronic photographyX32.Referenced Documents 2.1ASTM Standards:E 3Methods of Preparation of Metallographic Specimens 2E 7Terminology Relating to Metallography 2E 175Terminology of Microscopy 3E 768Practice for Preparing and Evaluating Specimens for Automatic Inclusion Assessment of Steel 2E 1951Guide for Calibrating Reticles and Light Micro-scope Magnifications 23.Terminology3.1Definitions —For definitions of terms used in this guide,see Terminologies E 7and E 175.4.Significance and Use4.1This guide is useful for the photomicrography and photomacrography of metals and other materials.4.2The subsequent processing of the photographic materi-als is also treated.5.Magnification5.1Photomicrographs shall be made at preferred magnifi-cations,except in those special cases where details of the microstructure are best revealed by unique magnifications.5.2The preferred magnifications for photomicrographs,are:253,503,753,1003,2003,2503,4003,5003,7503,8003,and 10003.5.3Magnifications are normally calibrated using a stage micrometer.Calibration procedures in Guide E 1951should be followed.6.Reproduction of Photomicrographs6.1Photomicrographs should be at one of the preferred magnifications.A milli-or micrometre marker shall be super-imposed on the photomicrograph to indicate magnification,in a contrasting tone.The published magnification,if known,should be stated in the caption.6.2Photomicrograph captions should include basic back-ground information (for example,material identification,etchant,mechanical or thermal treatment details)and should briefly describe what is illustrated so that the photomicrograph can stand independent of the text.6.3Arrows or other markings,in a contrasting tone,shall be used to designate specific features in a photomicrograph.Any marking used shall be referenced in the caption.1This guide is under the jurisdiction of ASTM Committee E04on Metallogra-phyand is the direct responsibility of Subcommittee E04.03on Light Microscopy.Current edition approved Nov 10,2002.Published April 2003.Originally published as E 883–st previous edition E 883–99.2Annual Book of ASTM Standards,V ol 03.01.3Annual Book of ASTM Standards,V ol 14.02.1Copyright ©ASTM International,100Barr Harbor Drive,PO Box C700,West Conshohocken,PA 19428-2959,United States.Copyright ASTM InternationalProvided by IHS under license with ASTMNot for ResaleNo reproduction or networking permitted without license from IHS--`-`-`,,`,,`,`,,`---7.Optical Systems7.1Microscope objectives are available in increasing order of correction as achromats,semiapochromats (fluorites)and apochromats (see Terminologies E 7and E 175).Plan objec-tives are recommended for photographic purposes because their correction provides a flatter image.The objective lens forms an image of the specimen in a specific plane behind the objective called the back focal plane.(This is one of several possible real image planes,called intermediary planes,where reticles may be inserted as optical overlays on the image.)7.2The eyepiece magnifies the back focal plane (or other)intermediary image for observation or photomicrography.Eye-pieces are sometimes also used to accomplish the full correc-tion of the objective’s spherical aberration and to improve the flatness of field.7.2.1The pupil of the observer’s eye must be brought to coincidence with the eyepoint of the visual eyepiece to view the entire microscopical image.High-eyepoint eyepieces are necessary for eyeglass users to see the entire image field.7.2.2Most microscopes have built-in photographic capa-bilities that use an alternate image path through the microscope leading to a camera attachment port or to a viewscreen.A projection eyepiece delivers the image to the camera port or screen.7.3Intermediate lenses (relay or tube lenses)are often required to transfer the specimen image from the intermediary plane of the objective to that of the eyepiece.They may also add their own magnification factor,either fixed or as a zoom system.7.4The objective,the eyepiece,and the compound micro-scope (including any intermediate lenses)are designed as a single optical unit.It is recommended to use only objectives and eyepieces which are intended for the microscope in use.7.5The resolution of the microscope depends primarily on the numerical aperture of the objective in use (1)4.The term empty magnification is used to describe high magnifications (above approximately 1100times the numerical aperture of an objective),which have been shown to offer no increase in image resolution.Nevertheless,some types of information,such as the distance between two constituents,may be more easily obtained from microstructures examined at moderate empty magnifications.8.Illumination Sources8.1Metallographic photomicrography typically uses Köhler illumination.To obtain Köhler illumination,an image of the field diaphragm is focused in the specimen plane,and an image of the lamp filament or arc is focused in the plane of the aperture diaphragm.Specific steps to obtain Köhler illumina-tion vary with the microscope used.The manufacturer’s instructions should be followed closely.8.2For incandescent lamps,the applied voltage determines the unit brightness and the color temperature of the source.Evaporated tungsten blackens the envelope,resulting in dimin-ished brightness and color temperature as the lamp ages.Tungsten-halogen lamps minimize envelope blackening,main-taining constant brightness and color temperature for most of their life.The high brightness and 3200K color temperature of these lamps makes them especially suitable for color photomi-crography.8.3With arc sources,brightness per unit area is substan-tially higher than that from any incandescent source.Their spectral output contains high energy spikes superimposed on a white-light continuum.They also contain significant ultraviolet (UV)and infrared (IR)emissions that should be removed for eye safety (and for photographic consistency,with UV);see 8.4,11.3.1,and 11.5.2.8.3.1Xenon arcs produce a spectral quality close to daylight (5600K),with a strong spike at 462nm.Strong emissions in the IR should be removed.Xenon arcs that do not produce ozone are recommended.8.3.2Carbon arcs have a continuous output in the visible portion of the spectrum,with a