过程监控系统在本钢 2 号高炉的应用 2号高炉和热风炉系统结构
浅析炼铁高炉的自动控制系统

C omputer automation计算机自动化浅析炼铁高炉的自动控制系统高永强摘要:随着我国经济的不断发展,社会生产对于钢铁材料的需求也在逐年不断增加。
钢铁行业作为我国的重工业,在钢铁行业的发展过程中,传统的炼铁高炉控制系统已经不能满足实际的工作需求,为有效推动我国钢铁企业产能和产品质量的提高,为钢铁行业的发展能跟上时代的步伐,本文将主要对高炉工艺及炼铁高炉的自动控制系统概述,来进一步分析炼铁高炉的自动控制系统的应用要点和组成。
关键词:炼铁;高炉;自动控制系统众所周知,炼铁是钢铁材料生产过程中的核心部分,而随着我国科学技术的不断发展,人们对钢铁企业的产品质量和生产能力也提出了更高的要求,传统的生产模式已然不能符合时代的发展需求,炼铁作为钢铁企业生产过程中不可忽视的重要环节,在钢铁企业的炼铁生产过程中只有保障高炉的高效运行和不停滞状态外,相关的工作人员还需注意高炉生产过程中的高温和工艺的复杂性,为提高运行的效率和保障生产的安全,钢铁企业应当重视对炼铁高炉自动控制系统的应用。
1 高炉工艺及炼铁高炉的自动控制系统概述1.1 高炉工艺概述高炉运行时通过将焦炭和铁矿石球团混合在一起,并通过氧化还原反映生成生铁和其他的物质,其具体的操作是从装料开始,将炉料从炉顶装入高炉内,然后将热风炉加热到1000℃以上,让热风通过鼓风机形式送入高炉,再经过燃烧的焦炭形成高温的还原气体后将加热缓慢下降的炉料,还原铁矿球团后成铁。
另炉内得铁矿石到达一定的温度时,还会熔化成铁水滴落,这时铁矿石中的其他物质转化为铁渣,形成铁渣分离的状态。
1.2 炼铁高炉的自动控制系统概述自动控制系统是指其运行主要通过PLC 控制系统、监控仪表、远程控制系统、电气系统等对企业的生产进行自动化控制的过程。
在钢铁企业的发展过程中,当前所有大型现代化炼铁高炉都是通过应用仪表检测控制系统、电气自动控制系统和计算机监控管理系统来实现高炉的自动控制炼铁生产,其中仪表检测控制系统和电气自动控制系统是由PLC或DCS系统完成,在其安装费用不会超过规定的预算范围的基础上,以满足提高高炉炼铁效率和保障生产安全的特定的要求。
软水密闭循环冷却系统在高炉中的应用

软水密闭循环冷却系统在高炉中的应用韩立军(本钢板材股份炼铁厂)摘要目前随着技术的进步和高炉长寿的要求,国内外高炉都采纳软水密闭循环系统对高炉炉体和一些阀体进行冷却,通过采纳相应的工艺和设备使软化水水质、供回水温度以及水中溶解气体量得到操纵,同时采取了专门多安全供水措施,保证了高炉冷却器的使用寿命,从而使高炉的一代炉龄得到了进一步的提高。
关键字软水密闭循环高炉长寿冷却壁脱气现代化大型高炉日产铁水达到6000t以上,一旦高炉停炉大修,不仅要花费庞大的大修费用,而且大修的时刻也专门长,同时也限制了钢厂的产量.因而高炉的顺产和长寿对企业的正常生产秩序和经营效益阻碍庞大.高炉生产的目标是优质、高产、低耗、长寿,而长寿是高产、低耗的必要要求。
实践说明要提高高炉一代炉龄,必须提高炉缸、炉底和炉身下部炉腹、炉腰的寿命。
而要提高炉体的寿命,要紧在于采纳高效、长寿的冷却装置,对高炉炉体进行冷却。
高炉冷却系统可分为:工业水冷却、软水密闭冷却循环、汽化冷却。
目前,国内外有相当数量的高炉仍采纳工业水冷却。
但工业水中的硬度、悬浮物和一些杂物极易在冷却器的冷却通道内结垢和堵塞水管,直截了当阻碍高炉冷却成效,是造成冷却器过热烧损的重要缘故。
因此,随着技术的进步和高炉长寿的要求,高炉炉体冷却必须采纳软水密闭循环冷却系统。
本钢的新三号和新四号高炉即采纳这种软水密闭循环冷却系统。
1 软水密闭循环系统冷却系统的优点:软化水是指将水中硬度(要紧指Ca2+、Mg2+离子)去除或降低一定程度的水,水在软化过程中,仅硬度降低而总盐量不变。
在高炉中采纳软水密闭循环系统,比其他冷却方式具有如下优点:1)软水冷却,改善了水质,幸免在冷却元件内因结垢而阻碍传热,改善了冷却成效。
2)软水密闭循环系统是一个与大气隔离的密闭系统,不产生水的蒸发缺失,且在循环中不受污染,损耗降低,对管道的腐蚀也减小。
软水漏损专门小,一样为0.05%~0.1%。
3)能充分利用静压头,幸免了开路循环系统静压头的缺失,还能调剂操纵系统的工作压力,使系统运行更加可靠。
高炉喷煤自动控制系统

高炉喷煤自动控制系统姚瑞英喷煤控制系统由烟气炉、原煤储运、制粉、喷吹四部分组成,主要实现了生产工艺设备的自动/手动控制及保护、工艺数据的自动采集和处理、PID回路的自动调节、工艺画面动态显示、历史和实时趋势显示纪录、紧急停喷报警等功能。
系统介绍 1 硬件配置系统采用Modicon TSX Quantum系列可编程控制器,烟气炉有一套单独的PLC系统,原煤储运、制粉、喷吹公用一套PLC系统,并采用远程I/O网络结构,原煤储运为主站,通过同轴电缆连接制粉、喷吹两个远程站。
两套PLC均通过以太网进行通讯。
2 软件配置运用Concept2.5软件对PLC系统组态编程,画面监控软件选用IFIX软件。
3 网络结构喷煤PLC系统包括烟气炉PLC系统和高炉喷煤PLC系统,如图1所示。
每个控制系统通过以太网进行数据传输和现场设备的控制。
共设两个控制室,5台上位机,其中烟气炉、制粉、喷吹以及主引风机高压变频监控站在一个控制室,原煤储运单独在一个控制室,各上位机之间通过交换机互联,其中由于原煤储运控制室距另外的控制室较远,为确保数据传输的准确性,两台交换机通过光纤介质互联,其他上位机及PLC之间通过双绞线互联。
高压变频监控站通过MB+网控制变频器的频率。
图1 喷煤系统网络拓扑该网络结构有两种方式可以为将来与高炉联网做准备,一是交换机预留光纤口,通过光纤与高炉进行数据通讯;二是通过CPU的MB+口进行数据通讯,实现数据的透明化。
工艺控制 1 原煤储运系统该系统包括8条皮带机、1#~4#圆盘给料机,1#、2#电磁分离器、犁式卸料器,主要负责向1#、2#原煤仓上煤。
根据现场设备情况,可以选择4个圆盘给料机中任何一个或两个圆盘给料机同时给1#或2#煤仓供料,这样共有12个料流可以选择,被选中的皮带则根据料流的方向逆启顺停。
操作人员根据原煤仓需煤量的大小选择相应的料流。
当某一料流运转时,从画面将程序打在“联动”位,若该料流的任一设备出现故障,则系统联停,设备停止顺序与启动顺序相反。
(完整word版)高炉热风炉的控制
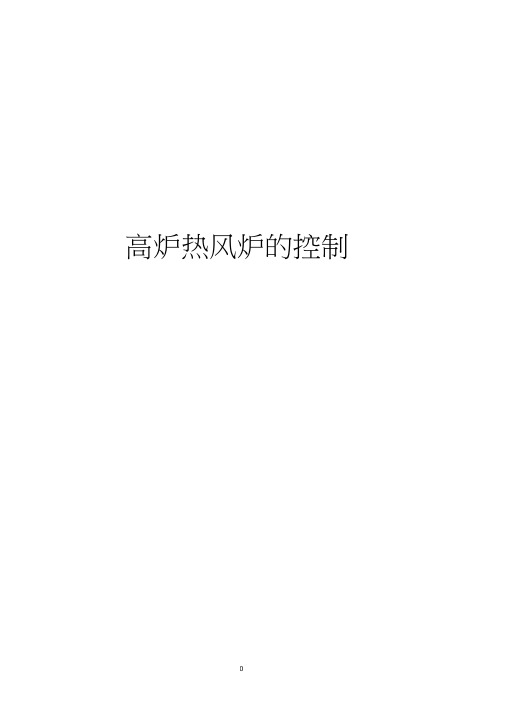
高炉热风炉的控制1. 概述钢铁行业的激烈竞争,也是技术进步的竞争。
高炉炼铁是钢铁生产的重要工序,高炉炼铁自动化水平的高低是钢铁生产技术进步的关键环节之一。
炉生产过程是,炉料(铁矿石,燃料,熔剂)从高炉顶部加入,向下运动。
