第二章 材料的变形塑性变形1
材料的塑性变形

22:10
11
滑移带和滑移线只是晶格滑移结果的表象; 重新抛光后可去除。
光镜下:滑移带。 电境下:滑移线。
22:10
12
问题二:
产生滑移的条件?
滑移面 :??? 滑移方向:????
22:10
13
产生滑移的条件:
2.1材料的塑性变形机理
面间距大; 滑移矢量(柏氏矢量)小;
+ + ++++ + + ++++
22:10
49
塑性变形的另一种方式
孪生
2.1材料的塑性变形机理
在切应力作用下,晶体一部分相对于另一部分沿一定
的晶面和晶向发生均匀切变,形成晶体取向的
镜面对称关系。双胞胎!
孪晶的形成 (动画)
孪生动画\孪 生变形.swf 变形
22:10
51
22:10
52
1. 孪生晶体学 晶体的孪晶面和孪生方向与晶体结构类型有关。
滑移面 :密排面 滑移方向:密排方向
fcc滑移系: 滑移面{111}, 滑移方向<110>; 滑移系
4×3=12个
22:10
Cu,Al,Ni,Au,γ-Fe等 塑性变形能力如何?
17
α-Fe,W,Mo等
塑性变形能力如何?
22:10
18
次滑移系:
Mg,Zn,Ti,Zr等
22:10
塑变能力? 20
44
☺ 滑移的表面痕迹 : ☺ 单滑移:单一方向的滑移带; ☺ 交滑移:波纹状的滑移带。 ☺ 多滑移:相互交叉的滑移带;
2.1材料的塑性变形机理
奥氏体钢交叉滑移带
问题二:
产生滑移的条件? 结构上
滑移面 :??? 滑移方向:????
第二章 金属材料的塑性变形与性能

9
根据载荷作用性质不同:
a)拉深载荷 --拉力 b)压缩载荷 —压力 c)弯曲载荷 --弯力 d)剪切载荷--剪切力 e)扭转载荷--扭转力
10
2.内力 (1)定义 工件或材料在受到外部载荷作用时,为使其不变形,在 材料内部产生的一种与外力相对抗的力。 (2)大小 内力大小与外力相等。 (3)注意 内力和外力不同于作用力和反作用力。
2
§1.金属材料的损坏与塑性变形
1.常见损坏形式
a)变形
零件在外力作用下形状和尺寸所发生的变化。 (包括:弹性变形和塑性的现象。
c)磨损
因摩擦使得零件形状、尺寸和表面质量发生变化的现象。
3
2.常见塑性变形形式 1)轧制 (板材、线材、棒材、型材、管材)
28
2)应用范围 主要用于:测定铸铁、有色金属及退火、正火、 调质处理后的各种软钢或硬度较低的 材料。 3)优、缺点 优点:压痕直径较大,能比较正确反映材料的平均 性能;适合对毛坯及半成品测定。 缺点:操作时间比较长,不适宜测定硬度高的材料; 压痕较大不适合对成品及薄壁零件的测定。
29
2.洛氏硬度(HR)——生产上应用较广泛 1)定义 采用金刚石压头直接测量压痕深度来表示材料的硬度值。 2)表示方法
11
3.应力 (1)定义 单位面积上所受到的力。 (2)计算公式 σ= F/ S( MPa/mm2 ) 式中: σ——应力; F ——外力; S ——横截面面积。
12
二、金属的变形 金属在外力作用下的变形三阶段: 弹性变形 弹-塑性变形 断裂。 1.特点 弹性变形: 金属弹性变形后其组织和性能不发生变化。 塑性变形: 金属经塑性变形后其组织和性能将发生变化。 2.变形原理 金属在外力作用下,发生塑性变形是由于晶体内部 缺陷—位错运动的结果,宏观表现为外形和尺寸变化。
材料的塑性变形
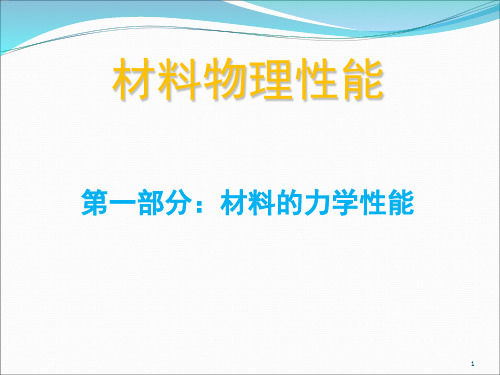
修 正 : m ’ ≈ G-G或 m ’ ≈ G。
1050
30
14
2.3 晶格缺陷——位错
2.3.1 位错的基本概念(dislocation)
(1)定义:线状缺陷。
实际晶体在结晶时,受到杂质、温度变化或振动产 生的应力作用或晶体由于受到打击、切割等机械应力作 用,使晶体内部原子排列变形,原子行列间相互滑移, 不再符合理想晶体的有序排列,形成线状缺陷,即为位 错。
15
2.3.1 位错的基本概念(dislocation)
(1)定义:线状缺陷。
位错的提出——解释晶体的塑性变形。
塑性变形理论 滑移模型,1920 线缺陷(位错)模型,1934
建立位错理论,1956
16
2.3.1 位错的基本概念(dislocation) 1934年 Taylor、Polanyi、Orowan三人几乎同 时提出晶体中位错的模型。
τm——完整晶体屈服强度,晶 体受到的切应力超过τm后产生永久 变形,即为晶体的塑性变形。
a.E-x变化曲线; b. τ-x变化曲线
