低碳钢输油管穿孔失效分析-论文
某平台外输油管道腐蚀穿孔原因分析及建议

H s的腐 蚀 过 程是 C O / H2 S 溶 于水 形 成碳 酸 和氢 硫 酸 , 释 放 出氢 离子 。 氢 离子 极 易夺 取 电子还 原 , 促使 阳极 铁溶解 而导 致 腐蚀 。 产 物为 铁 的碳酸物 和硫 化物 , 随 后表 面被 铁的腐 蚀产 物
所覆 盖 。 因此 C O / H S对管 道的腐蚀 , 还 与腐蚀 产物是 否在 钢 的表 面成膜及 膜的结构 和稳定性有 着重要 的关系 。 据采集 的数
情况分析 , 得 出穿孔主要是点蚀和 阴极保护失效造成 , 同时为其它输油管道提出防护建议 。
关键词 : 输 油管道 ; 腐蚀 穿孔 ; 防护措 施
1管 道的腐 蚀情 况
某 平 台外 输 油管 道 于2 O l 3 年l 1月、 1 2月先 后 两次 穿 孔 。 该 管 道材 质 为L 3 6 0 , 规 格 为 ̄4 5 7 X7 . 1 , 输 送 的介 质含 硫较 高 并 存 在一 定 的二氧 化 碳气体 , 已投 入使 用近 8 年, 经外 观检 查
量达 到了6 0 %。 这 为管道 内表 面腐蚀创造 了条件 。
( 2 ) 硫化氢 造成钢材 脆化和损伤 。 在湿 硫化氢环境 中 , 硫化 氢会 发生 电离 , 使水具有 酸性 , 硫 化氢在水 中的电离如 下。
H 2 s HS— H +HS— H +S 一
2 . 3阴极保护实施效果和维护力度不够。
隙 内外形成 了 “ 氧 浓差 电池 ” , 孔外氧浓 度高 , 为 阴极 ; 孔 内氧
2 穿孔 原 因分析
2 . 1 弱酸腐 蚀 ( 1 ) 管 道中的水含量 高为化学 腐蚀创造 了条件 。 二氧化碳 、
硫化 氢 腐蚀 的发生 都离 不开水 对钢 铁表 面的润 湿作 用 。 因此 , 水在 介质 中的含量是影 响管道 内腐 蚀的一 个重要 因素。 一 般说 来, 油水 混合介 质当油 中含水量小于 3 0 %时会形成 油包水 型乳 状液 , 水 包含在油 中 , 这 些水相对钢 铁表面 的润湿将 受到抑制 , 发生 腐 蚀的 倾 向较小 。 当水 含量 大于4 0 %时 , 会形 成水 包油 型 乳状 液 , 油 包含在 水 中 , 这 时钢 铁材料 表面 润湿 而易 引发二 氧 化碳 、 硫 化氢腐蚀 。 按 照作业区提供 的数据 , 该输 油管道 的水 含
油套管的缺陷失效分析
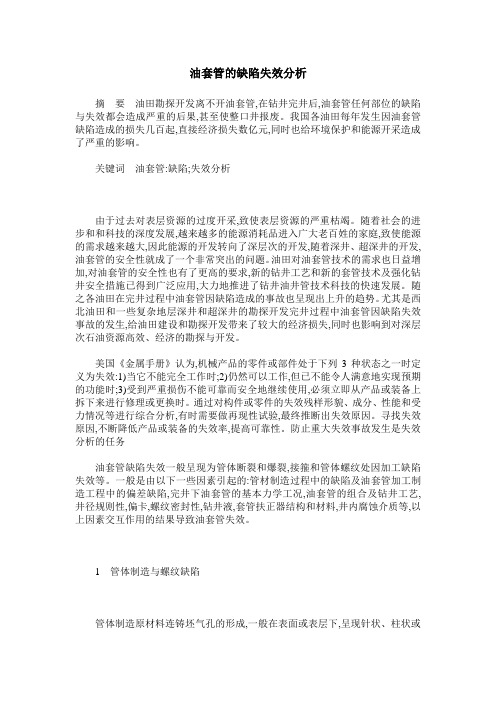
油套管的缺陷失效分析摘要油田勘探开发离不开油套管,在钻井完井后,油套管任何部位的缺陷与失效都会造成严重的后果,甚至使整口井报废。
我国各油田每年发生因油套管缺陷造成的损失几百起,直接经济损失数亿元,同时也给环境保护和能源开采造成了严重的影响。
关键词油套管:缺陷;失效分析由于过去对表层资源的过度开采,致使表层资源的严重枯竭。
随着社会的进步和和科技的深度发展,越来越多的能源消耗品进入广大老百姓的家庭,致使能源的需求越来越大,因此能源的开发转向了深层次的开发,随着深井、超深井的开发,油套管的安全性就成了一个非常突出的问题。
油田对油套管技术的需求也日益增加,对油套管的安全性也有了更高的要求,新的钻井工艺和新的套管技术及强化钻井安全措施已得到广泛应用,大力地推进了钻井油井管技术科技的快速发展。
随之各油田在完井过程中油套管因缺陷造成的事故也呈现出上升的趋势。
尤其是西北油田和一些复杂地层深井和超深井的勘探开发完井过程中油套管因缺陷失效事故的发生,给油田建设和勘探开发带来了较大的经济损失,同时也影响到对深层次石油资源高效、经济的勘探与开发。
美国《金属手册》认为,机械产品的零件或部件处于下列3种状态之一时定义为失效:1)当它不能完全工作时;2)仍然可以工作,但已不能令人满意地实现预期的功能时;3)受到严重损伤不能可靠而安全地继续使用,必须立即从产品或装备上拆下来进行修理或更换时。
通过对构件或零件的失效残样形貌、成分、性能和受力情况等进行综合分析,有时需要做再现性试验,最终推断出失效原因。
寻找失效原因,不断降低产品或装备的失效率,提高可靠性。
防止重大失效事故发生是失效分析的任务油套管缺陷失效一般呈现为管体断裂和爆裂,接箍和管体螺纹处因加工缺陷失效等。
一般是由以下一些因素引起的:管材制造过程中的缺陷及油套管加工制造工程中的偏差缺陷,完井下油套管的基本力学工况,油套管的组合及钻井工艺,井径规则性,偏卡,螺纹密封性,钻井液,套管扶正器结构和材料,井内腐蚀介质等,以上因素交互作用的结果导致油套管失效。
油管多项失效典型案例分析
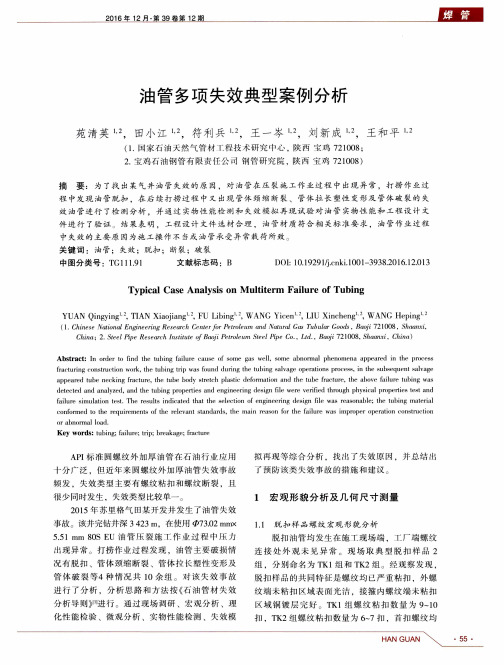
f a i l u r e s i mu l a t i o n t e s t . T h e r e s u l t s i n d i c a t e d t h a t t h e s e l e c t i o n o f e n g i n e e r i n g d e s i g n i f l e w a s r e a s o n a b l e ;t h e t u b i n g ma t e r i a l c o n 1 f ) mmd t u t h e r e q u i r e me n t s o f t h e r e l e v a n t s t a n d m’ d s . t h e n l a i n l e a s n n f ( u ‘ t h e f a i l u r e w a s i mp r o p m ’ o p e r a t i o n c o n s t r u ( 。 t i o n o r a t mo r ma I 】 ( ) a ( 1 .
