BSP170P_Rev2.52_pdf
MAX17127白光LED驱动器评估套件说明书
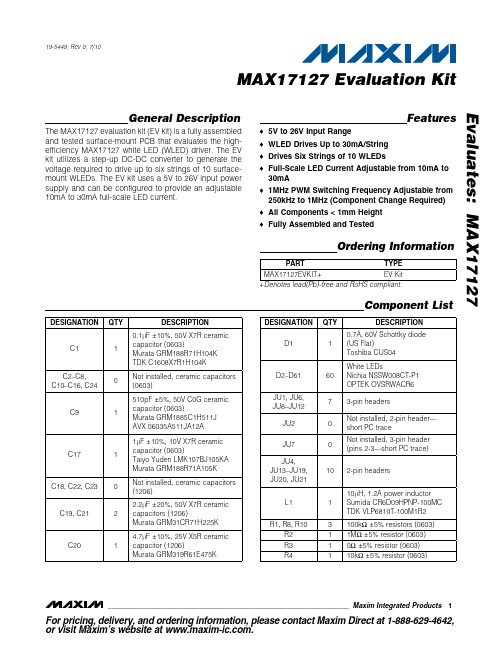
_______________________________________________________________ Maxim Integrated Products 1For pricing, delivery, and ordering information, please contact Maxim Direct at 1-888-629-4642, or visit Maxim’s website at .MAX17127 Evaluation KitEvaluates: MAX17127General DescriptionThe MAX17127 evaluation kit (EV kit) is a fully assembled and tested surface-mount PCB that evaluates the high-efficiency MAX17127 white LED (WLED) driver. The EV kit utilizes a step-up DC-DC converter to generate the voltage required to drive up to six strings of 10 surface-mount WLEDs. The EV kit uses a 5V to 26V input power supply and can be configured to provide an adjustable 10mA to 30mA full-scale LED current.FeaturesS 5V to 26V Input RangeS WLED Drives Up to 30mA/String S Drives Six Strings of 10 WLEDsS Full-Scale LED Current Adjustable from 10mA to30mAS 1MHz PWM Switching Frequency Adjustable from250kHz to 1MHz (Component Change Required)S All Components < 1mm Height S Fully Assembled and TestedOrdering Information19-5449; Rev 0; 7/10+Denotes lead(Pb)-free and RoHS compliant.Component ListPARTTYPEMAX17127EVKIT+EV Kit DESIGNATIONQTYDESCRIPTIONC110.1F F Q 10%, 50V X7R ceramic capacitor (0603)Murata GRM188R71H104K TDK C1608X7R1H104KC2–C8, C10–C16, C24Not installed, ceramic capacitors (0603)C91510pF Q 5%, 50V C0G ceramic capacitor (0603)Murata GRM1885C1H511J AVX 06035A511JA12A C1711F F Q 10%, 10V X7R ceramic capacitor (0603)Taiyo Yuden LMK107BJ105KA Murata GRM188R71A105K C18, C22, C230Not installed, ceramic capacitors (1206)C19, C2122.2F F Q 20%, 50V X7R ceramic capacitors (1206)Murata GRM31CR71H225K C2014.7F F Q 10%, 25V X5R ceramic capacitor (1206)Murata GRM319R61E475KDESIGNATIONQTY DESCRIPTIOND110.7A, 60V Schottky diode (US Flat)Toshiba CUS04D2–D6160White LEDsNichia NSSW008CT-P1OPTEK OVSRWACR6JU1, JU6, JU8–JU1273-pin headersJU20Not installed, 2-pin header—short PC traceJU70Not installed, 3-pin header (pins 2-3—short PC trace)JU4, JU13–JU19, JU20, JU21102-pin headersL1110F H, 1.2A power inductor Sumida CR6D09HPNP-100MC TDK VLP6810T-100M1R2R1, R8, R103100k I Q 5% resistors (0603)R211M I Q 5% resistor (0603)R310I Q 5% resistor (0603)R4110k I Q 5% resistor (0603)MAX17127 Evaluation Kit E v a l u a t e s : M A X 171272 ______________________________________________________________________________________*EP = Exposed pad.Component List (continued)Component SuppliersNote: Indicate that you are using the MAX17127 when contacting these component suppliers.Quick StartRecommended Equipment• MAX17127 EV kit• 5V to 26V power supply (VIN)ProcedureThe EV kit is fully assembled and tested. Follow the steps below to verify board operation. Caution: Do not turn on the power supply until all connections are completed.1) On the EV kit, verify that the shunts are installed, asshown in Table 1.2) Connect the positive terminal of the VIN powersupply to the VIN pad. Connect the ground terminal of the VIN power supply to the PGND pad.3) Set the VIN power supply to 12V and enable its output.4) Verify that the six strings of WLEDs are on.Detailed Description of HardwareThe MAX17127 evaluation kit (EV kit) operates on a 5V to 26V wide-input voltage range and provides adjust-able 10mA to 30mA full-scale LED current. The EV kit utilizes a step-up DC-DC converter to generate the voltage required to drive up to six strings of 10 surface-mount WLEDs.Table 1. Default Shunt PositionsSUPPLIERPHONE WEBSITEAVX CorporationMurata Electronics North America, Nichia OPTEK Technologies Sumida Taiyo Yuden TDK Corp.847-803-6100Toshiba America Electronic Components, /taec DESIGNATIONQTY DESCRIPTIONR5182.5k I Q 1% resistor (0603)R61 2.21M I Q 1% resistor (0603)R7171.5k I Q 1% resistor (0603)R110Not installed, resistor (0603)R120Not installed, multiturn potentiometerR142500k I multiturn potentiometerDESIGNATIONQTYDESCRIPTIONU11Six-string WLED driver (20 TQFN-EP*)Maxim MAX17127ETP+ —17Shunts—1PCB: MAX17127 EVALUATION KIT+JUMPER SHUNT POSITIONJU1, JU6, JU8–JU121-2JU4, JU14, JU15, JU17–JU20, JU21Not installed JU13, JU16InstalledMAX17127 Evaluation KitEvaluates: MAX17127_______________________________________________________________________________________ 3Table 3. Jumper Function (JU13)Table 2. Jumper Function (JU1, JU8–JU12)*Default position.*Default position.White LED String ConfigurationAs configured, the EV kit is assembled with six strings of 10 WLEDs. Each string has an associated 3-pin header (JU1, JU8–JU12) and feedback pin (FB1–FB6). The function of the 3-pin jumpers is summarized in Table 2. To evaluate the EV kit with off-board WLED strings, see the Off-Board WLED String Configuration section.Off-Board WLED String ConfigurationThe EV kit can also be used to drive off-board WLED strings. To evaluate external WLED strings, reconfigure shunts from jumpers JU1 and JU8–JU12. See Table 2 for jumpers JU1 and JU8–JU12 configuration and Table 3 for jumper JU13 configuration. Removing these jump-ers effectively disconnects the on-board WLED strings between the output and feedback pins, allowing the connection of external WLED strings. For each external WLED string, connect the cathode terminal of the string to the corresponding feedback pad (FB1–FB6) and connect the anode terminal of the string to the VOUT pad. Once the external WLED strings are connected between the VOUT pad and the FB1–FB6 pins, the EV kit can be evaluated in the same manner as the on-board WLED strings. Evaluating more than 10 WLEDs per string may require compo-nent changes. Refer to the MAX17127 IC data sheet for component selections.Enable (EN)The EV kit features 2-pin jumper JU16 to control the active-low shutdown input. Drive EN high to place the device in normal operation. If the JU16 shunt is removed, an internal 200k I (typ) pulldown resistor places the device in disabled mode. See Table 4 for shunt positions.Brightness Control by PWMSignal Input (PWM)The EV kit features 2-pin jumper JU20 to implement brightness control through the PWM signal input. See Table 5 for shunt positions.LED String CapacitanceIn some LCD panel applications, a 0.1F F (typ) capaci-tor (C LED ) is placed in parallel with each LED string to improve ESD immunity. As such, the EV kit provides a footprint across each LED string for optional C LED .Full-Scale LED Current Adjustment (ISET)The EV kit features 3-pin jumper JU6, along with R8 and R14, to set the full-scale LED current. The resistance from ISET to AGND controls the full-scale current in each LED string according to the following equation:LED(MAX)180k I 20mAR8R14Ω=× +where R8 is a 100k I resistor and R14 is a 500k I poten-tiometer. See Table 6 for jumper JU6 settings.Switching-Frequency Selection (FSLCT)The EV kit is configured to operate at 1MHz, but providesthe option to set the switching frequency of the step-up DC-DC converter from 250kHz to 1MHz. The switching frequency is set by adjusting the resistance from FSLCT to AGND according to the following equation:SW 100k f 1MHz R10Ω=×Changing the switching frequency might require differ-ent converter components (refer to the MAX17127 IC data sheet for proper component selections).Table 4. Jumper Function (JU16)*Default position.SHUNT POSITION EN PINMAX17127Installed*Connected to VDDIO Enabled Not installed Internally connected to AGNDDisabledSHUNT POSITION FB_ PINSTRING_1-2*Connected to cathodeof WLED string Enabled 2-3Connected to AGND Disabled Not installed Connect to an externalWLED stringOn-board WLED string not usedSHUNT POSITIONVOUTInstalled*Connected to anodes of on-boardWLED strings Not installed Connect to anodes of off-boardWLED stringsMAX17127 Evaluation Kit E v a l u a t e s : M A X 171274 ______________________________________________________________________________________Table 5. Jumper Function (JU20)Table 6. Jumper Function (JU6)*Default position.*Default position.SHUNT POSITION PWM PIN PWM DUTY CYCLE OF LED CURRENTInstalled Connected to AGND Zero Not installed* Connected to VDDIOthrough R2Maximum (100%)Not installedConnect to an exter-nal PWM signal (0.1kHz to 25kHz)Follows the signal applied at PWM padSHUNT POSITION ISET PIN I LED(MAX)1-2*Connected to AGND through R8 and R14Adjustable from 10mA to 30mA 2-3Connected to AGND0.3mA (typ)MAX17127 Evaluation KitEvaluates: MAX17127 Array_______________________________________________________________________________________ 5MAX17127 Evaluation Kit E v a l u a t e s : M A X 171276 ______________________________________________________________________________________MAX17127 Evaluation KitEvaluates: MAX17127 Array_______________________________________________________________________________________ 7MAX17127 Evaluation Kit E v a l u a t e s : M A X 171278 ______________________________________________________________________________________Maxim cannot assume responsibility for use of any circuitry other than circuitry entirely embodied in a Maxim product. No circuit patent licenses are implied. Maxim reserves the right to change the circuitry and specifications without notice at any time.Maxim Integrated Products, 120 San Gabriel Drive, Sunnyvale, CA 94086 408-737-7600 9© 2010 Maxim Integrated ProductsMaxim is a registered trademark of Maxim Integrated Products, Inc.MAX17127 Evaluation KitEvaluates: MAX17127Revision HistoryREVISION NUMBERREVISION DATE DESCRIPTIONPAGES CHANGED7/10Initial release—。
BZT52系列单极性电源芯片数据手册说明书

BZT52 seriesSingle Zener diodes in a SOD123 packageRev. 1 — 16 March 2017Product data sheet1Product profile1.1General descriptionGeneral-purpose Zener diodes in a SOD123 small Surface-Mounted Device (SMD)plastic package.1.2Features and benefits•Total power dissipation: ≤ 590 mW•Wide working voltage range: nominal 2.4 V to 75 V (E24 range)•Small plastic package suitable for surface-mounted design •Low differential resistance •AEC-Q101 qualified1.3Applications•General regulation functions1.4Quick reference data[1]Pulse test: t p ≤ 300 μs; δ ≤ 0.02.[2]Device mounted on an FR4 Printed-Circuit Board (PCB), single-sided copper, tin-plated and standard footprint.[3]Device mounted on an FR4 PCB, single-sided copper, tin-plated, mounting pad for cathode 1 cm 2.Single Zener diodes in a SOD123 package 2Pinning information[1]The marking bar indicates the cathode.3Ordering information[1]The series consists of 37 types with nominal working voltages from 2.4 V to 75 V.4MarkingSingle Zener diodes in a SOD123 package 5Limiting valuesTable 5. Limiting valuesIn accordance with the Absolute Maximum Rating System (IEC 60134).[1]t p = 100 μs; square wave; T j = 25 °C prior to surge.[2]Device mounted on an FR4 PCB, single-sided copper, tin-plated and standard footprint.[3]Device mounted on an FR4 PCB, single-sided copper, tin-plated, mounting pad for cathode 1 cm2.6Thermal characteristics[1]Device mounted on an FR4 Printed-Circuit Board (PCB),single-sided copper, tin-plated and standard footprint.[2]Device mounted on an FR4 PCB, single-sided copper, tin-plated, mounting pad for cathode 1 cm2.[3]Soldering point of cathode tab.7CharacteristicsTable 7. CharacteristicsT = 25 °C unless otherwise specified.[1]Pulse test: t p ≤ 300 μs; δ ≤ 0.02.Single Zener diodes in a SOD123 package Table 8. Characteristics per type; BZT52-C2V4 to BZT52-C24= 25 °C unless otherwise specified.T[1] f = 1 MHz; V R = 0 V.[2]t p = 100 μs; T amb = 25 °C.Single Zener diodes in a SOD123 packageTable 9. Characteristics per type; BZT52-C27 to BZT52-C51T= 25 °C unless otherwise specified.[1] f = 1 MHz; V R = 0 V.[2]t p = 100 μs; T amb = 25 °C.Table 10. Characteristics per type; BZT52-C56 to BZT52-C75T = 25 °C unless otherwise specified.[1] f = 1 MHz; V R = 0 V.[2]t p = 100 μs; T amb = 25 °C.Single Zener diodes in a SOD123 package8Test information8.1Quality informationThis product has been qualified in accordance with the Automotive Electronics Council(AEC) standard Q101 - Stress test qualification for discrete semiconductors, and issuitable for use in automotive applications.Single Zener diodes in a SOD123 package9Package outline10Packing informationTable 11. Packing methodsThe indicated -xxx are the last three digits of the 12NC ordering code.Single Zener diodes in a SOD123 package 11SolderingSingle Zener diodes in a SOD123 package 12Revision historySingle Zener diodes in a SOD123 package 13Legal information13.1 Data sheet status[1]Please consult the most recently issued document before initiating or completing a design.[2]The term 'short data sheet' is explained in section "Definitions".