color temperature near 3800K and a strong emission line at 386nm.8.3.3Mercury arcs have strong UV and near-UV output,and are particularly useful to obtain maximum resolution with a blue filter.The color quality is deficient in red;it cannot be balanced for color photomicrography.8.3.4Zirconium arcs have strong spectral output lines in the near IR,requiring filtration.Within the visible region,they are rated at 3200K color temperature.8.4Arc lamps require heat protection for filters and other optical components,and certainly for eye safety.Infrared removal may be obtained by:“hot”mirrors in the illumination beam to reflect IR while transmitting visible light;heat-absorbing filters to transmit visible light while absorbing IR,for example,solid glass filters or liquid-filled cells.8.5A detailed discussion of illumination sources and the quality of illuminants is given by Loveland (2).8.6Some advice on using metallographic microscopes for visual observation has been compiled in Appendix X1.9.Illumination of Specimens9.1Photomicrographs are made with a compound micro-scope comprised at least of an objective lens and an eyepiece with a vertical illuminator between them.Field and aperture diaphragms,with a lamp and lamp condenser lenses,are integral parts of the system.The microscope should allow sufficient adjustment to illuminate the field of view evenly and to completely fill the back aperture of the objective lens with light.9.2The vertical illuminator is a thin-film-coated plane glass reflector set at 45°to the optical axis behind the objective.It reflects the illumination beam into the objective and transmits the image beam from the objective to the eyepiece.In some microscopes prism systems are used to perform this function.9.3The field diaphragm is an adjustable aperture which restricts the illuminated area of the specimen to that which is to be photographed.It eliminates contrast-reducing stray light.The field diaphragm is also a useful target when focusing a low-contrast specimen.9.4The aperture diaphragm establishes the optimum bal-ance between contrast,resolution,and depth of field.It should be set to illuminate about 70%of the objective’s aperture4The boldface numbers in parentheses refer to the list of references at the end of this standard.diameter.This can be observed by removing the eyepiece and inspecting the back of the objective,either directly or with a pinhole eyepiece.The aperture diaphragm should never be used as a light intensity control.9.5See Fig.1for an illustration of a typical vertical illumination system.10.Focusing10.1Sharp focus is necessary to obtain good photomicro-graphs.10.2There are two systems for obtaining sharp focus:ground-glass focusing and aerial image focusing.10.2.1For ground-glass focusing,relatively glare-free sur-roundings and a magnifier up to about 33are required.To focus,the focusing knob is oscillated between underfocus and overfocus in succeedingly smaller increments until the image is sharp.10.2.2There are four possible variations for focusing an aerial image.10.2.2.1The simplest case is a transparent spot on a ground-glass containing a fiduciary mark in the film plane.The specimen image is focused to coincide with the fiduciary mark,using a magnifying loupe of about 33to 53.When the focus is correct,the specimen image and the fiduciary mark will not move with respect to each other when the operator’s head is moved.10.2.2.2A second case uses a reticle fixed within the optical system at an intermediary plane.Focusing is a two-step process:focus the eyepiece on the reticle;bring the image into focus against the reticle figure.10.2.2.3In the third case,a reticle is inserted into a focusing eyepiece.Depending on equipment used,this can be either a two or three-step process:focus the reticle within the eyepiece;next,set the proper interpupiliary distance,if required (some equipment requires a specific interpupiliary distance for eye-piece focus to coincide with camera focus);then focus the image coincident with the reticle.10.2.2.4The fourth case uses a single-lens reflex camera body,where the camera focusing screen is the plane ofreference.An eyepiece magnifier for the camera is animpor-tant accessory for this case.An aerial image focusing screen is preferred.10.3The critical focus point is affected by both the principal illumination wavelength in use and the size of the aperture diaphragm.Final focusing should be checked with all filters,apertures,and other components set for the photomicrograph.11.Filters for Photomicrography11.1Photomicrographs require filtration of the light source.This section describes filter types and their uses.11.2Each filter selectively removes some wavelengths from the transmitted beam of light.Two types of filters,interference and absorption,can be used for this purpose.11.2.1Interference filters act as selective mirrors.By means of coatings on a glass substrate,they selectively transmit certain wavelengths while reflecting all others.These filters may be used in high-energy light beams.The mirrored side of the filter should face the light source.(The hot mirrors in 8.4are interference filters.)11.2.2Absorption filters are dyed substrates of glass,plas-tic,or gelatine.They absorb some wavelengths of light and transmit the balance.Through their absorption,they can become overheated and damaged if placed in high-energy light beams without protection.The usual protection is either an interference filter or a liquid-filled cell placed in the beam before the absorption filter.Wratten gelatine filters are used below as examples (3).Many similar glass and plastic filters are also available.11.3Certain general purpose filters have application in both color and black-and-white photomicrography.11.3.1Ultraviolet light can be removed with an interference filter,a glass or gel filter from the Wratten #2series,or a liquid cell filled with a sodium nitrite solution (2%NaNO 2is used for a 1-cm path.It should be proportionately stronger or weaker for other cell path lengths).Ultraviolet light must be removed from arc lamps for eye safety,and should be removed for color photomicrography,as explained in 11.5.2.FIG.1Vertical Illuminating System for a Metallurgical Microscope11.3.2Gray neutral