选择机加工件测量器具的基本原则探讨
公差试题库

一、判断题(对画√,错画×)
55.三坐标测量机校准探针的目的是把每个探针调整到一个 设定的固定位置上。 56.选用三坐标测量机的测头组件时,应有一定的长度和质 量。 57.当圆柱体ϕ60 0的实际尺寸小于ϕ60mm时,允许其轴线 或素线存在直线度误差。 58.形状误差是指被测提取要素对拟台要素的变动量。 59.形状误差值是用最小包容区域的宽度或直径表示的。 60.位置误差分为定向、定位和轮廓度三类。 61.由基准目标建立基准时,基准点目标可以用球端支承来。
一、判断题(对画√,错画×)
119.蜗杆的类型很多,常用的为阿基米德螺旋线蜗杆和轴向 直廓蜗杆。 120.铸件箱体上的铸造斜度与垂直壁高有关,垂直壁越高, 铸造斜度越大。 121.箱体上支承啮合传动副的传动轴的两孔间的中心距,应 符合啮合传动副中心距的要求。 122.箱体上安装滚动轴承外圈孔的公差应按滚动轴承配合要 求来选择。 123.常见的V带轮有基准宽度制V带轮、有效宽度制V带轮、 汽车V带轮及深槽V带轮。 124.叉架类零件一般由工作部分、支承部分和连接部分组成。
一、判断题(对画√,错画×)
93.在确定被测件的形位公差时,同一平面上给出的形状公 差值一般应大于位置公差值。 94.在确定被测件的形位公差时,圆柱形零件的尺寸公差一 般应小于位置公差。 95.在确定被测件的形位公差时,形状公差值一般应大于表 面粗糙度值。 96.在确定被测件的形位公差时,在满足功能要求的前提下, 线对线和线对面,相对于面对面的平行度或垂直度可适当提 高1~2级。 97.在确定齿轮、蜗杆、花键、带轮等标准件的形位公差时, 应符合GB/T 1184—1996标准。
一、判断题(对画√,错画×)
62.形位误差测量不确定度与被测要素的公差等级有关,被 测要素的公差等级越高,测量不确定度占形位公差的百分比 越大。 63.槽形综合量规不适用检测细长轴轴线的直线度。 64.检测奇数棱形圆柱体的圆度时,可采用两点法,检测偶 数棱形圆柱体的圆度时,可采用三点法。 65.用平板、带指示器的测量架、V形块或直角座测量圆柱度 时,应测量若干个横截面,并取所有示值中的最大值与最小 值的差值之半作为圆柱度误差。 66.在测量轴肩面或轴端面对轴线的垂直度误差时,可以用 导向块模拟基准轴线。 67.在测量两孔轴线的平行度或垂直度误差时,都可以用心 轴来模拟基准轴线和被测孔轴线。
机加工作业指导书

机加工作业指导书机加工作业指导书编号:WHJX/ZD02-04编制:技术科审核:王煜梅批准:徐公明实施日期:2009.5.10诸城市五环机械有限公司机加工作业指导书1 总则本指导书适用于本公司各类机加工过程。
1.1操作者接到加工任务后,首先要检查加工所需的产品图样、工艺规程和有关技术资料是否齐全。
1.2要看懂、看清产品图样及其技术要求,有疑问之处应找有关人员问清后再进行加工。
1.3按产品图样或工艺规程复核工件毛坯或半成品是否符合要求,发现问题应及时向有关人员反映,待问题解决后才能加工。
1.4按工艺规程要求准备好加工所需的全部工艺装备,发现问题及时处理,对新设备、新夹具、磨具等要先熟悉其使用要求和操作方法。
1.5加工所用的工艺装备及量具应放在规定的位置,不得乱放,更不能放在机床导轨处。
1.6工艺装备不得随意拆卸和更改。
1.7检查加工所用的机床设备,准备好所需的各种附件,加工前机床要按规定进行润滑和空运转。
1.8在装夹各种工具前,一定要把刀柄、刀杆、导套等擦拭干净。
1.9刀具装夹后,应用对刀装置或试切削检查其正确性。
1.10在机床工作台上安装夹具时,首先要擦净其定位基面,并要找正其与刀具的相对位置。
1.11装夹前应将其定位面、夹紧面、垫铁和夹具的定位、夹紧面擦干净并不得有毛刺。
1.12按工艺规程中的规定定位基准装夹工件。
1.13对无专用夹具的工件,装夹时应按以下原则进行找正:1)对划线工件应按划线进行找正。
2)对不划线工件,在本工序后尚需继续加工的表面,找正精度应保证下道工序有足够的加工余量。
3)对在本工序加工到成品尺寸的表面,找正精度应小于尺寸公差和位置公差的三分之一。
4)对在本工序加工到成品尺寸的未注尺寸公差和位置公差的表面,其找正精度应保证对未注尺寸公差和位置公差的要求。
1.14夹紧工件时,夹紧力的作用点应通过支撑点或支撑面。
1.15夹持精加工面和软材质工件时,应垫以软垫,如紫铜皮等。
1.16用压板压紧工件时,压板支撑板应略高于被压工件表面,并且压紧螺栓应尽量靠近工件,以保证压紧力。
如何正确选择数控机床的使用参数

如何正确选择数控机床的使用参数数控机床作为一种重要的现代化加工设备,广泛应用于汽车制造、航空航天、机械制造等领域。
选择正确的使用参数对于保证加工质量、提高生产效率至关重要。
本文将从机床的类型、加工材料、加工工艺等方面来探讨如何正确选择数控机床的使用参数。
首先,在选择数控机床的使用参数之前,我们需要了解加工的具体需求以及机床的类型。
数控机床有多种类型,包括铣床、车床、钻床等,每一种类型的机床在使用参数上也会有所不同。
例如,在选择车床的使用参数时,需要考虑所加工零件的直径、长度、精度等因素。
在选择铣床的使用参数时,则需要考虑工件的尺寸、表面粗糙度要求、加工刀具的类型等因素。
因此,在选择数控机床的使用参数时,必须充分了解所加工零件的具体要求,合理选择机床类型,并根据不同类型的机床进行参数的设置。
其次,在选择数控机床的使用参数时,需考虑所加工材料的类型、性质和硬度。
不同的材料对机床的使用参数有着不同的要求。
例如,对于硬度较高的金属材料,应选择较高的切削速度和进给速度,以确保切削刀具与工件之间的接触时间较短,并减小切削力,提高加工效率。
而对于脆性材料,应选择较小的进给速度和切削速度,以避免过大的切削力造成工件断裂或表面破坏。
在选择数控机床使用参数时,必须根据材料的性质和硬度来调整切削速度、进给速度、进给深度等参数,以实现最佳的加工效果。
此外,在选择数控机床使用参数时,还需要考虑具体的加工工艺。
不同的加工工艺对机床使用参数有着不同的要求。
例如,在进行粗加工时,应选择较大的进给速度和切削速度,以提高加工效率;而在进行精加工时,则需要选择较小的进给速度和切削速度,以提高加工精度。
另外,还需要注意切削液的使用,以降低加工温度、延长刀具寿命,并减少切削过程中产生的摩擦和磨损。
在选择数控机床使用参数时,必须根据具体的加工工艺要求,合理调整各项参数,以实现高效、精确的加工。
最后,在选择数控机床使用参数时,还需要充分考虑机床本身的性能指标和技术参数。
测量基础知识

第三章 测量方法分类
