项目三内轮廓的加工
《数控车削编程与加工技术》课程标准
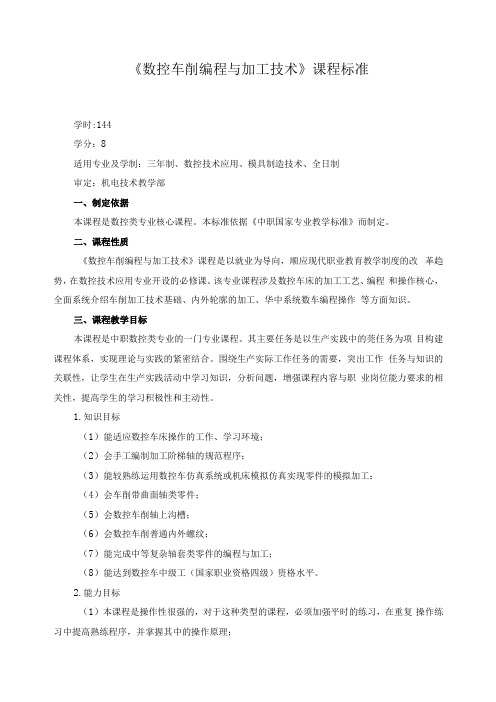
《数控车削编程与加工技术》课程标准学时:144学分:8适用专业及学制:三年制、数控技术应用、模具制造技术、全日制审定:机电技术教学部一、制定依据本课程是数控类专业核心课程。
本标准依据《中职国家专业教学标准》而制定。
二、课程性质《数控车削编程与加工技术》课程是以就业为导向,顺应现代职业教育教学制度的改革趋势,在数控技术应用专业开设的必修课。
该专业课程涉及数控车床的加工工艺、编程和操作核心,全面系统介绍车削加工技术基础、内外轮廓的加工、华中系统数车编程操作等方面知识。
三、课程教学目标本课程是中职数控类专业的一门专业课程。
其主要任务是以生产实践中的莞任务为项目构建课程体系,实现理论与实践的紧密结合。
围绕生产实际工作任务的需要,突出工作任务与知识的关联性,让学生在生产实践活动中学习知识,分析问题,增强课程内容与职业岗位能力要求的相关性,提高学生的学习积极性和主动性。
1.知识目标(1)能适应数控车床操作的工作、学习环境;(2)会手工编制加工阶梯轴的规范程序;(3)能较熟练运用数控车仿真系统或机床模拟仿真实现零件的模拟加工;(4)会车削带曲面轴类零件;(5)会数控车削轴上沟槽;(6)会数控车削普通内外螺纹;(7)能完成中等复杂轴套类零件的编程与加工;(8)能达到数控车中级工(国家职业资格四级)资格水平。
2.能力目标(1)本课程是操作性很强的,对于这种类型的课程,必须加强平时的练习,在重复操作练习中提高熟练程序,并掌握其中的操作原理;(2)能读懂零件图、能根据数控车床加工工艺文件选择、安装和调整数控车床常用刀具、能利用数控车床进行轮廓、螺纹、槽及孔的加工、能对数控机床进行日常的维护保养、上网查找相关资料、全面深入地掌握相关方法;(3)学会举一反三的方法,能在课外摸索一些新的加工工艺,并能学习使用。
3.素质目标(1)培养学生认真细致的学习态度和科学的求学态度,注重动手;(2)培养学生强烈的责任心和良好的敬业精神;(3)培养学生具有互助合作的精神。
数控加工工艺编程与操作(FANUC系统铣床与加工中心分册) 习题册的程序
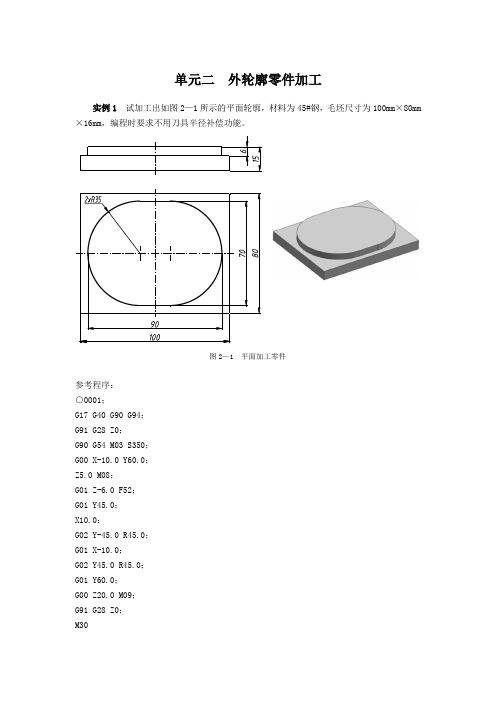
单元二外轮廓零件加工实例1试加工出如图2—1所示的平面轮廓,材料为45#钢,毛坯尺寸为100mm×80mm ×16mm,编程时要求不用刀具半径补偿功能。
图2—1 平面加工零件参考程序:○0001;G17 G40 G90 G94;G91 G28 Z0;G90 G54 M03 S350;G00 X-10.0 Y60.0;Z5.0 M08;G01 Z-6.0 F52;G01 Y45.0;X10.0;G02 Y-45.0 R45.0;G01 X-10.0;G02 Y45.0 R45.0;G01 Y60.0;G00 Z20.0 M09;G91 G28 Z0;M30实例二如图2—3所示为外轮廓加工零件图,材料为45#钢,毛坯尺寸为100×80×16,试运用刀具半径补偿功能对图示零件轮廓进行粗精加工。
图2—3 外轮廓加工零件参考程序:○0001;(主程序)G17 G40 G90 G94;G91 G28 Z0;G90 G54 M03 S660;G00 X25.0 Y50.0;Z5.0 M08;G01 Z0 F100;M98 P0002 L02;G90 G00 Z50.;G91 G28 Z0;M30;○0002;(子程序)G91 G01 Z-4.0 F50;G90 G41 D01 G01 X33.84 Y33.84 F70;G02 X47.5 Y28.19 R8.0;G01 Y-28.19;G02 X33.84 Y-33.84 R8.0;G01 X24.02 Y-24.02;G03 X16.34 Y-23.35 R6.0;G02 X-16.34 R28.5;G03 X-24.02 Y-24.02 R6.0;G01 X-33.84 Y-33.84;G02 X-47.5 Y-28.19 R8.0;G01 Y28.19;G02 X-33.84 Y33.84 R8.0;G01 X-24.02 Y24.02;G03 X-16.34 Y23.15 R6.0;G02 X16.34 R28.5;G03 X24.02 Y24.02 R6.0;G01 X33.84 Y33.84;G40 G01 X25.0 Y50.0;M99;单元三内轮廓零件加工实例一试加工出如图3—1所示的槽加工零件,材料为45#钢,毛坯尺寸为100×80×16,编写加工程序。
数控铣---内外轮廓的编程(最全)word资料

