金属工艺性能试验
金属力学及工艺性能试验方法国家标准
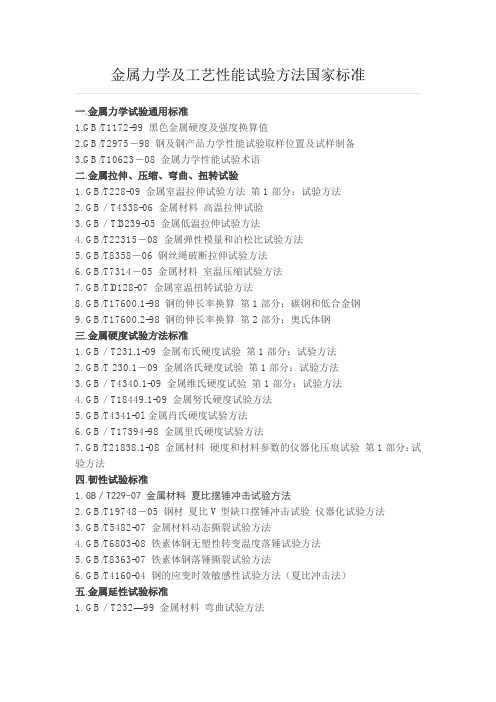
金属力学及工艺性能试验方法国家标准一.金属力学试验通用标准1.GB/T1172-99 黑色金属硬度及强度换算值2.GB/T2975-98 钢及钢产品力学性能试验取样位置及试样制备3.GB/T10623-08 金属力学性能试验术语二.金属拉伸、压缩、弯曲、扭转试验1. GB/T228-09 金属室温拉伸试验方法第1部分:试验方法2. GB/T4338-06 金属材料高温拉伸试验3. GB/Tl3239-05 金属低温拉伸试验方法4. GB/T22315-08 金属弹性模量和泊松比试验方法5. GB/T8358-06 钢丝绳破断拉伸试验方法6. GB/T7314-05 金属材料室温压缩试验方法7. GB/Tl0128-07 金属室温扭转试验方法8. GB/T17600.1-98 钢的伸长率换算第1部分:碳钢和低合金钢9. GB/T17600.2-98 钢的伸长率换算第2部分:奥氏体钢三.金属硬度试验方法标准1. GB/T231.1-09 金属布氏硬度试验第1部分:试验方法2. GB/T 230.1-09 金属洛氏硬度试验第1部分:试验方法3. GB/T4340.1-09 金属维氏硬度试验第1部分:试验方法4. GB/T18449.1-09 金属努氏硬度试验方法5. GB/T4341-0l 金属肖氏硬度试验方法6. GB/T17394-98 金属里氏硬度试验方法7. GB/T21838.1-08 金属材料硬度和材料参数的仪器化压痕试验第1部分:试验方法四.韧性试验标准1. GB/T229-07 金属材料夏比摆锤冲击试验方法2. GB/T19748-05 钢材夏比V型缺口摆锤冲击试验仪器化试验方法3. GB/T5482-07 金属材料动态撕裂试验方法4. GB/T6803-08 铁素体钢无塑性转变温度落锤试验方法5. GB/T8363-07 铁素体钢落锤撕裂试验方法6. GB/T4160-04 钢的应变时效敏感性试验方法(夏比冲击法)五.金属延性试验标准1. GB/T232—99 金属材料弯曲试验方法2. GB/T235—99 金属材料厚度等于或小于3mm薄板和薄带反复弯曲试验方法3. GB/T242—07 金属管扩口试验方法4. GB/T244—08 金属管弯曲试验方法5. GB/T245—08 金属管卷边试验方法6. GB/T246—07 金属管压扁试验方法7. GB/T17104-97 金属管管环拉伸试验方法8. GB/T241—07 金属管液压试验方法9. GB/T238-02 金属材料线材反复弯曲试验方法10. GB/T2976-04 金属线材缠绕试验方法11. GB/T239-99 金属材料线材扭转试验方法12. GB/T233-2000 金属材料顶锻试验方法13. GB/T5027-07 金属薄板和薄带塑性应变比(r值)试验方法14. GB/T5028-08 金属薄板和薄带拉伸应变硬化指数(n值)试验方法15. GB/T4156-07 金属杯突试验方法(厚度0.2~2mm)六.高温长时间试验1. GB/T2039-97 金属拉伸蠕变及持久试验方法2. GB/Tl0120-96 金属应力松驰试验方法七.金属疲劳试验标准1. GB/T4337-08 金属旋转弯曲疲劳试验方法(代替2107、4337、7733)3. GB/T3075-08 金属轴向疲劳试验方法4. GB/Tl2443-07 金属扭应力疲劳试验方法5. GB/T10622-89 金属材料滚动接触疲劳试验方法6. GB/T15248-08 金属材料轴向等幅低循环疲劳试验7. GB/T12347-08 钢丝绳弯曲疲劳试验方法8. GB/T6398-00 金属材料疲劳裂纹扩展速率试验方法八.金属断裂力学试验1 . GB/T21143-07 金属材料准静态断裂韧度统一试验方法(取代2038和2358)2. GB/T4161-07 金属材料平面应变断裂韧度KIC试验方法3. GB/T7732-08 金属板材表面裂纹断裂韧度KIe试验方法4. GB/T 19744-05 铁素体钢平面应变止裂韧度Kia试验方法九.金属力学试验其它标准1. GB/Tl2444-06 金属材料磨损试验方法试环-试块滑动磨损试验2. GB/T6400-07 金属丝和铆钉高温剪切试验方法3. GB/T6396-08 复合钢板力学及工艺性能试验方法。
GB 6397-1986__金属拉伸试验试样

3 . 4比 例试样系按公式2 。 =K丫 瓦计算而 得的试样, 式中系数K通常为56 5或 1 3 , 前 者称为短试样, 后者称为长试样。对短、 长比 例试样的标距 1 。 应分别等于s d 。 或5 . 5丫 6 于 蕊
二、 建 筑 用钢 材
1 1 1
及1 0 d 。 或1 1 . 3 丫 瓦。 一般应采用短比 例试样。 长比 例试样仅系过渡性质, 但如内
试样标距部分内最大 与最小直径的允许差值
0 . 0 1
0. 0 2
直径 d o 的允许偏差
士0. 0 5 土0. 1 士0. 2
5 -<1 0
多1 0
0 . 0 5
试样分为带头和不带头的两种, 仲裁试验时应采用前者, 后者一 般用于不宜或不经机加 工而整拉的棒材。 3 . 6 . 2 板材试样 对厚、 薄板材, 一般采用矩形试样, 其宽度根据产品厚度( 通常为0 . 1 0 - 2 5 m m ) , 采用
二、 建 筑用钢材
格
1 0 9
分格的 残余伸长, 所以第3 次施力使引伸计达到的读数为: 7 + ( 1 0 一 7 . 3 ) + 1 = 2 7 . 4 分格 试验直至试样的残余伸长达到或稍为超过 1 0 分格为止。试验结果见下表。 规定残余伸长应力 。 , 2 计算如下: 由下表查出残余伸长读数最接近 1 0 分格的力值读数为: 6 1 0 0 0 N 。用内插法可求得更 精确的F } , 2 值为:
_ F。} 一 试 样 平 行 部 分 原 始 横 截 面 积
带头试样从头部到平行部分过渡圆弧半径
r l 址 n Z
n卫 几1
3 试样形状及尺寸的一般规定 3 . 1 拉伸试样分为比例和定标距两种, 一般为经机加工试样和不经机加工的全截面试样, 其横截面通常为圆 形、 矩形、 异形以 及不经机加工的全截面形状。 对全截面试样原始横截面 积F O 可根据规定, 以名义或实侧尺寸进行计算。
钢材力学性能工艺性能试验实施细则
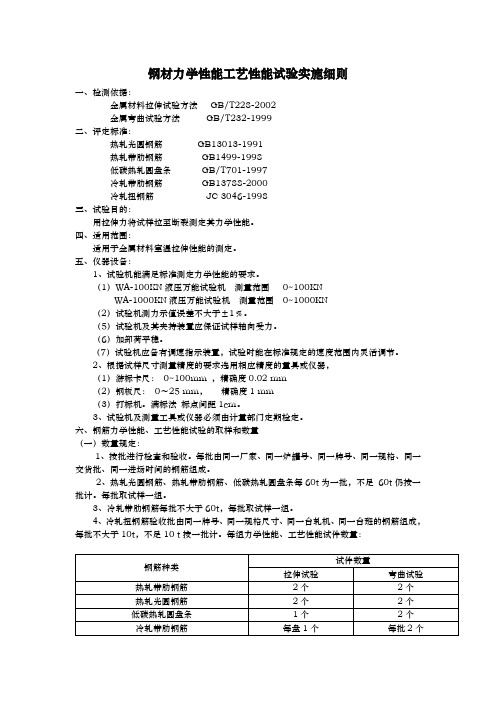
钢材力学性能工艺性能试验实施细则一、检测依据:金属材料拉伸试验方法GB/T228-2002金属弯曲试验方法GB/T232-1999二、评定标准:热轧光圆钢筋GB13013-1991热轧带肋钢筋GB1499-1998低碳热轧圆盘条GB/T701-1997冷轧带肋钢筋GB13788-2000冷轧扭钢筋JC 3046-1998三、试验目的:用拉伸力将试样拉至断裂测定其力学性能。
四、适用范围:适用于金属材料室温拉伸性能的测定。
五、仪器设备:1、试验机能满足标准测定力学性能的要求。
(1)WA-100KN液压万能试验机测量范围0~100KNWA-1000KN液压万能试验机测量范围0~1000KN(2)试验机测力示值误差不大于±1﹪。