( 1 . C h i n e s e N a t i o n f z f E n g i n e e r i n g R e s e a r c h C e n t e r i f ) r P e t r u l e mn a l l d N a t 1 + r a l G a s T u b u l r a G o o d s , 日 7 2 1 0 0 8 , S h < u m x i , C h i n a ; 2 . S t e e l l h ' p e R e s e a r c h I n s t i t u t e o fB t u  ̄ j i P e t r u h , u m S t e  ̄ , , I h ' p e C o . , L t d . , “ 7 2 1 0 0 8 , S h m mx i , C h i n “ )
某油田生产井中心管腐蚀穿孔失效分析

某油田生产井中心管腐蚀穿孔失效分析
郭增伍;练斌;秦立高;杨阳;柴圆圆
【期刊名称】《现代制造技术与装备》
【年(卷),期】2024(60)3
【摘要】某油田一口生产井中心管出现严重腐蚀穿孔现象。
为查找腐蚀原因,通过宏观分析、材质分析、水质分析、腐蚀产物分析、腐蚀模拟试验等对中心管腐蚀失效进行分析。
结果表明,失效管段位置出砂严重,泥沙几乎堆满整根油管。
泥沙的冲刷协同CO_(2)腐蚀,导致管壁不断减薄,最终穿孔失效。
【总页数】4页(P50-52)
【作者】郭增伍;练斌;秦立高;杨阳;柴圆圆
【作者单位】中海石油(中国)有限公司天津分公司;中海油能源发展股份有限公司工程技术分公司;中海油(天津)管道工程技术有限公司;海油来博(天津)科技股份有限公司
【正文语种】中文
【中图分类】TE9
【相关文献】
1.海上油田生产井油管腐蚀失效分析
2.海上某油田油管短节腐蚀穿孔失效分析
3.某油田注水管道环焊缝腐蚀穿孔失效分析
4.海上某油田油井管腐蚀穿孔失效分析
5.海上某生产井油管腐蚀穿孔失效分析
因版权原因,仅展示原文概要,查看原文内容请购买。
油井管腐蚀穿孔失效分析

油井管腐蚀穿孔失效分析摘要:油井井筒腐蚀是指油井井筒内壁被化学物质侵蚀而导致的损坏。
油井井筒是油井的重要组成部分,它是将油井表面与油层地下连接的管道,负责将钻井液、油层水、油气等物质输送到地面,同时也承受着来自地下油层的高压力、高温度等严酷环境,因此,井筒内壁的腐蚀问题是油井开采过程中不可避免的难题。
关键词:油井管;腐蚀;原因分析;防腐措施前言在油田多年的勘探开发过程中,由于历史原因,某些区块的一些地下设备和设施没有得到妥善保护,导致井筒、油管和油杆腐蚀严重。
油田油井发生腐蚀、穿孔和破裂,油田使用的金属设备和设施的腐蚀是由金属材料与周围环境的相互作用引起的。
尤其是对井筒套管的损坏。
影响金属材料腐蚀行为的因素很多,既与金属本身的因素有关,也与腐蚀环境有关。
了解金属材料的腐蚀有助于解决油田生产中的腐蚀问题,阐明影响腐蚀的主要因素,并对其进行分析。
这对油田的防腐工作具有重要意义。
1油井井筒腐蚀的原因分析1.1酸性介质的侵蚀油井开采过程中会产生一些酸性介质,如HCl、HF、H2S等化学物质,这些物质容易对井筒内壁产生腐蚀作用,导致井筒内壁的金属材料受损。
此外,油井开采过程中也会使用酸洗井筒的方法,虽然能够清除井筒内的垢层和沉积物,但也会进一步加剧井筒内壁的腐蚀。
1.2氧化腐蚀油井开采过程中,空气和水分都会进入井筒内,这些物质容易与井筒内壁的金属材料发生氧化反应,形成氧化膜,进而导致井筒内壁的腐蚀。
此外,高温下的氧化反应也会加速井筒内壁的腐蚀。
1.3电化学腐蚀油井井筒内的金属材料容易与地下水和油气形成电化学腐蚀环境,导致井筒内壁的金属材料发生电化学腐蚀。
此外,由于油井井筒内的金属材料具有不同的电位,也会形成电化学腐蚀环境,导致井筒内壁的金属材料受损。
1.4细菌腐蚀油田油井采出液中,含有很多的硫酸盐还原菌(SRB)、铁细菌、硫细菌等菌种,此类菌种长期潜伏在地层水和岩石中,当开采油层产生全新环境,有利于细菌生长时,这些菌种就会快速大量的繁殖。
集输管道腐蚀失效原因分析及防护措施研究
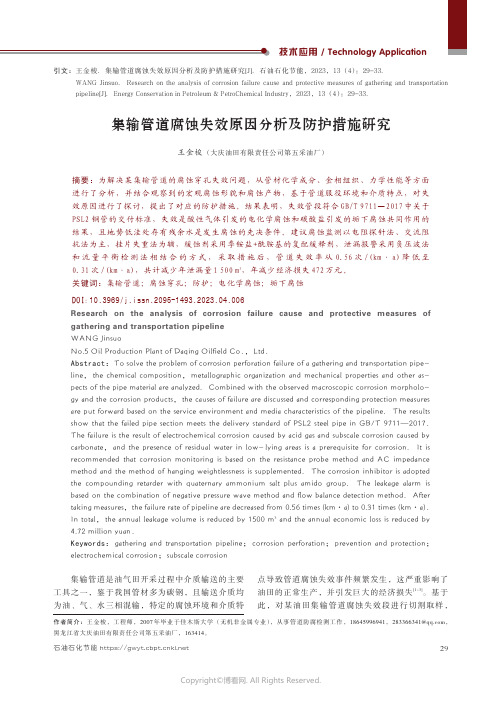
技术应用/TechnologyApplication集输管道是油气田开采过程中介质输送的主要工具之一,鉴于我国管材多为碳钢,且输送介质均为油、气、水三相混输,特定的腐蚀环境和介质特点导致管道腐蚀失效事件频繁发生,这严重影响了油田的正常生产,并引发巨大的经济损失[1-3]。
基于此,对某油田集输管道腐蚀失效段进行切割取样,集输管道腐蚀失效原因分析及防护措施研究王金梭(大庆油田有限责任公司第五采油厂)摘要:为解决某集输管道的腐蚀穿孔失效问题,从管材化学成分、金相组织、力学性能等方面进行了分析,并结合观察到的宏观腐蚀形貌和腐蚀产物,基于管道服役环境和介质特点,对失效原因进行了探讨,提出了对应的防护措施。
结果表明,失效管段符合GB/T 9711—2017中关于PSL2钢管的交付标准,失效是酸性气体引发的电化学腐蚀和碳酸盐引发的垢下腐蚀共同作用的结果,且地势低洼处存有残余水是发生腐蚀的先决条件。
建议腐蚀监测以电阻探针法、交流阻抗法为主,挂片失重法为辅,缓蚀剂采用季铵盐+酰胺基的复配缓释剂,泄漏报警采用负压波法和流量平衡检测法相结合的方式,采取措施后,管道失效率从0.56次/(km ·a)降低至0.31次/(km·a),共计减少年泄漏量1500m 3,年减少经济损失472万元。
关键词:集输管道;腐蚀穿孔;防护;电化学腐蚀;垢下腐蚀DOI :10.3969/j.issn.2095-1493.2023.04.006Research on the analysis of corrosion failure cause and protective measures of gathering and transportation pipeline WANG JinsuoNo.5Oil Production Plant of Daqing Oilfield Co .,Ltd .Abstract:To solve the problem of corrosion perforation failure of a gathering and transportation pipe-line,the chemical composition,metallographic organization and mechanical properties and other as-pects of the pipe material are analyzed.Combined with the observed macroscopic corrosion morpholo-gy and the corrosion products,the causes of failure are discussed and corresponding protection measures are put forward based on the service environment and media characteristics of the pipeline.The results show that the failed pipe section meets the delivery standard of PSL2steel pipe in GB/T 9711—2017.The failure is the result of electrochemical corrosion caused by acid gas and subscale corrosion caused by carbonate,and the presence of residual water in low-lying areas is a prerequisite for corrosion.It is recommended that corrosion monitoring is based on the resistance probe method and AC impedance method and the method of hanging weightlessness is supplemented.The corrosion inhibitor is adopted the compounding retarder with quaternary ammonium salt plus amido group.The leakage alarm is based on the combination of negative pressure wave method and flow balance detection method.After taking measures,the failure rate of pipeline are decreased from 0.56times (km·a)to 0.31times (km·a).In total,the annual leakage volume is reduced by 1500m 3and the annual economic loss is reduced by 4.72million yuan .Keywords:gathering and transportation pipeline;corrosion perforation;prevention and protection;electrochemical corrosion;subscale corrosion 作者简介:王金梭,工程师,2007年毕业于佳木斯大学(无机非金属专业),从事管道防腐检测工作,186****6941,****************,黑龙江省大庆油田有限责任公司第五采油厂,163414。
胜利油田某油井油管腐蚀穿孔失效分析

“煤 层 气 排 采 出 煤 粉 机 理 研 究 ”(ZR2018BEE016) 作者简介:张 辛(1987),女,山东泰安人,高级实验 师,博 士,从 事 石 油 钻 采 管 柱 力 学 和 煤 层 气 开 采 相 关 教 学 和 科 研 工
作 。Email:1285354170@qq.com。
犉犪犻犾狌狉犲犃狀犪犾狔狊犻狊狅犳犆狅狉狉狅狊犻狅狀犘犲狉犳狅狉犪狋犻狅狀狅犳犜狌犫犻狀犵犻狀犛犺犲狀犵犾犻犗犻犾犳犻犲犾犱
犣犎犃犖犌犡犻狀,犔犐犖犡狌犲狇犻犪狀犵,犉犈犖犌犉犪狀,犣犎犗犝 犕犻狀犵狀犪狀,犔犐犛犺犲狀犵犾狅狀犵 (ChinaUniversityofPetroleum,Qingdao266580,China)
犃犫狊狋狉犪犮狋:AimingattheproblemofcorrosionperforationoftubinginShengliOilfield,chemical
compositionanalysis,metallographicmicroscope,scanningelectron microscopy,energydispersive spectroscopy,Xraydiffractionwereusedtoinvestigatethemacroscopicmorphology,composition ofcorrosionproductsandcompositionofthecorrosionperforationsegementofthetubing.Thea nalysisresultsshowthatthecorrosionperforationofthepipeisfromtheoutsidetotheinside,the corrosionproductwiththemaincomponentofFeCO3atthecorrosionperforationpositionisrela tivelylooseandthethicknessofthecorrosionproductfilmisthinnerthanthatoftheunperforat edposition.TheelementcontentofSiandClinthecorrosionproductfilmattheperforationis higherthanthatintheportion.Thesandparticlespresentinthecorrosionproductfilm during thecorrosionprocessdestroytheintegrityofthecorrosionproductfilm,causingthelocalcorro sionproductfilmtobeporous.TheporeseasilybecomehighspeedchannelsthroughwhichCl- andothercorrosive mediapass,causinglocalcorrosionandcausingoilpipecorrosion,perfora tion,orevenfailureultimately.A simpleprotective measurementtopreventcorrosionperfora tionoftubingwereproposed.