绝对测量和相对测量:测量器具的示值直接反映被测量 量值的测量为绝对测量。用游标卡尺、外径千分尺测量 轴径。将被测量与一个标准量值进行比较得到两者差值 的测量为相对测量。如用内径百分表测量孔径为相对测 量。 被动测量和主动测量:产品加工完成后的测量为被动测 量;正在加工过程中的测量为主动测量。被动测量只能 发现和挑出不合格品。而主动测量可通过其测得值的反 馈,控制设备的加工过程,预防和杜绝不合格品的产生。
Page 13
第四章 测量误差 ①测量器具:测量器具设计中存在的原理误差,如杠杆机 构、阿贝误差等。制造和装配过程中的误差也会引起其示 值误差的产生。例如刻线尺的制造误差、量块制造与检定 误差、表盘的刻制与装配偏心、光学系统的放大倍数误差、 齿轮分度误差等。其中最重要的是基准件的误差,如刻线 尺和量块的误差,它是测量器具误差的主要来源。
Page 11
Page 12
第四章 测量误差
由于测量过程的不完善而产生的测量误差,将导致测得 值的分散入不确定。因此,在测量过程中,正确分析测 量误差的性质及其产生的原因,对测得值进行必要的数 据处理,获得满足一定要求的置信水平的测量结果,是 十分重要的。 测量误差定义:被测量的测得值x与其真值x0之差,即: △= x -x0 由于真值是不可能确切获得的,因而上述善于测量误差 的定义也是理想的概念。在实际工作中往往将比被测量 值的可信度(精度)更高的值,作为其当前测量值的 “真值”。 误差来源:测量误差主要由测量器具、测量方法、测量 环境和测量人员等方面因素产生。
Page 10
第三章 测量方法分类
接触测量和非接触测量:测量器具的测头与被测件表面接 触并有机械作用的测力存在的测量为接触测量。如用光切 法显微镜测量表面粗糙度即属于非接触测量。
量具的正确使用与维护保养
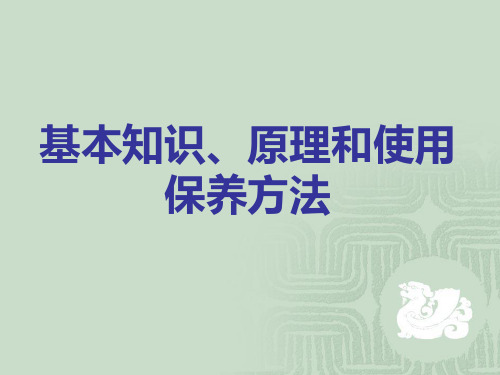
A.静态测量——对被测工件逐个地进行单项测量,这是日常测量中 大量地进行的。使用通用量具所进行的测量也是静态测量的一种。
B.动态测量——对被测工件进行连续的自动测量。这是目前还比较 新的测量方法,例如用激光比长仪检定精密线纹尺,用激光丝杆检 查仪检定精密丝杆的螺距,都属于动态测量。
(4)测量范围: 计量器具(测量仪器)的误差处在规定极限内的一组 被测量的值。 (5)示值: 由计量器具所指示的被测量值。 (6)示值误差: 计量器具示值与测量(约定)真值之差。 (7)分辩率: 显示装置能有效辨别的最小的示值差。 (8)稳定性: 计量器具保持其计量特性随时间恒定的能力。
(9)准确度等级:
(6)按测量过程对工艺所起作用可分主动测量和被动测量。
A.主动测量——加工中的测量,是一种最先进的测量方法,使加工 过程和测量同时,可以预防生产废品。
B.被动测量——在工件加工后进行测量,只能鉴别工件合格与否, 不能及时防止废品。
(3)长度计量器具的分类
(1)标准量具 是具体复现测量单位所用的物体。 标准量具主要用来检定测量设备、保证测量
否合格所进行的全部工作。 〈2〉为什么要对计量器具进行周期检定? 是为了防止使用失去 准确度的量具、量仪
测量工件 ,从而保证量值的统一、准确传 递。 〈3〉什么是计量检定规程?
是为了检定计量器具而制定的具有国家 法定性的技术文件。
其规程中明确规定了:
(1)计量器具的适用范围。(2)计量 器具的名称。(3)计量性能。(4)检 定项目。(5)检定方法。(6)检定条 件。(7)检定数据的处理及检定周期等。
(4)气动式量仪(压力式、流量计式);
(5)光 学机械式量仪(光学计、测长仪、投影仪、 干涉仪等);
第六章 检验和技术测量的规程及原则

6.2 检验和测量的基本原则
一、测量方法的选择原则
测量方法主要根据测量目的,生产批量, 被测件的结构、尺寸、精度特征,以及 现有计量器具的条件等来选择,其选择 原则是:
x x0
2.测量误差的表示方法 (1)绝对误差δ
绝对误差是测量结果与其真值差。由于测 量结果可大于或小于真值,因此绝对误差可 能是正值或负值。
(2)相对误差相对误差,是测量的绝对误差δ与其 真值之比,由于被测量的真值是不可知的, 实际中以被测几何量的量值代替真值进行估 算。相对误差是无量纲的数值,通常用百分 数表示。
1.在工序间检验时,测量基准面应与工艺基准面-致 2.在终结检验时,测量基准面应与装配基准面-致。
二、定位方式的选择原则
• (1)对平面可用平面或三点支撑定位; • (2)对球面可用平面或V形铁定位; • (3)对外圆柱表面可用V形块或顶尖、三爪卡盘定
位;
• (4)对内圆柱表面可用心轴、内三爪卡盘定位。
• 机械产品的质量检验依据是有关国家标准、设计图样和制造工艺艺,制订出检验操 作指导书,指导检验人员对产品质量进行合格性检验。
国家标准按性质可分为以下4种
1.基础标准
• 基础标准包括:通用技术语言标准(如名词 术语、标志标记、符号、代号和制图等); 精度与互换性标准(如形状和位置公差、表 面粗糙度、极限与配合等);系列化和配套 关系标准(如标准长度、直径和优先数与优 先数系等);结构要素标准(如中心孔、锥度 和T形槽等)。此外,还有工艺标准、材料标 准等。
• 按生产流程顺序分为以下几类。
机修钳工复习题
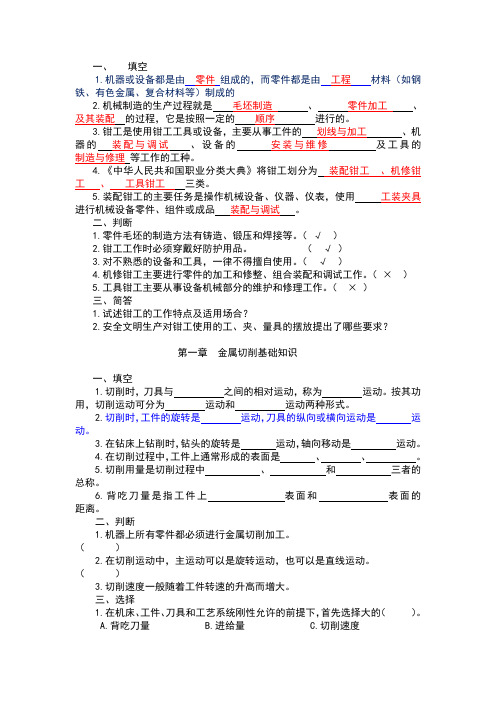
一、填空1.机器或设备都是由零件组成的,而零件都是由工程材料(如钢铁、有色金属、复合材料等)制成的2.机械制造的生产过程就是毛坯制造、零件加工、及其装配的过程,它是按照一定的顺序进行的。
3.钳工是使用钳工工具或设备,主要从事工件的划线与加工、机器的装配与调试、设备的安装与维修及工具的制造与修理等工作的工种。
4.《中华人民共和国职业分类大典》将钳工划分为装配钳工、机修钳工、工具钳工三类。
5.装配钳工的主要任务是操作机械设备、仪器、仪表,使用工装夹具进行机械设备零件、组件或成品装配与调试。
二、判断1.零件毛坯的制造方法有铸造、锻压和焊接等。
(√)2.钳工工作时必须穿戴好防护用品。
(√)3.对不熟悉的设备和工具,一律不得擅自使用。
(√)4.机修钳工主要进行零件的加工和修整、组合装配和调试工作。
(×)5.工具钳工主要从事设备机械部分的维护和修理工作。
(×)三、简答1.试述钳工的工作特点及适用场合?2.安全文明生产对钳工使用的工、夹、量具的摆放提出了哪些要求?第一章金属切削基础知识一、填空1.切削时,刀具与之间的相对运动,称为运动。
按其功用,切削运动可分为运动和运动两种形式。
2.切削时,工件的旋转是运动,刀具的纵向或横向运动是运动。
3.在钻床上钻削时,钻头的旋转是运动,轴向移动是运动。
4.在切削过程中,工件上通常形成的表面是、、。