数控铣---内外轮廓的编程(最全)word资料项目一数控铣---内外轮廓的编程1、何谓机床原点、机床参考点?【教学目的】:1.理解刀具半径补偿的概念及意义;2.掌握G40、G41、G42指令的应用格式和特点。
3.了解固定循环中孔系加工指令的功能及应用;4.掌握G81、G80、G84、G98、G99指令功能及应用格式。
【重点】:刀具半径补偿的意义及G40、G41、G42指令的应用;钻孔循环指令G81;攻螺纹循环指令G84【难点】:刀具半径补偿的方法;深孔钻孔循环指令G83一、旧课复习1、G92与G54有何差别?2、刀具长度补偿有什么意义?3、何谓插补平面?4、如何判断不同插补平面圆弧的顺逆方向?5、圆弧插补指令格式?二、新课教学内容(一)内外轮廓的编程与加工1.刀具半径补偿功能的概念(1)用铣刀铣削工件的轮廓时,刀具中心的运动轨迹并不是加工工件的实际轮廓。
如图10-1所示,由于数控系统控制的是刀心轨迹,编程时要根据零件轮廓尺寸计算出刀心轨迹图10-1 刀具半径的补偿(2)注意到零件轮廓可能需要粗铣、半精铣和精铣三个工步,由于每个工步加工余量不同,因此它们都有相应的刀心轨迹。
(3)另外刀具磨损后,也需要重新计算刀心轨迹,这样势必增加编程的复杂性。
编程工作简化成只按零件尺寸编程,将加工余量和刀具半径值输入系统内存并在程序中调用。
这样既简化了编程计算,又增加了程序的可读性。
(4)以按照零件轮廓编制的程序和预先设定的偏置为依据,自动生成刀具中心轨迹的功能即称为刀具半径补偿功能数控装置大都具有刀具半径补偿功能,为程序编制提供了方便。
当编制零件加工程序时,只需按零件轮廓编程,使用刀具半径补偿指令,数控系统便能自动计算出刀具中心的偏移量,并使系统按刀具中心轨迹运动。
如图10-2。
图10-2 刀具半径的补偿这样,既简化了编程,而且变换刀具后,无需更改程序,只需将对应的刀补值变换即可,在同一轮廓的粗精加工中也可以使用同一程序,粗加工时的补偿值等于刀具的半径值加上轮廓的余量值,精加工时的补偿值等于刀具的半径值。
《数控铣削编程与操作》精品课程建设方案
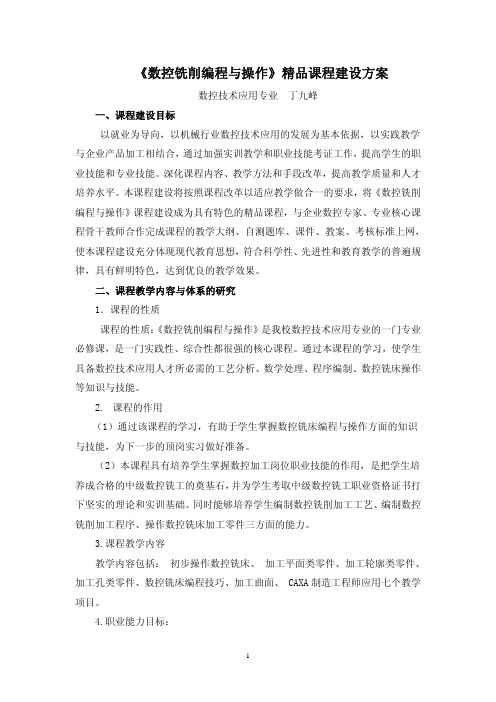
《数控铣削编程与操作》精品课程建设方案数控技术应用专业 丁九峰一、课程建设目标以就业为导向,以机械行业数控技术应用的发展为基本依据,以实践教学与企业产品加工相结合,通过加强实训教学和职业技能考证工作,提高学生的职业技能和专业技能。
深化课程内容、教学方法和手段改革,提高教学质量和人才培养水平。
本课程建设将按照课程改革以适应教学做合一的要求,将《数控铣削编程与操作》课程建设成为具有特色的精品课程,与企业数控专家、专业核心课程骨干教师合作完成课程的教学大纲、自测题库、课件、教案、考核标准上网,使本课程建设充分体现现代教育思想,符合科学性、先进性和教育教学的普遍规律,具有鲜明特色,达到优良的教学效果。
二、课程教学内容与体系的研究1.课程的性质课程的性质:《数控铣削编程与操作》是我校数控技术应用专业的一门专业必修课,是一门实践性、综合性都很强的核心课程。
通过本课程的学习,使学生具备数控技术应用人才所必需的工艺分析、数学处理、程序编制、数控铣床操作等知识与技能。
2. 课程的作用(1)通过该课程的学习,有助于学生掌握数控铣床编程与操作方面的知识 与技能,为下一步的顶岗实习做好准备。
(2)本课程具有培养学生掌握数控加工岗位职业技能的作用,是把学生培养成合格的中级数控铣工的奠基石,并为学生考取中级数控铣工职业资格证书打下坚实的理论和实训基础。
同时能够培养学生编制数控铣削加工工艺、编制数控铣削加工程序、操作数控铣床加工零件三方面的能力。
3.课程教学内容教学内容包括: 初步操作数控铣床、 加工平面类零件、加工轮廓类零件、加工孔类零件、数控铣床编程技巧、加工曲面、 CAXA制造工程师应用七个教学项目。
4.职业能力目标:(1)专业能力目标:A.根据各种典型零件数控加工图纸,能够正确分析零件加工的技术要求,具备零件图样分析的能力;B.能够正确合理地制定各种典型零件的数控加工工艺并编制符合技术规范的相关工艺文件,具备工艺设计与工艺文件编制的能力;C.能够在保证加工精度和质量要求的前提下,进行数控加工准备工作的合理安排,优化刀具路径,节约成本,具有一定的工艺改进创新的能力;D.能够应用数控加工程序编制的知识,编写各种典型零件的数控加工程序,并熟练操作数控加工仿真软件,具备程序编制与验证优化的能力;E.遵守操作规范,正确使用数控加工设备及相关工艺装备,通过对加工过程的有效控制完成典型零件的数控加工,具备加工过程控制能力;F.具有正确使用测量工具,检验产品的能力。
《数控编程技术》课程标准
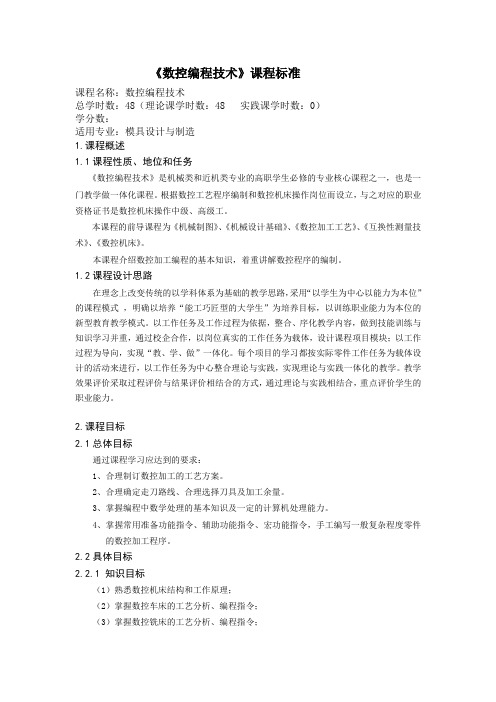