油气管道失效分析研究及展望
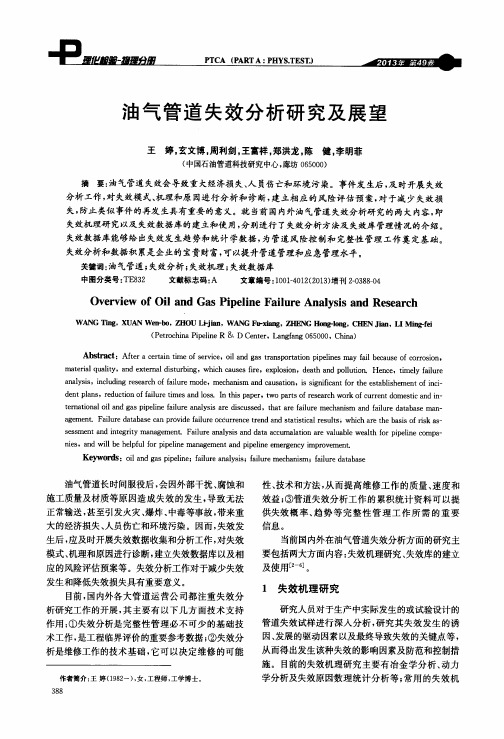
安:西安建筑科技大学,2005. r4]CASTELLANOSA V,ALBITERA A,HERNANDEZA
P,et a1.Failure analysis expert system for onshore pipelines.Part II:End user interface and algorithm
[J].Expert Systems with Applications,201 1,38(9):
11091 11104.
[5] 宋志强,李著信,傅在善.埋地油气管道失效分析及风 险评估[J].军事物流,2010(4):如6—108.
E6]李鹤林,赵新伟,吉玲康.油气管道失效分析与完整
性管理[J].理化检验一物理分册,2005,41(21):24—31. r7]PHMSA.Pipeline Incidents and Mileage Reports[-EB/
有限元分析利用数学近似的方法对真实物理系 统(几何和载荷工况)进行模拟,是用有限数量的未 知量去逼近无限未知量的真实系统,是用较简单的 问题代替复杂问题后再求解。由于大多数实际问题 难以得到准确解,而有限元不仅计算精度高,而且能 适应各种复杂形状,因而成为行之有效的工程分析 手段。 186
1990 1994 1998 2002 20016 2010
年份
蚕麓耋
石油消 耗量
管理里程
美国人 口数 产生环境后 果的泄漏
喜轰曩壹的
图2美国管道不同测量环境下的安全状况
Fig.2 Pipeline safety with context measures
言1.4
砉1‘。
喜0.6
(2)统一失效库数据收集标准,全面完善数据 库管理工作。
X油田管道失效分析

X 油田管道失效分析X 油田管道失效分析随着石油工业的不断发展,油田管道作为输送石油的重要设施,其失效问题越来越受到人们的关注。
本文基于X 油田某输油管道的失效情况,对其进行了深入的分析与探讨。
一、失效情况X 油田的某输油管道在使用几年后,出现了严重的泄漏事故。
事故原因初步判断是由于管道腐蚀导致的管壁破裂。
针对此事故,我们需要对输油管道进行全面的失效分析。
二、失效原因1.腐蚀:管道输送石油会产生许多化学反应,如水合、酸化和盐析等,从而对管道产生腐蚀作用。
此外,管道本身的物理结构也可能导致腐蚀的发生,如内腔的凸起、缺陷、裂纹等。
2.疲劳:长期使用的管道往往脆性变化越来越明显,可能会引起逐渐累积的疲劳损伤,从而导致管道的失效。
3.外界损伤:外部因素也是导致管道失效的一个主要因素。
可能会遭受碰撞或者外界损伤,从而导致管道失效。
4.焊接问题:管道的焊接质量也是导致管道失效的重要原因之一。
焊接的不良质量,如焊缝缺陷、焊接接头位于高应力部位等,会使得管道的强度出现大幅下降。
三、分类分析1.腐蚀失效经过对管道进行出土检查,发现大量的管材内外表面覆盖着薄薄的黑色氧化物,严重影响了管壁的强度。
进一步分析,发现这是由于不同级别的腐蚀导致的。
其中深层次的腐蚀在失效过程中占据了主要地位。
我们从获取的数据中看出,在管道的腐蚀位置处,大量的水合反应和电化学反应正同时进行,从而导致了腐蚀后残余厚度的下降以及局部应力集中,该区域发生了严重疲劳断裂。
同时,我们还发现在管道中存在了大量的缺陷,这说明在制作管材的过程中,存在不当的制造和工艺错误。
在管材生产过程和密封性能测试阶段包含严密的质量控制的步骤之后,应重视各种质量问题和安装后的检查,以避免失效风险的发生。
2.疲劳失效疲劳问题在管道失效中同样占据重要地位。
通常是由于管道内外的载荷引起的,包括管道自身权重、流体传输压力和温度变化等因素。
我们在分析中发现,这个特殊管道的内部应力分布存在明显的变化,主要是由于管道采用线性布置方式导致的。
南海某油田油管腐蚀失效原因分析

22
TOTAL CORROSION CONTROL VOL.35 No.06 JUN. 2021
图5 腐蚀产物SEM图
专论 Monograph
XRD分析进一步证实了腐蚀产物主要是碳酸 盐,如图7所示。 2.3 荧光显微镜探测
in an Oilfield in South China Sea
JIN Xi, FENG Jia-qi, SUN Ji-xing, ZHOU Xiao-jie, YANG Yue-cheng
(CNOOC Changzhou Coating Chemical Research Institute Co., Ltd. Changzhou 213012, China)
如图8所示,样品荧光探测图中无任何荧光显 示,说明其腐蚀产物中无细菌,从而排除掉管线的 腐蚀孔洞是由细菌引起的。
综合以上分析,可以得出该管线腐蚀失效的主 要原因是CO2腐蚀,它在油气工业领域中也被称为 Sweet Corrosion,这种腐蚀实质是CO2气体溶解在水 中生成H2CO3,金属表面接触H2CO3溶液发生电化学 腐蚀。对于CO2的腐蚀机制,有很多学者进行了研
2.2 腐蚀产物的微观分析 针对管线失效部位,取下腐蚀产物样品,对其
形貌(SEM)、元素组成(EDS)及物相(XRD) 进行分析,力图通过材料微观表征技术,得到腐蚀 失效的本质原因。
2.2.1 样品预处理 取失效管件内部腐蚀产物,其形貌如表4所示,
至于研钵中制成粉末,如表4所示。
表4
处理前后样品图片
H++e→H
油管失效原因及检修措施浅析
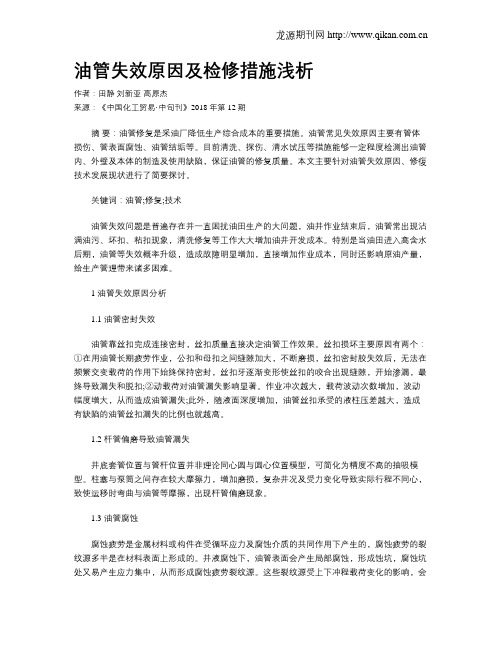
油管失效原因及检修措施浅析作者:田静刘新亚高原杰来源:《中国化工贸易·中旬刊》2018年第12期摘要:油管修复是采油厂降低生产综合成本的重要措施。
油管常见失效原因主要有管体损伤、管表面腐蚀、油管结垢等。
目前清洗、探伤、清水试压等措施能够一定程度检测出油管内、外壁及本体的制造及使用缺陷,保证油管的修复质量。
本文主要针对油管失效原因、修復技术发展现状进行了简要探讨。
关键词:油管;修复;技术油管失效问题是普遍存在并一直困扰油田生产的大问题,油井作业结束后,油管常出现沾满油污、坏扣、粘扣现象,清洗修复等工作大大增加油井开发成本。
特别是当油田进入高含水后期,油管等失效概率升级,造成故障明显增加,直接增加作业成本,同时还影响原油产量,给生产管理带来诸多困难。
1 油管失效原因分析1.1 油管密封失效油管靠丝扣完成连接密封,丝扣质量直接决定油管工作效果。
丝扣损坏主要原因有两个:①在用油管长期疲劳作业,公扣和母扣之间缝隙加大,不断磨损,丝扣密封胶失效后,无法在频繁交变载荷的作用下始终保持密封,丝扣牙逐渐变形使丝扣的咬合出现缝隙,开始渗漏,最终导致漏失和脱扣;②动载荷对油管漏失影响显著。
作业冲次越大,载荷波动次数增加,波动幅度增大,从而造成油管漏失;此外,随液面深度增加,油管丝扣承受的液柱压差越大,造成有缺陷的油管丝扣漏失的比例也就越高。