density filters reduce the intensity of a light beam equally across the visible spectrum.They are made in interference and absorption types in many different densi-ties,for example,the Wratten #96series.They are useful for eyepiece work with an arc source,and to modify the brightness of any tungsten source without changing its color temperature.11.4Filters for Black and White Photomicrography :11.4.1Generally,a monochromatic filter is used to optimize the resolution of the objective.With achromats,a green centered around 550nm is used;for apochromats and semi-apochromats,a blue centered around 486nm provides slightly better resolution,but with a penalty of more difficult visual focusing.11.4.2Cases arise where the visual contrast can be im-proved to emphasize a colored feature in the microstructure.The color will reproduce darker in the photomicrograph if a filter is used with a color complementary to that of the feature (for example,a cyan filter for reddish copper plating;a blue for yellow carbonitride particles).When maximum detail in a colored phase must be shown,choose a filter with the same color as the phase.11.5Filters for Color Photomicrography :11.5.1Color photomicrography generally requires filtration to balance the light at the image plane to the color temperature specified by the film’s manufacturer.Most transparency and negative color films are balanced for use with daylight at 5600K.Some films are balanced for tungsten source lighting at either 3200K or 3400K.11.5.2Color films record ultraviolet light as blue.Since different metals reflect varying amounts of ultraviolet light,the simplest solution is to remove all ultraviolet light,as in 11.3.1,and rebalance by adding compensatory blue filters.11.5.3Table 1lists filter recommendations appropriate for color photomicrography.These include strong conversion fil-ters (the blue 80series and the orange-yellow 85series)and weaker light-balancing filters (the yellow 81series and the blue 82series).Because of individual variations in equipment and other filtration (for example,IR and UV removal),some fine tuning is usually required with color correction filters .These filters are commonly used in color printing,and are available in sets containing various strengths of red,yellow,green,cyan,blue,and magenta.11.5.4The correct color balance for any color film can be determined using a first-surface mirror as the specimen (see Note 1).After the recommended filtration from Table 1has been inserted,a series of test exposures of the mirror is made with several color correction filters,until a neutral gray result is obtained.(Because of differences in manufacturing,differentfilms with the same color temperature ratings mayrequire slightly different groups of filters to achieve the correct color balance.)N OTE 1—It is important to have a standard to balance the effective illumination of the system to photographic neutrality.Aluminum is photographically neutral throughout the visible and UV wavelengths.A first-surface aluminum mirror can be used as a repeatable standard.(A protective chromium overcoating destroys the neutrality,but a thin silicon monoxide protective layer is acceptable.)12.Illumination Techniques12.1Metallographic specimens should be illuminated to reveal significant structural details with optimum contrast and resolution,and with sufficient brightness for accurate photo-graphic recording.12.2With bright field illumination,polished areas of the specimen that are perpendicular to the light path reflect incident vertical illumination back into the objective lens and appear bright (see 9.2and Fig.1).Features such as inclusions and etched grain boundaries have edges that are inclined to the polished surface and reflect light away from the objective lens,making them appear dark.12.3Oblique illumination is similar to bright field,but is nonspecular,with the light impinging on the specimen at an oblique angle to the optical axis.It is obtained by decentering the aperture diaphragm,or by tilting the specimen slightly (4).The technique is useful to enhance specimen surface relief and to determine if specific features are pits or projections,since shadows are cast by nonplanar features.Resolution decreases as the illumination is made more oblique.(It is important that the decentered diaphragm be completely imaged in the rear focal plane of the objective to keep the illumination reasonably uniform across the field.)12.4Dark field illumination is obtained by directing light to the specimen along the outside of the objective,blocking out the illumination passing through the lens.These outside rays are diverted onto the specimen plane obliquely by a conical reflector.No specular reflections enter the objective.Only features that are tilted with respect to the surface (for example,grain boundaries,pits,and inclusions)will reflect light into the objective.These features will appear bright against a dark background.Image contrast is higher in dark field illumination than in other modes and will frequently reveal specimen detail that would be completely obscured with other kinds of illumi-nation.12.5Polarized light reveals grain structure and twinning in metals with a hexagonal lattice structure,such as beryllium,tin,titanium and zinc.Polarized illumination is produced by optical components consisting of calcite prisms or Polaroid y filters.They selectively provide an image consisting of polar-ized light reflected from a specimen surface and scattered depolarized light from nonplanar surface features.Polarized light reacts differently when reflected from isotropic and anisotropic material lattices.For a cubic material,the micro-scope field appears dark because most of the light reflected from the specimen is absorbed by the system.With an anisotropic material,the plane polarized beam reflected from the specimen surface either becomes elliptically polarized or the polarization plane is rotated.In both cases,the system nowTABLE 1Suggested Filtration for Color PhotomicrographyFilm Color Balance Daylight 3200K3400K Light Source Wratten Filter NumberTungsten80A +82A 82A 82C Tungsten-halogen 80A None 82A Zirconium arc80A None 82A Carbon arc,4.5amp 80C81C 81A Carbon arc,10amp 82C +82C 81EF 81C Xenon