5.切削用量是切削过程中、和三者的总称。
6.背吃刀量是指工件上表面和表面的距离。
二、判断1.机器上所有零件都必须进行金属切削加工。
()2.在切削运动中,主运动可以是旋转运动,也可以是直线运动。
()3.切削速度一般随着工件转速的升高而增大。
三、选择1.在机床、工件、刀具和工艺系统刚性允许的前提下,首先选择大的()。
A.背吃刀量B.进给量C.切削速度2.粗加工时,进给量可以取得()。
A.大一些B.小一些C.以上都可以四、名词解释1.金属切削2.切削速度五、简答选择切削用量的基本原则是什么?六、计算1.工件毛坯直径为Φ50mm,主轴转速为600r/mm,一次车成直径为Φ48mm 的轴,求背吃刀量和切削速度。
技术测量基础
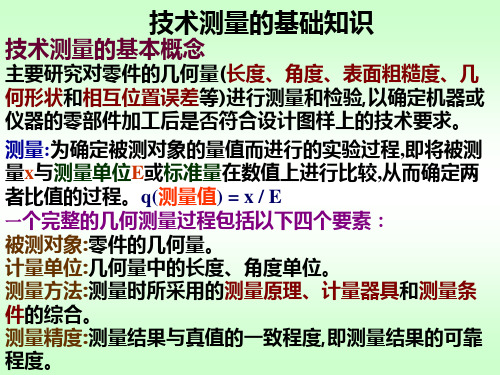
1.直接测量法
其误差来源:仪器误差、测量方法误差、基准件误差统称 为测量总误差的误差分量。按其性质分为已定系统误差、 随机误差和未定系统误差。
✓ 已定系统误差按代数和法合成。
测量误差合成
对于较重要的测量,不但给出测量结果,还应给出测量结 果的准确程度,即极限误差。 简单的测量,测量极限误差可从仪器的使用说明书或检定 规程中查得仪器的测量不确定度。 复杂的测量,只能分析测量误差的组成项并计算其数值,按 一定方法综合成测量方法极限误差。上述过程叫测量误差 的合成。
测量误差合成包括直接测量法和间接测量法测量误差的合 成:
立式测长仪工作原理
工作台1上放置被测件2,通过测量 轴体4上的可换测量头3与被测件接 触测量。测量轴体4是一个高精度圆 柱体,在精密滚动轴承支持下,通 过钢带8,滑轮9,平衡锤12和阻尼 油缸13完成平稳的轴向升降运动。 配重7用来调整测量力。
测量轴体的轴线上固定有基准标 尺(玻璃刻尺)5,其上有l01条刻线 ,刻度间隔为1mm。由光源11发 出的光,经透镜10,再透过基准玻 璃刻尺,将毫米刻线影象投射入螺 旋读数显微镜6,进行读数。
一个完整的几何测量过程包括以下四个要素: 被测对象:零件的几何量。 计量单位:几何量中的长度、角度单位。 测量方法:测量时所采用的测量原理、计量器具和测量条 件的综合。 测量精度:测量结果与真值的一致程度,即测量结果的可靠 程度。
在测量技术领域和技术监督工作中,常用到:
检验:确定被检几何量是否在规定的极限范围内,从而判断 其是否合格的实验过程.通常用无刻度量具来判断被检对 象的合格性,不能得到具体数值。
技术测量的基础知识
技术测量的基本概念
主要研究对零件的几何量(长度、角度、表面粗糙度、几 何形状和相互位置误差等)进行测量和检验,以确定机器或 仪器的零部件加工后是否符合设计图样上的技术要求。
测量的基本原则
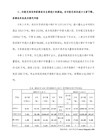
在实际测量中,对于同一被测量往往可以采用多种测量方法。为减小测量不确定度,应尽可能遵守以下基本测量原则:
(1)阿贝原则:要求在测量过程中被测长度与基准长度应安置在同一直线上的原则。若被测长度与基准长度并排放置,在测量比较过程中由于制造误差的 存在,移动方向的偏移,两长度之间出现夹角而产生较大的误差。误差的大小除与两长度之间夹角大小有关外,还与其之间距离大小有关,距离越大,误差也越大。
(2)基准统一原则:测量基准要与加工基准和使用基准统一。即工序测量应以工艺基准作为测量基准,终检测量应以设计基准作为测量基准。
最短链原则:在间接测量中,与被测量具有函数关系的其它量与被测量形成测量链。形成测量链的环节越多,被测量的不确定度越大。因此,应尽可能减少测量链的环节数,以保证测量精度,称之为最短链原则。 当然,按此原则最好不采用间接测量,而采用直接测量。所以,只有在不可能采用直接测量,或直接测量的精度不能保证时,才采用间接测量。 应该以最少数目的量块组成所需尺寸的量块组,就是最短链原则的一种实际应用。 最小变形原则:测量器具与被测零件都会因实际温度偏离标准温度和受力(重力和测量力)而产生变形,形成测量误差。被测零件有足够的等温时间、选用与被测零件线胀系数相近的测量器具、选用适当的测量力并保持其稳定、选择适当的支承点等,都是实现最小变形原则的有效措施。
仪器设计的基本原则

一样,否则将造成更大的测量误差。
1. 爱彭斯坦(Eppenstein)光学补偿方法
爱彭斯坦(Eppenstein)光学补偿方法主要被应用于高精度测长机的读数系统 中。图3-4a为测长机原理图。
刻尺面位于焦距f相同的两个透镜N1,N2的焦面上。M2,N2与尾座联为一体,
M1,N1与头座联为一体。刻尺由装在尾座内的光源照明。对零时,设0刻线成象 在s1点。测量时,尾座向左移动。当导轨平直时,设相应于被测长度读数值的刻线 0ˊ亦成象在s1处时不产生误差。现假设由于导轨直线度的影响,使尾座产生倾角
了解被测控参数的特点 1)了解精度、数值范围(一维、二维、量值范围)、量值性质 (单值、多值)、测量状态(动态、静态)等要求; 2) 按国家标准严格的定义确定仪器工作原理 了解测控参数载体的特点 机械与光学载体居多。要考虑载体的大小、形状、材料、 重量、状态等 了解仪器的功能要求 是静态还是动态、开环还是闭环、一维还是多维、单一参数 还是复合参数、检测效率、测量范围、承载能力、操作方式、 显示方式、自动诊断、自动保护等。 了解仪器的使用条件 室内还是室外、在线还是脱机、间断还是连续、环境状况。
新方法的创新研究。
对比
测量 原理 图示
光学投影式刀具预调仪
计算机视觉型刀具预调仪
工作 过程
将刀尖到影屏上,采用目视瞄准定 光学投影光路的加工及调整复杂, 由人眼控制刀尖对准十字线的微细 调整过程,要求二维光栅数字系统 的导轨必须具备微调机构,增加了 机构设计的难度;而且人眼目视瞄 准的精度低,工作效率差。
使用CCD摄像机采集被测刀具图像,测量时, 计算机影屏上的十字线自动跟踪刀具切削点, 当刀尖稳定在测量区域后,即已完成测量
优缺 点
消除了操作者的人为误差,实现了自动化、 数字化、微米级的测量精度。
检具设计的基本要求
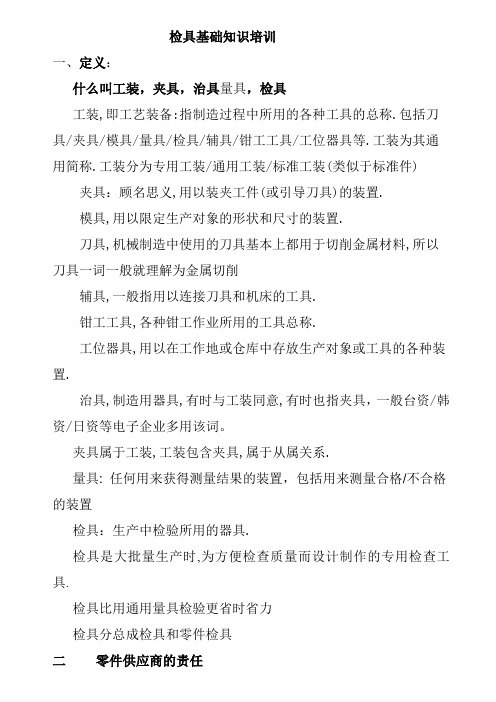
检具基础知识培训一、定义:什么叫工装,夹具,治具量具,检具工装,即工艺装备:指制造过程中所用的各种工具的总称.包括刀具/夹具/模具/量具/检具/辅具/钳工工具/工位器具等.工装为其通用简称.工装分为专用工装/通用工装/标准工装(类似于标准件) 夹具:顾名思义,用以装夹工件(或引导刀具)的装置.模具,用以限定生产对象的形状和尺寸的装置.刀具,机械制造中使用的刀具基本上都用于切削金属材料,所以刀具一词一般就理解为金属切削辅具,一般指用以连接刀具和机床的工具.钳工工具,各种钳工作业所用的工具总称.工位器具,用以在工作地或仓库中存放生产对象或工具的各种装置.治具,制造用器具,有时与工装同意,有时也指夹具,一般台资/韩资/日资等电子企业多用该词。