1.2 杆管偏磨导致油管漏失井底套管位置与管杆位置并非理论同心圆与圆心位置模型,可简化为精度不高的抽吸模型。
柱塞与泵筒之间存在较大摩擦力,增加磨损,复杂井况及受力变化导致实际行程不同心,致使运移时弯曲与油管等摩擦,出现杆管偏磨现象。
1.3 油管腐蚀腐蚀疲劳是金属材料或构件在受循环应力及腐蚀介质的共同作用下产生的,腐蚀疲劳的裂纹源多半是在材料表面上形成的。
井液腐蚀下,油管表面会产生局部腐蚀,形成蚀坑,腐蚀坑处又易产生应力集中,从而形成腐蚀疲劳裂纹源。
这些裂纹源受上下冲程载荷变化的影响,会快速的扩展,最终导致油管早期失效。
某输油管道腐蚀穿孔原因
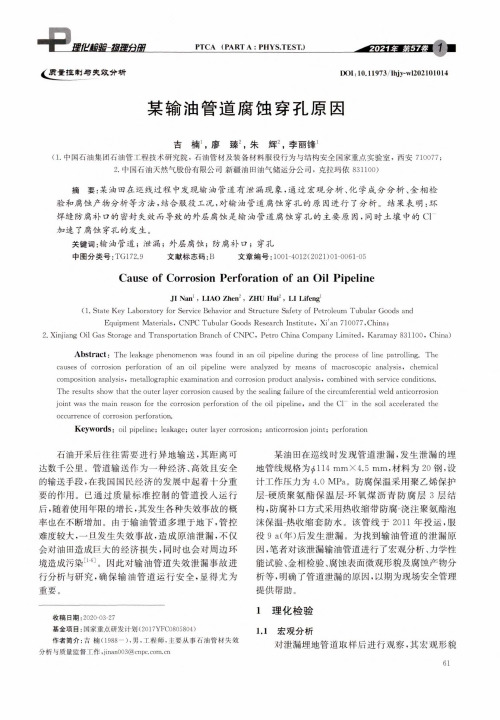
理化龜验-物理分册PTCA(PART A:PHVS.TEST.)1■DOI:10.11973/ll\jy-wl202101014某输油管道腐蚀穿孔原因吉楠「,廖臻?,朱辉',李丽锋'(1.中国石油集团石油管工程技术研究院,石油管材及装备材料服役行为与结构安全国家重点实验室,西安710077;2.中国石油天然气股份有限公司新疆油田油气储运分公司,克拉玛依831100)摘要:某油田在巡线过程中发现输油管道有泄漏现象,通过宏观分析、化学成分分析、金相检验和腐蚀产物分析等方法,结合服役工况,对输油管道腐蚀穿孔的原因进行了分析。
结果表明:环焊缝防腐补口的密封失效而导致的外层腐蚀是输油管道腐蚀穿孔的主要原因,同时土壤中的C1加速了腐蚀穿孔的发生。
关键词:输油管道;泄漏;外层腐蚀;防腐补口;穿孔中图分类号:TG172.9文献标志码:B文章编号:1001-4012(2021)01-0061-05Cause of Corrosion Perforation of an Oil PipelineJI Nan1,LIAO Zhen2,ZHU Hui2,LI Lifeng1(1.State Key laboratory for Service Behavior and Structure Safety of Petroleum Tubular Goods andEquipment Materials,CNPC Tubular Goods Research Institute»Xi'an710077,China;2.Xinjiang Oil Gas Storage and Transportation Branch of CNPC,Petro China Company Limited,Karamay831100,China)Abstract:The leakage phenomenon was found in an oil pipeline during the process of line patrolling.The causes of corrosion perforation of an oil pipeline were analyzed by means of macroscopic analysis,chemical composition analysis,metallographic examination and corrosion product analysis,combined with service conditions.The results show that the outer layer corrosion caused by the sealing failure of the circumferential weld anticorrosion joint was the main reason for the corrosion perforation of the oil pipeline,and the Cl in the soil accelerated the occurrence of corrosion perforation.Keywords:oil pipeline;leakage;outer layer corrosion;anticorrosion joint;perforation石油开采后往往需要进行异地输送,其距离可达数千公里。
油田抽油机井油管失效原因分析

油田抽油机井油管失效原因分析在油田开采作业中,抽油机井油管是起着重要作用的石油生产设备,同时也是容易出现失效的部件之一。
油管失效会导致生产受阻、安全事故等问题,因此对油管失效原因进行深入分析是非常重要的。
本文将从材料、设计、使用等方面分析油田抽油机井油管失效的原因。
一、材料原因油管作为石油生产中承受压力和腐蚀的重要部件,其材料质量直接影响油管的使用寿命和安全性。
常见的油管材料包括碳素钢、合金钢、不锈钢等。
油管材料选用不当或者质量不过关是导致油管失效的重要原因之一。
1. 选材不当油管的工作环境通常受到高温、高压和腐蚀等多种因素的影响,因此选材时需要考虑各种因素,选择适合的耐高温、耐腐蚀性能的材料。
如果选材不当,可能导致油管在使用过程中出现腐蚀、疲劳、开裂等问题,最终导致失效。
2. 材料质量不合格油管制造材料的质量是决定油管使用寿命的关键因素之一。
如果油管的材料质量不合格,存在内部缺陷、夹杂物等问题,易导致油管在使用过程中出现断裂、开裂等失效问题。
二、设计原因油管的设计合理性直接关系到其受力性能和使用寿命,设计不合理是导致油管失效的重要原因之一。
1. 结构设计不合理油管在使用过程中承受着来自地层压力、泵送压力等多方面的力的作用,如果结构设计不合理,可能导致油管受力不均,从而加速油管的疲劳破坏。
2. 连接设计不合理油管在井口、井筒等地方需要进行连接,连接部分的设计是否合理直接关系到油管的安全性。
如果连接设计不合理,易导致连接部位出现泄漏、腐蚀等问题,加速油管失效。
三、使用原因油管在使用过程中的维护、保养、操作等因素也是导致油管失效的重要原因之一。
1. 维护保养不到位油管在使用过程中需要进行定期的维护和保养,包括防腐处理、泄漏检查、防震等措施。
如果维护保养不到位,油管易受到外部环境的影响,加速失效。
2. 操作不当油管的操作不当也是导致油管失效的重要原因之一。
例如在油管工作压力范围之外使用、工作温度范围之外使用、操作超过油管的承受范围等,都可能导致油管失效。
某集输管线穿孔失效原因分析及对策
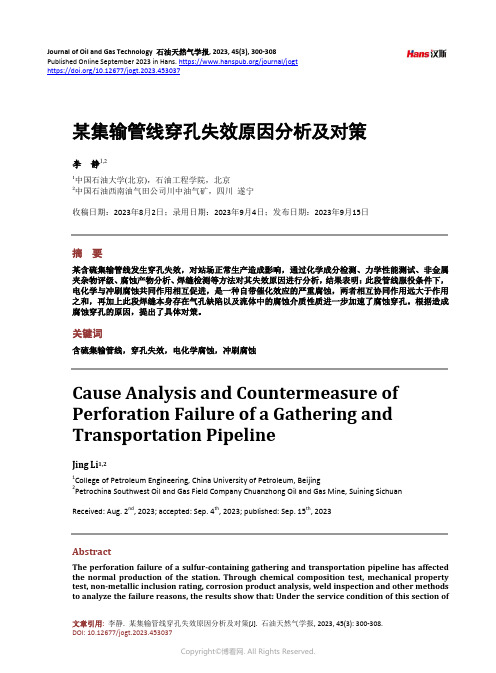