arcNone85B85passes a portion of the reflected light through to the viewing system.Polarized light is also used with optically inactive cubic metals that are treated to produce an anisotropic surface film on the substrate.It is also useful to identify optically active inclusions and phases and in defining domains in ferromagnetic materials.12.6Sensitive Tint—Many metals and nonmetallic crystals are birefringent.Plane polarized light is reflected from them as elliptically polarized light,which has a component not extin-guished by the system.If a quartz or gypsum sensitive tintfilter (also known as a l compensator,a full-wave plate or a first-order compensator)is used,a magenta color is seen with cubic metals and all birefringent metals appear in vivid color contrasts.Nodular cast iron demonstrates this effect particu-larly well,if a rotatable stage is used.12.7Differential Interference Contrast—(DIC or Nomarski illumination)This illumination technique shows edges of discontinuities on specimens as variations in brightness.Color contrast can be added as an additional indication of level variation.The method is termed differential because very minor discontinuities are emphasized,whereas slightly angled slopes are displayed almost as if they were perfectly normal to the optical axis;for example,a cylindrical phase looksflat with fairly sharp edges.A modified Wollaston prism located at the rear focal plane of the objective splits the illumination beam into two parallel beams,separated in phase by one-quarter wavelength.Any alteration of the optical path by the specimen, by either path length(feature height)or refractive index, produces an interference pattern in the image beams.As the beams return through the DIC prism,they are reunited and the interference effect appears as a variation in brightness and color.Most microscopes allow translation of the DIC prism to produce different color displays as well.DIC has several unique advantages:Since the full back aperture is illuminated, the full resolution of the objective is utilized;the interference plane is very shallow,keeping out-of-plane detail from inter-fering;there is an oblique appearance as an additional clue to level eful applications of DIC are:judging adequacy of specimen preparation for automated microscopy, as in Practice E768;display of surface relief,including changes of a few nanometres at abrupt edges.13.Instant-Processing Films13.1These materials yield photographic images within seconds after exposure(8).Both color and black-and-white versions are available.All use variations of the diffusion-transfer process,with each frame developed individually after exposure.13.1.1Instant materials should be exposed so that the lightest(white)tone in the image is reproduced as the brightest tone in the picture.(Shorter exposures will produce muddy whites,while longer ones will give insufficient separation between the lighter tones.)13.1.2The majority of the instant materials are of peel-apart construction,where the positive print is detached from the processing packet after development and the rest of the unit is discarded.A useful variation of this provides a transparent negative as well,for multiple print production by wet-process darkroom methods.Excellent photographic prints can be made from the negative instantfilms with great degrees ofenlarge-ment possible.(In order to optimize the exposure of the negative with a positive/negativefilm,the positive will be overexposed,and therefore not considered an acceptable print.)13.1.3The monopack materials,both black-and-white and color,require adapters that are unlike those normallyfitted to metallographic equipment.No processing control is possible. With some exceptions,monopack prints should not be cut.The use of the more adaptable peel-apart materials may be the better choice for metallography.13.2Processing Instant Films—All instant materials,both peel-apart and monopack,are processed by pulling the picture unit through an accurately-spaced roller pair.A chemical pod at the leading edge is ruptured and the contents spread throughout the unit by the rolls,starting the development action.The reaction goes to completion according to the time-temperature relationship supplied with thefilm.13.2.1The picture unit must be pulled in a straight line through the rollers,at a constant speed,to secure uniform processing.A pull-time of1⁄4to1⁄2second is suggested for peel-apart materials.Monopack instant materials permit no control over processing time,since the self-developing reaction is controlled by thefilm holder and proceeds to completion without attention from the user.13.2.2The roller pair should be kept clean,since evenfine debris on the rolls will cause uneven reagent spreading and picture nonuniformity.13.2.3Black-and-white peel-apart materials are best pro-cessed for at least the recommended time for the type involved. Extended processing up to three minutes is permissible.Be-yond this,problems may be encountered as the units are peeled.13.2.4Improved contrast and color saturation can be achieved with color peel-apart materials by processing to a two-minute standard,rather than the recommended one minute. The color balance will shift toward cyan,which can be corrected by adding some red to thefilter pack.14.Photographic Materials14.1Wet-Process Materials:General and Black-and-White—Conventional photographic materials provide an al-most unlimited choice of conditions for recording an image. Many of the readily available products can be usefully em-ployed in metallography.References(4-6)are recommended reading to learn the complete photographic characteristics of the products,as well as the terminology used to describe them.14.2The essential construction of a photographic material consists of a carrier base with a light-sensitive layer of silver halides in gelatine,commonly called the emulsion.Negative and projectable emulsions are on transparentflexible acetate or polyesterfilm bases,while reflection print materials have white paper or paper/plastic composite bases.14.3The most common materials are negative-acting,that is,exposure to light and subsequent chemical processing displays an image on afilm wherein the tonal values of the original scene(microscopicalfield)are