12
2.2 理想晶体的强度
在 原 子 位 移 很 小 的 情 况 下 , -x曲 线 的 斜 率 为 /x,
故 m 2π = bx
根 据 胡 克 定 律 : =G ≈ G x a
位错线 运动方向
晶体 切应力 滑移面 滑移方向 方向 个数
⊥位错线本身 与b一致 与b一致 唯一
⊥位错线本身 与b一致 与b一致 多个
混合
与位错线 成一定角度
⊥位错线本身
与b一致 与b一致
36
2.3.3 位错运动理论
(2)位错的攀移
位错除滑移外,还可以产生攀移,由于热运动,原子 之间扩散,空位扩散到位错处,使位错上移,杂质离子扩 散到位错处,使位错下移。
第二章 材料的变形——塑性变形1
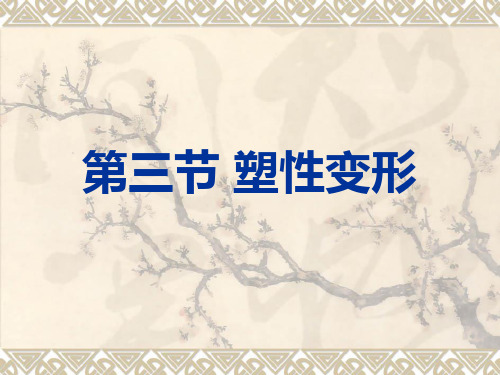
许多滑移系并非同时参与滑移。只有当外力 在某一滑移系中的分切应力达到一定临界值 时,该滑移系方可首先发生滑移,该分切应 力称为滑移的临界分切应力。 沿滑移面滑移方向的分切应力; 能够引起滑移系开动的分切应力。
切应力的作用下,晶格发生弹性外扭,进一步将使晶格发生滑 移。外力去除后,由于原子到了一新的平衡位置,晶体不能恢 复到原来的形状,而保留永久的变形。大量晶面的滑移将得到 宏观变形效果,在晶体的表面将出现滑移产生的台阶。
向(孪生方向)发生切变,形成对称的晶格排列,发生切变
部分叫做孪生带,或简称为孪晶。切变部分和未切变部分 呈镜面对称,对称面为孪生面。
孪生变形的特点
孪生需要的临界切应力很大,仅在滑移困难时才会发 生。一般孪生出现在滑移系很少的晶体结构的材料中 (如密排六方晶格金属);某些容易发生滑移的立方材 料仅在低温度滑移困难或受冲击时来不及滑移时才可 能产生孪生。 孪生是一种均匀切变,即切变区内与孪晶面平行的每 一层原子面均相对于其毗邻晶面沿孪生方向位移了一 定的距离,移动量都相同。
滑移、孪生、蠕变、晶界滑动。
2.1 滑移
单晶体的塑性变形的主要方式是滑移和
孪生。其中滑移是最基本、最普遍的塑 性变形方式,孪生只是在滑移难以进行 的情况下出现。
单晶体的圆柱试样表面抛光后拉伸,试样表
面就会出现一系列平行的变形痕迹。 光镜观察,试样表面形成的浮凸,由一系列 滑移迹线组成,称为滑移带。
就越来越大。
此外,塑性变形也会导致晶格畸变,使外力和滑移面的相 对位向也会发生变化。使开动位错所需应力增大。
பைடு நூலகம்
2.2孪生变形
——孪晶:两个晶体或者晶体的两个部分沿
一个公共晶面构成镜面堆成的位向关系
吉林大学工程材料第2章 金属的塑性变形和再结晶
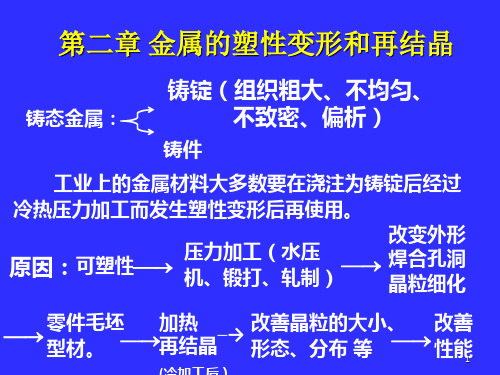
1、晶粒正常长大: 再结晶后的晶粒均匀、稳速地长大的现象。发生在
再结晶晶粒细小且均匀时。(希望的长大方式)
2、晶粒异常长大:
再结晶后的晶粒不均匀,急剧长大的现象。在再结晶 粒大小不均时,大晶粒吞并小晶粒,将得到异常粗大的 晶粒,也称“二次再结晶”。
d晶↑ 晶界面积↓ 能量↓∴晶粒长大是自发的 过程。因为粗晶是弱化,所以要避免晶粒长大,特别要
方向 σb(MPa) σ0.2(MPa) δ(%) ψ(%) αk(KJ/M2)
平行 701 垂直 659
460
17.5 62.8
608
431
10.0 31.0
294
34
四 、热加工的不足
在实际生产中,热加工与冷加工相比也有不足处
(1)热加工需要加热,不如冷加工简单易行。 (2)热加工制品的组织与性能不如冷加工均匀和易 于控制。
目的:1. 消除加工硬化 使、σ、HB↓ δ%、 %、ak↑ 2. 消除内应力,但保留加工硬化,使理化性能↑
对于冷加工后的金属,由于10%的变形能储存在 金属中,在加热时,随着温度的升高,原子活动能力 提高,在变形能的作用下,就要发生组织和性能的变 化,其主要包括三个阶段:回复、再结晶及晶粒长大。
18
底面对角线
1 面×3 方向=3
7
4、滑移机理
临界切应力(c): 能够发生滑移的最小切应
力叫做为)。当切应力()满足 c时滑移才 能发生。
铜的滑移临界切应力:理论计算 1500 Mpa 实际测试 1 MPa
滑移是由于滑移面上的位错运动造成的。
8
位错运动造成滑移示意图
9
10
二、 多晶体金属的塑性变形
700℃
第二章 弹性变形及塑性变形

1、弹性变形的物理本质
外力(F)与原子间引力(a / r m)、斥力(b / r n) 的平衡过程。
FfFab0 nm rm rn