Journal of Oil and Gas Technology 石油天然气学报, 2023, 45(3), 300-308 Published Online September 2023 in Hans. https:///journal/jogt https:///10.12677/jogt.2023.453037某集输管线穿孔失效原因分析及对策李 静1,21中国石油大学(北京),石油工程学院,北京2中国石油西南油气田公司川中油气矿,四川 遂宁收稿日期:2023年8月2日;录用日期:2023年9月4日;发布日期:2023年9月15日摘要某含硫集输管线发生穿孔失效,对站场正常生产造成影响,通过化学成分检测、力学性能测试、非金属夹杂物评级、腐蚀产物分析、焊缝检测等方法对其失效原因进行分析,结果表明:此段管线服役条件下,电化学与冲刷腐蚀共同作用相互促进,是一种自带催化效应的严重腐蚀,两者相互协同作用远大于作用之和,再加上此段焊缝本身存在气孔缺陷以及流体中的腐蚀介质性质进一步加速了腐蚀穿孔。
根据造成腐蚀穿孔的原因,提出了具体对策。
关键词含硫集输管线,穿孔失效,电化学腐蚀,冲刷腐蚀Cause Analysis and Countermeasure of Perforation Failure of a Gathering and Transportation PipelineJing Li 1,21College of Petroleum Engineering, China University of Petroleum, Beijing2Petrochina Southwest Oil and Gas Field Company Chuanzhong Oil and Gas Mine, Suining SichuanReceived: Aug. 2nd , 2023; accepted: Sep. 4th , 2023; published: Sep. 15th , 2023AbstractThe perforation failure of a sulfur-containing gathering and transportation pipeline has affected the normal production of the station. Through chemical composition test, mechanical property test, non-metallic inclusion rating, corrosion product analysis, weld inspection and other methods to analyze the failure reasons, the results show that: Under the service condition of this section of李静pipeline, electrochemical and scour corrosion act together to promote each other, which is a se-rious corrosion with catalytic effect. Their synergistic effect is far greater than the sum of their ef-fects. In addition, the porosity defects in this section of weld and the nature of corrosive medium in the fluid further accelerate the corrosion perforation. According to the causes of corrosion per-foration, the countermeasures are put forward.KeywordsSulfur-Bearing Gathering and Transportation Pipeline, Perforation Failure, Electrochemical Corrosion, Scour CorrosionCopyright © 2023 by author(s) and Hans Publishers Inc.This work is licensed under the Creative Commons Attribution International License (CC BY 4.0)./licenses/by/4.0/1. 引言某含硫集输管线气液混输,输送介质包括未经处理的原料气和为气田水,日输气量15万方,日输水量大于200方,运行温度40℃~70℃,CO 2含量为1.739%,H 2S 含量为0.563%,气田水为弱酸性,pH 值为6.55,矿化度118.429 g/L ,Ca 2+浓度2470 mg/L ,Na +浓度33,331 mg/L ,Cl −浓度30,000~90,000 mg/L ,水型为氯化钙水型。
_115_4输油管线穿孔原因分析
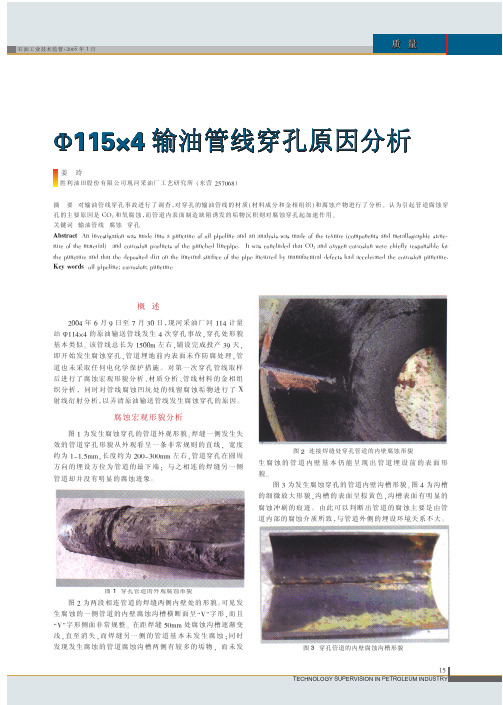
图 ! 穿孔管道的外观腐蚀形貌
图 % 为两段相连管道的焊缝两侧内壁处的形貌"可见发 生 腐 蚀 的 一 侧 管 道 的 内 壁 腐 蚀 沟 槽 横 断 面 呈 %( & 字 形 ! 而 且 % ( & 字 形 侧 面 非 常 规 整 " 在 距 焊 缝 #&$$ 处 腐 蚀 沟 槽 逐 渐 变 浅 !直 至 消 失 !而 焊 缝 另 一 侧 的 管 道 基 本 未 发 生 腐 蚀 $同 时 发现发生腐蚀的管道腐蚀沟槽两侧有较多的垢物! 而未发
!7, 溶 解 在 水 中 以 后 便 形 成 碳 酸 ! 9,!7-"# 碳 酸 在 水 中
发生电离而形成酸性环境’
图 # 未腐蚀管道横截面的显微组织
9,!7-" 94"9!7-8 9!7-8"94"!7-,8
发 生 电 化 学 腐 蚀 的 阴 %阳 极 过 程 如 下 ’ 阳 极 过 程 ’ 368,6"36,4 阴 极 过 程 ’ ,944,6" ,9"9,# 因 此 !7, 腐 蚀 所 形 成 的 最 终 腐 蚀 产 物 为 36!7- # 这 就 是 5 射 线 衍 射 产 物 中 出 现 36!7- 的 原 因 $ !, " 氧 腐 蚀
图 " 连接焊缝处穿孔管道的内壁腐蚀形貌
生腐蚀的管道内壁基本仍能呈现出管道埋设前的表面形 貌" 图 ’ 为发生腐蚀穿孔的管道内壁沟槽形貌"图 ) 为沟槽 的 细 微 放 大 形 貌 !沟 槽 的 表 面 呈 棕 黄 色 !沟 槽 表 面 有 明 显 的 腐蚀冲刷的痕迹" 由此可以判断出管道的腐蚀主要是由管 道 内 部 的 腐 蚀 介 质 所 致 !与 管 道 外 侧 的 埋 设 环 境 关 系 不 大 "
油田地面集输管线腐蚀穿孔分析及防治措施

田的价格也在经历了几个阶段,生产的规格也经历了几个大阶段。
之前油田的价格非常的便宜,不仅是因为生产量大,同时使用的范围也不广。
而现在油田资源变得越来越稀少,消耗变得越来越多,所以价格也会变得越来越高昂[1]。