热风从高炉下部鼓入,燃烧燃料,产生高温还原气体,向上运动。
炉料经过一系列物理化学过程:加热、还原、熔化、造渣、渗碳、脱硫,最后生成液态生铁。
高炉系统组成:1)高炉本体系统2)上料系统3)装料系统4)送风系统5)煤气回收及净化系统6)循环水系统7)除尘系统8)动力系统9)自动化系统高炉三电一体化自动控制系统架构:组成:控制站和操作站二级系统控制内容:仪表、电气传动、计算机控制自动化包括数据采集及显示和记录、顺序控制、连续控制、监控操作、人机对话和数据通信2.热风炉系统(1) 热风炉系统温度检测(2) 热风炉煤气、空气流量、压力检测(3) 热风炉燃烧控制(4) 热风炉燃烧送风换炉控制(5) 煤气稳压控制(6) 换热器入口烟气量控制(7) 空气主管压力控制热风炉燃烧用燃料为高炉煤气,采用过剩空气法进行燃烧控制,在规定的燃烧时间内,保持最佳燃烧状态燃烧;在保证热风炉蓄热量的同时,尽量提高热效率并保护热风炉设备。
热风炉燃烧分三个阶段:加热初期、拱顶温度管理期和废气温度管理⑴加热初期:设定高炉煤气流量和空燃比,燃烧至拱顶温度达到拱顶管理温度后,转入拱顶温度管理期。
在加热初期内,高炉煤气流量和助燃空气流量均为定值进行燃烧。
⑵拱顶温度管理期:保持高炉煤气流量不变,以拱顶温度控制空燃比,增大助燃空气流量,将拱顶温度保持在拱顶目标温度附近,燃烧至废气温度达到废气管理温度后,转入废气温度管理期。
在拱顶温度管理期内,高炉煤气流量为定值进行燃烧,助燃空气流量进行变化以控制拱顶温度。
⑶废气温度管理期:依据废气温度逐渐减小煤气流量,同时以拱顶温度调节控制助燃空气流量,将拱顶温度保持在拱顶目标温度附近,至废气温度达到废气目标温度后,如果热风炉燃烧制选择为“废气温度到” ,则燃烧过程结束;如果选择为“燃烧时间到” ,则调节煤气流量减小到仅供热风炉保持热状态的需要,直到燃烧时间到时燃烧过程结束。
智能化控制在钢铁冶炼中的应用

智能化控制在钢铁冶炼中的应用随着社会的进步和科技的发展,智能化控制越来越多的应用于工业制造中。
钢铁冶炼作为重要的制造产业,也逐渐掌握了智能化控制技术,并取得了良好的效果。
那么智能化控制技术在钢铁冶炼中的应用有哪些呢?一、智能化控制在炼钢中的应用1. 炼钢中的智能化控制技术智能化控制技术在炼钢过程中主要应用于炉料配料系统、炉外预处理系统、炉内自动控制系统、炉外回收系统等方面。
其中,炉料配料系统常采用智能化配料系统,该系统可以根据钢种、生产工艺和炉子的情况进行智能化控制,实现了炼钢生产的自动化和智能化。
2. 智能化控制技术的优势智能化控制技术在炼钢过程中具有控制精确、效率高、稳定性好、自动化程度高等诸多优势。
通过智能化控制技术,可以实现炼钢生产过程的智能化和高效化,大大提高了钢铁冶炼的生产效率和质量水平。
二、智能化控制在炼铁中的应用1. 炼铁中的智能化控制技术智能化控制技术在炼铁过程中主要应用于生铁制备系统、高炉自动控制系统、脱硫脱磷系统等方面。
其中,高炉自动控制系统采用智能化控制技术可以实现高炉自动调控,全面保证了高炉的正常运行和生产效率。
2. 智能化控制技术的优势智能化控制技术在炼铁过程中具有控制精确、效率高、稳定性好、自动化程度高等诸多优势。
通过智能化控制技术,可以实现炼铁生产过程的智能化和高效化,大大提高了钢铁冶炼的生产效率和质量水平。
三、智能化控制技术的未来智能化控制技术的发展前景十分广阔,未来可能应用于更多的制造领域中,包括汽车制造、机械制造、航空制造等。
在钢铁冶炼领域,智能化控制技术也将会在生产工艺、工作环境、设备维护等方面发挥更加重要的作用。
因此,智能化技术的掌握和应用将成为钢铁制造企业提高生产效率和质量水平的关键。
总之,智能化控制技术正在为钢铁冶炼领域带来新的机遇和挑战。
通过持续的技术创新和实践,钢铁制造企业将能够更加高效地进行生产,为现代工业的发展做出更大的贡献。
复吹转炉过程控制系统的研究与开发

第34卷 第4期2010年7月冶金自动化M e t a l l u r g i c a l I n d u s t r y A u t o m a t i o nV o l .34 N o .4J u l y 2010·系统与装置·复吹转炉过程控制系统的研究与开发顾佳晨1,安立文2,张 健1,郭英敏1(1.中冶京诚工程技术有限公司北京京诚鼎宇管理系统有限公司,北京100176;2.本钢板材股份有限公司)摘要:介绍自主研发的转炉过程控制系统功能与模型。
针对转炉静、动态模型不同的应用环境,设计开发了以冶金机理为内核的静态模型和以副枪检测值为基础的动态模型,模型的关键参数采用统计学习的方法进行修正。
其中静态模型中的氧耗计算、加料计算、装料计算、出钢合金计算以及二次补吹计算等,经过现场测试可以满足工艺要求;动态模型正在进一步测试中。
系统框架采用最新的.N E T /W C F 技术开发,以组件化方式设计,确保系统具有良好的扩展性和稳定性。
关键词:复吹转炉;过程控制;模型中图分类号:T F 345.3+4 文献标志码:A 文章编号:1000-7059(2010)04-0037-05R e s e a r c h a n d d e v e l o p m e n t o f p r o c e s s c o n t r o l s y s t e m f o r B O FG UJ i a -c h e n 1,A NL i -w e n 2,Z H A N GJ i a n 1,G U OY i n g -m i n1(1.C a p i t a l E n g i n e e r i n g &R e s e a r c hI n c o r p o r a t i o n L i m i t e d (C E R I )P r o c e s s C o n t r o l &I TD i v i s i o n ,B e i j i n g 100176,C h i n a ;2.B e n g a n g S t e e l P l a t e s C o .,L t d .)A b s t r a c t :T h e f u n c t i o n s a n d t h e m o d e l s o f a p r o c e s s c o n t r o l s y s t e mf o rB O F a r e i n t r o d u c e d i n t h i s p a -p e r .D e d i c a t e d t o t h e i r d i f f e r e n t a p p l i c a t i o n s c e n a r i o s ,t h e s t a t i c