2、弹性常数
E = 2 (1+ )G
E: 正弹性模量(杨氏摸量) :柏松比 G:切弹性模量
3、固体中一点的应力应变状态
z z z
多晶体的塑性变形
3 晶界对变形的阻碍作用 (1)晶界的特点:原子排列不规则;分布有大量缺陷。 (2)晶界对变形的影响:滑移、孪生多终止于晶界,极少 穿过。
3 晶界对变形的阻碍作用
(3)晶粒大小与性能的关系 a 晶粒越细,强度越高(细晶强化:霍尔-配奇公式) s=0+kd-1/2
原因:晶粒越细,晶界越多,位错运动的阻力越大。 (有尺寸限制)
材料来说会产生弹性变形、塑性变形,直至断裂。
物体受外力作用产 生了变形,除去外力 后物体发生的变形完 全消失,恢复到原始 状态的变形。
弹性变形示意
材料的弹性变形应用
弹簧是一种利用弹性来工作的机械零件。
材料的弹性变形应用
弹簧是一种利用弹性来工作的机械零件。
弹性变形: 变形可逆; 应力应变呈 线性关系。来自0e0
e
3、内耗 Q-1
弹性滞后使加载时材料吸收的弹性 变形能大于卸载时所释放的弹性变形能, 即部分能量被材料吸收-弹性滞后环的 面积。
工程上对材料内耗应加以考虑
4、包申格效应
产生了少量塑性变形的材料,再同向加载 则弹性极限与屈服强度升高;反向加载则弹性 极限与屈服强度降低的现象。
2.5 材料的塑性变形
二 孪生:在切应力作用下,晶体的一部分相对于另一部分 沿一定的晶面和晶向发生均匀切变并形成晶体取 向的镜面对称关系。
塑性变形_精品文档
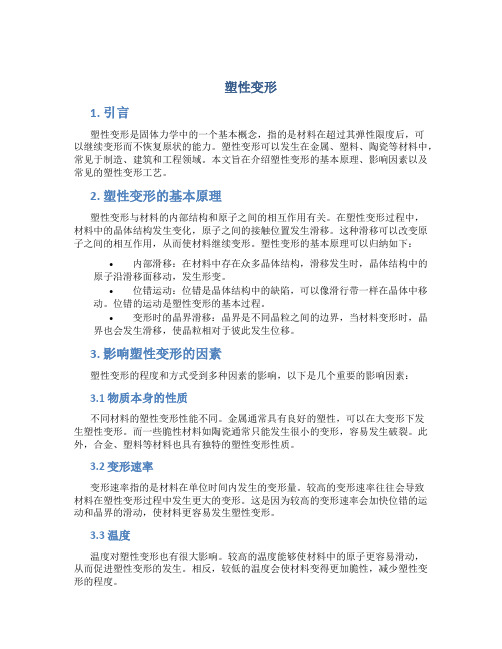
塑性变形1. 引言塑性变形是固体力学中的一个基本概念,指的是材料在超过其弹性限度后,可以继续变形而不恢复原状的能力。
塑性变形可以发生在金属、塑料、陶瓷等材料中,常见于制造、建筑和工程领域。
本文旨在介绍塑性变形的基本原理、影响因素以及常见的塑性变形工艺。
2. 塑性变形的基本原理塑性变形与材料的内部结构和原子之间的相互作用有关。
在塑性变形过程中,材料中的晶体结构发生变化,原子之间的接触位置发生滑移。
这种滑移可以改变原子之间的相互作用,从而使材料继续变形。
塑性变形的基本原理可以归纳如下:•内部滑移:在材料中存在众多晶体结构,滑移发生时,晶体结构中的原子沿滑移面移动,发生形变。
•位错运动:位错是晶体结构中的缺陷,可以像滑行带一样在晶体中移动。
位错的运动是塑性变形的基本过程。
•变形时的晶界滑移:晶界是不同晶粒之间的边界,当材料变形时,晶界也会发生滑移,使晶粒相对于彼此发生位移。
3. 影响塑性变形的因素塑性变形的程度和方式受到多种因素的影响,以下是几个重要的影响因素:3.1 物质本身的性质不同材料的塑性变形性能不同。
金属通常具有良好的塑性,可以在大变形下发生塑性变形。
而一些脆性材料如陶瓷通常只能发生很小的变形,容易发生破裂。
此外,合金、塑料等材料也具有独特的塑性变形性质。
3.2 变形速率变形速率指的是材料在单位时间内发生的变形量。
较高的变形速率往往会导致材料在塑性变形过程中发生更大的变形。
这是因为较高的变形速率会加快位错的运动和晶界的滑动,使材料更容易发生塑性变形。
3.3 温度温度对塑性变形也有很大影响。
较高的温度能够使材料中的原子更容易滑动,从而促进塑性变形的发生。
相反,较低的温度会使材料变得更加脆性,减少塑性变形的程度。
3.4 应力状态材料受到的应力状态也会影响其塑性变形。
在拉伸应力作用下,材料会发生延伸变形;而在剪切应力作用下,材料会发生屈服变形。
不同应力状态下,材料的塑性变形方式有所不同。
4. 常见的塑性变形工艺塑性变形工艺是一种通过对材料施加力来改变其形状和尺寸的方法。
弹性变形与塑性变形课件

对于金属材料,合金成分对晶格常数的改变不大,因 此其合金化对E改变不大。 在只要求增加抗变形刚度的场合,没必要选择合金, 因此,结构材料只用碳钢即可满足要求。
合金中形成高熔点高弹性模量的第二相质点,可提高弹性模量
学习交流PPT
21
2.2 弹性变形 6、影响弹性模量的因素
3)温度
5
2.2 弹性变形 1、弹性变形的物理本质
外力引起的原子间距的变化,即位移, 在宏观上就是所谓弹性变形。
外力去除后,原子复位,位移消失,
弹性变形消失,从而表现了弹性变形
的学可习交逆流PP性T 。
6
2.2 弹性变形
2、固体中一点的应力应变状态
z z z
z x x z
z y y z
x y y x x x
学习交流PPT
10
谁是“弹性定律”的提出者?