因为现在油气储产量不断增长,近年来中国油田企业加大勘探开发力度,油气被开采的越来越多,所以储存油气的装置也在不断的改革创新、突破。
1.1 防腐层被损坏或老化根据现在生活来看,集输管线腐蚀出现老化的原因,大部分都是由于这些因素所影响的。
首先是由于周围生活的自然环境所影响的,这些是导致集输管线出现老化的最重要的原因。
因为集输管线在使用的过程中,会长时间地暴露在空气中,与空气大面积的接触,风吹日晒,并受一些气候和天气气压的影响,会使集输管线老化比较快。
集输管线如果严重的话会出现穿孔的现象,在操作人员对技术管线进行焊接和制作时,焊接的某些部位也会因为时间的流逝而出现一些裂纹。
随着集输管线被长时间的使用,这些裂纹会被放大,变得更加影响集输管线的正常运行。
裂缝如果过大的话会使钢管和表层出现分开的现象,如果遇到恶劣的天气,如风雪交加的天气会使裂缝变得更加大。
这些裂缝如果不被及时修复,将会出现腐蚀穿孔的现象。
在集输管线表面有一层防腐剂,如果这些防腐剂经过风吹日晒脱离之后,将会失去自身的粘结性。
另外由于其他因素的影响,集输管线在运输的过程中,工作人员在进行安装工作时0 引言原油运输的主要方式就是集输管线。
管线运输在使用的过程中,由于受到其他因素的影响,使得集输管线被腐蚀或被侵害。
同时,也是因为设计人员在进行管线运输设计时,没有对管线的整体进行进一步地完善,没有将新型的设计技术和设计理念运用到管线运输中。
政府机构管理人员经过研究发现,集输管线内的一些管道会出现大量的辐射情况,远远地高于长输管道,管线运输的管道被腐蚀的速度较快。
其输管线在使用的过程中,外侧由于受到气温和气压的影响,很容易受到油田采油的影响和腐蚀。
管线管管端裂纹的产生原因分析与预防
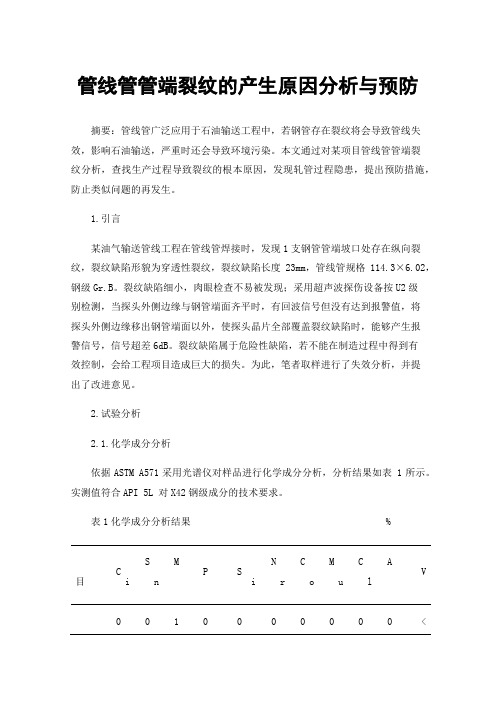
管线管管端裂纹的产生原因分析与预防摘要:管线管广泛应用于石油输送工程中,若钢管存在裂纹将会导致管线失效,影响石油输送,严重时还会导致环境污染。
本文通过对某项目管线管管端裂纹分析,查找生产过程导致裂纹的根本原因,发现轧管过程隐患,提出预防措施,防止类似问题的再发生。
1.引言某油气输送管线工程在管线管焊接时,发现1支钢管管端坡口处存在纵向裂纹,裂纹缺陷形貌为穿透性裂纹,裂纹缺陷长度23mm,管线管规格114.3×6.02,钢级Gr.B。
裂纹缺陷细小,肉眼检查不易被发现;采用超声波探伤设备按U2级别检测,当探头外侧边缘与钢管端面齐平时,有回波信号但没有达到报警值,将探头外侧边缘移出钢管端面以外,使探头晶片全部覆盖裂纹缺陷时,能够产生报警信号,信号超差6dB。
裂纹缺陷属于危险性缺陷,若不能在制造过程中得到有效控制,会给工程项目造成巨大的损失。
为此,笔者取样进行了失效分析,并提出了改进意见。
2.试验分析2.1.化学成分分析依据ASTM A571采用光谱仪对样品进行化学成分分析,分析结果如表 1所示。
实测值符合API 5L 对X42钢级成分的技术要求。
表1化学成分分析结果 %项目CSiMnP SNiCrMoCuAlV实0010000000<测.10.23.11.008.001.02.11.02.04.0310.01值2.2.力学性能试验依据ASTM A370-2021标准要求进行拉伸试验、冲击试验(纵向、10x5mm、V 型缺口、20℃)、维氏硬度试验。
拉伸试验数据表明,试验结果满足标准要求;冲击试验、硬度试验虽然在标准中没有具体要求,但从试验数据来看,冲击功和硬度值与原管体试验数据基本一致。
2.3.金相检验在样品基体部位取剖面试样,抛光后经硝酸酒精溶液侵蚀,用 ZEISS 光学显微镜进行显微组织观察,结果为回火贝氏体和铁素体,未见异常组织。
基体晶粒度为9.0级,实测值符合API 5L 第46版对X42钢级成分的技术要求。
关于油管失效原因及防范措施的分析
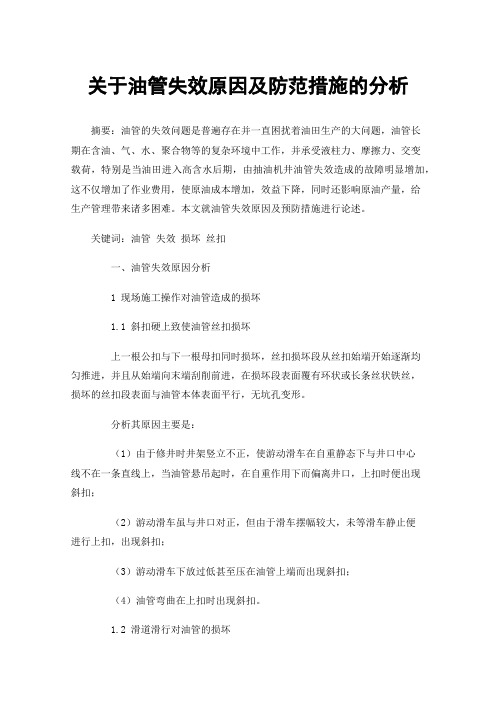
关于油管失效原因及防范措施的分析摘要:油管的失效问题是普遍存在并一直困扰着油田生产的大问题,油管长期在含油、气、水、聚合物等的复杂环境中工作,并承受液柱力、摩擦力、交变载荷,特别是当油田进入高含水后期,由抽油机井油管失效造成的故障明显增加,这不仅增加了作业费用,使原油成本增加,效益下降,同时还影响原油产量,给生产管理带来诸多困难。
本文就油管失效原因及预防措施进行论述。
关键词:油管失效损坏丝扣一、油管失效原因分析1 现场施工操作对油管造成的损坏1.1 斜扣硬上致使油管丝扣损坏上一根公扣与下一根母扣同时损坏,丝扣损坏段从丝扣始端开始逐渐均匀推进,并且从始端向末端刮削前进,在损坏段表面覆有环状或长条丝状铁丝,损坏的丝扣段表面与油管本体表面平行,无坑孔变形。
分析其原因主要是:(1)由于修井时井架竖立不正,使游动滑车在自重静态下与井口中心线不在一条直线上,当油管悬吊起时,在自重作用下而偏离井口,上扣时便出现斜扣;(2)游动滑车虽与井口对正,但由于滑车摆幅较大,未等滑车静止便进行上扣,出现斜扣;(3)游动滑车下放过低甚至压在油管上端而出现斜扣;(4)油管弯曲在上扣时出现斜扣。
1.2 滑道滑行对油管的损坏(1)油管在滑道上滑行时,当滑行油管长度大于滑道长度时,滑行时对丝扣损坏很大。
小滑车中心部位的胶皮由于长期使用已经损坏,不能有效的保护油管的丝扣部位。
(2)油管滑行时对滑道油管的损坏。
由于油管在滑道上滑行,从而使滑道油管本体形成痕迹,随着滑行根数增加,沟痕越深。
而且这样的沟痕通常表现为越靠近井口,沟痕越浅。
分析其原因主要是:各基层作业施工小队主要领导责任心不强,队伍管理制度不健全,职工质量意识淡薄,使职工的低标准、老毛病、坏习惯没有彻底根除;没有严格执行井下作业施工质量标准,没按“三标”施工;新作业、新形象没有得到充分的体现。
1.3 由于击打、碰撞、咬伤等使油管失效(1)作业时由于击打、碰撞在油管表面留下内陷的坑痕,导致管径缩小,活塞通不过造成工序返工或勉强通过而加剧杆、管摩擦导致漏失。
N80油管穿孔失效原因分析
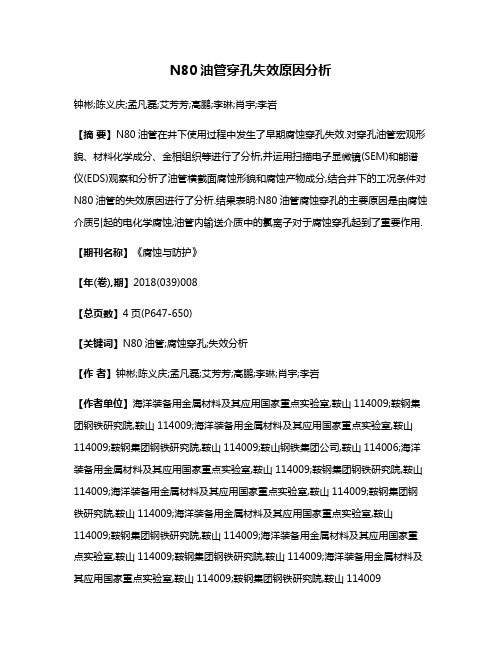