《数控编程技术》课程标准课程名称:数控编程技术总学时数:48(理论课学时数:48 实践课学时数:0)学分数:适用专业:模具设计与制造1.课程概述1.1课程性质、地位和任务《数控编程技术》是机械类和近机类专业的高职学生必修的专业核心课程之一,也是一门教学做一体化课程。
根据数控工艺程序编制和数控机床操作岗位而设立,与之对应的职业资格证书是数控机床操作中级、高级工。
本课程的前导课程为《机械制图》、《机械设计基础》、《数控加工工艺》、《互换性测量技术》、《数控机床》。
本课程介绍数控加工编程的基本知识,着重讲解数控程序的编制。
1.2课程设计思路在理念上改变传统的以学科体系为基础的教学思路,采用“以学生为中心以能力为本位”的课程模式,明确以培养“能工巧匠型的大学生”为培养目标,以训练职业能力为本位的新型教育教学模式。
以工作任务及工作过程为依据,整合、序化教学内容,做到技能训练与知识学习并重,通过校企合作,以岗位真实的工作任务为载体,设计课程项目模块;以工作过程为导向,实现“教、学、做”一体化。
每个项目的学习都按实际零件工作任务为载体设计的活动来进行,以工作任务为中心整合理论与实践,实现理论与实践一体化的教学。
教学效果评价采取过程评价与结果评价相结合的方式,通过理论与实践相结合,重点评价学生的职业能力。
2.课程目标2.1总体目标通过课程学习应达到的要求:1、合理制订数控加工的工艺方案。
2、合理确定走刀路线、合理选择刀具及加工余量。
3、掌握编程中数学处理的基本知识及一定的计算机处理能力。
4、掌握常用准备功能指令、辅助功能指令、宏功能指令,手工编写一般复杂程度零件的数控加工程序。
2.2具体目标2.2.1 知识目标(1)熟悉数控机床结构和工作原理;(2)掌握数控车床的工艺分析、编程指令;(3)掌握数控铣床的工艺分析、编程指令;(4)掌握数数控加工中心的工艺分析、编程指令;2.2.2 能力目标(1)掌握数控车程序的编制;(2)掌握数控铣程序的编制;(3)掌握数数控加工中心程序的编制;(4)培养学生独立工作能力及与团队合作完成任务的能力;(5)培养学生的自学能力;(6)熟悉国家标准及有关的基本规定;(7)理解、熟悉数控技术文件。
《计算机辅助编程与加工(数车)》教学大纲

淮海技师学院《计算机辅助编程与加工(数车)》教学大纲课程名称:计算机辅助编程与加工(数车)课程性质:单科精进总学时: 72适用专业:数控加工专业一、教学目的与要求(一)课程性质和内容《计算机辅助编程与加工(数车)》是数控专业的一门重要专业基础课程。
通过本课程的学习使学生能够利用CAXA数控车绘制二维图形、自动编程、生成加工程序、后置处理、各参赛的设置、零件的传输、零件加工的能力,培养学生实际动手操作能力。
学习好本门课程知识为以后工作中打下良好的基础。
(二)课程任务和要求通过本课程的学习让学生掌握了CAXA数控车自动编程软件的基本操作,能够完成轴、套类零件的绘图到生成程序的全过程,并且具备相应的实际操作能力完成零件的加工,培养其动手操作能力。
具体要求如下:1、了解CAXA数控车自动编程软件的基本概念和涉及内容;2、熟悉CAXA数控车自动编程软件的界面、绘图环境设置、层的操作;3、掌握基本绘图生成程序、后置处理、程序的传输等方法;4、掌握数控车床的基本操作;5、完成轴套类零件的绘制和数控加工;6、培养学生机械零件二维设计的能力;7、培养学生CAD设计能力;8、培养学生耐心、细致的学习态度;9、培养学生勇于创新的精神;(三)教学中应注意的问题1、根据技工学校的培养目标,本课程在教学中必须注重以基本图形绘制造型为主,造型和自动编程相结合,以绘图促加工的原则。
由于本课程实践性较强,在教学中,必须充分注意讲和练的结合。
2、教学与生产实习相结合,要尽量利用与本专业有关的零部件图例或实物组织教学。
本课程的教学环节有讲课、习题课、阶段测试、计算机绘图等。
讲课内容要少而精、重点突出,着重把基本方法讲清楚,注重平时练习。
二、教学内容与学时分配三、各部分知识点(或子项目)及教学要求项目一外形轮廓零件的加工24课时教学目标最终目标:能使用CAXA数控车完成外轮廓零件的造型、程序的生成、参数的设置、程序的传输,并且把零件加工出来。
项目三 零件轮廓度公差与测量

任务一 用轮廓样板测量线轮廓度误差
知 识 目 标 技 能 目 标
1. 熟悉线轮廓度公差的标注方法及相关 概念。 2. 掌握线轮廓度误差的测量评定方法。
1. 能正确使用轮廓样板测量线轮廓度误差。 2. 能对测量后的数值进行数据处理及评定零件 的合格性。
4
任务一 用轮廓样板测量线轮廓度误差
一.线轮廓度公差 确定被测要素的理想形状、理想 在平行于正投影面的任一截面内,被测实际要素的实
全国职业院校机电类专业 通用教材
公差配合与技术测量
项目三
1
任何零件都是由平面和曲面组成的。 曲面形状误差的检测也是产品检验中一个 非常重要的项目。在机械制造业中,用哪 些指标来评定其误差呢?