唐初,贾公彦对郑玄的注疏又作了进一步的注释。他指出: “郑又云‘假令弓力胜三石,引之中三尺’者,此即三石力弓 也。必知弓力三石者,当‘弛其弦,经绳缓擐之’者,谓不张 之,别以一条绳系两箫,乃加物一石张一尺,二石张二尺,三 石张三尺。” 从《考工记》的记述来看,当时制作的弓大多为三石(即90斤) 拉力的弓,这可能是当时较为标准的弓。
变曲线上的相应值,卸载时也立即恢
复原状,即加载与卸载应在同一直线
上,应变与应力始终保持同步。
0
e
学不完整性 2、弹性滞后(滞弹性)
在实际材料中有应变落后于应力现象,这种现象叫做滞弹性 (非瞬间加载条件下的弹性后效)
加载和卸载时的应力应变曲线不重合 形成一封闭回线 —— 弹性滞后环
学习交流PPT
24
2.3 弹性极限与弹性比功 1、比例极限 p
材料科学基础_材料的塑形变形

第三节
• • • • •
滑移的位错理论分析
滑移的实质是位错的运动 位错的增殖 位错的交割 位错的塞积 加工硬化
滑移的实质是位错的运动
大量的理论研究证明,滑移原来是由于滑移面上 的位错运动而造成的。图示例子表示一刃型位错在切 应力的作用下在滑移面上的运动过程,通过一根位错 从滑移面的一侧运动到另一侧便造成一个原子间距的 滑移。
滑移的实质是位错的运动
位错的滑移面就是晶体的滑移面,柏氏矢量的 方向就是晶体的滑移方向。为了使位错的能量较低, 在结构容许的条件下,尽量减小柏氏矢量,所以原子 的密排方向就成为了位错的柏氏矢量的方向。
位错的增殖
塑性变形的过程中,尽管位错移出晶体产 生滑移台阶,但位错的数量(位错密度)却在不 断的增加,这是因为在外应力作用下发生塑性 变形时位错会发生增殖。
3. 应变:物体形状尺寸所发生的相对改变。物体内部 某处的线段在变形后长度的改变值同线段原长之比 值称为“线应变”;物体内两互相垂直的平面在变 形后夹角的改变值称为“剪应变”或“角应变”; 变形后物体内任一微小单元体体积的改变同原单位 体积之比值称为“体积应变”。
变形过程
低碳钢的拉伸曲线如 图所示。 在应力低于弹性极限 σ e时,材料发生的 变形为弹性变形;应 力在σ e到σ b之间将 发生的变形为均匀塑 性变形;在σ b之后 将发生颈缩;在K点 发生断裂。
塑性变形过程--颈缩
1. 颈缩:试样将开始发生不均匀的塑性变形, 产生了颈缩,即塑性变形集中在一局部区域 进行。 2. 特点:颈缩发生后,宏观表现为外力在下降, 工程应力在减小,但颈缩区的材料承受的真 实应力依然在上升。
3. 极限强度:材料开始发生颈缩时对应的工程 应力σ b ,这时试样出现失稳,颈缩真实应 力依然在上升,但能承受的总外力在下降。
02 材料的变形
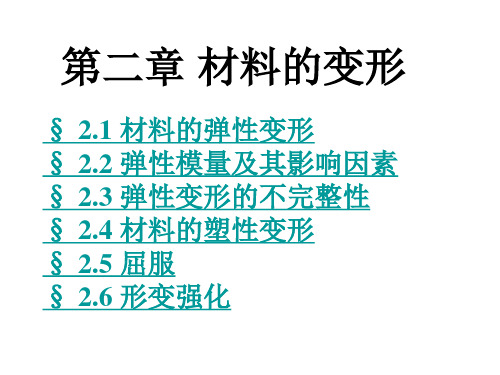
① 金属本质及晶格类型
A、晶格阻力 : 派—纳力
2G 2W exp 1 b
G-切变模量 2 13 ν-泊松比 b-滑移方向上的原子间距,柏氏 矢量的模 W-位错宽度:W=a/(1-ν) a-滑移面的晶面间距
p n
B、 开动F-R源所需的切应力
T Gb Gb br 2r L
C、位错交互作用阻力
包括平行交互作用和林位错交互作用
Gb
2 15
平行位错下,ρ为主滑移面位错密度; 林位错下, ρ为林位错密度
② 晶粒大小和亚结构
⊥ ⊥ ⊥ ⊥ ⊥⊥ ⊥ O
晶 界 Hall—Petch公式:
二、弹性模量的影响因素
凡影响键合强度的因素均能影响材料的弹性模量,如键合方式、 晶体结构、化学成分、微观组织、温度及加载方式和速度等。
对金属材料E:
1)原子半径和晶体学特征:
非过渡族,原子半径↑、 E↓;
过渡族,原子半径↑、E↑, 且E一般都较大。
原子密排向的E大(单晶 体)。
2)化学成分:
单晶体的屈服强度随取向因子而改变
;
值小,硬取向。
陶瓷材料的塑性变形
①金属键没有方向性,而离子键与共价键都具有明显的 方向性; ②金属晶体的原子排列取最密排、最简单、对称性高的 结构,而陶瓷材料晶体结构复杂,对称性低; ③金属中相邻原子(或离子)电性质相同或相近,价电 子组成公有电子云,属于整个晶体。陶瓷材料中,若为 离子键,则正负离子相邻,位错在其中若要运动,会引 起同号离子相遇,斥力大,位能急剧升高。 基于上述原因,位错在金属中运动的阻力远小于陶瓷,极易产 生滑移运动和塑性变形。陶瓷中,位错很难运动,几乎不发生 塑性变形。
工程材料与机械制造基础-第2章

图 低碳钢的σ-ε曲线
图 低碳钢的σ-ε曲线 图 铸铁的σ-ε曲线
第一阶段oe:弹性阶段。弹性极限:σe 第二阶段es:屈服阶段。屈服极限:σs 第三阶段sb:强化阶段。强度极限:σb 第四阶段bz:缩颈阶段(截面积减小,载荷下降) 。z:试样断裂。
(1)延伸率(伸长率)
L L1 L0 100%
屈服强度:
s
Ps F0
(MPa)
抗拉强度:
b
Pb F0
(MPa)
s /b
叫屈强比,一般为0.65-0.75。 屈强比越小,可靠性越高。 屈强比越大,强度利用率越高,可靠性降低。
金属材料的强度与其化学成分和工艺过程 ,尤其是热处理工艺有密切的关系。
如: (1)纯金属的抗拉强度低
纯铁为200MPa,铜为60MPa,铝为40MPa (2)铁碳合金:退火状态下
σ-1 —— 疲劳强度, MPa