(5)试验机及其夹持装置应保证试样轴向受力。
(6)加卸荷平稳。
(7)试验机应备有调速指示装置,试验时能在标准规定的速度范围内灵活调节。
2、根据试样尺寸测量精度的要求选用相应精度的量具或仪器,(1)游标卡尺:0~100mm ,精确度0.02 mm(2)钢板尺:0~25 mm,精确度1 mm(3)打标机。
满标法标点间距1cm。
3、试验机及测量工具或仪器必须由计量部门定期检定。
六、钢筋力学性能、工艺性能试验的取样和数量(一)数量规定:1、按批进行检查和验收。
每批由同一厂家、同一炉罐号、同一牌号、同一规格、同一交货批、同一进场时间的钢筋组成。
2、热轧光圆钢筋、热轧带肋钢筋、低碳热轧圆盘条每60t为一批,不足60t仍按一批计。
每批取试样一组。
3、冷轧带肋钢筋每批不大于60t,每批取试样一组。
4、冷轧扭钢筋验收批由同一牌号、同一规格尺寸、同一台轧机、同一台班的钢筋组成,每批不大于10t,不足10 t按一批计。
每组力学性能、工艺性能试件数量:钢筋种类试件数量拉伸试验弯曲试验热轧带肋钢筋2个2个热轧光圆钢筋2个2个低碳热轧圆盘条1个2个冷轧带肋钢筋每盘1个每批2个冷轧扭钢筋每批2个每批1个(二) 取样规定:1、凡取2个试件的(低碳热轧圆盘条冷弯试件除外)均从任意两根(或两盘)中分别切取,即在每根钢筋上切取一个拉伸试件,一个弯曲试件。
金属材料力学性能检测

K为常数,通常取5.65或11.3,k=5.65时也称为短试样,此时的原始标 距应不少于15mm;k=11.3试样称为长试样 对于圆形试样,标距长度为工作直径d的5倍时为短试样,为10倍时为长 试样。但在特殊情况有关标准有规定时,也用4d或8d的试样
2 拉伸试样分类
物理意义是在于它反映了最大均匀变形的抗力
抗拉强度 — 是脆性材料选材的依据。 屈服强度与抗拉强度的比值σS / σb称为屈强比。 屈强比小,工程构件的可靠性高,说明即使外载荷或某些 意外因素使金属变形,也不至于立即断裂。但若屈强比过 小,则材料强度的有效利用率太低。
3.刚度
材料在外力作用下抵抗弹性变形的能力称为刚度。
塑性:指金属发生塑性变形而不被 破坏的能力。
载荷
作用在机件上的外力——载荷
静载荷 动载荷
静载荷:逐渐而缓慢地作用在工作上的力 如机床床身的压力、钢索的拉力
动载荷:包括冲击及交变载荷 如空气锤杆所受的冲击力、齿轮、弹簧
静拉伸试验(所加载荷为静载荷)
是一种较简单的力学性能试验,能够清楚地反映出材料受力 后所发生的弹性、弹塑性与断裂三个变形阶段的基本特性。 经拉伸试验对所测试的力学性能指标的测量稳定可靠,而且 理论计算方便,因此各国及国际组织都制定了完善的拉伸试 验方法标准,将拉伸试验方法列为力学性能试验中最基本、 最重要的试验项目。
布
氏
表示方法:硬度值+HBS(HBW)+D+F+t
硬 度
120HBS10/1000/30
压 痕
表示直径为10mm的钢球在1000kgf
载荷作用下保持30s测得的布氏硬度
值为120。
金属材料力学性能试验取样方法大全

一、原材料(一)钢筋1、取样规则(1)钢筋应按批进行检查和验收,每批重量不大于60吨。
每批应由同一牌号、同一炉罐号、同一规格、同一交货状态的钢筋组成。
(2)冷拉钢筋应分批进行验收,每批由重量不大于20吨的同级别、同直径的冷拉钢筋组成。
2、取样数量钢筋的试样数量根据其供货形式的不同而不同。
直条钢筋:每批直条钢筋应做2个拉伸试验,2个弯曲试验。
用《碳素结构钢》验收的直条钢筋每批应做1个拉伸试验,1个弯曲试验。
盘条钢筋:每批盘条钢筋应做1个拉伸试验,2个弯曲试验。
冷拉钢筋:每批冷拉钢筋应做2个拉伸试验,2个弯曲试验。
3取样方法拉伸和弯曲试验的试样可在每批材料中任选两根钢筋切取。
(二)型钢1样坯的切取根据中华人民共和国国家标准《钢筋力学及工艺性能试验取样规定》的要求:(1)样坯应在外观尺寸合格的钢材切取。
(2)切取样坯时,应防止因受热、加工硬化及变形而影响其力学及工艺性能。
(3)用烧割法切取样坯时,从样坯切割线至试样边缘必须留有足够的加工余量,一般因不小于钢材的厚度或直径,但最下不得少于20毫米。
堆厚度或直径大于60毫米的钢材,其加工余量可根据双方协议适当减小。
(4)冷拉样坯所留的加工余量可按表选取:厚度或直径(毫米)加工余量(毫米)《4>4-10>10-20>20-35>35 4厚度或直径1015202样坯切取位置及方向(1)对截面尺寸小于或等于60毫米的圆钢、方钢和六角钢,应在中心切取拉力试验样坯;截面尺寸大于60毫米,则在直径或对角线距外端四分之一处切取。
(2)样坯不需要热处理时,截面尺寸小于或等于40毫米的圆钢、方钢和六角钢,应使用全截面进行拉力试验。
当试验条件不能满足要求时,应加工成《金属拉力试验法》中相应的圆形比例试样。
(3)样坯需要热处理时,应按有关产品标准规定的尺寸,从圆钢、方钢和六角钢上切取。
(4)应从圆钢和方钢端部沿轧制方向切取弯曲样坯,截面尺寸小于或等于35毫米时,应以钢材全截面进行试验。
2010金属力学及工艺性能试验方法标准汇编
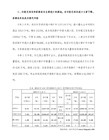
GB/T229-2007金属材料夏比摆锤冲击试验方法
GB/T460-2004钢的应变时效敏感性试验方法(夏比冲击法)
GB/T5482-2007金属材料动态撕裂试验方法
GB/T6803-2008铁素体钢的无塑性转变温度落锤试验方法
GB/T5028-2008金属材料薄板和薄带拉伸应变硬化指数(n值)的测定
GB/T7314-2005金属材料温室压缩试验方法
GB/T8358-2006钢丝绳破断拉伸试验方法
GB/T10128-2007金属材料室温扭转试验方法
一、通用标准
GB/T1172-1999黑色金属硬度及强度换算值
GB/T2975-1998钢及钢产品 力学性能试验取样位置及试样制备
GB/T10623-2008金属材料力学性能试验术语
GB/T24182-2009金属力学性能试验 出版标准的符号及定义
GB/T4161-2007金属材料平面应变断裂韧度KK试验方法
GB/T7732-2008金属材料表面裂纹拉伸试样断裂韧度试验方法
GB/T19744-2005铁素体钢平面应变止裂K试验方法
GB/T20832-2007金属材料试样轴线相对于产品结构的标识
GB/T4341-2001金属肖氏硬度试验方法
GB/T17394-1998金属里氏硬度试验方法
GB/T18449.1-2009金属材料努氏硬度试验方法第1部分:试验方法
GB/T18449.4-2009金属材料努氏硬度试验方法第4部分:硬度值表
GB/T8363-2007铁素体钢落锤撕裂试验方法
GB/T12778-2008金属夏比冲击断口测定方法
GB/T19748-2005钢材夏比V型缺口摆锤冲击试验仪器化试验方法
金属性能试验方法及标准
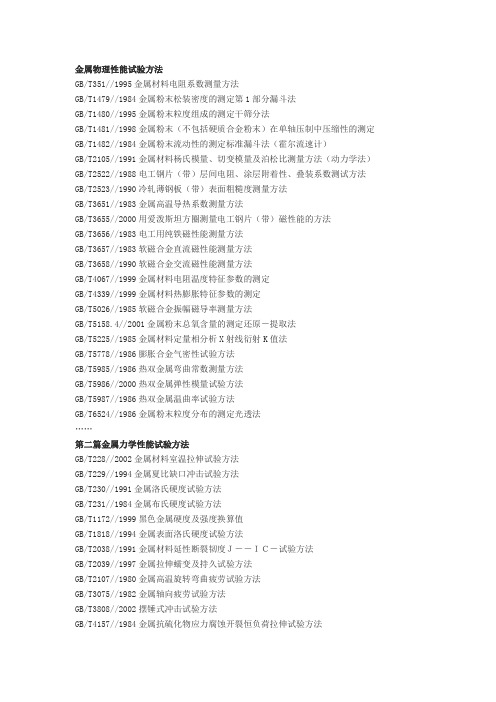