2
项目三
任务安排:
任务一 任务二
零件轮廓度公差与测量
用轮廓样板测量线轮廓度误差 用轮廓仪测量面轮廓度误差
3
10
回顾与总结
你学会了吗?
1.会识读线轮廓度公差带的含义。 2.知道线轮廓度误差的测量评定方法。 3.会用轮廓样板测量线轮廓度误差。
11
任务二
知 识 目 标 技 能 目 标
用轮廓仪测量面轮廓度误差
1.熟悉面轮廓度公差的标注方法及相关概念。 2.掌握面轮廓度误差的测量评定方法。
1.能正确使用轮廓样板测量面轮廓度误差。 2.能通过测量后的数值评定零件的合格。
方向或理想位置的尺寸。该尺寸 1)线轮廓度公差未标注基准 (属形状公差 ) 际轮廓线必须位于距离为 0.04mm 、对理想轮廓线对称分 不带公差,标注在方框中。
公差带形状为距离为公差值 t、对理想轮廓线对称分布的 布的两等距曲线间区域内。理想轮廓线由 R25、2×R10 和 两等距曲线间的区域,理想轮廓线由理论正确尺寸确定。 22 确定。公差带位置浮动。
服装设计(三)内轮廓设计

三.口袋的设计
3.缝内插袋 指在衣服的结构 线上设计衣袋, 袋口与服装的接 缝浑然一体。 特点:使服装具 有高雅、简洁、 含蓄、精致的特 征。
三.口袋的设计
领的种类
按领的高度分高领、中领、低领 按领线分为:方领、尖领、圆领、不规则 领 按穿着状态分:开门领、关门领 按领的结构分:连身领、装领 按造型分:无领、立领、翻领、袒领、装 饰领
无领
衣身上没有装领的领型,衣身领口的线形 就是无领的状态。 一字领 V形领 方形领
立领
(1)、不剪开直接缝合: 省道设计:通过省道转换完成的。 a、省道移位(一省变多省) b、变省为褶 (2)、分割后再缝合:可取代收省的作用。
公襟设计: 为了满足人穿脱舒适的需求而设计的,是 开剪后不缝合的分割线,需要一定的连接 设计。 可通过拉链、纽、扣、绳、带等连接,使 衣片闭合。
服装的内轮廓设计
一、服装的内轮廓设计范围 是服装外轮廓线形以内的零部件的边缘 形状及内部造型的线形设计。 如:领子、口袋等零部件的形状,以及衣 片上的省道褶裥和分割开刀线等
二、款式构成的方法
分割设计:根据服装的适体性、可动性和操作性进行分 割设计。 1、不剪开直接缝合或分割后缝合(适体性)
如:省道线、开剪线
袖身变化的袖型
立体袖 灯笼袖 喇叭袖 无袖
立体袖
指袖身形态吻合人体手臂自然形态的筒状 袖。袖身松紧适度,为达到微微前倾的立 体效果,需采用大小袖片或肘部收褶的方 法进行工艺处理。
灯笼袖
在袖身部位放出多余的量,缝成各种形式 的褶裥,收笼于袖口的一种袖型。
喇叭袖
从袖山开始到袖口,整个袖身愈来愈宽, 呈喇叭状的一种袖型,又称“渔夫袖”。
数控车床实训计划
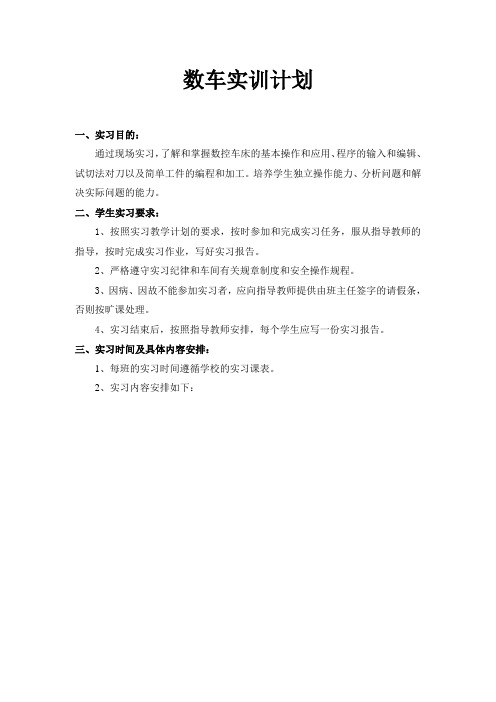
数车实训计划一、实习目的:通过现场实习,了解和掌握数控车床的基本操作和应用、程序的输入和编辑、试切法对刀以及简单工件的编程和加工。
培养学生独立操作能力、分析问题和解决实际问题的能力。
二、学生实习要求:1、按照实习教学计划的要求,按时参加和完成实习任务,服从指导教师的指导,按时完成实习作业,写好实习报告。
2、严格遵守实习纪律和车间有关规章制度和安全操作规程。
3、因病、因故不能参加实习者,应向指导教师提供由班主任签字的请假条,否则按旷课处理。
4、实习结束后,按照指导教师安排,每个学生应写一份实习报告。
三、实习时间及具体内容安排:1、每班的实习时间遵循学校的实习课表。
2、实习内容安排如下:1、实习目的及要求:1)培养学生对机床安全操作规程的认识。
2、教学内容1)抄写并熟记《数控车床安全操作规程》:进入车间实习时,要穿好工作服,大袖口要扎紧,衬衫要系入裤内。
长发要戴安全帽,并将发辫纳入帽中。
不得穿凉鞋、拖鞋、高跟鞋、背心、裙子或戴围巾进入车间;严禁在车间内追逐、打闹、喧哗、阅读与实习无关的书刊、背诵外语单词、收听广播和MP3等;应在指定的机床和计算机上进行实习。
未经允许,其他机床设备、工具或电器开关等均不得乱动;操作前必须熟悉机床的一切性能、结构、传动原理及控制程序,严禁超性能使用。
在弄懂整个操作过程前,不要进行机床的操作和调节;开动机床前,要检查车床电气控制系统是否正常,润滑系统是否畅通,油质是否良好,并按规定要求加足润滑油,各操作旋钮是否正确,工件、夹具及刀具是否加持牢固,检查周围有无障碍物,然后开慢车试转3-5分,检查各传动部件是否正常,确认无故障后,才可正常使用;机床操作时,必须严格按《数控车床操作步骤》进行,严禁私自跳步执行程序;程序调试完成后,必须经指导老师同意方可进行切削加工。
未经许可,擅自操作或违章操作,成绩归零。