夹具属于工装,工装包含夹具,属于从属关系.量具: 任何用来获得测量结果的装置,包括用来测量合格/不合格的装置检具:生产中检验所用的器具.检具是大批量生产时,为方便检查质量而设计制作的专用检查工具.检具比用通用量具检验更省时省力检具分总成检具和零件检具二零件供应商的责任A. 零件供应商对检具获得过程的所有要素应负直接的责任。
另外,零件供应商必须保存所有相关活动的文件。
B. 供应商应保证检具符合下列条件:1. 时间进度要符合整个项目的时间节点。
2. 与被测零件的使用功能相符合。
3. 通过遵循定位基准方案,使检具符合被测零件的几何尺寸和公差图纸(GD&T)。
3.1 注意:供应商必须核实检具上是否需要垫块。
(比如在有尼龙扣或没有尼龙扣的情况下)4. 在检具中必须包括所有关键产品特性(KPC:合理的预期的变差可能足以影响产品安全性或政府标准或法规的符合性,或很可能足以影响顾客对产品满意程度的产品特性),产品质量特性(PQC:指那些特殊特性:客户满意与其整个公差范围相符,但一旦超出规范,客户损失将急剧上升。
公差范围内的变差略微影响客户满意,而一旦超出公差,将严重影响客户满意)的测量。
机械加工检验标准及方法
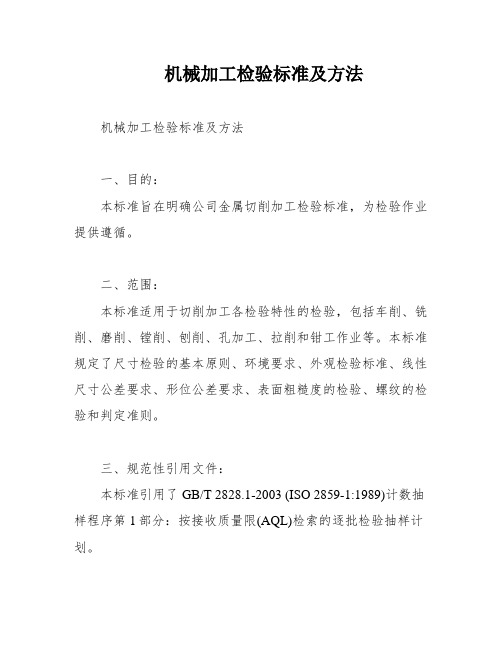
机械加工检验标准及方法机械加工检验标准及方法一、目的:本标准旨在明确公司金属切削加工检验标准,为检验作业提供遵循。
二、范围:本标准适用于切削加工各检验特性的检验,包括车削、铣削、磨削、镗削、刨削、孔加工、拉削和钳工作业等。
本标准规定了尺寸检验的基本原则、环境要求、外观检验标准、线性尺寸公差要求、形位公差要求、表面粗糙度的检验、螺纹的检验和判定准则。
三、规范性引用文件:本标准引用了GB/T 2828.1-2003 (ISO 2859-1:1989)计数抽样程序第1部分:按接收质量限(AQL)检索的逐批检验抽样计划。
四、尺寸检验原则:1.基本原则:符合设计图纸的尺寸为合格,否则为不合格。
2.最小变形原则:在不影响使用的情况下,尽量减小变形。
3.最短尺寸链原则:在不影响使用的情况下,尽量减小尺寸链。
4.封闭原则:尺寸链必须封闭,否则为不合格。
5.基准统一原则:采用同一基准进行测量。
6.其他规定。
五、检验对环境的要求:1.温度。
2.湿度。
3.清洁度。
4.振动。
5.电压。
六、外观检验:1.检验方法。
2.检验目距。
3.检测光源。
4.检测时间。
5.倒角、倒圆。
6.___、毛刺。
7.伤痕。
8.刀纹、振纹。
9.凹坑、凸起、缺料、多料、台阶。
10.污渍。
11.砂孔、杂物、裂纹。
12.防护包装。
七、表面粗糙度的检验:1.基本要求。
2.检验方法。
3.测量方向。
4.测量部位。
5.取样长度。
八、线性尺寸和角度尺寸公差要求:1.基本要求。
2.未注公差。
九、形状和位置公差的检验:1.基本要求。
2.检测方法。
十、螺纹的检验:1.使用螺纹量规检验螺纹制件。
2.单项检验。
十一、外协加工件的检验规定:1.来料检验。
2.成品检验计划。
十二、判定规则。
附注:1.___原则。
本文介绍了尺寸检验的相关标准和原则。
基本原则是只接收位于规定尺寸验收极限的工件,并且有配合要求的孔、轴的尺寸检验应符合泰勒原则。
最小变形原则要求尽量使各种因素的影响而产生的变形为最小,最短尺寸链原则要求测量链的环节应减到最少,封闭原则要求满足封闭条件,基准统一原则要求测量基准应与设计基准、工艺基准保持一致。
机械加工检验标准及方法

机械加工检验标准及方法一. 目的:二. 范围:三. 规范性引用文件四. 尺寸检验原则1.基本原则:2.最小变形原则:3.最短尺寸链原则:4.封闭原则:5.基准统一原则:6.其他规定五. 检验对环境的要求1.温度2.湿度3.清洁度4.振动5.电压六. 外观检验1.检验方法2.检验目距3.检测光源4.检测时间5 .倒角、倒圆6.批锋、毛刺7.伤痕8.刀纹、振纹9 .凹坑、凸起、缺料、多料、台阶10.污渍11 .砂孔、杂物、裂纹12 .防护包装七. 表面粗糙度的检验1.基本要求2.检验方法:3 .测量方向4.测量部位5.取样长度八. 线性尺寸和角度尺寸公差要求1.基本要求2 线性尺寸未注公差九.形状和位置公差的检验1.基本要求3.检测方法十.螺纹的检验1.使用螺纹量规检验螺纹制件2.单项检验十一.外协加工件的检验规定1.来料检验2. 成品检验计划十二.判定规则附注:1.泰勒原则目的:为了明确公司金属切削加工检验标准,使检验作业有所遵循,特制定本标准。
二. 范围:本标准适用于切削加工(包括外协、制程、出货过程)各检验特性的检验。
在本标准中,切削加工指的是:车削加工、铣削加工、磨削加工、镗削加工、刨削加工、孔加工、拉削加工和钳工作业等。
本标准规定了尺寸检验的基本原则、对环境的要求、外观检验标准、线性尺寸公差要求、形位公差要求、表面粗糙度的检验、螺纹的检验和判定准则。
注:本标准不适用于铸造、锻造、钣金、冲压、焊接加工后的检验,其检验标准另行制定。
本标准不拟对长度、角度、锥度的测量方法进行描述,可参看相关技术手册;形位公差的测量可参看GB/T1958-1980 ;齿轮、蜗杆的检验可参看相关技术手册。
三. 规范性引用文件下列文件中的条款通过本标准的引用而成为本标准的条款。
凡是注日期的引用文件,其随后所有的修改单(不包括勘误的内容)或修订版均不适用于本标准,然而,鼓励根据本标准达成协议的各方研究是否可使用这些文件的最新版本。
《计量学基础》试卷及答案
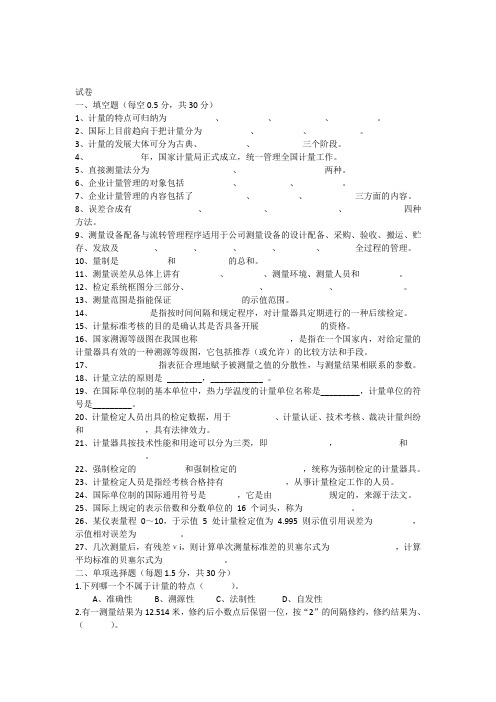
试卷一、填空题(每空0.5分,共30分)1、计量的特点可归纳为、、、。
2、国际上目前趋向于把计量分为、、。
3、计量的发展大体可分为古典、、三个阶段。
4、年,国家计量局正式成立,统一管理全国计量工作。
5、直接测量法分为、两种。
6、企业计量管理的对象包括、、。
7、企业计量管理的内容包括了、、三方面的内容。
8、误差合成有、、、四种方法。
9、测量设备配备与流转管理程序适用于公司测量设备的设计配备、采购、验收、搬运、贮存、发放及、、、、、全过程的管理。
10、量制是和的总和。
11、测量误差从总体上讲有、、测量环境、测量人员和。
12、检定系统框图分三部分、、、。
13、测量范围是指能保证的示值范围。
14、是指按时间间隔和规定程序,对计量器具定期进行的一种后续检定。