[3]The product status of device(s) described in this document may have changed since this document was published and may differ in case of multipledevices. The latest product status information is available on the Internet at URL .13.2 DefinitionsDraft — The document is a draft version only. The content is still under internal review and subject to formal approval, which may result in modifications or additions. Nexperia does not give any representations or warranties as to the accuracy or completeness of information included herein and shall have no liability for the consequences of use of such information.Short data sheet — A short data sheet is an extract from a full data sheet with the same product type number(s) and title. A short data sheet is intended for quick reference only and should not be relied upon to contain detailed and full information. For detailed and full information see the relevant full data sheet, which is available on request via the local Nexperia sales office. In case of any inconsistency or conflict with the short data sheet, the full data sheet shall prevail.Product specification — The information and data provided in a Product data sheet shall define the specification of the product as agreed between Nexperia and its customer, unless Nexperia and customer have explicitly agreed otherwise in writing. In no event however, shall an agreement be valid in which the Nexperia product is deemed to offer functions and qualities beyond those described in the Product data sheet.13.3 DisclaimersLimited warranty and liability — Information in this document is believed to be accurate and reliable. However, Nexperia does not give any representations or warranties, expressed or implied, as to the accuracyor completeness of such information and shall have no liability for the consequences of use of such information. Nexperia takes no responsibility for the content in this document if provided by an information source outside of Nexperia. In no event shall Nexperia be liable for any indirect, incidental, punitive, special or consequential damages (including - without limitation -lost profits, lost savings, business interruption, costs related to the removal or replacement of any products or rework charges) whether or not such damages are based on tort (including negligence), warranty, breach of contract or any other legal theory. Notwithstanding any damages that customer might incur for any reason whatsoever, Nexperia's aggregate and cumulative liability towards customer for the products described herein shall be limited in accordance with the Terms and conditions of commercial sale of Nexperia.Right to make changes — Nexperia reserves the right to make changesto information published in this document, including without limitation specifications and product descriptions, at any time and without notice. This document supersedes and replaces all information supplied prior to the publication hereof.Suitability for use — Nexperia products are not designed, authorized or warranted to be suitable for use in life support, life-critical or safety-critical systems or equipment, nor in applications where failure or malfunctionof an Nexperia product can reasonably be expected to result in personal injury, death or severe property or environmental damage. Nexperia and its suppliers accept no liability for inclusion and/or use of Nexperia products in such equipment or applications and therefore such inclusion and/or use is at the customer’s own risk.Applications — Applications that are described herein for any of these products are for illustrative purposes only. Nexperia makes no representation or warranty that such applications will be suitable for the specified use without further testing or modification. Customers are responsible for the design and operation of their applications and products using Nexperia products, and Nexperia accepts no liability for any assistance with applications or customer product design. It is customer’s sole responsibility to determine whether the Nexperia product is suitable and fit for the customer’s applications and products planned, as well as for the planned application and use of customer’s third party customer(s). Customers should provide appropriate design and operating safeguards to minimize the risks associated with their applications and products. Nexperia does not accept any liability related to any default, damage, costs or problem which is based on any weakness or default in the customer’s applications or products, or the application or use by customer’s third party customer(s). Customer is responsible for doing all necessary testing for the customer’s applications and products using Nexperia products in order to avoid a default of the applications and the products or of the application or use by customer’s third party customer(s). Nexperia does not accept any liability in this respect.Limiting values — Stress above one or more limiting values (as defined in the Absolute Maximum Ratings System of IEC 60134) will cause permanent damage to the device. Limiting values are stress ratings only and (proper) operation of the device at these or any other conditions above thosegiven in the Recommended operating conditions section (if present) or the Characteristics sections of this document is not warranted. Constant or repeated exposure to limiting values will permanently and irreversibly affect the quality and reliability of the device.Terms and conditions of commercial sale — Nexperia products aresold subject to the general terms and conditions of commercial sale, as published at /profile/terms, unless otherwise agreed in a valid written individual agreement. In case an individual agreement is concluded only the terms and conditions of the respective agreement shall apply. Nexperia hereby expressly objects to applying the customer’s general terms and conditions with regard to the purchase of Nexperia products by customer.No offer to sell or license — Nothing in this document may be interpreted or construed as an offer to sell products that is open for acceptance orthe grant, conveyance or implication of any license under any copyrights, patents or other industrial or intellectual property rights.Export control — This document as well as the item(s) described herein may be subject to export control regulations. Export might require a prior authorization from competent authorities.Single Zener diodes in a SOD123 packageNon-automotive qualified products — Unless this data sheet expressly states that this specific Nexperia product is automotive qualified, the product is not suitable for automotive use. It is neither qualified nor tested in accordance with automotive testing or application requirements. Nexperia accepts no liability for inclusion and/or use of non-automotive qualified products in automotive equipment or applications. In the event that customer uses the product for design-in and use in automotive applications to automotive specifications and standards, customer (a) shall use the product without Nexperia's warranty of the product for such automotive applications, use and specifications, and (b) whenever customer uses the product for automotive applications beyond Nexperia's specifications such use shall be solely at customer’s own risk, and (c) customer fully indemnifies Nexperia for any liability, damages or failed product claims resulting from customer design and use of the product for automotive applications beyond Nexperia's standard warranty and Nexperia's product specifications.Translations — A non-English (translated) version of a document is for reference only. The English version shall prevail in case of any discrepancy between the translated and English versions.13.4 TrademarksNotice: All referenced brands, product names, service names and trademarks are the property of their respective owners.Single Zener diodes in a SOD123 package TablesTab. 1.Quick reference data (1)Tab. 2.Pinning (2)Tab. 3.Ordering information (2)Tab. 4.Marking codes (2)Tab. 5.Limiting values (3)Tab. 6.Thermal characteristics (3)Tab. 7.Characteristics ...................................................3Tab. 8.Characteristics per type; BZT52-C2V4 toBZT52-C24 (4)Tab. 9.Characteristics per type; BZT52-C27 toBZT52-C51 (5)Tab. 10.Characteristics per type; BZT52-C56 toBZT52-C75 (5)Tab. 11.Packing methods (7)Tab. 12.Revision history (9)FiguresFig. 1.Non-repetitive peak reverse powerdissipation as a function of pulse duration;maximum values (6)Fig. 2.Forward current as a function of forwardvoltage; typical values .......................................6Fig. 3.Temperature coefficient as a function ofworking current; typical values (6)Fig. 4.Temperature coefficient as a function ofworking current; typical values (6)Fig. 5.Package outline SOD123 (7)Fig. 6.Reflow soldering footprint SOD123 (8)Single Zener diodes in a SOD123 packagePlease be aware that important notices concerning this document and the product(s)described herein, have been included in section 'Legal information'.Contents1Product profile ....................................................11.1General description ............................................11.2Features and benefits ........................................11.3Applications ........................................................11.4Quick reference data .........................................12Pinning information ............................................23Ordering information ..........................................24Marking .................................................................25Limiting values ....................................................36Thermal characteristics ......................................37Characteristics ....................................................38Test information ..................................................68.1Quality information .............................................69Package outline ...................................................710Packing information ............................................711Soldering ..............................................................812Revision history .. (913)Legal information (10)Mouser ElectronicsAuthorized DistributorClick to View Pricing, Inventory, Delivery & Lifecycle Information:N experia:BZT52-C10J BZT52-C12X BZT52-C15X BZT52-C16X BZT52-C18X BZT52-C5V6J BZT52-C6V2X BZT52-C7V5X BZT52-C8V2J BZT52-C33J BZT52-C39J BZT52-C3V3X BZT52-C3V9X BZT52-C4V7J BZT52-C5V1J BZT52-C11J BZT52-C22X BZT52-C24J BZT52-C7V5J BZT52-C2V7J BZT52-C30J BZT52-C39X BZT52-C36J BZT52-C6V8X BZT52-C15J BZT52-C51X BZT52-C10X BZT52-C56X BZT52-C13J BZT52-C51J BZT52-C20J BZT52-C2V7X BZT52-C27J BZT52-C4V3X BZT52-C56J BZT52-C62J BZT52-C33X BZT52-C12J BZT52-C3V3J BZT52-C3V9J BZT52-C68J BZT52-C75J BZT52-C43J BZT52-C3V6J BZT52-C24X BZT52-C3V6X BZT52-C62X BZT52-C9V1X BZT52-C47J BZT52-C30X BZT52-C11X BZT52-C68X BZT52-C36X BZT52-C47X BZT52-C27X BZT52-C2V4J BZT52-C5V1X BZT52-C13X BZT52-C22J BZT52-C9V1J BZT52-C4V3J BZT52-C6V8J BZT52-C18JBZT52-C16J BZT52-C3V0X BZT52-C75X BZT52-C43X BZT52-C2V4X BZT52-C4V7X BZT52-C20X BZT52-C8V2X BZT52-C3V0J BZT52-C6V2J BZT52-C5V6X。
ITW Devcon 2 Ton Epoxy 技术数据表说明书

14260Technical Data SheetRevision Date:25.07.14Rev 5Bay 150,Shannon Industrial Estate,Shannon County Clare,Ireland 2Ton EpoxyORDERING INFORMATIONStock No.1426020222Package Size 50ml Cartridge 200ml CartridgeDescriptionA high strength,non-shrinking,adhesive/potting compound specially formulated for high clarity,good impact strength,and water resistance.The adhesive bond is resistant to weathering,solvents,and wide variations in temperature.Features∙100%reactive,no solvents∙Good water and chemical resistance ∙Fills gaps and voids∙Room temperature curingRecommended applications∙Bonding or potting electronic components and assemblies ∙Creating moisture-resistant seals∙Suitable for bonding ceramics,ferrous and non-ferrous,ferrites,wood,glass and concretePRODUCT DATA Physical Properties (Uncured)ColourClear Mixed Viscosity8,000cps Mixed Ratio by Volume 1:1Mixed Ratio by weight 1.2:1Mixed Density1.10gm/cc Working time 28 grams @ 23˚C8–12minutes Fixture time @23oC 30–35minutes Functional cure @ 23˚C 2 hours Full Cure12hoursPhysical Properties (Cured)7days cured @24˚CAdhesive tensile shear,ASTM D100215.5MPa (0.25mm bondline)T peel4-5N/10mm Tensile Elongation1%Service temperature,dry-40–93oC Cured hardness,ASTM D224083DDielectric strength,ASTM D14924KV/mm Compression strength,ASTM D69575.86MPaSpecific Volume909cm 3/kg7days room temperature cure (30days immersion)Chemical ResistanceAcetic (dilute)10%Poor Acetone FairAmmonia Very Good Corn Oil Excellent Cutting oil Excellent Ethanol Poor Petrol (unleaded)Excellent Glycols/Antifreeze Excellent Hydrochloric 10%Poor Isopropanol Poor Kerosene Excellent MEK Poor Mineral Spirits Excellent Motor Oil Excellent Sodium Hydroxide 10%Very Good Sulphuric 10%PoorPlease consult ITW Devcon for other chemicalsTechnical Data SheetRevision Date:25.07.14Rev 5Bay 150,Shannon Industrial Estate,Shannon County Clare,Ireland 2Ton EpoxyAPPLICATION INFORMATION General Surface Preparation2Ton Epoxy works best on clean surfaces.Surfaces should be free of heavy deposits of grease,oil,dirt or other contaminants or cleaned with industrial cleaning equipment such as vapor degreasers or hot aqueous baths.Abrading or roughing the surfaces of metals will increase the microscopic bond area significantly and optimize the bond strength.MixingThis product is available in two cartridge sizes.The cartridge should be used with the appropriate manual Applicator Gun and Static Mixer Nozzle.The Static Mixer Nozzle enables the material to be thoroughly mixed when dispensed,and thus can be applied directly to the surfaces to be bonded.Please note:Once the product goes beyond its working time the nozzle has to be thrown away and a new nozzle used for further dispensing.ApplicationApply mixed epoxy directly to one surface in an even film or as a bead.Assemble with the mating part within the recommended working time.Obtain firm contact between the parts to minimize any gap and ensure good contact of the epoxy between the mating parts,clamping may optimize this part of the process.A small volume of epoxy should flow out the edges to show there is adequate gap filling.For very large gaps,apply epoxy to both surfaces and spread to cover the entire area,or make a bead pattern,which will allow flow throughout the joint.Let bonded assemblies stand for the recommended functional cure time before handling.They are capable of withstanding processing forces at this point,but should not be dropped,shocked or heavily loaded.Storage Shelf LifeDevcon Epoxy Adhesives should be stored in a cool dry place when not used for a longperiod of time.A shelf life of 3years from date of manufacture can be expected when stored at room temperature (22ºC)in their original containers.The expiry will be displayed on the product packaging.Precaution For complete safety and handling information,please refer to the appropriate Material Safety Data Sheets prior to using this product.WarrantyDevcon will replace any material found to be defective.Because the storage,handling and application of this material is beyond our control we can accept no liability for the results obtained.DisclaimerAll information on this data sheet is based on laboratory testing and is not intended for design purposes.ITW Devcon makes no representations or warranties of any kind concerning this data.For product information visit alternatively for technical assistance please call +35361771501(Ireland)or +49(0)431717910(Germany)14260。
ANALOG DEVICES OP177 数据手册
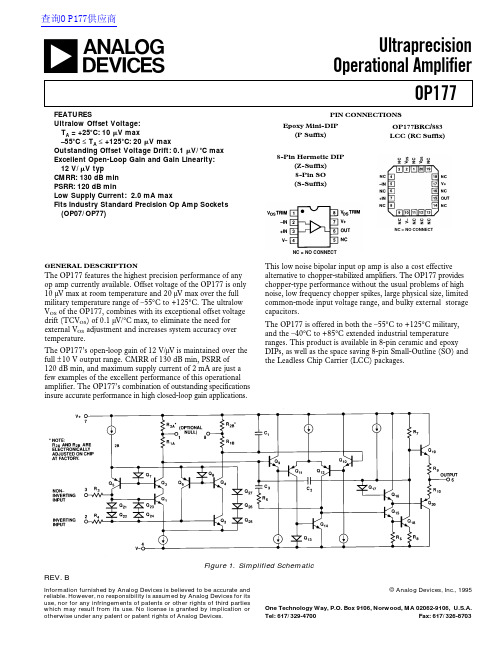
© Analog Devices, Inc., 1995
One Technology Way, P.O. Box 9106, Norwood, MA 02062-9106, U.S.A.