造成事故者,按相关规定处分并赔偿损失;加工零件前,必须严格检查各切削刀具,防止相邻刀具在切削时干涉;加工零件时,必须关上防护门,不准将头手伸入门内,加工过程中不允许打开防护门;加工过程中,操作者不得擅自离开机床,应保持思想高度集中,右手摸住急停开关,观察机床运行,若发生不正常现象或事故时,应立即拍下“急停”,并及时报告指导老师;严禁用力拍打控制面板、触摸显示屏,严禁敲击中心架、顶尖、刀架和导轨; 严禁私自打开数控系统控制柜进行观看、触摸;数车属于高精设备,机床上严禁堆放任何工、夹、刃、量具,工件和其他杂物;机床参数严禁私自修改,运行程序不得擅自修改;工作完成后,应切断电源,清扫铁屑,擦净机床,在导轨面上加注润滑油,各部件应调整到正常位置,打扫现场卫生,填写设备使用记录。
《数控铣床编程与操作项目教程》习题集附答案模块4
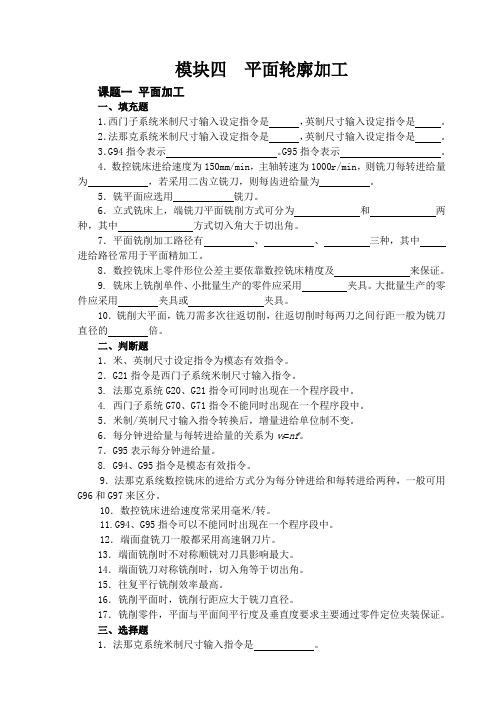
模块四平面轮廓加工课题一平面加工一、填充题1.西门子系统米制尺寸输入设定指令是,英制尺寸输入设定指令是。
2.法那克系统米制尺寸输入设定指令是,英制尺寸输入设定指令是。
3.G94指令表示。
G95指令表示。
4.数控铣床进给速度为150mm/min,主轴转速为1000r/min,则铣刀每转进给量为,若采用二齿立铣刀,则每齿进给量为。
5.铣平面应选用铣刀。
6.立式铣床上,端铣刀平面铣削方式可分为和两种,其中方式切入角大于切出角。
7.平面铣削加工路径有、、三种,其中进给路径常用于平面精加工。
8.数控铣床上零件形位公差主要依靠数控铣床精度及来保证。
9. 铣床上铣削单件、小批量生产的零件应采用夹具。
大批量生产的零件应采用夹具或夹具。
10.铣削大平面,铣刀需多次往返切削,往返切削时每两刀之间行距一般为铣刀直径的倍。
二、判断题1.米、英制尺寸设定指令为模态有效指令。
2.G21指令是西门子系统米制尺寸输入指令。
3. 法那克系统G20、G21指令可同时出现在一个程序段中。
4. 西门子系统G70、G71指令不能同时出现在一个程序段中。
5.米制/英制尺寸输入指令转换后,增量进给单位制不变。
6.每分钟进给量与每转进给量的关系为v f=nf。
7.G95表示每分钟进给量。
8. G94、G95指令是模态有效指令。
9.法那克系统数控铣床的进给方式分为每分钟进给和每转进给两种,一般可用G96和G97来区分。
10.数控铣床进给速度常采用毫米/转。
11.G94、G95指令可以不能同时出现在一个程序段中。
12.端面盘铣刀一般都采用高速钢刀片。
13.端面铣削时不对称顺铣对刀具影响最大。
14.端面铣刀对称铣削时,切入角等于切出角。
15.往复平行铣削效率最高。
16.铣削平面时,铣削行距应大于铣刀直径。
17.铣削零件,平面与平面间平行度及垂直度要求主要通过零件定位夹装保证。
三、选择题1.法那克系统米制尺寸输入指令是。
A. G71B. G70C. G21D. G202.西门子系统米制尺寸输入指令是。
数控铣床编程与加工技术项目三任务四八角凸台模板的加工

削底面,精加工基准面后,再以机用平口钳定位,用百 分表将机用平口钳的固定钳口侧面找正放平,然后在钳 口处利用标准块垫平。 4.选择刀、量具 由图样分析,该图样并没有内轮廓的最小曲率半径限制 对刀具的选取,故在这里选取ϕ20mm高速钢立铣刀,量 具可选用0~150mm游标卡尺、25~50mm的外径千分尺 等。
二、程序编制
1.根据图样特点选择编程零点 编程零点可以设定在加工零件上,也可以设定在夹具基 准面上,还可以设定在机床加工范围的某一特殊点上, 为了提高零件的加工精度和检测测量,编程零点应尽量 设定在零件的设计基准或工艺基准上,根据图样特点, 将编程零点设定在工件上表面的中心位置处。
二、程序编制
2.确定走刀路线 精加工走刀路线如图所示。 3.加工程序的编制 根据前面所学知识的编程步骤进行程序编制: (1)确定加工平面G17和编程方式 (2)从数控系统提取刀具补偿和编入工艺参数 (3)建立坐标系,并定义程序加工起点 (4)根据零件毛坯图,测量毛坯然后根据编程特点设定下刀点 (5)从下刀点开始下刀至背吃刀量 (6)建立刀具半径补偿 (7)圆弧进刀切入工件
一、 工艺分析
• (4)半精铣八角形凸台、圆柱体和正方形外轮廓 重新设 定刀具参数,选择程序,半精铣八角形凸台、圆柱体和 正方形外轮廓;留0.10mm单边余量。 (5)精铣八角形凸台、圆柱体和正方形外轮廓 实测工件 尺寸,调整刀具参数,精铣八角形凸台、圆柱体和正方 形外轮廓至尺寸要求。
一、 工艺分析
二、程序编制