reversed.This is subsequently printed by light exposure through the negativeonto photographic paper,where a positive image (the negative of the negative film image)is reproduced with similar chemical steps.14.4Some materials,either by controlled pre-exposure during manufacture or by specialized processing,yield a positive image directly and are called positive-acting.The principal uses are for projectables (slides)and negative dupli-cation.14.5Negative film materials are of the most concern for metallography.The film chosen to record a microscopical image must be able to reproduce the tonal values in the image in their correct relationship to produce satisfactory prints.The film choice is in part dictated by the subject matter to be recorded-a simple steel image in bright-field may have only a brightness ratio of 1:3,dark field and polarized light images can exceed a 1:100ratio.Reflection prints can at best repro-duce a 1:30brightness range.A film chosen for the first example should be capable of expanding the brightness range (contrast)by exposure and development control.A film for the latter example should compress the contrast of the original image.Typically,a film classified as high-contrast would be used in the first case,while a medium-to-low contrast material would be chosen for the other.(The extremely high-contrast lithographic films used for graphic arts purposes are excluded here.Their useful range of tonal reproduction is too restricted.)14.5.1The contrast potential of any film material ismost easily expressed graphically as the film’s characteristic curve published for all films in the manufacturers’literature.As an example of a film’s potential,such a curve is schematically represented in Fig. 2.As the exposure increases on the horizontal axis,the corresponding photographic effect (black-ening of the film)increases on the vertical axis.This effect becomes more prominent with increasing time of development,as indicated by the individual numbers on the curves.The useful part of a film’s sensitivity range is the mid-portion,where the slope is relatively constant,indicating a proportional change in density with a proportional change in exposure (shown on Fig.2by range m-n).The slope of the curve rises more steeply as development proceeds and thus the contrast of the film image increases with increasing development.14.6Several properties of negative emulsions that must be considered are:overall light sensitivity (film speed),spectral sensitivity,resolving power,graininess,and contrast potential.All of these qualities cannot be optimized at once in any film,hence choices must be made to suit the needs of the photomi-crograph.14.6.1Films are rated for general pictorial purposes by film speed numbers,for example,ISO speeds or DIN indices,with the higher rankings having increased light sensitivity.These rankings are not usually significant in metallography,since it isFIG.2Optical Density Versus Logarithm of Exposure for Photographic Materials。
MIL-STD-883GRESISTANCETOSOLVENTS-Q-Tech:mil-s。。。

METHOD 2015.13 18 December 2000 1METHOD 2015.13 RESISTANCE TO SOLVENTS1. PURPOSE. The purpose of this test is to verify that the markings will not become illegible on the component parts when subjected to solvents. The solvents will not cause deleterious, mechanical or electrical damage, or deterioration of the materials or finishes. 1.1 Formulation of solvents. The formulation of solvents herein is considered typical and representative of the desired stringency as far as the usual coatings and markings are concerned. Many available solvents which could be used are either not sufficiently active, too stringent, or even dangerous to humans when in direct contact or when the fumes are inhaled. 1.2 Check for conflicts. When this test is referenced, care should be exercised to assure that conflicting requirements, as far as the properties of the specified finishes and markings are concerned, are not invoked.2. MATERIALS. 2.1 Solvent solutions. The solvent solutions used in this test shall consist of the following: 1/a. At 20-30°C a mixture consisting of the following: (1) One part by volume of an aliphatic alcohol and/or aliphatic ester, USP grade or better. (2) Three parts by volume of mineral spirits in accordance with A-A-2904, type II, previously designated as TT-T-291, type II, grade A, or three parts by volume of a mixture of 80 percent by volume of kerosene and 20 percent by volume of ethylbenzene.b. A semiaqueous or nonaqueous based organic solvent e.g., a terpene or heterocyclic compound. 2/c. This solvent has been deleted. When a suitable replacement for this solvent has been found, it will be added as solution c. d. At 63°C to 70°C, a mixture consisting of the following: 1/ (1) 42 parts by volume of deionized water. (2) 1 part by volume of propylene glycol monomethyl ether. (3) 1 part by volume of monoethanolamine or equivalent inorganic base to achieve the same pH. 2.1.1 Solvent solutions, safety aspects. Solvent solutions listed in a through d above exhibit some potential for health and safety hazards. The following safety precautions should be observed: a. Avoid contact with eyes. b. Avoid prolonged contact with skin. c. Provide adequate ventilation. d. Avoid open flame. e. Avoid contact with very hot surfaces. 1/ Normal safety precautions for handling these solutions (e.g., same as those for diluted ammonium hydroxide) based on O.S.H.A rules for Monoethanolamine or other precautionary measures with regard to flash point, toxicity, etc. 2/ Or any EPA demonstrated equivalent. When using EPA approved alternative solutions for test, the device manufacturer should consider the recommended temperature for cleaning specified by the solvent supplier.METHOD 2015.13 18 December 2000 2 2.2 Vessel. The vessel shall be a container made of inert material, and of sufficient size to permit complete immersion of the specimens in the solvent solutions specified in 2.1. 2.3 Brush. The brush shall be a toothbrush with a handle made of a nonreactive material. The brush shall have at least three long rows of hard (or firm) bristles, the free ends of which shall lie substantially in the same plane. The toothbrush shall be used exclusively with a single solvent and when there is any evidence of softening, bending, wear, or loss of bristles, it shall be discarded. 