Tel: 617/329-4700
Fax: 617/326-8703
OP177–SPECIFICATIONS
ELECTRICAL CHARACTERISTICS (@ VS = ؎15 V, TA = +25؇C, unless otherwise noted)
ISY
Offset Adjustment Range
Conditions
(Note 1)
fo = 1 Hz to 100 Hz2 fo = 1 Hz to 100 Hz2 (Note 3)
(Note 4) VCM = ± 13 V VS = ± 3 V to ± 18 V RL ≥ 2 kΩ, VO = ± 10 V5 RL ≥ 10 kΩ RL ≥ 2 kΩ RL ≥ 1 kΩ RL ≥ 2 kΩ2 AVCL = +12
± 13.5 ± 14.0
± 12.5 ± 13.0
± 12.0 ± 12.5
0.1 0.3
0.4 0.6
60
50
60
3.5
4.5
1.6
2.0
±3
OP177B Min Typ Max
10 25
0.2
0.3 1.5
–0.2
2.0
118 150
3
8
26 45
200
± 13 ± 14
130 140ຫໍສະໝຸດ 115 125OP177A
OP177B
Min Typ Max Min Typ Max
罗克韦尔 ControlLogix 系统 说明书
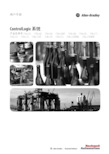
准备事宜 . . . . . . . . . . . . . . . . . . . . . . . . . . . . . . . . . . . . . . . . . . . . . . . . . . 19 1756-L7x 控制器部件. . . . . . . . . . . . . . . . . . . . . . . . . . . . . . . . . . . . . . 19
未随 1756-L6x 控制器提供的部件. . . . . . . . . . . . . . . . . . . . . . 33 1756-L6x 控制器安装. . . . . . . . . . . . . . . . . . . . . . . . . . . . . . . . . . . . . . 34 CF 卡的安装和取出 . . . . . . . . . . . . . . . . . . . . . . . . . . . . . . . . . . . . . . . 34 电池的连接与更换 . . . . . . . . . . . . . . . . . . . . . . . . . . . . . . . . . . . . . . . . 38 将控制器插入机架 . . . . . . . . . . . . . . . . . . . . . . . . . . . . . . . . . . . . . . . . 40 将控制器从机架拆下 . . . . . . . . . . . . . . . . . . . . . . . . . . . . . . . . . . . . . . 42
安装 1756-L7x 控制器 安装 1756-L6x 控制器
控制器使用入门
BSP171P(学习资料)
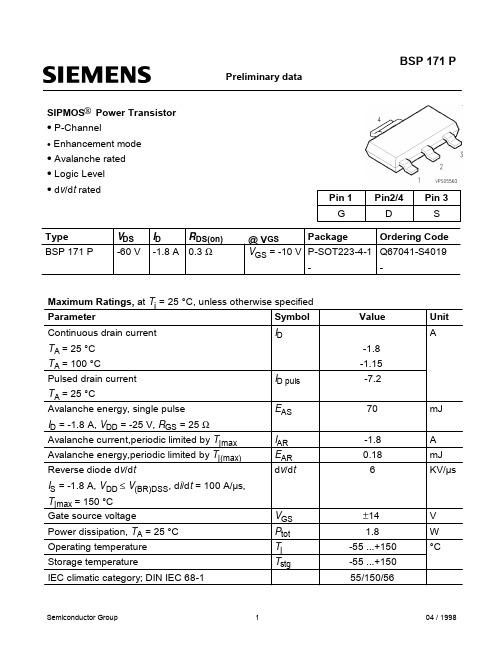
Preliminary dataSIPMOS ® Power Transistor • P-Channel• Enhancement mode• Avalanche rated • Logic Level • d v /d t ratedPin 1Pin2/4Pin 3GDSType V DS I DR DS(on)@ V GSPackage Ordering Code BSP 171 P-60 V-1.8 A 0.3 ΩV GS = -10 V P-SOT223-4-1-Q67041-S4019-Continuous drain current T A = 25 °CT A = 100 °CI D-1.8 -1.15 A-7.2Pulsed drain current T A = 25 °CI D puls mJAvalanche energy, single pulse I D = -1.8 A, V DD = -25 V, R GS = 25 Ω70E ASAvalanche current,periodic limited by T jmax I AR A -1.80.18mJ Avalanche energy,periodic limited by T j(max)E AR KV/µsd v /d tReverse diode d v /d tI S = -1.8 A, V DD ≤ V (BR)DSS , d i /d t = 100 A/µs, T jmax = 150 °C6Gate source voltageV GS ±14 V 1.8W Power dissipation, T A = 25 °C P tot °COperating temperature -55 ...+150T j Storage temperatureT stg-55 ...+15055/150/56IEC climatic category; DIN IEC 68-1Maximum Ratings, at T j = 25 °C, unless otherwise specified Value Unit ParameterSymbolPreliminary dataElectrical Characteristics UnitValues SymbolParameterat T j = 25 °C, unless otherwise specified typ.max.min.Thermal Characteristicstbd -R thJS Thermal resistance, junction -soldering point (Pin 4)K/Wtbd -Thermal resistance, junction - ambient R thJA -- - 70SMD version, device on PCB: @ min. footprint @ 6 cm 2 cooling area F)- -R thJAtbd tbdStatic Characteristics---60V (BR)DSSDrain- source breakdown voltage V GS = 0 V, I D = -0.25 mAV-1-1.5V GS(th)Gate threshold voltage, V GS = V DS I D = -460 µA, T j = 25 °C -2- - - - -0.1 - µAZero gate voltage drain current V DS = -60 V, V GS = 0 V, T j = -40 °C V DS = -60 V, V GS = 0 V, T j = 25 °C V DS = -60 V, V GS = 0 V, T j = 150 °C I DSS-0.1 -1 -100 -10-100nA -I GSS Gate-source leakage current V GS = -20 V, V DS = 0 V0.3 0.21Drain-Source on-state resistance V GS = -4.5 V, I D = -1.5 A V GS = -10 V, I D = -1.8 AR DS(on)0.45 0.3Ω- -Preliminary dataElectrical Characteristics ParameterValues UnitSymbolmax.min.typ.at T j = 25 °C, unless otherwise specified Dynamic Characteristics S TransconductanceV DS ≥2*I D *R DS(on)max , I D = -1.8 A 31g fs-pFInput capacitanceV GS = 0 V, V DS = -25 V, f = 1 MHz C iss 460-365135-105C ossOutput capacitanceV GS = 0 V, V DS = -25 V, f = 1 MHz 50Reverse transfer capacitance V GS = 0 V, V DS = -25 V, f = 1 MHz 40-C rssns Turn-on delay timeV DD = -30 V, V GS = -10 V, I D = -1.8 A, R G = 6 Ω20-13t d(on)Rise timeV DD = -30 V, V GS = -10 V, I D = -1.8 A, R G = 6 Ωt r45-30300-200t d(off)Turn-off delay timeV DD = -30 V, V GS = -10 V, I D = -1.8 A, R G = 6 ΩFall timeV DD = -30 V, V GS = -10 V, I D = -1.8 A, R G = 6 Ω-75t f115Preliminary dataElectrical Characteristics ParameterSymbolValues Unitat T j = 25 °C, unless otherwise specified min.typ.max.Dynamic Characteristics Gate charge at thresholdV DD = -24 V, I D ≥ -0,1 A, V GS = 0 to - 1 V Q G(th)-0.60.9nCGate charge at V gs =5VV DD = -24 V, I D = -1.8 A , V GS = 0 to -5 V Q g(5)-812Gate charge totalV DD = -24 V, I D = -1.8 A, V GS = 0 to -10 V Q g-1421nCGate plateau voltage V DD = -24 V, I D = -1.8 AV (plateau)- 2.8-VReverse Diode-1.8A--I SInverse diode continuous forward current T A = 25 °C-7.2Inverse diode direct current,pulsed T A = 25 °C-I SM --1.2V-0.95Inverse diode forward voltage V GS = 0 V, I F = -3.6 A -V SD150Reverse recovery timeV R = -30 V, I F =I S , d i F /d t = 100 A/µs t rr ns 100-0.3Reverse recovery chargeV R = -30 V, I F =l S , d i F /d t = 100 A/µs-Q rrµC0.2Preliminary dataEdition 7.97Published by Siemens AG,Bereich Halbleiter Vetrieb,Werbung, Balanstraße 73,81541 München© Siemens AG 1997All Rights Reserved.Attention please!As far as patents or other rights of third parties are concerned, liability is only assumed for components,not for applications, processes and circuits implemented within components or assemblies.The information describes a type of component and shall not be considered as warranted characteristics. Terms of delivery and rights to change design reserved.For questions on technology, delivery and prices please contact the Semiconductor Group Offices in Germany or the Siemens Companies and Representatives worldwide (see address list).Due to technical requirements components may contain dangerous substances. For information on the typesin question please contact your nearest Siemens Office, Semiconductor Group.Siemens AG is an approved CECC manufacturer.PackingPlease use the recycling operators known to you. We can also help you - get in touch with your nearest sales office. By agreement we will take packing material back, if it is sorted. You must bear the costs of transport. For packing material that is returned to us unsorted or which we are not obliged to accept, we shall have to invoice you for any costs incurred.Components used in life-support devices or systems must be expressly authorized for such purpose! Critical components1 of the Semiconductor Group of Siemens AG, may only be used in life-support devices or systems2 with the express written approval of the Semiconductor Group of Siemens AG.1)A critical component is a component used in a life-support device or system whose failure can reasonably be expected to cause the failure of that life-support device or system, or to affect its safety or effectiveness of that device or system.2)Life support devices or systems are intended (a) to be implanted in the human body, or (b) to support and/or maintain and sustain and/or protecf human life. If they fail, it is reasonable to assume that the health of the。
BSP317中文资料
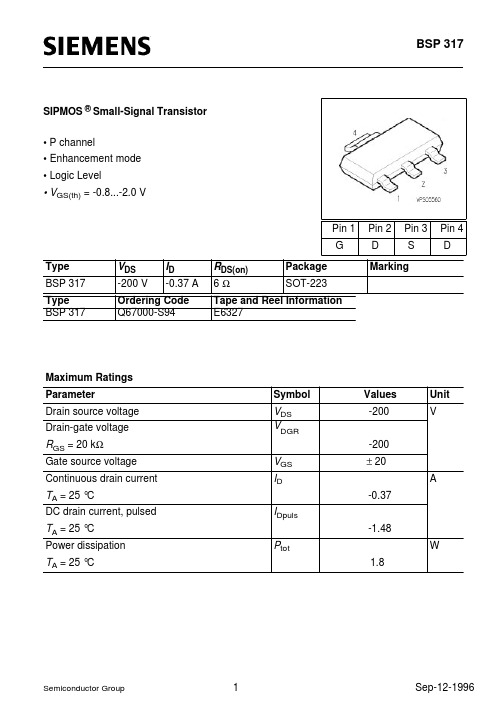
G
D
S
D
VDS -200 V
ID -0.37 A
Ordering Code Q67000-S94
RDS(on) 6Ω
Package SOT-223
Tape and Reel Information E6327
Marking
Maximum Ratings Parameter Drain source voltage Drain-gate voltage RGS = 20 kΩ Gate source voltage Continuous drain current TA = 25 °C DC drain current, pulsed TA = 25 °C Power dissipation TA = 25 °C
BSP 317
SIPMOS ® Small-Signal Transistor
• P channel • Enhancement mode • Logic Level • VGS(th) = -0.8...-2.0 V
Type
BSP 317
Type BSP 317
Pin 1 Pin 2 Pin 3 Pin 4
Electrical Characteristics, at Tj = 25°C, unless otherwise specified
Parameter
Symbol min.
Values
typ.
max.