δ —— 伸长率、延伸率 αK —— 冲击韧性,J/cm2
7.比较45HRC 650HBW 800HV 240HBS的大小。 答:800HV >650HBW>45HRC>240HBS
树立质量法制观念、提高全员质量意 识。20. 10.2420 .10.24Saturday , October 24, 2020 人生得意须尽欢,莫使金樽空对月。1 7:50:38 17:50:3 817:50 10/24/2 020 5:50:38 PM 安全象只弓,不拉它就松,要想保安 全,常 把弓弦 绷。20. 10.2417 :50:381 7:50Oc t-2024- Oct-20 加强交通建设管理,确保工程建设质 量。17:50:3817 :50:381 7:50Saturday , October 24, 2020 安全在于心细,事故出在麻痹。20.10. 2420.1 0.2417:50:3817 :50:38 October 24, 2020 踏实肯干,努力奋斗。2020年10月24 日下午5 时50分 20.10.2 420.10. 24 追求至善凭技术开拓市场,凭管理增 创效益 ,凭服 务树立 形象。2 020年1 0月24 日星期 六下午5 时50分 38秒17 :50:382 0.10.24 严格把控质量关,让生产更加有保障 。2020 年10月 下午5时 50分20 .10.241 7:50Oc tober 24, 2020 作业标准记得牢,驾轻就熟除烦恼。2 020年1 0月24 日星期 六5时50 分38秒 17:50:3 824 October 2020 好的事情马上就会到来,一切都是最 好的安 排。下 午5时50 分38秒 下午5 时50分1 7:50:38 20.10.2 4 专注今天,好好努力,剩下的交给时 间。20. 10.2420 .10.241 7:5017:50:381 7:50:38 Oct-20 牢记安全之责,善谋安全之策,力务 安全之 实。202 0年10 月24日 星期六5 时50分 38秒Sa turday , October 24, 2020 相信相信得力量。20.10.242020年10月 24日星 期六5 时50分3 8秒20. 10.24
第二章_金属塑性变形的物理基础

超塑性的特点
超塑性变形的一般特点: 1、大伸长率 2、无缩颈 3、低流动应力 4、易成形
采用超塑性成形工艺,可获得形状复杂和尺寸精确的锻件, 而变形力大大降低 。
超塑性成形实例
b 弥散强化
位错切过第二相粒子(表面能、错排能、 粒子阻碍位错运动)
四 塑性变形对金属组织和性能的影响
1 对组织结构的影响 (1) 形成纤维组织
晶粒拉长 杂质呈细带状或链状分布
H62黄铜挤压的带状组织
(2) 亚结构
变形量增大 位错缠结 位错胞 (大量位错缠结在胞壁,胞内位错密度低)
(3) 形变织构
四 塑性变形对金属组织和性能的影响
2 对力学性能的影响(加工硬化) (1)加工硬化(形变强化、冷作强化):随变形 量的增加,材料的强度、硬度升高而塑韧性下降 的现象。
2 对力学性能的影响(加工硬化)
强化金属的重要途径
利 提高材料使用安全性
(2)利弊
材料加工成型的保证
弊 变形阻力提高,动力消耗增大
孪生的特点
(1)孪生是一部分晶体沿孪晶面相对于另一部分晶体 作切变,切变时原子移动的距离是孪生方向原子间距的 分数倍;孪生是部分位错运动的结果;孪晶面两侧晶体 的位向不同,呈镜面对称;孪生是一种均匀的切变。
孪生的特点
(2)孪晶的萌生一般需 要较大的应力,但随后长 大所需的应力较小,其拉 伸曲线呈锯齿状。孪晶核 心大多是在晶体局部高应 力区形成。变形孪晶一般 呈片状。变形孪晶经常以 爆发方式形成,生成速率 较快。
位错密度越高,金属的强度、硬度越高。
S:位错线长度,V:体积,ρ:位错密度
第二章 金属材料的损坏与塑性变形
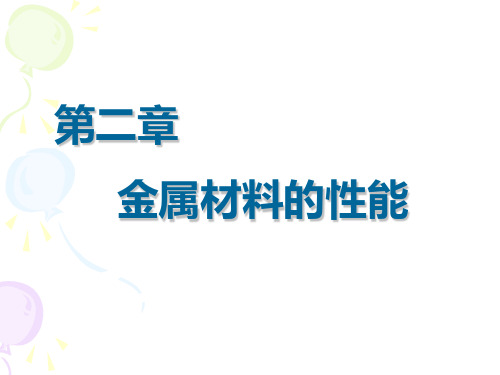
四、冲击韧性 金属材料抵抗冲击载荷作用而不破坏的 能力称为冲击韧性。材料的冲击韧性用 一次摆锤冲击弯曲实验来测定。 试样规格: U形或V形缺口的式样。
试样从一定高度被击断后,缺口处单位 横截面面积上吸收的功,即表示冲击韧 度值。
Ak k S0
αk—冲击韧度,J/cm2,αk值越大,材料的冲击韧性 越好;
符号HR前面的数字表示硬度值。HR后面的字母 表示不同的洛氏硬度标尺。
(3)常用洛氏硬度标尺及其适用范围:
HRA适用于测量硬质合金、表面淬火层或渗碳层; HRB适用于测量有色金属和退火、正火钢等; HRC适用于测量调质钢、淬火钢等。 洛氏硬度操作简便、迅速,应用范围广,压痕小,硬度 值可直接从表盘上读出,所以得到更为广泛的应用。
(4)洛氏硬度实验法的优缺点
优点:操作简单迅速,能直接从刻度盘上读 出硬度值;压痕较小,可以测定成品及较薄 工件;测试的硬度值范围大,可测从很软到 很硬的金属材料。 缺点:压痕小,当材料的内部组织不均匀时, 硬度数据波动较大,测量值的代表性差,通 常需要在不同部位测试数次,取其平均值来 代表金属材料的硬度。
F 2F HBW 0.102 2 2 S D( D D d )
S—球面压痕表面积,mm2;
F—实验力,N;