a n d d y n a m i c c o n t r o l m o d e l s a r e d e -v e l o p e da c c o r d i n g l y o n d i f f e r e n t p r i n c i p l e s .T h e s t a t i c m o d e l i s d e v e l o p e d o n t h e b a s i s o f m e c h a n i s mo f s t e e l m a k i n g p r o c e s s ,w h i l e t h e d y n a m i c m o d e l i s e s t a b l i s h e d o n t h e m e a s u r e m e n t s o f s u b l a n c e .P r i m a -r y p a r a m e t e r s o f t h e m o d e l s a r e u p d a t e dv i a s t a t i s t i c a l l e a r n i n g .V e r i f i c a t i o n s o f t h e s t a t i c m o d e l a r e m a d e o n e s s e n t i a l c a l c u l a t i o n s t h a t t h e m o d e l p e r f o r m s ,i n c l u d i n g t o t a l o x y g e n v o l u m e ,s c r a p s w e i g h t ,a d d i t i o n s w e i g h t ,a l l o y s a d d i t i o nw e i g h t a n d s e c o n db l o ws e t t i n g .T h e r e s u l t s o f t h e v e r i f i c a t i o n s ,i n w h i c h t h e c a l c u l a t e d v a l u e s a r e c o m p a r e d a g a i n s t p r a c t i c a l d a t a ,i n d i c a t e t h a t t h e m o d e l s a t i s f i e s t h er e q u i r e m e n t s o f p r o d u c t i o n .F u r t h e r t e s t s o n t h e d y n a m i c m o d e l a r e c u r r e n t l y u n d e r w a y .T h e c o n t r o l s y s t e mi s d e v e l o p e d w i t h .N E T /W C F f r a m e w o r k ,a n d t h e c o m p o n e n t b a s e d d e s i g n p r o v i d e s t h e s y s t e m w i t h b e t t e r e x p a n s i b i l i t y a n d s t a b i l i t y .K e y w o r d s :B O F ;p r o c e s s c o n t r o l ;m o d e l 转炉冶炼过程反应剧烈,变量间的相互影响复杂,需控制和调节的参数也较多,随着炉容的扩大和炼钢工艺的发展,单凭操作人员的经验炼钢已不能满足生产要求[1]。
贵冶2#闪速炉自控系统概况及优化

贵冶2#闪速炉自控系统概况及优化陈耕【摘要】贵溪冶炼厂2#闪速炉自控系统采用了当今最较先进的FF现场总线技术.自2007年8月投运以来,系统的稳定性、可靠性都很高.在系统的运行过程中也出现了一些问题,如:部分操作站的用户权限和权限范围发生了变化,导致部分设备不能操作;失重秤控制器(WB930)与Dehav系统的通讯出现过问断性通讯故障,导致失重秤间歇性停运等等.技术人员针对出现的问题进行分析并与生产厂家进行沟通,最终找到解决办法.技术人员根据工艺需要对系统中的控制方案不断进行优化、完善,同时充分利用FF总线系统中的AMS/PRM等资源管理软件对FF总线设备状态进行在线监视及诊断.这些举措大大降低了设备故障发生率,提高了闪速炉作业率.【期刊名称】《铜业工程》【年(卷),期】2013(000)001【总页数】5页(P58-62)【关键词】控制系统;闪速炉;FF总线技术;Dehav系统;预防性维修;资产管理系统【作者】陈耕【作者单位】江西铜业集团公司贵溪冶炼厂,江西贵溪335424【正文语种】中文【中图分类】TF8061 引言FF现场总线技术是当今国际上自动化领域发展的一大热点,纵观这几年国内投入使用的大型自控系统项目,越来越多的使用了FF总线技术,它不仅节省投资,而且可以缩短工程时间。
FF现场总线技术采用数字通讯,它不仅可以获取更多的设备信息,而且稳定性和可靠性都得到提高。
在连续的工艺生产过程中非计划性停车对工厂可能造成巨大损失,如何减少这种情况的发生?预防性维修被认为是一种较好的解决办法[1]。
近年来出现了很多检测设备性能状态的技术设备及软件,这些将预防性维修推向了一个新的高度。
贵冶2#闪速炉自控系统的维护人员采用了如:AMS/PRM等资源管理软件、ValveLink软件等监测和诊断设备的状态及性能,同时不断对工艺过程的控制方案进行优化改进。
这些举措减少了设备检修时间,提高了工艺参数指标及闪速炉作业率。
高炉高风温技术概述
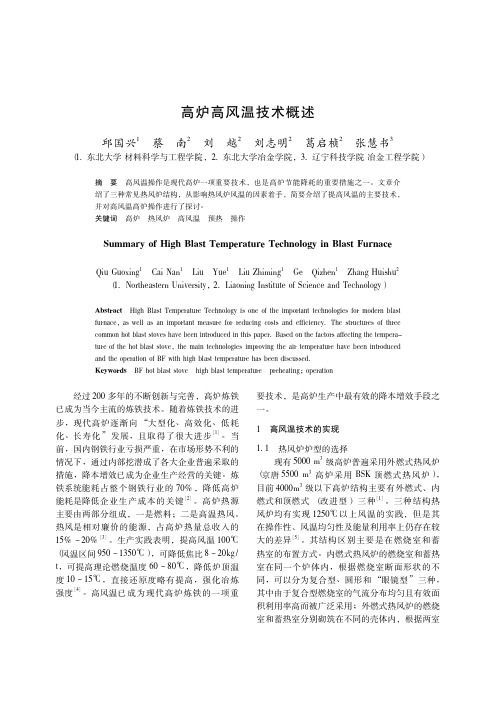
Abstract High Blast Temperature Technology is one of the important technologies for modern blast furnace,as well as an important measure for reducing costs and efficiency. The structures of three common hot blast stoves have been introduced in this paper. Based on the factors affecting the temperature of the hot blast stove,the main technologies improving the air temperature have been introduced and the operation of BF with high blast temperature has been discussed. Keywords BF hot blast stove high blast temperature preheating; operation
