棒材轧后控冷工艺微机控制系统软件的设计
棒材轧制中控制轧制和控制冷却的应用

棒材轧制中控制轧制和控制冷却的应用姓名:迟璐全班级:学号:棒材轧制中控制轧制和控制冷却的应用迟璐全材料成型及控制工程12级[摘要]控制轧制(Contorlled Rollign)是在热轧过程中通过对金属加热制度、变形制度和温度制度的合理控制,使热朔性变形与固态相变结合,以获得细小晶粒组织,使钢材具有优异的综合力学性能的轧制新工艺。
控制冷却(controlled Cooling)是控制轧后钢材的冷却速度达到改善钢材组织和性能的目的。
控制轧制和控制冷却相结合能将热轧钢材的两种强化效果相加,进一步提高钢材的强韧性和获得合理的综合力学性能。
并介绍了棒材轧制过程中控制轧制和控制冷却工艺的特点,金属学理论。
分析了控制轧制和控制冷却工艺对热轧棒材的影响,并提出目前需要研究的问题。
[关键词]热轧棒材控制轧制控制冷却ABSTRACT:Controlled rolling is in the process of hot rolled through the metal heating system, reasonable control of the deformation and temperature, and to integrate the thermal plastic deformation and solid-state phase transformation to obtain fine grain structure, make the excellent comprehensive mechanical properties of steel rolling process. Is controlled cooling after controlled rolling steel cooling speed to achieve the purpose of improving the microstructure and mechanical properties of steel. Controlled rolling and controlled cooling could add those two kinds of reinforcement effect of hot rolling steel, further improve the tenacity of steel and have a reasonable comprehensive,mechanical,properties.Anintroductionwasmadetothefeaturesandmetallo graphicaltheoryofrollingcontrolandcoolingcontrolprocessesduringbarrolling.Theeffects oftherollingcontrolandcoolingcontrolprocessesonthehotrolledbarswereanalyzed.Proble mstoberesearchedatpresentwerealsoputforward.KEY WORDS: hotrolledbars rollingcontrol coolingcontrol1.引言控制轧制和控制冷却技术是近十多年来国内外新发展起来的轧钢生产新技术,受到国际冶金界的重视。
棒材生产线自动控制系统改造设计与实现
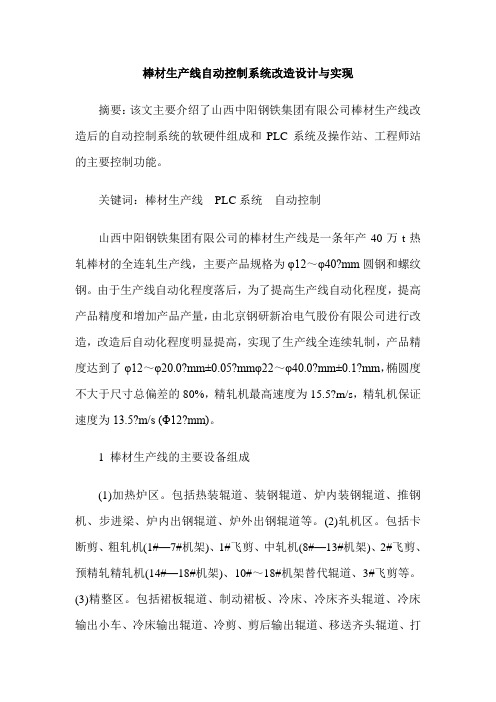
棒材生产线自动控制系统改造设计与实现摘要:该文主要介绍了山西中阳钢铁集团有限公司棒材生产线改造后的自动控制系统的软硬件组成和PLC系统及操作站、工程师站的主要控制功能。
关键词:棒材生产线PLC系统自动控制山西中阳钢铁集团有限公司的棒材生产线是一条年产40万t热轧棒材的全连轧生产线,主要产品规格为φ12~φ40?mm圆钢和螺纹钢。
由于生产线自动化程度落后,为了提高生产线自动化程度,提高产品精度和增加产品产量,由北京钢研新冶电气股份有限公司进行改造,改造后自动化程度明显提高,实现了生产线全连续轧制,产品精度达到了φ12~φ20.0?mm±0.05?mmφ22~φ40.0?mm±0.1?mm,椭圆度不大于尺寸总偏差的80%,精轧机最高速度为15.5?m/s,精轧机保证速度为13.5?m/s (Φ12?mm)。
1 棒材生产线的主要设备组成(1)加热炉区。
包括热装辊道、装钢辊道、炉内装钢辊道、推钢机、步进梁、炉内出钢辊道、炉外出钢辊道等。
(2)轧机区。
包括卡断剪、粗轧机(1#—7#机架)、1#飞剪、中轧机(8#—13#机架)、2#飞剪、预精轧精轧机(14#—18#机架)、10#~18#机架替代辊道、3#飞剪等。
(3)精整区。
包括裙板辊道、制动裙板、冷床、冷床齐头辊道、冷床输出小车、冷床输出辊道、冷剪、剪后输出辊道、移送齐头辊道、打包辊道、打包机、成捆器等。
2 轧线自动控制系统在本系统中通讯网络配置主要是由工业以太网(INDUSTRIAL ETHERNET)和Profibus-DP网,组成两层通讯网络系统。
系统配置如图1所示。