D—压头直径,mm;
D—压痕平均直径,mm。
一般情况不用计算,而是根据压痕直径 查表得出布氏硬度值。
(2)布氏硬度的表示方法 符号HBW之前的数字为硬度值,符号后 面按以下顺序用数字表示实验条件。 1)球体直径 2)实验力 3)实验力保持的时间(10~15s不标注)
金属材料的断后伸长率和断面收缩率越 高,其塑性越好。
三、硬度
材料抵抗局部变形,特别是塑性变形、 压痕或划痕的能力称为硬度。 常用的硬度实验法有布氏硬度实验法、 洛氏硬度实验法、维氏硬度实验法。
材料力学性能-2-材料变形
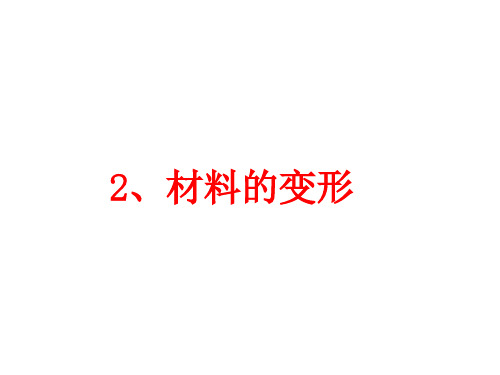
在对称性最高的各向同性体中,广义的Hooke定律为:
例:单轴拉伸(如X方向)时, 广义的Hooke定律简化为:
由此可见,在单轴加载条件下, 材料不仅有受力方向上的变形, 而且还有垂直于受力方向上的横 向变形(应变)。
工程常用弹性常数
• 弹性模量(E) σ E = (单向受力状态下) ε 它反映材料抵抗正应变的能力。 • 切变模量(G) τ G = (纯剪受力状态下) ν 它反映材料抵抗切应变的能力。 • 泊松比(ν ) ε ν =− (单向-X方向受力状态下) ε 它反映材料横向正应变与受力方向正应变的相对 比值。
2.4 材料的塑性变形
单晶体和多晶体材料塑性变形的特点
3)形变织构和各向异性 随着塑性变形程度的增加,各个晶粒的滑移方向逐 渐向主形变方向转动,使多晶体中原来取向互不相同的 各个晶粒在空间取向逐渐趋向一致,这一现象称为择优 取向;材料变形过程中的这种组织状态称为形变织构。
滞弹性与内耗
• 材料的内摩擦-内耗,导致振动机械能转 变为热能而消耗 • 研究目的:1、通过内耗特性,研究材料内 部的微观结构信息,如溶质原子浓度、位 错与溶质原子的交互作用等。2、获得高阻 尼合金,使结构振动衰减,减振降噪,提 高设备的运行精度。
求导得: 即:
dφ (u ) / du = u (d 2φ / du 2 )0
F = u (d 2φ / du 2 )0
实际上,对大块金属材料而言, 通常能达到的弹性变形量很小,主 要是因为实际材料中不可避免地存 在缺陷,在外力作用下,弹性变形 还未达到其最大可能值之前就已经 发生了塑性变形或断裂。因此,实 际金属材料中,可以认为Hooke定 律是正确的。
可逆性 单值性
正弹性应变-由正应力引起;
第2[1].3章 金属超塑性变形分析解析
![第2[1].3章 金属超塑性变形分析解析](https://img.taocdn.com/s3/m/19fd65ddd5bbfd0a7956735f.png)
第三节 金属的超塑性变形
对力学性能的影响主要表现为:
(1)超塑性变形后合金仍保持均匀细小的等轴晶组织,不存 在织构,所以不产生各向异性,且具有较高的抗应力腐蚀 能力。 (2)超塑性成形时,由于变形温度稳定、变形速度缓慢,所 以零件内部不存在弹性畸变能,变形后没有残余应力。 (3)对某些超塑性合金,存在加工软化现象,即硬度随压缩 率的增加而降低。 (4)高铬高镍不锈钢经超塑性变形后,形成细微的双相混合 组织,具有很高的抗疲劳强度。
第三节 金属的超塑性变形
晶界滑动和扩散蠕变联合机理(A-V机理)示意图
a.四个六边 形等轴晶粒 在应力作用 下,发生晶 粒滑动 c.四个晶粒发 生转动,形 成新的组态, 仍保持等轴 晶粒 晶粒转换机制的二维表示法
b在应力作用 下,发生晶粒 滑动,同时依 靠晶界扩散, 保持联结
d、e.伴随定向扩散的晶界滑动机制,虚线箭头代表体扩散方向
有人把上述的第二类及第三类超塑性统称为动态超 塑性,或环境超塑性。
第三节 金属的超塑性变形
二、超塑性变形机理
目前有这样几种解释: ①晶界滑移的作用;
超细晶粒材料的晶界有异乎寻常大的总面积,因此晶界运动在超塑性 变形中起着极其重要的作用。晶界运动分为滑动和移动两种,前者为 晶粒沿晶界的滑移,后者为相邻晶粒间沿晶界产生的迁移。 在研究超塑性变形机理的过程中,曾提出了许多晶界滑动的理论模型。
金属塑性成形原理
第二章 金属塑性变形的物理基础
第三节 金属的超塑性变形
主讲:刘华 华侨大学模具技术研究中心
第三节 金属的超塑性变形
一、超塑性概念及种类
概念:在一定条件下进行热变形,材料可得到特别大的 均匀塑性变形,而不发生缩颈,延伸率可达 500~2000%,材料的这种特性称为超塑性 特点: 大伸长率 无缩颈 低流动应力 对应变速率敏感 无加工硬化 易成形
第二章 塑性变形--第二节 塑性变形对组织和性能的影响

8
三、织构现象的产生
( 1 )形变织构:多晶体材料由塑性变形导致的 各晶粒呈择优取向的组织。变形量达到70-90%时 产生。 (2)类型 丝织构:某一晶向趋 于与拔丝方向平行。(拉 拔时形成) 板织构:某晶面趋于 平行于轧制面,某晶向趋 于平行于主变形方向。 (轧制时形成)
9
形变织构对性能的影响 力学性能:深冲板材变形易产生制耳。(各向异性) 物理性能:硅钢片{100}[100]织构可减少铁损。
6
加工硬化的利弊 (1)利 强化金属的重要途径(如铝、铜、不锈 钢); 材料加工成型的保证(如冷拔钢丝); 提高材料使用安全性。 (2)弊 变形阻力提高,动力消耗增大.