金属物理性能试验方法GB/T351//1995金属材料电阻系数测量方法GB/T1479//1984金属粉末松装密度的测定第1部分漏斗法GB/T1480//1995金属粉末粒度组成的测定干筛分法GB/T1481//1998金属粉末(不包括硬质合金粉末)在单轴压制中压缩性的测定GB/T1482//1984金属粉末流动性的测定标准漏斗法(霍尔流速计)GB/T2105//1991金属材料杨氏模量、切变模量及泊松比测量方法(动力学法)GB/T2522//1988电工钢片(带)层间电阻、涂层附着性、叠装系数测试方法GB/T2523//1990冷轧薄钢板(带)表面粗糙度测量方法GB/T3651//1983金属高温导热系数测量方法GB/T3655//2000用爱泼斯坦方圈测量电工钢片(带)磁性能的方法GB/T3656//1983电工用纯铁磁性能测量方法GB/T3657//1983软磁合金直流磁性能测量方法GB/T3658//1990软磁合金交流磁性能测量方法GB/T4067//1999金属材料电阻温度特征参数的测定GB/T4339//1999金属材料热膨胀特征参数的测定GB/T5026//1985软磁合金振幅磁导率测量方法GB/T5158.4//2001金属粉末总氧含量的测定还原-提取法GB/T5225//1985金属材料定量相分析X射线衍射K值法GB/T5778//1986膨胀合金气密性试验方法GB/T5985//1986热双金属弯曲常数测量方法GB/T5986//2000热双金属弹性模量试验方法GB/T5987//1986热双金属温曲率试验方法GB/T6524//1986金属粉末粒度分布的测定光透法……第二篇金属力学性能试验方法GB/T228//2002金属材料室温拉伸试验方法GB/T229//1994金属夏比缺口冲击试验方法GB/T230//1991金属洛氏硬度试验方法GB/T231//1984金属布氏硬度试验方法GB/T1172//1999黑色金属硬度及强度换算值GB/T1818//1994金属表面洛氏硬度试验方法GB/T2038//1991金属材料延性断裂韧度J--IC-试验方法GB/T2039//1997金属拉伸蠕变及持久试验方法GB/T2107//1980金属高温旋转弯曲疲劳试验方法GB/T3075//1982金属轴向疲劳试验方法GB/T3808//2002摆锤式冲击试验方法GB/T4157//1984金属抗硫化物应力腐蚀开裂恒负荷拉伸试验方法GB/T4158//1984金属艾氏冲击试验方法GB/T4160//1984的应变时效敏感性试验方法(夏比冲击法)GB/T4161//1984金属材料平面应变断裂韧度K--IC-试验方法GB/T4337//1984金属旋转弯曲疲劳试验方法GB/T4338//1995金属材料高温拉伸试验GB/T6398//2000金属材料疲劳裂纹扩展速率试验方法GB/T6400//1986金属丝材和铆钉的高温剪切试验方法GB/T6803//1986铁素体钢的无塑性转变温度落锤试验方法GB/T7314//1987金属压缩试验方法GB/T7733//1987金属旋转弯曲腐蚀疲劳试验方法GB/T8358//1987钢丝绳破断拉伸试验方法GB/T8363//1987铁素体钢落锤撕裂试验方法GB/T8640//1988金属热喷涂层表面洛氏硬度试验方法GB/T8641//1988热喷涂层抗拉强度的测定GB/T8642//1988热喷涂层结合强度的测定GB/T10120//1996金属应力松弛试验方法GB/T10128//1988金属室温扭转试验方法......第三篇金属工艺性能试验方法GB/T232//1999金属材料弯曲试验方法GB/T233//2000金属材料顶锻试验方法GB/T235//1999金属材料等于或小于3mm薄板和薄带反复弯曲试验方法GB/T238//1984金属线材反复弯曲试验方法GB/T239//1999金属线材扭转试验方法GB/T241//1990金属管液压试验方法GB/T242//1997金属管扩口试验方法GB/T244//1997金属管弯曲试验方法GB/T245//1997金属管卷边试验方法GB/T246//1997金属管压扁试验方法GB/T2976//1988金属线材缠绕试验方法GB/T4156//1984金属杯突试验方法(厚度0.2~2mm)GB/T17104//1997金属管管环拉伸试验方法GB/T5001//1993薄板双层咬合弯曲试验方法GB/T5126//1993钢筋平面反向弯曲试验方法附录现行标准与被代替标准对照表第四篇金属腐蚀及防护试验方法GB/T1838//1995镀锡钢析(带)镀锡量试验方法GB/T1839//1993钢铁产品镀锌层质量试验方法GB/T2972//1991镀锌钢丝锌层硫酸铜试验方法GB/T2973//1991镀锌钢丝锌层重量试验方法GB/T4157//1984金属抗硫化物应力腐蚀开裂恒负荷拉伸试验方法GB/T4334.1//2000不锈钢10%草酸浸蚀试验方法GB/T4334.2//2000不锈钢硫酸-硫酸铁腐蚀试验方法GB/T4334.3//2000不锈钢65%硝酸腐蚀试验方法GB/T4334.4//2000不锈钢硝酸-氢氟酸腐蚀试验方法GB/T4334.5//2000不锈钢硫酸-硫酸铜腐蚀试验方法GB/T4334.6//2000不锈钢5%硫酸腐蚀试验方法GB/T5776//1986金属材料在表面少不中常规暴露腐蚀试验方法GB/T8650//1988管线钢抗阶梯型破裂试验方法GB/T10123//2001金属和合金的腐蚀基本术语和定义GB/T10124//1988金属材料实验室均匀腐蚀全浸试验方法GB/T10125//1997人造气氛腐蚀试验盐雾试验GB/T10126//1988铁-铬-镍合金在高温水中应力腐蚀试验方法GB/T10127//1988不锈钢三氯化铁缝隙腐蚀试验方法GB/T13303//1991钢的抗氧化性能测定方法GB/T13448//1992彩色涂层钢板及钢带试验方法GB/T13912//1992金属覆盖层钢铁制品热镀锌层技术要求GB/T14165//1993黑色金属室外大气暴露试验方法……第五篇金属无损检验方法GB/T1786//1990锻制圆饼超声波检查方法GB/T2970//1991中厚钢板超声波检验方法GB/T4162//1991锻轧钢棒超声波检验方法GB/T5616//1985常规无损探伤应用导则GB/T5777//1996无缝钢管超声波探伤检验方法GB/T6402//1991钢锻件超声波检验方法GB/T7734//1987复合钢板超声波探伤方法GB/T7735//1995钢管涡流探伤检验方法GB/T7736//2001钢的低倍组织及缺陷超声波检验法GB/T8361//2001冷拉圆钢表面超声波探伤方法GB/T8651//1988金属板材超声波检验方法GB/T8652//1988变形高强度钢超声波检验方法GB/T10121//1988钢材塔形发纹磁粉检验方法GB/T11259//1999超声波检验用钢对比试块的制作与校验方法GB/T11260//1996圆钢穿过工涡流探伤检验方法GB/T12606//1999钢管漏磁探伤方法GB/T15830//1995钢制管道对接环焊缝超声波探伤方法和检验结果的分级GB/T16544//1996球形储罐Y射线全景曝光照相方法GB/T16673//1996无损检测用黑光源(UV-A)辐射的测量GB/T17990//1999圆钢点式(线圈)涡流探伤检验方法。