工业以太网(INDUSTRIAL ETHERNET)主要是完成操作站同PLC设备和工厂管理机的数据、信息通讯功能;留有同上级工厂管理机之间的工业以太网通讯接口;操作站、工程师站、PLC之间的工业以太网通讯速率100Mbit/s;工业以太网通讯介质采用工业用光纤;Profibus-DP网主要是完成PLC设备同传动设备和远程I/O装置之间的数据、信息通讯功能。
PLC控制系统轧钢棒材生产冷床顺序控制

PLC控制系统轧钢棒材生产冷床顺序控制引言PLC(可编程逻辑控制器)是一种常见的工业控制设备,常用于自动化生产线中的各种控制系统中。
在钢铁行业中,PLC控制系统被广泛应用于轧钢棒材的生产过程中,其中包括冷床顺序控制。
本文将对PLC控制系统在轧钢棒材生产冷床顺序控制中的应用进行详细介绍。
轧钢棒材生产冷床顺序控制的背景在钢铁行业的生产过程中,轧钢棒材是一个重要的环节。
冷床作为一个必要的设备,在轧钢棒材的生产过程中起到重要的作用。
冷床的主要功能是对刚出轧机的钢棒材料进行冷却,以达到理想的温度和质量要求。
冷床顺序控制是保证轧钢棒材生产过程中连续、高效运行的关键。
在传统的生产方式中,人工操作容易出现疏忽和失误,导致生产效率下降和质量受损。
而PLC 控制系统的应用能够实现对冷床顺序控制的自动化,提高生产效率和产品质量。
PLC控制系统在冷床顺序控制中的应用PLC控制系统在轧钢棒材生产冷床顺序控制中起到了至关重要的作用。
它能够自动化地控制冷床的运行顺序,并确保每个环节的正确操作和协调。
1.温度控制:PLC控制系统可以实时监测钢棒材料的温度,并根据设定的参数对冷床的冷却水进行调节。
通过精确的温度控制,可以保证钢棒材料的质量和硬度,提高产品的刚度和强度。
2.停车和启动控制:PLC控制系统可以精确地控制冷床的停车和启动时间,以及各个电机的运行状态。
通过对冷床的停车和启动进行有效控制,可以避免过度冷却和能源浪费,同时保护设备和延长使用寿命。
3.物料传送和排放控制:PLC控制系统可以自动控制物料的传送和排放过程。
通过设定合适的装载和卸载速度,并结合传感器的反馈信号,PLC可以实现对物料的准确和稳定的控制,从而提高整个生产过程的效率和质量。
4.故障监测和报警功能:PLC控制系统可以监测冷床运行过程中的各种故障,如电机故障、传感器故障等。
一旦发现故障,PLC会及时发出报警信号,并采取相应的措施,以确保生产的连续性和安全性。
PLC控制系统在轧钢棒材生产中的优势PLC控制系统在轧钢棒材生产冷床顺序控制中具有以下优势:1.高度可靠性:PLC控制系统经过严格测试和验证,具有较高的稳定性和可靠性。
圆钢控冷系统计算机软件的设计与实现

脚
图 1 小 断 面 圆 钢控 冷 工 艺 示意 图
图 中 :了1 2 精 轧 机凡 E 、 口 ( 却 器 入 口 )实删 轧 件 温 度 1, : l 出 挣 3 冷 床 ^ 口实捌 轧件 自日 火 温 度 : 卯 ~ Q :四 个分 水管 实 测 水 流 量 4 JMDI M D S : 精 轧 机 A l 出 E ( 却 器 凡 - I .H 2 W E, l 冷 1 E) 和 冷 床 入 E轧 件位 置 检 测 信 号 l
中圈分类号 : P 1 T 31
文献标 识码 : B
圆钢控冷 系统计算 机软件的设计与实现
杜 天苍 , 刘 华
( 京 石油 化 工 学 院 ,北 京 北 120) 0 60
摘要 :文章 介绍了圆钢 轧后 控冷工艺微 机系境控制软件 的设计方洼 。主要 内容包括 :冷却工艺原理 简进、工艺过程 控制分段 、控制要点和对控制软件 的要求 、软件构成和功能 及软件调试和运行 隋况等 。给 出了各个功能模块之间的数
节 约 能源 ,降低 材料 消耗 。 种工艺 是根据 产 品钢 种 、 这 规格 、 目标 自回火温 度 、实测 开 始冷 却温度 和进 水温 度. 计算 并设 定所 需冷却 水量 ,4' 圆钢 进行快 速冷 X ̄后 L
水温 等 因数有关 。从 内部组织 变化 上该 工 艺包括 3 个 阶段 :
却. 以达 到规 定的 自回火 温度 , 而提 高产 品的性 能 质 从 量 。整个 生 产过 程 中还 存 在一 些 环境 、 性 等 变 化 因 特
数, 因而 , 不 断 进 行 自学 习修 正 数 学 模 型 的 一 些 参 需
数 , 系统工 作在 最佳 状态 工艺 的微机 控制 系统 已 使 该 在某 钢铁 ( 团) 司取得 了成功 , 济效益 显著 。 文 集 公 经 本 主要介 绍这 一工 艺微机 系统 中控制 软件 的设 计方法 。
棒材生产线冷床自动控制系统的设计与实现
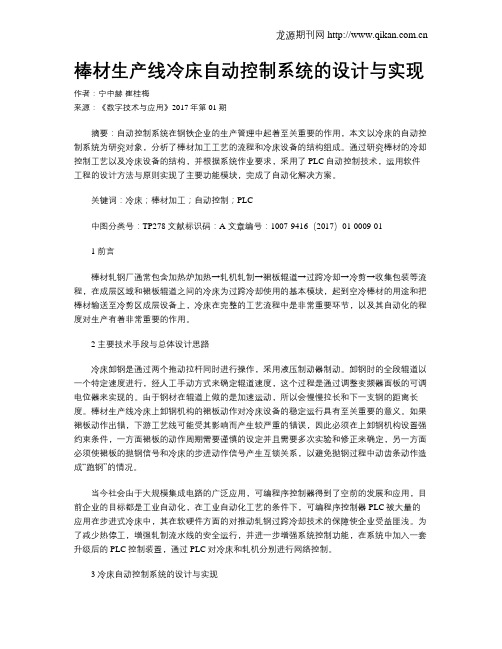
棒材生产线冷床自动控制系统的设计与实现作者:宁中赫崔桂梅来源:《数字技术与应用》2017年第01期摘要:自动控制系统在钢铁企业的生产管理中起着至关重要的作用,本文以冷床的自动控制系统为研究对象,分析了棒材加工工艺的流程和冷床设备的结构组成。
通过研究棒材的冷却控制工艺以及冷床设备的结构,并根据系统作业要求,采用了PLC自动控制技术,运用软件工程的设计方法与原则实现了主要功能模块,完成了自动化解决方案。
关键词:冷床;棒材加工;自动控制;PLC中图分类号:TP278 文献标识码:A 文章编号:1007-9416(2017)01-0009-011 前言棒材轧钢厂通常包含加热炉加热→轧机轧制→裙板辊道→过跨冷却→冷剪→收集包装等流程,在成层区域和裙板辊道之间的冷床为过跨冷却使用的基本模块,起到空冷棒材的用途和把棒材输送至冷剪区成层设备上,冷床在完整的工艺流程中是非常重要环节,以及其自动化的程度对生产有着非常重要的作用。