7
塑性变形对材料物理、化学性能的影响 导电率、导磁率下降,比重、热导率下降; 结构缺陷增多,扩散加快; 化学活性提高,腐蚀加快。
Ⅰ 残余应力易引起变形、开裂,如黄铜弹壳的腐蚀开裂体的加工硬化效应比单晶体强。晶粒越细,硬化效应越 强。
5
总结
1.固溶体的加工硬化:主要通过柯氏气团对位错 的钉扎作用。 2.单晶体的加工硬化:主要通过位错间的相互纠 缠作用。 3.多晶体的加工硬化:除了位错间的相互纠缠作 用外,还有晶界对位错运动的阻碍作用。多晶体 的加工硬化效应比单晶体的加工硬化效应强。
三个阶段组成: I阶段——易滑移阶 段; Ⅱ阶段——线性硬化 阶段; Ⅲ阶段——抛物线型 硬化阶段
3
位错的交割 晶体中位错线的方位各式 各样,不同滑移面上运动的位 错在运动中相遇就有可能发生 位错互相切割现象,称之为位 错的交割. 位错的交割的结果在原来 是直的位错线上形成一段一个 或几个原子间距大小的折线 (割阶),使原来的位错线变 长,能量增加,因此交割过程 对位错运动具有阻碍作用,使 变形过程中产生应变硬化。
材料的变形和塑性应变
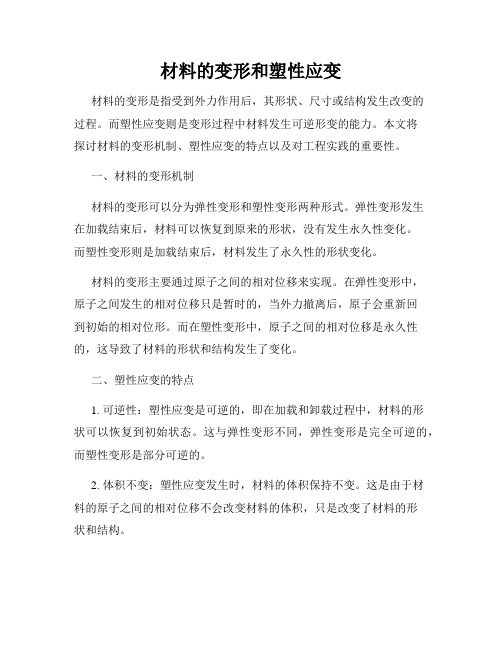
材料的变形和塑性应变材料的变形是指受到外力作用后,其形状、尺寸或结构发生改变的过程。
而塑性应变则是变形过程中材料发生可逆形变的能力。
本文将探讨材料的变形机制、塑性应变的特点以及对工程实践的重要性。
一、材料的变形机制材料的变形可以分为弹性变形和塑性变形两种形式。
弹性变形发生在加载结束后,材料可以恢复到原来的形状,没有发生永久性变化。
而塑性变形则是加载结束后,材料发生了永久性的形状变化。
材料的变形主要通过原子之间的相对位移来实现。
在弹性变形中,原子之间发生的相对位移只是暂时的,当外力撤离后,原子会重新回到初始的相对位形。
而在塑性变形中,原子之间的相对位移是永久性的,这导致了材料的形状和结构发生了变化。
二、塑性应变的特点1. 可逆性:塑性应变是可逆的,即在加载和卸载过程中,材料的形状可以恢复到初始状态。
这与弹性变形不同,弹性变形是完全可逆的,而塑性变形是部分可逆的。
2. 体积不变:塑性应变发生时,材料的体积保持不变。
这是由于材料的原子之间的相对位移不会改变材料的体积,只是改变了材料的形状和结构。
3. 局部应变:塑性应变主要发生在材料的局部区域,这与弹性应变相对应。
在弹性变形中,应变是均匀分布的,而在塑性变形中,应变主要集中在局部区域。
三、塑性应变在工程实践中的重要性塑性应变在工程实践中具有重要的意义和应用价值。
1. 材料加工:塑性应变是材料加工的基础。
通过塑性变形,材料可以被加工成各种形状和尺寸的零部件,满足不同工程需求。
例如,在金属加工中,通过塑性变形可以制造出各种精密零件和复杂结构。
2. 结构设计:塑性应变的控制可以提高结构的承载能力和抗变形能力。
工程结构中的材料常常需要承受大的外力作用,通过合理控制塑性应变,可以保证结构的稳定性和安全性。
3. 优化设计:塑性应变的分布对于材料性能的优化设计起着重要的作用。
通过调整材料中的塑性应变分布,可以改善材料的力学性能和耐久性。
四、总结本文介绍了材料的变形和塑性应变的相关概念,探讨了塑性应变的特点以及在工程实践中的重要性。
材料的塑性变形

材料的塑性变形材料的塑性变形是材料力学学科中的一个重要概念,指的是材料在受力作用下发生的可逆性变形过程。
塑性变形是材料的一种特性,表现为材料在一定温度和应力情况下,发生塑性变形后不会恢复到原状态。
本文将从塑性变形的定义、性质、影响因素和应用领域等方面展开探讨。
材料的塑性变形是指材料在外力的作用下,呈现出形状的变化,这种变化是可逆的。
与弹性变形不同的是,塑性变形是在超过材料的屈服点后发生的,且发生塑性变形后,材料不会完全恢复到原来的形状。
塑性变形是材料内部晶格结构发生改变的结果,通过滑移、重结晶等机制实现。
塑性变形是材料力学中一个重要的研究对象,它与材料的性能密切相关。
在工程实践中,我们常常需要考虑材料在受力状态下的塑性变形性能,以确保材料在服役过程中不会发生意外事故。
此外,塑性变形还与材料的加工性能、成形性能等密切相关,因此对塑性变形的研究具有重要的理论和实际意义。
塑性变形的性质主要包括以下几个方面:1. 可逆性:塑性变形是可逆的,并且不会引起材料的永久形变。
2. 体积不变性:塑性变形并不改变材料的体积。
3. 定向性:塑性变形是有方向性的,取决于材料的晶体结构和加载方向。
塑性变形的影响因素主要包括应力、温度和变形速率等。
在一定温度条件下,应力越大,材料的塑性变形越明显;温度越高,材料发生塑性变形的能力越强;变形速率对于塑性变形的影响也非常显著,通常情况下,变形速率越大,材料的塑性变形越明显。
材料的塑性变形在工程实践中有着广泛的应用。
例如,金属材料的塑性变形性能直接影响着金属制品的成形性能;塑料制品的塑性变形特性决定了其在加工过程中的可塑性等。
因此,通过研究材料的塑性变形特性,可以指导工程实践中材料加工的选择和工艺优化,提高材料的利用率和产品质量。
总之,材料的塑性变形是材料力学中一个重要的研究领域,具有重要的理论和实际意义。
通过深入研究材料的塑性变形特性,可以有效地指导工程实践中材料的选择和制造过程,为优化材料性能和提高产品质量提供理论支持。
- 1、下载文档前请自行甄别文档内容的完整性,平台不提供额外的编辑、内容补充、找答案等附加服务。
- 2、"仅部分预览"的文档,不可在线预览部分如存在完整性等问题,可反馈申请退款(可完整预览的文档不适用该条件!)。
- 3、如文档侵犯您的权益,请联系客服反馈,我们会尽快为您处理(人工客服工作时间:9:00-18:30)。
? 阵点(原子、分子、离子或 者原子团)在三维空间中呈 周期性规则排列形成的阵列 称为 空间点阵 ,简称 点阵。
? 在点阵中取出具有代表性的 基本单元(最小平行六面体) 作为点阵的组成单位,称为 晶胞 。
? 晶胞选取原则:
? 反映出点阵的对称性