6396复合钢板力学及工艺性能试验方法

d , d i
G B / T 6 3 9 6 一1 9 9 5
续表 1
符 号
名
称
单
位
s o
F
试样受剪面面积 试样环形结合面面积
试验 力 粘结 强度
mmZ
N
r n
a 介
剪切强度 弯曲角度
N/ mm'
O
圈周率( 3 . 1 4 1 6 )
分离率
写
C
4 拉伸试验方法
4 . 1 试样
4 . 1 . 1 拉伸试样取样数量、 方向 及部位按基材标准、 G B 2 9 7 5 和G B 6 3 9 7 执行。 4 . 1 . 2 试样一般为矩形试样。 4 . 1 . 3 当复合钢板总厚度 T , 不大于 4 0 m m时, 试样厚度 a 等于 T , , 其余按 G B 6 3 9 7 中P 7 试样执行。 4 . 1 . 4 当复合钢板总厚度 T , 大于 4 0 m m且试验机能力不足时, 可从基材和覆材两面按比例机械加工 厚度至 4 0 m m, 但试样覆材厚度a 。 不得小于3 m m, 当钢板覆材厚度 T : 小于等于 3 m m时, 只减薄基材 厚度T e , 其余按G B 6 3 9 7 中P 7 试样执行。 4 . 1 . 5 对于特殊要求, 可采用全部去除覆材的矩形试样或圆形试样。 4 . 1 . 6 试样尺寸的测量应按G B 2 2 8 中 有关规定执行, 必要时还应分别测量试样的基材厚度a 、 和筱材 厚度a 测量方法见附录 A ( 补充件) 。 4 . 2 试验设备和试验条件 试验设备和试验条件应按 G B 2 2 8 有关规定执行。 4 . 3 性能测定 性能测定应根据复合钢板标准要求和有关技术条件规定测定所要求的项 目, 试验方法按 G B 2 2 8
金属材料试验标准及样条要求
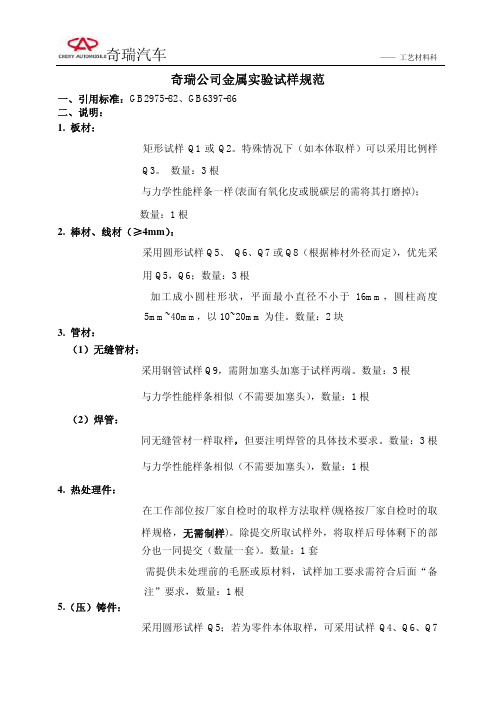
奇瑞公司金属实验试样规范一、引用标准:GB2975-82、GB6397-86二、说明:1. 板材:力学性能样条:矩形试样Q1或Q2。
特殊情况下(如本体取样)可以采用比例样Q3。
数量:3根化学成分样条:与力学性能样条一样(表面有氧化皮或脱碳层的需将其打磨掉);数量:1根2. 棒材、线材(≥4mm):力学性能样条:采用圆形试样Q5、 Q6、Q7或Q8(根据棒材外径而定),优先采用Q5,Q6;数量:3根化学成分样条:加工成小圆柱形状,平面最小直径不小于16mm,圆柱高度5mm~40mm,以10~20mm为佳。
数量:2块3. 管材:(1)无缝管材:力学性能样条:采用钢管试样Q9,需附加塞头加塞于试样两端。
数量:3根化学成分样条:与力学性能样条相似(不需要加塞头),数量:1根(2)焊管:力学性能样条:同无缝管材一样取样,但要注明焊管的具体技术要求。
数量:3根化学成分样条:与力学性能样条相似(不需要加塞头),数量:1根4. 热处理件:力学性能样条:在工作部位按厂家自检时的取样方法取样(规格按厂家自检时的取样规格,无需制样)。
除提交所取试样外,将取样后母体剩下的部分也一同提交(数量一套)。
数量:1套化学成分样条:需提供未处理前的毛胚或原材料,试样加工要求需符合后面“备注”要求,数量:1根5.(压)铸件:力学性能样条:采用圆形试样Q5;若为零件本体取样,可采用试样Q4、Q6、Q7或Q8。
数量:3根化学成分样条:试样要至少保证有两个互相平行的工作面,且其中一平面最小直径处不小于16mm ,两平行面的高度5mm~40mm ,以10~20mm 左右为佳。
数量:1块备注:1. 力学性能和化学成分的试样规格和数量厂家均应按照上述要求提供;厂家的自检报告中在“备注”栏里一定要注明引用标准号,铸铁、铝合金铸件要注明牌号及具体成分要求。
不合要求者材料科将不予接收。
2. 上述化学成分样条均是做光谱分析的标准,特殊件(如:小件、薄件)等不易做光谱分析,要取成化学分析的试样---试样应大于所需分析试样量的4倍,所送样品可取样量应在20g 以上。
P92钢焊接工艺性能试验研究
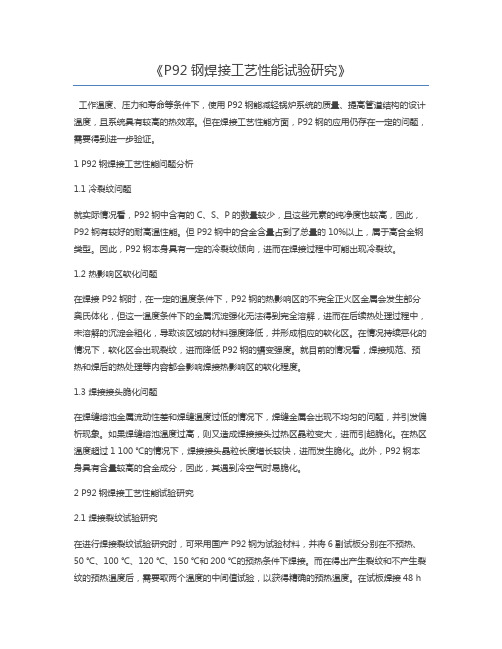
《P92钢焊接工艺性能试验研究》工作温度、压力和寿命等条件下,使用P92钢能减轻锅炉系统的质量、提高管道结构的设计温度,且系统具有较高的热效率。
但在焊接工艺性能方面,P92钢的应用仍存在一定的问题,需要得到进一步验证。
1 P92钢焊接工艺性能问题分析1.1 冷裂纹问题就实际情况看,P92钢中含有的C、S、P的数量较少,且这些元素的纯净度也较高,因此,P92钢有较好的耐高温性能。
但P92钢中的合金含量占到了总量的10%以上,属于高合金钢类型。
因此,P92钢本身具有一定的冷裂纹倾向,进而在焊接过程中可能出现冷裂纹。
1.2 热影响区软化问题在焊接P92钢时,在一定的温度条件下,P92钢的热影响区的不完全正火区金属会发生部分奥氏体化,但这一温度条件下的金属沉淀强化无法得到完全溶解,进而在后续热处理过程中,未溶解的沉淀会粗化,导致该区域的材料强度降低,并形成相应的软化区。
在情况持续恶化的情况下,软化区会出现裂纹,进而降低P92钢的蠕变强度。
就目前的情况看,焊接规范、预热和焊后的热处理等内容都会影响焊接热影响区的软化程度。
1.3 焊接接头脆化问题在焊缝熔池金属流动性差和焊缝温度过低的情况下,焊缝金属会出现不均匀的问题,并引发偏析现象。
如果焊缝熔池温度过高,则又造成焊接接头过热区晶粒变大,进而引起脆化。
在热区温度超过1 100 ℃的情况下,焊接接头晶粒长度增长较快,进而发生脆化。
此外,P92钢本身具有含量较高的合金成分,因此,其遇到冷空气时易脆化。
2 P92钢焊接工艺性能试验研究2.1 焊接裂纹试验研究在进行焊接裂纹试验研究时,可采用国产P92钢为试验材料,并将6副试板分别在不预热、50 ℃、100 ℃、120 ℃、150 ℃和200 ℃的预热条件下焊接。
而在得出产生裂纹和不产生裂纹的预热温度后,需要取两个温度的中间值试验,以获得精确的预热温度。
在试板焊接48 h后进行PT检测可发现,在预热温度≤120 ℃的情况下,试板的裂纹率为100%;预热温度>150 ℃的情况下,试板表面未出现缺陷。
杯突试验简介

杯突试验1杯突试验杯突试验,一种冲压工艺性能试验,用来衡量材料的深冲性能的试验方法。
用规定的钢球或球形冲头顶压在模内的试样,直至试样产生第一条裂纹为止,其压入深度(mm)即杯突深度,以此来判定金属材料冲压性能大小,其深度不小于规定时为合格按照国家标准,“试验采用端部为球形的冲头,将夹紧的试样压入压模内,直至出现穿透裂缝为止,所测量的杯突深度即为试验结果。
”这种试验通常是在杯突试验机上进行。
试样在做过杯突试验后就像只冲压成的杯子(不过是只破裂的杯子)。
钢板深冲性能不好的话,冲压件在制作过程中就很容易开裂。
2杯突试验简介Erichsen Test / Cupping Test杯突器Cupping Machinebejtu shjyon 杯突试验(Eriehsen test)评价金属薄板成形性的试验方法。
又称埃里克森试验(Erichsen test) 或埃氏杯突试验,是薄板成形性试验中最古老、最普及的一种。
试验时,用球头凸模把周边被凹模与压边圈压住的金属薄板顶入凹模,形成半球鼓包直至鼓包顶部出现裂纹为止。