2 主要技术手段与总体设计思路冷床卸钢是通过两个拖动拉杆同时进行操作,采用液压制动器制动。
卸钢时的全段辊道以一个特定速度进行,经人工手动方式来确定辊道速度,这个过程是通过调整变频器面板的可调电位器来实现的。
由于钢材在辊道上做的是加速运动,所以会慢慢拉长和下一支钢的距离长度。
棒材生产线冷床上卸钢机构的裙板动作对冷床设备的稳定运行具有至关重要的意义。
如果裙板动作出错,下游工艺线可能受其影响而产生较严重的错误,因此必须在上卸钢机构设置强约束条件,一方面裙板的动作周期需要谨慎的设定并且需要多次实验和修正来确定,另一方面必须使裙板的抛钢信号和冷床的步进动作信号产生互锁关系,以避免抛钢过程中动齿条动作造成“跑钢”的情况。
当今社会由于大规模集成电路的广泛应用,可编程序控制器得到了空前的发展和应用,目前企业的目标都是工业自动化,在工业自动化工艺的条件下,可编程序控制器PLC被大量的应用在步进式冷床中,其在软硬件方面的对推动轧钢过跨冷却技术的保障使企业受益匪浅。
棒材轧机的自动控制系统

轧钢厂一车间棒材轧机的自动控制系统轧钢厂一车间棒材生产线是由包头钢铁设计研究院设计。
该套年产量60万t的棒材轧机于2003年5月建成投产以后,设备运行基本稳定可靠,单位小时产量已经达到了原设计水平。
1主要工艺设备和系统配置1.1工艺设备概况该套轧机为连续式,由7台∮550mm(3台)/∮450mm (4台)可逆初轧机、1台切头切尾和事故碎断用的切头飞剪、、4台∮380mm中轧机、1台气钢推动的事故卡断剪、6台∮320㎜平立式精轧机(12H、14H、16H三架水平轧机和13V、15V、17V三架立式轧机组成)、6个活套装置、精轧后辊道、1台成品倍尺飞剪、冷床输入辊道(四段)、裙板拔钢装置、步进式冷床及横移装置、冷床输出辊道、冷剪和成品收集等设备组成,该轧机出口速度最高可达15m/s,可生产∮16~50㎜规格的圆钢和螺纹钢。
1.2系统配置根据工艺和生产的要求,在轧制线上配备了2套工控微机(在主操作台)和5套plc装置(在主电PLC室)。
Plc1 主要用于轧机辅助设备控制(如液压站、辊道、风机等);Plc 2主要完成轧制线17台直流电机的速度级联调速控制,6个活套的控制,切头飞剪和冷床的控制;Plc3用于成品倍尺飞剪区域设备的控制(整套引进意大利DANELI公司)、plc4用于精整区所有设备的控制、plc5用于冷剪设备的控制(整套引进意大利DANELI公司)。
2套工控微机各含有1个操作键盘、1台监控器CRT和1台主机。
2套工控微机都设在主操作台站内,其中,1套工控微机用于轧制表的输入和轧制速度等显示。
另1套工控微机用于监控并显示现场设备所处的状态,可记录当前和历史数据,它的CRT显示内容与前1套工控微机的内容基本相同,但是,在主操作室内,各输入参数既可供显示,也能做修改。
2主操作站功能和CRT显示主操作站内的工控微机有一个人机对话监控系统,主要用于输入各种轧制和控制用参数。
轧机监控系统的画面构成和相互调用关系.本监控系统从轧钢的工艺特点和操作要求出发,包括了轧机系统的所有主要工艺流程、检测参数、设备状态的显示,也集中了轧钢系统的监视和控制得到完全的统一。
40Cr钢棒材在线控轧控冷工艺的研发

suteT d t tts nl y s oi l cn ot han pnie t c r o h , t ho g a t l c l otl e i rc lad r u . o h e o i o ay r h tg p n a i c m g e i df m tn e at t pru pnie h m t drg o rlg c s e r ao aw l s e e t e c lo t e l n i htoi p e o i s l e a r r p f a u t - l r s h m i e i s n o ad aerld lg cdr Te tld l g n ldcon p c s n i froe con poeue h cn e- l & ot l - lg e wl t t - l oi r s . o r r i c r e o i r s i o o n o o ed t ip v ad a e p p t s h se t t gn s apci v e l m r e a n t r ei u a tn h o he a pla n iny o n d c h o r s s g , s n i t v e e c r u d o c ai r n- r wrr Ic bn b et s i ee y、 ipfn a bi o o d a ad eo t rg f i an nr s l i p l f b n i-d a i e i n g g y t u n n v mi g y p dcp c s idvoi nw l e T r le rl rlg otu r u r e ad e l n e seg d . a c tl o i ic i e o e s n n ep g t r s o i oo e l n n s o e a e z n d n n br , ay e tit con ui