Static Characteristics Drain- source breakdown voltage VGS = 0 V, ID = -0.25 mA, Tj = 25 °C Gate threshold voltage VGS=VDS, ID = -1 mA Zero gate voltage drain current VDS = -200 V, VGS = 0 V, Tj = 25 °C VDS = -200 V, VGS = 0 V, Tj = 125 °C VDS = -130 V, VGS = 0 V, Tj = 25 °C Gate-source leakage current VGS = -20 V, VDS = 0 V Drain-Source on-state resistance VGS = -10 V, ID = -0.37 A
17550中文资料

Document Number: MPC17550Rev. 2.0, 7/2006Freescale Semiconductor Advance Information* This document contains certain information on a new product.Specifications and information herein are subject to change without notice.© Freescale Semiconductor, Inc., 2006. All rights reserved.Quad H-Bridge Micromotor Driver with DC/DC Boostof 1.2 Ω•••••••Undervoltage Detection and Shutdown Circuit•Pb-Free Packaging Designated by Suffix Code EVFigure 1. 17550 Simplified Application Diagram17550Analog Integrated Circuit Device Data17550INTERNAL BLOCK DIAGRAMINTERNAL BLOCK DIAGRAMFigure 2. 17550 Simplified Internal Block DiagramVDDPSBAGNDOEINAF INARINBF INBRINCF INDF INDRGNDINCRHBDR HBDF VMDHBCR HBCFVMC PGNDHBBRHBBF VMB PGNDHBAR HBAF VMA LXVGPGNDPGNDAnalog Integrated Circuit Device Data 17550TERMINAL CONNECTIONSTERMINAL CONNECTIONSFigure 3. 17550 Terminal ConnectionsTable 1. Terminal Function DescriptionTerminalTerminal Name Formal Name Definition1AGND Analog Ground Analog and logic signal ground reference terminal.2NC No Connect No connection to this terminal.3PSB Power Standby Power standby mode control terminal.4OE Output EnableLogic output Enable control of H-Bridges (Low = True).5 ,9VMA Motor Drive Power Supply A Power supply voltage connection for Motor “A” (top of HBA).6HBAF HBA Forward Output Forward output of H-Bridge A.8HBAR HBA Reverse OutputReverse output of H-Bridge A.10, 14VMB Motor Drive Power Supply B Power supply voltage connection for Motor “B” (top of HBB).11HBBR HBB Reverse Output Reverse output of H-Bridge B.7, 12, 25, 30PGND Power Ground Power ground connection.13HBBF HBB Forward Output Forward output of H-Bridge B.15INAR Input Control HBA ReverseControl signal input for H-Bridge A reverse.16INAF Input Control HBA Forward Control signal input for H-Bridge A forward.17INBF Input Control HBB Forward Control signal input for H-Bridge B forward.18INBR Input Control HBB Reverse Control signal input for H-Bridge B reverse.19INDR Input Control HBD Reverse Control signal input for H-Bridge D reverse.20INDF Input Control HBD ForwardControl signal input for H-Bridge D forward.21INCF Input Control HBC Forward Control signal input for H-Bridge C forward.22INCR Input Control HBC ReverseControl signal input for H-Bridge C reverse.23, 27VMD Motor Drive Power Supply D Power supply voltage connection for Motor “D” (top of HBD).24HBDF HBD Forward Output Forward output of H-Bridge D.26HBDR HBD Reverse OutputReverse output of H-Bridge D.28, 32VMCMotor Drive Power Supply C Power supply voltage connection for Motor “C” (top of HBC).123456789101112131415161718363534333231302928272625242322212019AGND NC PSB OE VMA HBAF PGND HBAR VMA VMB HBBR PGND HBBF VMB INAR INAF INBF INBR VG VDD LX GND VMC HBCF PGND HBCR VMC VMD HBDR PGND HBDF VMD INCR INCF INDF INDRAnalog Integrated Circuit Device Data17550TERMINAL CONNECTIONS29HBCR HBC Reverse Output Reverse Output of H-Bridge C.31HBCF HCB Forward OutputForward Output of H-Bridge C.33GND GroundControl circuit ground terminal for DC/DC circuit ground.34LX DC/ D C Converter Switching Transistor OutputOpen-drain output of the internal DC/ D C converter circuit.35VDD Logic Supply Control circuit power supply terminal.36VGGate-Driver Circuit PowerSupplyInput terminal for the gate-drive voltage.Table 1. Terminal Function Description (continued)TerminalTerminal Name Formal Name DefinitionAnalog Integrated Circuit Device Data 17550ELECTRICAL CONNECTIONSMAXIMUM RATINGSELECTRICAL CONNECTIONSMAXIMUM RATINGSTable 2. Maximum RatingsAll voltages are with respect to ground unless otherwise noted. Exceeding the ratings may cause a malfunction or permanent damage to the device.RatingSymbol Value Unit Motor Supply VoltageV M -0.5 to 9.0V Gate-Driver Circuit Power Supply Voltage V G V DD - 0.5 to 14V Logic Supply Voltage V DD -0.5 to 6.0V Signal Input Voltage (1)V IN-0.5 to V DD + 0.5V Driver Output Current Continuous (2)Peak (3)I O I OPK0.72.0AESD Voltage (4)Human Body Model Machine ModelV ESD1V ESD2± 2000± 100VStorage Temperature Range T STG -65 to 150°C Operating Ambient Temperature T A -10 to 60°C Operating Junction Temperature T J -10 to 150°C Thermal Resistance (5)R θJA TBD °C/W Power Dissipation (6)P D 1500mW Soldering Temperature (7)T SOLDER260°CNotes1.V IN is the voltage level applied to any input terminal.2.I O is measured as the load current flowing through the H-bridge.3.T A = 25°C, pulse width < 10 ms at intervals > 0.2 seconds.4.ESD1 testing is performed in accordance with the Human Body Model (C ZAP = 100 pF, R ZAP = 1500 Ω), ESD2 testing is performed in accordance with the Machine Model (CZAP = 200 pF, RZAP = 0 Ω).5.Mounted on 37 x 50 Cu area (1.6 mm FR-4 PCB).6.Maximum at T A = 25°C.7.Soldering temperature limit is for 10 seconds maximum duration. Not designed for immersion soldering. Exceeding these limits may cause malfunction or permanent damage to the device.Analog Integrated Circuit Device Data17550ELECTRICAL CONNECTIONSSTATIC ELECTRICAL CHARACTERISTICSSTATIC ELECTRICAL CHARACTERISTICSTable 3. STATIC ELECTRICAL CHARACTERISTICSCharacteristics noted under conditions T A = 25°C, V DD = 3.0 V, V M = 2.5 V, GND = 0 V, f IN = 176 kHz unless otherwise noted. Typical values noted reflect the approximate parameter means at T A = 25°C under nominal conditions unless otherwise noted.CharacteristicSymbol Min Typ Max UnitPOWERMotor Supply Voltage V M 1.6 2.5 5.5V Logic Supply VoltageV DD 2.5 3.0 5.5V Standby Power Supply Current (8)Motor Supply Standby Current Logic Supply Standby Current I VMSTBY I V DDSTBY –––– 1.01.0µALogic Supply CurrentI VDD–0.31.0mAGate Driver Circuit Power Supply Current (9)Standby (PSB = “L”)No Signal Operating Input Signal Operating (10)I DDC0I DDCN I DDC ––––1.019 1.03.025µA µA mA Driver Output ON Resistance (11)R DS(ON)–0.71.2ΩGATE DRIVEGate Driver Circuit Power Supply Voltage (12) V G1011.513VCONTROL LOGIC Logic Input Voltage (13)V IN–V DDVLogic Input (F, R, PSB, OE ) High-Level Input Voltage Low-Level Input Voltage High-Level Input Current Low-Level Input CurrentV IH V IL I IH I ILV DD x 0.7––-1.0–––––V DD x 0.31.0–V V µA µANotes8.Applies individually to each H-Bridge.9.Average inductor current for DC/ D C converter (connected between V D D and LX [L = 1.0 mH, C = 2.2 µF]). 10.Full drive (input signal to all input control terminals). 11.The total H-bridge ON resistance when V G is 11.5 V. 12.When voltage is supplied externally without built-in DC/ D C. 13.V IN is the voltage level applied to any input.Analog Integrated Circuit Device Data17550ELECTRICAL CONNECTIONSDYNAMIC ELECTRICAL CHARACTERISTICSDYNAMIC ELECTRICAL CHARACTERISTICSTable 4. DYNAMIC ELECTRICAL CHARACTERISTICSCharacteristics noted under conditions T A = 25°C, V DD = 3.0 V, V M = 2.5 V, GND = 0 V, f IN = 176 kHz unless otherwise noted. Typical values noted reflect the approximate parameter means at T A = 25°C under nominal conditions unless otherwise noted.CharacteristicSymbolMinTypMaxUnitINPUTPulse Input Frequency (14) f IN ––200kHz Internal Oscillator Frequency f OSC–100200kHzOUTPUTGate Driver Circuit Power Supply Wake-Up Time t VGON –1020ms Propagation Delay Time Turn-ON Time Turn-OFF Timet PLH t PHL––0.20.21.01.0µsNotes14.f IN is the signal frequency applied to an input terminal (F, R).Analog Integrated Circuit Device Data17550ELECTRICAL CONNECTIONS TIMING DIAGRAMSTIMING DIAGRAMSFigure 4. DC/DC Converter Output Waveform Figure 5. H-Bridge Output Waveformt VGONPSBV G2.1VV ILV IH10 Vt PLH FO, RO50%t PHLF , R,50%Table 5. Truth TablePSB, OEINA / I NB / I NC / I NDHBA / H BB / H BC / H BC PSB OE IN*F IN*R HB*F HB*R H L L L L L H L L H L H H L H L H L H L H H Z Z H H X X Z Z LXXXZZH = High. L = Low.Z = High impedance. X = Don’t care. * = A, B, C, or D.Analog Integrated Circuit Device Data 17550FUNCTIONAL DESCRIPTIONINTRODUCTIONFUNCTIONAL DESCRIPTIONINTRODUCTIONThe 17550 is a monolithic quad H-Bridge ideal for portable electronic applications containing multiple bipolar stepper motors and / o r brush DC motors. The device features an on-board DC / D C converter to provide gate-drive voltages, as well as level-shifting circuitry. The control logic translates the input signals to the gate-driver circuitry while providing cross-conduction suppression.The 17550 has four operating modes: Forward, Reverse, Brake, and Tri-Stated (High Impedance). The MOSFETs comprising the output bridge have a total source + s ink R DS(ON) ≤ 1.2 Ω.The 17550 can simultaneously drive four brush DC motors or two bipolar stepper motors. The drivers are designed to be PWM’ed at frequencies up to 200 kHz.FUNCTIONAL TERMINAL DESCRIPTIONLOGIC SUPPLY (VDD)The VDD terminal carries the logic supply voltage and current into the logic sections of the IC. V DD has anundervoltage threshold. If the supply voltage drops below the undervoltage threshold, the output power stage switches to a tri-state condition. When the supply voltage returns to a level that is above the threshold, the power stage automatically resumes normal operation according to the established condition of the input control terminals.CONTROL SIGNAL INPUT FOR H-BRIDGE,F=FORWARD, R= REVERSE (INAF, INAR, INBF, INBR, INCF, INCR, INDF, INDR)These logic input control terminals control each H-Bridge output; e.g., IN*F logic HIGH = HB*F HIGH; likewise, IN*R logic HIGH = HB*R HIGH. However, if both “F” and “R” inputs are taken HIGH, the associated bridge’s outputs are both tri-stated (refer to Table 5, Truth Table , page 8).OUTPUT ENABLE (OE)OE terminal is a LOW = TRUE enable input. When OE = HIGH, all H-Bridge outputs are tri-stated (highimpedance) regardless of logic inputs states.OUTPUT OF H-BRIDGE, R=REVERSE,F=FORWARD (HBAF, HBAR, HBBF, HBBR, HBCF, HBCR, HBDF, HBDR)These terminals provide connection to the outputs of each of the internal H-Bridges (see Figure 2, 17550 Simplified Internal Block Diagram , page 2).POWER SUPPLY VOLTAGE CONNECTION FOR MOTORS A, B, C, D (VMA, VMB, VMC, VMD)The VM terminals carry the main supply voltage andcurrent into the power sections of the 17550. This supply then becomes controlled and/or modulated by the 17550 as it delivers the power to the loads attached between the H-Bridge output terminals. All VM terminals must be connected together on the printed circuit board.DC/ DC CONVERTER SWITCHING TRANSISTOR OUTPUT (LX)The LX terminal is the open-drain output of the internal DC / D C converter circuit. It is the junction for the external inductor and the anode of the external Schottky diode.GATE-DRIVER CIRCUIT POWER SUPPLY (VG)The VG terminal is the input terminal for the gate-drive voltage. It can be supplied from the built-in DC / D C converter or from an external source.GROUND TERMINALS (GND, AGND, PGND)All ground terminals must be tied together on the PCB.POWER STANDBY MODE CONTROL (PSB)The PSB input controls the functioning of power output stages (the H-Bridges). When this input signal turns Low, the output stages and Internal DC/DC Converter which makes Gate Voltage are disabled and all the outputs are opened (High Impedance). When this input signal turns High, the output stages and Internal DC/DC Converter are enabled and the H-Bridges operate normally.Analog Integrated Circuit Device Data17550TYPICAL APPLICATIONS INTRODUCTIONTYPICAL APPLICATIONSINTRODUCTIONThe 17550's built-in DC / D C converter must be connected to an external inductor, rectifier, and filter capacitor. This step-up converter generates the gate-drive voltage, V G , required by the internal gate driver circuits. Although there is some latitude in selecting the values for the externalcomponent, care must be taken that V G does not exceed 14 V. Additionally, too low an inductance will cause large instantaneous switching currents, which may damage the device.Important Do not use an inductance