3. PROCEDURE. The specimens subjected to this test shall be divided into three equal groups. Each group shall be individually subjected to one of the following procedures: Note: Metal lidded leadless chip carrier (LCC) packages shall be preconditioned by immersing the specimens in room temperature flux type symbols “A” or “B” (flux types “LO” or “L1”) in accordance with ANSI/J-STD-004 previously designated as RMA flux in accordance with MIL-F-14256, for 5 to 10 seconds. The specimens shall then be subjected to an ambient temperature of 215 °C ±5°C for 60 seconds +5, -0 seconds. After the preconditioning, each device lid shall be cleaned with isopropyl alcohol. a. The first group shall be subjected to the solvent solution as specified in 2.1a maintained at a temperature of 25°C ±5°C. b. The second group shall be subjected to the solvent solution as specified in 2.1b maintained at a suitable temperature. c. This solution has been deleted, (see 2.1c). d. The fourth group shall be subjected to the solvent solution as specified in 2.1d maintained at a temperature of 63°C to 70°C. The specimens and the bristle portion of the brush shall be completely immersed for 1 minute minimum in the specified solution contained in the vessel specified in 2.2. Immediately following emersion, the specimen shall be brushed with normal hand pressure (approximately 2 to 3 ounces) for 10 strokes on the portion of the specimen where marking has been applied, with the brush specified in 2.3. Immediately after brushing, the above procedure shall be repeated two additional times, for a total of three immersions followed by brushings. The brush stroke shall be directed in a forward direction, across the surface of the specimen being tested. After completion of the third immersion and brushing, devices shall be rinsed and all surfaces air blown dry. After 5 minutes, the specimens shall be examined to determine the extent, if any, of deterioration that was incurred. 3.1 Optional procedure for the fourth group. The test specimens shall be located on a test surface of known area which is located 15 ±2.5 centimeters (6 ±1 inches) below a spray nozzle(s) which discharges 0.6 ±0.02 liters/minute (0.139 gpm) of solution (2.1d) per 6.5 square centimeters (1 in 2)surface area at a pressure of 140 ±30 kilopascal (20 ±5 psi). The specimens shall be subjected to this spray for a period of 10 minutes minimum. After removal and within 5 minutes the specimens shall be examined in accordance with 3.1.1. The specimens may be rinsed with clear water and air blow dried prior to examination. 3.1.1 Failure criteria. After subjection to the test, evidence of damage to the device and any specified markings which are missing in whole or in part, faded, smeared, blurred, or shifted (dislodged) to the extent that they cannot be readily identified from a distance of at least 15.0 cm (6 inches) with normal room lighting and without the aid of magnification or with a viewer having a magnification no greater than 3X shall constitute a failure. 4. SUMMARY. The following detail shall be specified in the individual specification: The number of specimens to be tested (see 3). *。
L9338

L9338For optical switchesAbsolute maximum ratings (Ta=25 °C, unless otherwise noted)*1: W hen there is a temperature difference between a product and the surrounding area in high humidity environments, dew condensationmay occur on the product surface. Dew condensation on the product may cause deterioration in characteristics and reliability.*2: Guaranteed to resist temperature cycle test of up to 5 cycles Note: E xceeding the absolute maximum ratings even momentarily may cause a drop in product quality. Always be sure to use theproduct within the absolute maximum ratings.ApplicationsOptical switchesHigh reliability Low priceFeaturesElectrical and optical characteristics (Ta=25 °C)*3: Frequency at which the optical output drops by 3 dB from that at 10 kHzThe L9338 is an infrared LED developed for optical switches and is available at a low cost due to the improved manufacturingprocess.Emission spectrumForward current vs. forward voltageRadiant flux vs. forward currentDirectivity040206080100Wavelength (nm)R e l a t i v e r a d i a n to u t p u t (%)F 1101001000Forward current (mA)R a d i a n t f l u x(m W )101001000Forward voltage (V)F o r w a r d cu r r e n t (m A )Relative radiant output (%)(Typ. Ta=25 °C)90°80°50°40°30°70°60°90°80°50°40°30°70°60°KLEDB0255EAKLEDB0256EBKLEDB0257EBKLEDB0258EAAllowable forward current vs. duty ratioRadiant output vs. ambient temperatureAllowable forward current vs. ambient temperatureDuty ratio (%)A l l o w a b l e f o r w a r d c u r r e n t (A )0.010.1110-2-3-112Ambient temperature (°C)R e l a t i v e r a d i a n t o u t p u t (d B )(Typ. I F =50 mA)406080100Ambient temperature (°C)R e l a t i v e a l l o w a b l e f o r w a r d c u r r e n t (%)20KLEDB0259EAKLEDB0254EBKLEDB0038EBProduct specifications are subject to change without prior notice due to improvements or other reasons. This document has been carefully prepared and the information contained is believed to be accurate. In rare cases, however , there may be inaccuracies such as text errors. Before using these products, always contact us for the delivery specification sheet to check the latest specifications.The product warranty is valid for one year after delivery and is limited to product repair or replacement for defects discovered and reported to us within that one year period. However , even if within the warranty period we accept absolutely no liability for any loss caused by natural disasters or improper product use.Copying or reprinting the contents described in this material in whole or in part is prohibited without our prior permission.Information described in this material is current as of May, 2022.Dimensional outline (unit: mm)Related informationPrecautions ∙ Disclaimer∙ Safety consideration∙ Compound opto-semiconductors (photosensors, light emitters) Technical information ∙ LED / Technical noteKLEDA0058EB。
美军标883E