它是高炉热风炉的发展方向”,对于大修改造或
是新建的高炉来说,顶燃式热风炉不失为一种优
选方案。同时应该看到,我国热风炉结构多样化
将持续很长时间,三种结构热风炉将长期存在。
1. 2 富化空气及煤气
理论燃烧温度是燃烧过程中重要的指标,热 风炉风 温 一 般 采 用 T风温 = T拱顶 - 150℃ 估 算[7], 拱顶温度的高低主要取决于理论燃烧温度。绝热
Summary of High Blast Temperature Technology in Blast Furnace
本钢炼铁厂高炉热风炉烟气含氧分析系统实践
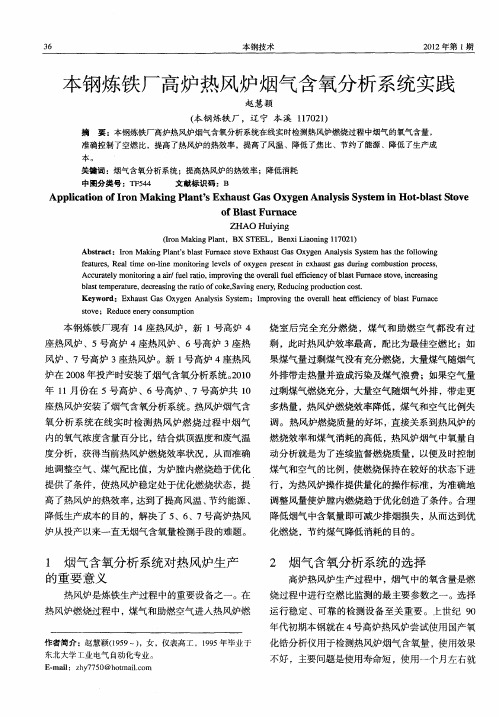
3 6
本钢技术
21 0 2年第 1 期
本钢炼铁厂 高炉热风 炉烟气含 氧分析 系统实践
赵 慧颖
( 钢 炼铁 厂 ,辽 宁 本 溪 17 2 ) 本 10 1
摘 要 :本 钢炼 铁厂高炉热风炉烟气含氧 分析 系统在线实时检测热 风炉燃烧过程 中烟气 的氧气含量 ,
准确控制 了空燃 比 ,提高 了热风炉 的热效率 ,提高 了风温 、降低 了焦 比、节约 了能源 、降低 了生产成
Ac u aeymo i rn i u l ai ,mp o igteo ealue fiin yo ls u aeso e ice sn c rtl n ti gaar e t i r vn v r lf l fce c f at r c tv ,n ra ig o /f r o h e b Fn ba te eaue d ce sn ert fc k ,a i ge ey Re u igp o u t nc s. ls mp rtr , e r aigt ai o o eS vn n r , d cn rd c o o t t h o i
座热风炉 、 5号高炉 4座热风炉、6 号高炉 3座热
风炉 、7 号高炉 3 座热风炉。新 1 号高炉 4座热风 炉在 2 0 年投产时安装 了烟气含氧分析系统 。00 08 2 1 年 1 月份在 5号高炉 、6号高炉 、 1 7号高炉共 1 0
高炉管理创新的探索
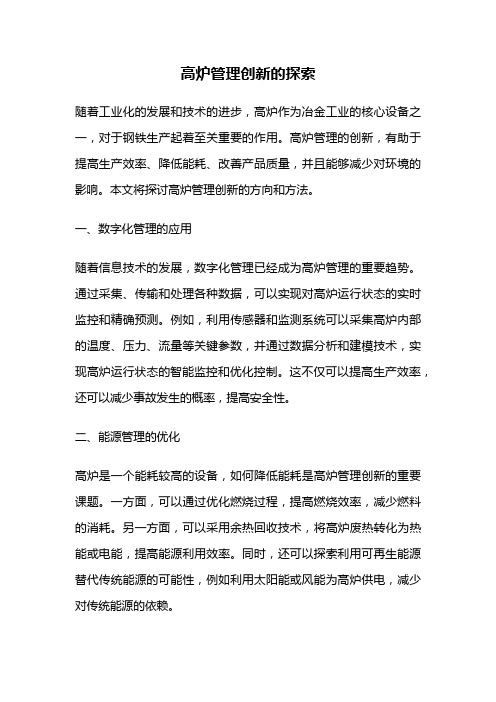
高炉管理创新的探索随着工业化的发展和技术的进步,高炉作为冶金工业的核心设备之一,对于钢铁生产起着至关重要的作用。
高炉管理的创新,有助于提高生产效率、降低能耗、改善产品质量,并且能够减少对环境的影响。
本文将探讨高炉管理创新的方向和方法。
一、数字化管理的应用随着信息技术的发展,数字化管理已经成为高炉管理的重要趋势。
通过采集、传输和处理各种数据,可以实现对高炉运行状态的实时监控和精确预测。
例如,利用传感器和监测系统可以采集高炉内部的温度、压力、流量等关键参数,并通过数据分析和建模技术,实现高炉运行状态的智能监控和优化控制。
这不仅可以提高生产效率,还可以减少事故发生的概率,提高安全性。
二、能源管理的优化高炉是一个能耗较高的设备,如何降低能耗是高炉管理创新的重要课题。
一方面,可以通过优化燃烧过程,提高燃烧效率,减少燃料的消耗。
另一方面,可以采用余热回收技术,将高炉废热转化为热能或电能,提高能源利用效率。
同时,还可以探索利用可再生能源替代传统能源的可能性,例如利用太阳能或风能为高炉供电,减少对传统能源的依赖。
三、智能化维护和保养高炉的维护和保养对于其正常运行和寿命的延长至关重要。
传统的维护方式往往是定期检修和修复,效率较低且容易出现事故。
而智能化维护和保养可以通过传感器和监测系统实现对高炉设备的远程监控和故障诊断,及时发现和解决问题,减少停机时间和维修成本。
此外,还可以利用大数据和人工智能技术,通过对历史数据的分析和挖掘,实现高炉设备寿命预测和优化维护策略的制定。
四、绿色环保的实践高炉作为重要的工业设备,对环境造成的影响不容忽视。
高炉管理创新的一个重要方向就是实现绿色环保。
首先,可以通过改善高炉燃烧过程和煤气净化技术,减少污染物的排放。
其次,可以采用循环利用技术,将高炉废渣和废气中的有价值物质回收利用,减少资源的浪费。
此外,还可以探索利用清洁能源替代传统能源,减少对环境的负面影响。
高炉管理创新是钢铁行业实现可持续发展的关键之一。
《电力建设施工质量验收规程 第2部分:锅炉机组》

DL I CS27F20备案号:J901-20XX中华人民共和国电力行业标准P DL/T 5210.2-XXXX电力建设施工质量验收规程第2部分:锅炉机组Code for construction quality acceptanceof electric power constructPart 2:boiler unit(报批稿)XXXX -XX-XX发布 XXXX-XX-XX实施国家能源局发布本规程是根据《国家能源局关于下达2014年第二批能源领域行业标准制(修)订计划的通知》(国能科技〔2015〕12号)的要求,在原《电力建设施工质量验收及评价规程第2部分锅炉机组》DL/T5210.2-2009和《电力建设施工质量验收及评价规程第8部分加工配制》DL/T5210.8-2009基础上修订的。
《电力建设施工质量验收规程》DL/T5210共6个部分:——DL/T 5210.1 第1部分土建工程——DL/T 5210.2 第2部分锅炉机组——DL/T 5210.3 第3部分汽轮发电机组——DL/T 5210.4 第4部分热工仪表及控制装置——DL/T 5210.5 第5部分焊接——DL/T 5210.6 第6部分火电机组调整试验本部分是DL/T 5210的第2部分。
本规程共14章和4个附录,主要内容包括:总则、术语、基本规定、施工质量验收范围划分表、施工质量验收通用表格及记录签证清单、锅炉本体安装、锅炉除尘装置安装、锅炉燃油系统设备及管道安装、锅炉辅助机械安装、输煤设备安装、烟气脱硫设备安装、烟气脱硝装置安装、锅炉炉墙砌筑、加工配制等。
附录A、附录B、附录C、附录D为规范性附录。
本规程由中国电力企业联合会提出。
由电力行业火电建设标准化技术委员会归口。
本规程主要起草单位:中国电建集团核电工程公司、中国能源建设集团天津电力建设有限公司、中国能源建设集团安徽电力建设第一工程有限公司。