bte e i snsw i m sh e amlnm l i e o a lg s e t rlg d h h t i o l i n t n d n l o i n e n h o n t , s t w l a c u a v eog d t c bte e h dFr e sn cnnebr wrr ml, nuh a e w e a sn. t s eii otus ad eo isi s i n e n t o h x tg i s c a o a n i-d t i d i ltgt llo t t no e ai l n bc s o t lk s c T i c t eaaa e h h n m c n arlg a e h a o p e o f u o vib f e - h c o i e u f c f . e l e a sle p b m t N .R l g i S G ) dvl e i o n tld olg o tts l , O3 l - l G S hs e p t w cn l - on u h re h io e oi M ( n a e o d s o r e c i o ssm b ape it ie eie fi i rlg n Ti yt w s e pd ye t e ld h n r d tad s n o i ti.h ssm dvl e t o p i n tm a n i h g n r e n l a s e a e o r pni tt ca c rts t ma s tn i o rl sc ifii sns e od g h hr ti ctt l e i -z f d k n h g d s n o e aes h h i a e l o se l t n sn t c oe o i a ad t no ehn a r i m iy t l g df m o o t br nn n t h n m cai l n a l cnoi t e ra n h a i o- h e- e c o g n o r l h o t f l n e i e n
《中厚板轧制和轧后冷却过程离线模拟软件的开发》范文
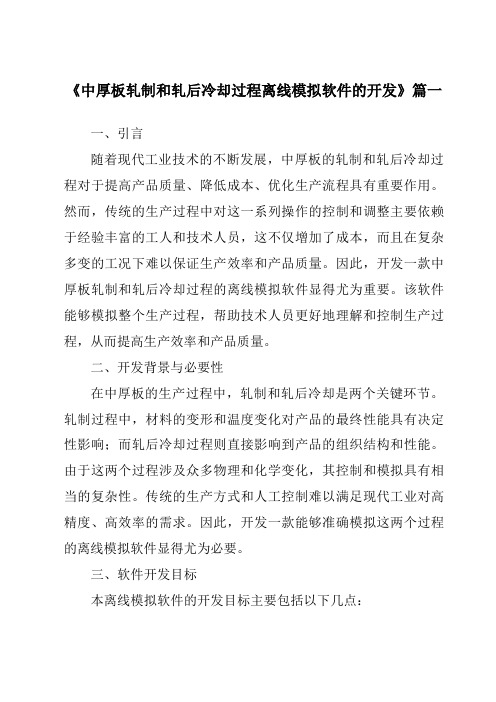
《中厚板轧制和轧后冷却过程离线模拟软件的开发》篇一一、引言随着现代工业技术的不断发展,中厚板的轧制和轧后冷却过程对于提高产品质量、降低成本、优化生产流程具有重要作用。
然而,传统的生产过程中对这一系列操作的控制和调整主要依赖于经验丰富的工人和技术人员,这不仅增加了成本,而且在复杂多变的工况下难以保证生产效率和产品质量。
因此,开发一款中厚板轧制和轧后冷却过程的离线模拟软件显得尤为重要。
该软件能够模拟整个生产过程,帮助技术人员更好地理解和控制生产过程,从而提高生产效率和产品质量。
二、开发背景与必要性在中厚板的生产过程中,轧制和轧后冷却是两个关键环节。
轧制过程中,材料的变形和温度变化对产品的最终性能具有决定性影响;而轧后冷却过程则直接影响到产品的组织结构和性能。
由于这两个过程涉及众多物理和化学变化,其控制和模拟具有相当的复杂性。
传统的生产方式和人工控制难以满足现代工业对高精度、高效率的需求。
因此,开发一款能够准确模拟这两个过程的离线模拟软件显得尤为必要。
三、软件开发目标本离线模拟软件的开发目标主要包括以下几点:1. 准确模拟中厚板轧制和轧后冷却的全过程,包括材料变形、温度变化、组织结构变化等。
2. 提供丰富的参数设置和调整功能,以适应不同材质、不同规格的中厚板生产需求。
3. 具备友好的用户界面,方便技术人员操作和使用。
4. 提供数据分析功能,帮助技术人员更好地理解和控制生产过程。
四、软件开发内容1. 材料模型开发:根据中厚板材料的特点,建立合适的材料模型,包括材料的力学性能、热学性能、组织结构变化等。
2. 轧制过程模拟:基于材料模型,建立轧制过程的数学模型,模拟材料的变形和温度变化。
3. 轧后冷却过程模拟:根据轧制后的材料状态,建立冷却过程的数学模型,模拟材料的组织结构变化和性能变化。
4. 参数设置与调整:提供丰富的参数设置和调整功能,以适应不同材质、不同规格的中厚板生产需求。
5. 用户界面开发:设计友好的用户界面,方便技术人员操作和使用。
《中厚板轧制和轧后冷却过程离线模拟软件的开发》

《中厚板轧制和轧后冷却过程离线模拟软件的开发》篇一一、引言随着现代制造业的快速发展,中厚板的轧制与轧后冷却过程在金属材料加工中占据着举足轻重的地位。
为了优化这一过程,提高生产效率、降低能耗、减少废品率,开发一款针对中厚板轧制和轧后冷却过程的离线模拟软件显得尤为重要。
本文将详细探讨该软件的开发过程、技术要点及其应用价值。
二、项目背景与意义中厚板轧制和轧后冷却是金属材料加工的关键环节,其过程涉及众多物理和化学变化,对产品的性能和质量有着直接影响。
然而,传统的生产过程往往依赖于经验丰富的操作员和技术人员,缺乏科学的模拟和预测手段。
因此,开发一款离线模拟软件,不仅能够提高生产效率和产品质量,还能为工艺优化和成本控制提供科学依据。
三、软件开发目标与技术路线1. 软件开发目标:(1)建立中厚板轧制和轧后冷却过程的数学模型;(2)开发离线模拟软件,实现对生产过程的精确模拟和预测;(3)提供数据分析和优化建议,帮助企业提高生产效率和产品质量。