15、计量标准考核的目的是确认其是否具备开展的资格。
16、国家溯源等级图在我国也称,是指在一个国家内,对给定量的计量器具有效的一种溯源等级图,它包括推荐(或允许)的比较方法和手段。
17、指表征合理地赋予被测量之值的分散性,与测量结果相联系的参数。
18、计量立法的原则是________,____________ 。
19、在国际单位制的基本单位中,热力学温度的计量单位名称是_________,计量单位的符号是_________。
20、计量检定人员出具的检定数据,用于、计量认证、技术考核、裁决计量纠纷和,具有法律效力。
21、计量器具按技术性能和用途可以分为三类,即,和。
22、强制检定的和强制检定的,统称为强制检定的计量器具。
23、计量检定人员是指经考核合格持有,从事计量检定工作的人员。
24、国际单位制的国际通用符号是,它是由规定的,来源于法文。
25、国际上规定的表示倍数和分数单位的16 个词头,称为。
26、某仪表量程0~10,于示值5 处计量检定值为4.995则示值引用误差为,示值相对误差为。
27、几次测量后,有残差νi,则计算单次测量标准差的贝塞尔式为,计算平均标准的贝塞尔式为。
试述精基准的选择原则

试述精基准的选择原则
精基准的选择原则主要包括以下几点:
1. 基准重合原则:选择设计基准作为定位基准,这样可以避免基准不重合误差,提高加工精度。
2. 基准统一原则:在多道工序中尽可能采用同一个定位基准,这样可以减少工装设计和制造的工作量,提高生产效率,同时可以保证各加工表面的相互位置精度。
3. 互为基准原则:对于两个相互位置精度要求较高的表面,可以采用互为基准、反复加工的方法,以保证其位置精度。
4. 自为基准原则:有些精加工或光整加工工序要求加工余量小而均匀,这时可以选择加工表面本身作为定位基准。
5. 便于装夹原则:选择的精基准应能保证工件定位准确、可靠,夹紧方便、可靠。
在实际生产中,精基准的选择应根据具体的加工要求和生产条件综合考虑,灵活应用上述原则。
同时,还应注意精基准的精度和表面质量,以确保加工质量和效率。
【doc】计量器具的选择和验收极限的确定:简介GB3177—82
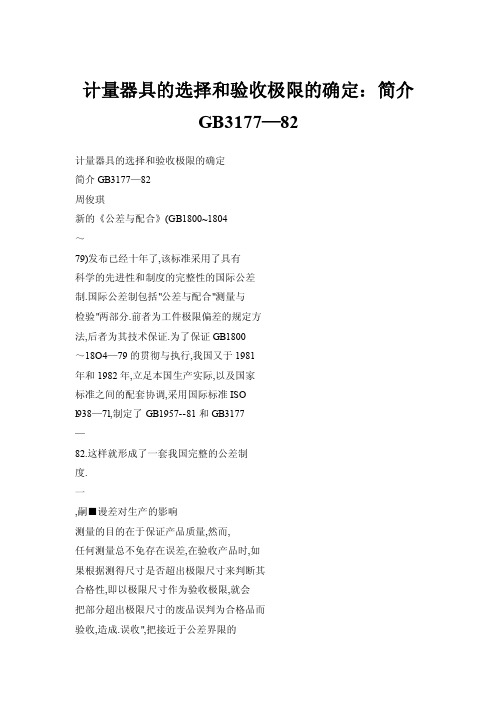
计量器具的选择和验收极限的确定:简介GB3177—82计量器具的选择和验收极限的确定简介GB3177—82周俊琪新的《公差与配合》(GB1800~1804~79)发布已经十年了,该标准采用了具有科学的先进性和制度的完整性的国际公差制.国际公差制包括"公差与配合"测量与检验"两部分.前者为工件极限偏差的规定方法,后者为其技术保证.为了保证GB1800~18O4—79的贯彻与执行,我国又于1981年和1982年,立足本国生产实际,以及国家标准之间的配套协调,采用国际标准ISOl938—7l,制定了GB1957--81和GB3177—82.这样就形成了一套我国完整的公差制度.一,嗣■谩差对生产的影响测量的目的在于保证产品质量,然而,任何测量总不免存在误差,在验收产品时,如果根据测得尺寸是否超出极限尺寸来判断其合格性,即以极限尺寸作为验收极限,就会把部分超出极限尺寸的废品误判为合格品而验收,造成.误收",把接近于公差界限的合格品判为废品,造成"误废".例如I用测量极限误差Alin=±4m^的一级千分尺测量4,20h6(一O1R)轴径●…时,工件的上下偏差分别为0和一13m.当被测工件的实际偏差在O至+4Jam之间时, 若千分尺的实际测量误差为+4Jam,则测得值将小于工件的上偏差0,这样就导致了将废品判为合格品,造成误收.当被测工件的实际偏差在一4至OlXm之间时,若千分尺的实际测量误差为一41Xm,则测得值将大于工-4O?件的上偏差0,这样就导致了将合格品判为废品,造成误废.?因此,由于测量中不可避免地存在测量误差,当按设计图纸上所规定的公差来验收产品时,总不免产生误收或误废现象,从而降低了产品质量,影响了工件的使用性能和生产的经济性很显然,检验工件尺寸时,量具的测量误差越小,这种影响也就越小,然而,选择高精度的测量器具和测量方法,不但台增大测量费用,而且在很多场合是难以实现的.所以,我们就必须首先确定检验原则,进而规定选择计量器具和确定验收极限的方法.=,拾嘧原卿GB3177--82是GB1800~18O4~79贯彻执行的技术保证,是测量与检验制中的一项重要内容.本标准的基本原则是;"所有验收方法应只接收位于规定尺寸极限之内的工件."这一基本原则是在1SO组织得到确认的.这一基本原则告诉我们:1.无论是在车间或计量室的条件下,无论采用何种计量器具和测量方法进行检验, 来确定工件合格与否,只要满足这一原则,都是可行的验收方法.也就是说,所有可行的验收方法,都只能接收位于规定尺寸极限之内的工件2.所谓"规定的尺寸极限",对有配合要求的工件,工件的作用尺寸不应超出最大实体尺寸}对无配合要求的工件,工件的实际尺寸不得超出极限尺寸.3.遵守这一基本原则,保证了产品质量和互换性,使工件的真实尺寸尽可能不超出最大极限尺寸和最小极限尺寸,遵守《公差与配台》(GB18OO~18O4—79)所规定的工件尺寸界限.因此,遵守遗一基本原则是非常重要的,这一基本原则也是GB317—-82制订的出发点.三,验收极限既然刊量误差必然影响检验结果,当检验目的在于按工件的极限尺寸划分合格品与{最小件卜一峨扭一峻啦搬豫最,譬{废品时,则工件实际尺寸处于极限尺寸附近,由于测量误差的作用,必然存在误收与误睦的危险.那么为了尽可能地保证工件尺寸不超越最大实体边界和最小实体边界,只接收位于规定尺寸极限之内的工件,GB3177—82规定按验收极限验收工件.验收极限是从规定的最大实体尺寸和晟小实体尺寸分别向工件公差带内移动一个安全裕度A来确定. 如图1所示.验收极限是对工件进行验收检验的界限,为一规定的尺寸.我们把这一确定验收极限的方案,称为内缩方案.I识限曲置内缩后的验收极限,是指最后工序加工合格的工件的验收极限.安全裕度A直接关系产品的质量和生产的经济性.A值较大,易于保证工件的l配合质量,也可选择低精度量具,但是占用了较多的工件公差,加工经挤性变差,A值较小, 则要选更精确的量具,工件的加工公差相应增大,生产的经济性也较好.因此,验收极限的确定,必须从技术和经济方面进行综合分析,以达到技术经济指标最佳的目的.GB3177--82的表格给出了公差值大于0.009至3.2ram的有配合要求的光滑工件尺寸的安全裕度A值.如表1所示.从表1看出,安全裕度A值的确定只与-器★悻只寸一上驻啦档啦ll5c酸陧最档传对工件公差有关.安全裕度A值实际上是由两部分组成的,一是计量器具内在误差引起的不确定度U,二是由测量条件,工件形状误差等【起的U:,且1.O0A√u}+u≈√(0.9A).