本规程参加起草单位:中国电建集团河南工程公司、中国能源建设集团湖南火电建设有限公司、四川电力建设三公司、中国能源建设集团浙江火电建设有限公司、上海电力建设有限责任公司、山东诚信工程建设监理有限公司、中国电力建设工程咨询有限公司。
100t电炉二级控制系统过程模型及应用

~
质 量平衡计算 一
设定 值计算
化工 程 和产 品 研 发工 作 。
收 稿 日期 : 2 0 1 2 . 1 2 . 2 8
}
图 1 装 料 模 型
自动化应用 } 2 0 1 3 4期 3 5
系 统 解 决 方 案 黼瀚豳黼 在E A F的冶炼 之前 有 充 足 的时 间 进 行上 料 计 算 . 为 了确 定 废 钢 斗 装 货 时 间 和使 废 料 准 备 好 . 上 料 计 算 必 须 由操 作 员 开 始 该 模 型 具 备 以下 特点 : ( 1 ) 目标 出 钢 重 量 、 计 划 的钢 成 分 和 电 炉 的 工 厂 实 际 以及 上 料 废 钢 斗 的数 量 都 被 考 虑 作 为模 型输 入 ( 2 ) 根 据 选 择 的标 准 桶 装 货 计 划 , 按 分 层 堆 积 的 顺 序 计 算 废 钢 料 种类 和重 量
Ke y wor d s: EAF e l e c t r i c s t o v e; s e c o n d s y s t e m; S I EM E NS VAI ; p r o c e d u r a l mo d e l
0引 言
特 殊 钢 系 统 产 品 升 级 技 改 项 目是 莱 钢 按 照 山东
要 功 能 如 图 1所 示
▲
1二级 系统过程模型功能
熔 化 过 程 的 冶 金 学 模 型 .由 提 供 商 基 于 物 理 、 化
高炉炼铁技术装备进步
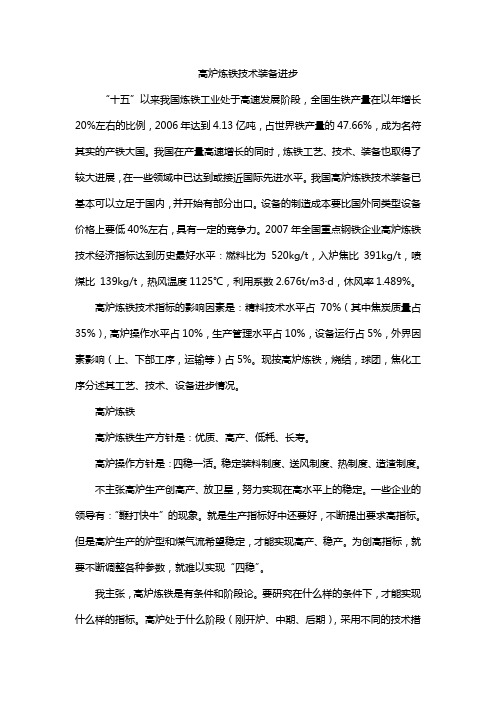
高炉炼铁技术装备进步“十五”以来我国炼铁工业处于高速发展阶段,全国生铁产量在以年增长20%左右的比例,2006年达到4.13亿吨,占世界铁产量的47.66%,成为名符其实的产铁大国。
我国在产量高速增长的同时,炼铁工艺、技术、装备也取得了较大进展,在一些领域中已达到或接近国际先进水平。
我国高炉炼铁技术装备已基本可以立足于国内,并开始有部分出口。
设备的制造成本要比国外同类型设备价格上要低40%左右,具有一定的竞争力。
2007年全国重点钢铁企业高炉炼铁技术经济指标达到历史最好水平:燃料比为520kg/t,入炉焦比 391kg/t,喷煤比139kg/t,热风温度1125℃,利用系数2.676t/m3〃d,休风率1.489%。
高炉炼铁技术指标的影响因素是:精料技术水平占70%(其中焦炭质量占35%),高炉操作水平占10%,生产管理水平占10%,设备运行占5%,外界因素影响(上、下部工序,运输等)占5%。
现按高炉炼铁,烧结,球团,焦化工序分述其工艺、技术、设备进步情况。
高炉炼铁高炉炼铁生产方针是:优质、高产、低耗、长寿。
高炉操作方针是:四稳一活。
稳定装料制度、送风制度、热制度、造渣制度。
不主张高炉生产创高产、放卫星,努力实现在高水平上的稳定。
一些企业的领导有:“鞭打快牛”的现象。
就是生产指标好中还要好,不断提出要求高指标。
但是高炉生产的炉型和煤气流希望稳定,才能实现高产、稳产。
为创高指标,就要不断调整各种参数,就难以实现“四稳”。
我主张,高炉炼铁是有条件和阶段论。
要研究在什么样的条件下,才能实现什么样的指标。
高炉处于什么阶段(刚开炉、中期、后期),采用不同的技术措施,实现什么样的指标。
高炉炼铁要讲科学,减少人为主观因素的影响。
不能不讲条件,只要先进指标,这不是用科学发展观炼铁。
当前,我国高炉炼铁存在的最大技术问题,就是原燃料质量不稳定,造成高炉生产难以稳定。
“一活”是指炉缸活跃。
评价炉缸活跃的指标是:一是高炉鼓风能否吹透中心料柱(要求风速要高,中心煤气CO2含量要高)。
高炉二级系统方案
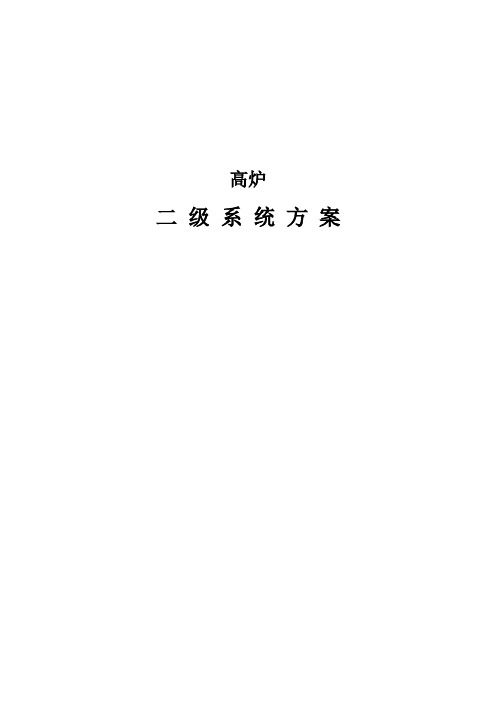
高炉二级系统方案“高炉二级系统”是基于高炉基础自动化系统之上的高炉管理系统,本系统通过OPC从一级自动化系统采集实时数据,存储于高炉二级系统的数据库,通过对这些数据的统计、计算、汇总、分析等一系列专业技术处理,完成实时数据显示、历史趋势显示、风口管理、出铁管理、物料成分管理、变料管理、报表管理等功能,为高炉的生产操作、管理和决策提供了有力的支持。
高炉二级系统已成为炼铁生产过程中不可或缺的组成部分。
1. 数据采集现代大型高炉检测和自动化系统的投入对高炉低能耗、提高生产效率以及稳定运行都起到了十分重要的作用,同时,大量的监测数据也为操作人员作出最佳决策提供了重要的依据。
因此,高炉相关数据采集应尽量全面和及时。
1.1. 定周期数据采集数据采集周期为1分钟。
定周期采集的数据有以下几部分:操作参数:风量、风温、热风压力、冷风压力、顶压、压差、富氧量、富氧率、顶温最高、顶温最低、顶温平均、喷煤量、大气湿度。
炉身部分:炉喉、炉基、炉衬温度测点。
炉顶十字测温数据。
冷却壁部分:铸铁冷却壁、铜冷却壁、高炉本体供水系统温度、流量、压力。
动力消耗:蒸汽流量、氧气流量、压缩空气流量。
布袋除尘:箱体和主管的温度、压力、压差、箱体及管道内粉尘检测值、箱体反吹时间等。
水温差及炉皮温度数据。
以上所有数据按小时、班、天进行统计、计算、汇总并保存到数据库中,用于形成报表、历史趋势图及查询。
1.2. 实时数据采集实时数据采集包括:焦炭称量数据、焦炭水分数据、矿称量数据、高炉布料数据。
以上所有数据按班、天进行统计、计算、汇总并保存到数据库中,用于形成报表及查询。
1.3. 定周期写回一级因高炉一级系统自身无法进行复杂化计算,本系统根据定周期采集的数据自动计算透气性、炉腹煤气量、透气阻力系数、标准风速、实际风速、鼓风动能、理论燃烧温度等高炉操作标参数并写回到一级,用于指导一级的操作。
回写周期为1分钟。
以上所有数据按小时、班、天进行统计、计算、汇总并保存到数据库中,用于形成报表、历史趋势图及查询。
高炉炉内监测技术新进展

高炉炉内监测技术的新进展高征铠(北京科技大学北京!"""#$)前言高炉是一个在高温高压条件下冶炼生铁的密闭反应器。
目前,工长通过常规的温度、压力、流量和煤气成分等检测结果来判断炉况、操作高炉。
对工长来说,高炉仍然是一个黑匣子。
根据高炉操作的需要,开发高炉炉内监测技术,打开高炉黑盒子,使高炉工长能及时了解高炉炉内的状况,变被动操作为主动操作是炼铁工作者梦寐以求的愿望。
为了改变现有炉内监测技术不足的状况,北京科技大学和北京神网创新科技有限公司发明了插入式炉窑摄像仪(专利号%&"’!’!()#*"),合作研制生产了高炉料面红外摄像仪和图像信息处理系统、高炉风口红外摄像仪和图像信息处理系统、高炉炉体监测与诊断系统等新型高炉炉内监测装置。