2. 技术路线:(1)收集中厚板轧制和轧后冷却过程的工艺参数及数据;(2)建立数学模型,包括轧制力计算、温度场模拟、组织性能预测等;(3)采用编程语言(如C++、Python等)开发离线模拟软件;(4)进行软件测试与验证,确保模拟结果的准确性和可靠性;(5)集成数据分析与优化模块,为企业提供决策支持。
四、软件功能与特点1. 功能:(1)建立中厚板轧制和轧后冷却过程的数学模型,实现精确的模拟和预测;(2)提供数据输入、处理、分析和可视化功能;(3)集成优化算法,为企业提供工艺优化建议;(4)支持多种金属材料和中厚板规格的模拟。
2. 特点:(1)高精度:基于先进的数学模型和算法,实现高精度的模拟和预测;(2)易用性:界面友好,操作简便,易于企业技术人员使用;(3)灵活性:支持多种金属材料和中厚板规格的模拟,适应不同企业的需求;(4)可扩展性:预留接口,便于后续功能扩展和升级。
五、软件开发与实施1. 开发环境与工具:选用适合软件开发的语言和工具,如C++编程语言、Python编程语言及相关开发环境。
《中厚板轧制和轧后冷却过程离线模拟软件的开发》
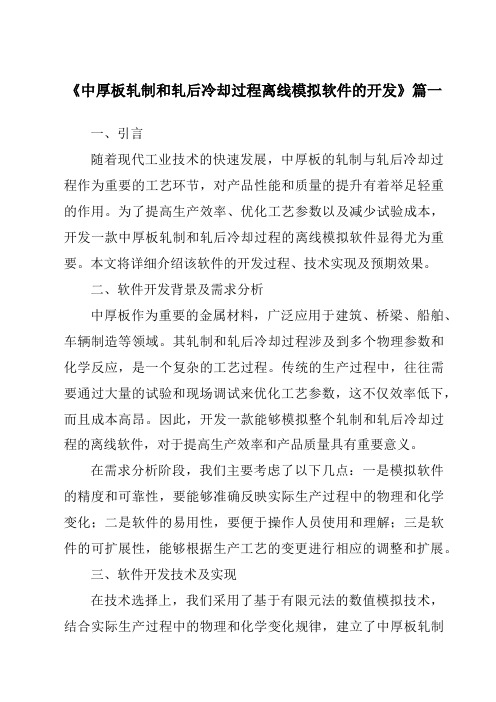
《中厚板轧制和轧后冷却过程离线模拟软件的开发》篇一一、引言随着现代工业技术的快速发展,中厚板的轧制与轧后冷却过程作为重要的工艺环节,对产品性能和质量的提升有着举足轻重的作用。
为了提高生产效率、优化工艺参数以及减少试验成本,开发一款中厚板轧制和轧后冷却过程的离线模拟软件显得尤为重要。
本文将详细介绍该软件的开发过程、技术实现及预期效果。
二、软件开发背景及需求分析中厚板作为重要的金属材料,广泛应用于建筑、桥梁、船舶、车辆制造等领域。
其轧制和轧后冷却过程涉及到多个物理参数和化学反应,是一个复杂的工艺过程。
传统的生产过程中,往往需要通过大量的试验和现场调试来优化工艺参数,这不仅效率低下,而且成本高昂。
因此,开发一款能够模拟整个轧制和轧后冷却过程的离线软件,对于提高生产效率和产品质量具有重要意义。
在需求分析阶段,我们主要考虑了以下几点:一是模拟软件的精度和可靠性,要能够准确反映实际生产过程中的物理和化学变化;二是软件的易用性,要便于操作人员使用和理解;三是软件的可扩展性,能够根据生产工艺的变更进行相应的调整和扩展。
三、软件开发技术及实现在技术选择上,我们采用了基于有限元法的数值模拟技术,结合实际生产过程中的物理和化学变化规律,建立了中厚板轧制和轧后冷却过程的数学模型。
通过编写高效的计算程序,实现了对轧制过程和轧后冷却过程的精确模拟。
在软件实现方面,我们采用了模块化设计思想,将整个软件分为数据输入模块、模拟计算模块、结果输出模块等几个部分。
数据输入模块负责接收用户输入的工艺参数和材料属性等数据;模拟计算模块根据数学模型进行计算,得到轧制和轧后冷却过程中的各种物理参数和化学反应;结果输出模块则将计算结果以图表等形式展示给用户。
四、软件功能及特点该离线模拟软件具有以下功能及特点:1. 高度还原实际生产过程:软件能够准确模拟中厚板的轧制和轧后冷却过程,包括温度场、应力场、组织结构等物理参数的变化。
2. 丰富的工艺参数设置:用户可以根据实际生产需求设置各种工艺参数和材料属性等数据。
《中厚板轧制和轧后冷却过程离线模拟软件的开发》

《中厚板轧制和轧后冷却过程离线模拟软件的开发》篇一中厚板轧制与轧后冷却过程离线模拟软件的开发一、引言在现代化工业生产中,中厚板的轧制与轧后冷却过程是金属材料加工的重要环节。
为了优化生产流程、提高产品质量和降低生产成本,开发一款能够模拟这一过程的高效离线模拟软件显得尤为重要。
本文将详细介绍中厚板轧制和轧后冷却过程离线模拟软件的开发过程,包括其背景、目的、意义以及相关技术与方法。
二、软件开发背景及目的随着工业自动化和计算机技术的发展,离线模拟软件在金属材料加工领域的应用越来越广泛。
中厚板轧制与轧后冷却过程的离线模拟软件的开发,旨在帮助生产厂商更准确地预测和控制轧制与冷却过程中的各种参数,从而提高产品质量、降低生产成本、优化生产流程。
此外,该软件还能为新产品的研发和工艺的改进提供有力支持。
三、软件开发相关技术与方法1. 软件开发技术:本软件采用先进的计算机编程语言和开发工具,如C++、Python等,结合数据库技术和图形界面开发技术,实现离线模拟软件的开发。
2. 轧制过程模拟:通过建立中厚板轧制过程的数学模型,模拟轧制过程中的轧制力、轧制温度、板形变化等关键参数的变化规律,为优化轧制工艺提供依据。
3. 轧后冷却过程模拟:根据中厚板轧后冷却过程的物理特性,建立冷却过程中的传热模型、相变模型等,模拟冷却过程中的温度场、组织变化等关键参数的变化规律。
4. 参数优化与控制:通过离线模拟软件,对轧制与轧后冷却过程中的关键参数进行优化与控制,以实现产品质量的提高和生产成本的降低。
5. 数据库与图形界面:将模拟结果存储在数据库中,并开发友好的图形界面,以便用户直观地查看和分析模拟结果。
四、软件开发流程1. 需求分析:明确软件的功能需求、性能需求和用户需求,为软件开发提供指导。
2. 系统设计:根据需求分析结果,设计软件的整体架构、数据库结构和图形界面等。
3. 编程实现:按照系统设计,使用相关编程语言和开发工具进行编程实现。
《2024年中厚板轧制和轧后冷却过程离线模拟软件的开发》范文