如图所示,试验用价Zomm的硬钢球或半球凸模4,将金属板料2压入内径27mm、圆角半径。
.75mm 的凹模1,板料边缘在凹模和压边圈3之间压紧。
为防止边缘金属向凹模内流动,板料尺寸应足够大。
试验时,金属板料被凸模顶成半球鼓包。
取鼓包顶部产生颈缩或有裂纹出现时的凸模压入深度作为试验指标,称为杯突值或I:值,以mm为单位。
决定试验指标的依据是最大载荷。
当不能确定最大载荷时,可以采用可见(透光)裂纹发生时凸模压入深度作为指标。
但用可见裂纹法测定的数值比最大载荷法测定的数值要大。
.3~ 0.smm。
赞羚杯突试验示意图1一凹模,2一金属板;3一压边圈.4一凸模当润滑条件良好时,鼓包顶部的应变状态接近于等双向拉伸。
因此,杯突值可以用来评价板材的胀形性能,几值与硬化指数n值及总延伸率有一定相关性。
试验条件对I。
值的影响较大。
金属的性能测试题一

1.工程中使用的金属材料在拉伸试验时,多数会出现显著的屈服现象。()
2•维氏硬度测量压头为正四棱锥体金刚石()
3.洛氏硬度值无单位。()
4•做布氏硬度测试时,当试验条件相同时,其压痕直径越小,材料的硬度越低。()
5.在实际应用中,维氏硬度值是根据测定压痕对角线长度再查表得到的。()
A强度B硬度C韧性
2•金属材料的变形随外力消除而消除为()
A弹性形变B屈服现象C断裂
3.做疲劳试验时,试样承受的载荷为()
A.静载荷B冲击载荷C交变载荷
4.用压痕的深度来确定材料的硬度值为()
A.布氏硬度B洛氏硬度C维氏硬度
5•现需测定某灰铸铁的硬度一般应选用何种方法测定()
A.布氏硬度机B洛氏硬度机C维氏硬度机
力
占
107I脚
第8题图
9.洛氏硬度常用标尺有、、三种。
二,选择题
1.拉伸试验时,试样拉断前所能承受的最大应力称为材料的()
A•屈服点B•抗拉强度C•弹性极限
2.材料抵抗局部变形,压痕及划痕的能力称为()
A.强度B.韧性C。硬度
3.洛氏硬度C标尺所用的压头是()
A.淬硬钢球B.金刚石圆锥体C.硬质合金球
金属的性能测试题一
一 •填空题(每空1分,共45分)
1•金属材料的性能一般分为两种,一类是使用性能,一类是工艺性能,前者包括
?
和,后者包括,,,
和。
2•力学性能是指金属在外力作用下所表现出来的性能,包
括,,,,及疲劳强度
等。
3•强度是指金属材料在载荷作用下,抵抗或的能力,
强度常用的衡量指标有和。
4•如果零件工作时所受的应力低于材料的或则不会产生过量
金属材料力学性能测试

❖ 弯曲试验不能使塑性很好的材料破坏,不 能测定其断裂弯曲强度。
❖ 试样上表面应力最大,可以较灵敏地反映
材料表面缺陷情况。
1) 的定义:试样拉断后,颈缩处横截面面积的
最大缩减量与原始横截面面积的百分比。
S0 S1 100%
S0
式中: S 0 为试样原始横截面面积;
截面面积S 。1 为试样断裂后,颈缩处最细部分的横
2) 的测定
.
34
拉伸试验机
❖ 拉伸试验一般在液压式万能试验机或电子 式万能试验机上进行。
❖ WE系列液压式万能材料试验机是一种适 用性强、用途广的试验机,系列规格有 l00KN、300KN 、600KN、1000KN,当 然也有特殊规格,目前为一般力学实验室 普遍配套使用。
(1)图解法
按公式: 公式中:
max
d
arctg(max d)
为试样直径2。Le
m a x 为试样标距范围的最大扭转角。
L e 为试样 .
54
§ 1.2 金属材料扭转时的力学性能
(五)剪切弹性模量的测定 1、定义:扭转时,剪应力与剪应变成线性比例
关系范围内,剪应力 与剪应变 之比称为剪切
弹性模量,以 G 表示。
18
§ 1.1 金属材料拉伸试验
各项强度指标定义如下:
1)比例极限: p
p
Pp A0
2)弹性极限: e
e
Pe A0
3)屈服极限: s
s
Ps A0
4)强度极限: b
b
Pb A0
5)断裂强度: k
.
k
Pk A0
19
§ 1.1 金属材料拉伸试验
各应力指标的定义及测试方法:
金属力学及工艺性能试验方法国家标准
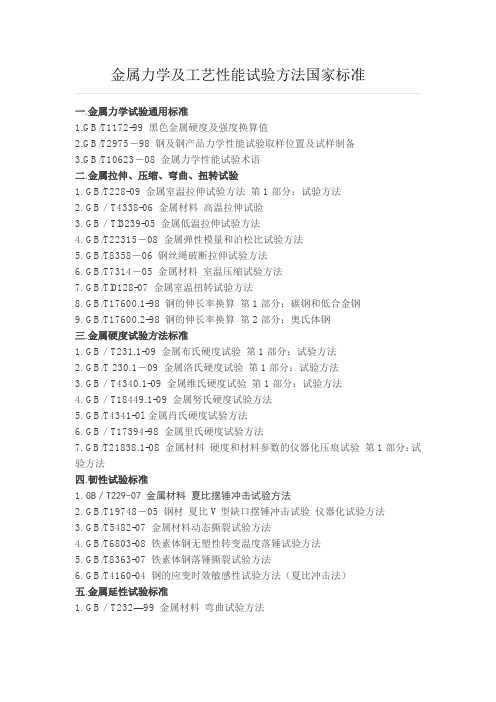
金属力学及工艺性能试验方法国家标准一.金属力学试验通用标准1.GB/T1172-99 黑色金属硬度及强度换算值2.GB/T2975-98 钢及钢产品力学性能试验取样位置及试样制备3.GB/T10623-08 金属力学性能试验术语二.金属拉伸、压缩、弯曲、扭转试验1. GB/T228-09 金属室温拉伸试验方法第1部分:试验方法2. GB/T4338-06 金属材料高温拉伸试验3. GB/Tl3239-05 金属低温拉伸试验方法4. GB/T22315-08 金属弹性模量和泊松比试验方法5. GB/T8358-06 钢丝绳破断拉伸试验方法6. GB/T7314-05 金属材料室温压缩试验方法7. GB/Tl0128-07 金属室温扭转试验方法8. GB/T17600.1-98 钢的伸长率换算第1部分:碳钢和低合金钢9. GB/T17600.2-98 钢的伸长率换算第2部分:奥氏体钢三.金属硬度试验方法标准1. GB/T231.1-09 金属布氏硬度试验第1部分:试验方法2. GB/T 230.1-09 金属洛氏硬度试验第1部分:试验方法3. GB/T4340.1-09 金属维氏硬度试验第1部分:试验方法4. GB/T18449.1-09 金属努氏硬度试验方法5. GB/T4341-0l 金属肖氏硬度试验方法6. GB/T17394-98 金属里氏硬度试验方法7. GB/T21838.1-08 金属材料硬度和材料参数的仪器化压痕试验第1部分:试验方法四.韧性试验标准1. GB/T229-07 金属材料夏比摆锤冲击试验方法2. GB/T19748-05 钢材夏比V型缺口摆锤冲击试验仪器化试验方法3. GB/T5482-07 金属材料动态撕裂试验方法4. GB/T6803-08 铁素体钢无塑性转变温度落锤试验方法5. GB/T8363-07 铁素体钢落锤撕裂试验方法6. GB/T4160-04 钢的应变时效敏感性试验方法(夏比冲击法)五.金属延性试验标准1. GB/T232—99 金属材料弯曲试验方法2. GB/T235—99 金属材料厚度等于或小于3mm薄板和薄带反复弯曲试验方法3. GB/T242—07 金属管扩口试验方法4. GB/T244—08 金属管弯曲试验方法5. GB/T245—08 金属管卷边试验方法6. GB/T246—07 金属管压扁试验方法7. GB/T17104-97 金属管管环拉伸试验方法8. GB/T241—07 金属管液压试验方法9. GB/T238-02 金属材料线材反复弯曲试验方法10. GB/T2976-04 金属线材缠绕试验方法11. GB/T239-99 金属材料线材扭转试验方法12. GB/T233-2000 金属材料顶锻试验方法13. GB/T5027-07 金属薄板和薄带塑性应变比(r值)试验方法14. GB/T5028-08 金属薄板和薄带拉伸应变硬化指数(n值)试验方法15. GB/T4156-07 金属杯突试验方法(厚度0.2~2mm)六.高温长时间试验1. GB/T2039-97 金属拉伸蠕变及持久试验方法2. GB/Tl0120-96 金属应力松驰试验方法七.