+(0.45A)安全裕度A大体占工件公差的5~1O%由于验收极限是从工件尺寸公差双向分别内缩一个A值,这样内缩量约占工件公差的10~20,与目前工厂实际生产情况相比较,一般来说,对计量器具的选择要求是提高了.41裹1安全裕度及计量署具不确定度允许值(mm) 工件公差安全褡度爿量器具不确定度允许值大于j至Auo.oogO.0】8O.ooi0.(}009o.Oi8o.O32O.0020.OO18o.O32o.0580.0030.00270.0580.1OO0.0060.005{0.1O0O.1800.Ol00.C'050.180O.32O0.0180.O16O.3200.5800.0320.0290.580】.000..0600.0541.000】.8000.1000.0901.8003.2000.1800.160四,计量嚣具的选择GB3177—82采用不确定度来描述计量器具和测量方法的各项误差.不确定度是用来表征测量结果分散特征的误差限,用来描述尚未确定的误差特征.计量器具不确定度就是用来表征计量器具内在误差影响测量结果分散程度的一个误差限.测量不确定度,是用以表征测量过程中各项误差综合影响测量结果分散程度的一个误差限,包括计量器具不确定度,测量条件,人员条件等引起的不确定度.按GB3l77—82的规定,测量一个具体工件所采用的计量器具将根据计量器具的不确定度u来选择,u包含各单个调整标准器的不确定度(例如调整比较仪的鼍块),且应使所选用的计量器具的不确定度等于或小于表中规定的U-值(约为0.9A).有关计量器具不确定度的数值,GB3177—82采用补充文件的形式给jb,定名为,B/zl81—82《G133177—82光滑工件尺寸的检验使用指南》.该文件推荐了普通计量器具不确定度的数值.如表2所示.其所以采用补充文件的形式给出,主要是考虑到这些数值还不够成熟,还有待完善修订.从对标准所提出的选择计量器具原则的分析,及对实际使用的验证,我们可知,按照GB3177--82规定的原则选用最具,量具的可测精度降低了1~2个精度等级.例如-级千分尺,按传统量具选择原则可测IT8的工件尺寸,而按GB3177--82,却只能测IT10级的工件尺寸(局部范围,可测lT9 级).对计量器具选择要求的提高,既有利于保证产品质量,也有利于促进国内计量技术和计量器具的不断发展和提高.五,应用举倒例1,工件250h12(一.460)确定t(1)安全裕度该工件的公差0.460mm是在GB3177~82表中(表1)规定的>O.320~0.580ram的工件公差范围内,由表查得:安全裕度A=0.032mm计量器具不确定度允许值Ul=0.029ram(2)计量器具襄2千分尺和游标卡尺的不■定度(mm) 计量器具类型亟巫生!不确定度050o.o04501ooo.005o.0080.05o1oo15oo.oo6o.02o1502ooo.0072oo250O.0080.0l32503ooo.o093oo3.50o.OlO3504ooo.0llo.02oo.1oo40o4500.01245050oo.o13o.0255006oo60o700o.03o7001oooo.15oO工件尺寸250mm:~表2规定的>200~250nun的工件尺寸范围内,由表2查知,分度值0.02ram游标卡尺的不确定度为0.02ram,小于上述计量器具不确定度允许值U.=O.029ram,可满足使用要求.(3)验收极限如图2^:D.c{2圈2上验收极限:撮大实体尺寸一A:250—0.032=249.968mm下验收极限=最小实体尺寸+A=最大实体尺寸一工件公差+A=250—0.460+0.032=249.572mm结论t使用分度值0.02的游标卡尺,测量工件尺寸250h12,测得尺寸位于249.572~249.968mm之间的是台格品,可以验收. 例2,工件140H10('¨.)根据工件公差T.=0.160re.m,由表1查得A:O.010ramUI=0.009ram则上验收极限刮Dm?一A:140+0.160—0.010:140.150ram'43?介绍机标《抽芯铆钉》宝鸡工程机械厂沈宣明JB4224--86《封闭型沉头抽芯铆钉,JB4225--86《抽芯铆钉技术条件》,JB4226--86《封闭型崩圆头抽芯铆钉》都标准已经实施.抽芯铆钉是一种先进的紧固件它不但可代替普通铆钉,而且在振动大的产品上可以代替自攻螺钉.我厂在轨道车,电气化架线车,电气化隧道凿孔车上均已贯彻采用, 取得了较好的效果.该铆钉是采用单面铆接的一种紧固件,它具有设计新颖,安全可靠, 铆接时嗓音小,劳动强度低,铆接效率高,使用方便等优点.JB4225规定t抽芯铆钉是采,H锅台金和碳素钢两种材料复台而成,即铆钉体采用防锈铝台金,易于变形,其外形与普通铆钉基本相似,杆芯则推荐采用碳素结构钢,铆接后外形美观.铆接时,将钉芯拉断即可铆接牢固;它的基本原理是.杆芯在其铆接工具一拉铆枪的作用下,使杆芯在铆钉体中产生轴向位下验收极限=Dmt.+A=t400.OlO=140.010mm4移.迫使铆钉体膨胀变形(变粗),其变形量大于铆钉休杆径的2O,正是}h于它的变形,即起到了铆接的作用.抽芯铆钉与普通铆钉相比,其最大的优点是单向铆接,解决了用普通铆钉所不能解决的问题.在工作空间狭小,很难进行操作的情况下,而甩抽芯铆钉则只需将铆钉插入预制孔中,用拉铆枪一拉,瞬间便把轩芯拉断以达到良好的铆接效果.有些薄板件联接用自攻螺钉的地方,由于经常振动自攻螺钉经常发生松脱,影响产质量,也可改用抽芯铆钉代替自攻螺钉,这样取得显着效果.我厂产品的车体内外蒙皮固定,车体内部压条装饰件的固定,司机台及发动机罩等部件h都逐步用拉铆代替自攻螺钉.抽芯铆钉非常广泛地应用在机械产品中,它不但甫用于共汽车等车辆的车身.船上的密判仓,还可用于各种要求防渗漏的场台,如用在各类容器中,联接件较厚的场台也可使用,自,988年起还列入了国家标准的镪定计划.如图3又根据表2可知.分度值Q..01mm的内径千分尺的不确定度(0.008mm)小于U:0.009mm,可以满足使用要求.即.140H10的工作尺寸可以使用分度值为0.01mm的内径千分尺测量,测得尺寸位于14O.O10~140.150m~之间的为台格品. GB3177—82所提出的计量器具的选择和验收极限的确定整套理论和方法是与我们所使用的传统力法是截然不同的,更具有科学性.GB3177—82的实施,不但会保证产品的质量,提高经济效益,而且会对贯彻全面质量管理,改善工艺过程起到推动作用,因而大力宣传贯彻这一标准就显得卜分必要和迫切了.r..●●~o峙+ll。
验收极限与计量器具的选择原则.