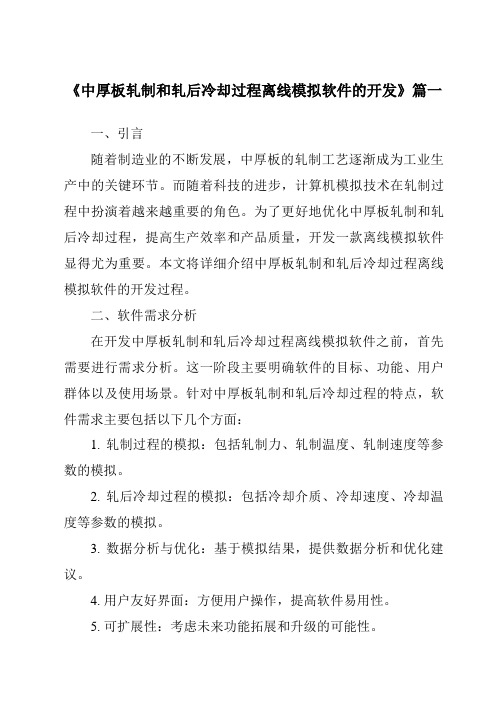
《中厚板轧制和轧后冷却过程离线模拟软件的开发》篇一一、引言随着制造业的不断发展,中厚板的轧制工艺逐渐成为工业生产中的关键环节。
而随着科技的进步,计算机模拟技术在轧制过程中扮演着越来越重要的角色。
为了更好地优化中厚板轧制和轧后冷却过程,提高生产效率和产品质量,开发一款离线模拟软件显得尤为重要。
本文将详细介绍中厚板轧制和轧后冷却过程离线模拟软件的开发过程。
二、软件需求分析在开发中厚板轧制和轧后冷却过程离线模拟软件之前,首先需要进行需求分析。
这一阶段主要明确软件的目标、功能、用户群体以及使用场景。
针对中厚板轧制和轧后冷却过程的特点,软件需求主要包括以下几个方面:1. 轧制过程的模拟:包括轧制力、轧制温度、轧制速度等参数的模拟。
2. 轧后冷却过程的模拟:包括冷却介质、冷却速度、冷却温度等参数的模拟。
3. 数据分析与优化:基于模拟结果,提供数据分析和优化建议。
4. 用户友好界面:方便用户操作,提高软件易用性。
5. 可扩展性:考虑未来功能拓展和升级的可能性。
三、软件开发与设计在需求分析的基础上,开始进行软件的开友好度及高效的运行速度等特点,符合实际生产和研发需求。
1. 数据库设计:建立用于存储轧制和冷却过程中各种参数的数据库,确保数据的安全性和可靠性。
2. 算法设计:针对轧制和冷却过程中的各种参数,设计相应的算法模型,以实现精确的模拟。
3. 界面设计:设计用户友好、操作简便的界面,方便用户进行操作和查看模拟结果。
4. 软件架构:采用模块化设计,便于后期功能拓展和升级。
四、软件功能实现1. 轧制过程模拟:通过算法模型,模拟轧制过程中的轧制力、轧制温度、轧制速度等参数,以获得准确的轧制结果。
2. 轧后冷却过程模拟:基于冷却介质、冷却速度、冷却温度等参数,模拟轧后冷却过程,以获得最佳的冷却效果。
3. 数据分析与优化:根据模拟结果,提供数据分析和优化建议,帮助用户提高生产效率和产品质量。
4. 用户界面:提供用户友好的界面,方便用户进行操作和查看模拟结果。
《中厚板轧制和轧后冷却过程离线模拟软件的开发》

《中厚板轧制和轧后冷却过程离线模拟软件的开发》篇一中厚板轧制与轧后冷却过程离线模拟软件的开发一、引言在现代化钢铁工业中,中厚板轧制及轧后冷却工艺作为关键的环节之一,对于保证钢材质量和提升生产效率起着至关重要的作用。
为有效应对复杂的工艺过程与生产需求,中厚板轧制与轧后冷却过程离线模拟软件的开发显得尤为重要。
该软件可帮助钢铁企业实现生产过程的数字化、智能化管理,提高产品质量和生产效率。
本文将详细探讨中厚板轧制与轧后冷却过程离线模拟软件的开发过程及其重要性。
二、开发背景与意义随着钢铁工业的快速发展,中厚板产品的需求量日益增长,对产品质量和生产效率的要求也日益提高。
为满足市场需求,提高生产效率和产品质量,必须对中厚板轧制及轧后冷却过程进行精确控制。
然而,由于该过程涉及众多复杂的物理和化学变化,单纯依靠传统的生产经验和现场操作难以实现精确控制。
因此,开发一款中厚板轧制与轧后冷却过程离线模拟软件显得尤为重要。
该软件的开发意义在于:首先,通过模拟实际生产过程,帮助企业实现生产过程的数字化、智能化管理;其次,通过对轧制及轧后冷却过程的精确模拟,可优化生产工艺,提高产品质量和生产效率;最后,通过实时监控生产过程,降低能耗和生产成本,提高企业的市场竞争力。
三、软件开发流程1. 需求分析:根据钢铁企业的实际需求,确定软件的功能和性能要求。
包括轧制和轧后冷却过程的模拟、工艺参数的优化、生产过程的监控等。
2. 方案设计:根据需求分析结果,设计软件的整体架构和各模块功能。
包括数据采集模块、数据处理模块、模拟计算模块、结果输出模块等。
3. 编程实现:按照方案设计,进行编程实现。
采用合适的编程语言和开发工具,确保软件的稳定性和可靠性。
4. 测试与调试:对编程实现的软件进行测试与调试,确保软件的功能和性能达到预期要求。
5. 用户界面设计:根据用户需求,设计友好的用户界面,方便用户使用和操作。
6. 文档编写:编写用户手册、技术文档等相关资料,方便用户使用和维护软件。
《2024年中厚板轧制和轧后冷却过程离线模拟软件的开发》范文

《中厚板轧制和轧后冷却过程离线模拟软件的开发》篇一一、引言随着现代工业技术的不断发展,中厚板的轧制和轧后冷却过程对于提高产品质量、降低生产成本以及优化生产流程具有至关重要的作用。
为了更好地模拟这一复杂过程,提高生产效率和产品质量,开发一款中厚板轧制和轧后冷却过程的离线模拟软件显得尤为重要。
本文将详细介绍该软件的开发过程、关键技术以及预期的效益。
二、软件开发的背景及意义中厚板是钢铁行业中应用广泛的材料,其轧制和轧后冷却过程的控制对于产品性能和质量有着决定性的影响。
然而,该过程涉及多变量、多物理场耦合的复杂系统,传统的实验和现场调试方法效率低下且成本较高。
因此,开发一款离线模拟软件,能够在不进行实际生产的情况下对轧制和冷却过程进行模拟和优化,对于提高生产效率、降低成本以及优化产品质量具有重要意义。
三、软件开发的关键技术1. 数学建模:建立中厚板轧制和轧后冷却过程的数学模型,包括轧制力计算、温度场分析、组织性能预测等。
这需要运用材料科学、力学、热学等多学科知识。
2. 软件开发:采用先进的编程语言和开发工具,如C++、Python等,开发离线模拟软件。