金属疲劳试验标准1. GB/T4337-08 金属旋转弯曲疲劳试验方法(代替2107、4337、7733)3. GB/T3075-08 金属轴向疲劳试验方法4. GB/Tl2443-07 金属扭应力疲劳试验方法5. GB/T10622-89 金属材料滚动接触疲劳试验方法6. GB/T15248-08 金属材料轴向等幅低循环疲劳试验7. GB/T12347-08 钢丝绳弯曲疲劳试验方法8. GB/T6398-00 金属材料疲劳裂纹扩展速率试验方法八.金属断裂力学试验1 . GB/T21143-07 金属材料准静态断裂韧度统一试验方法(取代2038和2358)2. GB/T4161-07 金属材料平面应变断裂韧度KIC试验方法3. GB/T7732-08 金属板材表面裂纹断裂韧度KIe试验方法4. GB/T 19744-05 铁素体钢平面应变止裂韧度Kia试验方法九.金属力学试验其它标准1. GB/Tl2444-06 金属材料磨损试验方法试环-试块滑动磨损试验2. GB/T6400-07 金属丝和铆钉高温剪切试验方法3. GB/T6396-08 复合钢板力学及工艺性能试验方法。
金属材料专业综合实验报告

综合实验报告课程名称:金属材料专业综合实验专业:金属材料工程班级:金属材料姓名:学号:指导教师:冶金工程学院2011-2012 学年第 1 学期目录实验一轧测力能参数综合测试实验二金属材料力学性能综合测试实验一轧制力能参数综合测试一、实现轧件咬入轧制参数的设定1.实验目的(1)掌握轧件咬入的条件(2) 掌握最大咬入角的测定(3) 学会分析最大咬入角与各轧制参数的关系2、相关理论知识背景轧辊与轧件的接触弧所对应的角称为接触角或咬入角。
为使轧件能够咬入轧辊,作用于轧件的出轧辊方向摩擦力F的水平分量必须大于或等于作用于轧件的轧制力Pr的水平分量.轧件能够被咬入的条件为:由上式可见,只有摩擦系数大于咬入角的正切值时,轧件才能被咬入轧辊。
对于给定的辊缝值,摩擦力越大,能够咬入的轧件的高度也越大。
tan α的值与轧辊的半径R,轧件的轧前高度h0和轧件的轧后高度h f有关。
轧辊的中心线与轧件和轧辊的入口接触点的距离用g表示. 用简单的几何学知识,可得下式:tan α为对边与邻边的比值,可得:3、实验内容根据设置辊子直径、轧件轧前厚度、轧件轧后厚度、摩擦系数不同的轧制参数实现轧件的咬入。
4、实验步骤(1)设置轧制参数:辊子直径为350㎜,轧件轧前厚度为134㎜,摩擦系数为0.4,调整轧件轧后厚度,得轧件轧后厚度最小为84㎜。
如下图所示:(2)设置轧制参数:辊子直径为450㎜,轧件轧前厚度为174㎜,摩擦系数为0.4,调整轧件轧后厚度,得轧件轧后厚度最小为110㎜。
如下图所示:(3)设置轧制参数:辊子直径为550㎜,轧件轧前厚度为204㎜,摩擦系数为0.4,调整轧件轧后厚度,得轧件轧后厚度最小为126㎜。
如下图所示:5、实验结果在实现轧件的咬入的前提下选择不同的参数,通过调节压下量来达到最大咬入h R g f。
所以,对于确定的轧辊直径和摩擦系角。
由前面的公式得到压下量2(/)数及轧件轧后厚度后,通过改变轧前厚度来达到最大咬入角。
金属材料的工艺性能

金属材料的工艺性能铸造性能金属材料铸造成形获得优良铸件的能力称为铸造性能。
用流动性、收缩性和偏析来衡量。
⑴流动性—熔融金属的流动能力称为流动性。
流动性好的金属易充满铸型,获得外形完整、尺寸精确、轮廓清晰的铸件。
⑵收缩性—铸件在凝固和冷却过程中,其体积和尺寸减少的现象称为收缩性。
收缩不仅影响尺寸,还会使铸件产生缩孔、疏松、内应力、变形和开裂。
⑶偏析—金属凝固后,铸锭或铸件化学成分和组织的不均匀现象称为偏析。
偏析会使铸件各部分的力学性能有很大的差异,降低铸件的质量。
锻造性能金属材料用锻压加工方法成形的能力称为锻造性。
塑性越好,变形抗力越小,金属的锻造性越好。
焊接性能金属材料对焊接加工的适应性称为焊接性。
在机械行业中,焊接的主要对象是钢材。
碳质量分数是焊接好坏的主要因素。
碳质量分数和合金元素质量分数越高,焊接性能越差。
切削加工性能切削加工性能一般用切削后的表面质量(以表面粗糙度高低衡量)和刀具寿命来表示。
金属具有适当的硬度(170HBS~230HBS)和足够的脆性时切削性能良好。
改变钢的化学成分(加入少量的铅、磷元素)和进行适当的热处理(低碳钢正火、高碳钢球化退火)可提高钢的切削加工性能。
热处理工艺性能钢的热处理工艺性能主要考虑其淬透性,即钢接受淬火的能力。
含Mn、Cr、Ni等合金元素的合金钢淬透性比较好,碳钢的淬透性比较差。
金属材料的机械性能材料的性能好坏关系到设备使用寿命,整个国民经济的发展,特别是在航空航天方面(I2-8)。
材料的机械性能包括这么几个方面。
强度金属材料抵抗塑性变形或断裂的能力称为强度。
根据载荷不同,可分为抗拉强度σb 、抗压ζbc 、抗弯ζbb 、抗剪ηb 、抗扭ηt 。
抗拉强度通过拉伸试验测定。
将一截面为圆形低碳钢拉伸试样(如图1a )在材料试验机I2-9)上进行拉伸,测得应力—应变曲线(如图1b )图1a 低碳钢试样图1b 低碳钢应力-应变图图中ζ为应力,ε为应变。
图中各个阶段:OA弹性变形阶段—试样的变形量与外加载荷成正比,载荷卸掉后,试样恢复原来样子。
金属材料的力学性能测试与分析

金属材料的力学性能测试与分析金属材料广泛应用于各个领域,具有优良的力学性能是其重要的特征之一。
为了保证金属材料的质量和可靠性,对其力学性能进行测试与分析是至关重要的。
本文将重点介绍金属材料力学性能测试方法及分析步骤。
一、金属材料的力学性能测试1. 强度测试强度是金属材料抵抗外力的能力,可以通过拉伸试验来进行测试。
该试验的原理是将金属试样放置在拉伸机上,施加逐渐增加的力,直到断裂为止。
在试验过程中,可以测量材料的屈服强度、抗拉强度、延伸率等指标。
这些参数对于评估金属材料的力学性能至关重要。
2. 硬度测试硬度是金属材料抵抗表面压力的能力。
硬度测试可通过使用洛氏硬度计或布氏硬度计进行。
试验时,试样表面受到一定压力,通过测量压印的深度来确定硬度指标。
硬度测试可以帮助判断金属材料的耐磨性和抗变形能力。
3. 韧性测试韧性是金属材料在承受外力时能够吸收能量并发生塑性变形的能力。
冲击试验是测试韧性的常用方法之一。
冲击试验中,将标准试样放置在冲击机上,施加特定冲击载荷,并记录试样失效前所吸收的能量。
韧性测试结果可以评估金属材料在低温环境下的可靠性。
二、金属材料力学性能分析1. 强度分析通过强度测试获得的数据,可以进行强度分析。
通常包括计算应力-应变曲线、屈服强度、抗拉强度、断裂延伸率等参数。
这些数据可用于比较不同金属材料的强度,评估材料的抗拉伸能力以及预测它们在实际应用中的行为。
强度分析对于材料的选择、设计和制造过程中的质量控制具有重要意义。
2. 硬度分析硬度测试结果的分析可用于比较不同金属材料之间的硬度差异。
通过硬度值,可以评估材料的耐磨性和抗变形能力。
硬度分析还可以为金属材料的工艺设计和材料选择提供重要参考。
3. 韧性分析韧性测试结果的分析有助于评估金属材料的抗冲击能力和低温性能。
韧性分析还可以用于指导金属材料的合金设计和淬火工艺的优化。