(8)执行刀补加工外轮廓 (9)加工八角形凸台 (10)圆弧进刀加工圆柱台 (11)圆弧进刀加工四方形台 (12)圆弧切出 (13)取消刀补 (14)抬刀至安全表面 (15)快速退刀 (16)程序结束
《数控铣床编程与操作项目教程》期未试卷一附答案

班级: 姓名: 学号: 考试号: 密封线内禁止答题 密封线内禁止答题学校期终考试试卷(一) 级 班《数控铣床编程与操作》试卷适用班级:________ 出卷教师: 审核人: 考试时间: 90 分钟1.企业中常用铣刀刀柄型号有 、 。
2.立式铣床圆弧插补平面为 平面。
3.法那克系统子程序结束指令为 ,西门子系统子程序结束指令有 。
4.西门子系统米制尺寸输入设定指令是 ,英制尺寸输入设定指令是 。
5.铣平面应选用 铣刀。
6. 西门子系统倒圆指令格式G01 X Z RND=;其中RND 表示 。
7. 刀具半径补偿过程中运动轨迹可分为 、 、 等三个步骤。
8.法那克系统G28指令表示 ,G29指令表示 。
9.加工内轮廓的进给路线有 、 、 三种,轮廓精加工应采用 才能获得较好表面质量。
10. 当加工内、外轮廓 的薄壁件时,可采用同一个程序,通过设置刀具半径值来分别进行内外轮廓的加工。
11.加工凹槽时铣刀半径应 凹槽拐角圆弧半径。
12. 西门子系统 凹槽循环指令加工凹槽,法那克系统 凹槽循环指令。
(填“有”或“没有”)13.法那克系统坐标系偏转是围绕 点进行偏转,西门子系统坐标系偏转是围绕 点进行偏转。
14.执行镜像功能后,G02与G03,G41与G42指令将被 。
15.每 程序中刀具工作的那一个坐标系通常又称为当前坐标系。
16.法那克系统中以子程序形式存储并带有 的程序称为用户宏程序。
17.西门子系统矩形型腔或圆形型腔循环中,铣刀半径应 矩形腔转角半径或圆形腔半径。
18. 在极坐标系中 运行G00、G01、G02、G03等指令。
(填“能”或“不能”) 19.寻边器装夹在 上,常用于 、 轴对刀。
20.Z 轴设定器一般放置在 上,用于 坐标轴的对刀。
21.机外对刀仪主要用于测量刀具的 、 、 等尺寸。
22.大部分数控机床可通过 、 等方法将程序传入数控机床。
23.将数控程序传入数控系统,法那克系统程序头为 。
数控车(铣)床编程与操作课题3 内轮廓综合加工
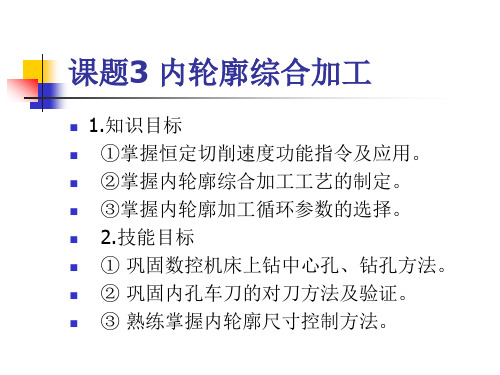
M0 T04 D1
程序停,手动钻中心孔、钻孔 换内孔粗车刀
G96 S100 LIMS=1500 G00 X12 Z5
恒定切削速度控制,切削速度为 100m/min,主轴最高转速1500r/min
刀具移至循环起点
CNAME=“L25”
R105=3 R106=0.4 R108=2 R109=0 设置循环参数,调粗加工循环 R110=1 R111=0.2 R112=0.1
二、加工工艺分析
1.工、量、刃具选择
(1)工具选择:铝棒装夹在三爪自定心卡盘中,用划线 盘校正,调头装夹用百分表校正,其余工具见表3-18。
(2)量具选择:外圆尺寸精度要求不高,用游标卡尺测 量,内孔精度较高用内径千分尺测量,内孔深度用深 度千分尺测量,内锥面用万能角度量角器测量,具体 规格见表3-18所示。
G00 G97 X100 Z200 M30
G00 X100 Z200 M0 M5 T05 D1
G96 S120 LIMS=2000 G00 X12 Z5 R105=7 R106=0 LCYC95 G00 G97 X100 Z200 M30
刀具退回至换刀点 主轴停、程序停、测量 换内孔精车刀 恒定切削速度控制,切削速度为 120m/min,最高工件转速2000r/min 刀具移至循环起点
图3-18恒定切削速度主轴转速与直径关系
2.指令代码
G96—恒定切削速度生效 G97—取消恒定切削速度
3.指令格式
表3-16法那克系统与西门子系统恒定切削速度功能指令格式
系统 格式
法那克系统
G96 S ;恒定切削速度生效。 ↑ 表示切削速度,单位:米/分钟
G50 S ;主轴转速上限。 ↑ 表示主轴转速,单位:转/分钟
- 1、下载文档前请自行甄别文档内容的完整性,平台不提供额外的编辑、内容补充、找答案等附加服务。
- 2、"仅部分预览"的文档,不可在线预览部分如存在完整性等问题,可反馈申请退款(可完整预览的文档不适用该条件!)。
- 3、如文档侵犯您的权益,请联系客服反馈,我们会尽快为您处理(人工客服工作时间:9:00-18:30)。
3.内圆锥的检测方法
图3.18 内圆锥加工的轨迹示意图
任务实施 ◆ 工艺分析
1.零件几何特点
零件加工面主要为端面、内台阶、内 圆锥面和倒角。 尺寸如图3.17所示,棒料伸出卡盘长 度为10mm。