软件应具备友好的用户界面,方便用户输入参数和查看结果。
3. 算法优化:针对中厚板轧制和轧后冷却过程的复杂性,采用优化算法对模拟过程进行优化,提高模拟的准确性和效率。
4. 数据库管理:建立数据库管理系统,用于存储模拟结果、历史数据以及生产参数等信息,方便用户查询和管理。
5. 交互式界面设计:设计交互式界面,使用户能够直观地了解模拟过程,方便用户进行参数调整和结果分析。
四、软件开发流程1. 需求分析:明确用户需求,确定软件的功能和性能要求。
2. 系统设计:根据需求分析结果,设计软件的系统架构、数据库结构和算法模型等。
3. 编程实现:按照系统设计,使用编程语言和开发工具进行编程实现。
4. 测试与调试:对软件进行测试和调试,确保软件的稳定性和准确性。
5. 用户培训与支持:为用户提供培训和技术支持,确保用户能够熟练使用软件。
《2024年中厚板轧制和轧后冷却过程离线模拟软件的开发》范文

《中厚板轧制和轧后冷却过程离线模拟软件的开发》篇一一、引言随着现代工业技术的不断发展,中厚板的轧制和轧后冷却过程对于产品质量和效率的重要性日益凸显。
为了更好地优化这一生产过程,提高产品质量和生产效率,离线模拟软件的开发显得尤为重要。
本文旨在探讨中厚板轧制和轧后冷却过程离线模拟软件的开发,从需求分析、设计思路、技术实现等方面进行详细阐述。
二、需求分析在中厚板轧制和轧后冷却过程中,离线模拟软件的需求主要包括以下几个方面:1. 精确模拟轧制过程:包括轧制力、轧制温度、轧制速度等参数的模拟,以及板材变形、应力分布的模拟。
2. 冷却过程模拟:包括冷却液的流动、温度分布、冷却速度等参数的模拟。
3. 结果可视化:将模拟结果以图表、曲线等形式进行展示,便于分析和优化。
4. 用户交互性:提供友好的用户界面,支持参数设置、模型调整、结果查看等功能。
三、设计思路针对中厚板轧制和轧后冷却过程的离线模拟软件,设计思路主要包括以下几个方面:1. 模块化设计:将软件分为数据输入模块、模拟计算模块、结果输出模块等,便于后期维护和功能扩展。
2. 数学模型建立:基于物理原理和工艺要求,建立精确的数学模型,包括轧制力学模型、热传导模型、流体力学模型等。
3. 算法选择与优化:选择合适的算法进行模拟计算,如有限元法、差分法等,并对算法进行优化,提高计算精度和效率。
4. 可视化与交互性设计:采用图表库、交互式界面等技术,实现结果的可视化和用户交互性。
四、技术实现在技术实现方面,中厚板轧制和轧后冷却过程离线模拟软件的开发涉及以下关键技术:1. 数据处理技术:包括数据采集、预处理、存储等技术,确保数据的准确性和可靠性。
2. 数值计算技术:采用高效的数值计算方法,如有限元法、差分法等,实现快速、准确的模拟计算。
3. 可视化与交互性技术:利用图表库、交互式界面等技术,实现结果的可视化和用户交互性。
4. 软件架构设计:采用模块化、层次化的软件架构设计,便于后期维护和功能扩展。
《2024年中厚板轧制和轧后冷却过程离线模拟软件的开发》范文

《中厚板轧制和轧后冷却过程离线模拟软件的开发》篇一一、引言随着现代工业技术的不断发展,中厚板的轧制与轧后冷却过程在制造业中占据着举足轻重的地位。
这一过程涉及到复杂的物理、化学变化和力学性能变化,要求极高的精度和效率。
因此,开发一款针对中厚板轧制和轧后冷却过程的离线模拟软件显得尤为重要。
本文将详细探讨该软件的开发过程、技术要点及其应用价值。
二、软件开发背景及需求分析中厚板作为钢铁产品的重要一环,其轧制和轧后冷却过程直接影响到产品的质量和性能。
传统的生产过程主要依赖操作人员的经验和现场调试,这不仅效率低下,而且难以保证产品的稳定性和一致性。
因此,开发一款能够准确模拟这一生产过程的离线模拟软件,对于提高产品质量、降低生产成本、优化生产流程具有重要意义。
在需求分析阶段,我们深入了解了用户的需求,包括对轧制和轧后冷却过程的精确模拟、对不同工艺参数的优化分析、以及与实际生产过程的衔接等。
此外,考虑到软件的易用性和扩展性,我们还需在设计中充分考虑到用户界面的友好程度以及软件的兼容性等问题。
三、软件开发技术及方法1. 开发平台:选用高效、稳定的软件开发平台,如Python或C++等,以便实现高效算法的集成和优化。
2. 数学模型:基于中厚板轧制和轧后冷却过程的物理、化学和力学原理,建立精确的数学模型,以描述这一过程的物理变化和性能变化。
3. 算法设计:针对不同工艺参数和材料特性,设计高效的算法,以实现模拟过程的快速、准确计算。
4. 界面开发:采用图形化界面设计,使用户能够直观地操作软件、查看模拟结果和分析数据。
5. 数据库管理:建立数据库管理系统,以存储和管理模拟过程中产生的数据,方便用户进行数据分析和比对。
四、软件功能实现1. 轧制模拟:根据建立的数学模型和算法,模拟中厚板的轧制过程,包括轧制力、轧制温度、轧制速度等参数的实时计算和显示。
2. 轧后冷却模拟:模拟中厚板轧制后的冷却过程,包括冷却速度、温度分布等参数的预测和分析。
- 1、下载文档前请自行甄别文档内容的完整性,平台不提供额外的编辑、内容补充、找答案等附加服务。
- 2、"仅部分预览"的文档,不可在线预览部分如存在完整性等问题,可反馈申请退款(可完整预览的文档不适用该条件!)。
- 3、如文档侵犯您的权益,请联系客服反馈,我们会尽快为您处理(人工客服工作时间:9:00-18:30)。