这些装置能在高炉生产条件下在线观察料面气流分布情况和炉顶设备运行状况、观察风口的工作状况和喷煤情况、了解炉衬的温度分布与侵蚀状况。
这些新型炉内监测装置,在打开高炉黑盒子状况方面取得了进展,获得的直观影像和图像信息对高炉工长操控高炉具有指导意义,已经在很多高炉上得到应用。
!高炉料面红外摄像仪和图像信息处理系统对高炉炉喉断面状况的检测需要推动了新技术的开发。
上世纪八十年代末、九十年代初,国内外研究开发了采用机械扫描方法得到高炉料面温度分布图像的“热图像仪”、“高炉炉顶料面温度摄像仪”,采用摄像机的“监视用摄像机”等装置,观察料面状况和分析料面的温度分布,用于指导高炉操作,在打开高炉黑盒子状况方面迈进了一大步。
受限于当时的技术水平和条件,装置形体大、价格昂贵,仪器安装在炉壳外部,观察孔很大、移动和防护装置复杂、扫描装置寿命短、保护气体用量大、生产维护费用高。
在高炉使用过程中镜头和视窗结灰问题一直没有解决,复杂的视窗活门和机械调焦装置经常出现故障,在高炉生产过程中不能进行维护和检修,只能等待休风时才能处理,因而没有得到推广应用。
热风炉计算——精选推荐

quotquotquotquot第十一篇热风炉计算第一章热风炉的结构形式第一节热风炉结构形式的演变高炉炼铁在quot年开始加热鼓风炼铁。
当时用的是铸铁管换热式热风炉。
到quot年改用固体燃料加热的蓄热式热风炉quotamp年采用了气体燃料加热的蓄热式热风炉形成了现在内燃式热风炉的雏形。
随着高炉冶炼技术的不断发展高炉风温不断提高当风温达到’’’以上时内燃式热风炉就频繁的发生拱顶裂缝、火井燃烧室倾斜、倒塌、掉砖甚至短路致使热风炉使用寿命大大缩短。
分析其主要原因是由于燃烧室和蓄热室同包在一个钢壳内用隔墙分开在燃烧和送风过程中产生温差波动尤其是下部温差很大加上金属燃烧器的脉动燃烧在燃烧室发生共振而引起的。
因而出现了取消隔墙的设计思想’年德国人首先提出了外燃式热风炉的专利quot年美国人建造了世界上第一座外燃式热风炉。
然而外燃式热风炉广泛应用生产还是近’年的事。
amp’amp年联邦德国先后建造了地得式、柯柏式、马琴式外燃热风炉年日本综合柯柏式和马琴式的优点建造了新日铁式外燃热风炉。
由于外燃式热风炉的应用使先进高炉的风温达到了’’’’的水平。
ampquot年我国安阳水冶铁厂和济南铁厂首先建造了外燃式热风炉称“水冶型”外燃式热风炉类似地得式。
年本钢号高炉炉容’’’建了“水冶型”外燃热风炉amp年鞍钢建成“鞍外型”外燃式热风炉类似马琴式应用于amp号高炉炉??-??第一章热风炉的结构形式容quotquotamp’’年鞍钢又设计建造了“鞍外型”外燃式热风炉类似新日铁式应用于’号高炉炉容quotamp年宝钢号高炉引进了日本新日铁式外燃热风炉。
在研制和建造外燃式热风炉的同时对内燃式热风炉的弊病进行改造荷兰霍戈文公司首先建成改造型内燃热风炉它基本上克服了传统内燃式热风炉的通病实现了高温、高效、长寿。
我国有代表性的效果较好的改造型内燃热风炉如amp 年投产的鞍钢amp号高炉炉容amp’热风炉和ampamp年投产的武钢号高炉炉容quotquot热风炉。
炼铁厂2高炉系统功能考核报告

炼铁厂2高炉系统功能考核报告炼铁厂2号高炉(1000m3)优化升级改造工程于2013年8月12日点火开炉,9月6日产量达到2403.8吨,9月12日焦比达到409.7kg/t,高炉实现达产达标,目前炉况稳定顺行。
依据2号高炉优化升级改造工程初步设计要求,炼铁厂制定方案从2013年9月22日至10月1日对2号高炉系统进行功能考核,考核内容包括工艺技术指标、能源指标、水渣指标、除尘指标四个部分,考核结果如下:一工艺技术指标考核2013年9月22至10月1日,进行了工艺技术指标考核,指标考核结果见表1,结果表明,5项工艺技术指标全部达到设计值,利用系数、焦比超过设计值,实现了达产达标。
表1 2号高炉工艺技术指标考核结果考核指标设计值实测平均值考核时间考核结果利用系数 2.4/m3.d 2.5303 9.22~10.1 合格焦比410 kg/t 407.02 9.22~10.1 合格喷煤比145kg/t 148.51 9.22~10.1 合格富氧率3% 3.257 9.22~10.1 合格炉顶压力0.16MPa,最大0.18MPa 0.15 9.22~10.1 合格二能源指标考核2013年9月22日至10月1日,按方案进行了能源指标考核,考核结果见表2,结果表明,22项能源指标中18项达到设计指标,有4项未达到设计指标。
其中:①工业净循环水流量设计145m3/h,实际平均为78.72m3/h,主要是由于炉喉十字测温影响布料,拆除炉喉十字测温后水量减少100 m3/h,导致工业净循环水流量未达标;②工业净化水流量设计300m3/h,实际平均为68.4m3/h,是由于该路水为高炉备用水,主要供风口损坏后的供水及炉前打水使用,目前用水量较少;③送风装臵最高温度未达标,设计要求≤260℃,实际平均为274℃,主要是吹管中间部位及下短节法兰处温度超标,目前尚无温度超过300℃的部位,在线送风装臵均能满足生产需要;④炉顶喷水流量设计60m3/h,实际平均为25.75m3/h,主要是炉顶喷水装臵的喷水孔太小,容易被粉尘堵塞导致水量小,已经联系厂家在高炉10月16日计划检修时处理。
棒材连轧二级过程控制系统的应用
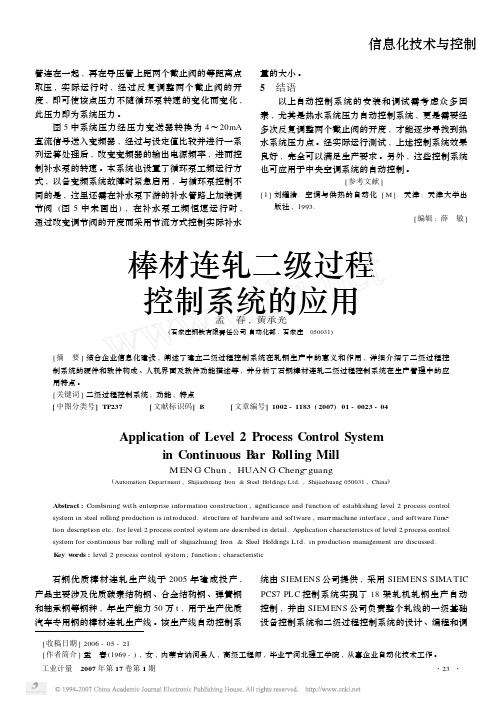
管连在一起,再在导压管上距两个截止阀的等距离点取压,实际运行时,经过反复调整两个截止阀的开度,即可使该点压力不随循环泵转速的变化而变化,此压力即为系统压力。
图5中系统压力经压力变送器转换为4~20mA 直流信号送入变频器,经过与设定值比较并进行一系列运算处理后,改变变频器的输出电源频率,进而控制补水泵的转速。
本系统也设置了循环泵工频运行方式,以备变频系统故障时紧急启用,与循环泵控制不同的是,这里还需在补水泵下游的补水管路上加装调节阀(图5中未画出),在补水泵工频恒速运行时,通过改变调节阀的开度而采用节流方式控制实际补水量的大小。
5 结语以上自动控制系统的安装和调试需考虑众多因素,尤其是热水系统压力自动控制系统,更是需要经多次反复调整两个截止阀的开度,才能逐步寻找到热水系统压力点。
经实际运行测试,上述控制系统效果良好,完全可以满足生产要求。
另外,这些控制系统也可应用于中央空调系统的自动控制。
[参考文献][1]刘耀浩.空调与供热的自动化[M ].天津:天津大学出版社,1993.[编辑:薛 敏]棒材连轧二级过程控制系统的应用孟 春,黄承光(石家庄钢铁有限责任公司自动化部,石家庄 050031) [收稿日期]2006-05-21 [作者简介]孟 春(1969-),女,内蒙古讷河县人,高级工程师,毕业于河北理工学院,从事企业自动化技术工作。