N80油管穿孔失效原因分析钟彬;陈义庆;孟凡磊;艾芳芳;高鹏;李琳;肖宇;李岩【摘要】N80油管在井下使用过程中发生了早期腐蚀穿孔失效.对穿孔油管宏观形貌、材料化学成分、金相组织等进行了分析,并运用扫描电子显微镜(SEM)和能谱仪(EDS)观察和分析了油管横截面腐蚀形貌和腐蚀产物成分,结合井下的工况条件对N80油管的失效原因进行了分析.结果表明:N80油管腐蚀穿孔的主要原因是由腐蚀介质引起的电化学腐蚀,油管内输送介质中的氯离子对于腐蚀穿孔起到了重要作用.【期刊名称】《腐蚀与防护》【年(卷),期】2018(039)008【总页数】4页(P647-650)【关键词】N80油管;腐蚀穿孔;失效分析【作者】钟彬;陈义庆;孟凡磊;艾芳芳;高鹏;李琳;肖宇;李岩【作者单位】海洋装备用金属材料及其应用国家重点实验室,鞍山114009;鞍钢集团钢铁研究院,鞍山114009;海洋装备用金属材料及其应用国家重点实验室,鞍山114009;鞍钢集团钢铁研究院,鞍山114009;鞍山钢铁集团公司,鞍山114006;海洋装备用金属材料及其应用国家重点实验室,鞍山114009;鞍钢集团钢铁研究院,鞍山114009;海洋装备用金属材料及其应用国家重点实验室,鞍山114009;鞍钢集团钢铁研究院,鞍山114009;海洋装备用金属材料及其应用国家重点实验室,鞍山114009;鞍钢集团钢铁研究院,鞍山114009;海洋装备用金属材料及其应用国家重点实验室,鞍山114009;鞍钢集团钢铁研究院,鞍山114009;海洋装备用金属材料及其应用国家重点实验室,鞍山114009;鞍钢集团钢铁研究院,鞍山114009【正文语种】中文【中图分类】TG172油管是油气田开发时下入到油井套管内的管柱钢管,是在钻探完成后将原油和天然气从油气层运输到地表的管道,在石油开采过程中,油管的使用量仅次于套管的使用量。
近几年,随着油气田开采条件的不断恶化,油田含水量越来越高,深层含CO2油气层的开发日益增多,以及注CO2强化采油工艺的推广及普及[1-3],使油田油管及设备的腐蚀问题越来越严重,该问题成为油田和油管生产厂急需解决的重要课题。
某生产井油管腐蚀穿孔的原因
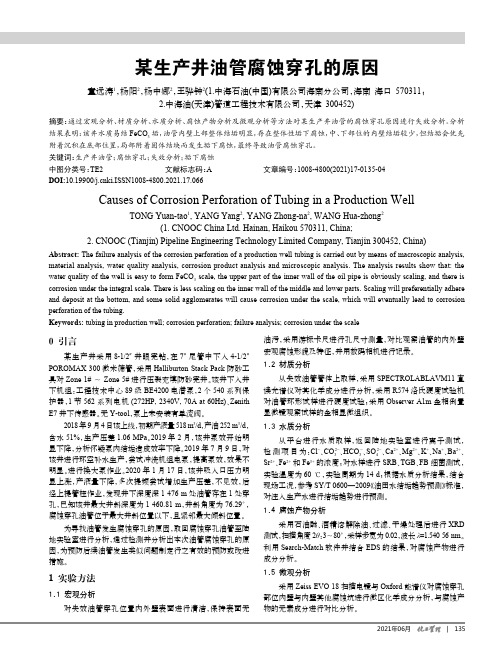
Mo 0.007 3
—
Cu 0.103 ≤0.35
2.2.2 硬度测试
采用 R574 洛氏硬度试验机对油管环形试样进行硬度试验, 检测位置如图 6 所示,检测标准为 ASTM E18-19 Standard Test Methods for Rockwell Hardness of Metallic Materials1, 2,试验结果 如表 2 所示,油管满足 API 5CT 标准中对 L80 钢的硬度要求。
结果表明:该井水质易结 FeCO3 垢,油管内壁上部整体结垢明显,存在整体性垢下腐蚀,中、下部位的内壁结垢较少,但结垢会优先 附着沉积在底部位置,局部附着固体结块而发生垢下腐蚀,最终导致油管腐蚀穿孔。
关键词:生产井油管;腐蚀穿孔;失效分析;垢下腐蚀
中图分类号:TE2
文献标志码:A
文章编号:1008-4800(2021)17-0135-04
进一步观察油管上部管段的垢层,如图 5 所示,清除部分 垢层后,发现底部某些位置存在明显腐蚀坑,见图中标注位置, 符合垢下腐蚀特征。
136 |
2021年06月
图4 油管中部管段内壁非结块位置宏观图 图5 油管上部管段内壁垢层宏观图
综合以上分析,油管外壁未见明显腐蚀,油管的上部管段 与下部、中部管段之间的内壁结垢形式存在差异。下部、中部管 段的内壁底部多处存在附着物结块,结块下明显腐蚀坑,符合 垢下腐蚀特征,上部管段垢层较厚且同样存在垢下腐蚀,推测 垢层差异可能与油管处于井斜最大位置有关,因流速存在变 化,对结垢趋势造成影响。 2.2 材质分析
表 3 金相检验结果
试样 编号
A 薄厚
非金属夹杂物
B
C
D
薄厚薄厚薄 厚
1# 0 0 0 0 0 0 0 1.5
- 1、下载文档前请自行甄别文档内容的完整性,平台不提供额外的编辑、内容补充、找答案等附加服务。
- 2、"仅部分预览"的文档,不可在线预览部分如存在完整性等问题,可反馈申请退款(可完整预览的文档不适用该条件!)。
- 3、如文档侵犯您的权益,请联系客服反馈,我们会尽快为您处理(人工客服工作时间:9:00-18:30)。
78
1 引言
近年来,连续发生某油田原油集输管线破损引发原油泄漏事件,导致大量原油泄漏,污染土壤、林地,甚至水源,严重影响当地老百姓的正常生活,造成巨大的损失。
目前油田上集输管线大部分采用低碳钢无缝钢管焊接而成,因此,对某区域油田低碳钢输油管线失效进行分析具有重大的经济意义和生产应用价值。
2 理化分析2.1 化学分析
使用牛津FOUNDRY-MASTER Pro全谱直读光谱仪对该输油管进行化学成分检测,从表1可知,所检元素含量符合GB/T699—1999《优质碳素结构钢》中20#的规定。
表1 输油管化学元素光谱分析
化学元素C S P Si Mn 20#
0.20
0.008
0.010
0.19
0.42
GB/T699—1999
0.17~0.23≤0.035≤0.0350.17~0.370.35~0.65
2.2 硬度检验
使用威尔逊BH3000布氏硬度计对该输油管进行硬度检测,从表2可知,送检输油管材质硬度符合GB/T699—1999《优质碳素结构钢》中20#的规定。
表2 输油管硬度检验(<156HB10/3000)
试样编号测量值(HB10/3000)
平均值第一次第二次第三次syg-01142.6139.8146.7143.0syg-02147.9146.8148.4147.7syg-03
145.8
148.2
140.3
144.8
2.3 金相组织检验
在腐蚀坑处截取横向金相试样,试样制备好后采用4%硝酸酒精溶液浸蚀。
使用蔡司Axio Observer /Z1进行观察分析,观察到的组织为铁素体+珠光体(图1),金相组织未发现异常。
图1 铁素体+珠光体
2.4 电镜形貌及能谱分析
送检输油管内壁有一孔洞及一腐蚀坑,腐蚀区域呈红褐色,宏观相貌见图2。
图2 输油管内壁空洞宏观形貌图3 管内壁腐蚀形貌
低碳钢输油管穿孔失效分析
张刚刚 马建东 陈汉 杨永霞
长庆油田分公司技术监测中心 陕西 西安 710000
摘要:低碳钢输油管穿孔失效是油田集输管线运行中面临的严重问题之一,会对油田正常生产产生极为不利的影响。
本文对低碳钢输油管穿孔失效的原因进行了实验分析并得出了相关结论。
关键词:输油管 穿孔 原因
Analysis on the low carbon steel pipeline perforation failure
Zhang Ganggang,Ma Jiandong,Chen Han,Yang Yongxia
Technology monitoring center of Changqing Oil field Company Xi ’an Shaanxi 710000
Abstract:Low carbon steelpipelineperforationfailureis a seriousprobleminoil fieldandwillhave an extremelynegative impact on the normal production of oil field.In this paper,the reasons forthe failureoflow-carbon steelpipelineperforation were analyzed experimentallyand drawthe relevantconclusions.