2.选择工具、量具和刀具
(1)工具选择。 (2)量具选择。 (3)刀具选择。 (4)粗、精车内圆锥面至尺寸。
4.常见的内圆检测方法
可采用内卡钳、游标卡尺、塞规和内 径百分表检测内圆,如图3.13所示。
图3.13 内圆的检测方法
用内径表测量时,要注意以下两方面。
(1)长指针和短指针应结合观察, 以防指针多转一圈。 (2)短指针位置基本符合,长指针 转动至“零”位线附近时,应防止 “+”、“−”数值搞错。
3.程序模拟加工 4.自动加工及尺寸控制
◆ 检测评分 零件加工结束后,检测结果按表3.5要 求填写。
◆ 任务反馈
(1)装夹钻头时,钻头轴心线和工 件轴心线要一致,否则钻头容易折断。 (2)在装夹钻头锪锥形套前,必须 把钻头锥柄、尾座套筒和锥形套擦拭 干净。否则会由于锥面接触不好,使 钻头在尾座锥孔内打滑旋转。
4.切削用量选择
内圆的加工工艺分析如表3.1所示。
◆ 加工操作
1.加工准备
(1)检查毛坯尺寸。 (2)开机、回参考点。 (3)装夹工件和刀具。 (4)程序输入。
2.对刀
(1)X方向对刀。 (2)Z方向对刀。
图3.15 内圆车刀对刀示意图
3.程序模拟加工 4.自动加工及尺寸控制
◆ 检测评分 零件加工结束后,检测结果按表3.2要 求填写。
图3.23 主偏角不同内圆弧面加工刀具示意图
2.内圆弧加工工艺设计技巧
图3.24 内腔轴向进刀加工示意图
3.内圆弧面加工相关编程指令
(1)内圆弧面加工编程指令。
格式:G18 G02(G03)X _ Z _ R _ F _ ; 式中: X、Z——圆弧终点坐标; R ——圆弧半径; F ——圆弧插补进给速度。
项目三 内轮廓的加工
学习目标
◎掌握内轮廓加工的编程指令 ◎学会内轮廓加工的对刀方法 ◎掌握常见内轮廓的加工方法 ◎掌握内轮廓加工刀具移动路线 ◎掌握内轮廓的检测方法
任务一 内圆的加工 任务二 内圆锥面的加工 任务三 内圆弧面的加工
任务一 内圆的加工
任务描述 本任务主要是训练学生掌握工件上内 圆的基本加工方法。 零件如图3.1所示,毛坯尺寸: 42 40 mm,材料为45号钢,分析零件加工工艺, 编写加工程序。
◆ 任务反馈
(1)装夹钻头时,钻头轴心线和工 件轴心线要一致,否则钻头容易折断。 (2)在装夹钻头锪锥形套前,必须 把钻头锥柄、尾座套筒和锥形套擦拭 干净。
(3)镗内圆时,应尽量增加刀杆的 截面积,这样可增强镗刀的刚性,切 削时不容易产生振动。 (4)镗刀杆伸出长度应尽可能缩短。
任务二 内圆锥面的加工
知识准备
1.内圆锥锥度的相关计算
锥度的定义见式3.1:
D2 D1 C L
2.内圆锥面加工相关编程指令
格式:G90 X(U)_ Z(W) _ R_ F_ ; 式中: X、Z——绝对坐标编程时,切削终点 在工件坐标系下的坐标; U、W ——增量坐标编程时,切 削终点相对于循环起点的有向距离。
R——每次循环切削起点与切削终点 的半径差; F——指定刀具进给速度。
① 钻孔前,先平端面,中心处不留凸 头,否则容易使钻头歪斜,影响正确定心。 ② 钻头装入尾座套筒后,需校正钻头 轴心线和工件回转中心重合,以防孔径扩 大和钻头折断。
③ 把钻头引向工件端面时,不可用力 过大,以防损坏工件和折断钻头8 所示。
零件加工面主要为端面、倒角以及内圆。 尺寸如图3.22所示,棒料伸出卡盘长度 为50mm。
2.选择工具、量具和刀具
(1)工具选择。 (2)量具选择。 (3)刀具选择。
图3.27 内圆弧面加工所需主要刀具
3.制定加工工艺路线
(1)平端面。 (2)粗、精车外圆。 (3)钻中心孔。 (4)钻孔。 (5)粗车内圆弧面和内圆。 (6)精车内圆弧面和内圆至尺寸。 (7)切断。
图3.8 刀架夹铜棒防止钻头跳动示意图
⑤ 孔加工时,先用中心钻定心,再用 麻花钻钻孔,使加工出的孔内外同轴,尺 寸正确。 ⑥ 孔加工一段后,需退出钻头,停车 测量孔径,以防孔径扩大,工件报废。 ⑦ 钻深孔时,切屑不易排出,必须经 常退出钻头,清除切屑。
⑧ 当钻头将要把孔钻穿时,因钻头横刃 不再参加切削,阻力大大减小,进刀时,就 会觉得手轮摇起来很轻松,这时,必须减小 进给量,否则会使钻头的切削刃“咬”在工 件孔内,损坏钻头,或使钻头的锥柄在尾座 锥孔内打滑,把锥孔和锥柄咬毛。 ⑨ 当钻削不通孔时,为了控制深度,可 应用尾座套筒上的刻度。
(2)回参考点指令。
格式:G28 X _ Z _ ; 式中: X、Z——指定中间点的坐标。
(3)返回固定点指令。
格式:G29 X _ Z _ ; 式中: X、Z——参考点返回目标点的坐标。