[摘 要]结合企业信息化建设,阐述了建立二级过程控制系统在轧钢生产中的意义和作用,详细介绍了二级过程控制系统的硬件和软件构成、人机界面及软件功能描述等,并分析了石钢棒材连轧二级过程控制系统在生产管理中的应用特点。
[关键词]二级过程控制系统;功能;特点[中图分类号]TP237 [文献标识码]B [文章编号]1002-1183(2007)01-0023-04Application of Level 2Process Control Systemin Continuous B ar R olling MillM EN G Chun ,HUAN G Cheng 2guang(Automation Department ,Shijiazhuang Iron &Steel Holdings Ltd 1,Shijiazhuang 050031,China )Abstract :Combining with enterprise information construction ,significance and function of establishing level 2process control system in steel rolling production is introduced.structure of hardware and software ,man 2machine interface ,and software func 2tion description etc.for level 2process control system are described in detail.Application characteristics of level 2process control system for continuous bar rolling mill of shijiazhuang Iron &Sleel Holdings Ltd.in production management are discussed.K ey w ords :level 2process control system ;function ;characteristic 石钢优质棒材连轧生产线于2005年建成投产,产品主要涉及优质碳素结构钢、合金结构钢、弹簧钢和轴承钢等钢种,年生产能力50万t ,用于生产优质汽车专用钢的棒材连轧生产线。
- 1、下载文档前请自行甄别文档内容的完整性,平台不提供额外的编辑、内容补充、找答案等附加服务。
- 2、"仅部分预览"的文档,不可在线预览部分如存在完整性等问题,可反馈申请退款(可完整预览的文档不适用该条件!)。
- 3、如文档侵犯您的权益,请联系客服反馈,我们会尽快为您处理(人工客服工作时间:9:00-18:30)。
过程监控系统在本钢2号高炉的应用张亮(浙江万里学院智能控制技术研究所,浙江 宁波,315101)摘要:本文以本钢2号高炉大修改造为背景,根据高炉工艺对计算机监控系统的要求,采用SIEMENS公司S7-400系列的PLC和控制计算机构成了计算机过程监控系统。
该系统具备了现场过程数据的动态监视功能、历史数据的归档功能、异常信号的报警功能、现场操作的指导功能和对生产过程的控制功能等,系统投入运行以来,工作正常,控制平稳,为高炉迅速达产创造了良好的环境和条件,具有较强的实用性。
关键词:高炉;过程控制;监控系统中图分类号:TP273+.5 文献标识码:BApplication of Process Monitoring System for NO.2 Blast Furnace ofBenxi Iron and Steel Co.Zhang Liang(Institue for Intelligence Control Technology of Zhejiang Wanli University,Ningbo,315101) ABSTRACT The article based on rebuilding of NO.2 BF in Benxi Iron and Steel Co.According to the equirement of the computer monitoring system in the crafts of BF, a process computer system has been set up and it adopted control computer and S7-400 series PLC produced by SIEMENS company .At the mean time, Monitoring and control parts are configured and programmed to realize the function of monitoring alarming of abnormal signals, logging of history date, guiding of control .After the system put to use, all the things have proved to be normal work, steadily control and it has practicality for the perfect condition and surrounding for the NO.2 BF achieving its goal in production.KEY WORDS blast furnace; process control; monitoring control system1 引言本钢集团公司2号高炉始建于1917年,高炉容量为380m3,配有4座热风炉,2台铸铁机,2台75m2烧结机。
本钢2号高炉由于连续生产多年,远远超过高炉长寿标准,高炉四段26号、3号、4号冷却壁发生破损、炉底温度高,设备老化,控制、监视不全面,故障率高,直接影响了生产。
本钢集团公司决定对2号高炉进行拆除性大修。
本次大修将仪表盘全部拆除,过程控制和监控部分全部采用计算机控制。
2 过程监控系统的构成与实现在对本钢2号高炉过程监控系统设计时,借鉴了国内外同类型高炉在自动化仪表方面的先进技术和经验,对高炉的过程检测和自动控制系统进行了全新的设计,除特别重要的工艺参数及操作器以外,取消了原检测控制系统庞杂的二次仪表,采用计算机过程监控系统,监控高炉的生产过程,由该系统完成对高炉的过程检测、自动控制,数据处理、数据图形显示和记录。