Keywords:
pipeline;perforation;reason
♜2
廱㰗䫿⃣⠟䧘㱼⫭夠⻀寪
♜3䫿⃣⠟傮嗞⻀寪
䘱Ự䗃⋩㇑ᴹаᆄ⍎৺а㞀㲰ඁˈ㞀㲰४ฏ㓒㽀㢢ˈᆿ㿲䊼㿱മ
2
79
在Quanta400扫描电镜下进行变倍观察,腐蚀坑处有较多腐蚀产物,腐蚀产物呈不规则团状块附着,局部腐蚀产物呈结晶状,见图3。
在腐蚀坑处进行EDS电镜能谱分析,其主要成分为C、O、Al、Si、S、Cl、Cr、Mn、Fe,具体结果见图4。
图4 管内壁腐蚀区域EDS能谱成分
表3 EDS能谱半定量分析元素含量元素质量百分比原子百分比
C 32.1856.43
O 18.123.82
Al 0.460.36Si 0.250.19S 0.440.29Cl 2.66 1.58Cr 0.550.22Mn 0.58
0.22
Fe
44.7916.89
20#输油管线,内壁与原油直接接触,内壁氧化锈蚀严重,EDS能谱中检出腐蚀性S及Cl元素,这两种元素形成的离子会与Fe元素发生电化学反应,加速输油管的腐蚀,导致输油管产生孔洞。
通过对20#钢输油管进行化学成分分析、硬度检测、金相
组织观察分析,可知该输油管本身质量符合相关标准规定。
在腐蚀坑处截取横向金相试样,观察到的组织为铁素体加珠光体,断口表面附近晶粒上没有明显的局部塑形变形,可以排除人为钻孔的可能性[1]。
由图2,图3可见到明显的腐蚀产物,断口形貌中未发现应力腐蚀的特征,且20#钢韧性较好,所以应力腐蚀不可能造成材料失效额原因。
结合输油管现场使用情况来看,输送原油压力不超过2MPa,因此可以排除应力腐蚀。
通过图3可发现在接近穿孔断口处有大量的小孔,结合图4内壁腐蚀区域EDS能谱成分分析,在小孔附近发现氯和硫元素的含量比较高,可以断定该材料失效是由于点蚀导致的局部腐蚀造成的。
输油管在内壁无防腐处理,使用过程中,油水混合物中存在大量氯盐、硫化物、环烷酸等物质形成硫腐蚀、硫化氢腐
蚀、氯化铵腐蚀等。
管线内壁原有的凹坑形成缺口,作为阳极迅速腐蚀溶解,进而穿透整个油管壁[2-3]。
3 结论
断口呈现明显的点蚀特征,属于比较典型的局部腐蚀。
一方面是由于原油中含有大量的氯盐、硫化物、环烷酸等腐蚀性介质使得钝化化膜难以形成[4];另一方面输油管道内壁无防腐保护处理,使得腐蚀性物质可以直接和管线接触造成管内壁腐蚀,管线内壁本身存在的凹坑促使点蚀的形成,从而造成局部腐蚀,造成输油管道腐蚀穿孔失效。
参考文献
[1]朱远志,沈燕.低碳钢输油管穿孔原因分析[J].机械工
程材料,2007.10(31):70-72
[2]邓民宪,张永凯,袁玉柱.埋地输油管道失效原因分析[J].腐蚀科学与防护技术,1999,11(6):373-375
[3]牛耀玉,李胜彪,梁庚白.宝浪油田联合站污水腐蚀性研究[J].石油化工与腐蚀,2003(5):31-35
[4]李自力,冯叔初白.油气混输管道的内壁腐蚀 [J].油气田地面工程,1996(1):
47-52.
ݳ㍐䍘䟿Ⲯ࠶∄ᆀⲮ࠶∄C 32.1856.43 O 18.123.82
Al 0.460.36 Si 0.250.19
S 0.440.29 Cl 2.66 1.58 Cr
0.550.22 Mn 0.580.22 Fe 44.7916.89
20#䗃⋩㇑㓯ˈо⋩ⴤ᧕᧕䀖ˈ≗ॆ䬸㲰ѕ䟽ˈEDS 㜭䉡ѝỰࠪ㞀㲰ᙗS ৺Cl ݳ㍐ˈ䘉єݳ㍐ᖒᡀⲴᆀՊоFe ݳ㍐ਁ⭏⭥ॆᆖ৽ᓄˈ࣐䙏
䗃⋩㇑Ⲵ㞀㲰ˈሬ㠤䗃⋩㇑ӗ⭏ᆄ⍎DŽ
的腐蚀水平。
(2)要使回注污水水质达标,处理水药剂投加量加大,使生产成本过高,有时为了降低运行成本,只能减少或暂停药剂的投加,造成出水水质不稳定,为注水带来很多麻烦。
(3)回注污水在沿程回注过程中,由于流速、压力、温度、细菌等方面因素的影响造成二次污染,使原本不合格的水质变的合格率更低,这是水质达标率低的一个重要原因。
(4)站内药剂投加的操作及维护往往不能按设计实施,使得设计思路的综合效应无法实现,这也是水处理站运行效率低的原因之一。
(5)我国许多油田水处理站的自动化程度不高,手动操作多,工人劳动强度大,而且一般比较笨重,不易操作管理,生产效益低。
(6)从我国各主要油田污水处理回注站所采用的净水工
艺可以看出,我国油田污水处理回注的整体技术、工艺、管理水平不是太高,这也是我国大部分油田污水处理回注站处理效率低、水质无法达标的主要原因之一。
4 建议
对油田污水处理工作的几点建议:(1)进一步完善注水水质标准;(2)深入开展高含水期油气水处理技术研究;(3)加强药剂使用的科学性,提高污水处理效果;(4)配套污水站过滤设施;(5)强化运行管理。
参考文献
[1]杨云霞,张晓健.我国主要油田污水处理技术现状及问题[J].油气田地面工程,2011(1)
[2]蔡永春.温米油田水处理工艺研究与应用[D].东北石油大学硕士论文,2011(5)
(上接第70页)。