通过分析韧性参数,可以对材料的破坏机理进行理解,并提供改进金属材料韧性的方法。
金属工艺性能试验—顶锻试验

金属工艺性能试验—顶锻试验顶锻试验金属顶锻试验是对规定尺寸的试样进行锻打或捶击以检验金属在室温或热状态下承受顶锻塑性变形的能力并显示其缺陷的试验。
1试验设备(1)顶锻试验设备通常为顶锻试验机、万能试验机、压力机、锻压机或手锤。
试验时可使用具有足够的刚性的支撑板和防止试样偏斜的夹具。
(2)对于热顶锻试样应用可控制温度的加热装置进行加热。
热顶锻试验装置2顶锻试验方法适用范围适用于下列横截面尺寸(直径,边长,或内切圆直径)范围的金属材料:①对于冷顶锻试验为3mm~30mm②对于热顶锻试验为5mm~200mm③对于热轧盘圆和盘条的顶锻试验检查表面的方法,适用于横截面尺寸为6mm~30mm范围并以盘圆,棒材和线材形状交货的金属材料。
试样的要求(1)切取试样时,应防止损伤试样表面和因过热或加工硬化而改变其性能。
(2)试样应保留原轧制或拔制表面,如试样表面要求机加工,应在相关产品标准中加以说明,但是试样机加工的轨迹应垂直于试样的中心线。
(3)试样的高度在相关产品标准中规定,如果未具体规定,对于黑色金属应为试样横截面尺寸的1.5倍至2倍,推荐采用1.5倍。
对于有色金属应为试样横截面尺寸的1/2倍,试样高度的允许偏差为±5%h。
(4)样试样端面应垂直于试轴线。
(5)试样标志应标记在试样的任一端面。
试验程序(1)顶锻试验应在静压力或动压力下进行。
(2)冷顶锻试验一般在10℃~35℃的室温下进行,对于温度要求较严格的试验,试验温度为23℃±5℃。
(3)对于热顶锻试验,试样的加热温度、加热时间和允许的终锻温度应按照相关产品标准规定的要求。
(4)对于顶锻试验试样所要达到的最终高度按h1=hX计算锻压比应在相关产品标准或协议中规定,如未具体规定,锻压比推荐为1/3。
合表1的规定,热顶锻时应符合表2规定。
表1室温顶锻前后试样高度允许偏差≤5 ±0.5 ±0.5 5~10 ±1 ±110~50 ±2 ±250~100 ±3 ±3100~150 ±4 ±4150~200 ±5 ±53试样顶锻时的变形图1圆柱试样顶锻时变为鼓形①试样顶锻时易趋向变为鼓形,这是由于试样两端面受摩擦力影响而限制了试样横向变形所致。
金属材料热处理试验方法

金属材料热处理试验方法一、实验目的1、了解钢的热处理的基本方法。
2、了解不同热处理方法对钢的组织与性能的影响。
二、实验设备箱式电阻炉(附温控装置)、洛氏硬度计、金相显微镜、淬火水槽、油槽、夹钳、砂纸、玻璃板、侵蚀剂、表1-4-4所列试样一套(试样尺寸:--10m m×12mm)三、实验原理1、碳钢的热处理钢的热处理是指将钢在固态下施以不同的加热、保温与冷却以改变其组织和性能的工艺。
热处理工艺主要包括退火、正火、淬火及回火。
退火是将工件加热到高于Ac3(或Ac1)温度,保温一定时间,随后缓慢冷却以得到近似平衡组织的方法。
根据工件退火加热温度的不同又可分为完全退火与不完全退火。
加热到Ac3以上得到均匀奥氏体组织后缓慢冷却转变为珠光体组织为完全退火,加热到Ac1以上得到奥氏体加未溶碳化物或铁素体再缓慢冷却为不完全退火。
正火是将工件加热Ac3(或Accm)以上,保温一定时间后在静止的空气中冷却得到细珠光体类型组织的热处理工艺。
淬火是将工件加热到Ac3或Ac1以上保温一定时间并以一定的冷却速度冷却,以得到马氏体或下贝氏体组织的热处理工艺。
根据淬火温度不同又可分为完全淬火和不完全淬火。
加热到Ac3以上进行的称为完全淬火,加热到Ac1以上得到的奥氏体加未溶碳化物或铁素体再淬火称为不完全淬火。
回火是将淬火后的工件重新加热到低于相变点的某一温度保温一定时间后冷却,以改善钢的组织和性能的热处理工艺。
任何热处理工艺都包括加热温度、保温时间以及冷却方式三个基本的工艺因素。
(1)加热温度碳钢热处理的加热温度原则上可按下表选定。
但生产中,应根据工件实际情况作适当调整。
碳钢淬火加热温度的控制是很重要的。
亚共析钢加热温度不足时,淬火组织中会出现铁素体,使淬火后硬度不足;共析钢和过共析钢正常淬火加热温度是Ac1+(30~50)℃,加热时有未完全溶解的二次渗碳体,可以提高钢淬火后的硬度和耐磨性。
若加热温度过高时(高于Accm),会因为得到粗大的马氏体以及过多的残余奥氏体而增大脆性或者导致硬度与耐磨性下降。
- 1、下载文档前请自行甄别文档内容的完整性,平台不提供额外的编辑、内容补充、找答案等附加服务。
- 2、"仅部分预览"的文档,不可在线预览部分如存在完整性等问题,可反馈申请退款(可完整预览的文档不适用该条件!)。
- 3、如文档侵犯您的权益,请联系客服反馈,我们会尽快为您处理(人工客服工作时间:9:00-18:30)。
弯曲试验设备
• 支辊式弯曲装置 L= (d+3a) ± 0.5 a • V型模具式弯曲装置 • 虎钳式弯曲装置 • 翻板式弯曲装置 L= (d+2a) ± 2~6mm
弯曲试验程序及结果
• 试样在力作用下弯至规定的弯曲角度后 卸载,并查看试样受拉表面; • 缓慢施加弯曲力; • 按相关产品标准评定结果; • 产品标准规定的弯曲角度认作为最小值, 规定的弯曲半径认作为最大值。
金属管压扁试验
• 适用于外径<600mm壁厚<15×600mm管材; • 试样长度:10mm<L<100mm; • 焊接管:焊缝与力轴可取90度、45度、或0度
金属杯突试验
• 定义:用球形冲头将夹紧的金属板或带状试样 压入规定尺寸的冲模中直至出现穿透裂缝,测 量杯突深度值的试验。 • 目的:检验金属板材(尤其是薄板)适应拉胀 成形的极限能力。 • 试样:一般为厚度0.1~2.0mm、宽度>90mm 未经加工的薄板。
取样定义
• 纵向 :试样长轴平行于轧制或锻造时的最 大延伸方向 • 横向 :试样长轴垂直于轧制或锻造时的最 大延伸方向 • 径向 :试样长轴沿圆半径方向且垂直于轴 向 • 切向 :试样长轴沿圆周方向且垂直于轴向
弯曲试样-通则
• 试样可为圆形、方形、长方形或多边形横截 面。 • 取样位置、方向按产品标准或GB/T2975 • 弯曲表面不得有划痕和损伤。 • 方形和长方形试样的棱边应锉圆,其半径不 应大于厚度1/10。 • 棱边倒圆时不应形成影响结果的横向毛刺、 伤痕或刻痕。 • 用机加工方法去除剪切或火焰切割等形成的 影响材料性能的区域,并保留一侧原表面。 • 弯曲试验时,原表面应位于弯曲的拉伸面。
分类
• • • • 棒材:顶锻试验、弯曲试验等 型材:展平弯曲、反复弯曲等 板材:弯曲、反复弯曲、锻平、杯突等 管材:液压、扩口、缩口、弯曲、压扁、 卷边等 • 线材:反复弯曲、扭转等 • 丝、带材:
常用试验标准
• • • • 金属材料 弯曲试验方法(GB/T232-1999) 金属管 扩口试验方法(GB/T 242-1997) 金属管 压扁试验方法(GB/T 246-1997) 焊接接头弯曲及压扁试验方法 (GB/T2653-1989) • 金属材料 薄板和薄带埃里克森杯突试验 (GB/T4156-2007)
金属反复弯曲试验
• 方法步骤 • 查表选取支座半径 及圆柱顶部至拨杆 底部距离 • 夹紧试样下端,并 将试样向左弯90度 然后返回起始位置 作为第1次弯曲,再 由此位置向右弯90 度并回到起始位置 作为第2次弯曲,依 次连续进行试验