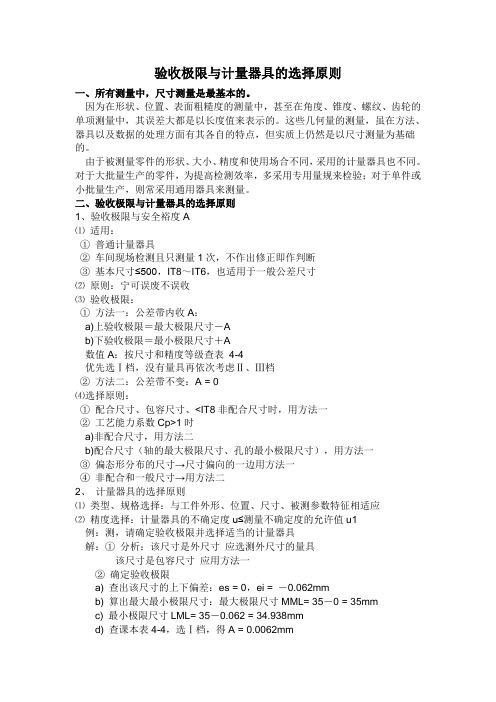
验收极限与计量器具的选择原则一、所有测量中,尺寸测量是最基本的。
因为在形状、位置、表面粗糙度的测量中,甚至在角度、锥度、螺纹、齿轮的单项测量中,其误差大都是以长度值来表示的。
这些几何量的测量,虽在方法、器具以及数据的处理方面有其各自的特点,但实质上仍然是以尺寸测量为基础的。
由于被测量零件的形状、大小、精度和使用场合不同,采用的计量器具也不同。
对于大批量生产的零件,为提高检测效率,多采用专用量规来检验;对于单件或小批量生产,则常采用通用器具来测量。
二、验收极限与计量器具的选择原则1、验收极限与安全裕度A⑴适用:①普通计量器具②车间现场检测且只测量1次,不作出修正即作判断③基本尺寸≤500,IT8~IT6,也适用于一般公差尺寸⑵原则:宁可误废不误收⑶验收极限:①方法一:公差带内收A:a)上验收极限=最大极限尺寸-Ab)下验收极限=最小极限尺寸+A数值A:按尺寸和精度等级查表4-4优先选Ⅰ档,没有量具再依次考虑Ⅱ、Ⅲ档②方法二:公差带不变:A = 0⑷选择原则:①配合尺寸、包容尺寸、<IT8非配合尺寸时,用方法一②工艺能力系数Cp>1时a)非配合尺寸,用方法二b)配合尺寸(轴的最大极限尺寸、孔的最小极限尺寸),用方法一③偏态形分布的尺寸→尺寸偏向的一边用方法一④非配合和一般尺寸→用方法二2、计量器具的选择原则⑴类型、规格选择:与工件外形、位置、尺寸、被测参数特征相适应⑵精度选择:计量器具的不确定度u≤测量不确定度的允许值u1例:测,请确定验收极限并选择适当的计量器具解:①分析:该尺寸是外尺寸应选测外尺寸的量具该尺寸是包容尺寸应用方法一②确定验收极限a) 查出该尺寸的上下偏差:es = 0,ei = -0.062mmb) 算出最大最小极限尺寸:最大极限尺寸MML= 35-0 = 35mmc) 最小极限尺寸LML= 35-0.062 = 34.938mmd) 查课本表4-4,选Ⅰ档,得A = 0.0062mmf) 算验收极限:上验收极限= 35-0.0062 = 34.994mmg) 下验收极限= 34.938 + 0.0062 = 34.944mm⑶选择量具①查课本表4-4(p143),选Ⅰ档,得u 1 = 5.6μm = 0.0056mm②查课本表4-5(p144),得分度值为0.01的外径千分尺的不确定度u =0.004mm③比较:u < u1 ,所以该量具可用。
- 1、下载文档前请自行甄别文档内容的完整性,平台不提供额外的编辑、内容补充、找答案等附加服务。
- 2、"仅部分预览"的文档,不可在线预览部分如存在完整性等问题,可反馈申请退款(可完整预览的文档不适用该条件!)。
- 3、如文档侵犯您的权益,请联系客服反馈,我们会尽快为您处理(人工客服工作时间:9:00-18:30)。
选择机加工件测量器具的基本原则探讨
作者:黄毅
来源:《科技风》2020年第25期
摘要:随着社会的发展和进步,机械加工与生产在社会经济发展过程当中占据的影响越来越大,并且得益于社会工业发展,社会各行业的生产和发展需求才得以满足。
从机械加工方面进行分析,对于一个零部件的加工和生产过程而言,其质量最为关键,而如何保障生产和加工的质量,就需要使用相关的测量器具做好测量与生产规格的控制,以此使得加工生产能够更加规范、更加合理、更加高效,最终提高企业的生产经济效益。
所以本文基于此,对选择机加工件测量器具的基本原则进行探讨。
整体首先从测量器具选择注意事项入手,进而阐述和分析测量器具使用的注意事项,最后则是提出选择机加工件测量器具的基本原则。
关键词:工业生产;测量器具;选择原则
一、选择机加工件测量器具的基本原则
(一)零件大小、表面质量与材料性质
对于所选择的测量器具,需要首先保证其测量范围大于零件的大小,以此才能够对零件进行有效地测量。
与此同时,不同零件的表面质量和材料特性也不一,因此在选择测量器具的过程当中,更要实际考虑材料表面的质量好坏,若是表面质量较好的零件,则要选择使用高精度测量器具,若是表面质量略差,则规避使用精度较高的测量器具。
并且材料本身性质也会表现出软硬不一的特性,根据实际软硬程度选择测量力度大小的测量器具,以此做到即完成测量,也保障零件质量不被破坏。
(二)零件加工工艺规范和生产批量
实际测量器具的选择当中,也需要根据实际零件的加工工艺规范和生产批量多少进行决定。
若是批量生产的零部件,在没有规定特殊加工工艺与测量要求时,则可以选择公用的测量器具完成测量,若是存在特殊加工工艺要求以及測量需求的零件,则要选择与之相对应的测量器具完成测量,以此保障测量效果。
例如,小批量生产L=80mm的零件采用的是150mm规格的游标卡尺,但是要想大规模生产,则需要专用的检验夹具和量规,来提升测量的效率和精准度。
另外,不同重量和零件结构的工件也需要采用不同的测量方法,对一些小型轻便的零部件采用测长机校对即可,但是重量大、工件复杂的零件则需要使用水平仪测量。
(三)明确测量器具本身存在的误差
对于生产的零件进行的测量工作,在选择相应测量器具的过程当中,必要认真考虑和明确每一种测量器具本身所存在的误差,从而在提前了解的基础上做好选择,避免由于对误差信息的不明确而影响最终的测量精度。
不同加工需求和使用规范的零部件有不同的误差标准,这和工件的生产规模、精细程度有关,一些生产规模小、精密性不高的零部件,生产造成的误差肯定会大,但是大规模生产和测量器具误差小的工件,其生产误差就小,生产人员需要根据自身生产需要,将误差控制在合理的范围内,采用量具误差在生产允许范围内的量具也是很重要的。
(四)测量器具的量程
具体而言,测量器具分为工作量程和有效量程,从而所选择的测量器具是否能够满足所测量零件的需求就需要进行认真分析,确保其测量的工作量程和有效量程均满足零件的测量需求,以此才能够有效完成测量工作。
一切工件生产都要建立在准确、规范的基础上,如果出现测量器具量程不够的问题也要及时解决,避免量程对生产工件自身的准确性产生影响。
二、测量器具使用注意事项
(一)使用安全方面与测量前的零件清理