s t na dfn t f h yt s w r , sd bl ga dr i i l x li d i d ti. t i n ci o ess m dtae i e I西n n m “ a a oepan ea mc o ∞s t e t g g d s e n l
棒 材 轧 后 控 冷 工 艺 微 机 控 制 系统 软 件 的 设 计
杜 天苍 刘 华 付小 美 ( 京 石 油 化 工 学 院 北 京 ,0 60 北 120 ) 摘 要 : 绍 了棒 材 轧 后 控 冷 工 艺 微 机 控 制 系 统 软 件 的 设 计 方 法 。 重 点 叙 述 了 控 制 要 点 和 对 介
()水 量 设 定 模 型 要 反 应 锕 种 规 格 、 始 冷 却 3 开
温度 、 水 温 度 等 参 数 的 影 响 。 在 冷 床 上 设 置 钢 温 进 规 定 精 度 时 , 水 量设 定 模 型 进 行 自学 习 修 正 。 对
度 检 测 点 , 测 自 回火 温 度 并 与 目标 值 比较 , 实 当超 过
计 算 及 预 设 定 。终 轧 后 对 该 轧 件 再 次 测 温 Байду номын сангаас 自学 习
图 1 棒 材控 玲 工 艺示 意 图 , 工 艺一 般 是轧 为 该
件 出 精 轧 机 组 后 , 即 进行 冷 却 , 分 利 用 钢 在 高 温 立 充 轧 制时 的细化 效 果。 冷却 后 自回火 温 度 的高 低 , 对 最 终 性 能有 显 著影 响 。 而 这 个 温度 又 与 冷 却 水 量 和 冷 却 时 间 、 温 等 因 数 有 关 。 根 据 生 产 需 要 和 现 场 水 实 际条 件 , 出 如 下 控 制要 点 : 提 ()棒 材 冷 却 后 的 表 面 自回 火 温 度 为 控 制 目标 1 值 ; 却 水 量 为 控 制 量 ; 却 时 间 由 冷 却 器 长度 决 定 冷 冷 ( 终 轧 速 度 基 本 固 定 ) 因 。
能质 量 。整 个 生 产 过 程 中 还 存 在 一 些 环 境 、 性 等 特
T m ] 精轧 机^ 口 、 1 持 却嚣 ^ 1 ) 1 l: r 出: 3( 3 : 窖捌轧 件祖 度 " 1 庠 ^ 口宴 ■ 轧件 卣回 强 度 挣
Ql 4四十 分东 管宴捌 东 谴 量 -Q :
维普资讯
自动 化 与 仪 器 仪 表 ZfON l) GHU Y YI A U QIYI AO BI 20 0 2年 第 1期 ( 总第 9 9期 )
文 章 编 号 :0 1—9 2 (0 2 0 —0 1 10 2 7 2 0 1 1 0 3—0 3
算 , 后 进 行 调 节 , 问 上 是 不 允 许 的 。 为 此 , 精 然 时 在
轧 人 口设 置 测 温仪 , 用 该 点 实 测 钢 温 经 温 度 预 报 利 1 冷 却 工 艺 控 制 要 点 和对 控 制程 序 的 要 求
1 1 冷 却 工 艺 控 制 要 点 .
模 型 计 算 出 开 始 冷 却 温 度 预 报 值 , 以 此 进 行 水 量 并 修 正预报模 型有关参 数。
H DI I I 、 w: 轧机^ 1 M 、 Y s 精  ̄ 2 3 : 出 口( 抟却 器^ 1 ) 持床 ^ 1 轧件 3 : 和 : 3
位 置 拴荫 信号
变 化 因 数 , 而 , 不 断 进 行 自学 习 修 正 数 学 模 型 的 因 需
一
图 1 棒 材 控 冷 工 艺 示 意 图
控 制冷 却 控 制 软 件
.
控 制 程 序 的 要 求 ; 统 软 件 的 构 成 和 功 能 以及 软 件 调 试 和 运 行 。 系
关键 词 : 材 棒
A S R C A d g eh do u B T A T:  ̄i m to f c—bsdcmrl yt sf aef o t l 0 h o terl db r n ae o o s m t r o c nr ( fh o e a s e ow r ocd l
()总 管 水 压 和 总 流 量 互 相 翩 约 , 者 不 能 同 4 二
时 调 节 , 则 引 起 系 统 震 荡 。 为 使 水 路 系统 稳 定 运 否
}fY 0RDS: a C nr l∞0 (三 W Br o to I C nr lsf r o t ot e o wa
中 图 分 类 号 :P 7 T 22
O 前 言
文 献 标 识 码 : B
棒 材 轧 后 控 冷 工 艺 可 有 效 地 提 高 产 品 性 能 质 量 , 约 能 源 , 低 材 料 消 耗 。 其 方 法 是 根 据 产 品钢 节 降 种、 规格 、 目标 自 回 火 温 度 , 测 开 始 冷 却 温 度 和 进 实 水 温 度 , 算 并 设 定 所 需 冷 却 水 量 , 轧后 棒 材进 行 计 对 冷却, 以达 到 规 定 的 自回 火 温 度 , 而 提 高 产 品 的 性 从
些参 数 , 系统工 作 在 最佳 状 态 。该工 艺 已在唐 使
( )水 量 调 节 阎 惯 性 太 , 渡 时 问 长 , 水量 调 2 过 使
钢 第 一 轧 钢 厂 取 得 了成 功 , 益 显 著 。 本 文 主 要 介 效
绍这 一工艺 微机 控制软件 的设计 。
节 变 化 迟 缓 。 由终 轧 出 口实 测 钢 温 进 行 水 量 设 定 计