NOTICE 3METHOD 2020.7PARTICLE IMPACT NOISE DETECTION TEST1. PURPOSE. The purpose of this test is to detect loose particles inside a device cavity. The test provides a nondestructive means of identifying those devices containing particles of sufficient mass that, upon impact with the case, excite the transducer.2. APPARATUS. The equipment required for the particle impact noise detection (PIND) test shall consist of the following (or equivalent):a. A threshold detector to detect particle noise voltage exceeding a preset threshold of the absolute value of 20 ±1millivolt peak reference to system ground.b. A vibration shaker and driver assembly capable of providing essentially sinusoidal motion to the device under test(DUT) at:(1)Condition A: 20 g peak at 40 to 250 Hz.(2)Condition B: 10 g peak at 60 Hz minimum.c.PIND transducer, calibrated to a peak sensitivity of -77.5 ±3 dB in regards to one volt per microbar at a point withinthe frequency of 150 to 160 kHz.d. A sensitivity test unit (STU) (see figure 2020-1) for periodic assessment of the PIND system performance. TheSTU shall consist of a transducer with the same tolerances as the PIND transducer and a circuit to excite thetransducer with a 250 microvolt ±20 percent pulse. The STU shall produce a pulse of about 20 mV peak on theoscilloscope when the transducer is coupled to the PIND transducer with attachment medium.e.PIND electronics, consisting of an amplifier with a gain of 60 ±2 dB centered at the frequency of peak sensitivity ofthe PIND transducer. The noise at the output of the amplifier shall not exceed 10 mV peak.f.Attachment medium. The attachment medium used to attach the DUT to the PIND transducer shall be the sameattachment medium as used for the STU test.g.Shock mechanism or tool capable of imparting shock pulses of 1,000 ±200 g peak to the DUT. The duration of themain shock shall not exceed 100 µs. If an integral co-test shock system is used the shaker vibration may beinterrupted or perturbed for period of time not to exceed 250 ms from initiation of the last shock pulse in thesequence. The co-test duration shall be measured at the 50 ±5 percent point.3. PROCEDURES.* 3.1 Test equipment setup. Shaker drive frequency and amplitude shall be adjusted to the specified conditions based on cavity size of the DUT (for condition A, see table I herein). The shock pulse shall be adjusted to provide 1,000 ±200 g peak to the DUT.3.2 Test equipment checkout. The test equipment checkout shall be performed a minimum of one time per operation shift. Failure of the system to meet checkout requirements shall require retest of all devices tested subsequent to the last successful system checkout.3.2.1 Shaker drive system checkout. The drive system shall achieve the shaker frequency and the shaker amplitude specified. The drive system shall be calibrated so that the frequency settings are within ±8 percent and the amplitude vibration setting are within ±10 percent of the nominal values. If a visual displacement monitor is affixed to the transducer, it may be used for amplitudes between 0.04 and 0.12 inch (1.02 and 3.05 mm). An accelerometer may be used over the entire range of amplitudes and shall be used below amplitudes of 0.040 inch (1.02 mm).Supersedes page 1 of MIL-STD-883EMETHOD 2020.722 March 19891NOTICE 33.2.2 Detection system checkout. With the shaker deenergized, the STU transducer shall be mounted face-to-face and coaxial with the PIND transducer using the attachment medium used for testing the devices. The STU shall be activated several times to verify low level signal pulse visual and threshold detection on the oscilloscope. Not every application of th e STU will produce the required amplitude. All pulses which are greater than 20 mV shall activate the detector.3.2.3 System noise verification. System noise will appear as a fairly constant band and must not exceed 20 millivolts peak to peak when observed for a period of 30 to 60 seconds.3.3 Test sequence. The following sequence of operations (a through i) constitute one test cycle or run.a. 3 pre-test shocks.b. Vibration 3 ±1 seconds.c. 3 co-test shocks.d. Vibration 3 ±1 seconds.e. 3 co-test shocks.f. Vibration 3 ±1 seconds.g. 3 co-test shocks.h. Vibration 3 ±1 seconds.i. Accept or reject.* 3.3.1 Mounting requirements. Special precautions (e.g., in mounting, grounding of DUT leads, or grounding of test operator) shall be taken as necessary to prevent electrostatic damage to the DUT. Batch testing is prohibited.Most part types will mount directly to the transducer via the attachment medium. Parts shall be mounted with the largest flat surface against the transducer at the center or axis of the transducer for maximum sensitivity. Where more than one large surface exists, the one that is the thinnest in section or has the most uniform thickness shall bemounted toward the transducer, e.g., flat packs are mounted top down against the transducer. Small axial-lead, right circular cylindrical parts are mounted with their axis horizontal and the side of the cylinder against the transducer.Parts with unusual shapes may require special fixtures. Such fixtures shall have the following properties:(1)Low mass.(2)High acoustic transmission (aluminum alloy 7075 works well).(3)Full transducer surface contact, especially at the center.(4)Maximum practical surface contact with test part.(5)No moving parts.(6)Suitable for attachment medium mounting.Supersedes page 2 of MIL-STD-883EMETHOD 2020.722 March 19892METHOD 2020.722 March 198933.3.2 Test monitoring. Each test cycle (see 3.3) shall be continuously monitored, except for the period during co-test shocks and 250 ms maximum after the shocks. Particle indications can occur in any one or combinations of the three detection systems as follows:a.Visual indication of high frequency spikes which exceed the normal constant background white noise level.b.Audio indication of clicks, pops, or rattling which is different from the constant background noise present with no DUT on the transducer.c.Threshold detection shall be indicated by the lighting of a lamp or by deflection of the secondary oscilloscope trace.3.4 Failure criteria. Any noise bursts as detected by any of the three detection systems exclusive of background noise, except those caused by the shock blows, during the monitoring periods shall be cause for