一、总体方案设计充分利用计算机网络的优势,以主操作站为中心实现集中操作、分散控制,尽可能减少计算机系统外围的布线量。
考虑到高炉系统有大量的顺序控制,具有较多的过程信号检测与控制的情况,选择德国西门子公司的S7-400 PLC为过程站的设备,采用性价比好的DELL PC 为上位机,编程软件和监控软件均采用西门子公司的产品,该方案集计算机、仪表和电气控制于一体。
二、系统的构成高炉计算机控制系统是集机械、电气控制和计算机应用为一体的技术。
计算机过程监控系统的布局及网络结构如图1。
系统由上料系统、高炉本体、热风炉三个过程站和三个操作站组成,每个过程站分别由前端采集控制站和控制站两部份组成。
所用模拟量输入均采用独立通道模板,以免相互影响;所有开关量输出均采用无触点输出模板,避免因继电器触点粘连引起的系统控制失灵等不必要的麻烦;所有阀位输入均采用光电藕合输入模板,避免因执行机构阀位反馈信号窜强电而损坏计算机。
图.1 2号高炉和热风炉系统结构Fig 1 System Structure of NO.2 BF and Airheater(1) 上料系统过程站从工艺方面说,上料系统包括卷扬和槽下两部份,它们共用一个过程站,该过程站既包含电气专业逻辑控制,又包含仪表专业的过程检测和控制,但以电气专业为主,故该站归属电气专业设计,采用S7-400 PLC作控制站。
该站除电气专业逻辑控制外,主要完成12个原料斗电子称量及料钟炉顶部分工艺参数的检测控制及各开关检测。
(2) 高炉本体过程站高炉本体过程站主要完成高炉本体工艺的数据采集与控制,包括炉身、炉缸各层温度,热风温度,热风压力,冷风压力,冷风流量,炉顶压力,料线料位,炉喉十字测温及料钟系统的各工艺参数的检测,炉顶压力及料罐均压的自动控制等。
(3) 热风炉过程站热风炉过程站主要完成4座热风炉、富氧系统及预热器各工艺参数的数据采集和控制,包括热风炉炉顶温度,烧炉用空气,煤气的流量压力,温度及冷风均压,烟气均压,烟气温度等参数的检测及燃烧配比自动控制;富氧系统的流量、压力,温度差压的检测及氧量控制和安全联锁;空气、煤气预热器前后温度、压力、差压的检测及冷风压力,流量、温度的检测和热风温度的控制等。
(4) 高炉本体操作站-高炉中央控制操作室为了适应工艺操作要求,本操作站设置两个站:一个为主操作员站用来显示高炉原料监视操作屏和高炉上料监视操作屏;另一个站主要用来显示生产操作技术参数、区域图、曲线图等画面,两者也可互为备用。
操作人员通过观察计算机监控屏的显示及工作状态,控制各种设备。
采用一机多屏的方式,用两台21寸彩色CRT显示高炉原料监视操作屏和高炉上料监视操作屏,两台CRT分别放在主控室和原料操作室。
(5) 工程师站工程师站由一台上位机、一台CRT和一台打印机组成。
工程师站具有对各系统进行组态权和运行权,可以进行料制的设定,当前料车的车次、周期、程序信息的显示,生产工艺过程的显示,程序打印等功能。
(6) 热风炉操作站动态显示5#、6#、7#、8#热风炉送风、闷炉、燃烧工作状态;冷风、热风、煤气、废气管道的工作状态监测,各种阀的工作状态显示和调节控制。
(7) 高炉计算机网络2号高炉三个过程站都可以独立完成各自的任务,根据生产工艺的需要,将原来各自独立的过程站和操作站连结起来组成工业以太网,做到资源共享,互调数据、画面等,构成完整的过程监控系统,因此在S7-400中增加了CP 443-1通讯模块,在上位机中增加了CP 1613通讯板,利用光链路模块(OLM)将3台PLC和4台上位机通过光纤电缆进行连接,形成管理级、单元级和现场级的通讯网络。
3 过程监控系统的实现一、过程站的编程和组态采用SIMATIC STEP 7软件通过个人电脑进行编程、组态。
SIMATIC STEP 7软件含有全部所需开发、编辑、打印、文件、程序上装、下装、监视、在线或离线改变,程序保持和组态等功能。
S7-400 PLC 不仅完成集中控制并且还完成多级分布控制。
整个系统共有AI/AO 200余点,DI/DO 1200余点,PID调节回路两个及若干个内部变量的运算。
二、监控系统人机界面的实现通过对SIEMENS工业控制软件包进行二次开发,完成了上位机监控系统的设计,监控系统的主要功能模块如下:(1)高炉工艺流程模块高炉工艺流程模块主要完成料制的设定,当前料车的车次、周期、程序信息的显示;燃料由料槽放入称量斗到料车、经斜桥达到炉顶、开小钟、均压、开大钟装入高炉等一系列过程监控,以动态画面显示高炉工艺流程。
(2) 高炉生产操作技术参数模块高炉生产操作技术参数模块,完成对炉况进行综合判断,同时根据原、燃料理化性能、风机能力、运输条件、设备运转情况等外界条件的变化,通过对风量、批重、负荷、煤粉喷吹量、风温、风口面积等及时准确的调整,保持炉况顺利,从而不断提高高炉的技术操作水平。
该模块除了完成对操作技术参数的监控和东西探尺的位置移动曲线显示外,还显示对应的上下限报警。
对于授权用户可在线设定风口面积,冷风风速,可在线计算鼓风动能和理论燃烧温度。
(3) 操作参数记录曲线操作参数记录模块主要记录风温、风压、风量曲线;焦矿、称重曲线;压力、压差曲线;全压差曲线;炉顶、炉喉温度曲线;炉缸、炉身温度曲线。
记录曲线存档一个月内容,分成四个区域:数值显示;风量、风压、风温、顶压;上、下部压差及炉顶温度曲线图。
(4) 称重曲线称重曲线模块分为两屏,焦炭和烧结称重,各种杂矿称重,画面不仅显示了每批炉料的重量,而且记录了每个班次所上的各种炉料。
(5) 高炉测温显示模块该模块主要完成炉顶、炉喉温度;炉身一层、三层温度;炉缸温度;炉基温度;炉底一层、四层温度;十字测温。
(6) 高炉炉底侵蚀计算与显示在高炉生产过程中,炉缸不断地被侵蚀,特别是在高炉服役后期,过分的炉缸侵蚀直接影响到高炉生产的安全。
为了测定高炉内衬的侵蚀情况,以传热理论为依据,建立了计算炉底或炉缸侧墙的剩余厚度。
运用了传热学及计算机技术,达到了较高的综合性能,目前运行图3 炉底侵蚀界面Fig.3 The Interface of Corrosion at the Blast Furnace Bottom(7) 生产操作数据打印利用历史数据库,可以预览和打印当班或当天生产操作数据报表,包括温度、流量、压力等系统参数,也可以直接将屏幕打印到打印机上,报表格式和报表打印周期由用户制定。
(8) 报警归档记录报警归档记录主要完成:压力、温度、重量、流量、开关量的上下限报警及记录归档,便于在线诊断各类故障,查找故障部位并报警。
(9) 热风炉监控模块热风炉操作参数模块主要完成热风炉焦炉煤气流量;高炉热风温度;热风炉炉顶温度;热风炉废气温度;热风炉高炉煤气流量;热风炉高炉煤气流量调节控制;热风炉高炉煤气流量调节阀位;热风炉助燃风流量;热风炉助燃风流量调节控制;热风炉助燃。