lower than 330 µH.To attain high-efficiency operation, the rectifier should be a Schottky diode, and the filter capacitor should be of the lowEquivalent Series Resistance (ESR) type. Attention should be paid to proper switch mode power supply PCB layout practice. Some experimentation may be required to determine optimal external component values. Therecommended starting values are L = 1.0 mH, C = 2.2 µF.The DC / D C converter includes its own internal oscillator and does not require an external clock input.TYPICAL APPLICATIONTwo typical application schematics are shown in Figure 6. and Figure 7.Figure 6. Typical 17550 Application - Controlling Stepper Motors2.2µFL = 1.0mH10µFVDD VMGNDPSBOE INARINAF INBF INBRINCRINCF INDFINDR VGLXHBAF HBARHBBRHBBF HBCF HBCRHBDRHBDF MCUNSNS17550V M = 2.5 VV DD = 3.0 V47µFAnalog Integrated Circuit Device Data 17550TYPICAL APPLICATIONSINTRODUCTIONFigure 7. Typical 17550 Application - No Internal DC-DC UsedVDD VMGNDPSBOE INARINAF INBF INBRINCRINCF INDFINDR VGLXHBAF HBARHBBRHBBF HBCF HBCRHBDRHBDF MCUNSNS17550V M = 2.5 VV DD = 3.0 V47µFVG 11.5VAnalog Integrated Circuit Device Data17550TYPICAL APPLICATIONS INTRODUCTIONCEMF SNUBBING TECHNIQUESCare must be taken to protect the IC from potentially damaging CEMF spikes induced when commuting currents in inductive loads. Typical practice is to provide snubbing of voltage transients by placing a capacitor or zener at the motor supply voltage terminal (VM) (see Figure 8).Figure 8. CEMF Snubbing Techniques175XX 5.0 V 5.0 VGNDC1L C1H C2L C2H CRESVM VDD OUTOUT 175XX 5.0 V 5.0 VGNDC1L C1H C2L C2H CRESVM VDD OUTOUTAnalog Integrated Circuit Device Data 17550PACKAGINGPACKAGE DIMENSIONSPACKAGINGPACKAGE DIMENSIONSImportant: For the most current revision of the package, visit and perform a keyword search on the 98A number listed below.Analog Integrated Circuit Device Data17550REVISION HISTORYREVISION HISTORYREVISIONDATE DESCRIPTION OF CHANGES2.07/2006•Converted to Freescale format and updated to the prevailing form and style •Added typical Application for non DC/DC use •Added RoHS complianceMPC17550Information in this document is provided solely to enable system and software implementers to use Freescale Semiconductor products. There are no express or implied copyright licenses granted hereunder to design or fabricate any integrated circuits or integrated circuits based on the information in this document.Freescale Semiconductor reserves the right to make changes without further notice to any products herein. Freescale Semiconductor makes no warranty, representation or guarantee regarding the suitability of its products for any particular purpose, nor does Freescale Semiconductor assume any liability arising out of the application or use of any product or circuit, and specifically disclaims any and all liability, including without limitation consequential or incidental damages. “Typical” parameters that may beprovided in Freescale Semiconductor data sheets and/or specifications can and do vary in different applications and actual performance may vary over time. All operating parameters, including “Typicals”, must be validated for each customer application by customer’s technical experts. Freescale Semiconductor does not convey any license under its patent rights nor the rights of others. Freescale Semiconductor products are not designed, intended, or authorized for use as components in systems intended for surgical implant into the body, or other applications intended to support or sustain life, or for any other application in which the failure of the Freescale Semiconductor product could create a situation where personal injury or death may occur. Should Buyer purchase or use Freescale Semiconductor products for any such unintended orunauthorized application, Buyer shall indemnify and hold Freescale Semiconductor and its officers, employees, subsidiaries, affiliates, and distributors harmless against all claims, costs, damages, and expenses, and reasonable attorney fees arising out of, directly or indirectly, any claim of personal injury or death associated with such unintended or unauthorized use, even if such claim alleges that Freescale Semiconductor was negligent regarding the design or manufacture of the part. Freescale™ and the Freescale logo are trademarks of Freescale Semiconductor, Inc. All other product or service names are the property of their respective owners.© Freescale Semiconductor, Inc., 2006. All rights reserved.How to Reach Us:Home Page: E-mail:support@USA/Europe or Locations Not Listed:Freescale SemiconductorTechnical Information Center, CH3701300 N. Alma School Road Chandler, Arizona 85224+1-800-521-6274 or +1-480-768-2130support@Europe, Middle East, and Africa:Freescale Halbleiter Deutschland GmbH Technical Information Center Schatzbogen 781829 Muenchen, Germany +44 1296 380 456 (English)+46 8 52200080 (English)+49 89 92103 559 (German)+33 1 69 35 48 48 (French)support@Japan:Freescale Semiconductor Japan Ltd. Headquarters ARCO Tower 15F1-8-1, Shimo-Meguro, Meguro-ku, Tokyo 153-0064 Japan0120 191014 or +81 3 5437 9125support.japan@Asia/Pacific:Freescale Semiconductor Hong Kong Ltd.Technical Information Center 2 Dai King StreetTai Po Industrial Estate Tai Po, N.T., Hong Kong +800 2666 8080@For Literature Requests Only:Freescale Semiconductor Literature Distribution Center P .O. Box 5405Denver, Colorado 802171-800-441-2447 or 303-675-2140Fax: 303-675-2150LDCForFreescaleSemiconductor@。
深圳佰芯微电子 isd17系列编程拷贝机 说明书

ISD17系列编程拷贝机使用说明书Version:1.02Update:2007.9.18摘要:本文对1700pro 语音编程拷贝机作了简要介绍,叙述了1700pro的使用方法,详细说明了1700pro软件的安装使用,ISD1700语音芯片母片制作,ISD1700语音芯片语音编程以及ISD1700芯片对芯片的语音拷贝。
一、前言(使用前必读)为了达到ISD1700系列语音芯片的录音、拷贝音质完好和正确录音、拷贝,防止损坏语音芯片和拷贝设备,请严格按照本说明书操作流程进行操作。
二、简介1700pro ISD17系列编程拷贝机是深圳佰芯微电子有限公司开发的专用ISD1700系列语音芯片编程拷贝机,通过专用配套软件可以把电脑音源文件下载编程到ISD1700系列语音芯片中,可以指定地址,修改地址,绝对准确的地址定位。
严格按照每一段地址拷贝芯片,根据这些地址,单片机可以方便准确无误地灵活播放内部的任何一段语音。
是开发ISD1700系列语音芯片的必备开发工具。
拷贝机正面图:1、 LCD显示屏:显示一些录音、拷贝操作进程、地址信息(地址16进制表示);2、 MASTER:源芯片插座,芯片对芯片拷贝时母片插座,测试播放时测试芯片插座;在电脑录音时为空。
3、 SLA VER1:从芯片插座1,在制作母片或用电脑对芯片录音、芯片对芯片拷贝时插入要录音的ISD1700芯片;在录音、拷贝时可以为空。
芯片放在此插座上随时可能被擦除!4、 SLA VER2:从芯片插座2,在制作母片或用电脑对芯片录音、芯片对芯片拷贝时插入要录音的ISD1700芯片;在录音、拷贝时不可以为空。
芯片放在此插座上随时可能被擦除!5、 RESET按钮:复位按钮,按下复位整个系统,录音过程中不要按此按钮。
6、 COPY按钮:芯片对芯片拷贝时开始按钮,更换从芯片插座上的芯片按COPY按钮拷贝新的芯片。
7、 PLAY按钮:在测试放音时按PLAY开始放音。
8、 MODE按钮:模式选择:地址拷贝模式、芯片拷贝模式、测试播放模式。
推荐电力 REV. 0 2017 PA-1 参考设计半桥驱动电源供应说明书

Reference DesignGate Drive Power Supply Reference Design (RD)especially for Semiconductors in TO247 and TO247-4L PackagesHalf Bridge DesignDescriptionThe Half-Bridge Gate Drive Power supply Reference Design (RD) consists of a half-bridge suitable for voltages up to 1kV and a fully isolated driver stage with isolated power supplies for the low-side and the high-side switching transistors. It is suitable for single gate drive supply voltages as low as +4V as well as dual gate drive supply voltages as high as +20V / -5V (30V max) with no maximum duty cycle limitations.NOTE: Transistors sold separately.The signal ground is galvanically isolated from the power ground and can be connected to any potential, as long as it is less than 2.5kV with respect to the power potential (high-side and low-side). The limiting element is the gate driver IC specification.Features:• Optimized for very high switching speed • 2.5kV continuous input to output isolation• High Gate Drive currents (up to 10A source and sink)• The RD is fitted with a SI8273 gate driver, but can be used with any pin compatible gate driver witha PWM input (SI8274) or for gate driver ICs with reinforced isolation, for example the UCC21520. (Dual pinout layout on PCB)This RD can easily be configured for the following topologies (see application suggestions section):• LLC half-bridge• Asymmetric duty cycle half-bridge (forward and flyback) • Active Clamp half-bridge (forward and flyback) • Full bridge / phase shifted full bridge • 3 Phase B6 bridge• NPC B6 bridge (additional driving circuit for NPC is required) • Double pulse test• Synchronous Boost Converter • Synchronous Buck ConverterFeatures•Half Bridge Voltage up to 1kV •TTL Compatible Signal Input •Single 15V to 42V Supply •Shoot-Through Protection•Separate Input for Low- and High Side Switch for use with different topologiesR-REF01-HBDelivered BoardHalf Bridge Reference Design Users GuideFigure 1: Reference Design SettingComponent ListPart DescriptionIC2 DC/DC isolated converter for high side gate driver. Depending on the Transistor type, fit the appropriate DC/DC converter (See Fig. 1)IC3 DC/DC isolated converter for low side gate driver. Depending on the Transistor type, fit the appropriate DC/DC converter (See Table 1)T1 High-side switching Transistor (Not Supplied). Read important notice below.T2 Low-side switch Transistor (Not Supplied). Read important notice below.Note: The transistors are placed on the edge of the PCB so that they are easy to mount to a heatsink. They can also be mounted inverted on the bottom side for a heatsink placed underneath the PCB. Both TO247-3L and TO247-4L format transistors can be used by using the appropriate hole set.CON1 Connector for logic and driver supply. Connect a 15V, 18V, 24V or 36V DC supply hereCON2 +V Bridge Voltage: connect a positive voltage up to 1kV in respect to Power-GND to this connectorCON3 -V Bridge Voltage: Power-GNDCON4 Enable: A high signal enables the driver signals. Leave the jumper on the connector to enable the signals permanentlyCON5 Switching node of the half-bridgeU1 Signal high-side: TTL compatible input for the high-side transistorU2 Signal low-side: TTL compatible input for the low-side transistorFollowing DC/DC Models are suitable for use with this Reference Design:Table 1Model Power [W] Output Voltage [V] ApplicationR12P22005D* 2 +20/-5 SiC MosfetsR12P21503D* 2 +15/-3 SiC MosfetsR12P21509D* 2 +15/-9 IGBTsR12P1509D 1 +15/-9 IGBTsR12P06S* 1 +6 GaNR12P12S 1 +12 Cascode/Si Mosfet*these models are included in the Reference DesignHalf Bridge Reference Design Users GuideNOTE: Transistors sold separately.Important: using three pin or four pin TO247 Packages:TO247-4L packages can be used without any modification of the PCB. The kelvin source pin is already connected to the gate driver ground.TO247-3L packages however require a minor modification to join the gate driver ground to the source pin ground. This can be done by soldering 0Ω resistors across R19 and R20 or by making a solder bridge between the source and kelvin source pads (recommended for lowest gate inductance).TO247-3L PackageTO247-4L PackageHalf Bridge Reference Design Users GuideSCHEMATICFigure 2: SchematicDescription:The Reference Design board requires a single supply voltage with a range of 15-42V.IC5 creates the regulated 12V supply for IC2 and IC3.IC2 generates the isolated high-side gate driver supply voltage. Choose the appropriate DC/DC converter from the selection provided.IC3 generates the isolated low-side gate driver supply voltage. Choose the appropriate DC/DC converter from the selection provided.IC8 creates a +Vcc rail required for the gate driverIC1 isolates the control signals and level shifts the TTL input to the gate drive voltages(IC7 can be mounted instead of IC1 if reinforced isolation is required)IC4 and IC5 amplify the maximum gate drive current to ±10AR24 and R25 are not fitted. Zero ohm resistors can be mounted if IC4 and IC5 are not required (for example GaN Transistors)The input GND1 is galvanically isolated from the high side GNDA and the low side GNDB.For single-ended designs, it is recommended to connect GND1 to Power-GND (CON3) with a star-earth configuration.For full bridge configurations, couple GND1 to Power-GND with Y-Capacitors to avoid generating high potentials caused by common mode currents.R15, R16, R17 and R18 are not fitted. The positions can be used to add dummy loads for the power supplies if needed, for example, under very light load conditions or low switching frequencies. Alternately, R16 and 18 can be used to allow single-output voltage DC/DC converters to be used by connecting -Vout to the gate driver ground.Configuration R15, R17 R16, R18Not required Not