? 棱和角相等的数目最多
? 直角数目最多
? 有最小的体积
对于Al单晶:每根滑移线的滑移量为100~200nm;两滑移线间距~20nm; 滑移带之间~2000nm
一、滑移变形的概念
? 是晶体在切应力作用下,一部分晶体相对 于另一部分沿一定晶面(滑移面)和晶向 (滑移方向)产生的相对位移,且不破坏晶 体内部原子排列规律性的塑变方式叫滑移。
二、滑移的晶体学特征
三、滑移的临界分切应力
? 滑移系只提供了金属滑移的可 能性,而金属在外力的作用下 滑移的驱动力是 沿滑移面滑移 方向上的分切应力 。
? 单晶体受力后,外力在任何晶 面上都可分解成正应力和切应 力。正应力只能引起弹性变形 及断裂。只有在切应力的作用 下金属晶体才能产生塑性变形。
临界分切应力
? 晶体滑移是在切应力作用下进行的,但其中 许多滑移系并非同时参与滑移。只有当外力 在某一滑移系中的分切应力达到一定临界值 时,该滑移系方可首先发生滑移,该分切应 力称为滑移的临界分切应力。
滑移、孪生、蠕变、晶界滑动。
2.1 滑移
? 单晶体的塑性变形的主要方式是滑移和 孪生。其中滑移是最基本、最普遍的塑 性变形方式,孪生只是在滑移难以进行 的情况下出现。
? 单晶体的圆柱试样表面抛光后拉伸,试样表 面就会出现一系列平行的变形痕迹。
? 光镜观察,试样表面形成的浮凸,由一系列 滑移迹线组成,称为滑移带。
左图中单晶体受拉应力 F作用, 滑移面法线方向 N与F夹角为f, 滑移方向和 F夹角为λ;注意: 滑移方向 S、拉力轴 F和滑移面 的法线 N三者不必在同一平面, 即 f+λ≠900 。
? 求该平行线上任一点的 坐标值并化为最小整数。 加方括号即为所求晶向。
晶向指数代表着所有互相平行、方向一致的晶向。 若所指方向相反,则晶向指数数字相同,但符号相反。
晶面指数确定步骤
? 设定坐标系,但不能将 坐标原点选在待定的晶 面上。
? 求得待定晶面在三个坐 标轴上的截距,如与某 坐标轴平行,则截距为 ∞。
晶向指数和晶面指数
? 为更好表明晶体生长、变形、相变及性能等问题中 的原子位置、原子列的方向和原子构成的平面,采 用密勒(Miller )指数来统一标定 晶面指数和晶向 指数 。
? 晶向:任意两个原子连线所指的方向 ? 晶面:原子构成的平面
晶向指数确定步骤
? 选择一个阵点作为原点, 过原点作所求晶向的平 行线。
? 取各截距的倒数,化为 最小整数。加上圆括号, 即晶面指数。
晶面指数代表着一组平行的晶面。
FCC
×6
×4
×2
×3
×3
滑移系对性能的影响
? 晶体中滑移系愈多,晶体发生滑移的可能性便愈大, 材料的塑性愈好。
? 滑移面密排程度高,滑移面上滑移方向个数越多,材 料塑性越好。
? bcc的α-Fe与fcc的Al及Cu,虽然都有12个滑移系,但体 心立方滑移面密排程度较面心立方晶格低,且滑移面 上滑移方向少,所以塑性不如铜及铝;具有hcp晶格的 Mg、Zn等,滑移系仅有3个,因此塑性较立方晶系金 属差。
? 边长a、b、c和镜面夹角 α、β、γ作为点阵常数表 示晶胞。
? 一共7种类型——7个晶系
立方
体心立方
面心立方
布
拉
菲
点
正交
体心正交
底心正交
面心正交
阵
四方
体心四方
单斜
ห้องสมุดไป่ตู้底心单斜
菱方
六方
三斜
Cu
NaCl
CaF2
金属中三种典型的晶体结构
体心立方: 钼、钨、α-Fe
面心立方: 铝、铜、γ-Fe
密排六方: 镁、锌、铍、镉
? 滑移系的数目=(滑移面的个数)×(每 个面上所具有的滑移方向的个数)
? 具体晶体内滑移系的数目是确定的
?晶格类型? ?密排面?
回顾晶体学基础
? 晶体与非晶体的区别?
? 晶体中的原子(或分子、离子)在三维空间中呈 周期性的重复排列 ————长程有序
? 有固定熔点 ? 各向异性
? 非晶体
? 没有固定的外形 ? 无固定熔点 ? 各项同性
? 滑移线(Slip Line ):滑移带中的细线。滑移线是滑移面两 侧晶体相对滑动所造成的。滑移带和滑移线间的晶体片层并 未发生塑性变形,仅仅发生了相对滑动。
? 滑移层:相邻滑移线间的晶体片层。
? 滑移量:每条滑移线所产生的台阶高度。
光学显微镜:滑移带 电子显微镜:每条个滑移带由许多平行滑移线组成
第三节 塑性变形
材料在外力作用下会产生变形,首先产生 弹性变形。当应力 超过材料的弹性极限时,金属将产生 塑性变形。
塑性变形
? 当外载荷在材料内部所产生的内应力超过了 材料的屈服强度以后,即使去掉外载荷,变 形也不能完全消失的变形称为塑性变形。
? 它不仅改金属的外形,而且使内部组织和结 构发生变化。经过塑性变形后的金属,在随 后的加热过程中,内部组织也发生一系列变 化,这些都对性能有明显的影响。
1、塑性变形特点
? 塑性变形过程中仍然保持着弹性变形,又称 弹塑性变形阶段。
? 变形量较大 ? 应力-应变不呈线性关系 ? 与温度和时间有关系 ? 结构敏感性能
2、塑性变形的机理
材料在外力作用下发生塑性变形, 依材料的性质、外界环境和受力方式不 同,进行塑性变形的方式也不相同。 ?通常发生塑性变形的方式有:
? 沿滑移面滑移方向的分切应力; ? 能够引起滑移系开动的分切应力。
切应力的作用下,晶格发生弹性外扭,进一步将使晶格发生滑 移。外力去除后,由于原子到了一新的平衡位置,晶体不能恢 复到原来的形状,而保留永久的变形。大量晶面的滑移将得到 宏观变形效果,在晶体的表面将出现滑移产生的台阶。
施密特定律
推动滑移的是在滑移方向上的 分切应力。同一外加应力作用 下,不同滑移系因取向不同, 对应的分切应力也不相同。
? 滑移通常沿原子密度最大的晶面 和晶向发生。
? 这一晶面和晶向分别称为 滑移面 和滑移方向。
? 一个滑移面和其面上任一滑移方 向组成一个滑移系。
? 滑移系的特点:
?滑移面总是晶体的 密排面,滑移方向也总 是密排方向
? 每一种晶格类型的金属都具有特定的滑移 系。滑移系的多少一定程度上决定了金属的 塑性好坏。