在机床上对相关加工零件进行测量的过程当中,必须保障机床和所加工零件完全停稳再进行测量,这样做的目的有二,一是为了确保测量工作的安全与稳定,避免因为测量工具不稳对实际的工作产生的负面影响,如果放置不稳,可能造成测量的不准确,或者因为放置不稳对测量人员的人身安全造成负面影响;二是为了减少运动件对测量器具产生的磨损,以此降低其测量的精度。
所以使用安全方面的问题需要进行重视。
在对有关零件进行测量之前,需要对零件待测表面和测量器具表面进行有效清理,将表面存在的杂物清理干净,避免由于存在细微杂物影响测量的精确度,尤其对于一些高精度测量器具和需要进行高精度测量的零件而言,更需要重视做好测量前的清理工作。
(二)测量器具的存放与专具专用
关于测量器具的使用与存放,具体应该将测量器具放置在专门的器具盒当中。
规避与其他刀具和设备一同放置。
诸如与锉刀、车刀、榔头等,以此防止这类工具对测量器具造成碰撞损伤,进而影响测量精度。
与此同时,也要规避放置在机床等运动机械之上,以此规避由于运动机械振动造成测量器具跌落,从而影响测量的精度。
另外对于机械加工和生产当中常见的游标卡尺、百分尺以及直尺等,要做到专具专用,切记使用专业测量器具挪作他用,诸如使用直尺划线、转螺钉等。
与此同时,专业测量工具在使用的过程当中也更要注意使用规范,切忌进行随意测量和随意使用。
为了避免生产过程中测量器具发生损坏,应当对所有的器具进行妥善管理,在使用之前应当对测量器具进行鉴定,保证器具安全稳定方可使用,不符合使用规范的器具严格不得使用。
有下列情况时,计量器具视为不合格:(1)器具表面明显损坏的;(2)之前有过过载或误操作的器具;(3)异常显示的器具;(4)功能可疑但不能排查问题的器具;(5)超过周检规定时间间隔的器具;(6)仪器密封的完整性被破坏的。
有上述不符合项的测量仪器和工具必须停止使用,分开存放,并做好标记。
(三)测量器具使用环境
部分测量器具对于使用环境有着较高的要求,尤其高精度的测量器具对于使用环境的要求更加严苛,诸如使用环境温度、使用环境是否存在较大的磁场等,都可能会对测量器具产生测量精度方面的影响。
从而实际使用过程当中就需要认真考虑使用环境的温度因素、磁场因素等。
三、测量器具选择一般方式与提高精度的主要措施
(一)测量器具选择一般方式
首先,需要对测量器具的外观进行观察,诸如制造许可是否存在,这是检验测量器具是否正规厂家生产的有效方法。
例如津制第00000456号,前四位数字属于制造商的地区代码,后面四位数字则是许可证的顺序号,“津”表示的是发证代号,即省、自治区、直辖市的简称。
若是测量器具当中并未明确或者清晰标明,则设备可能属于假冒伪劣。
其次,要对测量器具进行测量精度以及使用质量的检测,诸如要进行表面毛刺、锈蚀的检查,以及进行活动件松紧度的检查,若是正规厂家生产的测量器具,则表面毛刺处理较干净,相应的松紧度也适宜。
最后,也要观察和分析测量器具在质量检测时是否运转平滑,若是存在较大噪声和间隙过大,则质量不可靠。
再者,与其他已有测量精度可靠的测量器具进行对比实验,若是两者在相同测量条件下所测的结果一致,则可以判定该测量器具测量精度合格,若是出现较大的偏差,则要考虑是否存在质量问题或是精度调节不合理。
(二)提高测量器具精度的主要措施
1.提升操作人员的技能水平
对于实际进行的零部件加工和测量工作而言,重要的生产质量和测量工作效果体现,很大程度上会受到主要测量操作人员的影响,以此对于测量工作的展开,需要相关操作人员提升自身的技能水平和工作能力,以及对于测量器具的熟悉程度与使用熟练度。
从而企业有责任针对
测量器具的操作和使用人员进行专业的培训与教育,使之能够在基础工作能力和工作水平方面获得提升,进而保障测量工作的有效进行,也确保测量器具的使用安全与使用规范。
2.遵守测量工作的流程规范与基本要求
主要的测量人员应该使用同样的方式进行相关测量工件的装载,并且对于所进行的测量流程也应保持规范化、标准化,确保所测量的每个零件都基于相同流程。
并且对于一些测量精度要求较高的零件,也更要保障加紧力度与角度的规范性、合理性,以此确保整体测量的效果。
3.做好测量器具的检验与校准
由于机械加工与生产零件的产量一般较多,因此在面对批量生产抽样检测的过程当中,测量器具的使用较为频繁,久而久之会降低测量的精度,从而测量精度降低必然会影响到测量的效果,也更会影响到企业的稳定生产,以此对于相关测量器具必要做好检验与校准,并定期做好维护工作,以此减少测量器具发生测量精度失准的情况发生。
4.建立仪器使用台账
应建立仪器的总账户、使用账目和检定台账,计量组还应建立相应的测量仪器使用子账户。
测量仪器档案原件由项目技术部门保存,复印件由测量组和组长保存。
副本应与仪器一起包装。
仪器的使用者应负责仪器在使用期间的保管和维护,并应防止测量仪器的受潮和丢失。
使用完毕后,测量仪器应交由相关部门专人保管并登记归还。
未经许可,不得被他人使用或者擅自外借。
四、結语
尽管工业加工与生产以及相关工件测量,国家与相关部门都有规范与标准提出,并且企业在实际生产和测量的过程当中也会按照规范和标准进行生产与测量,但根本上影响机加工件测量器具测量精度的因素也在于是否对测量器具进行了合理选择,从而基于企业生产、加工和加工件测量需求,必要按照选择机加工件测量器具的基本原则进行测量器具的选择,并做好使用过程当中的质量检验与提高测量精度,以此推动企业稳定生产和发展。
参考文献:
[1]吉海标,刘志宏,吴杰峰,马建国,范小松,顾永奇.CFETR 1/32真空室机加工件的激光测量研究[J].核聚变与等离子体物理,2019,39(04):338-342.
[2]莫爵贤,王宇,吴智恒,童季刚.一种基于机器视觉的机加工件尺寸测量系统设计[J].机电技术,2018(03):25-27.
[3]叶宗茂.汽车行业几种机加工件支承率的含义及其测量[J].现代零部件,2004(09):70-72.
[4]叶宗茂.三坐标测量机在汽车机加工件检测中的实践[J].现代零部件,2004(05):
46+48+50.
作者简介:黄毅(1983—),男,汉族,福建漳州长泰人,本科,质量工程师,研究方向:机械工程。