requiredDual Output DC/DC,Normal Load (standard)Dual Output DC/DC,12k 12kLight LoadSingle Output DC/DC, Normal Load Not required. Zero OhmSingle Output DC/DC, Light Load 12k Zero OhmR1 and R4 are the resistors to control the turn on slew rate. 22 Ohm is fitted as standard.Half Bridge Reference Design Users GuideTruth Table (With IC1 SI8273 is mounted):Input OutputCommentU1 U2 Enable High Side Gate Low Side GateL L H L LL H H L HH L H H LH H H L L Invalid stateX X L L L Device is disabledBASIC CHARACTERISTICSParameter Condition Min. Typ. Max.Input Voltage Con1 15V 42VInput Voltage Con2 Con3 limited by C10 0V 1000VDigital U1, U2, Enable -0,5V 5,5VLogic High Input Threshold 2VLogic Low Input Threshold 0.8VInput Hysteresis 350mV 400mVMaximum Ratings -0.5V 5.5VDriver SectionSource and Sink Current (max) 10ATotal Drive Voltage positive and negative +4V 30VPropagation Delay whole system before gate resistors 20ns 40ns 70nsRise and Fall Times Refer to the datasheet of the gate driver ICIsolationIsolation Voltage Input to Output 2.5kVDCBOMFigure 3: Bill of MaterialsHalf Bridge Reference Design Users GuideLAYOUTFigure 4: Layer 1 with componentsFigure 5: Layer 2Half Bridge Reference Design Users GuideFigure 6: Layer 3Figure 7: Bottom ViewHalf Bridge Reference Design Users GuideTYPICAL SWITCHING WAVEFORMSFigure 8: Switching Waveform Ch.1: Low-side Gate Source VoltageCh.2: Low-side Drain Source VoltageSwitching Voltage: 1000VDCTransistor: C2M1000170D-NDIC2/IC3: R12P22005DSwitching Frequency: 50kHzMeasured Switching Slew Rate: 65kV/µsMeasured Switching Time: 15nsRevision Table Revision0/2017 OriginalHalf Bridge Reference Design Users Guide APPLICATION SUGGESTIONSHalf Bridge Reference Design Users Guide APPLICATION SUGGESTIONS REV.: 0/2017 PA-11 R-REF01-HBReference Design Half Bridge Reference Design Users GuideAPPLICATION SUGGESTIONSThe product information and specifications are subject to change without prior notice. RECOM products are not authorized for use in safety-critical applications (such as life support) without RECOM’s explicit written consent. A safety-critical application is defined as an application where a failure of a RECOM product may reasonably be expected to endanger or cause loss of life, inflict bodily harm or damage property. The buyer shall indemnify and hold harmless RECOM, its affiliated companies and its representatives against any damage claims in connection with the unauthorized use of RECOM products in such safety-critical applications.。
BC557 BC558 PNP Silicon Amplifier Transistor数据手册说明
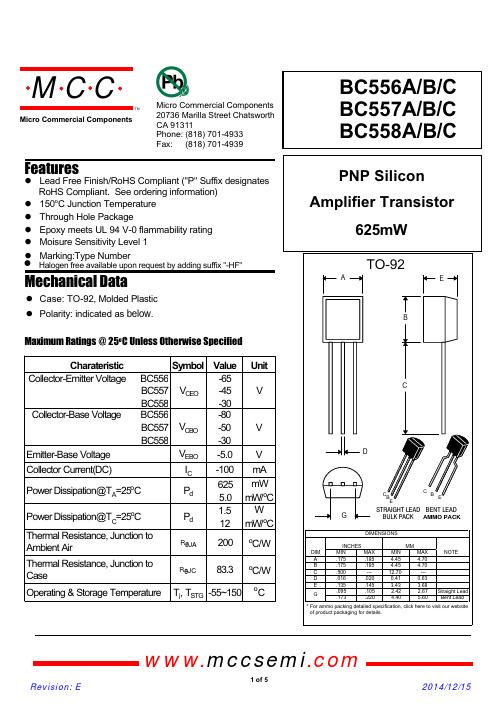
BC556A/B/C BC557A/B/C BC558A/B/C
PNP Silicon Amplifier Transistor
625mW
TO-92
A
E
B
C
D
CB E
CB E
STRAIGHT LEAD BENT LEAD
G
BULK PACK AMMO PACK
DIMENSIONS
INCHES
MM
DIM
MIN
MAX
MIN
MAX
NOTE
A
.175
.185
4.45
4.70
B
.175
.185
4.45
4.70
C
.500
---
12.70
---
D
.016
.020
0.41
0.63
E
.135
.145
3.43
3.68
G
.095 .173
.105
2.42
2.67 Straight Lead
.220
4.40
5.60 Bent Lead
Figure 10. Base–Emitter Temperature Coefficient
C, CAPACITANCE (pF)
40
TJ = 25°C
20
Cib
10 8.0
6.0
Cob
4.0
2.0 –0.1 –0.2
–0.5 –1.0 –2.0 –5.0 –10 –20 VR, REVERSE VOLTAGE (VOLTS)
Collector cut-off current
BC556 BC557
NXP UBA2017DB1064 2 x 28 W T5 示例板用户指南说明书
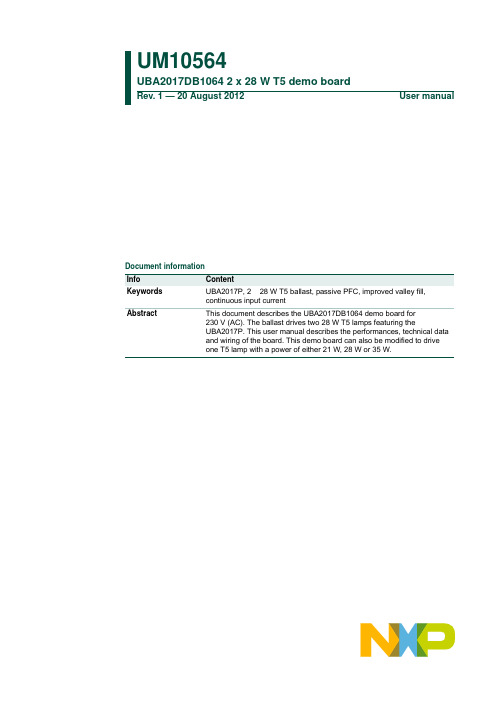
UM10564UBA2017DB1064 2 x 28 W T5 demo boardRev. 1 — 20 August 2012User manualDocument informationInfo ContentKeywords UBA2017P, 2×28W T5 ballast, passive PFC, improved valley fill,continuous input currentAbstract This document describes the UBA2017DB1064 demo board for230V(AC). The ballast drives two 28 W T5 lamps featuring theUBA2017P. This user manual describes the performances, technical dataand wiring of the board. This demo board can also be modified to driveone T5 lamp with a power of either 21W, 28W or 35W.Revision historyRev Date Descriptionv.120120820first issueContact informationFor more information, please visit: For sales office addresses, please send an email to: **********************1. IntroductionThe UBA2017DB1064 demo board is intended to serve as a two lamp ballast example using a passive PFC. This manual describes the specification and use of theUBA2017DB1064 board. The demo board can be reconfigured for single lamp operation which is described in Section 11 on page 18.2. SafetywarningConnect the board to the mains voltage. Avoid touching the board while it is connected tothe mains voltage. An isolated housing is obligatory when used in uncontrolled,non-laboratory environments. Galvanic isolation of the mains phase using a variable transformer is always recommended.WARNINGLethal voltage and fire ignition hazardThe non-insulated high voltages that are present when operating this product, constitute a risk of electric shock, personal injury, death and/or ignition of fire.This product is intended for evaluation purposes only. It shall be operated in a designated test area by personnel qualified according to local requirements and labor laws to work withnon-insulated mains voltages and high-voltage circuits. This product shall never be operated unattended.a.Top view.b.Bottom view.Fig 1.Photographs of the UBA2017P demo board3. Specifications4. Wiring diagramConnect the ballast as shown in Figure 3. Keep the wires connected to pins 1 and 2 ofconnector X1 and X2 short. One lamp connects to connector X1, the other lamp connects to connector X2. Connect the mains voltage of 230 V(AC) to pins 2 and 3 of connector X3.Table 1.Electrical specificationDescription comment Ballast type electronicStarting method programmed start with preheat Starting time <1 s Lamp terminals 2⨯4Line voltage 230V (AC), ±20%Line frequency 50Hz/60Hz Lamp type 21W/28W/35W T5Number of lamps 2Mains harmonics complies with IEC 61000-3-2, Class-C Conducted emission complies with IEC55015Table 2.Ballast performanceLamp typeNumber of lamps Lamp power (W)THD (%)Powerfactor I lamp (A)maximum crest factor maximum T5 28 W 228150.9841.651655. Board information5.1 Block diagramThe block diagram includes the functions:•The fuse•ElectroMagnetic Interference (EMI) filter•Full-wave rectifier•Continuous Input Current (CIC) circuit•Improved Valley Fill (IVF) circuit•Half-bridge•Resonant circuit•UBA2017 half-bridge controller5.2 Operating principleFigure5 is a simplified version of the complete diagram of the board. This sectiondescribes the basic functionality of the ballast.5.2.1Improved valley fill functionThe topology of this board is an improved valley fill (IVF), consisting of C vf1, C vf2, D vf1,D vf2, D vf3, D vf4 and C bus. The charge pump capacitors C pump1 and C pump2 which connect tothe lamp voltage signal improve the valley fill function. Both electrolytic capacitors have a rating of 250 V. Do not exceed the maximum rating of the electrolytic capacitors. Channel F1 in Figure5 shows the voltage across the upper electrolytic capacitor C vf1 = C4 in the schematic when the lamp does not ignite.5.2.2Mains harmonicsThe Continuous Input Current (CIC) circuit manages the IEC mains harmonics class-C requirements. The CIC circuit consists of D cic1, D cic2, L cic , C cic . D cic1 is a fast diode in series with the diode bridge. D cic1 ensures a fast switch off behavior of the bridge diodes.5.2.3Lamp current crest factorTo meet the lamp current crest factor for IEC requirements, the lamp current control loop is used. The lamp current control loop reduces the peak of the lamp current when the mains voltage it at the maximum. The lamp current is sensed using resistor R sense . Below 50 kHz the quasi-peak conducted emission requirements of IEC is 110 dB V. Therefore the half-bridge frequency is kept below 50 kHz, so there is headroom to allow some HF ripple in the mains current.5.2.4Small and low-cost half-bridge coilIf a lamp cannot ignite, the ballast generates a voltage of 750 V (RMS) which is sufficient to ignite any T5 lamp. The ignition voltage is maintained over approximate 150 ms to guarantee ignition of cold and old lamps. In this ignition phase, the LC tank inductor is saturating. The UBA2017 controller increases the half-bridge frequency instantaneously when the saturation current occurs. The level of saturation is set using a sense resistor in the source of the low side switch. Figure 7 shows the saturating current and the open lamp voltage during ignition.(1)C1 = V bus (2)C2 = anode V D5(3)F1 = V C4(4)C4 = connector V lampFig 6.Bus voltage during open lamp ignition5.2.5Electrode/filament heatingA winding coupled to the main LC tank inductor heats each electrode. The peak of the transfer is at 90 kHz. The components C fil and L fil set this peak frequency. The resonance frequency of the electrode circuit (C fil , L fil and electrode resistance) determines this peak frequency. The UBA2017 sets the preheat frequency at 90 kHz.There are several advantages to this type of heating circuit:•During the preheat phase, there is enough energy to allow preheat times below 1second.•During the ignition phase, the load of the electrode resistance is small because of the2nd order roll off the C fil and L fil filter. This feature increases the Q of the LC tank enabling either:– a higher ignition voltage to be achieved –the use of a smaller resonance inductor•During normal operation, the electrode current is small at 45 kHz because of the 2ndorder roll off from the C fil and L fil filter. This results in a lower Sum of Squares and higher ballast efficiency.(1)C1 = V bus .(2)C2 = V CPT .(3)C3 = I T2A .(4)C4 = V lamp(connector)Fig 7.Open lamp ignition6. Performance indicatorsThis section includes some of the measurements on the board. The measurements aremade using an Everfine HB-6 ballast analyzer.6.1 Mains harmonics data6.2 Input and output power versus mains input voltage6.3 Lamp voltage and lamp current versus mains input voltageNXP Semiconductors UM10564UBA2017DB1064 2 x 28 W T5 demo board6.4 ElectroMagnetic Interference (EMI) prescan dataa.Line L.b.Line N.Fig 11.Conducted emission pre-scan test results 230V (AC), 50 Hz, 2 28W T5UM10564All information provided in this document is subject to legal disclaimers.© NXP B.V. 2012. All rights reserved.User manual Rev. 1 — 20 August 2012 12 of 21NXP SemiconductorsUM10564UBA2017DB1064 2 x 28 W T5 demo board7. Schematic9. Bill of materialsTable 3.Bill of materialsPart reference Description and value Part number ManufacturerC1capacitor; 1.8nF; 1.6kV B32652A1182J EPCOSC2capacitor; 1.8nF; 1.6kV B32652A1182J EPCOSC3film capacitor; 27nF; 100V ECQV1273JM PanasonicC4capacitor; 22μF; 250V EEUED2E220PanasonicC5capacitor; 27nF; 100V ECQV1273JM PanasonicC6capacitor; 4.7nF; 2kV BFC238560472VishayC7capacitor; 10nF; 400V BFC237051103VishayC8Y-capacitor; 2.2nF VY2222M35Y5US63V7VishayC9capacitor; 4.7nF; 2kV BFC238560472VishayC10capacitor; 22nF; 400V BFC237051223VishayC11capacitor; 220nF; 400V B32562J6224K000EPCOSC12ceramic disc capacitor; 470pF; 1kV DEBB33A471KC1B MurataC13capacitor; 220nF; 400V BFC233922224VishayC14film capacitor; 27nF; 100V ECQV1273JM PanasonicC15film capacitor; 27nF; 100V ECQV1273JM PanasonicC16capacitor; 22μF; 250V EEUED2E220PanasonicC17capacitor; 470nF; X7R FK28X7R1C474K TDKC18capacitor; 220nF; 63V B32529C224J000EPCOSC19film capacitor; 470nF; 63V MKS4D034703C00KSSD WIMAC20capacitor; 100nF; X7R C326C104K5R5TA KEMETC21ceramic disc; 470pF; 1kV DEBB33A471KC1B MurataC22capacitor; 10nF; X7R C316C103K5R5TA KEMETC23capacitor; 470nF; X7R FK28X7R1C474K TDKC24capacitor; 470nF; X7R FK28X7R1C474K TDKC25capacitor (COG); 180pF; 5 %C315C181J1G5TA KEMETC26capacitor; 82nF; X7R C320C823K5R5TA KEMETC27capacitor; 100 nF; X7R C326C104K5R5TA KEMETD1diode; 1N49371N4937-E3_54VishayD2diode; 1N49371N4937-E3_54VishayD3diode; 1N40071N4007-E3_54VishayD4diode; 1N40071N4007-E3_54VishayD5diode; 1N49371N4937-E3_54VishayD6diode; 1N40071N4007-E3_54VishayD7diode; 1N49371N4937-E3_54VishayD8diode; 1N40071N4007-E3_54VishayD9diode; 1N41481N4148-TR NXP Semiconductors D10diode; 1N40071N4007-E3_54VishayD11diode; 1N40071N4007-E3_54VishayD12diode; 1N5244B1N5244B-TAP VishayTable 3.Bill of materials …continuedPart reference Description and value Part number ManufacturerD13diode; 1N49371N4937-E3_54VishayD14diode; 1N41481N4148-TR NXP Semiconductors D15diode; 