rejection of the device. Rejects shall not be retested except for retest of all devices in the event of test system failure. If additional cycles of testing on a lot are specified, the entire test procedure (equipment setup and checkout mounting, vibration, and co-shocking) shall be repeated for each retest cycle. Reject devices from each test cycle shall be removed from the lot and shall not be retested in subsequent lot testing.3.5 Screening lot acceptance. Unless otherwise specified, the inspection lot (or sublot) to be screened for lot acceptance shall be submitted to 100 percent PIND testing a maximum of five times in accordance with condition A herein. PINDprescreening shall not be performed. The lot may be accepted on any of the five runs if the percentage of defective devices in that run is less than 1 percent. All defective devices shall be removed after each run. Lots which do not meet the 1 percent PDA on the fifth run, or exceed 25 percent defectives cumulative, shall be rejected and resubmission is not allowed.TABLE I. Package height vs. test frequency for 20 g acceleration (condition A).Average internal cavityheightFrequency Milsmm Hz <4041-5051-6061-7071-8081-9091-100>100<1.02 1.03-1.27 1.28-1.52 1.53-1.78 1.79-2.03 2.04-2.29 2.30-2.54>2.54 130 120 110 100 90 80 70 60NOTE: The approximate average internal packageheight shall be measured from the floor of thepackage cavity or the top of the major substratefor hybrid or multichip assemblies and shallexclude the thickness of the die mounted insidethe package.4. SUMMARY. The following details shall be specified in the applicable acquisition document:a.Test condition letter A or B.b.Lot acceptance/rejection criteria (if other than specified in 3.5).c.The number of test cycles, if other than one.d.Pre-test shock level and co-test shock level, if other than specified.METHOD 2020.722 March 19894NOTES:1. Pushbutton switch: Mechanically quiet, fast make, gold contacts. E.G. T2 SM4 microswitch.2. Resistance tolerance 5 percent noninductive.3. Voltage source can be a standard dry cell.4. The coupled transducers must be coaxial during test.5. Voltage output to STU transducer 250 microvolts, ±20 percent.FIGURE 2020-1 Typical sensitivity test unit.METHOD 2020.722 March 19895。
- 1、下载文档前请自行甄别文档内容的完整性,平台不提供额外的编辑、内容补充、找答案等附加服务。
- 2、"仅部分预览"的文档,不可在线预览部分如存在完整性等问题,可反馈申请退款(可完整预览的文档不适用该条件!)。
- 3、如文档侵犯您的权益,请联系客服反馈,我们会尽快为您处理(人工客服工作时间:9:00-18:30)。
75
FM
DCP25
DCP50
DCP75
DCP75A
DCPT
Mean
ADCs of Methione (蛋氨酸消化率)
100
95
ab
ab
ab
a ab b
90
Methione
85
80
Mean+SD Mean-SD
干物质
Dry matter
粗蛋白
Crude protein
粗脂肪
Crude fat
灰分Ash 能量
Energy(MJ/kg)
Table 3 实验饲料的必需氨基酸组成 Essential amino acids composition of experimental diets
Diets Threonine Methionine Cysteine Met.+Cysteine Valine Isoleucine Leucine Phe.+Tyrosine Lysine Histidine Arginine
c
a
ab
ab
b
b
PER 蛋白质效率(%)
2.5
a
2.0
ab
ab
b
ab
c
1.5
1.0
0.5
0.0
FM
DCP25
DCP50
DCP75
DCP75A
DCPT
Mean+SD Mean-SD Mean
ADCs of Dry matter 干物质表观消化率 (%)
85
80
a
ab
75
ab
ab
b
b
70
65
Mean+SD Mean-SD Mean
Utilization of degossypolled cottonseed protein in aquatic feed 脱酚棉籽蛋白在水产饲料中的应用
Xue Min Luo Lin
薛敏
罗琳
Beijing Aquaculture Nutrition Research Centre, Beijing
北京友谊通元水产技术开发中心
Why research on degossypolled cottonseed protein (DCP)
研究脱酚棉籽蛋白在水产饲料中的应用的目的
Fish meal is deficient and expensive resources,phosphorus excretion •鱼粉是很好的水产饲料蛋白源,但资源短缺,价格昂贵,磷污 染严重 The market price of the fish has been decreased rapidly •由于养殖规模的扩大和产量的大幅提高,水产品价格降幅较大 The importance of vegetable alternative proteins •植物性替代蛋白源成为研究热点
脱酚棉籽蛋白氨基酸组成及与相关产品比较 Amino acids composition of DCP (% of crude protein)
一般棉籽粕 Cottonseed meal 精氨酸Arg 组氨酸His 异亮氨酸Iie 亮氨酸Leu 赖氨酸Lys 蛋氨酸+胱氨酸 Met+ Cys 苯丙氨酸Phe 苏氨酸Thr 缬氨酸Val 总必需氨基酸TEAA 粗蛋白含量 CP(%dw) 11.05 2.82 3.09 5.89 4.13 3.27 5.31 3.23 4.24 42.55 44.90 脱酚棉籽蛋白 DCP 12.21 3.22 3.61 6.28 4.79 3.88 5.62 3.29 5.03 47.95 56.25 豆粕 Soybean meal 7.52 2.76 4.42 7.41 5.98 2.93 4.99 3.96 4.90 44.51 53.80
1Requirement
FM
DCP25
DCP50
DCP75
DCP75A DCPT
Req.1
Essential amino acids (% of dry matter) 1.78 1.33 0.73 2.06 2.06 1.80 2.90 3.01 2.99 1.36 2.47 1.68 1.16 0.72 1.88 1.99 1.75 2.95 3.39 2.62 1.46 3.17 1.71 1.05 0.84 1.89 2.00 1.68 2.83 3.48 2.50 1.46 1.71 1.56 0.91 0.91 1.82 1.78 1.51 2.64 3.51 2.11 1.47 3.73 1.45 1.29 0.84 2.13 1.64 1.41 2.61 3.24 2.75 1.57 3.57 1.48 0.80 1.10 1.90 1.76 1.44 2.57 3.46 1.81 1.44 4.19 1.0 1.2 0.9 1.4 1.8 1.8 0.7 0.8 0.8
is for rainbow trout based on cruder protein 38% (NRC, 1993 )
2.
Fish, holding conditions and procedures
Fish: rainbow trout (Initial body weight:39.18±0.07g ) 实验鱼:虹鳟(平均初重39.18±0.07g ) 18 fish/tank (18尾鱼/桶) fed twice daily to satiation (09:00 and 17:00) 每天饱食投喂2次(09:00 and 17:00) T: 15±1℃; D.O: 7.2±0.5mg/l; pH: 7.5±0.3. 8 weeks growth trial(实验期为8周)
-Continue 研究脱酚棉籽蛋白在水产饲料中的应用的目的
DCP: the meal left after oil and gossypol have been extracted from the cottonseed with special treatment process 脱酚棉籽蛋白是采用液-液-固工艺将棉籽去油、脱酚处理后得 到的金黄色粉末 含量 Content(%) Crude protein 粗蛋白 gossypol 0mg/kg 国标 National standard
60
FM
DCP25
DCP50
DCP75
DCP75A
DCPT
ADCs of Crud protein 蛋白质表观消化率(%)
95
ac
90
ac
ac
c
ab
b
85
80
75
FM DCP25 DCP50 DCP75 DCP75A DCPT
Mean+SD Mean-SD Mean
ADCs of Energy 能量表观消化率(%)
ingredients
FM DCP25 DCP50 DCP75 DCP75A DCPT
豆粕Soybean meal 脱酚棉籽蛋白DCP 鱼粉Fishmeal 大豆磷脂Lecithin 鱼油Fish oil 面粉Flour 谷朊粉Wheat gluten 预混料Vitamins/Minerals
premix
90
a
85
ac abc bc b b
80
75
70
FM
DCP25
DCP50
DCP75
DCP75A
DCPT
Mean+SD Mean-SD Mean
ADCs of Threonine (苏氨酸消化率)
100
a
95
ab
ab
abc
bc
Threonine
90
c
85
80
Mean+SD Mean-SD
75
FM
DCP25
Objectives of the study 研究对象
To determine the effect of DCP on • 虹鳟Rainbow trout(Oncorhynchus mykiss) • 花鲈Japanese sea bass (Lateolabrax Japonicus) • 南美白对虾Penaeus. vannamei
8 0 45 2 4.6 31.3 5 4
8 15.2 33.75 2 5.6 26.05 5.3 4
8 30.5 22.5 2 6.5 20.8 5.6 4
8 46.5 11.25 2 7 15.65 5.5 4
8 46 11.25 2 7 15.9 4.5 4 0.93 0.32
8 61 0 2 8.6 9.8 6.5 4
-Continue 研究脱酚棉籽蛋白在水产饲料中的应用的目的
The annual product of cottonseed is about 5 million ton in China, but normal use of cottonseed meal in feed is less than 15% because of its low lysine, methionine, cystine availability and toxicity of gossypol. 我国年产棉籽500万吨,但由于传统榨油工艺导致棉籽粕中的 某些氨基酸利用率低以及游离棉酚的毒性,使得棉籽粕在饲料 中的正常使用量不足15%。
虹 鳟(冷水,淡水肉食性)
(Rainbow trout,Oncorhynchus mykiss, cold water, fresh water carnivorous fish)
I.
Materials and Methods 材料与方法