4.内圆弧面的检测
内圆弧表面用半径样板检测,表面粗 糙度用表面粗糙度样板比对。
任务实施 ◆ 工艺分析
1.零件几何特点
(6)钻孔加工冷却。
2.镗孔基础
(1)镗刀装夹方法。 (2)工件的装夹。 (3)薄壁套筒工件的装夹。
图3.9 镗刀装夹不正产生现象示意图
图3.10 薄壁工件的变形示意图
为减少薄壁工件的变形,可采用以下 方法。 ① 工件加工时分粗车和精车,粗车时, 夹紧些;精车时,夹得松些,以减少变形。
② 采用开缝套筒,由于开缝套筒的接 触面积大,夹紧力均匀分布在工件上,不 易产生变形。 ③ 采用软爪卡盘,软爪卡盘接触面积 大,定位精度好,可以减少变形。
图3.1 内圆加工零件图及三维效果图
技能目标
● 掌握数控车床上钻孔、镗孔加工的 基本方法 ● 掌握钻头的安装 ● 掌握镗刀的安装和对刀操作 ● 掌握通孔加工工艺
知识准备
1.钻孔基础
(1)中心孔的作用和种类。
图3.2 用顶尖安装定位示意图
① A型中心孔。 ② B型中心孔。 ③ C型中心孔。 ④ D型中心孔。
图3.3 中心孔的类型
图3.3 中心孔的类型(续)
(2)中心钻。
图3.4 常用中心钻
(3)钻孔的基本原理。
图3.5 数控车床钻孔原理
(4)麻花钻的装夹方法。
① 麻花钻在刀架上的装夹方法。
图3.6 钻头在刀架上的安装形式
② 麻花钻在尾座上的装夹方法。
图3.7 麻花钻在尾座上的装夹方法
(5)钻孔的加工方法。
(3)车削内圆锥面时,刀尖必须严 格对准工件的轴心线。 (4)用圆锥塞规检测内圆锥面时, 量具、工件表面必须擦干净,工件 的表面粗糙度必须小于3.2μm。
任务三 内圆弧面的加工
任务描述 本任务主要是训练学生掌握工件上内 圆弧面的基本加工方法。 零件如图3.22所示,毛坯尺寸: 52 37 mm,材料:45号钢,分析零件加工工艺, 编写加工程序。
(1)钻孔加工编程指令。
图3.11 深孔钻削循环示意图
格式:G74 R(e)_ ; G74 Z(W)_ Q(Δk)_ F_ ; 式中: e——退刀量; Z(W)——钻削深度; Q(Δk) ——每次钻削长度(不加符号)。
(2)镗内圆加工编程指令。
图3.12 G90内圆车削循环示意图
格式:G90 X(U)_ Z(W)_ F_ ; 式中: X、Z——绝对编程时,表示切削终点C 在工件坐标系下的坐标; U、W ——相对编程时,表示切削 终点C相对于循环起点B的有向距离; F ——刀具进给速度。
图3.22 内圆弧加工零件图及三维效果图
技能目标
● 熟练掌握数控车床上钻孔、镗孔加 工的基本方法 ● 熟练掌握镗刀的安装和对刀操作 ● 掌握内圆弧面的加工工艺 ● 掌握内圆弧面尺寸的测量方法
知识准备
1.车内圆弧刀具选用技巧
加工内圆弧面前需先用麻花钻钻孔 (含用中心钻钻中心孔),加工内圆弧选 用的内圆车刀的主、副偏角应足够大,防 止发生干涉;当内圆弧无预制孔时,内圆 车刀主偏角必须大于90°,如图3.23所示。
4.基点坐标计算 5.切削用量选择
内圆弧面的加工工艺分析如表3.7所示。
◆ 加工操作
1.加工准备
(1)检查毛坯尺寸。 (2)开机、回参考点。 (3)装夹工件和刀具。 (4)程序输入。
2.对刀
(1)X方向对刀。 (2)Z方向对刀。
3.程序模拟加工 4.自动加工及尺寸控制
◆ 检测评分 零件加工结束后,检测结果按表3.8要 求填写。
(4)镗内圆加工方法。
镗内圆加工时,循环点坐标位置选取 要适当,防止镗刀后壁与孔壁发生碰撞。
(5)镗内圆加工冷却。
用硬质合金镗刀镗内圆时,一般不需 要加冷却液。 镗铝合金内圆时,不要加切削液,因 为水和铝容易起化合作用,会使加工表面 产生小针孔。 精加工铝合金时,使用煤油较好。
3.内圆加工相关编程指令
◆ 任务反馈
(1)加工前检查镗孔刀是否干涉。 (2)注意冷却液浇注要充足。 (3)车端面、钻中心孔和钻孔如采 用手动方式加工,可不编写程序。
(4)镗刀杆伸出长度应尽可能缩短。
如刀杆伸出过长,就会降低刀杆的刚 性,容易引起振动和让刀现象。 因此,刀杆伸出长度只要略大于孔深 即可。
图3.20 内圆锥面加工所需主要刀具
3.制定加工工艺路线
(1)平端面。 (2)钻中心孔。 (3)钻孔。
4.切削用量选择
内圆锥面的加工工艺分析如表3.4所示。
◆ 加工操作
1.加工准备
(1)检查毛坯尺寸。 (2)开机、回参考点。 (3)装夹工件和刀具。 (4)程序输入。
2.对刀
(1)X方向对刀。 (2)Z方向对刀。
任务描述 本任务主要是训练学生掌握工件上内 圆锥的基本加工方法。 零件如图3.17所示,毛坯尺寸 45 27 mm,材料为45号钢,分析零件加工工艺, 编写加工程序。