1N41481N4148-TR NXP Semiconductors D16diode; 1N5244B1N5244B-TAP VishayD17diode; BAT85BAT85_133NXP Semiconductors F1fuse; 1A38211000000LittelfuseL1inductor; 1.5mH RL-5480-4-1500RencoL2inductor; 120μH RLB0712-121KL BournsL3inductor; 120μH RLB0712-121KL BournsL4inductor; 2⨯39mH B82731T2551A020EPCOSL5inductor; 120μH RLB0712-121KL BournsL6inductor; 120μH RLB0712-121KL BournsQ1transistor; TK5A50D TK5A50D ToshibaQ2transistor; TK5A50D TK5A50D ToshibaQ3transistor; BC547C BC547CBU FairchildR1resistor; 180kΩMRS25VishayR2resistor; 470kΩMRS25000C4703FC100VishayR3resistor; 150kΩMRS25000C1503FC100VishayR4resistor; 1ΩMRS25000C1008FC100VishayR5resistor; 1ΩMRS25000C1008FC100VishayR6resistor; 4.7kΩMRS25000C4701FC100VishayR7resistor; 680kΩMRS25000C6803FC100VishayR8resistor; 22kΩMRS25000C2202FC100VishayR9resistor; 1.5ΩMRS25000C1508FC100VishayR10resistor; 1.5 ΩMRS25000C1508FC100VishayR11resistor; 150kΩMRS25000C1503FC100VishayR12resistor; 33kΩMRS25000C3302FC100VishayR13resistor; 33 ΩMRS25000C3309FC100VishayR14resistor; 33 ΩMRS25000C3309FC100VishayR16resistor; 150kΩMRS25000C1503FC100VishayR17resistor; 150kΩMRS25000C1503FC100VishayR18resistor; 150kΩMRS25000C1503FC100VishayR19resistor; 33kv MRS25000C3302FC100VishayR20resistor; 36kΩMRS25000C3602FC100VishayR21resistor; 100kΩMRS25000C1000FC100VishayR22resistor; 56kΩMRS25000C5602FC100VishayR23resistor; 750kΩMRS25000C7503FC100VishayR24resistor; 120 kΩ MRS25000C1203FC100VishayR25resistor; 120 kΩ MRS25000C1203FC100VishayT1transformer; 2.0mH760800095Würth ElektronikT2transformer; 2.0mH760800095Würth ElektronikTable 3.Bill of materials …continuedPart reference Description and value Part number ManufacturerU1Half-bridge controller IC UBA2017P/N1NXP Semiconductors V1Varistor; V10E275P V10E275PL1B LittelfuseX1connector; 4-pin250-204_000-009WAGOX2connector; 4-pin250-204_000-009WAGOX3connector; 3-pin250-203_000-009WAGO10. Inductor appearance and dimensionsTable 4.Half-bridge transformer electrical specificationsParameter ValueCore EE20/10/6Inductance (4 to 1) 2.0 mHSaturation current (4 to 1) 1.1 ADC resistance (4 to 1) 4.95 ΩInductance (3 to 2)10 μHInductance (6 to 5)10 μHOperating temperature-40︒C to +125︒C11. Single lamp 21W/28W/35W T5 PCB variantTo modify the board to drive a single 21W/28W/35W T5 lamp replace or remove theitems in the BOM (Table3) using the components from Table5.Table 5.Table 5.Modified parts of the bill of material for single lamp operationPart reference Comment Manufacturer Part numberRemove--C2; C9; C14; C15; L5;L6; R11; R18; T2L1 2.2 mH Renco RL-5480-2200L42⨯68 mH EPCOS B82731T2351A020C4; C1610μF; 250 V Panasonic ECA-2EHG100C1010 nF; 400 V Vishay BFC237051103R9; R10 3.3ΩVishay MRS2512. References[1]UBA2017 — 600 V fluorescent lamp driver with linear dimming function[2]UBA2017DB1064 — Demo board[3]AN10971 — TL applications with NXP ballast controllers[4]AN10958 — Fluorescent lamp driver with PFC using the UBA2015/16/17 family[5]UBA2016A_15_15A — 600 V fluorescent lamp driver with PFC, linear dimming andboost function[6]UM10561 — UBA2017AT reference design for 420 V (DC)13. Legal information13.1 DefinitionsDraft — The document is a draft version only. The content is still under internal review and subject to formal approval, which may result in modifications or additions. NXP Semiconductors does not give any representations or warranties as to the accuracy or completeness of information included herein and shall have no liability for the consequences of use of such information.13.2 DisclaimersLimited warranty and liability — Information in this document is believed to be accurate and reliable. However, NXP Semiconductors does not give any representations or warranties, expressed or implied, as to the accuracy or completeness of such information and shall have no liability for the consequences of use of such information. NXP Semiconductors takes no responsibility for the content in this document if provided by an information source outside of NXP Semiconductors.In no event shall NXP Semiconductors be liable for any indirect, incidental, punitive, special or consequential damages (including - without limitation - lost profits, lost savings, business interruption, costs related to the removal or replacement of any products or rework charges) whether or not such damages are based on tort (including negligence), warranty, breach of contract or any other legal theory.Notwithstanding any damages that customer might incur for any reason whatsoever, NXP Semiconductors’ aggregate and cumulative liability towards customer for the products described herein shall be limited in accordance with the Terms and conditions of commercial sale of NXP Semiconductors.Right to make changes — NXP Semiconductors reserves the right to make changes to information published in this document, including without limitation specifications and product descriptions, at any time and without notice. This document supersedes and replaces all information supplied prior to the publication hereof.Suitability for use — NXP Semiconductors products are not designed, authorized or warranted to be suitable for use in life support, life-critical or safety-critical systems or equipment, nor in applications where failure or malfunction of an NXP Semiconductors product can reasonably be expected to result in personal injury, death or severe property or environmental damage. NXP Semiconductors and its suppliers accept no liability for inclusion and/or use of NXP Semiconductors products in such equipment or applications and therefore such inclusion and/or use is at the customer’s own risk.Applications — Applications that are described herein for any of these products are for illustrative purposes only. NXP Semiconductors makes no representation or warranty that such applications will be suitable for the specified use without further testing or modification.Customers are responsible for the design and operation of their applications and products using NXP Semiconductors products, and NXP Semiconductors accepts no liability for any assistance with applications or customer product design. It is customer’s sole responsibility to determine whether the NXP Semiconductors product is suitable and fit for the customer’s applications and products planned, as well as for the planned application and use of customer’s third party customer(s). Customers should provide appropriate design and operating safeguards to minimize the risks associated with their applications and products.NXP Semiconductors does not accept any liability related to any default, damage, costs or problem which is based on any weakness or default in the customer’s applications or products, or the application or use by customer’s third party customer(s). Customer is responsible for doing all necessary testing for the customer’s applications and products using NXP Semiconductors products in order to avoid a default of the applications and the products or of the application or use by customer’s third partycustomer(s). NXP does not accept any liability in this respect.Export control — This document as well as the item(s) described herein may be subject to export control regulations. Export might require a prior authorization from competent authorities.Evaluation products — This product is provided on an “as is” and “with all faults” basis for evaluation purposes only. NXP Semiconductors, its affiliates and their suppliers expressly disclaim all warranties, whether express, implied or statutory, including but not limited to the implied warranties ofnon-infringement, merchantability and fitness for a particular purpose. The entire risk as to the quality, or arising out of the use or performance, of this product remains with customer.In no event shall NXP Semiconductors, its affiliates or their suppliers be liable to customer for any special, indirect, consequential, punitive or incidental damages (including without limitation damages for loss of business, business interruption, loss of use, loss of data or information, and the like) arising out the use of or inability to use the product, whether or not based on tort (including negligence), strict liability, breach of contract, breach of warranty or any other theory, even if advised of the possibility of such damages. Notwithstanding any damages that customer might incur for any reason whatsoever (including without limitation, all damages referenced above and all direct or general damages), the entire liability of NXP Semiconductors, its affiliates and their suppliers and customer’s exclusive remedy for all of the foregoing shall be limited to actual damages incurred by customer based on reasonable reliance up to the greater of the amount actually paid by customer for the product or five dollars (US$5.00). The foregoing limitations, exclusions and disclaimers shall apply to the maximum extent permitted by applicable law, even if any remedy fails of its essential purpose.Translations — A non-English (translated) version of a document is for reference only. The English version shall prevail in case of any discrepancy between the translated and English versions.13.3 TrademarksNotice: All referenced brands, product names, service names and trademarks are the property of their respective owners.NXP SemiconductorsUM10564UBA2017DB1064 2 x 28 W T5 demo board© NXP B.V.2012.All rights reserved.For more information, please visit: Forsalesofficeaddresses,pleasesendanemailto:**********************Date of release: 20 August 2012Document identifier: UM10564Please be aware that important notices concerning this document and the product(s)described herein, have been included in section ‘Legal information’.14. Contents1 Introduction . . . . . . . . . . . . . . . . . . . . . . . . . . . . 32 Safety warning. . . . . . . . . . . . . . . . . . . . . . . . . . 33 Specifications. . . . . . . . . . . . . . . . . . . . . . . . . . . 44 Wiring diagram. . . . . . . . . . . . . . . . . . . . . . . . . . 45 Board information . . . . . . . . . . . . . . . . . . . . . . . 55.1 Block diagram. . . . . . . . . . . . . . . . . . . . . . . . . . 55.2 Operating principle . . . . . . . . . . . . . . . . . . . . . . 55.2.1 Improved valley fill function . . . . . . . . . . . . . . . 65.2.2 Mains harmonics . . . . . . . . . . . . . . . . . . . . . . . 75.2.3 Lamp current crest factor . . . . . . . . . . . . . . . . . 75.2.4 Small and low-cost half-bridge coil. . . . . . . . . . 75.2.5 Electrode/filament heating . . . . . . . . . . . . . . . . 86 Performance indicators. . . . . . . . . . . . . . . . . . . 96.1 Mains harmonics data. . . . . . . . . . . . . . . . . . . . 96.2 Input and output power versus mains inputvoltage . . . . . . . . . . . . . . . . . . . . . . . . . . . . . . 106.3 Lamp voltage and lamp current versusmains input voltage. . . . . . . . . . . . . . . . . . . . . 106.4 ElectroMagnetic Interference (EMI) prescandata. . . . . . . . . . . . . . . . . . . . . . . . . . . . . . . . . 117 Schematic. . . . . . . . . . . . . . . . . . . . . . . . . . . . . 128 PCB layout . . . . . . . . . . . . . . . . . . . . . . . . . . . . 139 Bill of materials . . . . . . . . . . . . . . . . . . . . . . . . 1410 Inductor appearance and dimensions. . . . . . 1711 Single lamp 21W/28W/35W T5 PCB variant 1812 References . . . . . . . . . . . . . . . . . . . . . . . . . . . . 1913 Legal information. . . . . . . . . . . . . . . . . . . . . . . 2013.1 Definitions. . . . . . . . . . . . . . . . . . . . . . . . . . . . 2013.2 Disclaimers. . . . . . . . . . . . . . . . . . . . . . . . . . . 2013.3 Trademarks. . . . . . . . . . . . . . . . . . . . . . . . . . . 2014 Contents . . . . . . . . . . . . . . . . . . . . . . . . . . . . . . 21。
Snap-on Equipment VPI SYSTEM II 轮子平衡仪零件手册说明书

41
1
EAC0053J01A
TRAY-WEIGHT,SO LOW DIG
42
1
EAC0053J15A
BRAKE SPACER
43
1
EAC0053J16A
MICROSWITCH PLATE
44
2
EAC0060G03A
BUSHING, WHEELGUARD
45
1
EAM0003J21A
SPRING-EXTENSION WHEELGUAR D, HD
5
1
1-13377A
CIRCLIP-27mm X 1.20mm DIN 471
6
1
1-13609
SCREW-HHCS,M4-16 X 8.8
7
4
1-13909
SCR - HEX SKT HD CAP (M4 x 30mm)DIN912
8
3
1-25433A NUT-M6 KEPS, SERRATED LW ZINC
ten consent of Snap-on Equipment.