金属反复弯曲试验
• 以每秒<1次的均匀速度进行弯曲操作,直至 规定的弯曲次数或出现肉眼可见的裂纹 • 试样断裂的最后一次弯曲不计入弯曲次数 • 为确保试样与支座连续接触可施加一些张紧力
弯曲试验的影响因素
• 宽厚比:宽度越大要求越严格; • 弯心直径:直径越小要求越严格; • 弯曲角度:角度越大要求越严格。
金属管弯曲试验
• 定义:在带槽弯心上将试样弯曲至规定程 度,检验金属管承受弯曲塑性变形的能力 并显示其缺陷的试验。 • 目的:检验金属管对弯曲加工的适用性。
金属管弯曲试验
• 弯心应具有与管外径轮廓相适应的沟槽。 • 弯曲装置应能限制管的横截面发生椭圆 变形(椭圆短轴最小值≥原外径85%)。 • 对焊接管,如相关标准对焊缝位置未做 规定,焊缝应置于试验位置的中心线。
试验标准
• • • • • 金属材料 顶锻试验方法(GB/T233-2000) 金属管 弯曲试验方法(GB/T 244-1997) 金属管 卷边试验方法(GB/T 245-1997) 金属材料 反复弯曲试验方法(GB/T235-1999) 金属材料 线材 反复弯曲试验方法(GB/T2382002) • 金属线材扭转试验方法(GB/T239-1999) • 金属材料 线材 缠绕试验方法(GB/T29762004)
焊接试板弯曲—术语
• 横弯:焊缝轴线与试样纵轴垂直时的弯曲。 • 纵弯:焊缝轴线与试样纵轴平行时的弯曲。 • 正弯:试样受拉面为焊缝正面的弯曲。
– 双面不对称焊缝、焊缝最大宽度面为正面;双面 对称焊缝,先焊面为正面。
• 背弯:试样受拉面为焊缝背面的弯曲。 • 侧弯:试样受拉面为焊缝纵剖面的弯曲。 • 焊接试板弯曲分类:横向正弯、横向背弯、 横向侧弯、纵向正弯、纵向背弯。
杯突试验示意图
• • • • 方法步骤 测量试样厚度 加润滑剂 将试样放入压模并 加约10kN压紧力 • 平稳施加压力直至 有裂纹穿透试样时 停机 • 测量压头压入的深 度,精确到0.1mm
影响杯突试验结果的因素
• • • • 试样夹紧力 润滑条件 试验加力速度 杯突试验终止(裂纹穿透)点的控制
焊接试板弯曲试样尺寸
• 横弯试样:厚度为焊接接头的试件厚度, 宽度≥1.5试件厚度(最小20mm); • 侧弯试样:厚度≥10mm,宽度等于焊接 接头母材厚度; • 样胚原则上取焊板的全厚度,如无法实现 (例如:对于横弯厚度大于30mm ;对于側弯 厚度大于40mm ),则可取多个试样样胚, 而且所取的试样样胚应覆盖焊板的全厚度。
线材扭转样品及设备
• 样品:平直的金属线材,可适当矫直 • 尺寸:根据直径选取夹头间标记长度 • 设备:俩夹头钳口硬度为55~65HRC,并 在试验中保持在同一轴线,一端固定另一 端可双向旋转并能沿轴向自由移动,可调 节速度,有计数装置和长度标尺
金属线材扭转试验程序
• 按要求选取夹持装置,并可加<2%的抗拉 强度拉紧力值 • 按条件选取扭转速度,偏差在10%之内 • 计数器调零,开机试验并记录不同方向的 扭转次数,Nt表示单扭,N1、N2表示双扭 • 当扭转次数,表面及断口符合要求时,试 验有效;若扭转次数未达要求、或断口离 夹头<2D则试验无效;试样发生劈裂时,最 后一次扭转次数不计入
金属顶锻试验
• 定义:对规定尺寸的试样进行锤击或锻打, 检验金属在室温或热状态下承受顶锻塑性 变形的能力并显示其缺陷的试验。 • 锻压比:顶锻后试样高度与锻前试样高度 之比,一般取1/3。 • 试样:横截面尺寸(直径、内切圆直径) 为6~30mm,高度h约为直径的1.5倍
金属反复弯曲试验
• 定义:将试样一端固定,绕规定半径的圆 柱支座弯曲90度,再沿相反方向弯曲的重 复弯曲试验 • 目的:检查金属线材(0.3~10mm)、薄 板和薄带(<3mm)在反复弯曲中承受塑 性变形的能力并显示其缺陷
金属管卷边试验
• 目的:检验圆形横截面金属管塑性变形的能 力,适用于外径<150mm壁厚<10mm管材; • 方法:先扩口,再卷边
金属管压扁试验
• 定义:将金属管压扁至规定尺寸,检验其 塑性变形能力并显示其缺陷的试验。 • 原理:垂直于管的纵轴方向对规定长度的 试样或管的端部施加力进行压扁,直至在 力的作用下两压板之间的距离达到相关产 品所规定的值H。如为闭合压扁,试样内表 面接触的宽度应至少为试样压扁后其内宽 度的1/2。 • 有时标准要求:H=(1+α)t/(α+t/D)
弯曲试样尺寸-直径
• 产品直径≤50mm--试样采用原横截面,如试 验机能力不足,对直径超过30~50mm的产 品,可加工成横截面内切圆直径>25mm的 试样。 • 产品直径>50mm--可加工成横截面内切圆 直径>25mm的试样。 • 钢筋类产品一般均应以其全截面进行试验。 • 非仲裁试验,经协议可用宽度和厚度大于以 上规定的试样。
金属线材缠绕试验
• 定义:将线材紧密地缠绕在一定直径的 芯棒上,以规定圈数成螺旋线圈 • 目的:测定金属线材在缠绕试验过程中 承受塑性变形的能力 • 试样:直径为0.1~10mm的金属线材
金属线材缠绕试验
• 试验程序 • 线材没有任何扭转,以<1圈/s的均匀速度 以螺旋线形式缠绕在规定芯棒上 • 缠绕时,可在自由端加不超过材料抗拉强 度5%的拉紧力 • 如要求解圈后再缠绕,速度应尽可能慢以 防样品发热 • 按规定检查试样表面,一般未发现裂纹判 为合格
金属工艺性能试验
上海材料研究所检测中心 凌霄
力学性能与工艺性能
力学性能:材料在外力作用下应力与 应变的关系;它是材料的使用性能; 结构强度设计的依据。 工艺性能:材料适应某种加工工艺的 能力。它是力学性能试验的一种补充 试验。
特点
• 试验过程与材料的加工工艺过程、使 用条件相似。 • 试验结果能反映材料的宏观塑性、韧 性及部分外表质量问题。 • 试样容易加工。 • 试验方法简便,无需复杂的试验设备 即可实现。
金属管扩口试验
• 定义:将规定锥度的顶心压入金属管一端,使 直径均匀地扩张至规定尺寸,检验金属管径向 扩张塑性变形的能力并显示其缺陷的试验。 • 原理:用圆锥形顶心扩大管段试样的一端,直 至扩大端的最大外径达到相关产品标准所规定 的值D0。 • 目的:检验在给定条件下管子的塑性变形能力, 适用于外径<150mm壁厚<10mm管材; • 扩口率:Xd=(D0-D)/D×100%
金属弯曲试验
• 目的:定性检验在给定试验条件下,试样 承受弯曲变形的能力,并揭露其缺陷。 • 原理:将一定形状和尺寸的试样放置于弯 曲装置上,以规定直径的弯心将试样弯曲到 所要求的角度后,卸除试验力检查试样承受 变形的能力。 • 弯曲试验与弯曲力学性能试验区别:前者 定性后者定量;前者用于韧性材料后者用 于脆性材料。
弯曲试样尺寸-宽度
• 按相关产品标准要求 • 产品标准未规定时: – 产品宽度≤20mm---试样采用原宽度 – 产品宽度>20mm
• 厚度<3mm---试样宽度为20mห้องสมุดไป่ตู้±5mm • 厚度≥3mm---试样宽度为20~50mm
弯曲试样尺寸-厚度
• 按相关产品标准要求 • 产品标准未规定时: – 产品厚度≤25mm--试样采用原厚度 – 产品厚度>25mm--机加工减薄至≥25mm