Parts Manual
1
TEEWB503D3
Table of Contents
BOM....................................................................................................................................... 3 Balancer Assembly........................................................................................................ 4 Upper display................................................................................................................... 6 2D SAPE assembly............................................................................................................ 7 Vibratory assembly....................................................................................................... 8 Cones and accessories............................................................................................... 9
阳光源电子有限公司 YUAN DC-DC 转换器 Shenzhen Sunyuan Technolo
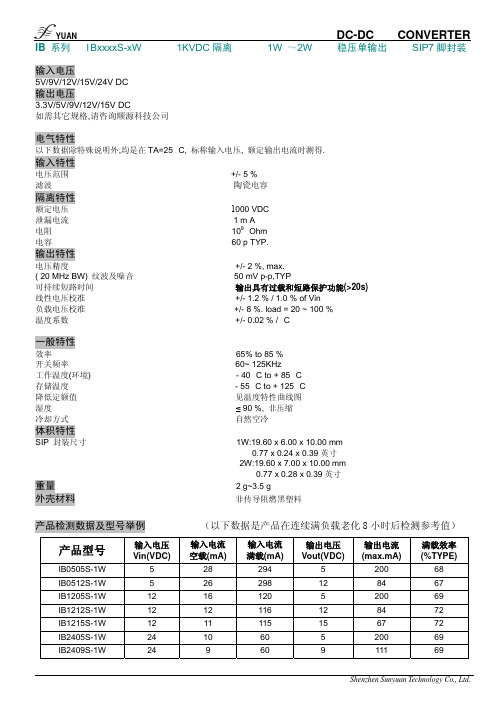
输入电压5V/9V/12V/15V/24V DC输出电压3.3V/5V/9V/12V/15V DC如需其它规格,请咨询顺源科技公司电气特性以下数据除特殊说明外,均是在TA=25° C, 标称输入电压, 额定输出电流时测得.输入特性电压范围+/- 5 %滤波陶瓷电容隔离特性额定电压1000 VDC泄漏电流 1 m A电阻109 Ohm电容60 p TYP.输出特性电压精度+/- 2 %, max.( 20 MHz BW) 纹波及噪音50 mV p-p,TYP可持续短路时间输出具有过载和短路保护功能(>20s)线性电压校准+/- 1.2 % / 1.0 % of Vin负载电压校准+/- 8 %. load = 20 ~ 100 %温度系数+/- 0.02 % / °C一般特性效率65% to 85 %开关频率60~ 125KHz工作温度(环境) - 40° C to + 85° C存储温度- 55 °C to + 125 °C降低定额值见温度特性曲线图湿度≤ 90 %, 非压缩冷却方式自然空冷体积特性SIP 封装尺寸1W:19.60 x 6.00 x 10.00 mm0.77 x 0.24 x 0.39英寸2W:19.60 x 7.00 x 10.00 mm0.77 x 0.28 x 0.39英寸重量 2 g~3.5 g外壳材料非传导阻燃黑塑料产品检测数据及型号举例(以下数据是产品在连续满负载老化8小时后检测参考值)产品型号输入电压Vin(VDC) 输入电流空载(mA)输入电流满载(mA)输出电压Vout(VDC)输出电流(max.mA)满载效率(%TYPE)IB0505S-1W 5 28 294 5 200 68 IB0512S-1W 5 26 298 12 84 67 IB1205S-1W 12 16 120 5 200 69 IB1212S-1W 12 12 116 12 84 72 IB1215S-1W 12 11 115 15 67 72 IB2405S-1W 24 10 60 5 200 69 IB2409S-1W 24 9 60 9 111 69产品型号输入电压Vin(VDC) 输入电流 空载(mA)输入电流 满载(mA) 输出电压Vout(VDC) 输出电流(max.mA) 满载效率(%TYPE)IB2412S-1W 24 8 59 12 84 71 IB2415S-1W 24 757 15 67 73IB0505S-2W 5 45 580 5 400 69 IB0509S-2W 5 42 571 9 200 70 IB1205S-2W 12 25 222 5 400 75 IB1209S-2W 12 23 216 9 200 77 IB1212S-2W12 21 213 12 167 78IB2405S-2W 24 10 119 5 400 70 IB2412S-2W 24 9 104 12 167 80 IB2415S-2W 24 899 15 133 84外形及PCB 布板参考尺寸温度特性曲线和引脚描述Pin 引脚 引脚功能说明1 + V in 输入正2 - V in 输入负3 空脚4 - V out 输出负5 空脚6 + V out 输出正7空脚z 产品设计与规格如有更改,恕不另行通知。
Modicon Premium自动化平台双格式PL7处理器数据表说明书

Product data sheetCharacteristicsTSXP57203Mdouble-format PL7 processor - 550 mA 5 V DCMainRange of productModicon Premium Automation platform Product or component type Double-format PL7 processor Software designationPL7 Junior/ProComplementaryNumber of racks 16 4/6/8 slots 8 12 slots Number of slots1286496Discrete I/O processor capacity 1024 I/O Analogue I/O processor capacity 80 I/O Number of application specific channel <= 24Number of process control channel <= 10 up to 30 simple loopsIntegrated connection type Non isolated serial link 2 female mini DIN 19.2 kbit/s Communication module processor capacity1 CANopen1 fieldbus module (none if CANopen used)1 network module4 AS-Interface bus modulesMemory descriptionInternal RAM (with PCMCIA card) 48 Kwords dataInternal RAM (without PCMCIA card) 48 Kwords program and data PCMCIA card 160 Kwords programPCMCIA card 2688 Kwords additional data storage Maximum size of object areas30.5 %MWi internal words located internal data 32 %KWi constant words located internal data 8132 %Mi located internal bits Application structure1 fast task 1 master task 64 event tasksExecution time per instruction0.19 µs Boolean without PCMCIA card0.25 µs word or fixed-point arithmetic without PCMCIA card 0.21 µs Boolean with PCMCIA card0.42 µs word or fixed-point arithmetic with PCMCIA card 2.6 µs floating points with PCMCIA card 2.6 µs floating points without PCMCIA cardNumber of instructions per ms2.5 Kinst/ms 65 % Boolean + 35 % fixed arithmetic with PCMCIA card3.57 Kinst/ms 65 % Boolean + 35 % fixed arithmetic without PCMCIA cardi s c l a i m e r : T h i s d o c u m e n t a t i o n i s n o t i n t e n d e d a s a s u b s t i t u t e f o r a n d i s n o t t o b e u s e d f o r d e t e r m i n i n g s u i t a b i l i t y o r r e l i a b i l i t y o f t h e s e p r o d u c t s f o r s p e c i f i c u s e r a p p l i c a t i o n s3.7 Kinst/ms 100 % Boolean with PCMCIA card4.76 Kinst/ms 100 % Boolean without PCMCIA cardSystem overhead0.35 ms fast task1 ms master taskMarking CELocal signalling 1 LED green processor running (RUN)1 LED red I/O module or configuration fault (I/O)1 LED red processor or system fault (ERR)1 LED yellow activity on the terminal port (TER)Current consumption750 mA 5 V DCModule format DoubleProduct weight0.52 kgEnvironmentStandards73/23/EEC89/336/EEC92/31/EEC93/68/EECCSA C22.2 No 142IEC 61131-2UL 508CSA C22.2 No 213 Class I Division 2 Group ACSA C22.2 No 213 Class I Division 2 Group BCSA C22.2 No 213 Class I Division 2 Group CCSA C22.2 No 213 Class I Division 2 Group DProduct certifications ABSBVDNVGLLRRINARMRSAmbient air temperature for operation0...60 °CAmbient air temperature for storage-25...70 °CRelative humidity10...95 % without condensation for operation5...95 % without condensation for storageOperating altitude0...2000 mProtective treatment TCIP degree of protection IP20Pollution degree2Offer SustainabilityRoHS (date code: YYWW)Compliant - since 0935 - Schneider Electric declaration of conformitySchneider Electric declaration of conformityREACh Reference not containing SVHC above the thresholdReference not containing SVHC above the thresholdProduct end of life instructions Need no specific recycling operationsContractual warrantyWarranty period18 monthsTSXP57203M is replaced by:Standard environment BMEP582020processor module M580 - Level 2 - DistributedQty 1Reason for Substitution: End of life | Substitution date: 31 December 2018 | Not same dimensions/design -better performances, more services provided。
创新开发平台实验指导书
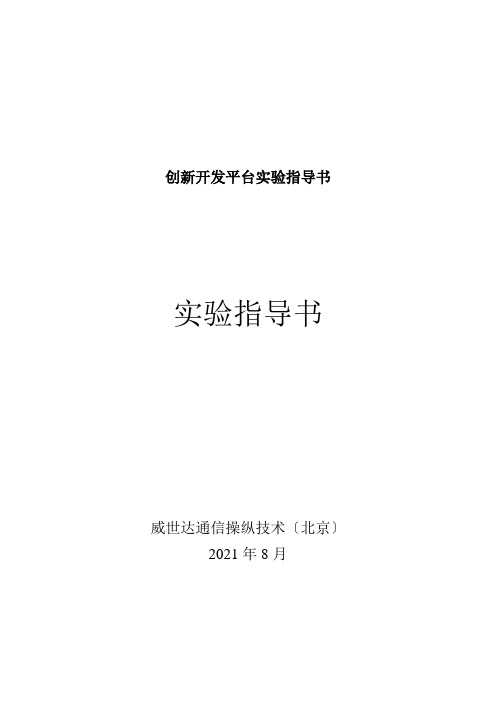
创新开发平台实验指导书实验指导书威世达通信操纵技术〔北京〕2021年8月第一节:FT3150/PL3150模块及其底板 (8)一、FT3150模块及底板 (8)二、PL3150模块及底板 (10)第二节:DI模块 (12)一、硬件原理及连接 (12)二、组网 (13)第一步:创建lonMaker网络 (13)第二步:添加DI设备 (16)第三步:通过配置属性对节点的功能进行配置 (19)三、摸索及实验 (26)第三节:DO模块 (28)一、硬件原理及连接 (28)二、组网 (28)第一步:打开之前创建的LonMaker网络 (28)第二步:添加DO设备 (30)第三步:通过配置属性对节点的功能进行配置 (33)三、摸索及实验 (36)第四节:AI模块 (39)一、硬件原理及连接 (39)二、组网 (40)第一步:创建LonMaker网络 (40)第二步:添加AI设备 (41)第三步:通过配置属性对节点的功能进行配置 (42)三、摸索及实验 (44)第五节:AO模块 (46)一、硬件原理及连接 (46)第一步:打开之前创建的LonMaker网络 (47)第二步:添加AO设备 (47)第三步:通过配置属性对节点的功能进行配置 (48)第四步:PID功能块 (52)三、摸索及实验 (54)第六节:LCD模块 (57)一、硬件连接 (57)二、组网 (57)第一步:打开之前创建的LonMaker网络 (57)第二步:添加LCD设备 (58)第三步:通过配置属性对节点的功能进行配置 (60)三、摸索及实验 (62)第七节:网关 (63)一、硬件连接 (63)二、组网 (63)第一步:创建新的LonMaker网络 (63)第二步:添加Gate设备 (64)第三步:连接绑定 (64)三、摸索及实验 (67)实验一:第一个NodeBuilder项目 (69)一、目标 (69)二、描述 (69)三、实验步骤 (69)第一步:创建一个LonMaker网络 (69)第二步:从LonMaker中启动NodeBuilder并创建一个新的项目 (70)第三步:从NodeBuilder启动设备模板向导并创建一个新的设备模板 (71)第四步:Build一个简单的应用程序 (74)第五步:在LonMaker网络中添加使用新设备模板的设备 (75)实验二:为设备添加设备接口 (76)二、描述 (77)三、实验步骤 (77)第一步:打开之前创建的LonMaker网络及NodeBuilder (77)第二步:为设备添加一个功能块和设备接口 (77)第三步:为新的功能块添加具体功能 (80)实验三:使用NodeBuilder代码向导 (82)一、目标 (82)二、描述 (83)三、实验步骤 (83)第一步:打开之前创建的LonMaker网络及NodeBuilder (83)第二步:使用NodeBuilder代码向导为设备添加一个功能块 (84)第三步:为新的功能块添加具体功能 (88)实验四:输入网络变量数组的处理 (91)一、目标 (91)二、描述 (91)三、实验步骤 (92)第一步:使用代码向导创建DI、DO设备模板 (92)第二步:创建DI设备并添加DI功能代码 (94)第三步:创建DO设备并添加DO功能代码 (95)实验五:指导函数及Debugger操作 (96)一、目标 (96)二、描述 (97)三、实验步骤 (97)第一步:进入Debug状态并设置断点 (97)第二步:一步一步执行代码 (99)组态一:人机界面实验 (101)一、创建网络 (101)1、运行LNS DDE Server。
Keysight Technologies 电路测试产品说明书

Select the essential accessories to complete the testing system you need.
TriMode™ Long Reach Solder Tip
Order #: P75TLRST, Kit of 1 High performance solder tip. Up to 20 GHz bandwidth.
Precision Differential Probing Module
Order #: P75PDPM High performance handheld probing module. Up to 18 GHz bandwidth.
Tip Cable
Order #: P75TC, Kit of 1 Replacement cable for the P75PDPM.
Marker Bands
Order #: 016-0633-XX, Kit of 10 Five pairs of colored bands for marking probe cables to oscilloscope channels.
Adhesive Tape
Order #: 006-8237-XX, Strip of 10 Double sided foam tape for securing solder tips in place.
Copyright © 2008, Tektronix. All rights reserved. Tektronix products are covered by U.S. and foreign patents, issued and pending. Information in this publication
- 1、下载文档前请自行甄别文档内容的完整性,平台不提供额外的编辑、内容补充、找答案等附加服务。
- 2、"仅部分预览"的文档,不可在线预览部分如存在完整性等问题,可反馈申请退款(可完整预览的文档不适用该条件!)。
- 3、如文档侵犯您的权益,请联系客服反馈,我们会尽快为您处理(人工客服工作时间:9:00-18:30)。
SIPMOS®
Tape and reel information Marking Lead free Packing
BSP170P
Parameter Symbol Conditions Unit
min.typ.max. Thermal characteristics
Thermal resistance,
junction -soldering point
R thJS--20K/W SMD version, device on PCB:R thJA minimal footprint--110K/W
6 cm2 cooling area1)--70 Electrical characteristics, at T j=25 °C, unless otherwise specified
Static characteristics
Drain-source breakdown voltage V(BR)DSS V GS=0 V, I D=-250 µA-60--V Gate threshold voltage V GS(th)V DS=V GS, I D=-250 µA-2.1-3-4
Zero gate voltage drain current I DSS V DS=-60 V, V GS=0 V,
T j=25 °C
--0.1-1µA
V DS=-60 V, V GS=0 V,
T j=125 °C
--10-100
Gate-source leakage current I GSS V GS=-20 V, V DS=0 V--10-100nA Drain-source on-state resistance R DS(on)V GS=-10 V, I D=-1.9 A-239300mΩ
Transconductance g fs |V DS|>2|I D|R DS(on)max,
I D=-1.9 A
1.3
2.6-S
1) Device on 40mm*40mm*1.5 epoxy PCB FR4 with 6cm2 (one layer, 70µm thick) copper area for drain connection. PCB is vertical without blown air.
Values
BSP170P
Parameter
Symbol Conditions
Unit
min.
typ.
max.
Dynamic characteristics Input capacitance C iss -328410pF
Output capacitance
C oss -105135Reverse transfer capacitance C rss -3848Turn-on delay time t d(on)-1421ns Rise time
t r -2842Turn-off delay time t d(off)-92138Fall time
t f
-60
90
Gate Charge Characteristics Gate to source charge Q gs --1.4-1.9nC
Gate to drain charge Q gd --4.9-7.4Gate charge total Q g --10-14Gate plateau voltage V plateau
--4.34
-V Reverse Diode
Diode continuous forward current I S ---1.98A
Diode pulse current I S,pulse ---7.6Diode forward voltage V SD V GS =0 V, I F =-1.9 A, T j =25 °C
--0.83-1.1V Reverse recovery time t rr -3654ns Reverse recovery charge
Q rr
-41
62
nC T A =25 °C
Values V GS =0 V, V DS =-25 V, f =1 MHz
V DD =-30 V, V GS =-10 V, I D =-1.9 A, R G =6 Ω
V DD =-48 V, I D =-1.9 A, V GS =0 to -10 V
V R =30 V, I F =|I S |, d i F /d t =100 A/µs
1 Power dissipation
5 Typ. output characteristics
9 Drain-source on-state resistance
13 Avalanche characteristics
BSP170P Package Outline
SOT-223: Outline
Footprint Packaging
Tape
Operating and storage temperature
Dimensions in mm
BSP170P。